3D-Drucker versorgen Druckerpressen: Robotikanwendungen und Ersatzteile bei HEIDELBERG
Die Heidelberger Druckmaschinen AG ist der weltweit führende Hersteller von Offsetdruckmaschinen und in über 170 Ländern tätig, mit mehr als 10 000 Beschäftigten rund um den Globus. Das Unternehmen produziert eine große Bandbreite an Werkzeugen und Automatisierungslösungen für die gesamte Wertschöpfungskette des Drucks, angefangen von einigen der größten und schnellsten Druckpressen nach neuestem Stand bis hin zu Schneid- und Falzmaschinen.
Ungefähr vor sechs Jahren fügte HEIDELBERG seinen Prozesse eine neue Dimension hinzu: den 3D-Druck. Ursprünglich führte das Unternehmen die Technologie ein, um die Prototypen- und Produktentwicklung zu optimieren, indem es Kosten und Durchlaufzeiten verringerte. Heute jedoch nutzt es 3D-gedruckte Teile in der Serienproduktion und produziert Tausende von Teilen pro Jahr für etwa 15 verschiedene Anwendungen.
Lesen Sie im Folgenden alles darüber, wie leichtgewichtige Teile aus dem SLS-3D-Drucker (selektives Lasersintern) Robotikanwendungen möglich machen und wie Druckteile selbst Stahlkomponenten in Falzmaschinen ersetzen können.
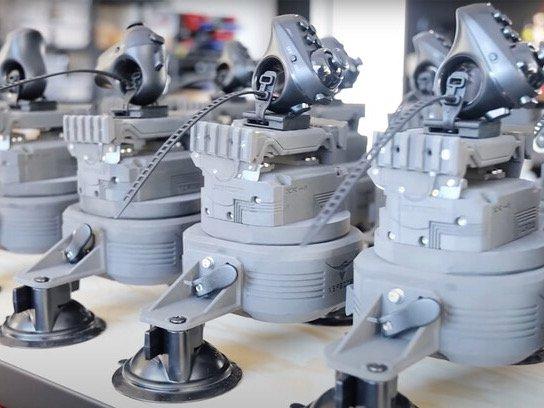
3D-gedruckte Teile für die Endverwendung im Belastungstest
In diesem Whitepaper stellen wir Formlabs' Hardware und Materialien für den 3D-Druck von Endverbrauchsteilen vor. Der Bericht schildert verschiedene Fallbeispiele von Kunden und gibt Ergebnisse von Belastungstests an, um die Eignung von 3D-Druckmaterialien für die Endverwendung zu belegen.
Beschleunigte Produktentwicklung
„HEIDELBERG kommt mit Projekten in der Neu- und Weiterentwicklung auf uns zu, speziell bei Entwicklungen von Bauteilen und Baugruppen, die außerhalb der konventionellen Fertigung liegen“, erzählt uns Joachim Krumma.
Nach 15 Jahren in der Produkt- und Anwendungsentwicklung bei HEIDELBERG ist Krumma heute Geschäftsführer der CTS-3 GmbH, einem Technologie-Beratungsunternehmen im Bereich der additiven Fertigung. Das Unternehmen arbeitet eng mit dem Forschungs- und Entwicklungsteam von HEIDELBERG zusammen und unterstützt es bei der Produktentwicklung sowie der Überführung neuer Anwendungen in die Serienproduktion.
Ein Teil der Entwicklung findet in Praxistests statt, sodass das HEIDELBERG-Produkt direkt geprüft und durch Echtzeit-Rückmeldungen vom Endkunden verbessert werden kann.
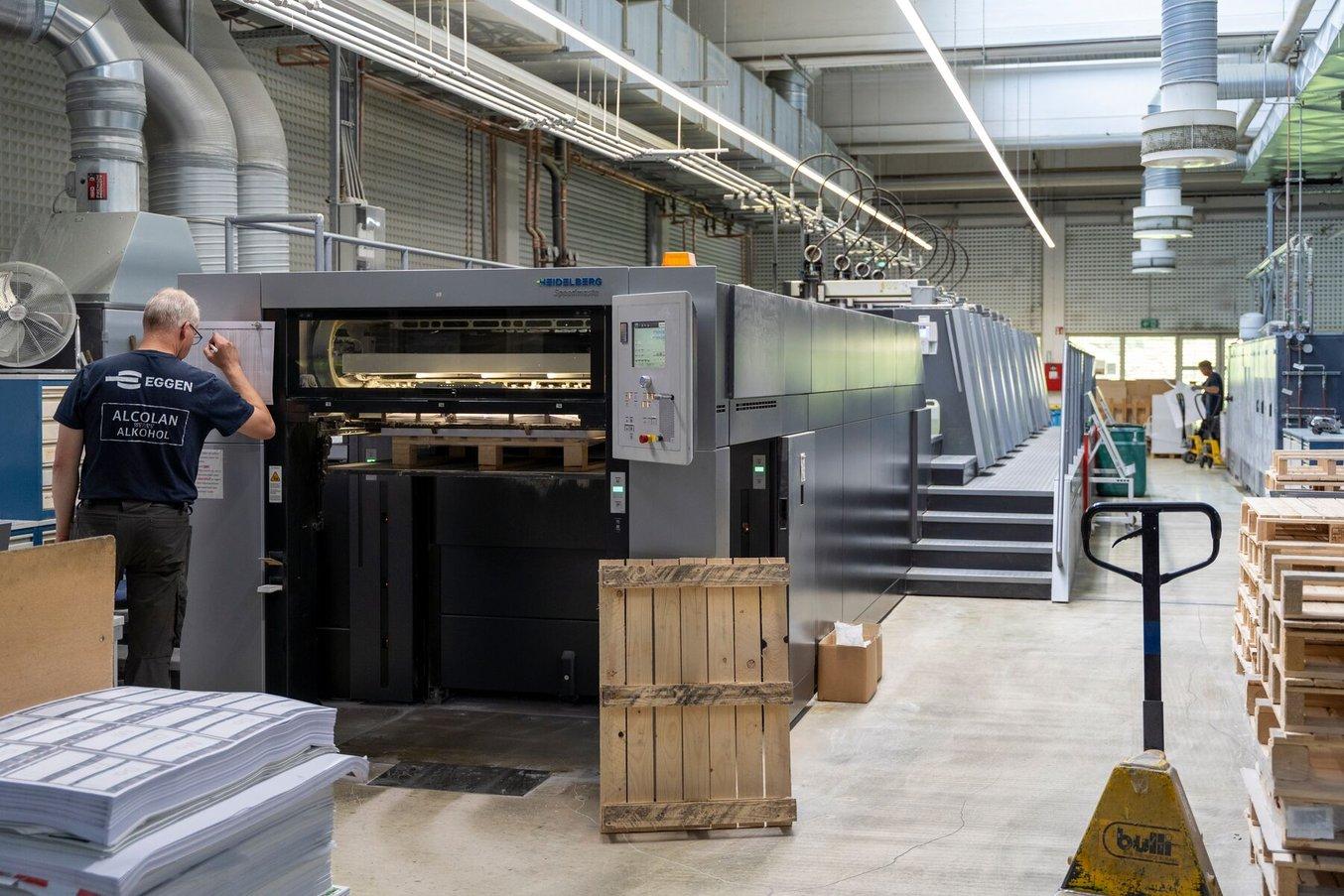
Meinders & Elstermann ist eine große Offsetdruckerei in Belm.
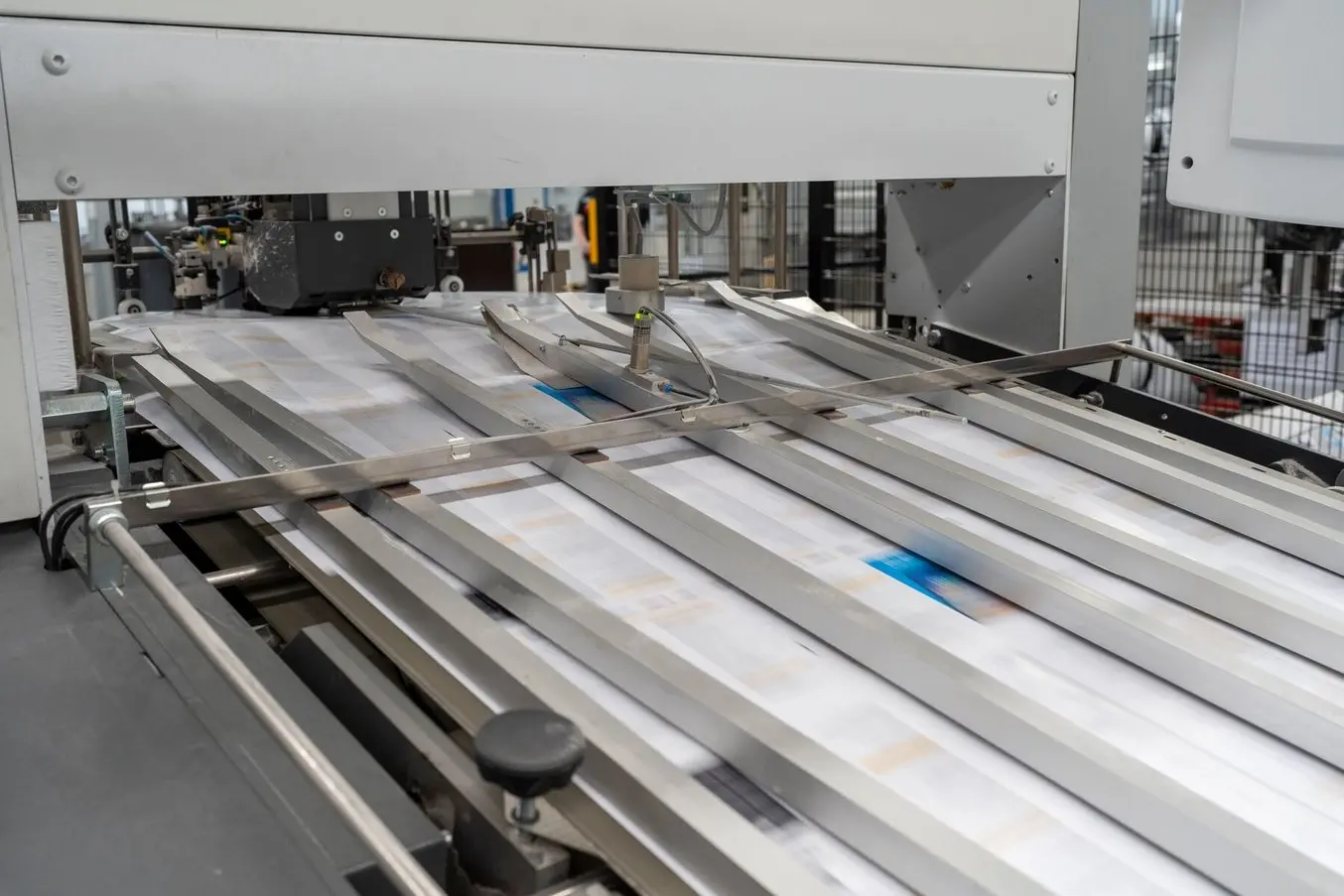
Neue HEIDELBERG-Produkte werden in ihrem Werk getestet und weiterentwickelt.
