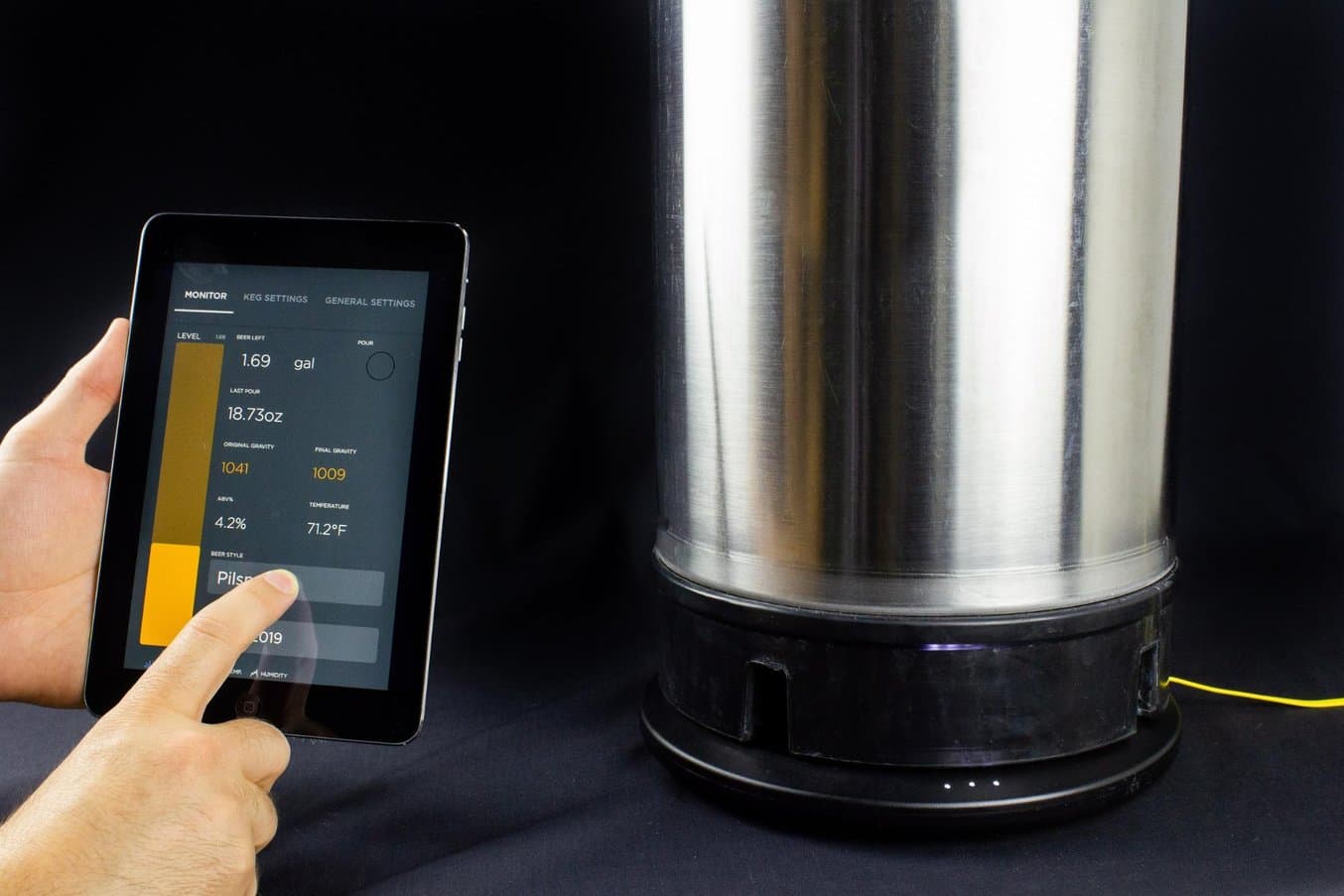
Der Name Plaato kommt Lesern unseres Blog wahrscheinlich bekannt vor. Letztes Jahr berichteten wir von der Entwicklung eines intelligenten Gärspunds für Hobbybrauer, der die CO2-Menge bei der Gärung misst.
Seitdem führen Michael Kononsky und sein Team weiter ihre Mission fort, Brauern mehr Daten an die Hand zu geben. Sie haben ein neues Produkt auf den Markt gebracht namens Plaato Keg. Dabei handelt es sich um eine intelligente Waage zur Überwachung von Bierfässern.
Beim Gärspund steckte der Teufel in den komplexen, transparenten Teilen. Bei der Entwicklung ihres jüngsten Produkts gab es hingegen eine Reihe neuer Herausforderungen. „Wir brauchten ein wasserdichtes Gerät, das das Gewicht eines Fasses aushalten kann. Wenn sie voll sind, wiegen die Dinger irgendwas zwischen 20 und 60 kg", erklärt Kononsky.
Im Folgenden erfahren Sie, wie das Team von Plaato über 100 Prototypen für Betatester auf der ganzen Welt anfertigte, indem 3D-Druck sowohl am Standort als auch beim Vertragshersteller genutzt wurde. So finalisierte man das DFM (Design for Manufacturing) des neuen Produkts, mit dem man bereits zwei der renommierten Red Dot Design Awards gewinnen konnte.
Mehr Kontrolle für Brauer durch Daten
„Wir unterhielten uns mit einem unserer Vertriebspartner und sprachen nur zum Spaß über unsere Ideen. Wir sagten: ,Hey, wie wär's, wenn man wüsste, wie viel man trinkt, wie viel man noch auf Lager hat?’ Viele Leute haben nämlich zahlreiche verschiedene Fässer und einen Kegerator, also einen Fassbier- oder Zapfkühlschrank. Der steht dann im Keller und keiner weiß, wie viel noch drin ist oder wie alt es ist. Also haben wir ein paar Prototypen angefertigt und unsere Vertriebspartner waren begeistert. Sie wollten uns unterstützen“, berichtet Kononsky.
