Die Herstellung von gendersensiblen und individualisierten Designs mit dem Fuse 1
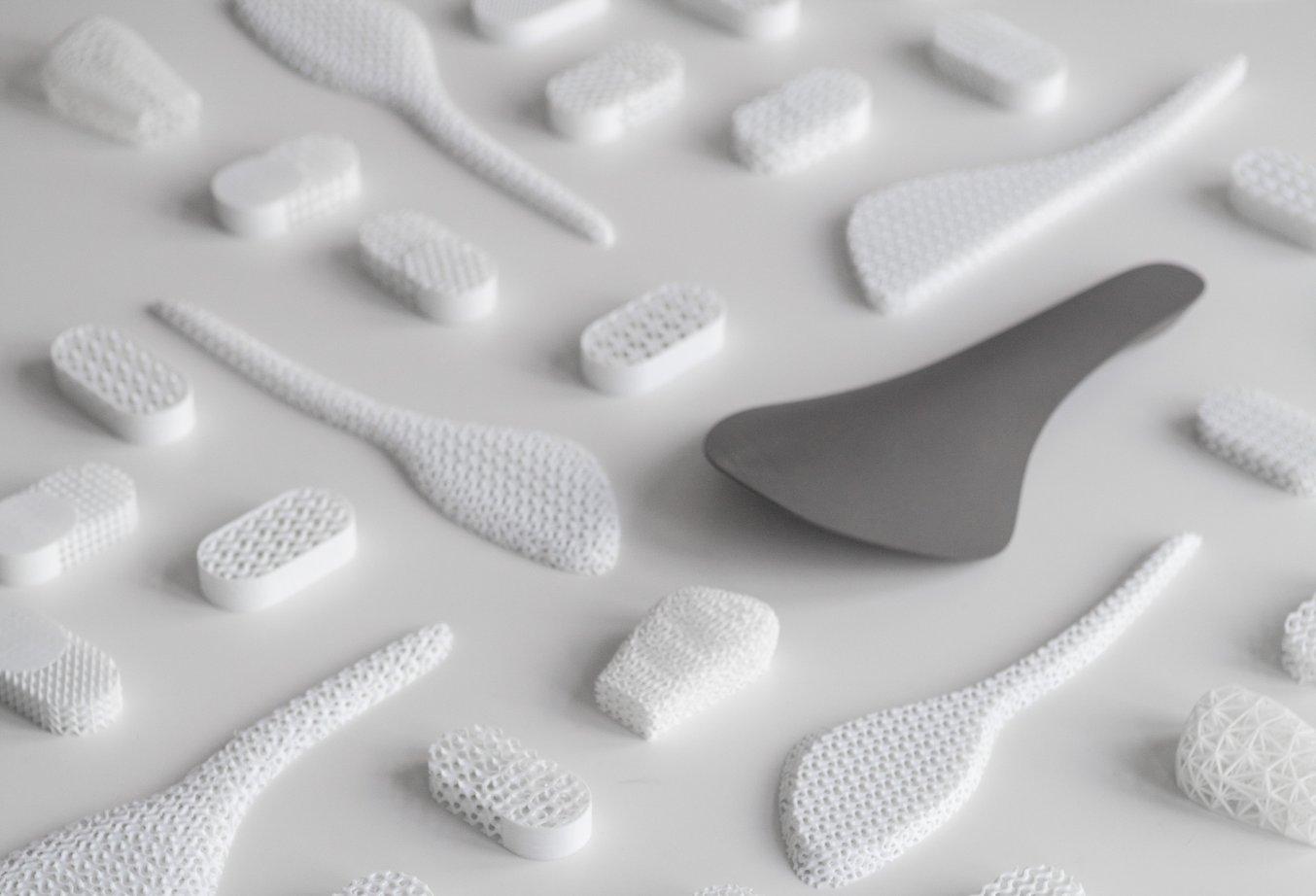
In den letzten Jahren gab es in verschiedenen Bereichen der Wirtschaft immer wieder Bestrebungen, geschlechtsspezifische Normen zu überwinden. Dennoch gibt es nach wie vor starke Unterschiede zwischen - der gesellschaftlichen Auffassung von - männlich und weiblich. Einer der Bereiche, in denen dies immer noch stark zu spüren ist, sind ergonomische Produkte - diese folgen oftmals geschlechtlichen Stereotypen. Dabei können insbesondere moderne Technologien wie der 3D-Druck bei der Gestaltung von auf den Einzelnen zugeschnittenen Produkten von Nutzen sein.
Auch Industriedesign Student Tim Schütze hat dies erkannt. Im Rahmen seiner Bachelorarbeit, hat er sich daher auf die Förderung von Gleichberechtigung und Vielfalt durch gender-sensitives Design fokussiert. Das Ergebnis ist ein mit teils selektivem Lasersintern (SLS) gedruckter gendersensitiver Fahrradsattel.
