Die Verbindung von Informatik und Maschinenbau verleiht Robotikanwendungen ein großes Potenzial im Gesundheitswesen. Ob zur Desinfektion von Patientenzimmern oder als Laborassistenten – Roboter eignen sich für ein breites Anwendungsspektrum im Gesundheitswesen. Bei anspruchsvollen medizinischen Eingriffen wie Operationen ist Präzision das A und O. In Nordamerika sind medizinisch bedingte Fehler verantwortlich für mehr als 400 000 Todesfälle pro Jahr. Somit sind sie nach Krebs und Herzkrankheiten die dritthäufigste Ursache unnatürlicher Todesfälle. Wie können Robotikanwendungen dabei helfen?
Das 2018 gegründete Unternehmen Haply Robotics mit Sitz in Montreal unterstützt Chirurgen mit Robotern bei der Feinabstimmung chirurgischer Eingriffe. Haply Robotics entwickelt die nächste Generation physischer Simulationskonsolen. Mehr als zwei Millionen Chirurgen weltweit erhalten damit die Möglichkeit, über 260 chirurgische Eingriffe zu perfektionieren, mithilfe modernster Virtual- und Augmented-Reality-Technologien. Die liebevoll „PlayStation für Chirurgen“ genannte Haply-Konsole mit inverser Kraftrückkopplung ermöglicht Chirurgen die Simulation einer Operation, bevor sie diese durchführen. Ziel ist es, das Risiko für Patienten zu verringern und die Operationszeiten zu verkürzen.
Haply Robotics hat betriebsinternen 3D-Druck für das Rapid Prototyping eingeführt und setzt FDM-, SLA- und SLS-3D-Druck in seinen Projekten ein. In diesem Beitrag wird beschrieben, wie Haply Robotics verschiedene 3D-Drucktechnologien einsetzt und weshalb man dort einen Fuse 1 erworben hat.
Die Zusammenarbeit begann mit der Entwicklung von Beatmungsgeräten für COVID-19
Felix Desourdy, Leiter der Maschinentechnikabteilung bei Haply Robotics, gab an, dass er die Mitbegründer von Haply Robotics Colin Gallacher und Steve Ding im Jahr 2018 kennen lernte. „Wir lernten uns beim National Research Council of Canada kennen, wo wir in einem Team an der Entwicklung haptischer Systeme für die Simulation medizinischer Eingriffe arbeiteten. Jeder einzelne von uns war ein Fan der neuen Ära, in der wir etwas entwerfen, schnell überarbeiten und einen Prototyp nach dem anderen erstellen, bis wir die perfekte Umsetzung unserer Idee haben.“
Im Jahre 2020 wurde eine wichtige Zusammenarbeit mit der kanadischen Regierung auf Eis gelegt. Stattdessen wandte sich das Team mit seinen Design- und Robotikanwendungen der CODE LiFE Ventilator Challenge zu, einem Aufruf an Gerätehersteller zur Entwicklung eines kostengünstigen, einfachen, benutzerfreundlichen und leicht zu erstellenden Beatmungsgeräts, das für COVID-19-Patienten geeignet ist.
Mehr als 2600 Anmeldungen gingen ein mit über 1000 Teams aus 94 Ländern. Das Haply-Design wurde als beste Variante ausgewählt, aufgrund des einfachen Designs und Betriebs sowie der niedrigen Produktionskosten und der einfachen Schulung.
„Die CODE LiFE Ventilator Challenge war für uns eine unglaubliche Herausforderung, aber eine der bereicherndsten Erfahrungen, die wir als Team gemacht haben. Motiviert hat uns die Ungleichheit zwischen Industrie- und Entwicklungsländern hinsichtlich des Zugangs zu lebenswichtigen medizinischen Technologien wie Beatmungsgeräten – eine Problematik im Rahmen von COVID-19. Wir sind sehr dankbar, dass das Organisationskomitee und insbesondere Prof. Reza Farivar, die Montreal General Hospital Foundation, das RI-MUHC und die McGill-Fakultät für Ingenieurwesen eine so sinnvolle Initiative auf die Beine gestellt haben“, so Colin Gallacher, Mitbegründer von Haply Robotics.
