Comment SiOCAST révolutionne le marché des figurines avec des masters imprimés en 3D
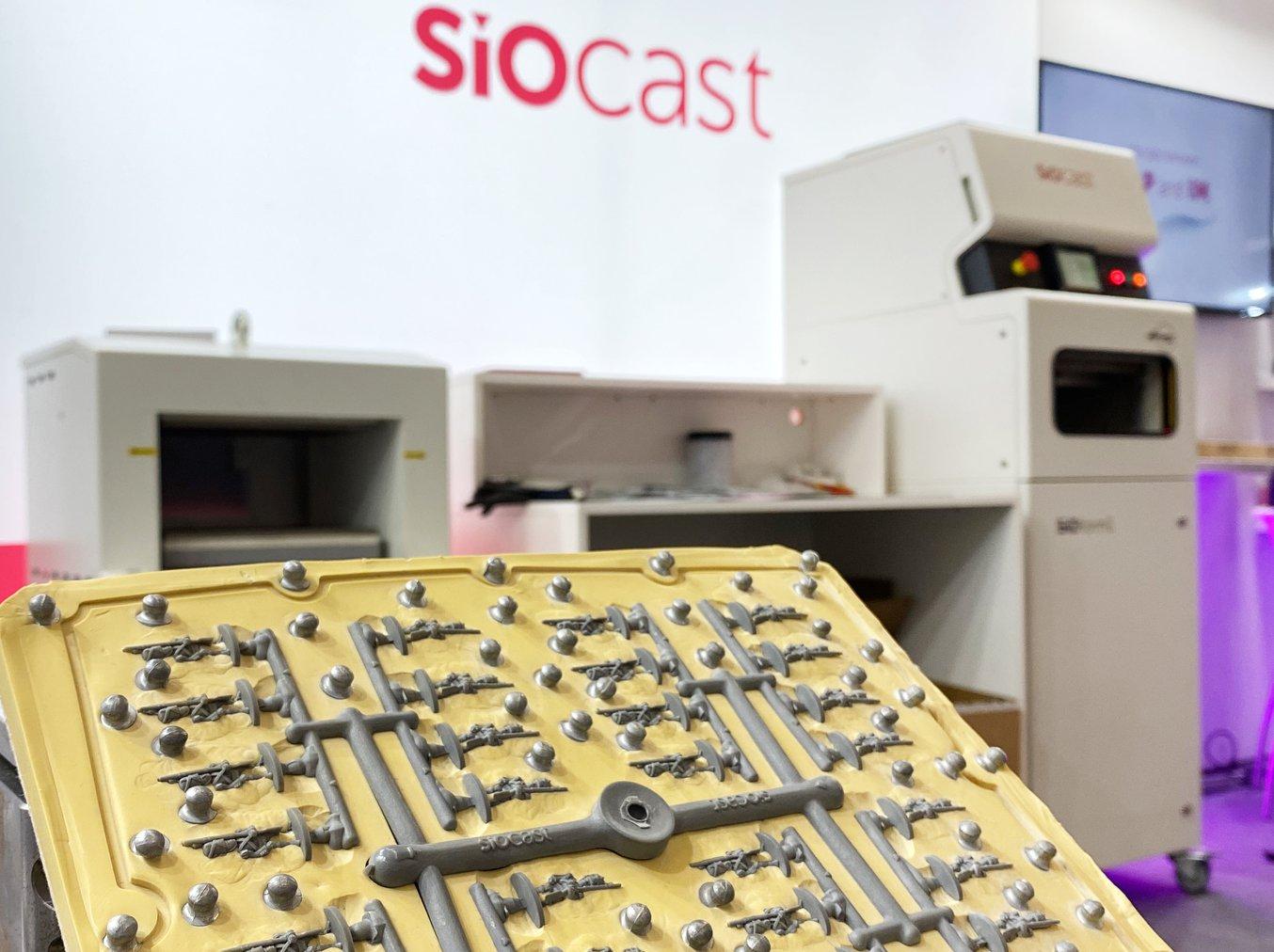
SiOCAST est en passe de redéfinir l'avenir de la fabrication de figurines en utilisant son propre système de production agile, y compris ses propres équipements et matériaux, pour produire en interne des pièces non toxiques de haute qualité à un coût abordable.
