Wie Dorman dank 3D-Druck mit den Erstausrüstern der Automobilindustrie Schritt hält
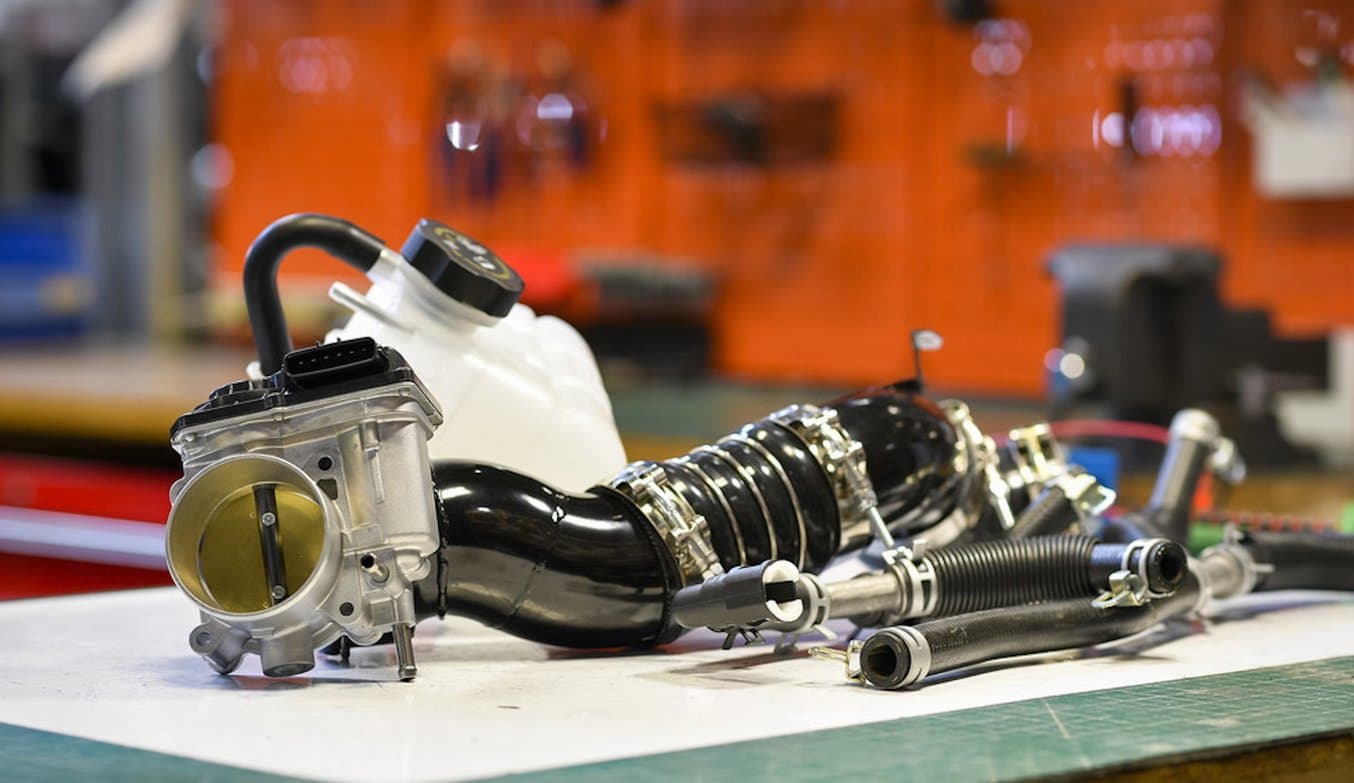
Ob Neuwagen oder gebraucht: Die Automobilpreise sind in den vergangenen zwei Jahren in die Höhe geschossen, was auf den weitgreifenden Mangel an Computerchips, Lieferverzögerungen und Fabrikschließungen zurückzuführen ist. Fahrzeughalter können sich den Kauf eines neuen Autos nach Ablauf der Garantie ihres aktuellen Wagens häufig nicht leisten, und somit gewinnen Wartungsarbeiten und Routineüberprüfungen eine immer größere Bedeutung, um Fahrzeuge in Gang zu halten. Zwar verkaufen Automobilhersteller Ersatzteile und bieten Reparaturen an, aber auch sie haben mit denselben Lieferkettenproblemen zu kämpfen und sind für den Durchschnitt zudem häufig weniger bezahlbar als unabhängige Werkstätten.
Dorman Products blickt auf eine hundertjährige Geschichte als Hersteller von Kfz-Bauteilen für den Aftermarket zurück, sowohl für leichte Nutzfahrzeuge als auch Schwerlastfahrzeuge, und hat mithilfe von 3D-Druck seine Produktionsdauer verkürzt und die Qualität gesteigert. Das Unternehmen stützt sich dabei auf acht 3D-Drucker an zwei Standorten, um mit der ständigen Flut neuer Ausführungen und Modelle von den Erstausrüstern (OEMs) Schritt zu halten.
Chris Allebach, Leiter der additiven Fertigung bei Dorman, und der Teamleiter für mechanische Konstruktion Eric Tryson nutzen die Stereolithografie-3D-Drucker (SLA) Form 2, Form 3 und Form 3L sowie mehrere FDM-Drucker für das Rapid Prototyping neuer Bauteile, aber auch zur Herstellung maßgefertigter Halterungen und Vorrichtungen für ihre Validierungsprozesse.
„Bei den Erstausrüstern entwerfen ganze Teams von Leuten ein einziges Teil, womit sie manchmal zwei Jahre vor der Veröffentlichung eines neuen Autos beginnen. Wir müssen Wege finden, um sicherzustellen, dass unsere Ersatzteile zuverlässig sind und trotzdem schnell auf den Markt kommen. Mittels 3D-Druck im Nu iterieren und Designs anpassen zu können, hat uns neue Projekte eröffnet, die wir in der Vergangenheit nie hätten umsetzen können. Die Gewissheit, dass die Teile eine hohe Qualität haben, stärkt unser Vertrauen in das, was wir tun“, so Allebach.
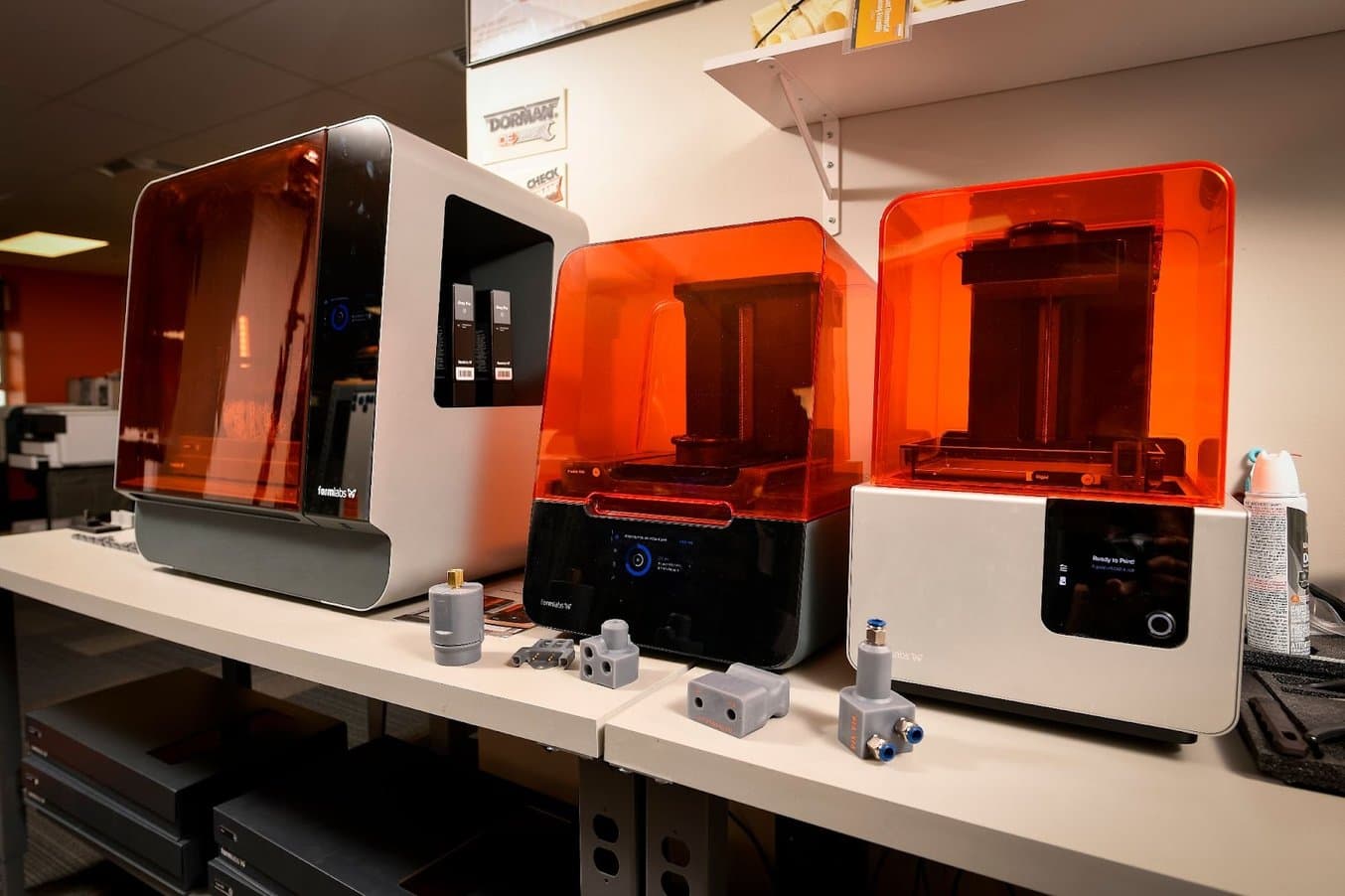
Das Entwicklerteam von Dorman nutzt die Drucker Form 2, Form 3+ und Form 3L.