„Meinders & Elstermann ist eine große Offsetdruckerei in Belm. Wir bedrucken etwa 100 bis 120 Millionen Bögen Papier pro Jahr. Wir haben in der Druckerei vier HEIDELBERG-Druckmaschinen und in der Druckweiterverarbeitung sieben Falzmaschinen. Maschinen, die HEIDELBERG neu auf den Markt bringen will, werden von uns getestet und bei uns auch permanent weiterentwickelt“, berichtet Klaus Harig, Abteilungsleiter der Weiterverarbeitung bei der Meinders & Elstermann GmbH & Co. KG.
3D-Druckteile kommen hier in einer breiten Palette von Anwendungen zum Einsatz: Es gibt leichtgewichtige Teile für Pick-and-Place-Roboter, neue Bauteile für Falzmaschinen und Ersatzteile für Maschinenkomponenten, die früher aus Stahl gefertigt wurden. Für die Produktion all dieser Teile nutzt das Team einen SLS-3D-Drucker der Fuse-Serie, auf dem starre Teile aus Nylon 12 Powder und flexible Teile aus TPU 90A Powder gedruckt werden.
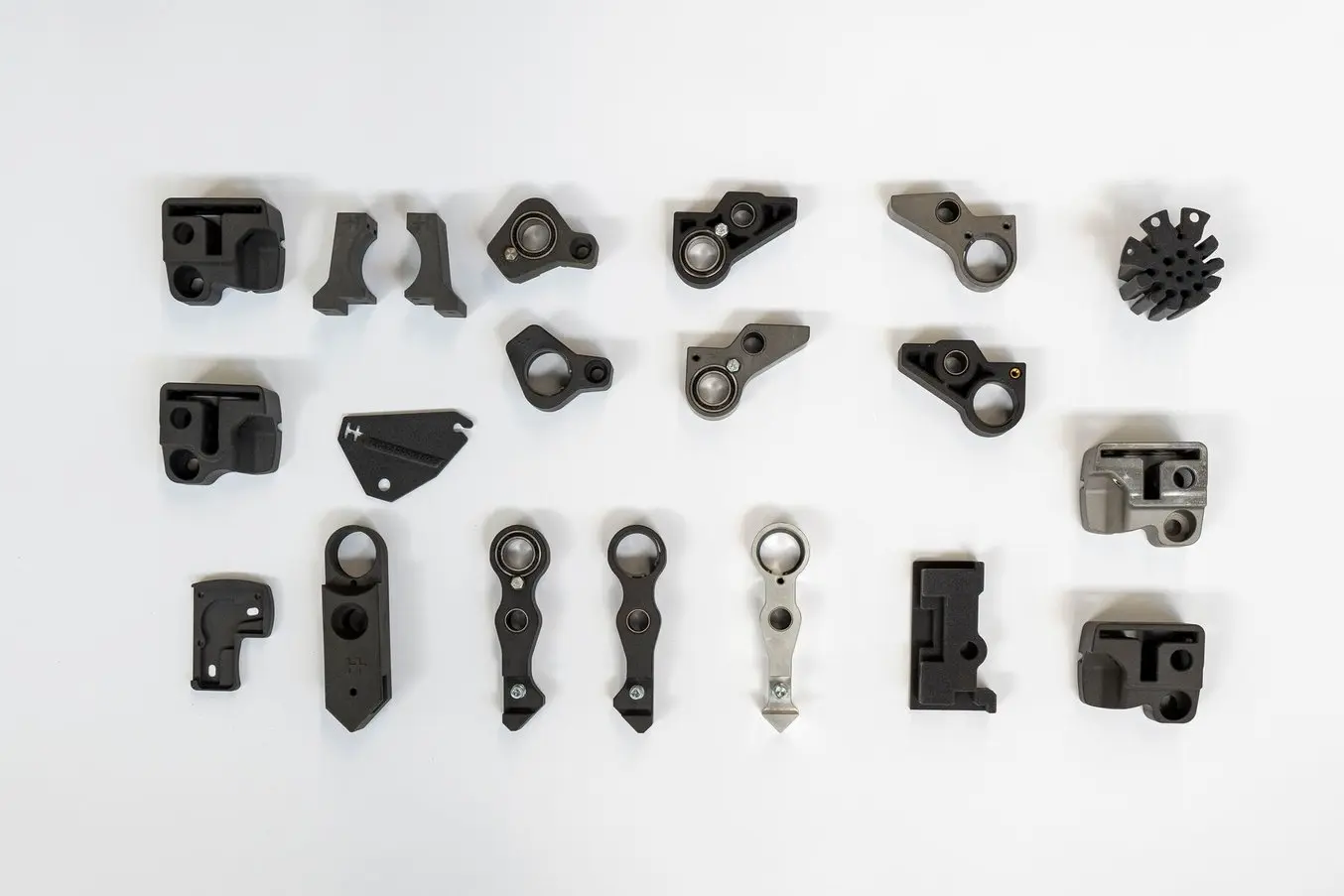
Bei HEIDELBERG kommen 3D-Druckteile in einer breiten Palette von Anwendungen zum Einsatz, z. B. leichtgewichtige Teile für Roboter und Ersatzteile für Maschinenkomponenten, die früher aus Stahl gefertigt wurden.
„Der essenziellste Punkt für uns ist die Geschwindigkeit des 3D-Drucks. Wir haben eine schnelle Reaktionszeit auf die ständig wechselnden Kundenanforderungen. Wir können neue Teile innerhalb von einem oder zwei Tagen entwickeln und produzieren, was uns früher manchmal mehrere Wochen gekostet hat. Deswegen ist der 3D-Druck perfekt für uns.“
Joachim Krumma, Geschäftsführung, CTS-3 GmbH
Neben den verkürzten Durchlaufzeiten kann sich das Unternehmen auch über enorme Kosteneinsparungen freuen. Dies gilt vor allem für den Bereich der Prototypenentwicklung, aber auch für die Serienproduktion von kundenindividuellen Teilen oder Kleinserien für die Endverwendung. „Bei der Fertigung von Teilen haben wir oft eine Kostenreduktion im Faktor 10 bis 20 im Vergleich zur konventionellen Produktion“, so Krumma.
