Kundenindividuelle Fertigung: Mit 3D-Druck Herausforderungen bewältigen und skalieren
In der kundenindividuellen Fertigung wird eine Ware basierend auf den einmaligen Spezifikationen des Kunden entworfen, entwickelt und produziert. Dazu zählen besondere Kundenwünsche, Einzelanfertigungen, Kleinserien aber auch die serielle Maßanfertigung.
Moderne Fertigungstheorie, Werkzeuge und bewährte Praktiken konzentrieren sich darauf, wie man Tausende oder Millionen identischer Teile oder Produkte zu niedrigen Stückkosten herstellt. Design- und Fertigungspraktiken sind für die Großserienfertigung optimiert und ermöglichen es Unternehmen, Waren an die Verbraucher zu akzeptablen Preisen zu liefern. Hersteller arbeiten mit kleinen Gewinnmargen, die sich über einen kompletten Fertigungslauf zu beträchtlichen Erträgen summieren.
Einzelstücke oder Kleinserien wie maßgefertigter Schmuck, Spezialelektronik, Medizinprodukte oder dentale Anwendungen, die auf den Körper einer Person zugeschnitten werden, stellen eine einzigartige Herausforderung dar, an die die Hersteller ihre Produktionsprozesse anpassen müssen.
Additive Fertigung, besser bekannt als „3D-Druck“, hat sich in den letzten Jahren dank Verbesserungen in Sachen Technologie und Materialien zunehmend als vollwertiges Herstellungsverfahren etabliert. 3D-Druck eignet sich hervorragend für die kundenindividuelle Fertigung, aufgrund seiner hohen Flexibilität, seiner werkzeuglosen Herstellungsprozesse und seiner Fähigkeit, schnell auf erhöhte Nachfrage zu reagieren.
Im Folgenden erfahren Sie mehr über die Herausforderungen der kundenindividuellen Fertigung und erhalten reale Beispiele, wie Branchen 3D-Druck zur individualisierten Produktion nutzen, von der Personalisierung im Gesundheitswesen zur seriellen Maßanfertigung von Konsumgütern.
Herausforderungen der kundenindividuellen Fertigung
Verglichen mit der Serienproduktion bringt die kundenindividuelle Fertigung ganz andere Herausforderungen mit sich, sowohl bezüglich des Geschäftsmodells als auch bei der Fertigungsstrategie.
Verfahren: Kundenindividuelle Fertigung vermeidet üblicherweise die Fertigungsverfahren großer Mengen, da komplexe Formen und aufwändige Werkzeugbestückung sich aufgrund der hohen Anschaffungskosten bei Einzelstücken und Kleinserien bis in den dreistelligen Bereich nicht rentieren. Stattdessen müssen sich Hersteller alternative Fertigungsverfahren ausgucken, die agiler sind und geringere Anschaffungskosten haben. Leider haben solche Fertigungsverfahren oft auch längere Zyklen und sind arbeitsintensiver, was sich wiederum in den Kosten pro Teil niederschlägt.
Effizienz: In jedem Produktionsprozess ist die Effizienz der Schlüssel zur Wirtschaftlichkeit. Doch der Weg zur Effizienz hängt von der Größe und dem Stil der Produktion ab. Bei der traditionellen Massenproduktion liegt der Schwerpunkt auf der Reduzierung der Zyklen durch strikte DFMA-Prozesse, Kostensenkung durch große Mengen und Verringerung der Arbeitszeit. Bei der kundenindividuellen Fertigung macht die Varianz im Design standardmäßige DFMA-Ansätze ineffektiv und Kostenkontrolle und Mengenvorteile lassen sich nur schwer umsetzen. Stattdessen konzentriert sich die kundenindividuelle Fertigung auf die Effizienz der Nachfrage: Waren werden erst bei der Bestellung angefertigt. Dem gegenüber verlässt sich die Massenproduktion auf einen Schätzwert der Nachfrage, auf Serienfertigung und auf Lagerung des Inventars.