Die Entwicklung von über 100 000 Produkten
Die Vielfalt der Produktpalette von Dorman ist imposant: Das Unternehmen entwirft und verwaltet eine Datenbank von 118 000 unterschiedlichen Teilen (Stand 25. Dezember 2021) für Hunderte verschiedener Fahrzeuge. „Wir führen eine große Bandbreite von Produkten, die einen Großteil der Komponenten im Auto abdecken, und haben bisher 4000–5000 neue Teile pro Jahr herausgebracht“, erläutert Tryson.
Dormans Produkte reichen von Autoschlüsselgehäusen und standardmäßigen Motorbauteilen bis hin zu komplexen Elektronikmodulen und robusten Bauteilen für Lastfahrzeuge.Dorman analysiert die Fehlerursachen von OEM-Bauteilen und konstruiert dann das Produkt über Reverse Engineering, wobei das Team das Design manchmal komplett neu entwickelt und optimiert. Oft muss das Team auch das Original-Bauteil beschaffen, wozu es manchmal ganze Autos kauft, um die Konstruktion des Fahrzeugs vollkommen zu verstehen und das verbesserte Design zu validieren.
Für den Designprozess muss das Modell zunächst digital rekreiert werden, damit Änderungen am Design implementiert werden können. Anschließend werden die Teile an das Metrologielabor von Dorman gesendet, das entweder einen kontaktlosen Laserscan erstellt oder für präzisere Teile eine Kontaktsonde nutzt. Die Referenzdaten werden an das Team von Allebach und Tryson zurückgesendet, das die Produkte über Reverse Engineering in Solidworks entwirft.
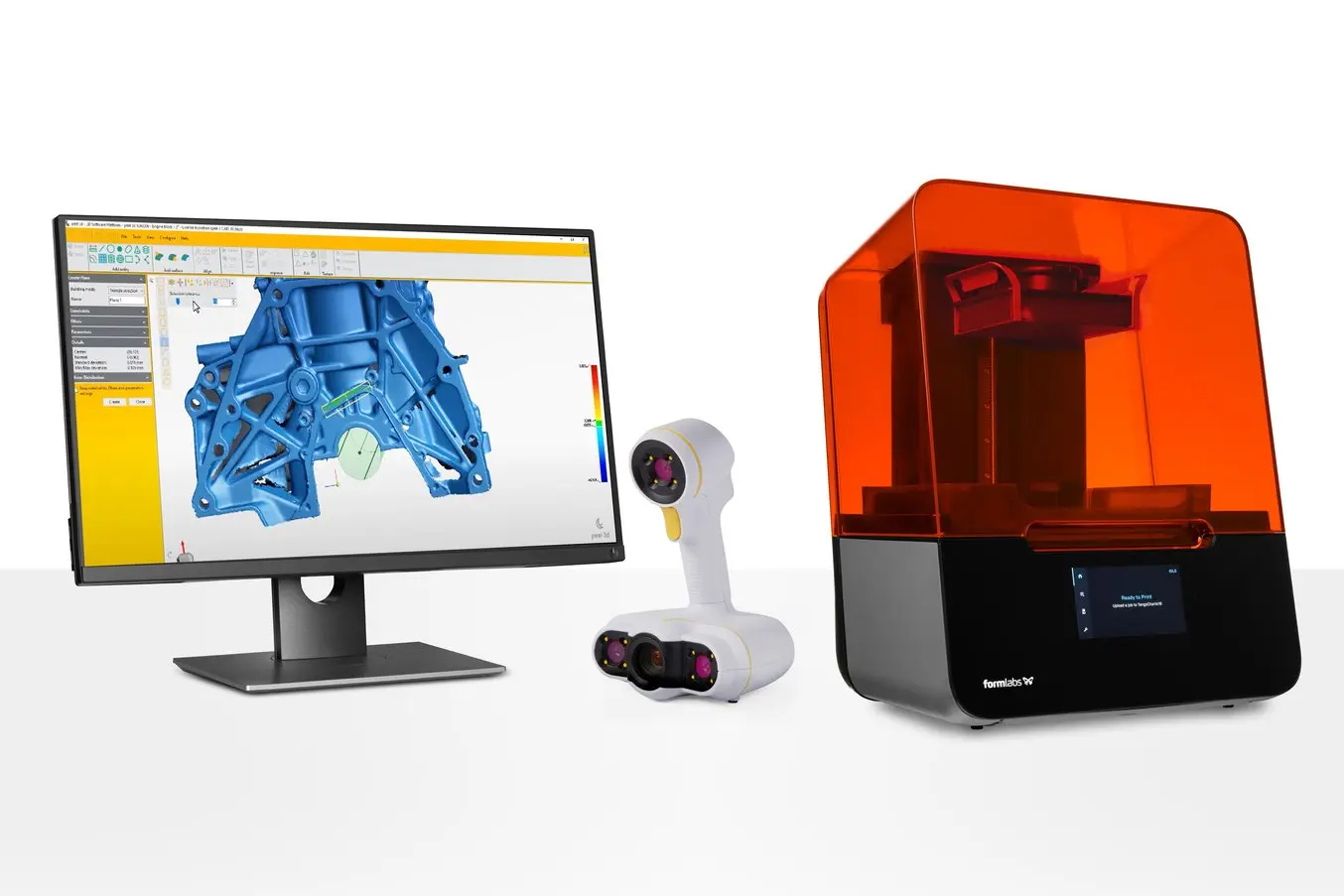
3D-Scan und 3D-Druck für Reverse Engineering und andere Anwendungen
In diesem Bericht behandeln wir einige der wichtigsten Anwendungsfälle dieser beiden Technologien und geben einen Überblick über den aktuellen 3D-Scanner-Markt, damit Sie leichter entscheiden, welches Gerät für Ihr Unternehmen am geeignetsten ist.
„Wir fertigen schnell einen Prototyp, an dem der Designer überprüfen kann, ob die Geometrie und die Abmessungen stimmen, und drucken danach einen weiteren 3D-Prototyp – der geht dann zur Beurteilung an den Produktingenieur. Sie möchten das Teil selbst in die Hand nehmen, damit sie es mit eigenen Augen begutachten oder es mit den dazugehörigen Fahrzeugkomponenten testen können, um sicherzustellen, dass es passt“, erklärt Tryson.
Die Abteilung von Allebach und Tryson versucht allerdings nicht einfach Teile zu ersetzen. Dormans Produktlinie OE FIX™ hat auch das Ziel, das Originaldesign zu verbessern. „Wir betreiben nicht nur Reverse Engineering, sondern wir analysieren und ermitteln, warum ein Teil versagt und wie wir es verbessern können. Manchmal ist die Antwort einfach eine Materialänderung, oder aber eine grundsätzliche Designänderung. Bei solchen Redesigns ist es uns wichtig, Prototypen zu erstellen und Funktionstests durchzuführen“, so Tryson.
Prototyping eines Bauteils von OE FIX™
Ein Beispiel solcher Designoptimierungen war ein Motorbauteil, das in zahlreichen Fahrzeugen einen Defekt erlitt. Es bestand ursprünglich aus Kunststoff und bekam aufgrund der anhaltenden Hitzeeinwirkung durch den Motor einen Riss. Das Team von Dorman untersuchte das Bauteil, ließ es von seinem Metrologieteam scannen und beschloss, es aus gegossenem Aluminium neu zu entwickeln. Das Teil für ein anderes Material zu entwerfen, umfasst jedoch mehr, als einfach ein Material gegen ein anderes auszutauschen – das Teil musste sich auch für den Druckguss eignen. Um zu gewährleisten, dass die Leistung des Bauteils auch nach dem Neuentwurf unverändert blieb, musste das Team ausgiebig Prototypen erstellen und jede Iteration testen.
„Diese Designiterationen in ein paar Stunden abschließen zu können und damit sogar zwei Iterationen an einem Tag durchzuführen, ist unglaublich hilfreich. Vor dem 3D-Druck hat man gehofft und gebetet, dass es direkt beim ersten Mal passt. Falls nicht, hatte man Wochen oder Monate mit dem Warten auf einen Artikel verschwendet, nur um festzustellen, dass man ihn nochmal anpassen und wieder raussenden musste“, erinnert sich Tryson.
Nachdem betriebsintern ein Prototyp eines Designs angefertigt wurde, führte Dorman Funktionstests durch, um sicherzustellen, dass das Bauteil wie vorgesehen funktionierte.
