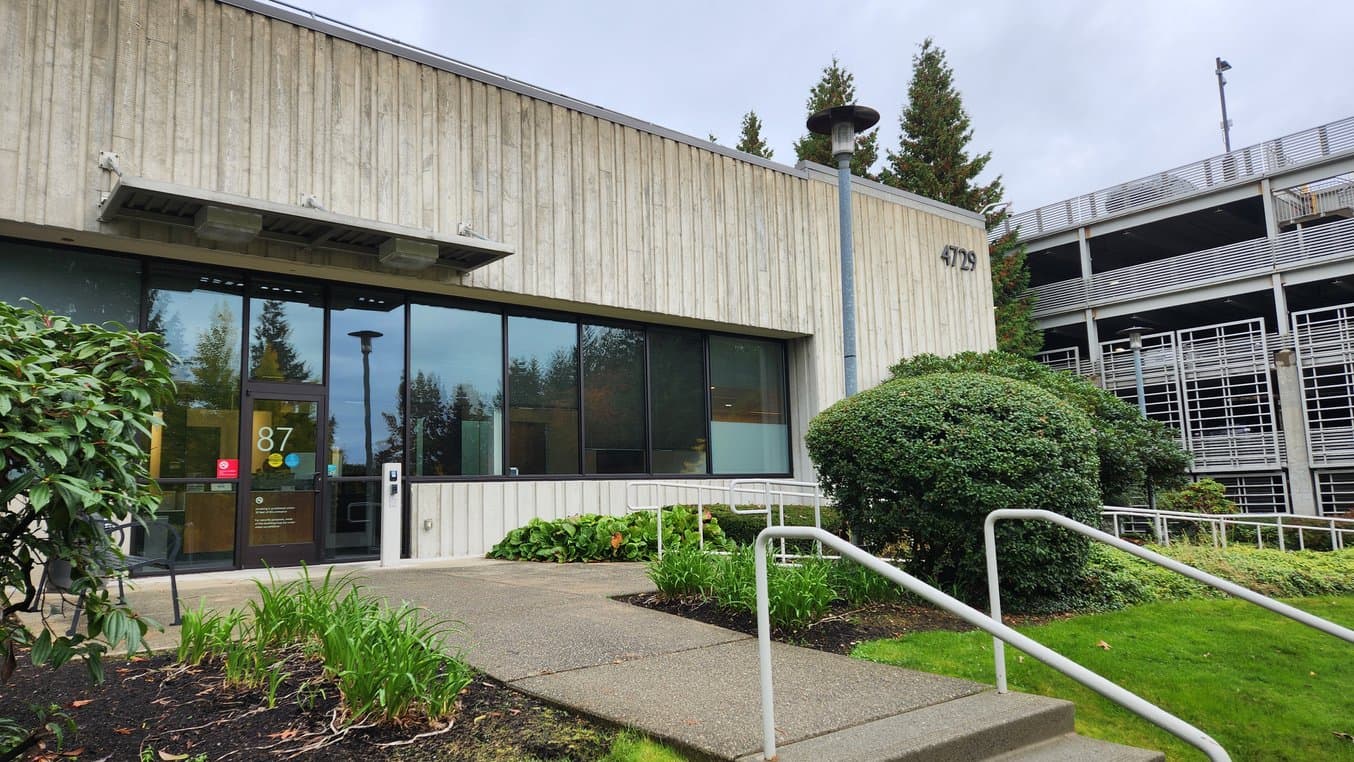
Es gibt viele Gründe, warum Microsoft als einer der Vorreiter der Technologiebranche sowohl für Hardware als auch Software so lange an der Spitze bleiben konnte. In einer derart dynamischen Branche ganz vorne dabei zu sein erfordert kompromisslose Schnelligkeit, ein Engagement für die besten Ideen und die Entschlossenheit, die Messlatte für jedes einzelne Bauteil hoch zu legen.
Seit acht Jahren leitet Mark Honschke das Rapid Prototyping im Advanced Prototyping Center (APC) von Microsoft, wo 95 % der Hardwareprodukte des Tech-Giganten entworfen, getestet oder entwickelt werden. Das APC bleibt Microsofts Streben nach Schnelligkeit treu – wie Honschke es beschreibt, ähnelt die Arbeit einem „Marathonlauf im Sprinttempo“. Sein Team bearbeitet Anfragen aus über 80 Hardware-Kategorien und mehreren Teams innerhalb dieser Kategorien, hält dabei aber stets eine Durchlaufzeit von 24 Stunden ein.
Durch die Ergänzung seiner Flotte um einen Form 4 und Form 4L kann Honschke mehr Druckaufträge umsetzen, sodass einige Drucke statt über Nacht nun tagsüber gedruckt werden, um die Iteration zu beschleunigen und die Produktivität zu steigern. Zusätzlich zu den Desktop- und Benchtop-Stereolithografie-Druckern (SLA) von Formlabs betreibt das APC auch zwei Drucker der Fuse-Serie für selektives Lasersintern (SLS), um funktionale Nylonteile in Endproduktqualität herzustellen.
