Amerikas beliebtester Zeitvertreib auf dem Weg in die Zukunft: Innovationen bei Louisville Slugger
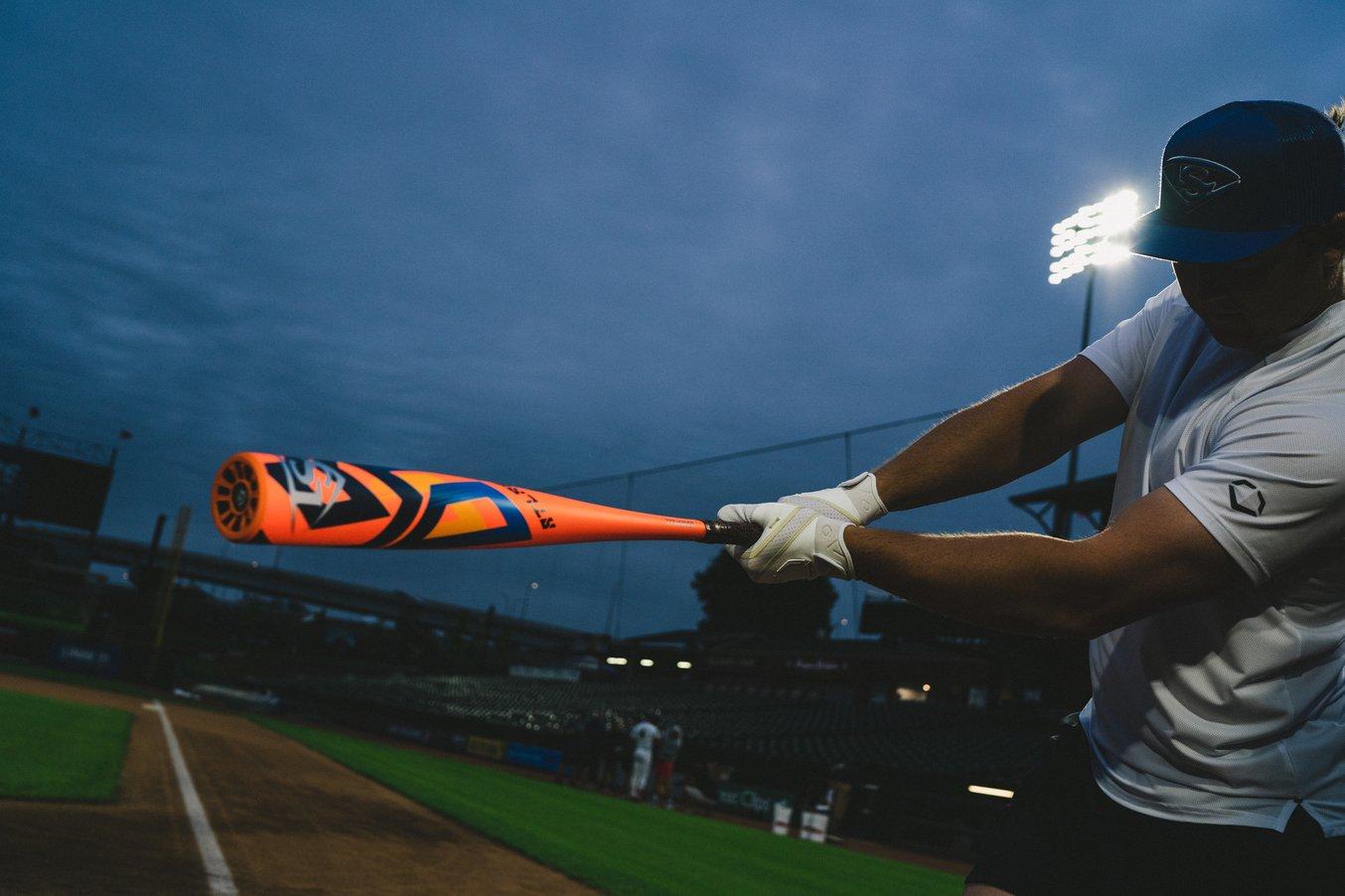
Der neue BBCOR Atlas ist ein Paradebeispiel für die Premiumprodukte, die im Innovationszentrum von Louisville Slugger mit fortschrittlichen Innovationstechnologien entwickelt werden.