Der 3D-Druck half Haply bei der Entwicklung des Beatmungsgeräts, wobei der Form 3 und Tough Resin zur Herstellung des Innenlebens des Geräts verwendet wurden. Der betriebsinterne 3D-Druck half dem Team bei der Herstellung der endgültigen Teile für das Innere des Beatmungsgeräts. In kürzester Zeit wurde ein Design erstellt und zum Sieger des Wettbewerbs gekürt, was die Verfügbarkeit von Beatmungsgeräten während der Pandemie verbesserte.
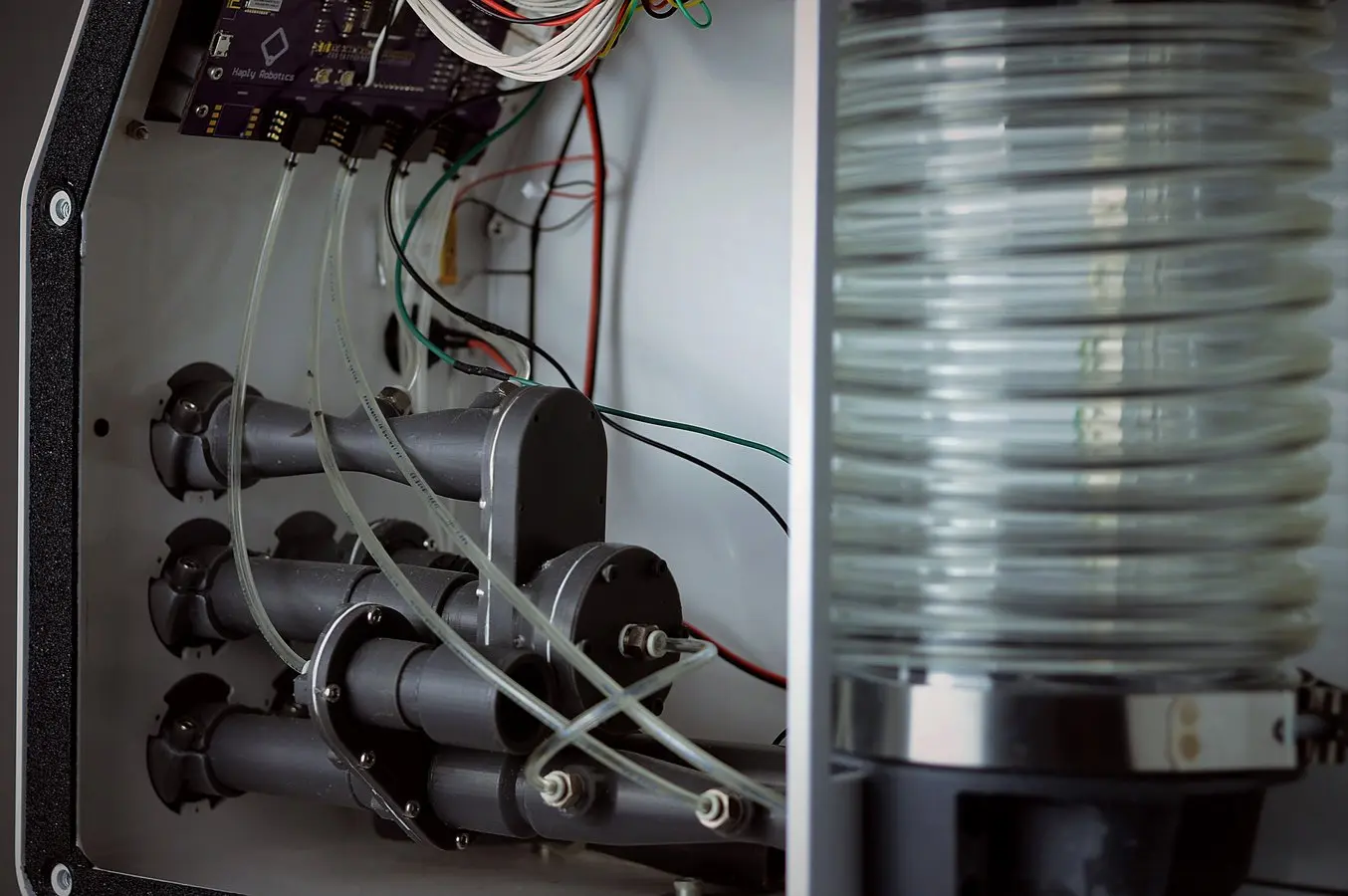
Das 3D-gedruckte Innenleben des Beatmungsgerätes von Haply.
