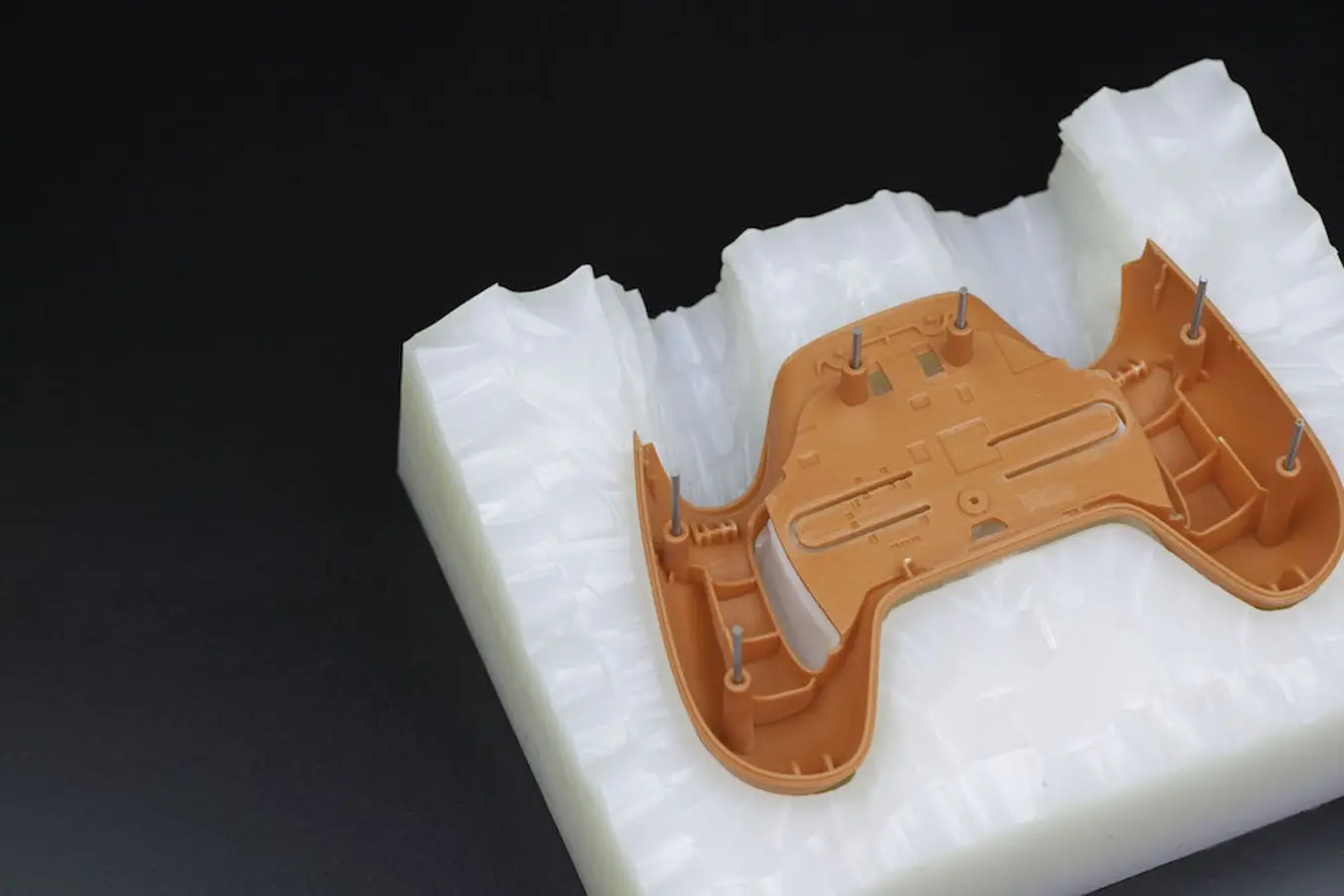
Ein Prototyp, der via Urethanguss hergestellt wurde. Quelle: Fictiv
Vakuumgießen ist ein beliebtes Fertigungsverfahren für Kleinserien von Prototypen als Markteinführungstests, für personalisierte Produkte, maßgeschneiderte Medizinprodukte und darüber hinaus.
Dieser Leitfaden behandelt die Einzelheiten des Vakuumgießverfahrens, wie es sich im Vergleich zu anderen Fertigungstechniken verhält, die besten Urethan-Gießgeräte und wie man 3D-gedruckte Modelle für das Vakuumgießen herstellt.
Was ist Vakuumgießen/Urethanguss?
Vakuumgießen ist ein Fertigungsverfahren, das dem Spritzguss ähnelt. Dabei wird Urethanharz zwischen die zwei Hälften einer Silikonform gegossen.
Dieser Prozess arbeitet mit einer detailgetreuen Abbildung des Urmodells, indem eine Silikonform um dieses Urmodell gegossen wird. In einem höchst präzisen Schritt wird die Form in zwei Hälften geteilt, das Urmodell entfernt und ein Zuführungs- sowie Belüftungssystem hinzugefügt. Anschließend wird ein Harz auf Urethanbasis in den entstandenen Hohlraum eingegossen. Dabei härtet es unter Vakuumbedingungen aus, um das Eindringen von Luftblasen zu verhindern.
Das Ergebnis ist eine höchst präzise Replikation des ursprünglichen Objekts.
Hinweis: In den USA ist das Vakuumgießen besser bekannt als Urethanguss oder Polyurethanguss. In diesem Artikel werden diese Begriffe synonym verwendet.
Anwendungsbereiche des Vakuumgießens
Das Vakuumgießen ist ein ideales Fertigungsverfahren für Kleinserien von Produkten, die nahezu produktionsreife Qualität erreichen müssen.
Der Prozess erzeugt äußerst detailgetreue Modelle, die praktisch nicht vom Endprodukt zu unterscheiden sind. Somit eignen sich Urethangussmodelle hervorragend für Investorenpräsentationen, Messen und kommerzielle Fotografie. Da mit einer Silikonform etwa 50 Gussteile erstellt werden können, nutzen Unternehmen das Vakuumgießen auch oft für die erste Serie ihres Produkts, z. B. bei Markteinführungstests.
Falls das Projekt höhere Stückzahlen erfordert, stehen den Kunden verschiedene Möglichkeiten offen:
-
Das gleiche Urmodell kann für mehrere Silikonformen wiederverwendet werden.
-
Mithilfe mehrerer Urmodelle lassen sich Formen mit gleich mehreren Gussräumen erstellen.
-
Anstelle von kaltvernetzendem Silikonkautschuk (RTV, von Raumtemperatur vernetzend) kann auf heißvernetzenden Silikon (HTV, von Hochtemperatur vernetzend) oder Gummi zurückgegriffen werden. Dies führt zu einer robusteren Form und verlängert ihre Lebensdauer auf bis zu 300–500 Gießvorgänge pro Form.
Mit nur etwa 10 Tagen Durchlaufzeit von der Herstellung des Hauptmodells bis zum gegossenen Produkt eignet sich das Vakuumgießen nicht nur für schnelle Prototypen, sondern auch für die Brückenproduktion ohne die erheblichen Anfangsinvestitionen, wie sie bei industriellen Fertigungsverfahren wie Spritzguss, Thermoformen und Schleuderguss erforderlich sind.
Weil das Vakuumgießen äußerst detaillierte Modelle mit makelloser Oberflächenbeschaffenheit erstellt sowie in einer breiten Vielfalt von Materialien mit einem weiten Spektrum mechanischer Eigenschaften, eignet es sich zudem für Endprodukte in geringen Stückzahlen, wie beispielsweise:
-
Maßgefertigte Medizinprodukte wie Prothesen, Orthesen, Hörgeräte
-
Automobilteile: Armaturenbretter, Bedienknöpfe, Anzeigen, Embleme, Kühlerfiguren, Beleuchtungslinsen, Ansaugkrümmer
-
Verbraucherelektronik: Gehäuse, Steuergeräte, Bedienfelder, Sensoreinbindung
-
Kritische Komponenten und Ersatzteile für Roboter und Industriemaschinen
-
Konsumgüter: Sonnenbrillen, Stifte oder Handyhüllen in limitierter Edition
-
Musikinstrumente
-
Wissenschaftliche Instrumente
-
Zubehör für Sportgeräte
-
Kunstwerke, Figuren, Maßstabsmodelle, Requisiten
Vakuumgießen ist zudem eine beliebte Methode, um bestehende Objekte ohne kompliziertes Reverse Engineering zu kopieren. Dabei handelt es sich häufig um seltene oder nicht mehr erhältliche Gegenstände wie Skulpturen, Fossilien, historische Relikte, Antiquitäten, Sammlerstücke und Handwerksmodelle, für die keine CAD-Modelle oder andere Baupläne verfügbar sind.