Im Innovationszentrum von Louisville Slugger in Roseville, Kalifornien, treffen der Traditionssport und der charakteristische Zukunftsdrang der Vereinigten Staaten von Amerika aufeinander. Seit 1884 stellt Louisville Slugger Baseballschläger und Ausrüstung für den Verband Major League Baseball her, aber auch für Teams in College-, High-School- und Jugendligen. Im Slugger-Innovationszentrum setzt Produktdesigner John Steel für das Design und die Fertigung von Baseballschlägern aus Aluminium und Verbundwerkstoffen eine Kombination traditioneller und moderner Hilfsmittel ein. „Wer nicht 3D-druckt, der wird nicht mithalten können“, meint Steel. Er nutzt den Stereolithografie-3D-Drucker (SLA) Form 3 einerseits für die Herstellung visueller Prototypen und andererseits für Fertigungshilfsmittel zur Entwicklung der Schläger aus Aluminium und Verbundwerkstoffen, die von Jugend- und College-Teams weltweit geschwungen werden.
Innovation bei Slugger
Spieler*innen jagen ständig nach einem Vorsprung – dem gewissen Etwas, mit dem sie schneller ausholen und fester aufschlagen können. In der Jugendliga kann es bereits einen Vorteil bedeuten, einen richtig gewichteten Schläger zu finden, mit dem man einen soliden Kontakt erzielen und einen festen Griff halten kann, während man das Spiel erlernt. Auf College-Niveau kann ein um ein paar Zentimeter breiterer Stand den Unterschied machen. Das Streben nach Verbesserung, unabhängig vom Niveau, wird von Louisville