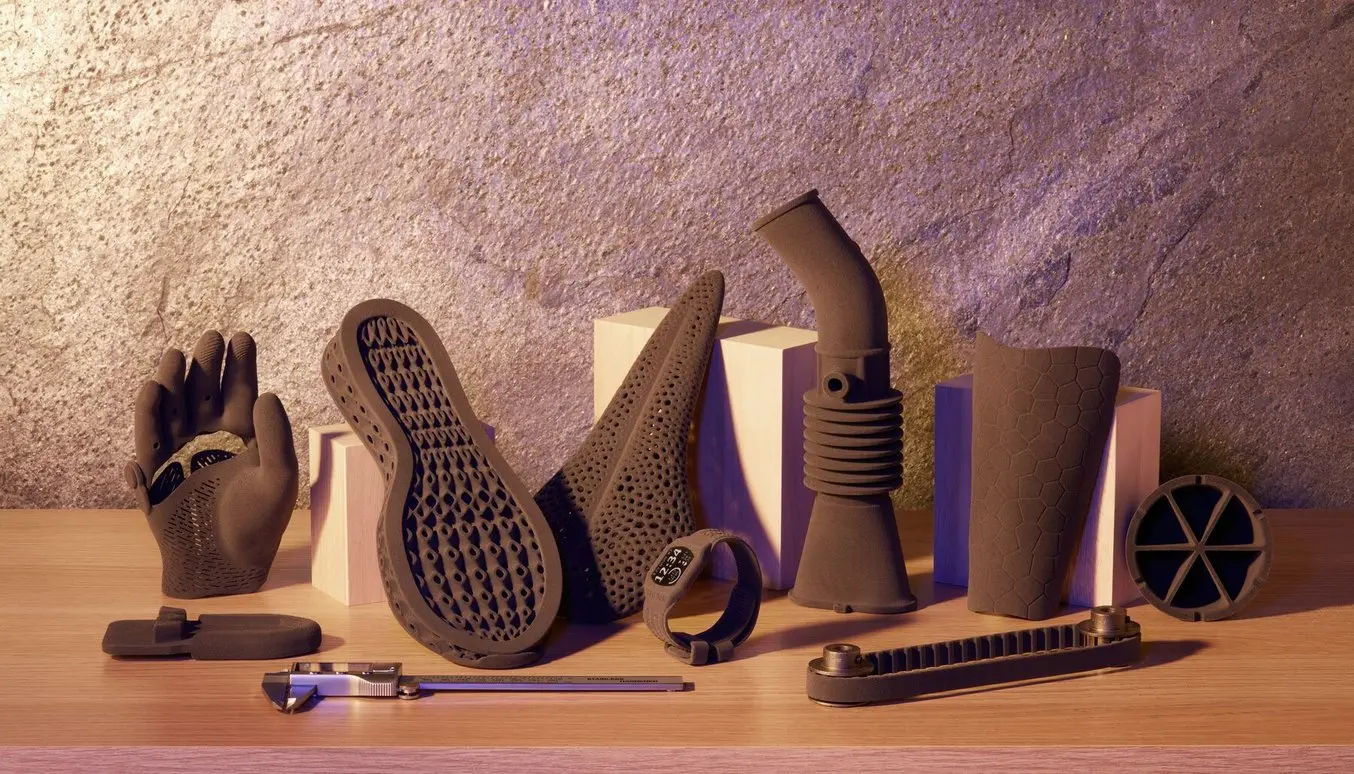
Mit TPU 90A Powder präsentiert Formlabs sein erstes Material mit weicher Haptik für die SLS-Drucker der Fuse-Serie. TPU eröffnet völlig neue Anwendungsbereiche, indem es die hohe Reißfestigkeit und Bruchdehnung von Gummimaterialien mit der Gestaltungsfreiheit und Widerstandsfähigkeit des SLS-3D-Drucks vereint.
TPU 90A Powder ist ein flexibles Elastomer und damit ideal für den 3D-Druck folgender Teile:
- Wearables für das Tragen auf der Haut
- Sohlen, Schienen, Orthetik und Prothetik
- Schutzausrüstung für den Sport
- Dichtungen, Abdeckungen, Riemen, Stöpsel und Schläuche
- Polsterung, Dämpfer und Greifer
Indem Sie Ihre SLS-Materialbibliothek um TPU 90A Powder erweitern, kombinieren Sie die Effizienz, Erschwinglichkeit und Benutzerfreundlichkeit der Drucker der Fuse-Serie mit der völlig neuen Option, SLS-Teile mit weicher Haptik betriebsintern zu fertigen. Die Neuzuführungsrate ist mit 20 % die niedrigste unter allen bisherigen SLS-Pulvern und trägt dazu bei, dass die Stückkosten gesenkt werden und gummiartige Prototypen, Endverbrauchsteile und Fertigungshilfen auch ohne teures Werkzeug betriebsintern produziert werden können.