„Der Form 4 ist unsere erste Wahl für Projekte, die enge Toleranzen und industrietaugliche Materialien erfordern. Er produziert hochleistungsfähige Teile in beeindruckend kurzer Druckzeit und erlaubt es unseren Modellbauern, innerhalb von 24 Stunden gleich mehrere Iterationen zu fertigen.“
Mark Honschke, Leiter der additiven Prototypenfertigung im Advanced Prototyping Center von Microsoft
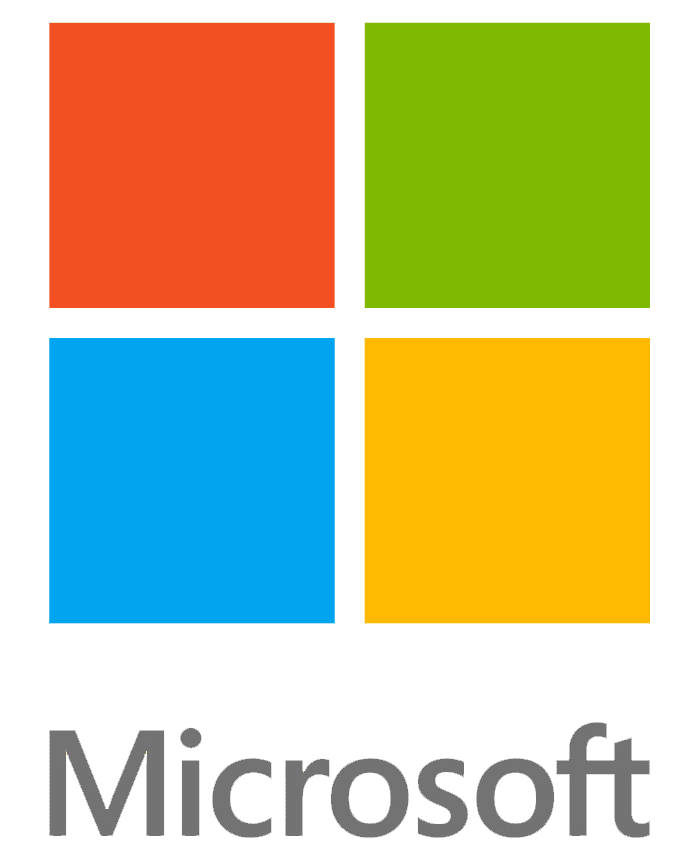
Ein Blick hinter die Kulissen von Microsofts Advanced Prototyping Center: Prototypen aus dem 3D-Drucker
Dieses Gespräch mit Fragerunde liefert Ihnen einen exklusiven Einblick in die Funktionsweise des APC als Fertigungsdienstleister: ein zentraler Knotenpunkt, der als interner Produktionsservice für die Hardware-Teams von Microsoft dient.
Wie sich Formlabs' 3D-Drucker bei Microsoft einfügen
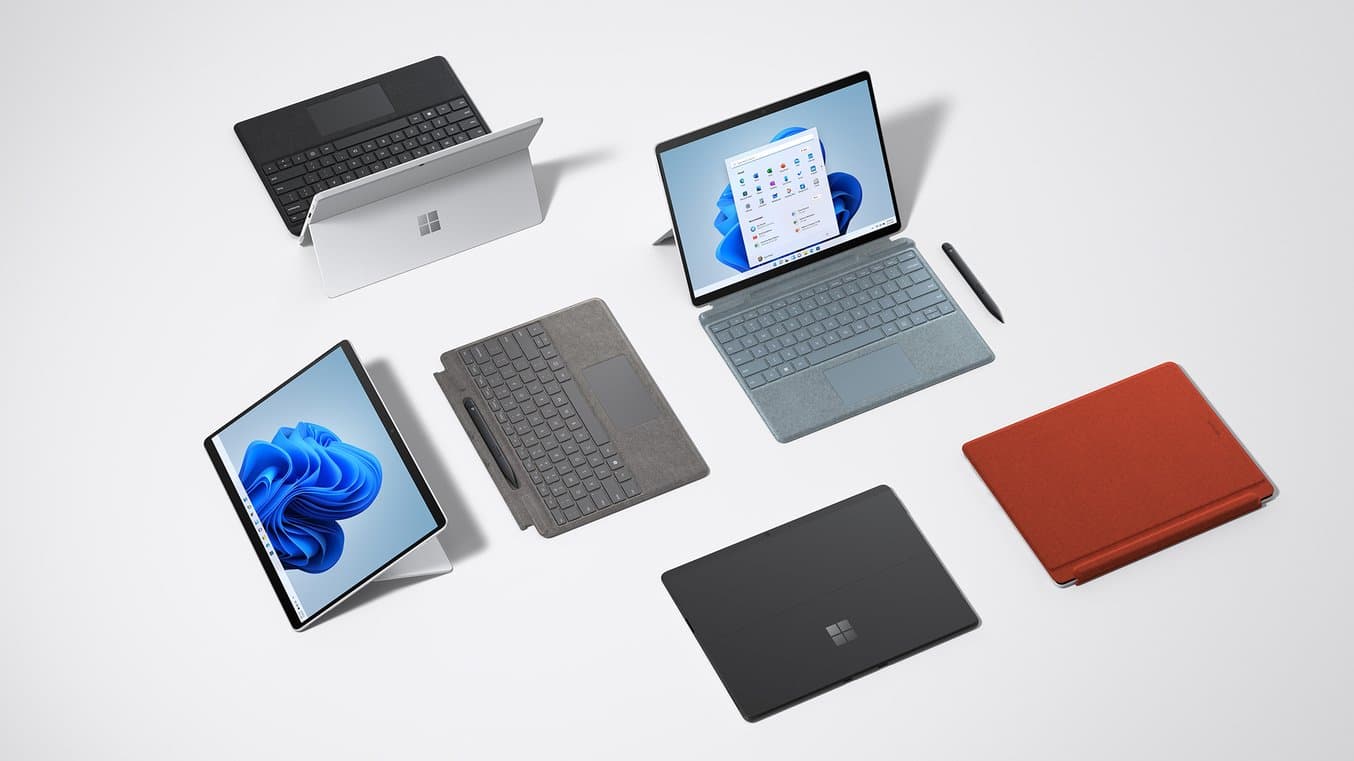
Mithilfe von Formlabs-3D-Druckern hat das APC Anfragen nach Baugruppen für Konzeptnachweise (Proof of Concept oder POC) von Surface-Tablets umgesetzt.
Im APC sind gleich mehrere Drucker Tag und Nacht in Betrieb. Bei 80 Produktkategorien und zahlreichen Projekten innerhalb dieser Kategorien kann das Team nie wissen, was für Anfragen der Tag bringen wird – was jedoch konstant bleibt, ist ihre Menge. Um den ständigen Strom von Anfragen zu bewältigen, verfügt das APC über mehrere FDM-Drucker (Fused Deposition Modeling bzw. Schmelzschichtung), zwei Formlabs-Drucker vom Typ Fuse 1+ 30W für selektives Lasersintern (SLS), sieben PolyJet-Farbdrucker und fünf SLA-3D-Drucker von Formlabs, darunter der Form 4 und Form 4L.
Honschkes Team arbeitet als interner Fertigungsdienstleister: Das Team entscheidet selbst, welches Material und welches Gerät für ein Projekt am besten geeignet sind, und stimmt dies mit dem Auftraggeber ab, bevor das Teil eingerichtet, gedruckt, nachbearbeitet und ausgeliefert wird – alles innerhalb von 24 Stunden.
