Serienproduktion von professionellen Lautsprechersystemen mittels SLS-3D-Druck in der Pro-Audio-Branche
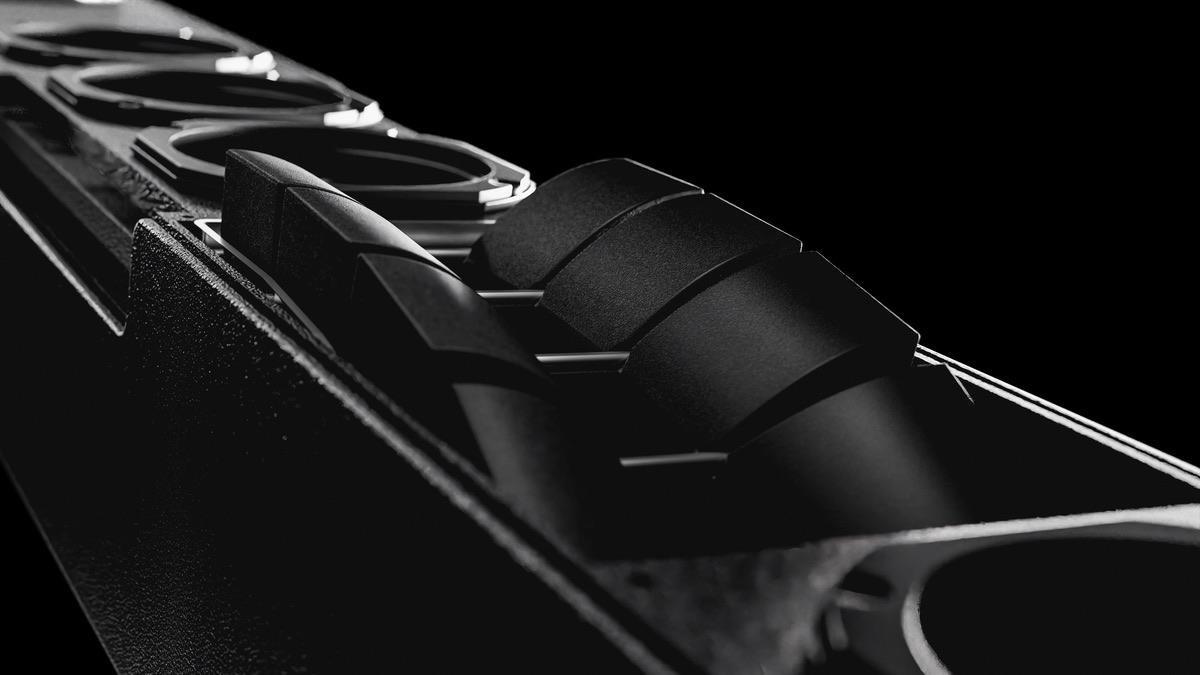
Durch die ständige Weiterentwicklung ihrer Technologien, das moderne Design und die flexiblen Einsatzmöglichkeiten setzten sich die Beschallungssysteme von Kling & Freitag von ihrer Konkurrenz ab.
Schon seit 20 Jahren nutzt der Ausstatter für statische sowie temporäre Soundsysteme die additive Fertigung in der Entwicklung seiner Produkte. Zunächst noch für das Rapid Prototyping, doch seit Kurzem auch für die Serienproduktion von Elementen eines innovativen Lautsprechersystems PIA M, welches sich perfekt an seine Umgebung anpasst.
Im Interview mit André Figula, tätig in der Konstruktion bei Kling & Freitag, erzählt er von seiner langjährigen Erfahrung mit additiver Fertigung, den Vorteilen des 3D-Drucks in der Konstruktion und wie dieser voraussichtlich auch in Zukunft die Innovation bei Kling & Freitag vorantreiben wird.
