Formlabs has hit many major milestones in the last ten and a half years—from our first Kickstarter campaign in 2011 to our $2 billion valuation in July 2021. Our mission, to expand access to digital fabrication so that anyone can make anything, has resonated with thousands of our users, and well, they’re making everything. Formlabs customers are printing end-use automotive parts, props for Hollywood blockbusters, and lifesaving medical devices, all powered by our stereolithography (SLA) and selective laser sintering (SLS) 3D printers.
Enabling Production
To reach 100,000,000 parts in just ten years, our users have been printing many parts, but more than that, they’ve also been able to scale up production of the same part, many times. We’ve worked hard to improve production capacity on our printers, which means dialing in the repeatability and consistency of the technology to ensure that they can run non-stop and be the work horses that businesses need them to be.
One customer established a new threshold of production capacity when they created the one product that every country, community, and individual can recognize after the past two years—the COVID-19 nasal swab. Singaporean Health Consortium National Additive Manufacturing Innovation Cluster (NAMIC) and Formlabs partner Eye-to-Eye Communications collaborated to produce over 30,000 nasal swabs per day on their Form 3 printers using Surgical Guide Resin. Formlabs co-founder and CEO Maxim Lobovsky spoke for the 3D printing community when he said that their efforts were “a testament to the agility and distributed manufacturing capabilities 3D printing can offer.”
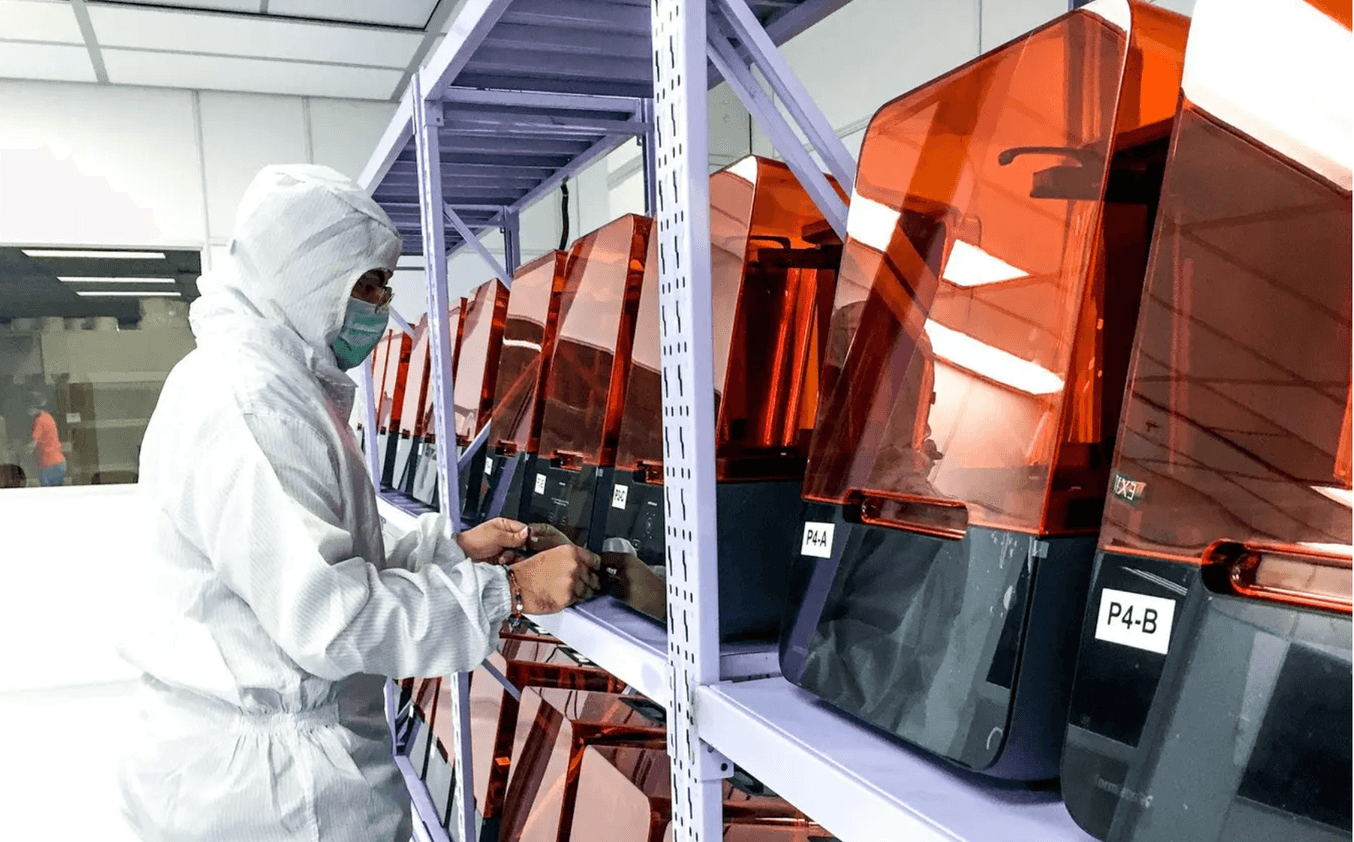
Another production customer, Ashley Furniture, uses every Formlabs printer, the Form 2, Form 3, Form 3L, and now Fuse 1 to keep their manufacturing process efficient. By creating 3D printed jigs and fixtures, Ashley Furniture improved their own production abilities, without spending resources on expensive tooling that needs to change with each of their product lines or models. The manufacturing company created 700 pieces with the Form 2 printers alone, and expanded their production, adding a Form 3, Form 3L, and Fuse 1 across two different manufacturing locations since then.
