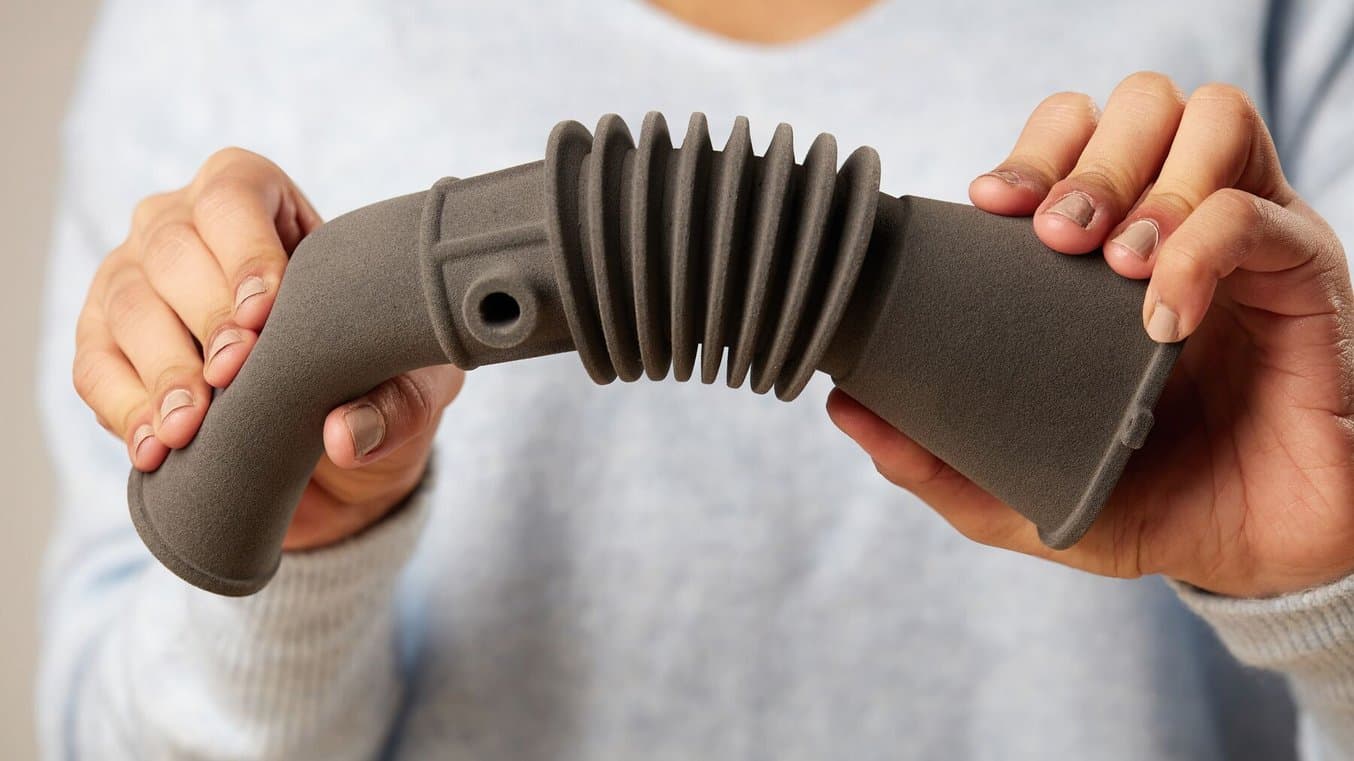
Was ist TPU?
TPU, oder thermoplastisches Polyurethan, ist ein thermoplastisches Elastomer (TPE), das in der Fertigung für die Automobilbranche, das Transportwesen, die Luft- und Raumfahrt, die Sportgerätebranche und in der Herstellung von Medizinprodukten weit verbreitet ist. TPU vereint die hohe Haltbarkeit von Kunststoffteilen mit der Elastizität von Gummi und ist damit das ideale Material für Anwendungen, die wiederholte Biegung oder Kompression von Teilen erfordern.
Aufgrund seiner Elastizität kommt TPU häufig als Schlagzähmodifikator in Produkten wie Helmen, Schutzverpackungen, vibrationsdämpfenden Produkten oder Dichtungen zum Einsatz. TPU verfügt zudem über eine exzellente Abrasionsbeständigkeit und wird daher in Anwendungen mit hoher Reibung eingesetzt (z. B. Innenkomponenten von Fahrzeugen) oder für elektrische Kabel und Isolierungen verwendet. Da TPU in Industriezweigen Anwendung findet, in denen häufig mit Öl gearbeitet wird, stellt auch seine Beständigkeit gegenüber Ölflecken einen Vorteil dar.
Wie werden TPU-Teile hergestellt?
TPU-Produkte sind in unserem täglichen Leben allgegenwärtig, weshalb sich Massenproduktionsmethoden für ihre Herstellung anbieten – für gewöhnlich umfasst dies konventionelle Spritzgussverfahren. Viele Produkte, die wir für Gummi halten, bestehen eigentlich aus TPU.
Spritzguss ist eine kosteneffiziente Lösung zur Produktion von Teilen in hohen Stückzahlen. In Bezug auf die geometrische Flexibilität und Individualisierung ist das Verfahren jedoch eingeschränkt. Spritzgegossene Teile sind standardisiert, damit sie in Stückzahlen von Hunderttausenden bis hin zu Millionen Teilen produziert werden können – daher besteht in Branchen wie der Herstellung von Medizinprodukten oder Sportausrüstung ein Bedarf an Alternativen, die sich besser für die Kleinserienproduktion und kundenindividuelle Fertigung eignen.
Außerdem hindert die Massenproduktion kleine Unternehmen und Startups daran, ihre Produkte schnell auf den Markt zu bringen, die sie auf die externe Produktion in großangelegten, industrielle Spritzgussmaschinen angewiesen sind.
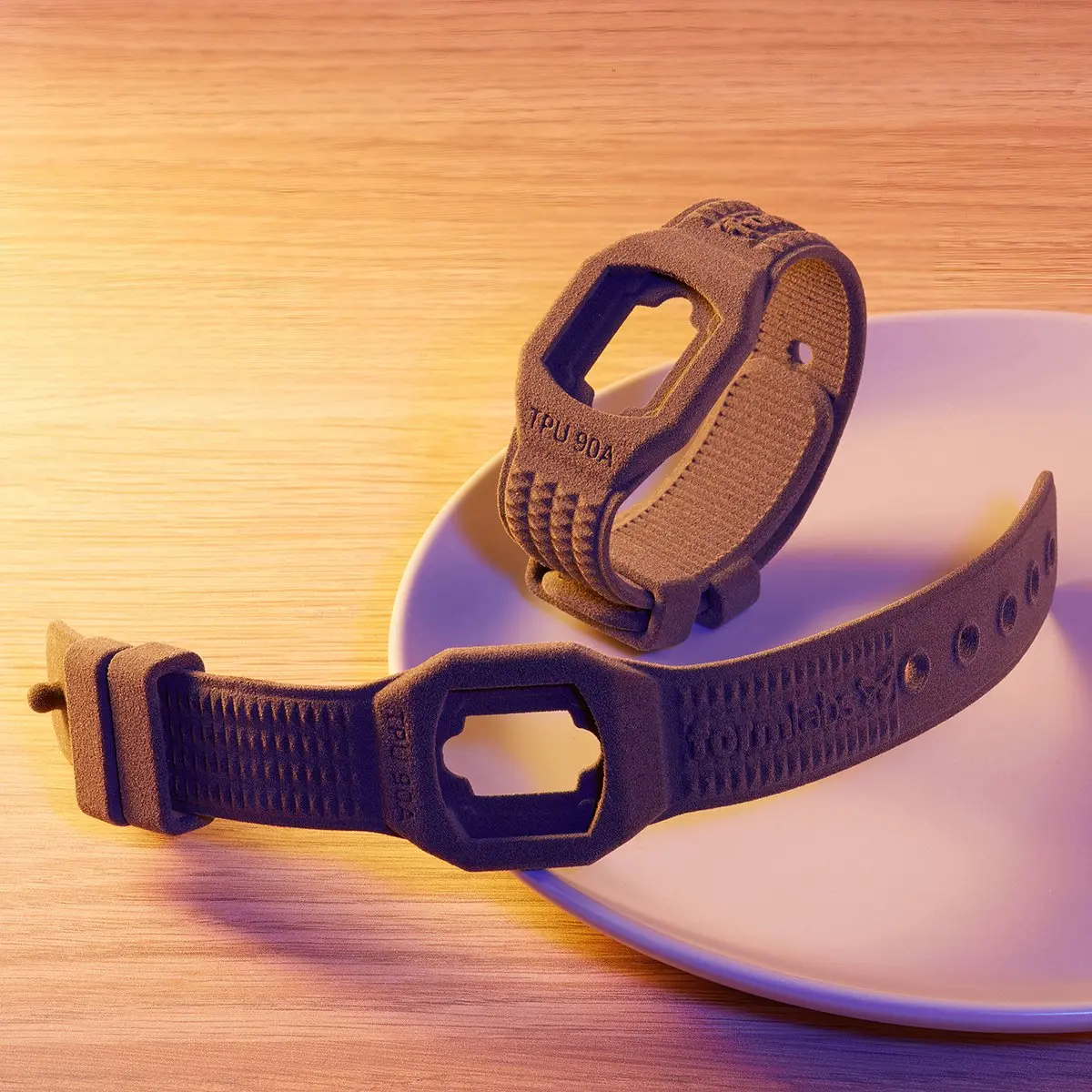
Das neue TPU 90A Powder für flexible, belastbare und hautverträgliche SLS-Teile
Erfahren Sie in unserem Webinar, wie TPU 90A Powder Ihnen zur betriebsinternen Herstellung weicher Gummiteile mit den 3D-Druckern der Fuse-Serie verhilft.
Warum TPU 3D-drucken?
Der 3D-Druck von TPU und anderen TPE-Materialien bietet Möglichkeit jenseits traditioneller Fertigungsprozesse. Er ermöglicht Teile mit höherer geometrischer Komplexität, personalisierte oder maßgefertigte Designs, schnellere Iterationen und eine kosteneffizientere Kleinserienfertigung.
Es gibt zahlreiche Optionen für den 3D-Druck von TPU, unter anderem die Drucktechnologien Schmelzschichtung (Fused Deposition Modeling, FDM) und selektives Lasersintern (SLS). Mit der Weiterentwicklung der Technologie und der Materialien für den 3D-Druck ist auch die Zahl von Herstellern, die das Verfahren in ihre Prozesse integrieren, exponentiell angestiegen.
Der 3D-Druck mit TPU ermöglicht einen kürzeren Iterationszyklus beim Rapid Prototyping sowie Individualisierungsoptionen bei der Produktion für die Endverwendung. In Branchen, die eine Phase der Produktentwicklung in der Regel auslagern (typischerweise die Phase der Massenfertigung), bietet der 3D-Druck einen optimierten, vertikal integrierten Workflow von Anfang bis Ende.
Durch 3D-gedrucktes TPU können Hersteller außerdem die Nachfrage nach individuell angepassten, personalisierten Produkten bedienen. Laut einer Studie von Deloitte äußerten in einigen Kategorien mehr als 50 % der Verbraucher ein Interesse an individualisierten Produkten oder Dienstleistungen. Dabei war die Mehrheit auch bereit, für solche Angebote mehr zu bezahlen. Für Anwendungen, die häufig auf TPU oder Gummi zurückgreifen, wie etwa Schutzausrüstung wie Helme oder Orthesen und Einlagen, stellen 3D-gedruckte Teile aus TPU die perfekte Lösung dar, um beispielsweise Helmpolsterungen, Orthesen, Sportausrüstung, Schutzbrillen, Kopfhörer oder ergonomische Griffe von Elektronikprodukten in kundenindividueller Massenproduktion (Mass Customization) herzustellen.