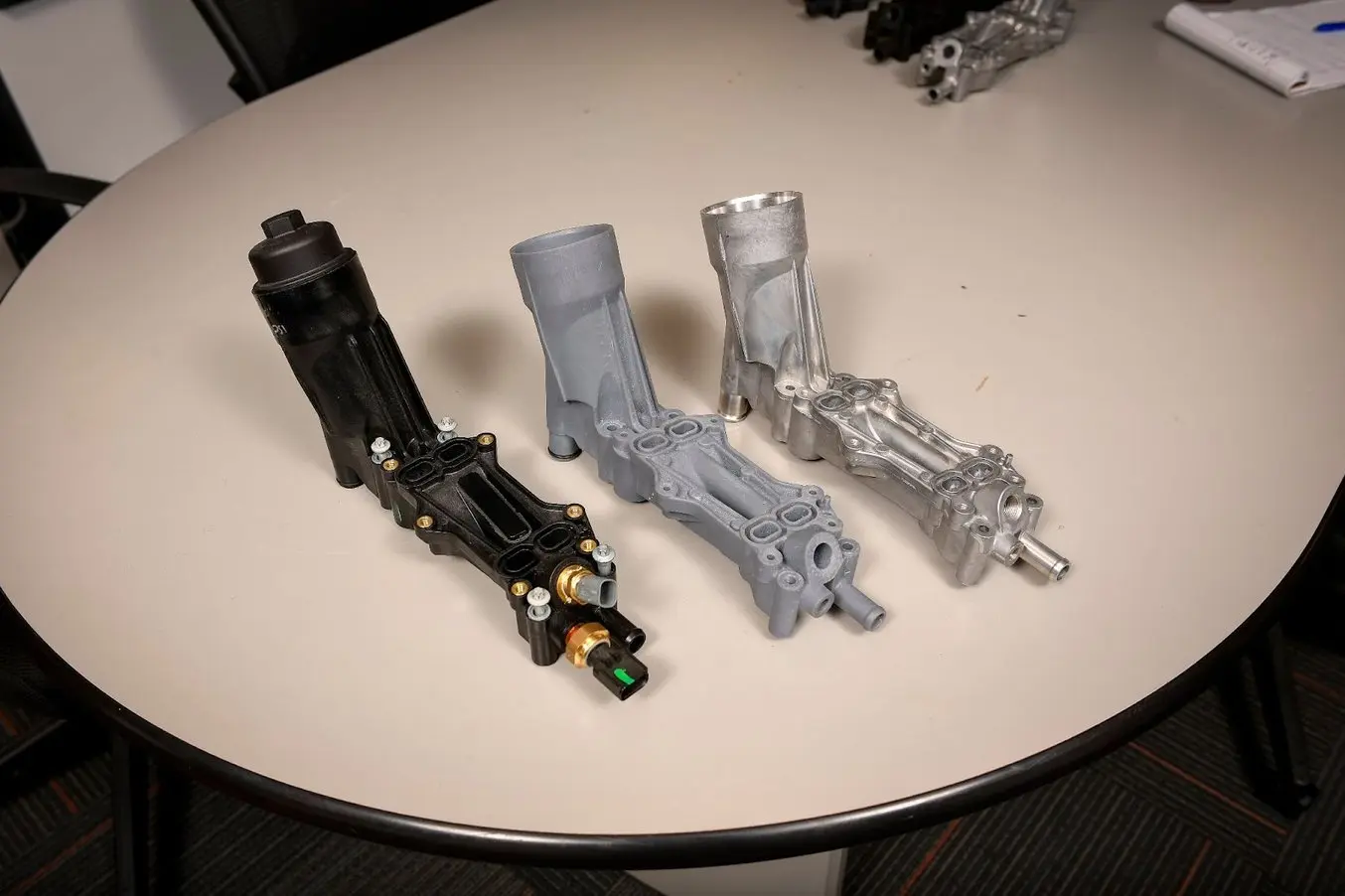
Diese Motorkomponente erlitt in zahlreichen Fahrzeugen einen Defekt. Hier sind mehrere Iterationen der Neuentwicklung von Dorman abgebildet.
Der Validierungsprozess
Da jedes Produkt eine andere Funktion erfüllt, sind auch alle Testprotokolle und Validierungsprozesse verschieden. Wenn etwa eine Durchflussprüfung für die Valdierungsprozesse gleich zweier verschiedener Teile erforderlich ist, werden aufgrund der verschiedenen Teilgeometrien dennoch unterschiedliche Halterungen benötigt.
Vorrichtungen für Funktionstests zu fertigen, gehört zum Tagesgeschäft für unsere Formlabs-3D-Drucker. Aus allen Materialien, von Elastic Resin bis zu Rigid 10K Resin und allem dazwischen. Das ist ein Riesengewinn in Sachen Durchlaufzeit und Kosten.
Chris Allebach, Leiter der additiven Fertigung, Dorman Products
Bevor das Unternehmen 3D-Drucker in seinen Prozess integrierte, war ein Hindernis für schnelle Produktentwicklung der Mangel an maßgefertigten Testvorrichtungen. Für ein Unternehmen wie Dorman, das mit Erstausrüstern Schritt halten muss, die jedes Jahr neue Modelle auf den Markt bringen, bedeuten Verzögerungen das Risiko, sich neue Produktchancen entgehen zu lassen.
Haltevorrichtungen sind speziell an jedes einzelne Produkt angepasst und können somit nicht in großen Stückzahlen bestellt werden – daher kommt Spritzguss als kostengünstige Fertigungslösung nicht infrage. Die einzige Option war bisher das Zerspanen, das sowohl teuer als auch zeitaufwendig war. Das Team musste sicherstellen, dass sein Design perfekt war, es zur Fertigung aussenden und wochenlang auf das Teil warten, bevor es die Validierung abschließen konnte.
„Für Halterungen und Lehren mussten wir uns auf Metallwerkstätten stützen, die fünf bis sechs Wochen dafür benötigten. Die Kosten lagen etwa fünf- bis zehnmal höher pro Teil und hinsichtlich der Geometrie waren wir durch die konventionellen Fertigungsverfahren eingeschränkt. Mit den 3D-Druckern können wir Testvorrichtungen und Lehren jetzt zugleich mit den Prototypen des Produkts entwickeln. Wenn wir uns für ein endgültiges Design entscheiden, steht uns also auch die richtige Vorrichtung für den Test zur Verfügung. Wir versuchen dabei so proaktiv wie möglich zu sein“, sagt Allebach.
In einem Validierungsprozess wurden für eine Schlauchprüfung unter Druck zwei 3D-gedruckte Testvorrichtungen benötigt. Eine der Vorrichtungen diente dazu, den Schlauch an einem Ende zu verschließen und durch das Durchleiten von Flüssigkeit den Grenzwert der Druckbeaufschlagung zu ermitteln. Die andere Vorrichtung simulierte die Geometrie des Gegenstücks, das beim tatsächlichen Gebrauch an das Teil anschließen würde, nämlich einen großen Heizkörper unter der Motorhaube. Die Möglichkeit, lediglich die an das Teil anschließende Seite des Heizkörpers zu drucken, verschaffte dem Team eine größere Flexibilität und erlaubte es ihm außerdem, das Teil zur Fertigungsstraße zu senden und dort als zusätzliche Qualitätskontrolle Validierungstests mit Teilen durchführen zu lassen, die gerade gefertigt wurden.
„Wenn das Gegenstück ein riesiger Heizkörper ist, kann man nicht einfach einen Haufen dieser Heizkörper kaufen und versenden, nur um dann einen winzigen Abschnitt davon abzuschneiden. Mit dem neuen Verfahren fertigen wir einfach, was wir wollen, produzieren es in großen Mengen und verteilen es. Falls ein Teil kaputtgeht, dann kostet das letztendlich nur ein paar Dollar und wir drucken einfach ein neues“, so Tryson.
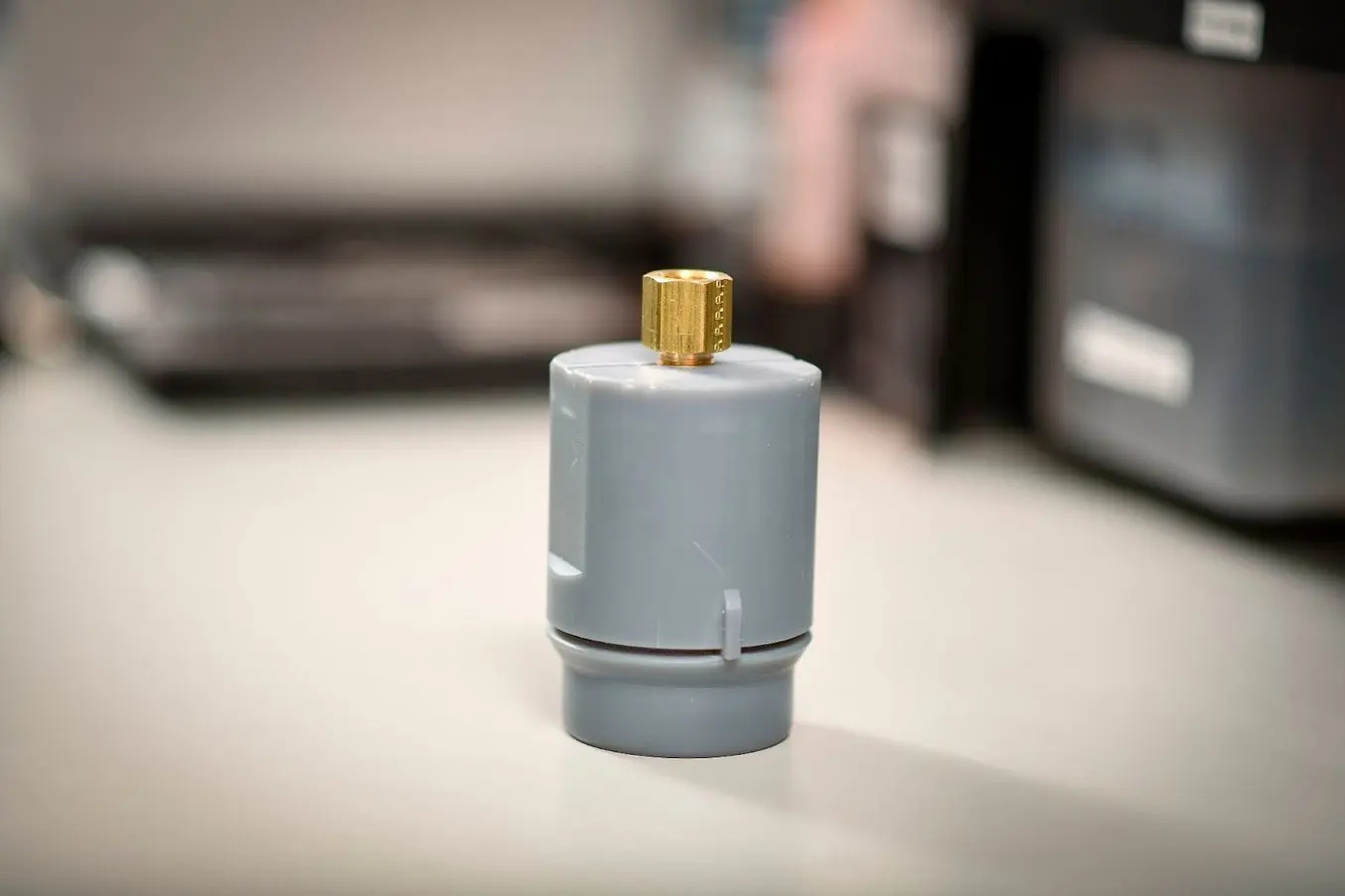
Eine der beiden Testvorrichtungen für die Schlauchprüfung unter Druck.