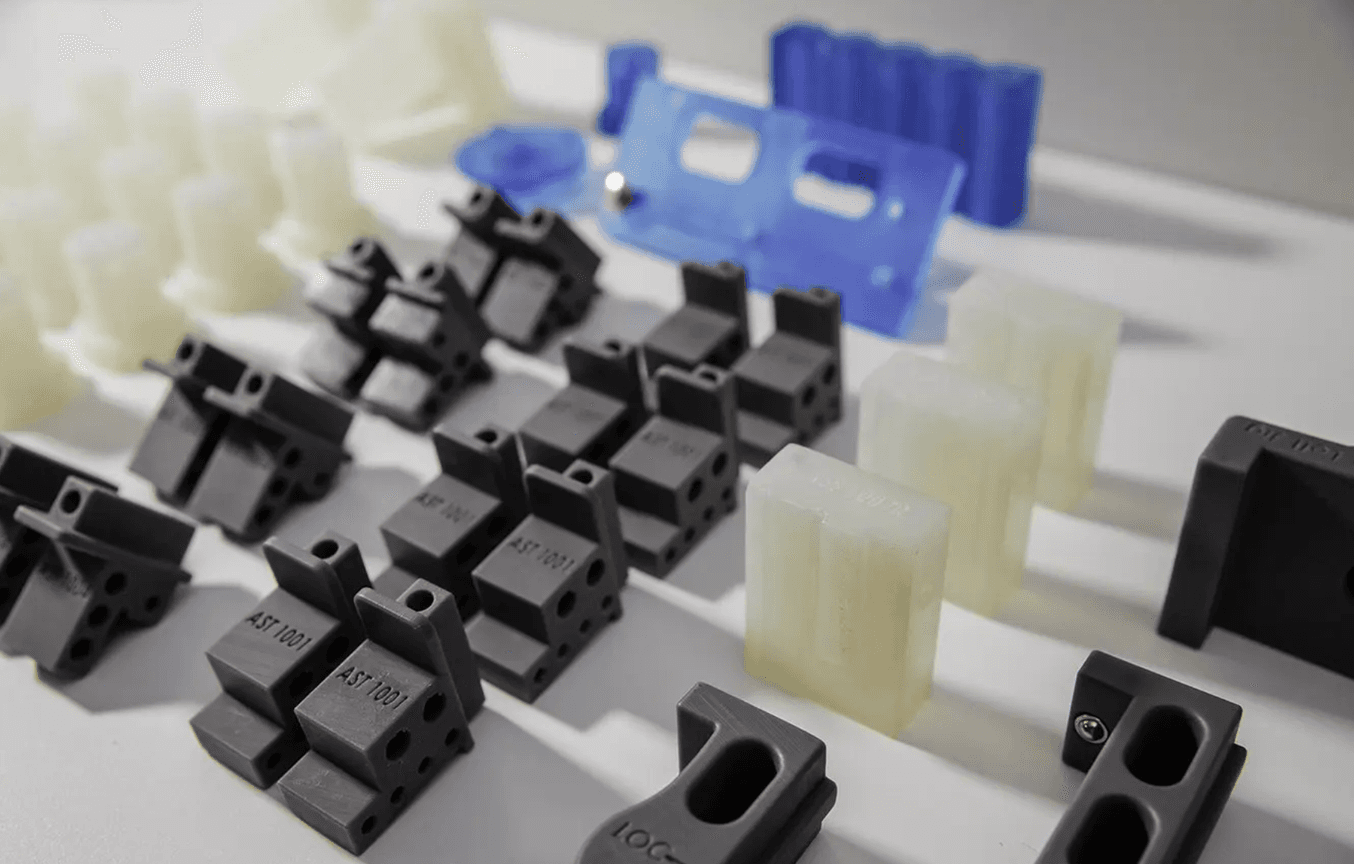
Customization
Though mass production will certainly always be the larger contributor to our overall number of prints, customization is gaining traction in each industry where additive manufacturing, and especially Formlabs printers, are utilized. No customization conversation would be complete without mentioning the dental industry, and Formlabs is committed to being a partner that dentists, lab owners, technicians, orthodontists, surgeons, and prosthodontists can rely on. Most people don’t know it, but the single biggest use by volume for 3D printing is the creation of orthodontic models— the parts on which the average retainer or aligner are formed!
The integration of cutting-edge scanning and design technology with the Formlabs printer and material workflow has improved standards of care and opened up the door to customization for every patient, clinic, and practice. Our customers have printed hundreds of thousands of teeth, including models in Grey Resin for thermoformed orthodontic appliances, restoration work in our Permanent Crown Resin, or even replacements in Denture Base and Denture Teeth Resins. Dental labs and practices have been some of the earliest adopters of 3D technology, and continue to push the industry towards faster, more precise printers and materials. Our reformulated Model Resin promises to make labs and practices even more efficient. With its high accuracy and consistency, Model Resin is specifically formulated for our dental customers.