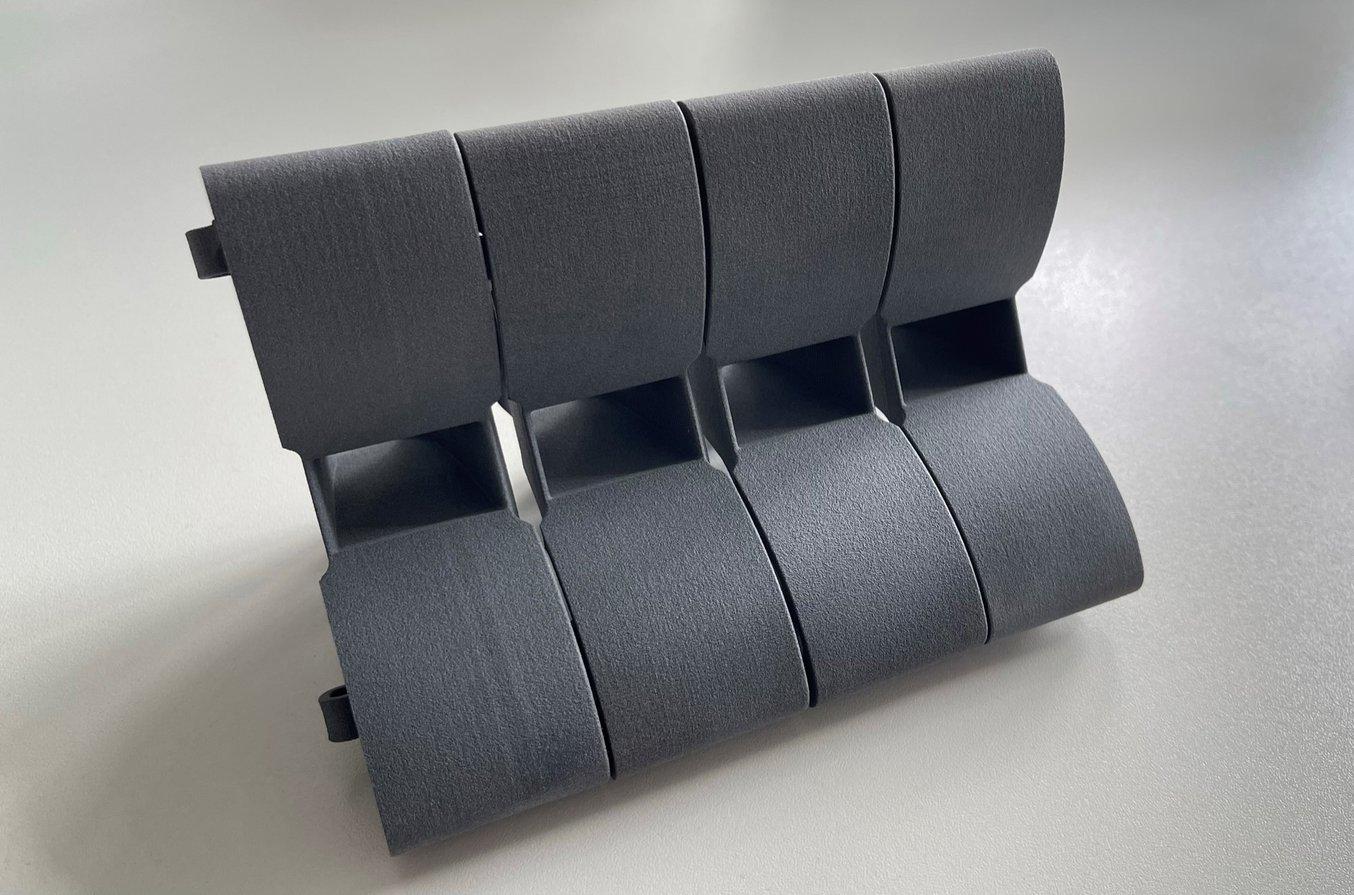
SLS-Serienfertigung in der Pro-Audio-Branche
Der gute Ton macht die Musik: Erfahren Sie von André Figula, Design-Ingenieur bei Kling & Freitag, wie der SLS-3D-Druck von Formlabs in der Fertigung ihrer Lautsprechersysteme zur Anwendung kommt.
Professionelle Beschallungssysteme und Lautsprechersysteme seit über 30 Jahren
Mit erstklassigem Klang und einem breitem Portfolio an professionellen Beschallungssystemen überzeugen – das sind die Stärken der Firma Kling & Freitag.