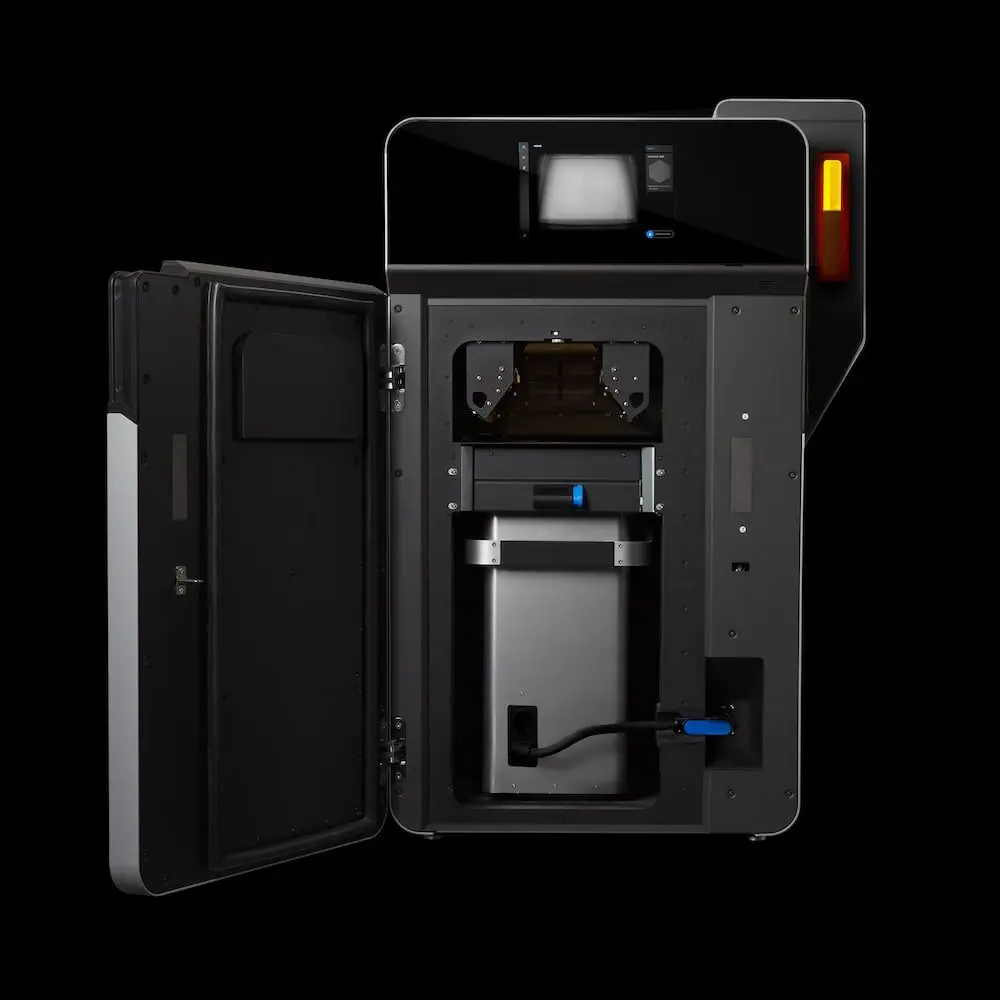
Rekordschnelle Produktion leistungsstarker SLS-Teile mit dem neuen Fuse 1+ 30W
Sehen Sie sich unsere Produktvorführung an und lassen Sie sich den Fuse 1+ 30W und den SLS-3D-Druck durch einen Formlabs-Experten erklären.
Leichte Bauteile für die Robotik
Der Meistertitel für die Maschine mit den meisten 3D-gedruckten Bauteilen geht an den P-Stacker, einen innovativen Pick-and-Place-Roboter, der Stapel gefalzter Papierbögen von der Falzmaschine aufnimmt und auf einer Palette ablegt.
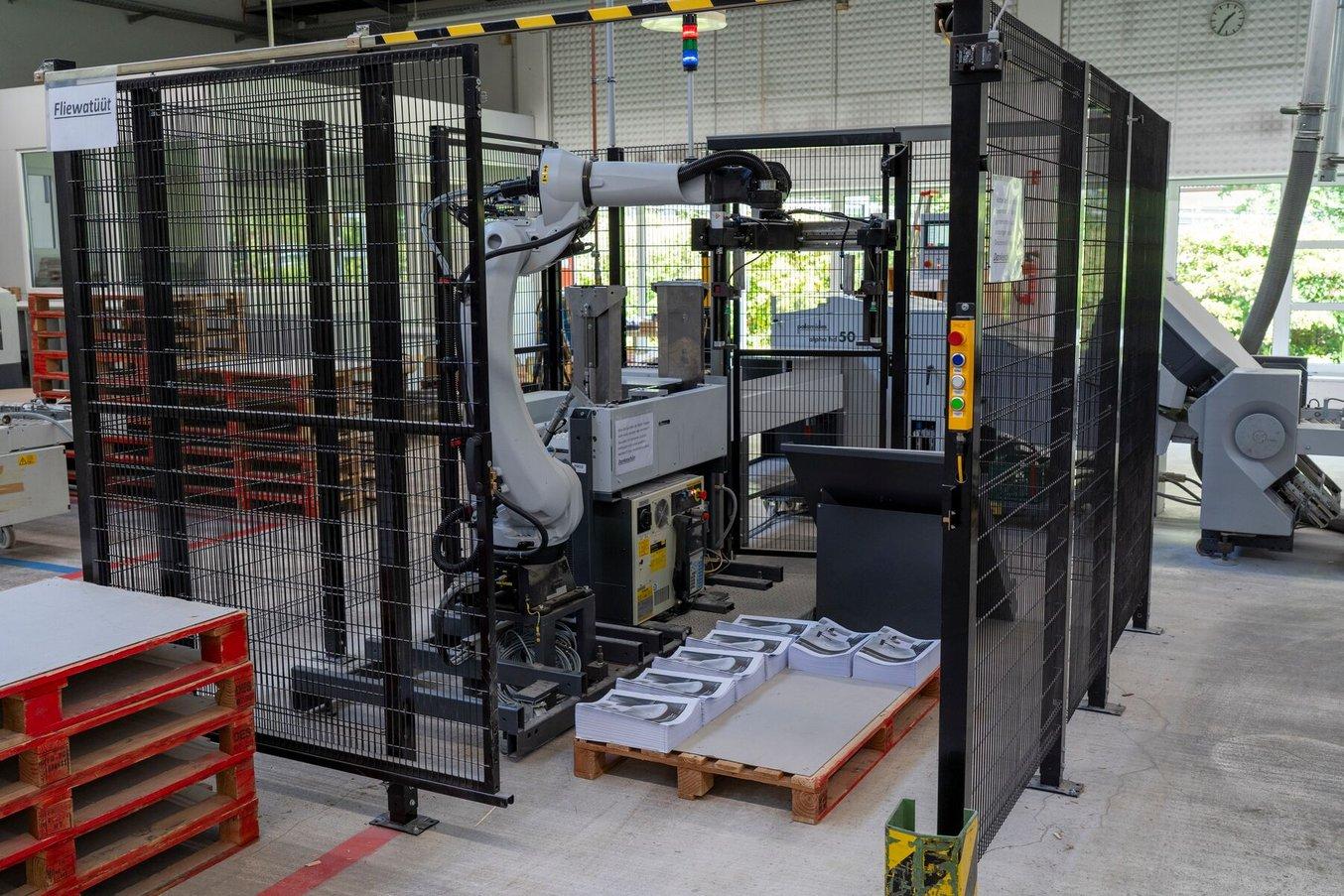
Der P-Stacker übernimmt die mühsame Aufgabe, Pakete hinter der Falzmaschine zu stapeln, und nimmt dem Personal damit viel Arbeit ab.
„Der Roboter kann die Paletten bis zu einen Meter hoch stapeln. Je nach Laufleistung kann er bis zu 18 000 Bögen die Stunde absetzen. Bevor wir den P-Stacker in Einsatz genommen haben, musste eine Person jeden Tag die vier bis sechs Tonnen auf Palette absetzen“, erzählt Harig.
Viele der 3D-gedruckten Komponenten in diesem Roboter sind hochgradig komplex und üben mehrere Funktionen zugleich aus. So enthält er zum Beispiel Verbindungsteile und Halterungen, die für die Achsenbewegung, Achsklemmung, den pneumatischen Saugeffekt, die Sensortechnologie und die Schiebeeigenschaften zuständig sind.
„Vor allem bei Robotikanwendungen spielt das Gewicht eine entscheidende Rolle. Je mehr Gewicht wir haben, desto mehr werden die Teile mechanisch beansprucht, und das geht auf die Dauerfestigkeit der Teile. Wir haben eine ziemlich hohe Packungsdichte in der Anlage, das heißt, wir haben wenig Spielraum für große Verbauungen und Teile“, so Krumma.
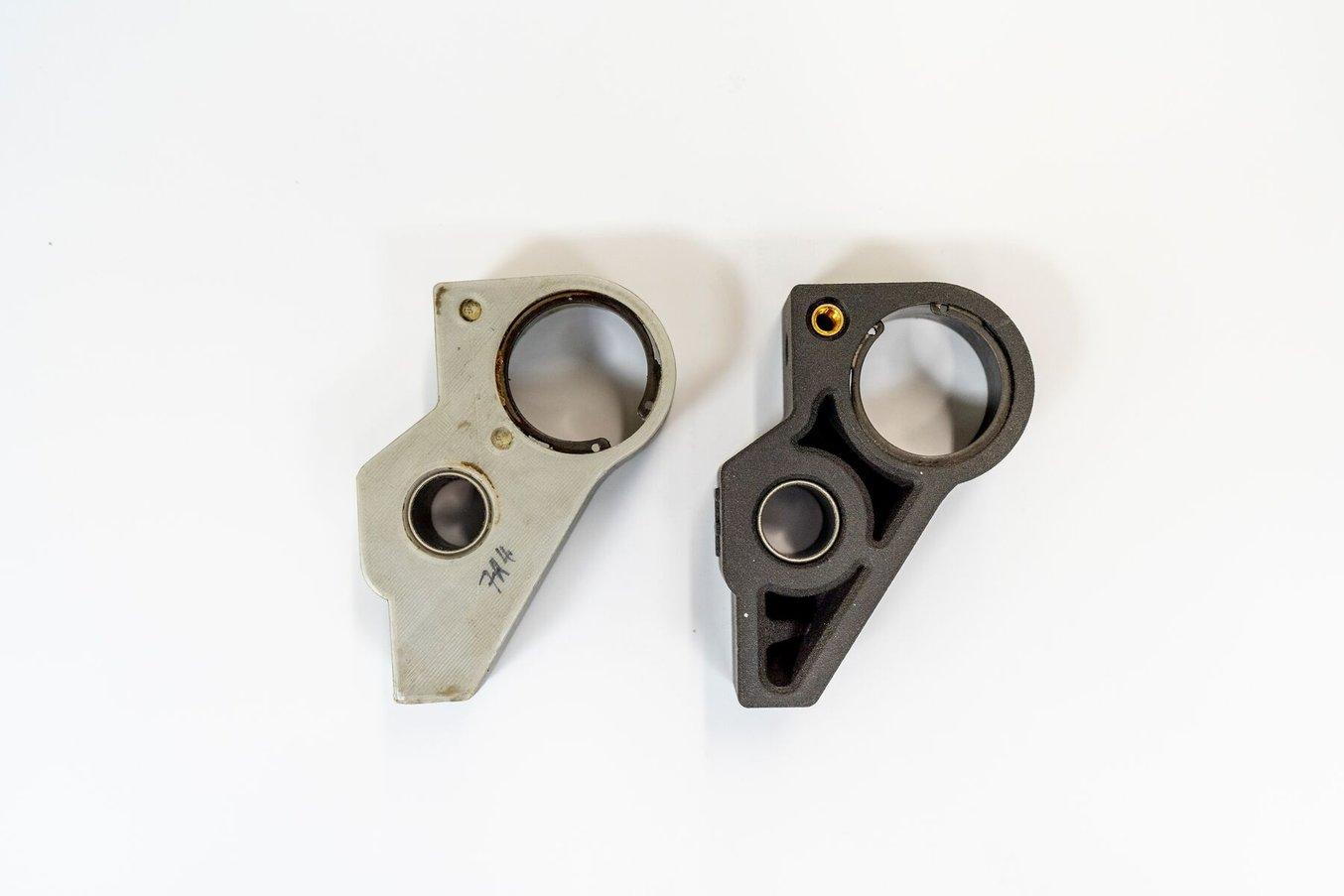
Kunststoff-3D-Druckteile sind leichter als Stahl, und die Designs können abhängig von der Belastung und den Kräften, denen sie ausgesetzt werden, weiter optimiert werden. Erhöhte Designkomplexität verursacht dabei keine höheren Kosten, anders als bei konventionellen Fertigungsprozessen wir der Zerspanung.