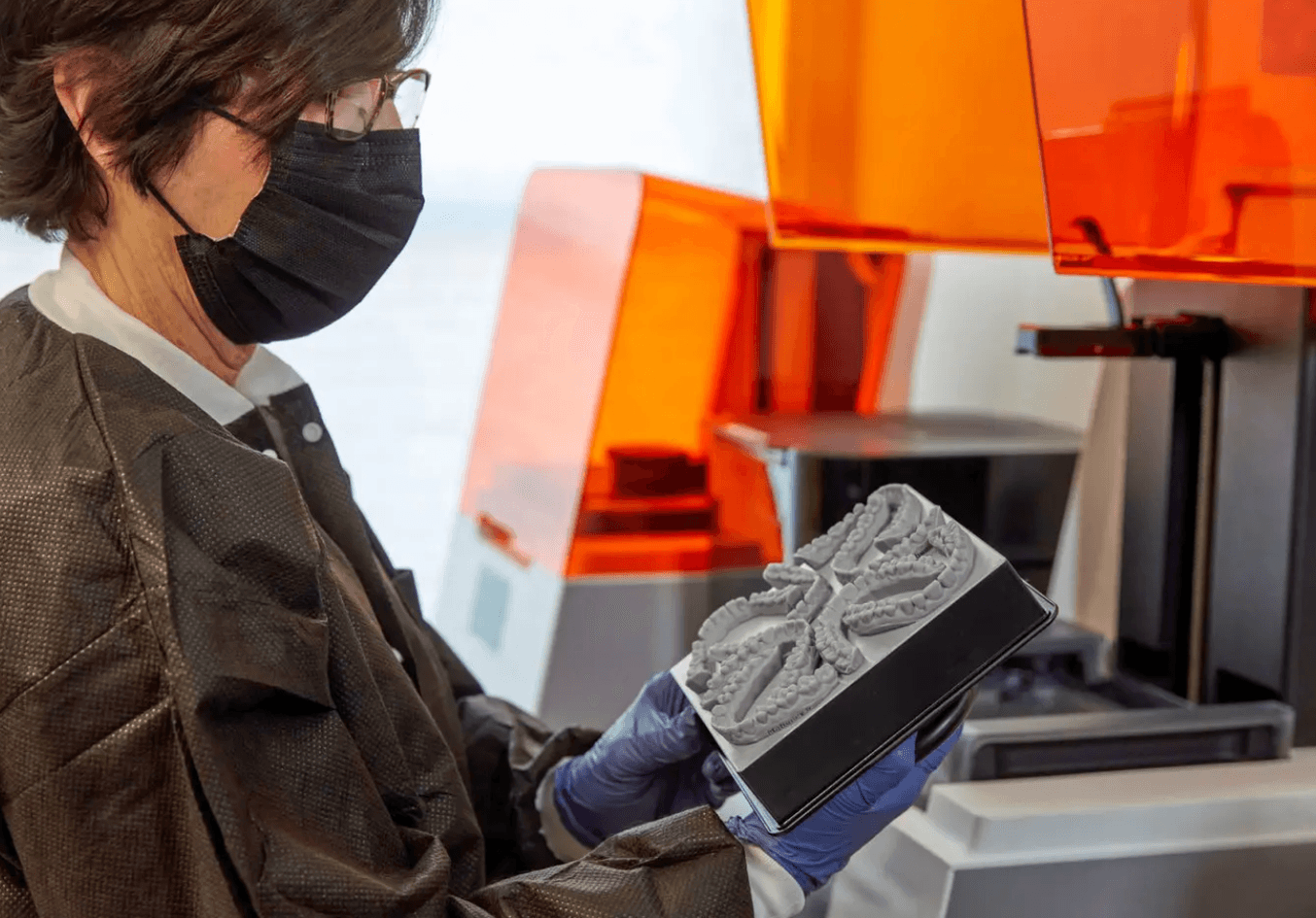
Customization in medicine doesn’t yield big numbers in terms of part production (after all, we hope each surgery involves as few bones as possible), but there is real, tangible improvement in operating room time, patient recovery, and surgical outcome when our point of care customers create surgical models on their Form 3+ and Form 3L printers.
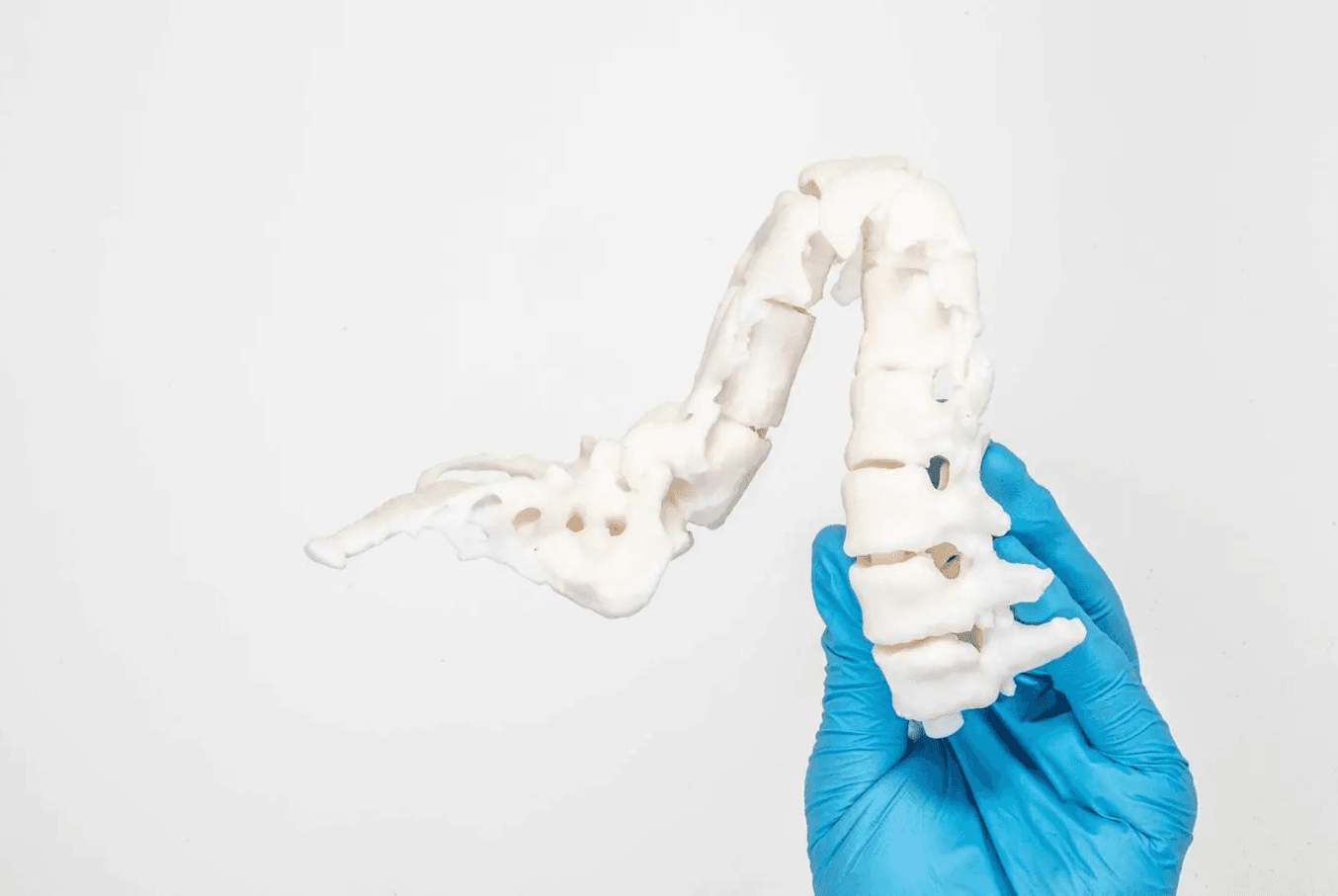