Gegründet 1991, stattet Kling & Freitag heute zahlreiche Theater, Stadien und Konzerthäuser weltweit mit innovativen Soundsystemen aus. Auch für temporäre Zwecke wie Festivals, Messen oder auf Open-Air-Veranstaltungen bieten sie ihre Lautsprechersysteme als Service an.
2018 schloss Kling & Freitag z.B. mit dem akustischen Hauptbeschallungssystem des Großen Konzertsaals der Elbphilharmonie in Hamburg eines der vielen renommierten Projekte ab.
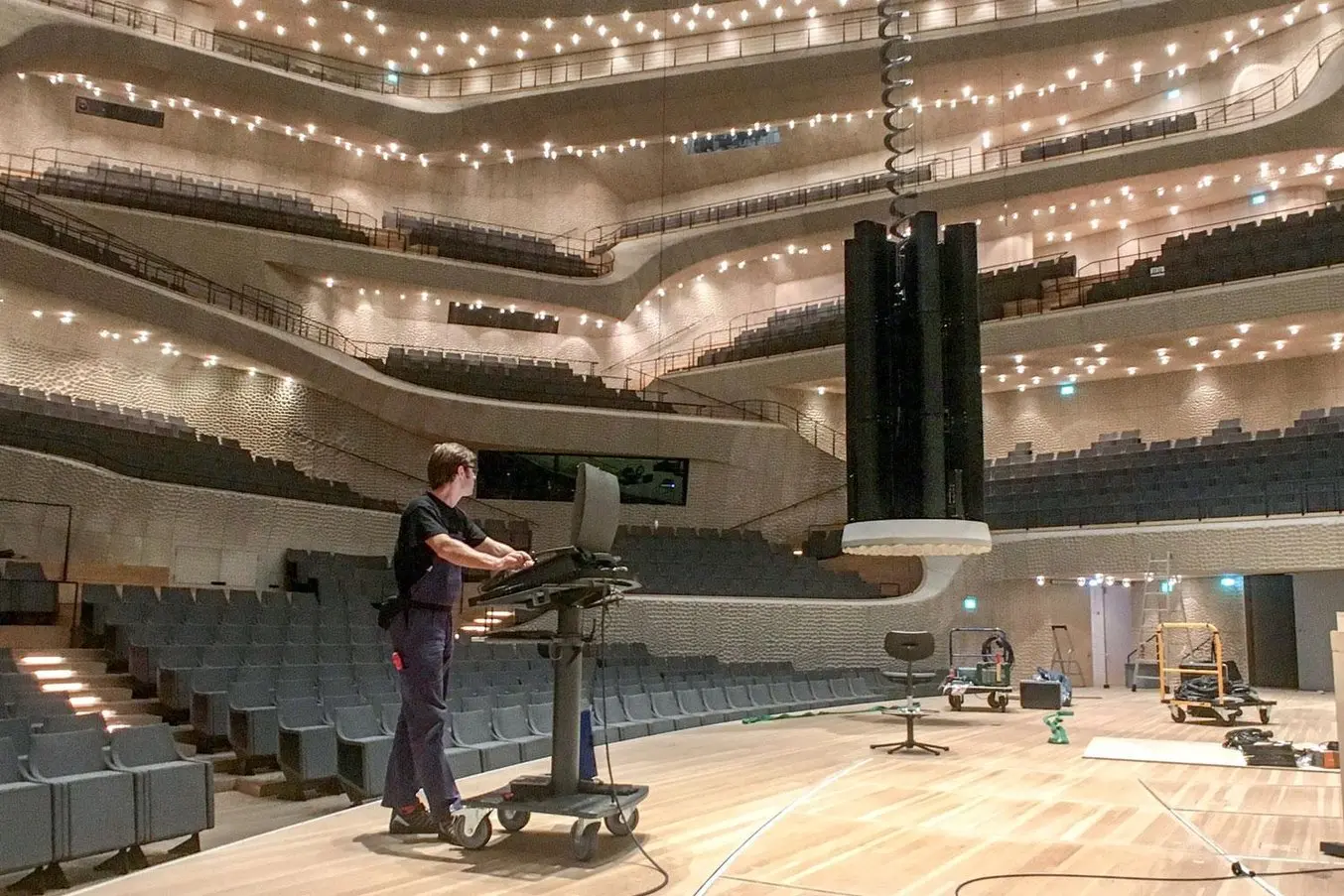
Der von der Decke hängende VIDA L Lautsprecher-Cluster von Kling & Freitag im Großen Saal der Elbphilharmonie verleiht dem gesamten Saal ein extravagantes Klangerlebnis.