Qualität: Artikel aus der Massenproduktion haben den Vorteil, sich mit der Zeit zu bewähren, von bekannten Toleranzen und von erprobter Leistungsfähigkeit. Abweichungen in der Produktqualität lassen sich anhand von Kontrollfaktoren wie Geschwindigkeit und Temperatur vermeiden. Das minimiert die Varianz. Etablierte Prüfsysteme der Massenproduktion nutzen vordefinierte Tests zur Verifikation und Aufrechterhaltung der Produktqualität anhand von Stichproben in festen oder zufälligen Zeitintervallen. Kundenindividuelle Fertigung mit Einzelstücken hat von Natur aus eine hohe Varianz, was die Ergebnisse betrifft. Das erhöht den Zeitaufwand und die Kosten der Validierung der entsprechenden Produktspezifikationen bezüglich Detailgenauigkeit und Abmessungen.
Kundenindividuelle Fertigung mit 3D-Druck
Hochpräzise additive Fertigungsverfahren wie die Stereolithografie (SLA) oder das selektive Lasersintern (SLS) eignen sich ideal für individualisierte Produktion, da sie viel Flexibilität bei minimalem Einrichtungsaufwand bieten und Teile mit vielfältigen Geometrien und aus unterschiedlichsten Materialien produzieren. So fällt die Anpassung an sich ändernde Bedürfnisse leicht. Additive Fertigung hilft oft dabei, Handarbeit und manuelle Arbeitsabläufe zu digitalisieren. Das verbessert die Qualität und verringert die Anzahl der Produktionsschritte sowie den Arbeitsaufwand, also unterm Strich die Durchlaufzeit und die Kosten.
Betrachten wir ein paar Praxisbeispiele aus Maschinenbau, Schmuckherstellung, Zahnmedizin und Konsumwarenfabrikation, um besser zu verstehen, wie sich die additive Fertigung in Personalisierungsabläufe einfügt.
Gussmodelle