In some cases, customization can also happen at scale. Our partner Gillette’s innovation, the Razor Maker™ project, created customized razor blade handles for their customers, printing hundreds of models on the Form 2 printers using a variety of our resins. Consumer product customization is fairly new, but our Boston-based partners leveraged their best-selling brand awareness to bring attention to the possibilities of 3D printing.
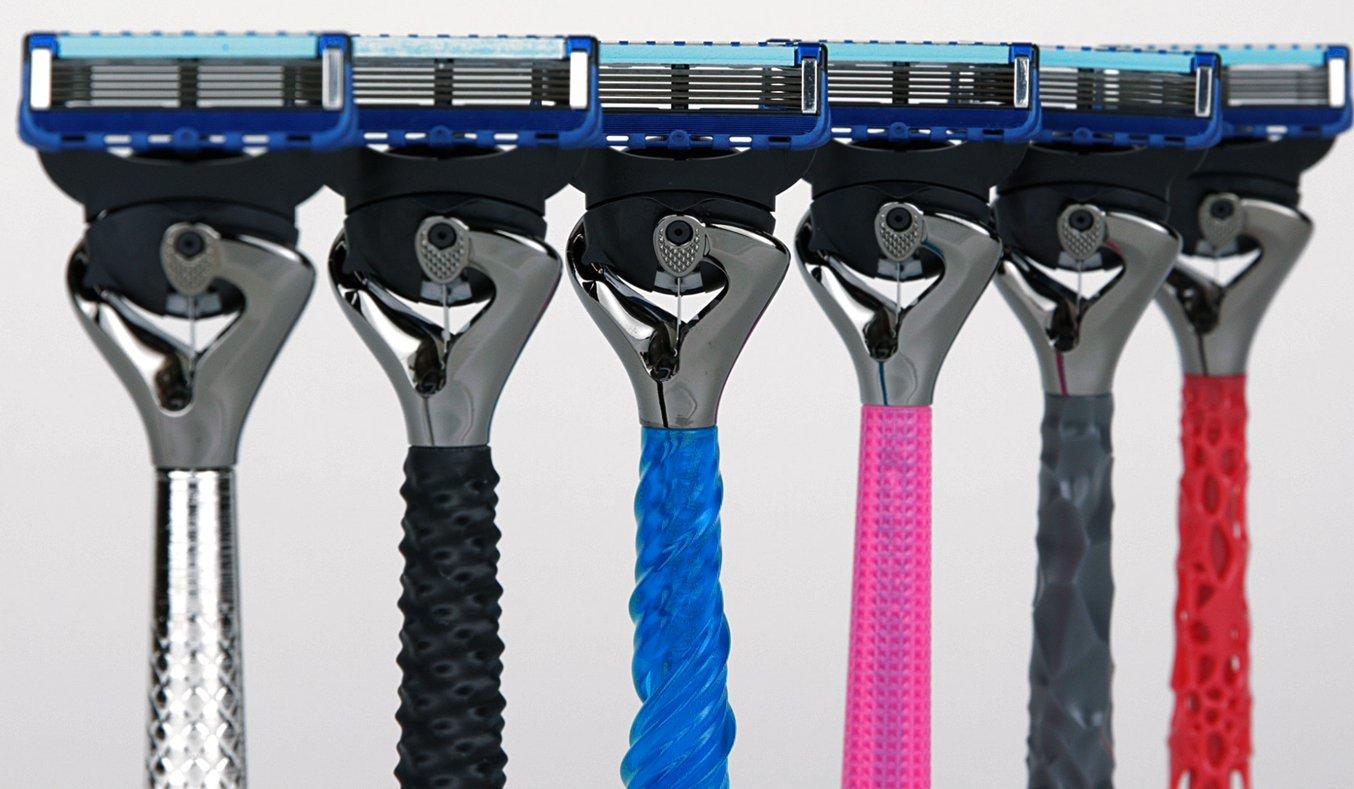
Razor handles printed on Formlabs printers as part of Gillette's Razor Maker™ platform.
