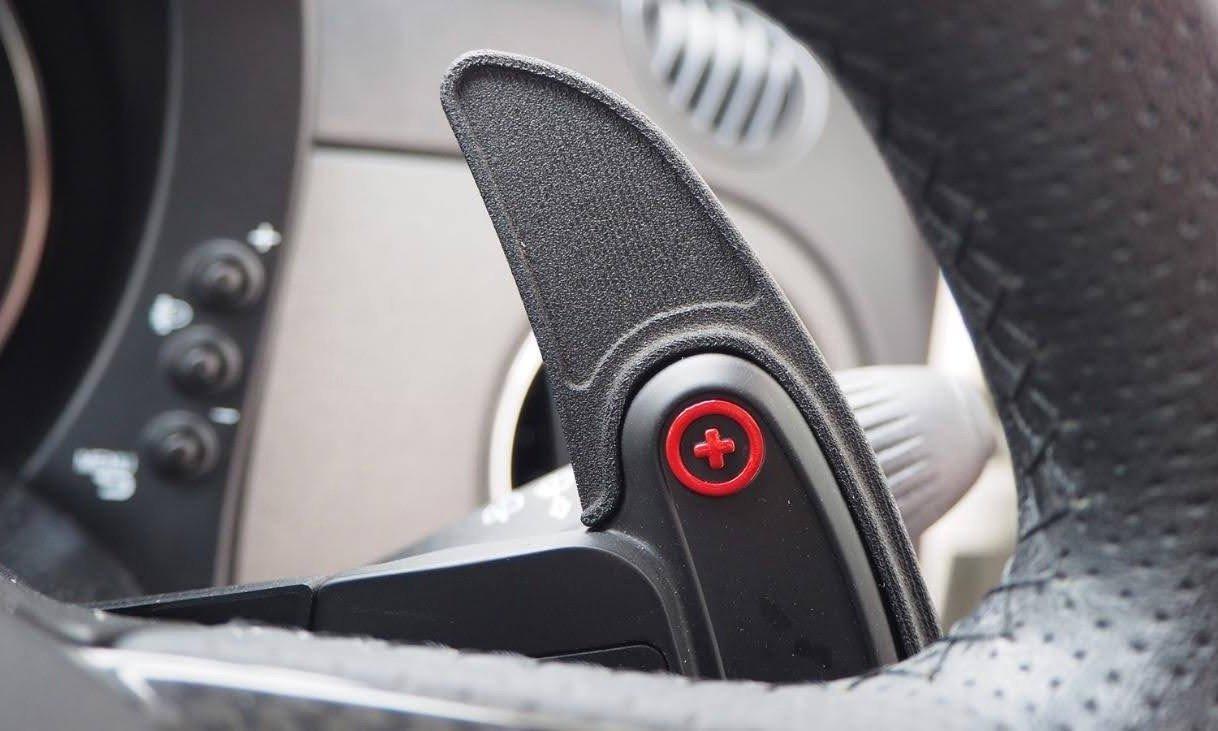
Japan steht seit Jahrzehnten im Zentrum der Innovation in der Automobilindustrie. Die Prinzipien der schlanken Produktion, die ihren Ursprung in der Philosophie japanischer Automobilhersteller haben – genau wie „Kaizen“ oder kontinuierliche Verbesserung – werden in aller Welt in Weiterbildungen für Führungskräfte gelehrt und als grundlegende Protokolle für alle Arten von Produktion angepriesen. Der Leitgedanke der Innovation und der kontinuierlichen Entwicklung, der bei großen Erstausrüstern startete, ist auch beim japanischen Aftermarket-Automobilhersteller Codetech CAM sehr lebendig.
Codetech hat sich in der umkämpften japanischen Automobilbranche eine Nische geschaffen, indem das Unternehmen Nachrüstungsteile für importierte Autos anbietet. Sein Kundenstamm mag zwar klein sein, doch Liebhaber importierter Autos haben hohe Ansprüche, und die Nachfrage nach Personalisierung und luxuriösen Zusatzausstattungen steigt.
