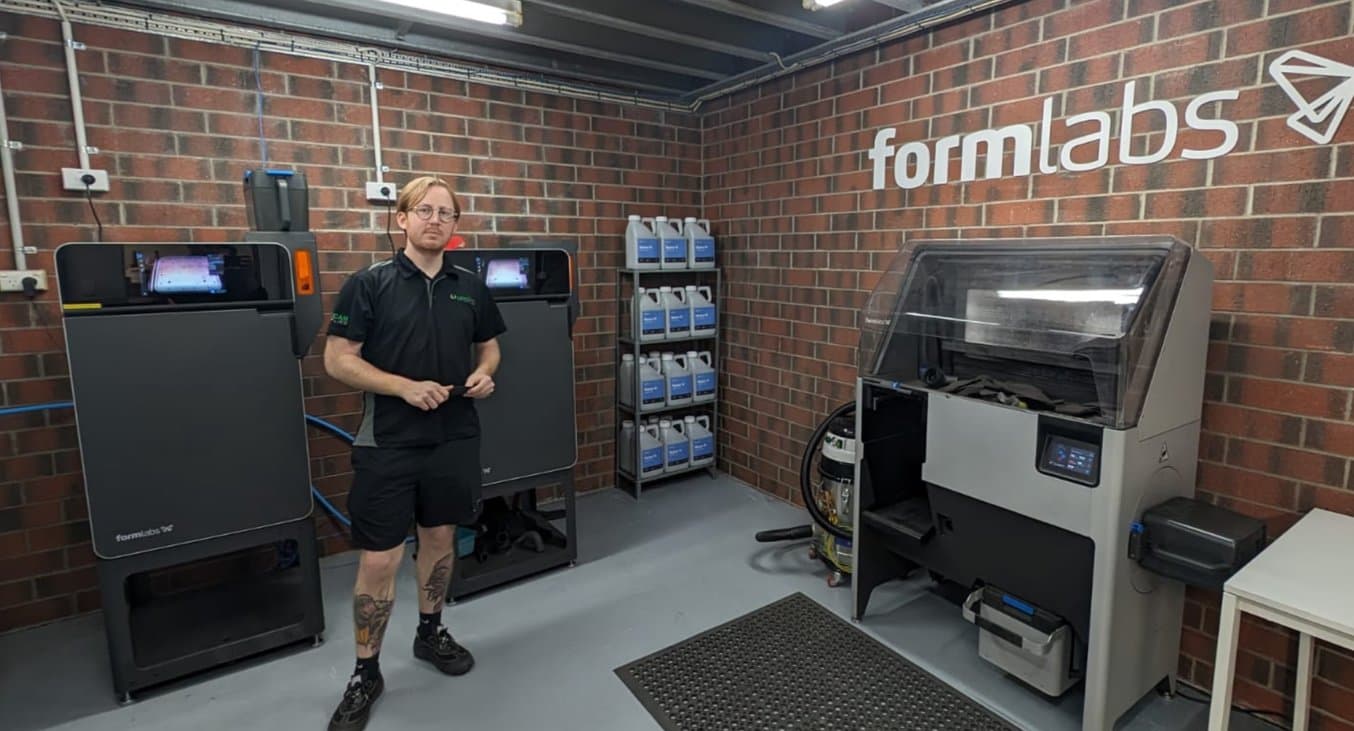
GMZ Medical ist ein australischer Fachhersteller von orthopädischen Einlagen, der von der Bereitstellung von Zubehör über Design-Software bis hin zur Eigenfertigung alles abdeckt. Aufgrund dieses vielfältigen Angebots verfügt das Team über fundierte Kenntnisse aller Aspekte der Orthesenfertigung sowie über Erfahrungen mit verschiedenen Arbeitsabläufen und Materialien. Nicht nur verwendet das Labor für die Fertigung von Orthetik, CADCAM Orthotics, zwei SLS-3D-Drucker (selektives Lasersintern) des Typs Fuse 1+ 30W, sondern auch der Zulieferer, PodCAM Supplies, empfiehlt das Fuse-Ecosystem an Orthesenhersteller und Gesundheitsdienstleister.
Laut Konrad Job, Podologe bei GMZ Medical, ist es diese Kombination von Geschäftszweigen, darunter auch die Softwarelösung LaserCAM Orthotics, die es GMZ Medical möglich macht, jeden Aspekt der Orthesenfertigung zu testen, um den Prozess und Arbeitsablauf optimal abzustimmen.
„Wir versuchen, eine Blaupause zu erstellen, an der sich andere orientieren können. Wir möchten, dass die Leute sehen, dass wir mit unserer eigenen Software und unserem eigenen Produktionszyklus kostengünstig ein wirklich erfolgreiches Geschäft aufbauen können. Wir testen den gesamten Prozess gründlich, bevor wir ihn weiterempfehlen.“
Konrad Job, Podologe, CADCAM Orthotics
CADCAM Orthotics' „Blaupause“ zur Produktion 3D-gedruckter Einlagen beruht auf dem Fuse-Ecosystem von Formlabs. Wir haben uns mit Job unterhalten, um von ihm mehr über die Vorteile digitaler Arbeitsabläufe zu erfahren und zu entdecken, wie dieses Konzept die Hauptprobleme von Orthesenherstellern und Gesundheitsdienstleistern löst.
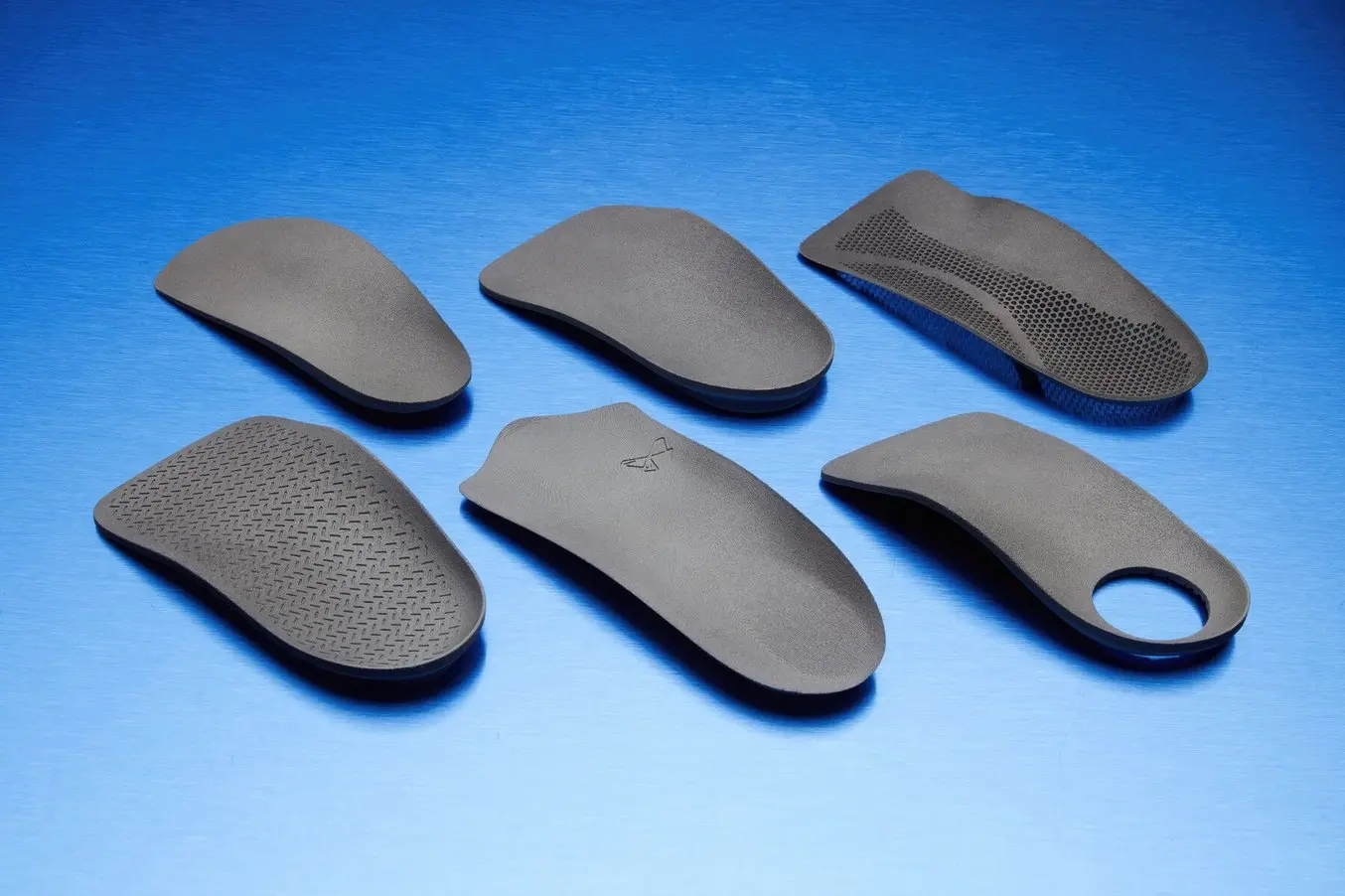
Revolutionieren Sie Ihre Einlagenproduktion mit dem Fuse 1+ 30W von Formlabs
Bringen Sie Ihre Einlagenproduktion auf Touren und sparen Sie zugleich Zeit und Geld. In diesem Webinar erfahren Sie, was den Fuse 1+ 30W von Formlabs zur perfekten Lösung für den Einstieg in die digitale Fertigung macht oder wie Sie Ihre Produktion damit kostengünstig und effizient skalieren.
