Fortschrittliche Prothetik wird erschwinglich: So entwickelte PSYONIC eine bionische Hand mithilfe additiver Fertigung
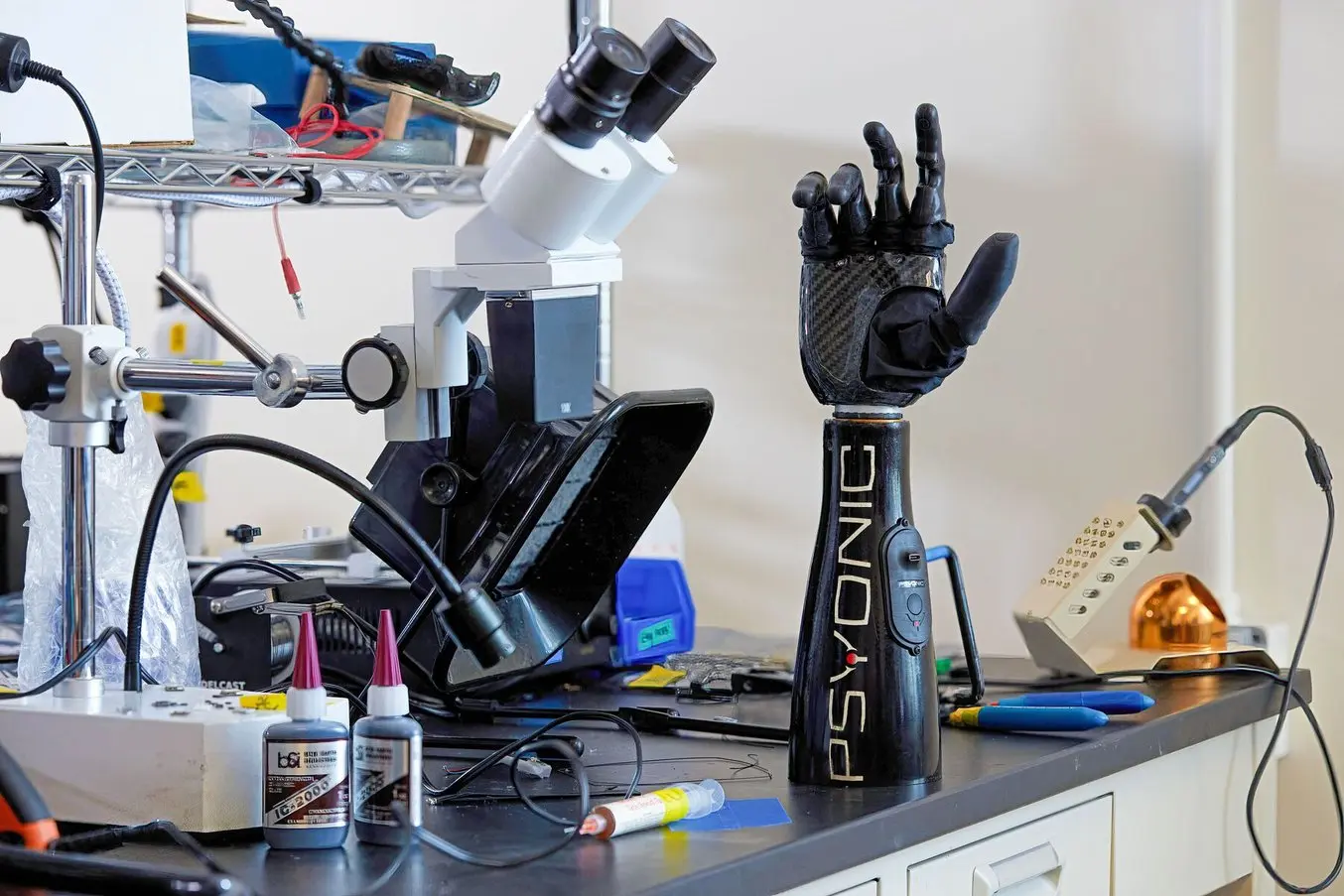
Weltweit gibt es mehr als 50 Millionen Menschen, die aufgrund traumatischer Ursachen eine Amputation von Gliedmaßen1 durchlaufen haben. Für Betroffene, die sich von einem Notfalleingriff erholen, kann es eine schmerzvolle Erfahrung bedeuten, sich mit dem Feld der Prothetik auseinanderzusetzen. Die meisten von ihnen möchten in ihr normales Leben zurückkehren: Sie wollen Auto fahren, Sport treiben, ihren Haushalt führen. Traditionelle Prothesen für Gliedmaßen sind jedoch meist plump, teuer und empfindlich. Nur etwa 10 % aller Patienten, die eine fortschrittliche Armprothese benötigen, können sie sich derzeit leisten.
Ein Unternehmen, das diesen Markt auf den Kopf stellen will, ist PSYONIC, der Entwickler der Ability Hand. Diese wurde mittels hybrider Fertigungsmethoden, einschließlich 3D-Druck, Spritzguss, Silikonguss und CNC-Bearbeitung, betriebsintern entworfen und gefertigt und verspricht, das Leben und die Mobilität Betroffener wieder auf ihr ursprüngliches Niveau zu bringen.
Was hat PSYONIC mithilfe von SLA-3D-Druckern von Formlabs erreicht?
- Die Entwicklung einer völlig neuen, bei der FDA registrierten, von Medicare abgedeckten Prothese für obere Extremitäten, die die Branche neu definiert
- Die Sammlung von Kundenrückmeldungen und rekordschnelles betriebsinternes Prototyping zur Verbesserung von Design und Funktionalität der Ability Hand
- Den Einsatz einer tatsächlich hybriden Fertigungsmethode, um die Ability Hand zu einem erschwinglichen Preis anzubieten
- Die Unterstützung Betroffener wie Sergeant Garrett Anderson bei der Rückkehr in ihr normales Leben
- Die Steigerung des Patientenanteils, für den die Prothese bezahlbar und verfügbar ist, von 10 auf 75 %
- Die Nutzung neuer, haltbarer und stoßfester 3D-Druckmaterialien zur Fertigung langlebiger Teile für die Endverwendung
In diesem Beitrag unterhalten wir uns mit Geschäftsführer Aadeel Akhtar, Ph.D., und dem leitenden Maschinenbauingenieur James Austin, um zu erfahren, wie die Ability Hand entstanden ist, warum dieser Markt so unterversorgt ist und welche grundlegende Rolle der 3D-Druck in der Markteintrittsstrategie des Unternehmens spielte. Außerdem lernen wir Sergeant Garrett Anderson kennen, einen der ersten Hauptbenutzer der Ability Hand.
Der Notwendigkeit einer besseren Lösung
Bei einem Einsatz im Irak im Jahr 2005 wurde Sergeant Garrett Andersons Fahrzeug von einer Straßenbombe getroffen. Anderson erlitt leichte traumatische Hirnverletzungen, hatte einen gebrochenen Kiefer – und vom Ellbogen abwärts musste sein rechter Arm amputiert werden. Nach seiner Heimkehr normalisierte sich sein Leben zum größten Teil, doch viele Dinge blieben eine Herausforderung. Er schrieb sich an der Illinois State University ein, erwarb einen Bachelor- und Masterabschluss und wurde Vater zweier Kinder.
Die meisten heute auf dem Markt erhältlichen Prothesen sind veraltet; für grundlegende Funktionen werden immer noch Haken verwendet. Trotz der rasanten Innovationen in anderen markanten Bereichen der Medizin in den vergangenen Jahren steckt die Prothetik immer noch in der Vergangenheit fest.