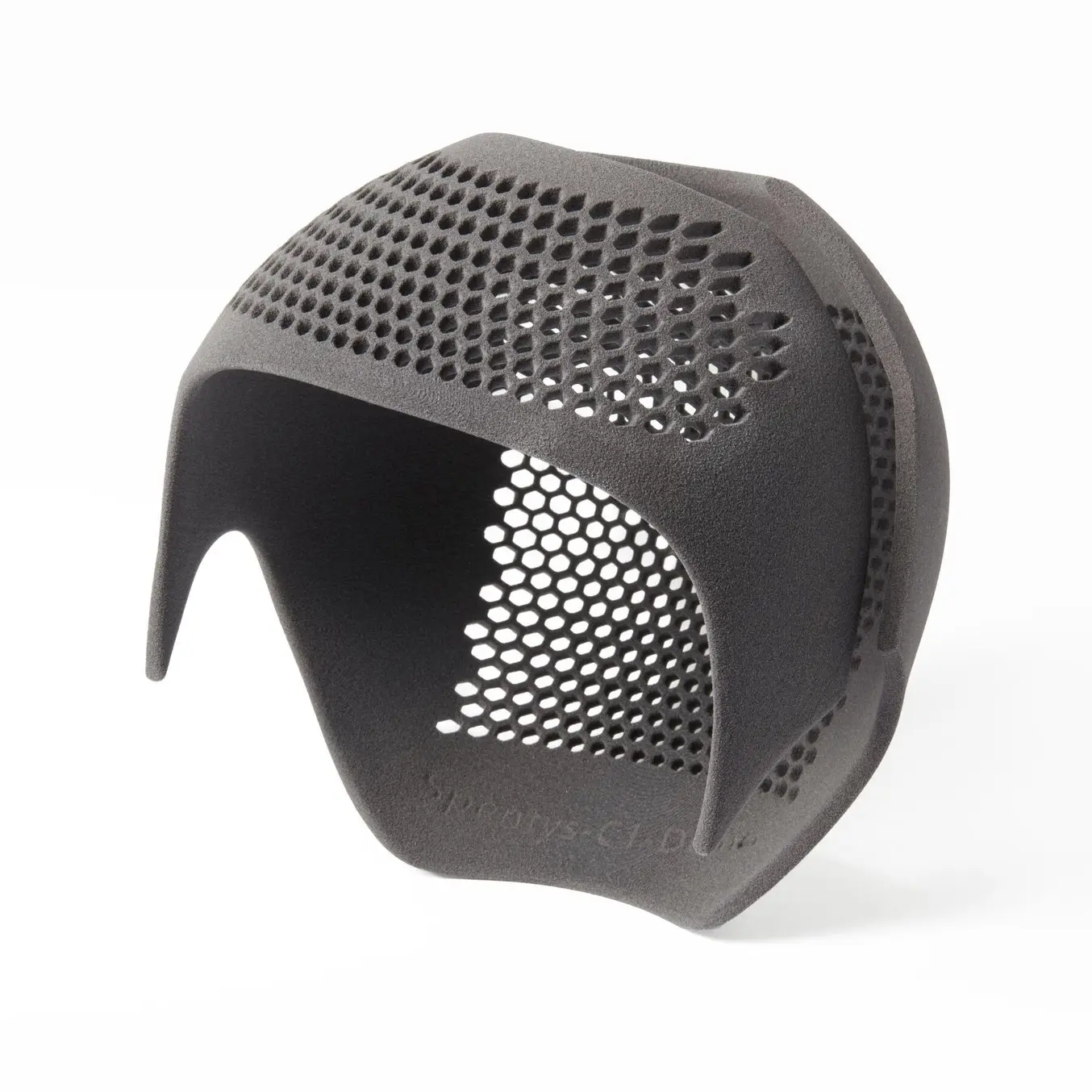
TPU 90A Powder von Formlabs ermöglicht für Anwendungen wie diese schützende Kopfbedeckung die Individualisierung von Produkten anhand von anthropometrischen Daten.
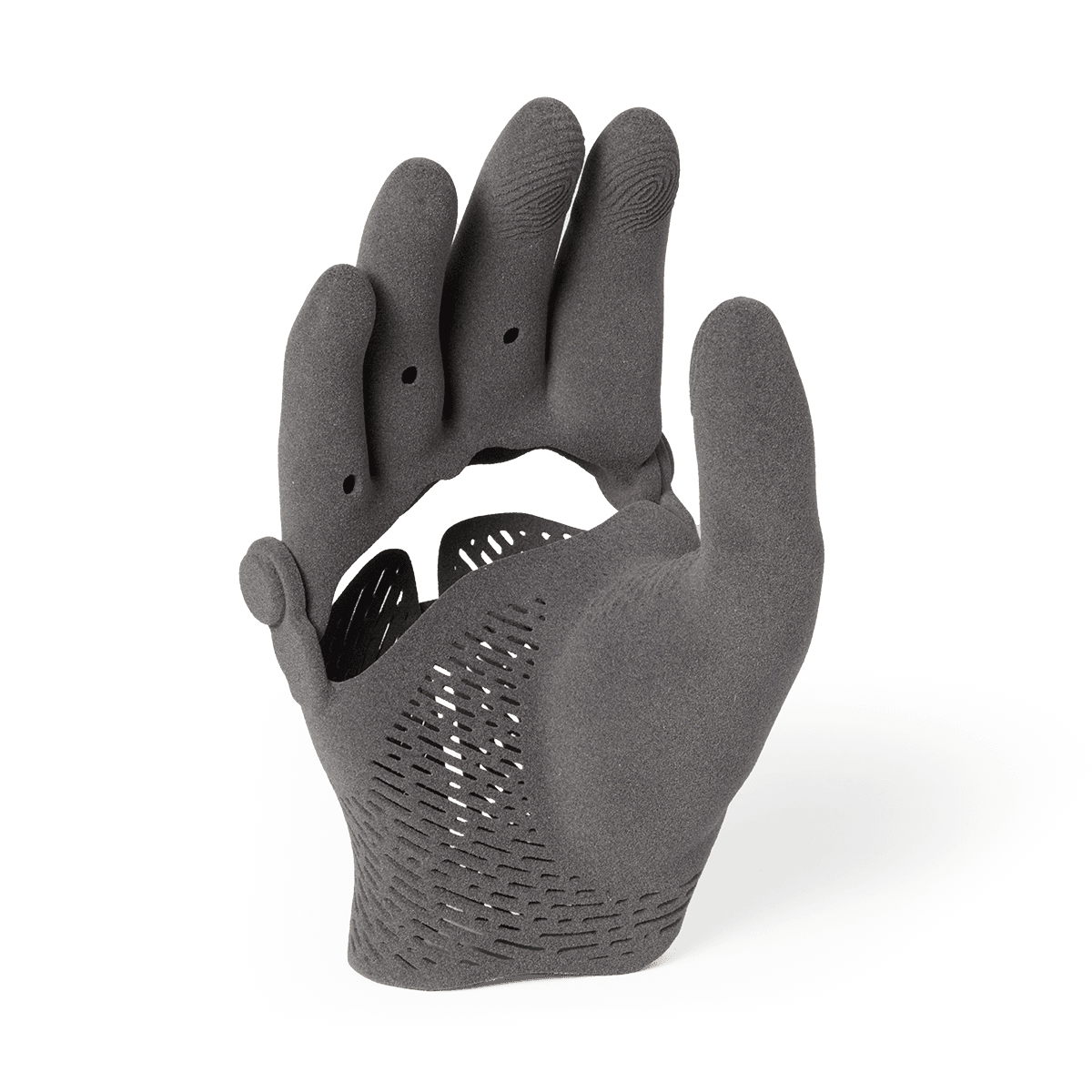
Diese prothetische Handschiene wurde aus TPU 90A Powder 3D-gedruckt und ist flexibel, fest und robust.
Wie man TPU 3D-druckt
TPU lässt sich sowohl auf FDM- als auch SLS-3D-Druckern verarbeiten. Jede dieser Technologien geht mit spezifischen Vorteilen einher. Vor der Entscheidung für eine Technologie sollte bestimmt werden, welche Eigenschaften sich für den eigenen Arbeitsprozess und die Geschäftsanforderungen am meisten anbieten.
FDM-3D-Druck mit TPU | SLS-3D-Druck mit TPU | |
---|---|---|
Materialfestigkeit | ★★☆☆☆ | ★★★★★ |
Auflösung | ★★☆☆☆ | ★★★★☆ |
Genauigkeit | ★★★★☆ | ★★★★★ |
Oberflächenbeschaffenheit | ★★☆☆☆ | ★★★★☆ |
Durchsatz | ★★☆☆☆ | ★★★★★ |
Komplexe Designs | ★★☆☆☆ | ★★★★★ |
Benutzerfreundlichkeit | ★★★★★ | ★★★★☆ |
Vorteile | Kostengünstige Geräte und Materialien für Verbraucher Schneller und einfacher Prozess für einfache, kleine Teile | Funktionale, feste, isotrope Teile Durchsatz auf Produktionsniveau Selbststützende Designs Höchste Gestaltungsfreiheit |
Nachteile | Teile sind anisotrop, nicht wasserdicht und ohne funktionale Festigkeit Eingeschränkte Gestaltungsfreiheit | Leicht raue Oberfläche |
Anwendungen | Kostengünstiges Rapid Prototyping Einfache Konzeptnachweismodelle | Funktionsfähige Prototypen Kleinserienfertigung von Endverbrauchsteilen: Automobildichtungen, Krümmer, Konsumgüter, Schuhe, Prothesen und Orthesen |
3D-Druck von TPU mittels FDM
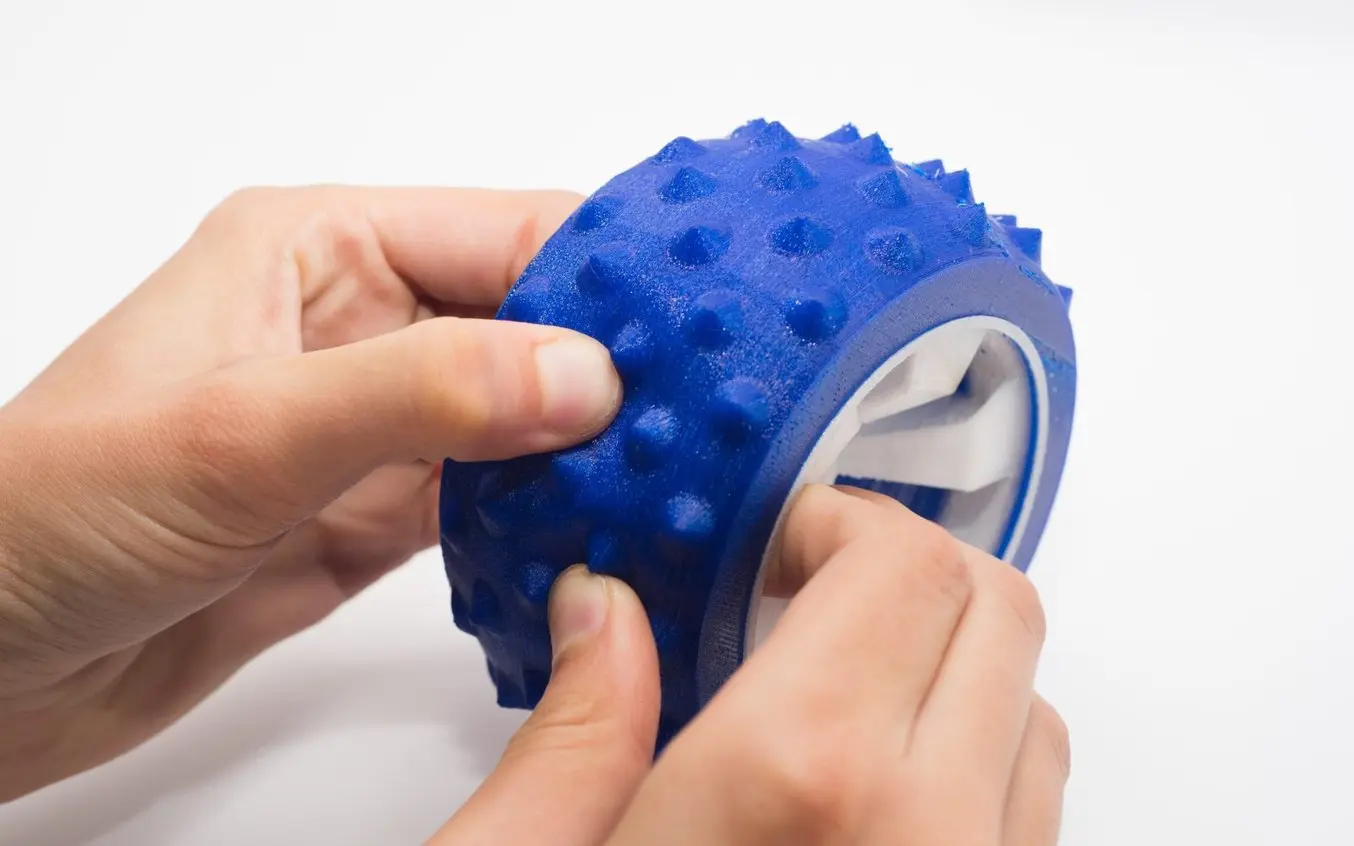
Der TPU-3D-Druck mit dem FDM-Verfahren eignet sich gut als Einstiegsoption, doch das Material stellt für diese Drucktechnologie eine Herausforderung dar, welche zudem mit Designeinschränkungen einhergeht. (Bildquelle: Hubs)
Für Unternehmen, die gerade erst mit dem 3D-Druck von TPU beginnen möchten, bieten sich preiswerte FDM-Drucker als Einstiegslösung an. TPU-Filament für den FDM-Druck ist kostengünstig erhältlich und kann eine gute Option für Konzeptnachweise und visuelle Prototypen sein, besonders wenn letztendlich über traditionelle Spritzgussverfahren massenproduziert werden soll.