The Evolution of Formlabs in Entertainment
We knew from the beginning that digital sculpting would be right in the wheelhouse of the powerful Formlabs SLA print engine, but we couldn’t have expected the amazing range of projects that our printers would be a part of.
From one of our first user stories in 2013 with Robert Vignone, a digital designer for Dreamworks, to our collaboration with Marvel’s Head of Props Russell Bobbitt, Formlabs has gone Hollywood (and stayed there). We work with some amazing production companies, like Aaron Sims Creative, who are printing custom props and prosthetics, set pieces, and even using the printers themselves as part of the plot. Fan favorites like Raised By Wolves, Stranger Things, and Grey’s Anatomy all feature Formlabs printed parts, costume components, and even printers themselves!
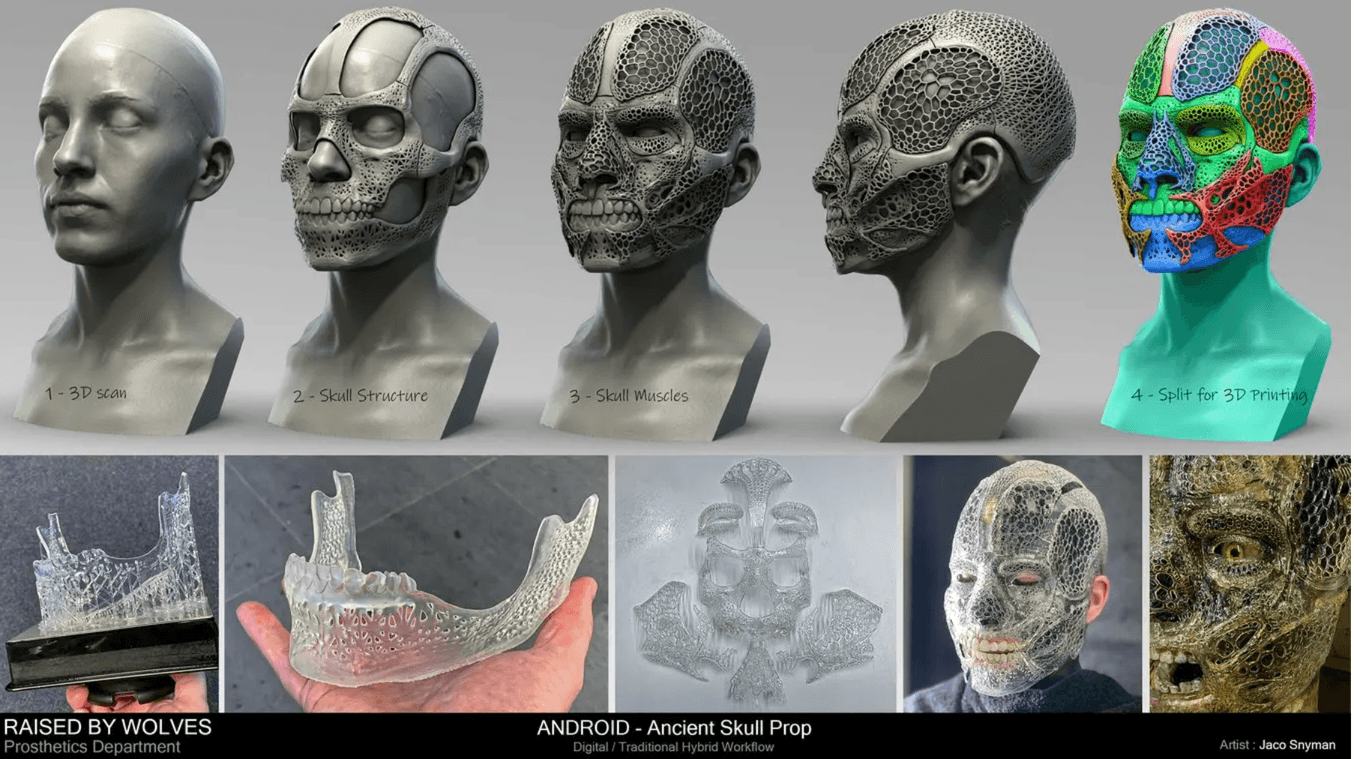
The Pursuit of Perfection
Both globally and among Formlabs customers, the most common 3D printing application is rapid prototyping. Product designers and engineers have seen the utility of industrial quality, accessibly sized 3D printers since our beginnings over ten years ago. Though their end result might be just one product, the pursuit of perfection requires tens, if not hundreds, of iterations, all coming together to help us hit this 100 million milestone.
Master jeweler Tariq Riaz creates works of architecturally inspired art, drawing on his engineering background to create rings that are functional, moving assemblies of up to 60 small pieces. He prototypes extensively, and each of those 60 parts might get redesigned 20 times. Though these parts are small, they must fit perfectly together and allow for a smooth expansion and contraction as the ring wearer moves.