Anderson kam eines Tages mit einem jungen Ph.D.-Studenten namens Aadeel Akhtar in Kontakt. Genau wie Anderson war dieser mit dem bisherigen Stand der Prothetik unzufrieden. „Das ist etwas, das ich mein ganzes Leben lang tun wollte, seit ich sieben Jahre alt war. Meine Eltern kommen aus Pakistan. Als ich dort zu Besuch war, habe ich zum ersten Mal jemanden mit einer Gliedmaßenamputation getroffen. Es war ein Mädchen in meinem Alter, dem ein Bein fehlte und das einen Ast als Krücke benutzte. Das hat mich inspiriert, auf diesem Gebiet zu arbeiten, um die fortschrittlichsten bionischen Geräte zu entwickeln und sie für jeden verfügbar zu machen.“
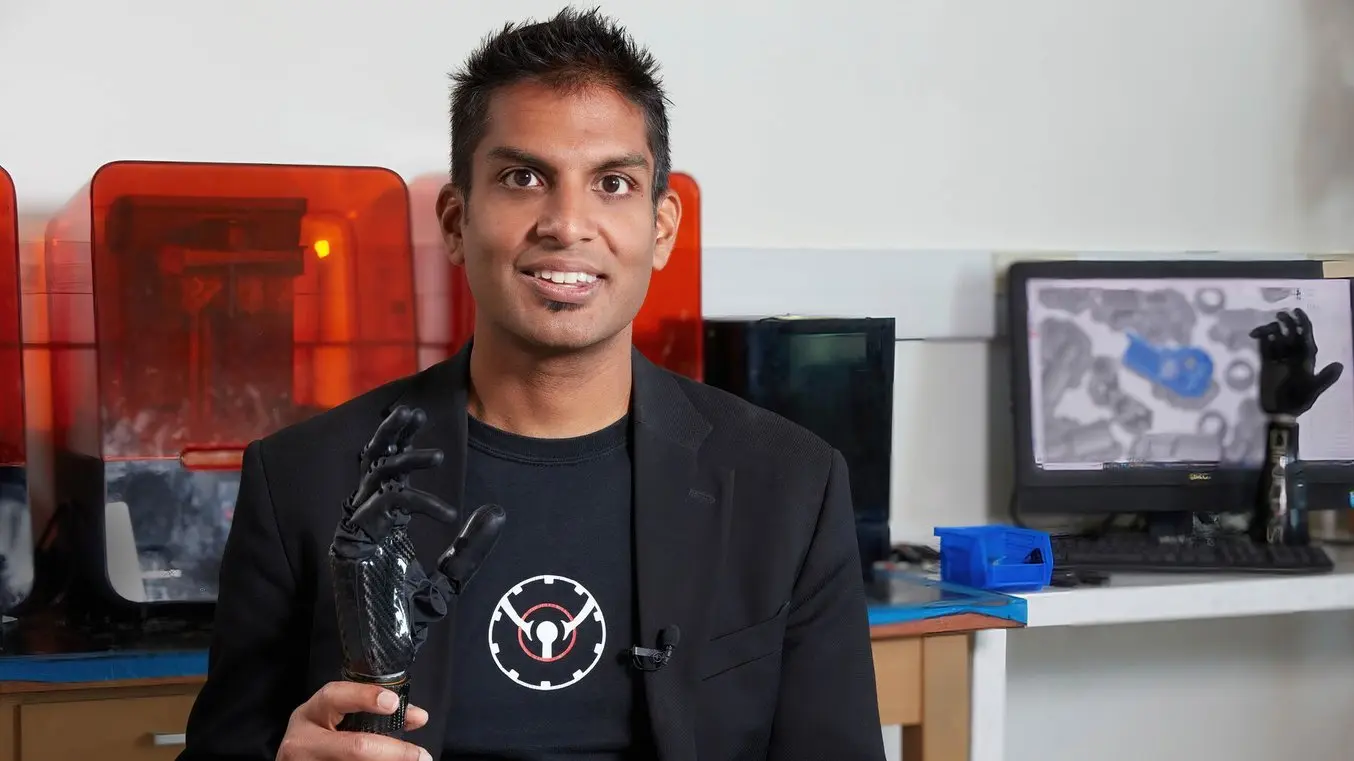
Geschäftsführer Aadeel Akhtar, Ph.D., mit der neuesten Version der Ability Hand.
Aber ein neues Prothesenprodukt auf den Markt zu bringen, das die Branche neu definiert, war keine einfache Aufgabe. „In den letzten sieben Jahren haben wir neun verschiedene Prototypen der Ability Hand entwickelt, die heute in den gesamten Vereinigten Staaten erhältlich ist und außerdem bei der FDA registriert und von Medicare abgedeckt“, berichtet Akhtar.
Wie moderne hybride Fertigung funktioniert
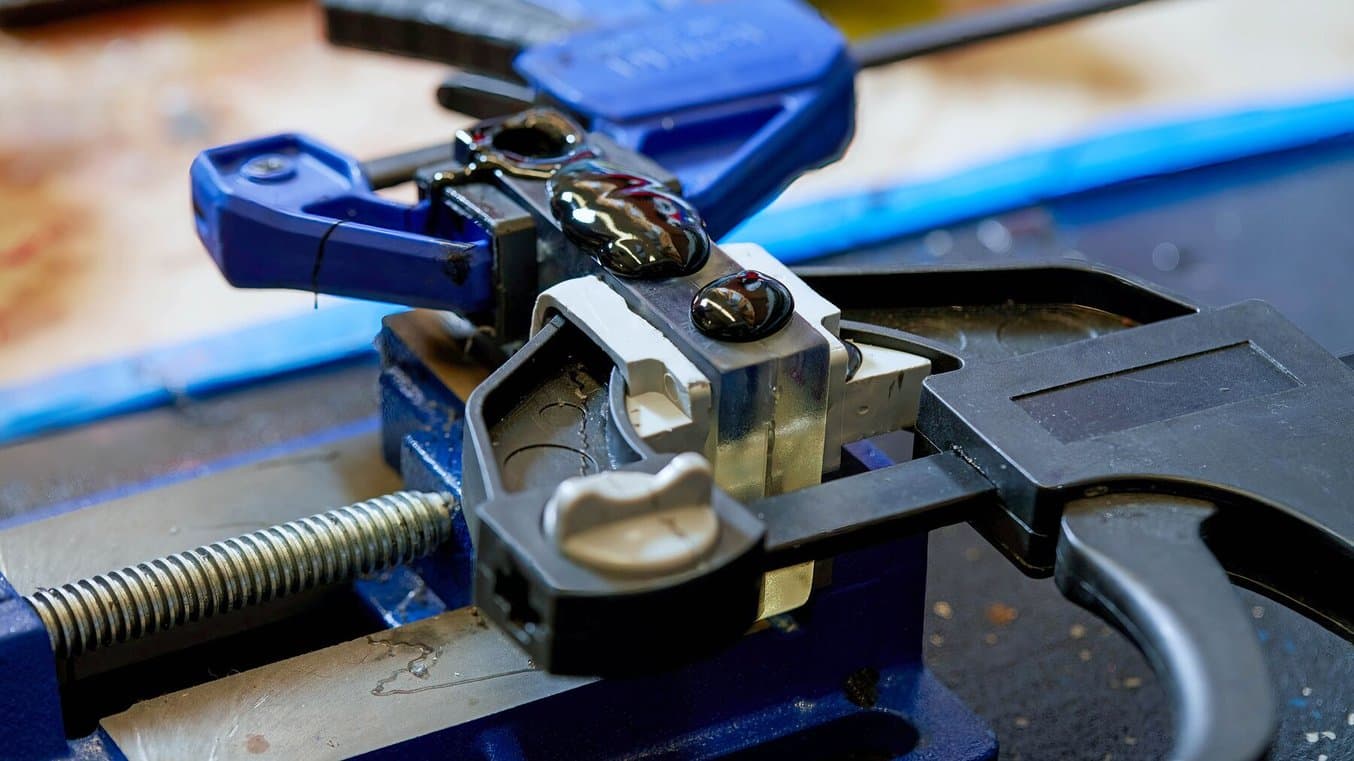
Immer mehr große und kleine Unternehmen wechseln zum betriebsinternen 3D-Druck, um ihre Prototypenentwicklung und die Markteinführung neuer Produkte zu unterstützen. In Bereichen mit hohen Vorabkosten für F&E, wie etwa der Herstellung von Medizinprodukten, stellt der 3D-Druck für Entwicklerteams heute ein essenzielles Werkzeug dar.
Eine wirklich neuartige Prothese muss schnell auf Anwendereingaben reagieren, muss belastbar und robust genug sein, um durch Alltagsaufgaben nicht kaputtzugehen, darf nicht so viel wiegen, dass sie Überanstrengung oder Krämpfe verursacht, und muss echtes sensorisches Feedback geben. Das ist keine leichte Aufgabe!
Was hat sich in der Fertigung solcher Geräte verändert, wodurch es kleinen Unternehmen wie PSYONIC möglich ist, den Markt traditioneller Prothesen auf den Kopf zu stellen?
- Der 3D-Druck wird seit Jahrzehnten zur Prototypenfertigung und Produktentwicklung verwendet. Inzwischen findet diese immer etabliertere Technologie, insbesondere das selektive Lasersintern (SLS) und die Stereolithografie (SLA), auch in der Fertigung weitläufigen Einsatz.
- Verbesserte Technologien für den Druck hochwertiger Teile für die Endverwendung bei hohem Durchsatz und eine Reihe verbesserter Materialien machen den 3D-Druck für die Herstellung neuer Medizinprodukte praktikabel.
- Zusätzlich zur Herstellung von Endverbrauchsteilen bietet der 3D-Druck gewichtige Vorteile für die „hybride Produktion“, als Zwischenschritt, der parallel zu konventionellen Prozessen zur Anwendung gebracht wird, zum Beispiel zur Herstellung von Modellen, Werkzeugen, Halterungen und Vorrichtungen. Dies ist als Rapid Tooling bzw. Produktion von Fertigungshilfen bekannt.