Dieser Ansatz ist zwar unglaublich schnell, doch für eine Gruppe innerhalb von Microsoft war er dennoch nicht schnell genug: für die Architekten. „Die Architekten stehen zwischen den Designern und den Ingenieuren. Sie erhalten Informationen vom Designteam und erstellen eine Skizze, dann entwickeln sie Prototypen, bis die Designer mit dem Produkterlebnis zufrieden sind. Danach geben sie den Prototyp an die Ingenieure weiter, damit diese das Produkt herstellen können“, erklärt Honschke. „Sie arbeiten auf einer uneingeschränkt kreativen Ebene, und nicht immer nach demselben Zeitplan.“
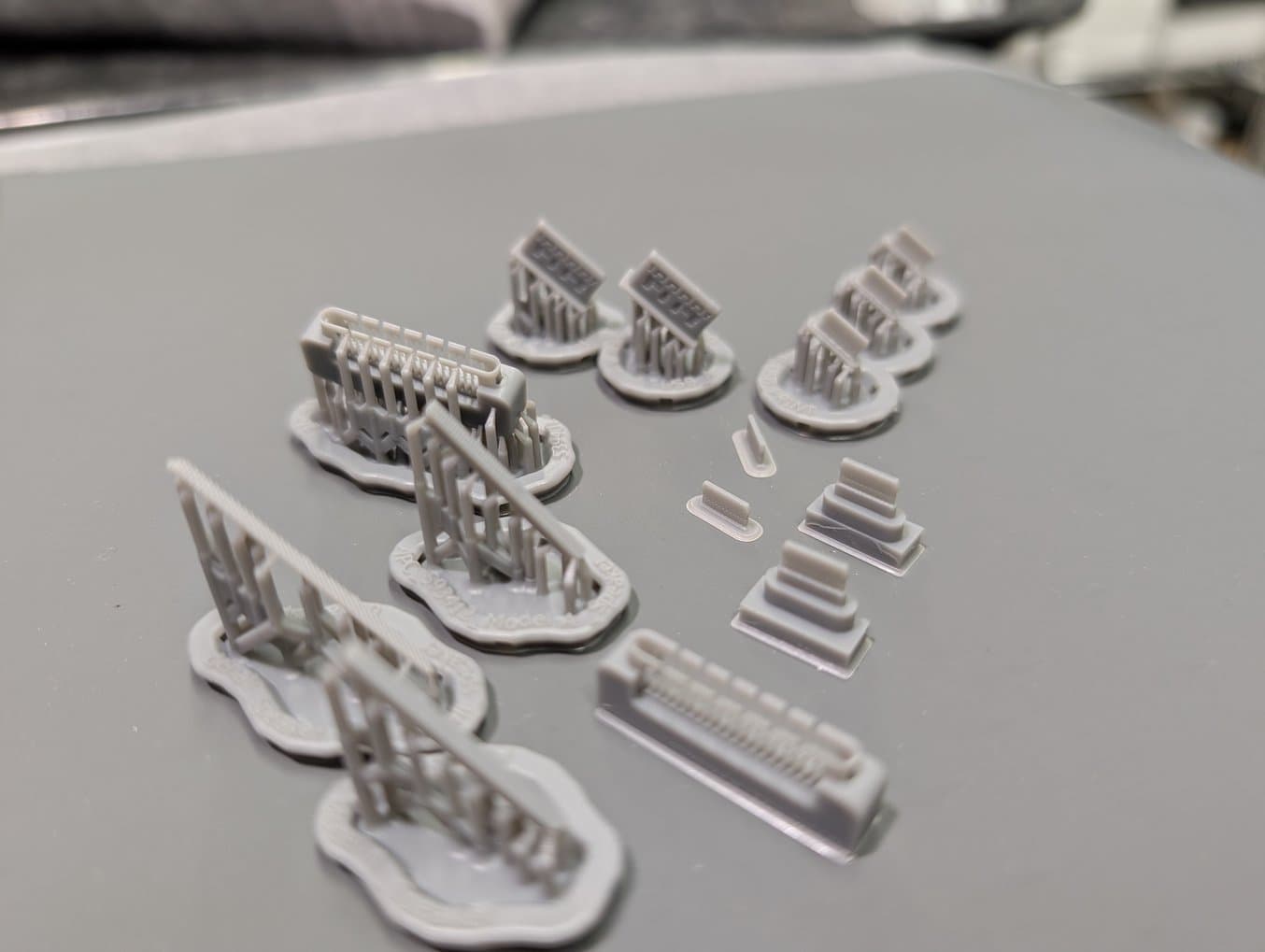
Der SLA-3D-Druck ist ideal für das Prototyping von Teilen, die eine hohe Genauigkeit erfordern, wie diese Verbinder.
Das APC benötigte zusätzliche Druckkapazitäten, die einfach zu bedienen, erschwinglich und schnell waren und qualitativ hochwertige Teile aus einer Reihe von Materialien liefern konnten. Ein Architekt, der Formlabs von einem früheren Arbeitsplatz kannte, schlug den Form 3 vor, der schon sehr bald um einen Form 3L, Fuse 1+ 30W, Form 4 und jetzt den Form 4L ergänzt wurde.
„Meiner Meinung nach ist die Formlabs-Technologie für uns ein unabdingliches Werkzeug. Ein großer Teil meiner Arbeit besteht darin, die Druckerflotte mit den bei uns eingehenden Anfragen zu vergleichen, Lücken in unseren Kapazitäten zu finden und dann die richtige Technologie zu ermitteln, um diese Lücken zu schließen. Formlabs erfüllt für uns eine ganz bestimmte Aufgabe. Es geht nicht um allgemeine 3D-Drucke, obwohl Formlabs darin sehr gut ist. Wir brauchen es wegen seiner technischen Materialien mit hoher Auflösung und einer hochwertigen Oberflächenqualität.“
Mark Honschke, Leiter der additiven Prototypenfertigung im Advanced Prototyping Center von Microsoft
Die Vielfalt der Materialien und die Bandbreite der mechanischen Eigenschaften, die über das Formlabs-Ecosystem verfügbar sind, bieten dem Team für jeden Auftrag das richtige Kunstharz. Da die schnellen Druckzeiten des Form 4 und Form 4L es Honschkes Team erlauben, sogar mehrmals am Tag problemlos zwischen Materialien zu wechseln, kann das Team stets das beste Material für jeden Auftrag auswählen – anstatt aus praktischen Gründen schlicht dabei zu bleiben, was bereits im Drucker eingerichtet ist.