3D-Druck: Ein einfacher Arbeitsablauf in einer sauberen Umgebung
CADCAM Orthotics ist der Fertigungsbetrieb von GMZ Medical. Das Unternehmen begann 1997 mit der Fertigung von EVA-Einlegesohlen mit einer CNC-Fräse und startete einige Jahre später mit dem Vakuumformen von Polypropylen-Produkten.
Bei vakuumgeformten Produkten aus Polypropylen begann der Arbeitsablauf mit einem 3D-Scan. CADCAM Orthotics musste dann ein Positivmodell in CAD entwerfen, es aus MDF-Platten (Medium Density Fiberboard) fräsen und dann mehrere Schichten des Vakuumformens auf dem MDF-Positiv durchführen, um eine Orthese mit den richtigen Spezifikationen zu fertigen.
Job erinnert sich: „Die größten Probleme waren die Anzahl der Arbeitsschritte und die damit verbundene Einarbeitung, um sicherzustellen, dass alle unsere Mitarbeiter diese Schritte wiederholt durchführen können. Mit der Zeit hatten wir dann einen Mitarbeiter, der wirklich gut in diesem Produktionsprozess war.“
Nicht nur die Einarbeitung war ein Problem; der Werkstoff MDF schaffte auch ein staubiges, unangenehmes Arbeitsumfeld. Job sagt: „MDF war nicht angenehm zu bearbeiten, es ist staubig, man muss Masken tragen. Wir haben es mit hochdichtem Schaumstoff versucht, aber der ist ein bisschen geschmolzen. Als wir vom Fräsen von Fußpositiven auf 3D-Druck umgestiegen sind, hat sich kein einziger Mitarbeiter beschwert.“

EVA-Einlagen müssen mit einer CNC-Fräse gefertigt werden, die mit den von LaserCAM Orthotics erstellten Designs kompatibel ist.
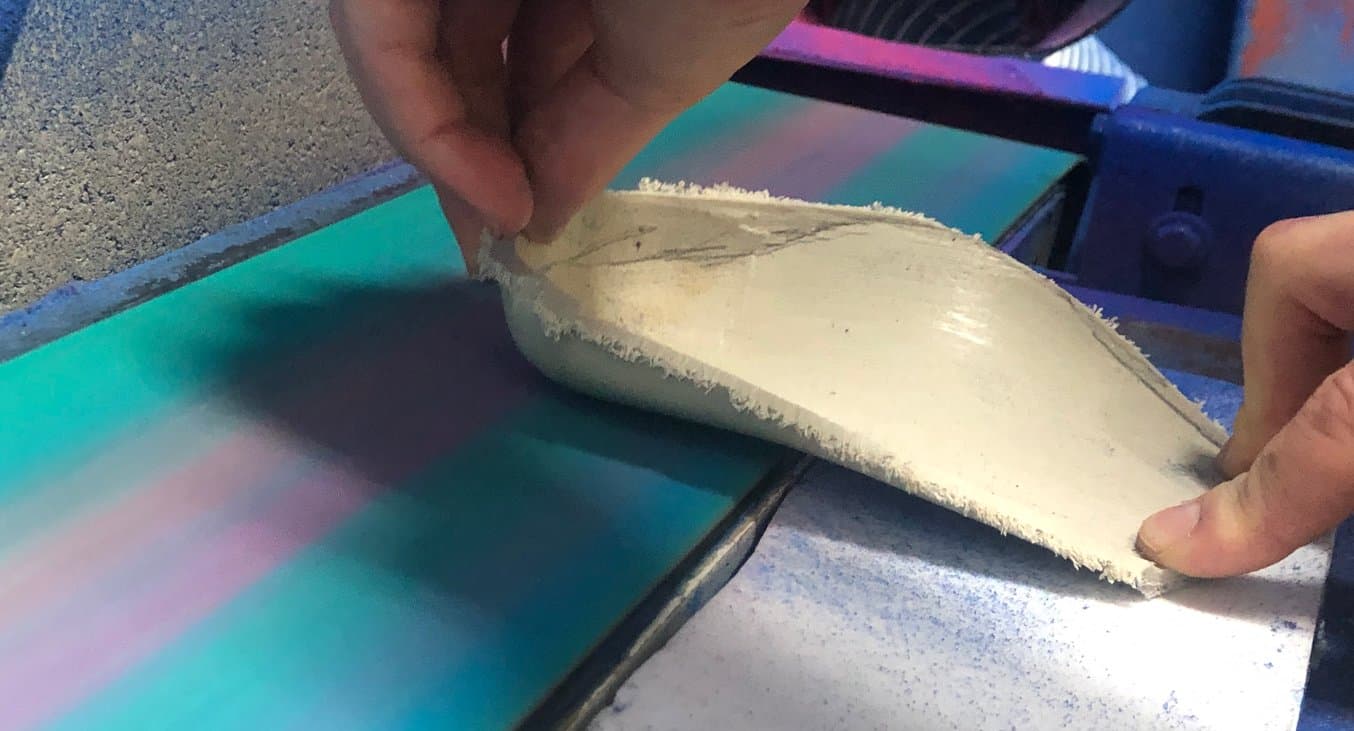
Vakuumformen mehrerer Schichten, um Einlagen mit der erforderlichen Steifigkeit zu erstellen.
Ein drittes Problem beim Vakuumformen war die Oberflächenbeschaffenheit. Wie Job es beschreibt: „Man hat den Daumen draufgelegt, und schon war ein Haar dran. Man musste ständig aufpassen, dass man es beim Schleifen der anderen vakuumgeformten Schichten nicht zerkratzt.“
Anfangs ersetzte CADCAM Orthotics die Polypropylen-Fertigung durch ausgelagerten 3D-Druck. Das Unternehmen griff zwei Jahre lang auf Outsourcing des 3D-Drucks zurück. Job sagt: „Die Zusammenarbeit war großartig, sie haben uns sehr unterstützt, aber letztendlich hatten wir nicht genug Kontrolle über die Fertigungszeit und auch nicht über die Feinheiten, z. B. wie viel Pulver recycelt wurde. Wir wollten die Teile aus dem Drucker nach unseren eigenen Maßstäben prüfen.“
Um mehr Kontrolle über den 3D-Druck zu erhalten, beschloss CADCAM Orthotics im Jahr 2022, auf betriebsinternen Druck umzusteigen.
