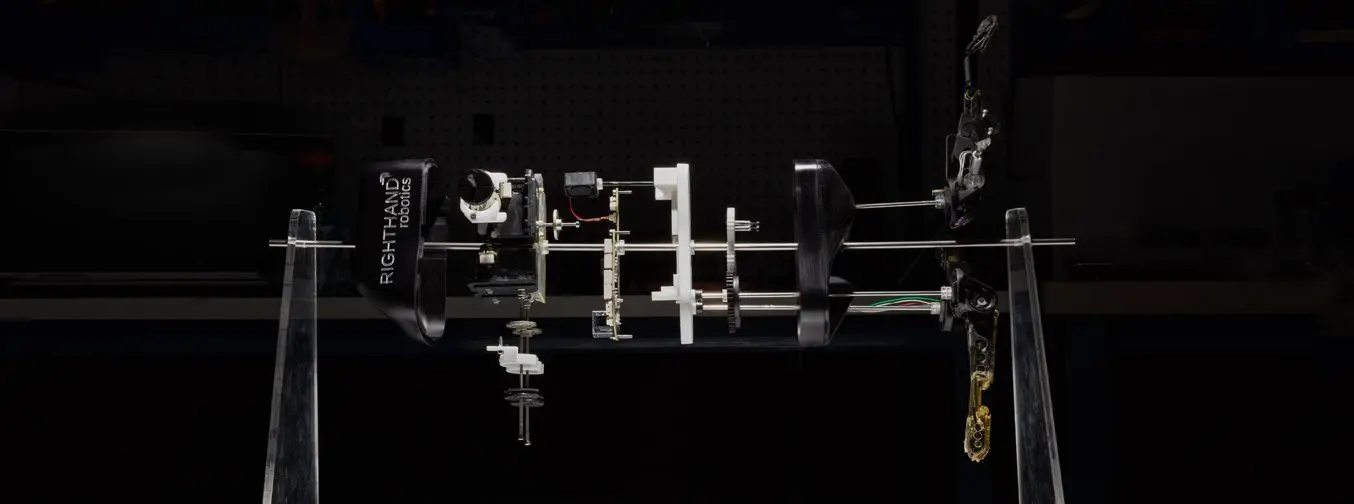
Kunststoffe sind die geläufigsten Materialien für die Produktion von fertigen Teilen und Endprodukten – von Konsumgütern bis hin zu Medizinprodukten. Kunststoffe sind eine vielseitige Materialkategorie, bei der sich tausende Polymermöglichkeiten anbieten, von denen jede einzelne ihre spezifischen mechanischen Eigenschaften hat. Aber wie werden Kunststoffteile hergestellt?
Es existiert eine Vielzahl an Fertigungsverfahren für Kunststoffe, um die große Bandbreite an Anwendungen, Druckgeometrien und Kunststoffarten abzudecken. Jeder Designer und Ingenieur, der in der Produktentwicklung arbeitet, muss unbedingt mit den heute verfügbaren Fertigungsoptionen vertraut sein und die neuen Entwicklungen kennen, die andeuten, wie Teile in der Zukunft gefertigt werden.
Dieser Leitfaden bietet einen Überblick über die geläufigsten Fertigungsprozesse für Kunststoffteile und Richtlinien zur Auswahl der besten Option für Ihre Anwendung.
Auswahl des richtigen Fertigungsverfahrens für den Kunststoff
Bedenken Sie die folgenden Faktoren, wenn Sie ein Herstellungsverfahren für Ihr Produkt auswählen:
Form: Weisen Ihre Teile komplexe interne Merkmale auf oder erfordern sie sehr enge Toleranzen? Abhängig von der Geometrie eines Designs können die Herstellungsoptionen begrenzt sein oder erhebliche Optimierungen in Sachen Design for Manufacturing (DFM) erfordern, damit sich das Teil wirtschaftlich fertigen lässt.
Volumen/Kosten: Was ist das gesamte oder jährliche Teilevolumen, das Sie fertigen möchten? Einige Fertigungsverfahren bergen hohe Anschaffungskosten für die Werkzeugbestückung und Einrichtung, liefern aber niedrige Kosten pro Teil. Im Gegensatz dazu sind die Anschaffungskosten bei Fertigungsverfahren mit geringem Volumen niedrig, doch durch geringere Durchlaufzeiten, den geringeren Automatisierungsgrad und Handarbeit bleiben die Kosten pro Teil gleich oder sinken nur unerheblich, wenn das Volumen zunimmt.
Durchlaufzeit: Wie schnell müssen die Teile oder Endprodukte hergestellt werden? Bei manchen Prozessen lassen sich die ersten Teile innerhalb von 24 Stunden herstellen, während die Werkzeugbestückung und die Einrichtung bei bestimmten Fertigungsprozessen mit hohen Volumina Monate in Anspruch nehmen können.
Material: Welchen Belastungen und Spannungen wird Ihr Produkt ausgesetzt sein? Das optimale Material für eine bestimmte Anwendung wird von verschiedenen Faktoren bestimmt. Die Kosten müssen mit funktionellen und ästhetischen Anforderungen abgewogen. Bedenken Sie die idealen Eigenschaften für Ihre spezifische Anwendung und stellen Sie diese den verfügbaren Möglichkeiten in einem bestimmten Fertigungsverfahren gegenüber.