Wie Austin berichtet, ist „das Kombinieren verschiedener Fertigungsmethoden für Startup-Unternehmen generell extrem wichtig, für PSYONIC jedoch umso mehr. Bei unserer Größe hätten wir mit anderen Prothetikunternehmen unmöglich konkurrieren können, wenn wir uns allein auf die traditionelle Fertigung hätten stützen müssen. Für Verfahren wie CNC-Bearbeitung und Spritzguss wären die Einstiegskosten für uns schlicht viel zu hoch gewesen, besonders bei Prototyping-Versuchen mit mehreren Iterationen. Doch dank des Aufkommens verschiedener Varianten des 3D-Drucks konnten wir das Prototyping auf eine Rekordzeit beschleunigen, Iterationen anpassen und Teile auch in geringen Mengen zu niedrigen Kosten produzieren. Der 3D-Druck, insbesondere mit 3D-Druckern von Formlabs, hat sich für den Entwicklungsprozess in einem Startup unserer Größe als absolut unverzichtbar erwiesen.“
Sehen wir uns an, wie PSYONIC den 3D-Druck bei der Herstellung der Ability Hand auf unterschiedliche Weisen einsetzt.
Betriebsinterne Fertigung von Kohlenstofffaserteilen
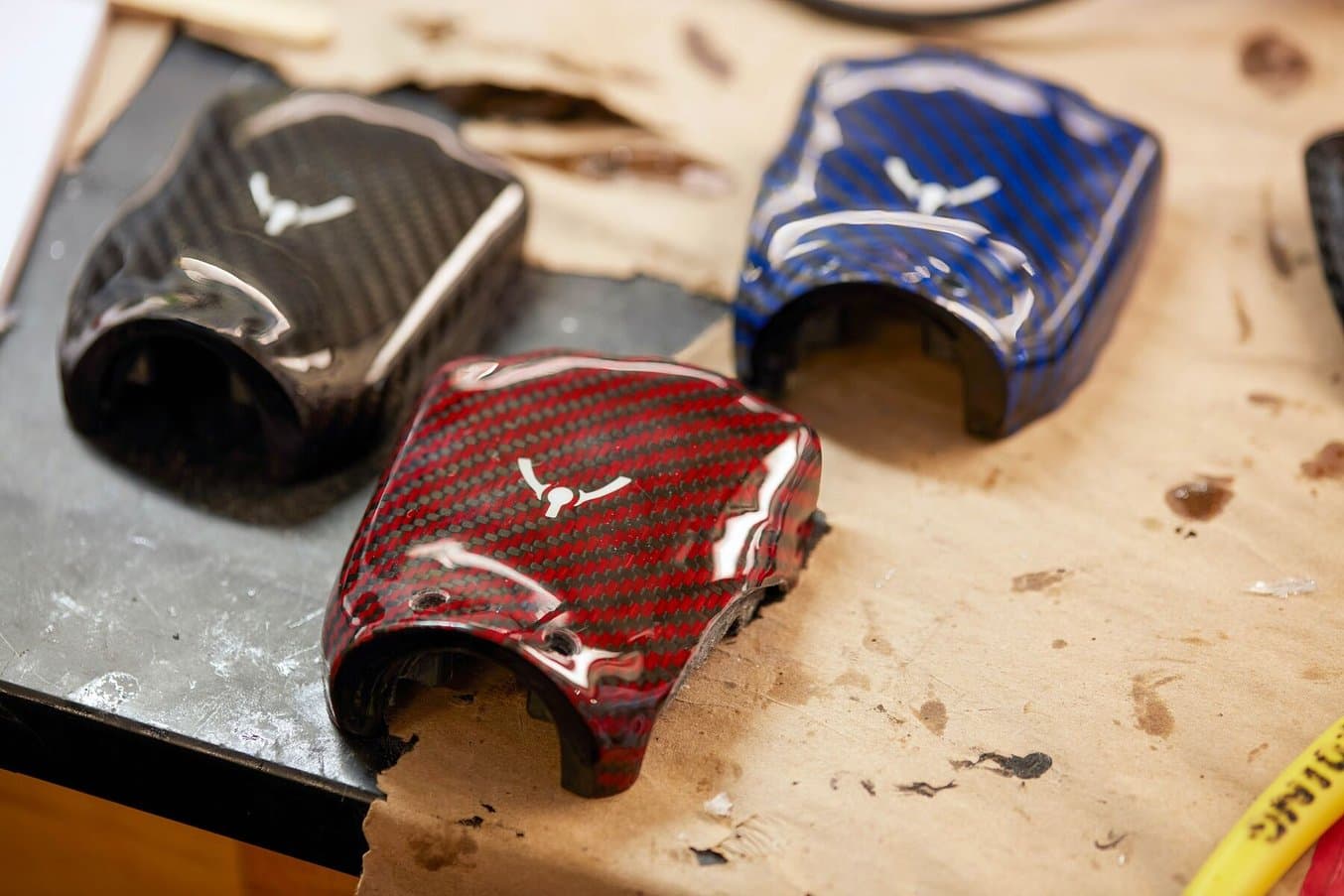
Dank der betriebsinternen Herstellung kohlenstofffaserverstärkter Formteile konnte PSYONIC das Design der Ability Hand erheblich verbessern.
Kohlenstofffaser oder Carbonfaser ist ein leistungsstarkes Material für derartige Konstruktionen, da es die Belastbarkeit und Steifigkeit der Ability Hand steigert, bei gleichzeitiger Verringerung ihres Gewichts. Herkömmliche Formen sind jedoch teuer zu produzieren, sodass die Iteration von Prototypen und die Fertigung der nötigen Formen für die Kleinserienproduktion unerschwinglich werden. Heute müssen sich Unternehmen allerdings nicht mehr zwischen additiver Fertigung und traditioneller CNC-Bearbeitung entscheiden, sondern können einfach beide Verfahren nutzen.
Austin erklärt: „Bei den frühen Iterationen der Form für die Carbonfaserteile hat der 3D-Druck eine sehr wichtige Rolle gespielt. Wir hatten nicht die nötigen Mittel für den Formenbau durch Verfahren wie Zerspanung. Also stellten wir stattdessen Formen aus High Temp Resin her. Die waren zwar zerbrechlich, aber hitzebeständig, sodass wir die Carbonfaserplatten exakt in die gewünschte Form pressen, sie zum Aushärten in einen Ofen mit hoher Temperatur stellen und dann auf unsere Hand aufkleben konnten.“
3D-gedruckte Formen verringern die Kosten und die Durchlaufzeit bei der Herstellung von Kohlenstofffaserteilen. Entwicklungsteams können Formen direkt drucken, und zwar kostengünstig und innerhalb von Stunden, sodass kein Schnitzen von Hand oder Fräsen mit CNC-Maschinen nötig ist. Mit High Temp Resin und Rigid 10K Resin können junge Medizintechnikunternehmen wie PSYONIC sogar komplexe Formen mit filigranen Details erstellen, die mit herkömmlichen Fertigungsmethoden nur schwer erzielbar wären.
Austin stellte aus High Temp Resin gleich mehrere Formen her und testete seinen Entwurf so auf erschwingliche Weise. Darüber berichtet er: „Wenn uns eine Geometrie nicht gefiel, änderten wir sie in der CAD-Software einfach ab, schickten sie wieder an den 3D-Drucker, bekamen eine neue Form aus High Temp Resin und konnten sofort neu iterieren. Für einen langfristig tragbaren Prozess wechselten wir irgendwann zu zerspanten Formen, aber für die frühe Prototypenentwicklung und kurzfristige Tests war der 3D-Druck mit High Temp Resin auf dem Form 3 unglaublich nützlich.“ High Temp Resin hat eine Wärmeformbeständigkeitstemperatur von 238 °C bei 0,45 MPa und hält der Hitze und dem Druck eines Autoklavs somit stand.
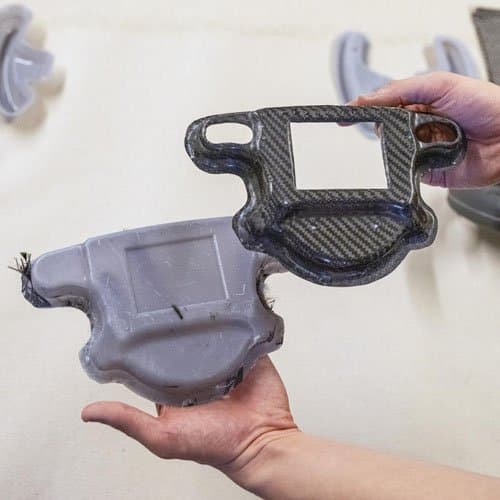
Fertigung von Kohlenstofffaserteilen mit 3D-gedruckten Formen
Laden Sie dieses Whitepaper zur Erstellung von Kohlenstofffaserteilen herunter. Es erläutert Designleitfäden für Verbundwerkstoffformen sowie schrittweise Anleitungen für die Prepreg- und Handlaminierung.