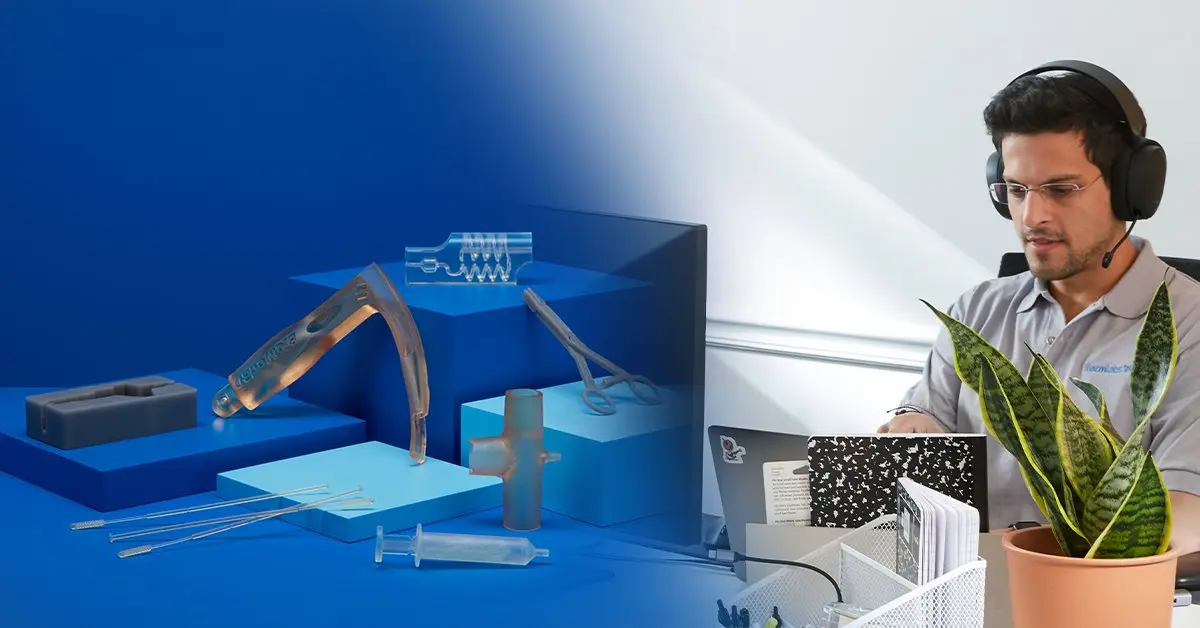
Kontakt zum Vertriebsteam von Formlabs Medical
Ob Sie patientenspezifische chirurgische Instrumente erstellen möchten oder Prototypen kardiologischer Medizinprodukte anfertigen: Wir stehen Ihnen zur Seite. Hinter Formlabs Medical steht ein engagiertes Spezialistenteam, das Sie und Ihr Unternehmen bei Bedarf mit professioneller Hilfe unterstützt.
Betriebsinterne Fertigung mit dem Fuse-Ecosystem
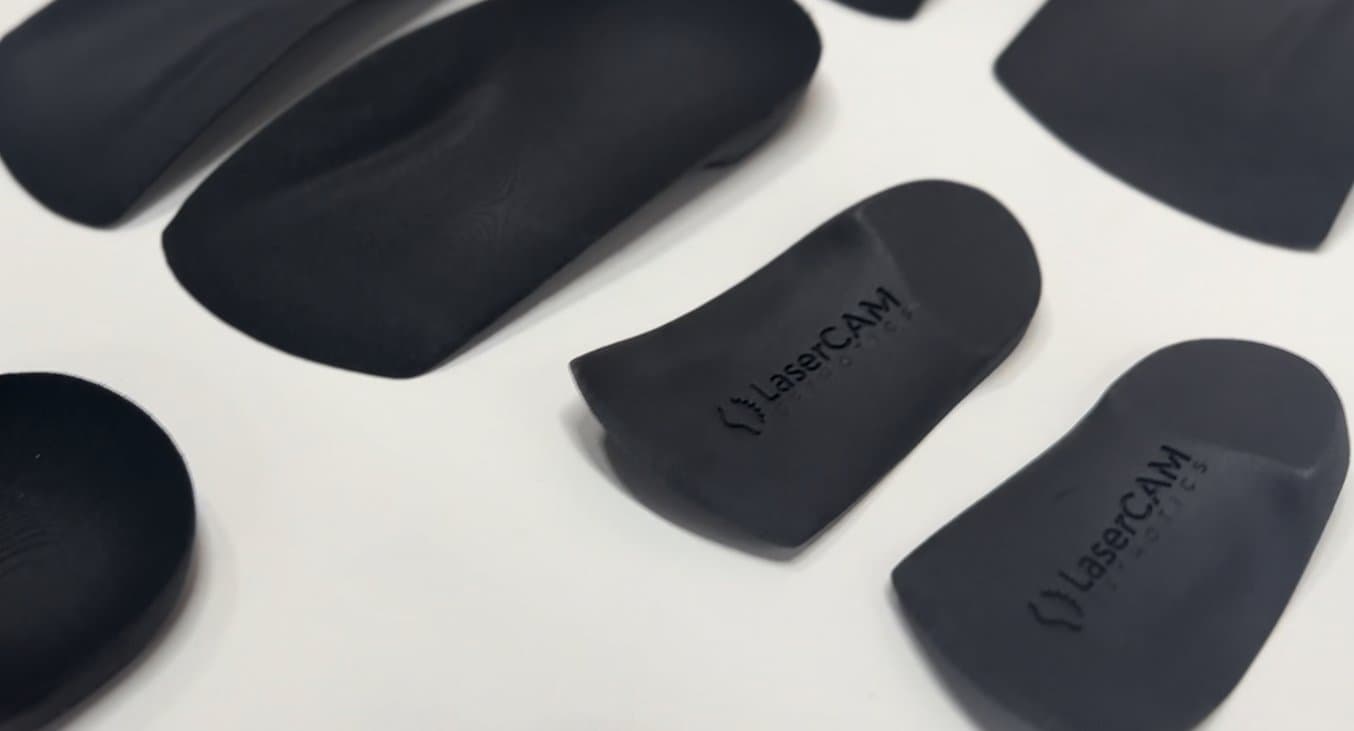
LaserCAM-Einlagen, die mit dem Fuse 1+ 30W aus Nylon 11 Powder gedruckt werden, kosten 40 % weniger als die Auslagerung des 3D-Drucks.
Outsourcing ist letzten Endes eine gute Möglichkeit, den 3D-Druckprozess zu validieren, bevor zur Eigenfertigung übergegangen wird. Indem ein Unternehmen die Fertigung in den eigenen Betrieb verlagert, übernimmt es die Kontrolle über den gesamten Produktionsprozess und erreichte kürzere Durchlaufzeiten; für CADCAM Orthotics bedeutete dies eine Beschleunigung von zehn auf vier Werktage. Außerdem hat die Umstellung auf 3D-Druck zu erheblichen Einsparungen in der Fertigung geführt.
Fertigungsverfahren | Kosten pro Paar | Arbeitsaufwand (in Stunden) | Durchlaufzeit |
---|---|---|---|
Konventionelles Thermoformen | 77,20 $ | 1,5 | 10 Arbeitstage |
Ausgelagerter 3D-Druck | 92,63 $ | 0,7 | 10 Arbeitstage |
Betriebsinterner 3D-Druck | 54,29 $ | 0,8 | 4 Arbeitstage |
Der betriebsinterne 3D-Druck gewährt mehr Kontrolle über Produktionszyklen. Bei CADCAM Orthotics bedeutet dies einen tagtäglichen Druckbetrieb, um mindestens fünf Druckaufträge pro Woche fertigzustellen – und manchmal noch einen weiteren am Wochenende. So werden insgesamt 30 bis 50 Einlagenpaare pro Woche produziert. Der SLS-3D-Druck erfordert nach Druckabschluss eine Abkühlzeit. CADCAM Orthotics berücksichtigt dies, indem das Team den Drucker während des Arbeitstages entleert und einen neuen Druckauftrag startet, sodass die Drucke noch am selben Tag nachbearbeitet werden können und am nächsten Tag neue Drucke bereitstehen.