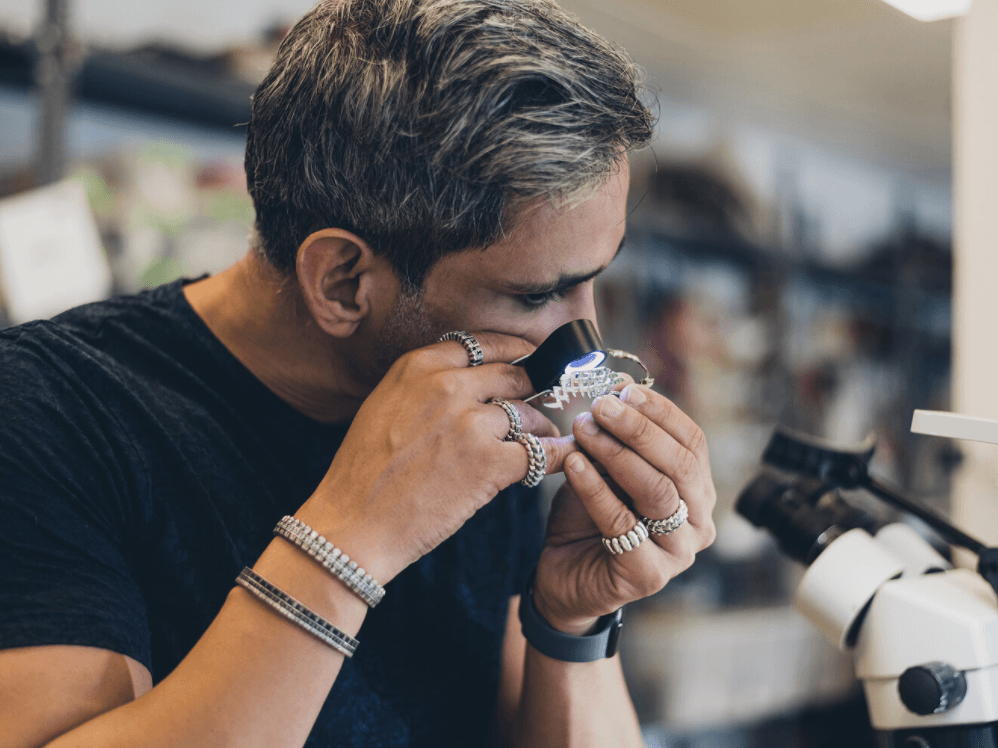
The automotive industry has always been at the forefront of innovation, ever since Henry Ford developed the modern assembly line process in 1908. Their continued drive to go faster and farther opens the door for new technologies to gain ground.
Automotive aftermarket manufacturer Dorman Products prototypes replacement parts for cars on their Form 3 and large-format Form 3L, creating a product catalog 180,000 lines long—and each of those products goes through its own prototyping process! Using almost every resin Formlabs offers, Dorman relies on the consistency of the Form 3 line to release up to 5,000 new products each year.
The Kids Are Alright
Though typically we talk about the customers who are using our printers in their careers as engineers, technicians, dentists, or designers, so much work to get to this 100 million milestone was done by the people who might not have figured out their career quite yet. Students in K-12 schools, community colleges, vocational programs, and universities are producing parts that challenge conventional design and manufacturing ideas, and their 3D design and printing skills are more in demand than ever.
