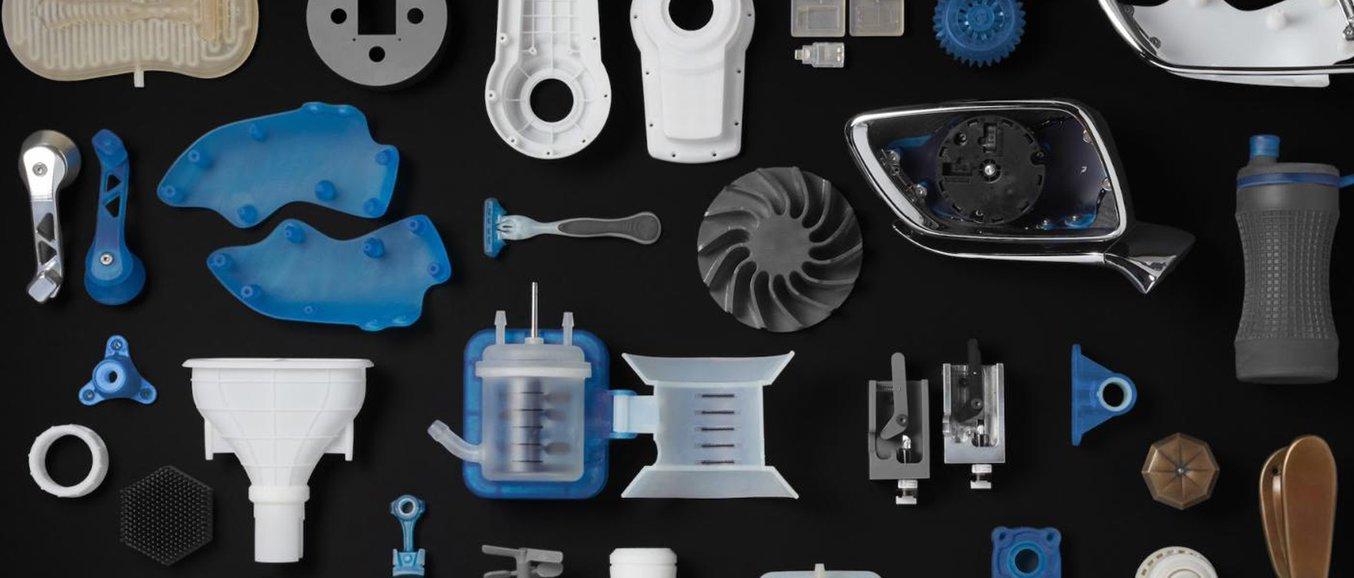
Additive Fertigungs- (Additive Manufacturing, AM) oder 3D-Druck-Technologien erstellen dreidimensionale Teile aus computergestützten Entwürfen (Computer-Aided Design, CAD), indem Sie Schicht um Schicht Material hinzufügen, bis ein fertiges Teil entsteht.
Während AM-Technologien bereits seit den 1980ern existieren, hat die Branche ihren prägendsten Hype-Zyklus zu Beginn der 2010er-Jahre durchlebt. Verfechter der Technologie vertraten damals die Meinung, dass sie in Nutzeranwendungen und dem Nachbestellungsgeschäft vom Home Depot bis hin zu UPS umfassend zur Anwendung kommen würden.
Seit dieser extreme Hype vor einigen Jahren abgeklungen ist, haben professionelle Drucktechnologien auf viele sehr konkrete Arten und Weisen ein fortgeschrittenes Reifestadium erreicht. Dank jüngster Fortschritte im Hinblick auf Maschinen, Materialien und Software ist der 3D-Druck für ein breiteres Spektrum an Unternehmen zugänglich geworden. Dadurch können immer mehr Unternehmen Werkzeuge nutzen, die bisher auf wenige Hightech-Branchen beschränkt waren.
Heute beschleunigen gewerbliche Desktop- und Benchtop-3D-Drucker die Innovation. Unternehmen in vielen verschiedenen Branchen wie Technik, Fertigung, Dental, Gesundheit, Bildung, Unterhaltung, Schmuck und Hörakustik & Otoplastiken greifen auf sie zurück.
Im Folgenden finden Sie einen ausführlichen Überblick über fünf wichtige Trends, die für die additive Fertigung prägend waren, sowie Prognosen für die Zukunft.
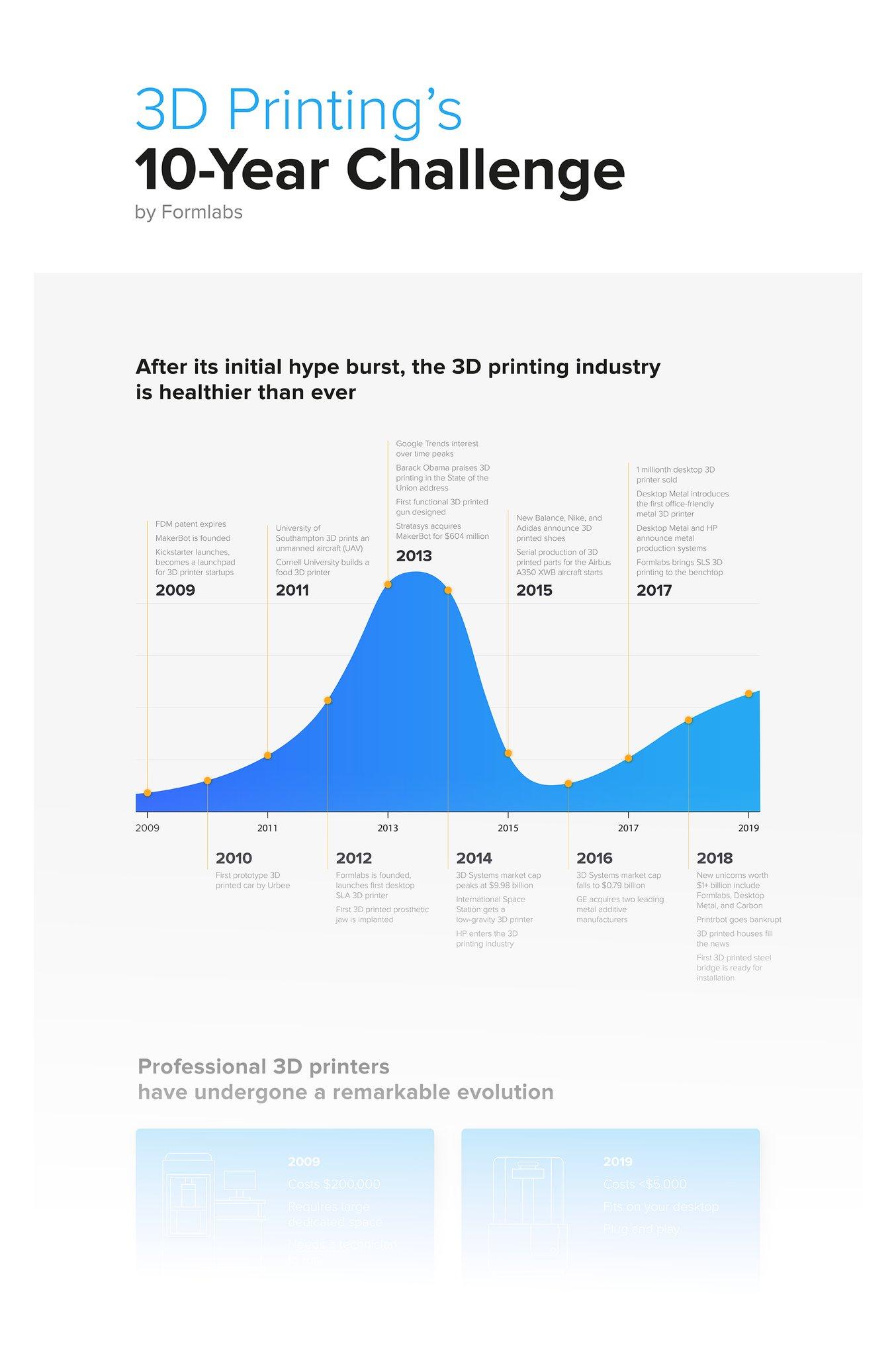
Laden Sie die komplette Infografik herunter, um einen Überblick darüber zu erhalten, wie sich die additive Fertigungsbranche im Verlauf des letzten Jahrzehnts gewandelt hat.