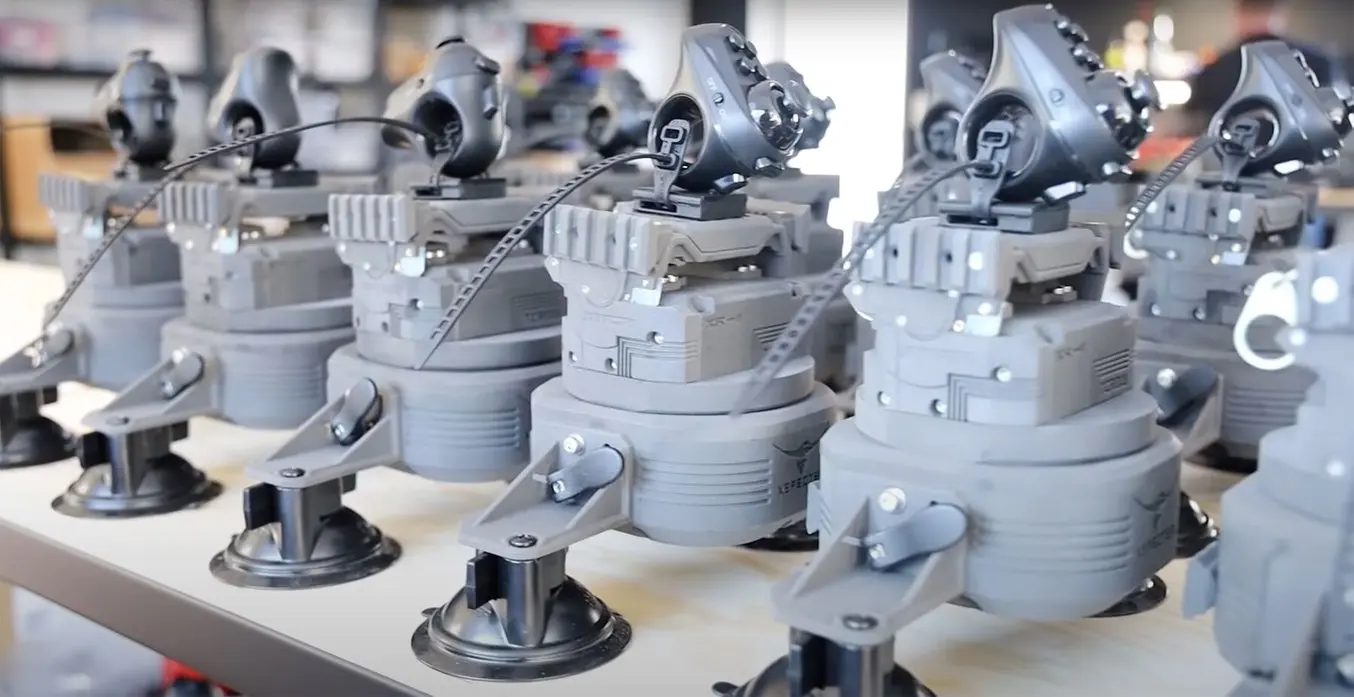
SLS-Produktion für die Endverwendung
3D-Druck für die Endverwendung ist nicht nur möglich, sondern dank des SLS-Ecosystems der Fuse-Serie auch noch erschwinglicher, agiler und leichter skalierbar denn je. Besuchen Sie unsere Seite zum Thema SLS für die Produktion und vergleichen Sie Produktionsverfahren, informieren Sie sich über unsere Mengenrabatte auf Pulver und entdecken Sie die Produktionsabläufe 15 verschiedener Hersteller, die derzeit die Fuse-Serie nutzen.
Einfache, effiziente Arbeitsabläufe
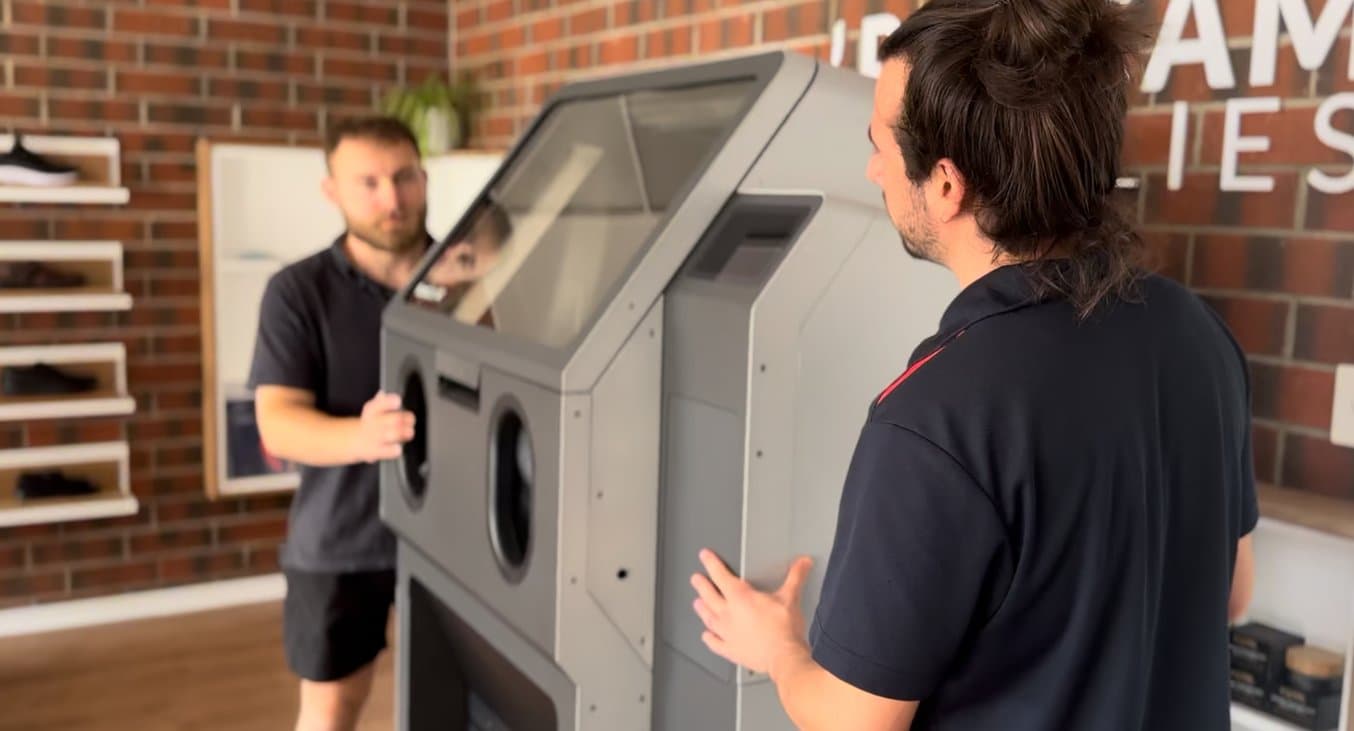
CADCAM Orthotics hat vor kurzem einen Fuse Blast in seine Prozesse integriert, mit dem die Reinigung von Einlagen 78 % schneller geht.
Wie Job betont, gab es bei den konventionellen Verfahren letzten Endes nur ein Teammitglied, das sich gut auskannte. „Aber jetzt, mit 3D-Druck, haben wir mindestens fünf Leute, die das machen können. Die Einarbeitung ist also ein enorm wichtiger Faktor.“ Die Einfachheit der Abläufe beim 3D-Druck im Fuse-Ecosystem bedeutet nicht nur, dass das gesamte Team produktiver arbeiten kann, sondern auch, dass die Prozesse einfacher und sauberer sind als bei herkömmlichen Verfahren.
„Ich bin begeistert von diesem Prozess, denn es ist das erste Mal, dass wir Teile einfach aus der Maschine nehmen und beschichten können. Ich für meinen Teil verbringe lieber Zeit mit dem Design als mit dem Schleifen von Teilen.“
Konrad Job, Podologe, CADCAM Orthotics
Durch den Wegfall des körperlich anspruchsvollen Schleifens und Polierens, das bei herkömmlichen Arbeitsabläufen erforderlich ist, setzt das Fuse-Ecosystem bei CADCAM Orthotics Arbeitskräfte für höherwertige Aufgaben frei, wie etwa das Design.
