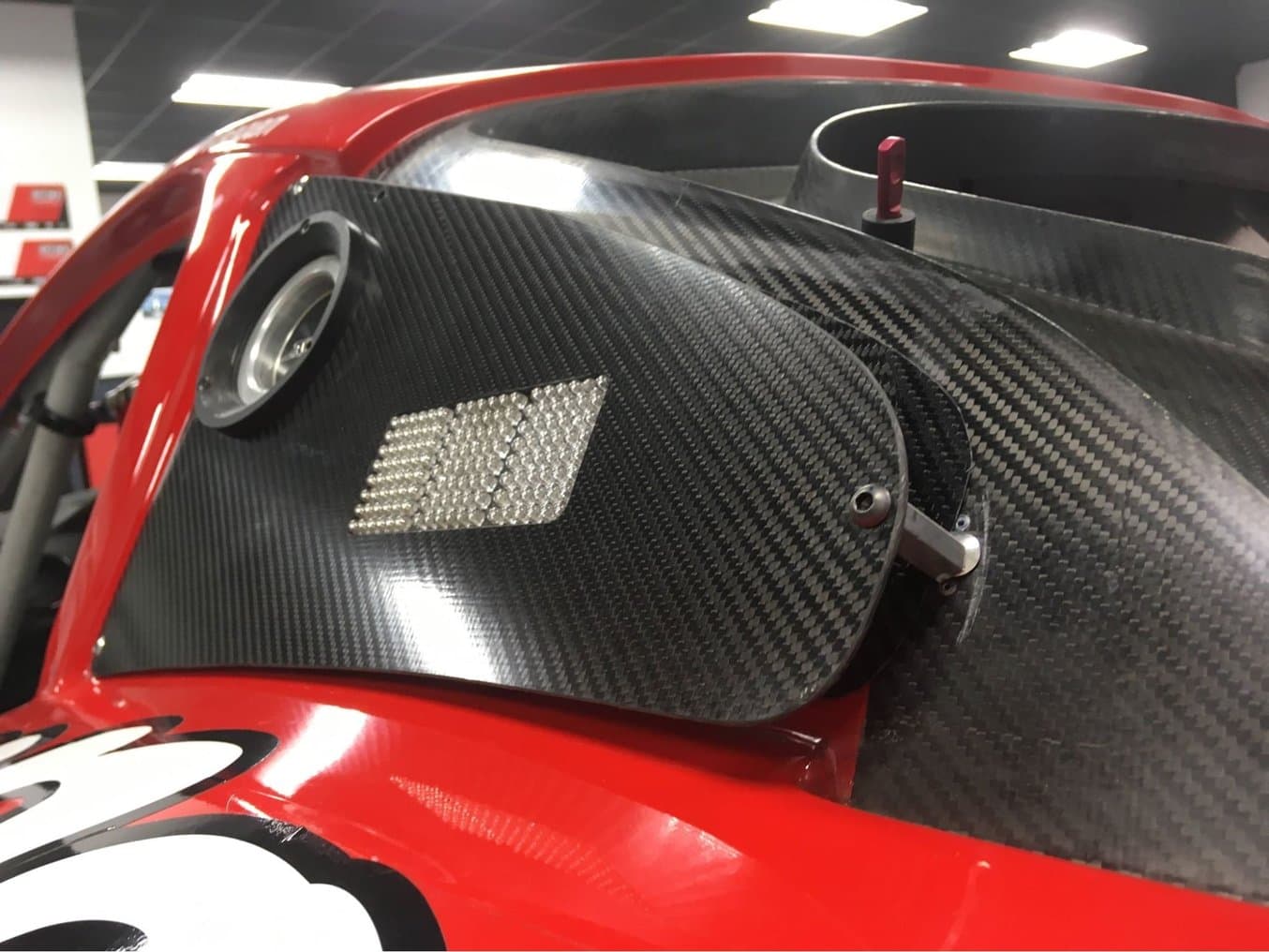
Verbundwerkstoffe wie beispielsweise kohlenstofffaserverstärkte Kunststoffe sind höchst vielseitige und effiziente Materialien, die die Innovation in vielen Branchen vorantreiben, z. B. in der Luft- und Raumfahrt oder im Gesundheitswesen. Dabei übertreffen sie traditionelle Materialien wie Stahl, Aluminium, Holz oder Kunststoff und ermöglichen die Fertigung leichtgewichtiger Hochleistungsprodukte.
In diesem Leitfaden erlernen Sie die Grundlagen der Herstellung von Kohlenstofffaserteilen, einschließlich mehrerer Methoden zur Schichtung von Kohlenstofffasern, Laminierung und Umformung, sowie Möglichkeiten, mit 3D-Druck die Kosten zu senken und Zeit zu sparen.
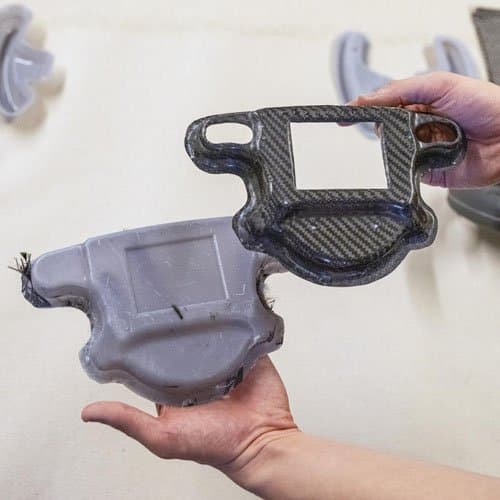
Fertigung von Kohlenstofffaserteilen mit 3D-gedruckten Formen
In diesem Whitepaper zur Herstellung von Kohlenstofffaserteilen erhalten Sie Designleitfäden für Verbundwerkstoffformen sowie schrittweise Anleitungen für die Prepreg- und Handlaminierung.
Was sind Verbundwerkstoffmaterialien?
Ein Verbundwerkstoff ist ein Werkstoff aus zwei oder mehr verbundenen Materialien, der andere Werkstoffeigenschaften besitzt als seine einzelnen Komponenten. Dabei verbessern sich üblicherweise die technischen Eigenschaften wie Festigkeit, Effizienz oder Haltbarkeit. Bei Verbundwerkstoffen ist eine Verstärkung in Form von Fasern oder Teilchen in eine andere Komponente eingebettet, die sogenannte Matrix (aus Polymer, Metall oder Keramik).
Faserverstärkte Polymere regieren den Markt und treiben neue Anwendungen in verschiedenen Branchen voran. Kohlenstofffaserverstärkter Kunststoff (auch CFK, Kohlefaser oder Carbon) ist eines davon und kommt als weit verbreiteter Verbundwerkstoff vor allem in Luftfahrzeugen, Rennwagen und Fahrrädern zum Einsatz, da es dreimal stärker und starrer ist als Aluminium und trotzdem 40 % weniger wiegt. Es wird als Verbund verstärkter Kohlenstofffaser mit Epoxidharz geformt.