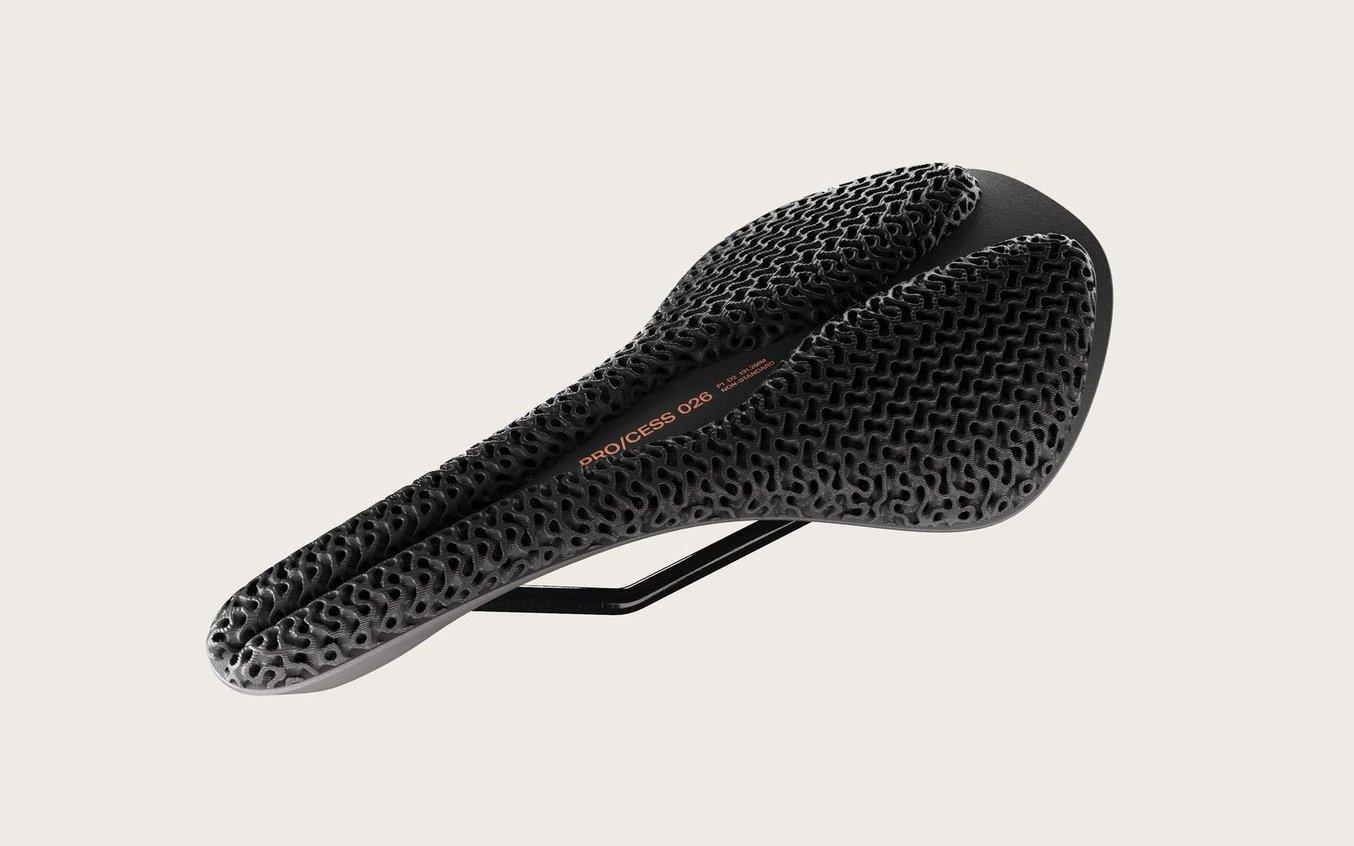
Für seine Bachelorarbeit spezialisierte sich Industriedesign-Student Tim Schütze auf die Herstellung von geschlechtersensiblen und individualisierten Designs - das Ergebnis ist ein geschlechtersensibler Fahrradsattel, der teilweise mit selektivem Lasersintern (SLS) gedruckt wurde.
"Ich wollte etwas kreieren, hinter dem ich voll und ganz stehe", erzählt Tim über seine Themenwahl. Somit wollte er für seine designtheoretische Studie mit praktischer Ausarbeitung zum einen die aktuelle Thematik der Gleichberechtigung und Vielfalt der gender-sensitiver Designs aufgreifen. Ein Thema, dem er sich auch außerhalb seines Studiums aktiv widmet: "Ich habe gemerkt, dass es unglaublich große Schwierigkeiten, Probleme und Unzugänglichkeiten im geschlechtersensiblen Design gibt - aber gleichzeitig auch ein großes Potenzial". In Kombination mit seiner Leidenschaft für den Radsport war das Thema seiner Bachelorarbeit somit entschieden.
“Der Bereich der Fahrradsättel ist extrem symptomatisch für geschlechterspezifische Annahmen - nämlich, dass sich männliche und weibliche Anatomie in genau zwei Kategorien unterscheiden lassen. Das ist ein falsches Vorurteil, das sich dringend ändern muss.”