Gussverfahren werden in verschiedenen Branchen genutzt, um komplexe Teile herzustellen, die mit anderen Verfahren schwierig oder unwirtschaftlich währen. SLA-3D-Druck ist eine geläufige Methode zur Fertigung von Modellen direkt aus CAD-Designs aufgrund der hohen Auflösung und der Abbildung filigraner Details.
In der Schmuckbranche ist der 3D-Druck Teil des Feingussverfahrens. Schmuckhersteller beginnen mit dem digitalen Design eines Schmuckstücks und 3D-drucken es dann aus gussfähigem Kunstharz, das in einer Einbettmasse platziert und dann in einem Ofen rückstandslos weggebrannt wird – wie ein herkömmliches Wachsmodell. Maßgefertigte Stücke können dann gegossen und fertiggestellt werden, mit denselben Arbeitsabläufen wie bei den traditionellen Prozessen.
Ähnliche Prozesse kommen in der Zahntechnik zum Einsatz für gießbare oder druckbare Kronen, Brücken und andere Restauration oder auch im Maschinenbau beim werkzeuglosen Feinguss oder Sandguss.
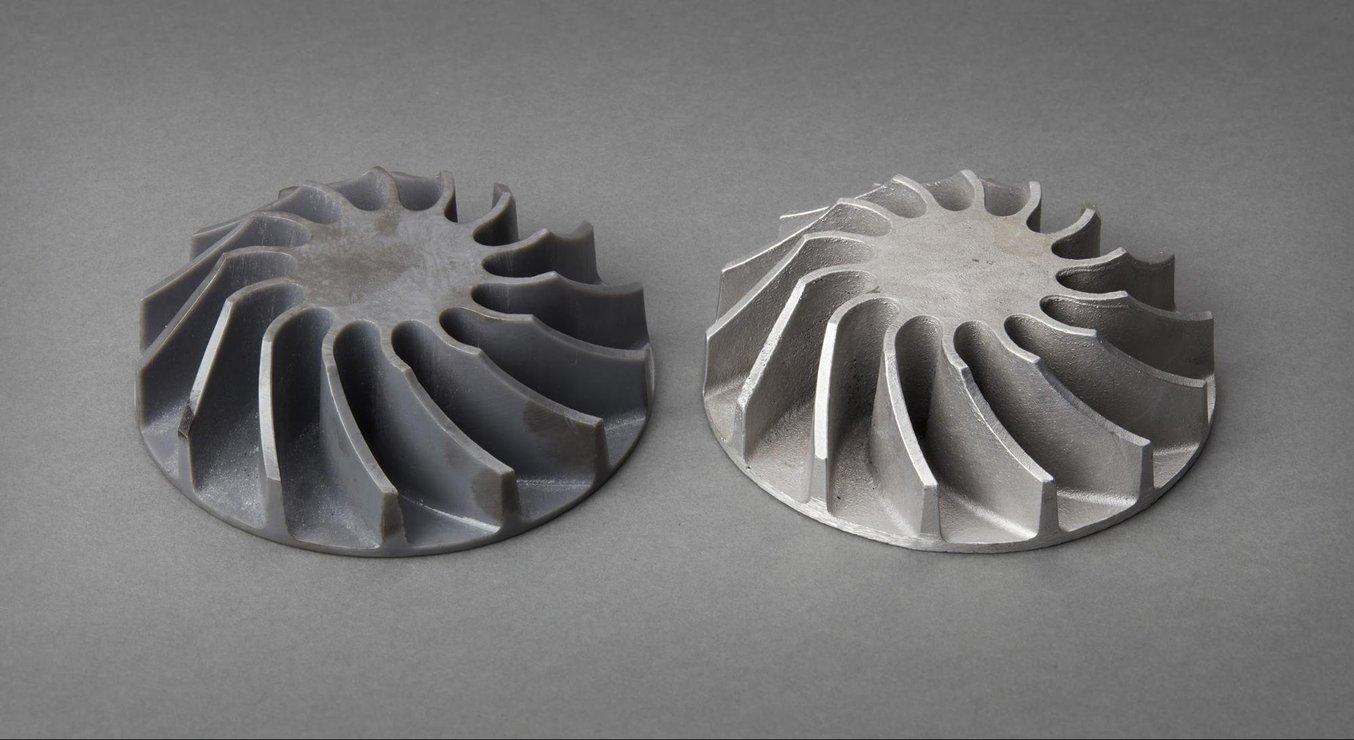
Ein 3D-gedrucktes Laufrad und dessen Guss aus Metall. Schauen Sie unser Webinar und erfahren Sie, wie Sie kostengünstige Modelle für den Fein- und Sandguss anfertigen.
Mit 3D-Druck werden auch die Urformen für flexible Latexformen oder RTV-Silikonformen hergestellt. In der Schmuckherstellung kommen solch kostengünstige Formen zum Einsatz bei der Herstellung begrenzter Stückzahlen (25 bis 100) von Wachsmodellen für den Feinguss.
Formenbau
Einer der ersten Anwendungsfälle mit großen Stückzahlen beim 3D-Druck sind maßgefertigte transparente Aligner und Retainer in der Zahntechnik. Bei diesem Prozess scannt ein Kieferorthopäde das Gebiss des Patienten mit einem Intraoralscanner, plant die Behandlung in einer CAD-Software und druckt Modelle für jeden Schritt der Behandlung. Jeder Schritt hat dabei ein einzigartiges Modell, das als Grundlage zum Thermoformen der transparenten dentalen Anwendungen dient.