For large industrial customers to keep printing, they’ll need to hire talented new workers, and starting 3D printing education in school is the best way to make sure the workforce is prepared. At large universities like The Pennsylvania State University, faculty and administration are emphasizing 3D printing as a tool to both prepare students for their careers and help upskill the workforce by involving the community. Using the Form 3, Form 3L, and Fuse 1 printers in the Eric J. Barron Innovation Hub, students and community members can print everything from prototypes to low volume production runs.
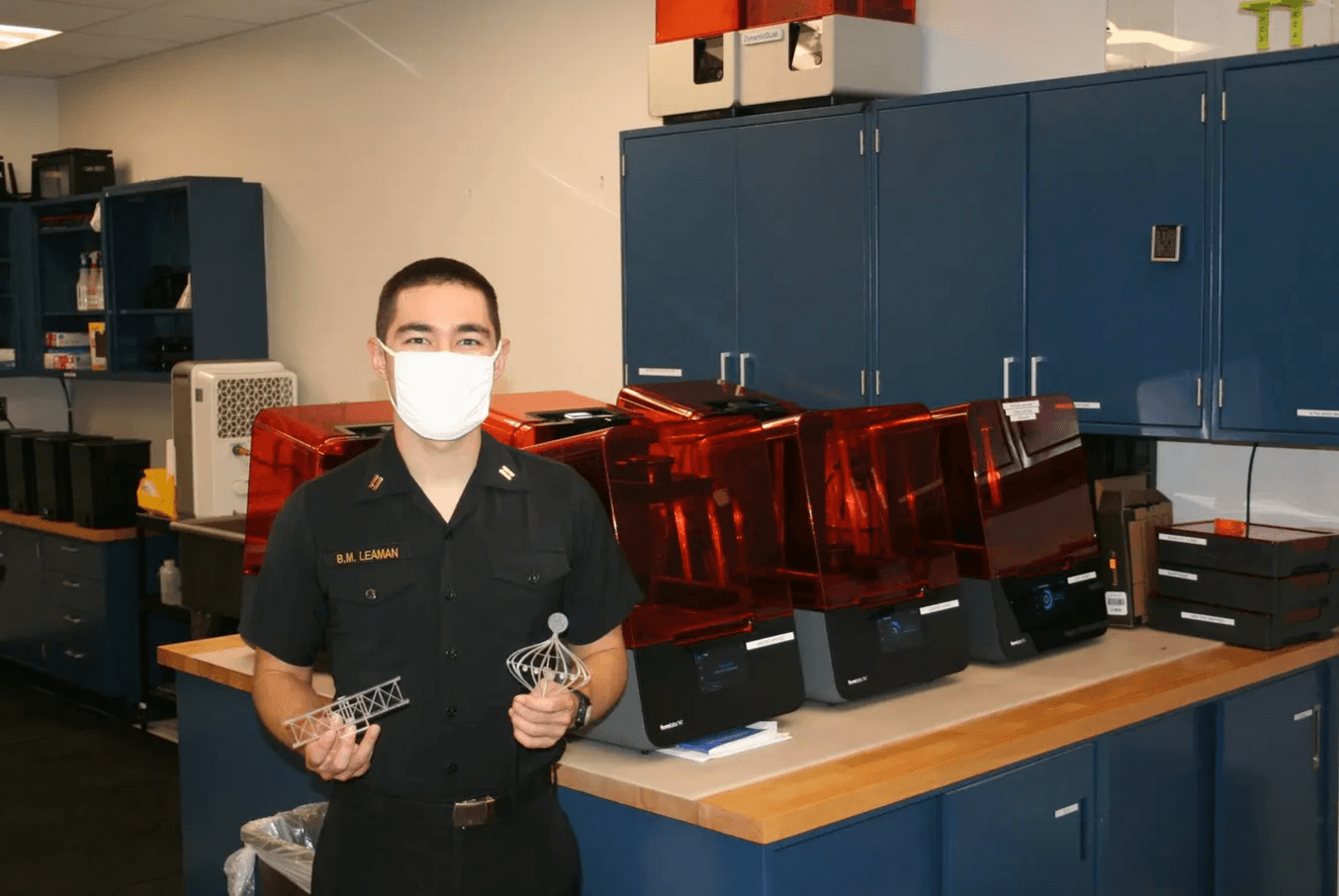
At the US Naval Academy’s MakerSpaceUSNA, Form 3 printers are put to work every day.
Celebrating Formlabs Users
To celebrate our amazing users, Formlabs is delighted to announce that the Formlabs User Summit will be returning as a fully virtual event running from October 26-27. Last year we gathered with thousands of users from 150 countries (with events in seven languages) and this year we expect even more global representation. We’ll be acknowledging a decade of innovation, sharing insights and celebrating milestones. We have a fantastic line of speakers, including innovators from NASA, Deutsche Bahn, the Mayo Clinic, and more! Tickets are completely free, and we’re so excited to see you there.
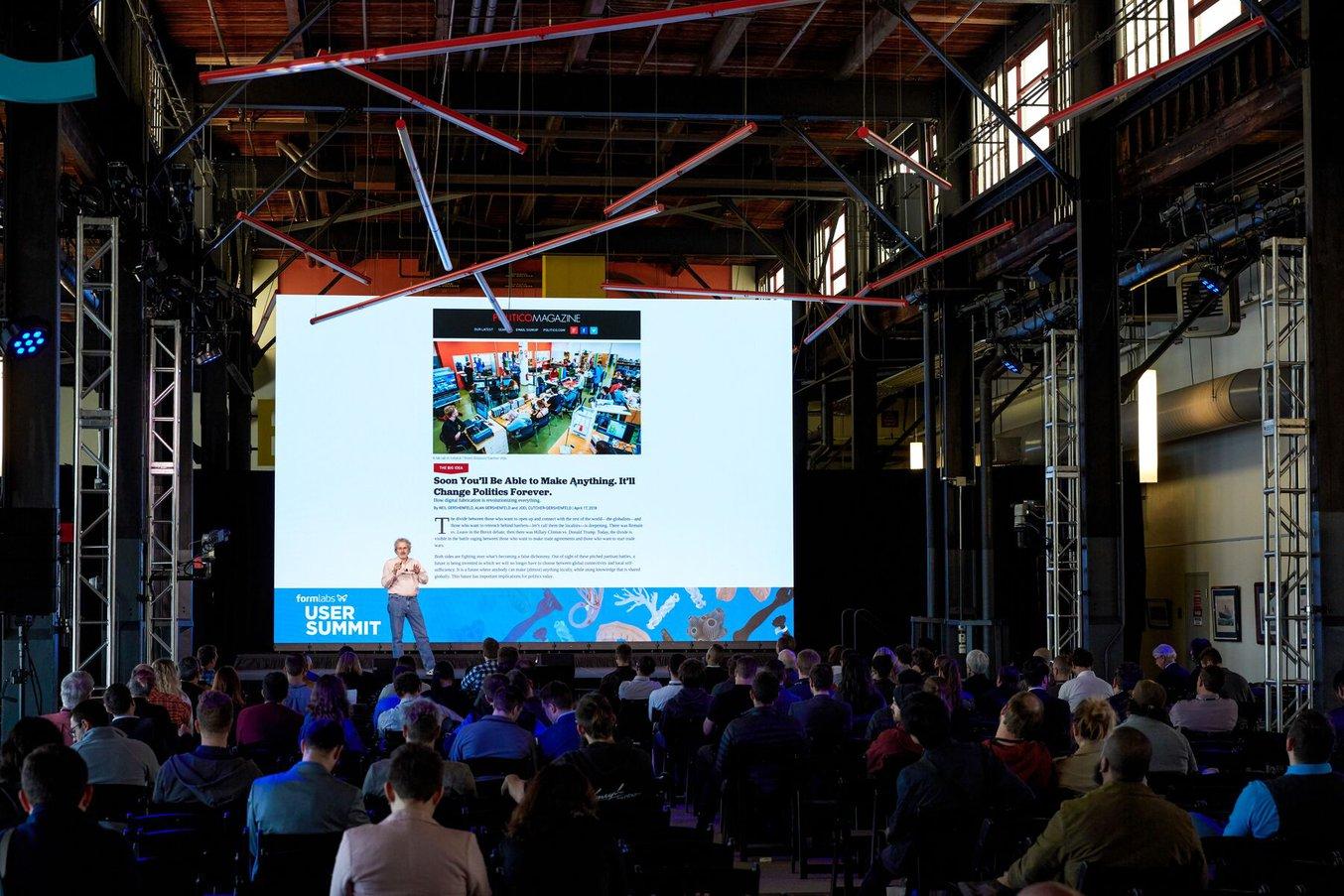
The 2019 Formlabs User Summit brought together users from across the world to share, learn, and collaborate. We're so excited to hear from our amazing community at the 2022 FUS!