Dieser Artikel erschien ursprünglich im Digital Factory Report. Laden Sie den kompletten Bericht herunter, um mehr Einblicke zur digitalen Transformation in der Fertigung zu erhalten, und registrieren Sie sich für The Digital Factory am 7. Mai 2019 in Boston. Dort hören Sie Einsichten von Führungskräften, die topmoderne Fertigungstechnologien einführen und zur Transformation ihrer Unternehmen verwenden.
Überblick: Die additive Fertigung heute
Der 3D-Druck-Markt mit einem Umsatz von 6 Mrd. USD im Jahr 2017 soll Prognosen zufolge pro Jahr um 30,2 % wachsen und 2022 einen Umsatz von 22 Mrd. Usd erreichen.
- Der 3D-Druck wird seit Jahren zur Prototypenfertigung und Produktentwicklung verwendet. Mittlerweile hat die Technologie einen Reifegrad erreicht, der eine breite Anwendung in der Fertigung erlaubt.
- Verbesserte Technologien für den Druck von hochwertigen fertigen Teilen mit hohem Durchsatz und eine Reihe verbesserter Materialien machen den 3D-Druck für kleine und mittlere Fertigungsunternehmen praktikabel – in manchen Fällen bestehen die Produktionsbatterien gar aus zehntausenden Einheiten.
- Zusätzlich zur Herstellung fertiger Produkte bietet der 3D-Druck gewichtige Vorteile für die „Hybrid-Fertigung“ als Zwischenschritt, der parallel zu konventionellen Prozessen zur Anwendung gebracht wird, zum Beispiel zur Herstellung von Modellen, Werkzeugen, Mustern und Vorrichtungen.
- Kompakte, erschwingliche „Desktop“-3D-Drucker bieten mehr Funktionen und sind teuren gewerblichen 3D-Druckern in Sachen Kosten und Durchsatz überlegen, wenn sie parallel betrieben werden.
- Fertigungsunternehmen arbeiten daran, den mit den Workflows zur additiven Fertigung (Additive Manufacturing, AM) verbundenen Arbeitsaufwand zu minimieren, was für die Verwendung von 3D-Druck für die Fertigung mittlerer mit großer Volumina erforderlich ist.
- Die Investitionen in Metall-AM sind sprunghaft angestiegen; Prozessverbesserungen und neue Technologien senken die Stückkosten.
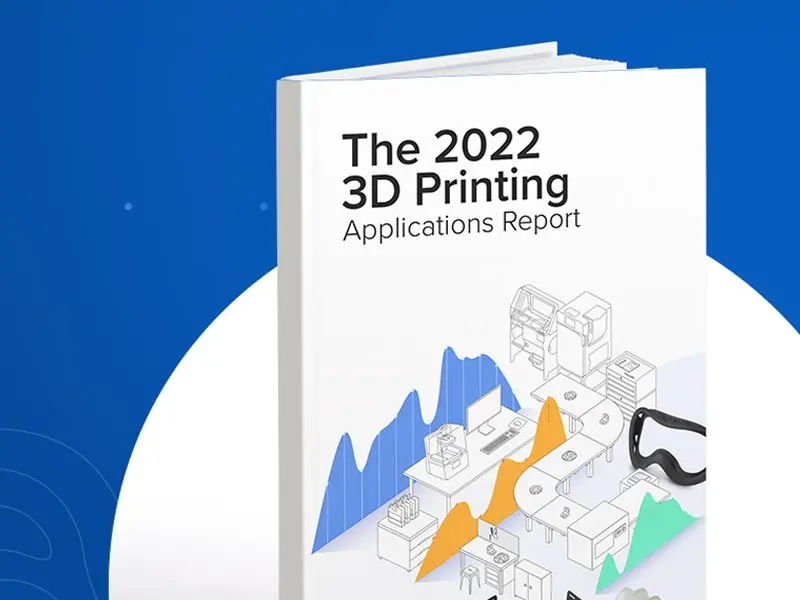
Der 3D-Druck-Anwendungsbericht 2022
Dieser Bericht untersucht die vergangenen, gegenwärtigen und zukünftigen Trends in Bezug auf die Rolle des 3D-Drucks in der Fertigung.
Die wichtigsten Trends in der additiven Fertigung:
Kompakte, modulare Systeme für Kunststoff
Während ihrer ersten drei Jahrzehnte waren 3D-Drucker aufgrund ihrer Kosten und komplexen Anwendung großen Unternehmen und Dienstleistungsbüros vorbehalten. Anfang der 2010er Jahre wagten sich aufgrund von besserer eingebetteter Hardware, ausgelaufenen Patenten und einem höheren technologischen Reifegrad Hunderte von Unternehmen auf den Markt und brachten eine Unmenge von 3D-Druckern heraus. Eine Blase bildete sich.
Die erste Technologie, die für den Desktop verfügbar wurde, war die Schmelzschichtung (Fused Deposition Modelling, FDM). 3D-Drucker, die Kunststoff schmelzen und selektiv verfestigen, wurden für Verbraucher erschwinglich, doch ihre Funktionalität war nach wie vor beschränkt. Auf die erste Begeisterung folgt schnell die große Ernüchterung und der Traum, dass 3D-Drucker ganz verständlich zu jedem Haushalt gehören würden, wurde nie Realität.
Doch jenseits des überhitzten Verbrauchermarktes für 3D-Drucker entwickelten sich die additiven Technologien rasch weiter. Drucker zur gewerblichen Nutzung in Maschinenbau, Prototypenherstellung und Fertigung überschritten wichtige Schwellen bezüglich Druckqualität, Zuverlässigkeit und Kostenstruktur.
Die zweite Technologie, die in einem erschwinglichen, kompakten und einfach zu nutzenden Format verfügbar wurde, war die Stereolithographie (SLA). 2013 brauchte Formlabs mit dem Form 1 einen hochauflösenden 3D-Drucker zu einem Kostenpunkt von 3300 USD auf den Markt – die Technologie war bis dato nur in 3D-Druckern für über 80 000 USD verfügbar gewesen. Die Technologie ermöglichte die Nutzung einer Vielzahl funktionaler Materialien und erweiterte somit die Anwendungsgebiete des 3D-Drucks in Produktdesign und Maschinenbau sowie in der Dental- und Schmuckbranche.