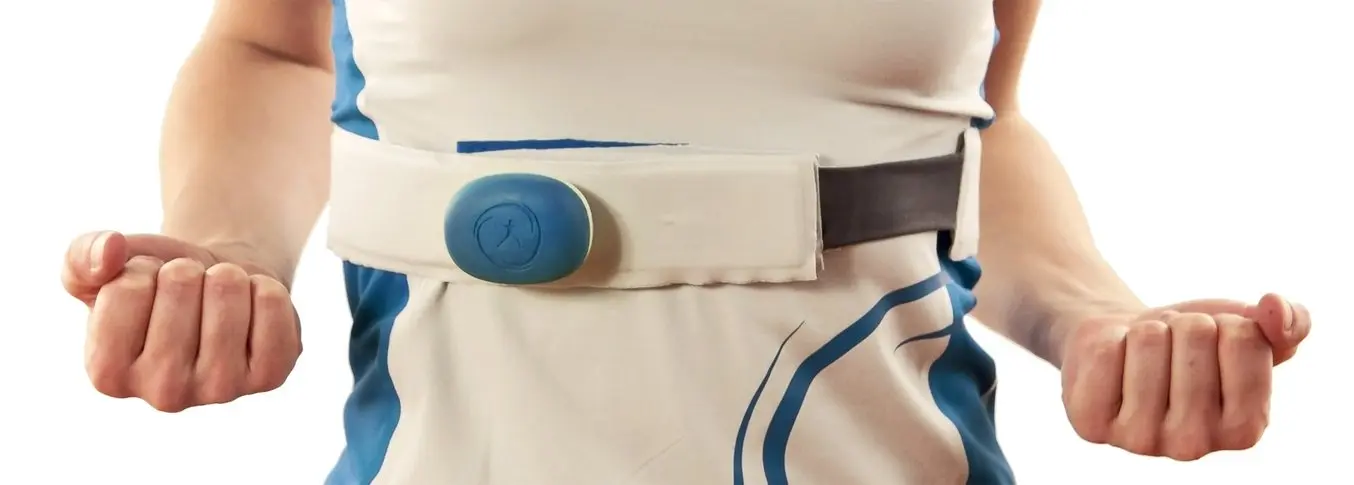
Elektronikgehäuse für tragbare Atemsensorgeräte, hergestellt durch Silikonumspritzung im Vakuumguss. Quelle: IDZone Product Design Guss: Venture Rapid Technologies
Urethanguss im Vergleich
Vergleich zwischen Vakuumgießen und Spritzguss
Produktdesigner und Ingenieure greifen in der Designvalidierung oft auf 3D-Druck zurück und machen dann den direkten Schritt zum Spritzguss für die Produktvalidierung. Das Problem dabei sind allerdings die Kosten einer Spritzgussform. Diese werden üblicherweise aus hochwertigem Stahl mittels CNC-Bearbeitung hergestellt, damit sie sich für die Produktion von Millionen von Teilen eignen. Das wiederum treibt den Preis schnell auf 5000 bis 100 000 €, je nach Größe und Komplexität des Gussteils.
Daher werden als Zwischenschritt oft Formwerkzeuge von geringerer Qualität verwendet. Beispielsweise ermöglicht eine Aluminiumform immer noch 1000 bis 5000 Formzyklen zu einem deutlich geringeren Preis. Da die Herstellung von Soft-Tooling wesentlich schneller vonstattengeht und eine vereinfachte Formgestaltung erlaubt, verkürzt sich auch die Durchlaufzeit im Vergleich zum Spritzguss um etwa die Hälfte.
Auch ein Acrylformwerkzeug oder Kleinserienspritzguss mit 3D-gedruckten Formen können eine Option sein, abhängig von den benötigten Stückzahlen und der erforderlichen Teilequalität. Eine 3D-gedruckte Form aus einem SLA-Drucker von Formlabs kostet in der Regel weniger als 100 € und übersteht mehr als 100 Schüsse ohne merklichen Qualitätsverlust.
Allerdings wird oft übersehen, dass Vakuumgießen häufig ein klügerer Ansatz ist, um die Brücken zwischen Prototypenphase und Produktion zu schlagen. Von all den Verfahren der frühen Prototypenfertigung ähnelt der Harzguss dem Spritzguss am meisten. Außerdem ist er äußerst kosteneffizient: Formen kosten zwischen 200 und 1000 € und Teile liegen üblicherweise zwischen 10 und 100 € pro Stück.
Eine Silikonform für den Urethanguss wird ähnlich wie eine Spritzgussform aufgebaut. Sie besteht aus zwei Hälften – eine bildet den Kern, die andere den Hohlraum. Dazwischen wird das flüssige Material eingespritzt und formt das endgültige Produkt. Es gibt jedoch einige Unterschiede:
-
Beim Spritzguss wird ein geschmolzenes Polymer unter hohem Druck und hoher Temperatur mithilfe eines Trichters und einer Leitspindel in den Hohlraum gepresst. Das Vakuumgießen arbeitet mit niedrigen Temperaturen. Statt geschmolzenen Kunststoffs verwendet man dort flüssige Kunstharze, die unter Vakuum in die Form gezogen werden, ähnlich der Kapillarwirkung im Inneren eines Pflanzenstängels. Und obwohl es viele verschiedene Kunstharze gibt, die unterschiedliche Polymere nachahmen, ist die Prototypenerstellung im endgültigen Spritzgussmaterial nicht möglich.
-
Nach der Aushärtung im Ofen unterliegen die Teile immer noch einer gewissen Nachhärtung für bis zu einer Woche. Sie bleiben anfällig für UV-Strahlung und hohe Temperaturen.
-
Da die Gussform flexibel ist, gibt es Grenzen hinsichtlich der Größe und Form der Teile. Dennoch gibt es spezielle Techniken, um Ausnahmen zu ermöglichen. Ein Beispiel hierfür wäre das gestaffelte Gießen unter Verwendung von Metallstützen, um der Schwerkraft bei der Herstellung länglicher Teile in einer dreiteiligen oder vierteiligen Form entgegenzuwirken.
-
Das Vakuumgießen bewältigt variable Wandstärken besser als der Spritzguss, da es keinen Zyklus aus Erhitzen und Abkühlen gibt. Dies führt zu weniger Verformungen der Teile.
-
Mit einer Silikonform lassen sich ausgeprägte Hinterschneidungen im Teiledesign realisieren. Dennoch wird bei Spritzgusstests empfohlen, sich möglichst an das spritzgegossene Design zu halten. Es ist ratsam, die erforderlichen Winkel des endgültigen Produkts zu berücksichtigen.
-
Beim Vakuumgießen fällt nahezu kein Abfall an, während beim Spritzguss bis zu 20% des verwendeten Polymers aufgrund von Ausschussraten, Rückständen und Überproduktion verloren gehen.
Die hohe Originaltreue zwischen einem Vakuumgussmodell und einem endgültigen Produkt aus einer Spritzgussform ermöglicht die Optimierung des Designs für die Fertigung. Auf diese Weise erhalten Sie eine hochwertige Produktvorschau, ohne die Geschäftsführung mit den enormen Fixkosten zu belasten, die bei der Auftragsfertigung in einem Spritzgusswerk anfallen.
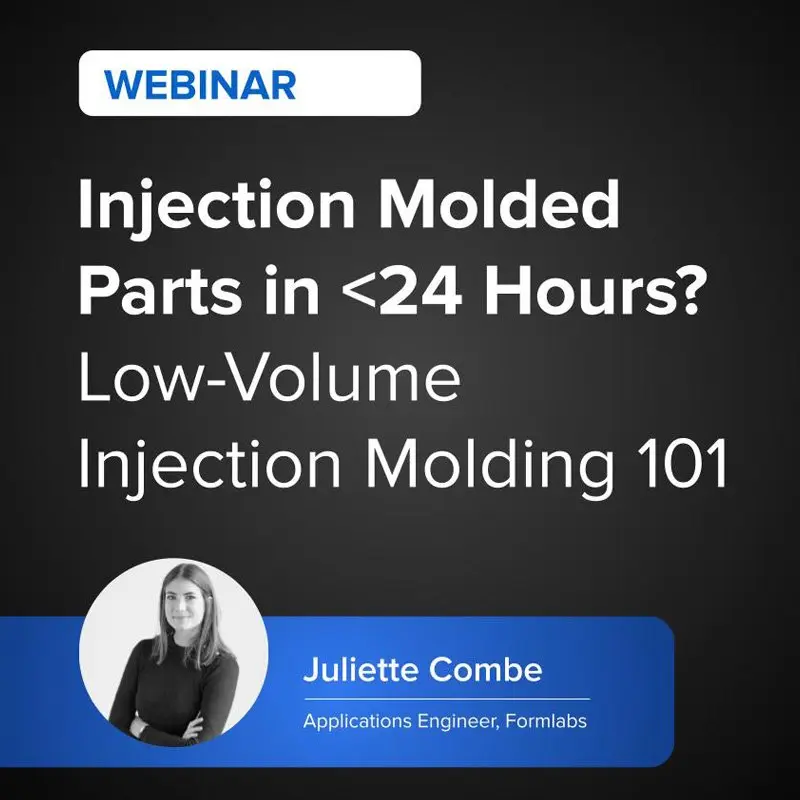
Spritzgussteile in unter 24 Stunden? Einführung in den Spritzguss für Kleinserien
In diesem Webinar zeigen wir Ihnen, wie Sie in Ihrem Spritzgussverfahren Formen aus dem SLA-3D-Drucker einsetzen, um Kosten und Durchlaufzeiten zu verringern und bessere Produkte zu liefern.
Vergleich zwischen Vakuumgießen und 3D-Druck
It is a common misunderstanding that 3D printing is restricted to one-offs only. On the contrary, it is a viable method for low volume manufacturing of end-use parts. It is also increasingly popular for companies to invest in an in-house print farm. Such an array of 3D printers can handle low-volume batches of hundreds or even thousands of products.
