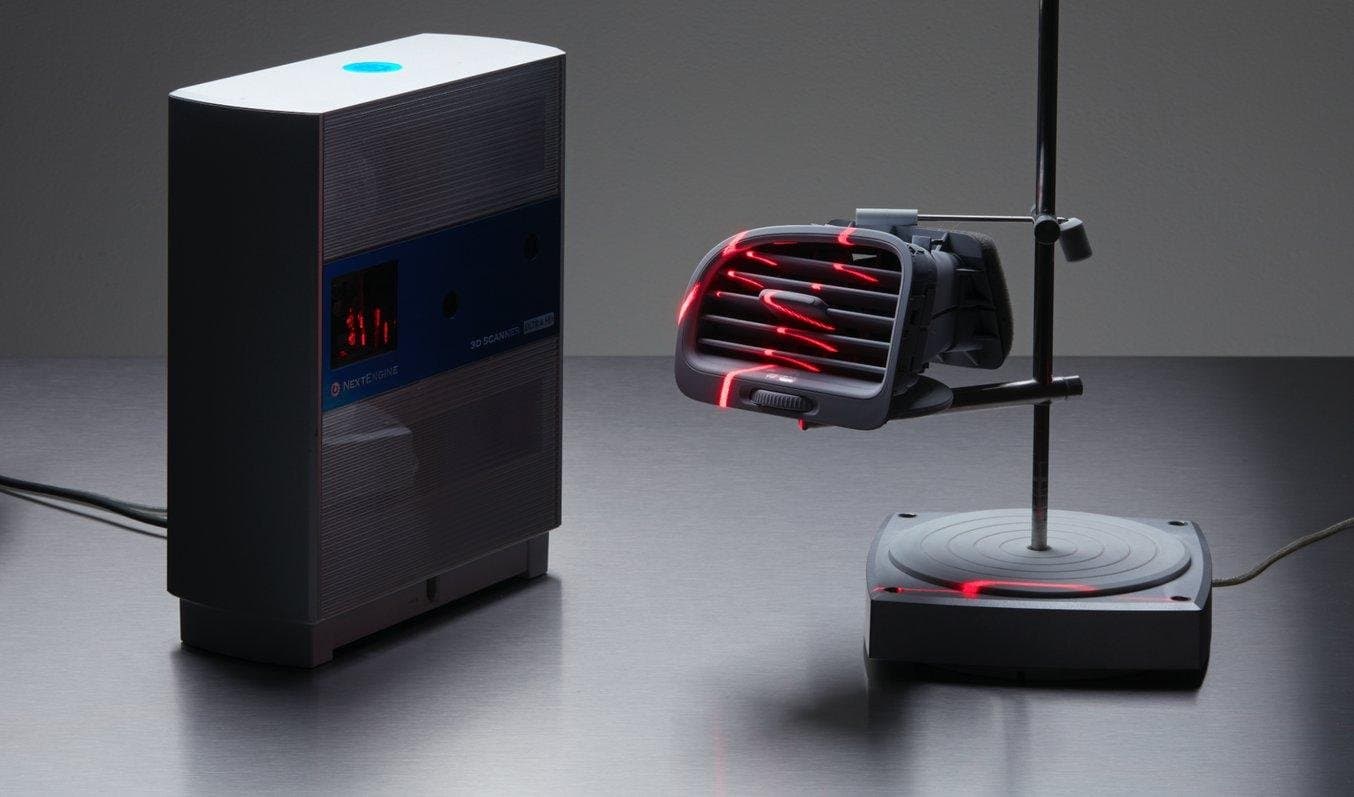
Reverse Engineering ist eine bewährte Methode zur Digitalisierung von Produktdesigns. Herstellerfirmen ermöglicht das die Ersatzteilproduktion nach Bedarf. Zudem lassen sich dadurch digitale Bestände erstellen und pflegen und Probleme mit veralteten Werkzeugen oder Designs vermeiden. Diese Technik finden wir häufig in der Automobilindustrie, Luft- und Raumfahrt, Biomedizintechnik, im Design for Manufacturing und im Industriedesign.
In diesem umfassenden Leitfaden behandeln wir den Prozess des Reverse Engineering ausführlich, stellen die besten Werkzeuge für das Reverse Engineering vor und präsentieren reale Fallstudien aus verschiedenen Bereichen.
Was ist Reverse Engineering?
Reverse Engineering ist ein Verfahren, bei dem ein Produkt zerlegt und untersucht wird, um die darin verwendeten Herstellungskonzepte zu identifizieren. Ziel ist es, ein ähnliches Produkt herzustellen oder ein bestehendes zu verbessern.
Zumindest ist dies die anerkannte Definition. Doch gibt es auch viele andere Gründe, den Ansatz des umgekehrten Maschinenbaus zu verfolgen. Innovation entsteht oft aus nicht mehr als einer geringfügigen Anpassung oder Ergänzung eines fertigen Produkts: in der Chemie zur Schaffung neuer molekularer Verbindungen oder Impfstoffe, in der Elektronik zur Nachbildung von Leiterplatten und in der Softwareentwicklung zur Neugestaltung von Firmware, Back-End-Architekturen und Benutzeroberflächen.
Mit Technologien und digitalen Fertigungswerkzeugen wie 3D-Scannern und -Druckern stehen (Rückwärts-)Ingenieurteams heute bessere Werkzeuge zur Verfügung als je zuvor.
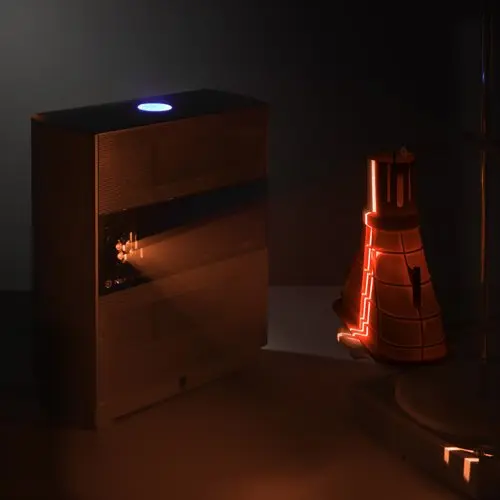
Vom 3D-Scan zum 3D-Druck: Reverse Engineering im Schnellverfahren für Maschinenüberholung, Montagevorrichtungen und Aftermarket-Produkte
In diesem Webinar erhalten Sie einen detaillierten Einblick darin, wie Sie 3D-Scan einsetzen, um in Kombination mit CAD-gestütztem Reverse Engineering und 3D-Druck das Design und die Produktion von Teilen zu verbessern.
Reverse Engineering von Hardware
Es gibt zahlreiche Beweggründe für das Reverse Engineering mechanischer Teile.
Erweiterungen: In der Produktentwicklung werden existierende Komponenten oft umgestaltet, als ergänzende Artikel oder Aftermarket-Produkte, als individuelle Anpassungen, als Reparaturen oder zum Einbau in neue Bauteile.
Produktverbesserungen: Vorhandene Komponenten werden demontiert, eingescannt und eingehend analysiert, um die Herstellungs- und Montageprozesse zu optimieren. Kostensenkung kann auf folgende Weisen erreicht werden:
-
Lockerung der geometrischen Abmessungen, Toleranzen und Einschränkungen.
-
Gewichtsreduzierung durch Optimierung der Struktur anhand von Rippen, Wandstärken, Radien und anderen Übergängen.
-
Neugestaltung zur Anpassung an Änderungen im Herstellungsprozess, um die Montage zu erleichtern, die Demontage, Formbarkeit, Funktionsintegration oder die Entsorgung am Ende der Lebensdauer.
-
Verfeinerung zentraler Funktionsmerkmale, der Ergonomie oder der Benutzerfreundlichkeit.
-
Verbesserung der Produktleistung wie Gesamtfestigkeit, Einrastung, Biegescharniere, Montagepunkte für elektronische Bauteile, Haltbarkeit und Schutz vor Eindringen von Wasser und Staub.
Innovationsanstoß: Das Auseinandernehmen bestehender Geräte – um ihre Funktionsweise und Designabsicht im Detail zu verstehen – kann radikale Innovation auslösen.
Ein Verständnis vergangener Lösungen technischer Herausforderungen erspart es Unternehmen, das Rad neu zu erfinden. Das Feld der Bionik ist besonders notorisch dafür, da biologische Systeme wie die Beine von Heuschrecken, die Füße von Geckos, die Hydrodynamik von Walen, das Verhalten von Ameisenkolonien, die Arme von Fangschreckenkrebsen sowie Spinnennetze und Ammonitenschalen als Ausgangspunkt für neuartige Erfindungen dienten.
Durch die Demontage existierender Geräte erfahren Unternehmen auch mehr über das, was unter der Haube der Konkurrenzprodukte steckt, sowie über deren Montageprozesse. Diese Informationen dienen dann zur Evaluierung, ob das Unternehmen tatsächlich ein gutes Preis-Leistungs-Verhältnis bietet und wo Verbesserungspotenzial seitens der Lieferkette und der Geschäftsstrategie besteht.
Wiederbelebung: Falls ein Erstausstatter (OEM) ohne Veröffentlichung von Bauplänen oder CAD-Daten das Geschäft aufgibt, ist Reverse Engineering die erste Wahl, um verlorene Artikel wiederzubeleben. Zum Beispiel können Oldtimer, für die keine Ersatzteile mehr lieferbar sind, dank Rückwärtsentwicklung der Motoren, Getriebe und Antriebssysteme wieder fahrtüchtig gemacht werden.
Reverse Engineering ist auch eine großartige Möglichkeit, eingestellte Produktserien mit abgelaufenem Patentschutz zurückzubringen und sie für das heutige Publikum anzupassen.
Die Rückwärtsentwicklung dient auch zu Erhaltungszwecken, wenn ein digitales Archiv verlorener Objekte erstellt wird. Historische Produkte, die vor dem Zeitalter von Computern und CAD hergestellt wurden, können jetzt durch die Erstellung digitaler Zwillinge nachgebildet werden. So erhalten Unternehmen ihre vollständige Produktgeschichte.
Nachahmungen: Die fragwürdigste Anwendung des Reverse Engineering ist die weit verbreitete Praxis der Produktfälschungen. Auf der ganzen Welt beobachten wir heute Imitate von Bestseller-Produkten, die oft vereinfacht oder fehlproportioniert sind oder ungeschickt unter einem anderen Markennamen verkauft werden.
In vielen Fällen verletzt dies Patente und erfordert rechtliche Schritte. Jedoch kann es auch als Kompliment für die ursprüngliche Designleistung aufgefasst werden. Außerdem ist es unter Umständen ein brauchbarer Weg, neue Märkte für eben dieses Design zu erschließen, die nicht zum Vertriebsgebiet des Eigners gehören oder nicht vom Schutz des geistigen Eigentums abgedeckt sind.
Hier sind einige Anwendungsbeispiele für Reverse Engineering:
Branche | Anwendungen | |||
---|---|---|---|---|
Automobilindustrie | Stoßstangen, Dächer, aerodynamische Modifikationen, Kit-Cars, Abgaskrümmer, Ersatzteile, Digitalisierung von Tonmodellen | |||
Biomedizintechnik | Anatomiemodelle, Implantate, chirurgische Instrumente, Prothesen/Orthesen, Orthopädie | |||
Konsumgüter | Erweiterungen, Prototypen, Verpackungen | |||
Maschinenbau | Ersatzteile, Teileverbesserung, Wertanalyse, Maschinenumbau, Fehleranalyse | |||
Möbel | Verzierung, Beine, Formen, Zierränder, Ersatzteile | |||
Schmuck | Repliken, Formen, maßgeschneiderte Artikel, Konservierung |
Ist Reverse Engineering rechtlich erlaubt?
In der Regel ist Reverse Engineering legal – gemäß der europäischen Richtlinie zum Schutz von Geschäftsgeheimnissen (Richtlinie EU/2016/943) und dem U.S. Defense Trade Secrets Act (DTSA) –, um sich einen kommerziellen Vorteil gegenüber Konkurrenten zu verschaffen. Vorausgesetzt, dies erfolgt ohne Verletzung vertraglicher Vereinbarungen und nach rechtmäßigem Erwerb des Originalprodukts.
Es wird als rechtmäßige Methode zur Aufdeckung von Geschäftsgeheimnissen angesehen, die sich von Diebstahl oder Spionage unterscheidet, solange dies nicht in Konflikt gerät mit dem Patentrecht, der Endbenutzerlizenzierung oder anderen vertraglichen Verpflichtungen.
In einigen Fällen können jedoch Wettbewerber, die Produkte nachahmen, schwerwiegende Folgen für das Geschäft des Urhebers haben. Und Unternehmen ergreifen häufig aktive Schritte, um zu verhindern, dass ihre Produkte in falsche Hände geraten.
Reverse Engineering von Software
Reverse Engineering von Software verfolgt denselben Zweck, unterscheidet sich jedoch fundamental von der Hardware-Nachbildung, da kommerzielle Anwendungen in der Regel als „Closed-Source“ (proprietäre Software) gelten. Das bedeutet, dass der Quellcode bewusst für Dritte unzugänglich gemacht wird.