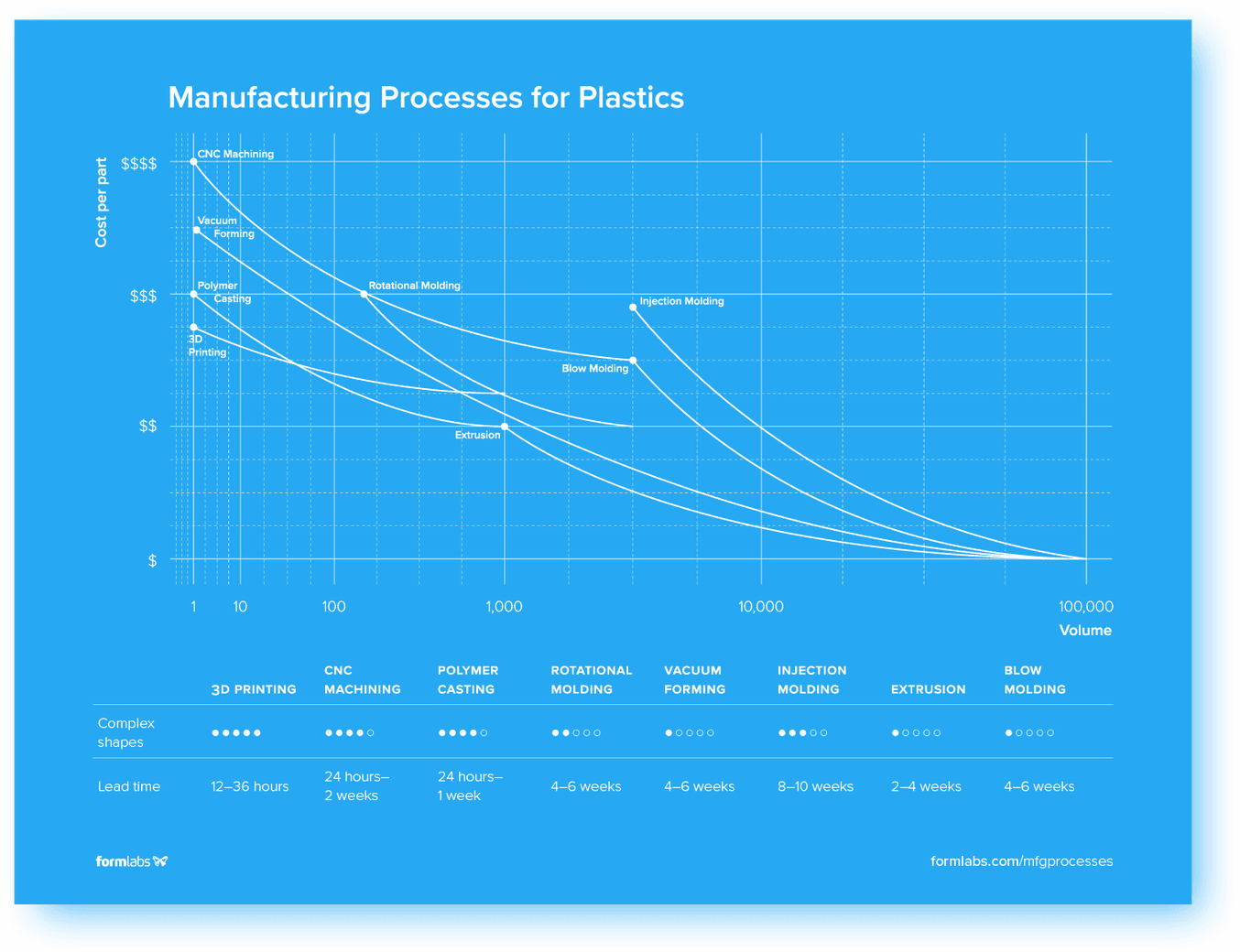
Laden Sie die hochauflösende Version dieser Infografik hier herunter.
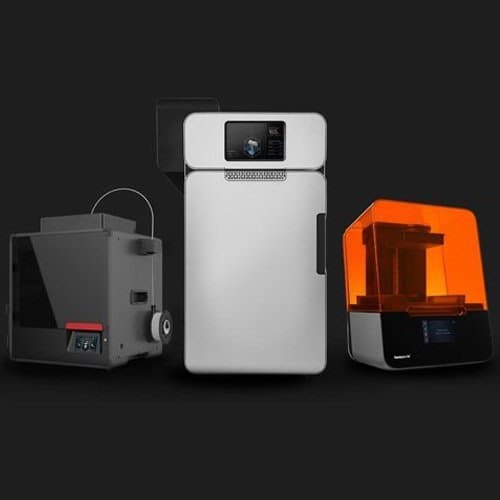
So wählen Sie die richtige 3D-Drucktechnologie
Brauchen Sie Hilfe bei der Wahl der richtigen 3D-Drucktechnologie, zugeschnitten auf Ihre Bedürfnisse? In diesem Videoleitfaden vergleichen wir die FDM-, SLA- und SLS-Technologien in Bezug auf häufige Kaufkriterien.
Kunststoffarten
Es gibt tausende verschiedene Kunststoffe mit unterschiedlichen chemischen Strukturen, Derivaten und Additiven, die so formuliert sind, dass sie eine große Bandbreite an funktionellen und ästhetischen Eigenschaften abdecken.
Um es Ihnen einfacher zu machen, das Material zu finden, das sich am besten für ein bestimmtes Teil oder Produkt eignet, wollen wir zunächst zwei Hauptarten von Kunststoffen betrachten: Thermoplaste und Duroplaste.
Thermoplaste
Thermoplaste sind die am häufigsten eingesetzten Kunststoffe. Ihr Hauptunterscheidungsmerkmal von Duroplasten ist ihre Fähigkeit, mehrfach schmelzen und erstarren zu können, ohne dass es dabei zu bedeutender Zersetzung kommt. Thermoplaste werden für gewöhnlich in Form kleiner Pellets oder Platten bereitgestellt, die erwärmt und mit verschiedenen Fertigungsverfahren in die gewünschte Form gebracht werden. Der Prozess ist vollständig umkehrbar, da keine chemischen Bindungen entstehen. So lassen sich Thermoplaste recyceln oder schmelzen und wiederverwenden.
Gängige Arten thermoplastischer Materialien:
- Acrylglas (PMMA)
- Acrylnitril-Butadien-Styrol-Copolymere (ABS)
- Polyamid (PA)
- Polylactide (PLA)
- Polycarbonat (PC)
- Polyetheretherketon (PEEK)
- Polyethylen (PE)
- Polypropylen (PP)
- Polyvinylchlorid (PVC)
Duroplaste
Im Gegensatz zu Thermoplasten bleiben Duroplaste nach dem Aushärten dauerhaft im festen Zustand. Die Polymere in Duroplasten vernetzen sich bei der Aushärtung, die durch Wärme, Licht oder geeignete Strahlung erzielt werden kann. Bei der Aushärtung entsteht eine irreversible chemische Bindung. Duroplaste zersetzen sich beim Erwärmen, anstatt zu schmelzen, und bilden sich beim Abkühlen nicht neu. Die Wiederverwertung von Duroplasten und die Rückführung des Materials in seine Grundbestandteile ist somit nicht möglich.
Gängige Arten thermoplastischer Materialien:
- Cyanatester
- Epoxidharz
- Polyester
- Polyurethan
- Silikon
- Vulkanisierter Kautschuk
Arten von Fertigungsverfahren
3D-Druck
Professionelle 3D-Drucker erzeugen dreidimensionale Teile direkt aus CAD-Modellen, indem sie das Material Schicht für Schicht aufbauen, bis ein vollständiges physisches Teil vorhanden ist.
Fertigungsprozess
- Druckeinrichtung: Eine Druckvorbereitungssoftware wird eingesetzt, um Modelle im Fertigungsvolumen eines Druckers zu platzieren und auszurichten, bei Bedarf Stützstrukturen hinzuzufügen und das gestützte Modell Schicht für Schicht zu prüfen.