La technologie de SiOCAST, qui consiste à produire des moules en silicone à l'aide de masters imprimés en 3D grâce à un processus spécial combinant les avantages de l'impression 3D, de la fabrication de moules en silicone et du moulage par injection, a déjà été adoptée par nombre de sociétés, des petits studios aux plus grands fabricants de figurines de l'industrie, tels que Monster Fight Club (The Witcher, Cyberpunk RED), Reaper figurines (Bones), et Warlord Games (Blood Red Skies, Bolt Action).
Dans cet article, Ferran Navarro, directeur et cofondateur de SiOCAST, nous guide à travers le processus de fabrication de figurines et de petites pièces thermoplastiques avec le système dit « Alemany », et nous explique comment son équipe utilise des imprimantes 3D Formlabs pour ce processus.
La nouvelle technologie de SiOCAST comble le fossé entre l'impression 3D et le moulage par injection
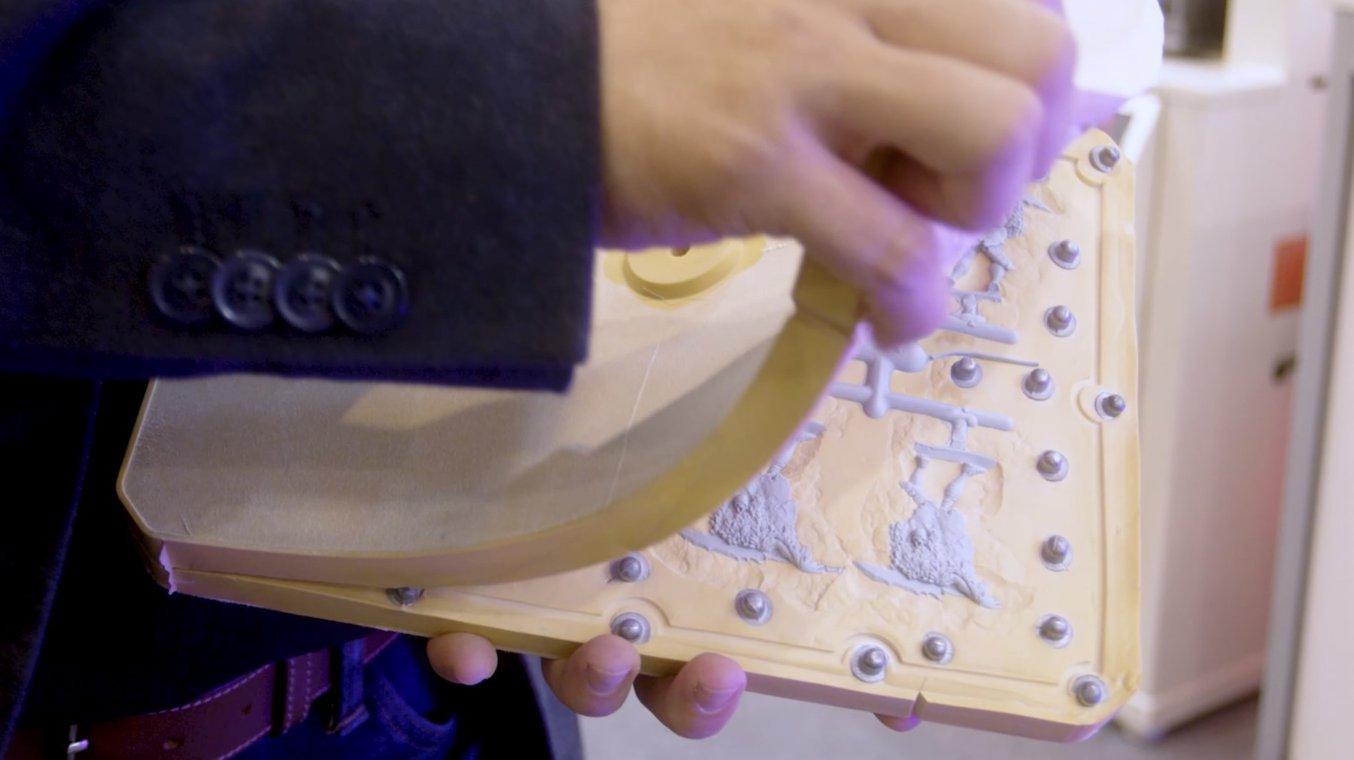
Les technologies traditionnelles permettant de fabriquer de grandes quantités de figurines pourraient être coûteuses, de qualité médiocre et difficilement ajustables. L'un des procédés les plus populaires, le moulage par injection, permet d'atteindre des volumes de plusieurs millions d'unités, mais il est connu pour ses coûts d'outillage élevés et ses longs délais de fabrication, de sorte que l'investissement initial et le seuil de rentabilité élevé constituent un obstacle majeur à l'entrée sur le marché pour les petites entreprises. Cela représente également un obstacle majeur pour les grands acteurs de la fabrication de figurines, en raison du risque important que représente le lancement de nouveaux modèles de figurines.