Die dritte Welle von 3D-Drucktechniken, die für den Desktop (oder genauer gesagt für den Benchtop) verfügbar wurde, basiert auf selektivem Lasersintern (SLS), das schon seit längerem eine unverzichtbare Technologie für industrielle Nutzer war. Anders als bei anderen Desktop-AM-Prozessen werden per SLS ausgesprochen robuste Teile aus Thermoplasten wie Nylon hergestellt, die fast so beständig sind wie im Spritzgussverfahren gefertigte Teile. Nicht verschmolzenes Pulver stützt die Arbeitsteile, wodurch mehr Teile auf einmal gedruckt und ein höherer Durchsatz erzielt werden kann. Zudem erfordert so die Nachbearbeitung weniger Arbeit.
Bis vor drei Jahren kosteten die günstigsten SLS-Drucker etwa 200 000 USD (und die größten industriellen Systeme bis zu mehreren Millionen). Benchtop-SLS-Drucker, mit denen Nylonteile gefertigt werden, sind jetzt in der Preisspanne um 10 000 USD verfügbar. Damit wird die Technologie mehr Nutzern zugänglich und die Fertigungskosten sinken beträchtlich, wenn man die Anschaffungskosten einrechnet. Benchtop-SLS hat das Potential, für mehr als nur die Prototypenfertigung zur Anwendung zu kommen und fertige Teile zu produzieren.
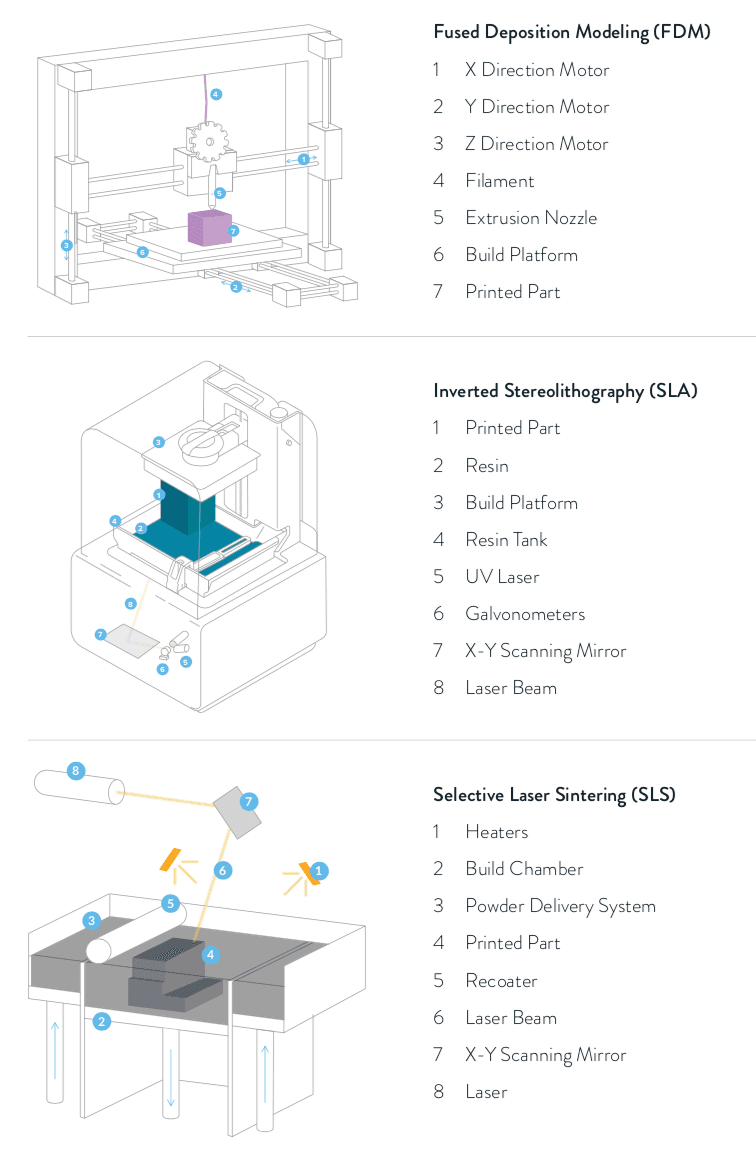
Die drei häufigsten Kunststoff-3D-Druck-Technologien. 3D-Drucker auf Basis der Schmelzschichtung (Fused Deposition Modeling, FDM) fertigen Teile, indem sie Thermoplastfilament schmelzen und extrudieren. Bei der Stereolithographie (SLA) wird flüssiges Kunstharz mit einem Laser gehärtet. Selektives Lasersintern (SLS) bringt einen Hochleistungslaser zur Anwendung, um kleine Partikel von Polymerpulver zu verschmelzen.
3D-Druck mit Metallen
Der Markt für die additive Fertigung war schon immer interessiert an Metallen, und die Investitionen in den 3D-Druck von Metall ist in den vergangenen Jahren sprunghaft angestiegen.
Der 3D-Druck von Metallen verbindet die Vorteile außergewöhnlicher hochperformanter Teile aus Stahl, Titan, Nickellegierungen und Aluminium mit komplexen geometrischen Formen für anspruchsvolle Branchen mit hoher Wertschöpfung wie Aeronautik und medizinische Geräte. Diese Branchen können den 3D-Druck zur Fertigung von Metallteilen voll ausnutzen – insbesondere für generativ designete Teile mit Gitterstrukturen, was Materialbedarf und Gewicht senkt.
Die verbreitetsten traditionellen Metall-AM-Systeme sind das selektive Laserschmelzen (Selective Laser Melting, SLM) und das direkte Metalllasersintern (Direct Metal Laser Sintering, DMLS). Wie Kuntstoff-SLS erstellen diese Verfahren Objekte aus dünnen Schichten von Pulvermaterial, indem sie sie selektiv mithilfe einer Hitzequelle schmelzen. Aufgrund des höheren Schmelzpunktes von Metallen sind stärkere Laser und eine industrielle Arbeitsumgebung von Nöten.
Bis vor Kurzem waren diese Metall-3D-Drucker aufgrund enormer Kosten und Komplexität nur zur Fertigung einiger weniger teurer, in geringen Stückzahlen hergestellter Produkte praktisch einsetzbar. DMLS- und SLM-Metalldrucker sind ab 400 000 USD zu haben und können leicht über 1 000 000 USD kosten. Für ihren Betrieb sind hoch spezialisierte Fachkräfte und penibel kontrollierte Umgebungen von Nöten. Anders als beim SLS-Druck von Kunststoff, benötigen lasergesinterte Metallteile Stützstrukturen. Die Nachbearbeitung ist arbeitsintensiv und bei manchen Teil ist nachträgliches Fräsen erforderlich, um die Endanforderungen zu erfüllen.