- Druck: Der Druckprozess hängt von der Art der 3D-Drucktechnologie ab: Bei der Schmelzschichtung (Schmelzschichtung, FDM) wird ein Kunststoff-Filament geschmolzen, bei der Stereolithografie (SLA) wird flüssiges Kunstharz gehärtet und beim Selektiven Lasersintern (SLS) wird Kunststoffpulver verschmolzen.
- Nachbearbeitung: Wenn der Druck abgeschlossen ist, werden die Teile aus dem Drucker genommen, gereinigt oder gewaschen, nachgehärtet (abhängig von der Technologie) und die Stützstrukturen werden entfernt (falls vorhanden).
Da bei 3D-Druckern keine Werkzeugbestückung erforderlich ist und sie nur eine minimale Einrichtungszeit für ein neues Design benötigen, sind die Kosten für die Produktion eines maßgeschneiderten Teils im Vergleich mit herkömmlichen Fertigungsverfahren vernachlässigbar.
3D-Druckverfahren sind im Allgemeinen langsamer und arbeitsaufwendiger als Fertigungsverfahren, die für die Massenproduktion genutzt werden.
Angesichts der Verbesserungen der 3D-Drucktechnologie sinken die Teilekosten weiter, wodurch sie für eine größere Bandbreite an Anwendungen für kleine und mittelgroße Chargen in Frage kommt.
3D-Druck | |
---|---|
Form | Große Freiheit |
Durchlaufzeit | Weniger als 24 Stunden |
Zyklus | < 1 Stunde bis mehrere Stunden, abhängig von der Teilgröße und dem Volumen |
Einrichtungskosten | $ |
Kosten pro Teil | $$$ |
Volumen | Kleine bis mittlere Chargen (ca. 1–1000 Teile) |
Obwohl die meisten Fertigungsverfahren für Kunststoffe teure Industrieanlagen, dedizierte Einrichtungen und fachkundige Bediener erfordern, können Unternehmen mit 3D-Druck Kunststoffteile und Prototypen leicht firmenintern herstellen.
Kompakte Desktop oder Benchtop 3D-Drucksysteme zum Fertigen von Kunststoffteilen sind kostengünstig und verbrauchen sehr wenig Platz. Es sind keine besonderen Fähigkeiten erforderlich, wodurch Ingenieure, Designer und Hersteller Iterationen beschleunigen und Produktionszyklen von Tagen oder Wochen auf einige wenige Stunden verkürzen können.
Materialien
Es gibt viele verschiedene Arten von 3D-Druckern und 3D-Drucktechnologien auf dem Markt, und die verfügbaren Materialien unterscheiden sich je nach Technologie.
3D-Druckmaterialien | |
---|---|
Schmelzschichtung (Fused Deposition Modeling, FDM) | Verschiedene Thermoplaste, vor allem ABS und PLA |
Stereolithografie (SLA) | Thermoplastische Kunststoffe |
Selektives Lasersintern (SLS) | Thermoplaste, für gewöhnlich Nylon und seine Verbundwerkstoffe |
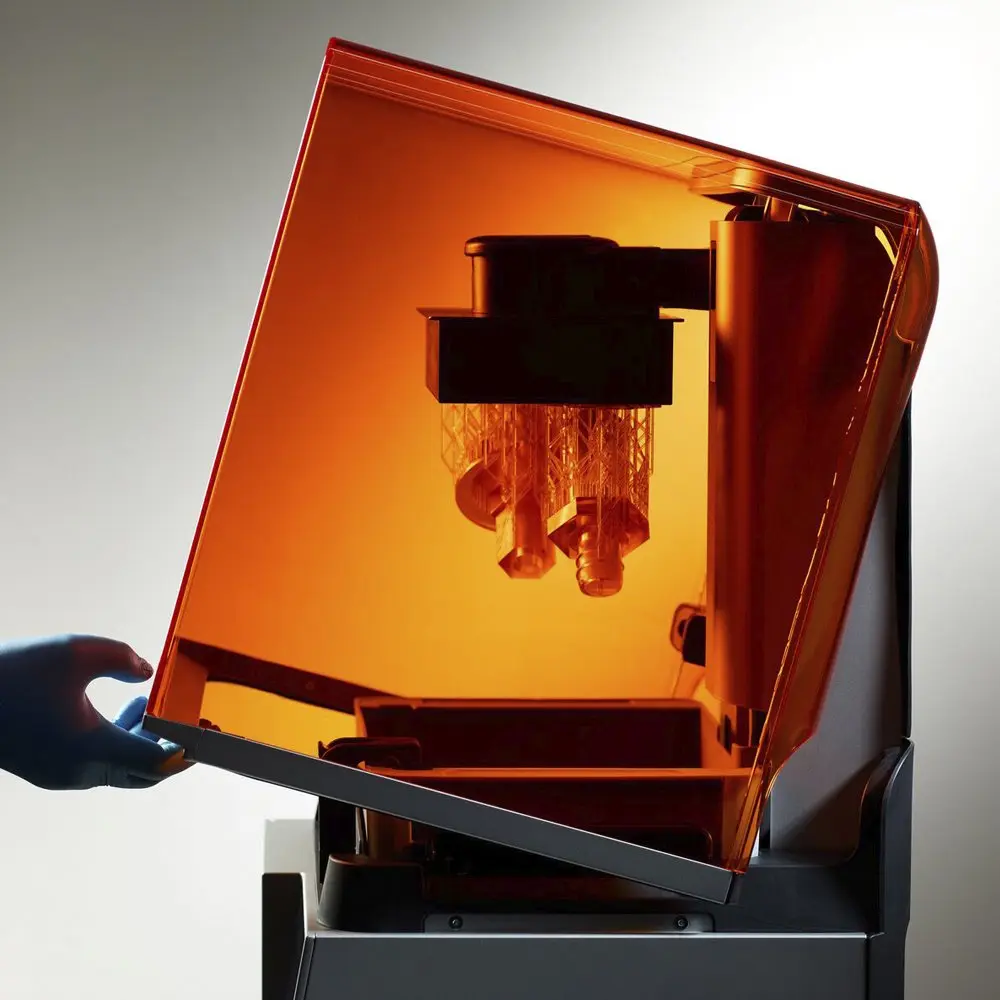
Einführung in den 3D-Druck mit Desktop-Stereolithografie (SLA)
Sie suchen einen Kunstharz-3D-Drucker, der Ihre 3D-Modelle in hochauflösender Qualität Wirklichkeit werden lässt? Lernen Sie in diesem Whitepaper das Verfahren der Stereolithografie (SLA) näher kennen – von seiner Funktionsweise bis hin zu den Gründen für seinen Status als populärste 3D-Drucktechnologie bei der Umsetzung hochgradig detailtreuer Modelle.