Codetech bedient diese Nachfrage, indem es ein reaktionsschnelles und flexibles Fertigungsmodell aufbaut, das auf hochleistungsfähigen 3D-gedruckten Teilen basiert. Durch den Einsatz der Technologien Stereolithografie (SLA) und selektives Lasersintern (SLS) ist Codetech in der Lage, seinen Kunden Lösungen anzubieten, die sowohl das Fahrerlebnis als auch die Ästhetik des importierten Fahrzeugs verbessern. „Mit einem fundierten Verständnis für die Bedürfnisse der Kunden und den technischen Möglichkeiten, diese umzusetzen, gibt es zahllose Möglichkeiten, interessante Produkte zu kreieren“, so Masato Uchida, Leiter des Design-Labors bei Codetech.
Die Lücke auf dem Markt für Importautos finden
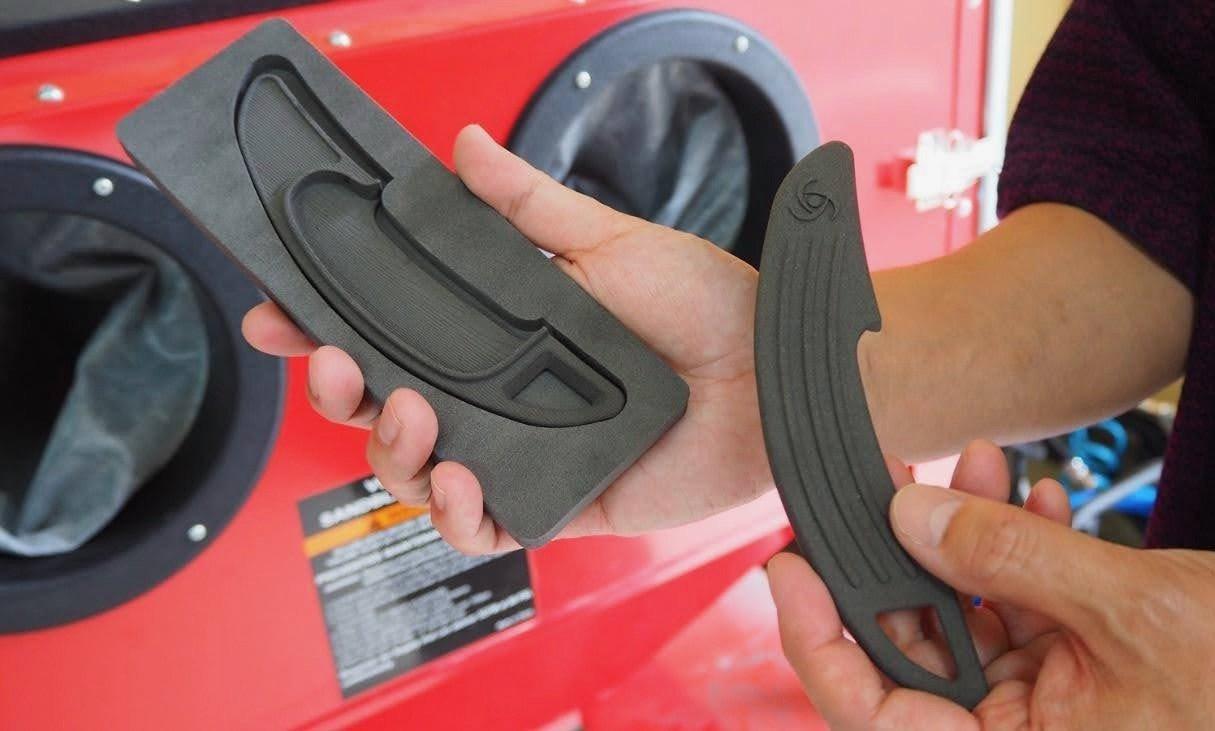
Diese Core-OBJ-Schaltwippenerweiterung ist ein beliebtes Produkt von CodeTech. Sie verlängert die originalen Abarth-Lenkradschaltwippen und sorgt für eine angenehmere Größe und Textur für die Finger.
Japanische Autohersteller wie Toyota, Honda und Nissan beherrschen die große Mehrheit des japanischen Marktes, aber europäische Marken wie BMW oder Volkswagen werden von einer kleinen Gruppe von Verbrauchern als Luxusartikel geschätzt. Diese wünscht sich individualisiertes Zubehör und Nachrüstungsteile, aber es ist fast unmöglich, Hersteller von Automobilbauteilen zu finden, die eine große Bandbreite an Erstausrüstern (OEMs) abdecken.