Die Fasern können eine einheitlich direktionale Webung haben und strategisch ausgerichtet werden, um Festigkeit relativ zu einem spezifischen Vektor zu bieten. Fasern mit Kreuzgeflecht sorgen für Festigkeit gegenüber mehreren Vektoren. Außerdem sind sie verantwortlich für die gesteppte Optik, die man von Verbundwerkstoffteilen kennt. Üblicherweise werden Teile aus einer Kombination beider hergestellt. Es gibt viele verschiedene Arten von Fasern, dazu zählen:
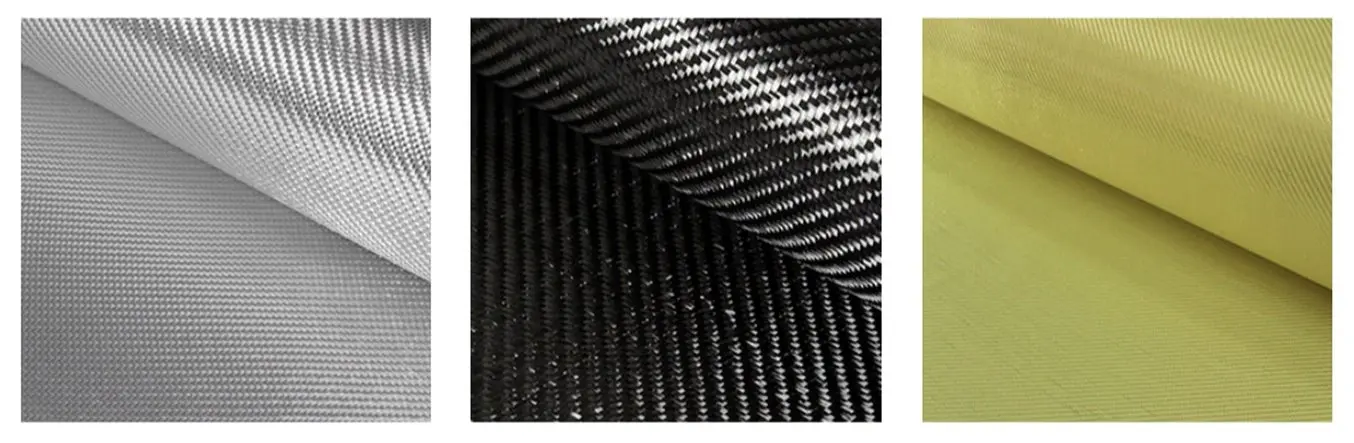
Glasfaser | Kohlenstofffaser | Aramidfasern (Kevlar) |
---|---|---|
Das beliebteste Fasermaterial Leichtgewichtig, moderate Zug- und Druckfestigkeit Kostengünstig und leicht zu verarbeiten | Höchste Festigkeit und bestes Verhältnis von Steifigkeit zu Gewicht (Zug-, Druck- und Biegebruchfestigkeit) Teurer als andere Fasern | Höhere Zähigkeit und mehr Abrasionswiderstand als bei Kohlenstofffaser Geringe Zugfestigkeit Schwer zu schneiden oder maschinell zu bearbeiten |
Harz hält diese Fasern zusammen und bildet einen harten Verbundwerkstoff. Es lassen sich Hunderte Harztypen verwenden. Hier sind einige der beliebtesten:
Kunstharz | Vorteile | Nachteile | Nachhärten |
---|---|---|---|
Epoxidharz | Höchste Zugfestigkeit Geringstes Gewicht Längste Haltbarkeit | Höchster Preis Reagiert empfindlich auf Mischungsverhältnis und Temperaturschwankungen | Verwendet einen spezifischen Aushärter (zweiteiliges System) Einige Epoxidharze benötigen Hitze |
Polyester | Leichte Handhabung (beliebteste Option) UV-beständig Niedrigster Preis | Geringe Festigkeit und Korrosionsbeständigkeit | Benötigt einen Katalysator (Methylethylketonperoxid) |
Vinylesterharz | Schlägt die Brücke zwischen der Leistung von Epoxidharz und den Kosten von Polyesterharz Beste Korrosions- und Temperaturbeständigkeit sowie Dehnung | Geringere Festigkeit als Epoxidharz und höhere Kosten als Polyesterharz Begrenzte Haltbarkeit | Benötigt einen Katalysator (Methylethylketonperoxid) |
Drei Methoden zur Produktion von Kohlenstofffaserteilen
Die Fertigung faserverstärkter Polymerteile wie beispielsweise bei Kohlenstofffaser benötigt viel Geschick und Arbeitsaufwand. Sie kommt sowohl bei der Produktion von Einzelstücken als auch von Serien zum Einsatz. Arbeitszyklen reichen von einer Stunde bis zu 150 Stunden, abhängig von der Größe und Komplexität des Teils. Üblicherweise werden bei der Fertigung faserverstärkter Polymere durchgängige, gerade Fasern in der Matrix eingebettet, um einzelne Lagen zu formen. Diese Lagen werden dann Schicht für Schicht auf das fertige Teil laminiert.
Die Eigenschaften des Verbundwerkstoffs stammen ebenso von den Materialien wie vom Laminierungsprozess – die Art und Weise, wie die Fasern eingebettet werden, hat große Auswirkungen auf die Leistung des Teils. Die Duroplast-Harze nehmen zusammen mit der Verstärkung in einem Werkzeug oder einer Form die gewünschte Gestalt an. Durch Aushärtung wird dann daraus ein festes Produkt. Es gibt verschiedene Laminierungstechniken, die sich in drei Haupttypen untergliedern lassen:
1. Handlaminierung
Bei der Nasslaminierung wird das Fasermaterial in eine Form gelegt. Danach wird mit einem Pinsel, einer Rolle oder einer Sprühpistole das Harz aufgetragen. Diese Methode benötigt das meiste Geschick, um hochqualitative Teile herzustellen. Sie ist jedoch auch die billigste und einstiegsfreundlichste für eigenproduzierte Kohlenstofffaserteile. Falls die Herstellung von Kohlenstofffaserteilen für Sie Neuland ist und Sie noch nicht über die nötige Ausrüstung verfügen, empfehlen wir Ihnen zunächst die Nasslaminierung von Hand.
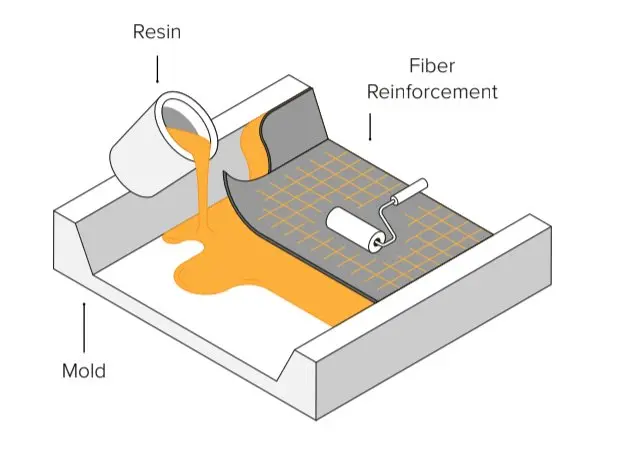
Dieses kurze Video zeigt den Nasslaminierungsprozess für Kohlenstofffaserteile.
2. Prepreg-Laminierung
Bei der Prepreg-Laminierung werden die Fasern vorher mit Harz angereichert. Die vorimprägnierten Bögen werden kalt gelagert, damit sie nicht aushärten. Die Lagen werden dann unter Hitze und Druck mittels eines Autoklavs in der Form ausgehärtet. Das lässt sich besser konsistent wiederholen und ist präziser, da die Harzmenge kontrollierbar ist. Es ist aber auch die teuerste Technik. Sie kommt für gewöhnlich bei Hochleistungsanwendungen zum Einsatz.
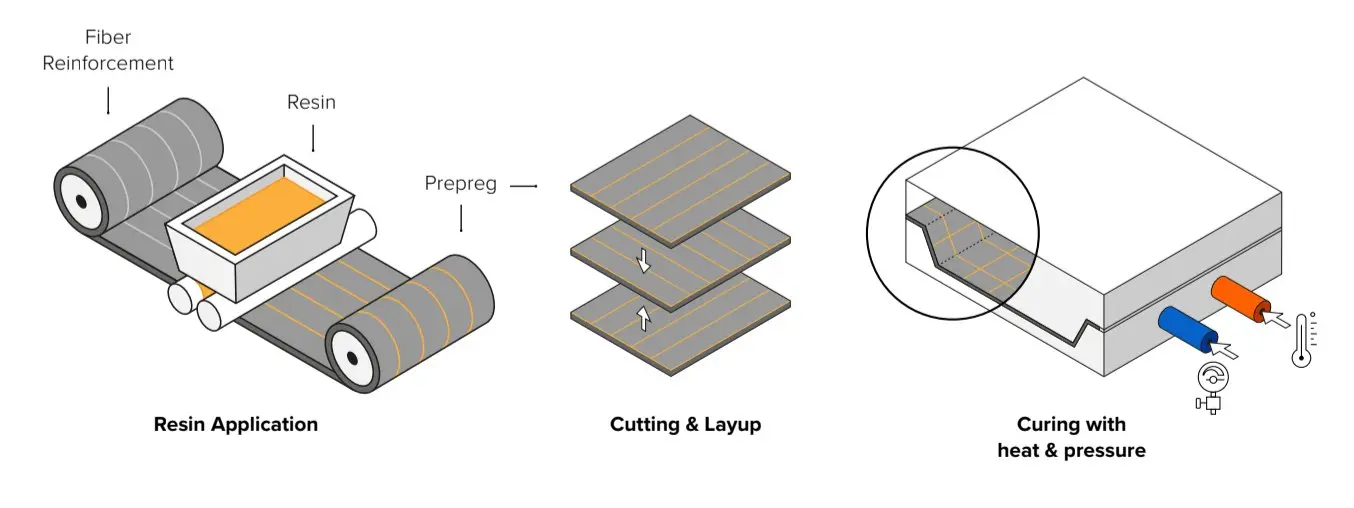
3. Resin Transfer Molding (RTM)
Beim RTM-Verfahren werden die trockenen Fasern in eine zweiteilige Form eingelegt. Die Form wird fest verschlossen und anschließend wird Kunstharz unter hohem Druck in den Hohlraum gespritzt. Der Prozess ist für gewöhnlich automatisiert und wird zur Produktion großer Mengen eingesetzt.