- Tim Schütze, Industriedesign Student
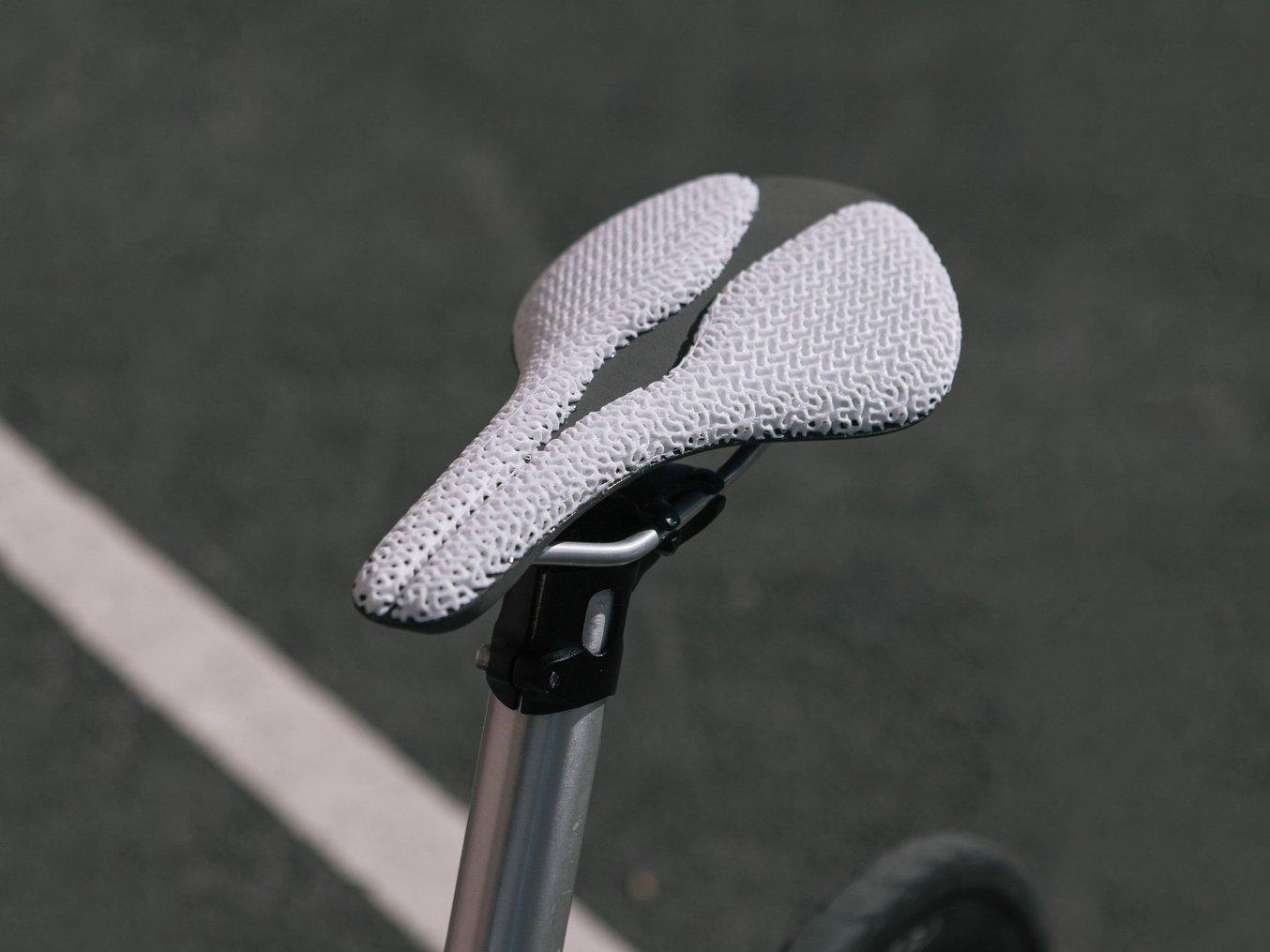
Gerade der Bereich der Fahrradsättel ist laut Tim Schütze äußerst symptomatisch für geschlechtsspezifische Annahmen und wird dem Individuum häufig nicht gerecht.
Der Bedarf nach gendersensitiven Designs
Die Konzeption und Gestaltung ergonomischer Produkte beruht häufig auf Normen, nach denen sie entworfen werden. So sind beispielsweise Produkte für männlich-gelesene Personen oft dynamisch, schwer und auf Leistung ausgelegt - Varianten für weibliche-gelesene Personen hingegen oftmals eine abgeschwächte Version dessen.
Das Problem, so Tim Schütze, beginnt mit der Konzeption und Gestaltung von Produkten nach "Normen". Wer von Normen spreche, gehe von einer konstanten Komponente aus, und genau das haben Körperformen nicht, erklärt er weiter. "Selbst wenn man zum Beispiel 100.000 Menschen zusammennimmt und nach weiblich und männlich gelesenen Personen unterscheidet, kann man natürlich gewisse Trends abbilden. Jedoch sagt das noch nichts über das Individuum aus. Es wird immer Menschen geben, die stark von diesen Trends abweichen und nicht für das Produktdesign geeignet sind".