„Tough Resin war für dieses Projekt ideal, da es abgedichtet werden kann. Und wir konnten in das Harz bohren und Verbindungsstücke einfügen, ohne dass es undicht wurde. Es ist vergleichbar mit ABS“, sagt Desourdy.
Rapid Prototyping für das perfekte Design
Die Erkenntnisse aus der Entwicklung des COVID-19-Beatmungsgeräts nutzte das Team, um an seinem Hauptprojekt weiterzuarbeiten: die Entwicklung der Haptik für die Simulation medizinischer Eingriffe.
Rapid Prototyping ist der Hauptgrund, warum Haply in betriebsinternen 3D-Druck investiert. Mit Desktop-Druckern erstellt das Team mehrere Iterationen komplexer Teile, bis die optimale Form gefunden ist. Für Desourdy gibt es zwei Hauptgründe, warum Iteration so wichtig ist: Ergonomie und die richtige Geometrie. „Wir sind Fans der neuen Designära: Wir erstellen Prototyp um Prototyp, bis wir die perfekte Form gefunden haben. Alles, was wir herstellen, hat die perfekte Größe für den 3D-Druck.“
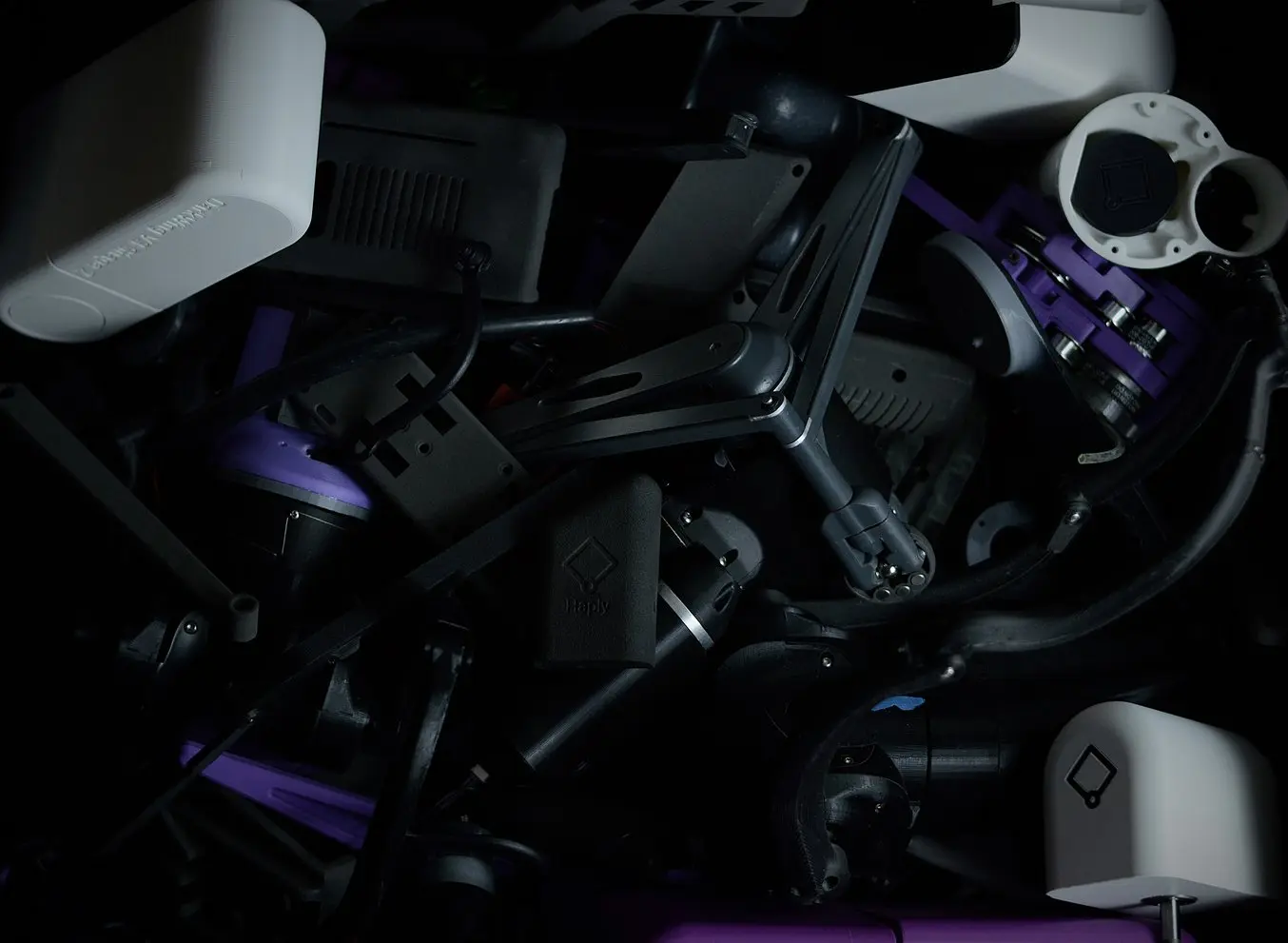
Haplys Kraftrückkopplungskonsole hat Dutzende von Iterationen durchlaufen.