Es gibt jedoch spezielle Tools, sogenannte Disassembler, die die internen Abläufe und den algorithmischen Aufbau der Zielanwendung offenlegen. Diese Software-Reversing-Lösungen dekompilieren in ihre eigene plattformspezifische Assemblersprache, ohne den Originalcode zu kopieren.
Durch diese innere Umwandlung entsteht ein einzigartiger Maschinencode, wodurch der gesamte Prozess völlig legal ist. Auf ganz ähnliche Weise entwickeln Hersteller wie AMD Intel-kompatible Mikroprozessoren. Auf diesem Wege passen Unternehmen legal auch Softwareumgebungen an, um eine Integration ihre bestehenden IT-Systeme zu gewährleisten.
In einem berühmten Fall entdeckte Googles Project Zero durch Reverse Engineering eine gravierende Schwachstelle in Mikroprozessoren. Dabei fand man heraus, dass es möglich ist, Auslesevorgänge von zuvor zwischengespeicherten Segmenten zu erstellen, die sensible Informationen wie Passwörter enthalten können. Dies führte zu einer neuen Idee: die Speicherung in einem separaten System-on-a-Chip (SoC), um die Daten vor einem Abfangen zu schützen.
Ein entscheidender Unterschied zwischen dem Reverse Engineering von Software und Hardware liegt darin, dass Code verschlüsselt werden kann. Cyberkriminelle nutzen dies oftmals, um Malware zu entwickeln, die selbst bei Verwendung von Tools wie der NSA-Software Ghidra äußerst schwer zu entschlüsseln ist.
Um die Cybersicherheit zu stärken, führt in manchen Unternehmen ein internes „Hacker“-Team häufig virtuelle Angriffe auf das eigene Netzwerk durch, während ein anderes „Schutz“-Team die Angriffe überwacht und rückanalysiert, um neue Lösungen zu finden.
Überblick über den Reverse-Engineering-Prozess
Der genaue Ablauf von Reverse Engineering variiert je nach Art des Objekts. In diesem Leitfaden konzentrieren wir uns auf das Reverse Engineering von Hardware.
Der Prozess des Reverse Engineering von Hardware besteht aus vier Schritten. Es stellt den Entwicklungsprozess neuer Produkte quasi auf den Kopf. Die Ingenieurteams beginnen mit dem fertigen Produkt und leiten daraus die zugrunde liegenden Anforderungen ab.
Der Prozess sieht in der Regel folgendermaßen aus:
-
Datenbeschaffung: Zuerst wird der 3D-Scanner kalibriert und Hintergrund und Beleuchtung werden vorbereitet. Das Ergebnis ist oft eine Punktwolke, die mehrere Gigabyte groß sein kann. Allerdings reicht es oft nicht aus, nur das Modell zu digitalisieren. Reverse Engineers möchten auch das Design und die Montagemerkmale verstehen, indem sie das Produkt auseinandernehmen und verschiedenen Tests unterziehen.
-
Nachbearbeitung: Die anfängliche Punktwolke wird in ein Netzmodell umgewandelt. Die meisten Software-Tools bieten automatische Funktionen, erfordern jedoch möglicherweise manuelles Schließen von Lücken und Entfernen von Unregelmäßigkeiten. In diesem Schritt geht es darum, das gegenwärtige System und seine Bestandteile detailliert zu untersuchen und aufzuschlüsseln.
-
Modelldesign: Die Netzdarstellung des Objekts wird in ein parametrisches Modell auf der Grundlage von Festkörpern und Oberflächen umgewandelt. Wir arbeiten nun von der Implementierungsebene aus rückwärts, um die zugrunde liegende Designabsicht aufzudecken. Während dieser Phase können Ingenieurteams die Abmessungen anpassen und Verbesserungen einfügen.
-
Überprüfung: In diesem Stadium erfolgen dimensionsbezogene Vergleiche zwischen dem Scan und der resultierenden Reproduktion. Danach folgen Absicherungen, Prototypenbau, Tests und Iterationen in verschiedenen Szenarien, damit das rückentwickelte Produkt den neuen Anforderungen auch gerecht wird.
Reverse Engineering unterscheidet sich vom Maschinenbau auf grundlegende Weise. Da wir von einer vorhandenen Implementierung rückwärts gearbeitet haben, ist das überarbeitete Produkt niemals zu 100 % genau, spezifikationsgerecht oder „korrekt“ in CAD modelliert.
Weil Reverse Engineering von Natur aus in den Abmessungen ungenau, in der Interpretation mehrdeutig und in der Oberflächenkonstruktion eigenartig ist, müssen wir uns mit der bestmöglichen Annäherung zufriedengeben. Trotzdem schaffen wir so in sehr kurzer Zeit erheblichen Wert. Bei der Neuentwicklung von Grund auf erfordern solche Teile das 10- oder 100-fache der Ressourcen. Es bedarf einer anderen Denkweise als bei der Neuentwicklung, die normalerweise durch das Streben nach Perfektion gekennzeichnet ist.
Die besten Werkzeuge für das Reverse Engineering
3D-Scanner für Reverse Engineering
Es gibt verschiedene Methoden, um ein Objekt in ein digitales Abbild zu verwandeln. 3D-Scanner sind dabei die gängigsten Erfassungsgeräte und existieren in verschiedenen Formen.
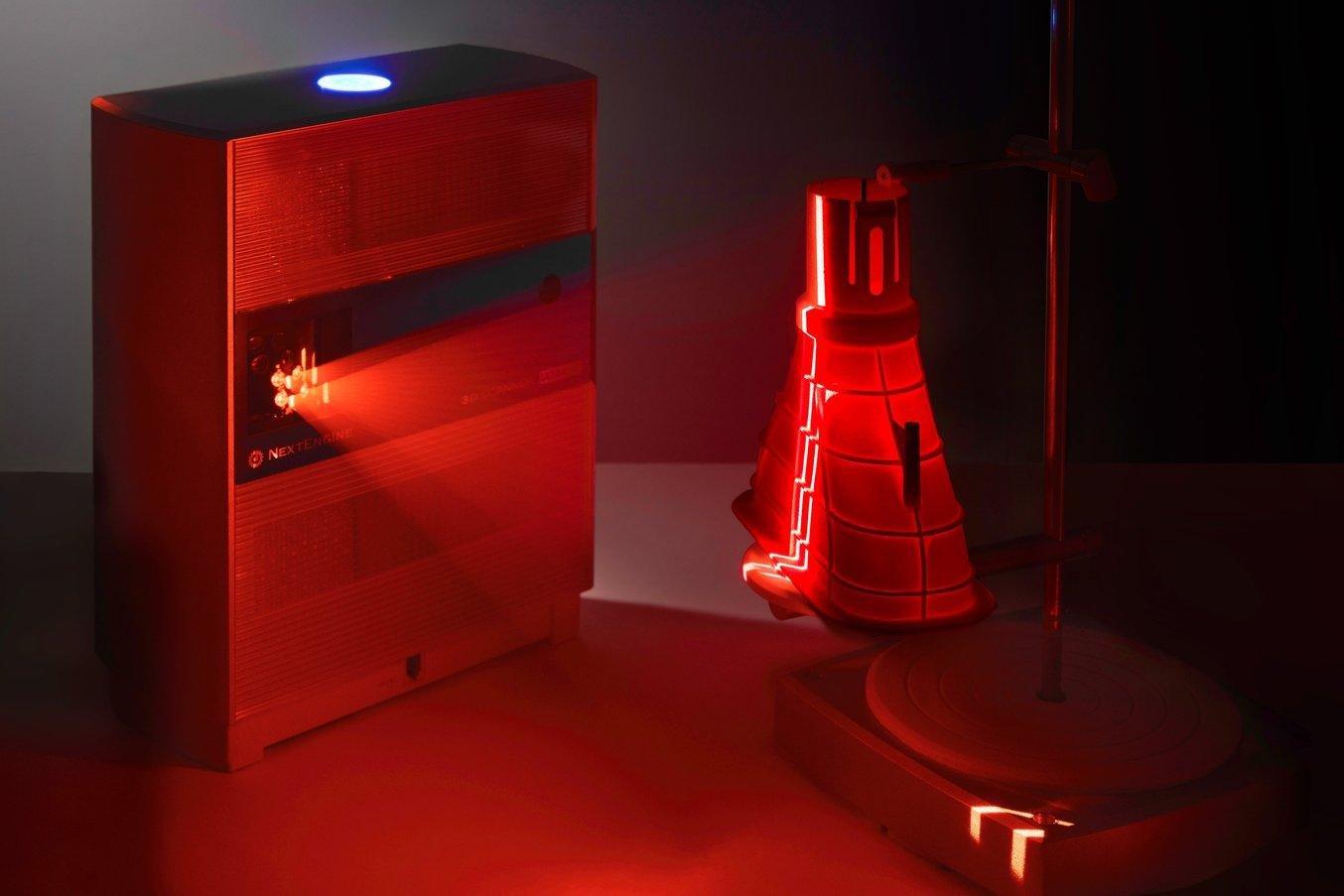
3D-Scanner sind die am häufigsten verwendeten Erfassungsgeräte im Reverse Engineering.
Streifenlichtscanner projizieren ein Lichtmuster über das Objekt und verwenden zwei Kameras, um zu erfassen, wie das Objekt das Licht verändert. Die resultierenden Bilder werden zu einer 3D-Abbildung zusammengefügt.
Im Allgemeinen werden solche 3D-Scanner für handgeführte und nicht-invasive medizinische Anwendungen eingesetzt. Zu den bekanntesten Einsteigermodellen zählen der Shining3D Einstar, der Creality CR-Scan Lizard und der Structure Sensor Pro. Die beworbenen Präzisionsniveaus genießt man jedoch besser mit Vorsicht, da die durchschnittliche Abweichung für diese Art von Geräten etwa 1 % beträgt.
Fortschrittlichere Scansysteme findet man in den Handscannern von Peel3D, Calibry und Artec Eva. Sie bieten höhere Genauigkeit, integrierte Verarbeitungssoftware und Echtzeit-Feedback zur Unterstützung des Scanvorgangs. Außerdem ermöglichen sie verschiedene Modi, darunter Scans mithilfe aufgeklebter Markierungen. Dies ist besonders nützlich bei flachen Objekten mit einer Größe von mehreren Metern. Jedoch geht die Steigerung der Qualität in der Regel mit einem exponentiellen Preisanstieg einher.
Laser-Triangulationsscanner projizieren Millionen von Laserpunkten pro Sekunde auf das Zielobjekt, das normalerweise mit Markierungen versehen werden muss. Für undurchsichtige Teile mit feinen Details wie filigranen Maschen, konvexen Oberflächen und Gitterstrukturen ist diese Kategorie von 3D-Scannern die beste Wahl.
Beliebte Produkte wie der 3D-Scanner von Matter and Form, der HandyScan von Creaform, der T-Scan Hawk von Zeiss und der Freestyle von FARO können sogar komplette Fahrzeuge scannen. Für anspruchsvolle Scanprojekte verwenden Fachleute oft eine Hybridmethode, die sowohl eine tragbare Koordinatenmessmaschine als auch einen stationären berührungslosen Scanarm einschließt.
Für Einsteiger und Enthusiasten, die die Unvollkommenheiten ihrer Scans mit ihren erstklassigen CAD-Fähigkeiten ausgleichen, gibt es einige kostengünstige Alternativen.
Infrarotkameras mit Tiefensensoren und LiDAR-Sensoren liefern weniger genaue Netzmodelle, können aber in einigen Fällen für einfache Scans immer noch zufriedenstellend sein und sind in den neuesten Modellen des Apple iPhone und iPad zu finden.
Photogrammetrie beruht auf herkömmlicher Fotografie. Eine Sequenz von Bildern aus verschiedenen Blickwinkeln wird um das Objekt herum aufgenommen. Anschließend kommt rechenintensive Software wie Meshroom, RealityCapture, Regard3D, Trnio, RecFusion oder Zephyr zum Einsatz, um die Bilder in eine 3D-Rekonstruktion zu verwandeln.
Die Technologie bietet zwar den Vorteil, dass einige Apps kostenlos sind, es erfordert aber etwas mehr Geschick und Geduld, um brauchbare Modelle aus der Photogrammetrie abzuleiten, unabhängig von der Anwendung.
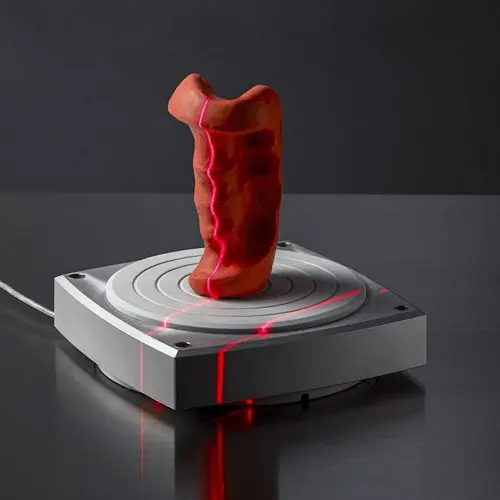
3D-Scan und 3D-Druck für Reverse Engineering und andere Anwendungen
3D-Scan- und 3D-Druckverfahren lassen sich zum Nachbau, zur Restauration, für Reverse Engineering, Metrologie und viele weitere Anwendungen einsetzen. Laden Sie unser Whitepaper herunter, um diese Anwendungen kennenzulernen, und erfahren Sie, womit Sie beginnen sollten.