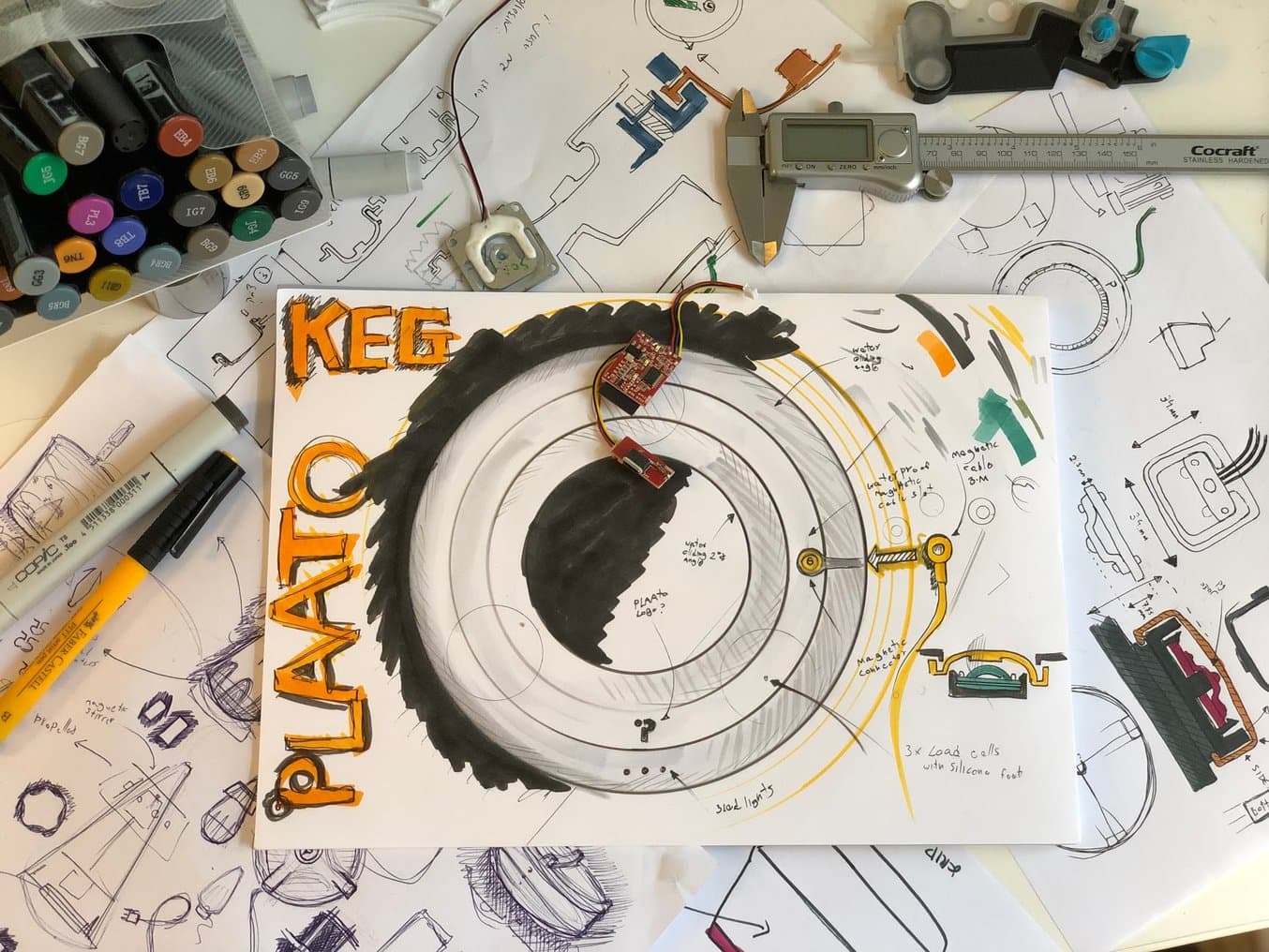
Designiterationen des Plaato Keg mit Anschluss und Kraftmessdosen.
Die auf dem Markt verfügbaren Lösungen basieren alle auf Durchflusssensoren, die verschmutzen und vom Brauer eingebaut und mit den Schläuchen verknüpft werden müssen. Kononsky und sein Team glaubten, das Volumen einfacher und sauberer messen zu können, indem sie das Gewicht und die Wichte (=Gewichtskraft bezogen auf Volumen) umrechnen.
„Wir wollten einfach nur die Menge des Biers messen, ohne es berühren oder anschließen zu müssen. Etwas Kinderleichtes, auf dem das Fass steht. Man stellt einfach das Fass drauf und holt sich die Daten aus der Cloud. Fertig. Allein hier in Norwegen, in unserem winzigen Land, gibt es unseren Schätzungen nach 14 000 Kegerators. Und der Durchschnittsbrauer hat sieben oder acht Fässer“, sagt Kononsky.
Entwicklung und Test eines Produkts, das Fässern stand hält
„Wir bezogen unsere Community in die Entwicklung mit ein. Wir sandten eine Umfrage an 300 unserer Gärspund-Kunden, die Interesse an Fassprodukten zeigten. Dabei fragten wir, welche Art Fässer sie nutzen, mit welchen Problem sie kämpfen, wie sie die Fässer einsetzen, ob es dort feucht ist und welche Anschlüsse und Kabel in ihren Kegerator passen. Daraufhin erhielten wir Bilder und Abmessung tausender Fässer, die alle unterschiedlich waren. Deshalb mussten wir unser Produkt wirklich dementsprechend optimieren“, gibt Kononsky an.