Allerdings kann die Fertigung von TPU mit einem FDM-3D-Drucker eine Herausforderung sein, denn das weiche, dehnbare Filament kann die Extrusionsdüse leicht verstopfen und dadurch technische Probleme und Fehldrucke verursachen. Der 3D-Druck von TPU auf FDM-Geräten lässt außerdem nur eingeschränkte Gestaltungsoptionen zu, ergibt weniger maßgenaue Teile und erzeugt sichtbare Schichtlinien.
Mittels FDM hergestellte TPU-Teile sind anisotrop, was bedeutet, dass sie nicht in allen Achsen und Flächen dieselbe Festigkeit aufweisen – mit anderen Worten haben Krafteinwirkungen auf den verschiedenen Achsen eines FDM-3D-gedruckten Teils einen unterschiedlichen Effekt. Da TPU-Teile häufig gedehnt, gestaucht und gedreht werden müssen, stellt Anisotropie für jegliche Funktionsteile eine Herausforderung dar, auch bereits in der Phase der Prototypenentwicklung.
TPU-Filamente für FDM-Drucker
Viele FDM-Drucker und Materialhersteller bieten TPU-Filamente mit unterschiedlichen Materialeigenschaften an. TPU-Filamente für den FDM-3D-Druck sind zumeist etwas härtere, elastische Materialien mit einer Shore-Härte von ungefähr 95A, was durch Änderung der Druckparameter oder des Designs jedoch angepasst werden kann.
3D-Druck von TPU mittels SLS
Das SLS-3D-Druckverfahren eignet sich ideal für höhere Durchsätze und funktionalere Anwendungen, beispielsweise funktionale Prototypen für Tests oder die Kleinserienfertigung von individualisierten Endprodukten wie Orthesen, Helmpolstern und Wearables. Der SLS-3D-Druck nutzt die erstklassige Festigkeit und Flexibilität von TPU aus, um Produkte schneller auf den Markt zu bringen oder die Patientenversorgung zu optimieren. Die hohe Reißfestigkeit sorgt für starke, langlebige, elastomerische Teile und dank der Erschwinglichkeit von Benchtop-SLS-Systemen wie der Fuse-Serie lassen sich niedrige Stückkosten erzielen. Zusätzlich tragen die niedrigen Neuzuführungsraten zur Erschwinglichkeit und Skalierbarkeit des Systems bei, da sie eine effizientere Pulvernutzung bedeuten und damit die Materialkosten verringern.
TPU-Teile aus dem SLS-3D-Drucker sind perfekt für Anwendungen geeignet, in denen komplexe Geometrien erforderlich oder zwecks Leistungssteigerung wünschenswert sind. Aufgrund des selbststützenden Druckvorgangs beim SLS werden keine Stützstrukturen benötigt, sodass sich auch komplizierte Geometrien wie interne Kanäle, Gitterstrukturen oder Faltenstrukturen wie in Krümmern umsetzen lassen. Bei Produkten wie schützenden Kopfbedeckungen oder Einlagen und Orthesen für Schuhe sorgen gummiartige Gitterstrukturen für eine hohe Druckbelastbarkeit, die die Effektivität des Produkts steigert.
TPU-Materialien für SLS-Drucker
Es gibt zahlreiche Systeme für selektives Lasersintern (SLS), die Pulvermaterialien aus TPU anbieten. Bei vielen dieser Systeme handelt es sich um große industrielle Maschinen, die eine komplizierte Infrastruktur erfordern, wie etwa Belüftungssysteme, eine große Stellfläche, mehrere Stromkreise oder sonstige Anforderungen an die Stromversorgung. Mit der Einführung leichter zugänglicher SLS-Systeme wie der Fuse-Serie von Formlabs ist der 3D-Druck von TPU mit pulverbasierten Druckverfahren erschwinglicher und unkomplizierter geworden.
Formlabs' Material TPU 90A Powder ist hautverträglich. Es eignet sich daher für den Einsatz in der Herstellung von Wearables und Medizinprodukten, wo Sicherheitsbestimmungen die Verwendung vieler 3D-gedruckter Komponenten einschränken. Mit TPU 90A Powder können sich Entwicklungs- und Designteams die Gestaltungsfreiheit des 3D-Drucks, die hohe Reißfestigkeit und Dehnbarkeit von Gummi und die Hautverträglichkeit vieler traditionell spritzgegossener Thermoplaste zunutze machen, und zwar in einem einzigen Arbeitsprozess.
Der 3D-Druck mit Formlabs' TPU 90A Powder und den SLS-Druckern der Fuse-Serie ist unkompliziert und lässt sich leicht in bestehende SLS-Workflows integrieren. Das Material eignet sich aber auch für den Einstieg in SLS. Es kann in Umgebungsluft gedruckt werden und erfordert im Gegensatz zu einigen anderen SLS-Materialien keine Inertgaszufuhr.
Des Weiteren nutzen TPU-Drucke auf Druckern der Fuse-Serie keine Surface Armor (die halbgesinterte Hülle um Druckteile aus Pulvern mit höherer Steifigkeit), was den Prozess der Pulverentfernung mit dem Nachbearbeitungsgerät Fuse Sift vereinfacht. Trotz des Fehlens von Surface Armor bei Teilen aus TPU 90A Powder wird das Sandstrahlen dennoch empfohlen, um überschüssiges Pulver vollständig von den Teilen zu entfernen und ein sauberes, leichter zu bearbeitendes Material zu erhalten. Es ist möglich, mit einem bestehenden Fuse-Drucker auf TPU 90A Powder umzusteigen. Formlabs empfiehlt jedoch die Nutzung eines eigens dafür vorbehaltenen Druckers sowie eines eigenen Fuse Sift und einer separaten Konstruktionskammer.
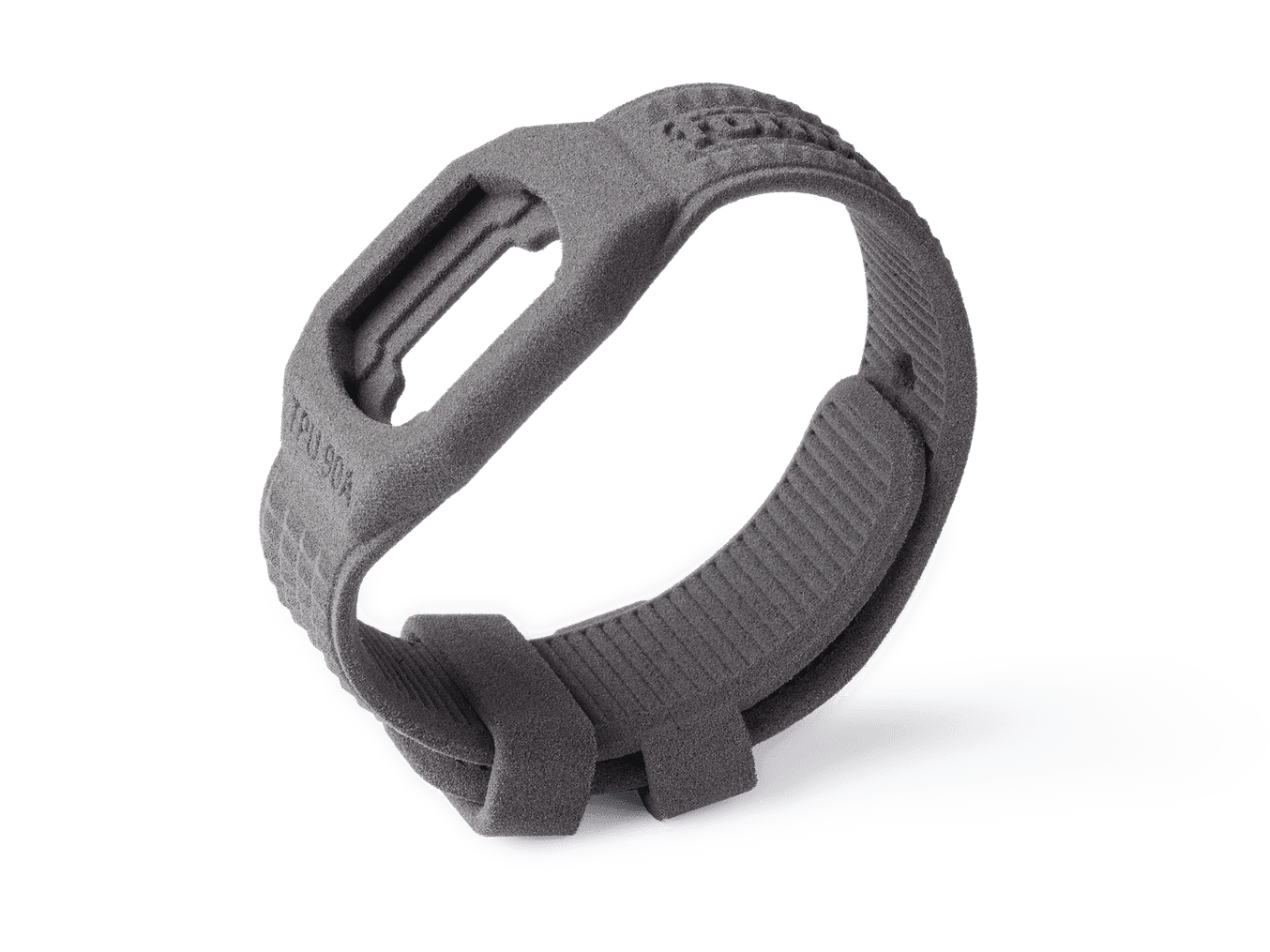
TPU 90A Powder: Formlabs' flexibles SLS-Pulver
Fordern Sie einen kostenlosen Probedruck eines Uhrenarmbands aus TPU 90A Powder an, unserem ersten flexiblen SLS-Material.
Anwendungsbereiche des 3D-Drucks mit TPU
Für die konventionelle Herstellung von TPU-Teilen gibt es bewährte Verfahren, und für massenproduzierte Gummiprodukte eignen sich diese Prozesse nach wie vor ideal. In vielen Szenarien liefert der 3D-Druck von TPU-Materialien jedoch eine wunderbare Alternative. So zum Beispiel in Fällen, in denen es auf Geschwindigkeit und Benutzerfreundlichkeit ankommt, beim Rapid Prototyping, der Herstellung von Fertigungshilfen auf Abruf und der Individualisierung von Produkten. Sei es der Beginn des Designprozesses, wo Prototypen kurzfristig benötigt werden, die Erstellung endgültiger Designs von Endverbrauchsteilen oder sogar die kundenindividuelle Massenproduktion von Konsumgütern: Der 3D-Druck von TPU-Teilen macht Abläufe schneller und effizienter, ohne Kompromisse bei den mechanischen Eigenschaften oder der Maßgenauigkeit einzugehen.
Rapid Prototyping
Durch den 3D-Druck mit TPU verlagern Unternehmen die Prototypenfertigung in den eigenen Betrieb, verkürzen ihre Durchlaufzeiten und reduzieren Kosten, die bis dahin für Fertigungsdienstleister anfielen.
Um beispielsweise einen Prototyp eines Sporthelms herzustellen, müssen sowohl für die harte Schale als auch für die weiche Polsterung Fertigungskapazitäten vorhanden sein. Innovative Unternehmen entwickeln für solche Polsterungen neuartige Gitterstrukturen und Stoßdämpfungstechnologien, wofür TPU das perfekte Material darstellt.