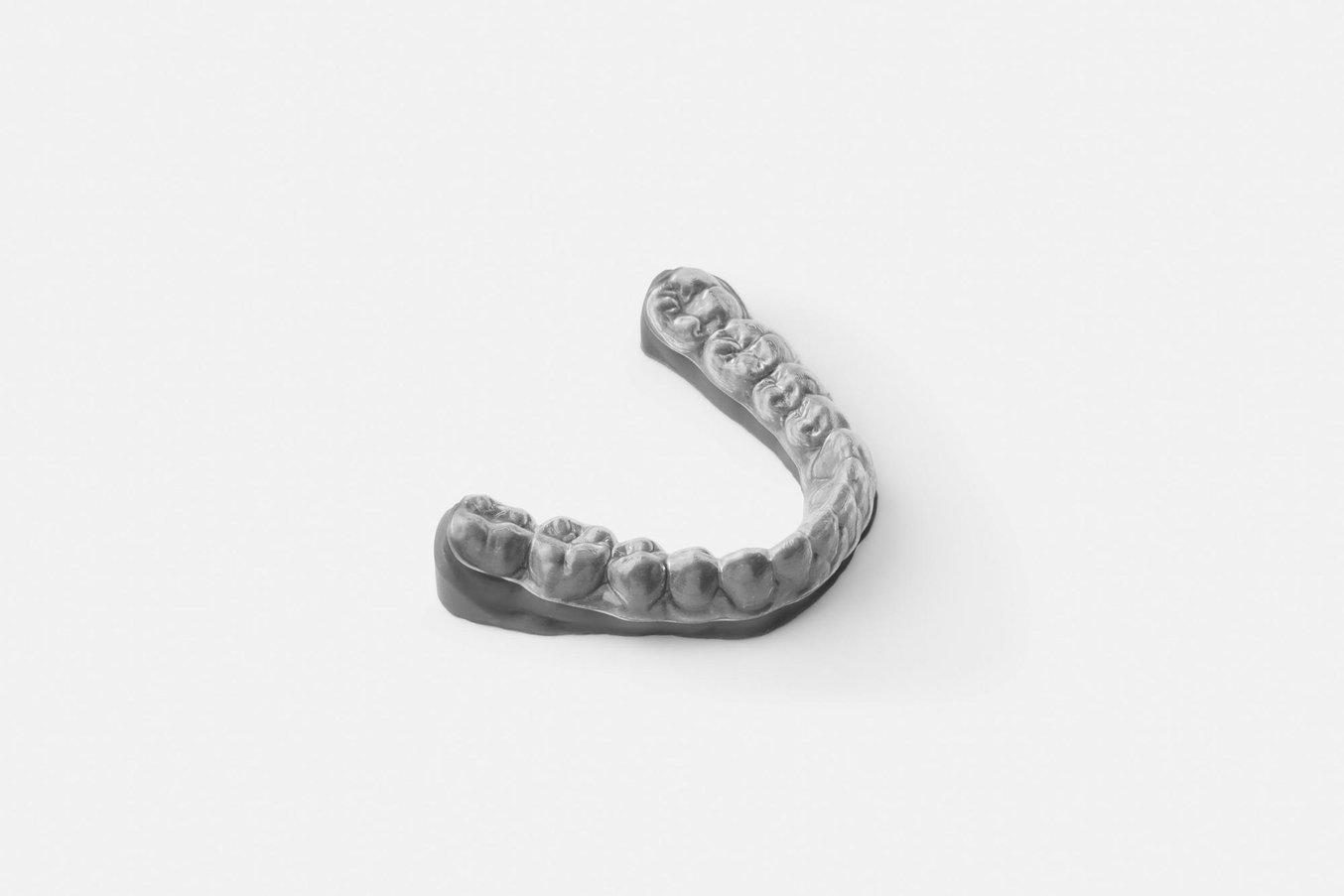
Das Thermoformen über 3D-gedruckten Modellen ist heute eine der gängigsten Produktionsmethoden transparenter Aligner in der Zahnmedizin.
Hitzebeständige SLA-Kunstharze lassen sich im Kunststoff-Spritzguss bei niedrigem Druck und selbst beim Guss weicher Metalle wie Zinn einsetzen. Die Gussformqualität mag zwar der von harter Werkzeugausstattung unterlegen sein, eignet sich aber dennoch hervorragend für kleine und mittelgroße Produktionsmengen, bei denen sich die teure Werkzeugbestückung sonst nicht rentiert.
In der Audiologie werden mit 3D-Druck auf erschwingliche Weise maßgefertigte Ohrstöpsel produziert. Dieser Prozess beginnt mit einem digitalen Scan des Gehörgangs des Kunden, aus welchem ein digitales Design erstellt wird. Das 3D-Druckteil dient als Gussform, die mit biokompatiblem Silikon gefüllt wird. Wenn das Silikon ausgehärtet ist, entfernt ein Techniker das 3D-gedruckte Gehäuse, trägt eine Beschichtung auf, und fertig ist das Produkt.
Direkt gedruckte Endverbrauchsteile
Die additive Fertigung wird immer mehr direkt für Endverbrauchsteile eingesetzt. Dabei sind die Medizin und Zahnmedizin aktuell die führenden Branchen. Viele patientenspezifische Endverbrauchsteile kommen direkt aus dem Drucker. Heute werden maßgefertigte Orthetik, Prothesen, Einlegsohlen, Hörgeräte und biokompatible Anwendungen wie Zahnprothesen und Schienen alle mit 3D-Druckverfahren hergestellt.