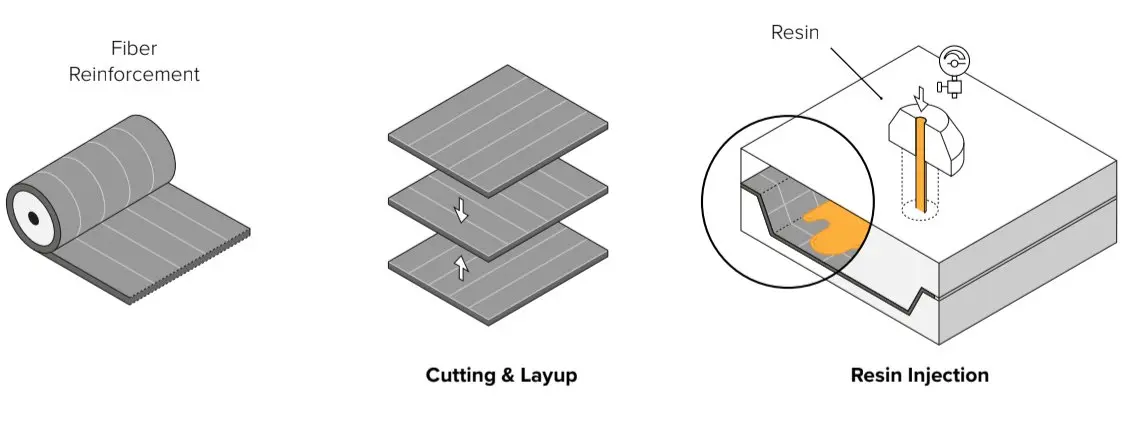
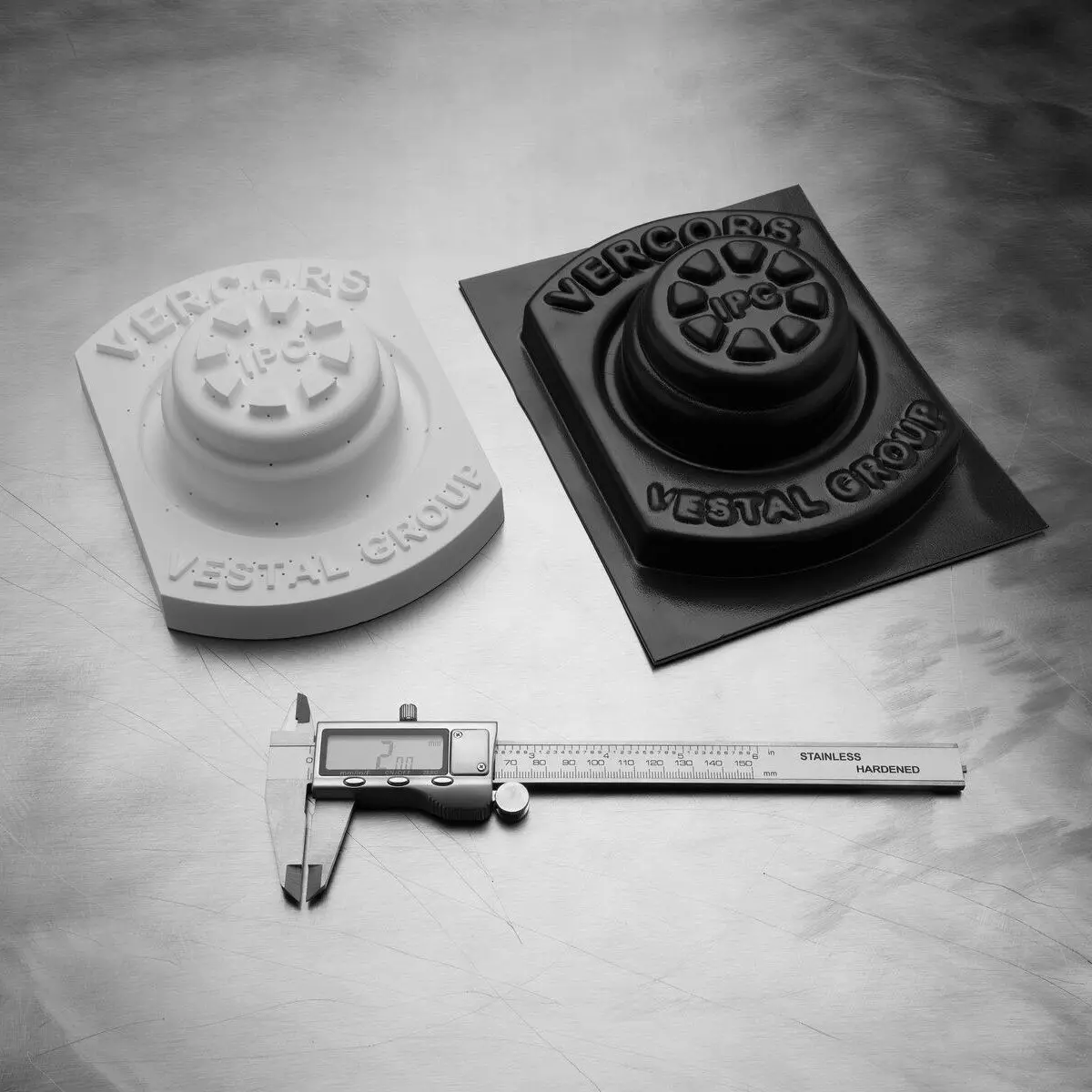
Schnelles Thermoformen in Kleinserie mit 3D-gedruckten Formwerkzeugen
Laden Sie unser Whitepaper herunter und erfahren Sie mehr über die schnelle Fertigung komplexer Formwerkzeuge mittels 3D-Druck. Wir geben außerdem Tipps und Richtlinien zur Vorbereitung der Bestandteile der Form.
3D-Druck von Formen zur Herstellung von Kohlenstofffaserteilen
Da die Qualität der Form die Qualität des fertigen Teils direkt beeinflusst, ist die Werkzeugbestückung ein entscheidender Aspekt der Fertigung faserverstärkter Polymere. Die meisten Formen bestehen aus Wachs, Schaumstoff, Holz, Kunststoff oder Metall aus CNC- oder Handbearbeitung. Manuelle Techniken sind höchst arbeitsaufwändig und CNC-Bearbeitung durchläuft noch immer einen langwierigen Arbeitsprozess – insbesondere bei schwierigen Geometrien. Außerdem bringt das CNC-Outsourcing hohe Kosten und lange Durchlaufzeiten mit sich. Beide Optionen benötigen geübte Fachkenntnisse und gewähren nur geringe Flexibilität bezüglich Designiterationen und Anpassungen der Form.
Die Lösung dazu ist die additive Fertigung. Sie ermöglicht die schnelle Produktion der Formen und Modelle für die Herstellung von Carbonfaserteilen — und das Ganze bei geringen Kosten. Der Einsatz von Polymer-Werkzeugbestückung im Fertigungsprozess wächst stetig. Dabei ersetzen Sie metallische Werkzeuge durch betriebsintern gedruckte Kunststoffteile. Das ist eine leistungsstarke und kostengünstige Methode, um die Produktionszeiten zu verkürzen und gleichzeitig mehr Designfreiheit zu bekommen. Ingenieure arbeiten bereits mit 3D-Druckteilen aus Polymerharzen bei der Herstellung von Halterungen und Vorrichtungen für Methoden wie Faserwickelverfahren oder die automatisierte Faserpositionierung. Ebenso kommen gedruckte Formen und Formwerkzeuge für Kleinserien im Spritzguss, Thermoformen oder bei der Blechumformung zum Einsatz.
Betriebsinterner Desktop-3D-Druck benötigt nur wenig Ausrüstung und verringert die Komplexität des Arbeitsprozesses. Professionelle Kunstharz-Drucker wie der Form 3+ sind erschwinglich, einfach einzurichten und bei steigender Nachfrage gut skalierbar. Die Anfertigung großer Werkzeuge und Formen ist mit großformatigen 3D-Druckern wie dem Form 3L ebenfalls möglich.