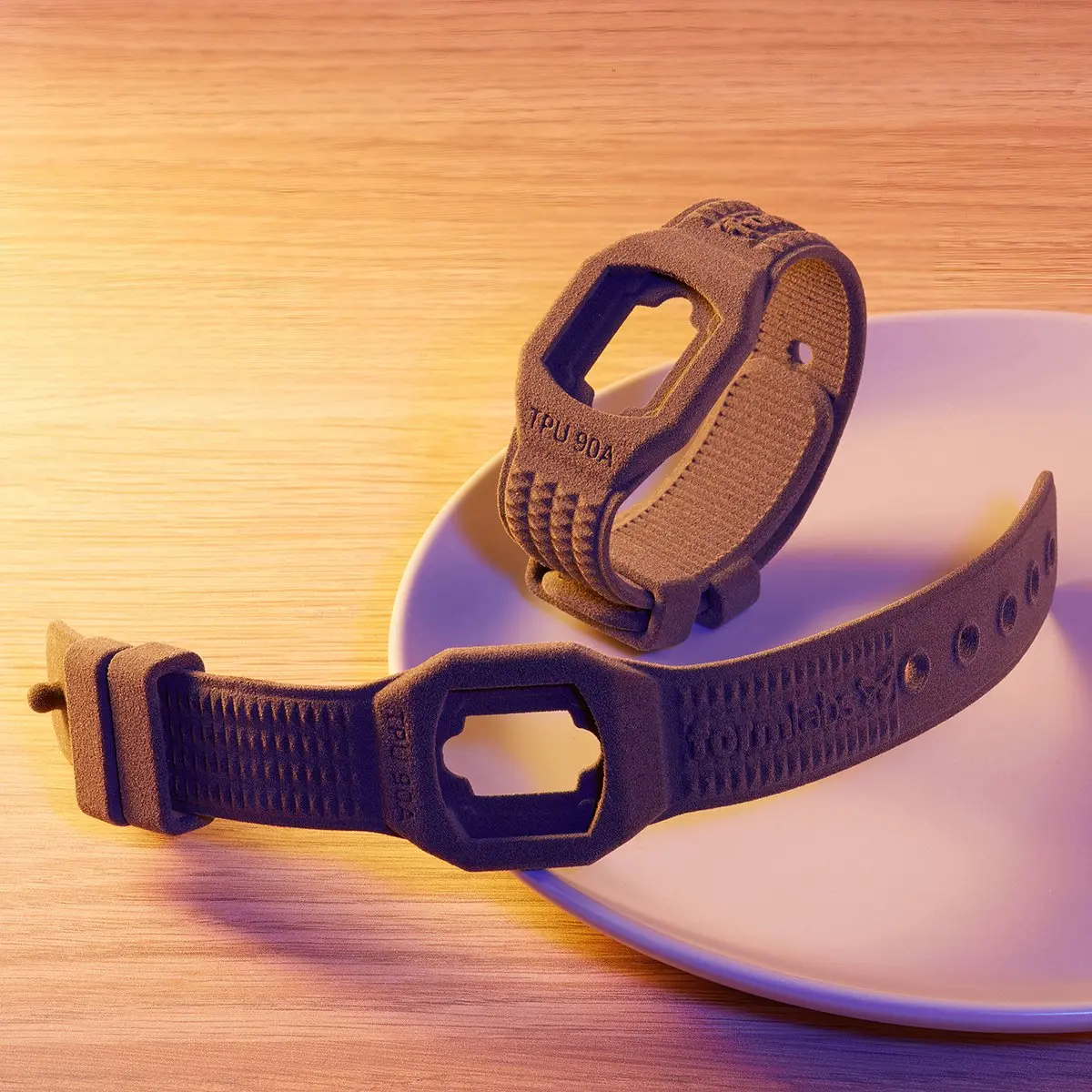
TPU 90A Powder: Formlabs' flexibles SLS-Pulver
Erfahren Sie in unserem Webinar, wie TPU 90A Powder Ihnen zur betriebsinternen Herstellung weicher Gummiteile mit den 3D-Druckern der Fuse-Serie verhilft.
Warum TPU mit der Fuse-Serie drucken?
Es existieren zahlreiche Optionen zur Fertigung von Elastomerteilen, einschließlich traditionelle Umformverfahren oder 3D-Druck mit Pulverbettfusion auf herkömmlichen Druckern. Diese Methoden werden entweder durch die geometrischen Einschränkungen des Formenbaus beeinträchtigt, oder aber durch die Kosten und komplexen Prozesse der meisten großformatigen, industriellen 3D-Drucklösungen. TPU 90A Powder für die Fuse-Serie von Formlabs bietet die ideale Lösung zur betriebsinternen Herstellung geometrisch fortschrittlicher, flexibler Teile in kurzer Zeit.
Die Drucker der Fuse-Serie von Formlabs sind die ersten 3D-Drucksysteme mit Pulverbettfusion, die industrielle SLS-Leistung auf kleiner Stellfläche und zu einem erschwinglichen Preis liefern. Nun da sich der Arbeitsprozess der Fuse-Serie bereits für Tausende von Kunden bewährt hat, liegt unsere höchste Priorität in der Vergrößerung der Materialbibliothek der SLS-Pulver. Erschwinglicher SLS-Druck ermöglicht es kleinen Unternehmen, Kontrolle über Ihre Produktion zu übernehmen und diese erheblich zu steigern, während er großen Unternehmen die Chance bietet, Ihre Fertigung zu diversifizieren und zu dezentralisieren, was für stabilere Lieferketten sorgt. Durch die Veröffentlichung von Materialien, die für die Fuse-Serie zwar eine Neuheit sind, dafür aber in der Branche wohlbekannt, bieten wir eine effiziente Möglichkeit zur Implementierung neuer Arbeitsprozesse und Innovationen in jedem Anwendungsbereich.
Eigenschaft | Nylon 11 CF Powder | Nylon 12 GF Powder | Nylon 12 Powder | Nylon 11 Powder | TPU 90A Powder |
---|---|---|---|---|---|
Steifigkeit | ★★★★ | ★★★★ | ★★★ | ★★ | ★ |
Duktilität | ★★★ | ★ | ★★ | ★★★★ | ★★★★★ |
Wärmebeständigkeit | ★★★★ | ★★★★ | ★★★ | ★ | ★ |
Neuzuführungsrate | 30 % (N2) | 30–50 % (Luft) | 30 % (Luft) | 30 % (N2) 50 % (Luft) | 20 % (Luft) |
TPU 90A Powder bietet die geringste Steifigkeit und höchste Duktilität in unserer Materialfamilie der SLS-Pulver.
Wofür eignet sich TPU 90A Powder?
TPU, oder thermoplastisches Polyurethan, ist einer der am häufigsten verwendeten elastomeren Thermoplaste in den Bereichen Maschinenbau, Design und Fertigung. Dieses gummiartige, robuste Material findet überall Einsatz: von Sportausrüstung über Medizinprodukte bis hin zu den Schuhsohlen an unseren Füßen.
Für die konventionelle Herstellung von TPU-Teilen gibt es bewährte Verfahren – und für massenproduzierte Gummiprodukte eignen sich diese Prozesse nach wie vor ideal. Die Vorteile des Drucks von TPU 90A Powder mit den Druckern der Fuse-Serie liegen in der Einfachheit der Nutzung dieses Systems für Rapid Prototyping, Fertigungshilfen auf Abruf und die Individualisierung von Produkten.