Das Team investierte ursprünglich in FDM-Drucker, da diese preisgünstig sind und eine hohe Druckgeschwindigkeit aufweisen. Diese Maschinen erfüllten ursprünglich die Ziele des Teams beim Rapid Prototyping. Mit der Zeit wünschte sich das Team jedoch Prototypen, die optisch und funktionell vergleichbar sind – was Drucke in höherer Qualität erforderte. Letztendlich erwarbt man einen Form 2 und dann einen Form 3 für den hochauflösenden Druck.
„Insbesondere im chirurgischen Simulator arbeiten wir häufig im Umfeld menschlicher Hände. Man muss in der Lage sein, zu iterieren und zu iterieren“, berichtet Desourdy. „Wir haben versucht, ein steiferes Gerät zu entwickeln und mehr darüber zu erfahren, was die Steifigkeit ausmacht, ohne zunächst das Material zu ändern oder die richtige Geometrie für das, was man erreichen will. Ich glaube, dass man sich iterativ an etwas herantastet, das eine bessere Geometrie hat. Und wenn wir fertig sind, ist es einfach, zu einem steiferen Material zu wechseln. Um die Geometrie zu verändern, muss man aber noch ein bisschen weiter gehen, um dies zu erreichen.“
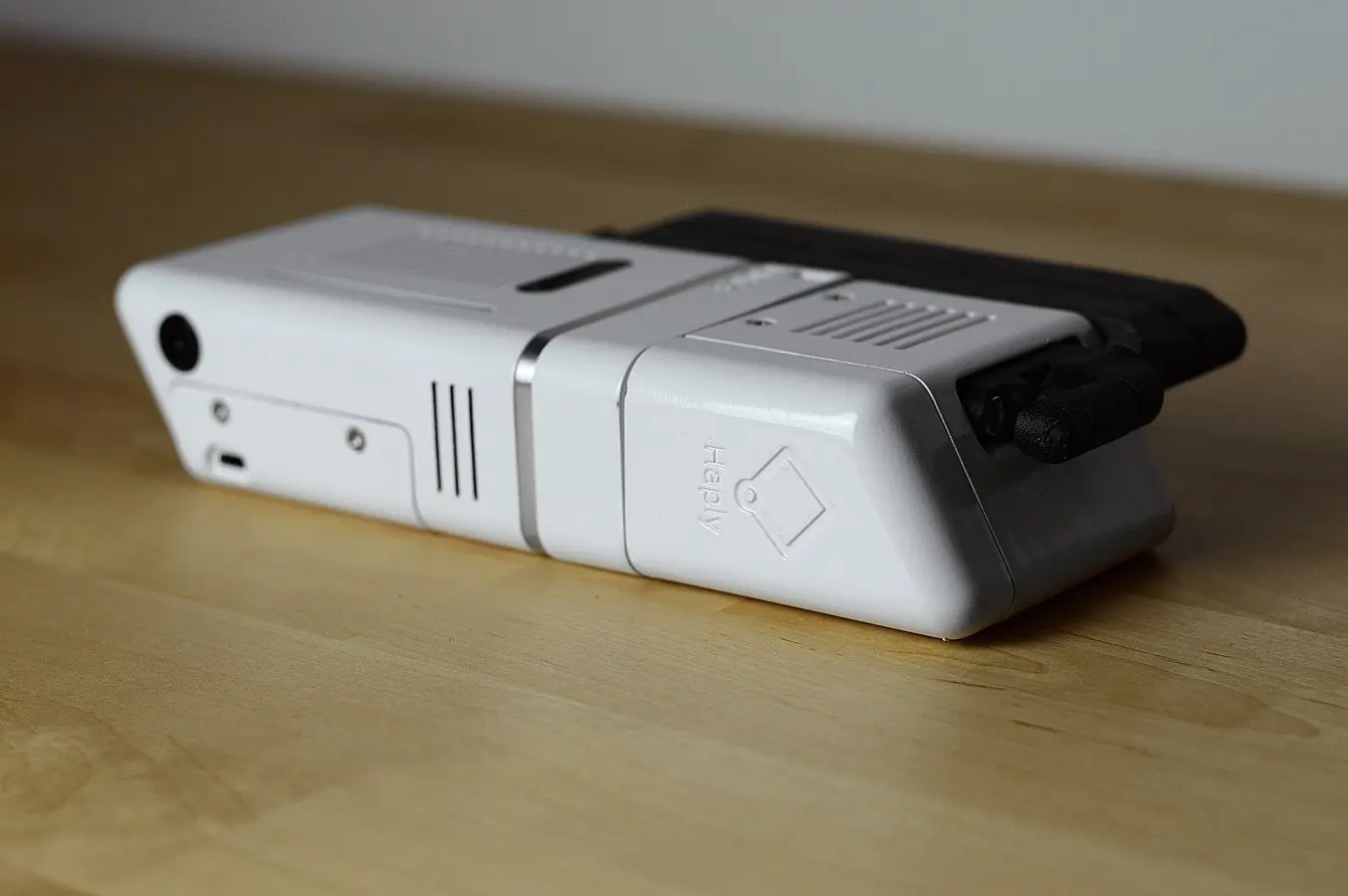
Der geschlossene Roboterarm
Prototypenerstellung für Endverbrauchsteile mit dem Fuse 1