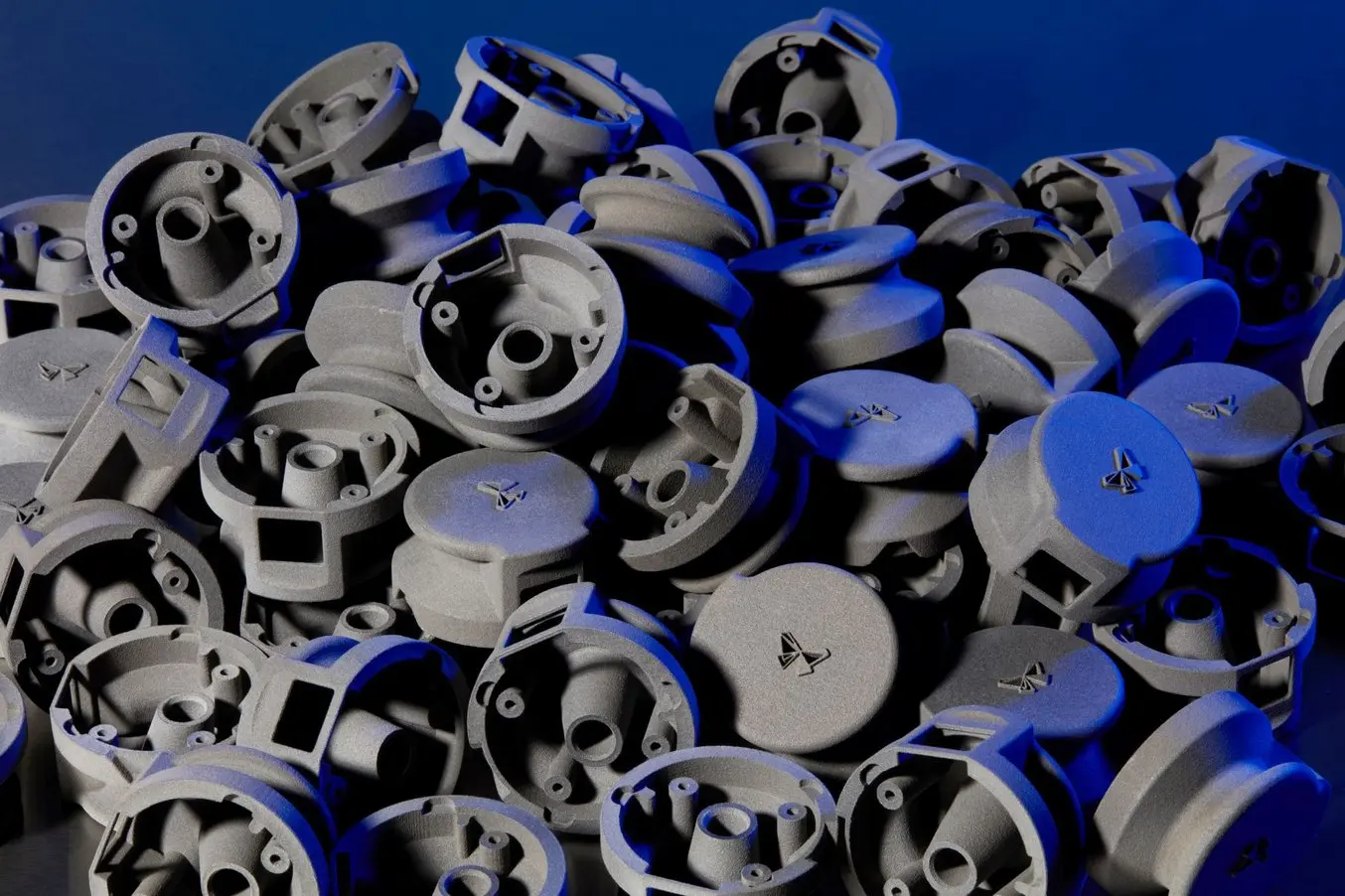
Fuse 1 SLS Design-Leitfaden
Erfolg beim selektivem Lasersintern (SLS) beginnt mit Teilen, die für das SLS-3D-Druckverfahren optimiert sind. Dieser Leitfaden behandelt die wichtigen Abmessungen und Designüberlegungen, die bei der Konstruktion von Teilen für den Fuse 1 zu beachten sind.
Von der Idee zum Prozess
Unter dem Leitsatz "Wir brauchen keine Produkte, wir brauchen Prozesse", begann die Umsetzung seiner Arbeit. "Mir war es von Anfang an wichtig, dass am Ende des Projektes nicht ein Sattel, sondern ein Prozess herauskommt" erklärt Tim Schütze seine Vision. Der Einsatz moderner Technologien wie das Auslesen personalisierter Daten, die Erstellung von Designs basierend auf Algorithmen sowie der Einsatz von 3D-Druck sollten dies ermöglichen.
Um den Prozess zu starten und seine Konzeptgrundlage zu überprüfen, wurden in einem ersten Schritt ergonomische Daten und Präferenzen von Freiwilligen gesammelt. Die etwa 30 Teilnehmer*innen druckten ein Druckmuster aus, setzten sich gemäß der Anweisungen darauf und fotografierten es in den vorgegebenen Winkeln.