Reverse Engineering
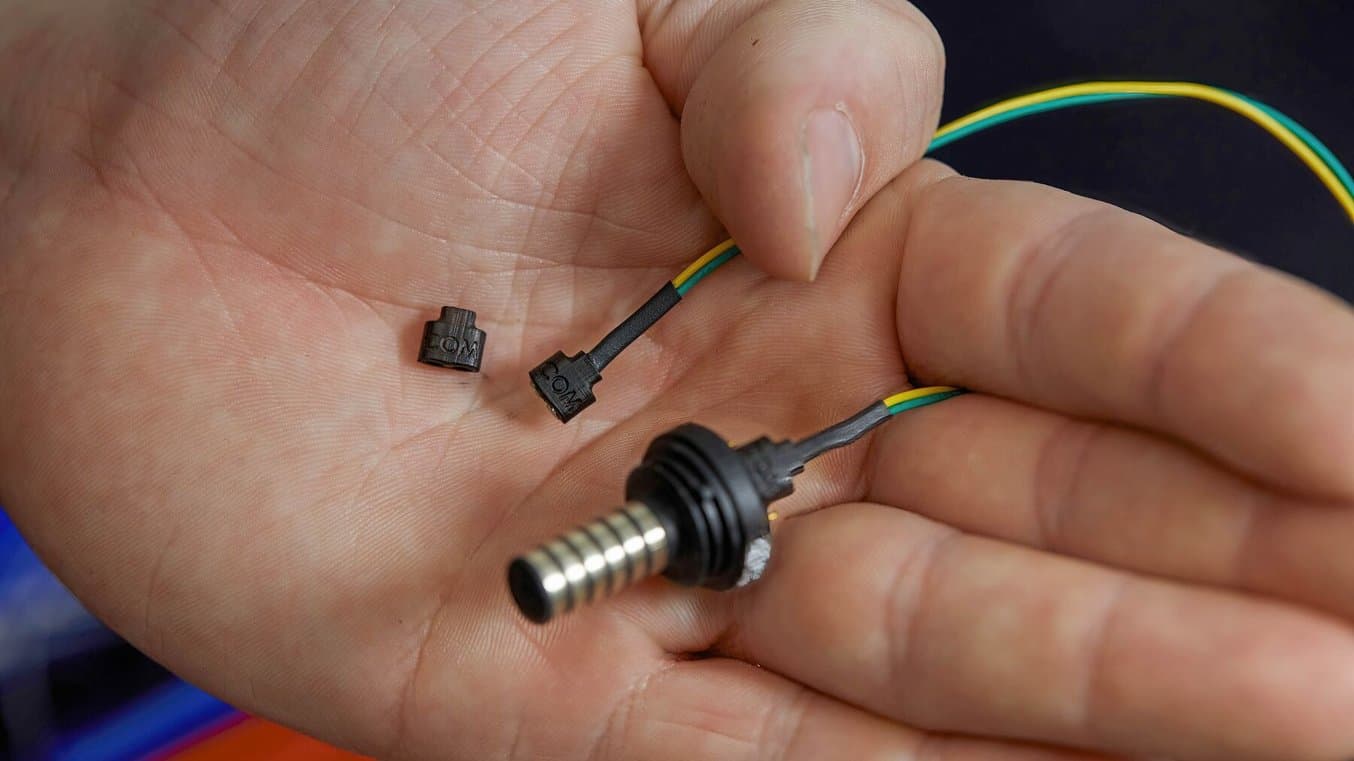
Um Kosten zu sparen, stellte PSYONIC kleine Verbindungen via Reverse Engineering her.
Reverse Engineering ist eine vielseitige Methode, um aus physischen Teilen digitale Designs zu erstellen, und kann ein wertvolles Hilfsmittel im Toolkit für die Prototypenfertigung darstellen. Mithilfe eines 3D-Druckers fertigen erfahrene Entwicklerteams über Reverse Engineering in kürzester Zeit Teile nach und beschleunigen damit die Produktion.
Jeder, der in der Medizinbranche tätig ist, wo selbst der Austausch kleiner Klammern Hunderte Dollar kosten kann, ist sich des hohen Preises proprietärer Bauteile wohl bewusst. Für kleine Unternehmen wie PSYONIC sind Ersatzteile oft unerschwinglich teuer.
Deshalb nahm PSYONIC die Sache selbst in die Hand: Abermals konnte sich das Unternehmen auf seine betriebsinternen 3D-Drucker stützen, um die Produktentwicklung schneller und günstiger zu machen. Austin berichtet: „Hin und wieder gibt es Teile, die mit den Produkten anderer Firmen kompatibel sein müssen. Manchmal sind diese käuflich erhältlich, doch wie so vieles in der Medizinbranche haben sie astronomische Preise. Handelt es sich um kleinere Teile, können wir deren Form relativ leicht über Reverse Engineering rekonstruieren und sie dann einfach selbst betriebsintern produzieren.“
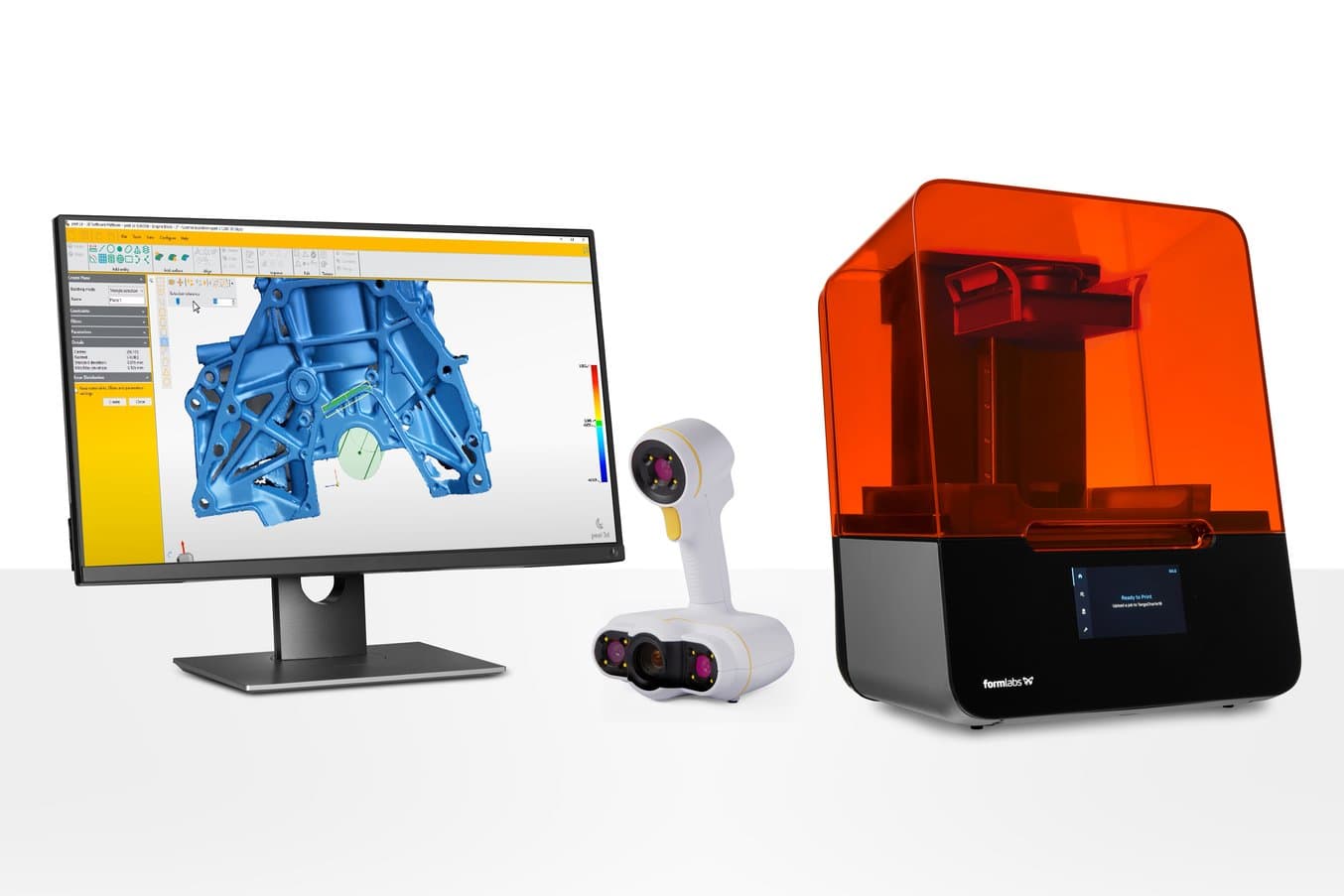
3D-Scan und 3D-Druck für Reverse Engineering und andere Anwendungen
Laden Sie unser Whitepaper herunter und erhalten Sie Einblick darin, wie Reverse Engineering durch den vereinten Einsatz von 3D-Scan und 3D-Druck möglich wird. Der Bericht gibt auch einen Überblick über den aktuellen Markt für 3D-Scanner.
