Bei Google ATAP: Herausforderungen bei der Vorfertigung mit 3D-Druck begegnen
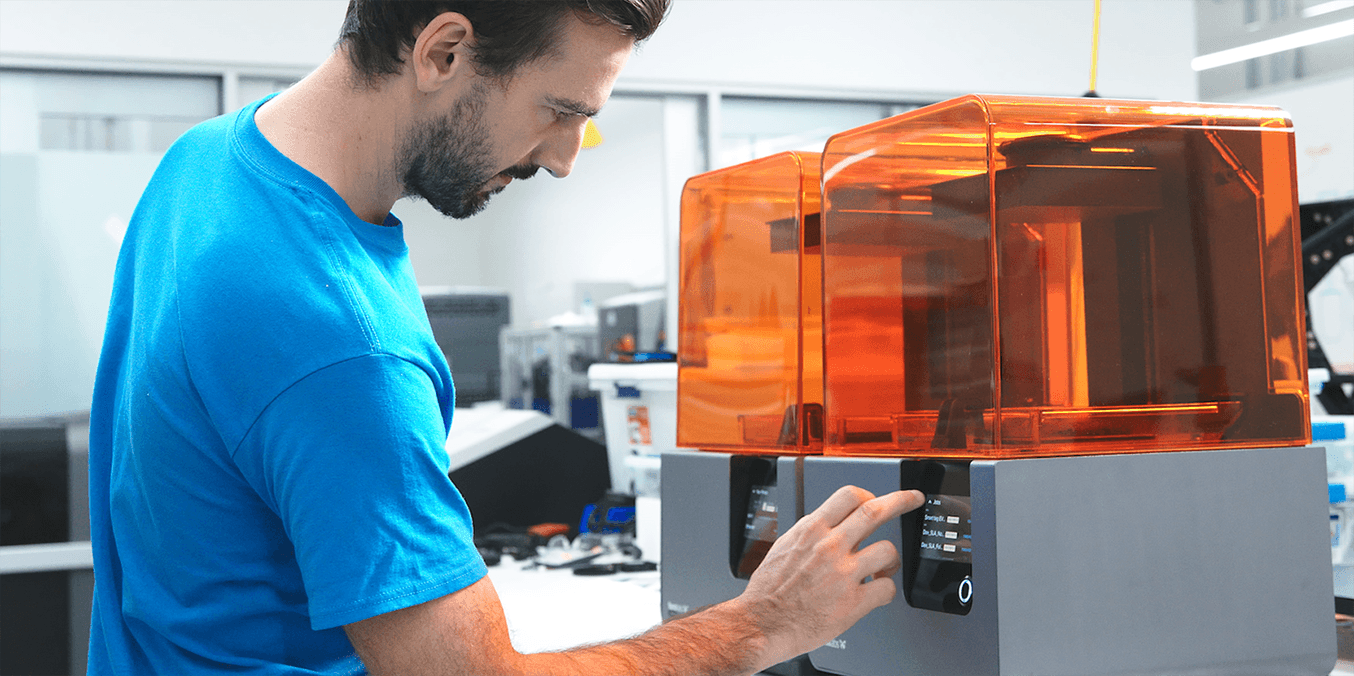
Das Google Advanced Technology and Projects (ATAP) Labor ist die ideale Adresse zur Umsetzung von Hardwareprojekten. Das Labor bietet einen Blick in die Zukunft von Produkten und Produktion, benutzt jedoch dabei Problemlösungsmethoden, von denen jedes Unternehmen heute lernen kann. Das reicht von einer iterativen Herangehensweise in jeder Entwicklungsphase hin zu einer technologischen Ausstattung, die agile, kreative Lösungen ermöglicht.
