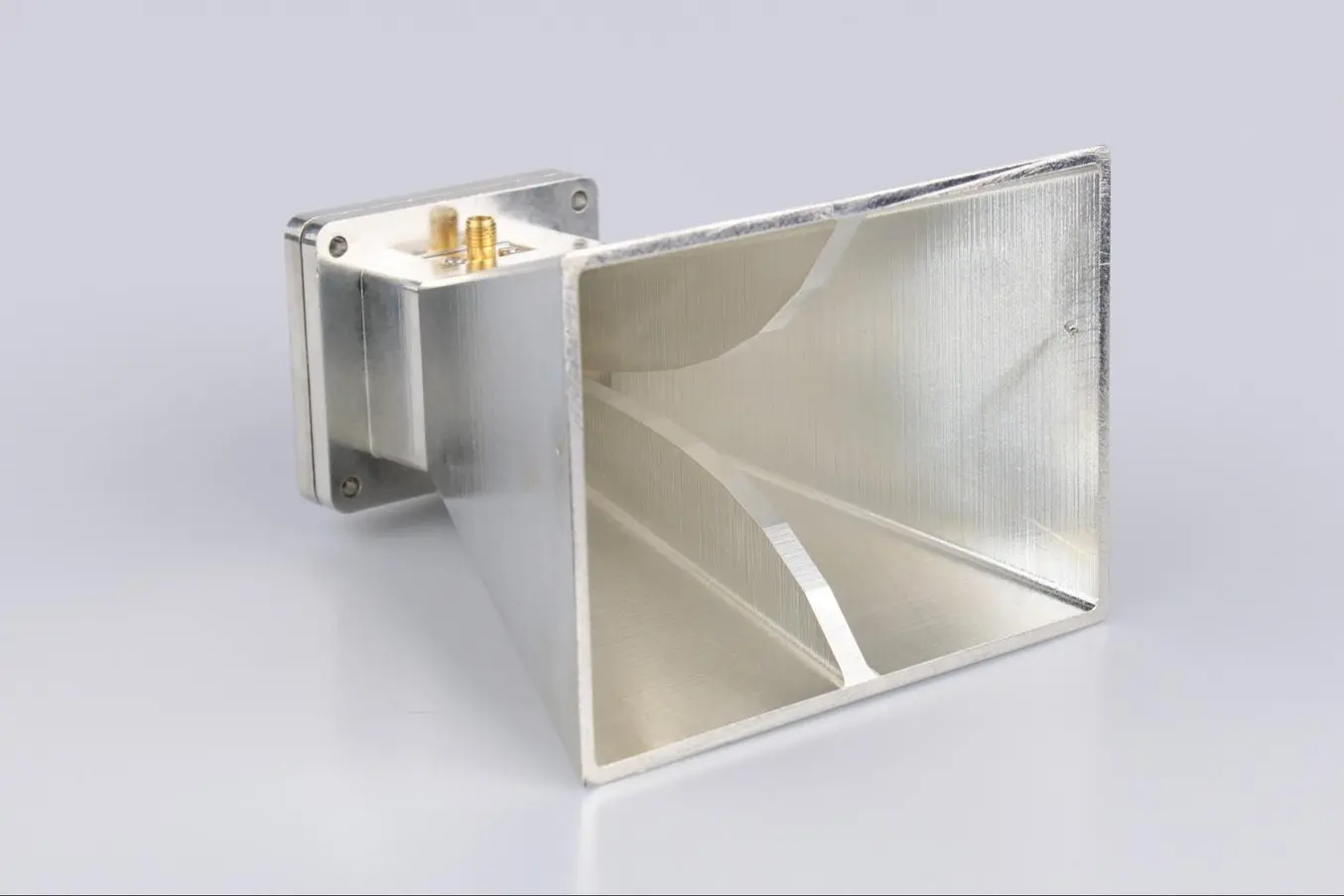
Die Firma Elliptika mit Sitz im französischen Brest ist spezialisiert auf das Design und die Entwicklung von HF- und Mikrowellenprodukten und -lösungen. Das Unternehmen entwirft maßgefertigte Spitzenfilter und -antennen für die Forschung und Entwicklung in der Automobilindustrie, im Verteidigungswesen, der Medizin, der Bildung oder auch bei Weltfirmen wie Thales.