Rapid Tooling für Spritzguss und Silikonformung
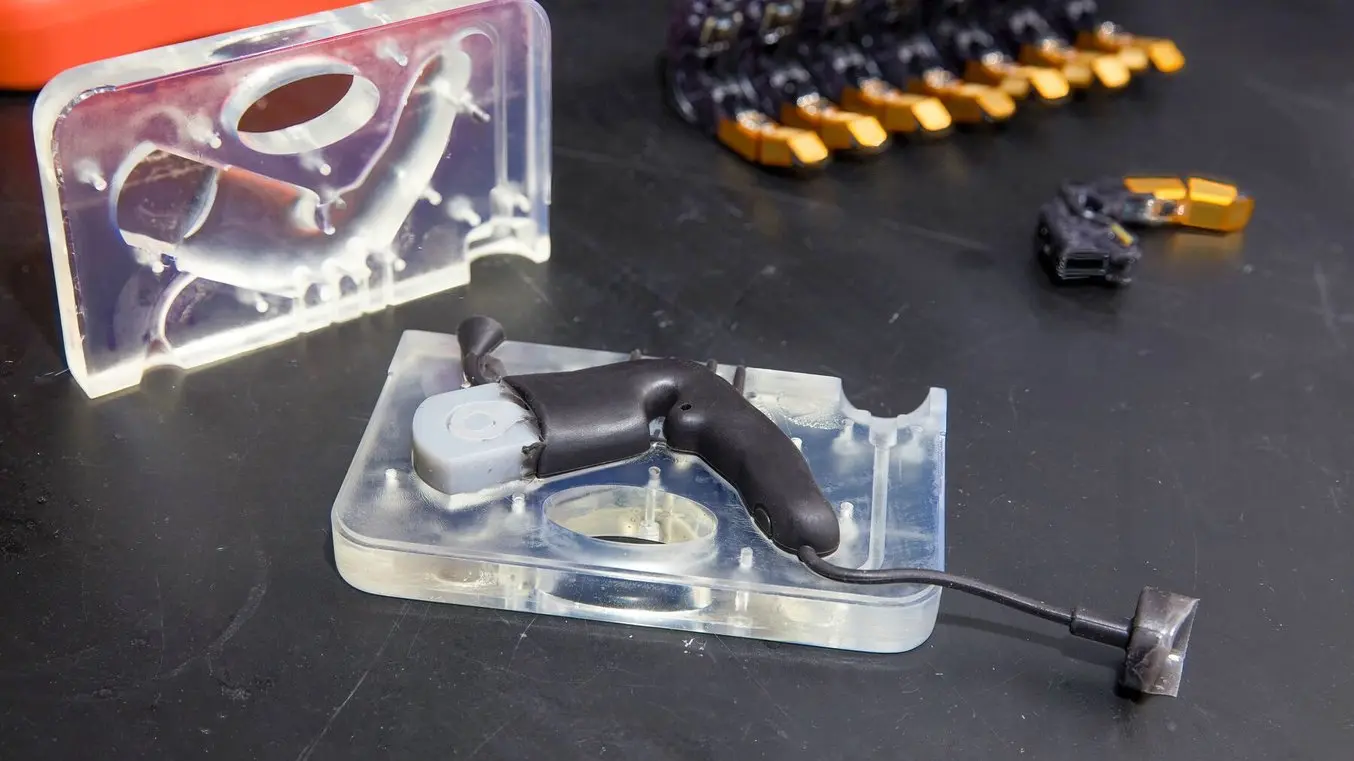
Der Spritzguss kleiner Stückzahlen als Teil des Entwicklungsprozesses für Medizinprodukte ist für viele Entwicklerteams eine echte Bereicherung. In der Anfangsphase der Produktentwicklung stellt die Herstellung von Endverbrauchsteilen in geringen Mengen mithilfe von Rapid Tooling eine effektive und günstige Lösung dar, um eine Brücke zwischen Prototyping und der Massenproduktion mit teurem Werkzeug zu schlagen. Um Kosten zu sparen, fertigte das Team von PSYONIC zunächst sämtliche Bauteile der Ability Hand über 3D-Druck, einschließlich der Finger. Schnell zeigte sich aber, dass die Finger robuster sein mussten, sodass das Team statt der Finger nun Gussformen 3D-druckte.
Über diesen Übergang berichtet Akhtar: „Eine unserer größten Herausforderungen war es, dass die Hand in der Fertigung kostengünstig sein musste, aber dennoch robuster als alle anderen vergleichbaren Produkte. Als wir mit der Produktion dieser Hände begannen, stellten wir sie erst komplett über 3D-Druck her und erreichten eine sehr hohe Kosteneffizienz. Doch im Gespräch mit Hunderten von Patienten und Ärzten war ihre größte Beschwerde, dass die 50 000 € teure bionische Hand leicht kaputtging. Sie stießen versehentlich gegen die Tischkante, und da die Finger aus steifen 3D-gedruckten Komponenten bestanden, brachen sie am Gelenk und gingen kaputt. Menschliche Finger sind aber flexibel. Wenn man sich stößt, biegen sie sich und kehren dann zu ihrer Ausgangsstellung zurück. Genau so eine Funktionalität wollten wir auch in unsere Handprothese einbauen, damit sie strapazierfähiger ist als alle anderen Produkte.“
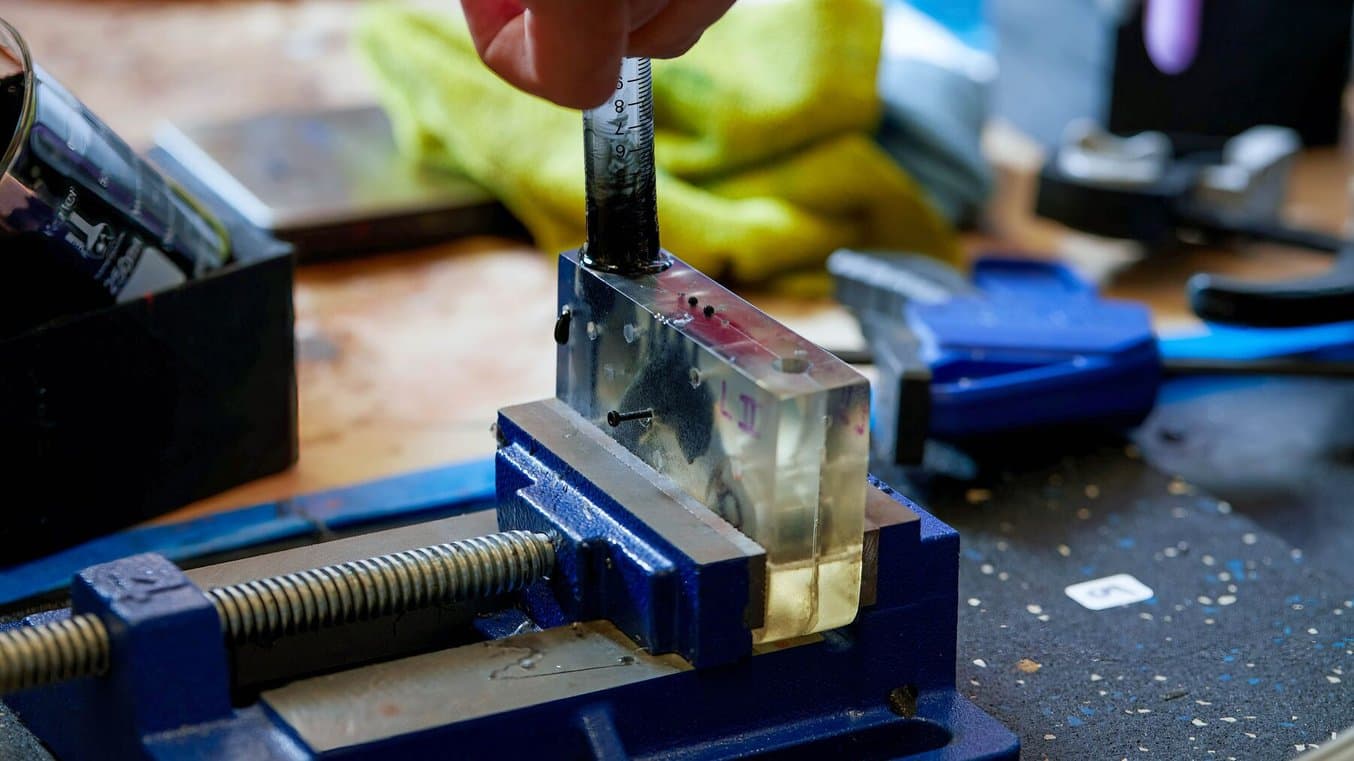
Zu Herstellung seiner Gussformen setzte das Team zunächst FDM-3D-Drucker (Schmelzschichtung) ein. FDM-Drucker drucken schnell und kostengünstig, halten anspruchsvollen Bedingungen aber oft nicht stand. Da Formen besonders glatt und hochauflösend sein müssen, ist der SLA-3D-Druck die bessere Wahl. Das bestätigt auch Austin: „Die Fertigung der Finger war etwas, für das wir lange Zeit FDM-3D-gedruckte Formen eingesetzt haben. Diese verursachten beim Spritzguss aber eine Menge Probleme, vor allem aufgrund der unzureichenden Oberflächenqualität. Sie wiesen die für FDM-Druckteile typischen Streifen auf, die sich dadurch ergeben, dass Material Schicht für Schicht aufgetragen wird. So hatten am Ende auch alle unsere Gussteile diese seltsamen Streifenmuster auf der Oberfläche. Als wir schließlich zum Druck mit Clear Resin wechselten, erzielten wir dank der höheren Auflösung eine weitaus glattere Oberfläche. Wir fertigten diese Formen, indem wir das Negativ der gewünschten Finger- oder Daumenform nahmen, dies aus einem Materialblock entfernten und Angusskanäle und Einlässe zum Einspritzen des Zweikomponenten-Silikons hinzufügten. Sobald diese Form entworfen und 3D-gedruckt war, setzten wir einen 3D-gedruckten Knochen in sie ein, der das Skelett des Fingers bildet.“