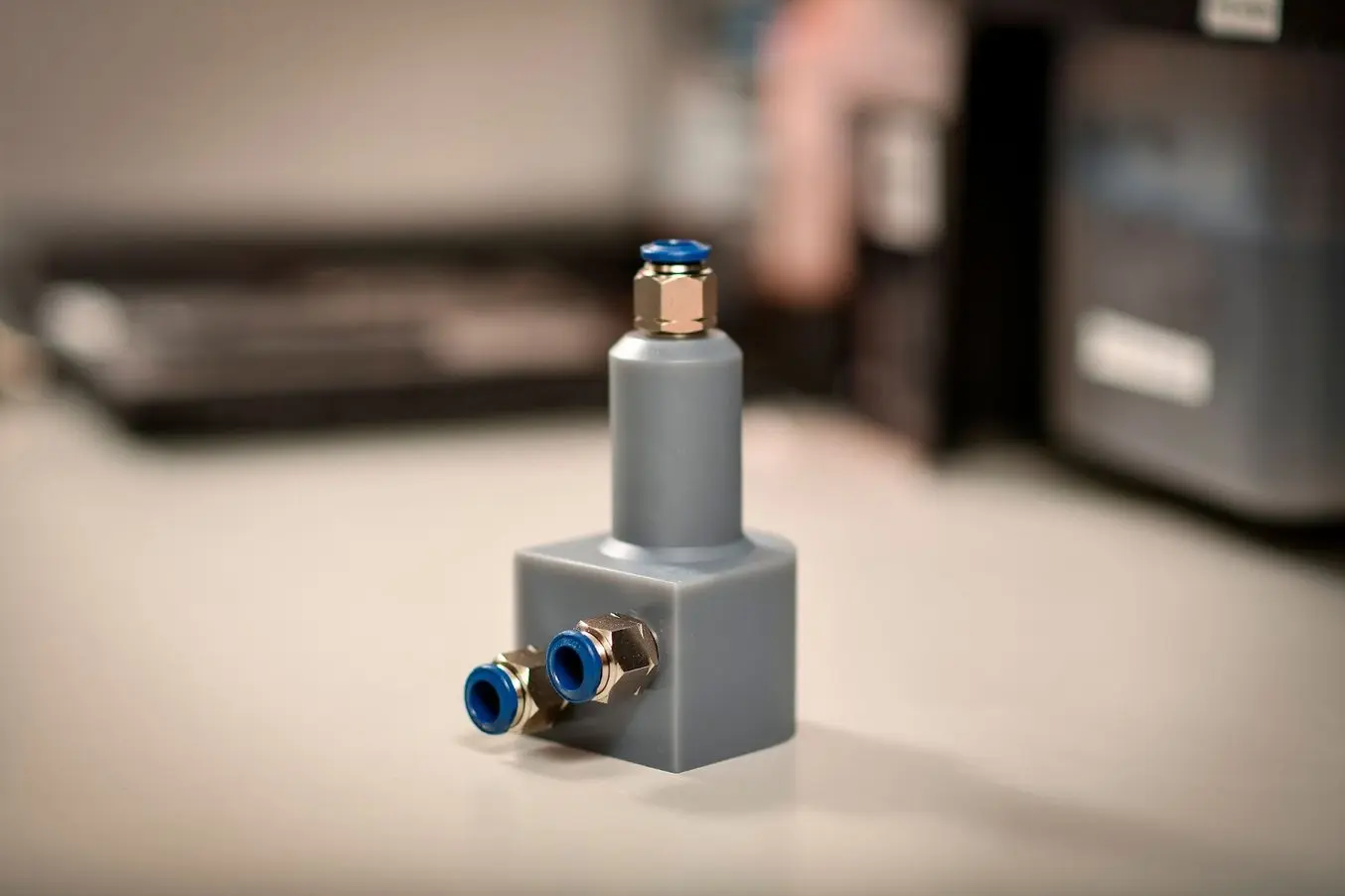
Die maßgefertigte Vorrichtung zur Simulation der Geometrie des Gegenstücks, sodass kein vollständiger Heizkörper für die Passungsprüfung benötigt wird.
Enge Toleranzen für Go/No-Go-Prüfungen
Bevor diese Produkte in den Handel gelangen und in Kundenfahrzeugen installiert werden können, muss das Team von Dorman genau herausfinden, wieviel Maßabweichungen die Teile tolerieren können. Hierzu führt das Team eine Maßanalyse durch, mit der es Teile entweder als "Go" oder "No-Go" beurteilt. In einigen Fällen können hierfür enge Toleranzen erforderlich sein – ob sich diese in einer 3D-gedruckten Lehre einhalten ließen, dessen waren sich Tryson und Allebach vor dem Erhalt ihrer Drucker Form 3+ und Form 3L nicht sicher.
„Wir stellen eine Menge Lehren mit Formlabs-Druckern her, da wir so gute Toleranzen erreichen. Ein Teil, das ich nicht für möglich gehalten hatte, war eine Go/No-Go-Lehre, die wir zur Prüfung von Bauteilen nutzen wollten. Der Ingenieur kam zu uns und erklärte, dass wir bei einem Durchmesser eine Toleranz von +/- 0,05 mm schaffen müssten. Es ist uns gelungen, das Teil mit einem Durchmesser zu drucken, dessen Toleranz bei 0,025 mm lag. Ich konnte kaum glauben, dass man auf einem Form 3L solche Toleranzen erreichen kann“, erzählt Allebach.
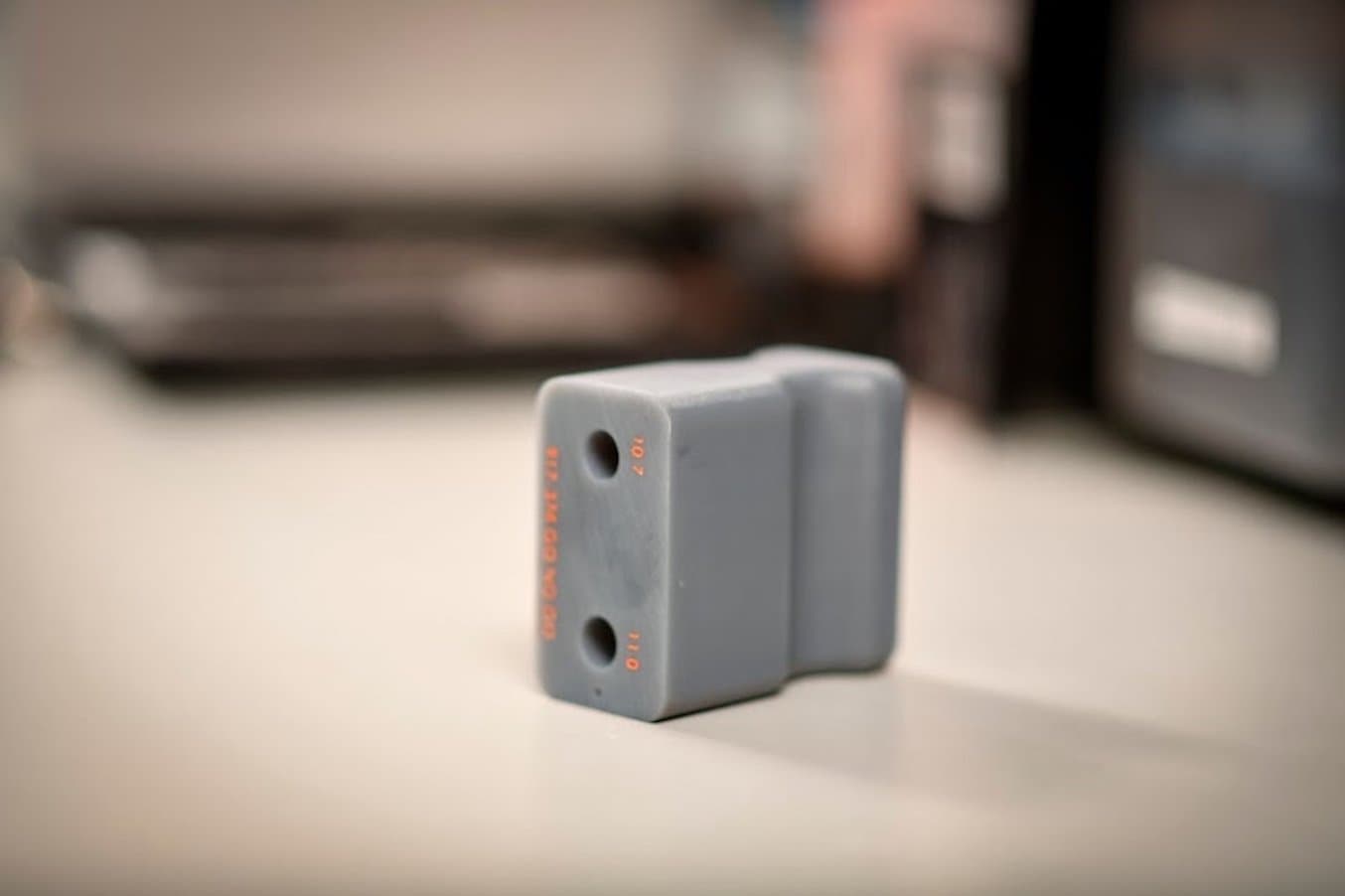
Eine aus Grey Resin gedruckte Go/No-Go-Lehre.
Dichtungen für Druckprüfungen durch Silikon-3D-Druck
Für Druckprüfungen von Komponenten zur Validierung neuer Designs muss das Team bestimmte Anschlüsse und Flächen versiegeln können. Allerdings steht nicht immer eine Geometrie mit geeigneter Passfläche zur Verfügung, um jedes Teil abzudichten. Deshalb muss das Team kreativ werden, was in den meisten Fällen bedeutet, individuelle Dichtungen und Vorrichtungen anzufertigen.