Rapid Prototyping
Mit der Fuse-Serie verlagern Unternehmen die Prototypenfertigung in den eigenen Betrieb, verkürzen ihre Durchlaufzeiten und reduzieren Kosten, die bis dahin für Fertigungsdienstleister anfielen.
Um beispielsweise einen Prototyp eines Sporthelms herzustellen, müssen sowohl für die harte Schale als auch für die weiche Polsterung Fertigungskapazitäten vorhanden sein. Innovative Unternehmen entwickeln für solche Polsterungen neuartige Gitterstrukturen und Stoßdämpfungstechnologien, wofür TPU das perfekte Material darstellt.
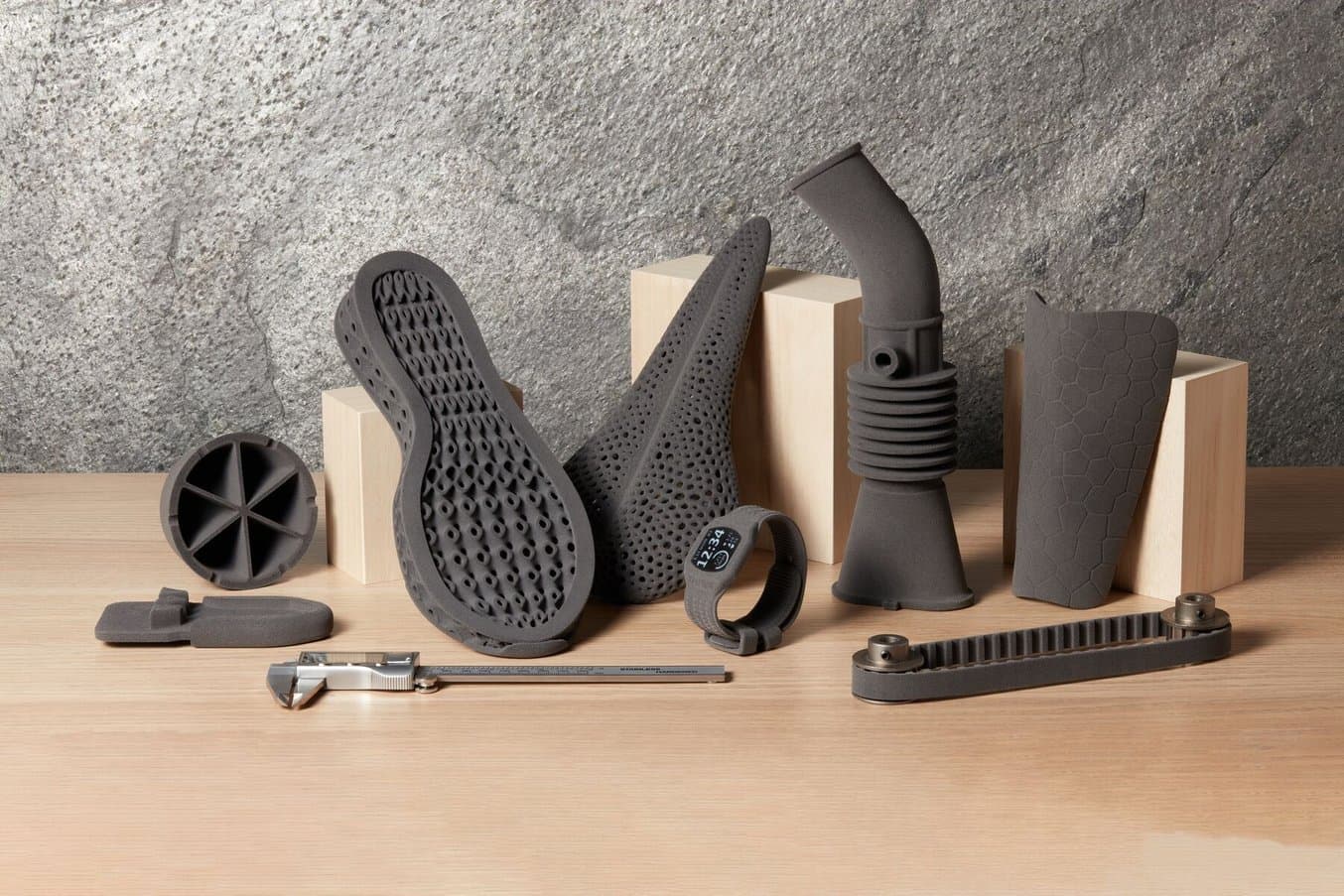
TPU 90A Powder eignet sich ideal für funktionsfähige Prototypen von flexiblen Teilen, wie etwa hautverträgliche Wearables, Sportausrüstung oder Schuhsohlen.
Das Ausprobieren neuer Designs und Geometrien ist mit traditionellen Methoden des Werkzeugbaus unerschwinglich teuer, die Auslagerung an Dienstleister wiederum kann Wochen beanspruchen. Wenn derselbe Arbeitsprozess und dieselbe Technologie sowohl für die harte äußere Schale als auch für die weiche Polsterung im Inneren genutzt werden können, laufen die Iterationen in einem viel schnelleren Takt ab. Da die Helme ausgiebigen physischen Tests unterzogen werden, sind für einen einzigen Testdurchlauf zehn Polster erforderlich. Das sind zu hohe Stückzahlen, um die Oberfläche der Polsterung in akribischer Handarbeit herzustellen, gleichzeitig aber zu wenig Teile für eine kosteneffiziente TPU-Umformung mit konventionellen Methoden. Die Lösung ist der betriebsinterne 3D-Druck. Mit den 3D-Druckern der Fuse-Serie und TPU 90A Powder lassen sich mit Leichtigkeit mehrere gummiartige Gitterstrukturen drucken, die zum Testen verschiedener Designs auch leichte Variationen aufweisen. Durch Anpassungen am Design des Teils, etwa der Wandstärke, können Teile mit unterschiedlicher Härte für verschiedene Anwendungen oder als Iterationen für Produkttests gefertigt werden.
Der Arbeitsablauf mit der Fuse-Serie lässt den Einsatz verschiedener Materialien zu, die eine große Bandbreite mechanischer Eigenschaften abdecken. So wird die Fertigung komplett betriebsintern erledigt und die Entwicklung zahlreicher verschiedener Komponenten mit nur einer Technologie umgesetzt. TPU 90A Powder eröffnet eine völlig neue Art 3D-gedruckter Komponenten, alles auf derselben bewährten Plattform.