Slugger sowohl gefördert als auch verkörpert. Durch Einrichtungen wie das Innovationszentrum, das sich auf die Verbesserung des Equipments konzentriert, und Slugger Science, das für verbesserte sportliche Analyse zuständig ist, hält Louisville Slugger den beliebtesten Zeitvertreib Amerikas nicht nur zeitgemäß, sondern auch zukunftsorientiert.
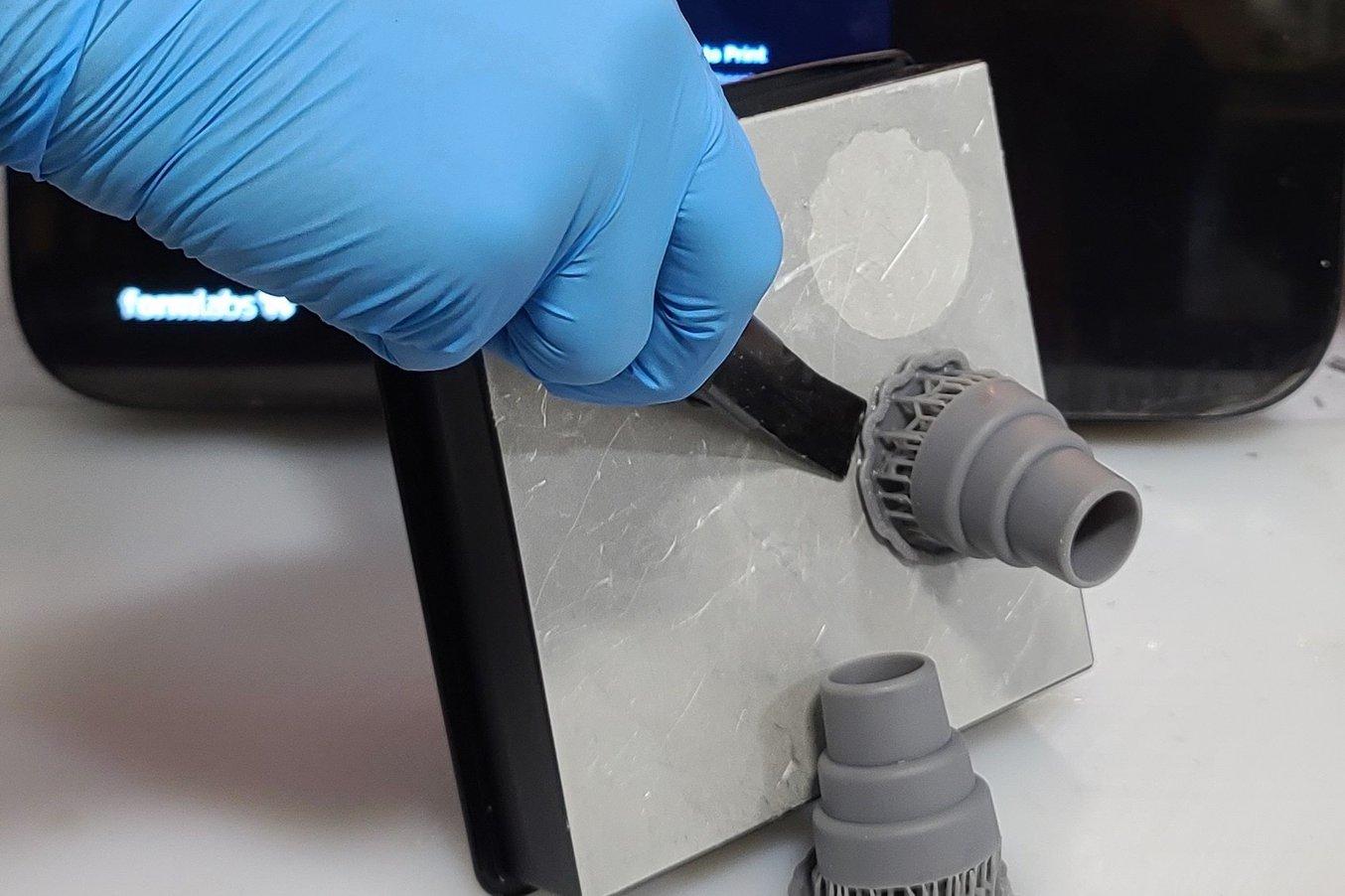
Steel entfernt einen Prototyp der Komponente Pyramid Grip, der als Positivform dienen wird. Die Form wird dann mit einem anderen Material wie Silikon oder Urethan gegossen.
Entwicklungsgeschwindigkeit
Beim Innovationszentrum Louisville Slugger in Roseville hat das Entwicklungs- und Designteam Zugang zu jeglichen Hilfsmitteln, die es braucht, um die bestmöglichen Produkte zu erschaffen. Steel hatte seine erste Arbeitsstelle in einer Eisen- und Stahlgießerei, wo er traditionelle Fertigungstechniken wie Holzmodellierung und CNC-Zerspanung kennenlernte und entdeckte, wie großformatiger, industrieller SLA- und SLS-3D-Druck mit konventionellen Holzmodellierungstechniken kombiniert werden kann. Obwohl der 3D-Druck durch Outsourcing abgewickelt wurde, bot ihm diese Erfahrung eine umfassende Einführung in die Verschmelzung traditioneller und moderner Verfahren.