Zum Bau weiterer Prototypen für den Roboterarm führte Haply Robotics mit dem Fuse 1 den betriebsinterne SLS-3D-Druck ein. Grund dafür ist, dass die mit dem Fuse 1 hergestellten Nylonteile dem vom Team gewünschten Endprodukt näher entsprechen. Zuvor wurden Prototypen aus Nylon extern hergestellt, was eine Reihe von Problemen mit sich brachte. „Mit dem Fuse 1 erreichen wir eine ganz neue Dimension der Prototypenentwicklung. Wir erhalten ein Teil in zwei statt in fünf Tagen und ich habe dann etwas, das aus Nylon besteht und näher am Endprodukt ist. Da der Druck betriebsintern erfolgt, lernt man die Toleranz der Maschine und des Materials kennen. Es ist alles einfach viel präziser“, erklärt Desourdy.
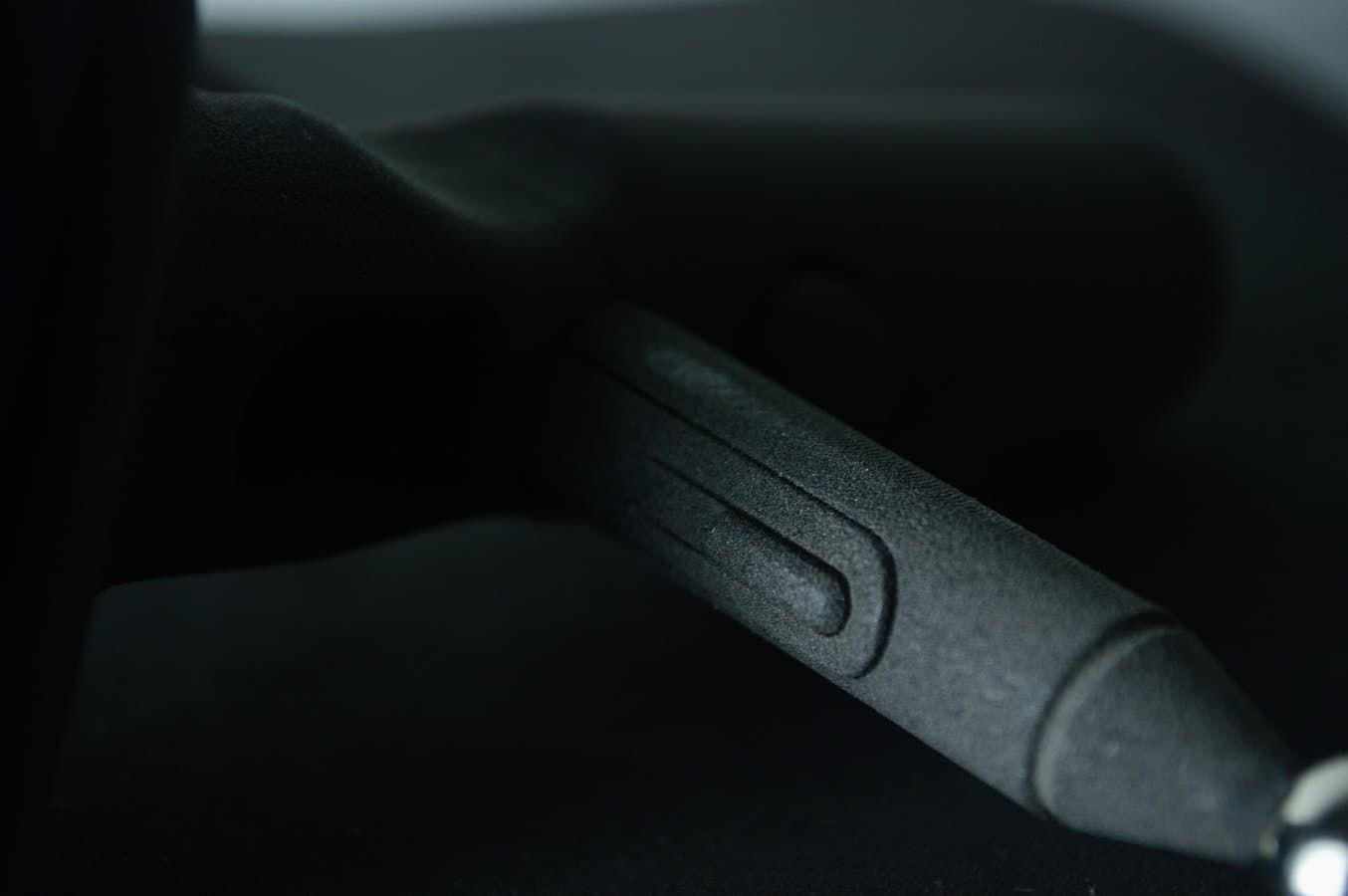
Das Team druckte mit dem Fuse 1 einen funktionsfähigen Knopf.
Desourdy ergänzte, dass Outsourcing weniger Kontrolle über die Ergebnisse bedeutet. „Wenn man den Druckauftrag vergibt, hat man nicht notwendigerweise die richtige Ausrichtung oder die richtige Spezifikation dafür. Außerdem weiß man nicht, welchen Drucker die Agentur hat oder wie gut sie ihn wartet, sodass man nicht sagen kann, wie das Ergebnis ausfällt“, gibt er an. „Ich finde, die Möglichkeit schneller Verbesserung ist das Wertvollste, was man haben kann.“