Stereolithografie-3D-Druck (SLA) erstellt Teile mit sehr glatter Oberflächenbeschaffenheit, was bei Carbonfaser-Laminierungsformen ausschlaggebend ist. Das ermöglicht komplexe Geometrien mit höchster Präzision. Außerdem bietet die Materialbibliothek von Formlabs technische Kunstharze mit mechanischen und thermischen Eigenschaften, die sich ideal zur Herstellung von Formen und Modellen eignen.
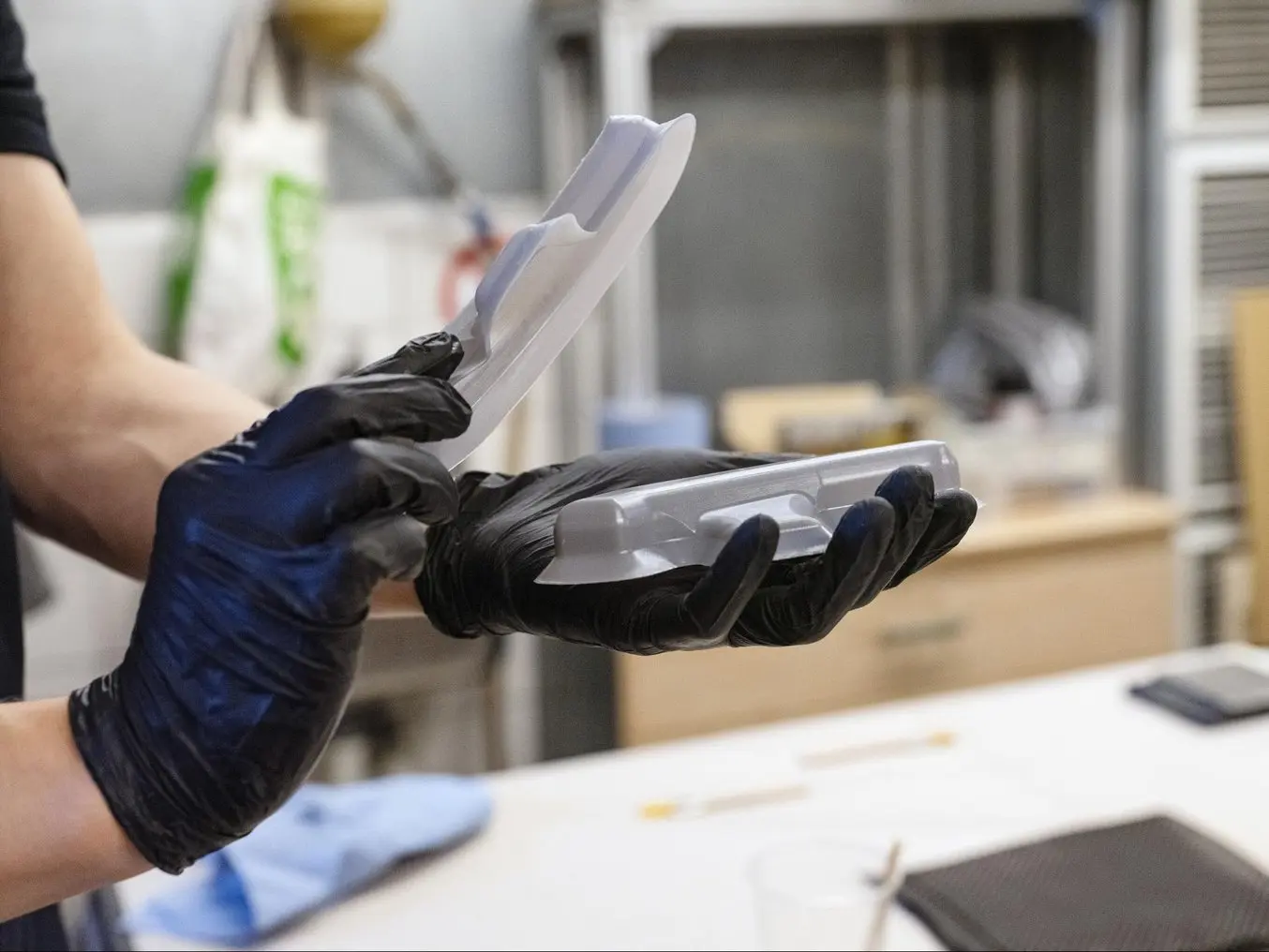
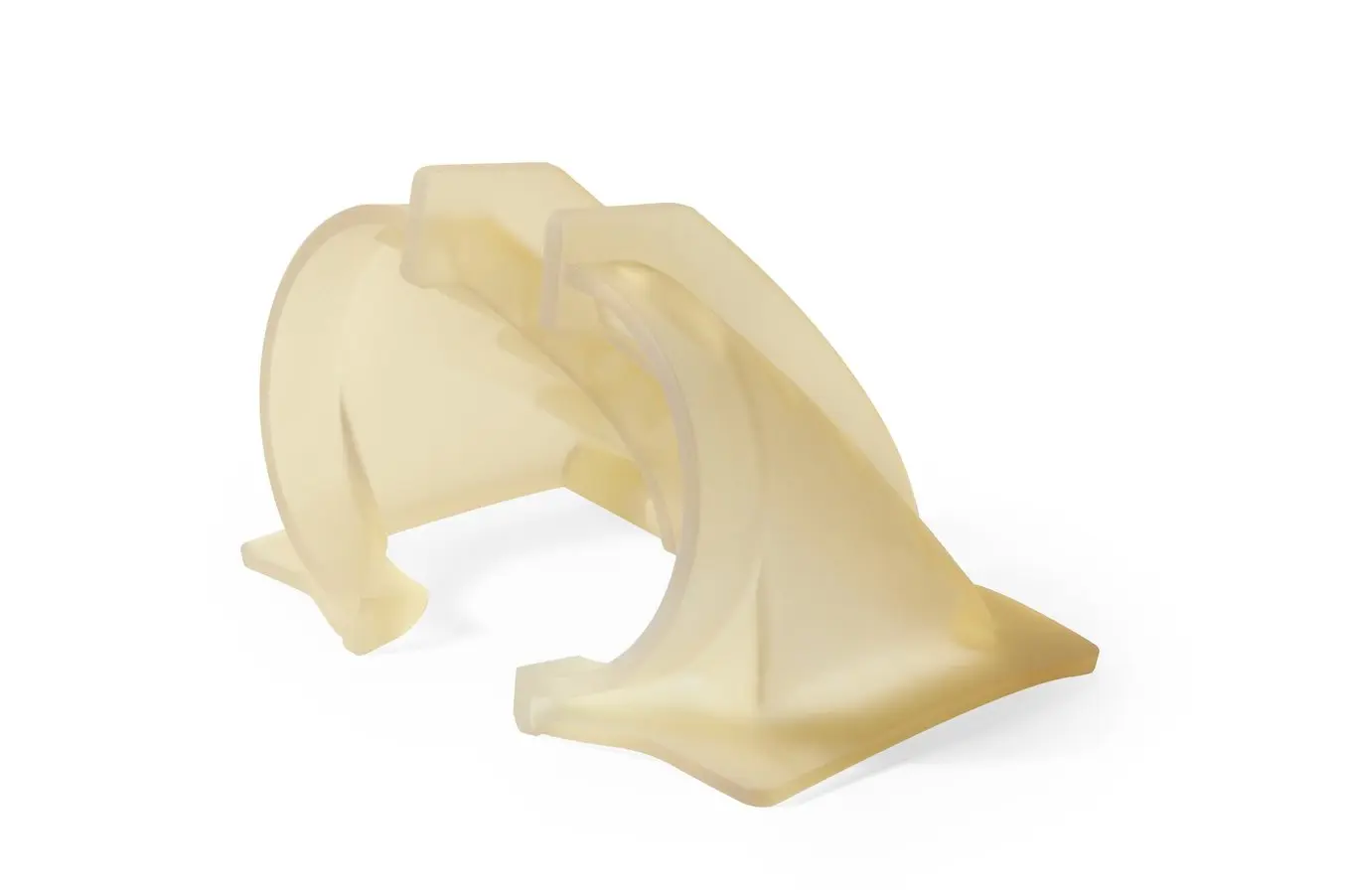
3D-gedruckte Formen verringern die Kosten und die Durchlaufzeit bei der Herstellung von Kohlenstofffaserteilen.
Für kleinformatige Teile können Ingenieure die Form in nur wenigen Stunden kostengünstig direkt drucken. So sparen Sie sich die manuelle Bearbeitung, CNC-Maschinerie, CAM-Software, maschinelle Einrichtung, Einspannung, Werkzeugbestückung oder Spanabfuhr. Arbeit und Durchlaufzeit des Formenbaus sind dabei drastisch verringert. Das wiederum ermöglicht schnelle Designiterationen und individuelle Anpassung der Teile. Dabei können sogar komplexe Formen mit filigranen Details hergestellt werden, die mit herkömmlichen Fertigungsmethoden nur schwer erzielbar wären.