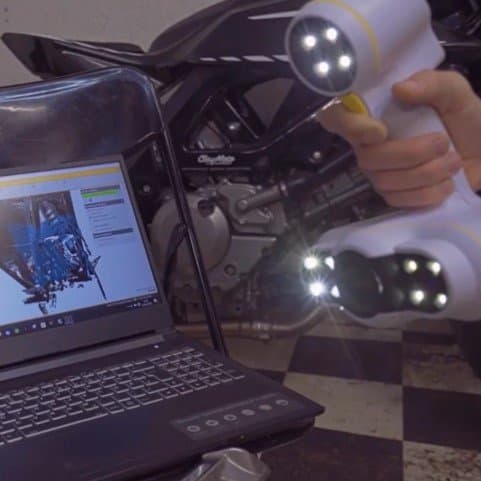
Wie 3D-Scannen moderne Produktentwicklungsprozesse unterstützt
In diesem Webinar mit Peel 3D erklären wir, wie Sie 3D-Scanner in Ihren 3D-Druckablauf integrieren, um Ihren Produktentwicklungsprozess zu optimieren.
Software für das Reverse Engineering
Die relative Leichtigkeit des Arbeitsablaufs vom 3D-Scan zum CAD hängt oft von einer Reihe separater Software-Tools ab, die unterschiedliche Kompatibilitätsgrade aufweisen. Um den Prozess zu optimieren, empfiehlt sich jedoch eine Softwarelösung, die von den Rohdaten des Scans bis zur vollständigen und hochwertigen Rekonstruktion des Originaldesigns führt.
Die besten Software-Tools für das Reverse Engineering laden Punktwolken in verschiedenen Formaten wie .ply, .asc, .ptx, .pcg (Autodesk), .e57, .xyz, .fls (Faro), .pcd, .las und .obj. Diese Programme erstellen und reparieren das resultierende Gitterobjekt automatisch und bieten eine Vielzahl intelligenter Funktionen zur Rekonstruktion von NURBS-Oberflächen (nicht-uniforme rationale B-Splines). Das erspart es, jedes kleine Detail manuell zu vermessen, wie es vor dem 3D-Scanner der Fall war.
In einigen virtuellen Designstudios kann das Ergebnis sogar direkt für die Prototypenerstellung via CNC, 3D-Druck oder Guss vorbereitet werden. Und da ein Zehntel eines Millimeters den Unterschied ausmachen kann, wie gut zwei gefertigte Teile zusammenpassen, ist Präzision entscheidend im gesamten Reverse-Engineering-Prozess.
Um Genauigkeit zu gewährleisten, muss ein Reverse-Engineering-Tool die folgenden Funktionen bieten:
-
Interferenzprüfung, damit die Teile reibungslos in einer Baugruppe zusammenarbeiten und externe Komponenten passgenau sind.
-
Wandstärkeanalyse zur Optimierung der Formbarkeit und Leichtbauweise.
-
Entwurfsanalyse, um korrekte Winkel sicherzustellen, Hinterschneidung zu verhindern und Trennlinien zu validieren.
-
Oberflächenanalyse, einschließlich Zebraanalyse und Krümmungskontrolle, um die Eignung für große komplexe Formen zu gewährleisten, wie sie in Verbraucherprodukten und der Automobilindustrie erforderlich sind.
-
Abmessungsprüfung, darunter Masse, Volumen und Begrenzungsrahmen.
Hier sind einige der besten Reverse-Engineering-Softwaretools.
Mesh2Surface
Mesh2Surface ist eine Komplettlösung. Mit ihr konvertiert die Produktentwicklung eine Punktwolke direkt in ein Gittermodell für das Reverse Engineering mit Rhinoceros oder SolidWorks.
Anschließend können Bezugsebenen und Punkte des Gittermodells extrahiert werden, um komplexe Geometrien anzupassen. Mesh2Surface bietet eine Vielzahl intelligenter Werkzeuge für 3D-Skizzen, Querschnitte und Umrisse. Die Software verfügt auch über eine Abweichungsanalyse, automatisierte Flächenbildung mit anpassbaren Präzisionseinstellungen und die Erstellung bestpassender Freiformflächen.
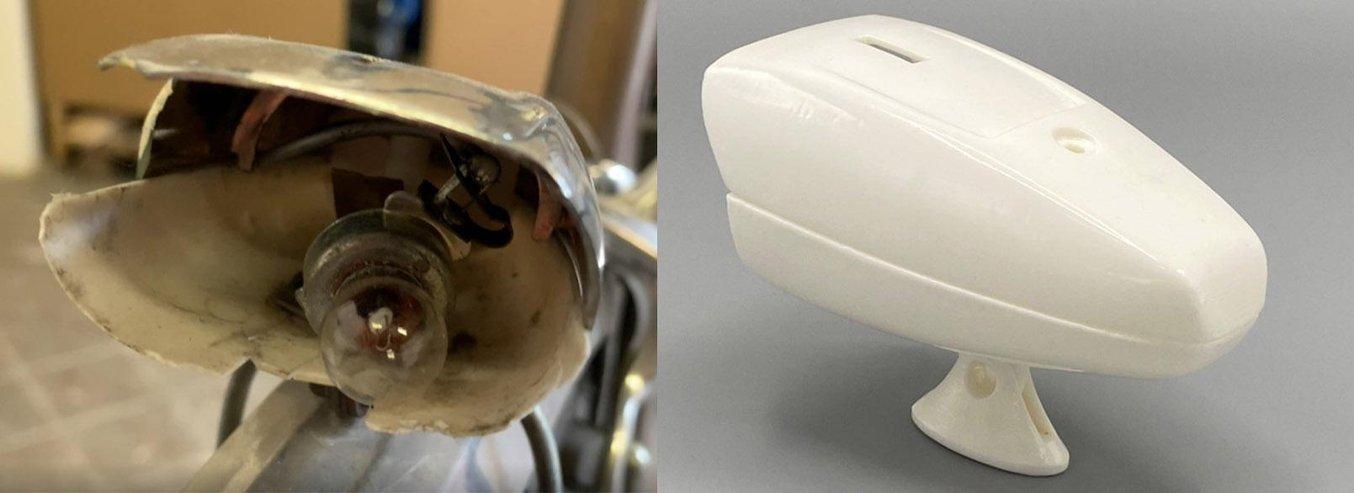
Mesh2Surface zeichnet sich besonders bei der Erstellung von Ersatzteilen stark beschädigter Komponenten aus, wie bei diesem Motorrad-Scheinwerfer.
Artec Studio
Artec ist eine weitere führende Option unter den Tools für das Reverse Engineering von Hardware. Die Software legt großen Wert auf Benutzerfreundlichkeit und bietet maximale Geschwindigkeit bei der Umwandlung von Scans in CAD-Modelle. Dank Echtzeit-Rückmeldung zur Gerätebewegung und der Möglichkeit, mehrere Scans für eine umfassende Dateneinbindung zu überlagern, können Sie ein gesamtes Auto in nur etwa 15 Minuten digitalisieren.
Obwohl Artec keine vollständige CAD-Funktionalität bietet, ermöglicht es dennoch die Erstellung genauer Modelle durch Funktionen zur Anpassung von Grundformen, fortschrittliche Algorithmen zur Verfolgung von Textur und Geometrie sowie das „Auto Surface“-Tool, das organische Formen in ein solides Modell umwandelt.
Artec Studio bietet außerdem einen Autopilot-Modus, der einen Großteil des Modellierungsvorgangs automatisiert.
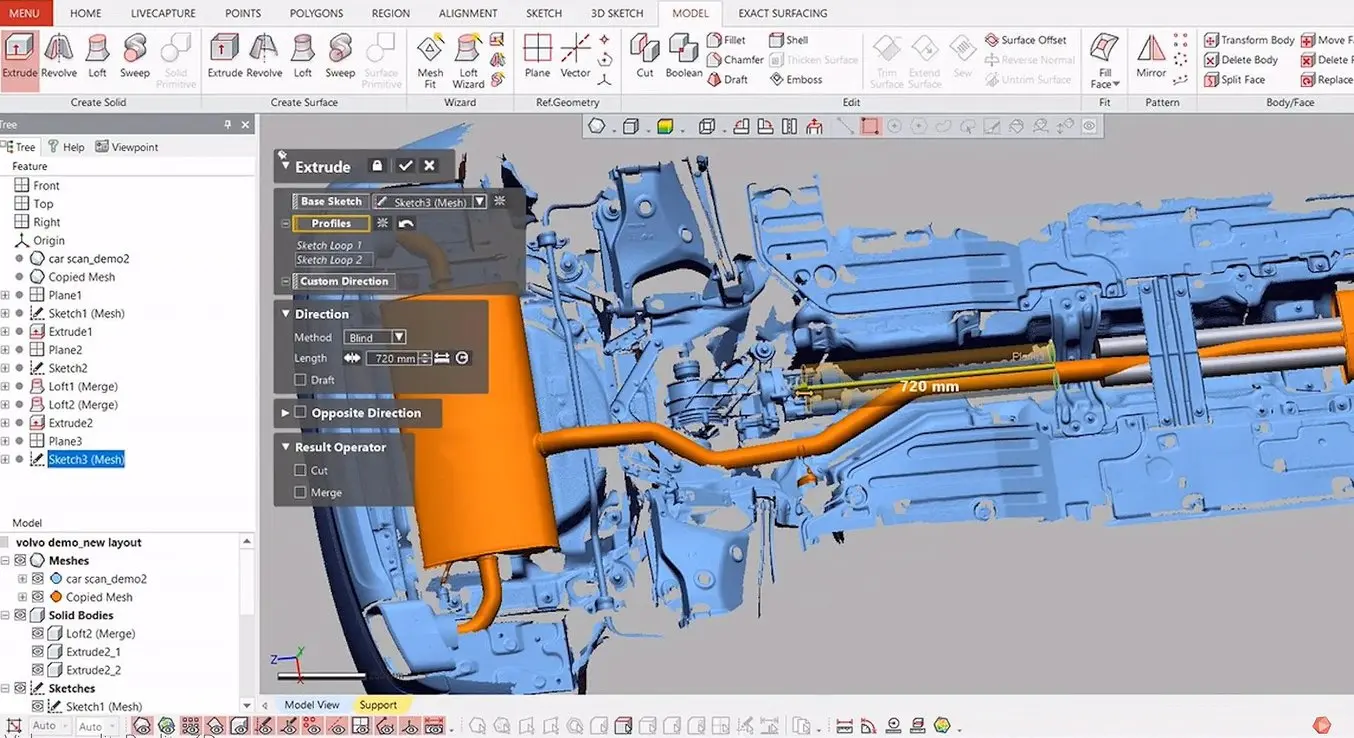
Ein Reverse Engineer konnte mit Artec Studio Teile des Unterbodens eines Volvo XC90 in weniger als einer Stunde scannen und reproduzieren, um ein neues Auspuffsystem zu entwickeln.
Fusion 360
Autodesk Fusion 360 gehört zu den beliebtesten Tools für das Reverse Engineering. Es handelt sich um ein cloudbasiertes CAD-System, das eine Lösung der Mittelklasse darstellt, da es nur einfache Gittermodelle verarbeitet und im Vergleich zu den Branchenführern eine begrenzte Auswahl geometrischer Operationen bietet.
Fusion 360 erlaubt verschiedene Ansätze für den Arbeitsprozess vom Gittermodell zum Festkörper, wie etwa die Isolierung von Konturen im Arbeitsbereich für Gittermodelle. Zudem verfügt es in verschiedenen Arbeitsbereichen über vielfältige Analysetools für die Belastungssimulation und topologische Optimierung. Da es in Meshmixer integriert ist, bietet es auch immer zuverlässigere Tools zur Reparatur von Gittermodellen.