Je komplexer die Softwaresysteme für Fahrzeuge werden, desto schwieriger wird es, Teile auf dem Aftermarket zu finden. Wenn sich die Softwaresysteme in einem neuen Fahrzeugmodell ändern, werden elektrische Bauteile häufig ebenfalls aktualisiert, sodass die Nachrüstungsteile auf dem Aftermarkte veraltet sind.
CodeTech ist in der Lage, dort anzusetzen, wo andere Aftermarket-Hersteller es nicht können, weil das Unternehmen auf eine flexiblere Fertigungsmethode setzt: den 3D-Druck.
Wie 3D-Druck Reverse Engineering ermöglicht
Traditionelle Fertigungsverfahren der Automobilindustrie, wie Spritzgießen, CNC-Bearbeitung, Blasformen oder Sandguss, sind für Erstausrüster effiziente Methoden der Massenproduktion. Für Hersteller auf dem Aftermarket, die Bauteile durch Reverse Engineering anpassen oder nachfertigen müssen, ist eine kosteneffiziente Fertigung mit diesen Methoden unmöglich.
Das CodeTech-Team wusste von Anfang an, dass es eine flexiblere und kostengünstigere Fertigungsmethode würde anwenden müssen, um konsistent und kostengünstig Teile herzustellen, die mit den massenproduzierten Importautos kompatibel sind.
Uchida und das Team des Design-Labors begannen mit dem SLA-3D-Drucker (Stereolithografie) Form 1, fügten dann den Form 2, Form 3 und jetzt den SLS-Drucker Fuse 1+ 30W hinzu. So konnte das Team mit der steigenden Nachfrage seines kleinen Kundenstamms seine Kapazität vergrößern. Wenn das Team eine Anfrage für ein neues Teil erhält, kann es das OEM-Bauteil durch 3D-Scannen und CAD mittels Reverse Engineering fertigen. Sobald Uchida die Datei hat, kann er sofort drucken und ein fertiges Endbauteil liefern, das ganz ohne teure Produktionswerkzeuge gefertigt wurde. „Am Fuse 1 gefällt mir unter anderem, dass ich von Anfang an ein fast fertiges Produkt drucken kann“, sagt Uchida.
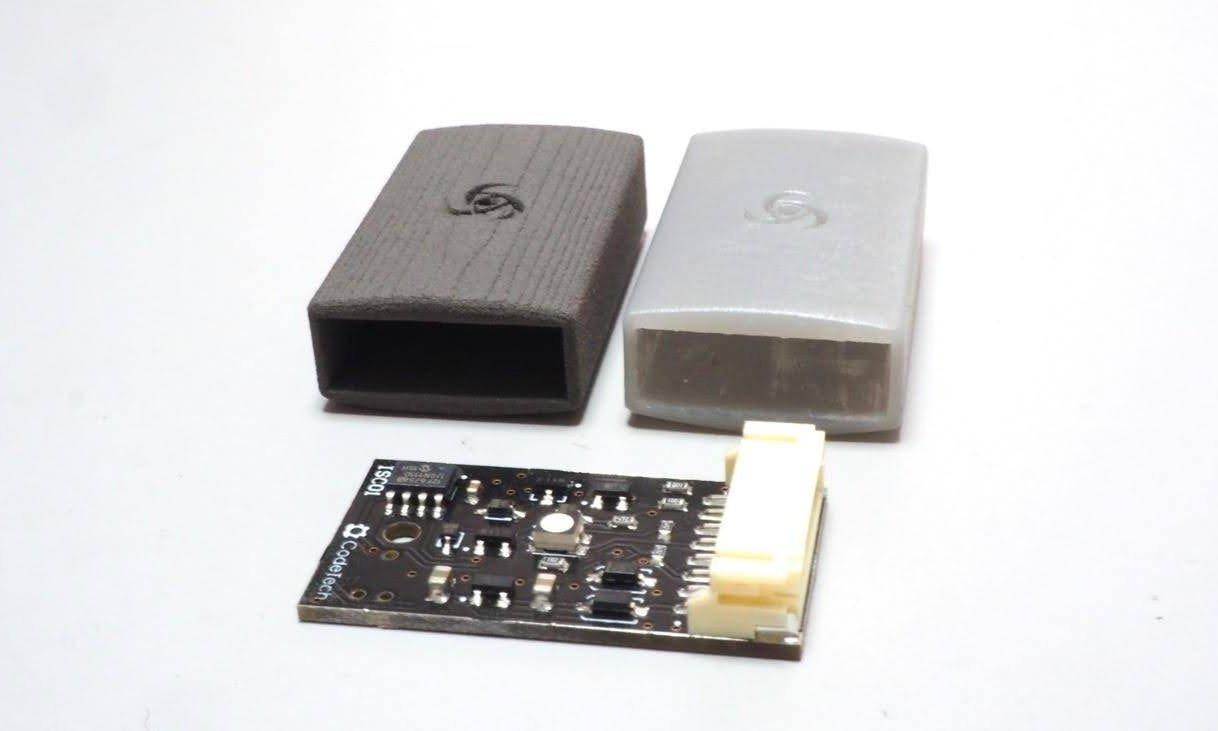
Diese Elektronikgehäuse wurden auf dem SLA-Drucker Form 3 innerhalb kurzer Zeit aus Draft Resin prototypisiert und dann als fertiges Endbauteil auf dem SLS-Drucker Fuse 1+ 30W gedruckt.