Später arbeitete Steel bei einem Startup für Produktdesign, in dem er zwei 3D-Drucker des Typs Form 1+ nutzte, um in kurzer Zeit zu iterieren. „Wir brachten Tag und Nacht am laufenden Band Prototypen heraus. Ich hatte damals noch eigene Wasch- und Nachhärtegeräte konstruiert“, erinnert sich Steel. Bei Louisville Slugger kann Steel nun abermals Tradition und Moderne vereinen, durch den Einsatz von Desktop-3D-Druck sowie Drehmaschinen, einer CNC-Metallwerkstatt, einer Verbundstoffwerkstatt und mehr.
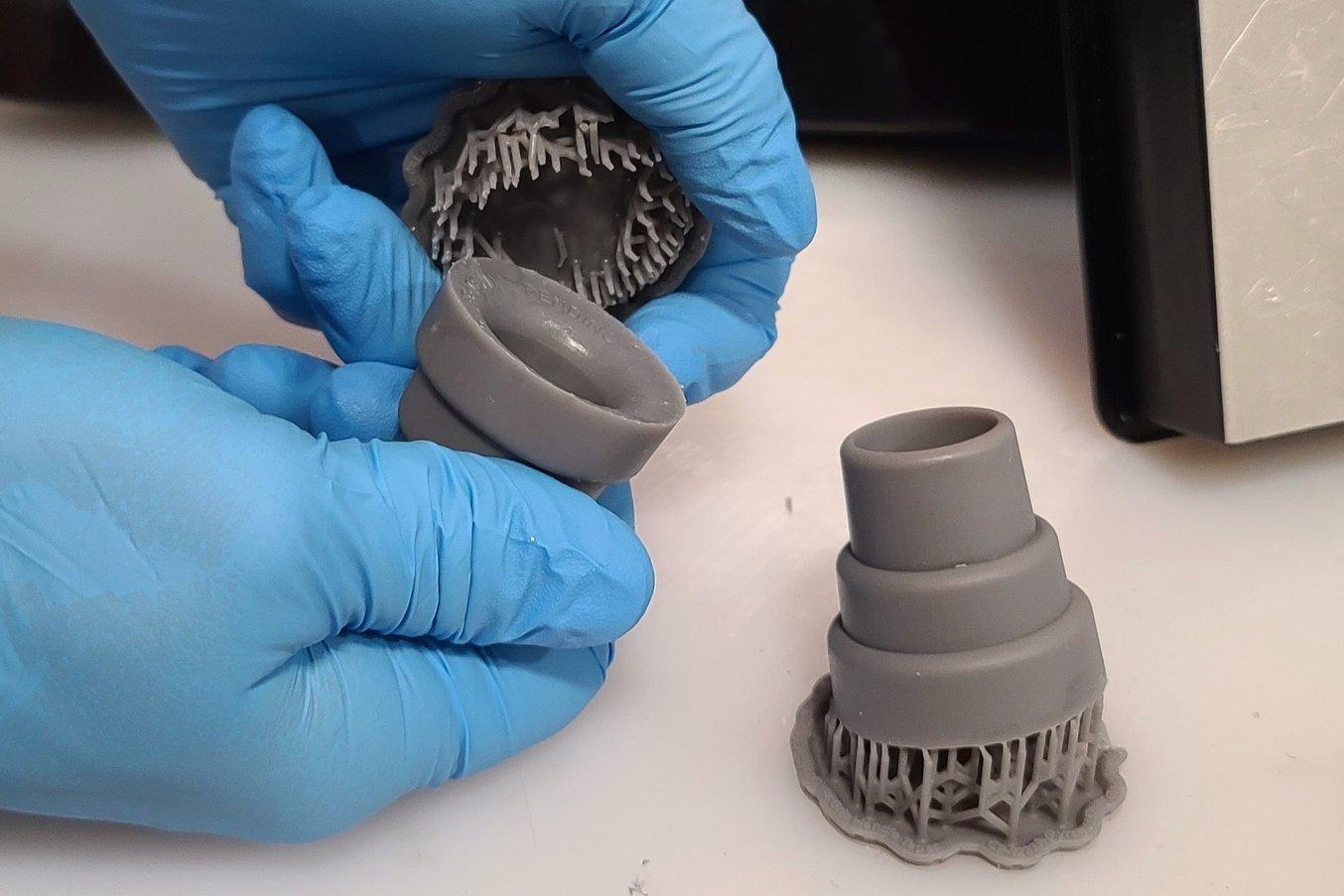
Die leicht zu bearbeitenden Stützstrukturen machen die Nachbearbeitung schneller, leichter und ordentlicher.
„Wir können Prototypen in kürzester Zeit produzieren und somit schnell iterieren und testen. Wir benutzen den Drucker jede Woche, und wenn wir an einem neuen Design arbeiten, kreieren wir jeden Tag neue Iterationen“, so Steel. Die kurze Durchlaufzeit der Iterationen erlaubt es dem Team von Slugger, regelmäßig neue Produkte zu veröffentlichen und mit der Nachfrage an Schlägern für alle erdenklichen Spielerniveaus mitzuhalten. „Der 3D-Druck ist ein tolles Hilfsmittel, um die Markteintrittszeit zu verringern. Man kann ihn vom Prototyping bis zur Fehlerbehebung für alles Mögliche nutzen. Von den ursprünglichen Designs werden Prototypen erstellt und es werden Probleme mit der letztendlichen Fertigung gelöst“, berichtet Steel. Auf dem Markt herrscht ein ständiger Wettbewerb, selbst für so geschichtsträchtige Marken wie Slugger. Steel und das Innovationsteam entwickeln laufend Iterationen und neue Ideen, und der Form 3 unterstützt sie dabei, diese Ideen noch schneller in die nächste Phase zu überführen.