Austin erklärt weiterhin: „Wir spannten die Form aus Clear Resin darum, mischten ein Zweikomponenten-Silikon mit Platin-Katalysator, spritzten es mithilfe einer Injektionsspritze von Hand in ein Loch in der Form und füllten die Form so mit dem Zweikomponenten-Silikon, dass der Finger komplett umschlossen war. Wenn wir die Form öffneten, hatten wir dann einen schönen neuen Finger vor uns. Diese Formen haben wir sehr, sehr oft einsetzen können. Man kann sie wieder und wieder verwenden, zigmal wahrscheinlich. Die einzige Einschränkung von Clear Resin ist der Verschleiß der Formen mit der Zeit, hauptsächlich durch den Gebrauch an sich. Wenn das passiert, ist es aber ganz einfach, einen neuen Druckauftrag zu starten. Bei der hohen Auflösung, die wir nutzen, dauert es dann 24 Stunden, bis wir eine neue Form haben und mit dem Formen der Finger weitermachen können.“
Austin nutzte beim Druck auf seinem Form 3 die höchstmögliche Auflösung (25 Mikrometer), sowohl bei Teilen für die Endverwendung als auch bei Formen. Dazu erläuterte er: „Wir drucken mit all unseren Materialien in der höchsten verfügbaren Auflösung. Bei den Teilen aus Tough 1500 Resin liegt das daran, dass sie präzise aneinandergefügt werden. Sie haben eine sehr enge Passung im Inneren der Hand und um die von ihnen umschlossenen Komponenten herum. Jegliche Variationen oder Toleranzen könnten hier übermäßige Reibung bei der Bewegung oder eine unzureichende Ausrichtung zusammengefügter Bauteile verursachen. Deshalb müssen sie so präzise wie möglich gefertigt werden, um eine optimale Passung und Funktionalität zu erreichen. Die Formen drucken wir in der höchsten Auflösung, weil die Oberflächenbeschaffenheit so glatt wie möglich sein muss. Danach waschen wir die Teile gründlich im Form Wash, um eine besonders glatte Oberfläche auf der Form zu erhalten, die sich auch im darin gegossenen Silikon widerspiegelt.“
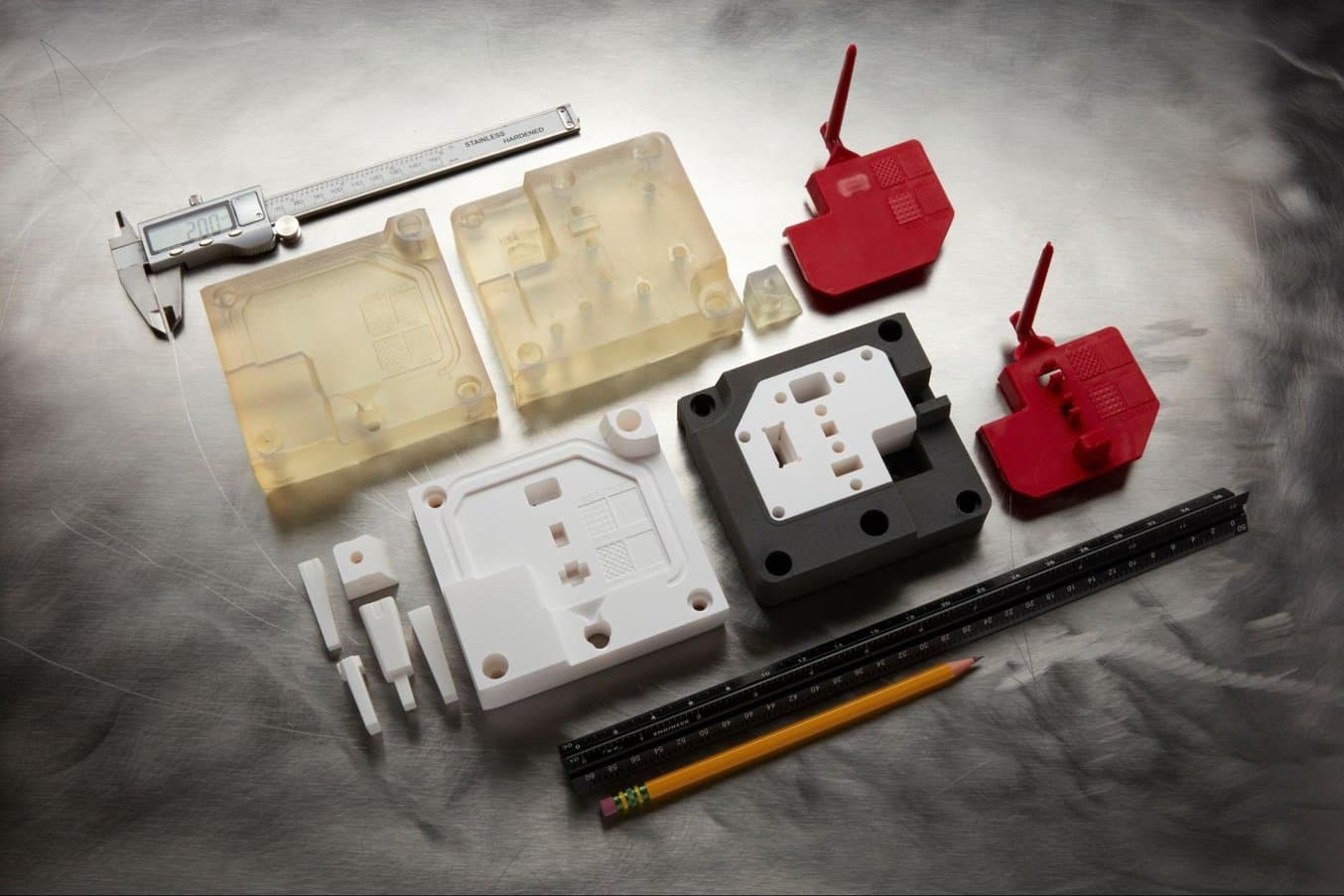
Leitfaden zum Rapid Tooling
In diesem Whitepaper sprechen wir über die Kombination von Rapid Tooling mit traditionellen Herstellungsverfahren wie Spritzguss, Vakuumformen oder anderen Gießverfahren.
Aus Kundenfeedback entsteht Rapid Prototyping
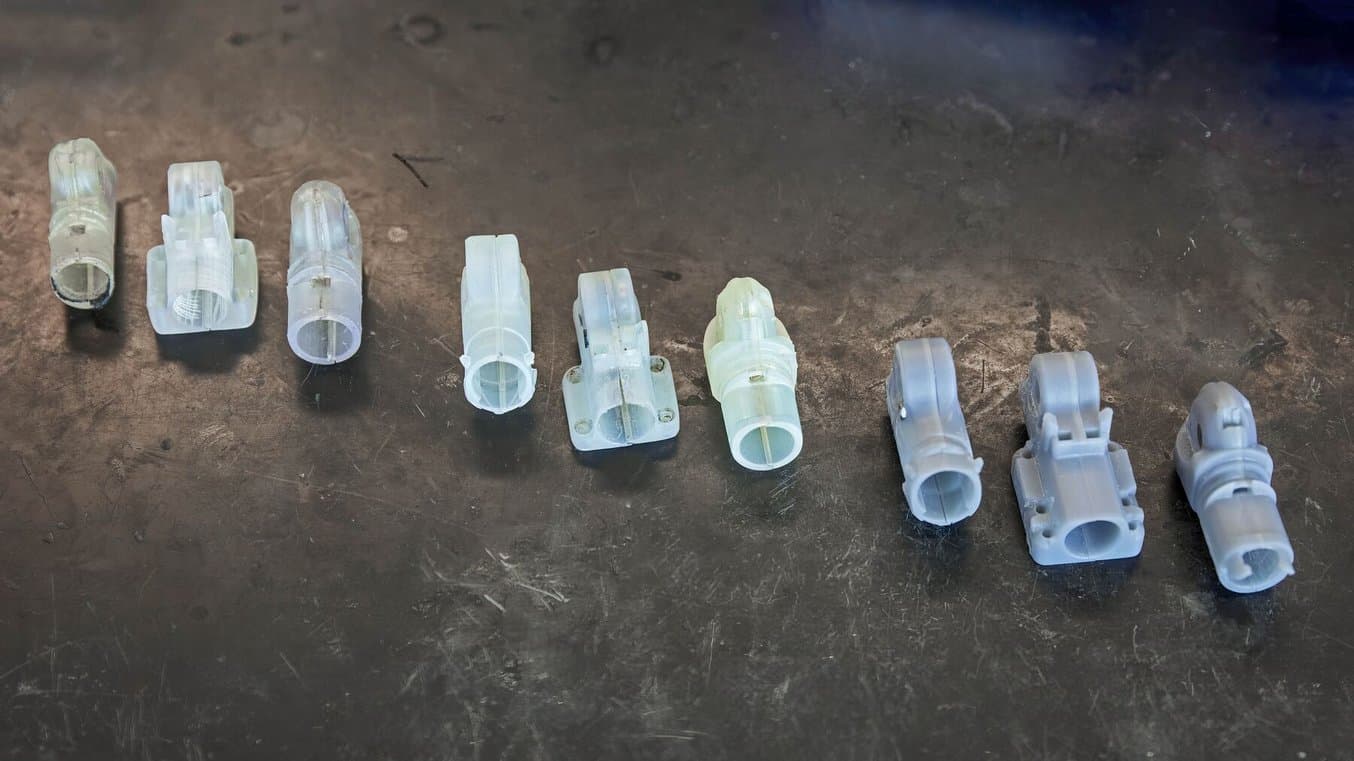
In den letzten paar Jahren hat PSYONIC Prototypen für zahllose Teile erstellt und dabei Rückmeldungen von Kunden in das Design der Ability Hand einbezogen.