„Tough 2000 Resin ist unser wichtigstes Material. Grey Pro Resin und Tough 2000 Resin bieten eine technische Festigkeit bei sehr hoher Auflösung, die wir mit kaum einer anderen Technologie erreichen“, berichtet Honschke.
Die Erweiterung des Microsoft APC durch den Form 4
Im APC nimmt Honschke bis etwa 16 Uhr Anfragen entgegen, bevor er die Drucker über Nacht in Betrieb nimmt. Am Morgen, nachdem die Druckteile entnommen, nachbearbeitet und ausgeliefert wurden, sucht das Team unter den neuen Aufträgen nach Teilen, die tagsüber fertiggestellt werden können. Ein Präzisionsdrucker, der ein Teil statt über Nacht schon innerhalb des Tages druckt, stellt damit eine immense Produktivitätssteigerung dar.
„Ein Teil habe ich auf dem Form 3+ in 8 Stunden und 19 Minuten gedruckt. Beim Form 4 waren es rund zwei Stunden. Dadurch können wir diese Drucker jetzt für die Tagesproduktion nutzen, vor allem dank ihrer Geschwindigkeit. Der Form 3+ war für uns keine Technologie für die Tagesproduktion“, lässt Honschke uns wissen.
Für ein Labor mit einem derart großen Durchsatz wie dem des APC – Hunderte von Teilen pro Woche – ist es eine große Hilfe, Drucke am Tag abzuwickeln, statt über Nacht darauf zu warten, und es sorgt für effiziente Prozesse bei Microsoft. Bei manchen Druckteilen handelt es sich um erste Designideen für neue Produkte, bei denen der Geistesblitz bis zum nächsten Morgen verflogen wäre. Bei anderen geht es um Werksreparaturen und Neuentwürfe, die Produktionsausfälle verhindern oder Zeit und Geld im Montageprozess sparen können.
„Das Ziel unseres Labors ist es, innerhalb von 24 Stunden mehrere Iterationen durchführen zu können. Wir bekommen Anfragen von überall, und einige davon sind sehr zeitabhängig. Beispielsweise müssen sie ermitteln, warum ein bestimmtes Teil versagt, damit sie ans Werk weitergeben können, welche geometrische Änderung das Problem löst“, beschreibt Honschke.
Seit der Anschaffung des Form 4 druckt das Team mehrmals am Tag und konnte sofort einige Kapazitäten von anderen SLA-Druckern umstellen. „Schon innerhalb von Minuten nach dem Einschalten des Geräts waren wir am Drucken. Die Einrichtung war selbsterklärend. Die neue Wischerkonstruktion und der neue Verriegelungsmechanismus für die Harztanks gefallen uns sehr gut“, lobt Honschke.
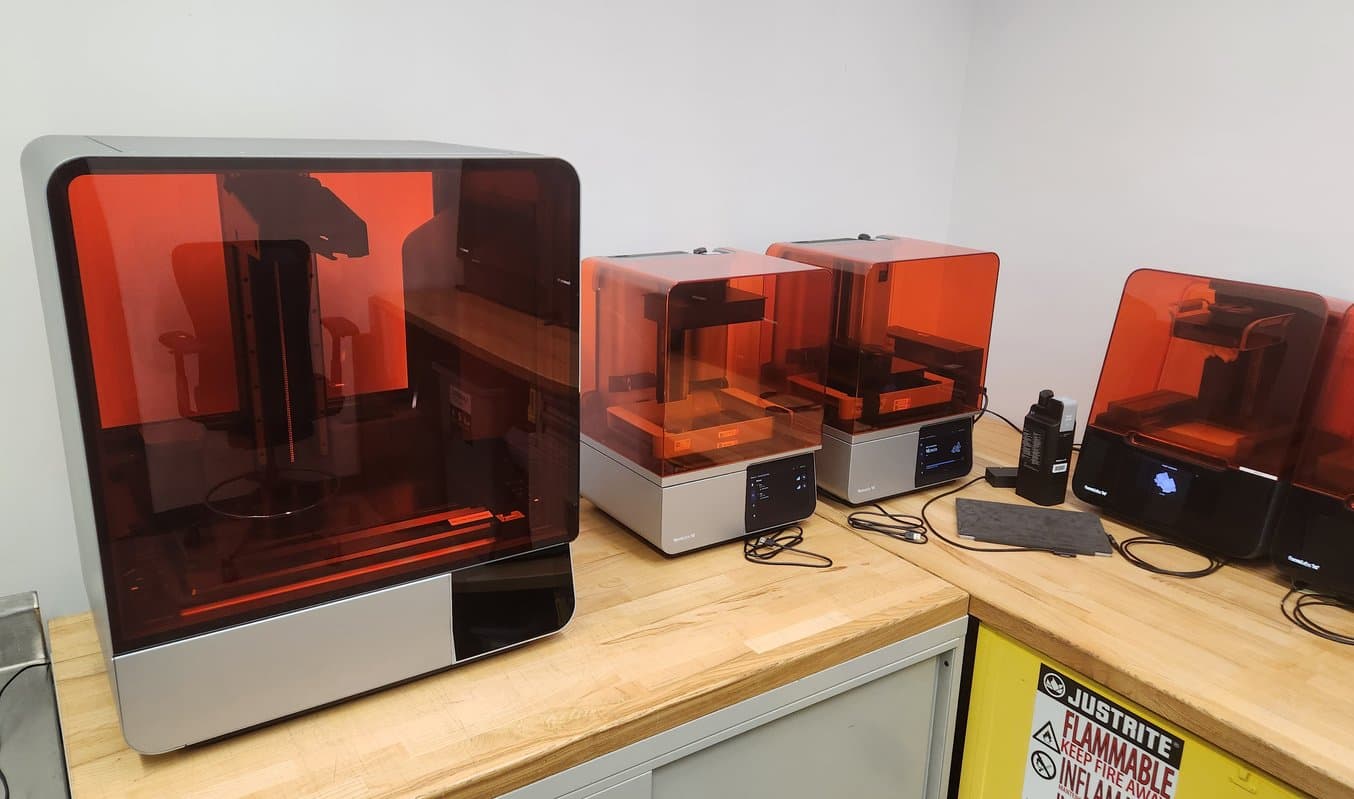
Das APC hat fünf Kunstharz-3D-Drucker von Formlabs im Einsatz, darunter zwei Form 4 und ein Form 4L.