Das Ergebnis sind häufig komplizierte, amorphe Strukturen, da das Design ausgehend von den wirkenden Kräften und Lasten speziell für die jeweilige Anwendung entwickelt wird. Und weil die Teile kontinuierlich im Einsatz sind, kann die auf sie wirkende Belastung sehr hoch sein. Häufig werden die 3D-gedruckten Bauteile auch mit anderen Komponenten kombiniert, so zum Beispiel mit metallenen Lagern oder Bauteilen mit Teflon-Beschichtung, die reibungsmindernd wirkt.
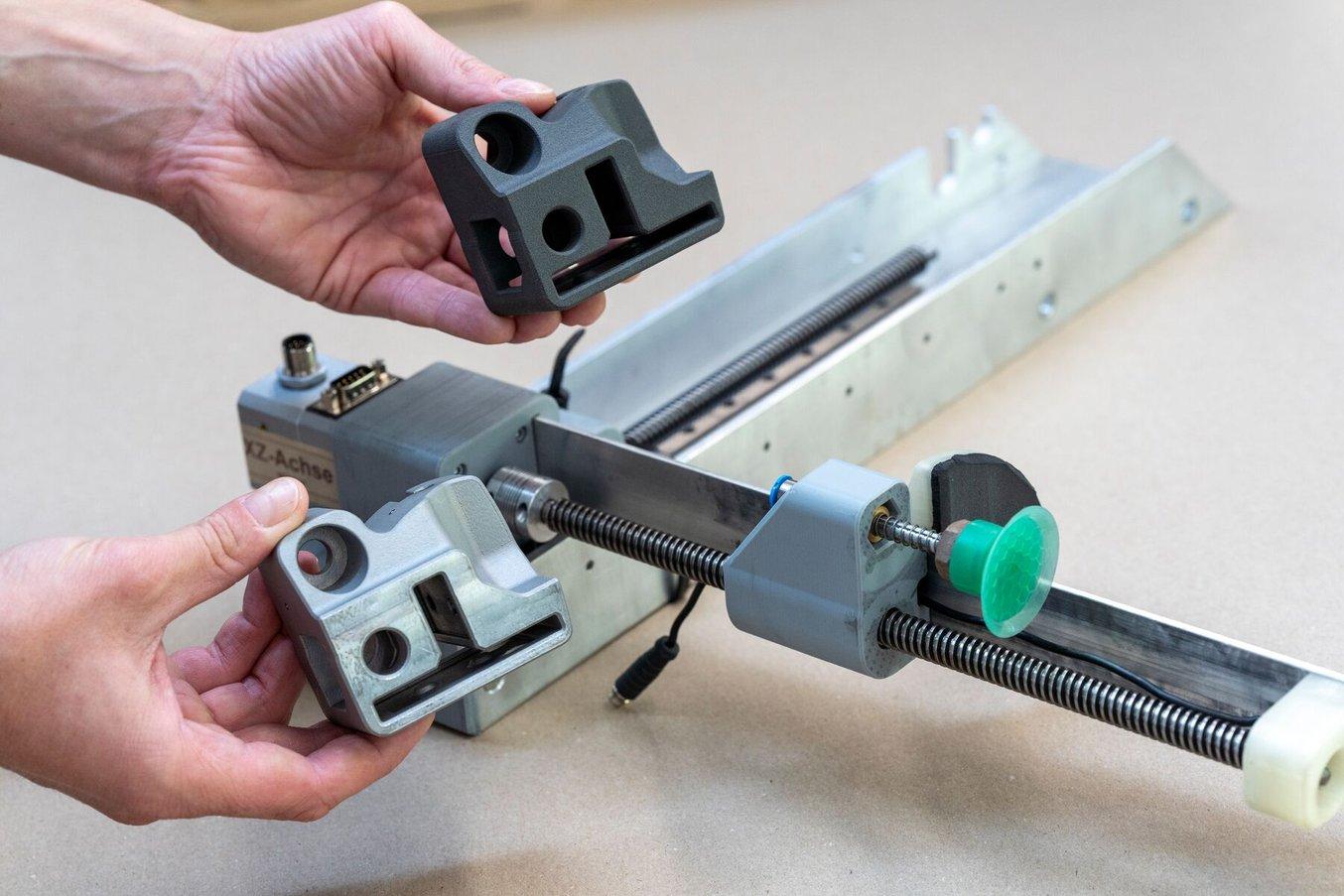
Viele der 3D-gedruckten Teile in dem Roboter sind hochgradig komplex und üben unterschiedliche Funktionen aus. Mit Nylon 12 Powder werden starke, haltbare Bauteile hergestellt.
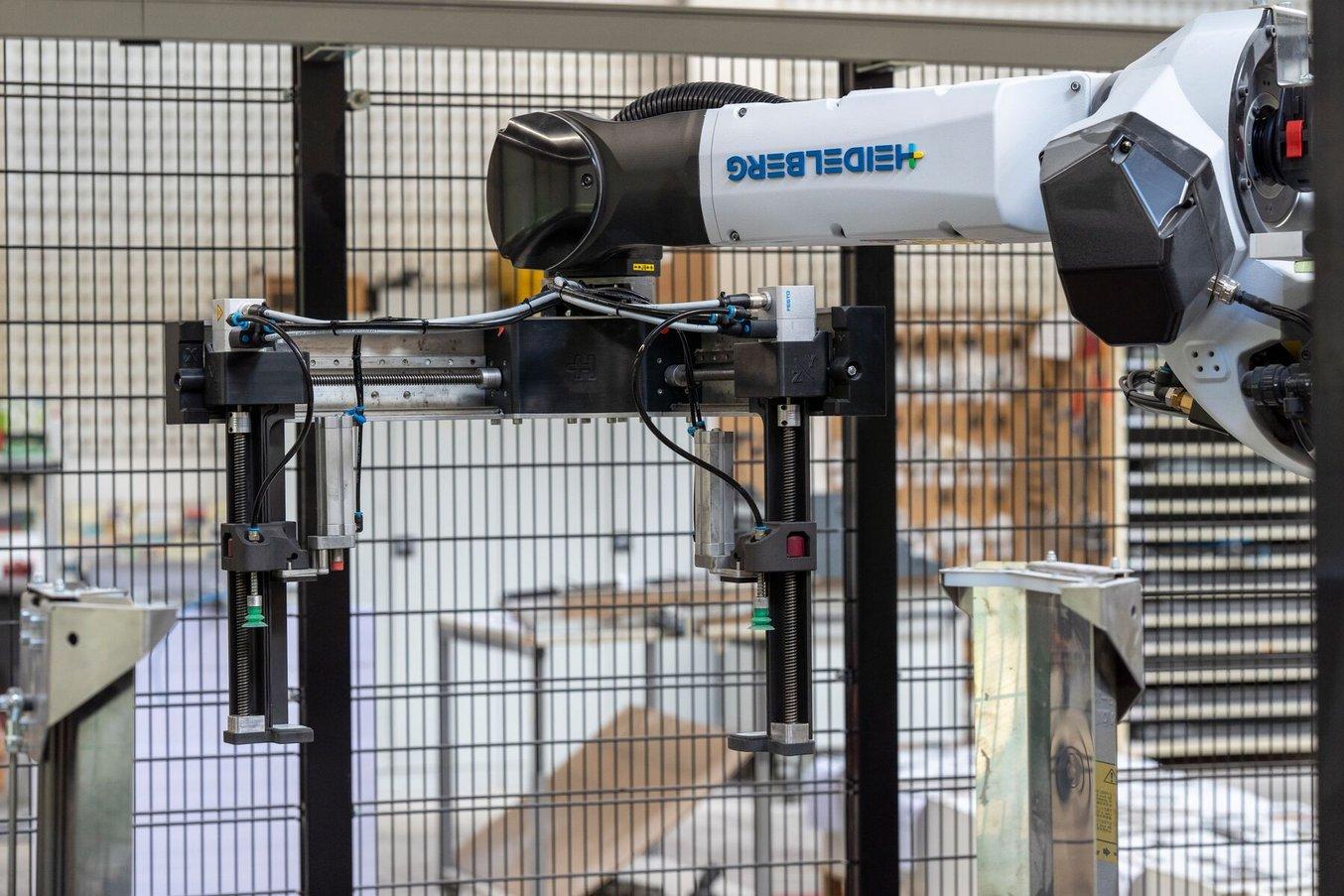
In der Robotik spielt das Gewicht eine essenzielle Rolle, da es die mechanische Belastung erhöht, die auf die Teile einwirkt.