Neben der klanglichen Leistung der Produkte beeindrucken die Systeme von Kling & Freitag außerdem optisch. Vor allem in der Zusammenarbeit mit Architekten kommen die schlanken und häufig kaum sichtbaren Lautsprecherelemente gut an.
Hausinterner SLS-3D-Drucker
3D-Druck kommt bei Kling & Freitag schon lange zum Einsatz. Bereits Anfang der 2000er Jahre wurde Figula auf die Option der additiven Fertigung aufmerksam. Damals entwickelten er und sein Team sogenannte Hochtonhörner noch in wochenlanger Handarbeit, um den Anforderungen ihrer Kunden an die Präzision und die damit einhergehende Klangqualität gerecht zu werden.
Zu dieser Zeit waren SLS-3D-Drucksysteme mit Preisen von über 200 000 € jedoch noch so kostspielig, dass das Team sich dafür entschied, funktionale Prototypen in Zusammenarbeit mit Dienstleistern der additiven Fertigung herzustellen. So sparte es schon damals Wochen an Arbeitszeit und konnte die Prototypen direkt in die Lautsprecher einbauen, um sie zu testen.
Mit der Einführung des Fuse 1 kam dann ein Drucker auf den Markt, der die Kosten für den SLS-3D-Druck um etwa ein 10-faches senkte und somit kleinen und mittleren Unternehmen wie Kling & Freitag die perfekten Einstiegsmöglichkeiten für die betriebsinterne additive Fertigung bot.
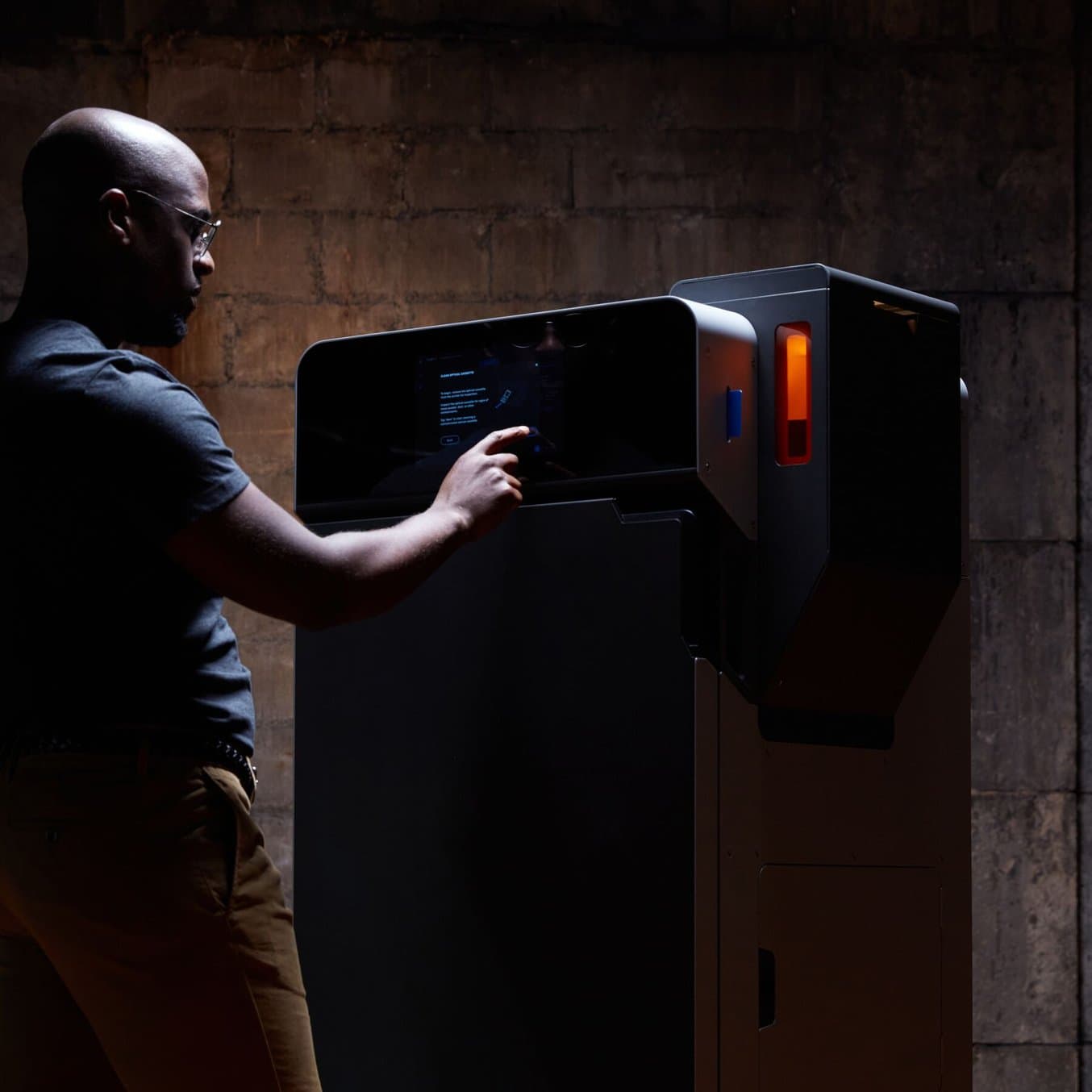
Outsourcing oder betriebsintern: Wann sollte man SLS-3D-Druck in den eigenen Betrieb holen?
In diesem Whitepaper untersuchen wir den Mehrwert von betriebsinternem selektiven Lasersintern (SLS) im Vergleich zum Outsourcing von SLS-Teilen an einen Fertigungsdienstleister.
Serienproduktion des neuen Waveguides mit dem Fuse 1
Eine von Kling & Freitags jüngsten Produkteinführungen ist der innovative Säulenlautsprecher PIA M. Das Besondere: Das sogenannte Hochtonhorn oder auch Waveguide des Lautsprechers ist durch den Einbau von vier verstellbaren Horn-Arrays anpassungsfähig an seine jeweilige Umgebung. Eine gleichbleibende Klangqualität beim mobilen Einsatz in immer wechselnden Räumlichkeiten oder für