Prototypenfertigung bei einem amerikanischen Spielzeug- und E-Bike-Hersteller: Radio Flyer und TPU
Als seit über 100 Jahren bewährtes und von Familien geschätztes Unternehmen ist Radio Flyer vor allem für seinen klassischen Ziehwagen Little Red Wagon® bekannt, der auch einen Platz in der US-amerikanischen Toy Hall of Fame errungen hat. Die Produkte des Unternehmens sind in der Populärkultur und auf Weihnachtswunschzetteln seit jeher ganz vorne dabei, denn im Bereich fahrender Spielzeuge ist Radio Flyer führend. Dazu gehören etwa Wagen, Roller, Dreiräder, Go-Karts, elektrische Fahrräder und andere innovative Produkte, mit denen Familien gemeinsam neue Orte entdecken.
Der 3D-Druck spielt eine wichtige Rolle im Entwicklungsprozess von Radio Flyer, und mit TPU 90A Powder erstellt Designingenieur Agostino Lobello jetzt vollkommen funktionsfähige Prototypen. „Die hochgradig griffige Oberflächenbeschaffenheit ist einzigartig im Vergleich zu anderen 3D-gedruckten TPE-/TPU-Materialien, die ich gesehen habe. In dieser Hinsicht scheint es doch unserem spritzgegossenen TPE/TPU ähnlicher zu sein, was für das Prototyping spannend ist. Bisher wäre die nächstbeste Alternative zu diesem Prozess, einen Werkzeugprototyp herzustellen und echtes TPE oder ein anderes Urethan einzuspritzen, was sowohl teurer als auch zeitaufwendiger wäre“, so Lobello.
Die Produkte von Radio Flyer werden rigorosen Tests unterzogen, um zu gewährleisten, dass sie sicher und praktikabel sind und ihrer jungen Kundschaft Freude bereiten. Prototypen unter lebensechten Bedingungen testen zu können ist entscheidend; deshalb müssen Designteams in kurzer Zeit Iterationen von Teilen fertigen können, die robust sind und hoher Beanspruchung standhalten. „Die Teile selbst scheinen recht widerstandsfähig zu sein. Sie würden sich problemlos auf funktionalen Prototypen installieren und für Tests zur Ergonomie und Praktikabilität nutzen lassen. Wir freuen uns darauf, dieses Material für Reifenprofile, Lenkergriffe, Stoßstangen, Sitzpolster und für Prototypen von TPE-Federn mit der perfekten Federrate einzusetzen“, sagt Lobello.
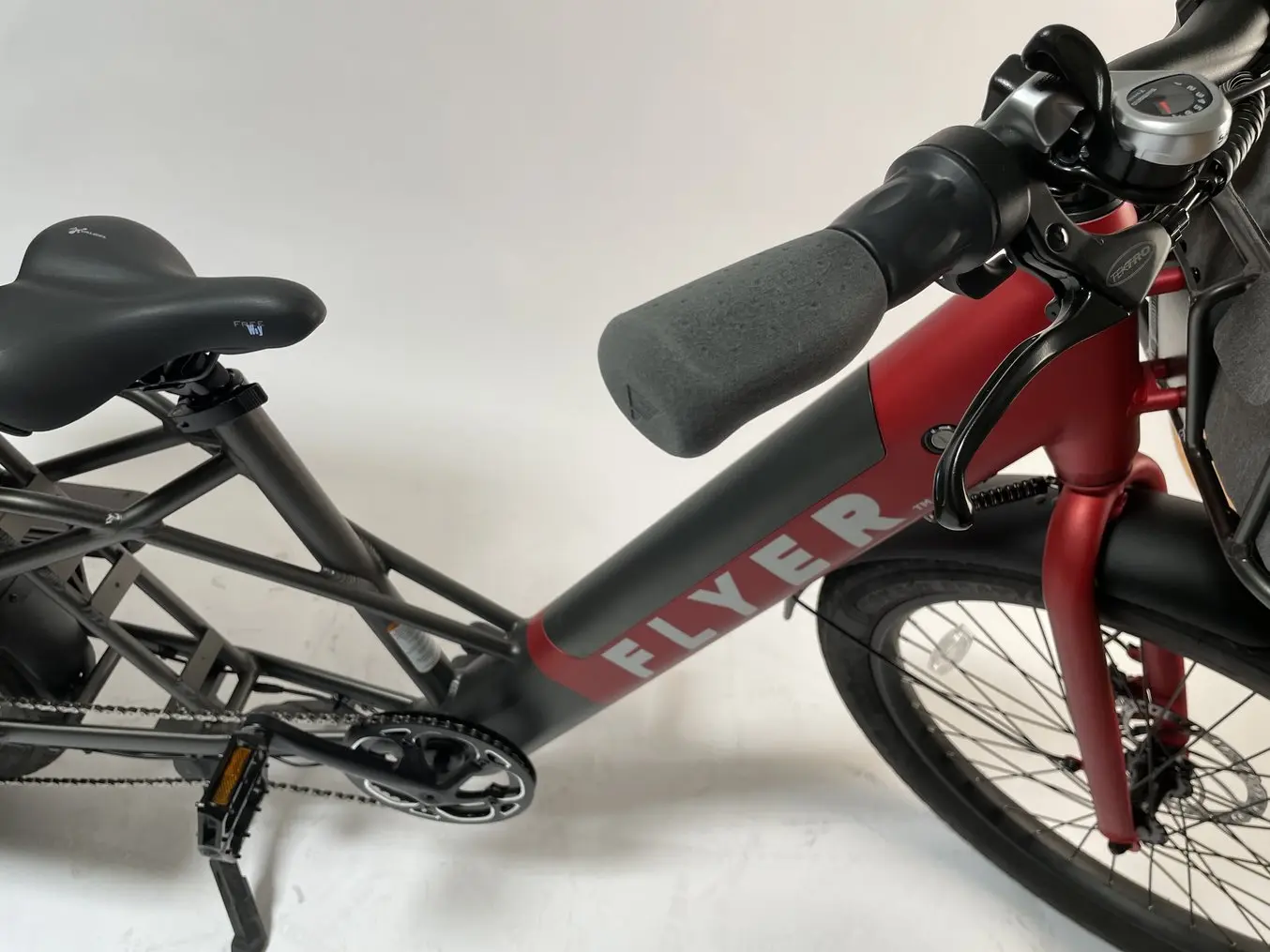
Durch die Nutzung von TPU 90A Powder auf den Druckern der Fuse-Serie erstellt Radio Flyer funktionsfähige Prototypen von Teilen wie diesen weichen Lenkergriffen am Flyer™ L885 Family Cargo eBike.