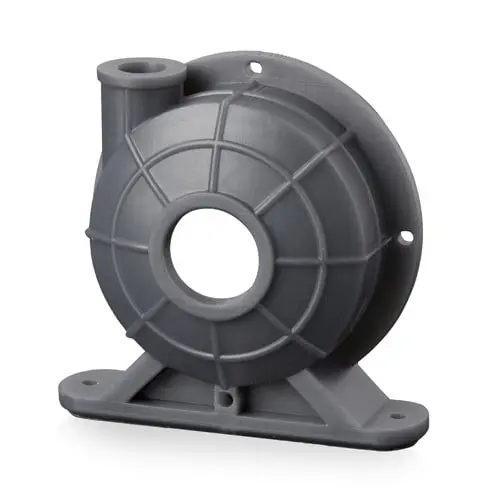
Kostenlosen Probedruck anfordern
Sehen und fühlen Sie die Qualität von Formlabs aus erster Hand. Wir senden Ihnen einen kostenlosen Probedruck an Ihren Arbeitsplatz.
CNC-Bearbeitung
Die CNC-Bearbeitung umfasst Fräsmaschinen, Drehmaschinen und andere computergesteuerte Zerspanungsverfahren. Bei diesen Verfahren sind die Ausgangsstoffe feste Blöcke oder Stäbe aus Metall oder Kunststoff, die geformt werden, indem Material durch Schneiden, Bohren und Schleifen abgehoben wird.
Im Gegensatz zu den meisten anderen Fertigungsverfahren für Kunststoffe ist die CNC-Bearbeitung ein zerspanendes Verfahren, bei dem Material entweder durch ein rotierendes Werkzeug und ein festes Teil (Fräsen) oder ein rotierendes Teil und ein festes Werkzeug (Drehmaschine) abgehoben wird.
Fertigungsprozess
- Einrichtung: Bei CNC-Maschinen ist ein Zwischenschritt erforderlich, bei dem Werkzeugwege erstellt und validiert werden (CAD zu CAM). Die Werkzeugwege bestimmen, wie sich die Schneidwerkzeuge bewegen, mit welcher Geschwindigkeit und ob Werkzeuge ausgetauscht werden müssen.
- Zerspanung: Die Werkzeugwege werden an die Maschine gesendet, auf welcher das entsprechende subtraktive Verfahren beginnt. Abhängig von der gewünschten Form des Endprodukts muss das Werkstück neu ausgerichtet werden, damit der Werkzeugkopf neue Bereiche erreichen kann.
- Nachbearbeitung: Nach der Fertigung wird das Teil gereinigt, entgratet und getrimmt.
Die zerspanende Bearbeitung eignet sich ideal für Kunststoffanwendungen mit geringen Volumen, die enge Toleranzen und schwer formbare Geometrien erfordern. Typische Anwendungen sind Prototypen und Fertigteile wie Riemenscheiben, Zahnräder und Buchsen.
Die CNC-Bearbeitung erfordert geringe bis mittlere Einrichtungskosten und ermöglicht die Fertigung hochwertiger Kunststoffteile aus vielen verschiedenen Materialien mit geringen Durchlaufzeiten.
Bei den Bearbeitungsprozessen sind die möglichen Teilegeometrien im Vergleich zum 3D-Druck eingeschränkter. Beim zerspanenden Bearbeiten nehmen die Kosten pro Teil mit zunehmender Teilekomplexität zu. Hinterschneidungen, Durchbrüche und Merkmale auf verschiedenen Teileflächen tragen alle zu erhöhten Teilekosten bei.
Die Zerspanungsprozesse erfordern Aufmaße für den Werkzeugzugang und bestimmte Geometrien wie geschwungene, interne Kanäle lassen sich mit herkömmlichen subtraktiven Verfahren nur schwer oder gar nicht herstellen.
CNC-Bearbeitung | |
---|---|
Form | Mittlere Gestaltungsfreiheit |
Durchlaufzeit | Weniger als 24 Stunden |
Zyklus | < 1 Stunde bis mehrere Stunden, abhängig von der Teilgröße, dem Design und der Komplexität |
Einrichtungskosten | $$ |
Kosten pro Teil | $$$$ |
Volumen | Kleine bis große Chargen (ca. 1–5000 Teile) |
Materialien
Die meisten harten Kunststoffe können mit leicht unterschiedlichem Schwierigkeitsgrad zerspant werden. Weichere Duroplaste erfordern Spezialwerkzeuge, die das Teil beim Bearbeiten stützen, und gefüllte Kunststoffe können abrasiv wirken und die Standzeit des Schneidwerkzeugs verringern.
Einige häufig bearbeitete Kunststoffe sind:
- Acrylglas (PMMA)
- Acrylnitril-Butadien-Styrol-Copolymere (ABS)
- Polyamidnylon (PA)
- Polylactide (PLA)
- Polycarbonat (PC)
- Polyetheretherketon (PEEK)
- Polyethylen (PE)
- Polypropylen (PP)
- Polyvinylchlorid (PVC)
- Polycarbonat (PC)
- Polystyrol (PS)
- Polyoxymethylen (POM)
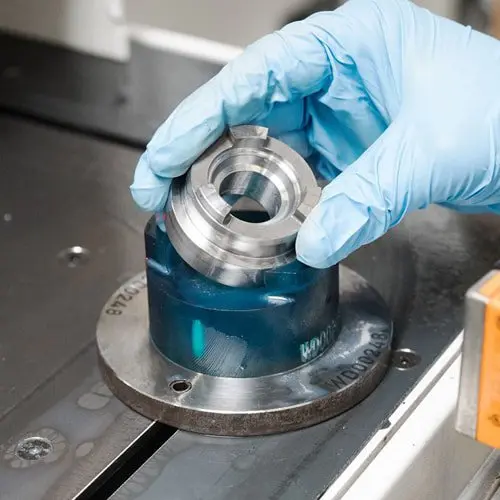
Innovation im Produktionswerk: 3D-Druck von Halterungen und Vorrichtungen
In diesem Webinar erfahren Sie, wie Sie Halterungen und Vorrichtungen entwerfen und 3D-drucken, die zerspante Metallteile ersetzen können. Außerdem stellen wir fünf Wege vor, um die Effizienz Ihres Werks mit 3D-Druck zu steigern.
Polymerguss
Beim Polymerguss füllt ein reaktionsfähiges, flüssiges Kunstharz oder Kautschuk eine Form, was zu einer chemischen Reaktion und zum Aushärten führt. Typische Polymere zum Gießen sind Polyurethan, Epoxidharz, Silikon und Acrylglas.
Fertigungsprozess
- Vorbereitung der Form: Die Form wird mit einem Trennmittel beschichtet, um das Entformen zu erleichtern, und häufig auf eine materialspezifische Temperatur vorgeheizt.