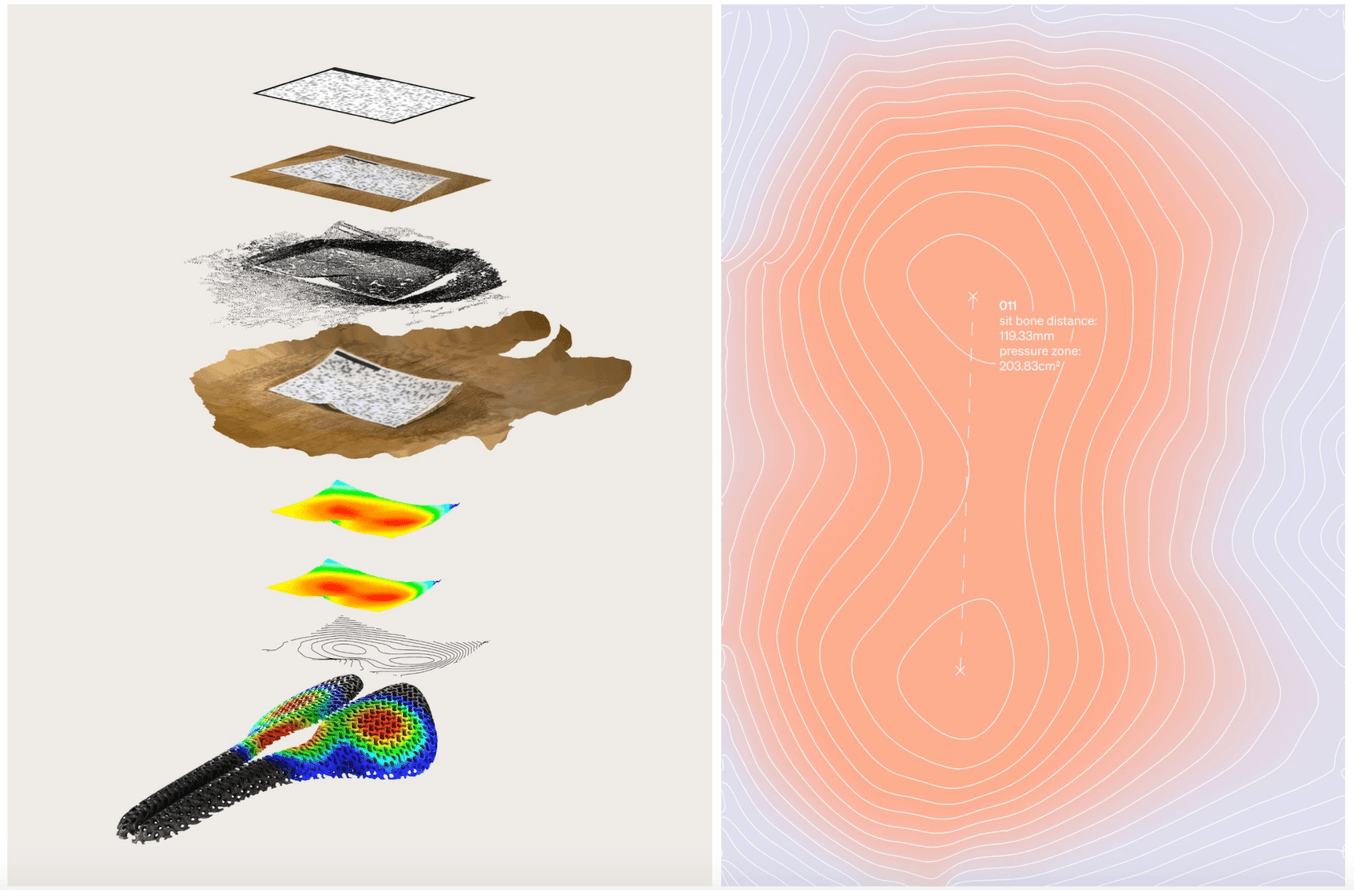
Mit dem Bilderkennungsverfahren structure-for-motion werden dreidimensionale Abdrücke erstellt, die Auskunft über Abstände zwischen den Sitzknochen und die Ausdehnung von Druckstellen der einzelnen Personen geben und als Grundlage dienen.
Unter Anwendung des Bilderkennungsverfahrens Structure for Motion wurden die zweidimensionalen Bilder in eine dreidimensionale sogenannte Punktwolke umgewandelt - eine Sammlung von Messpunkten, die ein dreidimensionales Abbild des Abdrucks ergaben. Diese lieferten Aufschluss über Kriterien wie die Abstände zwischen den Sitzhöckern und der Ausdehnung von Druckstellen der einzelnen Personen und diente als Grundlage für das später zu erstellende Modell.
"Die Datenerhebung diente auch als Proof of Concept - schon bei dieser relativ kleinen Stichprobe habe ich gemerkt, dass sich einfach kein Trend erkennen lässt und dass der Bedarf an Individualisierung da ist"
- Tim Schütze, Industriedesign Student

Der zu erstellende Fahrradsattel besteht jeweils aus zwei 3D-gedruckten Auflagen, einer aus Nylon 12 gedruckten Basis und einer Rail.
Für die Ausführung in seiner Bachelorarbeit fertigte Tim Schütze zunächst drei verschiedene Modelle an, die alle aus einem 3D-gedruckten Polster sowie einer Basis und einer Rail bestehen.