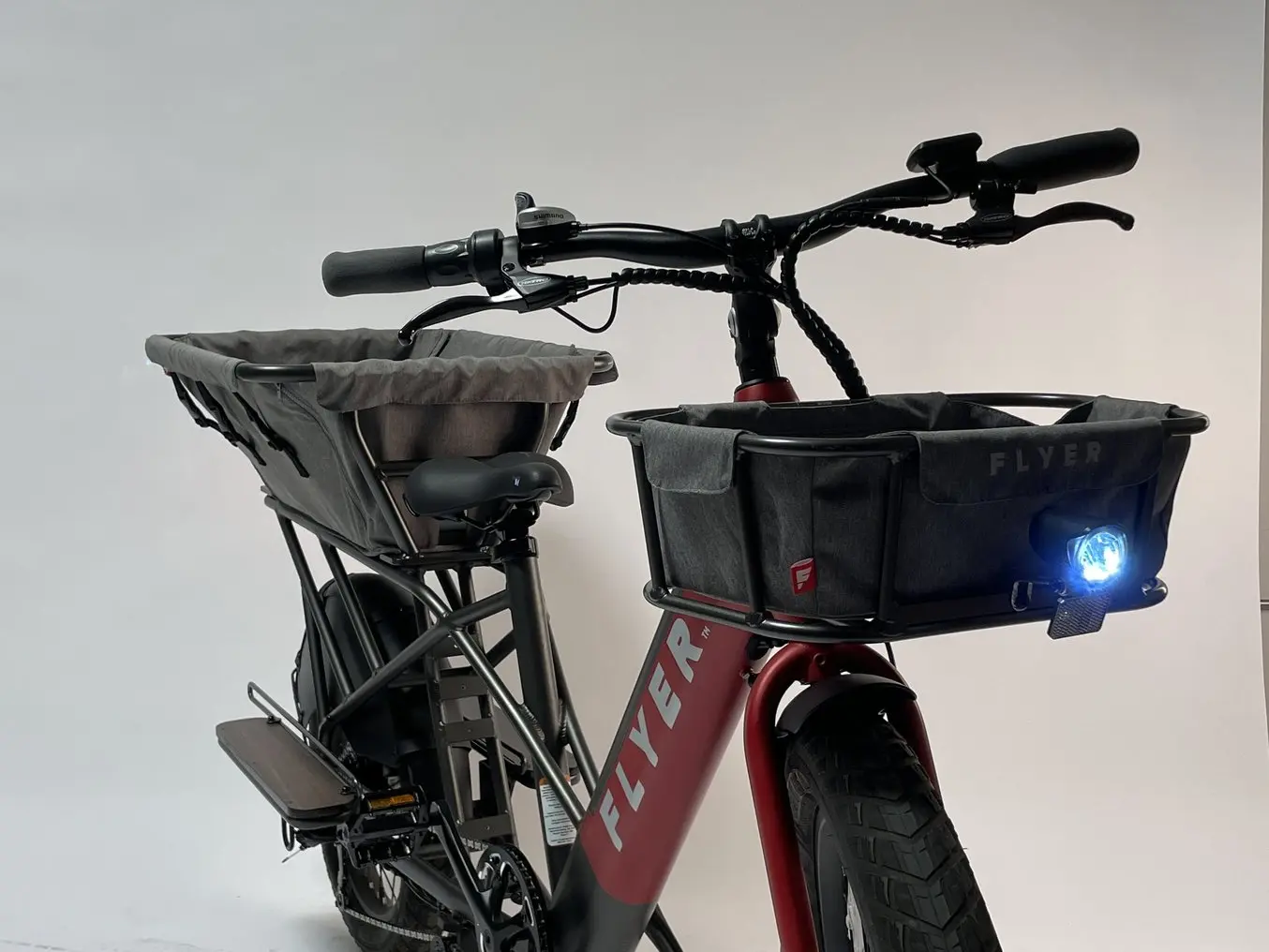
Fertigungshilfen
Wer nicht mit der Fertigung vertraut ist, für den sind die verschiedenen Arten von Fertigungshilfen vermutlich schwer zu überblicken. Im Endeffekt haben Halterungen, Klemmen, Gehäuse oder eine der vielen anderen Vorrichtungen zum Zusammenhalt von Maschinen jedoch alle die gleiche Wichtigkeit – wenn man sie braucht, dann braucht man sie dringend. TPU 90A Powder gibt die Antwort auf ein Problem, dem zahlreiche Hersteller gegenüberstehen: ihre millionenschwere Fertigungstechnik vor zu viel Verschleiß zu bewahren.
Fertigungshilfen aus weichen Materialien können die Lebensdauer schwerer Maschinen verlängern, indem sie Stöße abdämpfen oder Greifer in der perfekten Form liefern. Treten an Dichtungen nach Jahren der kontinuierlichen Nutzung Risse auf, kann sofort ein Ersatz gedruckt werden, sodass die Fertigungsstraße innerhalb von Stunden wieder in Betrieb ist, statt dass tage- oder wochenlang auf ein Ersatzteil gewartet werden muss.