Das Formula-Student-Team der TU Berlin (FaSTTUBe) hat ein Dutzend Kohlenstofffaserteile für Rennwagen angefertigt. Die Ingenieure des Team führen die Laminierung von Hand durch, in einer 3D-gedruckten Form aus Formlabs Tough 1500 Resin. Dieses Kunstharz besticht durch seinen Zugmodul von 1,5 GPa und eine Bruchdehnung von 51 %. Nicht nur ist es stark genug für den Laminierungsprozess, es ist außerdem flexibel genug, um das Teil nach der Aushärtung leicht von der Form zu trennen.
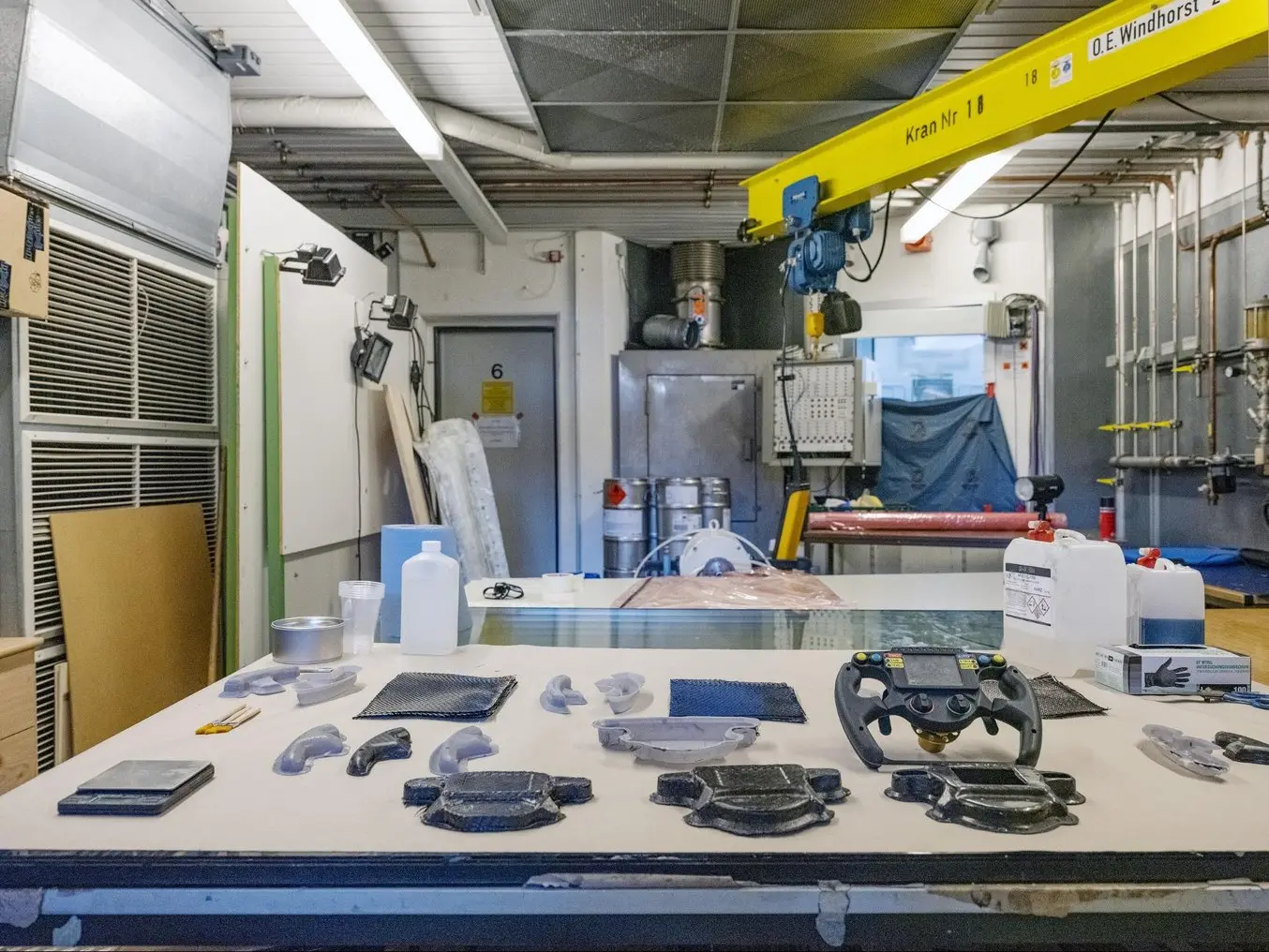
Die Werkbank des FaSTTUBe mit dem Fertigungsaufbau für Kohlenstofffaserteile
Diese Technik unterliegt nicht den intensiven Aushärtungsbedingungen der anderen Laminierungsprozesse mit höherem Druck und heißeren Temperaturen. Die Firma DeltaWing Manufacturing setzt High Temp Resin ein, um Luftstromkomponenten via Prepreg-Verfahren herzustellen. High Temp Resin hat eine Wärmeformbeständigkeitstemperatur von 238 °C bei 0,45 MPa und hält der Hitze und dem Druck eines Autoklavs somit stand. DeltaWing Manufacturing nutzt Direktdruck für die Formen einer Serie von etwa 10 maßgefertigten Teilen.
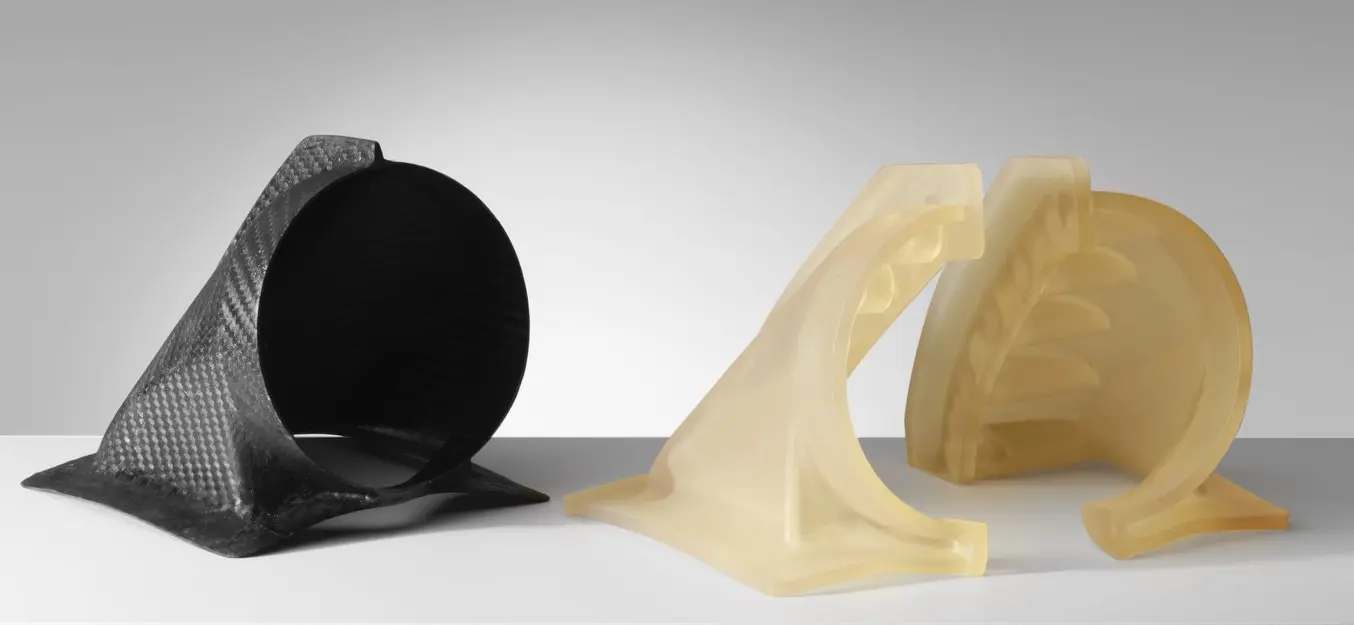
Ein Kotflügellufteinlass aus Carbon neben der zweiteiligen Form aus High Temp Resin, hergestellt von DeltaWing Manufacturing.
Der 3D-Direktdruck von Polymerformen ist ein großartiges Werkzeug zur Optimierung der Kleinserienfertigung. Leider ist ihre Lebensdauer verglichen mit traditionellen Formen begrenzt und deshalb eignen sie sich nicht für die Massenproduktion.