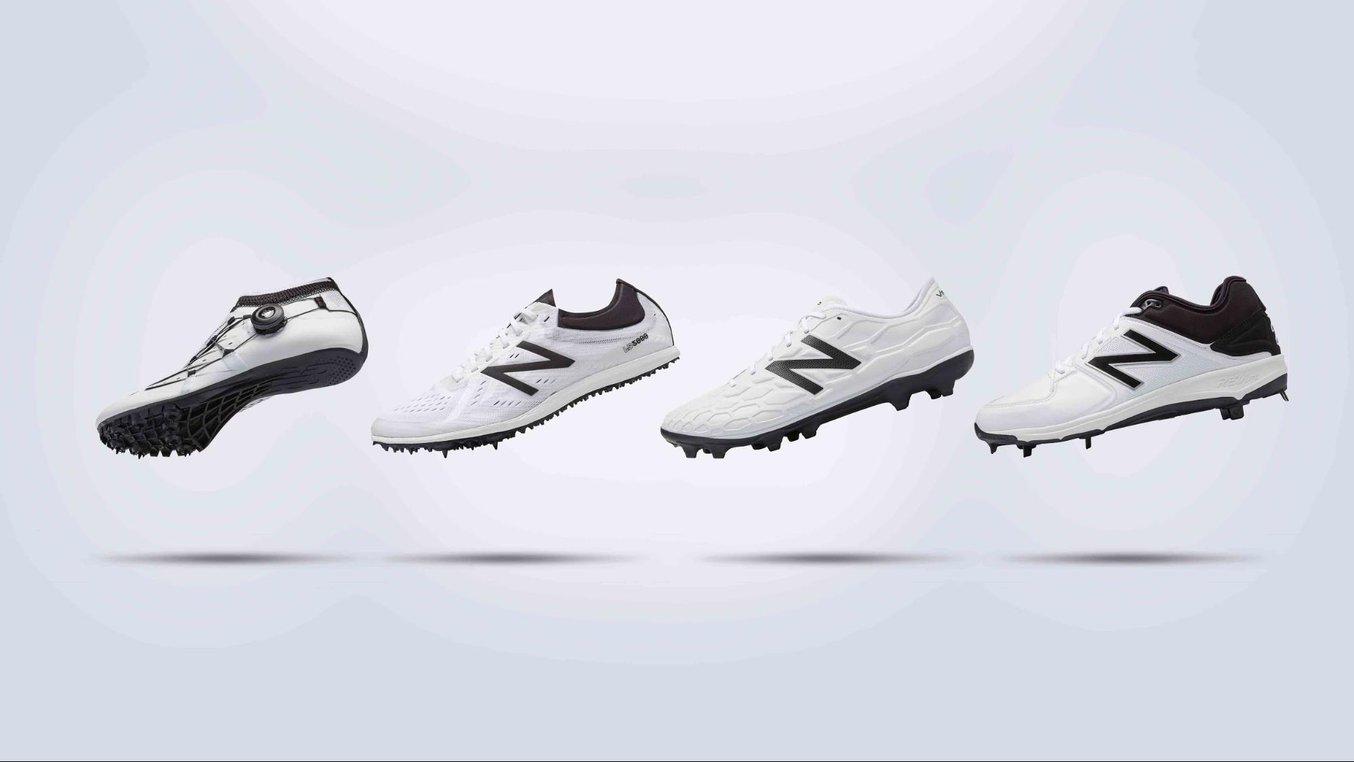
Schuhkonzepte von New Balance mit 3D-gedruckten Zwischensohlen
Schuhhersteller wie New Balance und Adidas haben Pläne angekündigt, im Verlauf der nächsten Jahre die Massenfertigung von personalisierten Zwischensohlen per 3D-Druck aus hartem Polyurethan aufzunehmen. Dabei wird 3D-Druck mit herkömmlichen Fertigungsverfahren kombiniert. Das nutzt die Wirtschaftlichkeit der Massenproduktion und erhöht gleichzeitig mit individualisierten Elementen die Leistung des Produkts und den Wert für den Endverbraucher.