The main factor influencing a choice between 3D printing and vacuum casting is product geometry. Vacuum casting is explicitly intended to simulate injection-molded parts. As a low-investment alternative to full-scale injection molding, it can even combine flexible and rigid materials in an overmold or add metal components directly in the prototype through insert molding. For creating a small series of injection-moldable components, vacuum casting is more cost-effective than 3D printing.
Another advantage of vacuum casting is that bigger parts can be created much faster and cheaper than 3D printing. It allows for mold sizes of roughly 50 cm (20 inches) for the longest dimension, and casting weight up to 1.5kg (3.3 lbs).
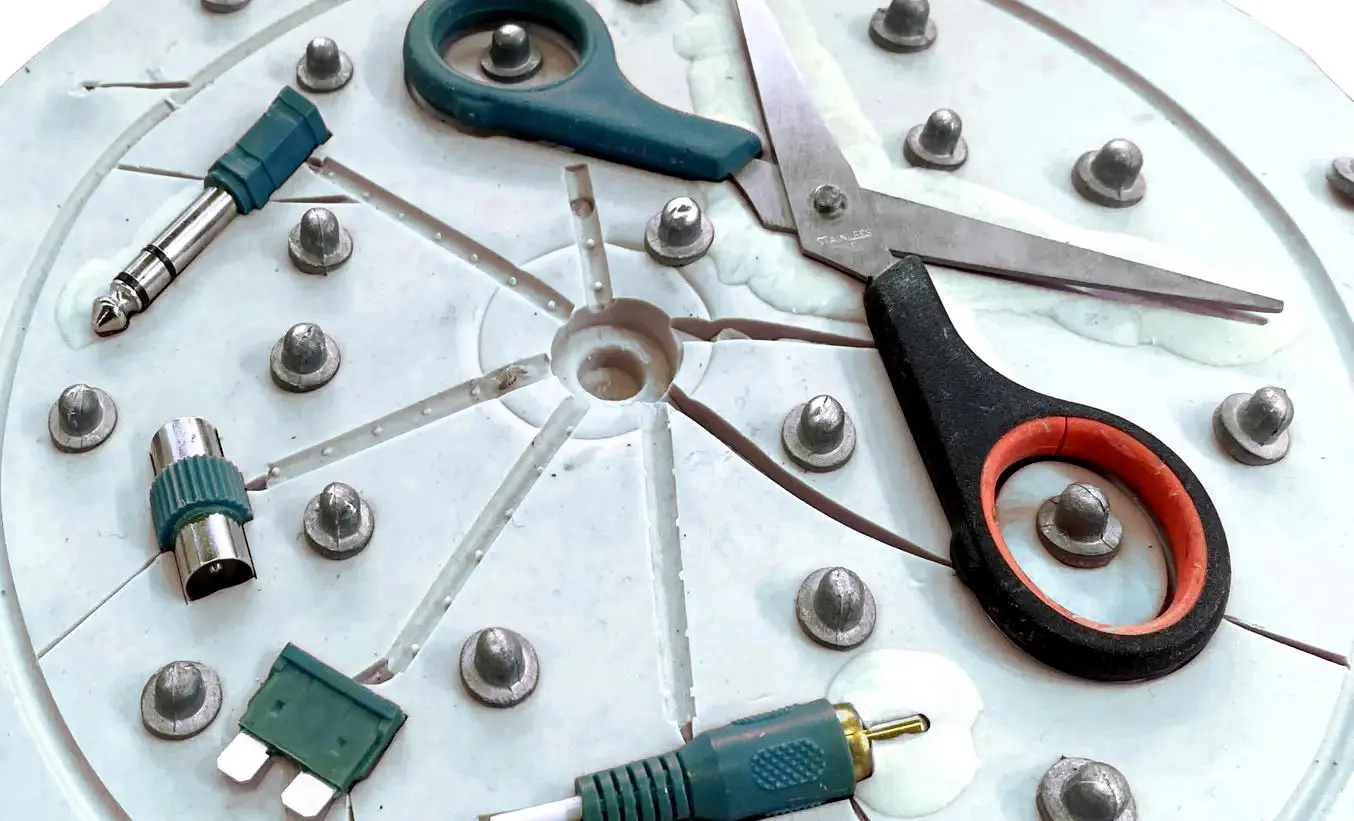
Vakuumgießen in einer Silikonform mit Metalleinsätzen.
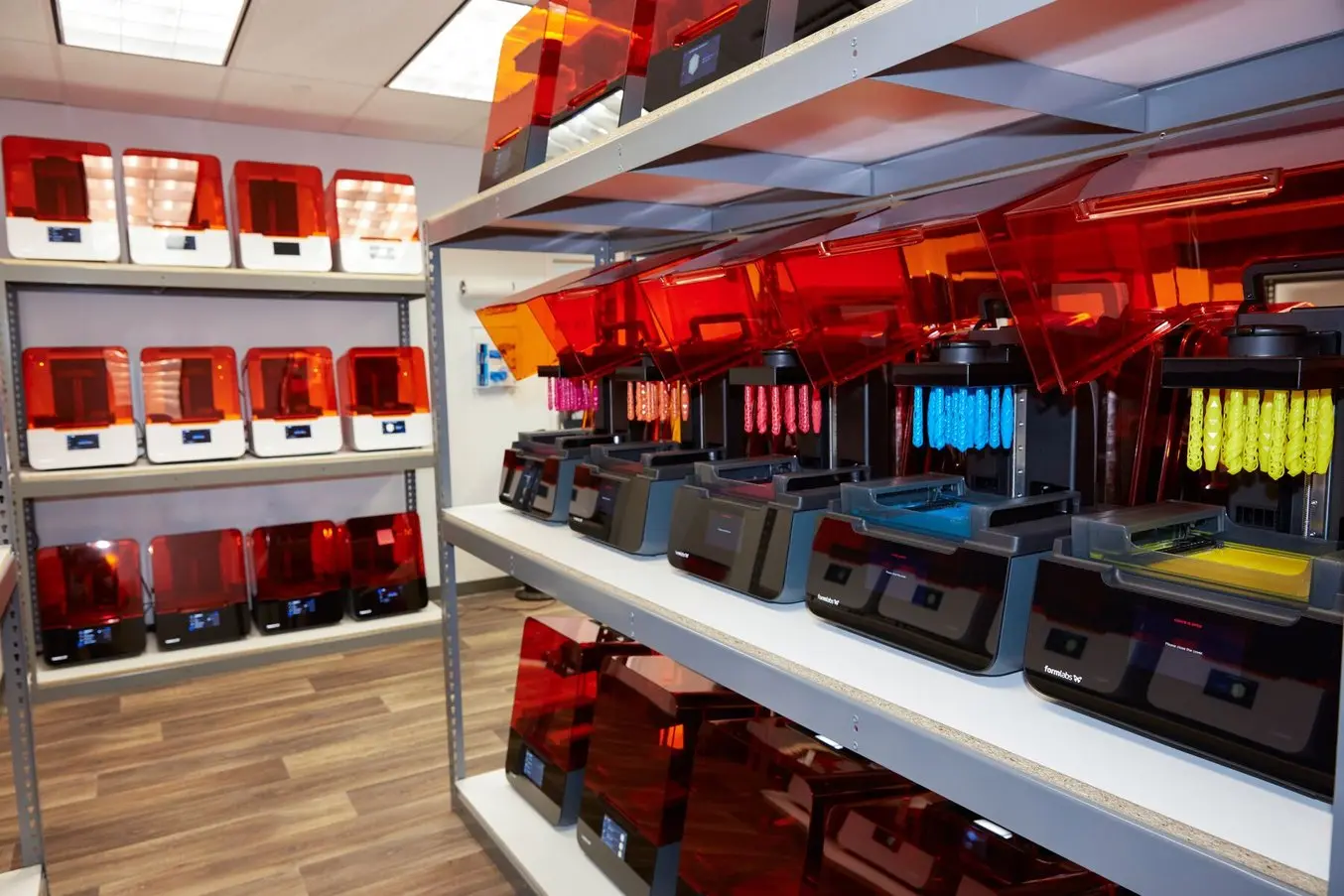
So realisieren Sie die Kleinserienproduktion und kundenspezifische Fertigung mit 3D-gedruckten Endverbrauchsteilen
Erfahren Sie in diesem Webinar alles darüber, wie Sie mit 3D-Druck schnell und kosteneffizient kundenspezifische Produkte und Kleinserien für die Endverwendung fertigen.
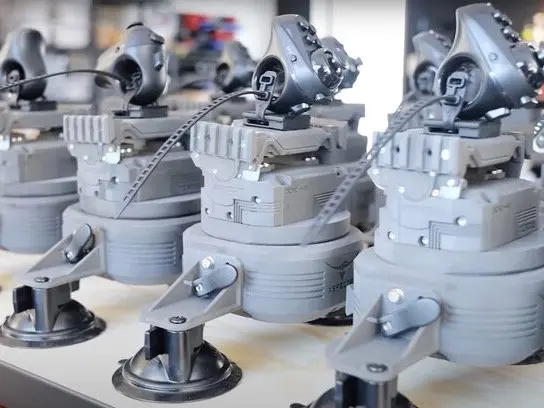
3D-gedruckte Teile für die Endverwendung im Belastungstest
Dieses Whitepaper stellt die 3D-Druck-Hardware und -Materialien von Formlabs im Rahmen der Produktion von Endverbrauchsteilen vor, einschließlich Fallstudien und der Ergebnisse von Belastungs- und Eignungstests der 3D-Druckmaterialien für die Endverwendung.