Die Marktfähigkeit von 3D-gedruckten SLS-Teilen wurde kürzlich auf einer Automobilmesse bestätigt. Als kleine Demonstration dessen, wozu CodeTech in der Lage ist, hatte Uchida schnell ein Computerchip-Gehäuse entworfen und einen Prototyp auf dem Form 3 aus Draft Resin gedruckt. Auf der Messe erhielt er unerwartet positives Feedback – die Leute wollten wissen, wann das Produkt zu kaufen sein würde. Uchida kehrte ins Design-Labor zurück und druckte eine größere Charge auf dem Fuse 1+ 30W aus Nylon 12 Powder.
„Die Messe kam nur zustande, weil ich mit dem Fuse 1 direkt nach dem Modellieren ein fast fertiges Produkt erstellen konnte. Ich finde, diese Schnelligkeit ist notwendig und sehr zeitgemäß.“
Masato Uchida, Leiter des Design-Labors bei CodeTech
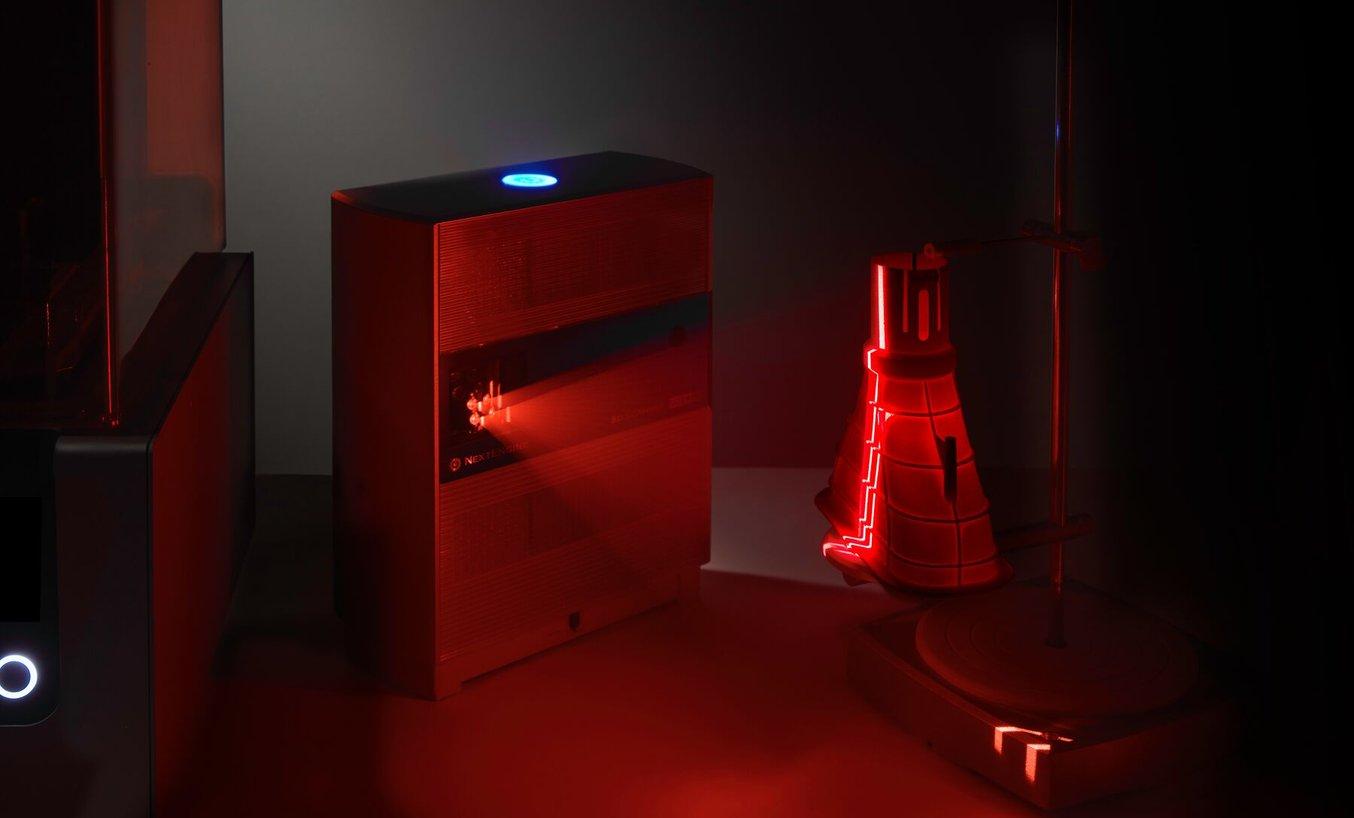
3D-Scan und 3D-Druck für Reverse Engineering und andere Anwendungen
3D-Scan- und 3D-Druckverfahren lassen sich zum Nachbau, zur Restauration, für Reverse Engineering, Metrologie und viele weitere Anwendungen einsetzen. Laden Sie unser Whitepaper herunter, um diese Anwendungen kennenzulernen, und erfahren Sie, womit Sie beginnen sollten.
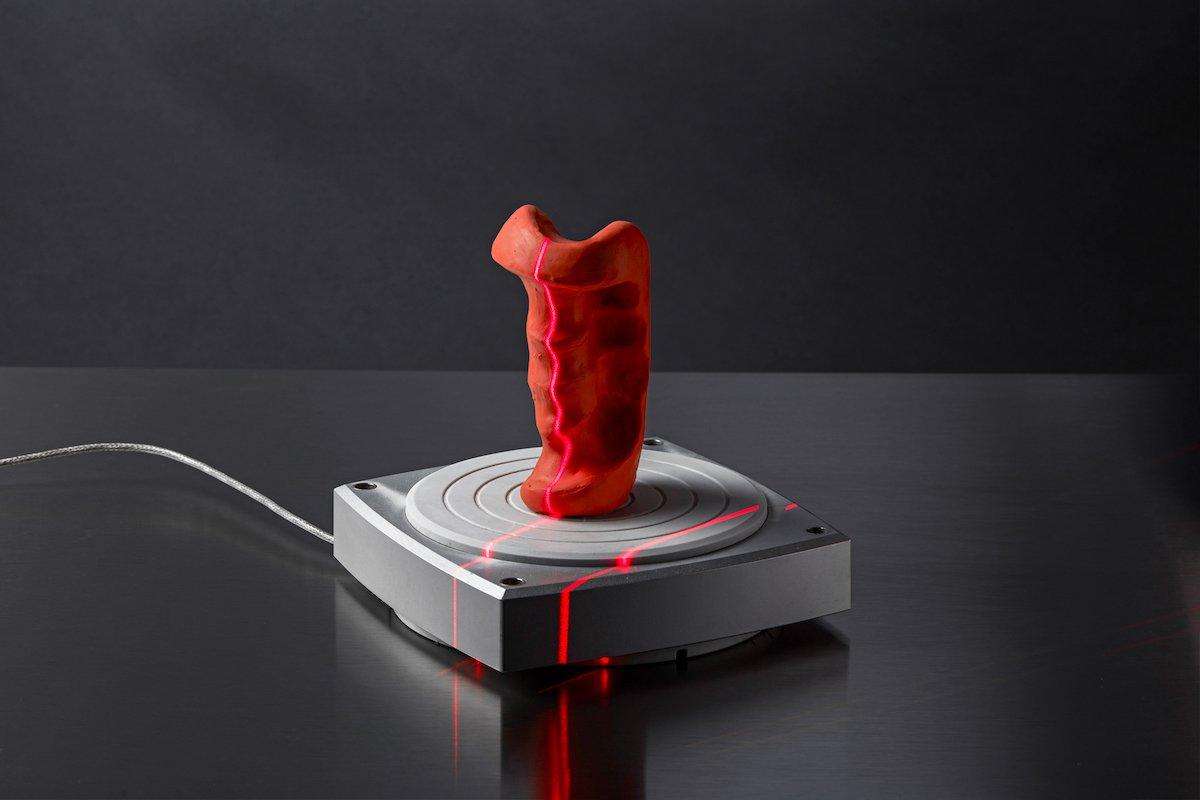
Vom 3D-Scan zum 3D-Druck: Reverse Engineering im Schnellverfahren für Maschinenüberholung, Montagevorrichtungen und Aftermarket-Produkte
In diesem Webinar erhalten Sie einen detaillierten Einblick darin, wie Sie 3D-Scan einsetzen, um in Kombination mit CAD-gestütztem Reverse Engineering und 3D-Druck das Design und die Produktion von Teilen zu verbessern.