Um die Produktion also zu erhöhen, druckt DeltaWing Manufacturing auch Formmodelle aus High Temp Resin und gießt sie dann anschließend aus Kunstharz. Der Druck eines Formmodells ist auch eine gewinnbringende Alternative für Laminierungsprozesse mit fordernden Aushärtungsbedingungen, für die 3D-gedruckte Formen nicht in Frage kommen. Hersteller können individuelle Modelle nach Bedarf drucken und so einen Schritt beim Formenbau eliminieren: die Anfertigung des Modells.
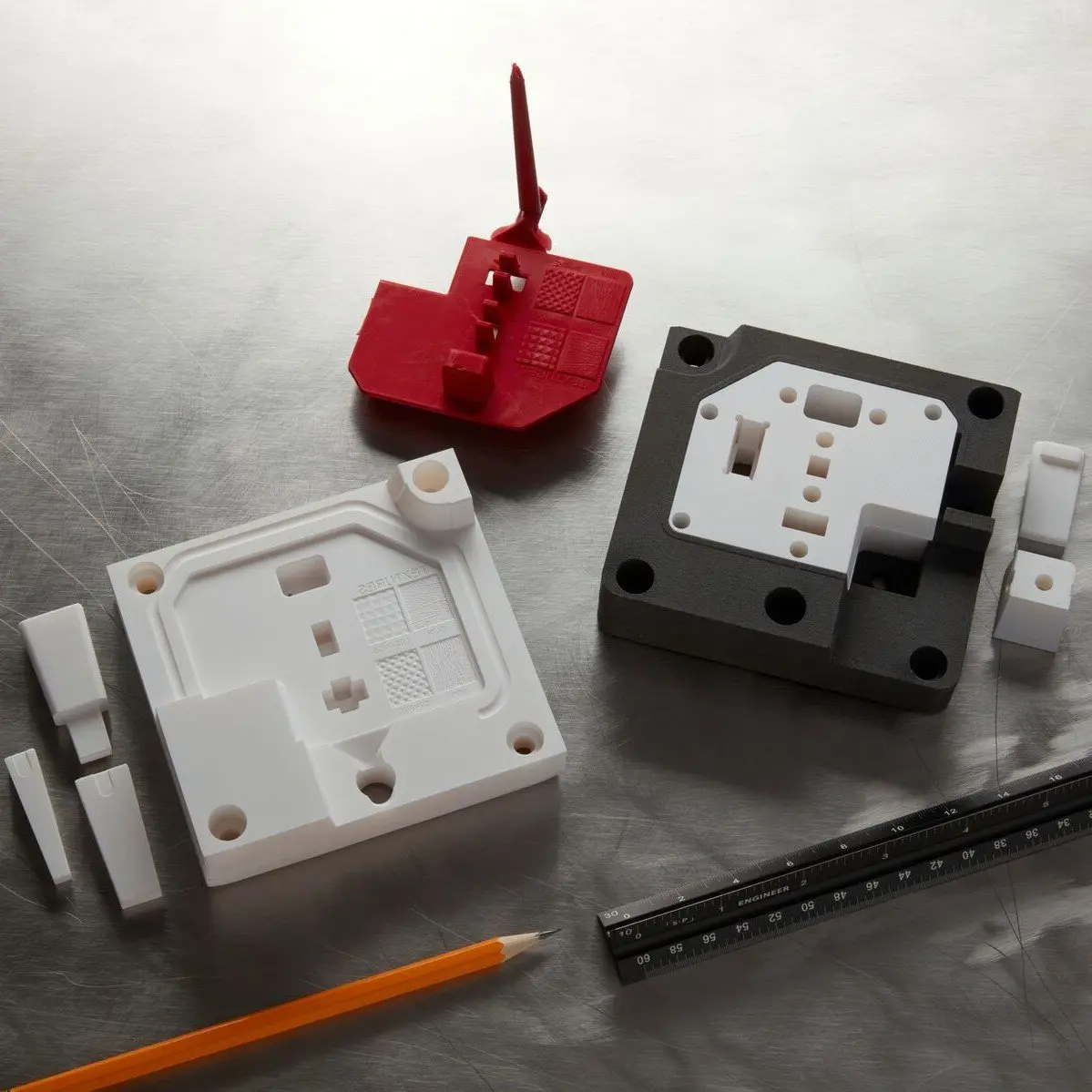
Leitfaden zum Rapid Tooling
In diesem Whitepaper sprechen wir über die Kombination von Rapid Tooling mit traditionellen Herstellungsverfahren wie Spritzguss, Thermoformen oder anderen Gießverfahren.
3D-Druck mit Kohlenstofffasern