unterschiedliche Publikumsgrößen ist nicht einfach zu realisieren. Durch die ausgeklügelte Mechanik des PIA M kann die Akustik immer wieder neu angepasst werden und sorgt so für eine gleichmäßige Pegelverteilung über das jeweilige Publikum, egal in welcher Umgebung das Gerät zum Einsatz kommt.
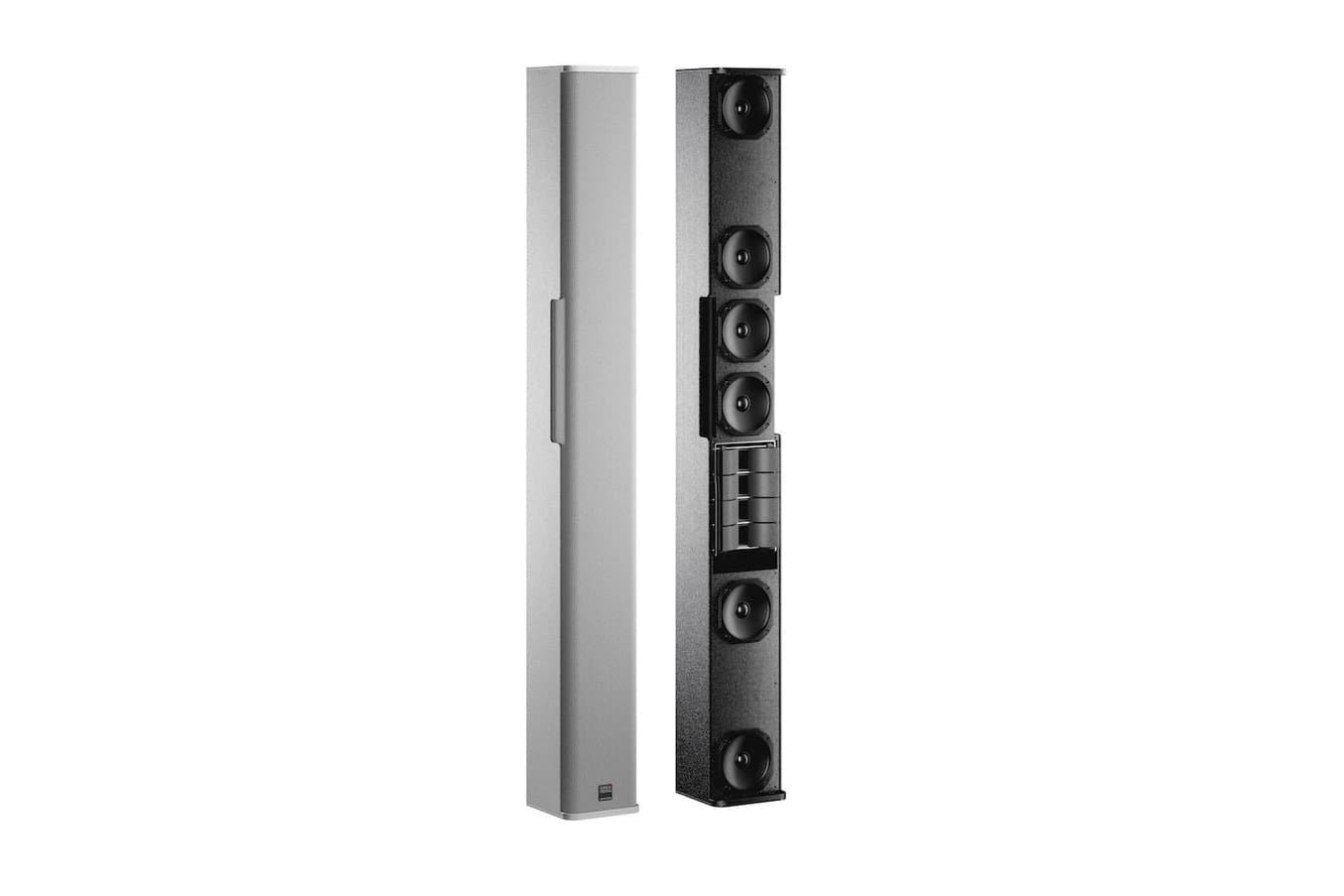
Vier flexible Horn-Arrays, die eine anpassungsfähige Pegelverteilung ermöglichen.
Aufgrund ihrer komplexen Form wäre die Herstellung dieser verstellbaren Horn-Arrays mittels eines Spritzgussverfahrens sehr anspruchsvoll und teuer gewesen.
„Wenn überhaupt machbar, hätte ein Spritzgussverfahren ungefähr so viel gekostet wie ein SLS-3D-Drucker von Formlabs. Aus diesem Grund haben wir uns entschieden, unseren eigenen Drucker für die Entwicklung und spätere Serienproduktion der Waveguides zu kaufen.“
André Figula, Konstruktion bei Kling & Freitag
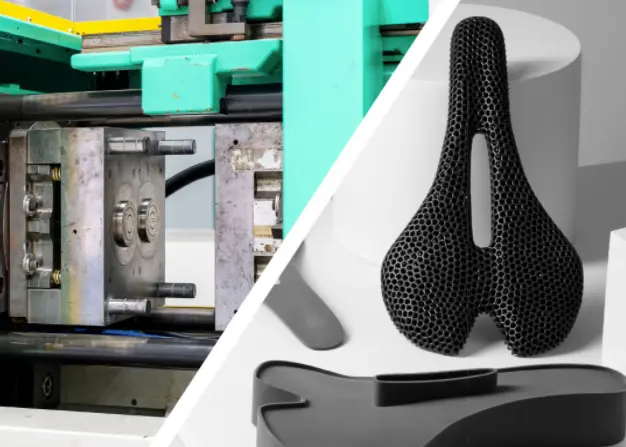
SLS-3D-Druck oder Spritzguss: Wann sollte man Spritzgussteile durch 3D-Druck ersetzen?