Vergleich zwischen Vakuumgießen und alternativen Fertigungsverfahren
Schauen wir uns die Vor- und Nachteile unterschiedlicher Fertigungstechniken an:
Vakuumgießen | Spritzguss | 3D-Druck | Rapid Tooling | Zerspanung | Handfertigung | ||
---|---|---|---|---|---|---|---|
Gestaltungsfreiheit | ★★★☆☆ | ★★☆☆☆ | ★★★★★ | ★★☆☆☆ | ★★★★☆ | ★★★☆☆ | |
Größe der Teile | ★★★★☆ | ★★★★☆ | ★★★☆☆ | ★★★☆☆ | ★★★★☆ | ★★★★★ | |
Durchsatz | ★★★☆☆ | ★★★★★ | ★★★☆☆ | ★★★★☆ | ★★☆☆☆ | ★☆☆☆☆ | |
Materialauswahl | ★★★☆☆ | ★★★★☆ | ★★★★☆ | ★★★★☆ | ★★★★★ | ★★★☆☆ | |
Investitionskosten | ★★★☆☆ | ★☆☆☆☆ | ★★★☆☆ | ★★☆☆☆ | ★★★★★ | ★★☆☆☆ | |
Kosten pro Teil | ★★★★☆ | ★★★★★ | ★★★☆☆ | ★★★★☆ | ★★★☆☆ | ★★★☆☆ | |
Durchlaufzeit | ★★★★☆ | ★☆☆☆☆ | ★★★★★ | ★★★☆☆ | ★★★★☆ | ★★☆☆☆ |
Der Vakuumgussprozess
Das Vakuumgießen ist ein äußerst anspruchsvoller Prozess in vier Schritten.
1. CAD-Design
Ein*e Designer*in oder Ingenieur*in erstellt eine digitale Darstellung des herzustellenden Objekts mithilfe einer CAD-Software wie Fusion 360 oder SolidWorks. Hierbei sollten die folgenden Designrichtlinien für den Urethanguss berücksichtigt werden:
-
Wandstärken zwischen 1,5 mm und 4 mm. Die absolute Mindeststärke beträgt 1 mm.
-
Rippen können dünner sein, bis ca. 60 % der Wandstärke.
-
Verwenden Sie großzügige Radien > 3 mm.
-
Vermeiden Sie Wände mit 90-Grad-Winkeln, um die Festigkeit des Teils zu verbessern.
-
Integrieren Sie eine Nut von 0,5 mm zwischen zwei sich verbindenden Schalen, um das Erscheinungsbild des Produkts zu verbessern.
-
Die Wandstärke eines Schraubdoms sollte dem Lochdurchmesser entsprechen.
-
Gravierte Buchstaben kommen am besten bei einer Tiefe von 0,25 mm zur Geltung.
Wenn das CAD-Modell fertig ist, wird es im STL-Format exportiert, um das Modell herzustellen.
2. Herstellung des Urmodells
Das Urmodell ist das Positiv-Modell, von dem durch Gießen Kopien erstellt werden. Da eine Silikon-Vakuumgussform die genaue Replik des Urmodells erstellt, ist es von größter Bedeutung, dass das 3D-gedruckte Modell das ursprüngliche CAD-Modell präzise widerspiegelt – insbesondere hinsichtlich der überaus glatten Oberflächenqualität. Einige sekundäre Eigenschaften eines hochwertigen Urmodells sind Härte, Beständigkeit gegenüber Chemikalien und Temperaturen sowie Haltbarkeit, um Degradation zu verhindern.
CNC-gefräste Urmodelle waren früher der Standard, jedoch ist ihre Herstellung teuer und zeitintensiv. Außerdem unterliegen sie Einschränkungen, wenn es um Löcher, Kanäle, interne Radien und organische Oberflächen geht. 3D-Druck bietet eine innovative Alternative und ist derzeit das prävalente Verfahren in der Herstellung von Urmodellen.
Es gibt verschiedene 3D-Druckertypen, sowohl im Mainstream als auch für gewerbliche Kunden. Die am häufigsten verwendeten Verfahren für den Urethanguss sind jedoch SLA- und SLS-3D-Druck.
SLA-3D-Druck produziert die Teile mit den glattesten Oberflächen, was für Vakuumgussmodelle ideal ist. Zwar sind SLA-Drucke mit den richtigen Druckeinstellungen schon sehr glatt, dennoch erfordern sie etwas Schleifen und Polieren, um Stützstrukturen zu entfernen und eine absolut makellose Oberfläche zu erzielen. Einige fortschrittliche Materialien wie Rigid 10K Resin bieten auch überlegene mechanische Eigenschaften, Temperaturbeständigkeit und Haltbarkeit.
SLS-3D-Druck mit Nylonpulver erstellt starke, temperaturbeständige und präzise Druckteile. Da diese Technologie keine Stützstrukturen erfordert, eignet sie sich auch ideal für komplexe Merkmale wie dünne Wände, Gravuren, Schnappverbindungen, Scharniere und ineinandergreifende Teile. Die Oberflächenqualität der gedruckten Teile ist für Urmodelle zum Urethanguss etwas zu grob. Daher benötigen 3D-gedruckte SLS-Teile Nachbearbeitung wie Sandstrahlen oder Vibrationsschleifen, um ihre Oberfläche zu glätten.
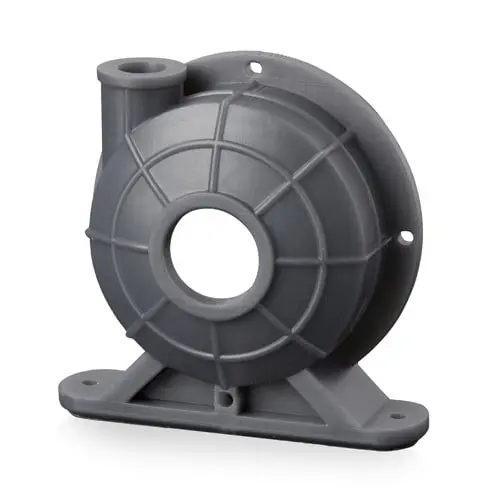
Kostenlosen Probedruck anfordern
Sehen und fühlen Sie die Qualität von Formlabs aus erster Hand. Wir senden Ihnen einen kostenlosen Probedruck an Ihren Arbeitsplatz.
3. Herstellung der Form
In diesem arbeitsintensivsten Stadium des Prozesses wird zunächst eine Formbox aus Melaminplatte und Heißkleber gefertigt. Das Urmodell wird dann mit kleinen Tropfen CA-Klebstoff am Boden befestigt. Manchmal werden auch Aussparungen mithilfe eines Drehwerkzeugs eingearbeitet, in die die passenden Erhebungen am Urmodell greifen. Dies bietet zusätzliche Fixierung.
Für eine enge Trennlinie zwischen den beiden Hälften der Form müssen alle Löcher zwischen dem Urmodell und dem Bodenpanel aufgefüllt werden. Styrolblöcke und Plastalina-Modelliermasse eignen sich dafür besonders. Anschließend werden Stifte und Stege eingesetzt, um die perfekte Ausrichtung mit der anderen Formhälfte zu gewährleisten.
Nachdem die zweikomponentige Silikonmasse gründlich gemischt wurde, wird sie in eine Vakuumkammer gegossen und entgast. Bevor dies geschieht, kommt ein Säurepinsel zum Einsatz, um geschickt alle winzigen Lücken im Urmodell mit der Silikonmischung zu füllen und so Lufteinschlüsse zu verhindern. Anschließend wird durch das Eingießen des Silikons die erste Formhälfte gebildet.
Nach einer Aushärtungszeit von mehreren Stunden wird die Formhälfte aus der Formbox gelöst und umgedreht. Die Fachleute für den Formenbau arbeiten nun geschickt Acrylbelüftungen ein, Steiger und einen Einfüllstutzen für die zweite Hälfte des Prozesses. Formtrennmittel wird auf das Silikon gesprüht und mit einem Pinsel in den tieferen Bereichen verteilt. Dann wird eine neue Formbox in ähnlicher Weise für das Gießen der zweiten Formhälfte erstellt.
Um die Form auf das Vakuumgießen vorzubereiten, wird sie aus der Formbox gelöst und mit einer gleichmäßigen Schicht Urethan-Formtrennmittel (E236) überzogen. Die Formhälften werden wieder zusammengefügt, um einen einzigen Block zu bilden. Hier kommen die Stifte bei der Ausrichtung zum Einsatz.
4. Vakuum-Urethanguss
In diesem Schritt wird das Urmodell in einer Vakuumkammer durch Gießen kopiert. Zuerst wird die Form auf einer Holzplatte befestigt und mit Belüftungsröhren sowie einem Einfülltrichter versehen.
Das Zweikomponenten-Kunstharz wird abgemessen und mit einem Farbstoff gemischt. Anschließend wird das Gießmaterial einige Minuten lang in einer Vakuumkammer entgast.