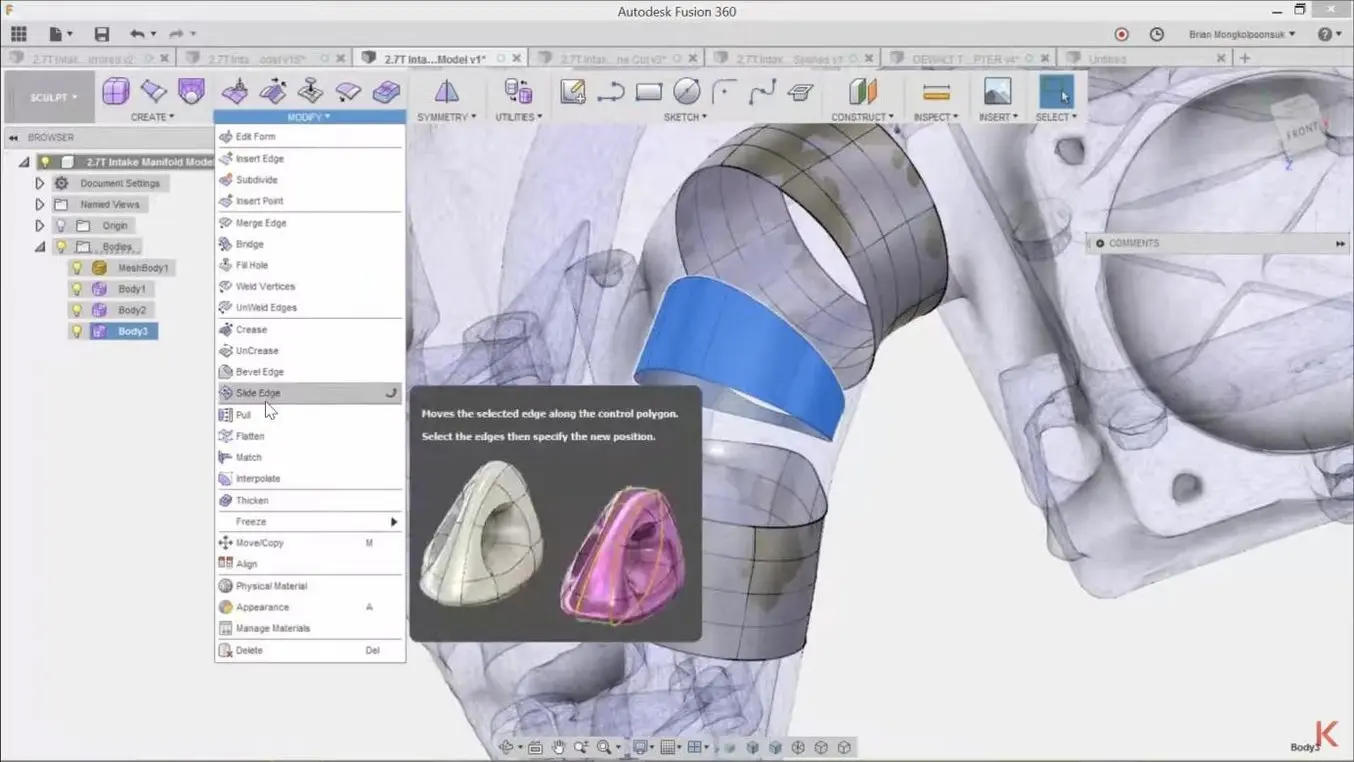
Fusion 360 stellt eine ausgezeichnete Lösung in der mittleren Preisklasse dar und bietet eine breite Palette an polygonalen Modellierungswerkzeugen zur Anpassung der Gittergeometrie.
Geomagic Design X
Geomagic ist die Spitzenlösung zur Umwandlung von 3D-Scandaten in funktionierende CAD-Modelle. Eine präzise Rekonstruktion wird sichergestellt durch das Nachzeichnen von Umrissen verschiedener Abschnitte des Gittermodells. Die Auswahlbürste ermöglicht das Einbeziehen oder Ausschließen spezifischer Bereiche für die verschiedenen Schritte des Rekonstruktionsprozesses. Zudem bietet die Software eine leistungsstarke Funktion für die automatische Oberflächenerstellung, die die Arbeit erleichtert.
Die Benutzeroberfläche fühlt sich vertraut an, da sie SolidWorks ähnelt. Das „Live Transfer“-Werkzeug exportiert sogar den Verlauf in eine dedizierte CAD-Modellierungsumgebung wie NX, Creo, Inventor, Pro/Engineer oder SolidWorks.
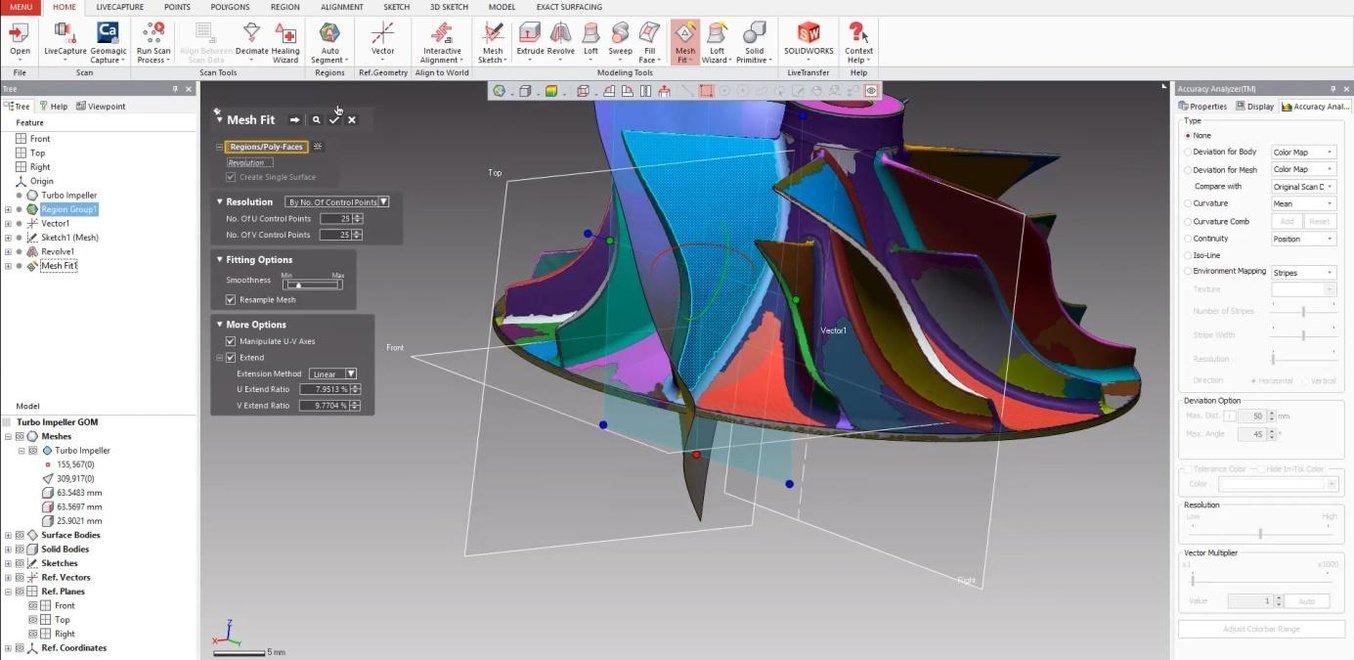
Mit fortschrittlichen Werkzeugen zur Oberflächenrekonstruktion bewältigt Geomagic Design X auch komplexe Reverse-Engineering-Designs wie beispielsweise dieses 3D-gescannte Turbolader-Laufrad.
Xtract3D
Für Design- und Ingenieurteams, die ihr Reverse Engineering lieber geschlossen innerhalb von SolidWorks halten, ist Xtract3D ein unverzichtbares Plugin. Es ermöglicht den direkten Import von Gittermodellen oder Punktwolken-Daten, ist aber nur eine vereinfachte Alternative zu leistungsstärkeren Reverse-Engineering-Paketen, da es in erster Linie auf einfachere Geometrie ausgerichtet ist.
Dennoch verfügt es über lobenswerte Werkzeuge. Xtract3D bietet leistungsstarke Schneide-, Skizzier- und Rastertools. So zeichnen Designteams direkt über 2D-Querschnitte der 3D-Scan-Daten und erstellen mühelos parametrische Modelle.
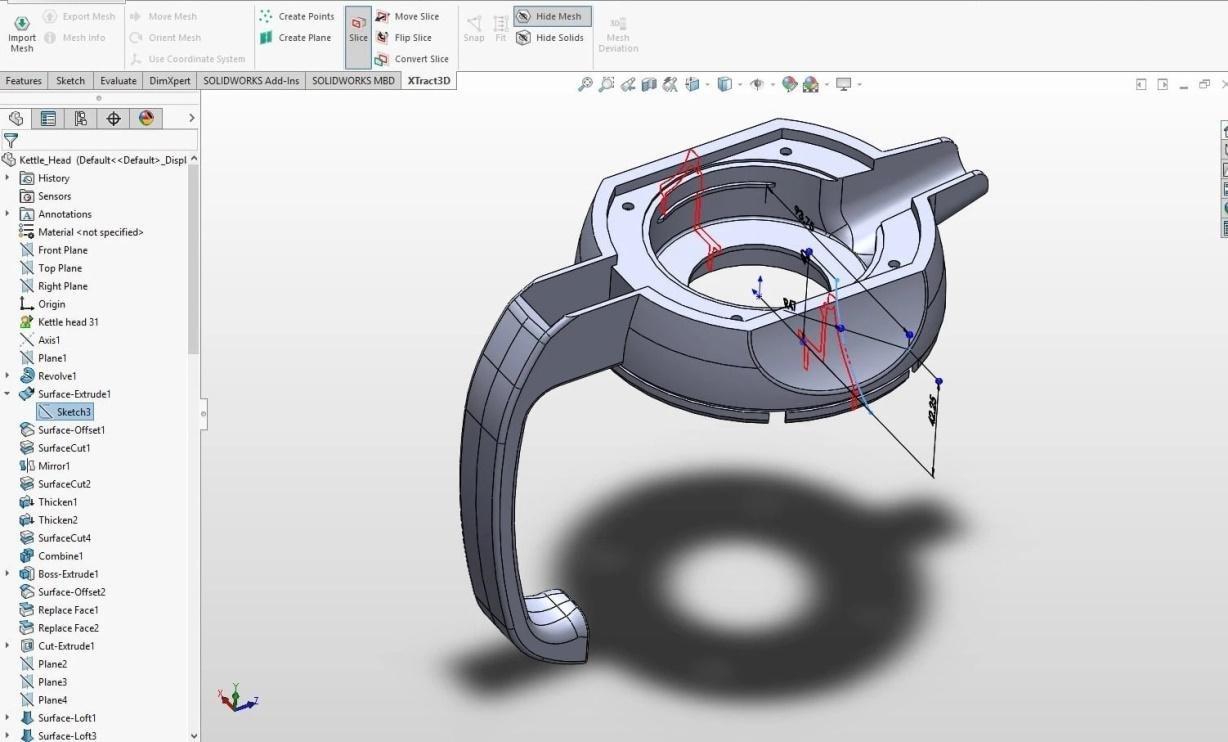
Xtract3D für SolidWorks umfasst die nötige Funktionalität, um Konsumgüter wie dieses Wasserkocheroberteil auf Basis von 3D-Scan-Daten nachzubilden.
Ansys SpaceClaim
SpaceClaim ist eine renommierte und innovative CAD-Software mit fortgeschrittenen Reverse-Engineering-Funktionen. Sie ist die bevorzugte Lösung für Direktmodellierungen mit einem Schwerpunkt auf Freiheit und Geschwindigkeit – verglichen mit den komplexen Abläufen des engen Definierens der Geometrie in parametrischen Modellierungsumgebungen mit Verlaufsbäumen.
Intelligente Funktionen wie Merkmalsidentifikation, Skin Surface und Push/Pull-Bearbeitung zeichnen SpaceClaim aus, wenn es darum geht, den Reverse-Engineering-Ablauf zu optimieren. Während des Rekonstruktionsprozesses erkennt die Software automatisch gewünschte Modellierungsvorgänge und macht Vorschläge für eine optimale Neugestaltung mit äußerst präzisen Ergebnissen.
Darüber hinaus können Ingenieurteams, die mit SpaceClaim arbeiten, ihr Modell problemlos mit anderen Ansys-Modulen verknüpfen, wie zum Beispiel solchen für CFD oder mechanische Simulationen.
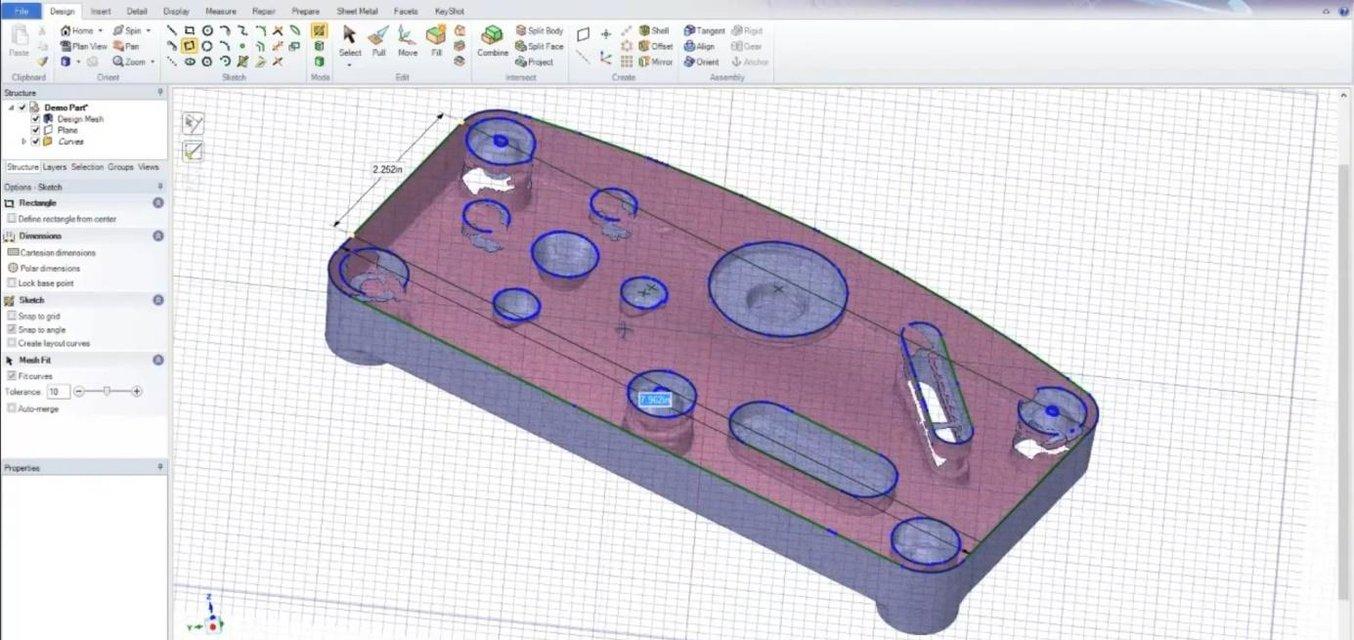
SpaceClaim erkennt automatisch Merkmale und fügt neue Geometrie an das ursprüngliche Gittermodell an, um den Umbauprozess schnell und präzise zu gestalten.