In einem Fall führte die Herangehensweise des Teams zu einer Prozessinnovation, die es ihm erlaubte, eine komplexe Lieferkette für die Validierungsstufe bei der Vorfertigung eines umspritzten Wearables zu umgehen. Mit Formlabs High Temp Resin, einem 3D-Druckmaterial mit hoher Wärmebeständigkeit, hat Google ATAP den Übergang vom Prototypenbau zur Produktion gemeistert, die Durchlaufzeit für eine wichtige Komponente um 85 Prozent gesenkt und gleichzeitig 100 000 USD gespart.
„Wir untersuchen nicht nur, wie Produkte in der Zukunft aussehen werden, sondern blicken auch auf die Produktion. Additive Fertigung ist dabei ein wirklich wichtiger Faktor, der sich auch direkt auf viele Projekte auswirkt, an denen wir arbeiten“, so Bryan Allen, Designtechnologe bei Google ATAP, der auf 3D-Druck und fortschrittliche Fertigungstechnologien spezialisiert ist.
„Ich freue mich immer, wenn wir etwas Neues beim 3D-Druck entdecken – ein neues Material, einen neuen Prozess – und das dann mit einer neuen Herangehensweise auf eine Projektpipeline anwenden, wodurch Dinge effizienter, schneller, besser oder ästhetisch ansprechender umgesetzt werden können.“
Fallstudie: Eine Herausforderung bei der Vorfertigung
Das Team steckte fest. Es befand sich in der Vorfertigungsphase und stellte das Umspritzverfahren für ein Wearable ein. Schnellere Ergebnisse waren notwendig. Der Prozess war neu, die Lieferkette komplex, und sie mussten das Problem meistern, um das Produkt ausliefern zu können.
„Wir hatten Elektronikbauteile, die umspritzt und anschließend nochmal umspritzt wurden, wodurch wir ein flexibles, wasserdichtes Objekt erhielten, das wir im Wearable einsetzen konnten“, so David Beardsley, Modellwerkstattleiter bei Google ATAP.
Das Umspritzen ist ein gängiger Herstellungsprozess. Für ein umspritztes Teil ohne Elektronik fertigt eine Fabrik möglicherweise Tausende von Erstmustern zu Centpreisen pro Teil oder Baugruppe. Das ATAP-Team führte allerdings einen zweiten Umspritzvorgang bei einer bereits umspritzten elektronischen Unterbaugruppe durch – einer Leiterplatte mit komplexer Elektronik, die von einer anderen Fabrik bereitgestellt wurde. Darum waren die Erstmuster teuer, und man war von der Produktions- und Liefergeschwindigkeit der Leiterplatten durch die Zulieferfabrik abhängig.

Die Lösung: 3D-gedruckte Funktionsprototypen aus High Temp Resin
Die Parameter waren eng. Allen entschied sich dafür, die Funktionsprototypen mit High Temp Resin auf dem Form 2 Stereolithografie-3D-Drucker zu drucken. Er war sich bewusst, dass er an die Grenzen des Materials gehen würde; die endgültigen Teile würden bei einer Temperatur von 270 °C bei einem Druck von etwa 1860 bar umspritzt werden – also nahe am Maximum der spezifizierten Wärmeformbeständigkeitstemperatur (HDT) von High Temp Resin.
Erfahren Sie mehr über die neueste Formulierung und weitere Anwendungen für dieses wärmebeständige 3D-Druckmaterial oder fordern Sie einen kostenlosen Probedruck an.
„Um die kleine Detailgröße und die erforderlichen Verschlussoberflächen zu erzielen, war diese Auflösung nötig. Es war wirklich die Kombination aus der Auflösung und der hohen Temperaturbeständigkeit, die es uns ermöglichte, den Form 2 hier einzusetzen“, so Allen. „Wir haben die Möglichkeit, aus vielen anderen Fertigungsverfahren auszuwählen, aber die Option zu haben, diese Teile herzustellen, ist wirklich ein wichtiger Aspekt unseres Labors.“
Das Team machte sich schnell an die Arbeit und druckte über Nacht einige Testteile.
