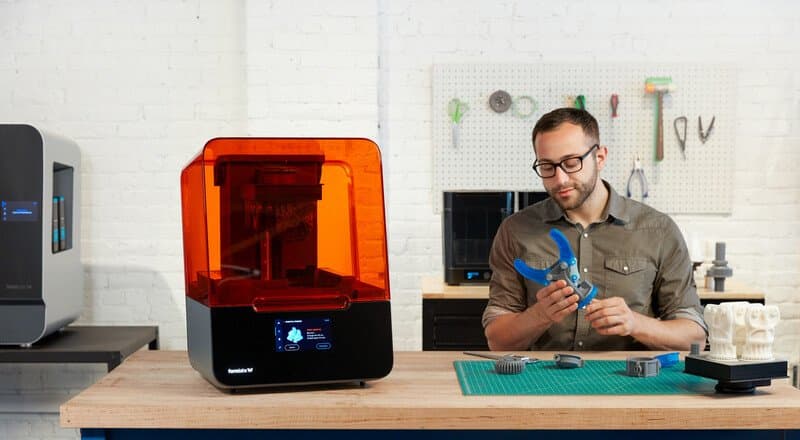
Der Form 3 mit Low Force Stereolithography (LFS) Technologie wurde im Frühjahr 2019 veröffentlicht. Seitdem wurde er von Testern, unseren Formlabs Botschaftern und Tausenden von Nutzern auf die Probe gestellt.
Für diesen Beitrag haben wir mit drei Kunden gesprochen, die bereits fleißig mit ihrem brandneuen Form 3 arbeiten. Erfahren Sie, wie der Form 3 bei der betriebsinternen Prototypenfertigung und bei Endverbrauchsteilen für die Kunden abschneidet.
Druck und Versand von Endverbrauchsteilen
Dan und Ruth Stewart sind die Gründer von Stewart Dollhouse Creations, einem Unternehmen, das in Heimarbeit Miniaturen entwirft. Am Anfang stellten sie die Miniaturen aus Modelliermasse her. Nachdem ihr Unternehmen wuchs und es zu Skalierungsproblemen kam, entschied sich das Ehepaar für 3D-Druck. Mit der Zeit hat Stewart Dollhouse Creations eine Flotte aus Druckern des Typs Form 2 aufgebaut, bevor sie schließlich in einen Form 3 investierten.
Stewart Dollhouse verwendet Photogrammetrie, eine einzigartige Technik, bei der mehrere 2D-Fotos zu 3D-Daten zusammengefügt werden, um die Geometrie verschiedener Teile besser zu erfassen. Softwaretools wie Rhino oder ZBrush werden eingesetzt, um zusätzlich feinere Details an den Modellen aufzubereiten oder zu verschönern. Nach dem Design setzt das Team seine 3D-Drucker aus dem Hause Formlabs ein, um die fertigen Teile zu drucken. Nach dem Waschen und Aushärten werden die Teile – häufig noch mit Stützstrukturen – an die Kunden versendet. Die berührungsempfindlichen Stützstrukturen aus dem Form 3 sind für sie eine deutliche Verbesserung, da so das Fertigstellen und Bemalen auf Kundenseite deutlich einfacher wird.
Laut Dan war die Erweiterung Ihrer aktuellen Flotte um den Form 3 problemlos, da das Gerät dieselbe Konstruktionsplattform und dieselben Harzkartuschen unterstützt wie der Form 2. Das erleichterte den Übergang zu einer gemischten Druckerflotte.