In den letzten Jahren hat der 3D-Metalldruckmarkt aktive Investitionen angezogen. 2016 übernahm GE zwei führende AM-Unternehmen, Concept Laser und Arcam. Mehrere Wagniskapitalunternehmen wie Desktop Metal, Markforged und Xjet entwickln neue 3D-Metalldruckverfahren, die für geringere Stückkosten sorgen und die Technologie für ein breiteres Anwendungsgebiet erschließen sollen.
Desktop Metal und Markforged wollen den Markt vom unteren Ende her aufrollen und haben kompakte, zugängliche Systeme entwickelt. Deren Technologie ist FDM ähnlich, hat aber Verbundswerkstoffe zum Endprodukt, bei denen Metallpulver in einer Plastikmatrix gebunden wird. Nach dem Druck werden die Teile gesäubert und in einem Schmelzofen gesintert, wodurch das Bindemittel entfernt und das Metallpulver zu festen Metallteilen verschmolzen wird. Mit Preisen ab 100 000 USD für ein vollständiges System ist diese Technologie sehr viel erschwinglicher als laserbasierte Metall-AM-Systeme.
Das zweite, teurere Fertigungssystem kombiniert erprobte Materialien aus dem Metall-Spritzgussdruck mit einer Technologie, die dem Binder Jetting ähnelt, um ein Ökosystem aufzubauen und die Kosten um ein beträchtliches Maß zu senken. Beim Metal Jetting von XJet werden Metallpartikel in Flüssigkeit in einem Schwebezustand gehalten und dann mit Hitze zu Teilen aus Festmetal und Keramik verfestigt.
Zwar werden diese Technologien den Metall-3D-Druck (noch) nicht massentauglich machen, doch wird ihre Verfügbarkeit zu einer stärkeren Verbreitung additiver Fertigung in verschiedenen Branchen mit geringen bis mittleren Fertigungsvolumina führen und die Prototypenfertigungs- und Produktentwicklungsprozesse für Metallteile modernisieren.

Das Studio System von Desktop Metal funktioniert nach einem ähnlichen Prinzip wie FDM, verwendet allerdings Verbundwerkstoffe aus Metallpulver, das in einer Plastikmatrix festgehalten wird. Nach dem Druck werden die Teile gesäubert und in einem Schmelzofen gesintert, wodurch das Bindemittel entfernt und das Metallpulver zu festen Metallteilen verschmolzen wird. Bild: Desktop Metal.
Automatisierung und rationalisierte Arbeitsabläufe
Überraschenderweise ist Arbeitskraft die kostenintensivste Komponente der meisten AM-Verfahren. Ein 3D-Drucker ist keine Wunderkiste, die auf einen Knopfdruck ein lupenreines Teil ausspuckt; Techniker müssen Teile aus den Druckern nehmen und bestimmte Nachbearbeitungsschritte anwenden. Dabei kann es sich um alles von leichtem Abbürsten über Waschen in Lösungsmittel, Hitzebehandlung, abrasives Polieren und das Auftragen einer Beschichtung handeln. Um in Fertigungshallen Fuß zu fassen, müssen AM-Systeme den erforderlichen Arbeitsaufwand senken und sich in die vorhandenen Fertigungsabläufe einpassen.
Verbesserte Arbeitsabläufe und Technologien halten das Versprechen sinkender Arbeitskosten. Manche FDM-Drucker mit zwei Düsen arbeiten mit löslichen Stützstrukturen, die einfach mit Lösungsmitteln weggewaschen werden können. Manche SLA-Systeme vereinfachen die Nachbearbeitung mit automatisierten Reinigungs- und Nachhärtestationen. Da SLS-Drucke aus Plastik keine Stützstrukturen erfordern sind die Arbeitsabläufe zur Nachbearbeitung hier oft weniger arbeitsintensiv als bei anderen Technologien, und mehr Teile passen in das Fertigungsvolumen, was die erforderliche Bearbeitung pro Teil senkt. Fertigungsunternehmen, die mit Metall-AM arbeiten, bieten immer häufiger modulare, halbautomatisierte Systeme, die die Arbeitsabläufe zur Nachbearbeitung wie zum Beispiel die Handhabung und Beseitigung des Pulvers, Hitzebehandlung und Teilentnahme vereinfachen.
Wie das Computing sich in den 1980er Jahren von Mainframes auf Desktop-PCs verlagerte, befinden sich auch 3D-Drucksysteme in einem Umbruch zu einer stärkeren Verteiltheit. Formlabs, Stratasys, 3D Systems und Mass Portal haben Zellen automatisierter modularer Kunststoffdrucker auf den Markt gebracht. Roboterarme und Gantry-Systeme entnehmen das Produkt aus dem Drucker, um den Arbeitsaufwand zu reduzieren. So können die Drucker ohne menschliches Eingreifen 24 Stunden am Tag laufen. Intelligente Zellmanagement-Software optimiert Druckerwarteschlangen, ermöglicht die Überwachung auf Distanz und kann mit CRM-, ERP- und MES-Systemen der Fabrik integriert werden. Eine Reihe von Sensoren erfassen Fehldrucke und schützen das bedienende Personal. Modulare Systeme verfügen zusätzlich über den Vorteil der Redundanz: Wenn eine Maschine kaputtgeht, können die anderen Drucker ihre Arbeitslast übernehmen und die Produktion unterbrechungsfrei fortführen.