Dabei musste Elliptika die Grenzen traditioneller Fertigungstechniken überwinden, damit die Antennen den hohen Anforderungen entsprechen – z. B. mit kompakter Größe oder extremer Verstärkungsleistung – und gleichzeitig kostengünstig und schnell umsetzbar bleiben.
Im Folgenden erfahren Sie von Elliptikas Radio Frequency Designern Gwendal Cochet und Alexandre Manchec, wie man dort mit 3D-Druck und Galvanisierung bei der Fertigung von Hochleistungsantennen die Kosten und Durchlaufzeiten um über 90 % reduziert.
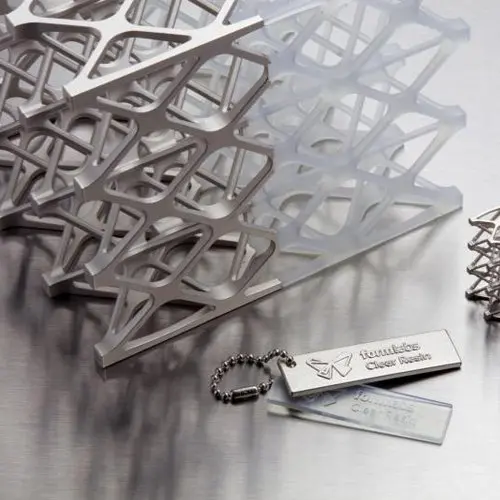
Eine Alternative zum Metall-3D-Druck aus einem Drucker für 3500 €
In diesem Webinar erfahren Sie, wie Galvanisierung die Materialpalette des SLA-3D-Drucks in der Produktion hochfester und verschleißbeständiger Endverbrauchsteile bereichert. SLA-Druck ermöglicht die Umsetzung komplexer Sonderanfertigungen und Galvanisierung verleiht diesen SLA-Teilen Metall-ähnliche Eigenschaften wie beispielsweise einen hohen Elastizitätsmodul, elektrische Leitfähigkeit oder metallische Ästhetik.
Webinar ansehenWie die Galvanisierung von 3D-Druckteilen funktioniert
Antennen müssen den elektrischen Strom leiten können, um Funkwellen zu übertragen. 3D-Druckteile leiten zwar keine Elektrizität, bieten dafür aber fast grenzenlose Designfreiheit sowie Materialien mit herausragenden mechanischen und thermischen Eigenschaften. Diese Vorteile lassen sich mit Galvanisierung kombinieren, um die gewünschte Leitfähigkeit zu erzielen. Das macht diese Kombination zu einer großartigen Lösung für maßgefertigte Antennen.
Das Team bei Elliptika hat verschiedene additive Fertigungsverfahren ausprobiert und entschied sich für Stereolithografie-3D-Druck (SLA) als beste Grundlage für die Galvanisierung.
„Die Oberflächen unserer HF-Komponenten müssen glatt sein, da bei Unebenheiten Verluste auftreten. Wenn wir also beispielsweise einen FDM-Drucker (Schmelzschichtung) mit großen Schichten verwenden, wird das zum Problem. Neben erhöhten Verlusten führen Unebenheiten der Teile auch beim Galvanisierungsprozess zu Schwierigkeiten, weil die Metallbeschichtung nicht haften bleibt. Bei SLA-Teilen sparen wir uns solche Probleme“, so Cochet.