Das Ausprobieren neuer Designs und Geometrien ist mit traditionellen Methoden des Werkzeugbaus unerschwinglich teuer, die Auslagerung an Dienstleister wiederum kann Wochen beanspruchen. Wenn derselbe Arbeitsprozess und dieselbe Technologie sowohl für die harte äußere Schale als auch für die weiche Polsterung im Inneren genutzt werden können, laufen die Iterationen in einem viel schnelleren Takt ab. Da die Helme ausgiebigen physischen Tests unterzogen werden, sind für einen einzigen Testdurchlauf zehn Polster erforderlich. Das sind zu hohe Stückzahlen, um die Oberfläche der Polsterung in akribischer Handarbeit herzustellen, gleichzeitig aber zu wenig Teile für eine kosteneffiziente TPU-Umformung mit konventionellen Methoden. Die Lösung ist der betriebsinterne 3D-Druck.
Mit den SLS-3D-Druckern der Fuse-Serie und TPU 90A Powder lassen sich mit Leichtigkeit mehrere gummiartige Gitterstrukturen drucken, die zum Testen verschiedener Designs auch leichte Variationen aufweisen. Durch Anpassungen am Design des Teils, etwa der Wandstärke, können Teile mit unterschiedlicher Härte für verschiedene Anwendungen oder als Iterationen für Produkttests gefertigt werden.
Der Arbeitsablauf mit der Fuse-Serie lässt den Einsatz verschiedener Materialien zu, die eine große Bandbreite mechanischer Eigenschaften abdecken. So werden Produktdesign und Fertigung komplett betriebsintern erledigt und die Entwicklung zahlreicher verschiedener Komponenten mit nur einer Technologie umgesetzt. TPU 90A Powder eröffnet den direkten 3D-Druck von Prototypen für völlig neue Produkttypen auf der bewährten Plattform der Fuse-Serie.
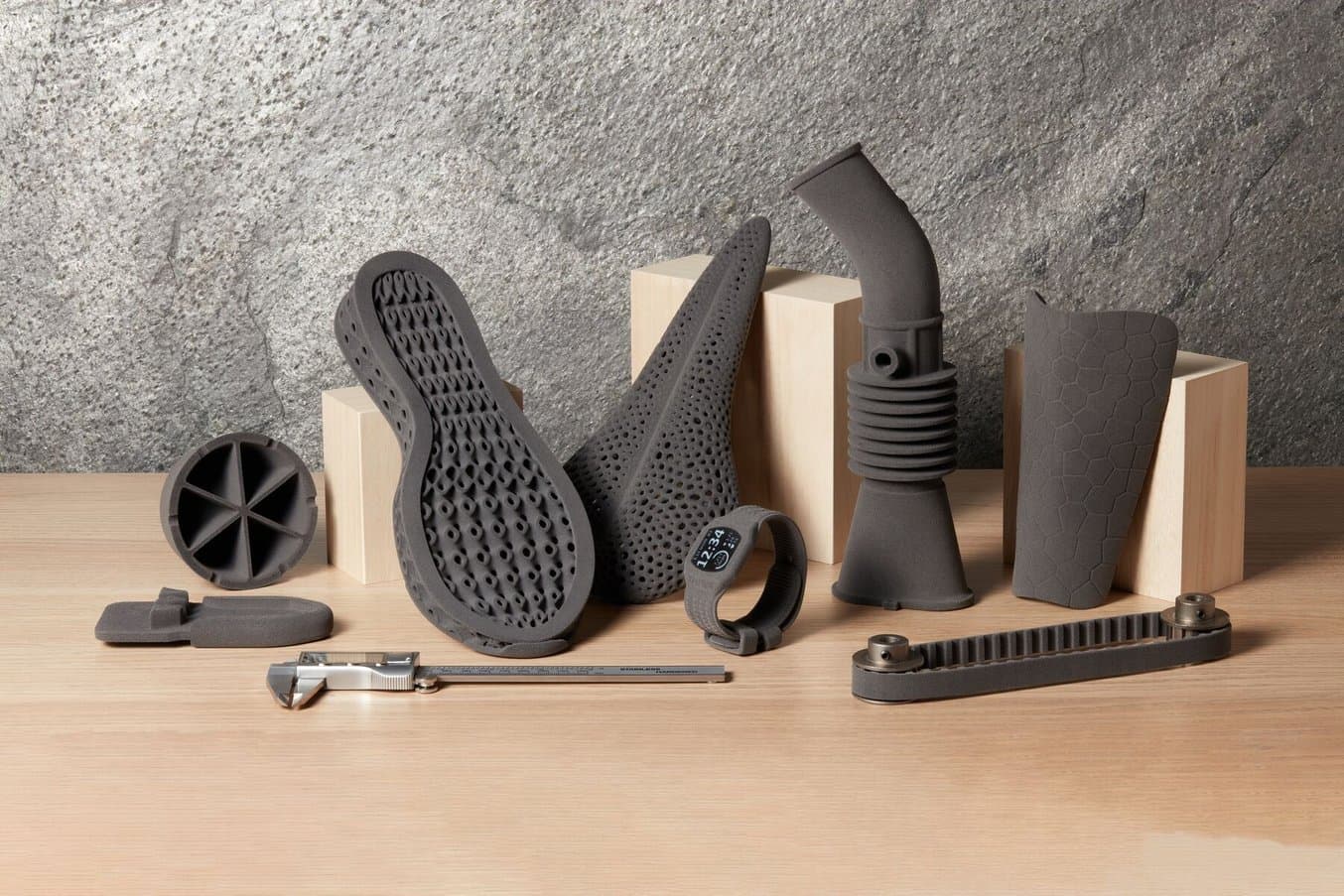
TPU 90A Powder eignet sich ideal für funktionsfähige Prototypen von flexiblen Teilen, wie etwa hautverträgliche Wearables, Sportausrüstung oder Schuhsohlen.
Fertigungshilfen
Wer nicht mit der Fertigung vertraut ist, für den sind die verschiedenen Arten von Fertigungshilfen vermutlich schwer zu überblicken. Im Endeffekt haben Halterungen, Klemmen, Gehäuse oder eine der vielen anderen Vorrichtungen zum Zusammenhalt von Maschinen jedoch alle die gleiche Wichtigkeit – wenn man sie braucht, dann braucht man sie dringend. TPU liefert die Antwort auf ein Problem, dem zahlreiche Hersteller gegenüberstehen: ihre millionenschwere Fertigungstechnik vor zu viel Verschleiß zu bewahren.
Fertigungshilfsmittel aus weichen Materialien können die Lebensdauer schwerer Maschinen verlängern, indem sie Stöße abdämpfen oder Greifer in der perfekten Form liefern. Treten an Dichtungen nach Jahren der kontinuierlichen Nutzung Risse auf, kann sofort ein Ersatz gedruckt werden, sodass die Fertigungsstraße innerhalb von Stunden wieder in Betrieb ist, statt dass tage- oder wochenlang auf ein Ersatzteil gewartet werden muss.
Zusätzliche Materialoptionen stellen für Hersteller eine Versicherung dar – sie bieten ihnen Schutz vor den Folgen unvorhergesehener Defekte von Bauteilen oder Geräten. Umso mehr verschiedene mechanische Eigenschaften betriebsintern erreichbar sind, desto besser sichert sich ein Unternehmen gegen Verzögerungen in der Lieferkette und hohe Reparaturkosten des Erstausrüsters ab. Mit 3D-gedruckten Gummiteilen wird eine komplett neue Klasse von Bauteilen erschlossen, die repariert oder auf Abruf ersetzt werden können. Indem der Stillstand einer Fertigungsstraße oder eines Produktionsprozesses verhindert wird, sparen Unternehmen pro Tag Beträge im Tausenderbereich.
TPU kann für Schwingungsdämpfer in der Automobilbranche oder Luft- und Raumfahrt eingesetzt werden, oder auch für Haltevorrichtungen in industriellen Prozessen wie dem Thermoformen von Teilen mit einzigartigen Geometrien. In Automobilfabriken bedienen großangelegte Robotiksysteme Wandlaufkräne, die biegsam und schwenkbar sein müssen. Mithilfe maßangefertigter Polsterung und weichen Gehäusen kann die Reibung an diesen Systemen vermindert und somit ihre Lebensdauer verlängert werden.
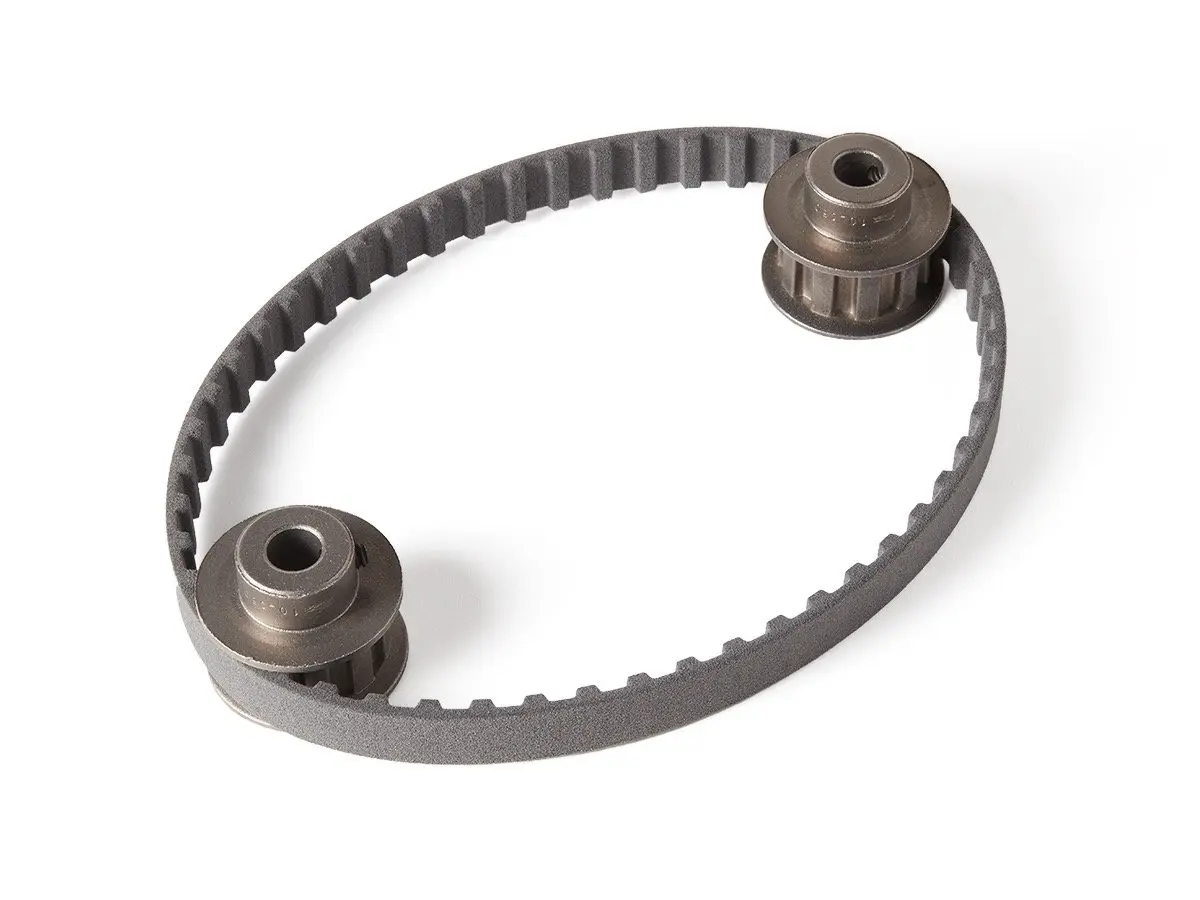
Steht ein TPU-Material zur Verfügung, können flexible Ersatzteile und Fertigungshilfen innerhalb eines Tages entworfen und gedruckt werden, sodass die Produktion niemals zum Stillstand kommen muss.
Tragbare Produkte in kleinen Mengen oder Sonderausführungen
In den Branchen Sport, Mode und tragbare Technologien (Wearables) sind Personalisierungsoptionen unabdinglich, um den Marktanteil einer Marke zu erhöhen. Aufgrund der mit dem Werkzeugbau verbundenen Kosten war die Produktion von Sonderanfertigungen oder Kleinserien nahezu unvorstellbar, bevor der erschwingliche 3D-Druck das Hindernis aus dem Weg räumte.
Für die Branche der Sportausrüstung oder Wearables waren die meisten bisher verfügbaren 3D-Druckmaterialien aber dennoch zu steif – bis TPU verfügbar wurde. Von Schuhsohlen, die genau an die individuelle Fußform und Gewichtsverteilung angepasst werden können, über für Stoßdämpfung entwickelte Football-Helme bis hin zu an das Handgelenk angepassten Uhrenarmbändern sind die Möglichkeiten endlos.