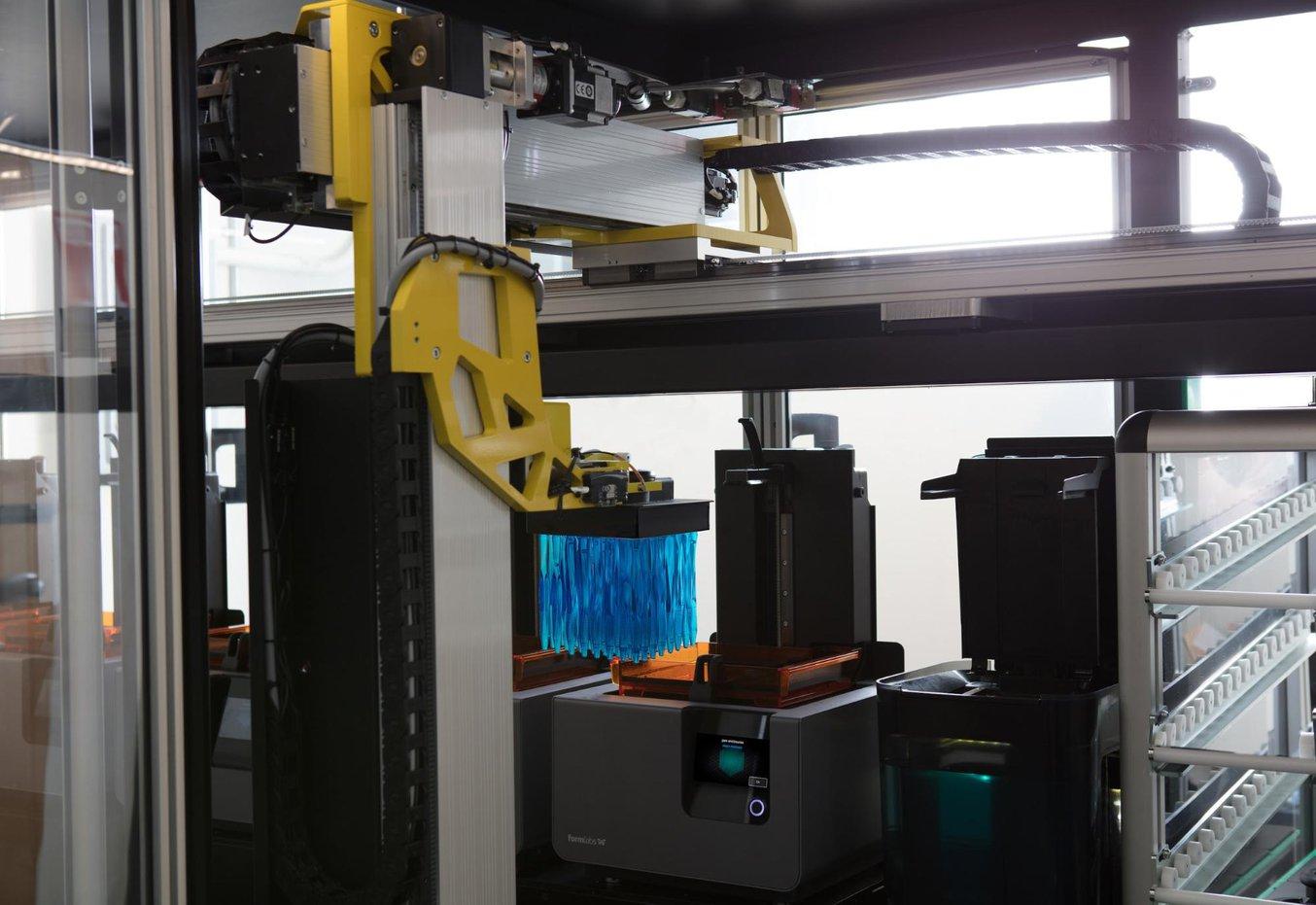
Form Cell, eine modulare Fertigungszelle von Formlabs, verwendet einen Roboterarm und ein Gantry-System, um fertige Teile zu entnehmen und sie in einer Waschstation zu säubern. Dann wird das Teil zur Nachbearbeitung auf einem Ständer abgelegt. Insgesamt wird so maßgeblich Arbeitskraft eingespart.
Diese automatisierten Zellen transformieren die Ökonomie des 3D-Drucks noch weiterhin, indem sie Cluster von Desktopanlagen in Fertigungsmaschinerie verwandeln, die einen hohen Durchsatz bei geringen Kosten bietet. Zudem erlauben sie Technikern und Designern, dieselbe 3D-Druckplattform zu verwenden, um sowohl Prototypen herzustellen als auch die Fertigung zu betreiben, was teure Design-für-Fertigung-Prozesse senkt und Produktionsentwicklungszyklen verkürzt.
Während Automatisierungssysteme stetig optimiert werden und auch unförmige Einzelteile bearbeiten können, rückt die Möglichkeit immer näher, weitere Aspekte des 3D-Drucks zu automatisieren. Roboter können Stützstrukturen entfernen, Beschichtungen auftragen und Klebemittel auftragen, um mehrere 3D-gedruckte und konventionell hergestellte Teile zu verbinden. Dies führt uns von der digitalen Fertigung hin zur „digitalen Montage“.
Fortschritt bei Materialien
Additive Fertigungssysteme sind die Schweizer Taschenmesser der Fertigungsanlagen. Sie sind mit einer breiten Spanne von Materialien kompatibel; und durch Hin- und Herwechseln zwischen verschiedenen Materialien kann eine einzige Maschine Teile für verschiedene Lösungen fertigen.
Eines der besten Beispiele dieser Vielseitigkeit sind kunstharzbasierte Polymer-3D-Druckverfahren wie die Stereolithographie (SLA). Ein- und derselbe Desktop-SLA-3D-Drucker kann in einem kleinen Zahnlabor biokompatible Schienen und Bohrschablonen herstellen, und in einer Automobilfabrik Vorrichtungen und hitzebeständige Formen.
Ähnlich erlauben andere fortgeschrittene 3D-Druckmaterialien die Digitalisierung vormals analoger Verfahren. Hitzebeständige Kunstharze können für den Kunststoffspritzguss bei geringem Druck und sogar zum Gießen von Weichmetallen wie Zinn verwendet werden können. Während die Formqualität die von Metallwerkzeugen nicht erreicht, sind 3D-gedruckte Formen hervorragend für kleine und mittelgroße Fertigungsserien geeignet, bei denen die Kosten der Werkzeuge andernfalls unter Umständen nicht wieder hereinzuholen sind.
SLA-, SLS- und FDM-Teile können zur Fertigung von Vorrichtungen für industrielle Fertigungsverfahren verwendet werden und damit kostenintensive Fräsprozesse überflüssig machen. PEEK, ULTEM und verstärkte technische Thermoplaste für FDM bieten verbesserte mechanische Eigenschaften und eine höhere Hitzebeständigkeit und können so sogar Metallteile ersetzen. Und neue Keramik-SLA-Teile bringen eine außergewöhnliche Hitzebeständigkeit mit sich, während sie gleichzeitig keinerlei chemische Interaktionen hervorrufen.