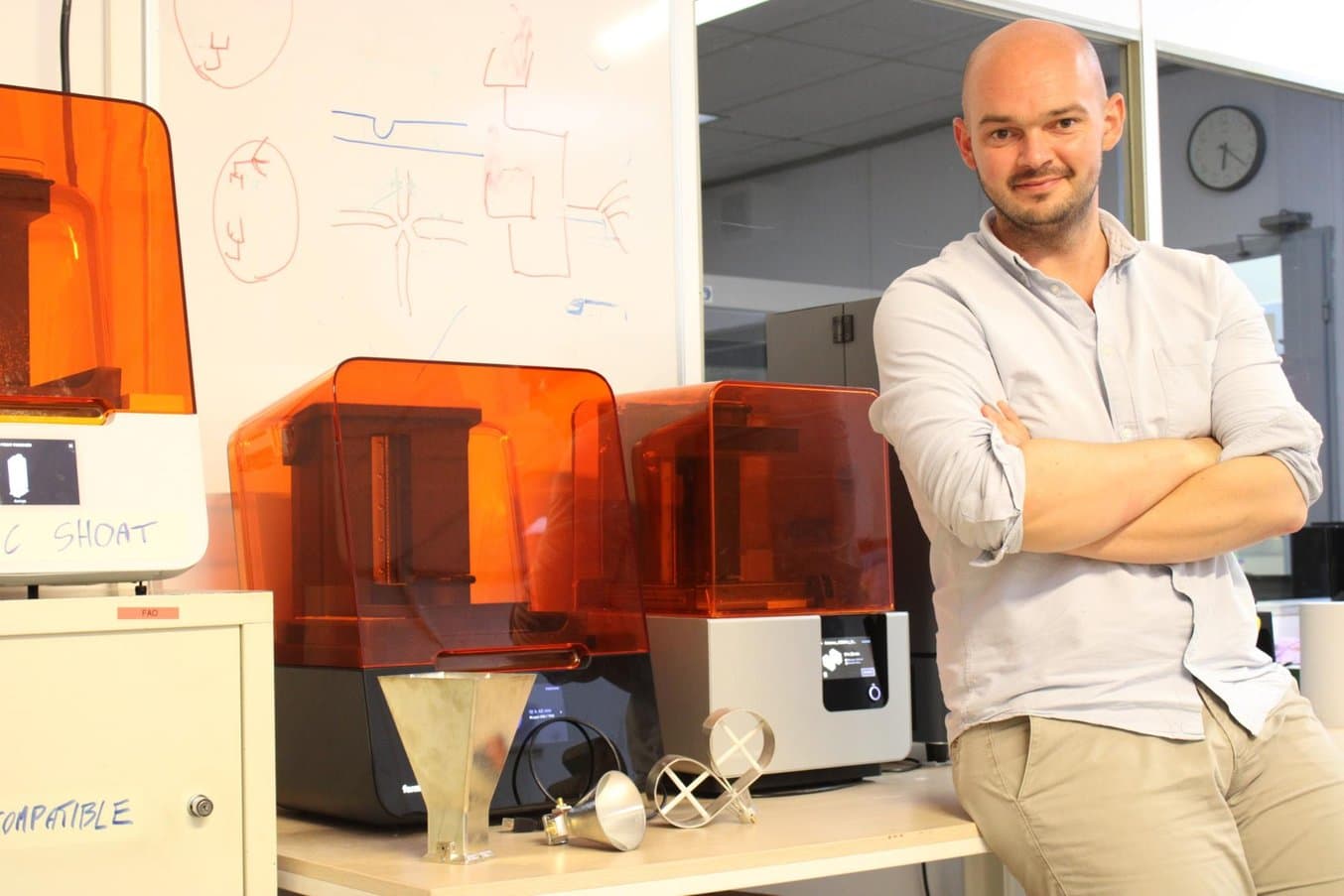
Angefangen hat das Team mit dem SLA-Drucker Form 2 und kaufte später den Nachfolger Form 3. Vor Kurzem folgten dann noch sieben Drucker vom Typ Form 3B, um Hilfsprojekte während der COVID-19-Pandemie zu unterstützen. Die Teile für die Galvanisierung werden hauptsächlich aus White Resin hergestellt, zudem kamen auch bereits Tough Resin und High Temp Resin für mechanische Teile zum Einsatz.
Und so funktioniert der Galvanisierungsprozess:
„Nach dem Druck des Teils entfernen wir die Stützstrukturen, reinigen die Oberfläche und härten es nach. Dann wird das Druckteil in chemischen Prozessen mit einer dünnen Schicht (ca. 3 µm) Kupfer überzogen. Zu guter Letzt folgt dann die Oberfläche des Teils, zum Beispiel eine dickere Zinnschicht“, erklärt Cochet.