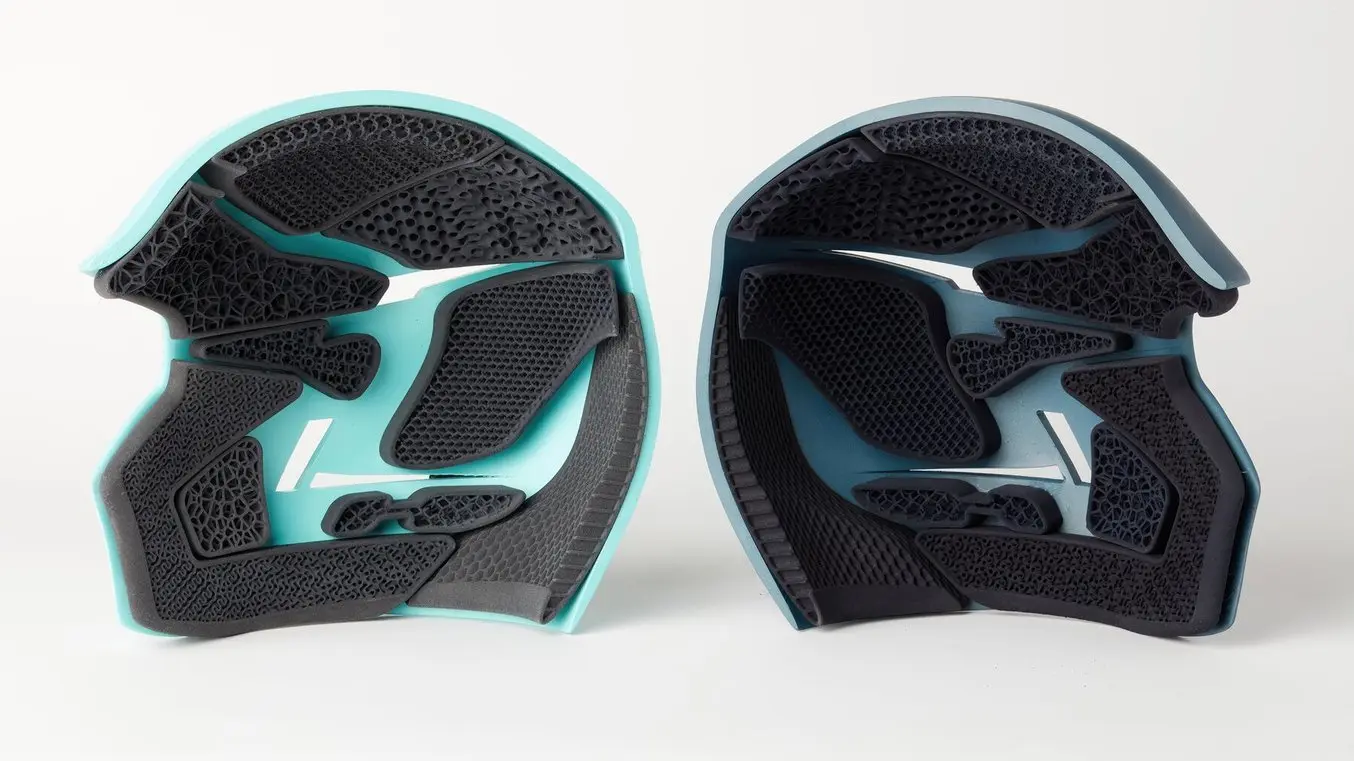
Helm für American Football mit maßgefertigter Polsterung, 3D-gedruckt aus TPU auf einem SLS-3D-Drucker der Fuse-Serie.
Medizinprodukte
Dank seiner überragenden Haltbarkeit und Zähigkeit eignet sich 3D-gedrucktes TPU ideal für Prothesen, Orthesen, patientenspezifische Geräte und andere Medizinprodukte. Der 3D-Druck flexibler, starker Teile für die Endverwendung eröffnet völlig neue Möglichkeiten in der Gesundheitsbranche, indem es die hohe Reißfestigkeit und Bruchdehnung von Gummimaterialien mit der Gestaltungsfreiheit und Widerstandsfähigkeit des SLS-3D-Drucks vereint.
TPU ist ein flexibles Elastomer und damit ideal für den 3D-Druck folgender medizinischer Teile:
-
Prototypen von Medizinprodukten, Medizinprodukte für die Endverwendung und deren Komponenten
-
Orthetische Polster und Prothesenauskleidungen
-
Wearables, Dichtungen, Dämpfer und Schläuche
-
Schienen, Schädel-Orthesen
-
Sporteinlegesohlen und Korrektureinlagen
Der 3D-Druck für das Gesundheitswesen ist zwar ein wachsender Anwendungsbereich, wird jedoch durch strenge Materialanforderungen eingeschränkt – sowohl hinsichtlich der Sicherheitszertifikationen als auch ihrer Festigkeit und mechanischen Eigenschaften. Der 3D-Druck von TPU eröffnet zusätzliche Anwendungsmöglichkeiten in der Gesundheitsbranche und bietet damit ein weiteres Hilfsmittel für die Fertigung.
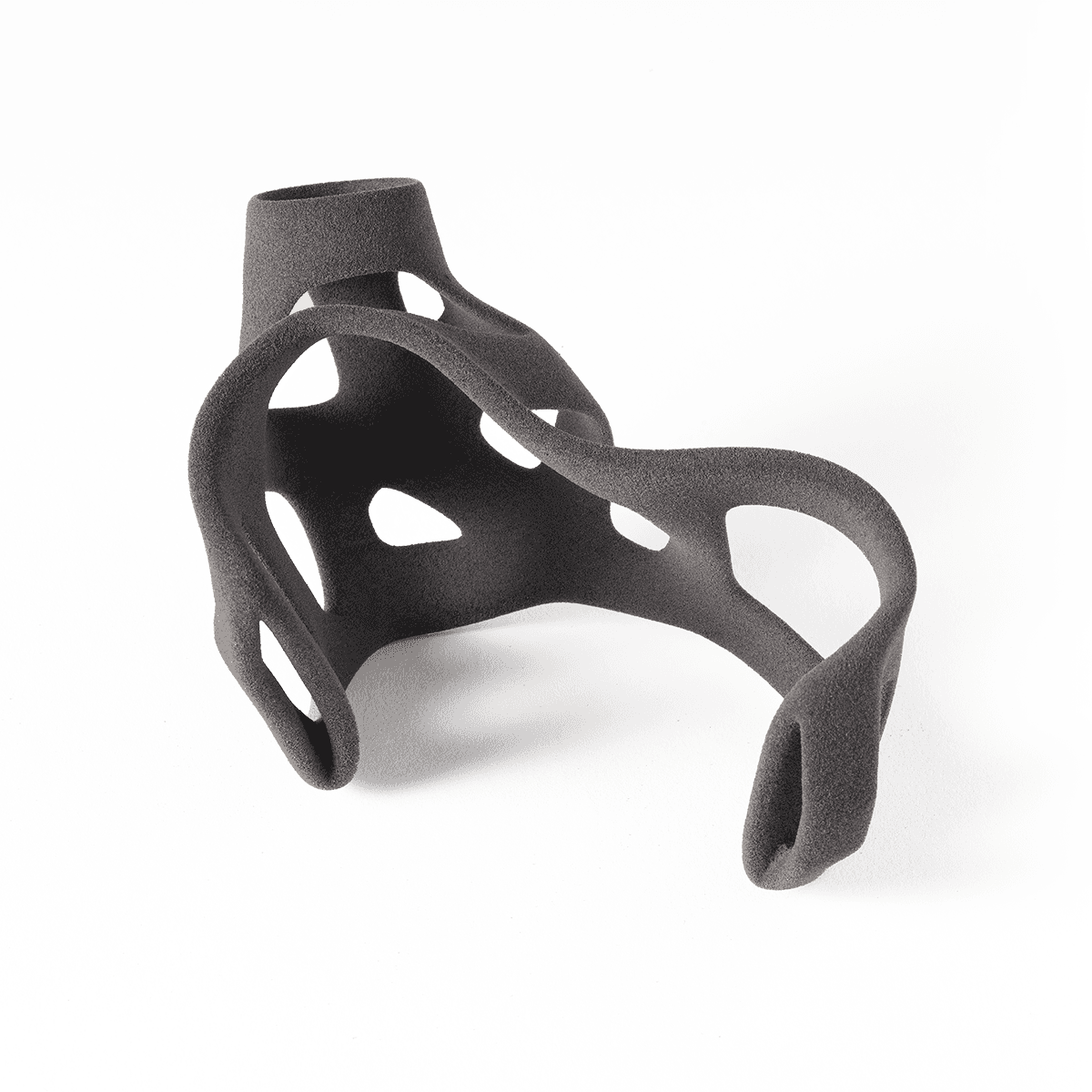
Diese maßgefertigte orthetische Daumenschiene bietet größere Flexibilität und mehr Kontrolle als konventionelle Schienen, um den Finger zu stützen und vor weiteren Verletzungen zu schützen.
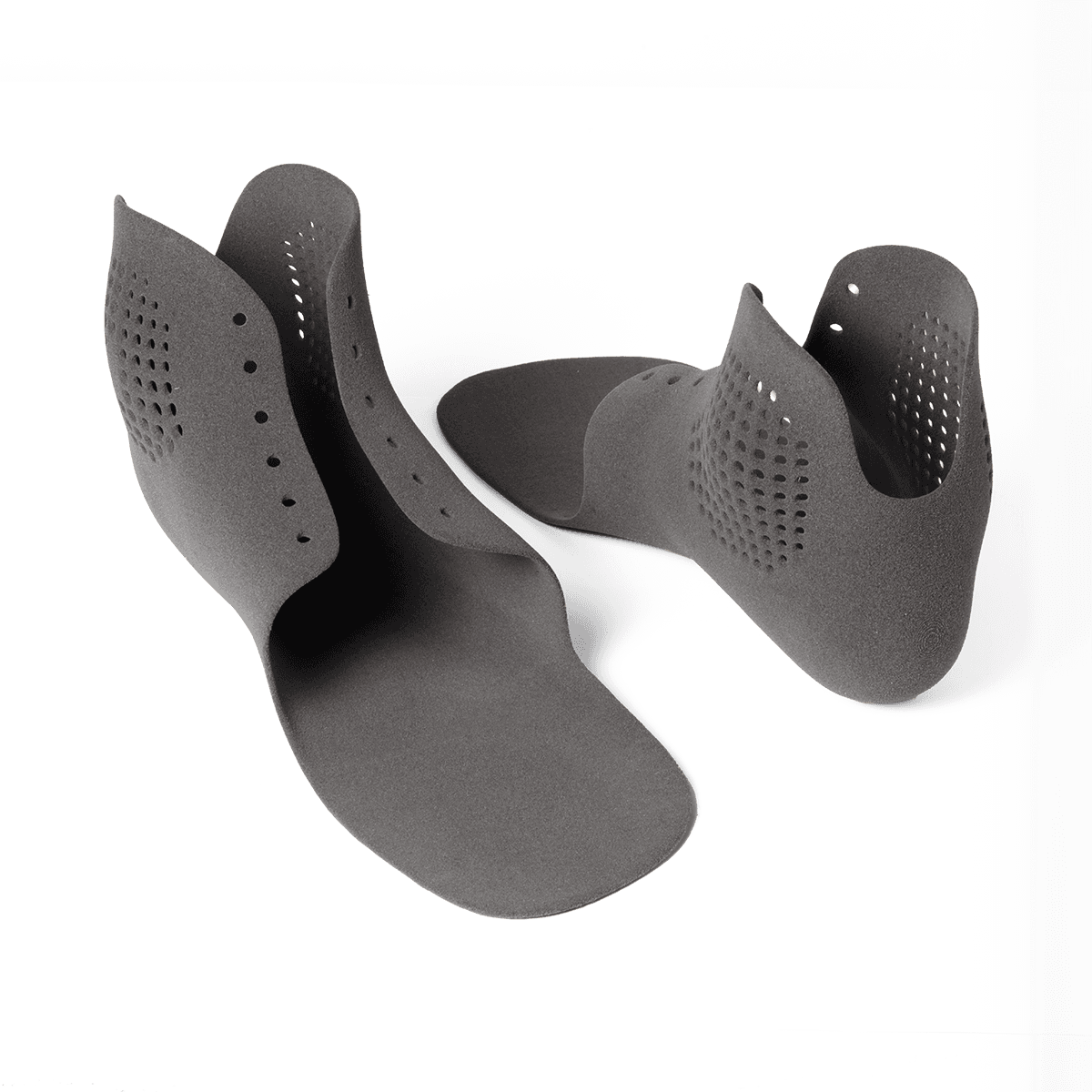
TPU eignet sich ideal für eine Vielzahl an Orthesen, beispielsweise orthopädische Einlegesohlen sowie Sporteinlagen.