„Wenn ich eine Idee habe, erstelle ich ein Design, sende es in 30 Minuten an den Drucker und bringe es zum nächsten Meeting mit. 3D-gedruckte visuelle Hilfen sind ihr Gewicht in Gold wert“, so Steel. Der 3D-Druck verbessert das Verständnis des Produktentwicklungsprozesses im Team und kann Fehlkommunikation verhindern. Die Kohäsion innerhalb des Teams macht es Steel und anderen Designern möglich, einen effizienten Workflow und eine hohe Produktivität beizubehalten. „Bei der Betrachtung digitaler 3D-Modelle fehlt einem häufig ein Maßstab. Der 3D-Druck von Teilen hilft dabei, einen Größenbezug zu liefern, und ermöglicht es, die Ergonomie und die Passung mit bestehenden Produkten zu testen.“
Größere Kontrolle über den Prozess
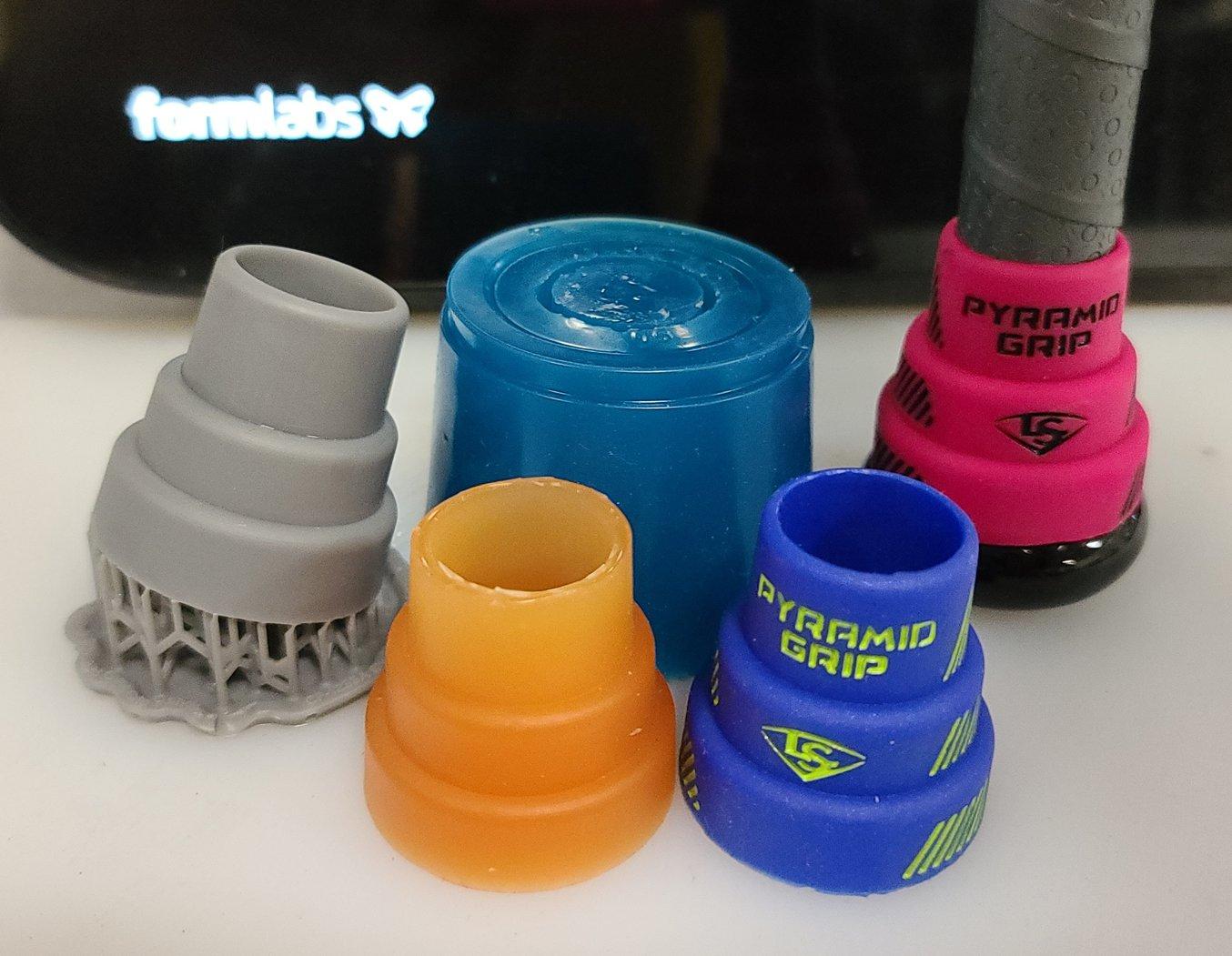
Der 3D-Druck kann iterative Prozesse beschleunigen und dabei helfen, neue Innovationen vom Konzeptentwurf (hellgraues 3D-gedrucktes Teil, ganz links) bis hin zum endgültigen, konventionell gefertigten Teil zu entwickeln (pinkes Teil, ganz rechts).