Geschwindigkeit und Benutzerfreundlichkeit sind für einen erfolgreichen Druck jedoch nicht alles. Die Oberflächenbeschaffenheit und die Druckqualität sind nach wie vor enorm wichtig – viele der Teile werden später zur endgültigen Designfreigabe oder als Muster verwendet und müssen entsprechend aussehen.
„Bei einigen kleinen Teilen habe ich festgestellt, dass die Oberflächenqualität besser ist als bei früheren Druckern. Für transparente Teile verwenden wir Formlabs, weil man dort weniger Schichtbrechung hat und ein wirklich klares Teil erhält – ich sage immer, näher kommt man beim SLA-Druck nicht an komplett transparente Teile heran“, erzählt Honschke.
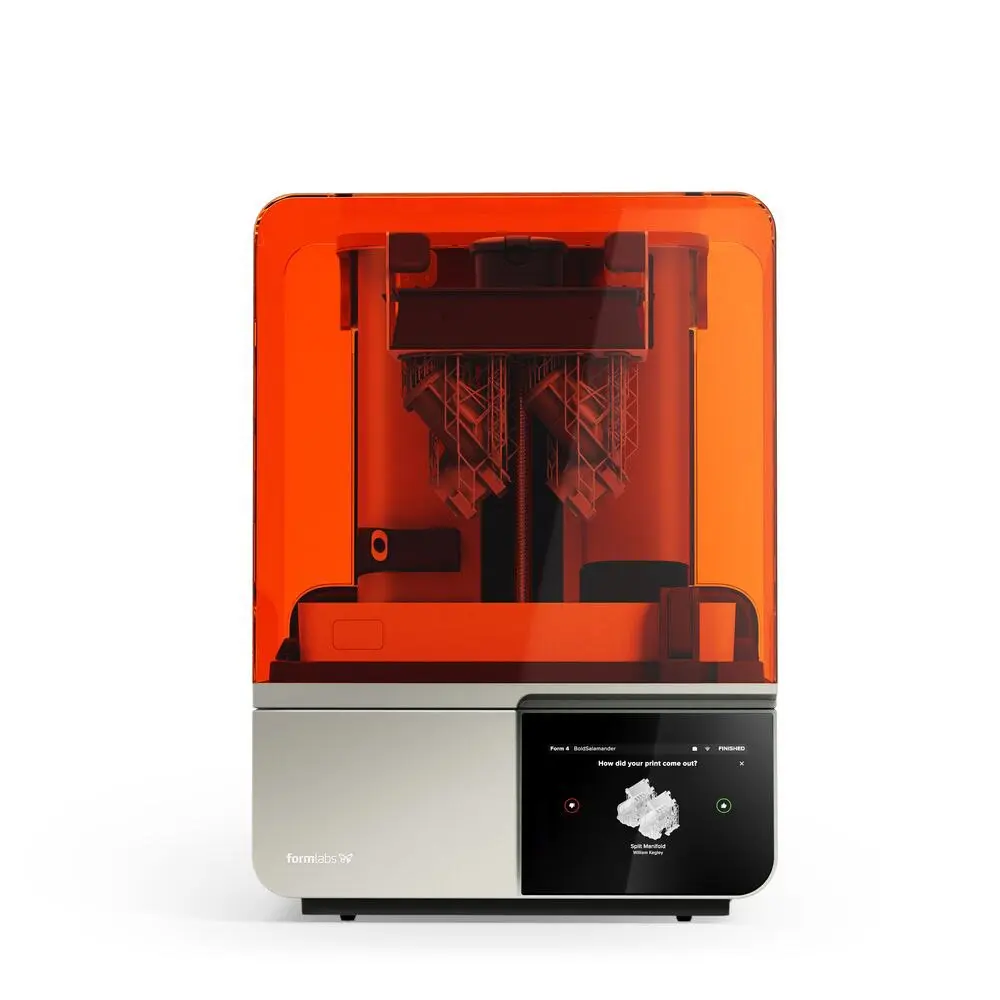
Produktdemo: Form 4
Entdecken Sie, wie der Form 4 neue Maßstäbe der Produktivität und Innovation setzt, dank beispielloser Schnelligkeit, Genauigkeit und Zuverlässigkeit.
Form 4L: Erhöhung des Formfaktors beim APC
Seitdem das APC seine Flotte um den Form 4L erweitert hat, konnten Honschke und sein Kollege Ryan Laprise mehr Aufträge annehmen und den Durchsatz des Zentrums erhöhen.
Vor kurzem benötigte ein Mitarbeiter ein Tablet-Gehäuse, das das Fertigungsvolumen des Form 4 überstieg, allerdings schon bald gebraucht wurde. „Vor dem Form 4L konnten wir so etwas nicht drucken, die Durchlaufzeit hätte zu lange gedauert, weshalb 3D-Druck ausgeschlossen gewesen wäre. Das hätte den Iterationsprozess verlangsamt“, so Honschke. Das 3D-Druck-Team sendete die Prototypen an den Form 4L und stellte die Teile noch am selben Nachmittag bereit. „Mit nur vier Stunden ist das für uns eine Revolution“, so Honschke.
Aber die Druckzeit ist nicht alles – auch die Vor- und Nachbearbeitungszeit kann sich auf die Produktivität und Effizienz eines Teams auswirken. Der Form 4L hat den Arbeitsablauf des Kunstharz-3D-Drucks für das APC vereinfacht und sowohl die Vorbereitungsarbeiten als auch die Fertigstellung verkürzt, damit Teile noch schneller vom Konzept zur Lieferung gelangen.
Dank des Bauvolumens des Form 4L gehört das Zerteilen von Modellen der Vergangenheit an, und das Team ist in der Lage, tagsüber schnelle Teile sowie über Nacht größere Stückzahlen zu produzieren. Die Nachbearbeitungszeit hat sich dank kleinerer Berührungspunkte bei den Stützstrukturen ebenfalls verkürzt.