Kononsky und sein Team begannen mit Laserschnitten aus Kunststoffplatten, die sie dann miteinander verbanden. Aber es war schwierig, dabei der Form der Fässer zu entsprechen. Außerdem war der Prozess extrem zeitintensiv. Als nächstes verwendeten Sie einen FDM 3D-Drucker mit einer angepassten Düse von 1 mm, um grobe Prototypen zur schnellen Marktvalidierung herzustellen. Und sobald sie anspruchsvollere und detailliertere Prototypen brauchten, gingen sie zum Stereolithografie (SLA) 3D-Druck über.
Das Team von Plaato setzte verschiedene Technologien in unterschiedlichen Entwicklungsphasen ein: lasergeschnittene Kunststoffplatten (durchsichtig), FDM 3D-Druck (schwarz mit grober Textur) und später SLA 3D-Druck für detailliertere Prototypen (weißer Rahmen und poliertes, schwarz gefärbtes Gehäuse)
„Wir arbeiteten an einem dünnen Produkt, das wasserdicht sein und schwere Stöße aushalten sollte. Das war schon eine Herausforderung. Rigid Resin war hierbei bahnbrechend. Wir konnten alle Sensoren anschrauben, alle Kunststoffverankerungen produzieren und alles wasserdicht machen. Außerdem bot es uns die nötige Detailstufe, um uns an unsere Hersteller zu wenden“, sagt Kononsky.
Rigid Resin war hierbei bahnbrechend.
Michael Kononsky, Mitbegründer von Plaato
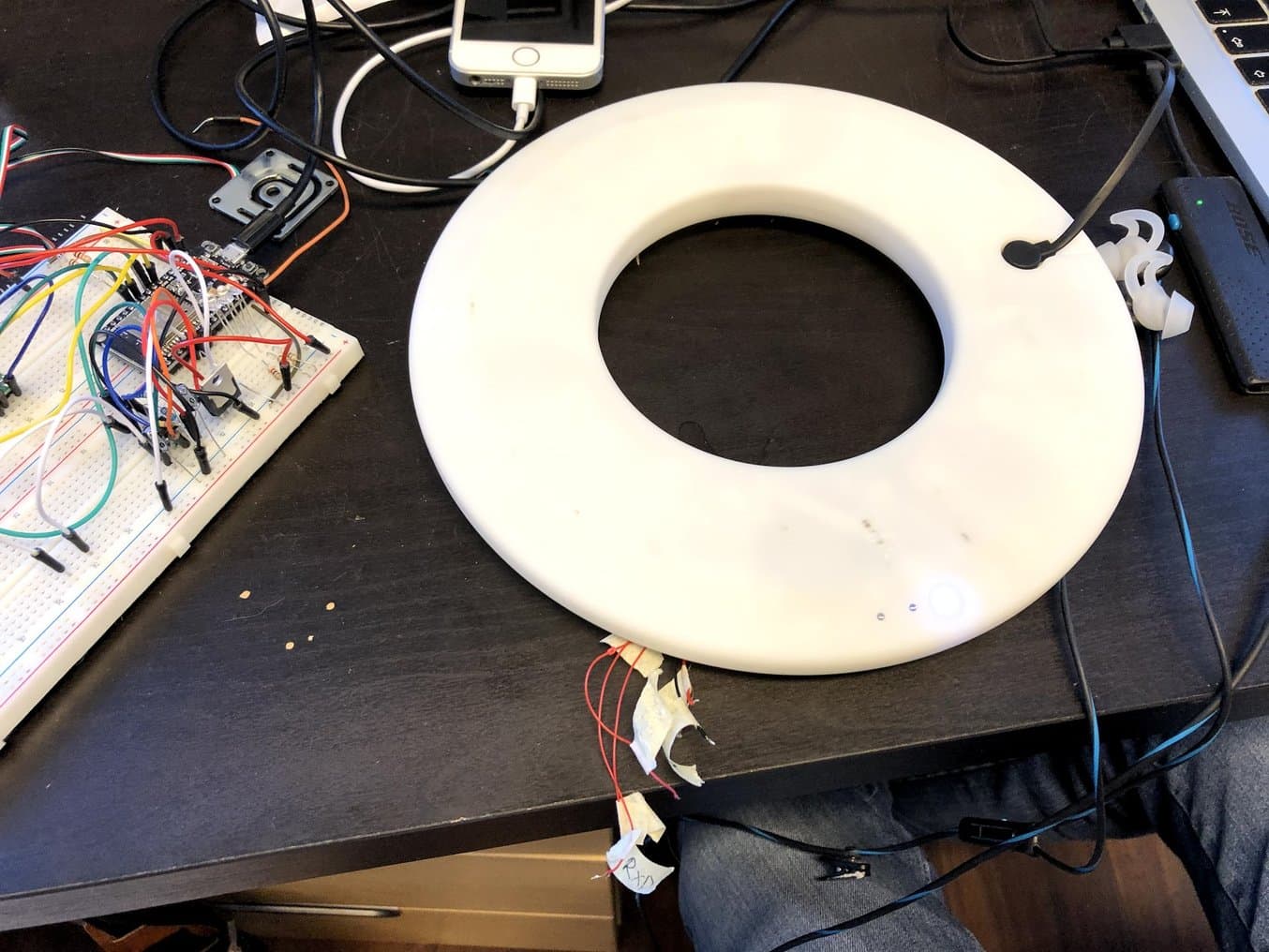
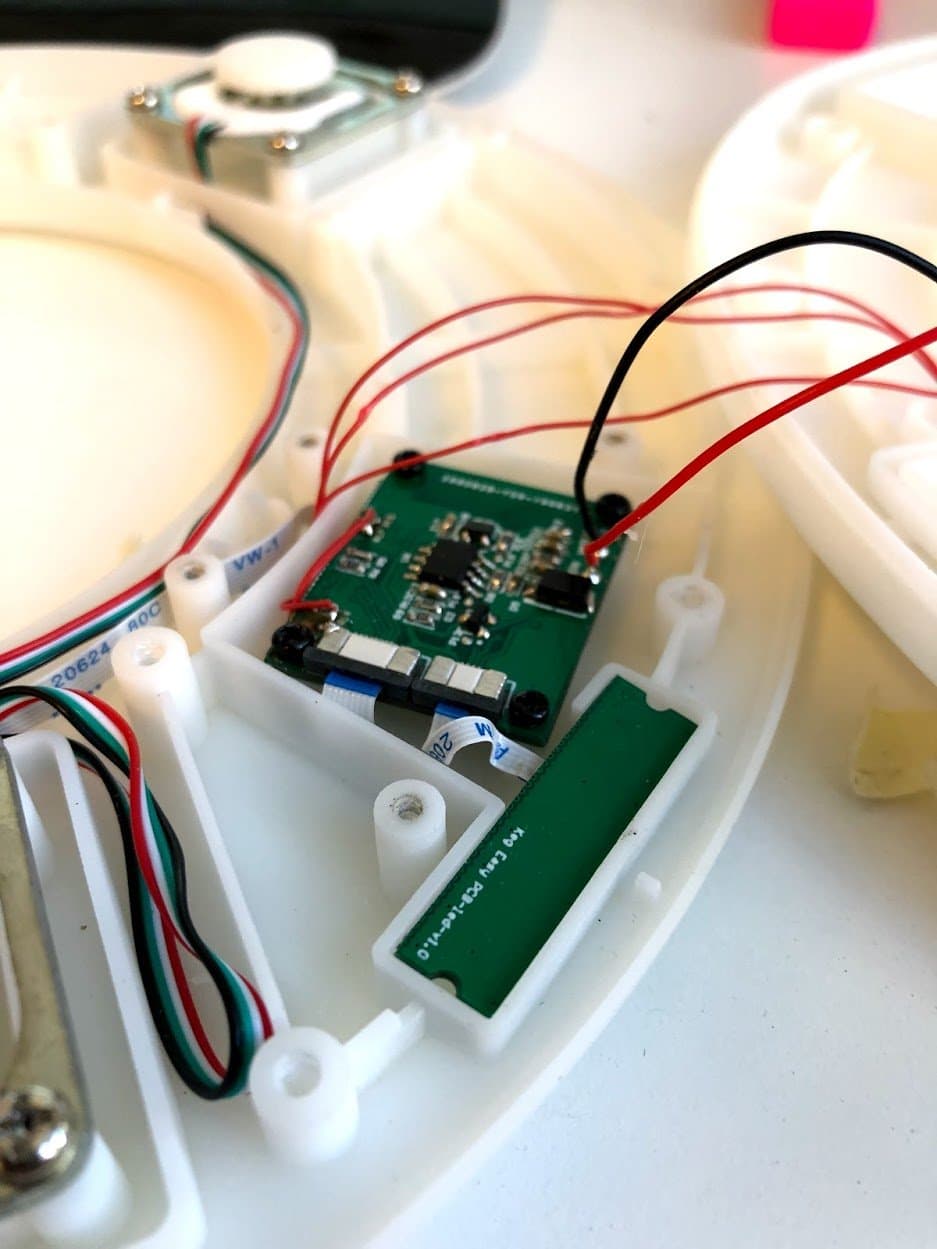
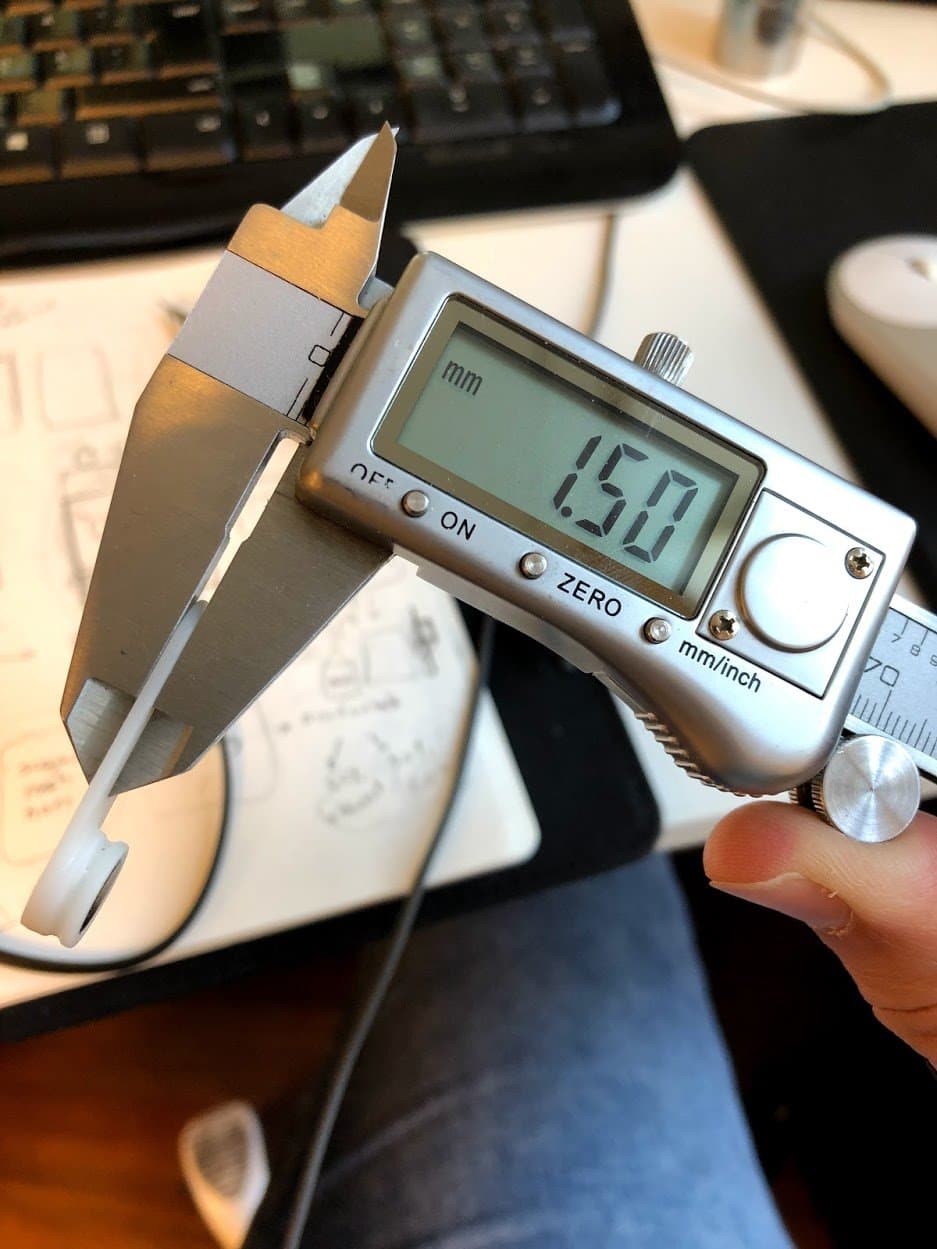
Die Ingenieure nutzten Rigid Resin, um detaillierte Prototypen mit dünnen Wänden herzustellen, die alle Eigenschaften des letztendlichen Spritzgussdesigns umfassten.