Flexibles Angebot und Online-Bestellungen
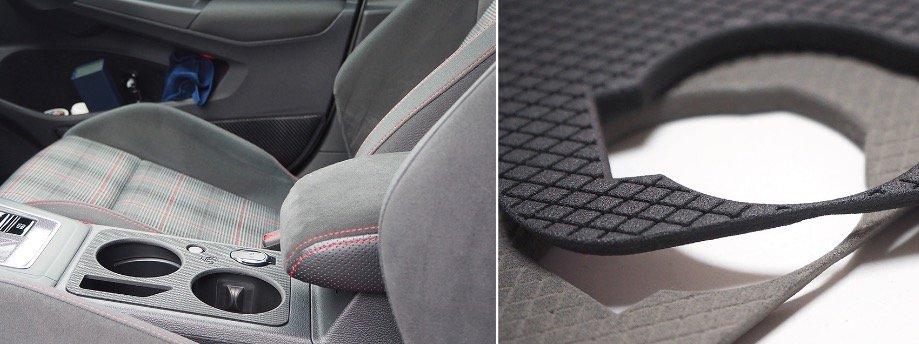
Die Becherhalter für den Volkswagen Golf 8 werden sandgestrahlt und anschließend mit einer mattschwarzen Urethanbeschichtung beschichtet (links). Die dünne Kante des Halters (rechts im Bild) wäre mit herkömmlichen Fertigungsmethoden unmöglich zu erstellen; der betriebsinterne 3D-Druck ermöglicht es, Teile mit derart engen Toleranzen und feinen Details zu erstellen.
Mit einem digitalen Inventar und Fertigungsprozessen gestützt durch 3D-Druck kann CodeTech schnell auf Nachfrageänderungen reagieren und muss keine großen physischen Lagerbestände aufbauen. Durch das Design und die Produktion von Einzelanfertigungen, die dann für die Online-Werbung verwendet werden, kann CodeTech die Nachfrage abschätzen, bevor es in die Produktion geht. Das Team kann flexibler und effizienter arbeiten und es vermeiden, Ressourcen für Produkte auszugeben, die sich nicht verkaufen lassen. Wenn es eine Nachfrage gibt, können die Fertigungsabläufe umgestellt werden, um sie sofort zu bedienen.
Im Fall eines Becherhalters, der für die Mittelkonsole eines Volkswagen-Fahrzeugs entworfen wurde, veröffentlichte CodeTech zunächst Werbung für das Produkt und stellte seinen Produktionsablauf dann entsprechend um. Uchida druckt 25 Becherhalter pro Konstruktionskammer; dank des Packalgorithmus der Fuse-Serie und des Pulverrecyclings ist eine derartige Kleinserienfertigung möglich. Das Becherhalter-Design erfreute sich sofort großer Beliebtheit, da seine dünnen Außenkanten perfekt in eine bestehende VW-Konsole passen, aber zu dünn für die Fertigung mit herkömmlichen Verfahren wären – dies ist ein Fall, in dem die additive Fertigung Teile nicht nur nachbildet, sondern sogar verbessert.