„Wir hatten keine Zeit, die CAD-Datei nochmal zu bearbeiten. Ich habe sie geöffnet, in STL exportiert und in PreForm geladen. Sobald wir die erste Charge für die Validierung hatten, haben wir richtig losgelegt. Wir haben im ersten Durchgang 200 Teile gefertigt und anschließend 100 weitere“, so Allen
PreForm ist die kostenlose Druckvorbereitungssoftware von Formlabs, mit der Teile in Chargen auf der Konstruktionsplattform ausgerichtet werden können. Sobald die Produktion angelaufen war, druckte Allen 250 Einsätze in 10er-Chargen, was etwa vier Stunden dauerte. So konnte das Team hunderte Teile an einem Wochenende fertigen.
Allen platzierte Stützstrukturen an den Teilen aus High Temp so, dass die Kontaktpunkte nur an den Verschlussoberflächen vorhanden sind, nicht an den Formoberflächen. So mussten die Teile nicht zusätzlich geschliffen oder nachbearbeitet werden. Ein herkömmlicher Wasch- und Nachhärtevorgang vor dem Einsatz reichte aus.
Die 3D-gedruckten Teile eigneten sich ideal als Ersatz für die elektronischen Unterbaugruppen. Durch den Prozess wurden die Durchlaufzeiten bei den Leiterplatteneinsätzen von drei Wochen auf drei Tage verkürzt. Die Kosten pro Einsatz sanken von 100 USD auf bloß 0,80 USD.
„Wir konnten den Prozess so im weiteren Verlauf abfangen und zusätzliche Arbeitsschritte vermeiden. Drei oder vier Arbeitsschritte fielen durch diese Methode einfach weg. Wir haben so jede Menge Zeit gespart“, so Beardsley.

Da die Teile unglaublich günstig in der Herstellung waren, konnte das Team mehr bereitstellen, als die Fabrik an Bedarf eingeplant hatte. So wurde sichergestellt, dass ununterbrochen gespritzt werden konnte, bis befriedigende Ergebnisse erzielt wurden.
„Die Tatsache, dass wir das Werkzeug um 3D-gedrucktes Material schließen und mit hohem Druck einspritzen konnten und es sich nicht einmal ein Grat gebildet hat, ist schon etwas Besonderes. Hätten wir nicht den Form 2 gehabt, wäre uns das nicht gelungen“, so Beardsley.
„Als wir zu einem vollständigen Produktzyklus übergingen, waren wir sicher, dass es funktionieren würde“, sagt Allen.
Im Überblick: Was hat Google ATAP geschafft? Mit dem Formlabs Form 2 SLA 3D-Drucker und High Temp Resin konnte das Team:
- mit High Temp Resin Ersatzeinsätze drucken, die dem Umspritzen mit TPU bei einer Temperatur von über 250 °C und 1860 bar standhielten;
- etwa 100 000 USD an verlorenen Elektronikunterbaugruppen sparen – und sogar mehr, wenn die Arbeitskosten miteinberechnet werden;
- etwa 100 000 USD an verlorenen Elektronikunterbaugruppen sparen – und sogar mehr, wenn die Arbeitskosten miteinberechnet werden;
3 Lektionen von Google ATAP zum Einsatz von 3D-Druck in der Produktion
Auch wenn der Produktionsprozess bei dem Wearable in dieser Fallstudie einzigartig war, kann der Lösungsansatz des Teams, die Art und Weise, wie die Technologie eingesetzt wurde und die Einstellung gegenüber 3D-Druck wertvoll für Unternehmen jeder Größe sein. Lassen Sie sich von diesen drei Lehren aus unserem Gespräch mit dem Designtechnologen Bryan Allen und dem Modellwerkstattleiter David Beardsley von Google ATAP inspirieren.
Gehen Sie an jede Phase der Entwicklung vom Prototypenbau bis zur Auslieferung des Produkts mit einer iterativen Einstellung heran.