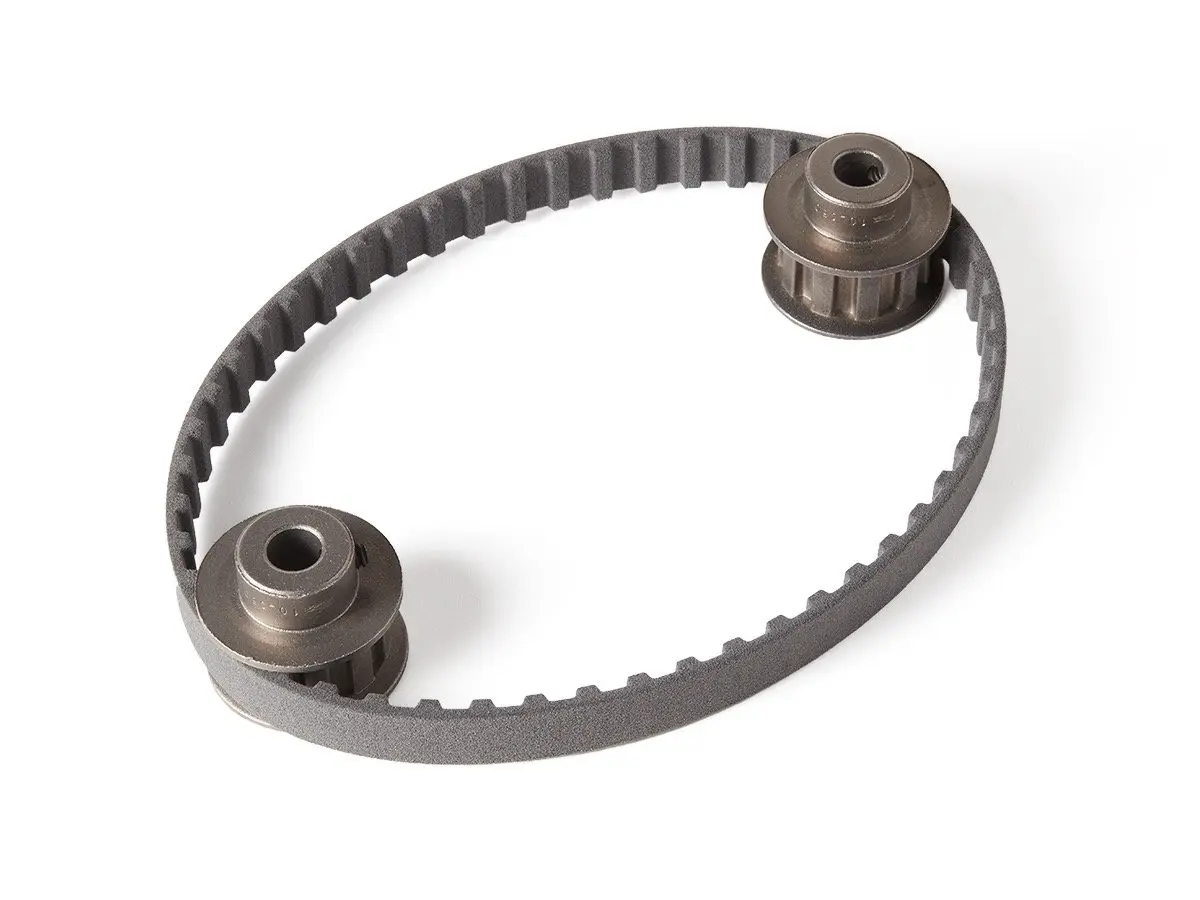
Steht ein TPU-Material zur Verfügung, können flexible Ersatzteile und Fertigungshilfen innerhalb eines Tages entworfen und gedruckt werden, sodass die Produktion niemals zum Stillstand kommen muss.
Zusätzliche Materialoptionen stellen für Hersteller eine Versicherung dar – sie bieten ihnen Schutz vor den Folgen unvorhergesehener Defekte von Bauteilen oder Geräten. Umso mehr verschiedene mechanische Eigenschaften betriebsintern erreichbar sind, desto mehr sichert sich ein Unternehmen gegen Verzögerungen in der Lieferkette und hohe Reparaturkosten des Erstausrüsters ab. Mit 3D-gedruckten Gummiteilen wird eine komplett neue Klasse von Bauteilen erschlossen, die repariert oder auf Abruf ersetzt werden können. Indem der Stillstand einer Fertigungsstraße oder eines Produktionsprozesses verhindert wird, sparen Unternehmen pro Tag Beträge im Tausenderbereich.
TPU 90A Powder kann für Schwingungsdämpfer in der Automobilbranche oder Luft- und Raumfahrt eingesetzt werden, oder auch für Haltevorrichtungen in industriellen Prozessen wie dem Thermoformen von Teilen mit einzigartigen Geometrien. In Automobilfabriken bedienen großangelegte Robotiksysteme Wandlaufkräne, die biegsam und schwenkbar sein müssen. Mithilfe maßangefertigter Polsterung und weichen Gehäusen kann die Reibung an diesen Systemen vermindert und somit ihre Lebensdauer verlängert werden.
Tragbare Produkte in kleinen Mengen oder Sonderausführungen
In den Branchen Sport, Mode und tragbare Technologien (Wearables) sind Personalisierungsoptionen unabdinglich, um den Marktanteil einer Marke zu erhöhen. Aufgrund der mit dem Werkzeugbau verbundenen Kosten war die Produktion von Sonderanfertigungen oder Kleinserien nahezu unvorstellbar, bevor der erschwingliche 3D-Druck das Hindernis aus dem Weg räumte. Für die Branche der Sportausrüstung oder Wearables waren die meisten bisher verfügbaren 3D-Druckmaterialien aber dennoch zu steif – bis TPU 90A Powder kam. Von Schuhsohlen, die genau an die individuelle Fußform und Gewichtsverteilung angepasst werden können, über für Stoßdämpfung entwickelte Football-Helme bis hin zu an das Handgelenk angepassten Uhrenarmbändern sind die Möglichkeiten endlos.
Die Hautverträglichkeit von TPU 90A Powder und der Arbeitsablauf mit der Fuse-Serie machen es erstmals möglich, individualisierte tragbare Produkte direkt durch 3D-Druck zu produzieren. Einige Luxusmarken für Uhren, Accessoires und Schuhe bieten zwar personalisierte Details wie Monogramme oder Wunschgrafiken an, doch die Individualisierung der eigentlichen Form von Produkten ist für Hersteller bisher unerschwinglich teuer gewesen. Dank des kostengünstigen Arbeitsprozesses mit der Fuse-Serie und der Hautverträglichkeit von TPU 90A Powder ist die Individualisierung in der Branche tragbarer Produkte jetzt Realität geworden.