Zusätzlich zu seiner elementaren Rolle bei der Prototypenfertigung kommt der Form 3 bei Steel auch noch für andere Anwendungen zum Einsatz, wie für die Herstellung von Silikonformen und anderen Fertigungshilfsmitteln. Die vielfältige Materialbibliothek eröffnet eine große Bandbreite von Arbeitsabläufen und erlaubt es Steel, größere Kontrolle über verschiedene Prozesse zu behalten. „Mit dem Form 3 können wir die breite Palette von Materialien auch für andere Verfahren ausnutzen, wie etwa die Fertigung von Positivformen für den Guss aus Urethan, Silikon oder Epoxidharz“, erklärt Steel. Solche Formen werden zur Kreation letzter Prototypen eingesetzt, die bereits alle endgültigen Materialtypen wie Urethan oder Epoxidharz enthalten, wie sie auch in den finalen, konventionellen Fertigungsprozessen zum Einsatz kommen.
Zuvor musste das Team Gusswerkzeug aus Aluminium beschaffen, wenn es Silikonteile fertigen wollte. Jetzt kann die Positivform einfach 3D-gedruckt werden, um diese anschließend mit Silikon zu umgießen, die Silikonform zu zerschneiden und das entstandene Negativ zur Fertigung von anderen Teilen zu verwenden, wie etwa funktionalen Prototypen. „SLA hat eine sehr scharfe Maßgenauigkeit und hält enge Toleranzen ein. Das liefert uns nicht nur Teile nach unseren Anforderungen, sondern macht auch einen Großteil der Nachbearbeitung von Positivformen überflüssig. Für Gießverfahren benötigt man Positivformen mit einer möglichst glatten Oberflächenbeschaffenheit, um das Entfernen von Teilen aus der Form zu erleichtern. Eine gewisse Textur ist in Ordnung, aber die Fissuren, die durch den Schichtaufbau entstehen, machen die Sache schwierig – und bei den Form-Druckern ist die Qualität der Schichten niemals ein Problem. Außerdem ist die Nachbearbeitung dieser Materialien extrem einfach“, erzählt Steel.
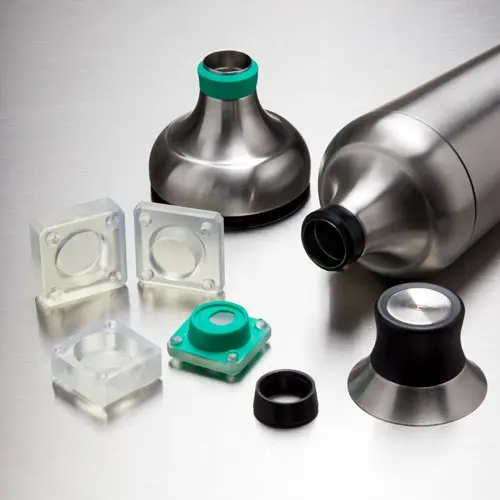
Silikonformenbau für das Produktdesign
Laden Sie diesen Bericht mit Fallstudien von OXO, Tinta Crayons und Dame Products herunter, um von drei verschiedenen Umsetzungen des Silikonformenbaus in Produktdesign und Fertigung zu erfahren, einschließlich Umspritzung und Insert-Molding.
In vielen Fertigungsprozessen ist Outsourcing ein gängiges und zumeist notwendiges Übel. Doch wenn gleich mehrere Schritte ausgelagert werden müssen, kann das zu Verzögerungen im Zeitplan und damit zur Stagnation der Produktentwicklung führen. Kann auch nur ein weiterer Aspekt des Prozesses selbst umgesetzt werden, können Designteams größere Kontrolle behalten. Beim Beispiel des Silikongusses kann die Iteration der Positivform und die Durchführung des Silikongussprozesses Designfehler aufzeigen, die andernfalls erst nach wochenlanger Wartezeit und Testphasen entdeckt worden wären, wenn man sich auf einen externen Dienstleister stützte.
„3D-Drucker sind die einfachste Technologie, um Dinge schnell herzustellen – man erstellt einen Entwurf und fertigt das Teil selbst, statt es an einen Fachmann weitergeben zu müssen und auf die Lieferung zu warten, bevor man testen kann“, erklärt Steel.