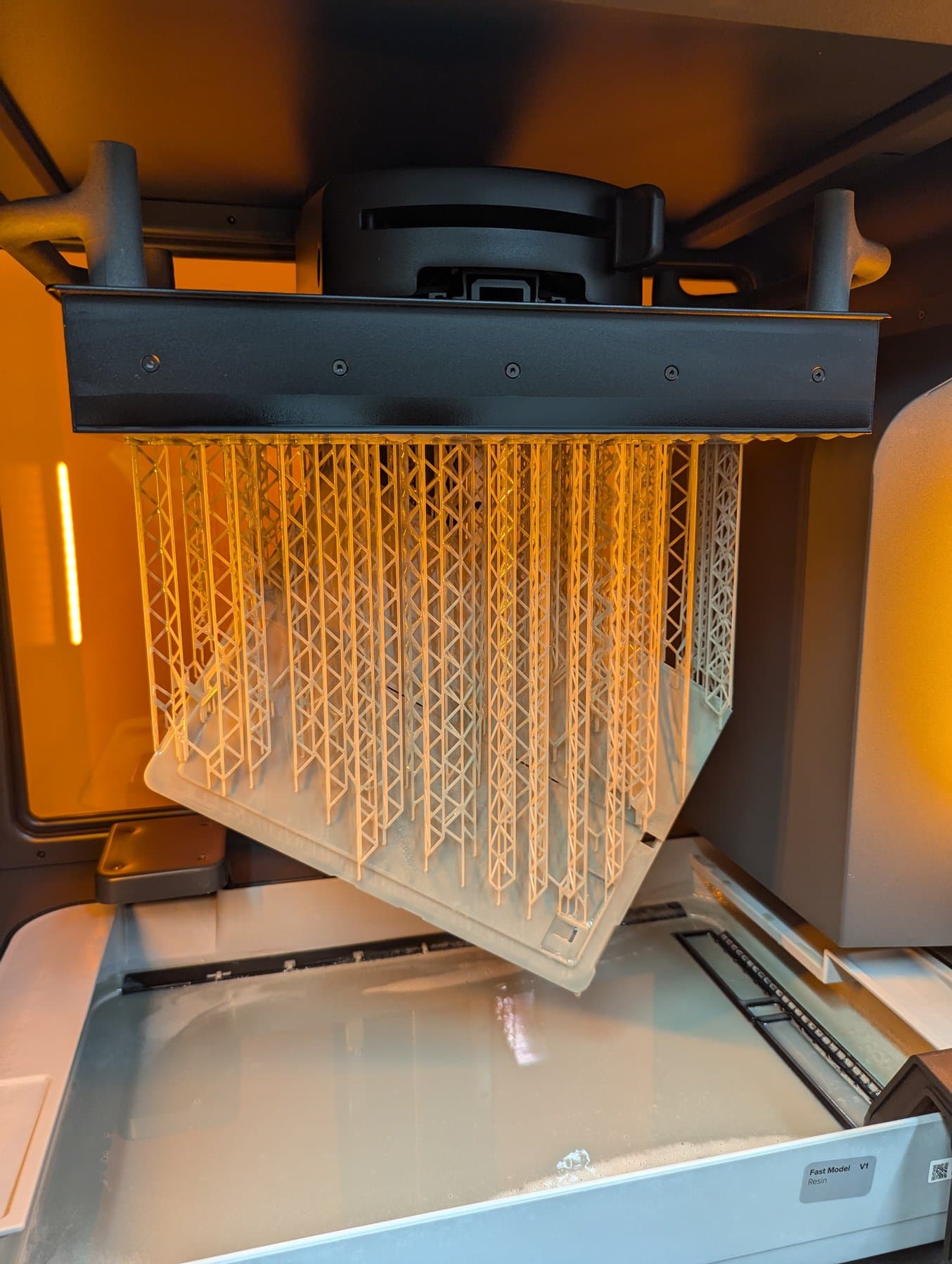
Das große Fertigungsvolumen des Form 4L erlaubt es dem Team, Prototypen einer größeren Bandbreite von Bauteilen aus Microsofts Produktpalette zu erstellen.
Das APC erhält häufig Anfragen nach Baugruppen für Konzeptnachweis-Prototypen (Proof of Concept), die von Xbox über Surface-Tablets bis hin zu Headsets und mehr reichen. Da die Bauteile aber nicht zur gleichen Zeit gefertigt werden, muss der 3D-Druck einspringen. „Sie bekommen die Leiterplatinen vielleicht in einer Woche, aber erst drei Wochen später die Midframes. Und wir müssen Probleme lösen wie zum Beispiel, dass die Leiterplatine einen halben Millimeter zu dick ist und wir den Gehäusedeckel nicht schließen können. Wenn wir also solche Teile fertigen, sind es nicht nur ein, zwei Stück, sondern 50 bis 100 Teile“, berichtet Honschke.
Vor kurzem wurde ein Konzeptnachweis für 50 Xbox-Midframes angefordert, da es Probleme mit dem Outsourcing einiger interner Bauteile gab. „Ich sagte: 'Ja, wir können euch die 50 Teile liefern, aber wir können sie nicht reinigen.' Aber mit dem Form 4L war das eigentlich kein Problem, weil sich die Stützstrukturen so viel leichter ablösen lassen.“
„Wir konnten drei komplette Druckaufträge in drei Tagen statt in anderthalb Wochen durchführen. Der Form 4L hat sich also schon allein durch dieses Projekt bezahlt gemacht.“
Mark Honschke, Leiter der additiven Prototypenfertigung im Advanced Prototyping Center von Microsoft
Gemeinsam haben Form 4 und Form 4L dem APC einen ganz neuen Weg geebnet – wenn das Team hochwertige Teile in so kurzer Zeit bereitstellen kann, ist es in der Lage, mehr große Konzeptnachweise betriebsintern umzusetzen. „Xbox macht ein bis zwei Konzeptnachweise pro Jahr, Surface zwei bis drei, und wenn wir diese Dienstleistung betriebsintern anbieten können, ist das einerseits sicherheitstechnisch besser und andererseits können wir Probleme auch schneller erkennen, wenn wir schneller arbeiten. Meiner Meinung nach bieten Form 4 und Form 4L gute Geschäftsmöglichkeiten. Ich denke, es wird sich sogar lohnen, Personal einzustellen, um sie zu betreiben“, meint Honschke.