- Guss: Das Kunstharz wird mit einem Härter gemischt und in die Form gegossen oder gespritzt und füllt so den Formhohlraum.
- Aushärtung: Das Gussstück härtet in der Form aus (wenn die Form Wärme ausgesetzt wird, kann die Aushärtezeit bei bestimmten Polymeren beschleunigt werden).
- Entformung: Die Form wird geöffnet und das gehärtete Teil entfernt.
- Zuschneiden: Gussrückstände, wie Grate, Angüsse und Nähte werden weggeschnitten oder abgeschliffen.
Flexible Formen aus Latex oder bei Raumtemperatur vulkanisiertem (RTV) Silikonkautschuk sind kostengünstig, eignen sich jedoch nur für eine begrenzte Anzahl an Gussteilen (zwischen 25 und 100), da die chemische Reaktion von Urethan, Epoxidharz, Polyester und Acrylharz die Formoberflächen zersetzt.
RTV-Silikonformen können selbst die kleinsten Details wiedergeben, wodurch sich hochwertige Gussteile erzielen lassen. Stereolithografie-3D-Druck ist eine geläufige Methode zur Fertigung von Modellen für Formen direkt aus CAD-Designs, zum Teil wegen seiner hohen Auflösung und der ähnlichen Fähigkeit, filigrane Details wiederzugeben.
Der Polymerguss ist verhältnismäßig kostengünstig und erfordert geringe Startinvestitionen, aber Duroplaste zum Gießen sind für gewöhnlich teurer als entsprechende Thermoplaste und das Gießen von Teilen ist arbeitsaufwendig. Jedes Gussteil erfordert etwas Handarbeit beim Nachbearbeiten, wodurch die Gesamtkosten pro Teil im Vergleich zu automatisierten Fertigungsverfahren wie dem Spritzguss hoch sind.
Das Polymergießen wird für gewöhnlich zum Prototypenbau, bei der Kleinserienfertigung und bei bestimmten zahntechnischen und Schmuckanwendungen eingesetzt.
Polymerguss | |
---|---|
Form | Große Freiheit |
Durchlaufzeit | Weniger als 24 Stunden bis einige Tage |
Zyklus | Minuten bis mehrere Tage, abhängig von der Aushärtedauer |
Einrichtungskosten | $ |
Kosten pro Teil | $$ |
Volumen | Kleine Chargen (ca. 1–1000 Teile) |
Materialien
- Polyurethan
- Epoxidharz
- Polyether
- Polyester
- Acrylglas
- Silikon
Rotationsguss
Der Rotationsguss (auch bekannt als Rotationsformen) ist ein Verfahren, bei dem eine hohle Form mit einem Thermoplast in Pulverform gefüllt und um zwei Achsen rotiert wird, um in erster Linie große Hohlkörper herzustellen. Verfahren zum Rotationsformen von Duroplasten sind auch verfügbar, sind jedoch weniger häufig.
Fertigungsprozess
- Beschicken: Der Formhohlraum wird mit Kunststoffpulver beschickt; anschließend werden die restlichen Teile der Form montiert und der Hohlraum so zum Erwärmen geschlossen.
- Erhitzen: Die Form wird erwärmt, bis das Kunststoffpulver schmilzt und an den Wänden der Form haftet, während die Form um zwei zueinander senkrechte Achsen rotiert wird, um eine einheitliche Kunststoffbeschichtung zu gewährleisten.
- Abkühlen: Die Form wird langsam abgekühlt, während sie sich weiterhin dreht, um sicherzustellen, dass die Haut des Teils nicht durchhängt oder zusammenfällt, bevor sie vollständig ausgehärtet ist.
- Teileentnahme: Das Teil wird aus der Form entnommen und Gräte werden entfernt.
Der Rotationsguss erfordert weniger teure Werkzeuge als andere Gussverfahren, da der Prozess die Zentrifugalkraft nutzt, um die Form zu füllen, und nicht Druck. Die Formen können aus Epoxidharz oder Aluminium gefertigt, zerspant, gegossen oder geformt werden, und das zu geringeren Kosten und deutlich schneller als die Werkzeugausstattung bei anderen Gussverfahren, besonders bei großen Teilen.
Der Rotationsguss sorgt für eine nahezu einheitliche Wandstärke. Nach der Werkzeugausstattung und der Einrichtung des Verfahrens sind die Kosten pro Teil im Verhältnis zur Teilgröße sehr gering. Es können auch vorgefertigte Teile wie Metallgewinde, innere Rohre und Strukturen zur Form hinzugefügt werden.
Durch diese Faktoren eignet sich der Rotationsguss ideal für die Kleinserienfertigung oder als Alternative zum Blasformen bei kleineren Chargen. Typische durch Rotationsguss hergestellte Produkte sind Tanks, Bojen, große Behälter, Spielzeug, Helme und Kanurümpfe.
Beim Rotationsgießen gibt es einige Designeinschränkungen, und die fertigen Produkte weisen größere Toleranzen auf. Da die gesamte Form erwärmt und abgekühlt werden muss, weist der Prozess auch lange Zykluszeiten auf und ist verhältnismäßig arbeitsintensiv, wodurch seine Effizienz bei Anwendungen mit größerem Fertigungsvolumen eingeschränkt wird.
Rotationsguss | |
---|---|
Form | Mittlere Freiheit, ideal für große Hohlkörper |
Durchlaufzeit | Tage bis einige Wochen |
Zyklus | Typisch < 1 Stunde |
Einrichtungskosten | $$$ |
Kosten pro Teil | $$ |
Volumen | Mittlere Chargen (ca. 200–5000 Teile) |
Materialien
Das häufigste Material für den Rotationsguss ist Polyethylen (PE), das bei 80 Prozent aller Anwendungen eingesetzt wird, vor allem weil PE bei Raumtemperatur leicht zu einem Pulver zermahlen werden kann.
Häufig beim Rotationsguss eingesetzte Kunststoffe:
- Polyethylen
- Polypropylen
- Polyvinylchlorid
- Nylon
- Polycarbonat
Vakuumformen
Vakuumformen oder Thermoformen ist ein Fertigungsverfahren, bei dem ein Kunststoff für gewöhnlich in einer Form erwärmt und geformt wird. Vakuumformmaschinen unterscheiden sich in Größe und Komplexität und reichen von kostengünstigen Desktop-Geräten bis hin zu automatisierten Industriemaschinen. Die nachfolgenden Schritte beschreiben das typische Verfahren beim industriellen Vakuumformen.
Fertigungsprozess
- Einspannen: Eine Kunststoffplatte wird in einen Rahmen geklemmt.