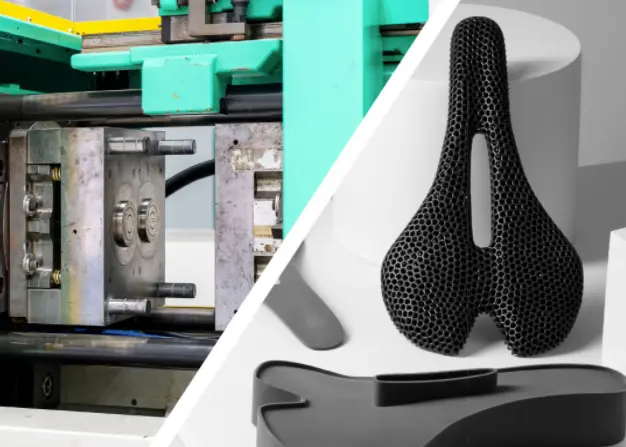
SLS-3D-Druck oder Spritzguss: Wann sollte man Spritzgussteile durch 3D-Druck ersetzen?
In diesem Whitepaper werden der Spritzguss und seine Vor- und Nachteile erörtert sowie der SLS-3D-Druck und die Anwendungen vorgestellt, bei denen er als ergänzende Technologie eingesetzt werden kann.
3D-Druck als Technologie für Personalisierung
Dass der 3D-Druck Teil seines Prozesses sein wird, war für Tim Schütze von Anfang an klar "Ich wollte selbst Hand anlegen und meine Arbeit durch den Prozess begleiten" erklärt er.
"Der 3D-Druck ist meiner Meinung nach als Technologie der Zukunft nicht mehr wegzudenken und ermöglicht im Vergleich zu anderen Herstellungsmethoden eine sehr große Zugänglichkeit"
- Tim Schütze, Industriedesign Student
Zu Beginn seiner Arbeit mit dem 3D-Druck setzte der Industriedesign-Student zunächst einen FDM-Drucker ein. Aufgrund der kostengünstigen und schnellen Produktion mit FDM sowie der erforderlichen Elastizität der Auflagen, werden diese auch heute noch mit Shore 72A Hart-TPU gedruckt. Bei der Basis des Sattels stieß FDM als Herstellungsverfahren jedoch schnell an seine Grenzen. "Die Qualität und Zuverlässigkeit des Drucks, die Stützstrukturen und Handhabung sowie die Materialeigenschaften passen einfach nicht zur Anwendung." erklärt er.
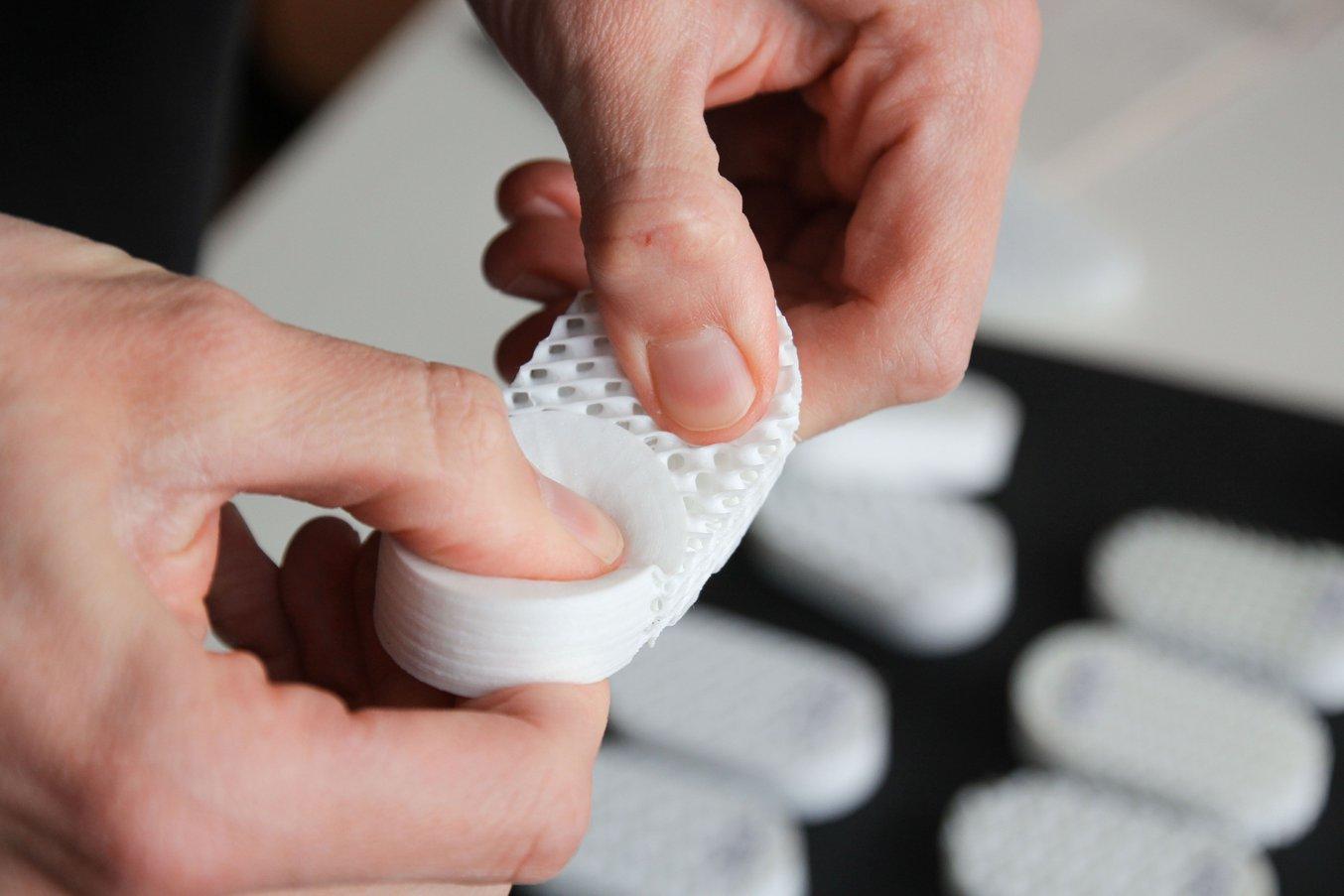
Die Auflagen für den Sattel wurden aufgrund der erforderlichen Elastizität sowie der kostengünstigen und schnellen Produktion mit FDM hergestellt.