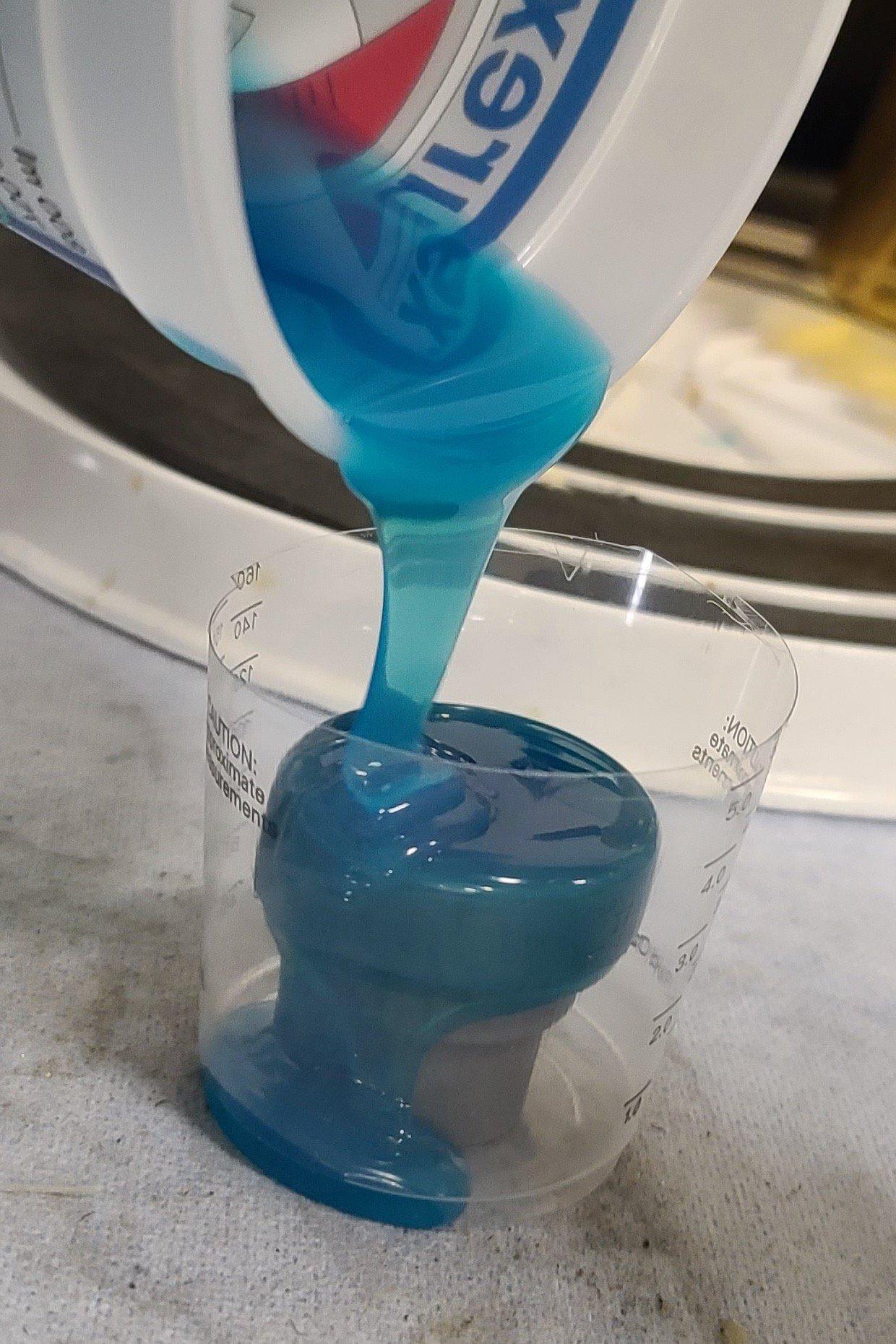
Mithilfe einer 3D-gedruckten Urform gießt Steel Silikon, um Werkzeug für den Prototyp des Pyramid Grip herzustellen.