Die Leiterplatten, Sensoren und andere Elektronikteile befinden sich in Einsätzen, die mit dem Gehäuse verschraubt werden. Diese sind an sich nicht wasserdicht, deshalb musste das Team angepasste Dichtungen und Hüllen erstellen, die sowohl Halt als auch Schutz bieten. Sie mussten eng anliegen und gute Toleranzwerte aufweisen, um Kompression und Abdichtung zu bieten.
„Bei der schnellen Prototypenentwicklung haben wir Elastic Resin verwendet. Dabei haben wir verschiedene Stärken ausprobiert. Es ist praktisch, 20 verschiedene Dichtungstypen auf einer einzigen Konstruktionsplattform unterzubringen: eine mit 1,1 mm, eine mit 1,2 mm, 1,4 mm und so weiter. Ich kann sie alle direkt ausprobieren und voilà. Das spart einen Haufen Geld“, berichtet Kononsky.
Insgesamt hat das Team bei Plaato ungefähr 35 bis 40 Prototypen mit seinem SLA 3D-Drucker von Formlabs erstellt. Sie unterteilten die Modelle und eine Vielzahl kleiner Teile, damit alle im selben Druckvorgang angefertigt wurden, der ungefähr neun Stunden dauerte.
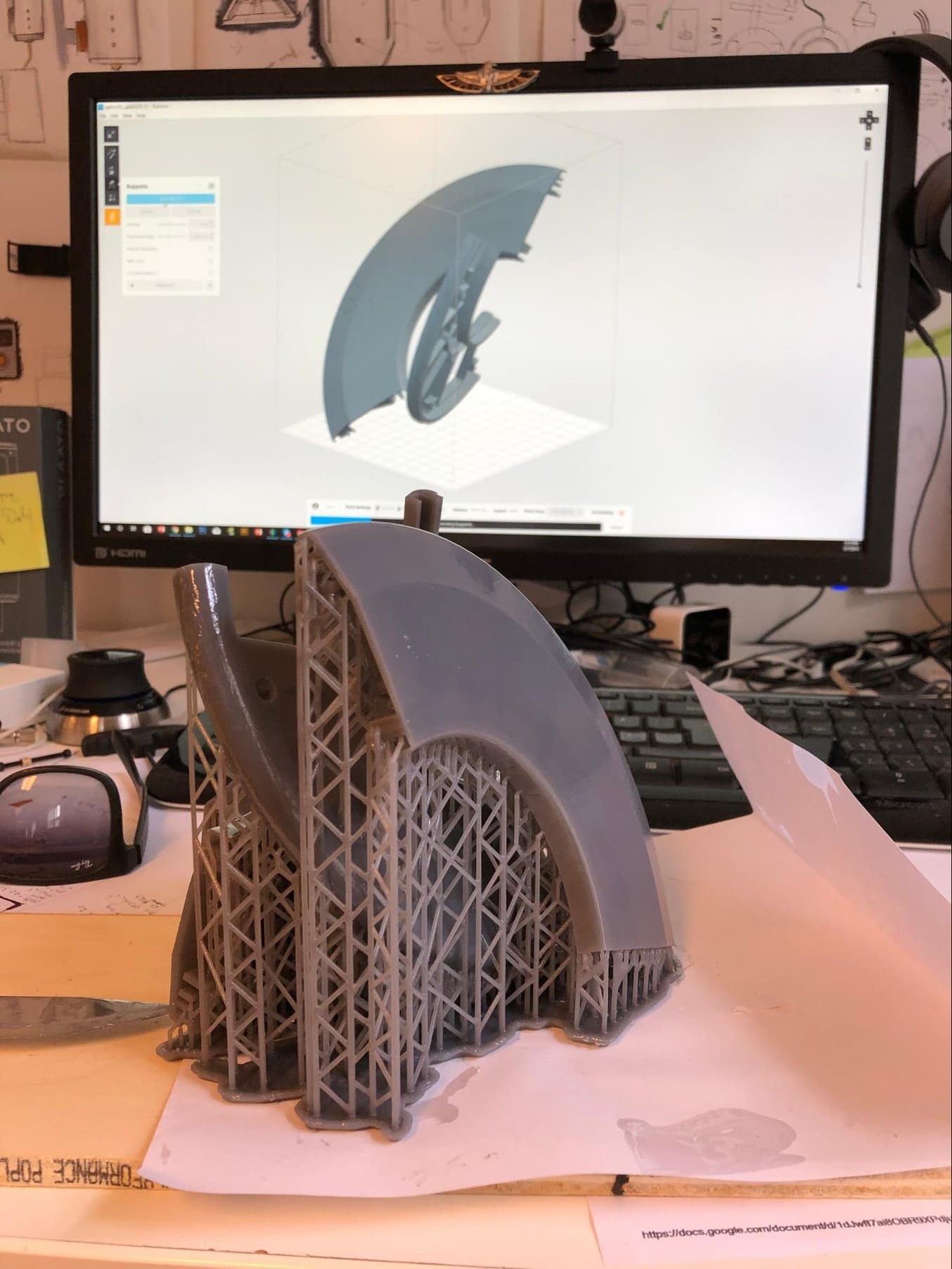
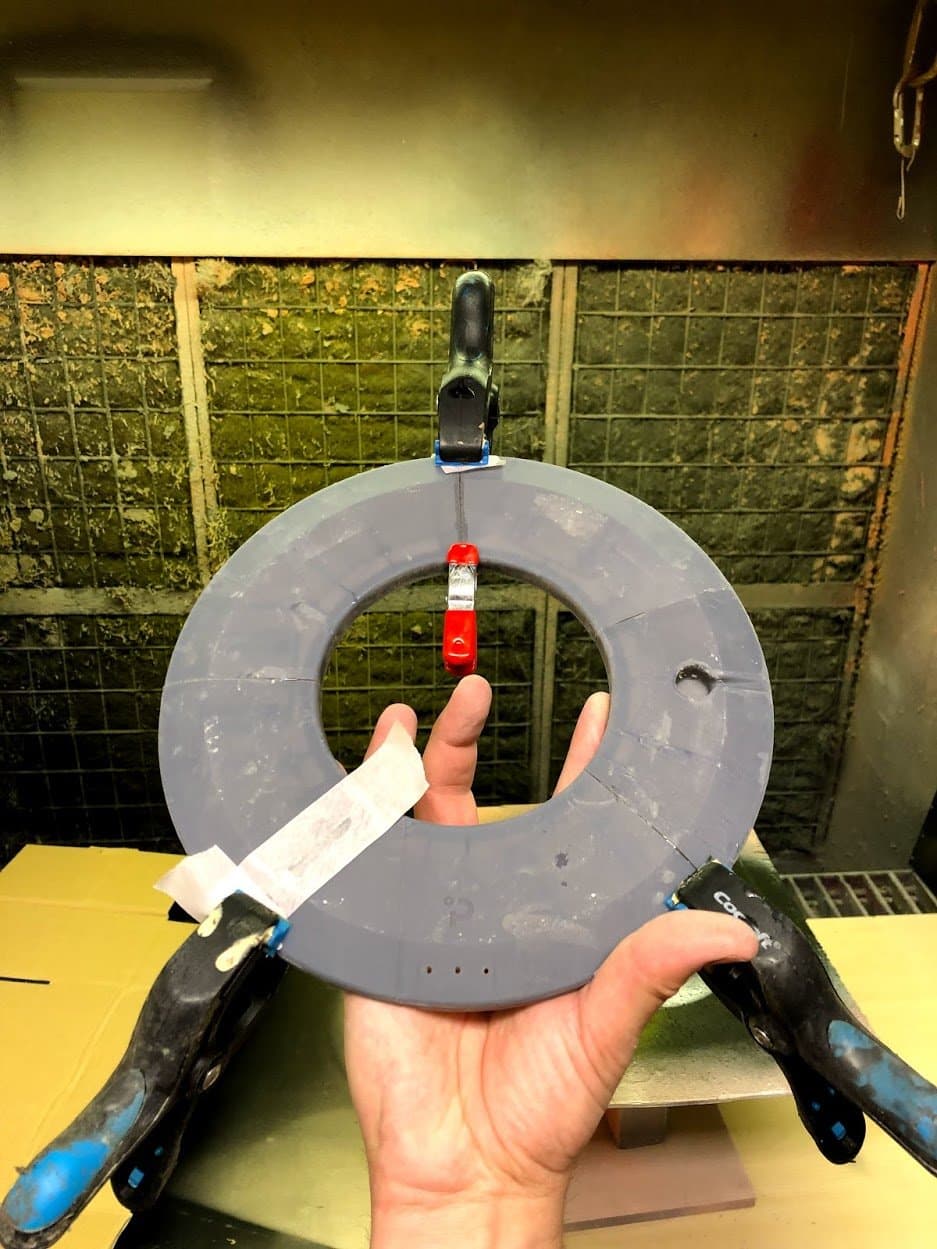
Das Team von Plaato unterteilte die Modelle und eine Vielzahl kleiner Teile, damit alle im selben Druckvorgang angefertigt wurden.
„Das Coole an diesem Drucker ist, dass ich ihn über Nacht arbeiten lassen kann. Somit ist das letzte, was ich vor Feierabend tue, den Druck einzurichten. Und wenn ich morgens wiederkomme, ist er fertig. Ich wasche alles, härte es nach und brauche vielleicht eine Stunde, um alles mit der Elektronik zusammenzusetzen. Und so haben wir noch vor der Mittagspause eine neue Iteration“, so Kononsky.