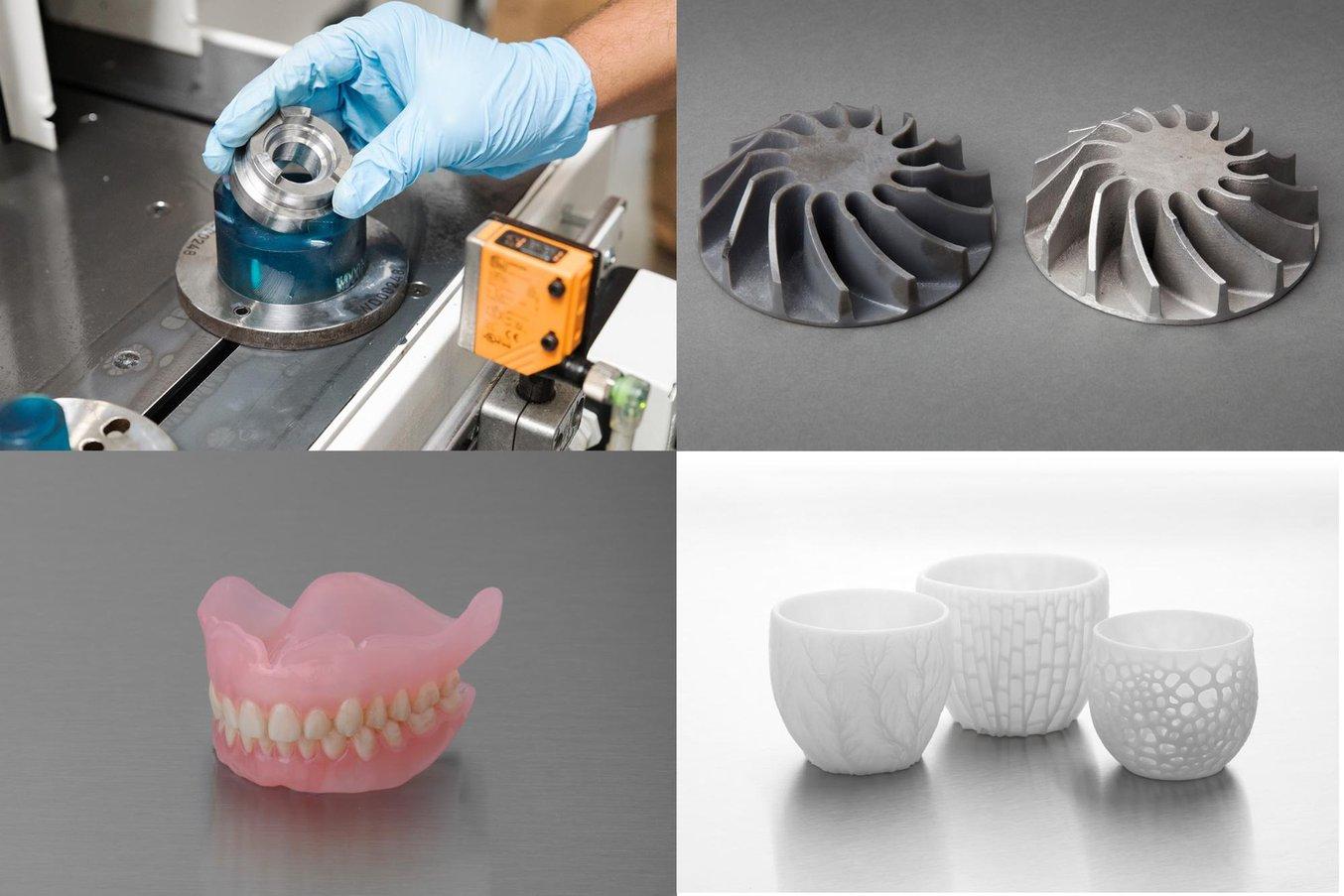
Vier Teile, die mit demselben SLA-3D-Drucker hergestellt wurden. Von oben links nach unten rechts: eine Vorrichtung in einer automatisierten Fertigungsstraße in einer Automobilfabrik; ein mithilfe eines 3D-gedruckten Modells gegossenes Metallteil; eine biokompatible Prothese; und Keramikgeschirr.
Mehr Ökonomie für die Fertigung
3D-Druck ist kein Allheilmittel für jegliche Fertigungsanforderungen; bislang war seine Nutzung nur für die am stärksten individuell angepassten Teile mit dem höchsten Wert und den geringsten Stückzahlen zu rechtfertigen. Für die Fertigung großer Serien sind konventionelle Methoden weiterhin kosteneffektiver. Nichtsdestotrotz wird der 3D-Druck ökonomischer und der Stückkostenschwellenwert bewegt sich: Die Technologie wird zunehmend praktikabel für Anwendungen mit geringerem Wert und höheren Stückzahlen. Angetrieben durch technologische Innovationen und bessere Materialeigenschaft wird die AM Anwendungsfälle über die Prototypenfertigung hinaus erschließen und mehr und mehr zur Herstellung fertiger Teile und zur Massenproduktion herangezogen werden.
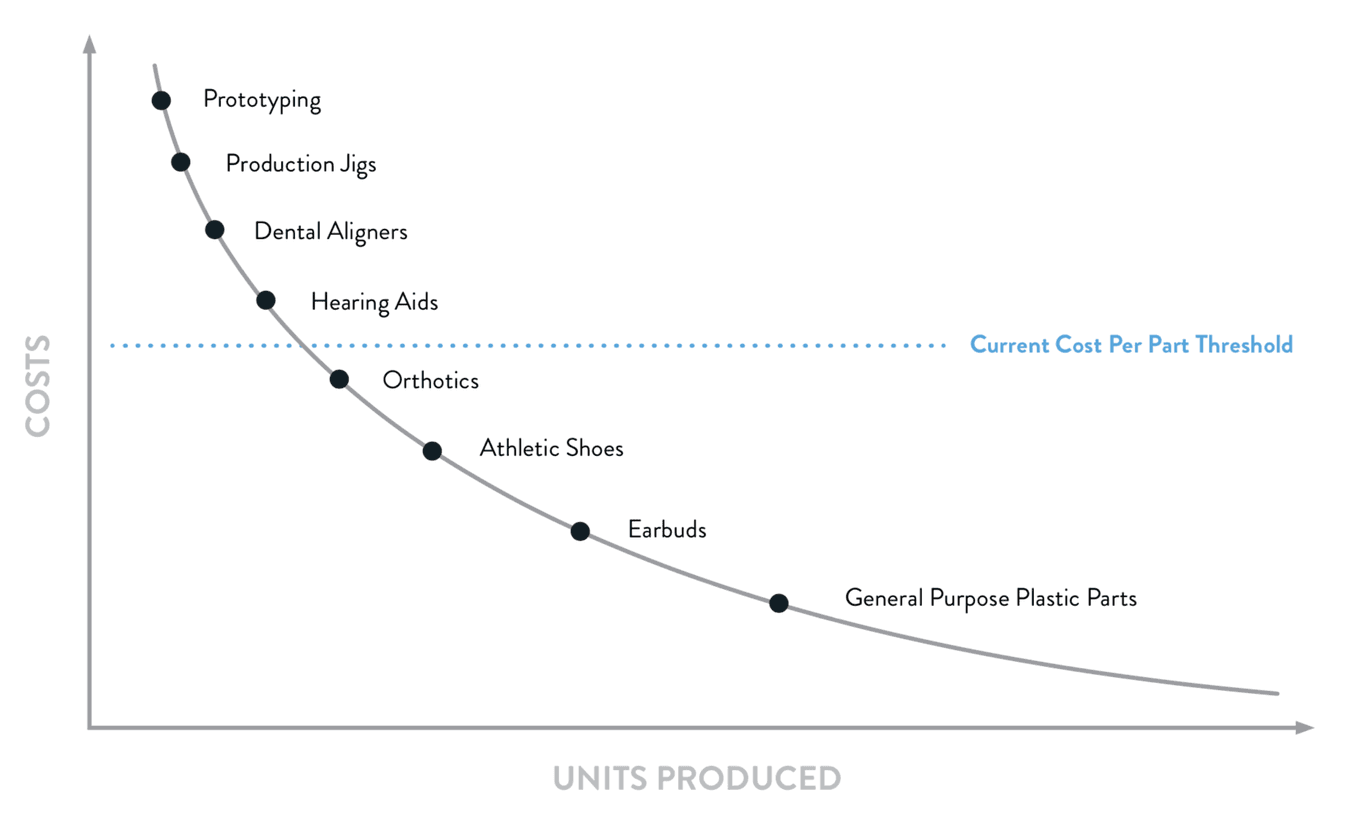
Nichtsdestotrotz wird der 3D-Druck ökonomischer und der Stückkostenschwellenwert bewegt sich: Die Technologie wird zunehmend praktikabel für Anwendungen mit geringerem Stückwert und höheren Stückzahlen.