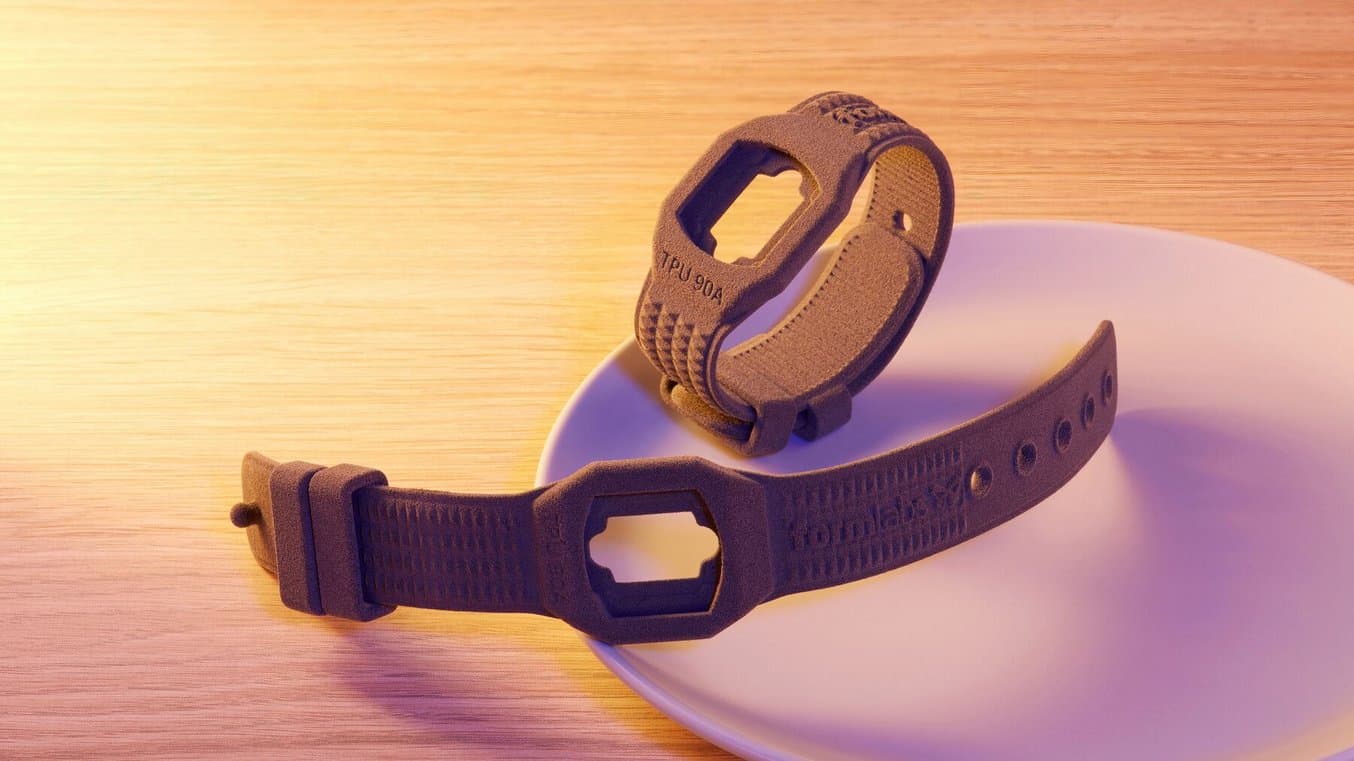
Die Fuse-Serie und TPU 90A Powder ermöglichen die betriebsinterne Produktion individualisierter Güter zu erschwinglichen Kosten und in einem effizienten Verfahren.
Medizinprodukte
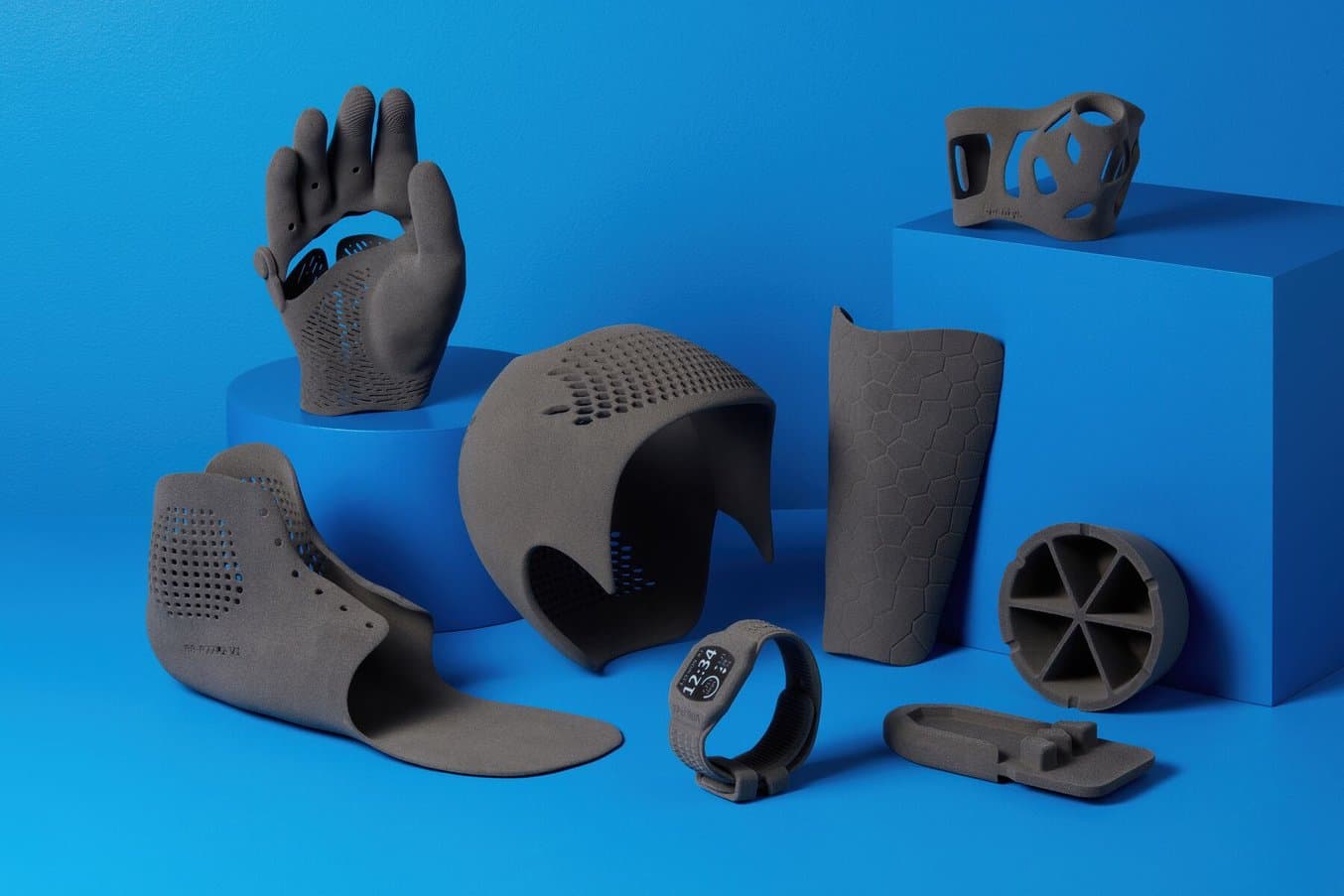
TPU 90A Powder kann auch zur Herstellung leistungsstarker Medizinprodukte eingesetzt werden. Hier abgebildet: Prothese (Modell: OT Supply GmbH), Daumenschiene (Modell: Spentys), orthetische Knöchelstütze (Modell: Spentys), Uhrenarmband und mehr.