„Einer der wirklich einzigartigen Aspekte unserer Arbeitsweise ist, dass wir den gesamten Produktionsprozess als Prototyping-Prozess betrachten, wo wir in jeder Phase der Produktion Prototypenzyklen durchführen. Wir sagen nicht einfach: ‚In Ordnung, Prototypenphase, Lieferkettenphasen, Produkteinführungsphase.‘ Wir wenden ein Designprozess und Iteration im gesamten Produktionsprozess und nicht nur am Anfang an“, erklärt Allen.
„Durch den Prototypenbau, den wir bei jedem kleinen Schritt des Prozesses machen, kommen Dinge ans Licht. Sie werden dann behandelt, bevor sie in späteren Schritten zu größeren Problemen werden“, so Beardsley.
Halten Sie Ihre Technologie nicht im Silo; betrachten Sie jede Maschine als Teil Ihrer Problemlösungs-Ausstattung, die Ihnen dabei hilft, die beste Lösung für jede Herausforderung zu finden.
„Wir versuchen nie, einen ganzen Prozess zu ersetzen. Wir versuchen immer, nachzuforschen und fragen uns: ‚Okay, was kann diese Maschine wirklich gut? Was ist die Sache, die diese Maschine wirklich besser kann als alles andere, und wie wenden wir das an?‘ Indem wir uns nicht so sehr an einen Prozess oder eine Maschine klammern, können wir die Vorteile bei vielen verschiedenen Materialien und vielen verschiedenen Prozessen erkennen und diese entsprechend einsetzen“, so Allen.
„Wir betrachten 3D-Druck als ein weiteres Werkzeug in einem Werkzeugkasten neben CNC und Formen und allen traditionelleren Herstellungsverfahren. Es verstärkt unsere Fähigkeit, darüber nachzudenken, wie wir diese neuen Technologien auf produktive Weise einsetzen können.“
Der Form 2 3D-Drucker ist Teil der Laborausrüstung von Google ATAP, die Ingenieure und Designer nutzen, um komplexe Probleme zu lösen und ehrgeizige Hardwareprojekte umzusetzen.
Beginnen Sie mit der Problemlösung.
„Es gibt immer noch so viele Einschränkungen beim Design von Teilen. Laboren, die additive Fertigung in ihren Prozessen einsetzen möchten, raten wir, ein spezifisches Problem zu isolieren, das nur bei einem Teil auftritt; sie sollten nicht das gesamte Werkzeug, sondern nur einen Einsatz drucken. Nehmen Sie ein Teil und lernen Sie daraus“, meint Allen.
Erfahren Sie mehr über den Form 2, technische Materialien und Anwendungen
Der Form 2 und High Temp Resin gehören zu den zahlreichen Werkzeugen, die im Labor von Google ATAP eingesetzt werden und Ingenieuren und Designern dabei helfen, komplexe Probleme zu lösen und ehrgeizige Hardwareprojekte umzusetzen.
„Großunternehmen mit großen Werkstätten denken sich immer ‚Oh, wir müssen diese wirklich teure Maschine haben.‘ Wir haben sie hier, und sie sind großartig. Aber die Tatsache ist, dass der Form 2 jeden Tag dominiert“, erklärt Beardsley. „Genauigkeit, Geschwindigkeit, Oberflächengüte, die Möglichkeit, direkt ein fertiges Endprodukt zu erhalten. Das ist wirklich beeindruckend.“
Lernen Sie den Form 2 und die Bibliothek an technischen Materialien bei Formlabs für Ihr eigenes Projekt kennen oder fordern Sie einen kostenlosen Probedruck an](/request-sample-part/?high-temp-nozzle), um sich selbst einen Eindruck von der Qualität von High Temp Resin und anderen Materialien zu verschaffen.
Lernen Sie mehr Techniken zum Einsatz von 3D-Druck beim Prototypenbau und der Produktion mit unserem Whitepaper Formenherstellung mit 3D-Druck.