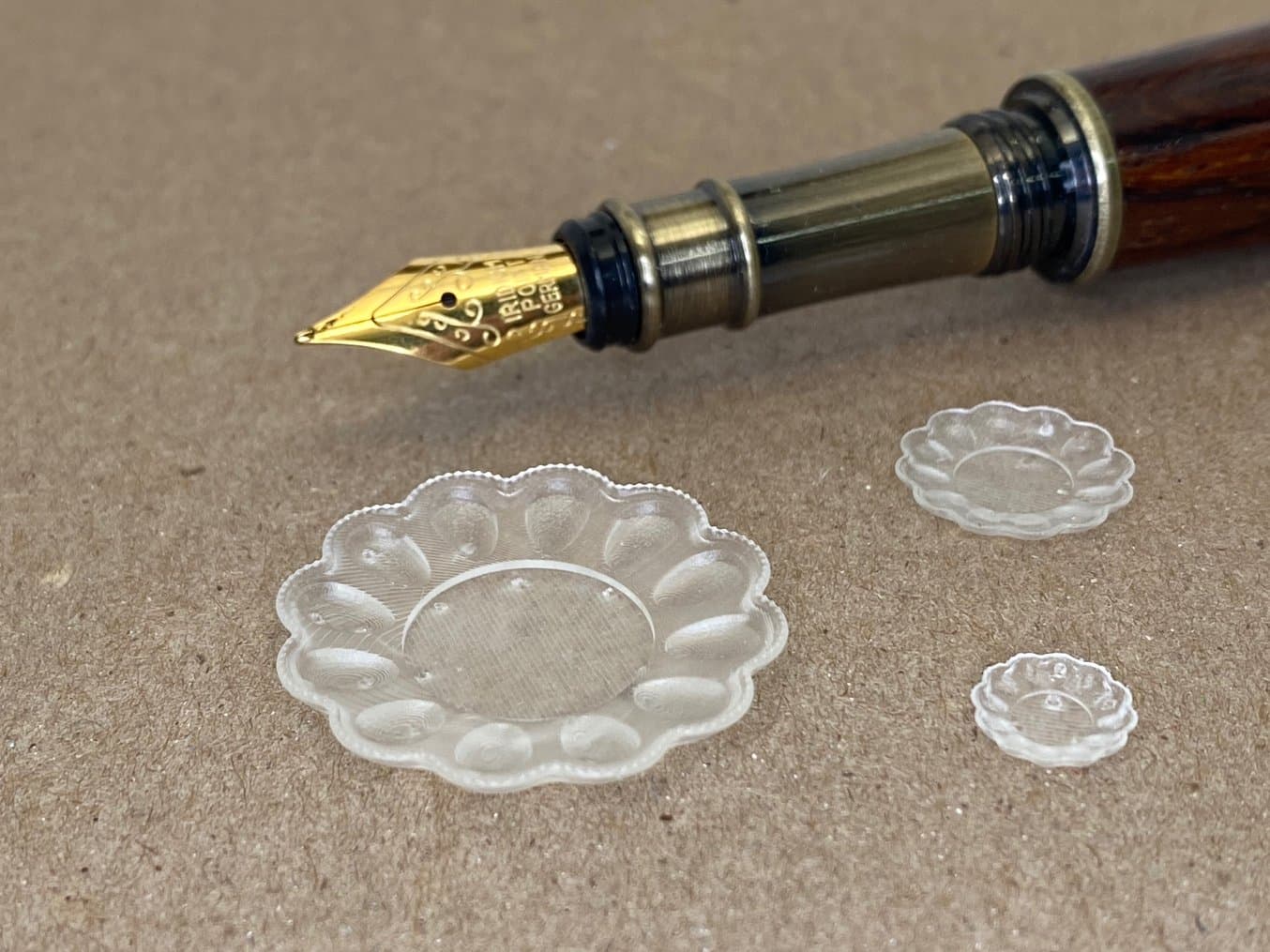
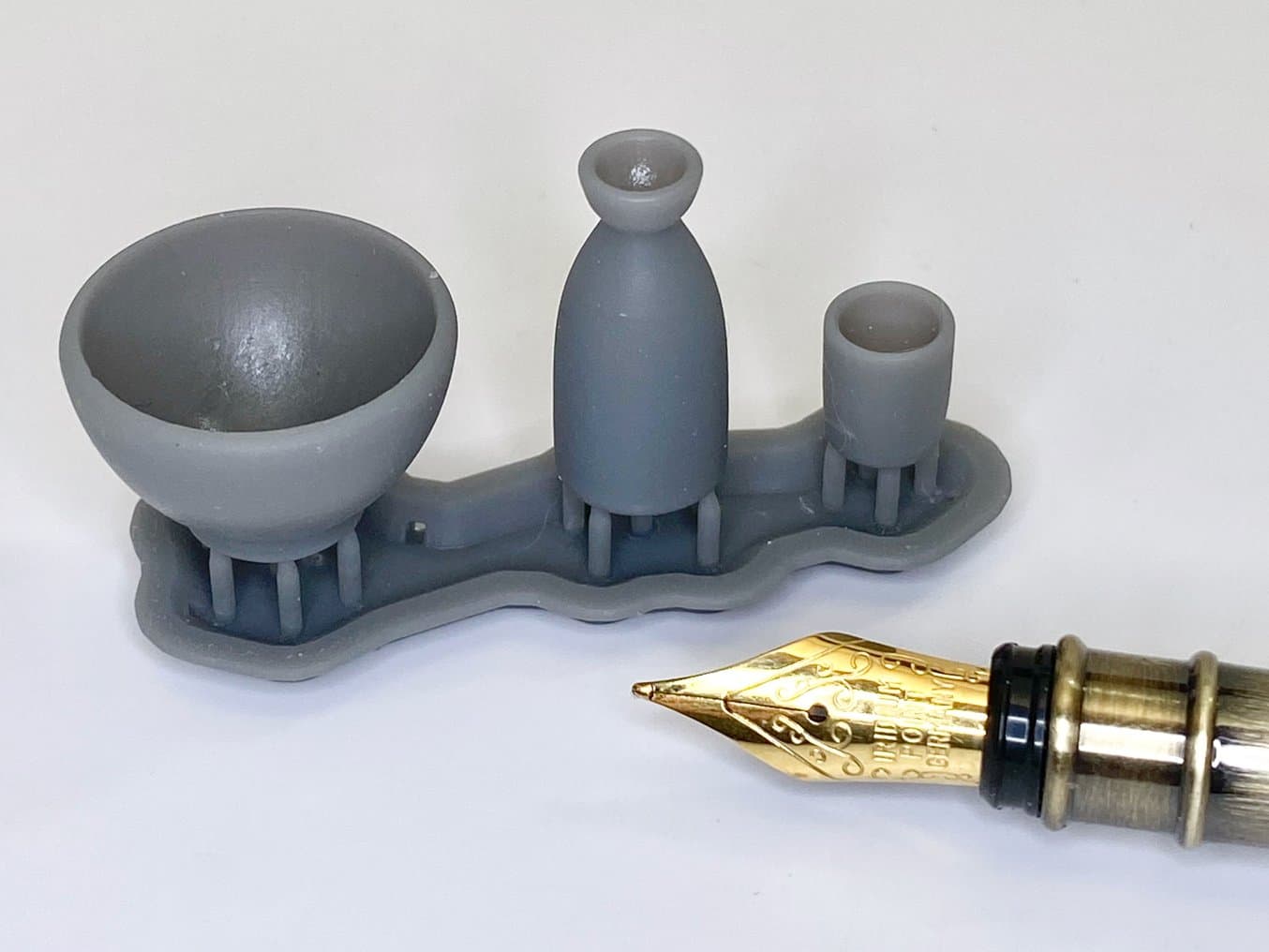
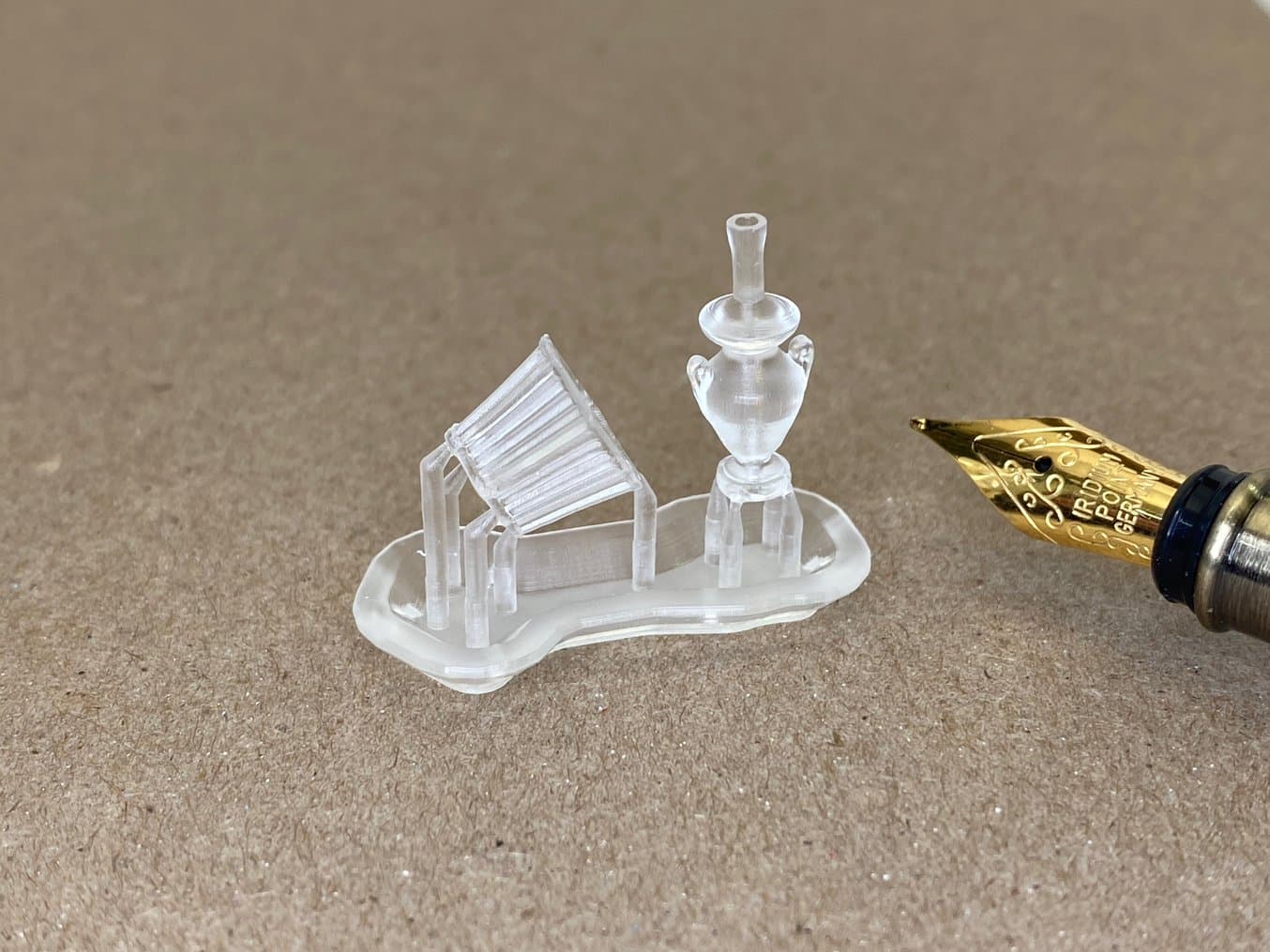
Prototypenfertigung von medizinischem Gerät
Eine Designberatungsagentur für Medizinprodukte aus dem Großraum Minneapolis hat vor kurzem zwei Drucker des Typs Form 3 zu ihrer bestehenden Flotte aus Form 2s hinzugefügt. Angesichts des wachsenden Bedarfs an Kapazitäten wollte das Unternehmen weiter Formlabs' Geräte nutzen, da diese sich durch hochwertige Drucke und ihre Zuverlässigkeit auszeichnen.