- Erhitzen: Die Platte und der Rahmen werden den Heizelementen angenähert, wodurch der Kunststoff weich und biegsam wird.
- Vakuum: Der Rahmen wird abgesenkt und der Kunststoff wird über die Form gespannt, während ein Vakuum erzeugt wird, um alle Luft zwischen dem Kunststoff und der Form zu herauszusaugen. Auf diese Weise wird das Teil geformt.
- Abkühlen und Entformung: Wenn das Teil über der Form geformt wurde, muss es einige Zeit abkühlen, bevor es entfernt werden kann. Kühlsysteme wie Lüfter und Sprühnebel werden gelegentlich eingesetzt, um die Zykluszeiten zu verringern.
- Zuschneiden: Sobald das Teil entfernt wurde, wird überschüssiges Material entweder von Hand oder einer CNC-Maschine entfernt.
Die Werkzeugkosten beim Vakuumformen sind im Vergleich zu anderen Formverfahren niedrig, da nur geringe Kräfte und Drücke eingesetzt werden. Die Formen bestehen bei der Kleinserienfertigung und bei Maßanfertigungen aus Holz, Gips oder 3D-gedrucktem Kunstharz. Bei großen Volumina nutzen Hersteller haltbarere Metallwerkzeuge.
Aufgrund der Vielzahl an Thermoform- und Vakuumformgeräten auf dem Markt und den Automatisierungsmöglichkeiten bei High-End-Ausrüstung eignet sich Thermoformen ideal für jede beliebige Anwendung von maßgeschneiderten Produkten oder Prototypen bis hin zur Massenfertigung. Allerdings wird durch das Verfahren die Formfreiheit häufig eingeschränkt und es kann nur zur Fertigung von Teilen eingesetzt werden, die verhältnismäßig dünne Wände und einfache Geometrien aufweisen.
Häufig vakuumgeformte Teile sind Produktverpackungen, Duschwannen, Kfz-Türverkleidungen, Bootsrümpfe und maßgeschneiderte Produkte wie Aligner in der Zahntechnik.
Vakuumformen | |
---|---|
Form | Eingeschränkte Freiheit, nur dünnwandige Teile, keine komplexen Geometrien |
Durchlaufzeit | Weniger als 24 Stunden bis Wochen |
Zyklus | Sekunden bis Minuten, abhängig vom Gerät |
Einrichtungskosten | $–$$$$ |
Kosten pro Teil | $–$$$ |
Volumen | Beliebiges Volumen |
Materialien
Die meisten Thermoplaste können für das Thermoformen eingesetzt werden, wodurch die Materialauswahl flexibel ist.
Häufig genutzte Kunststoffe für das Thermoformen sind:
- Acrylglas (PMMA)
- Acrylnitril-Butadien-Styrol-Copolymere (ABS)
- Polyethylenterephthalat, glykolmodifiziert (PETG)
- Polystyrol (PS)
- Polycarbonat (PC)
- Polypropylen (PP)
- Polyethylen (PE)
- Polyvinylchlorid (PVC)
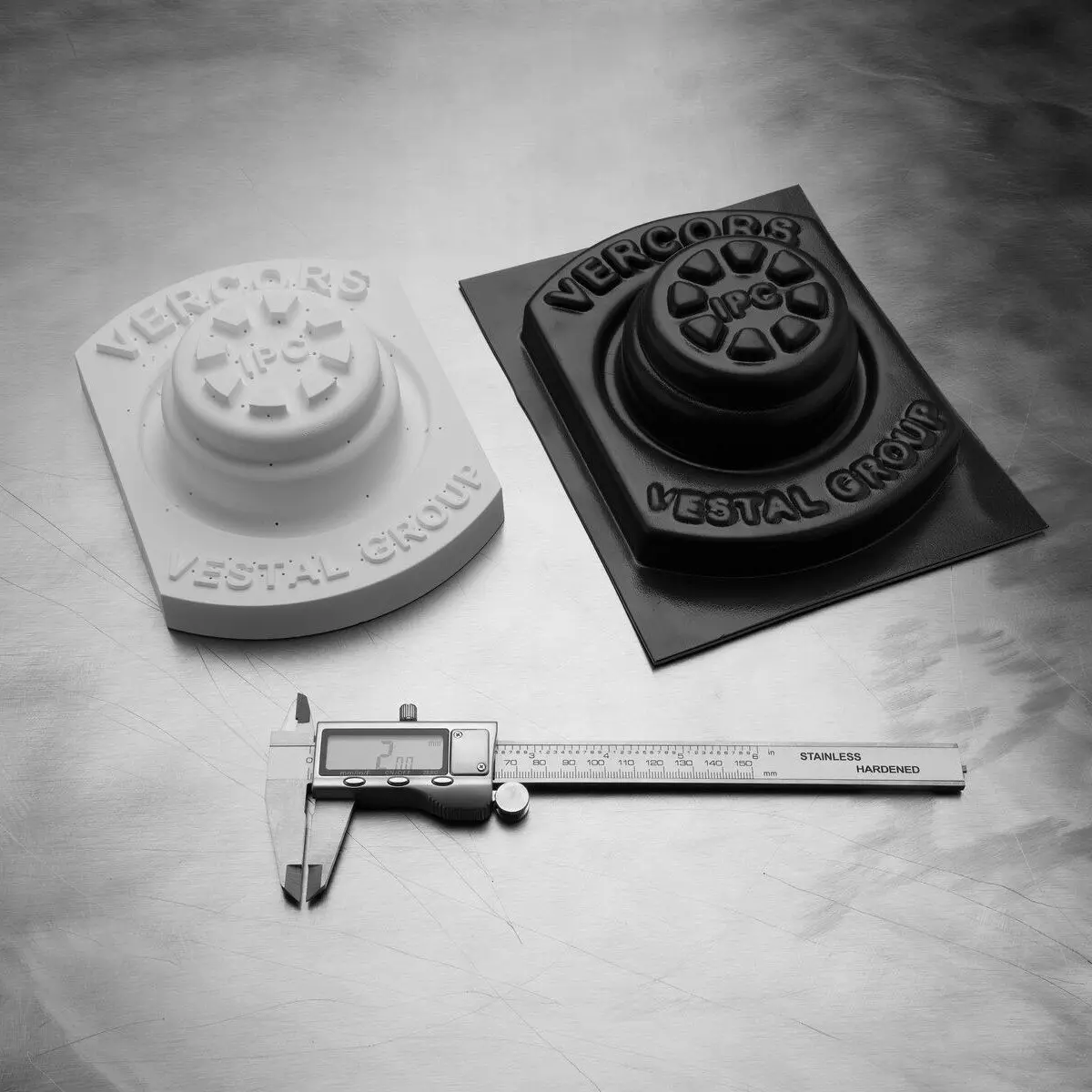
Schnelles Thermoformen in Kleinserie mit 3D-gedruckten Formwerkzeugen
Laden Sie unser Whitepaper herunter und erfahren Sie mehr über die schnelle Fertigung komplexer Formwerkzeuge mittels 3D-Druck. Wir geben außerdem Tipps und Richtlinien zur Vorbereitung der Bestandteile der Form.