Die Polyurethan-Mischung ist jetzt bereit für den Guss. Die Steigrohre zeigen an, wann der Hohlraum vollständig gefüllt ist. Nach der Aushärtung bei 70 °C wird die Form geöffnet. Sie enthält eine exakte Kopie des Originalmodells mit allen Details und Oberflächenstrukturen.
Die abschließenden Schritte umfassen das Abschneiden der Ränder aus überschüssigem Material, einen zusätzlichen Poliervorgang mit 1000er Körnung und die Aushärtung im Ofen, um die Materialeigenschaften des Teils zu verbessern.
Profi-Tipps
Der obige Prozess findet insbesondere Anwendung bei dünnwandigen Prototypen, wie Elektronikgehäusen, Aufbewahrungsbehältern und anderen Fällen, bei denen wir eine sichtbare Trennlinie auf der primären Oberfläche des Produkts vermeiden möchten.
Bei weniger kritischen Objekten reicht es aus, das Urmodell in einen Silikonblock zu integrieren und diesen anschließend manuell aufzuschneiden. Dieser Schnitt erfolgt in einer Sinuswellenform, was ein gewisses Maß an Erfahrung und Geschick erfordert.
Hier sind einige bewährte Praktiken zur Optimierung der Ergebnisse beim Urethanguss:
-
Achten Sie darauf, Trennmittel nicht direkt auf das Modell aufzutragen, da dies leichte Oberflächentexturen hinterlassen kann, die im Guss sichtbar werden.
-
Erwärmen Sie die Kunstharze auf 40 °C, idealerweise bereits einen Tag vor der Verwendung, und schütteln Sie die Flasche gelegentlich, um Kristallbildung zu verhindern.
-
Vermeiden Sie, dass Feuchtigkeit in die Kunstharzflaschen eindringt. Feuchtigkeit agiert bei PU als Treibmittel. Dazu können Sie die Flaschen unmittelbar nach Gebrauch beispielsweise mit Argongas füllen.
-
Verwenden Sie beim Mischen von Zweikomponentenchemikalien stets zwei Becher nacheinander (double-cup mixing) . Das Gießen direkt aus dem ersten Becher führt mit an Sicherheit grenzender Wahrscheinlichkeit zu ungemischten Streifen, was den Guss ruiniert.
-
Beim Zerlegen des Formgehäuses für zukünftige Verwendungen können Sie Heißkleber mit Isopropanol lockern.
-
Positionieren Sie den Einfüllstutzen so, dass er den kürzesten durchschnittlichen Abstand zu verschiedenen Abschnitten des Teils bietet. Dadurch wird sichergestellt, dass alle Bereiche gefüllt werden.
-
Um die Bildung von Luftblasen zu verhindern, gießen Sie von einem einzigen Punkt aus. Umgießen Sie außerdem empfindliche Bereiche mit vielen Details. Gießen Sie niemals direkt von oben darauf.
-
Legen Sie den Anguss niedrig und die Entlüftung hoch an.
-
Verleihen Sie Ihrem Guss mit metallischen Pulvern eine spektakulär lebendige Oberfläche oder verwenden Sie Polypyrrol- oder Graphitpulver für elektrische Leitfähigkeit.
-
Wenn Sie Urethan mischen, lassen Sie ausreichend Platz über der Oberfläche, da die Flüssigkeitsmischung aufschäumen und im Vakuumbehälter aufsteigen kann, wie ein Marshmallow in der Mikrowelle.
-
Nutzen Sie eine professionelle Vakuumgussmaschine, um den Prozess zu beschleunigen und zuverlässigere Ergebnisse zu erzielen.
Vakuumgussmaschinen
Due to the complexity of the process, most companies subcontract jobs to third-party urethane casting service providers.
For those planning to do vacuum casting in house, a professional vacuum casting machine provides an integral solution for taking prototyping efforts to the next level and speeding up the process towards production ramp-up. As much as fifty castings can be achieved within two days, each in a different material and color if needed.
A vacuum resin casting machine is a refrigerator-sized contraption that automates the process from mixing to casting to curing. It lets operators control parameters such as chamber pressurization, mixer speed, heated cup, and oven heat. The latest systems are programmable so that operators can create custom sequences to optimize casting cycles for specific materials and product types.
Vacuum casting machines come in different sizes to allow for different mold sizes. Most models can, next to working with resin, also be set up for casting injection-grade nylon, ceramics, wax, and even low-melt metal alloys.
Urethane casting machines are ideal for pre-production runs because they pull a vacuum much quicker and minimize manual labor. The downside is that they cost tens of thousands of dollars. Jewelry vacuum casting machines are much smaller and generally cost a few thousand dollars.
Here are some of the best vacuum casting machines:
-
Renishaw 5/01 PLC: Max. mold size 530 x 450 x 420 mm, price roughly $45k. The larger 5/04 model allows molds up to 750 x 750 x 900 mm and more materials, like glass-fiber reinforced nylon and wax, but it comes at nearly double the price.
-
SLM VCM 04: Max. mold size 750 x 750 x 900 mm, casting volume 2.2L, and includes casting with nylon and wax.
-
MCP 5/01: Max. part size 400 x 400 x 400 mm. MCP offers many larger models, including the MCP 003 with 560 x 600 x 600 mm part size, the 4/04 with 900 x 750 x 600 mm part size, and the 4/05 with 1300 x 750 x 800 mm part size. These machines are fully programmable and allow vario-pressure casting with wax, silicone, and nylon, next to PU resins. They can also be used with 3D printed injection molds.
-
Scott AM 1000: Max. mold size 500 x 450 x 425 mm, 1 kg casting weight. The 4000 model has a max. mold size of 750 x 750 x 900 mm and 5 kg casting weight. Besides resins, these apparatuses can be used for vacuum investment casting with ceramics and metals.
-
Multistation CSV 340: Max. mold size 340 x 340 x 435 mm, casting volume 600 mL. The CSV500 model fits molds up to 500 x 500 x 635 mm and casting volumes up to 1 liter.
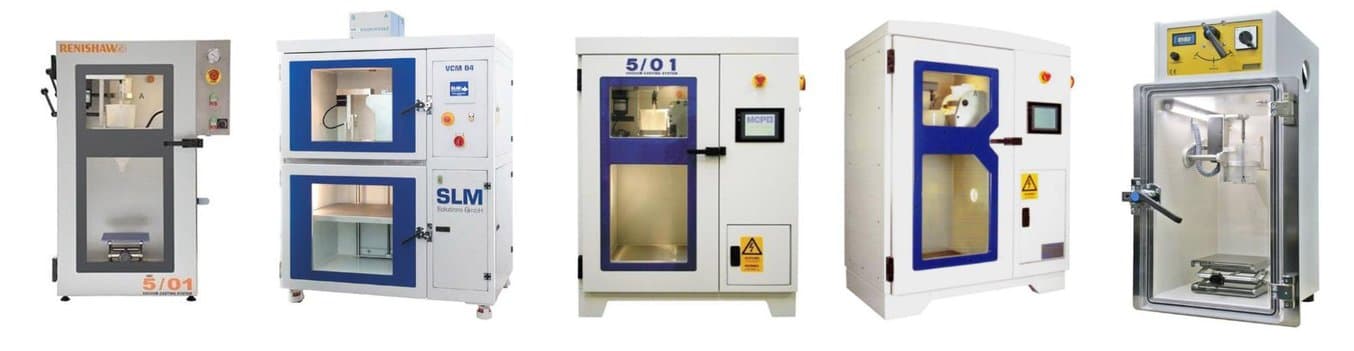
Eine Auswahl an Vakuumgussmaschinen von Herstellern wie Renishaw, SLM, MCP, Scott AM und Multistation
Vergleich zwischen Vakuumgussmaschinen und Druckkammern
Als kostengünstige Alternative ist es durchaus möglich, selbst eine schwerkraftbasierte Vakuumgussmaschine zu bauen. Da bereits eine einzige Luftblase im Inneren der Form den gesamten Guss ruinieren kann, ist das Entgasen eine grundlegende Herausforderung des Kunstharzgusses.
Um alle Blasen aus der Mischung zu entfernen, gibt es zwei bewährte Methoden: eine Vakuumkammer oder ein Drucktopf.
Eine Vakuumkammer ist ein Behälter, um die Luft aus Silikonkautschuk zu entfernen, bevor die Form erstellt wird. Beachten Sie jedoch, dass der Vakuumansatz langsamer ist als der Hochdruckansatz. Er funktioniert daher nur mit Kunstharzen mit einer Aushärtezeit von zwanzig Minuten oder länger.
Ein Vakuumbehälter verfügt über zwei Hebel: einen für die Luftzufuhr und einen für die Vakuumpumpe. Er hat ein Manometer zur Prüfung des Vakuums sowie einen transparenten Acryldeckel zur Kontrolle der Entgasung. Die Investition in einen gehärteten Glasdeckel lohnt sich, da er im Gegensatz zu einem Kunststoffdeckel im Laufe der Zeit nicht einreißt.
Drucktöpfe sind etwas teurer, da sie einen Luftkompressor erfordern. Allerdings sind sie wohl die beste Wahl für blasenfreie Kunstharzmischungen und Gussstücke. Im Gegensatz zu Vakuumkammern können sie mit der Form genutzt werden. Sie sind für schnell aushärtende Harze geeignet, die einen kurzen Verarbeitungszeitraum haben. Und die resultierenden Gussstücke sind zu 100 % frei von eingeschlossener Luft.