Wir bei Formlabs Medical glauben, dass jeder medizinischen Einrichtung die neusten Hilfsmittel zur Verfügung stehen sollten, um die Versorgung zu verbessern und höchsten Patientenkomfort zu gewährleisten. TPU 90A Powder ist der nächste Schritt zur Verwirklichung dieser Vision. Es ergänzt unsere branchenführende Materialpalette von SLS-Pulvern und bietet einen echten Mehrwert bei der Nutzung der 3D-Drucker der Fuse-Serie.
Dank seiner überragenden Haltbarkeit und Zähigkeit ist TPU 90A Powder ideal für Prothesen, Orthesen, patientenspezifische Geräte und andere Medizinprodukte geeignet. Das Material eröffnet völlig neue Möglichkeiten in der Gesundheitsbranche, indem es die hohe Reißfestigkeit und Bruchdehnung von Gummimaterialien mit der Gestaltungsfreiheit und Widerstandsfähigkeit des SLS-3D-Drucks vereint.
TPU 90A Powder ist ein flexibles Elastomer und damit ideal für den 3D-Druck folgender medizinischer Teile:
-
Prototypen von Medizinprodukten, Medizinprodukte für die Endverwendung und deren Komponenten
-
Orthetische Polster und Prothesenauskleidungen
-
Wearables, Dichtungen, Dämpfer und Schläuche
-
Schienen, Schädel-Orthesen
-
Sporteinlegesohlen und Korrektureinlagen
Wie andere SLS-Materialien auch stellt TPU 90A Powder für medizinisches Fachpersonal die kosteneffizienteste Lösung zur hausinternen Produktion dar. Von Schuhsohlen, die genau an die individuelle Fußform und Gewichtsverteilung angepasst werden können, über für Stoßdämpfung entwickelte Football-Helme bis hin zu an das Handgelenk angepassten Uhrenarmbändern sind die Möglichkeiten endlos.
TPU 90A Powder ist für kurzzeitigen Hautkontakt zertifiziert und kann als sicher für das Tragen auf der Haut betrachtet werden. Da das Material jedoch nicht für andere biokompatible Anwendungen getestet wurde, liegt es in der Verantwortung des Herstellers, die Eignung der Druckteile für ihren Verwendungszweck zu überprüfen.
Wie Sie TPU 90A Powder in Ihre Fertigung integrieren
TPU 90A Powder lässt sich ganz einfach in den Arbeitsablauf mit den Druckern der Fuse-Serie und dem Fuse Sift integrieren. Das Material kann in Umgebungsluft gedruckt werden und erfordert keine Inertgaszufuhr. Des Weiteren nutzen TPU-Drucke keine Surface Armor (die halbgesinterte Hülle um Druckteile aus Pulvern mit höherer Steifigkeit), was den Prozess der Pulverentfernung vereinfacht. Trotz des Fehlens von Surface Armor bei Teilen aus TPU 90A Powder wird das Sandstrahlen dennoch empfohlen, um überschüssiges Pulver vollständig von den Teilen zu entfernen und ein sauberes, leichter zu bearbeitendes Material zu erhalten.
Es ist durchaus möglich, mit Ihrem bestehenden Fuse-Drucker auf TPU 90A Powder umzusteigen; wir empfehlen jedoch die Nutzung eines eigens dafür vorbehaltenen Druckers sowie eines eigenen Fuse Sift und einer separaten Konstruktionskammer.
Brandneue Möglichkeiten mit TPU 90A Powder
Ob Sie ein kleines Unternehmen sind, dass noch vor der Markteinführung seines ersten Produktes steht, oder ein Großunternehmen, das sich vor dem Lieferkettenchaos der letzten Jahre absichern möchte: Durch die Implementierung leistungsstarken 3D-Drucks im eigenen Betrieb senken Sie Kosten und stabilisieren Ihr Geschäft. Ein Material wie TPU 90A Powder steigert diese Vorteile noch, indem es neue Anwendungsbereiche und sogar völlig neue Geschäftsmodelle eröffnet. Teile mit weicher Haptik, die zuvor nur durch Massenproduktion zuverlässig herstellbar waren, können jetzt durchgehend auf einem erschwinglichen Gerät 3D-gedruckt werden.
Materialvielfalt ist der Schlüssel zur Erschließung neuer Wege und zur Neukonzipierung der Möglichkeiten in Design und Fertigung. TPU-Teile sind in unserer Welt allgegenwärtig, und indem wir ihre bewährte Leistung mit dem effizienten SLS-Arbeitsprozess der Fuse-Serie vereinen, ebnen wir den Weg für Innovationen in jeder Branche.