Fallstudien
Schützende Maschinenkomponenten bei global führendem Druckpressenhersteller Heidelberg
Die Heidelberger Druckmaschinen AG ist der weltweit führende Hersteller von Offsetdruckmaschinen und in über 170 Ländern tätig, mit mehr als 10 000 Beschäftigten rund um den Globus. Das Unternehmen produziert eine große Bandbreite an Werkzeugen und Automatisierungslösungen für die gesamte Wertschöpfungskette des Drucks, angefangen von einigen der größten und schnellsten Druckpressen nach neuestem Stand bis hin zu Schneid- und Falzmaschinen.
Das Team nutzt seine SLS-3D-Drucker vom Typ Fuse 1+ 30W für zahlreiche Zwecke: Es produziert Maschinenkomponenten wie leichtgewichtige Teile für Pick-and-Place-Roboter, neue Bauteile für Falzmaschinen und Ersatzteile für Maschinenkomponenten, die früher aus Stahl gefertigt wurden. Mit TPU 90A Powder kann das Unternehmen flexible Teile herstellen, die Stößen standhalten und verformbar genug sind, um in bestehende Maschinen eingefügt zu werden.
Da die Ersatzteile oder Fertigungshilfsmittel in bestehende Robotiksysteme eingebaut werden müssen, haben die Teile oft ungewöhnliche, komplexe Formen. Sie werden abhängig von den Belastungen und Kräften, denen sie ausgesetzt werden, speziell für die jeweilige Anwendung entwickelt und unterliegen einem ständigen Verschleiß. Häufig werden die 3D-gedruckten Bauteile auch mit anderen Komponenten kombiniert, so zum Beispiel mit metallenen Lagern oder Bauteilen mit Teflon-Beschichtung, die reibungsmindernd wirkt. Einige Teile sind weniger komplex, erfordern aber dennoch eine hohe Genauigkeit oder Präzision.
Flexible TPU-Teile dienen hier dazu, Querkontamination zu verhindern, scharfe Kanten abzudecken, Sensoren zu schützen oder Verschleiß vorzubeugen. Der SLS-3D-Druck mit TPU 90A Powder ist der perfekte Prozess für diese Art von Teilen und kann teure Maschinen vor den Schäden schützen, die mit einer derart hohen Beanspruchung verbunden sind.
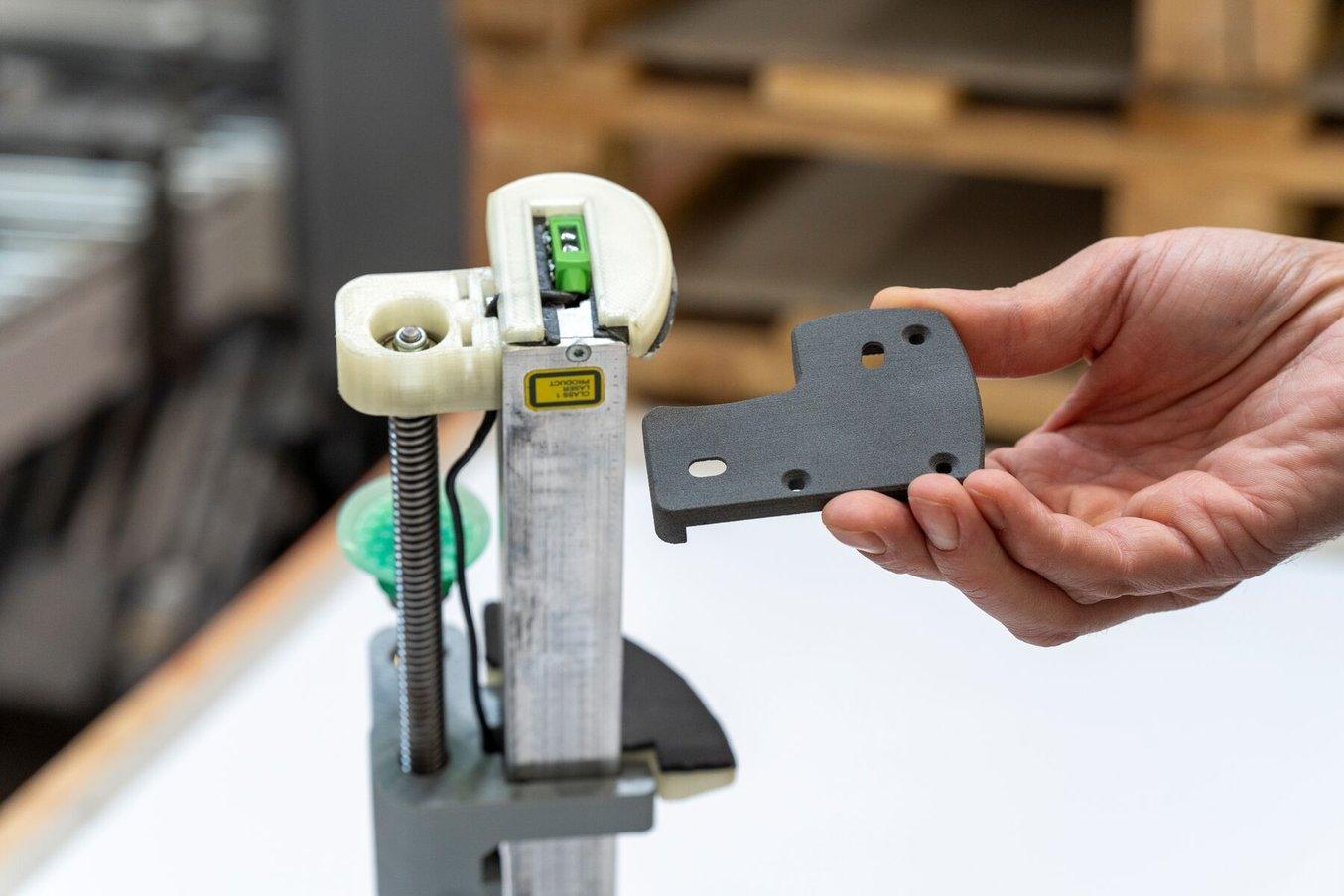
Ein flexibles Bauteil, das aus TPU 90A Powder 3D-gedruckt wurde und Sensoren und anderes End-of-Arm-Tooling schützt.
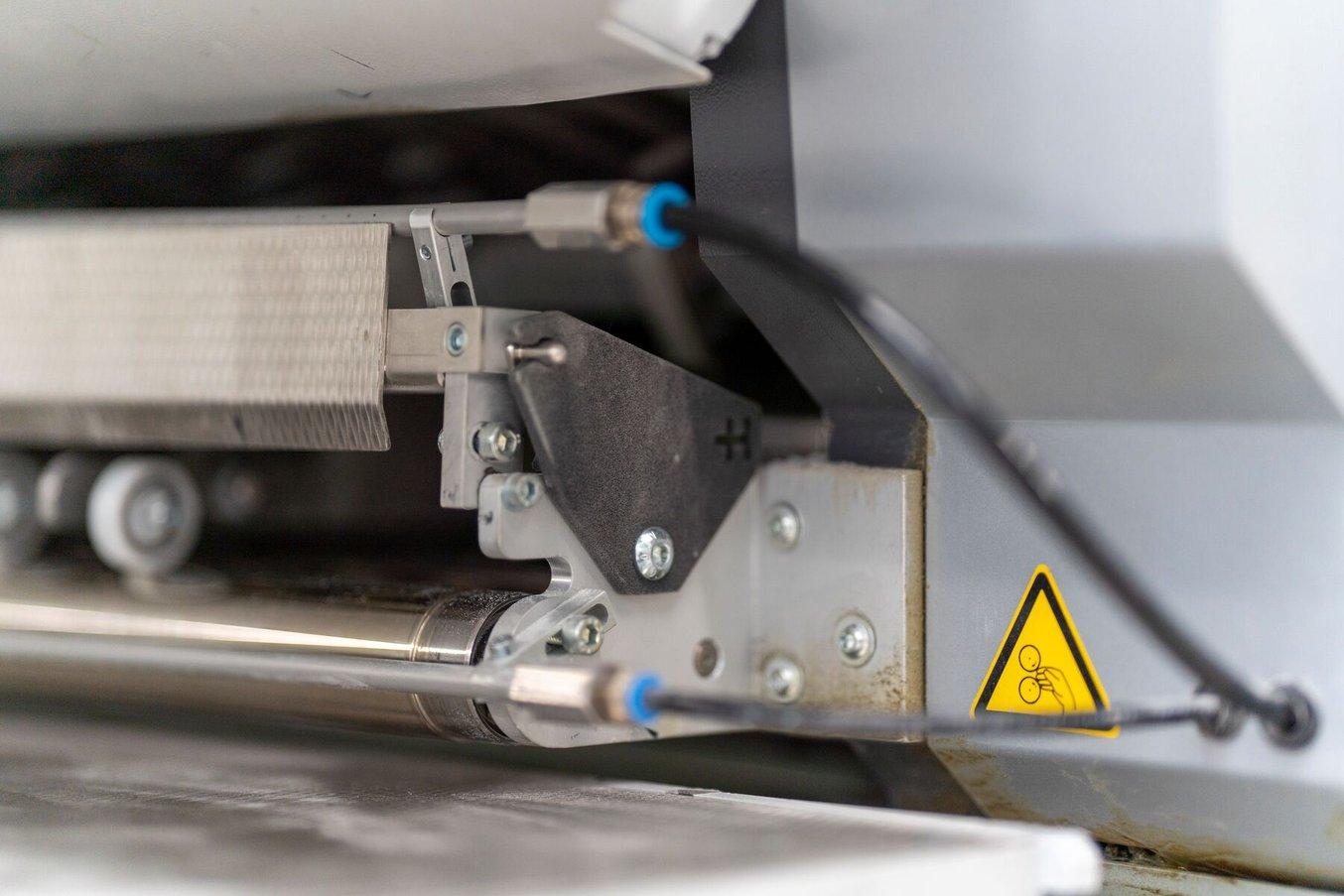
Flexible Komponenten eignen sich ideal für Schnappverbindungen. Indem Sie scharfe Kanten abdecken, dienen sie auch zum Schutz des Bedienpersonals.
Eines der Teile – eine Kabelführungskomponente hergestellt aus TPU 90A Powder – schützt elektrische Kabel vor Reibung, was die Langlebigkeit der Kabel erhöht und Ausfallzeiten minimiert. Wenn eines der Kabel reißt oder ausfranst, ist die gesamte Maschine außer Betrieb, bis ein Ersatz bestellt und installiert werden kann. Schützende Maschinenkomponenten wie diese Kabelführung können dazu beitragen, einen Betrieb am Laufen zu halten.