Tebis Reverser
Tebis bietet eine spezialisierte Reverse-Engineering-Umgebung für das Automobildesign. Die Software wurde in Zusammenarbeit mit der BMW Design Group entwickelt, um den Übergang vom Ton-Modell zum CAD-Design zu erleichtern. Auf diese Weise verbringen Designteams mehr Zeit mit dem manuellen Designprozess, bevor man in die 3D-Welt eintaucht.
Das Reverser-Softwarepaket analysiert Gittermodelldaten und erstellt eine Drahtgitterstruktur, die anschließend zur Generierung einzelner Oberflächen dient. Diese Oberflächen werden analysiert und gemäß dem Industriestandard bis zur höchsten Qualitätsklasse geglättet.
Neben einer Vielzahl manueller Steuerungsparameter können Oberflächen auch automatisch berechnet und Übergänge in großem Detail gesteuert werden, ganz ohne tiefgehende Fachkenntnisse. Die assoziative Oberflächentechnologie sorgt dafür, dass das Gittermodell und die generierten Oberflächen verknüpft bleiben, um konstante Übergänge und sanfte Oberflächenprogressionen sicherzustellen.
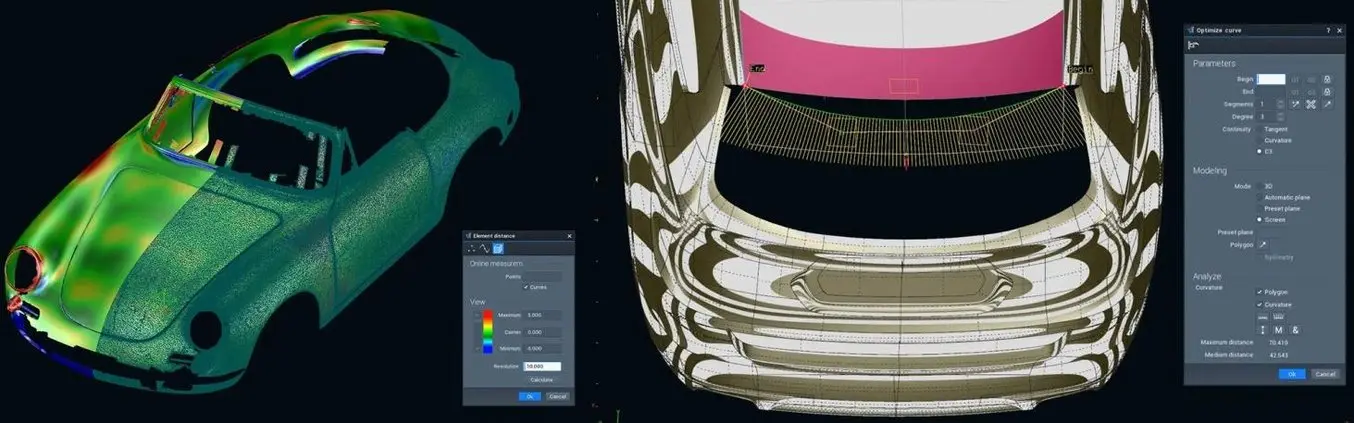
Tebis Reverser ist eine zuverlässige Lösung für hochwertige Oberflächenmodelle anhand von 3D-Fahrzeugscans.
PTC Creo
Creo ist ein parametrisches Modellierungspaket, das sich für die Arbeit an Baugruppen aus über 1000 Teilen eignet. Es wird in den Bereichen Konsumgüter und Mobilität immer beliebter und wird von Branchengrößen wie Aston Martin, John Deere, Volkswagen, Toyota und Amazon genutzt.
Für Ingenieurteams interessant ist das gegen Aufpreis erhältliche Advanced-Plus-Paket, in dessen Rahmen zusätzlich ein erweitertes Feature-Set rund um Flächenmodellierung, Slicing für den 3D-Druck, GD&T, das Design von Gussformen sowie für Simulationen zur Verfügung steht.
PTC hat nun auch eine Reverse-Engineering-Erweiterung für sowohl Pro/Engineer als auch die professionelle Version Creo veröffentlicht. Nach dem Import von Punktwolkendaten und der Erstellung des Facetten-Gittermodells kann dieses bereinigt und seine Modellierungselemente automatisch mit der Restyle-Funktion extrahiert werden. Creo bietet dazu leistungsstarke Synthese- und Analysewerkzeuge für die Erstellung eines hochgenauen Modells mit durchgehender Krümmung.

Die Reverse-Engineering-Erweiterung für Creo und Pro/Engineer umfasst fortgeschrittene Werkzeuge für professionelle und präzise Ergebnisse.
VXElements
VXElements, Creaforms Softwarepaket glänzt mit einer Vielzahl von Modulen für den Scan-to-CAD-Prozess. Besonders erwähnenswert ist die Software VXModel, die als virtueller Assistent dient und Rohdaten aus einem Gittermodell in ein hochwertiges solides Modell umwandelt.
Die Highlights der Software sind die automatischen und manuellen Oberflächenwerkzeuge, Gitterbereinigungsfunktionen, Ausrichtungswerkzeuge und die Möglichkeit, Begrenzungen sowie Querschnitte zu extrahieren und zu bearbeiten. Darüber hinaus ermöglicht die Software den Export von Modellen für den 3D-Druck und die direkte Übertragung von Reverse-Engineering-Modellen in Inventor, SolidWorks und SolidEdge zur weiteren Bearbeitung.
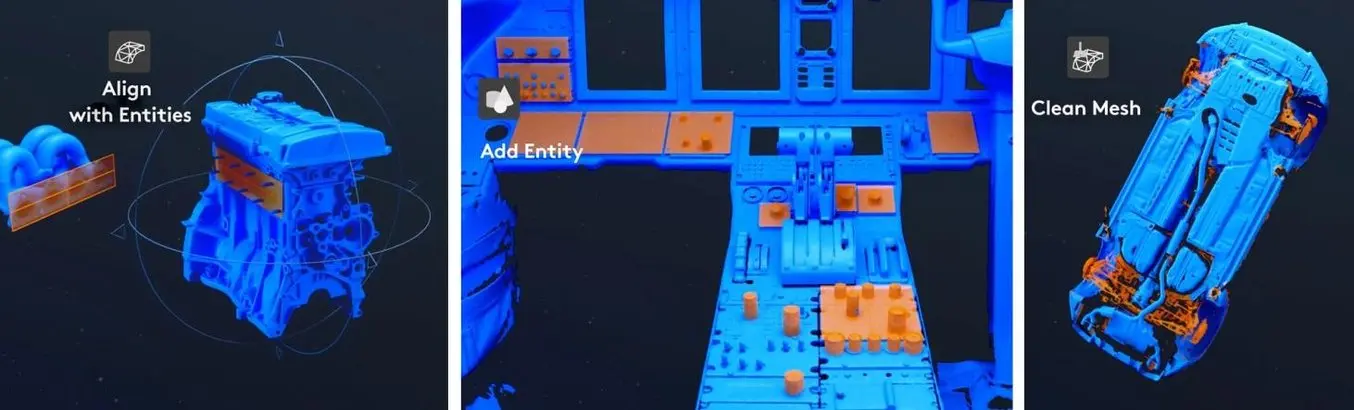
VXModel bietet eine breite Palette von Reverse-Engineering-Tools.
3D-Scanner für das Reverse Engineering
Durch den 3D-Druck von Reverse-Engineering-Teilen entwickeln Designteams ein tieferes Verständnis, welche Merkmale und Parameter den Erfolg beeinflussen. Darüber hinaus erlaubt er schnellere Verbesserungszyklen und sogar die Produktion von Endverbrauchsteilen.
Stereolithografie-3D-Drucker (SLA) verwenden einen Laser, um flüssige Kunstharze zu gefestigten Kunststoffen auszuhärten. Dieser Prozess nennt sich Photopolymerisation. SLA-Teile bieten die höchste Auflösung und Präzision, die filigransten Details und die glattesten Oberflächen aller 3D-Drucktechnologien für Kunststoffe. Außerdem hat SLA-Druck auch die breiteste Materialpalette.
SLA eignet sich ideal für hochdetaillierte Prototypen mit engen Toleranzen und glatten Oberflächen wie Gussformen, Modelle und Funktionsteile. SLA ist in vielen Branchen weit verbreitet, vom Maschinenbau und Produktdesign über die Fertigung, Zahntechnik, Schmuckherstellung und den Modellbau bis hin zur Bildung.
SLA-3D-Drucker für den Desktop wie der Form 3+ von Formlabs sind eine leistungsstarke und erschwingliche Lösung für Ihre Reverse-Engineering-Projekte. Und großformatige Kunstharz-Drucker wie der Form 3L von Formlabs bewältigen auch die größten Projekte.
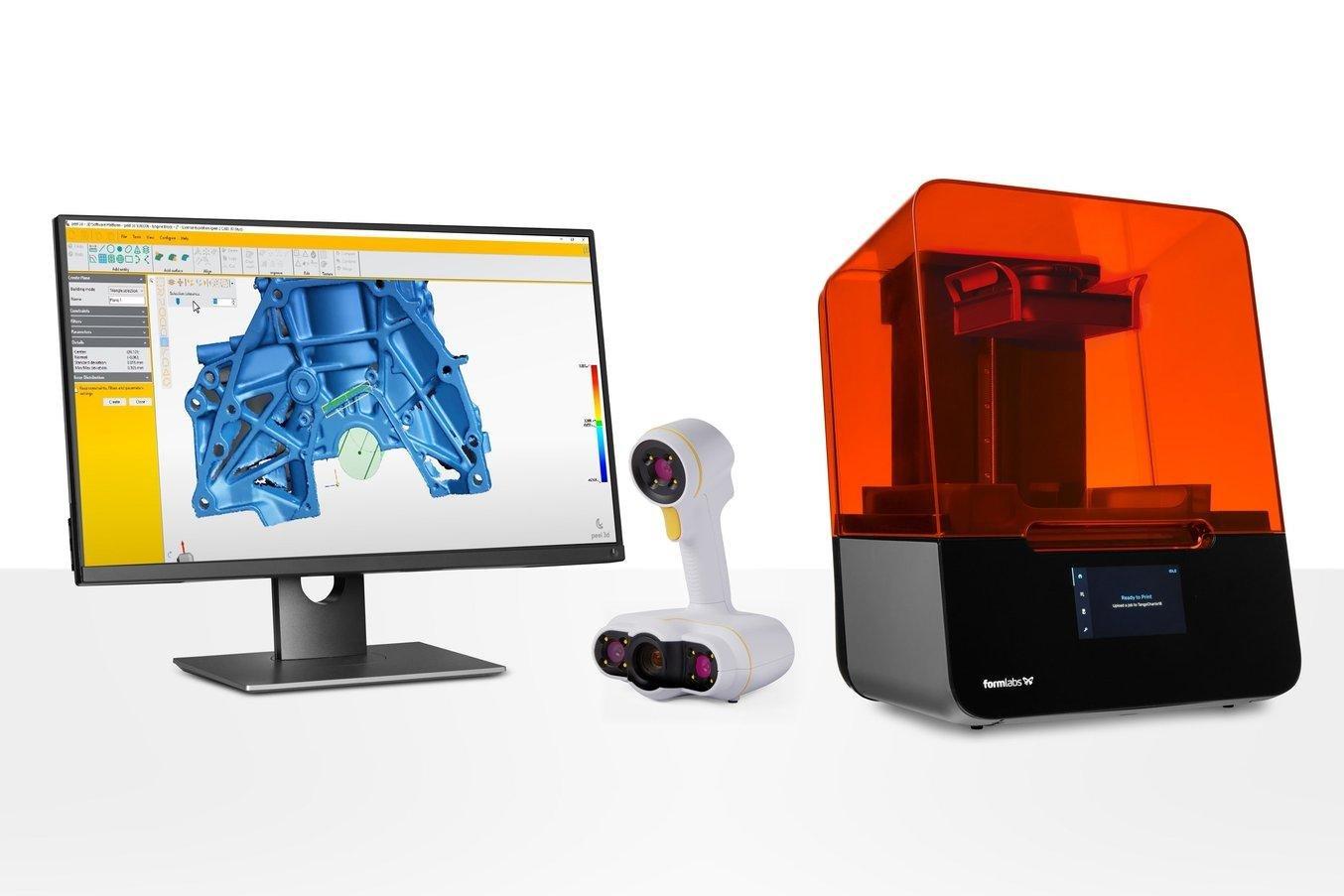
Desktop-SLA-3D-Drucker eignen sich ideal, um Reverse-Engineering-Designs in handfeste Teile zu verwandeln.