Früher hätte das Team die Komponenten im Labor ausgemessen, Formwerkzeuge aus Metall herstellen lassen und die individuellen Dichtungen mit den Formen in einer Dornpresse ausgeschnitten. „Das war wie Kekse ausstechen. Es war ein ineffizienter Prozess in Bezug auf den Materialverbrauch und die aufgebrachte Zeit durch unser Laborpersonal“, erzählt Allebach.
Der Wechsel zum 3D-Druck erlaubte es dem Team, Durchlaufzeiten und Kosten drastisch zu reduzieren, besonders im Hinblick auf die große Anzahl neuer Komponenten. „Wir haben Hunderte von individuellen Dichtungen für unseren Drosselklappentester gedruckt, die beide Enden des Drosselklappengehäuses versiegeln, sodass wir daran Durchflussprüfungen durchführen können“, berichtet Allebach.
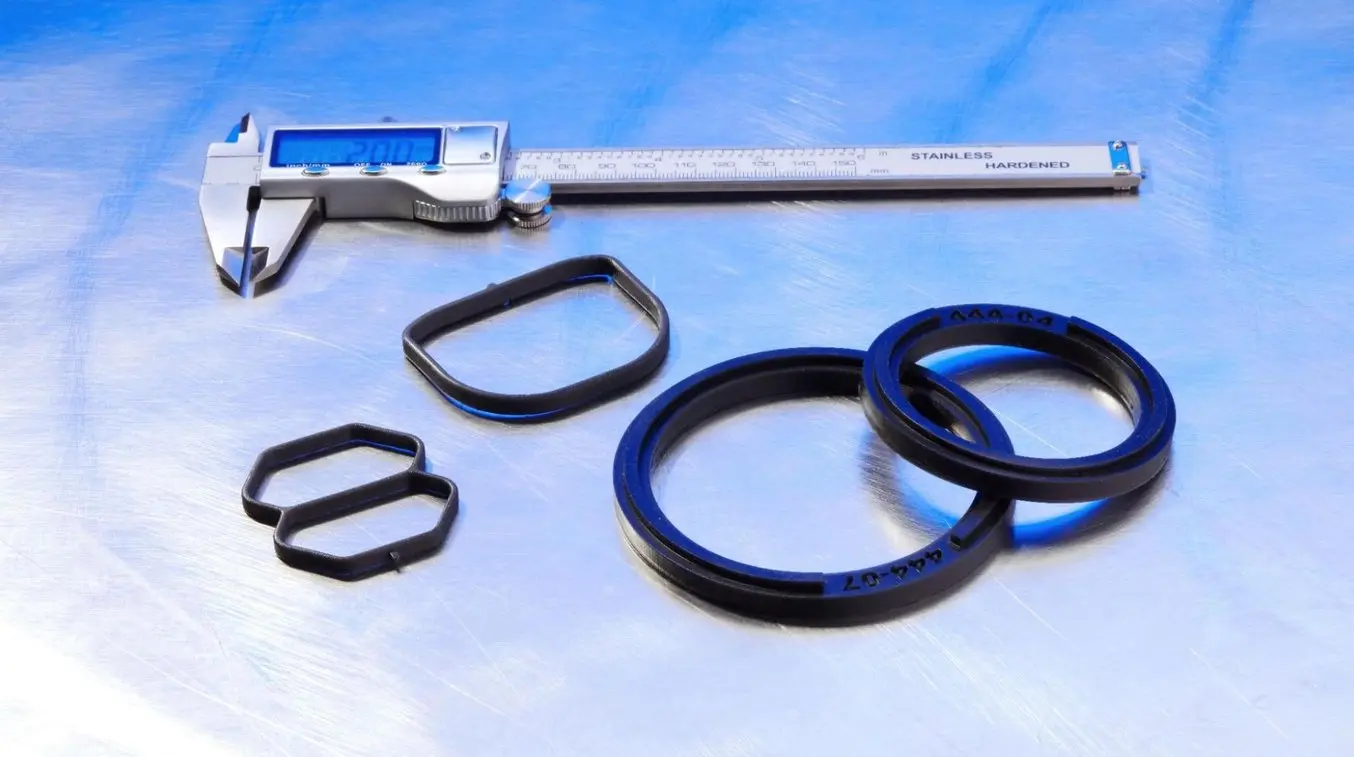
Individuelle Dichtungen von Dorman Products, die aus Silicone 40A Resin 3D-gedruckt wurden.
Zwar war in einigen Fällen auch Formlabs' silikonähnliches Elastic 50A Resin für solche Zwecke geeignet, doch das neue Silicone 40A Resin, das erste erschwingliche 3D-Druckmaterial aus reinem Silikon, dehnt die Grenzen möglicher Anwendungen noch weiter aus. „Es ist unglaublich, wie viel robuster Silicone 40A Resin [im Vergleich zu silikonähnlichen 3D-Druckmaterialien] ist“, so Allebach. „Es ist im Grunde ein Silikon-Kunstharz, also hatte ich das zwar erwartet, aber das Material verhält sich tatsächlich wie spritzgegossenes Silikon.“
Zwei der wichtigsten Eigenschaften, die das Team sich von Silicone 40A Resin versprach, waren chemische und thermische Beständigkeit. Über zwei Monate hinweg wurden die 3D-gedruckten Teile unter anderem in Öl und Waschlösung chemisch getestet und unter UV-Bestrahlung geprüft, woraufhin zusätzlich der Druckverformungsrest untersucht wurde. Die Rückfederung und andere mechanische Eigenschaften hielten den Anforderungen des Teams stand.
Dichtungen für Validierungstests
Durchlaufzeit | Kosten | |
---|---|---|
Schneiden von Silikonplatten mit gefrästen Metallformen | 2 Wochen pro Set | 250 € pro Set |
SLA-3D-Druck mit Silicone 40A Resin | 3 Stunden pro Set | 12 € pro Set |
„Individuelle Dichtungen herstellen zu können, die in einem Wärmealterungsofen getestet werden, in einer Umgebung, die den Motorraum simuliert, oder auch in Luft, Wasser, Kühlmittel, Öl oder jeglichen anderen Stoffen, mit denen das Teil in der Praxis in Kontakt kommt – das ist eine riesige Sache, besonders für uns.“
Chris Allebach, Leiter der additiven Fertigung, Dorman Products
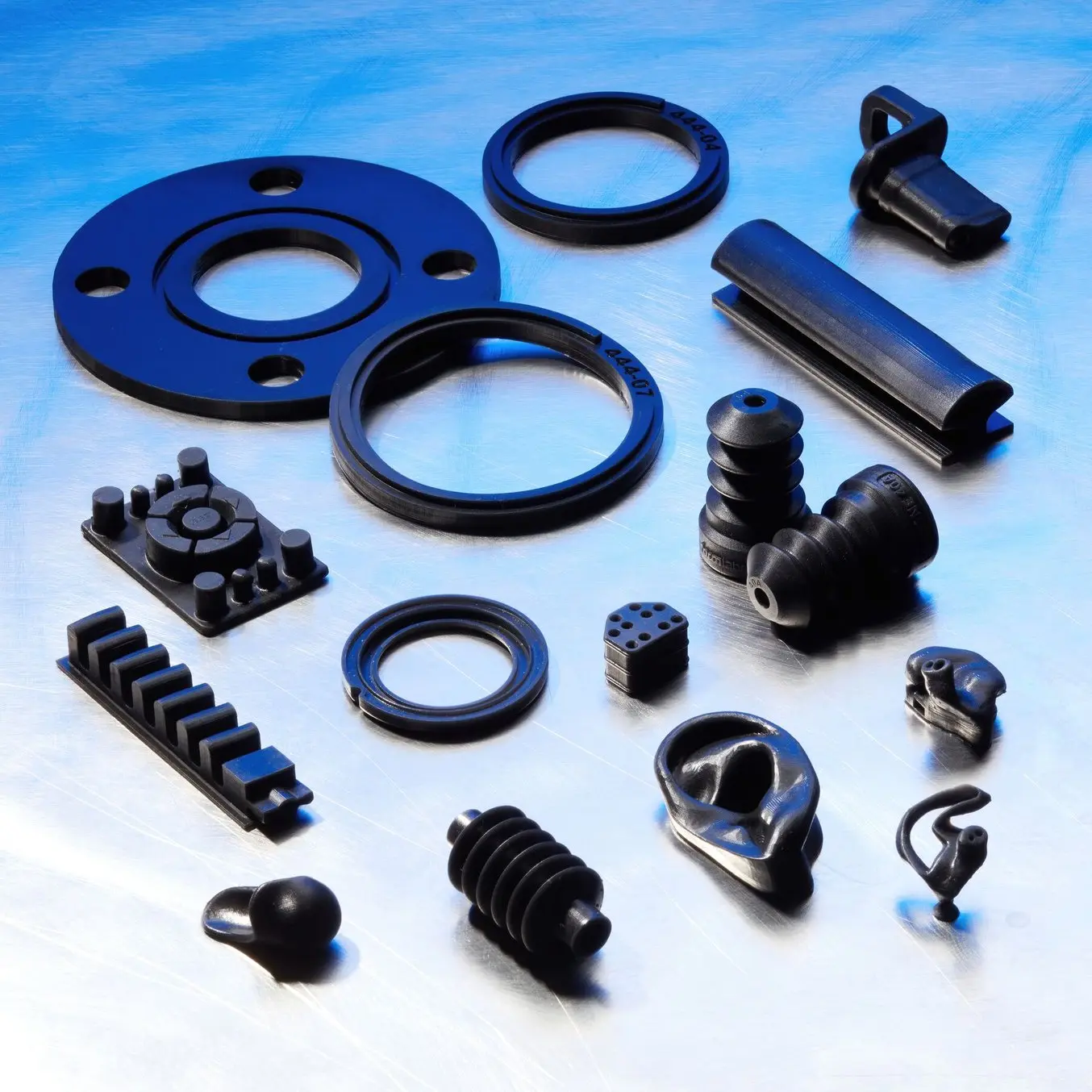
Einführung in Silicone 40A Resin
In diesem Webinar führt Sie unser Expertenteam für 3D-Druck durch die zentralen Vorteile und Anwendungsbereiche von Silicone 40A Resin und stellt die Materialeigenschaften und den Arbeitsprozess dieses Kunstharzes vor.