Eine Vakuumkammer hat den Vorteil, dass sie für viele Anwendungen nützlich ist, wie das Entgasen von Gips, Beton oder Holzinfusionen, während ein Drucktopf in der Regel nur zur Entgasung von Silikonchargen verwendet wird.
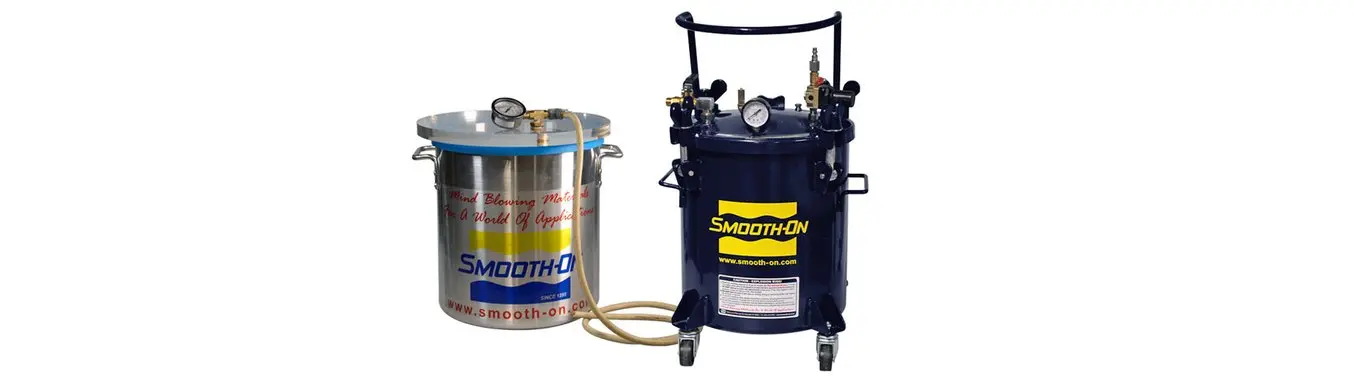
Vakuumkammer (links) und Drucktopf (rechts)
Vakuumgussmaterialien
Silikonformmaterialien
Gießsilikone lassen sich in Zinnsilikone und Platinsilikone unterteilen. Zinnsilikone sind auch als Kondensationssilikone bekannt und weisen eine Schrumpfung von etwa 1–4 % auf. Fachleute können versuchen, diese Schrumpfung auszugleichen. Für Anwendungen mit engen Toleranzen sind hochwertige Platinsilikone oder Kautschuk mit Hochtemperaturvulkanisation (HTV) trotzdem ratsam.
Eine Härte von 40–50 Shore A sorgt für eine robuste Form, die mehrfach wiederverwendet werden kann und das Entformen erleichtert – selbst bei Teilen, die in einer starren Form aufgrund von Rückzugsproblemen stecken bleiben würden. Eine transparente Silikonsorte wird empfohlen, da sie Lufteinschlüsse, Blasen, Verunreinigungen und andere Probleme im Inneren der Form sichtbar macht.
Einige erstklassige Marken für Zweikomponentensilikon sind Smooth-On, Elastosil, V-Sure und Silicones and More (S.A.M.). Eine Direktbestellung bei einer Chemiefabrik im Ausland spart Kosten und liefert gleichzeitig ein hochwertiges Produkt nach den genauen Vorgaben des jeweiligen Käufers, insbesondere bei größeren Bestellungen.
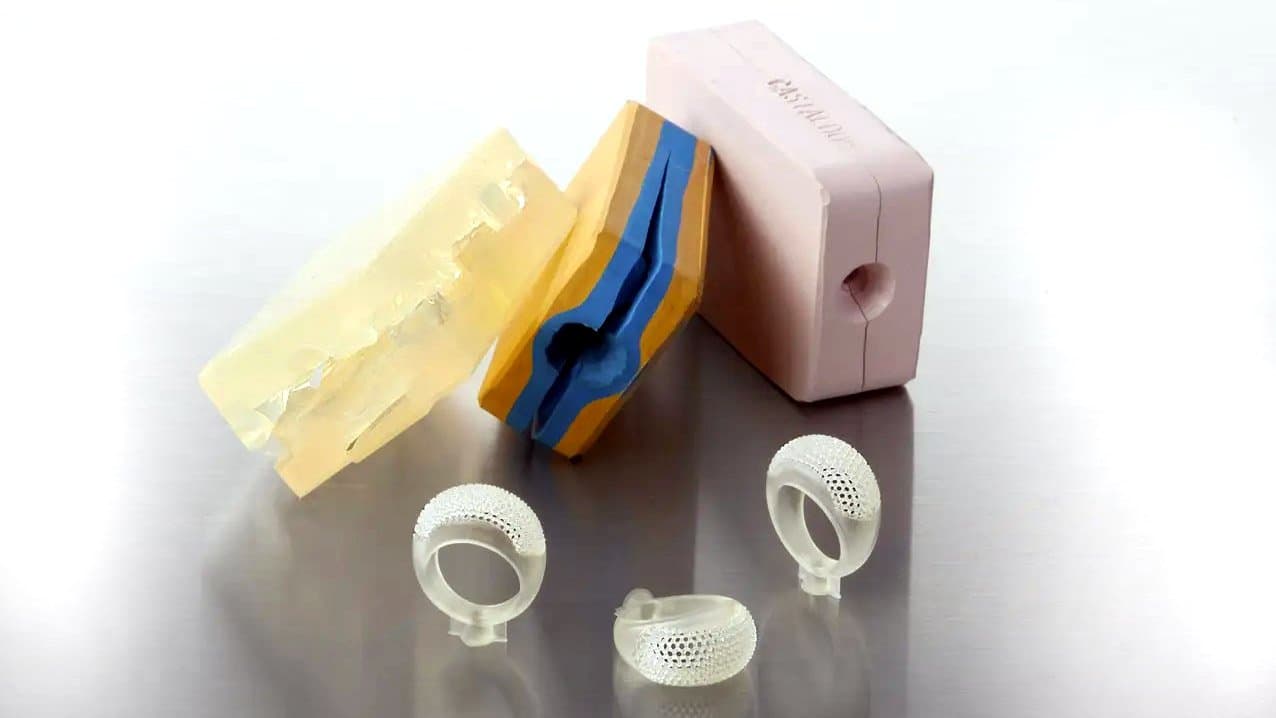
RTV- und HTV-Schmuckformen bilden filigrane Details präzise ab und werden in der Schmuckbranche verwendet.
Urethan-Kunstharze zum Gießen
Es gibt eine Fülle von Vakuumgussmaterialien mit unterschiedlichen Eigenschaften hinsichtlich Flexibilität, Elastizität, Steifigkeit und Härte:
-
ABS-ähnliche Allzweckharze
-
Glasgefüllte, nylonähnliche Materialien für überlegene Steifigkeit
-
TPE-ähnliche Elastomere für Anwendungen wie Wearables, Handgriffe, Tasten und Dichtungen
-
Polycarbonat-ähnliche Materialien
-
Transparente oder wasserklare Guss-Urethane (PMMA-ähnlich)
-
POM-ähnliche oder hitzebeständige PU-ähnliche Materialien
Es gibt auch einige exotische Urethan-Gussmaterialien, wie Bruchglas, Wachs, Epoxidharze, Keramik, Verbundstoffe sowie lebensmittelechte, leitfähige, niedrigdichtige und feuerfeste Optionen. Einige renommierte Marken sind FastCast, Smooth-On und SRC Specialty Resin.
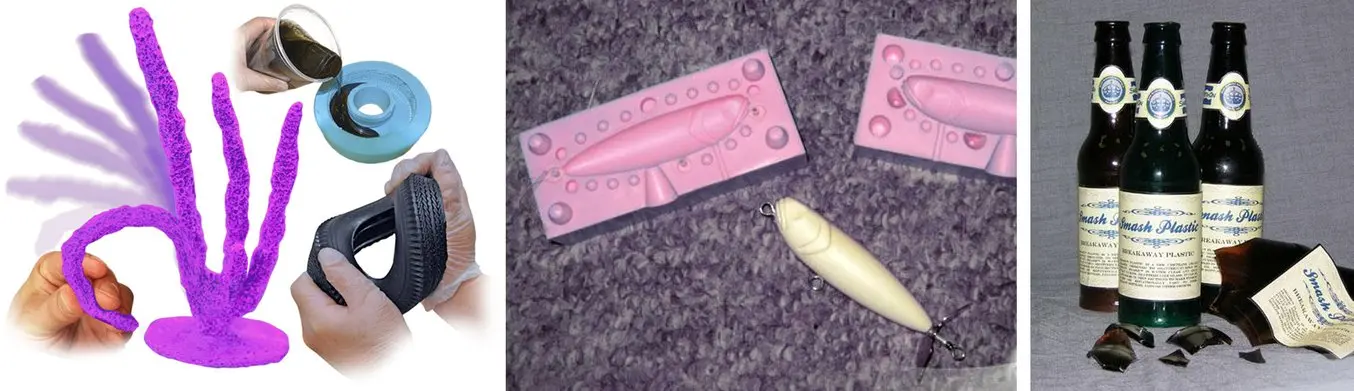
Eine Vielzahl von Urethan-Kunstharzen, von gummiartig über schwimmend bis glasartig
Fallstudien: Urethan-Guss mit 3D-gedruckten Modellen
Calibur Fencing
Vakuumgießen ist ideal für Vorserienläufe, um das endgültige Produkt zu testen und anzupassen, bevor in die Massenproduktionswerkzeuge für den Spritzguss investiert wird. Eine Erfolgsgeschichte ist Calibur Fencing, ein drahtloses Wearable zur Punktzählung im Fechtsport.