Viele dieser komplizierten Formen ließen sich mit traditionellen Verfahren wie der Zerspanung nicht kosteneffizient oder gar überhaupt nicht umsetzen. Einige Teile würden aus verschiedenen Baugruppen und Einzelkomponenten bestehen, welche mühsam montiert, ausgerichtet und nachgearbeitet werden müssten. Sie wären deutlich schwerer und würden die Packungsdichte des Systems noch weiter erhöhen.
„Sollte es möglich sein, verschiedene Teile konventionell zu fertigen, wäre der Aufwand im Gegensatz zum 3D-Druck enorm hoch. Der SLS-Druck erlaubt uns, ziemlich komplexe Formen abzubilden. Dadurch vereinfachen wir so manche Komponenten und Baugruppen, da wir sehr amorphe Geometrien entwickeln und drucken können. Das ist für uns hier perfekt.“
Joachim Krumma, Geschäftsführung, CTS-3 GmbH
Einige Teile sind weniger komplex, erfordern aber dennoch eine hohe Genauigkeit oder Präzision. Das umfasst zum Beispiel flexible Teile, die Querkontamination verhindern, scharfe Kanten abdecken, Sensoren schützen oder Verschleiß vorbeugen.
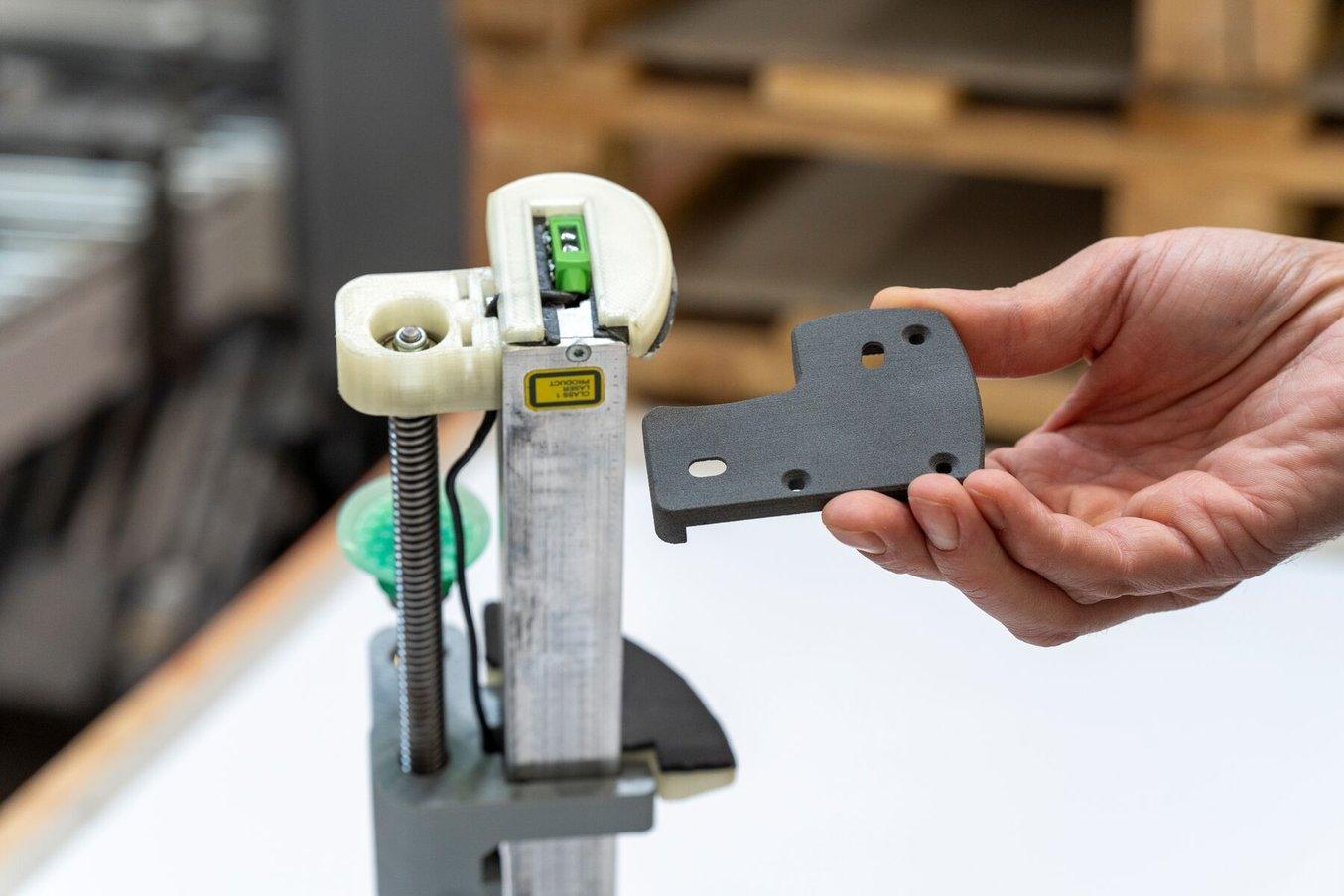
Ein flexibles Bauteil, das aus TPU 90A Powder 3D-gedruckt wurde und Sensoren und anderes End-of-Arm-Tooling schützt.
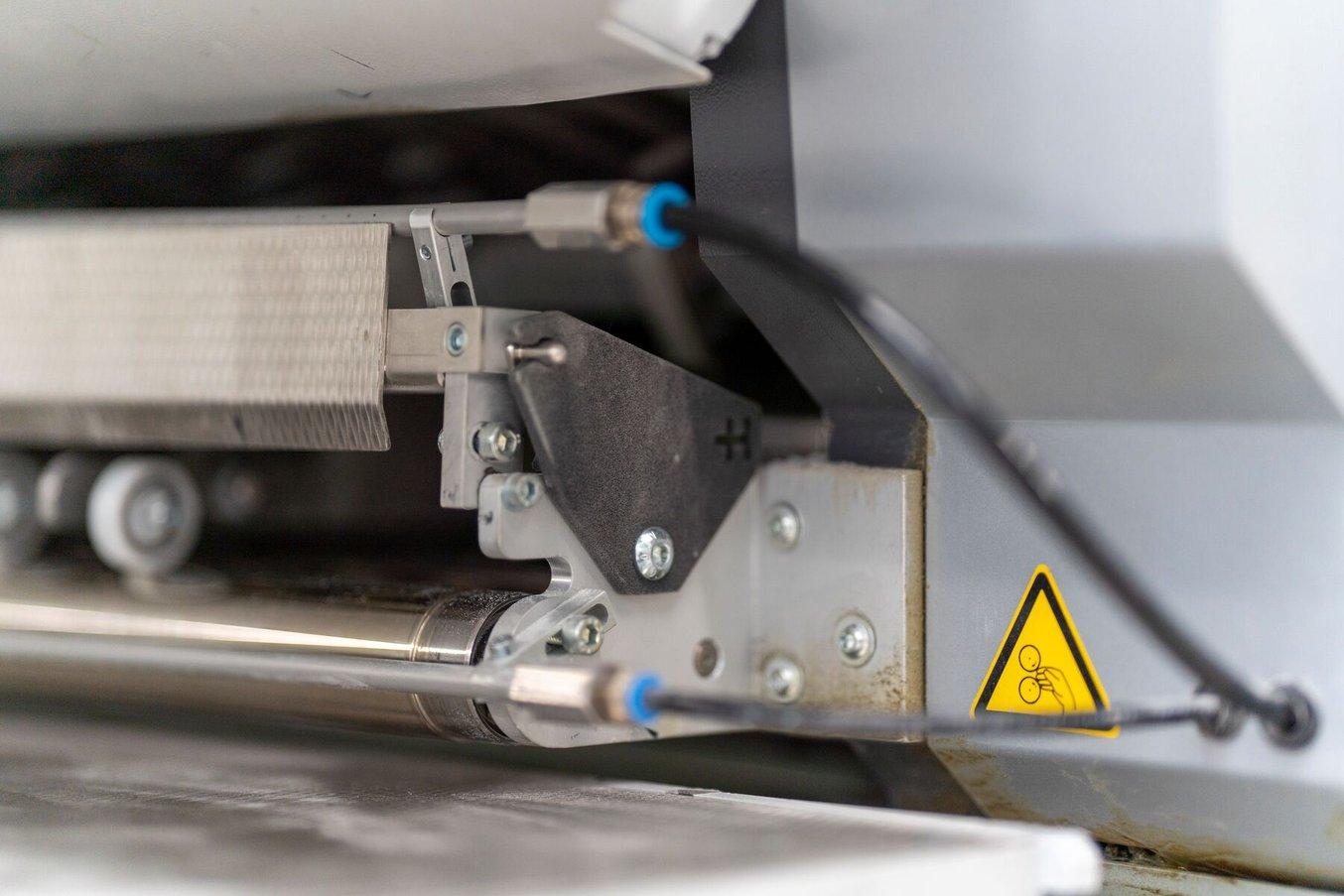
Flexible Komponenten eignen sich ideal für Schnappverbindungen. Indem Sie scharfe Kanten abdecken, dienen sie auch zum Schutz des Bedienpersonals.