Für das Reinigen und Abschleifen verwendet CADCAM Orthotics den Fuse Blast, eine vollautomatische Lösung für Produkte, die sich sauber anfühlen – und das in 78 % weniger Zeit. Außerdem findet die Reinigung geschlossen statt, wodurch der Arbeitsbereich für die Mitarbeitenden sauberer bleibt und ein angenehmeres Arbeitsumfeld geschaffen wird.
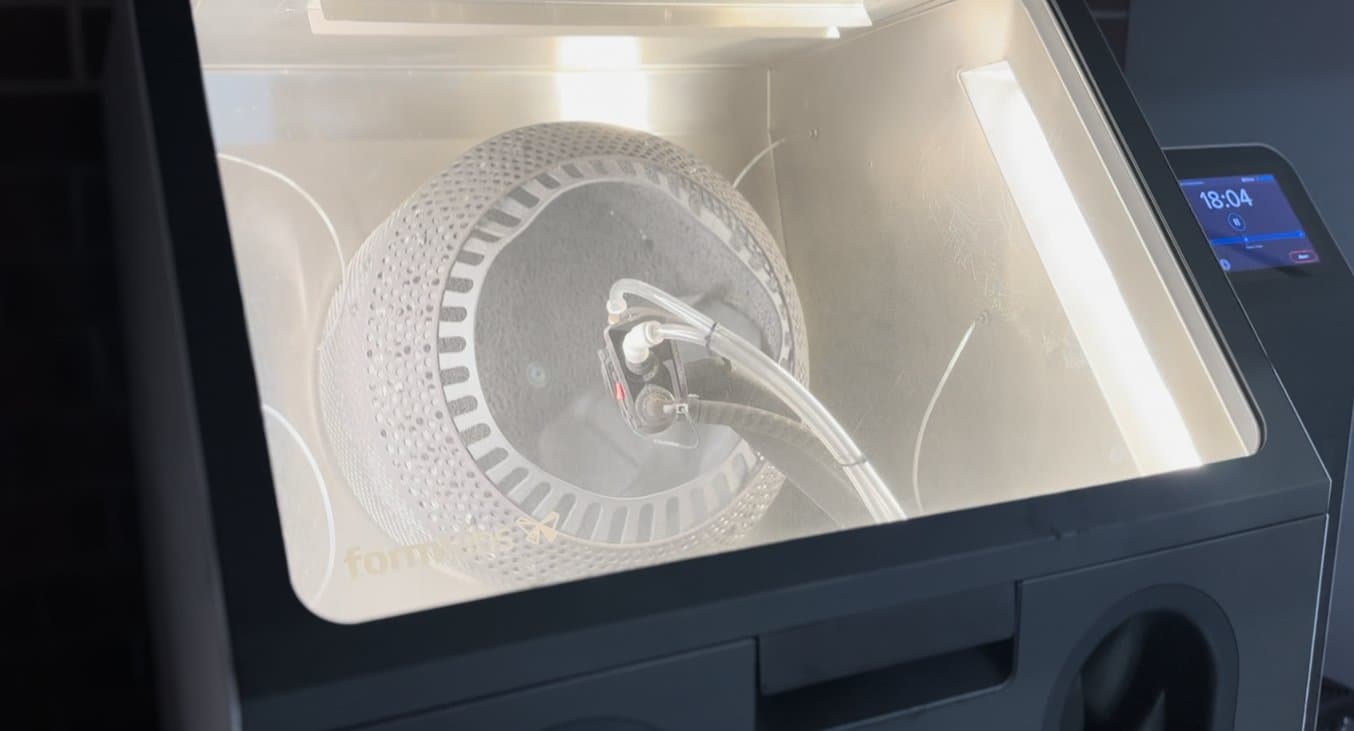
Der Fuse Blast reinigt automatisch eine ganze Charge von Einlagen und spart so Zeit.
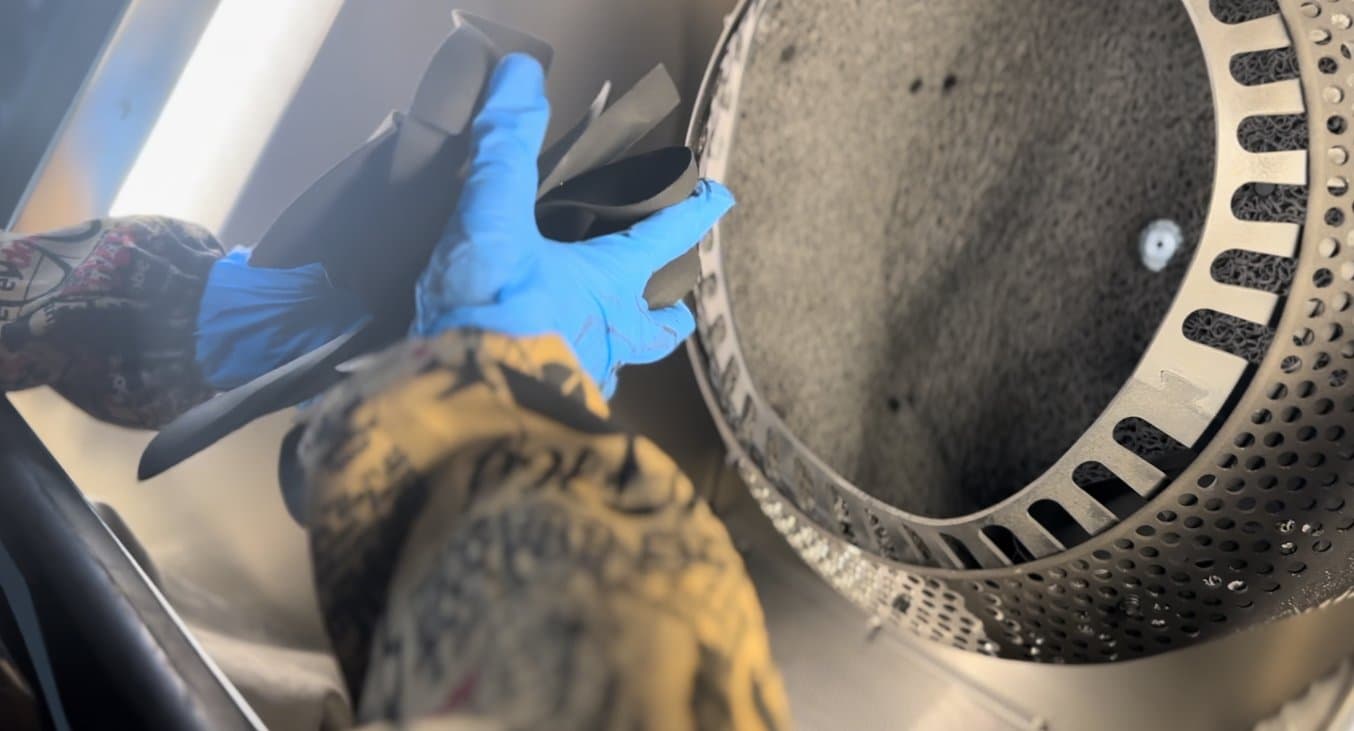
Die Teile werden im Fuse Blast gereinigt und sind sofort bereit für die Beschichtung.