Das Designteam begann mit einfachen Prototypen, um die Funktionalität des Geräts zu überprüfen. Es wechselte dann zum FDM-Druck für grobe Modelle, um die geeignete Form zu finden. Und letztendlich erwies sich der SLA-Drucker Form 3 von Formlabs als unverzichtbar, um hochwertige Prototypen zu erstellen, die das endgültige Produkt authentisch wiedergaben.
Das Team nutzte daraufhin die SLA-Druckteile als Modelle und beauftragte einen Vakuumguss-Dienstleister, um Beta-Testprodukte für die Kunden herzustellen. So machte man rasche Fortschritte in Richtung des finalen Produkts und gewährleistete dabei gleichzeitig die Qualitätskontrolle.
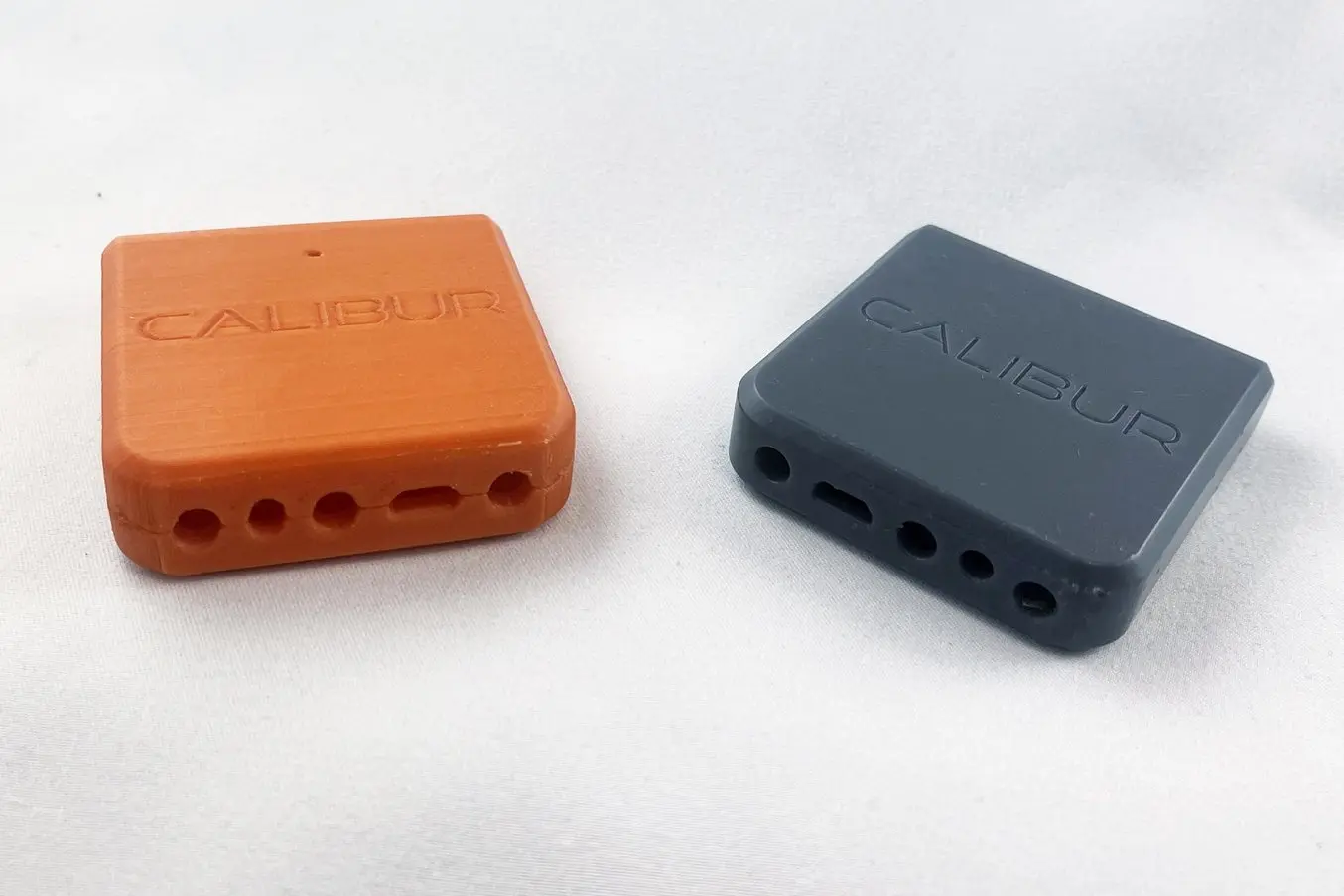
Für die ersten Entwurfsmodelle verwendete das Calibur-Team FDM-3D-Druck und wechselte dann zum SLA-3D-Druck, um realistische und funktionale Prototypen zu erstellen.
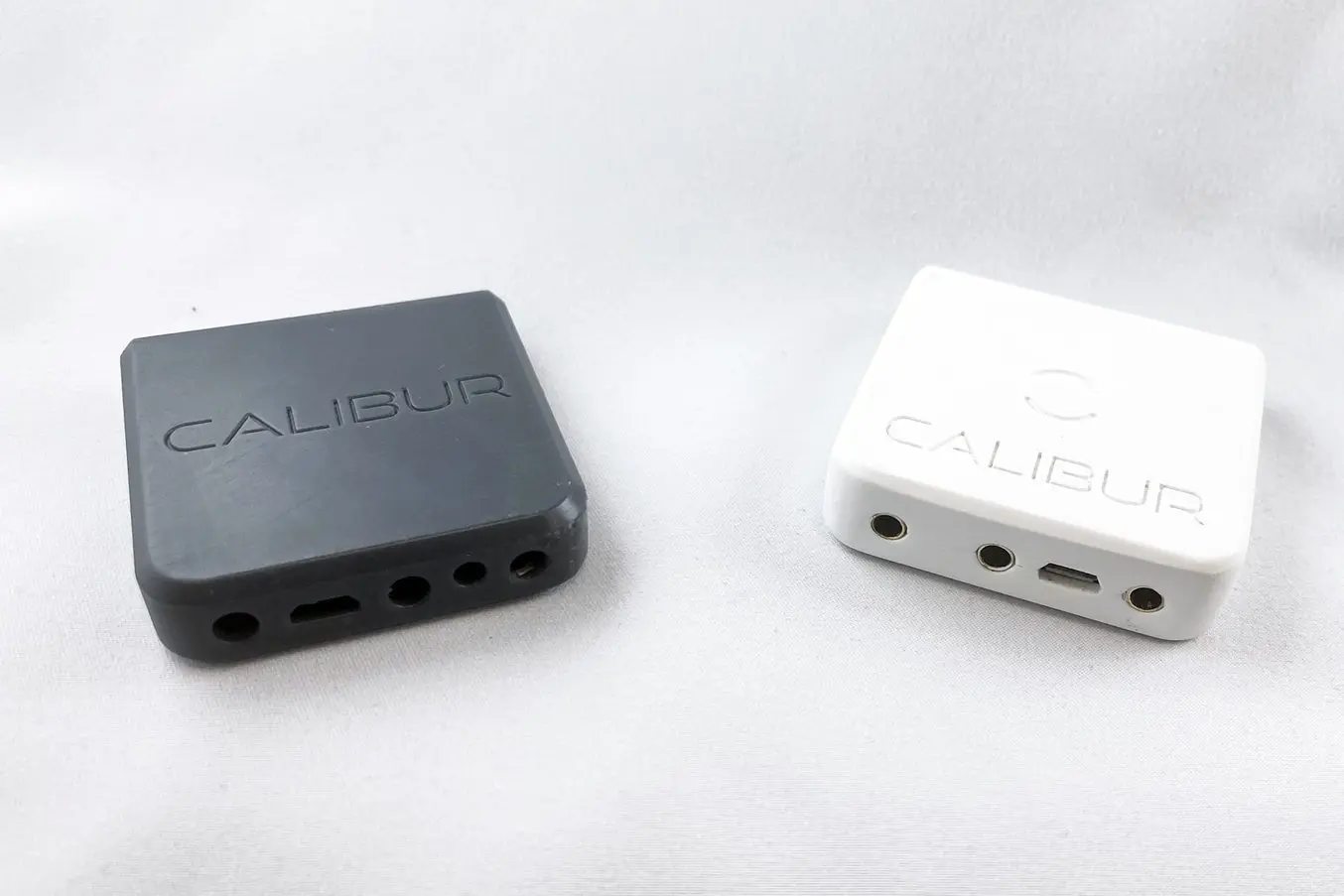
Anschließend nutzte das Team die SLA-gedruckten Teile als Modelle, um die erste kleine Serie von Endverbrauchstest-Einheiten im Vakuumguss herzustellen.
Louisville Slugger
Das Team im Louisville Slugger Innovation Center stellte fest, dass kleine Dinge einen großen Unterschied ausmachen. Seit 1884 stellt es Baseballschläger her und kennt alle Faktoren eines immer schnelleren und kraftvolleren Schwungs.