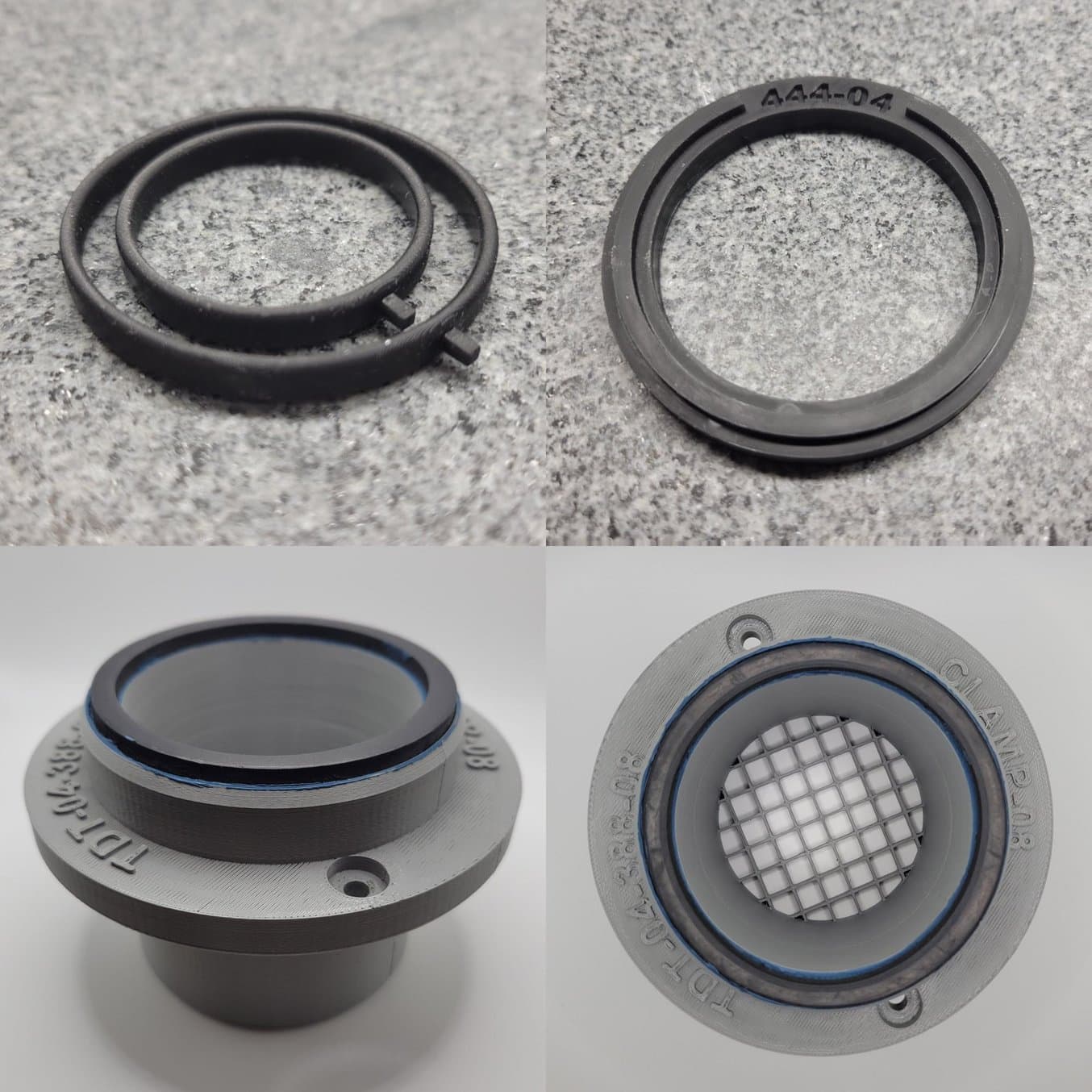
Individuelle Ansaugkrümmer-Dichtungen und 3D-gedruckter Adapter für Luftstromprüfungen.
Allebach war auch von der Gestaltungsfreiheit begeistert, die für flexible 3D-Druckmaterialien beispiellos ist.
„Die Druckbarkeit des Kunstharzes ist unglaublich. Ich hatte nicht erwartet, dass ein derart weiches Material feine Details so gut drucken können würde. Wir haben Teile gedruckt, die wir aus einem 40A-Material nie so gefertigt hätten. Sie wurden sonst immer spritzgegossen. In Bezug auf Druckbarkeit haben wir die Grenzen wirklich bis zu einem unglaublichen Maß ausgereizt. Ich konnte die Qualität der kleinen Geometrien unserer Druckteile einfach nicht fassen. Es hat uns alle vollkommen umgehauen, wie sich das Material anfühlt und wie es zurückfedert.“
Chris Allebach, Leiter der additiven Fertigung, Dorman Products
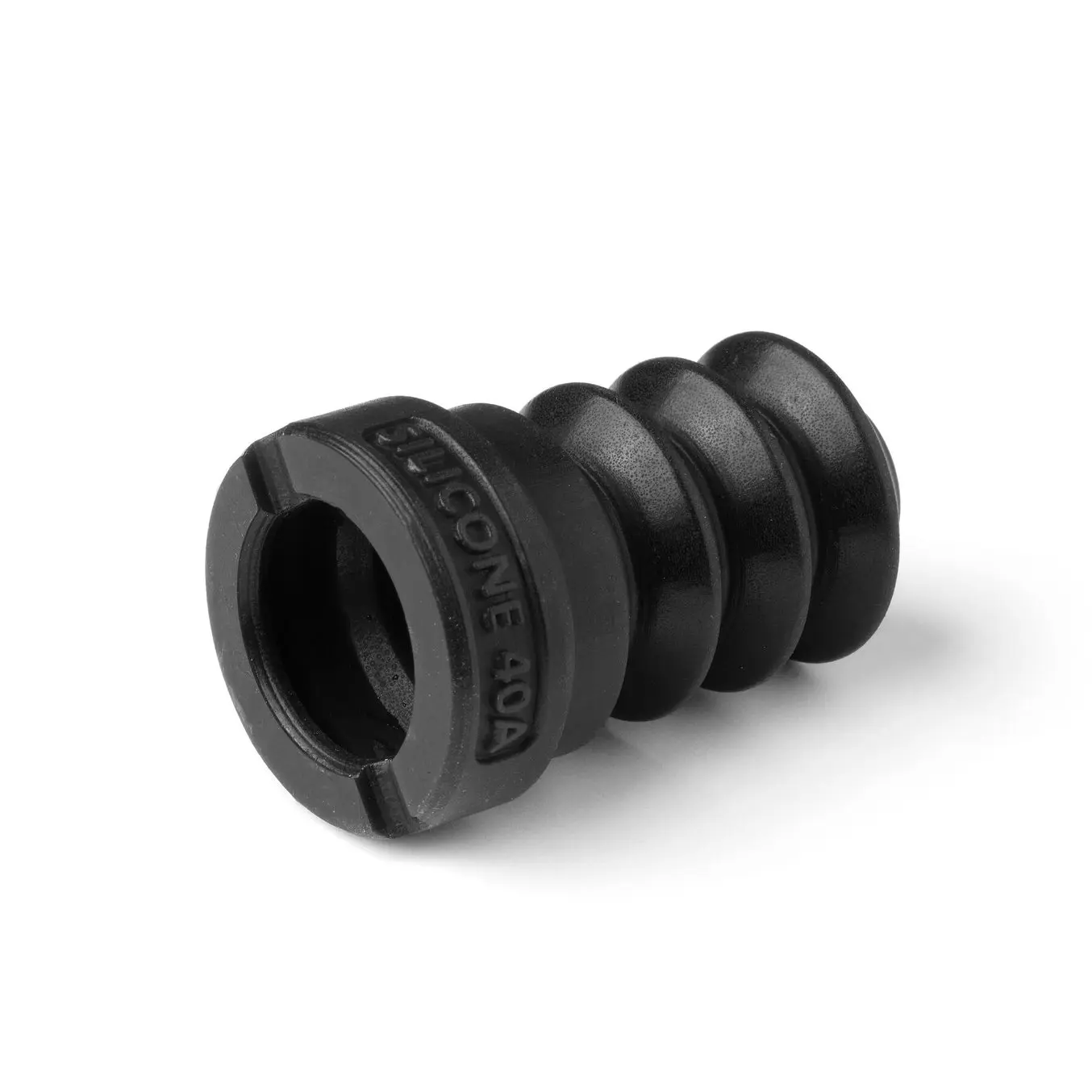
Kostenlosen Probedruck anfordern
Sehen und fühlen Sie selbst die Qualität von Formlabs. Wir senden Ihnen einen kostenlosen Probedruck aus Silicone 40A Resin an Ihren Arbeitsplatz.
Metallteile, die alle Vorstellungen übersteigen
Tryson und Allebach bearbeiten ihre Teile oft zusätzlich nach, bevor sie sie an die Marketing- und Vertriebsteams von Dorman weiterleiten. Bei Bauteilen, die letztendlich aus Metall massenproduziert werden, durchlaufen die SLA-Druckteile vor der Präsentation in Abteilungen mit Kundenkontakt noch einen Veredelungsprozess. Vor Kurzem druckte das Team Kugelzapfen für das Fahrgestell aus Grey Pro Resin und ließ diese galvanisieren, bevor es sie zu Marketingzwecken an andere Abteilungen weiterleitete (die Galvanisierung stammte von Repliform INC). Es gab allerdings ein Problem – die Oberflächenqualität war beinahe zu gut! „Das Marketing-Team erklärte uns: Diese Teile werden normalerweise geschmiedet oder gegossen und dann mit Zink beschichtet. Wenn wir dieses Teil verwenden, dann sieht das besser aus als das Bauteil, das am Ende geliefert wird“, erzählt Allebach.