Die Agentur benötigt funktionsfähige Modelle mit entsprechender Optik, deren Eigenschaften ABS (Acrylnitril-Butadien-Styrol-Copolymer) entsprechen. Oberflächengüte und Druckerzuverlässigkeit sind unglaublich wichtig bei der Arbeit des Unternehmens. Mit dem Form 3 durfte man dort bei beiden Aspekten Verbesserungen feststellen. Einer der Ingenieure sagte: „Die Oberflächengüte bei einer Schichtdicke von 100 Mikrometern auf dem Form 3 ist mit einer Schichtdicke von 25 Mikrometern auf dem Form 2 vergleichbar.“
„Die Oberflächengüte bei einer Schichtdicke von 100 Mikrometern auf dem Form 3 ist mit einer Schichtdicke von 25 Mikrometern auf dem Form 2 vergleichbar.“Die Designberater nutzen Grey Resin auf dem Form 3, um funktionsfähige Prototypen wie Spulen, Gewinde und Gegenstücke zu drucken. Das Team hat bereits mehrere Iterationen durchgeführt und arbeitet schnell auf das endgültige Design hin
Von FDM zu makellosen Drucken auf dem Form 3
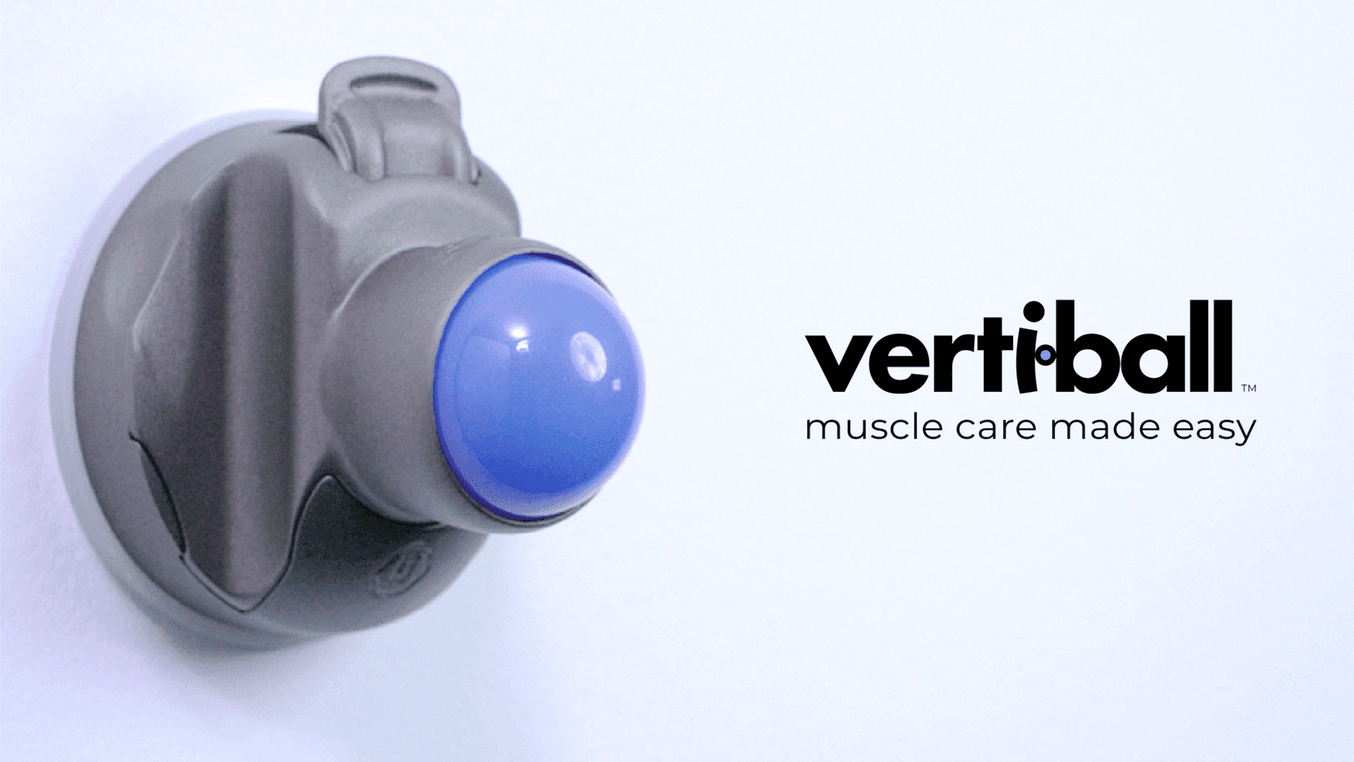
Curtis Kennedy ist der Erfinder von Vertiball, einem wandhaftenden Muskelmassagesystem, das Verspannungen, Schmerzen und Zerrungen lindert. Curtis begann mit dem Design des Produkts als Student an der University of New Brunswick und verwendete dabei die Schmelzschichtungs-3D-Drucker (FDM) der Universität.
Leider führten die anistropen Eigenschaften bei der FDM-Technologie dazu, dass sich viele seiner Prototypen bereits nach nur drei Einsätzen an den Schichtlinien ablösten. Trotz dieser Probleme konnte er nach Hunderten von Prototypen schließlich in die Werkzeuge investieren, die er zur Herstellung des Vertiball benötigte.