Die Mitarbeiter*innen des Slugger Innovation Centers verfolgen bei der Gestaltung von Sportgeräten einen analytischen Ansatz und haben mit den 3D-Drucklösungen von Formlabs einen Griffzusatz entwickelt. Die stufige Geometrie hilft Schlagmännern und -frauen beim perfekten Griff für den festmöglichsten Schlag.
Wie in anderen Fällen stellte das Slugger-Designteam fest, dass die Kombination von 3D-Druck und Vakuumguss unter einem Dach die Designiterationen beschleunigt und gleichzeitig das Wissen verbessert. Detaillierte Prototypenmodelle, die auf dem SLA-Drucker Form 3 mit einer Schichthöhe von 50 μm gedruckt wurden, dienten zur Erstellung eines positiven Formwerkzeugs. Dank der Leistungsfähigkeit des Urethangusses erreichte das Team robuste und testfähige Modelle, die fast der Qualität eines finalen Spritzgussprodukts aus Silikon entsprechen.
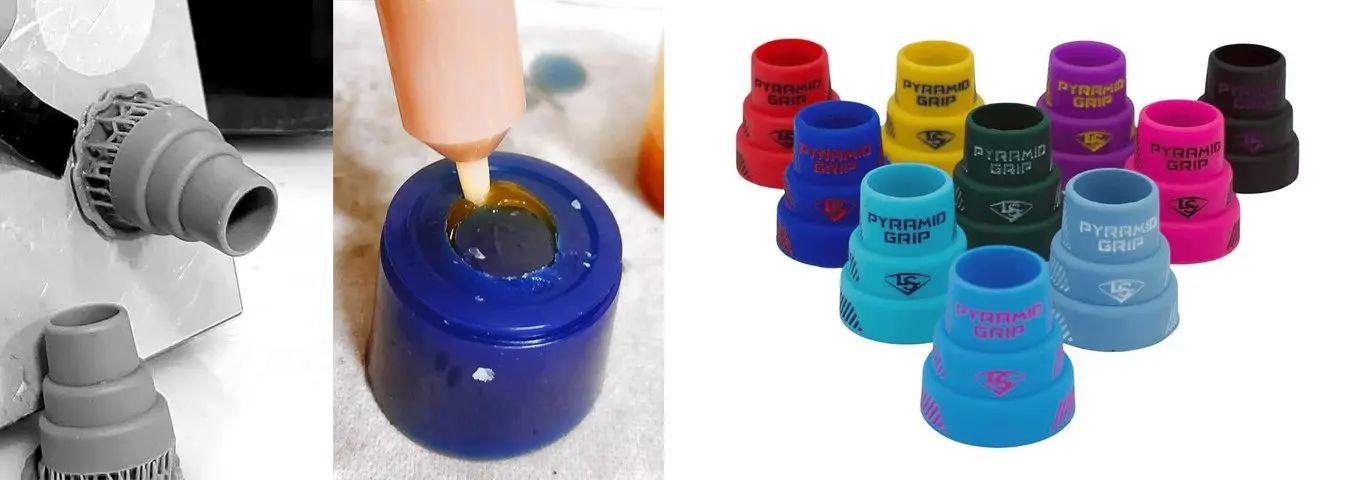
Vom 3D-gedruckten Positiv über betriebsinternen Guss bis zum fertigen Produkt
SiOCAST
SiOCAST hat bezüglich der Integration von 3D-Druck und Kunstharzguss eine einzigartige Geschichte zu erzählen. Mit dem Siegeszug der MMORPG-Online-Spiele sowie der RPG-Brettspiele ist die Nachfrage nach individualisierten Miniaturfiguren rasant gestiegen. Anstatt den kostspieligen Weg des Schleudergusses zu gehen oder sich auf die begrenzten Serien zu beschränken, die Vakuumguss-Silikonformen erlauben, entwickelte das Unternehmen ein patentiertes Kunstharzspritzsystem, das mit einer speziell dafür ausgelegten Maschine und HTV-Kautschukformen arbeitet.
Das hauseigene Material, SiOres, funktioniert sogar mit verflüssigten Thermoplast-Kunstharzen von bis zu 240 °C. Eine SiOCAST-Maschine ist bis zu zwanzigmal schneller als der herkömmliche Kunstharzguss und kann mit Automatisierung und rotierenden Multiformen bis zu 1000 Teile pro Stunde herstellen.
Alle Urmodelle werden mit einem SLA-Drucker von Formlabs 3D-gedruckt und nach dem Druck werden sie mit den automatisierten Reinigungs- und Nachhärtesystemen von Formlabs nachbearbeitet, dem Form Wash und Form Cure . Durch wiederverwendbare Produktionswerkzeuge aus dem SLS-3D-Drucker wird der Prozess weiter beschleunigt, mit bis zu 64 Miniaturen pro Guss.
Im Gegensatz zum Spritzguss, der gelegentlich Fehler aufweist, da er mit schwierigeren Bedingungen und zähflüssigen Materialien umgehen muss, sind diese Vakuumgussmodelle stets einwandfreie Nachbildungen der ursprünglichen Skulpturen, die viele Spieler begeistern.
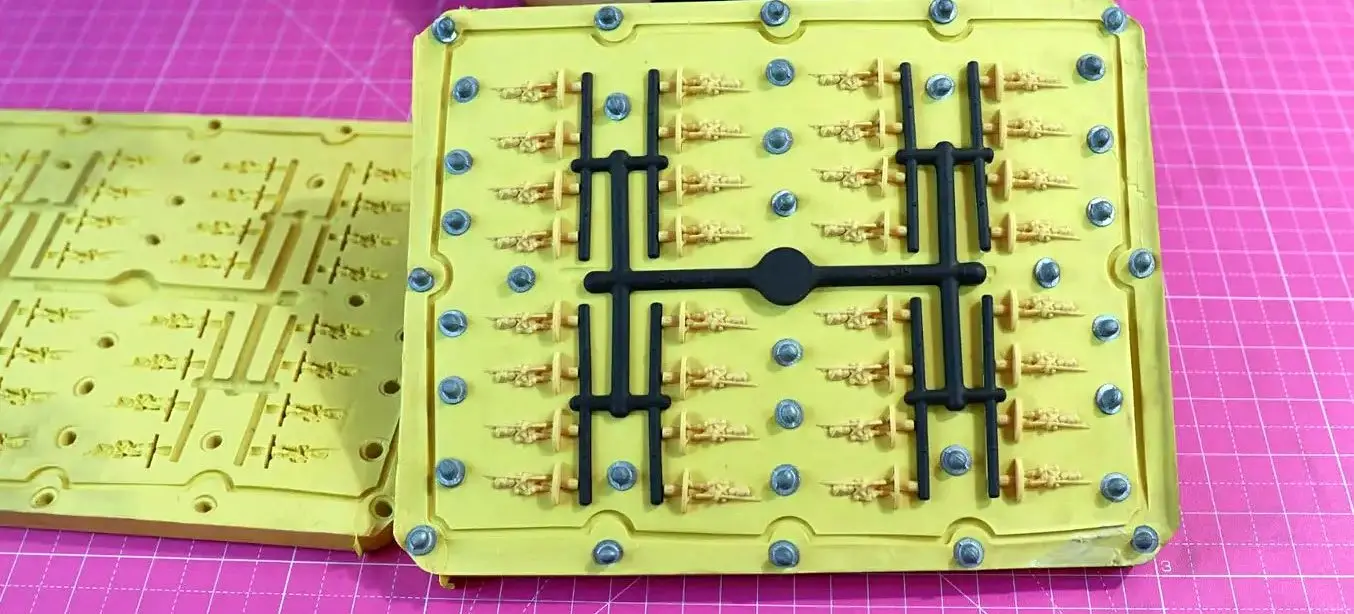
SiOCAST setzt auf ein eigens entwickeltes HTV-Silikon, SLA-Urmodelle und wiederverwendbare SLS-Nylonkanäle, um Miniaturen in Serien von bis zu 10 000 Stück zu erstellen.
Erste Schritte mit Vakuumguss und 3D-Druck
Vakuumguss ist der ideale Prozess zur Herstellung formgerechter Produkte und vermeidet die hohen Anfangsinvestitionen industrieller Produktionsmethoden. Das Verfahren eignet sich zur Herstellung von Prototypen, Modellen, Vorproduktionsserien und sogar Endprodukten für nahezu jede Anwendung. Das gegossene Modell ist eine exakte Kopie des Urmodells, sofern die Produktgeometrie das Entformen ermöglicht und spezifische Designrichtlinien für das Vakuumgussverfahren erfüllt.
Darüber hinaus profitiert der Vakuumguss von den neuesten Entwicklungen im 3D-Druck, da der 3D-Druck mit seinen hochdetaillierten Urmodellen und extrem glatten Oberflächen perfekt mit dem Vakuumgussprozess harmoniert.
Im Gegensatz dazu gestaltet sich Vakuumguss in Eigenregie schwierig und erfordert die strikte Einhaltung aller Prozeduren. Mit hoher Präzision, einem unkomplizierten Ablauf und kurzen Vorlaufzeiten bietet der 3D-Druck auch eine lohnenswerte Alternative zum Vakuumguss, insbesondere in der Prototypenfertigung und zunehmend auch in der Produktion von Kleinserien.