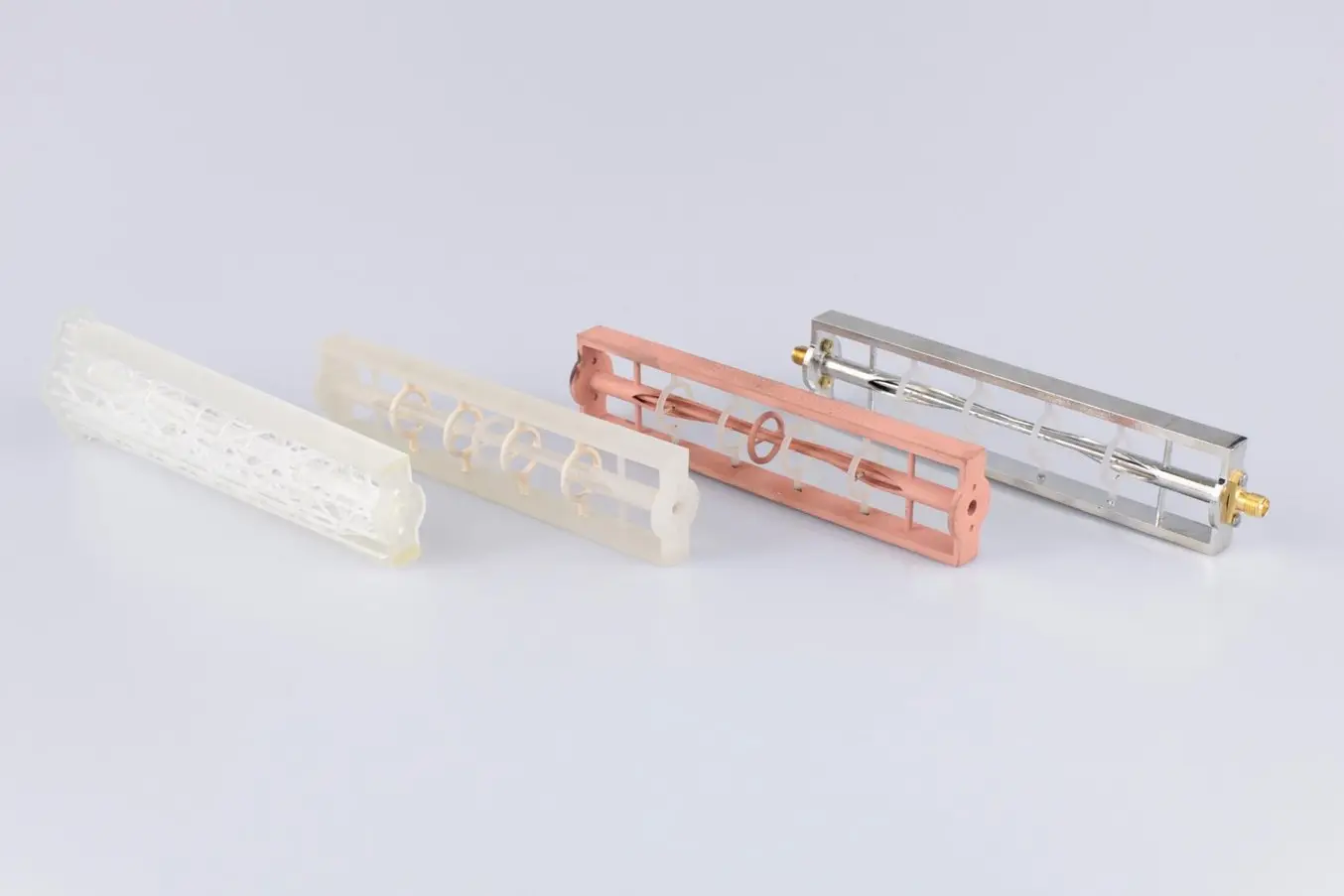
Die unterschiedlichen Galvanisierungsphasen, von links nach rechts: 3D-Druckteil aus Kunststoff, nachgehärtetes Teil mit entfernten Stützstrukturen, galvanisiertes Teil mit Kupferüberzug, das fertig galvanisierte Teil mit Zinnüberzug.
Kosten und Durchlaufzeiten um über 90 % reduzieren
Da die meisten Antennen in der Forschung und Entwicklung zum Einsatz kommen, muss Elliptika nur Kleinstserien von 1 bis 20 Teilen herstellen.