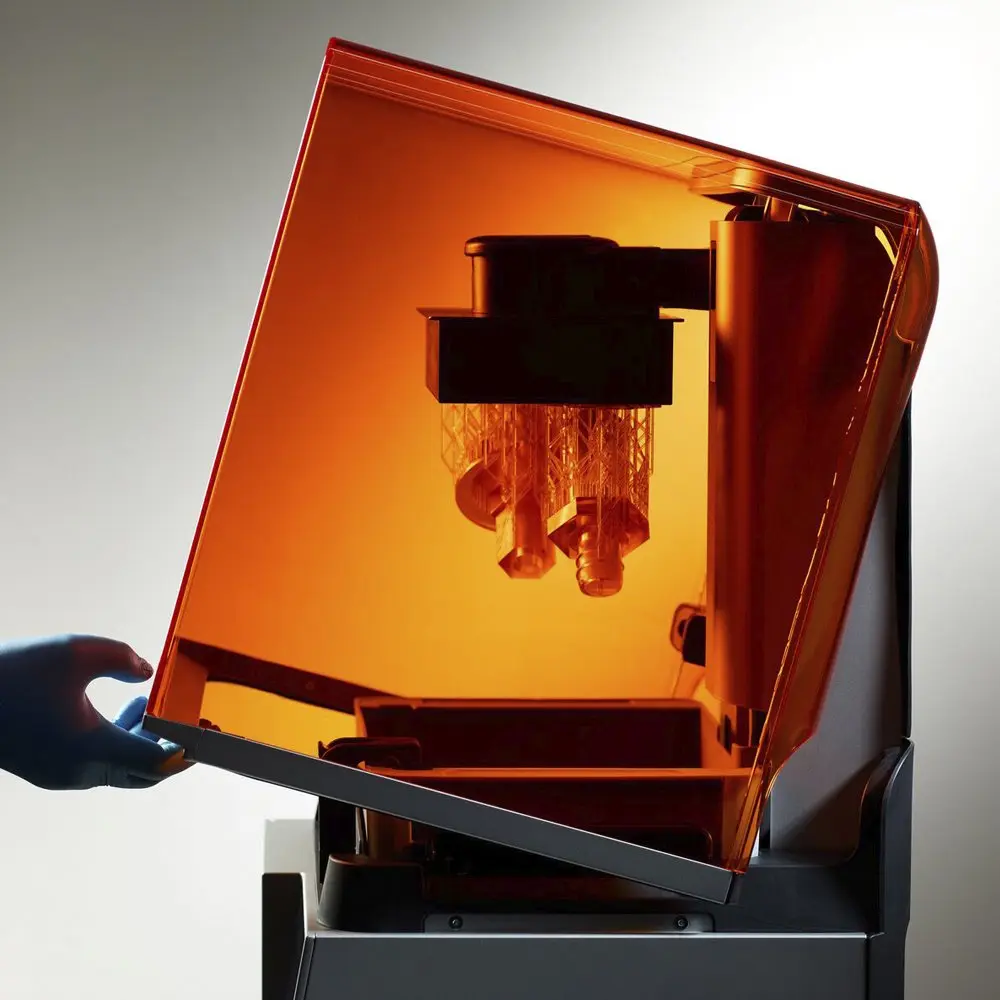
Einführung in den 3D-Druck mit Desktop-Stereolithografie (SLA)
Sie suchen einen 3D-Drucker, der Ihre 3D-Modelle in hochauflösender Qualität Wirklichkeit werden lässt? Lernen Sie in diesem Whitepaper das Verfahren der Stereolithografie (SLA) näher kennen – von seiner Funktionsweise bis hin zu den Gründen für seinen Status als populärste 3D-Drucktechnologie bei der Umsetzung hochgradig detailtreuer Modelle.
Selektives Lasersintern ist die am häufigsten genutzte Technologie der additiven Fertigung bei industriellen Anwendungen. Ingenieur*innen und Hersteller verschiedener Branchen vertrauen darauf, um starke und funktionsfähige Teile zu produzieren.
SLS-3D-Drucker verwenden einen Hochleistungslaser, um kleine Partikel aus Polymerpulver zu sintern. Da das ungesinterte Pulver das Teil beim Drucken stützt, sind keine zusätzlichen Stützstrukturen erforderlich. SLS eignet sich somit ideal für komplexe Geometrien wie Merkmale im Inneren von Teilen, Hinterschneidungen, dünne Wände und negative Details. SLS-Teile bieten Teile mit herausragenden mechanischen Eigenschaften, deren Festigkeit mit der von Spritzgussteilen vergleichbar ist.
Die Kombination aus geringen Kosten pro Teil, hoher Produktivität und bewährten Materialien macht SLS-Drucker wie die Fuse-Geräte von Formlabs zu einer beliebten Wahl für die Herstellung funktionsfähiger Prototypen. Selektives Lasersintern stellt auch eine kosteneffiziente Alternative zum Spritzguss bei der Kleinserienfertigung und beim Bridge Manufacturing dar.
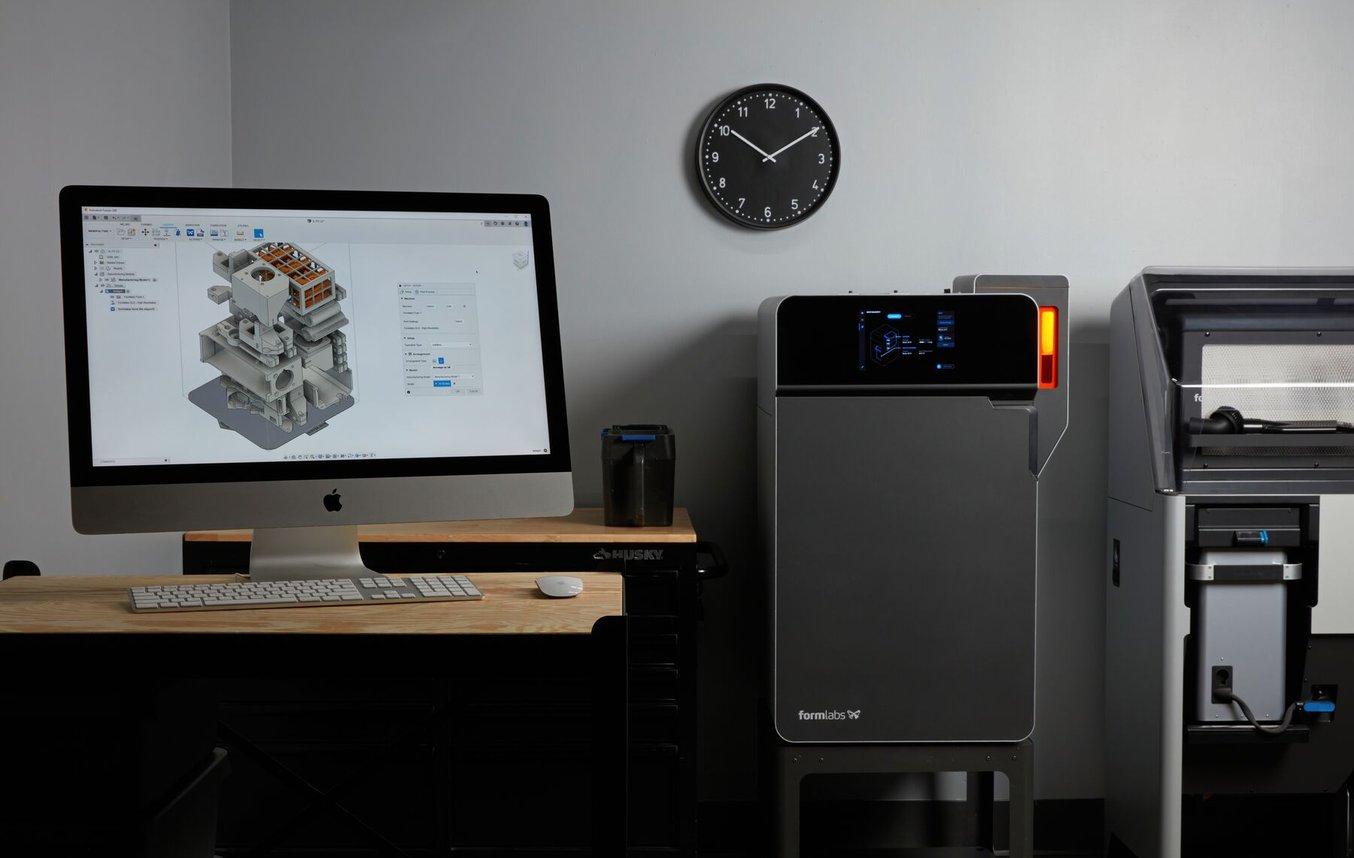
SLS-3D-Drucker sind die idealen Werkzeuge zum Reverse Engineering komplexer Geometrien.
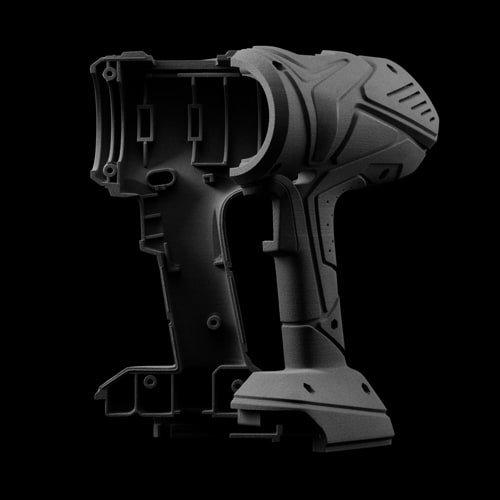
Einführung in den 3D-Druck mit selektivem Lasersintern (SLS)
Suchen Sie nach einem 3D-Drucker, mit dem Sie feste, funktionsfähige Teile herstellen können? Laden Sie unser Whitepaper herunter und erfahren Sie, wie der SLS-Druck funktioniert und wieso er ein beliebtes 3D-Druckverfahren für funktionales Prototyping und die Produktion von Teilen für die Endverwendung ist.
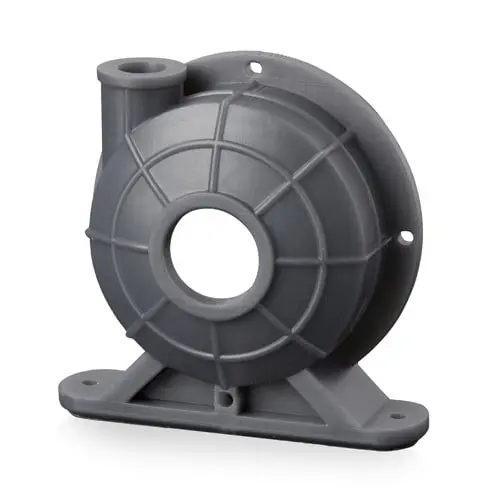
Kostenlosen Probedruck anfordern
Sehen und fühlen Sie die Qualität von Formlabs aus erster Hand. Wir senden Ihnen einen kostenlosen Probedruck an Ihren Arbeitsplatz.
Fallstudien: Reverse Engineering mit 3D-Scans und 3D-Druck
Reverse Engineering hat eine Vielzahl an Anwendungsbereichen. Betrachten wir einige echte Fallstudien, in denen der gesamte Arbeitsablauf vom 3D-Scannen bis zum 3D-Druck verwendet wurde, um Maßanfertigungen, Ersatzteile, Nachrüstteile und mehr zu erstellen.
Für den Branchenriesen im Bereich Kfz-Nachrüstteile, Dorman Products, ist Reverse Engineering das Herzstück des Geschäftsmodells. Dorman analysiert die Fehlerursachen von OEM-Bauteilen und konstruiert dann das Produkt über Reverse Engineering, wobei das Team das Design manchmal komplett neu entwickelt und optimiert. Oft muss das Team auch das Original-Bauteil beschaffen, wozu es manchmal ganze Autos kauft, um die Konstruktion des Fahrzeugs vollkommen zu verstehen und das verbesserte Design zu validieren.