Ein weiterer Aspekt für kleine, aber wachsende Unternehmen wie Haply Robotics ist der begrenzte Platz in ihrem wachsenden Büro. Herkömmliche SLS-3D-Drucker nehmen viel Platz in Anspruch und sind oft schwer unterzubringen. Der Fuse 1 hat eine relativ kompakte Größe und liefert dennoch eine hohe Leistung. „Der Fuse ist wirklich schön, weil er nicht so groß ist. Er braucht mehr Platz als ein gewöhnlicher Desktop-3D-Drucker. Im Vergleich zu einer industriellen Maschine für diese Art der Produktion ist er aber wirklich sehr klein“, schwärmt Desourdy. Ihm zufolge hatte das Team die Investition in einen SLS-Drucker von HP in Betracht gezogen, die Größe des Geräts war jedoch ein Hindernis. Er fügt hinzu: „Schaut man sich die anderen industriellen Maschinen auf dem Markt an, ist der Fuse 1 schon klein.“
Jessica Henry, Product Owner bei Haply, ist überzeugt, dass der 3D-Druck mit dem Fuse 1 ihre Prozesse optimiert und automatisiert. Henry betont, dass die Abbildung von Details, wie subtil sie auch sein mögen, im 3D-Druck entscheidend ist. „Wir ändern ein kleines Detail und schon läuft der Roboterarm völlig reibungslos. Und wir können mit jedem Druck auch die kleinsten Details verändern“, erzählt Henry. Dank des Fuse 1 ist das Team in der Lage, mehrere Teile pro Druckzyklus zu drucken. Die Kapazität für die gleichzeitige Produktion von Roboterarmen wird damit erweitert. Um diese Leistung zu erreichen, müsste das Team mehrere FDM-Geräte kaufen, würde aber dennoch nicht die Anforderungen an die Leistung der Teile erreichen.