„Ganz aktuell wurde in unserem Roboter ein 3D-gedrucktes Teil verbaut, das einen Kabelbruch verhindern kann und dadurch die Langlebigkeit erhöht. So können wir gewährleisten, dass wir es nicht irgendwann mit einem Tag Ausfall zu tun haben, an dem die Kabelbäume ausgewechselt werden müssen“, erklärt Harig.
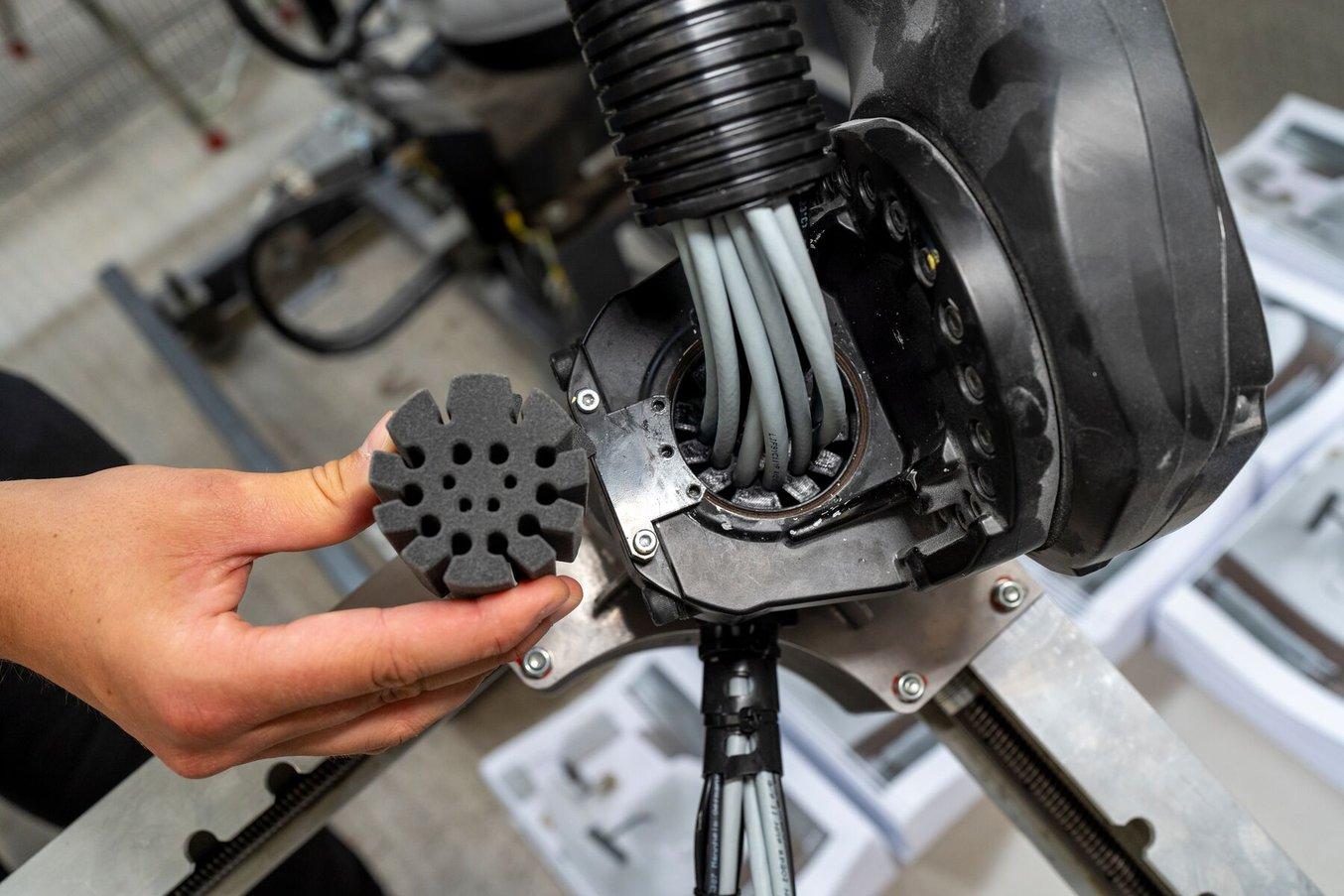
Diese biegsame Kabelführung, die auf dem SLS-3D-Drucker der Fuse-Serie produziert wurde, lässt ein komplexes Design zu und bietet eine langfristig haltbare Lösung, um Kabel vor Verschleiß zu bewahren.
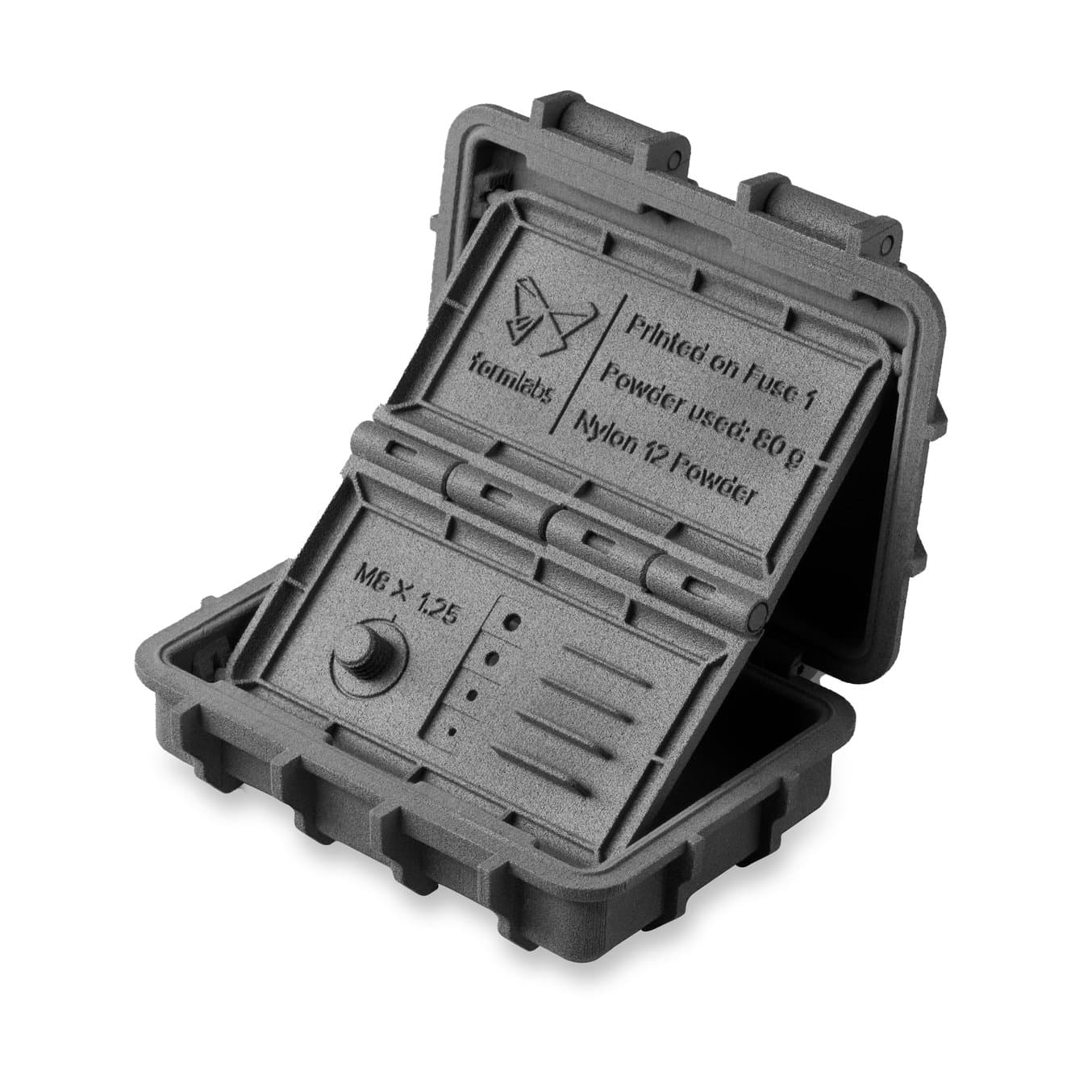
Kostenlosen Probedruck anfordern
Sehen und fühlen Sie die Qualität von Formlabs aus erster Hand. Wir senden Ihnen einen kostenlosen Probedruck aus dem Fuse 1+ 30W an Ihren Arbeitsplatz.
Ersatzteile, die an die Stelle von Stahlteilen treten
Ausfallzeiten von Maschinen zu minimieren, ist für einen Druckereibetrieb essenziell – denn jede Verzögerung kann verpasste Fristen zur Folge haben und die Druckware obsolet werden lassen. Dank seines weitläufigen Kundenservice-Netzwerks kann HEIDELBERG 95 % der Ersatzteile innerhalb von 24 Stunden an jeden beliebigen Standort auf der Welt versenden. Dennoch war das Team neugierig, ob auf Abruf produzierte, 3D-gedruckte Ersatzteile nicht genau die passende Lösung für veraltete Bauteile bieten könnten.