Unabhängig von der Art des Geräts spielt Rapid Prototyping bei Entwicklungsprozessen eine essenzielle Rolle. Bei Medizinprodukten ist dies umso mehr der Fall, wenn von Patient*innen und Anwender*innen deutliches Feedback zu einem Teil eingeht. Hersteller von Medizinprodukten durchlaufen oft Hunderte von Prototypen für ein einziges Bauteil, bevor sie bereit für Feldversuche sind oder gar behördlichen und klinischen Ansprüchen gerecht werden. Diesem Problem ist Austin bei der Entwicklung der Ability Hand aus nächster Nähe begegnet. „Es ist mehrmals vorgekommen, dass einem Patienten etwas auf eine Weise kaputtgeht, die ich nicht für so wahrscheinlich hielt, wie sie tatsächlich ist, wofür es aber eine einfache Lösung gibt. Dann nahm ich eine Änderung vor, implementierte sie, erstellte einen Prototyp, führte einen Test durch und hatte eine neue Ability Hand parat, die binnen ein oder zwei Wochen versendet wurde“, berichtet Austin.
Austin erklärt: „Wir versuchen unsere Fertigungsmethoden zu variieren, um die jeweils anstehende Aufgabe optimal anzugehen. Viele unserer Prototypen werden zuerst mittels FDM-3D-Druck aus Kunststoff hergestellt oder mit SLA-Druck aus Kunstharz, und sobald wir uns auf ein größtenteils endgültiges Design geeinigt haben, lassen wir das Teil beispielsweise durch CNC-Bearbeitung aus Metall neu fertigen, was teurer und zeitaufwendiger ist, aber auf lange Sicht haltbarer. Einige Dinge sind schon in der SLA-3D-gedruckten Variante vollkommen benutzbar und lassen sich gut aus Kunstharz umsetzen. Andere Dinge erreichen durch den Wechsel zu Metall jedoch eine höhere Strapazierfähigkeit. Da uns all diese Optionen zur Verfügung stehen, können wir sie ganz nach Wahl kombinieren, um jedes Bauteil zu optimieren und sicherzustellen, dass wir für unser Geld die größtmögliche Leistung bekommen. Die niedrigsten Fertigungskosten, aber dennoch höchste Leistungsfähigkeit.“
3D-Druck von Endverbrauchsteilen
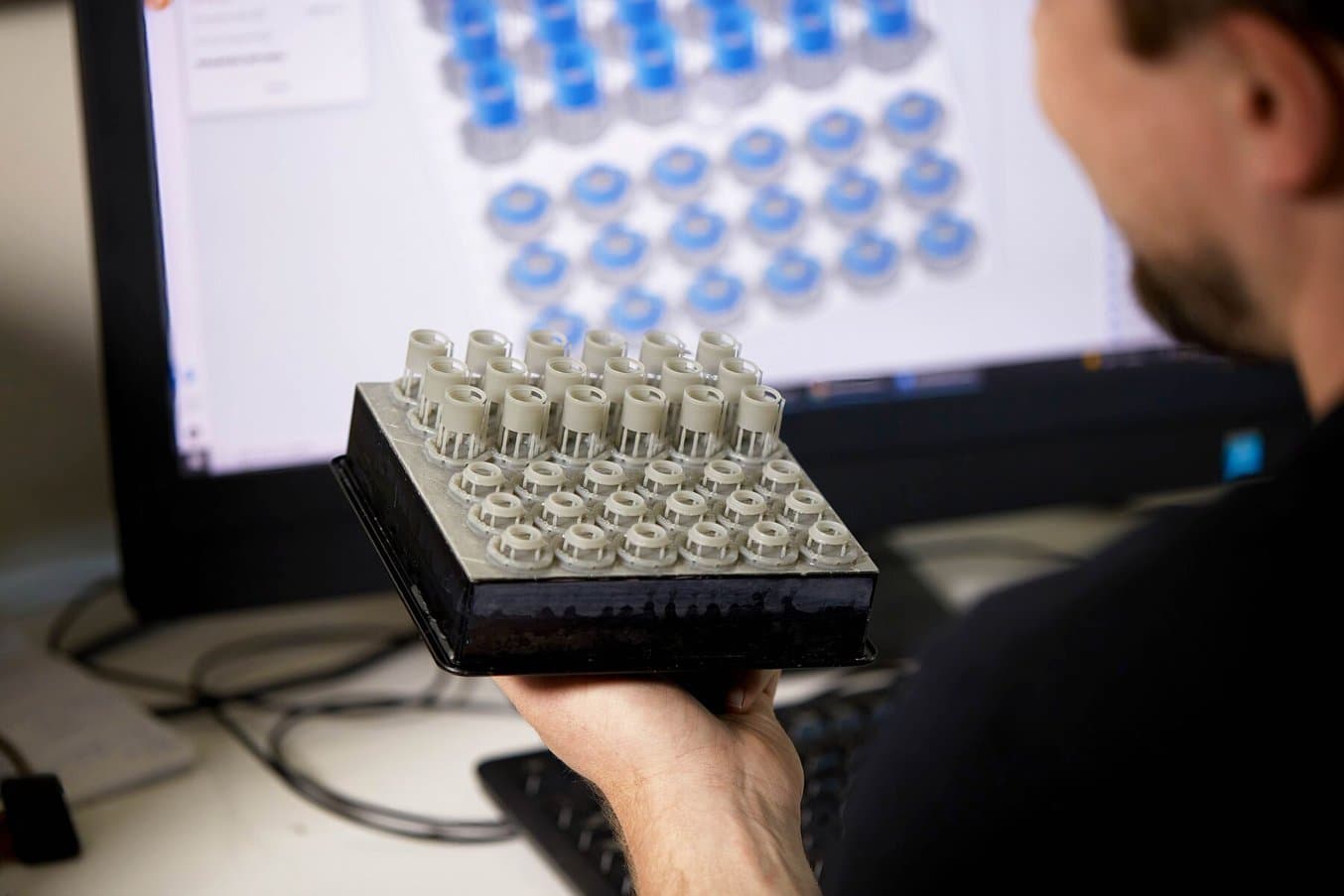
Hier hält Austin eine Reihe frisch aus Tough 1500 Resin gedruckter Teile für die Endverwendung in der Hand.
Dank jüngster Fortschritte in den 3D-Druckmaterialien sind viele Teile bereits unmittelbar nach dem Druck als Modelle für Kundenpräsentationen oder gar als Endverbrauchsteile geeignet, wodurch der Bedarf an teurem, konventionellem Fertigungswerkzeug sowie die Entwicklungszeit deutlich gesenkt werden.
Mit Tough 1500 Resin als Druckmaterial fand Austin ein Material, das für die Herstellung gleich mehrerer endgültiger Bauteile der Ability Hand hervorragend geeignet ist.
„Zum Teil nutzen wir den SLA-3D-Druck zwar hauptsächlich für Prototypen, doch viele unserer Druckteile sind tatsächlich für die Endverwendung bestimmt. Dies gilt insbesondere für Teile aus Tough 1500 Resin, die allen anderen 3D-Druckteilen in derselben Auflösung überlegen sind und gleichzeitig viel kosteneffizienter als Spritzguss. Für unsere Zwecke, unser Produktionsvolumen und die Anforderungen an unsere Teile hinsichtlich Stärke, Auflösung, physischer Eigenschaften, thermischer Beständigkeit und Stoßfestigkeit ist Tough 1500 Resin wirklich das Beste, das uns je untergekommen ist, und wir setzen es weiterhin in all unseren kommerziellen Produkten ein“, teilt Austin uns mit.