Verbesserte Wirtschaftlichkeit dank serieller Maßanfertigung
Gesundheitswesen, Zahnmedizin und Schmuckherstellung waren die ersten Branchen, die die Vorteile der additiven Fertigung zur seriellen Maßanfertigung für sich entdeckten. Doch mit der Verbesserung der Technologien und Materialien und den sinkenden Kosten findet der 3D-Druck weitere Anwendungen bei einer noch größeren Produktpalette, einschließlich Verbrauchsgüter und funktionsfähiger Teile für Industriegeräte.
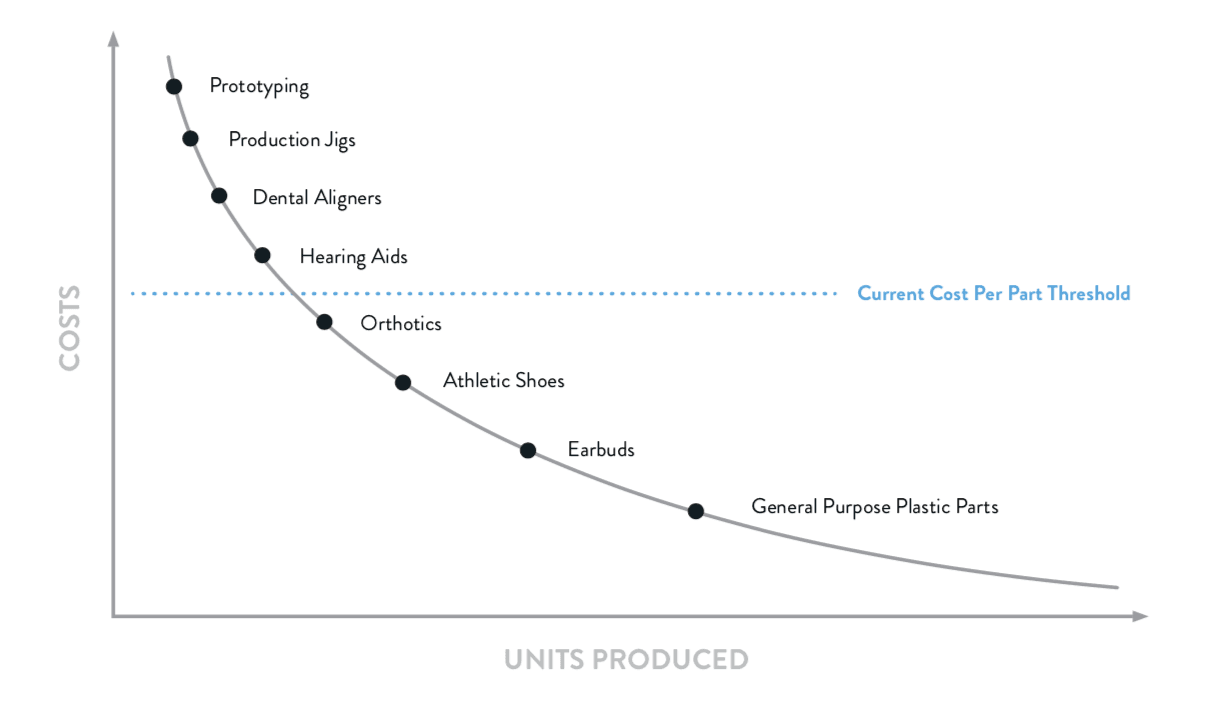
Mit der Verbesserung der Materialien und Technologien der additiven Fertigung läuft 3D-Druck traditionellen Herstellungsverfahren immer mehr den Rang ab, und das bei einer ganzen Reihe an Anwendungen.
Dabei ist einer der vielversprechendsten Trends die serielle Maßanfertigung, die die Flexibilität maßgefertigter Produkte mit den Kosteneinsparungen der Massenproduktion kombiniert. Personalisierte Produkte bieten handfeste Vorteile und erhöhen den gefühlten Wert beim Kunden. Gleichzeitig steigt die Gewinnspanne für den Hersteller gegenüber der Massenproduktion.
Indem sie die Zeit vom Konzept zum Produkt verkürzt, erhöht die additive Fertigung obendrein die Agilität und Reaktionsfähigkeit in der Fertigung, um schneller auf wechselnde Trends und Kundenbedürfnisse einzugehen.