Auch bei der Prototypenentwicklung wandte sich das Team an seine Community. Von den ersten Prototypen für MVPs zu denen, die schon wie das letztendliche Produkt aussahen, sandte das Team ungefähr 100 Prototypen an Kunden in den USA, Südamerika, Asien, Australien, Europa und Nahost. Dadurch erhielt man wichtige Einblicke, die in die folgenden Iterationen einflossen. So kam zum Beispiel die Idee eines Warnsystems auf, das den Nutzer über ein Leck im Fass informiert. Oder auch ein Temperatursensor, der bei Thermostatbrand Alarm schlägt – etwas, das bei einem selbstgebauten Kegerator schon einmal vorkommt.
Die 3D-gedruckten Prototypen halfen außerdem bei der Validierung seitens Plaato, dass das Design Anwendungen mit Fässern standhält.
„Wie bei einem Crashtest ließen wir das Gerät aus einer Höhe von 10 cm fallen, dann 20, dann 30, 40 ... Selbst bei einem Meter überstand es alles. Wir wussten, wenn das Kunstharz das aushält, dann müssen wir uns auch bei der Spritzgussversion keine Sorgen machen, da wir uns für ein schlagfestes Polycarbonat entschieden hatten – dasselbe Material, das auch für die Schutzschilde der Polizei verwendet wird. Was wir 3D-gedruckt haben, kann sogar 48 Stunden lang einen Meter tief unter Wasser stehen, ohne dass das irgendwelche Folgen hat. Das hat uns einen Haufen Zeit gespart und einen Haufen anderer äußerst kostspieliger Lösungen, die wir bei herkömmlichen Produktionsmethoden benötigt hätten“, sagt Kononsky.
Design for Manufacturing via 3D-Druck von Iteration am Standort und in China
Kononsky und sein Team hatten es dieses Mal etwas leichter, da sie sich beim neuen Produkt für denselben Vertragshersteller entschieden wie beim Gärspund. Indem man SLA 3D-Druck sowohl am Standort als auch beim Vertragshersteller einsetzte, konnte man den Validierungsprozess beschleunigen und schneller zur Produktion übergehen.
„Ich möchte 90 bis 95 % des Designs auf unserer Seite erledigen, bevor wir dem Hersteller einen Auftrag erteilen. So ein bisschen Freiheit möchte ich ihnen lassen, da sie ihre Maschinen und Kapazitäten am besten kennen. Wir vertrauen darauf, dass unser Partner professionell arbeitet. Deshalb wollte ich ihn nicht mit Kleinkram einschränken, der nur grundlos das Projekt verkompliziert hätte“, so Kononsky.
„Unser Partner auf Herstellerseite hatte sich auch einen Form 2 zugelegt. Das erleichterte uns die Kommunikation. Weil sie denselben Drucker wie wir haben, konnte ich ihnen die von mir selbst bearbeiteten Dateien zuschicken und dort drucken lassen. Anschließend erhielt ich ihren Entwurf zurück, druckte ihn, probierte ihn aus und alles lief bestens. Das war eine wirklich interessante Arbeitsweise. Die gemeinsame Entwicklung hatte ihre Vorzüge“, verrät Kononsky.
Die meisten Unternehmen schicken die Teile mit ihrem ausländischen Vertragsherstellern hin und her. Dadurch wird die Festlegung der letzten Details zu einem sehr langwierigen Prozess.