„Mit dem Fuse Blast haben wir im Grunde einen völlig perfekten Produktionskreislauf ganz ohne manuelle Nachbearbeitung. Wir modellieren, laden das Modell in den Drucker und decken die Einlage ab – es ist sehr, sehr einfach.“
Konrad Job, Podologe, CADCAM Orthotics
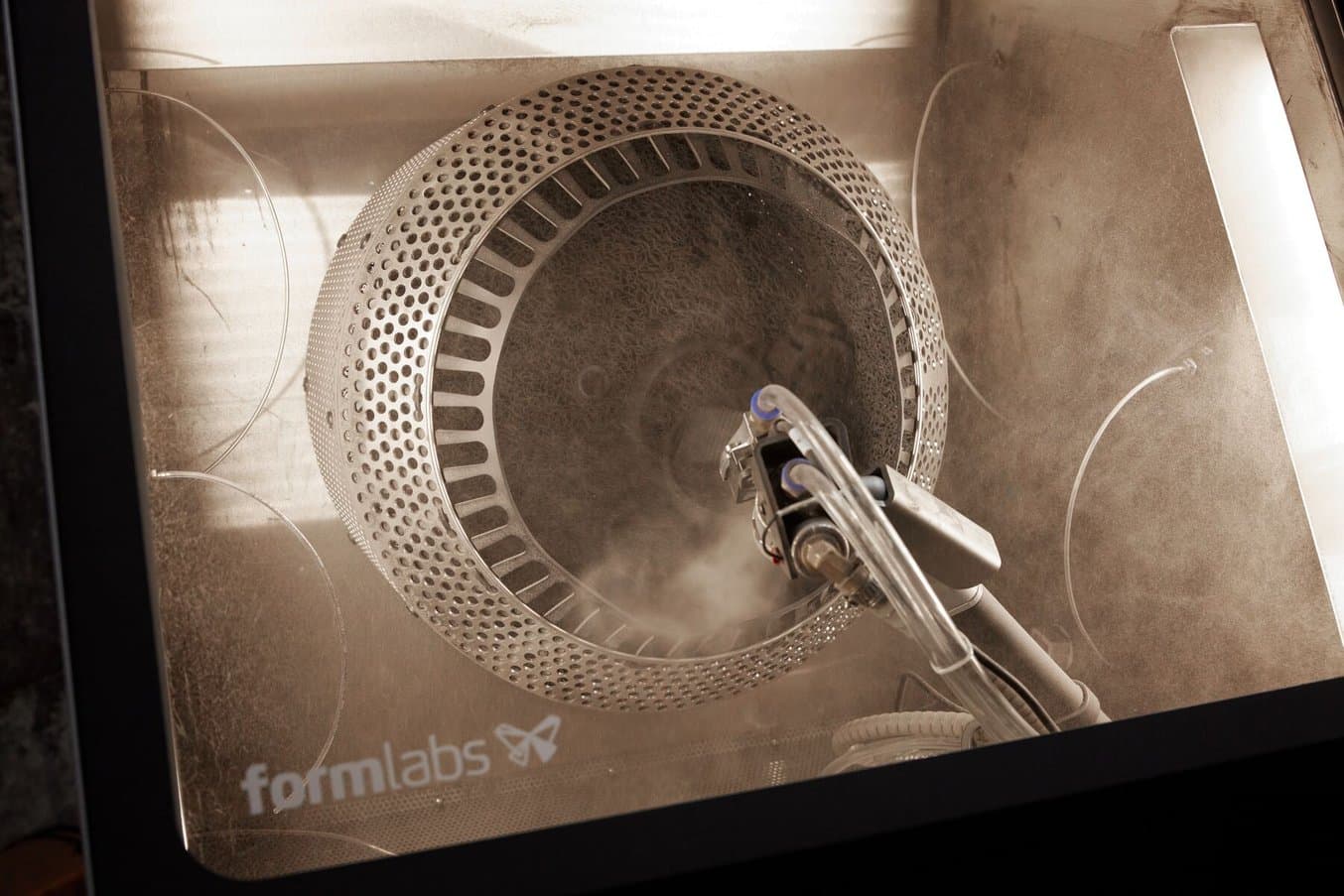
SLS-Teile in 10 Minuten nachbearbeiten: Fuse Blast für Einlegesohlen
Mit dem Fuse Blast wird die Zeit für die Nachbearbeitung erheblich verkürzt. Unser Referent Shiden zeigt, wie man eine ganze Konstruktionskammer mit mehr als 40 Einlagen in nur 10 Minuten entpulvert und so die Nachbearbeitungszeit von 45 Min. um 78 % reduziert.
Mehr Sicherheit durch Redundanz
Job sagt: „Da wir bereits CNC-Technologie integriert und CNC-Systeme verkauft haben, war uns sehr früh bewusst, wie wichtig Redundanz in der Fertigung ist. Deshalb beurteilen wir SLS-Maschinen auch danach, ob wir in der Lage sind, zwei zu erwerben.“
Selbst bei den zuverlässigsten 3D-Druckern können Fehler bei der Anwendung oder allgemeine Wartungsbedürfnisse zum Ausfall eines Geräts führen. Bei einem einzigen Drucker bedeutet dies den totalen Stillstand der Produktion. Mit zwei Druckern können Sie sicherstellen, dass die Produktion nie zum Stehen kommt. Redundanz ermöglicht auch Flexibilität bei Eilaufträgen oder großen Bestellungen.
„Der Preis des Fuse 1+ 30W ermöglichte uns den Kauf von zwei Geräten, und das System war skalierbar. Das war unser erstes Kriterium: das Element der Redundanz und die Möglichkeit, mehrere Geräte zu kaufen.“
Konrad Job, Podologe, CADCAM Orthotics
Neben Redundanz ermöglicht der Einsatz von zwei Druckern auch Flexibilität beim Skalieren der Fertigung. Wenn die Anzahl der Drucke auf dem zweiten Drucker erhöht wurde, können weitere Geräte hinzugefügt werden – und das alles mit demselben Arbeitsablauf und ohne die Notwendigkeit, Aufträge abzulehnen, während Sie die Einrichtung der zusätzlichen Drucker abwarten.
Die Vorteile einer kleinen Stellfläche
„Bei der Kommerzialisierung unserer Software war es wirklich wichtig, einen SLS-Drucker zu haben, der klein genug für den Einsatz in einer Klinik ist.“
Konrad Job, Podologe, CADCAM Orthotics
LaserCAM Orthotics ist die Softwarelösung von GMZ Medical für das Design von orthopädischen Einlagen und die Software, die CADCAM Orthotics firmenintern für die Designarbeiten vor der Produktion verwendet. Die betriebsinterne Fertigung ermöglicht es CADCAM, Systeme und Arbeitsabläufe zu testen, bevor sie den Kliniken über PodCAM Supplies empfohlen werden.
Bei den Kunden von PodCAM Supplies handelt es sich um medizinische Einrichtungen. Daher muss LaserCAM nicht nur einfach zu bedienen sein, sondern bei den von PodCAM Supplies empfohlenen Druckern müssen auch die Ansprüche einer Klinik berücksichtigt werden – etwa der Platzverbrauch des Druckers und der Nachbearbeitungsgeräte, der Preis und die Arbeitsabläufe.