„Der 3D-Druck ist für uns äußerst interessant, da wir so komplexe Antennen zu einem sehr attraktiven Preis produzieren können. Wir wollen nicht mit anderen Lösungen wie Zerspanung oder Spritzguss arbeiten“, berichtet Alexandre.
Mit diesen traditionellen Herstellungsverfahren kann die Produktion einer Antenne bis zu drei Monate in Anspruch nehmen. Faktoren dabei sind die Durchlaufzeit zur Herstellung der benötigten Werkzeugbestückung und das Hin und Her mit dem Dienstleister bezüglich der Designdetails.
„Mit betriebsinternem 3D-Druck haben wir in nur zwei Tagen funktionsbereite Teile. Ein Tag zum Drucken, ein Tag zum Galvanisieren und los. Es geht also viel, viel schneller. Auch der Preis macht einen entscheidenden Unterschied. Im Outsourcing kostet die Herstellung einer Antenne ungefähr 3000 €. Gedruckt sind wir vielleicht bei 20 €. So rentieren sich die Kosten dieser Antenne [unter Einbeziehung der Anschaffungskosten des Druckers] schon beim ersten Auftrag“, gibt Cochet an.
Herstellung einer Antenne | Kosten | Durchlaufzeit |
---|---|---|
SLA-3D-Druck | 20€ | 2 Tage |
Outsourcing | 3,000€ | Bis zu 3 Monate |
Individualisierung und schnelle Entwicklung eröffnen neue Chancen auf dem Markt
Die Kombination aus 3D-Druck und Galvanisierung hat für das Unternehmen auch neue Marktsegmente erschlossen.
„Vor dem 3D-Druck haben wir uns nur auf Leiterplattenantennen und Filter konzentriert. Jetzt stellen wir auch volumenspezifische Teile her. Das war schon möglich, aber nicht für so kleine Betriebe wie uns. Unsere Kunden erwarten schnelle Entwicklung neuer Antennen. Und dafür war es für uns einfach zu langsam und zu kostspielig, bevor wir 3D-Druck eingesetzt haben“, erklärt Cochet.