„Als ich noch ein Fachberater war, hatten wir genau das. Es dauerte vier Tage hin und zurück [mit Expressversand]. Diese Zeit ist kostbar, deshalb verlässt man sich mehr auf Bilder und PowerPoint-Präsentationen. Aber das wiederum führt zu Kommunikationsproblemen. Die können das Teil auch einfach fräsen, aber leicht ist das nicht und die gegenseitigen Erwartungen werden damit auch nicht erfüllt. [3D-Druck] macht alles viel leichter. Man erstellt einfach genau die Datei, die man braucht. Insbesondere Radien und Kompressionsniveaus lassen sich ohne nur schwer übermitteln“, erklärt Kononsky.
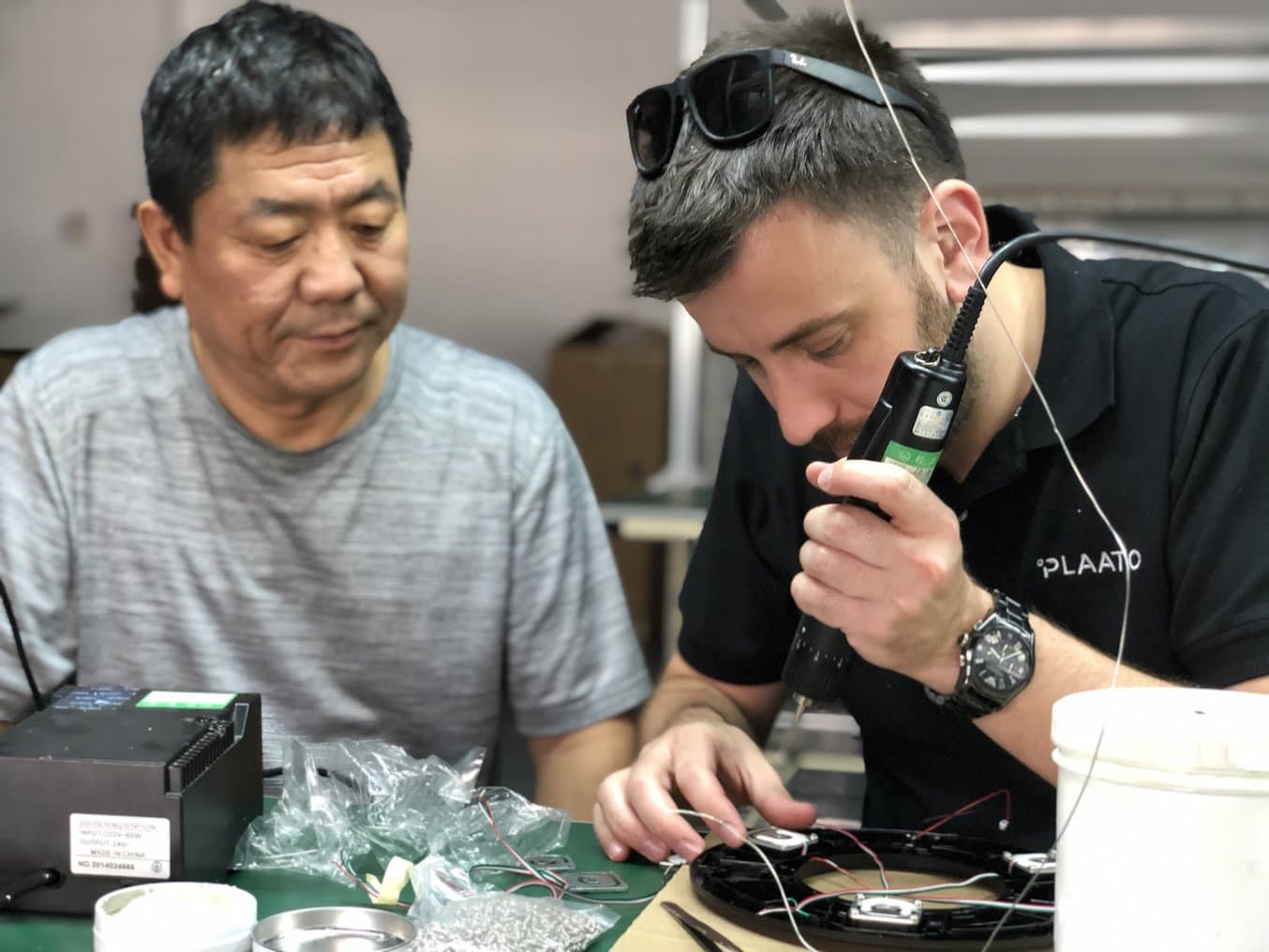
Mit dem 3D-Drucker beim Vertragshersteller druckte man auch Halterungen und Vorrichtungen für die Fertigungsstraße.
Dank des 3D-Druckers beim Vertragshersteller konnte auch die Werkzeugbestückung der Fertigungsstraße beschleunigt werden.
„Wir haben auch viele Haltevorrichtungen für die Montage gedruckt, zum Einsetzen von Komponenten, um sie zu sichern, [die korrekte] Platzierung [zu gewährleisten] und mehr. Wir haben sie alle mit dem Drucker gedruckt, den wir aus den Büros unseres Herstellers ins Werk mitgenommen hatten, als ein Kollege und ich bei der Fertigungsstraße waren“, so Kononsky.
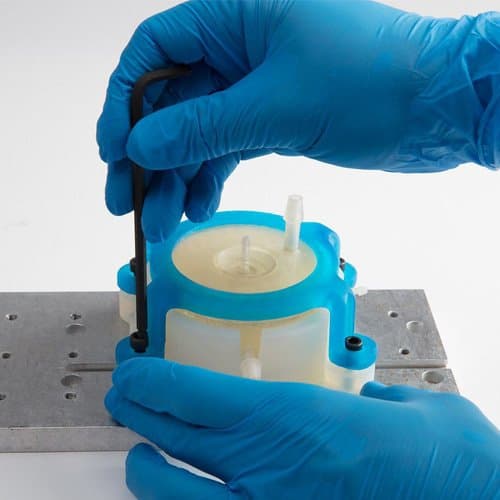
Vorrichtungen und Halterungen mit 3D-Druck designen
Laden Sie unser Whitepaper herunter und erhalten Sie Einblick in das grundlegende Design von Halterungen und Vorrichtungen, in bewährte Praktiken zum Design 3D-gedruckter Halterungen und Vorrichtungen so wie Tipps zur Validierung gedruckter Vorrichtungen.
Von einer erfolgreichen Markteinführung zu neuen Anwendungen
Als kleines Unternehmen war eine solche Markteinführung ein gewisses Risiko, dessen war man sich bewusst. Deshalb ging man wieder zum Crowdfunding über und sammelte 150 000 USD mittels einer Kickstarter-Kampagne.
Die Vorbestellungen der Unterstützer wurden mittlerweile ausgeliefert und die COVID-19-Pandemie hat zur Freude der Branche noch mehr Leute zum Brauen in den eigenen vier Wänden angeregt. Deshalb war die erste Produktionsserie des neuen Produkts schnell ausverkauft.
Als Zeugnis des innovativen Designs hat das Plaato Keg auch den Red Dot Design Award in zwei Kategorien gewonnen: „Smart Products“ und „Industrial Design“.
Einige Kunden haben weitere kreative Anwendungen für das Produkt gefunden. „Wir haben herausgefunden, dass es sich bei vielen der Kunden um Bars und vielschichtige Dienstleister handelt, die Fässer und Zapfanlagen in Büroeinrichtungen anbieten. Darunter ist ein Unternehmen mit 150 Zapfstationen für Cold-Brew-Kaffee. Der Kunde erzählte uns: ‚So verwalte ich meinen ganzen Bestand von hier aus. Ich fahre nicht einfach in der Gegend rum oder warte, bis die Leute mich anrufen, weil ihnen der Kaffee oder das Bier ausgegangen ist. Ich weiß alles vorher und kann meinen Tag planen.‘ Und das ist schon ziemlich cool, denn so eine Lösung gab es vorher nicht. Der Nutzer kann seinen Kunden besseren Service anbieten“, sagt Kononsky.
Entdecken Sie den neuesten SLA 3D-Drucker von Formlabs – den Form 3 – sowie unsere wachsende Bibliothek an technischen Kunstharzen und überwinden Sie komplexe Herausforderungen in der Produktentwicklung. Möchten Sie sich selbst von der Qualität überzeugen?