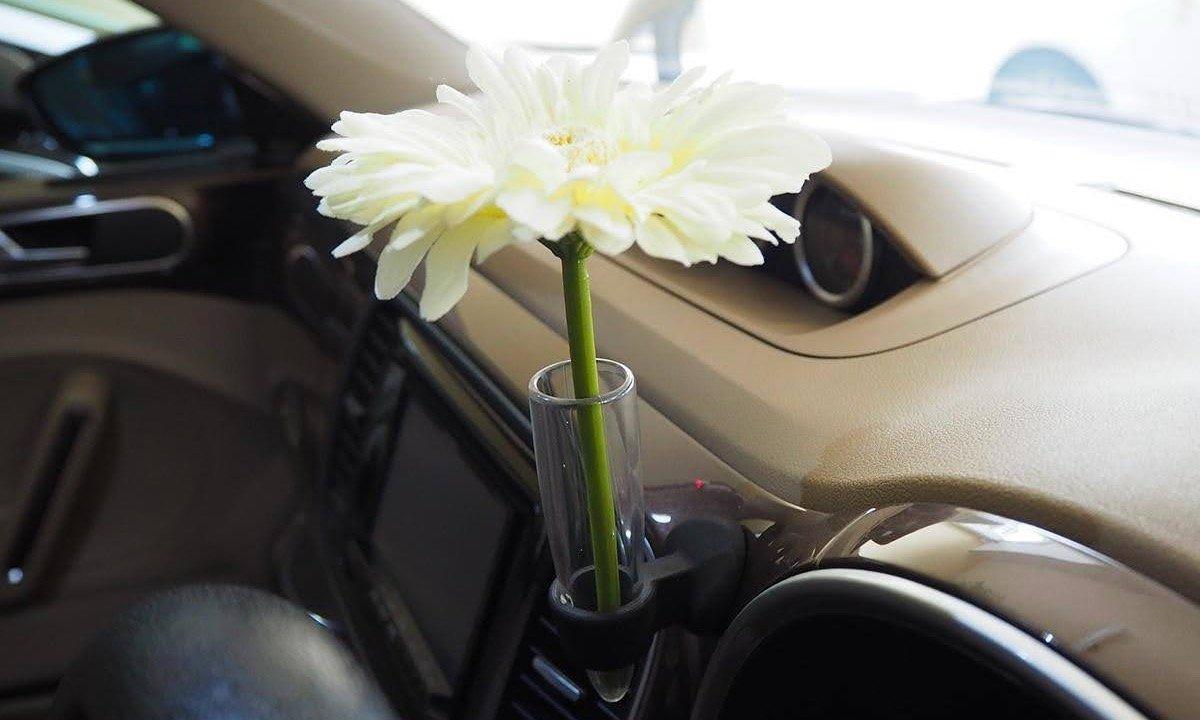
Aftermarket-Teile können bei der Personalisierung helfen, wie diese Blumenvasen-Erweiterung mit einer in 3D-gedruckten Haltevorrichtung.
Um SLS-Teile für die Endverwendung wie diese noch attraktiver für Kunden zu machen, setzt das Team des Design-Labors fortgeschrittene Nachbearbeitungstechniken ein, welche die Oberfläche der Nylonteile glätten. Die Becherhalter wurden im Fuse Sift entpulvert, sandgestrahlt und anschließend mit einer mattschwarzen Urethan-Beschichtung versehen, sodass sie sich nahtlos in die Innenausstattung des Volkswagen einfügen.
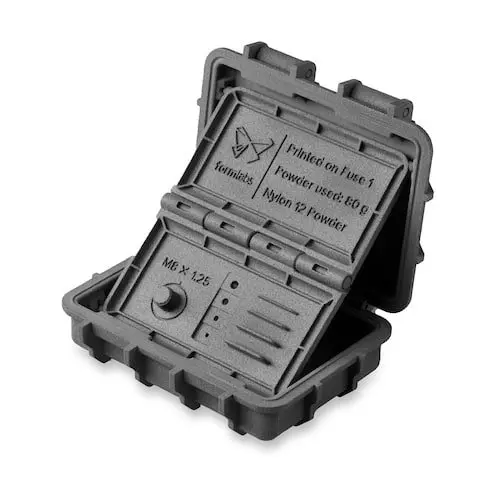
Kostenlosen SLS-Probedruck anfordern
Sehen und fühlen Sie die Qualität von Formlabs aus erster Hand. Wir senden Ihnen einen kostenlosen Probedruck aus dem Fuse 1+ 30W an Ihren Arbeitsplatz.