In diesem Whitepaper werden der Spritzguss und seine Vor- und Nachteile erörtert sowie der SLS-3D-Druck und die Anwendungen vorgestellt, bei denen er als ergänzende Technologie eingesetzt werden kann.

Eine komplett ausgefüllte Konstruktionskammer des SLS-3D-Druckers Fuse 1, zu sehen in der Software PreForm.
Zurzeit befinden sich Figula und sein Team in der ersten Serienproduktion der Waveguides und stoßen auf hohe Nachfrage in der Pro-Audio-Branche.
Außerdem entdecken sie immer mehr Synergieeffekte des Fuse 1. So nutzen sie den überbleibenden Raum der Konstruktionskammer für das Rapid Prototyping in der Entwicklung anderer Bauelemente und sparen dadurch wiederum viel Zeit und Geld.
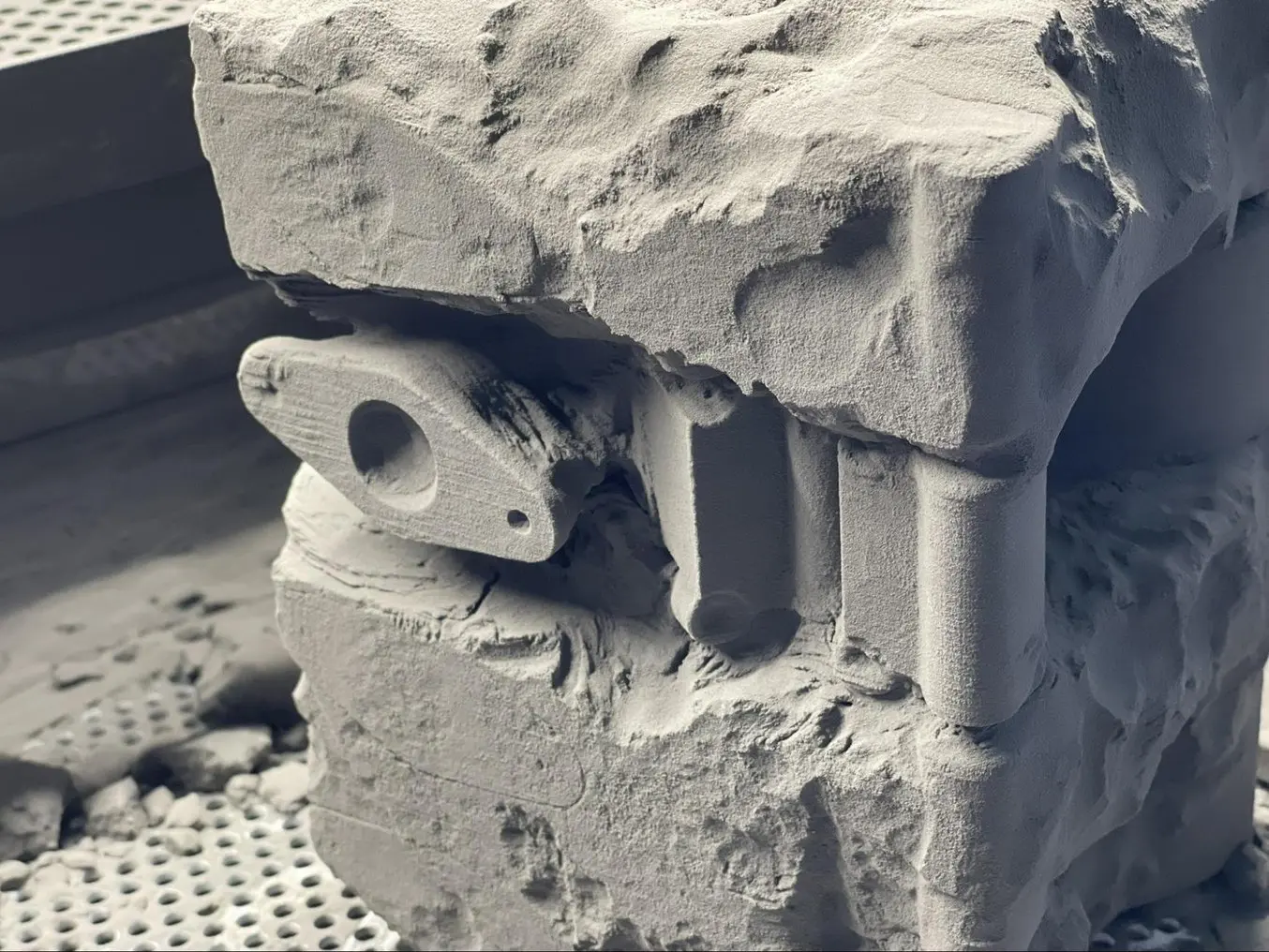
Eine SLS-3D-gedruckte Komponente während der Nachbearbeitung mit dem Fuse Sift.