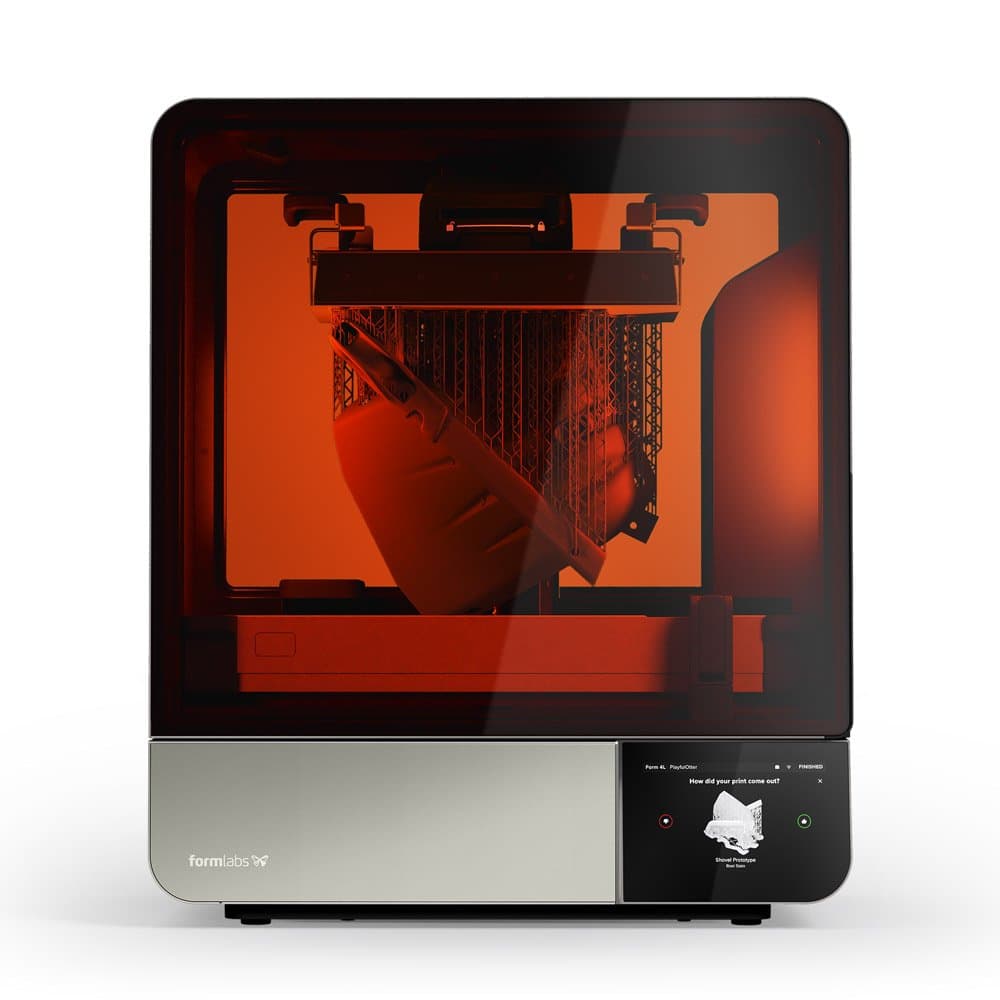
Produktdemo: Form 4L
Entdecken Sie, wie der neue Form 4L, unser großformatiger Kunstharz-3D-Drucker der nächsten Generation, die Schnelligkeit, Genauigkeit und Zuverlässigkeit des Form 4 in einem völlig neuen Maßstab eröffnet.
Wie die Fuse-Serie reibungslos Funktionsteile liefert
Obwohl die Schnelligkeit des Form 4 und Form 4L Honschkes Team dazu verholfen hat, seinen Durchsatz zu erhöhen und Anfragen nach großformatigen Prototypen umzusetzen, greifen sie auf andere Technologien zurück, wenn Endproduktfunktionalität und robuste, funktionale Prototypen gefragt sind.
Mit dem wachsendem Produktportfolio unter dem Dach von Microsoft musste das APC sich anpassen. Eine Möglichkeit, mit der steigenden Zahl von Anfragen aus neuen Produktkategorien Schritt zu halten, ist das Hinzufügen von Technologien speziell für bestimmte Anwendungen. „Als Microsoft seine Produktkategorien erweiterte, stellten wir fest, dass es eine Nachfrage nach hochauflösenden Prototypen gab, die auch dem Praxisgebrauch standhielten, von Kopfhörerbändern bis hin zu Controller-Gehäusen. Für solche Prototypen war SLS die beste Option“, meint Honschke.
SLS-3D-Drucker und andere Drucktechnologien für Pulverbettfusion, wie etwa MJF, kommen beim funktionalen Prototyping häufig zum Einsatz. Sie liefern Produkte mit hoher Maßgenauigkeit, die aber auch Belastungen standhalten wie Biegen, Dehnen, Draufsetzen oder das Hineinstopfen in eine Tragetasche. Als das APC nach dem richtigen Pulverdrucker für seine Flotte suchte, fiel die Wahl auf die Fuse-Serie, die durch ihren geringen Platzbedarf und ihre Benutzerfreundlichkeit überzeugte.
„Die meisten Standard-SLS-Systeme benötigen viel Platz, verursachen hohe Installationskosten und sind im Allgemeinen sehr schmutzig im Betrieb. Neben der kompakten Bauweise des Druckers ist das benutzerorientierte System von Formlabs darauf ausgelegt, die Nachteile standardmäßiger SLS-Systeme zu beseitigen, und mit den laufenden Verbesserungen ist die Herstellung von SLS-Teilen so reibungslos wie möglich.“
Mark Honschke, Leiter der additiven Prototypenfertigung im Advanced Prototyping Center von Microsoft
Mithilfe der Fuse-Serie konnten die Entwicklungsteams Produkte durch die letzten Genehmigungsphasen bringen, bevor sie in die Massenproduktion gehen. Bei den meisten Microsoft-Produkten kann es sein, dass die Einzelteile der komplexen, mehrteiligen Baugruppen an verschiedenen Standorten hergestellt werden, was die Fertigung eines endgültigen, kompletten Konzeptnachweises erschwert. Muss man sich auf die Zeitpläne von Logistikunternehmen und Teams aus aller Welt verlassen, dann kommt es vor, dass die Bauteile nicht zugleich eintreffen – selbst wenn die Genehmigungsfrist kurz bevorsteht. Mit der Fuse-Serie können Teams endgültige Konzeptnachweise erstellen, die das Endprodukt simulieren, damit mögliche Problemquellen analysiert und schnelle Änderungen vorgenommen werden können, bevor das Produktionswerkzeug bestellt wird.