In vielen Fällen dient der 3D-Druck als Zwischenschritt für konventionelle Fertigungsmethoden, was auch als Hybrid-Fertigung bezeichnet wird. In der Schmuckbranche ist der 3D-Druck zum Beispiel Teil des Feingussverfahrens. Schmuckhersteller beginnen mit dem digitalen Design eines Schmuckstücks und 3D-drucken es dann aus gussfähigem Kunstharz, das in einer sandartige Einbettmasse platziert und dann in einem Ofen rückstandslos weggebrannt wird. So bleibt wie bei normalen Modellen aus Juwelierwachs eine Gussform für Edelmetalle zurück.
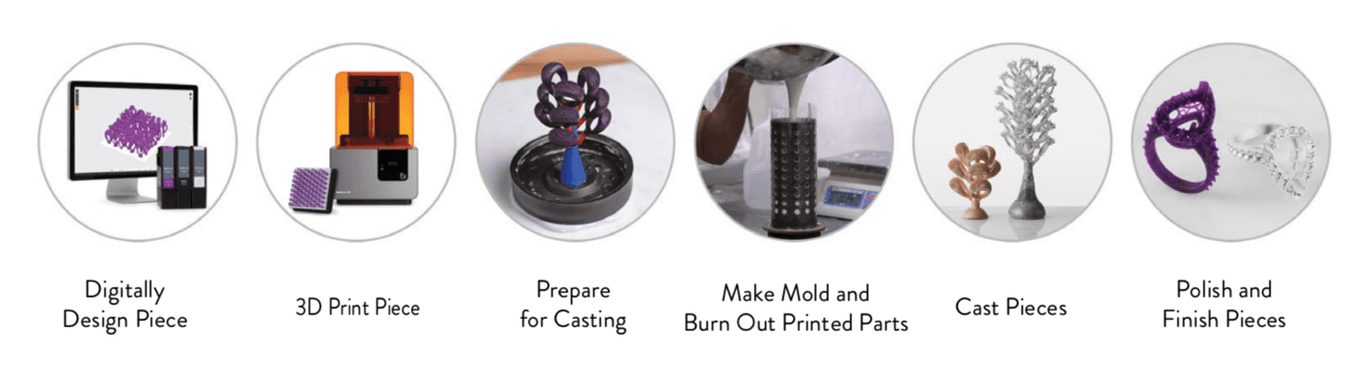
Per Hybrid-3D-Druck können zudem kostengünstige personalisierte In-Ear-Kopfhörer hergestellt werden. Zu Beginn des entsprechenden Verfahrens wird mithilfe eines 3D-Scanners ein schneller, nicht-invasiver digitaler Scan des Ohrkanals des Kunden angefertigt. Ein Techniker verarbeitet die digitale Datei zu einer 3D-druckbaren Form und sendet sie kabellos an einen SLA 3D-Drucker. Nach dem Druck werden die Teile gesäubert und der Techniker gießt biokompatibles Silikon in die Formen und entfernt das 3D-gedruckte Gehäuse. Zuletzt bearbeitet er das Endprodukt nach und beschichtet es. Der 3D-Druck wird so zu einem integralen Bestandteil dieses traditionell handwerklichen Verfahrens, obwohl das Endprodukt selbst nicht 3D-gedruckt wird.
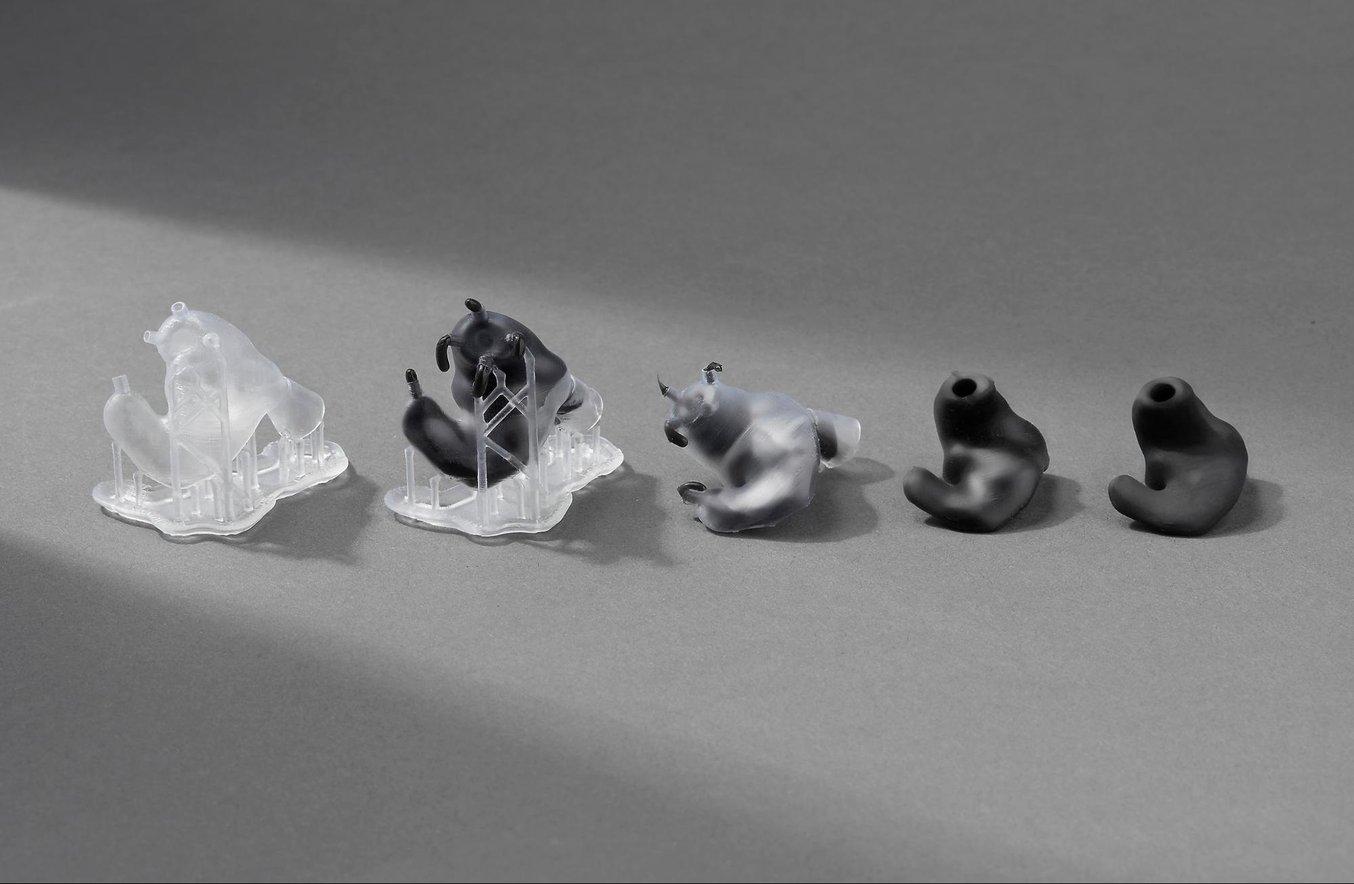
Personalisierte In-Ear-Kopfhörer werden durch das Gießen biokompatiblen Silikons in 3D-gedruckte Hohlformen hergestellt. Jede gedruckte Form kostet etwa 0,40 bis 0,60 USD für Kunstharz, und die Rohmaterialien für die gesamte Fertigung eines Kopfhörerpaars kosten etwa 3 bis 4 USD (inklusive Silikon und Lack).