„Individualisierung ist für uns relativ einfach umzusetzen. Unsere Kunden haben oft Prototypen mit sehr spezifischen Anforderungen, für die wir sehr schnell und kostengünstig Lösungen anbieten können. Manchmal spielen auch das Gewicht oder das Volumen eine wichtige Rolle. Gelegentlich konstruieren wir Antennen in sehr engen Räumen, wie wir es mit Zerspanung nicht hinbekommen würden. Bei zerspanten Antennen muss man üblicherweise mehrere Teile erstellen, die hinterher zusammengesetzt werden. Das ist natürlich viel größer als ein einzelner 3D-Druck“, so Cochet.
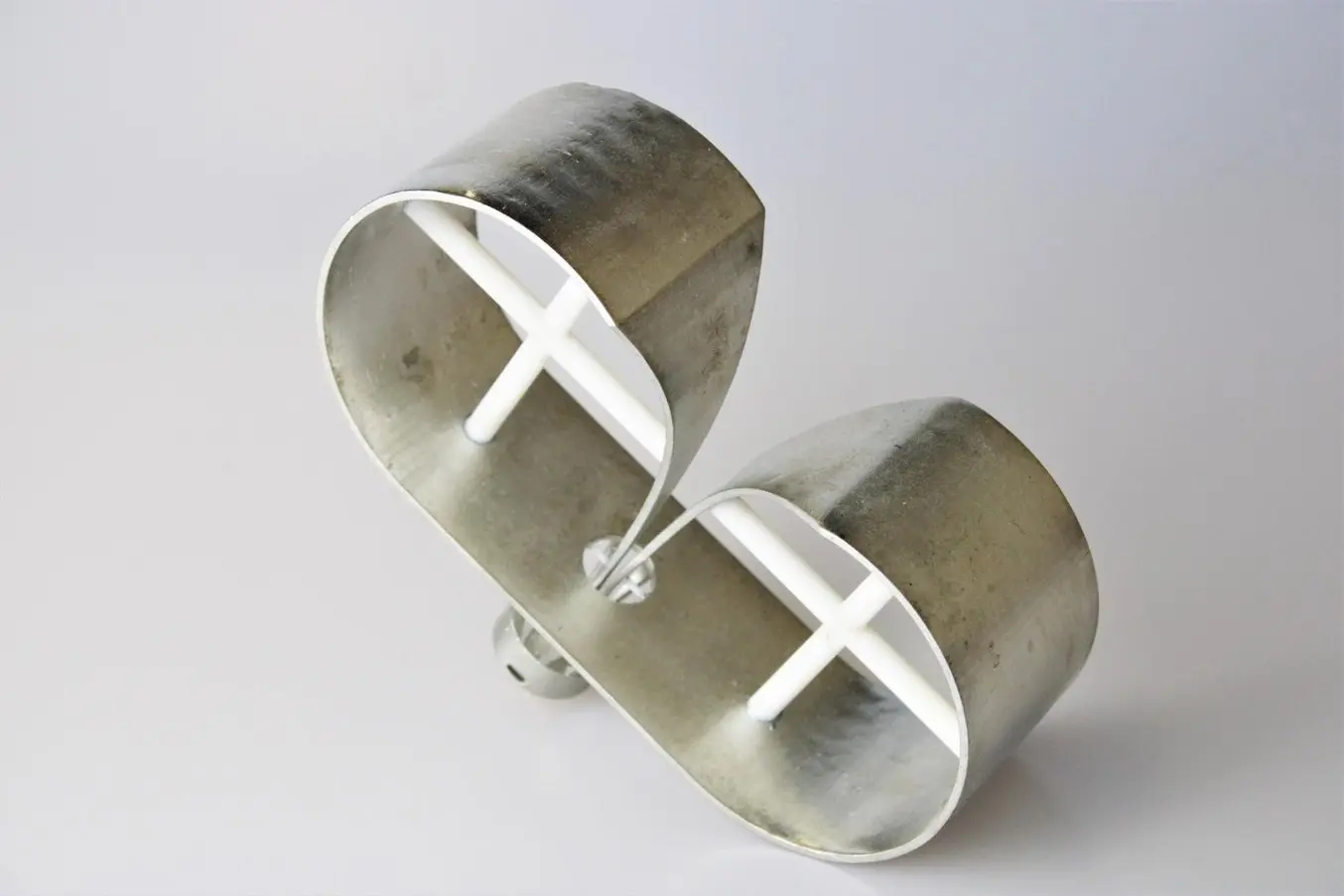
Eine 3D-gedruckte und selektiv galvanisierte TEM-Hornantenne nach dem Entwurf von Julien Haumant, F+E-Ingenieur bei Elliptika.
„Eine unserer Antennen ist beispielsweise besonders kompliziert, da sie stark gebogen ist. Dank 3D-Druck lässt sie sich als Einzelkomponente herstellen und wiegt gerade einmal 75 Gramm. Zum Vergleich: Eine Komponente mit solchen Eigenschaften würde bei Zerspanungsverfahren aus mehreren Teilen bestehen, wäre wesentlich schwerer und 10 bis 20 Mal größer", gibt Cochet an.
Weitere Anwendungen der Galvanisierung
Die Galvanisierung 3D-gedruckter Teile ist vielseitig einsetzbar. Volkswagen und Autodesk haben diese Technologie zur Herstellung spektakulärer Radkappen für ein futuristisches Konzeptfahrzeug verwendet. Forscher in der Schweiz erschufen so einen fortschrittlichen Versuchsaufbau mit Strahlteilern. Und viele weitere Unternehmen galvanisieren 3D-gedruckte Kunststoffteile, um kostengünstig komplexe Teile mit der Festigkeit von Metallen herzustellen.
Schauen Sie unser kostenloses Lehrwebinar mit Sean Wise, Gründer und Präsident von RePliForm, und erfahren Sie, wie sein Team bei RePliForm mit Galvanisierung das Spektrum der 3D-Druckanwendungen erweitert. Dabei erfahren Sie mehr über die Galvanisierung und ihre spezifischen Anwendungen in Kombination mit dem SLA-3D-Druck sowie über die zahlreichen Prozesse, die bei der Produktion fertiger galvanisierter 3D-Drucke ablaufen.