The Next Hundred Million
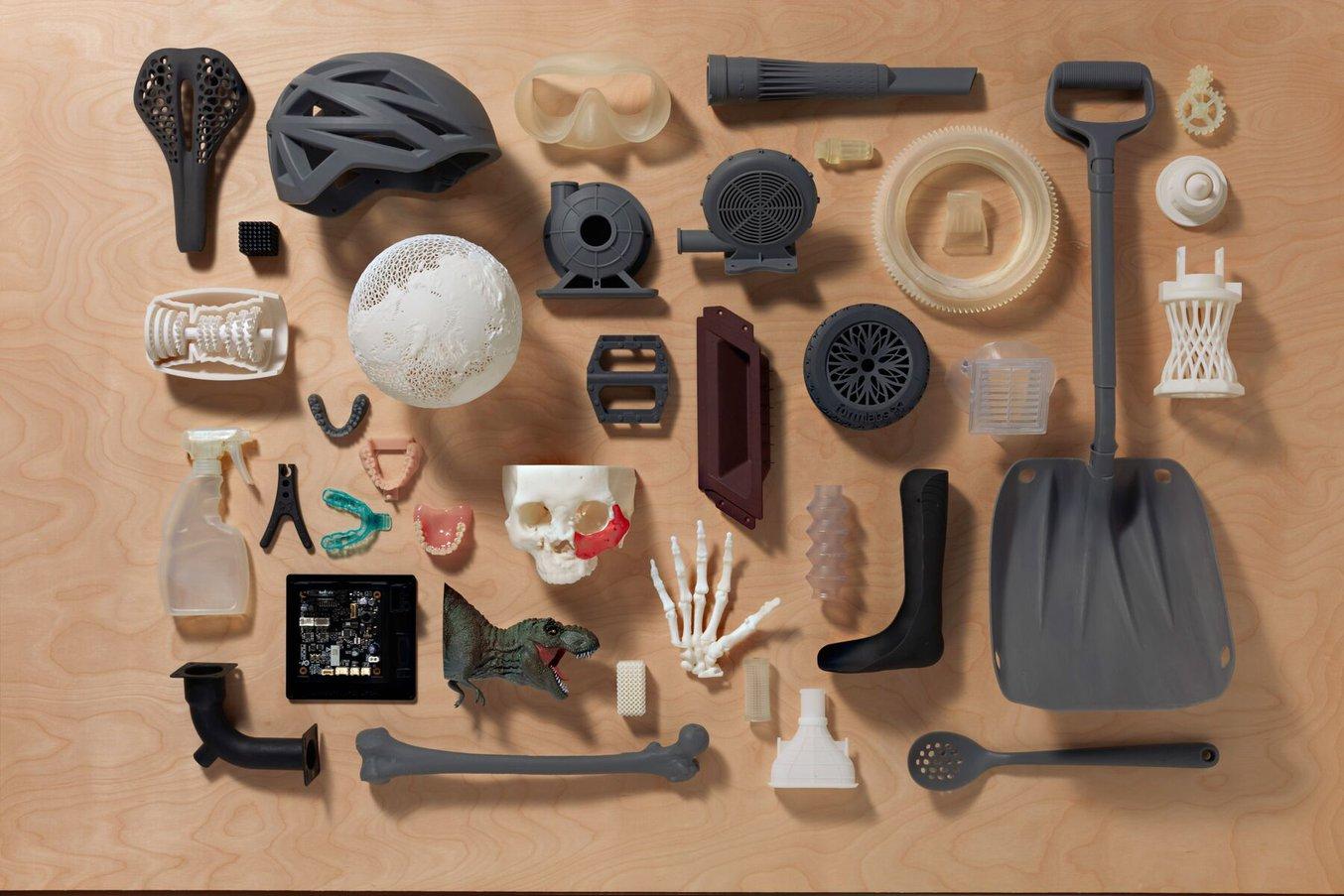
The 3D printing industry is always looking forward, pushing speed, size, strength farther than before, and unlocking new possibilities. For a moment though, Formlabs is proud to look back at everything the Formlabs community has accomplished.
These 100 milion parts represent a community effort, to try, iterate, innovate, scale-up, pare down, innovate, and overhaul. We’re so excited to print the next 100 million with you, and we can’t wait to see what comes next.