Branchen wie die Zahnmedizin, medizinische Geräte und Hörakustik & Otoplastiken sehen im 3D-Druck eine Chance, fertige Teile zu fertigen, die für individuelle Patientenprofile ausgelegt sind. Während sich der 3D-Druck in Zahnarztpraxen und Dentallaboren als Standard durchsetzt, werden in der Zukunft vermehrt Schienen und Zahnersatz aus biokompatiblen Materialien hergestellt. Im Bereich Hörakustik & Otoplastiken werden die meisten personalisierten Hörhilfen bereits 3D-gedruckt. Auch der Markt für medizinische Geräte bietet ein unschätzbares Potential. Beispielsweise können haltbare, biokompatible SLS-Teile für personalisierte Orthesen und andere Geräte verwendet werden, die in direkten Kontakt mit der menschlichen Haut treten.
Mit sinkenden Kosten wird die additive Fertigung also auch verstärkt in traditionellen Verbraucherprodukten anzutreffen sein. Für die Verbraucherelektroniksegmente mit den höchsten Produktionsvolumina ist beispielsweise der Spritzguss bislang die einzige praktikable Möglichkeit, um Plastikteile herzustellen. Aber für Elektronikartikel mit mittleren Fertigungsvolumina fasst der 3D-Druck langsam aber sicher Fuß. Elektronikhersteller, die den Spritzguss durch additive Fertigung ersetzen, können zudem Produktdesign und Fertigung rationalisierten und ihre Flexibilität beibehalten. Da für den 3D-Druck keine Werkzeugausstattung nötig wird, ist er dem Spritzguss bei Stückzahlen bis über 10.000 ebenbürtig.
Schuhhersteller wie New Balance und Adidas haben Pläne angekündigt, im Verlauf der nächsten Jahre die Massenfertigung von personalisierten Zwischensohlen per 3D-Druck aus hartem Polyurethan (Rigid Polyurethane, RPU) aufzunehmen. Auch hier wird der 3D-Druck mit anderen Fertigungsmethoden kombiniert, um die wichtigsten, am stärksten individuell angepassten Produktteile herzustellen. Die übrigen Teile werden auch weiterhin mithilfe von konventionellen, kosengünstigen Fertigungsmethoden produziert.
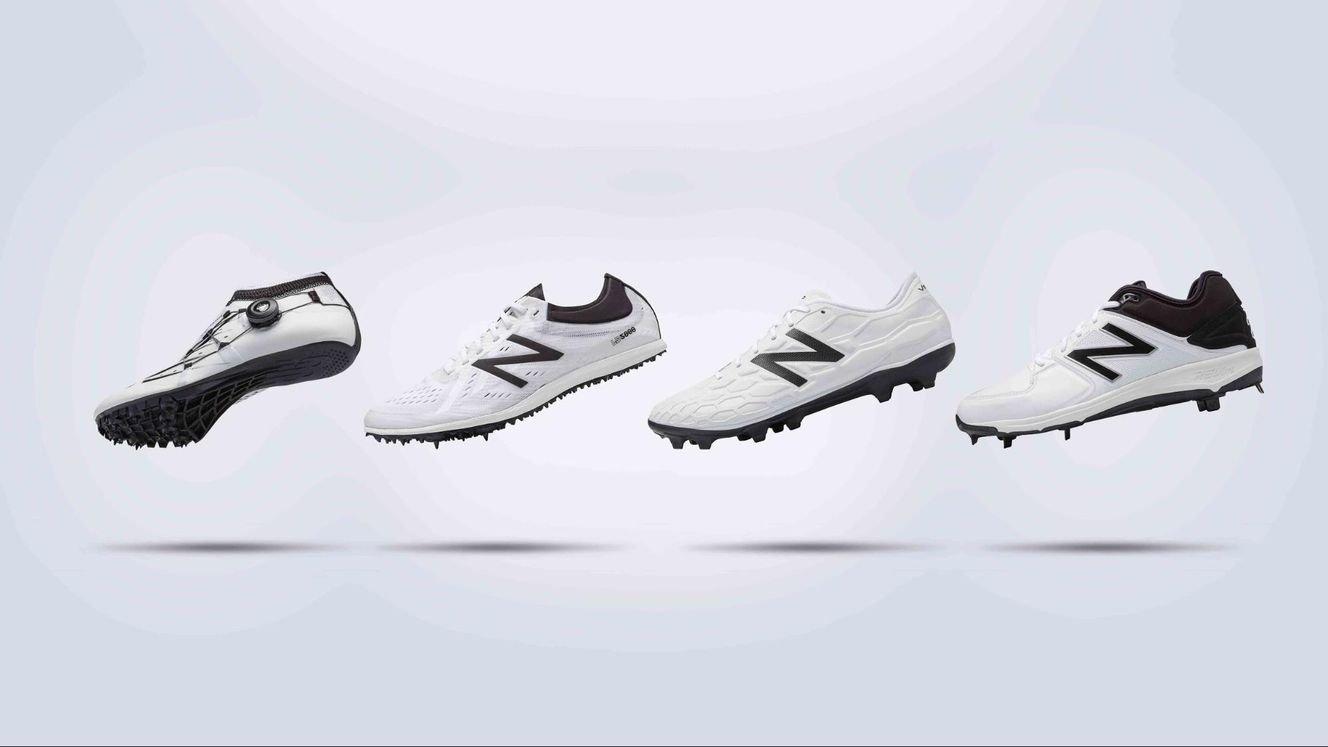
Schuhkonzepte von New Balance mit 3D-gedruckten Zwischensohlen.
Erfahren Sie, wie 3D-Druck und digitale Technologien Maschinenbau und Fertigung transformiert
Laden Sie en Digital Factory Report herunter und hören Sie sich den Podcast an, um Einblicke in die digitale Transformation in der Fertigung sowie zu Technologien wie der additiven Fertigung, KI, Robotikanwendungen und Automatisierung zu erhalten. Nehmen Sie an der nächsten Digital Factory am 7. Mai in Boston teil und wohnen Sie Vorträgen von Führungskräften in der digitalen Fertigung bei, wie zum Beispiel vom CEO von Align Technologies, dem CIO von FedEx, dem CTO von GE, dem CEO von Desktop Metal, dem Fertigungsleiter von Ford Motor und weiteren.
Hardware und Materialien für die additive Fertigung entwickeln sich rasant weiter und die Stückkosten befinden sich auch weiterhin im Senkflug. Damit öffnet sich diese Technologie zunehmend für eine größere Bandbreite an Anwendungen mit niedrigem bis mittlerem Fertigungsvolumen eignet. Sehen Sie sich an, wie führende Fertigungsunternehmen auf additive Fertigungsmethoden zurückgreifen, um Kosten einzusparen, Durchlaufzeiten zu senken, komplexe Probleme zu lösen und verschiedene Verfahren von der Prototypenfertigung bis hin zur Fertigung von Endprodukten zu optimieren.