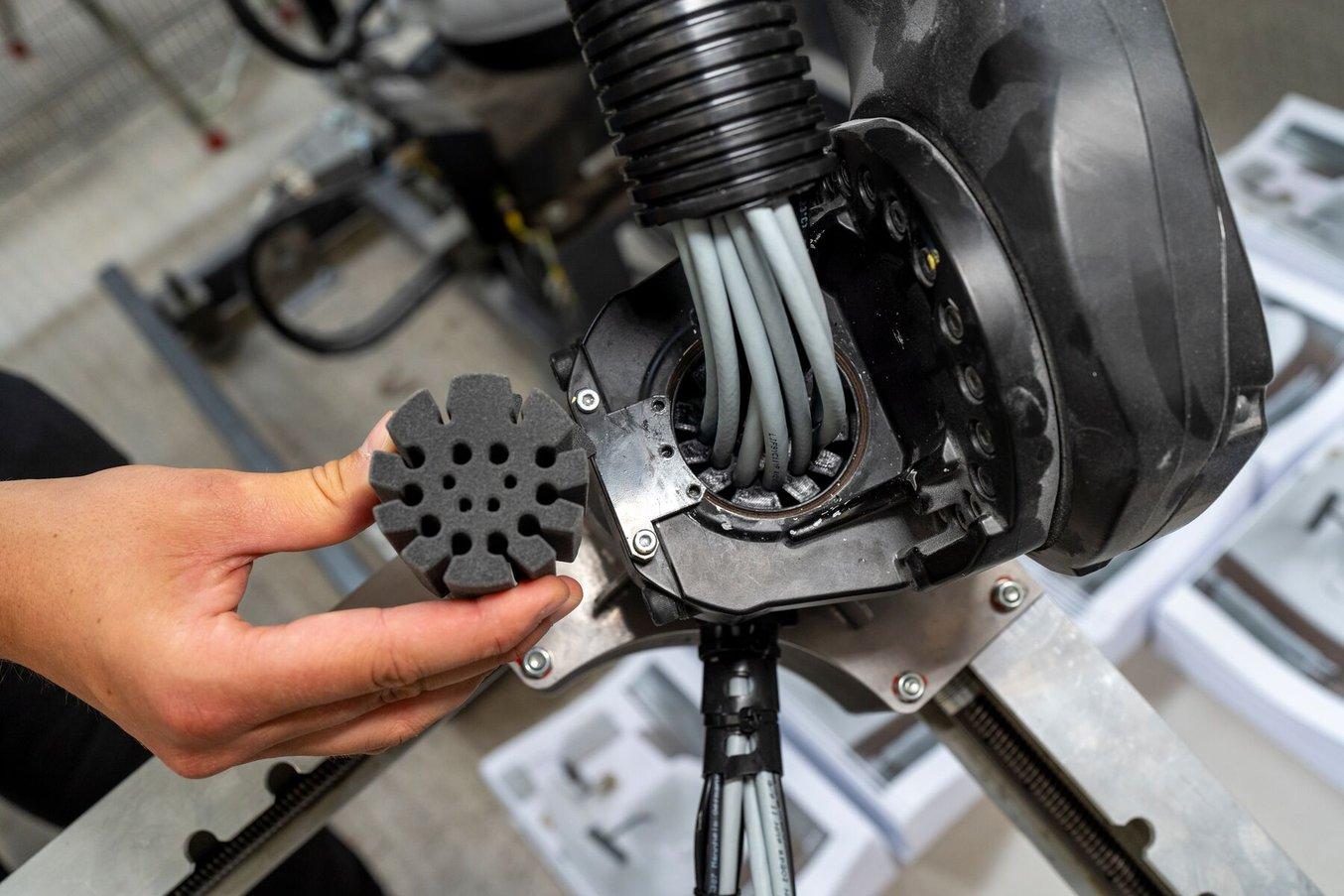
Diese biegsame Kabelführung, die auf dem SLS-3D-Drucker der Fuse-Serie produziert wurde, lässt ein komplexes Design zu und bietet eine langfristig haltbare Lösung, um Kabel vor Verschleiß zu bewahren.
Die Zugänglichkeit und Erschwinglichkeit der Fuse-Serie und von TPU 90A Powder ermöglichen es dem Unternehmen, die Kontrolle über seine Lieferkette und seine Wartung zu übernehmen. Teile aus TPU 90A Powder sind ideal für den Schutz von Maschinen, die Verbesserung der Langlebigkeit von Komponenten und letztlich die Kostenreduzierung und Vermeidung von Ausfallzeiten.
Wie die Deutsche Bahn mit TPU-Fertigungshilfsmitteln Züge am Laufen hält
Die Fahrzeuginstandhaltung der Deutschen Bahn in Neumünster ist für die Überholung und Wartung der Züge des ÖPNV in Deutschland zuständig, und der 3D-Druck trägt dazu bei, den Betrieb so effizient wie möglich zu gestalten. Durch die Integration des 3D-Drucks in ihren Arbeitsablauf konnte die Deutsche Bahn Millionen von Euro einsparen und die Durchlaufzeiten für die Wiederinbetriebnahme von Zugwaggons verkürzen.
Carsten Wolfgramm, Fertigungsingenieur und Experte für additive Fertigung, ist zuständig für zwei SLS-3D-Drucker vom Typ Fuse 1+ 30W, von denen einer mit Nylon 12 Powder und der andere mit TPU 90A Powder betrieben wird. „Die Maschinen von Formlabs verwenden wir, weil das Preis-Leistungs-Verhältnis für uns unschlagbar ist. Die Zuverlässigkeit ist gegeben und die Maschinen, gerade die SLS-Drucker, sind wirklich Plug-and-Play. Das erleichtert die Arbeit sehr, wenn wir iterationsschleifende Teile drucken. Die Geräte laufen 24 Stunden am Tag, sieben Tage die Woche, das ganze Jahr über“, so Wolfgramm.
Im Zuge der üblichen Wartungsarbeiten werden die Gepäckablagen entfernt, um die Wände der Waggons neu zu streichen und zu folieren. Das Bewegen der Ablagen führte dabei häufig zu Schäden an den Wänden und machte die mühsame Arbeit des Wartungsteams sofort wieder zunichte. Um die Wände zu schützen, entwarf das DB-Team maßgeschneiderte Abdeckungen aus TPU 90A Powder und produzierte sie mittels 3D-Druck. Die Abdeckungen werden auf die Ablagen geschoben und isolieren deren Kanten, sodass sie beim Abnehmen und Wiedereinsetzen keine Schäden an den frisch lackierten Zuginnenräumen verursachen.
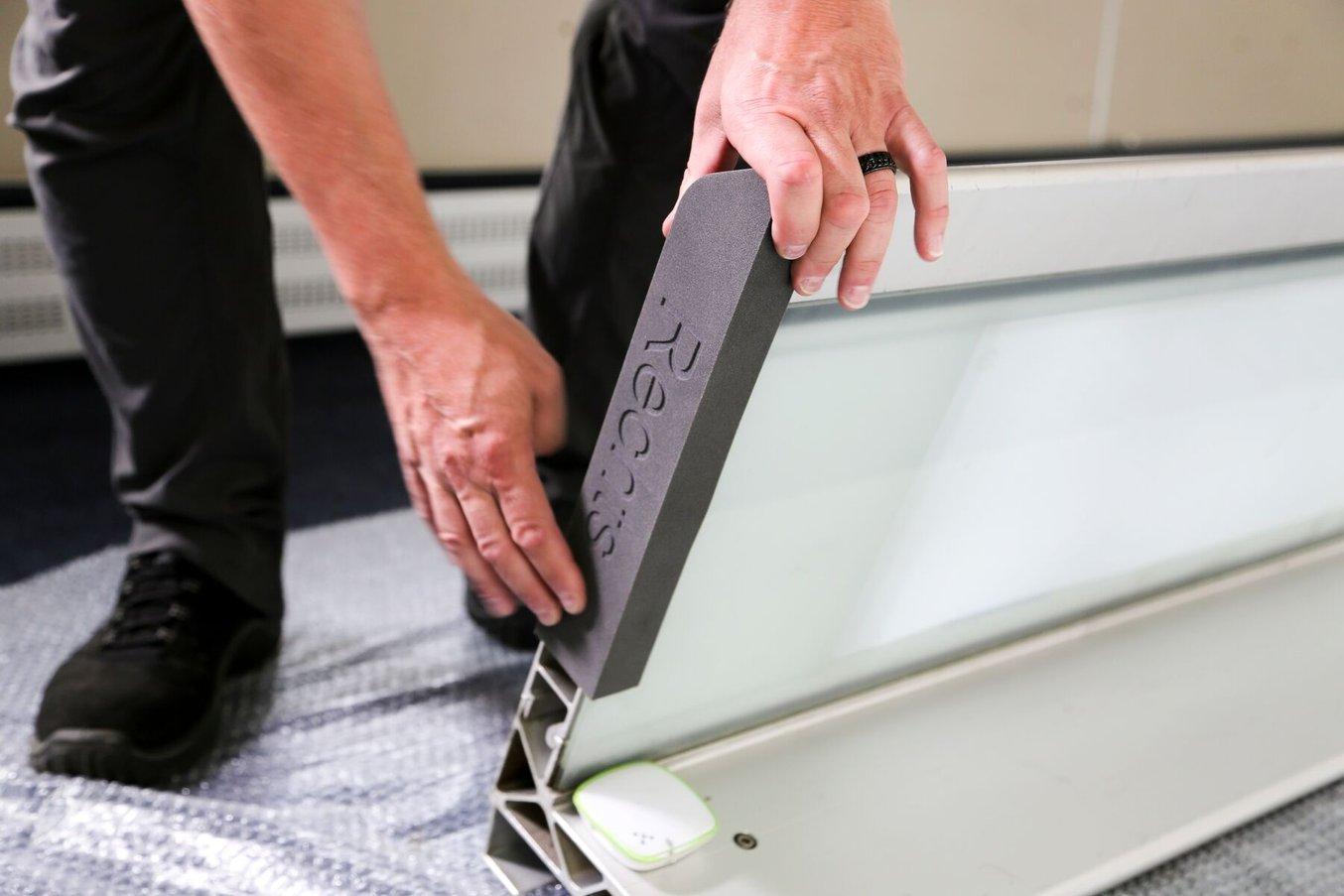
Das Team verwendet für den Kratz- und Stoßschutz ein flexibles Material, nämlich TPU 90A Powder.
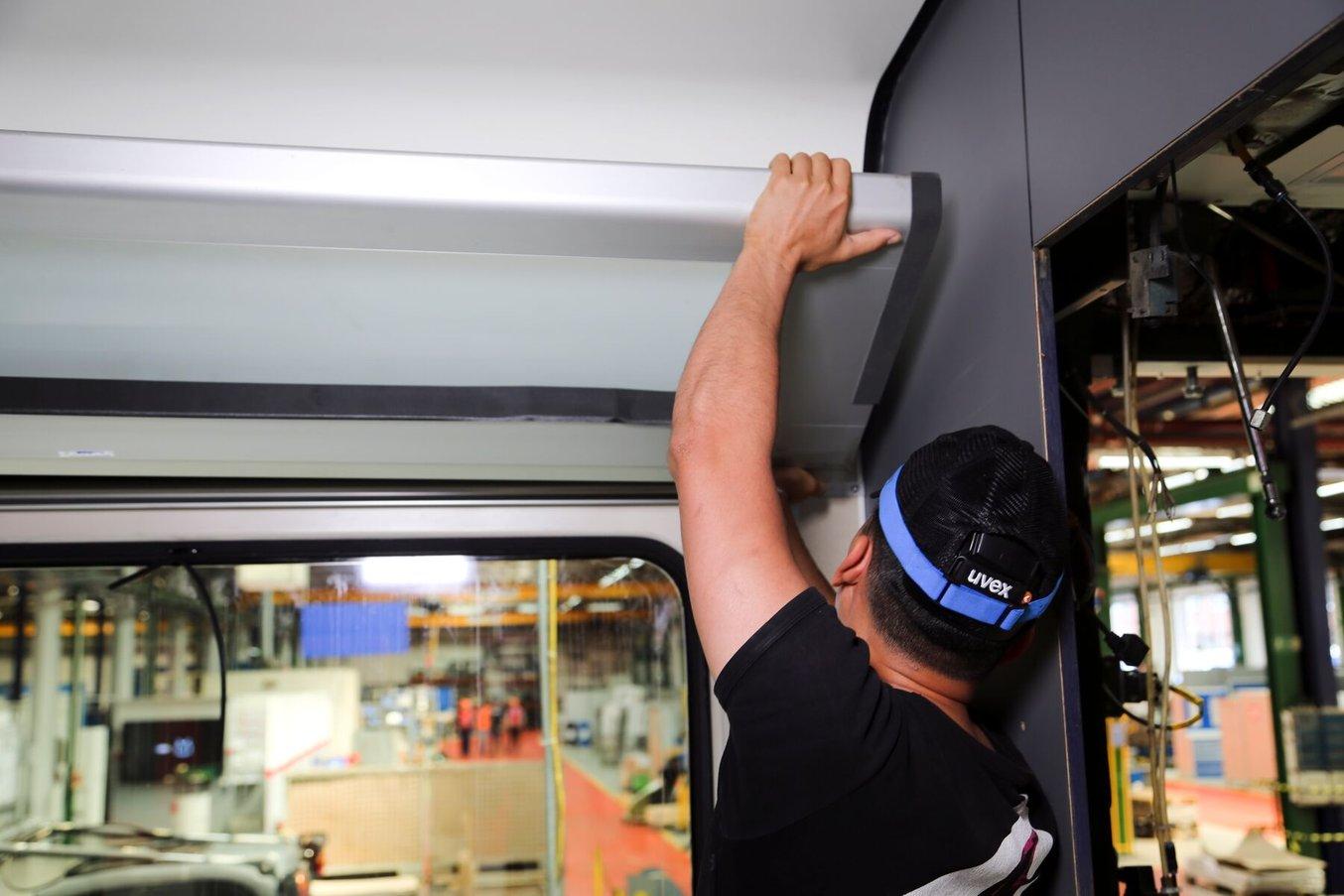
Der SLS-3D-Druck ermöglicht ein schmales Design, das zwischen die Gepäckablage und die Wand passt.