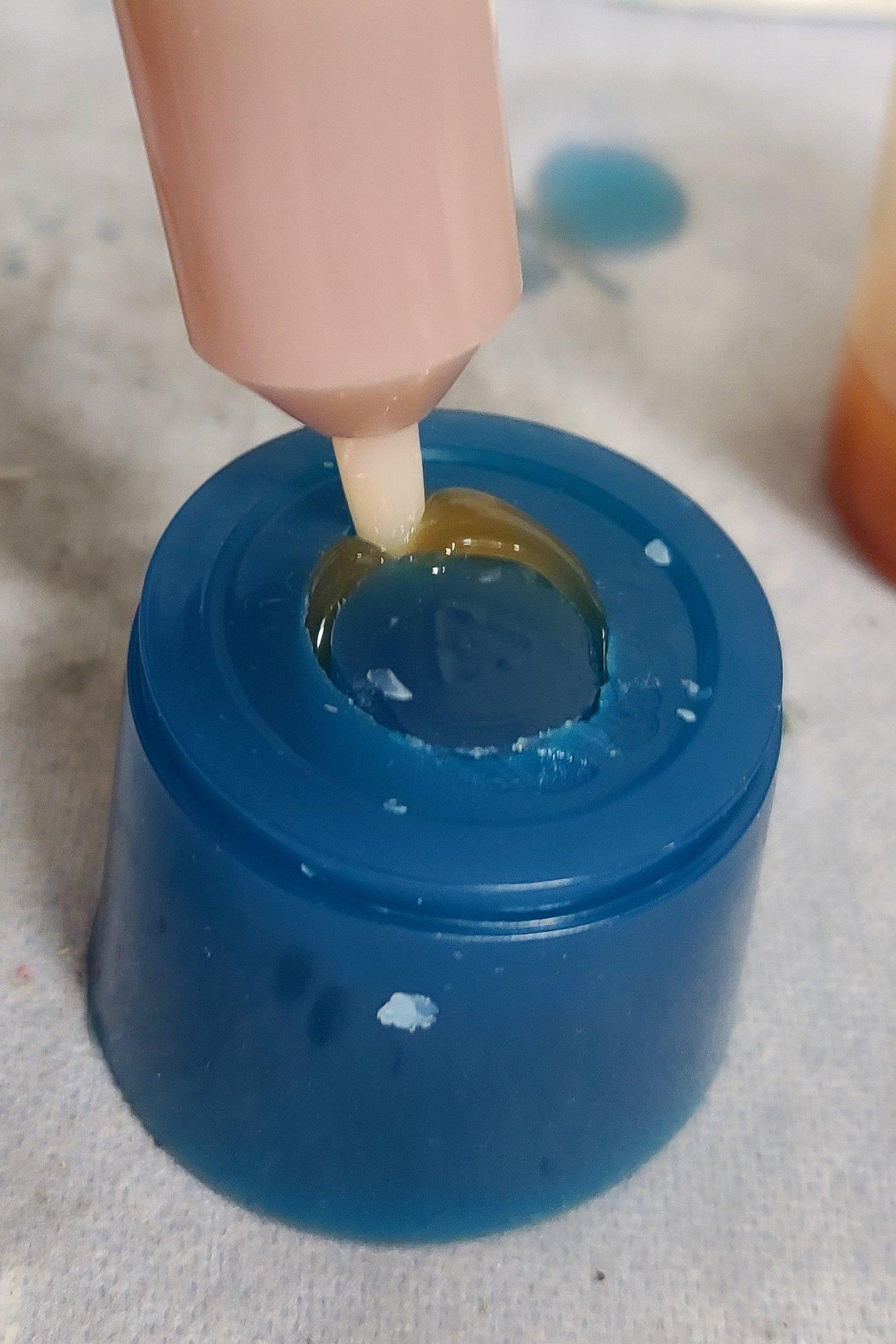
Nachdem die Silikonform gefertigt wurde, kann Steel ein anderes Material wie Urethan oder Epoxidharz einspritzen, um den fertigen Prototyp zu erstellen.
Immer am Ball
In Zukunft möchte Steel die Einsatzmöglichkeiten des 3D-Drucks noch stärker ausweiten, auch in der Fertigung. „Die Herstellung von Werkzeug mit dem Drucker kann noch lohnenswerter sein als die Herstellung von Teilen“, meint er. Zwar benutzt Slugger schon jetzt 3D-gedrucktes Werkzeug wie die Positivformen für den Silikonguss, doch dank des Problemlösungspotenzials des 3D-Drucks stehen noch viele weitere Einsatzbereiche offen. „Mit hochwertiger Ausrüstung macht der Sport größeren Spaß, und genau darum geht es uns im Innovationszentrum“, so Steel. „Mithilfe von Technologien wie den 3D-Druckern wollen wir uns weiter verbessern, und wir halten ständig Ausschau nach neuen Chancen.“"