In einer der älteren Falzmaschinen von Meinders & Elstermann installierte Krumma 3D-gedruckte Bauteile, die eine Reihe ursprünglich aus Stahl gefräster Komponenten ersetzten, beispielsweise Verbindungsteile für Metallrollen, die bis zu 13 kg wiegen. Die Teile befinden sich im Inneren der Maschine, wo sie einer äußert schmutzigen und öligen Umgebung ausgesetzt sind. Sie stehen unter schwerer mechanischer und physischer Belastung über einen längeren Nutzungszeitraum hinweg, zum Beispiel im Fall von Notfallstopps, bei denen das gesamte Maschinensystem im Bruchteil einer Sekunde zum Stillstand kommt.
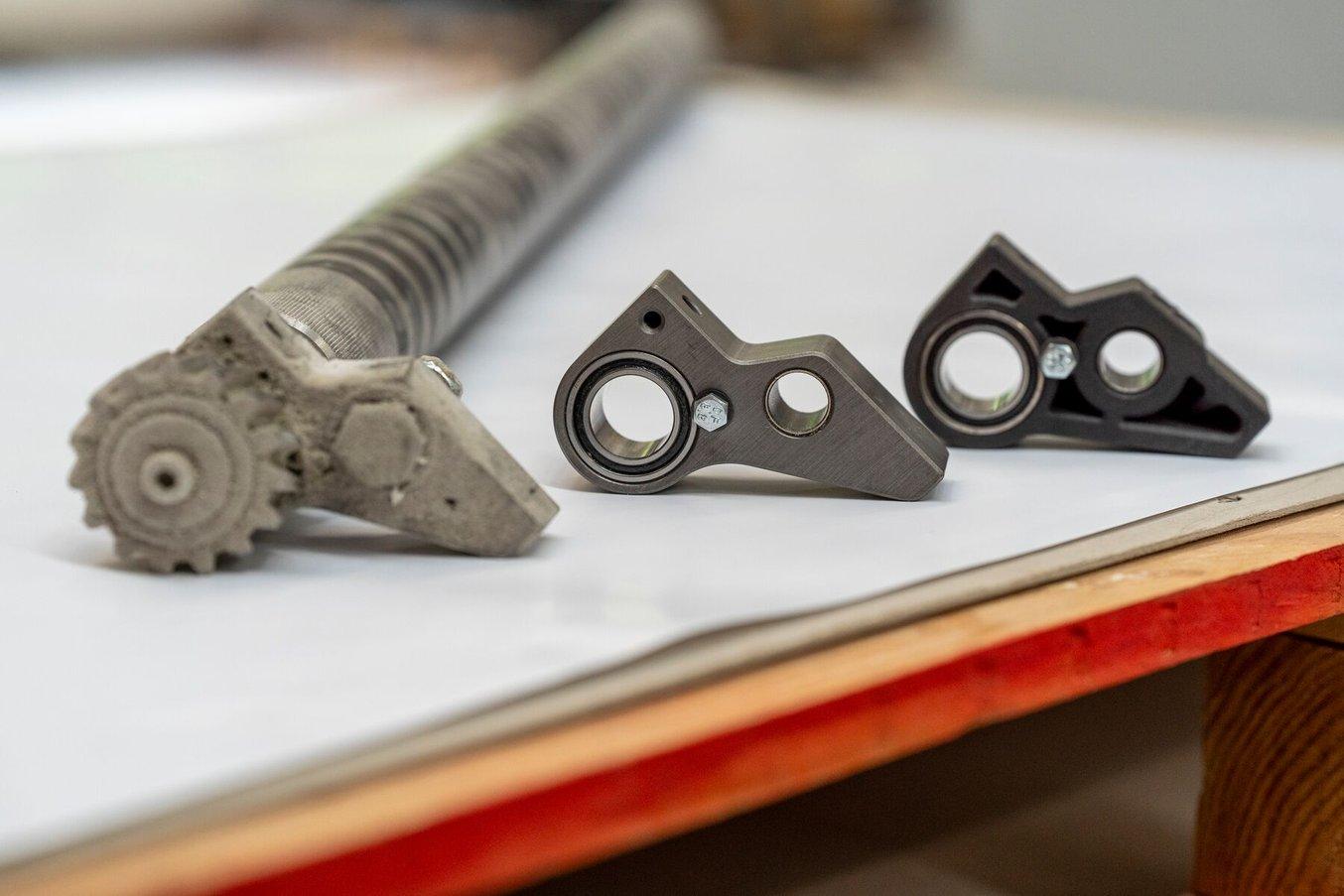
Die 3D-gedruckten Ersatzteile werden mit Lagern und reibungsmindernden Metallkomponenten verbaut.
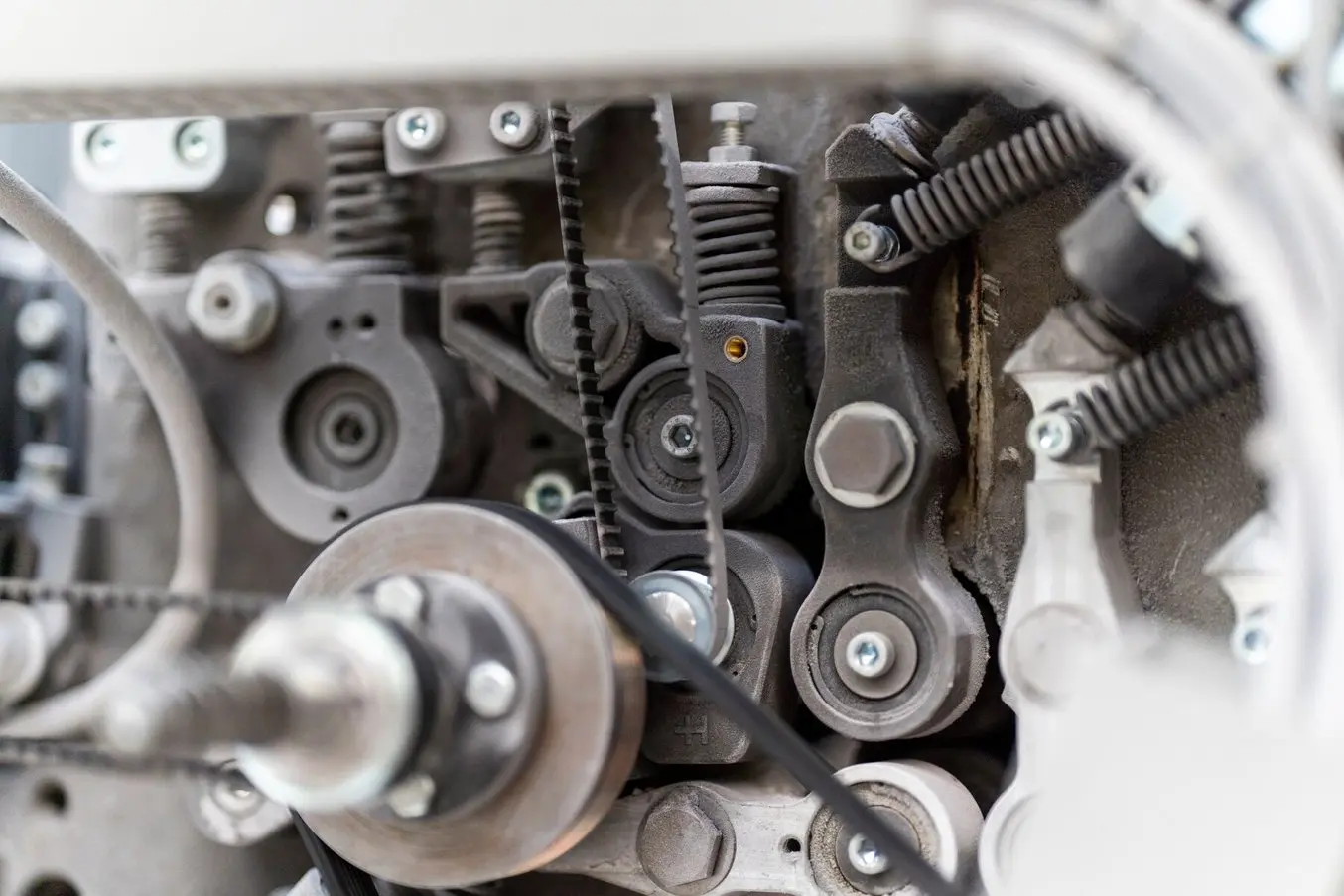
Die Verbindungsteile halten Metallrollen, die in hoher Geschwindigkeit rotieren und jeweils bis zu 13 kg wiegen.
„Sie müssen andauernder Beanspruchung standhalten, wie etwa zwei Schichten, fünf Tage die Woche, bei extrem hoher Last. Derzeit haben wir Teile installiert, die schon seit mehr als 2,5 Jahren in den Maschinen verbaut sind. Das war bei der ursprünglichen Entwicklungsphase nicht geplant. Wir haben die Teile jedoch ständig beobachtet, und es wurde sehr bald klar, dass sie der Dauerbelastung standhalten würden.“
Joachim Krumma, Geschäftsführung, CTS-3 GmbH
„Ich muss ganz deutlich sagen, dass die sehr langlebig sind. Ich hatte das auch nicht geglaubt, aber wir haben noch keine Teile bei uns in den Falzmaschinen auswechseln müssen“, fügt Harig hinzu.