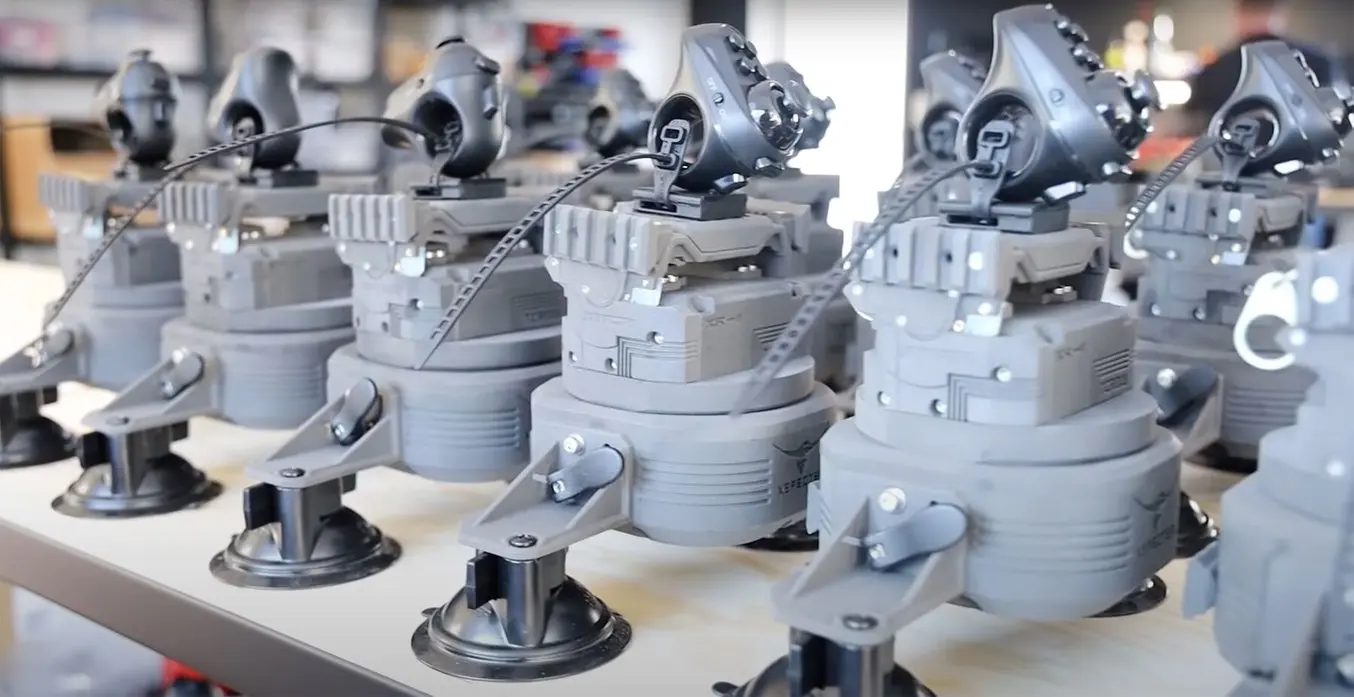
SLS-Produktion für die Endverwendung
3D-Druck für die Endverwendung ist nicht nur möglich, sondern dank des SLS-Ecosystems der Fuse-Serie auch noch erschwinglicher, agiler und leichter skalierbar denn je. Besuchen Sie unsere Seite zum Thema SLS für die Produktion und vergleichen Sie Produktionsverfahren, informieren Sie sich über unsere Mengenrabatte auf Pulver und entdecken Sie die Produktionsabläufe 15 verschiedener Hersteller, die derzeit die Fuse-Serie nutzen.
Mit additiver Fertigung voranschreiten
Uchida und sein Team bei CodeTech verfolgen den Leitgedanken der ständigen Innovation und der Entwicklung von Produkten, die den dynamischen Kundenanforderungen gerecht werden. Durch den Einsatz von Formlabs-Druckern, die Uchida als „intuitiv und einfach zu bedienen“ bezeichnet, kann das CodeTech-Team einen flexiblen und reaktionsschnellen Fertigungsprozess aufbauen. Die Produktion von Endbauteilen auf Abruf mit dem Fuse 1+ 30W ermöglicht es dem Unternehmen, Geld und Zeit für teure konventionelle Fertigungsverfahren oder die Wartung umfassender physischer Bestände zu sparen.
Um mehr über 3D-Druck in der Automobilindustrie zu erfahren, lernen Sie unsere Anwendungen und Fallstudien kennen. Um zu erfahren, wie SLA- oder SLS-3D-Druck Ihre Arbeitsabläufe unterstützen kann, wenden Sie sich an unser Expertenteam für die Automobilbranche.