„Wir konnten kein Ungetüm im Wert von einer halben Million Dollar in einen kleinen Schleifraum stellen und diesen in einen Druckraum umwandeln. Doch mit dem Fuse war das kein Problem. Für den Fuse-Drucker zu werben und den medizinischen Fachleuten bewusst zu machen, dass sie ihn direkt in der Klinik einsetzen können, hatte große kommerzielle Vorteile.“
Konrad Job, Podologe, CADCAM Orthotics
Obwohl das Fuse-Ecosystem einen geringen Platzbedarf hat, kann CADCAM Orthotics bis zu 12 Paar Einlagen in einem einzigen Druckauftrag unterbringen. Job sagt: „Da wir CAD-Software vertreiben, ist der Fuse sehr wettbewerbsfähig im Vergleich zu größeren SLS- und MJF-Maschinen, denn viele unserer Kunden möchten in ihrer eigenen Klinik und kleineren Laboren drucken.“
Eine vielseitige Materialbibliothek auf einem einzigen Drucker
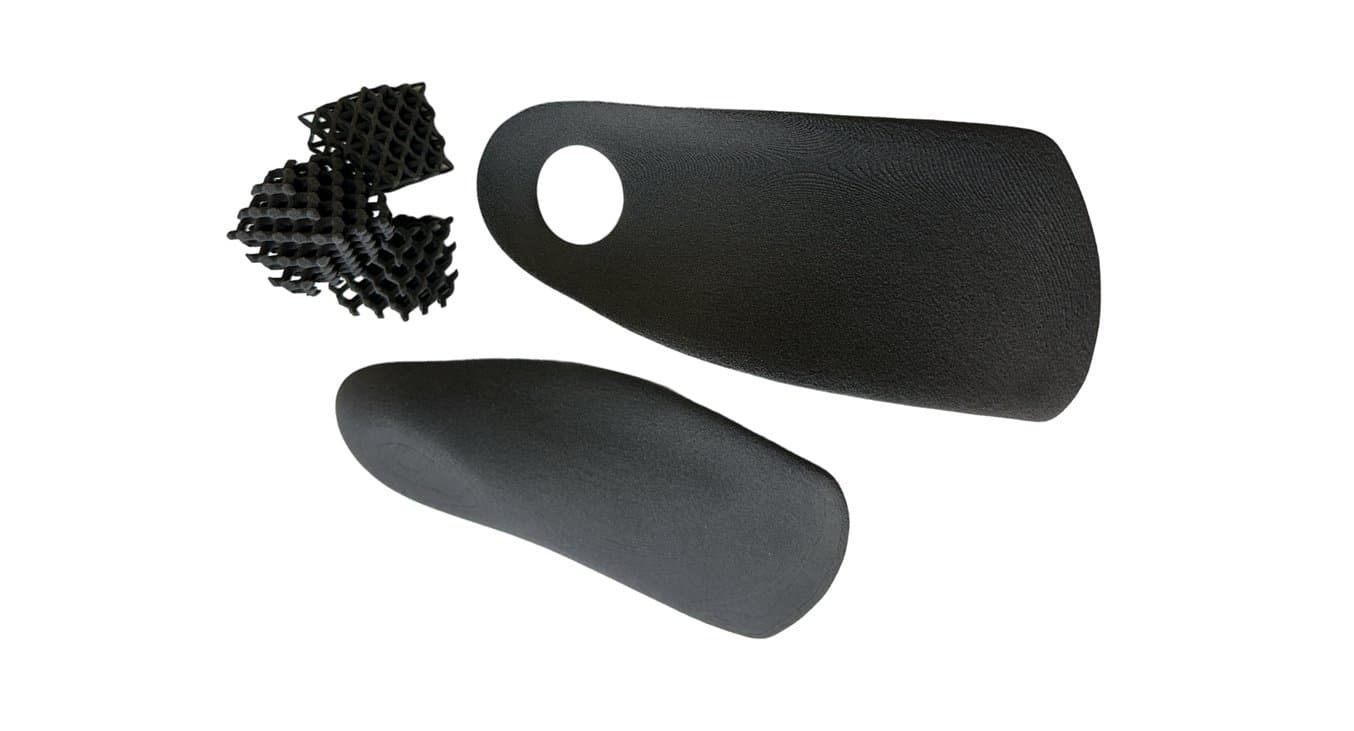
3D-gedruckte Probeteile aus dem Fuse 1+ 30W zeigen Designs von LaserCAM Orthotics und die Materialeigenschaften von Nylon 11 Powder.
Als CADCAM Orthesis in den 3D-Druck einsteigen wollte, suchte das Unternehmen nach Optionen für Polypropylen, dem damaligen Branchenstandard, der inzwischen von Nylon abgelöst wurde. Bei der Beurteilung von 3D-Druckmaterialien für Nylon-Einlagen war es Job wichtig, „dass die Teile eine ausreichende Festigkeit hatten, im Hinblick auf Zugfestigkeit und Biegeprüfungen, damit sie nicht zerbrachen oder sich verformten.“
Auf dem Fuse 1+ 30W ist Nylon 11 Powder ein ideales Material für feste Orthesen mit hoher Duktilität und langfristiger Stabilität, so auch für Einlegesohlen. Darüber hinaus sind mit Nylon 11 Powder gedruckte Teile umweltstabil, nehmen nur sehr wenig Feuchtigkeit auf, sind licht-, hitze- und chemikalienbeständig und für den Hautkontakt als biokompatibel zertifiziert.
Tabelle zum Materialvergleich | Nylon 11 Powder |
---|---|
Maximale Zugfestigkeit | 49 MPa |
Bruchdehnung (X/Y) | 40 % |
Biegebruchfestigkeit | 55 MPa |
Biegemodul | 1,4 GPa |
Fordern Sie ein kostenloses Probeteil an und überzeugen Sie sich selbst von der Leistung und Qualität von Einlagen aus Nylon 11 Powder.
Auch die große Materialauswahl floss in die Entscheidung für den Fuse 1+ 30W mit ein. Job erzählt: „Wir wollten mit Nylon 11 Powder ursprünglich unser Polypropylen ersetzen, und es hat sich dafür als gutes Produkt erwiesen. Was aber, wenn wir unterschiedliche Produkte aus Nylon 12 Pulver, Polypropylen oder TPU drucken möchten? Ganz zu schweigen davon, welche anderen Materialien Formlabs in den nächsten 10 Jahren entwickeln könnte.“
Der Fuse 1+ 30W ist in der Lage, sechs Pulver zu drucken, darunter auch biokompatible Materialien, und das interne Materialentwicklerteam von Formlabs arbeitet ständig an neuen, branchenführenden Materialien.
Diese wachsende Materialbibliothek ist eine Stärke des Fuse-Ecosystems. Job sagt: „Wenn wir unsere Produktion mit dem Fuse skalieren, werden wir in der Lage sein, eine breitere Materialpalette mit größerer Redundanz im Vergleich zur Konkurrenz anzubieten, was uns definitiv auch einen Wettbewerbsvorteil verschaffen wird.“
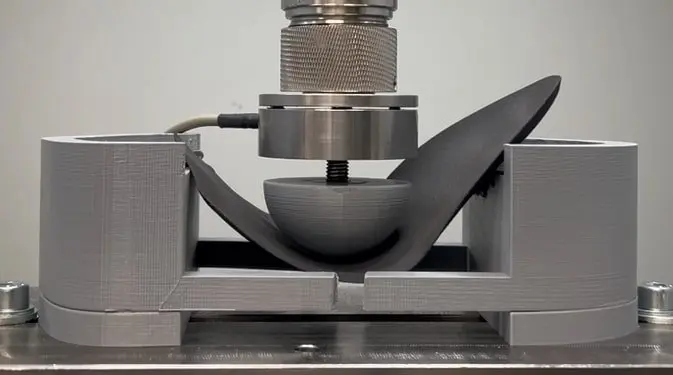
Analyse der mechanischen Leistung 3D-gedruckter und konventionell gefertigter Einlagenrohlinge
Diese Studie untersucht die Materialeigenschaften und Fertigungsmethoden für maßgefertigte orthopädische Einlegesohlen – hergestellt mit dem Fuse 1+ 30W und Nylon 11 Powder von Formlabs, HP 3D High Reusability PA 11 bzw. traditionell verarbeitetem Polypropylen.
Design-Software LaserCAM
Es gibt zahlreiche Software-Lösungen für das Design von Orthesen, was für einen regen Wettbewerb in diesem Bereich sorgt. Job ist sich bewusst, dass jede Software-Lösung ihre eigenen individuellen Funktionen und Vorteile hat. LaserCAM konzentriert sich daher „auf das Design von Medizinprodukten, bei dem präskriptive Daten direkt zur Generierung von Orthesenmodellen verwendet werden“.