Die Nachfrage nach Arbeitsabläufen, die die Festigkeit, Haltbarkeit und Robustheit traditioneller Carbonfaserteile mit der Agilität, der geometrischen Freiheit und der Reproduzierbarkeit des 3D-Drucks vereinen, ist sehr hoch. Daher überrascht es kaum, dass viele 3D-Druckunternehmen auch 3D-Druck von carbonfaserverstärktem Kunststoff anbieten, wobei die beiden bisher verfügbaren Prozesse entweder zerkleinerte oder durchgängige Fasern einsetzen.
Das mit Carbon-Kurzfasern angereicherte Nylon 11 CF Powder für den industriellen SLS-3D-Ducker (selektives Lasersintern) Fuse 1+ 30W produziert starke, leichte und hitzebeständige Teile, ohne auf herkömmliche Methoden wie Überzug oder Zerspanung angewiesen zu sein.
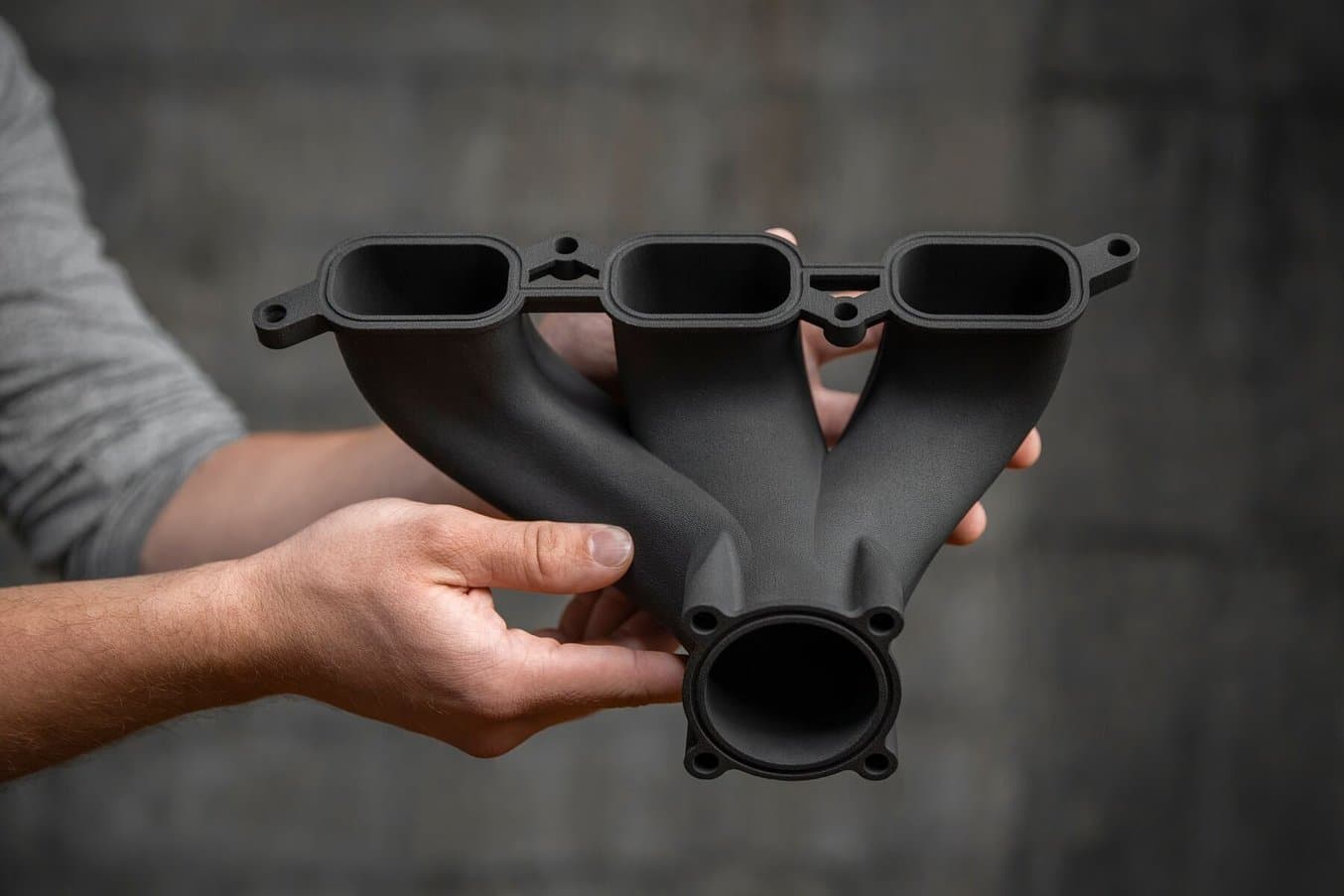
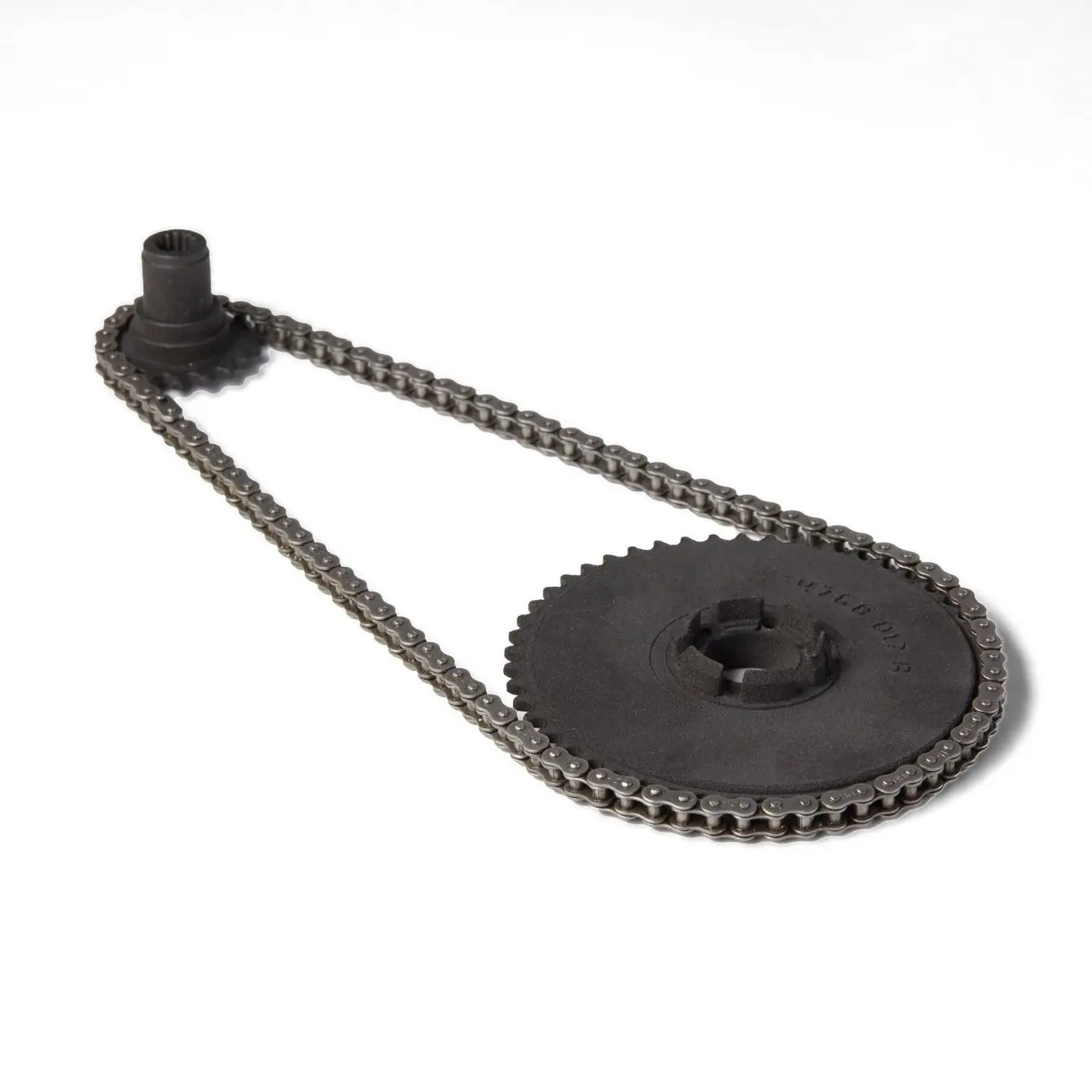
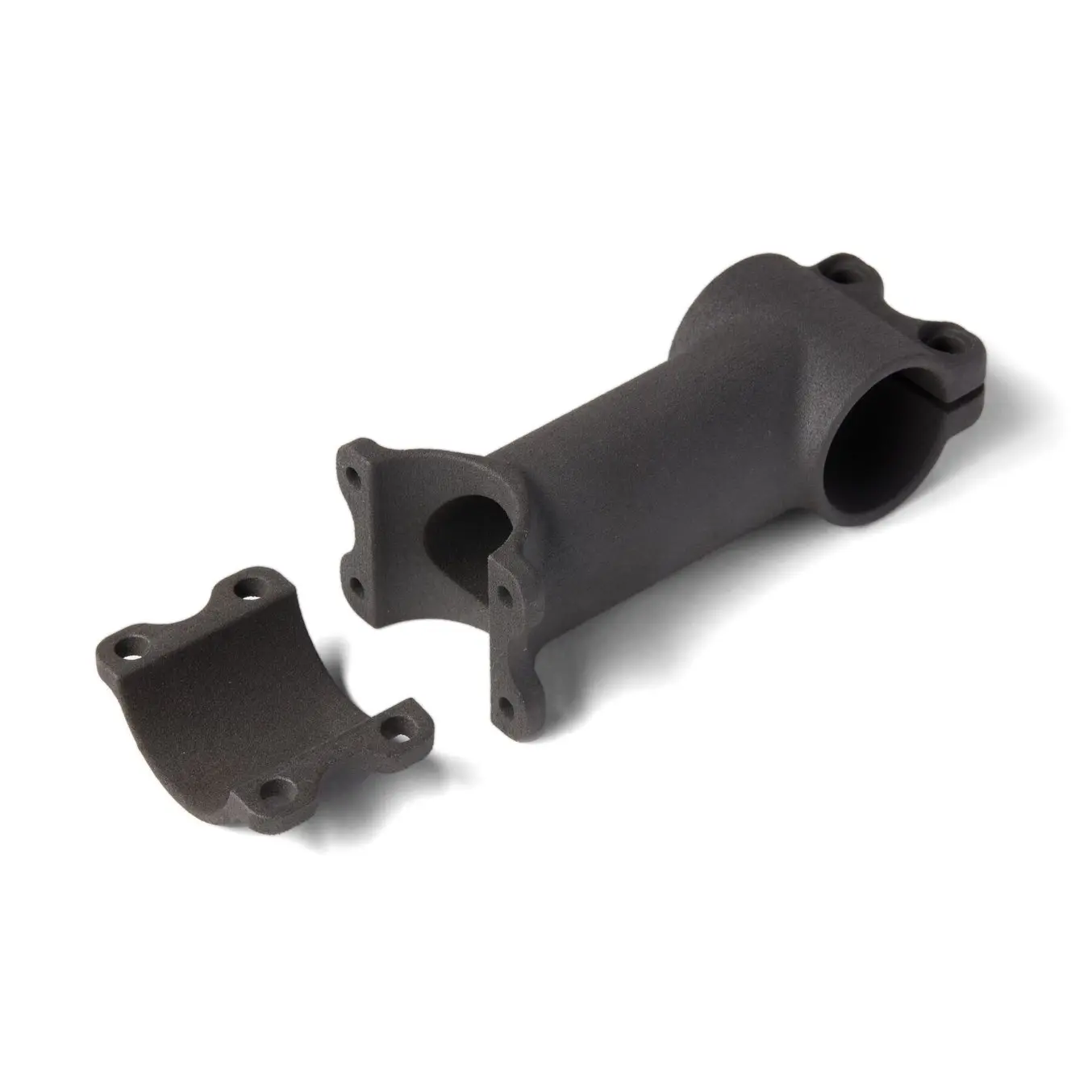
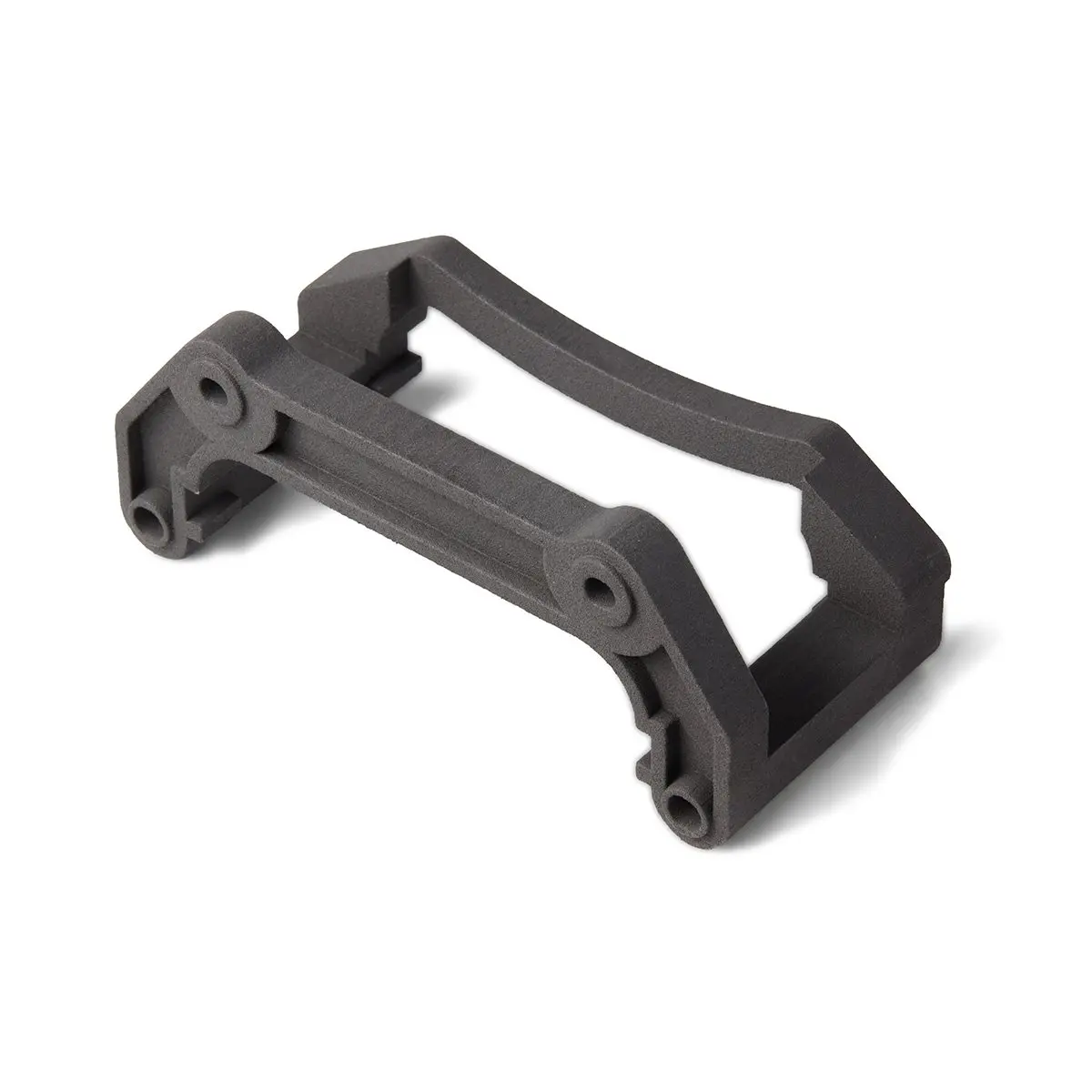
Nylon 11 CF Powder von Formlabs ist stark, leicht und hitzebeständig und damit ideal geeignet für Anwendungen in der Automobilindustrie, Luft- und Raumfahrt und der Fertigung.