Ein großer Vorteil des Fuse 1 im Gegensatz zu FDM und SLA ist schließlich die Abwesenheit der Stützstrukturen an den Teilen.
Desourdy sagte, er habe das gleich bemerkt: „Wenn ich für FDM entwerfe muss ich wissen, dass ich entweder eine ebene Fläche für Stützstrukturen brauche oder eine Fläche, die unansehnlich sein darf. Auch bei einem Kunstharzdrucker muss eine Seite die Stützstrukturen aufnehmen. Der Fuse 1 hat die Art und Weise verändert, wie ich die Teile entwerfe, eben weil er ohne Stützstrukturen auskommt. Bei jeder Ausrichtung wird das Detail beibehalten.“ Diese Veränderung beeinflusst auch den Designprozess, wie Desourdy anmerkt. „Ich kümmere mich weniger um den 3D-Druckprozess und konzentriere mich mehr auf das Design, was ja auch mein Ziel ist.“
Um seinen Prototypen noch mehr Leben einzuhauchen, sucht das Team nach Lösungen zum Einfärben oder Lackieren der nachbearbeiteten Teile.
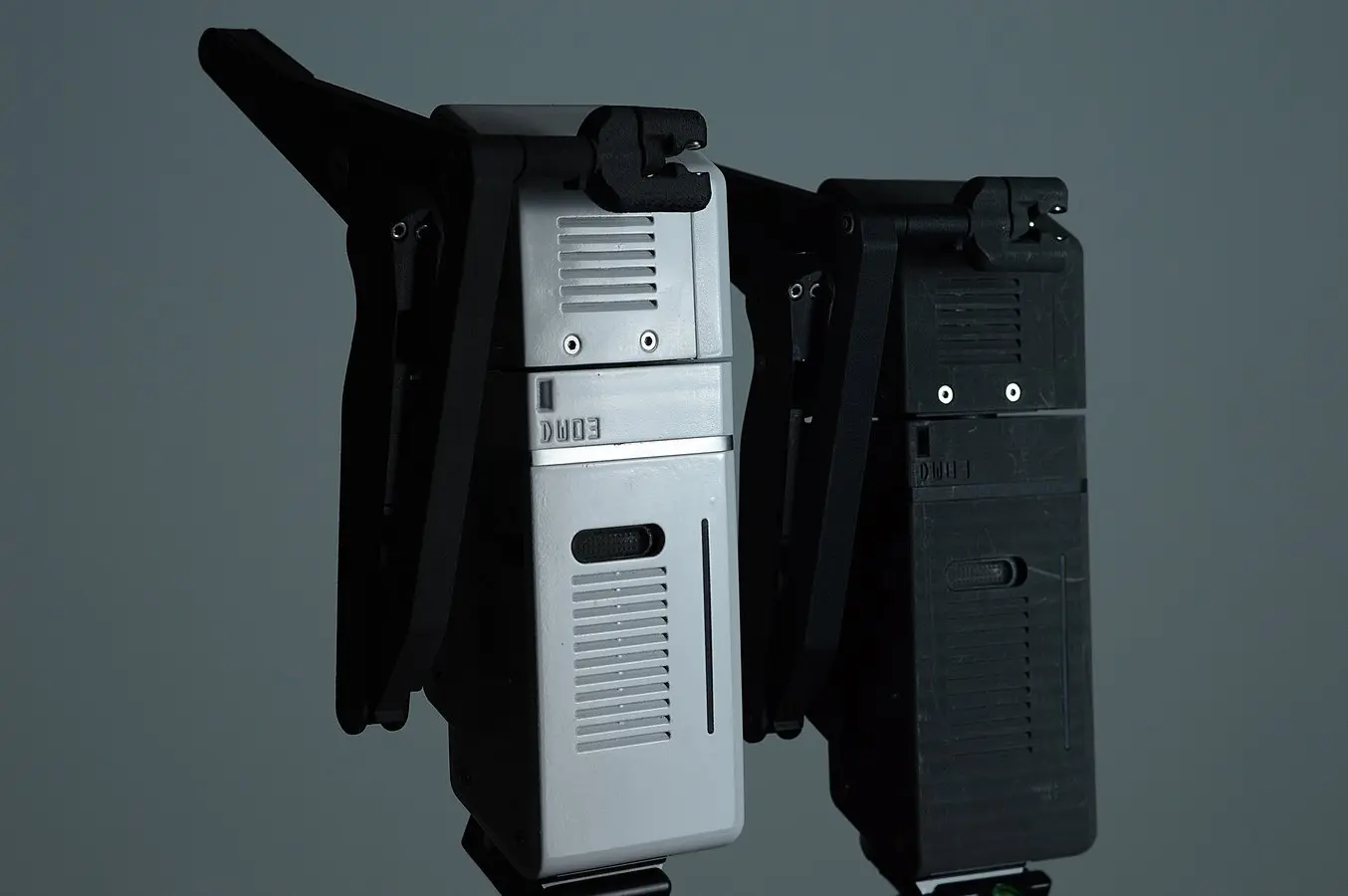
Das Gehäuse des Roboterarms wurde aus Nylon gedruckt und lackiert.
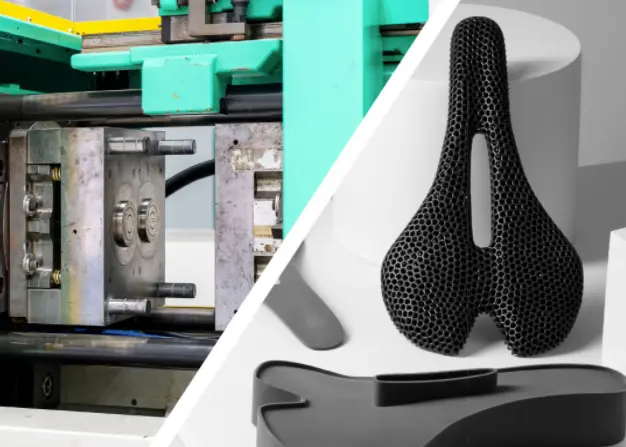
SLS-3D-Druck oder Spritzguss: Wann sollte man Spritzgussteile durch 3D-Druck ersetzen?
In diesem Whitepaper werden der Spritzguss und seine Vor- und Nachteile erörtert sowie der SLS-3D-Druck und die Anwendungen vorgestellt, bei denen er als ergänzende Technologie eingesetzt werden kann.