Auf der Suche nach neuen Möglichkeiten zur Herstellung der Basis wandte sich Tim Schütze an das Formlabs-Team in Berlin und bat um Unterstützung. "Ich war super happy, dass ich eine so positive Resonanz bekommen habe", sagt er.
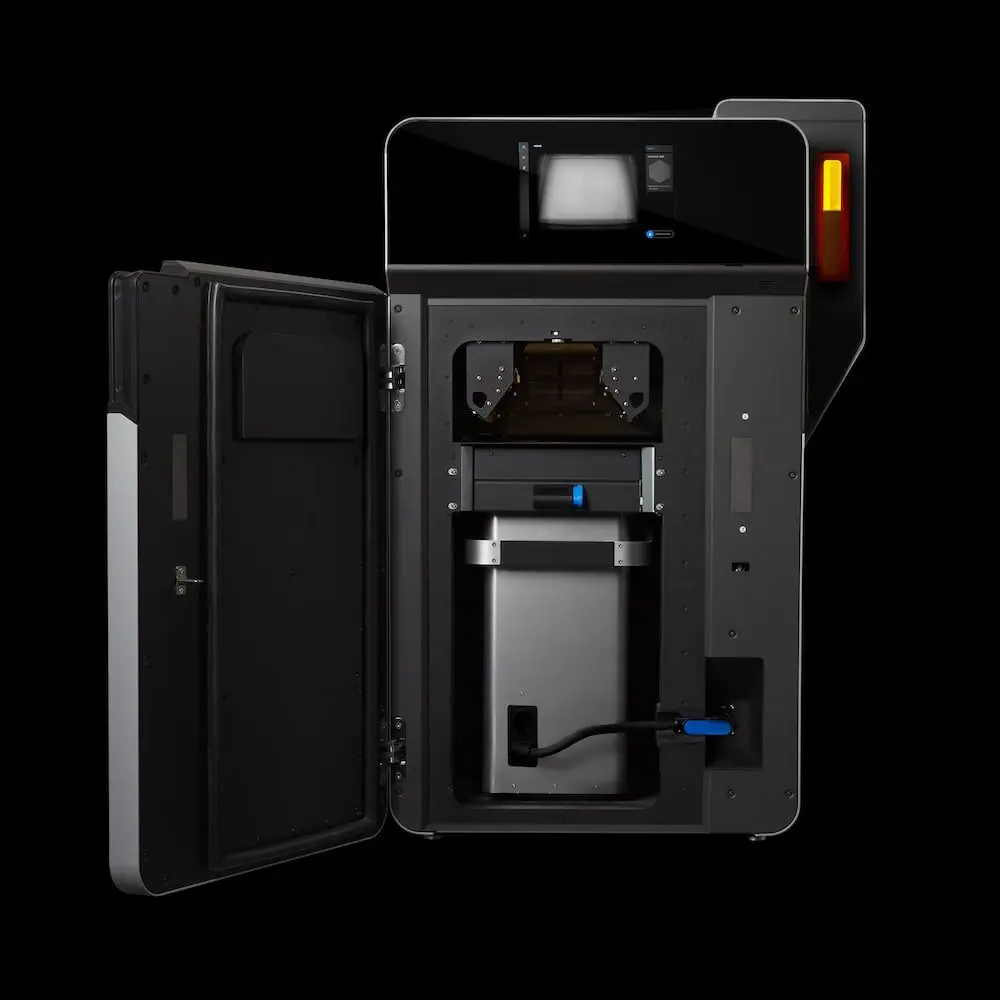
Produktvorführung des Fuse 1
Sehen Sie sich unsere Produktvorführung an und lassen Sie sich von unserem Experten durch die Vielseitigkeit des Fuse 1 und SLS 3D-Drucks führen.
Aufgrund der benötigten Belastbarkeit und Qualität entschieden sich das Engineering-Team von Formlabs und Tim Schütze gemeinsam für den 3D-Druck mit selektivem Lasersintern. Nach einem Rundgang durch das Berliner Büro durfte er dann seine frisch gedruckten Modelle selbst aus dem Fuse 1 nehmen und begutachten “Gleich die ersten Ergebnisse waren wirklich erstaunlich.” erinnert Tim Schütze sich.