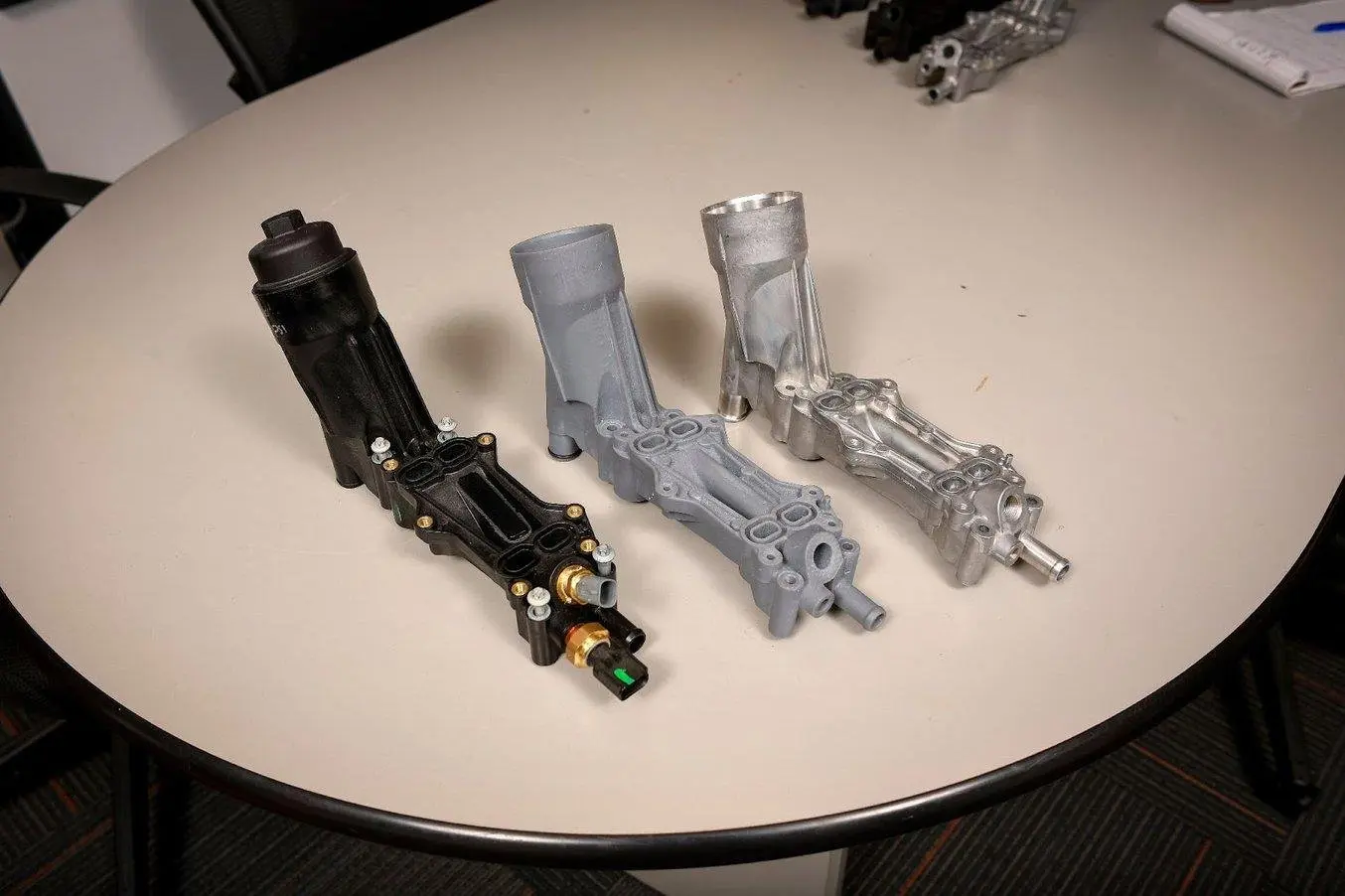
Dorman Products arbeitet mit den SLA-3D-Druckern von Formlabs, um die Prototypen der Aftermarket-Produkte herzustellen.
Ingenieur*innen der STS Technical Group verwendeten einen 3D-Scanner von Creaform und die Software VXElements, um einen maßgefertigten Greifer für einen Pick-and-Place-Roboter zu entwickeln und dessen Kompatibilität mit einer spezifischen Kraftstoffeinspritzdüse zu verbessern. Die Ergebnisse waren dem kommerziellen Produkt selbst weit überlegen.
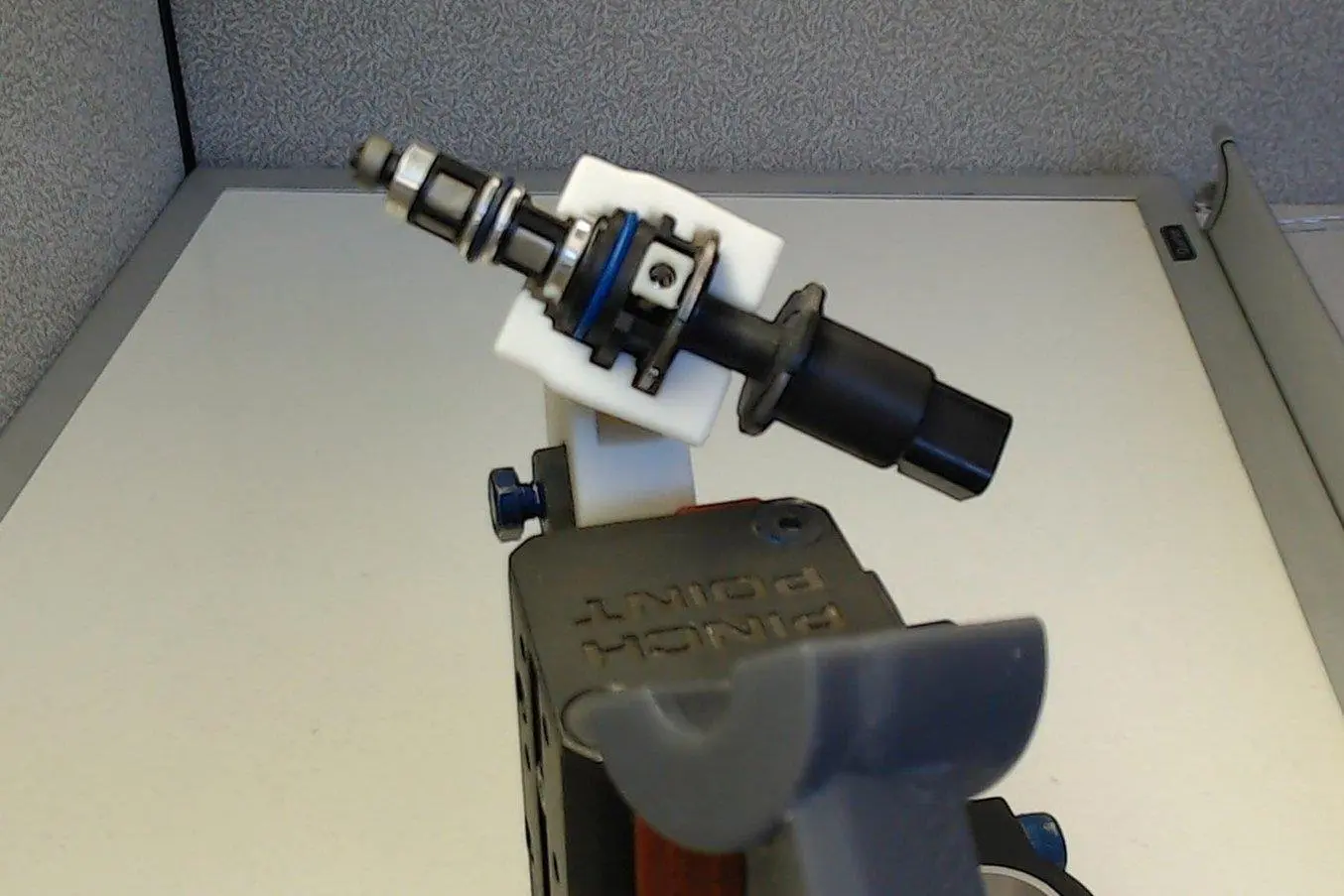
Das Team der STS Technical Group nutzte SLA-3D-Druck, um die maßgefertigten Roboter-Greifer herzustellen.
In einem anderen Projekt entwickelte das Team von Help3D einen maßgefertigten Ansaugkrümmer für ein professionelles Rennmotorrad. Es verwendete 3D-Scans, um ein präzises Modell des Viertaktmotors und der umgebenden Baugruppe zu erstellen. Dann kam Fusion 360 für den Reverse-Engineering-Prozess zum Einsatz. Das luftdichte 3D-Druckergebnis wurde dann mithilfe eines Formlabs-SLA-Druckers und Rigid 10K Resin hergestellt und führte zu einer Leistungssteigerung von 10 %.
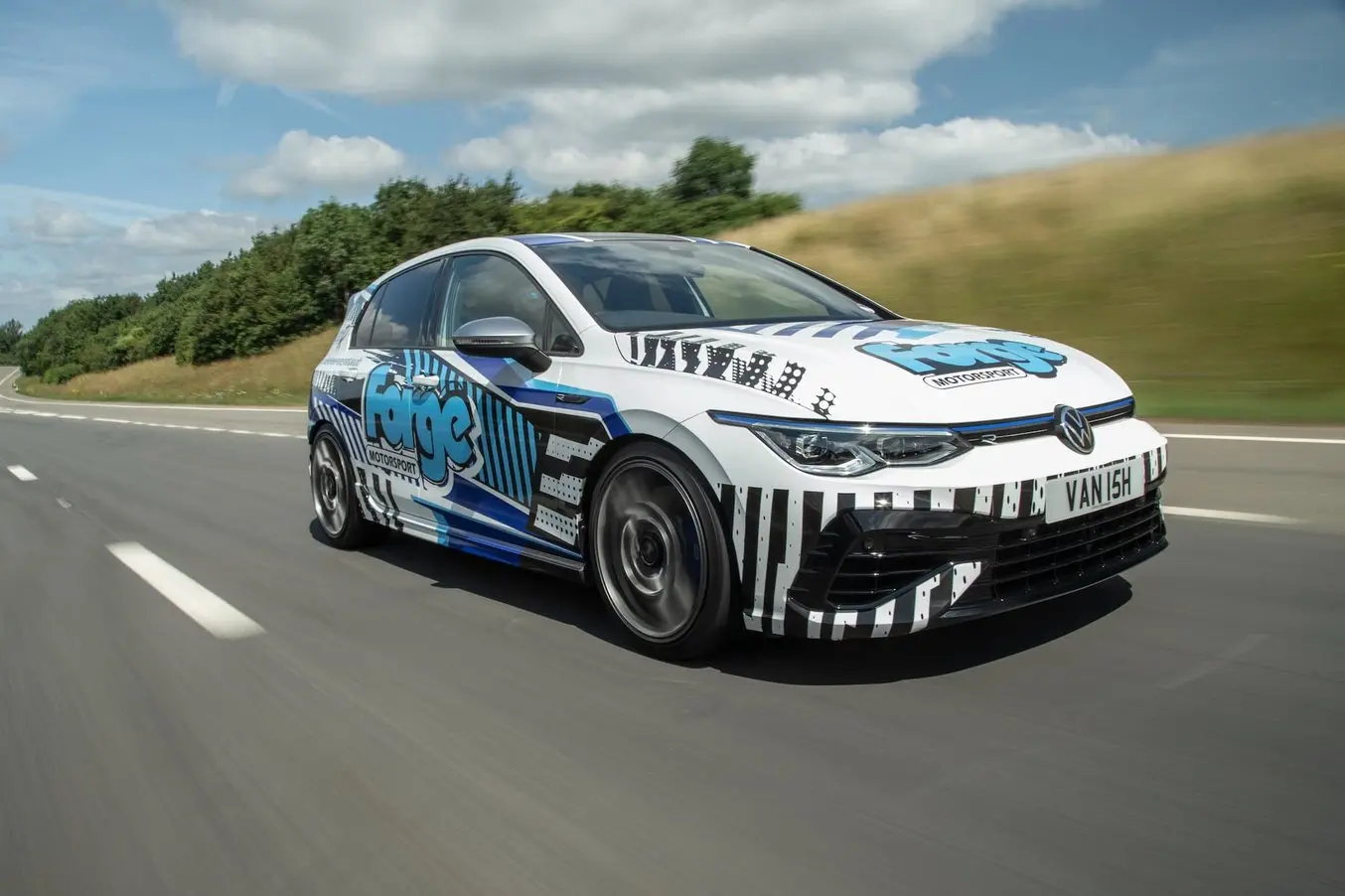
3D-Scan und 3D-Druck in der Automobilindustrie mit Forge Motorsport
In diesem Webinar gibt Forge Motorsport, ein Entwickler von Leistungssteigerungen für die Automobil-Aftermarket-Branche, Einblicke in die Nutzung von 3D-Druck- und 3D-Scan-Technologien zur Verbesserung der Arbeitsabläufe.