„Bevor wir diesen Kratzschutz entwickelt und gedruckt hatten, haben die Kollegen das immer herkömmlich mit Blasenfolie und Ähnlichem abgeklebt und versucht, Kratzer zu vermeiden – das ist aber nicht immer geglückt. Erst durch die neuen TPU-Teile konnten wir Kratzer zum ersten Mal ganz eliminieren.“
Carsten Wolfgramm, Fertigungsingenieur und Experte für additive Fertigung, Deutsche Bahn
Durch die Demonstration der Kosteneinsparungen und der minimierten Arbeitszeit, die mit 3D-gedruckten MRO-Teilen wie diesen möglich sind, bietet die Deutsche Bahn eine Blaupause für große Transportunternehmen, die den 3D-Druck in ihre Arbeitsabläufe integrieren möchten. Der Zugang zur internen Fertigung von individualisierbaren, flexiblen 3D-gedruckten Teilen wie diesen Schutzabdeckungen macht es der Deutschen Bahn möglich, ihre Prozesse effizienter zu gestalten und Züge schneller wieder aufs Gleis zu bringen.
Prototypenfertigung bei einem amerikanischen Spielzeug- und E-Bike-Hersteller: Radio Flyer und TPU
Als seit über 100 Jahren bewährtes und von Familien geschätztes Unternehmen ist Radio Flyer vor allem für seinen klassischen Ziehwagen Little Red Wagon® bekannt, der auch einen Platz in der US-amerikanischen Toy Hall of Fame errungen hat. Die Produkte des Unternehmens sind in der Populärkultur und auf Weihnachtswunschzetteln seit jeher ganz vorne dabei, denn im Bereich fahrender Spielzeuge ist Radio Flyer führend. Dazu gehören etwa Wagen, Roller, Dreiräder, Go-Karts, elektrische Fahrräder und andere innovative Produkte, mit denen Familien gemeinsam neue Orte entdecken.
Der 3D-Druck spielt eine wichtige Rolle im Entwicklungsprozess von Radio Flyer, und mit TPU 90A Powder erstellt Designingenieur Agostino Lobello jetzt vollkommen funktionsfähige Prototypen. „Die hochgradig griffige Oberflächenbeschaffenheit ist einzigartig im Vergleich zu anderen 3D-gedruckten TPE-/TPU-Materialien, die ich gesehen habe. In dieser Hinsicht scheint es doch unserem spritzgegossenen TPE/TPU ähnlicher zu sein, was für das Prototyping spannend ist. Bisher wäre die nächstbeste Alternative zu diesem Prozess, einen Werkzeugprototyp herzustellen und echtes TPE oder ein anderes Urethan einzuspritzen, was sowohl teurer als auch zeitaufwendiger wäre“, so Lobello.
"Wir freuen uns darauf, dieses Material für Reifenprofile, Lenkergriffe, Stoßstangen, Sitzpolster und für Prototypen von TPE-Federn mit der perfekten Federrate einzusetzen."
Agostino Lobello, Designingenieur
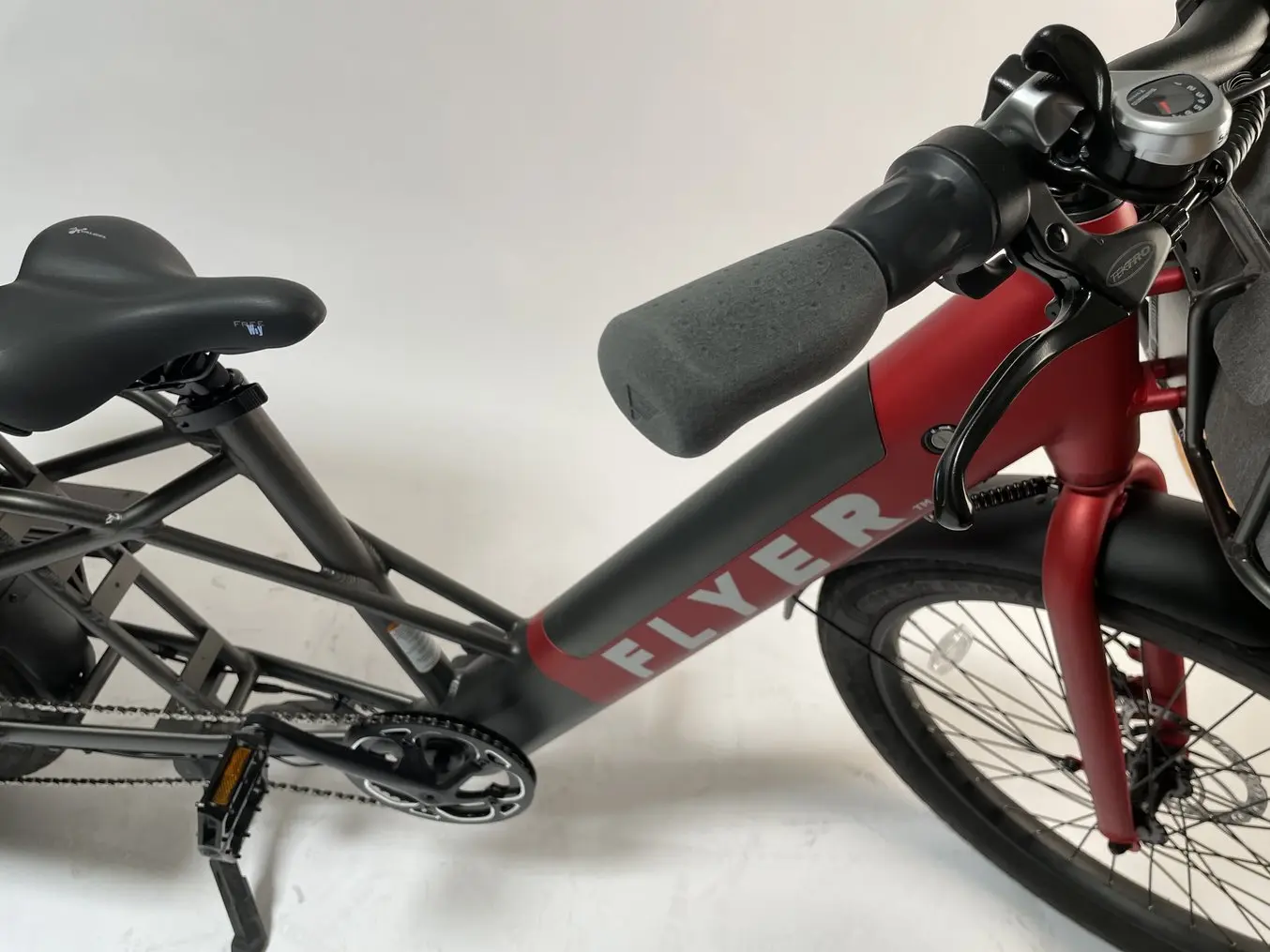
Durch die Nutzung von TPU 90A Powder auf den Druckern der Fuse-Serie erstellt Radio Flyer funktionsfähige Prototypen von Teilen wie diesen weichen Lenkergriffen am Flyer™ L885 Family Cargo eBike.
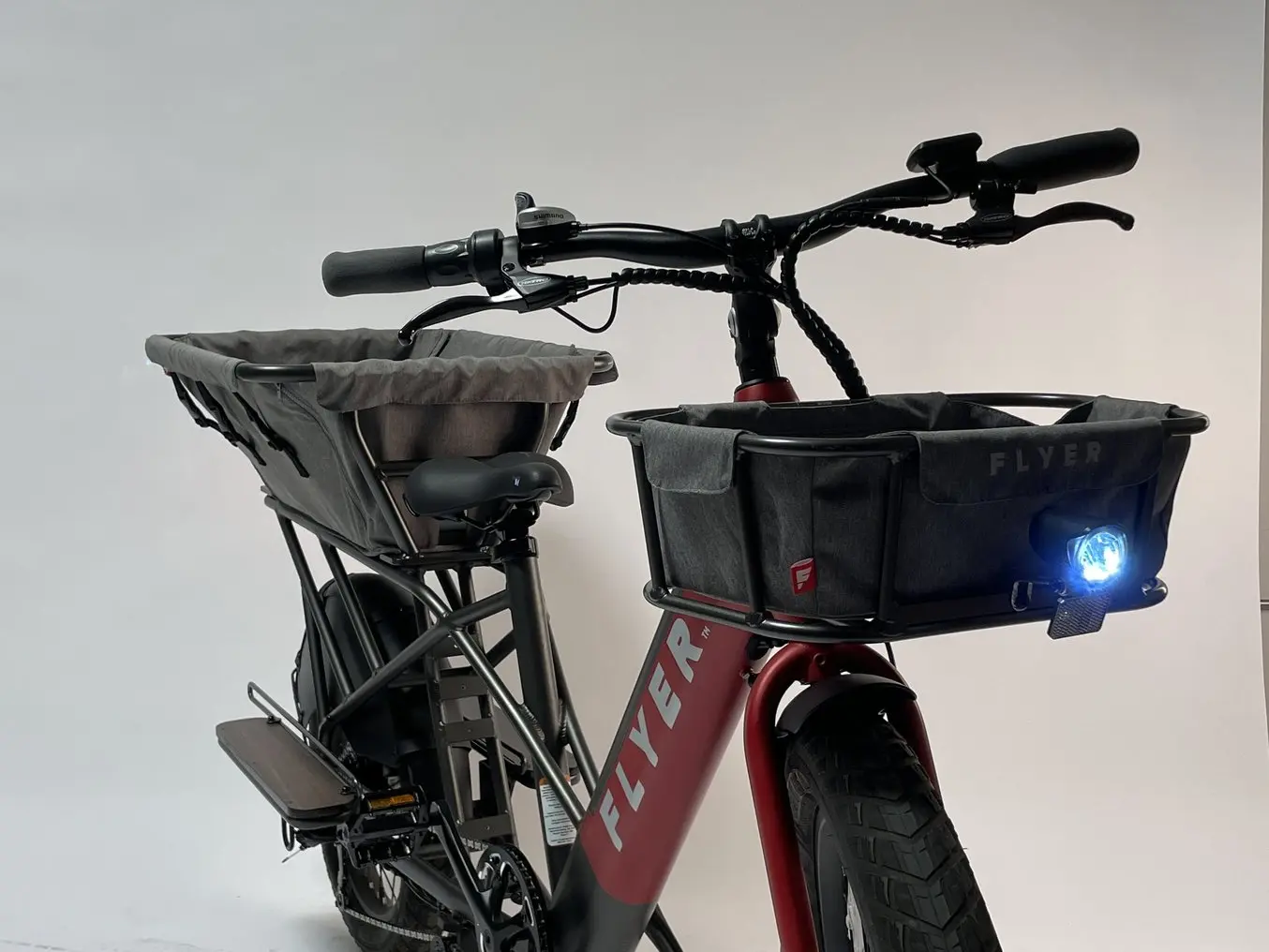
Steigen Sie ein in den 3D-Druck von TPU mit der Fuse-Serie
Der unkomplizierte Workflow des SLS-3D-Drucks mit TPU 90A Powder ebnet Herstellern den Weg zu neuen Möglichkeiten, ihren Designprozess durch qualitatives iteratives Prototyping zu verbessern oder individualisierte Teile für die Endverwendung zu produzieren.
Das SLS-Ecosystem der Fuse-Serie, einschließlich Drucker und Fuse Sift, ist kompakt und erschwinglich. Formlabs' TPU 90A Powder lässt neue Anwendungsbereiche zu und optimiert Prozesse durch die Produktion starker, flexibler und isotroper Teile, die zuvor nur mit Spritzguss umsetzbar waren. Betriebsinterne Fertigungslösungen für gummiartige Teile gewähren Ihnen größere Kontrolle und Flexibilität in Ihren Design- und Herstellungsprozessen, ganz gleich, um welche Anwendung oder Branche es geht. TPU 90A Powder von Formlabs ist als hautverträglich bewertet und eröffnet damit zahlreiche Möglichkeiten für die Gesundheitsbranche und die Herstellung von Wearable-Technologien.
Um mehr über den 3D-Druck von TPU-Teilen mit dem SLS-Workflow von Formlabs zu erfahren, fordern Sie einen kostenlosen Probedruck aus TPU 90A Powder an oder kontaktieren Sie unser Vertriebsteam für eine Beratung zu Ihrem spezifischen Anwendungsfall.