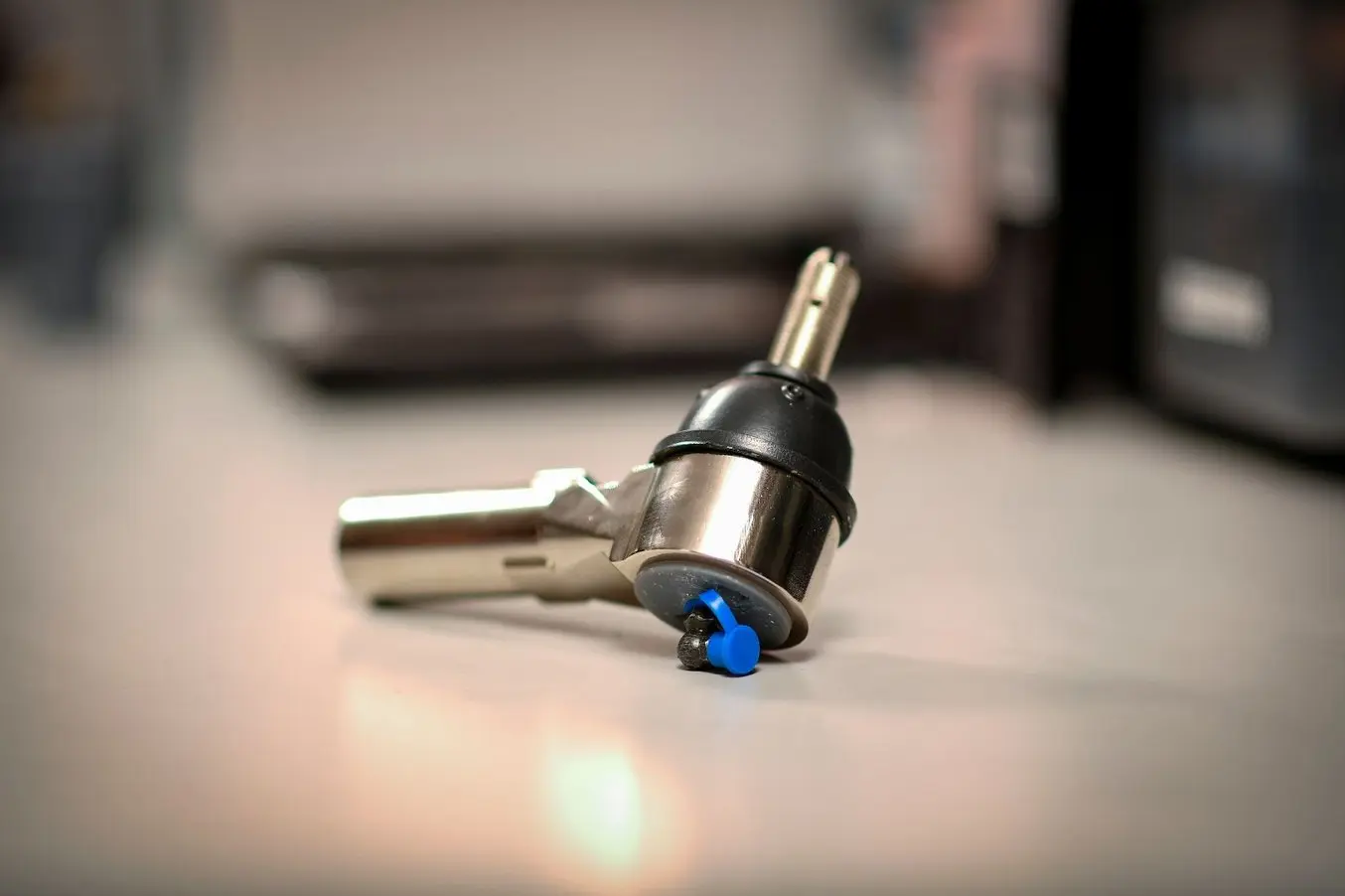
Eine galvanisierte Baugruppe.
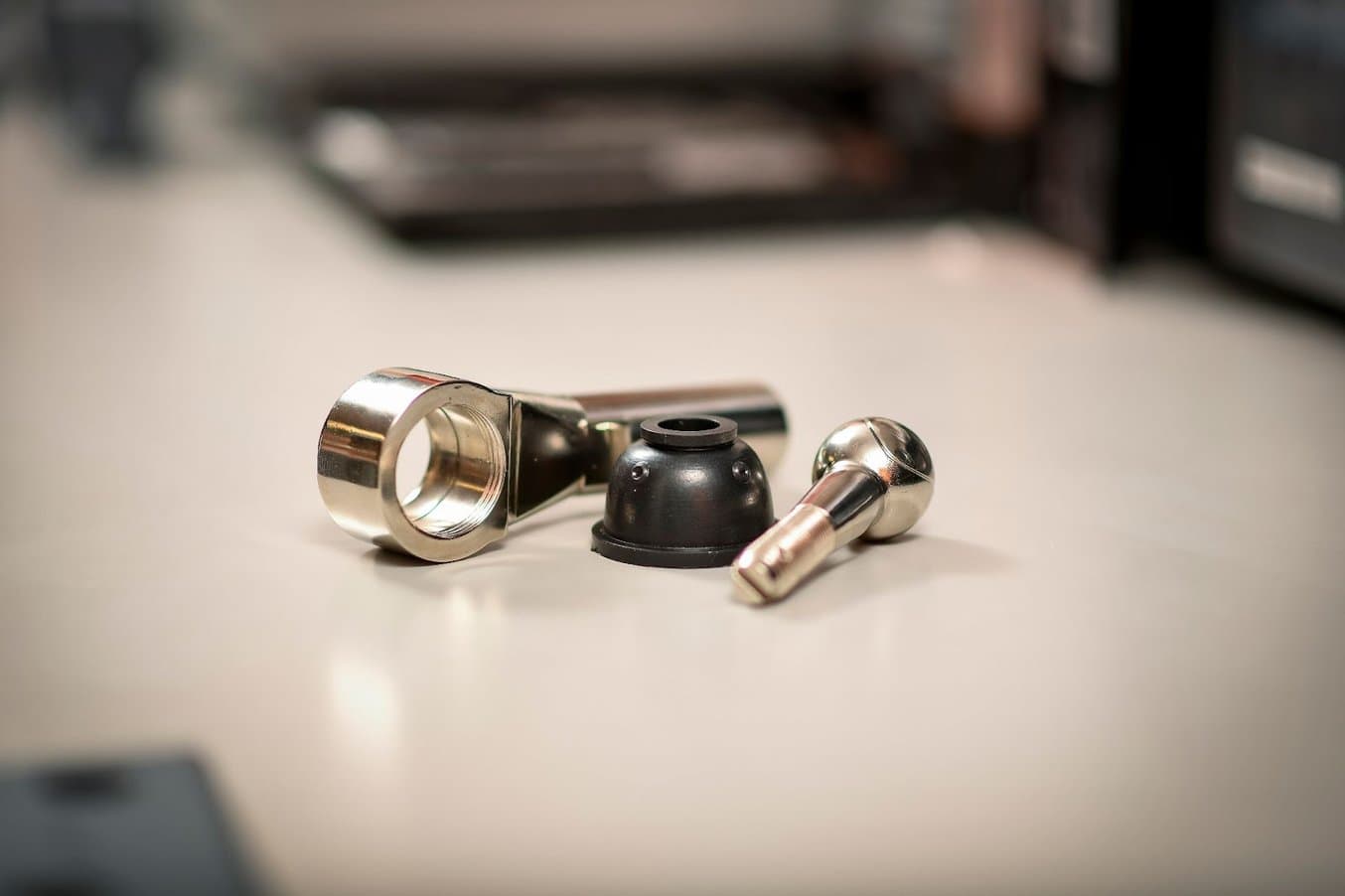
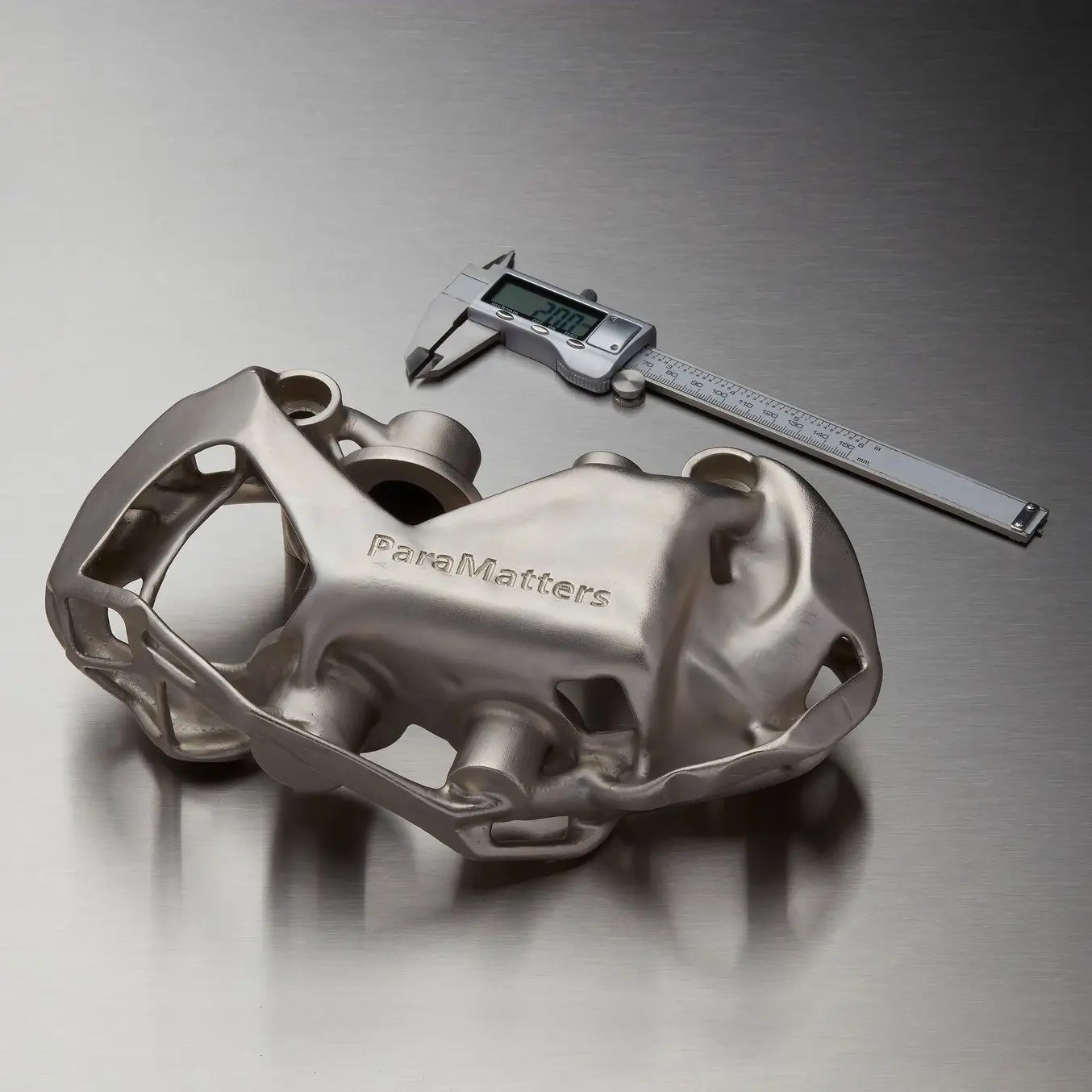
Metallische Festigkeit: Strategien und Anwendungsfälle zur Galvanisierung von SLA-Teilen
Im Folgenden erfahren Sie, wie Ingenieurteams 3D-Druckteile aus Kunstharz mit Metall überziehen und warum solche Hybridteile eine überraschend große Anzahl an Anwendungsbereichen eröffnen, z. B. durch mehr Festigkeit und Haltbarkeit in der Endverwendung.