Die Basis wurde mit Hilfe des Fuse 1 und Nylon 12 gedruckt, welches sich durch seine hohe Zugfestigkeit, Dehnbarkeit und Stabilität auszeichnet, die der Sattel benötigt.
Als Material kam Nylon 12 Powder zum Einsatz, das sich durch seine hohe Zugfestigkeit, Dehnbarkeit und Stabilität auszeichnet und sich ideal für die Herstellung von Endverbrauchsteilen eignet - davon konnte sich Tim Schütze auch gleich selbst überzeugen: "Ich bin den SLS-gedruckten Sattel mehrere Wochen lang selbst gefahren, mit der Akzeptanz, dass er kaputt gehen könnte - aber alles hat wunderbar funktioniert. Das hat mich wirklich beeindruckt."
Nach fünf intensiven Monaten, zahlreichen Datensätzen und Prototypen war der Prozess im Mai vorerst abgeschlossen. Das Ergebnis - drei individualisierte Modelle, gedruckt auf dem Fuse 1 und bereit für den Einsatz.
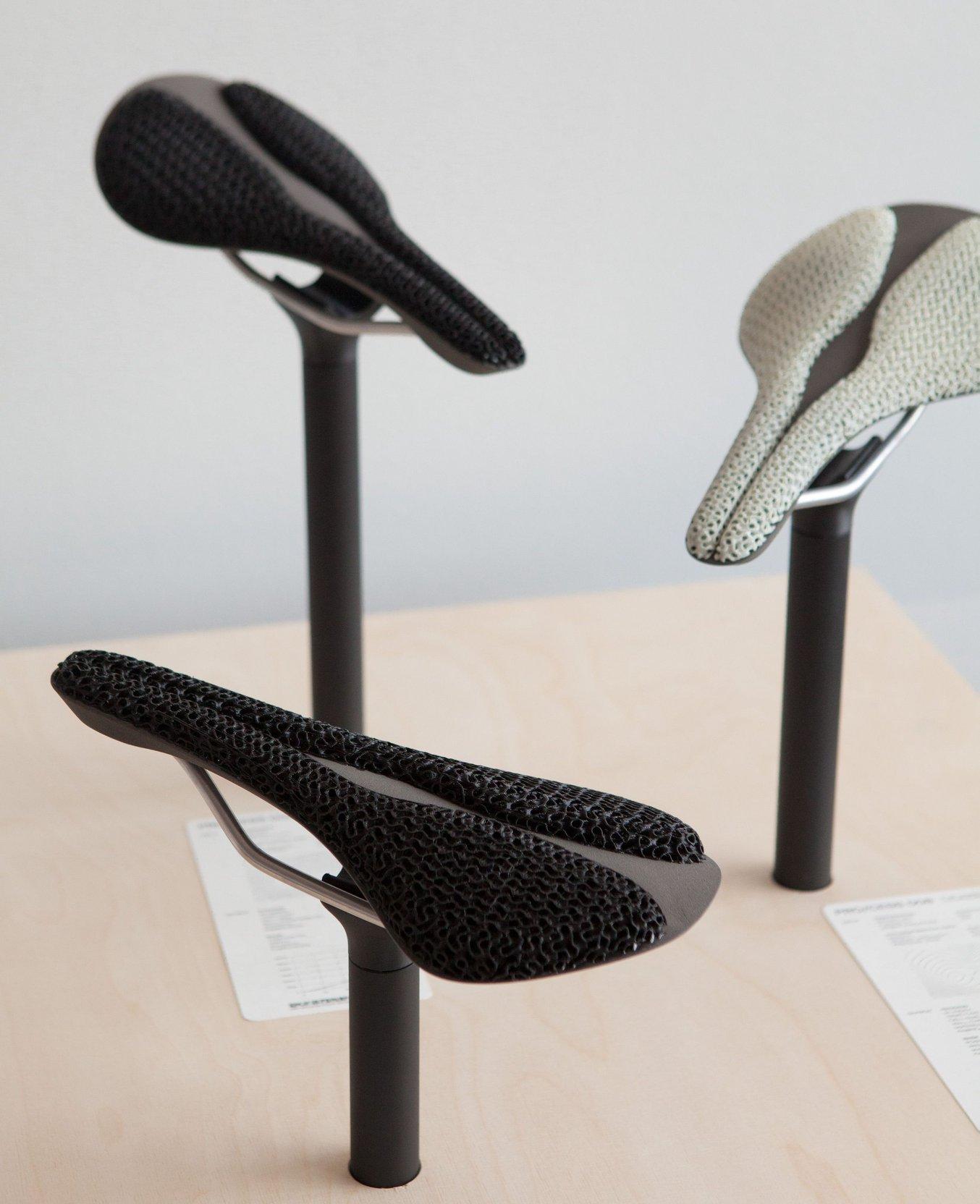
Am Ende seiner Bachelorarbeit hatte Tim Schütze drei gendersensible, individualisierte und einsatzbereite Fahrradsättel sowie einen Open-Source-Prozess.