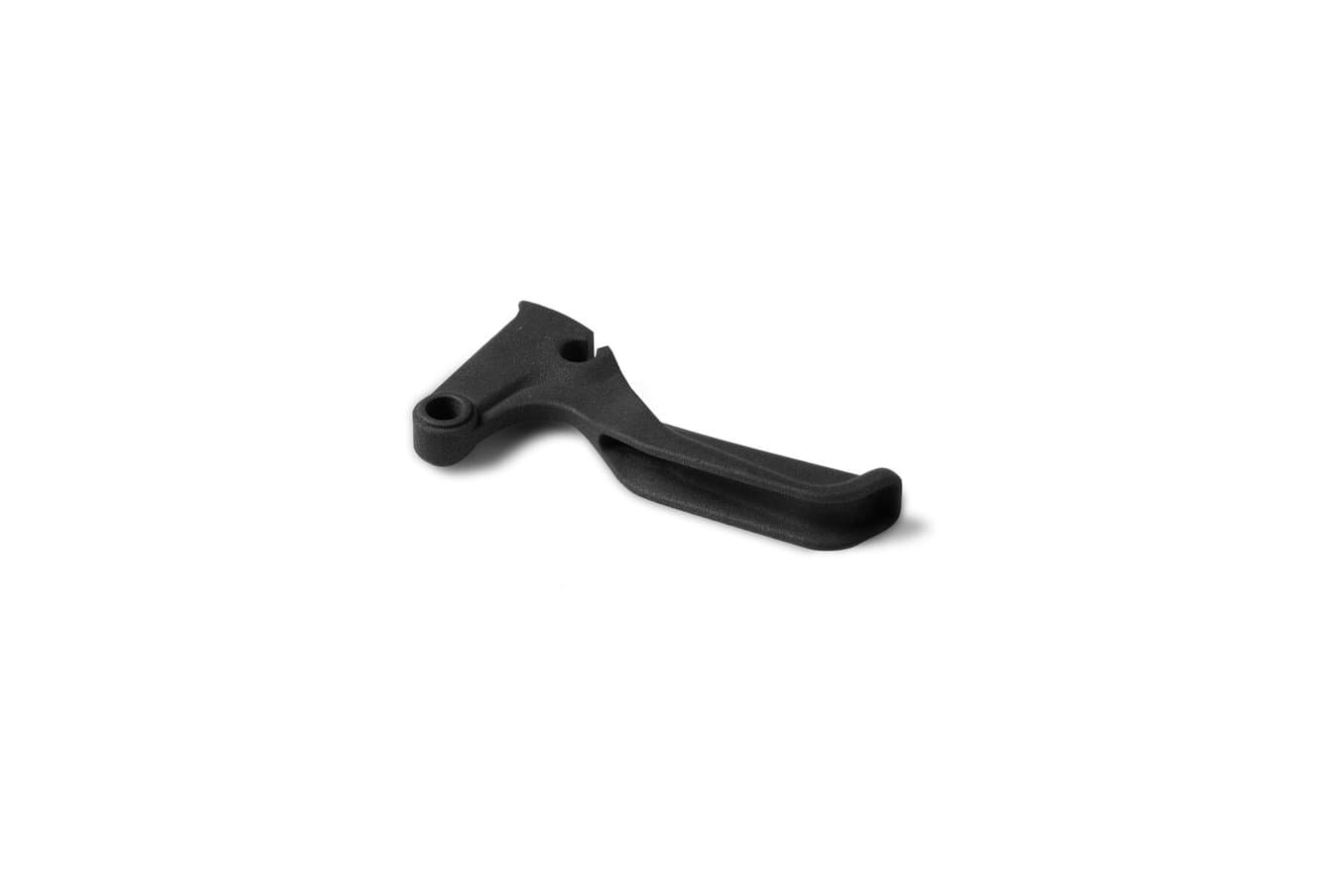
Kostenlosen Probedruck anfordern
Sehen und fühlen Sie die Qualität von Formlabs aus erster Hand. Wir senden Ihnen einen kostenlosen Probedruck an Ihren Arbeitsplatz.
Steigen Sie in die Kohlenstofffaser-Fertigung ein
Die Fertigung faserverstärkter Polymere ist ein aufregender, aber auch schwieriger und arbeitsaufwändiger Prozess. Mit 3D-gedruckten Formen und Modellen für Carbonfaserteile verringern Unternehmen die Komplexität dieses Arbeitsablaufs, gewinnen mehr Flexibilität und Gestaltungsfreiheit und reduzieren die Kosten sowie die Durchlaufzeit.
Anhand der Fallstudien der TU Berlin und von DeltaWing Manufacturing behandelt unser Whitepaper drei Arbeitsabläufe, die den 3D-Druck bei der Fertigung von Verbundwerkstoffen zur Produktion von Formen und Modellen nutzen.