Hohe Produktivität rentiert sich in Rekordzeit
Seit Dorman vor zehn Jahren den ersten FDM-Drucker anschaffte, haben Allebach und Tryson ständig neue Drucker hinzugefügt, da die Kapazitäten der vorhandenen Geräte stets ausgelastet waren. Das Team nutzt dabei die gesamte Materialpalette auf seinen SLA-Druckern von Formlabs.
Obwohl Dormans jährlicher globaler Umsatz bei fast 1,35 Mrd. Dollar lag (Stand 25. Dezember 2021), muss die Anschaffung neuer Ausrüstung dennoch begründet werden. „Wir entschieden uns für den Form 2 aufgrund seiner Oberflächenqualität und Maßgenauigkeit und stellten fest, dass er sich für uns schon innerhalb von zwei Monaten rentierte. Wenn wir eine Kostenbegründung erstellen oder den ROI für einen beliebigen Formlabs-Drucker berechnen, zeigt sich, dass er sich statt in zwei Jahren schon innerhalb von Monaten bezahlt macht. Das stärkt bei unserem Führungsteam das Vertrauen darin, dass sich die Investition in 3D-Druck lohnt“, sagt Tryson.
Dank genau dieses Vertrauens war es Tryson und Allebach möglich, vor etwas über einem Jahr in ihren ersten großformatigen Drucker zu investieren, den Form 3L. Genau wie ihre anderen 3D-Drucker ist dieser 10-12 Stunden pro Tag in Betrieb, manchmal sogar über Nacht. Da das Team mit sämtlichen Kunstharzen der Materialbibliothek arbeitet, steigerte die Option, die mechanischen Eigenschaften sowohl für kleine als auch große Teile genau anzupassen, die Effizienz ihrer Arbeitsprozesse enorm.
Für nur 10 000 $ SLA-Teile in dieser Größe drucken zu können, ist unglaublich. Das gibt es sonst nirgendwo auf dem Markt. Durch die Kosten- und Zeitersparnis schon bei nur wenigen Teilen haben sich die Drucker in unserem Fall schnell bezahlt gemacht.
Eric Tryson, Mechanical Design Team Manager, Dorman Products
Der Blick in die Zukunft mit 3D-Druck
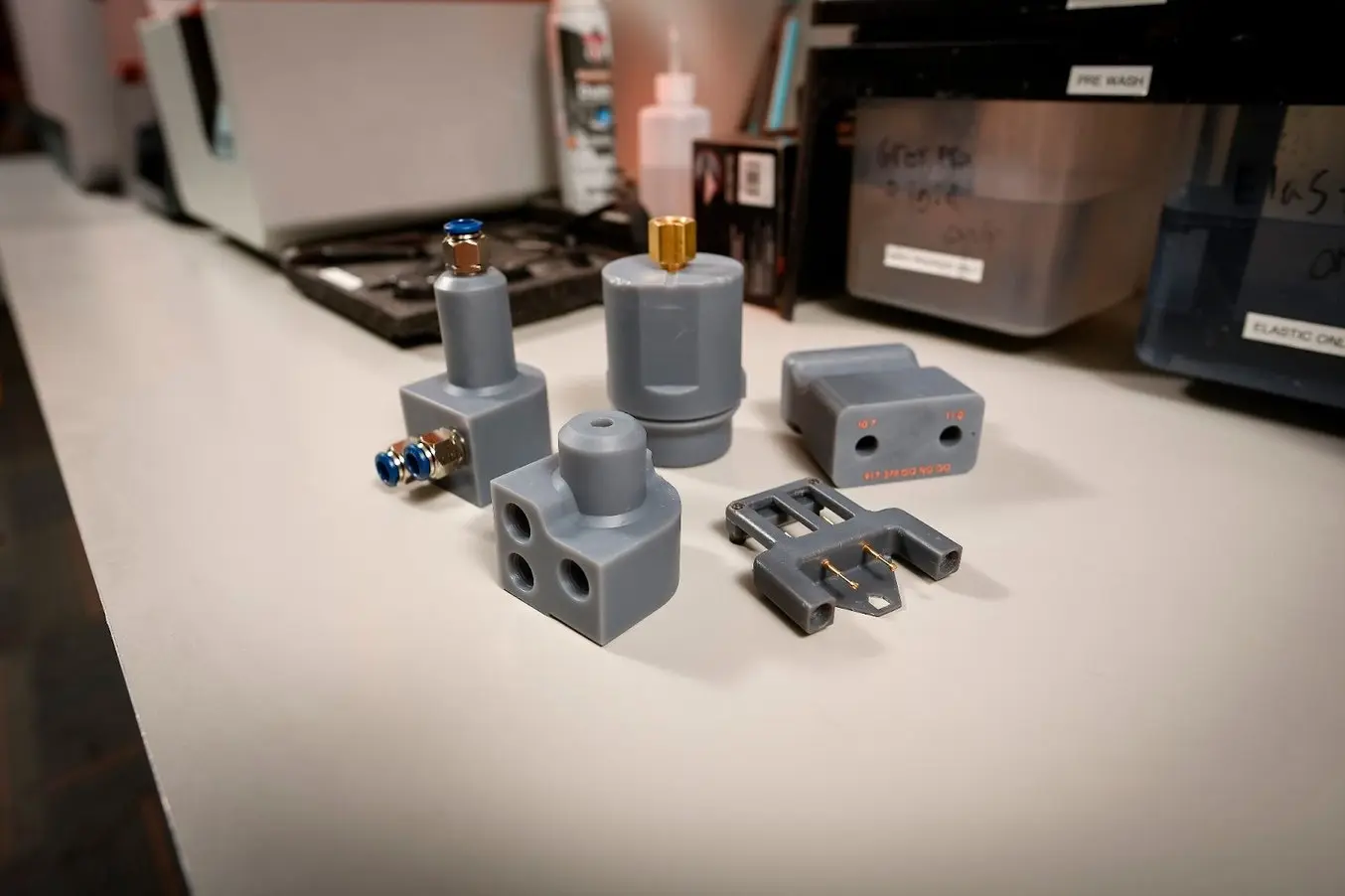
Die Komplikationen der Lieferketten werden sich voraussichtlich nicht in nächster Zukunft lösen, und auch die Preise für Neu- und Gebrauchtwagen sind nach wie vor hoch. Durch den Einstieg vieler Erstausrüster in die Herstellung von Elektroautos werden viele Bauteile neuer Modelle immer leichter, sind auf neue (und häufig additive) Fertigungsverfahren optimiert und werden aus unkonventionellen Materialien gefertigt. Die Automobilindustrie stützt sich immer stärker auf additive Fertigungstechnologien, sowohl bei Originaldesigns als auch für Aftermarket-Teile. Mit seiner jetzigen Ausrüstung ist Dorman Products zwar bereits dem Trend voraus, doch Allebach und Tryson schauen dennoch bereits weiter in die Zukunft.
„Wir können Bauteile mit Leichtigkeit entwerfen und herstellen, sind nicht durch traditionelle Fertigungsmethoden eingeschränkt und haben auch anderen Abteilungen beigebracht, dass Hinterschneidungen oder Grate jetzt keine Zusatzkosten mehr verursachen wie bei der Zerspanung. Das hat Türen geöffnet und uns neue Ideen verschafft, um Vorrichtungen genau so zu entwerfen, wie sie sie haben wollen“, berichtet Allebach.
Nachdem das Unternehmen sich seiner Kapitalrendite sicher ist und immer mehr Abteilungen Routine in der Nutzung der FDM- und SLA-Drucktechnologien gewonnen haben, ist das Team nun bereit, als Nächstes in den 3D-Druck mit Pulverbettfusion einzusteigen. „Mit FDM haben wir eine schnelle und einfache Lösung, mit SLA eine hohe Genauigkeit und Haltbarkeit, aber wenn es um hochfunktionale Bauteile in niedrigen Stückzahlen geht, dann wird letztendlich Pulver die Antwort für uns sein“, meint Tryson.