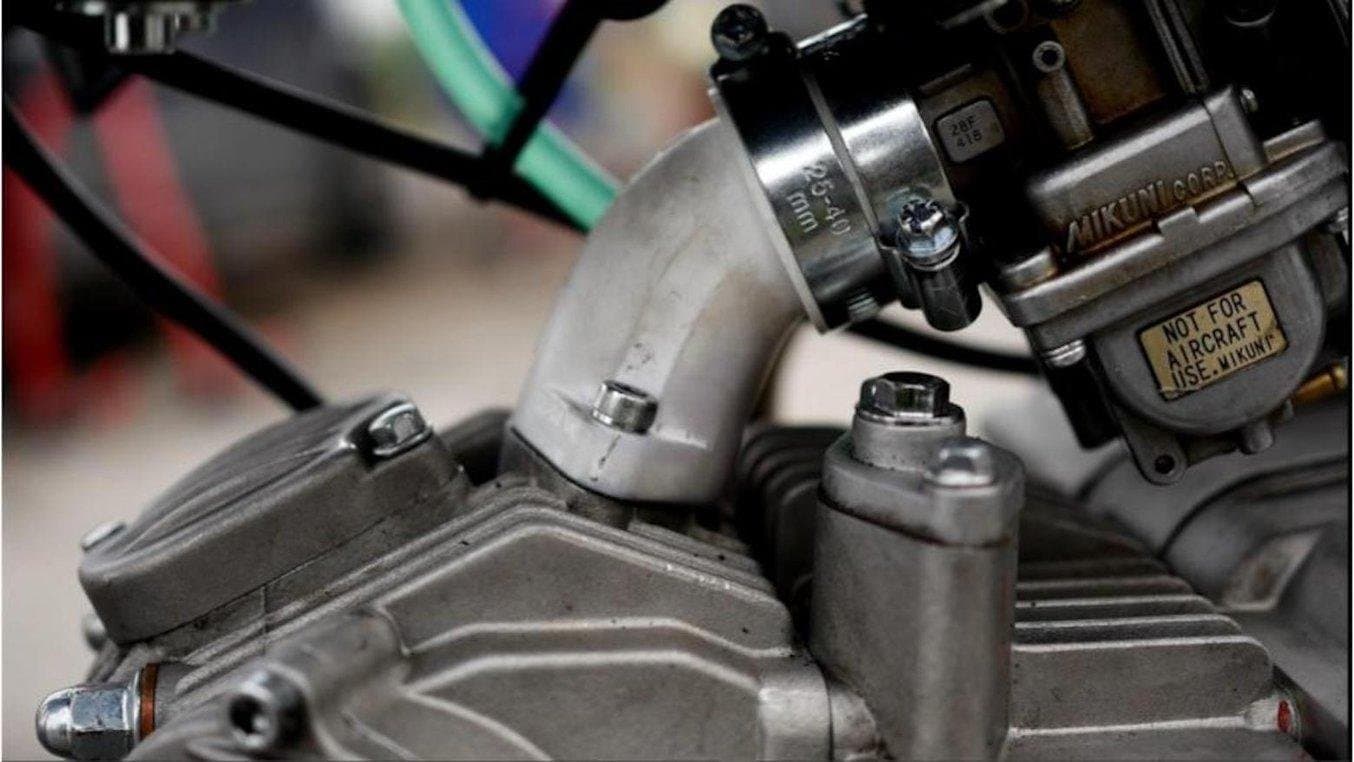
Der im Reverse Engineering erstellte Ansaugkrümmer wurde aus einem hitzebeständigen Material 3D-gedruckt.
Die Möglichkeiten des Reverse Engineerings erweisen sich auch als äußerst hilfreich bei der Herstellung von Ersatzteilen für industrielle Produktionsgeräte. In einem konkreten Fall gelang es Productive Plastics, ein Laufrad für eine Thermoformmaschine rückzuentwickeln. Mithilfe eines SLS-Druckers der Fuse-Serie wurde ein strapazierfähiges Ersatzteil gedruckt, das als temporäre Lösung diente und dazu beitrug, Ausfallzeiten des Unternehmens zu minimieren.
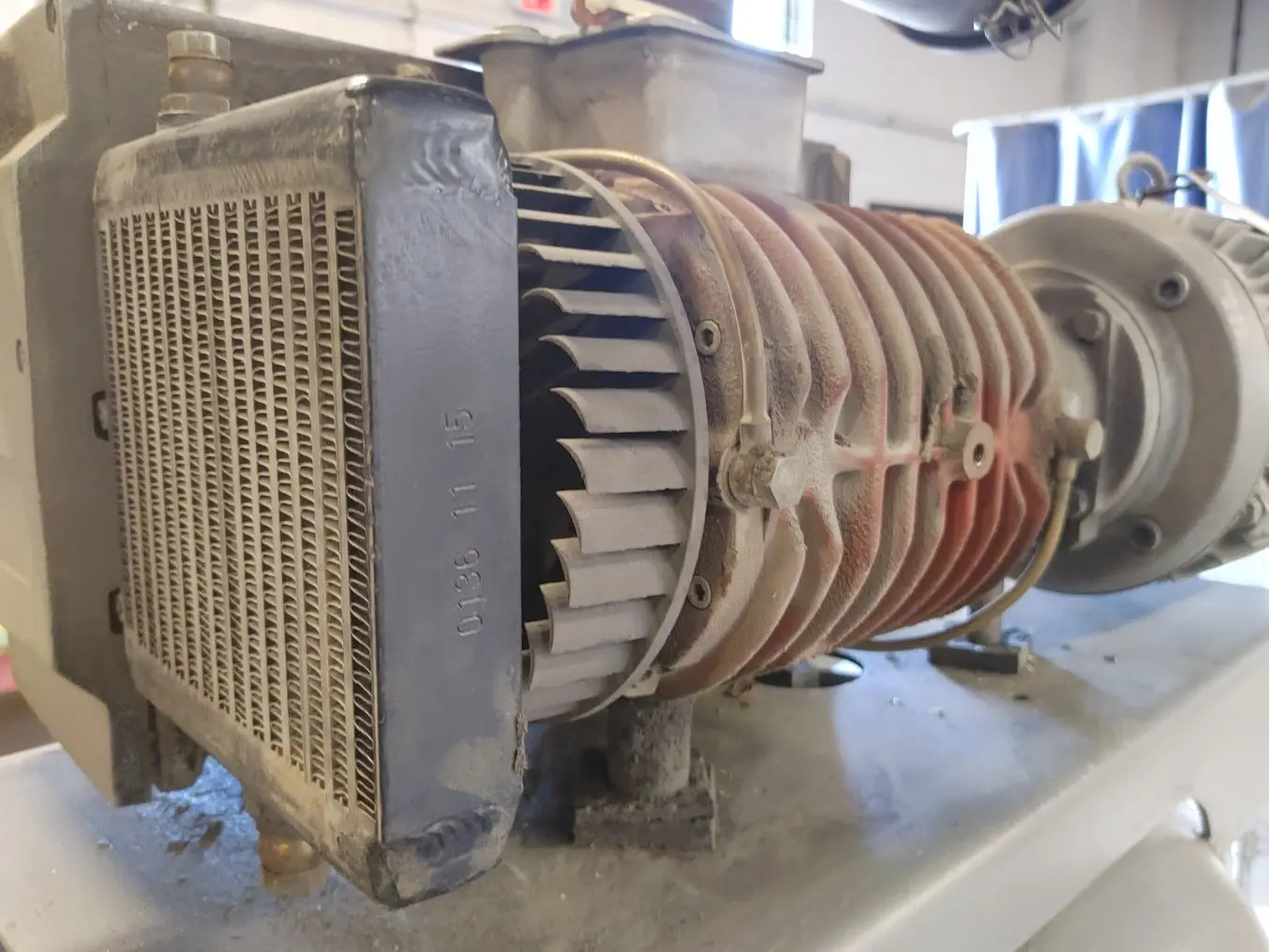
Eine Nahaufnahme (rechts) und eine Gesamtansicht (links) des 3D-gedruckten Laufrads, das sich nahtlos in die Vakuumpumpe der industriellen Thermoformmaschine einfügt.
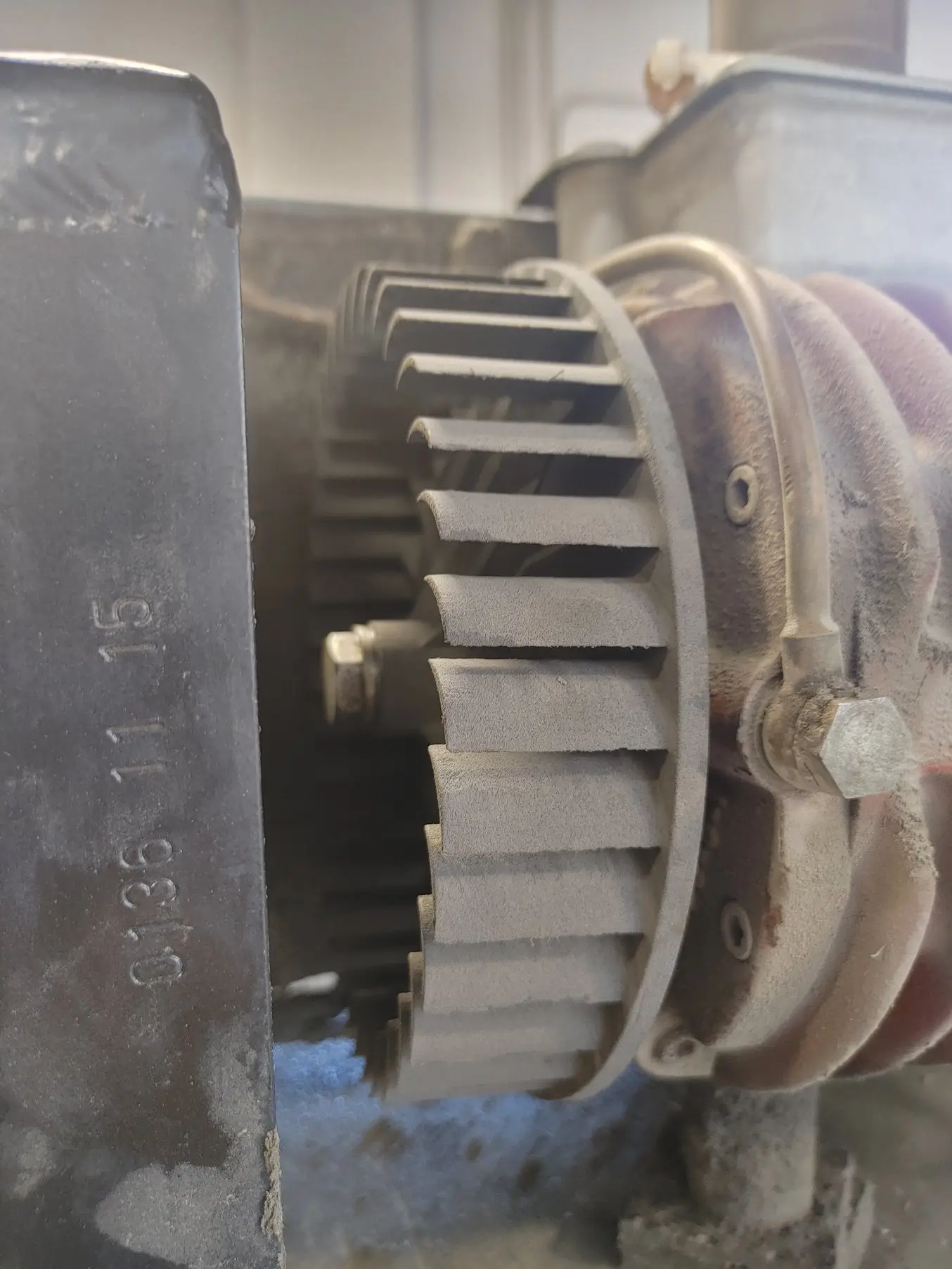
Erste Schritte im Reverse Engineering
Früher war es eine gewaltige Aufgabe, selbst ein einfaches Bauteil bewaffnet nur mit einem Messschieber, einem Bleistift und Zeichenpapier manuell rückzuentwickeln. Glücklicherweise gehören diese Zeiten der Vergangenheit an. Moderne Reverse Engineers verfügen über ein beeindruckendes Arsenal an Werkzeugen, um Erstaunliches zu erreichen.
Wie bereits erläutert, beginnt der heutige Reverse-Engineering-Prozess mit einem hochwertigen 3D-Scan. Anschließend werden die Daten in ein Drahtgitter übersetzt, das für die Oberflächenüberarbeitung in einer hochmodernen CAD-Umgebung verwendet wird. Hier können Design- und Ingenieurteams das Teil perfektionieren.
Dies ist besonders hilfreich, wenn es um organisch geformten Objekte geht, die teuer zu beschaffen sind, keine digitale Darstellung haben, überarbeitet werden müssen oder Ersatz- oder Reparaturteile benötigen. Mit herausragenden Reverse-Engineering-Fähigkeiten sind Teams außerdem in der Lage, bestehende Lösungen auf Herz und Nieren zu prüfen, ohne das Rad neu zu erfinden.
In all diesen Fällen haben hochmoderne SLS- und SLA-3D-Drucker wie unsere Fuse-Serie und unser Form 3+ ihren revolutionären Wert bewiesen, indem sie professionelle Prototypen und Teile in höchste Qualität noch am selben Tag ermöglichen. Unternehmen in allen Branchen beschleunigen so ihre Produktentwicklung und fördern neue Innovationen.