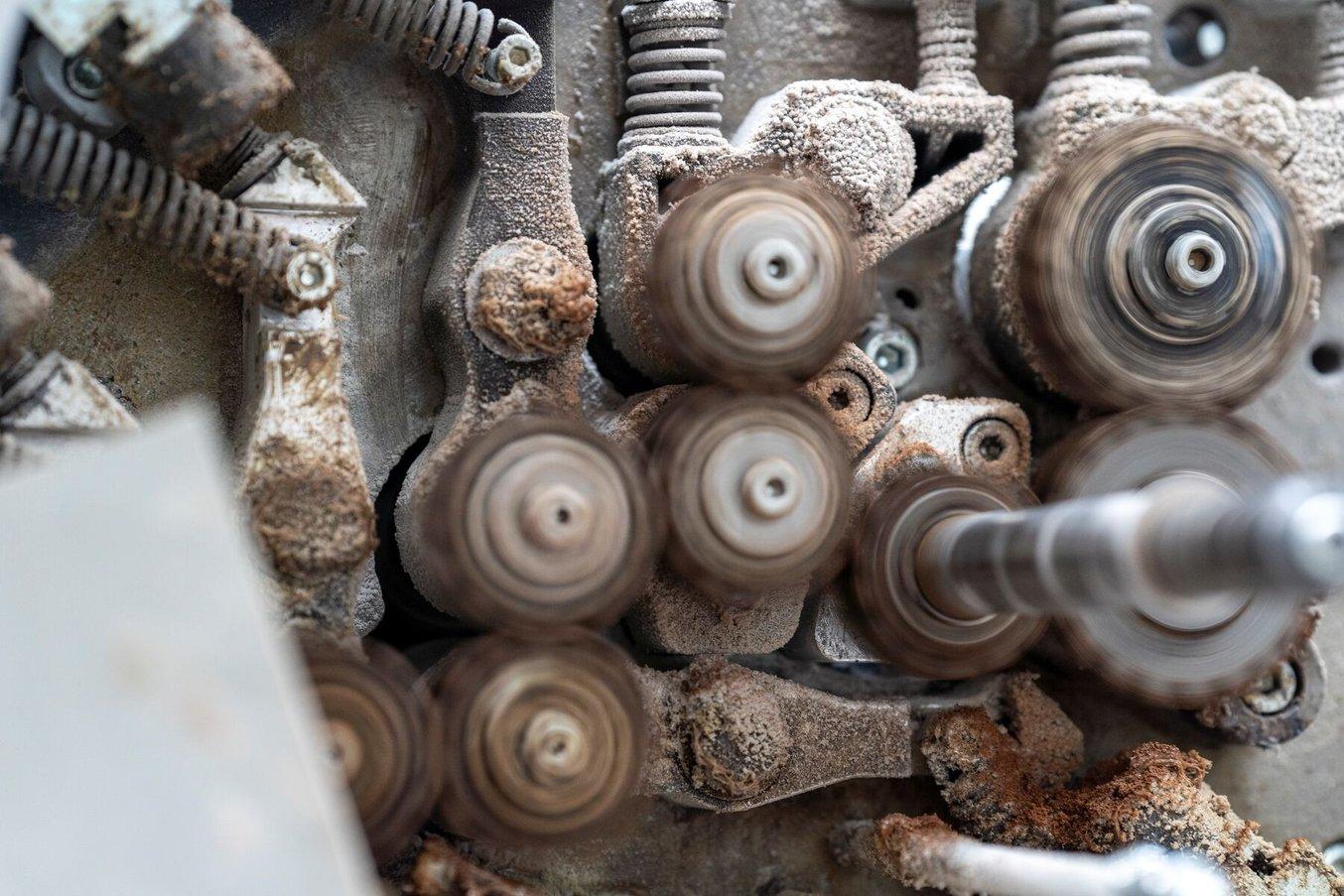
Einige der 3D-gedruckten Ersatzteile sind seit 2,5 Jahren in der Falzmaschine installiert und sind über zwei Schichten, fünf Tage die Woche im Einsatz. Dabei sind sie einer äußerst schmutzigen und öligen Umgebung ausgesetzt.
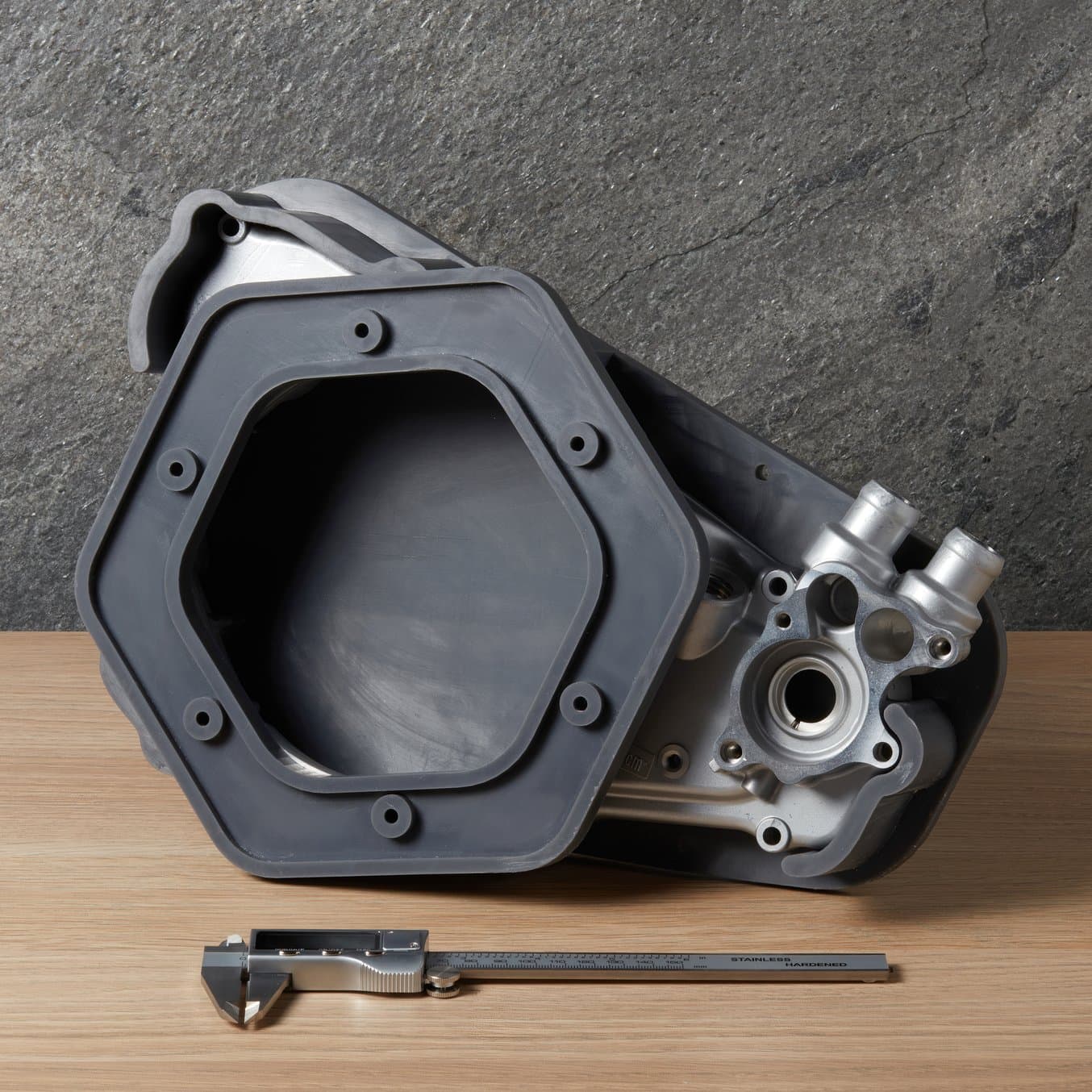
Wie Sie Halterungen, Vorrichtungen und sonstige Fertigungshilfen betriebsintern 3D-drucken
Dieses Whitepaper erläutert die Prinzipien hinter der Produktion effektiver Halterungen, Vorrichtungen und anderer Fertigungshilfsmittel im eigenen Betrieb.
Druckereien wettbewerbsfähig halten
„Viele Kunden setzen eher auf Online- als auf Printprodukte. Daher sind viele Aufträge nicht mehr da, die man vorher hatte. Die Auflagen werden geringer, und sie müssen auch schneller verfügbar sein. Da kann man wirklich nur noch mit neuen Maschinen gegensteuern. Es wird in Zukunft weniger Druckereien geben. Und diejenigen, die übrigbleiben, müssen zusehen, dass sie sich für die Zukunft gut aufstellen“, meint Harig.
Dank 3D-Druck und der Zusammenarbeit mit Fachleuten wie Krumma und CTS-3 ist HEIDELBERG in der Lage, die Produktentwicklung zu beschleunigen, was es seinen Endkunden wiederum möglich macht, trotz des rasanten Marktwandels wettbewerbsfähig zu bleiben.
„Hätten wir keinen Zugang zu dieser Technologie, besonders zum SLS-3D-Druck mit der Fuse-Serie, dann wären die Entwicklungsprozesse enorm in die Länge gezogen. Die Maschinen erlauben uns, in kürzester Zeit sehr große Entwicklungsschritte zu leisten. Wir können Teile über Nacht produzieren und am nächsten Tag beim Kunden testen, um sie dann zu verwerfen oder weiterzuentwickeln. Ohne diesen Zugang wäre der Entwicklungsprozess nahezu wie bei der konventionellen Fertigung.“
Joachim Krumma, Geschäftsführung, CTS-3 GmbH
Krumma zieht Resümee: „Der 3D-Druck macht jedes Jahr enorme Sprünge. Man sieht es: Wer stehen bleibt, bleibt zurück. Wir sind jetzt ziemlich schnell an den Punkt gelangt, wo sich das 3D-Druckverfahren gegenüber der konventionellen Fertigung durchaus gerechnet hat. Es ist spannend, zu beobachten, was kommt und noch kommen wird. Und wir freuen uns darauf.“