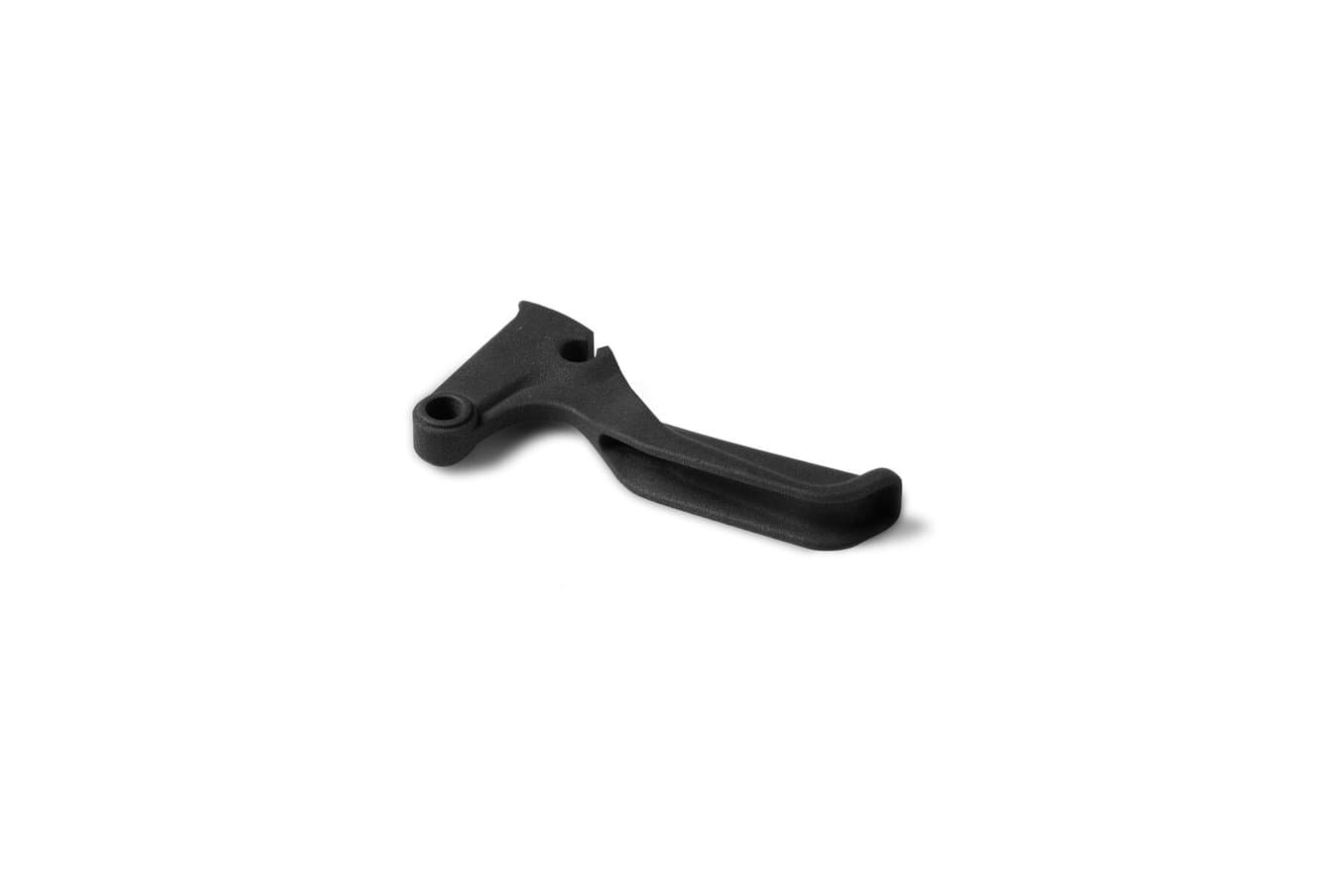
Kostenlosen Probedruck anfordern
Sehen und fühlen Sie selbst die Qualität von Formlabs. Wir senden Ihnen einen kostenlosen Probedruck an Ihren Arbeitsplatz.
Produkte, die alles überstehen
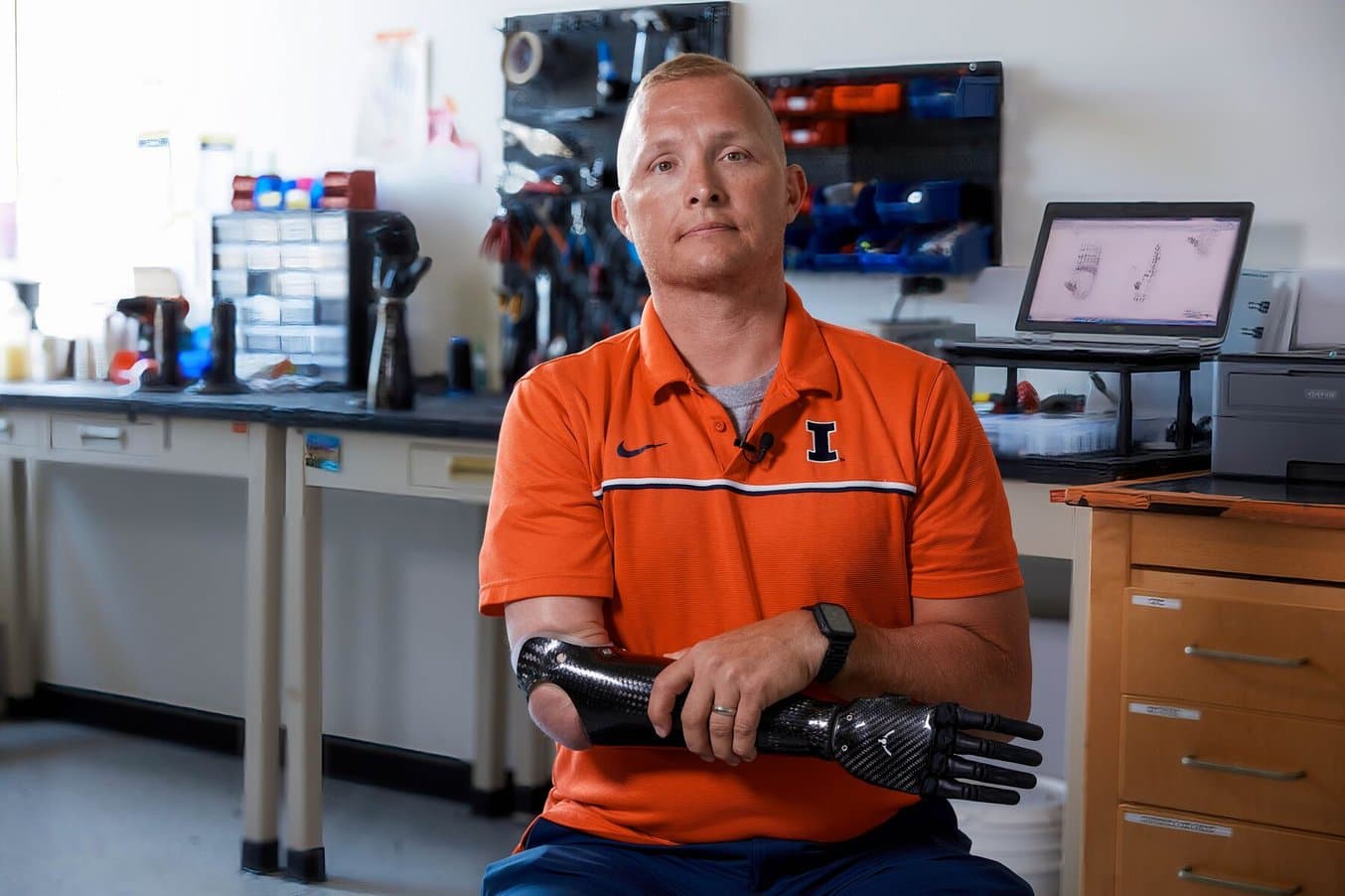
Das Geschäft von PSYONIC weiter auszubauen, war Akhtar und seinem Team ein Ansporn, und hierfür waren moderne, hybride Fertigungstechniken und innovative Maschinenbaulösungen notwendig. Als Nächstes hat sich PSYONIC zum Ziel gesetzt, seinen Betrieb zu skalieren und sein Produkt auf der ganzen Welt zu verkaufen. Bisher beschränkt sich das Unternehmenswachstum auf den nordamerikanischen Markt, mit einem starken Produktionsanstieg der Ability Hand Ende 2022.
„Was unsere Patienten wollen, ist ihren Alltag ganz normal zu bestreiten. Mit den auf dem Markt verfügbaren Geräten konnte man oft aber nicht einmal einfache Aufgaben erledigen, und wir schaffen nicht nur das, sondern noch weitaus mehr. Das liegt an den vielen Innovationen, die wir im Design der Ability Hand umgesetzt haben“, so Akhtar. Anderson fügt hinzu: „Dank des sensorischen Feedbacks konnte ich Anfang dieses Jahres zum ersten Mal fühlen, wie ich die Hand meiner Tochter mit dieser Prothese berühre.“