Jedoch ließen sich die massengefertigten Teile nicht so montieren, wie er es erwartet hatte. Schließlich fand er heraus, dass eine der wichtigen Komponenten aufgrund der Schrumpfung beim FDM-Druckverfahren ungenau war. So musste die Werkzeugausstattung neu eingestellt werden, was kosten- und zeitintensiv ist.
Für Curtis war klar, dass er einen Drucker benötigte, der hochgenau ist und eine Oberflächengüte bietet, die mit der von spritzgegossenen Teilen vergleichbar ist. Nachdem er seine CAD-Datei angepasst hatte, forderte Curtis einen individuellen Probedruck von Formlabs an, um das neue Design zu verifizieren. Das Teil war genau das, was er benötigte, und er verwendet es auch noch 8 Monate später! Mithilfe des Stereolithografie-Druckteils (SLA) konnte er die Werkzeugausstattung anpassen und seine Aufträge erfüllen.
Diese Erfahrung mit Formlabs war der Grund, weshalb Curtis einen Form 3 kaufte, was sich ungemein auf das Design einiger seiner anderen Vertiball-Module auswirkte. Laut Curtis war das Anwendererlebnis des Form 3 ganz anders als bei allen anderen Druckern, mit denen er bislang gearbeitet hatte. „Die Benutzeroberfläche ist intuitiv, PreForm lässt sich leicht bedienen und die Einstellung des Druckers ist kinderleicht. Die Berührungspunktgrößen der Stützstrukturen machen wirklich einen Unterschied. Ich hatte bislang sehr wenige Fehldrucke. Er ist ziemlich makellos.“
Erleben Sie den Form 3 selbst
Die Berichte anderer zu hören oder anzusehen, ist ein guter erster Schritt, um herauszufinden, ob sich der Form 3 SLA-Drucker für Ihr Unternehmen oder Ihren Arbeitsprozess eignet. Doch am besten ist es immer noch, ein Druckteil aus nächster Nähe zu sehen und anzufassen. Wenn Sie sich gerne aus nächster Nähe von der Qualität des Form 3 überzeugen möchten, fordern Sie einfach unten einen kostenlosen Probedruck an.