Weitere Informationen über den Fuse 1
Obwohl der Fuse 1 derzeit für die Prototypenfertigung eingesetzt wird, hat Haply Robotics das Ziel, den Fuse 1 auch für Endverbrauchsteile zu verwenden. „Soweit ich das beurteilen kann, lässt sich das für die Kleinserienfertigung leicht umsetzen. Das dürfte höchst interessant werden. Ein bestimmter Teil ist für die Prototypenentwicklung vorgesehen. Ein Teil davon wird für den Endverwendung eingesetzt werden“, bekundet Desourdy. Henry ergänzt: „Das Produkt wird niemals überholt sein, denn man kann jederzeit Teile am Gerät hinzufügen oder optimieren.“
Der Fuse 1 wird gegenwärtig von einer Reihe von Herstellern im Gesundheitswesen eingesetzt, darunter auch Unternehmen, die an Medizinprodukten arbeiten. Unternehmen wie Partial Hand Solutions und Tension Square entwickeln mit dem Fuse 1 patientenspezifische Prothetiklösungen und unterstützende Geräte für kollabierte Lungen – erstmals im betriebsinternen SLS-3D-Druckverfahren.
„Ich wollte immer schon einen SLS-Drucker, aber zum aktuellen Preispunkt waren sie für mich nicht erschwinglich. Der Fuse 1 eignet sich ideal für kleine Unternehmen, wie Partial Hand Solutions.“