Spritzguss
Beim Spritzgießen wird ein geschmolzener Thermoplast in eine Form gespritzt. Es handelt sich dabei um den am häufigsten genutzten Prozess zur Massenfertigung von Kunststoffteilen.
Fertigungsprozess
- Vorbereitung der Form: Weist das Teil Einsätze auf, werden diese entweder von Hand oder per Roboter hinzugefügt. Die Form wird mit einer hydraulischen Presse geschlossen.
- Kunststoffextrusion: Kleine Kunststoffpellets werden geschmolzen und mit einer Schnecke durch eine beheizte Kammer extrudiert.
- Formen: Der geschmolzene Kunststoff wird in die Form gespritzt.
- Abkühlen und Entformung: Das Teil kühlt in der Form ab, bis es fest genug ist, um entweder mechanisch oder mit Druckluft ausgeworfen zu werden.
- Nachbearbeitung: Angüsse und Gräte (sofern vorhanden) werden vom Teil entfernt, häufig automatisch beim Öffnen der Form.
Formen für den Spritzguss sind hochgradig komplex und müssen mit engen Toleranzen hergestellt werden, damit hochwertige Teile erzielt werden. Aufgrund der hohen Temperaturen und Drücke werden diese Formen aus Metallen wie gehärtetem Stahl zerspanend gefertigt. Weichere Aluminiumformen sind günstiger, verschleißen aber auch schneller, weshalb sie eher für mittelgroße Chargen eingesetzt werden.
Das Spritzgießen kann zur Fertigung hochkomplexer Teile verwendet werden. Jedoch sorgen bestimmte Geometrien für einen bedeutenden Anstieg der Kosten. Durch Befolgen von Richtlinien zum Design for Manufacturing (DFM) bleiben die Werkzeugkosten in einem akzeptablen Umfang. Es kann Monate dauern, um neue Formen für den Spritzguss herzustellen. Ihre Kosten können fünf- bis sechsstellige Beträge erreichen.
Trotz der hohen Anfangskosten und dem langsamen Anfahren gibt es für das Spritzgießen keine Konkurrenz bei Anwendungen mit hohem Volumen. Sobald die Werkzeugbestückung erfolgt ist, belaufen sich die Zykluszeiten auf wenige Sekunden, und Millionen von hochwertigen Teilen können zu einem Bruchteil der Kosten aller anderen Fertigungsverfahren gefertigt werden.
Spritzguss | |
---|---|
Form | Mittlere bis große Freiheit |
Durchlaufzeit | 2–4 Monate |
Zyklus | Sekunden |
Einrichtungskosten | $$$$$ |
Kosten pro Teil | $ |
Volumen | Anwendungen mit hohen Volumina (über 5000 Teile) |
Materialien
Der Spritzguss kann mit fast jedem Thermoplasten durchgeführt werden. Eine ähnliche Methode, bekannt als Reaction Injection Molding (RIM), wird verwendet, um Teile aus Duroplasten herzustellen.
Häufig genutzte Kunststoffe für das Spritzgießen sind:
- Acrylglas (PMMA)
- Acrylnitril-Butadien-Styrol-Copolymere (ABS)
- Polyamid (PA)
- Polyethylenterephthalat, glykolmodifiziert (PETG)
- Polystyrol (PS)
- Polycarbonat (PC)
- Polypropylen (PP)
- Polyethylen (PE)
- Polyvinylchlorid (PVC)
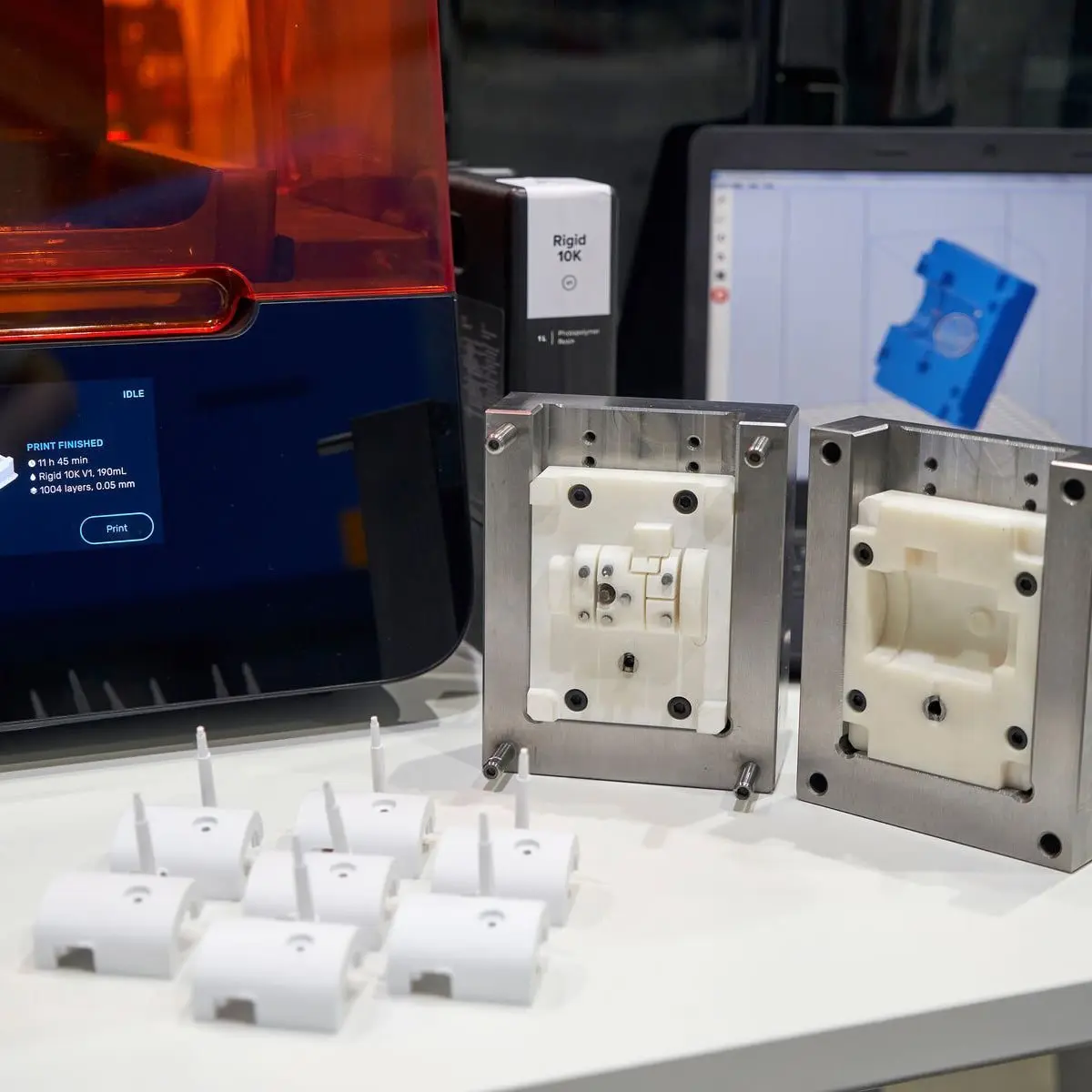
Schnelles Spritzgießen von Kleinserien mit Formen aus dem 3D-Drucker
Laden Sie dieses Whitepaper herunter und erfahren Sie mehr über die Methoden und Richtlinien zur Herstellung 3D-gedruckter Spritzgussformen, um die Kosten zu senken und Lieferzeiten zu verkürzen. Es enthält Fallstudien aus der Praxis von Braskem, Holimaker und Novus Applications.