Das Team bemüht sich auch um eine offene Plattform, die es ermöglicht, mit jeder beliebigen Technologie zu arbeiten. Job erklärt: „Wir beschränken unsere Dateien nicht auf einen Drucker oder eine Art von 3D-Scanner. Wir versuchen, alle Scans anzunehmen und eine STL-Datei zu erzeugen, die mit jeder CNC-Fräse und heute mit jedem 3D-Drucker kompatibel ist. Ich denke, das hat uns geholfen, denn dadurch sind wir weniger voreingenommen, sodass wir direkt Empfehlungen darüber abgeben können, welche Hardware unserer Meinung nach am besten mit der Software funktioniert.“
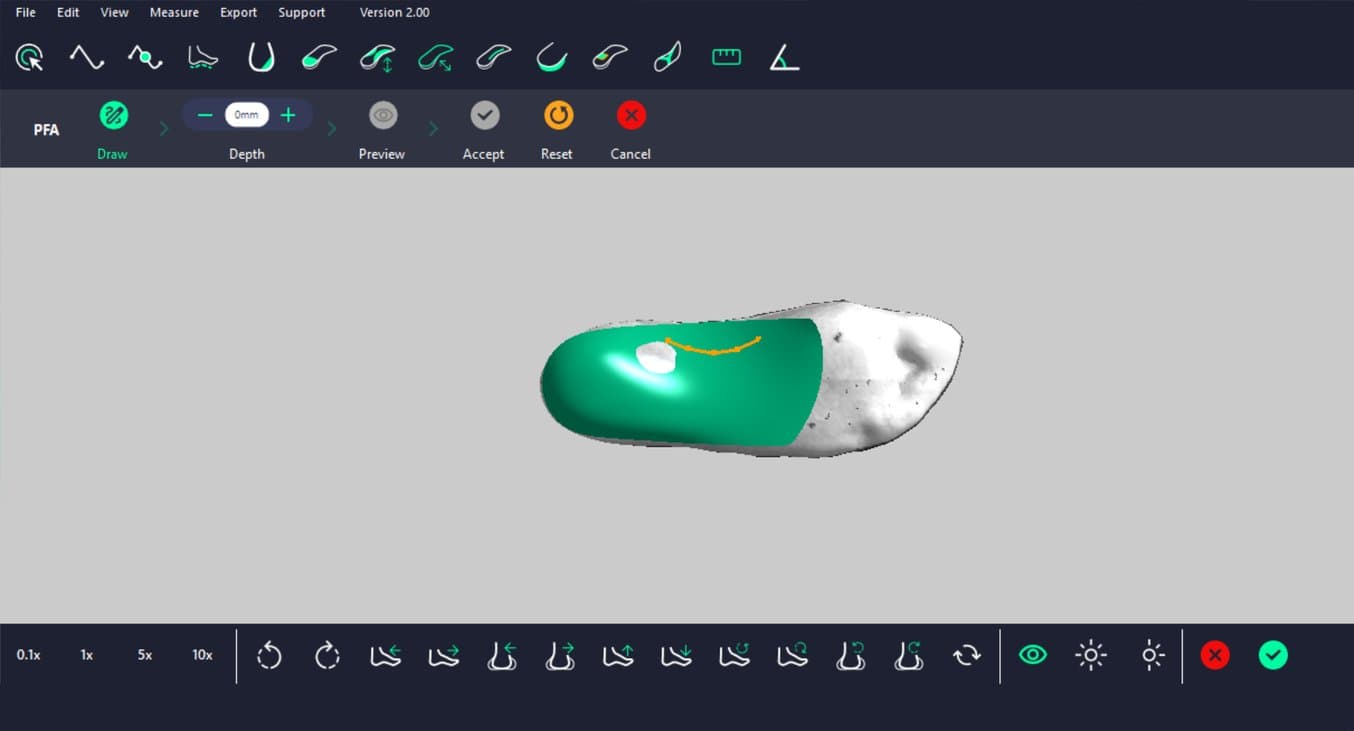
Nach dem Design einer Einlage in LaserCAM kann der Nutzer das Design selbst fertigen oder es zur Fertigung an CADCAM Orthotics senden.
Dank dieser Flexibilität kann die Zulieferabteilung des Unternehmens, PodCAM Supplies, mit den Gesundheitsdienstleistern und Orthesenherstellern zusammenarbeiten, um die optimalen Systeme für ihr Geschäft auszuwählen. Dabei wird für das Design der orthopädischen Einlagen stets die LaserCAM-Software verwendet.
Innovation zulassen
Die Vorteile des 3D-Drucks – Kosteneinsparungen, Effizienz, ein sauberer Arbeitsbereich – ebnen in der Summe den Weg für mehr Innovationen. Job sagt: „An jedem Arbeitsplatz macht ein 3D-Drucker den Mitarbeitern Spaß, weil man damit innovativ sein kann und verschiedene Produkte und Prototypen entwickeln kann, die man sonst mit der CNC-Fräse nur schwer hätten herstellen können.“
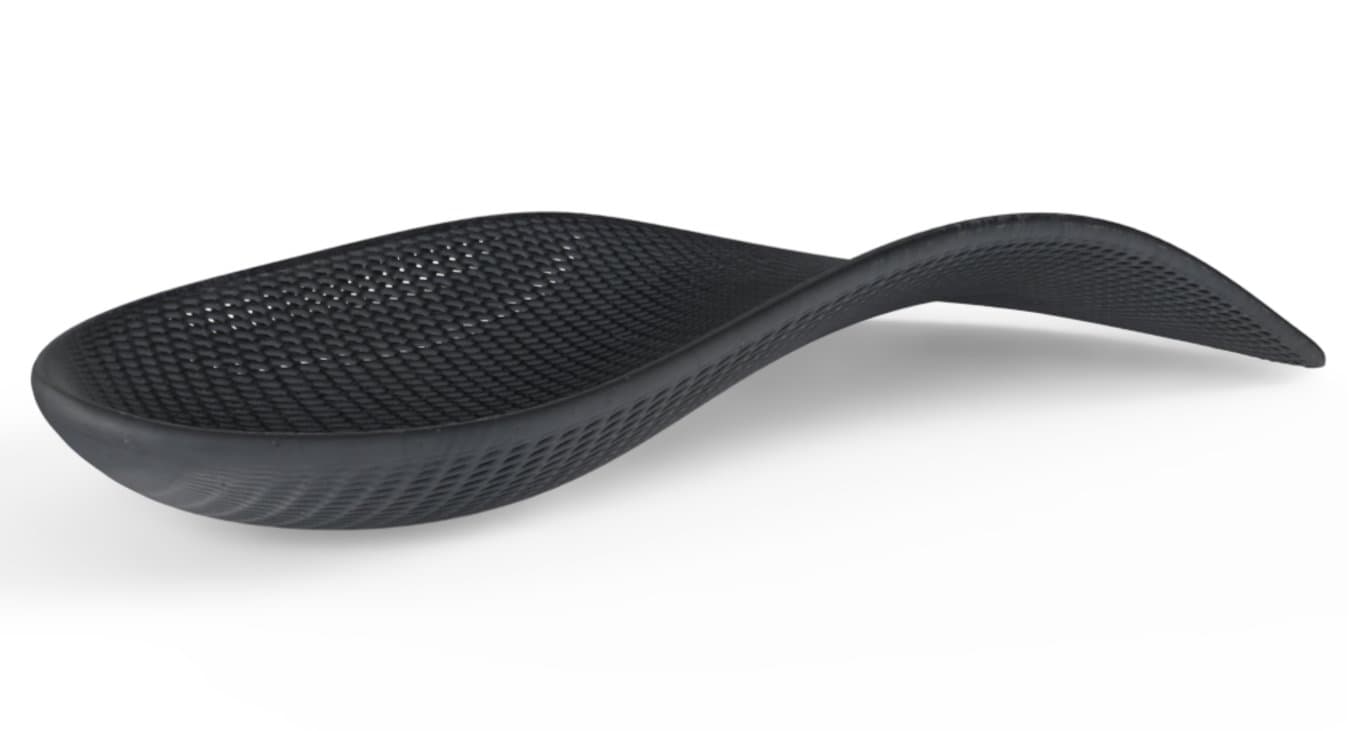
Eine Einlage mit Gitterstruktur zeigt die Vielseitigkeit, die mit LaserCAM Design und 3D-Druck erreicht werden kann.
Mit einfacheren Arbeitsabläufen, saubereren Arbeitsbereichen und den hervorragenden mechanischen Eigenschaften der SLS-Pulver dehnt das Fuse-Ecosystem in Kombination mit der LaserCAM-Software die Grenzen des Möglichen bei orthopädischen Einlagen weiter aus.
Wenn Sie erfahren möchten, wie das Fuse-Ecosystem Ihre Fertigung und Innovation vorantreiben kann, sprechen Sie mit unserem Expertenteam für 3D-Druck, oder fordern Sie eine mit dem Fuse 1+ 30W gedruckte Einlegesohle an, um sich selbst ein Bild von der Qualität zu machen.