„Die manuelle Montage eines vollständigen Teilesatzes hilft den Ingenieuren, Passform- und Montageprobleme zu erkennen, die die Produktion verzögern könnten. Aufgrund von Verzögerungen bei der Fertigung oder Lieferproblemen ist es oft schwierig, alle Teile für einen Proof of Concept zum richtigen Zeitpunkt zu beschaffen. Da kommt der Fuse gerade richtig. Mit ihm können wir Teile erstellen, die konventionell hergestellte Teile simulieren“, erläutert Honschke.
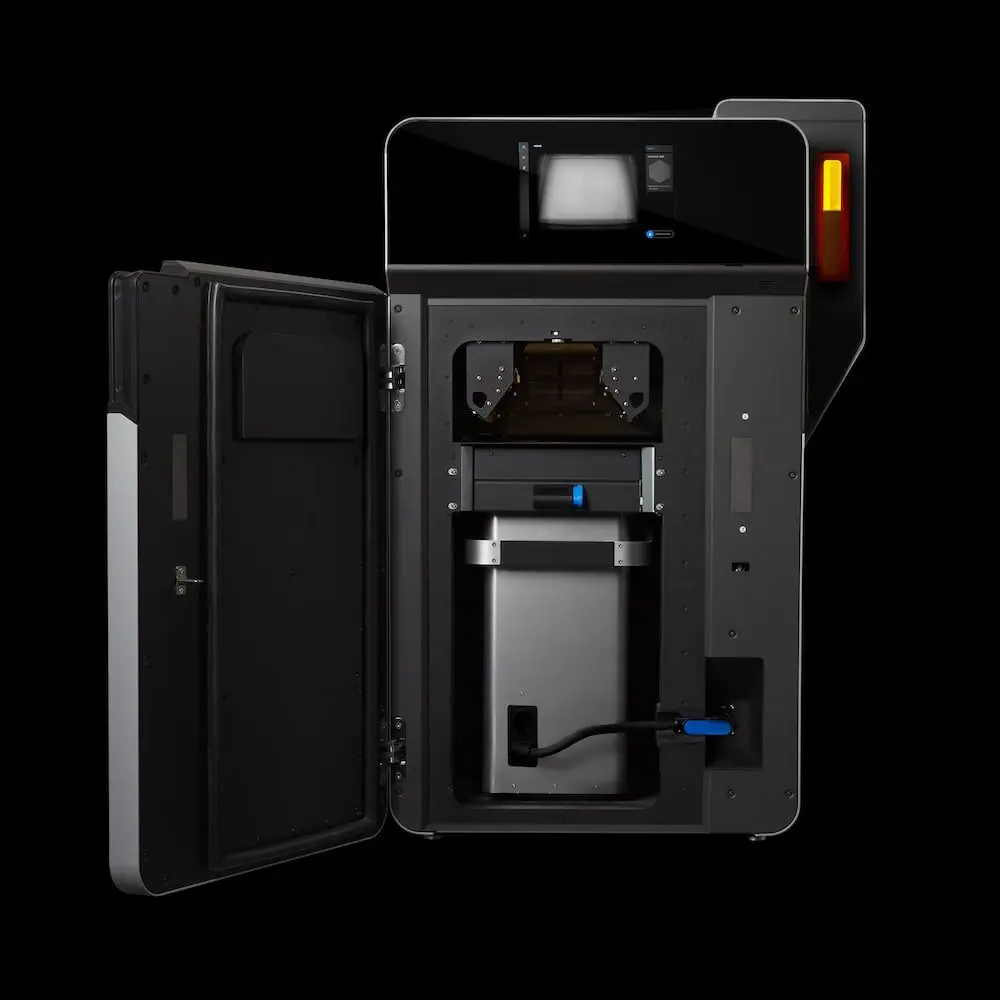
Rekordschnelle Produktion leistungsstarker SLS-Teile mit dem neuen Fuse 1+ 30W
Sehen Sie sich unsere Produktvorführung an und lassen Sie sich den Fuse 1+ 30W und den SLS-3D-Druck durch einen Formlabs-Experten erklären.
Stetige Optimierung bei Formlabs
Ein großer Teil von Honschkes Arbeit besteht darin, dafür zu sorgen, dass das APC die richtigen Werkzeuge für die vielfältigen, sich ständig ändernden Anfragen und Projekte zur Verfügung hat. Die Skalierung mit Formlabs, sowohl bei der SLA- als auch der SLS-Technologie, hat dem Team geholfen, in kürzerer Zeit auf mehr Anfragen zu reagieren.
Die technologischen Fortschritte des Form 4 und Form 4L haben es Microsoft möglich gemacht, pro Tag mehr zu schaffen, und mit der Fuse-Serie entschärft das Team etwaige Schwierigkeiten in der Lieferkette, bevor die Endproduktion anläuft. Für ein Unternehmen, das einen Marathon im Sprinttempo läuft – und das seit Jahrzehnten an der Spitze der Technologiebranche –, bedeuten die Geschwindigkeit und Zuverlässigkeit dieser Drucker eine Erleichterung.
„Alle unsere Drucke waren sehr erfolgreich, und seit wir den Form 4L in Betrieb genommen haben, drucken wir fast nur noch damit. Ich denke, das entspricht dem, was man von einem Drucker der nächsten Generation erwartet. Wenn wir unsere Drucker austauschen, werden wir auf mehr Form 4 und Form 4L umsteigen“, so Honschkes Pläne.
Wenn Sie sich selbst von der Qualität des SLA- oder SLS-3D-Drucks überzeugen möchten, fordern Sie ein kostenloses 3D-gedrucktes Probeteil an. Um mehr über den Arbeitsprozess von Microsoft zu erfahren, sehen Sie sich unser auf Abruf verfügbares Webinar an.