Extrusion
Bei der Extrusion wird Kunststoff durch ein Formwerkzeug gepresst. Das Formwerkzeug hat die Form des Querschnitts des Fertigteils.
Fertigungsprozess
- Kunststoffextrusion: Kunststoff wird erwärmt und mit einer Schnecke durch eine beheizte Kammer gefördert.
- Formen: Kunststoff wird durch ein Formwerkzeug gepresst, das die endgültige Form des Teils abbildet.
- Abkühlen: Der extrudierte Kunststoff wird abgekühlt.
- Schneiden oder aufspulen: Der Strang wird aufgespult oder zurechtgeschnitten.
Im Vergleich zu anderen Industriemaschinen wie CNC-Zentren oder Spritzgussmaschinen sind Extruder verhältnismäßig günstig, da sie weniger komplex sind und eine geringere Genauigkeit erfordern. Aufgrund der einfachen Formen sind die Formwerkzeuge ebenfalls günstiger, wodurch die Werkzeugkosten lediglich einen Bruchteil der Formkosten beim Spritzguss ausmachen.
Ähnlich wie der Spritzguss ist das Extrudieren ein nahezu kontinuierlicher Prozess, wodurch der Preis extrudierter Teile sehr gering ist.
Die Formen, die durch die Extrusion erzeugt werden können, sind auf Produkte mit durchgehenden Profilen beschränkt, so etwa auf T-Profile, I-Profile, L-Profile, U-Profile und quadratische oder kreisförmige Profile. Typische Anwendungen sind Rohre, Schläuche, Strohhalme und Formen für Fensterrahmen.
Extrusion | |
---|---|
Form | Begrenzt, nur lange, durchgehende Formen |
Durchlaufzeit | Wochen |
Zyklus | Sekunden (oder durchgehend) |
Einrichtungskosten | $$$ |
Kosten pro Teil | $ |
Volumen | Anwendungen mit mittleren bis hohen Volumina (über 1000 Teile) |
Materialien
Nahezu alle Thermoplaste, die extrudiert werden können, darunter:
- Acrylglas (PMMA)
- Acrylnitril-Butadien-Styrol-Copolymere (ABS)
- Polyamid (PA)
- Polyethylenterephthalat, glykolmodifiziert (PETG)
- Polystyrol (PS)
- Polycarbonat (PC)
- Polypropylen (PP)
- Polyethylen (PE)
- Polyvinylchlorid (PVC)
Blasformen
Das Blasformen ist ein Fertigungsverfahren, das zur Fertigung hohler Kunststoffteile genutzt wird, indem ein beheiztes Kunststoffrohr in einer Form aufgeblasen wird, bis es die gewünschte Geometrie aufweist.
Fertigungsprozess
- Vorbereitung der Form: Kleine Kunststoffpellets werden geschmolzen und zu einem hohlen Rohr geformt, das als Vorformling bezeichnet wird.
- Formen: Der Vorformling wird in einer Form eingespannt und mit Druckluft aufgeblasen, bis er sich an die Innengeometrie der Form angepasst hat.
- Abkühlen und Entformung: Das Teil kühlt in der Form ab, bis es fest genug ist, um ausgeworfen zu werden.
Beim Blasformen werden deutlich niedrigere Drücke als beim Spritzgießen eingesetzt, wodurch die Werkzeugkosten geringer sind. Ähnlich wie das Spritzgießen und das Extrudieren ist das Blasformen ein kontinuierlicher Prozess, der vollständig automatisiert werden kann, was für hohe Produktionsraten und geringe Stückkosten sorgt.
Das Blasformen ist der häufigste Prozess zum Herstellen von Kunststoffprodukten in großem Umfang. Typische Anwendungen sind Flaschen, Spielzeuge, Kfz-Bauteile, Industriebauteile und Verpackungen.
Blasformen | |
---|---|
Form | Eingeschränkte Freiheit, nur hohle, dünnwandige Teile, keine komplexen Geometrien |
Durchlaufzeit | Wochen |
Zyklus | Sekunden |
Einrichtungskosten | $$$$ |
Kosten pro Teil | $ |
Volumen | Anwendungen mit hohen Volumina (über 5000 Teile) |
Materialien
Zum Blasformen können verschiedene Thermoplaste eingesetzt werden. Die am häufigsten eingesetzten Materialien sind:
- Polyethylenterephtalat (PET)
- Polypropylen (PP)
- Polyvinylchlorid (PVC)
- Polystyrol (PS)
- Polycarbonat (PC)
- Acrylnitril-Butadien-Styrol-Copolymere (ABS)
Stellen Sie Kunststoffteile schnell mit 3D-Druck her
Fertigungsverfahren für Kunststoffe entwickeln sich ständig weiter und die Wendepunkte, an denen es Sinn ergibt, von einer Technologie auf eine andere umzusteigen, verschieben sich aufgrund der Verbesserungen bei Ausrüstung, Materialien und Skaleneffekten.
Der 3D-Druck ist eine neuere, aber sich schnell entwickelnde Gruppe an Technologien, die sich zunehmend für eine größere Bandbreite an Anwendungen mit niedrigem bis mittlerem Volumen eignet, da sich die Hardware und die Materialien verbessern und die Kosten pro Teil weiter fallen.
Erfahren Sie mehr darüber, wie führende Hersteller den 3D-Druck nutzen, um Geld zu sparen und Durchlaufzeiten vom Design bis zur Produktion zu verkürzen.