Konstruktive Flexibilität durch additive Fertigung
Ein weiterer großer Vorteil des hauseigenen SLS-3D-Druckers bei Kling & Freitag ist die hohe Flexibilität in der Konstruktion neuer Produkte.
„In der Entwicklung neuer Produkte können wir beispielsweise mit jeder Iteration Merkmale des Prototypen neu anpassen. In einem Spritzgussverfahren hätten wir diese Flexibilität nicht und wären so nicht zum gleichen Ergebnis gekommen.“
André Figula, Konstruktion bei Kling & Freitag
Auch die komplexe Geometrie des Waveguides sowie diverse Hinterschnitte im Design hätten die Herstellung mittels Spritzgussverfahren unmöglich gemacht.
„Den Waveguide des PIA M Lautsprechers hätten wir ohne den Fuse 1 nicht auf den Markt bringen können.“
André Figula, Konstruktion bei Kling & Freitag
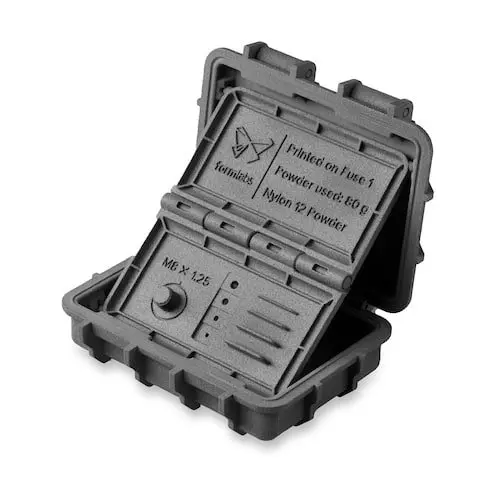
Kostenloser Probedruck
Sehen und fühlen Sie selbst die Qualität von Formlabs. Wir schicken Ihnen einen kostenlosen Probedruck gedruckt mit Formlabs' SLS-Technologie an Ihren Arbeitsplatz.
Die nächste Etappe: Patentreife Innovation mit dem Fuse 1
Aktuell sind die Maschinen bei Kling & Freitag durchgängig im Einsatz. Hauptsächlich für die Serienproduktion des neuen Waveguides des PIA M Lautsprechersystems, aber auch für Neuentwicklungen.
„Mit 3D-Druck wird es schneller, es wird erschwinglicher und wir bleiben während der gesamten Entwicklung flexibel.“
André Figula, Konstruktion bei Kling & Freitag
Eine dieser neuen Innovationen wurde zu 100 % auf dem SLS-3D-Drucker Fuse 1 iteriert und steht jetzt kurz vor der Patentanmeldung.
„Wenn ich jeden Iterationsschritt in einem Prototypen-Verfahren mit externen Dienstleistern machen würde, hätte ich jedes Mal ungefähr acht Wochen auf einen neuen Prototypen warten müssen. Und so lade ich jede neue Variante einfach auf dem Fuse 1 hoch und habe dann in relativ kurzer Zeit ein funktionierendes Teil“, erzählt Figula.
Um herauszufinden, wie der Fuse 1 auch Ihr Unternehmen im Rapid Prototyping und der Serienproduktion voranbringen kann, kontaktieren Sie unsere Expert:innen im Vertriebsteam und fordern Sie einen kostenlosen Probedruck an.