Les figurines directement imprimées en 3D se situent à l'opposé : grâce à des technologies telles que l'impression 3D stéréolithographique (SLA) , il est possible d'obtenir des détails extrêmement précis avec une faible barrière à l'entrée. Toutefois, l'impression 3D n'est pas compétitive par rapport au moulage par injection pour les grands volumes de pièces. Les fabricants de figurines utilisent généralement l'impression 3D pour des pièces uniques, les toutes petites séries ou pour des pièces personnalisées en masse.
D'autres technologies de fabrication de figurines, telles que le moulage par centrifugation ou la coulée de résine, nécessitent souvent beaucoup de main-d'œuvre, sont sales, difficiles à faire évoluer et utilisent des matériaux toxiques, ce qui en fait des technologies difficiles à adapter à la production industrielle.
SiOCAST a été fondée pour relever ces défis. Entreprise dérivée du groupe espagnol Coniex, spécialisé depuis plus de 35 ans dans les solutions pour les industries du moulage par centrifugation et du moulage en silicone, SiOCAST est le résultat de 8 années de recherche et de développement internes visant à combler le fossé de productivité entre l'impression 3D et le moulage par injection, en étant capable d'atteindre des volumes de production de 50 à 50 000 pièces uniques, et même jusqu'à 400 000 pièces.
SiOCAST propose un système breveté d'injection de résine thermoplastique qui fonctionne avec des moules en caoutchouc de silicone vulcanisé à haute température, fabriqués à partir de masters imprimés en 3D très détaillés, afin de produire des petites pièces de qualité dans un matériau durable et sans danger pour les jouets.
L'ensemble du processus est respectueux de l'environnement et peut être réalisé localement, sans qu'il soit nécessaire de faire appel à des fournisseurs étrangers. En moins de quatre ans, le système SiOCAST s'est avéré rentable et a déjà été adopté par des entreprises dans plusieurs pays et régions, dont les États-Unis, le Royaume-Uni, l'Asie et l'Union européenne.
Il s'agit d'une nouvelle technologie qui se situe entre le moulage par centrifugation, la coulée de résine et le moulage par injection. Nous avons fait beaucoup de progrès pour rendre cette technologie aussi simple que possible, afin que tout le monde puisse l'adopter. Grâce à l'automatisation, nous sommes en mesure d'atteindre la même productivité qu'une très grosse machine de moulage par injection, avec l'avantage que notre silicone est vraiment bon marché, sûr et fabriqué localement.
Ferran Navarro, PDG et cofondateur de Siocast
Processus de moulage du silicone avec un outillage rapide imprimé en 3D
La fabrication de moules en silicone implique généralement le développement de moules à partir d'un modèle ou d'un patron physique, qui serait traditionnellement réalisé par sculpture manuelle, moulage par centrifugation ou usinage CNC.
Cependant, grâce aux progrès d'imprimantes 3D SLA de haute qualité et abordables, comme les imprimantes 3D Formlabs, SiOCAST a été en mesure d'introduire de manière fiable des masters imprimés en 3D très détaillés dans son flux de travail.
Le processus de fabrication des moules SiOCAST.
Le processus SiOCAST comprend les étapes suivantes :
1. Conception numérique des moules
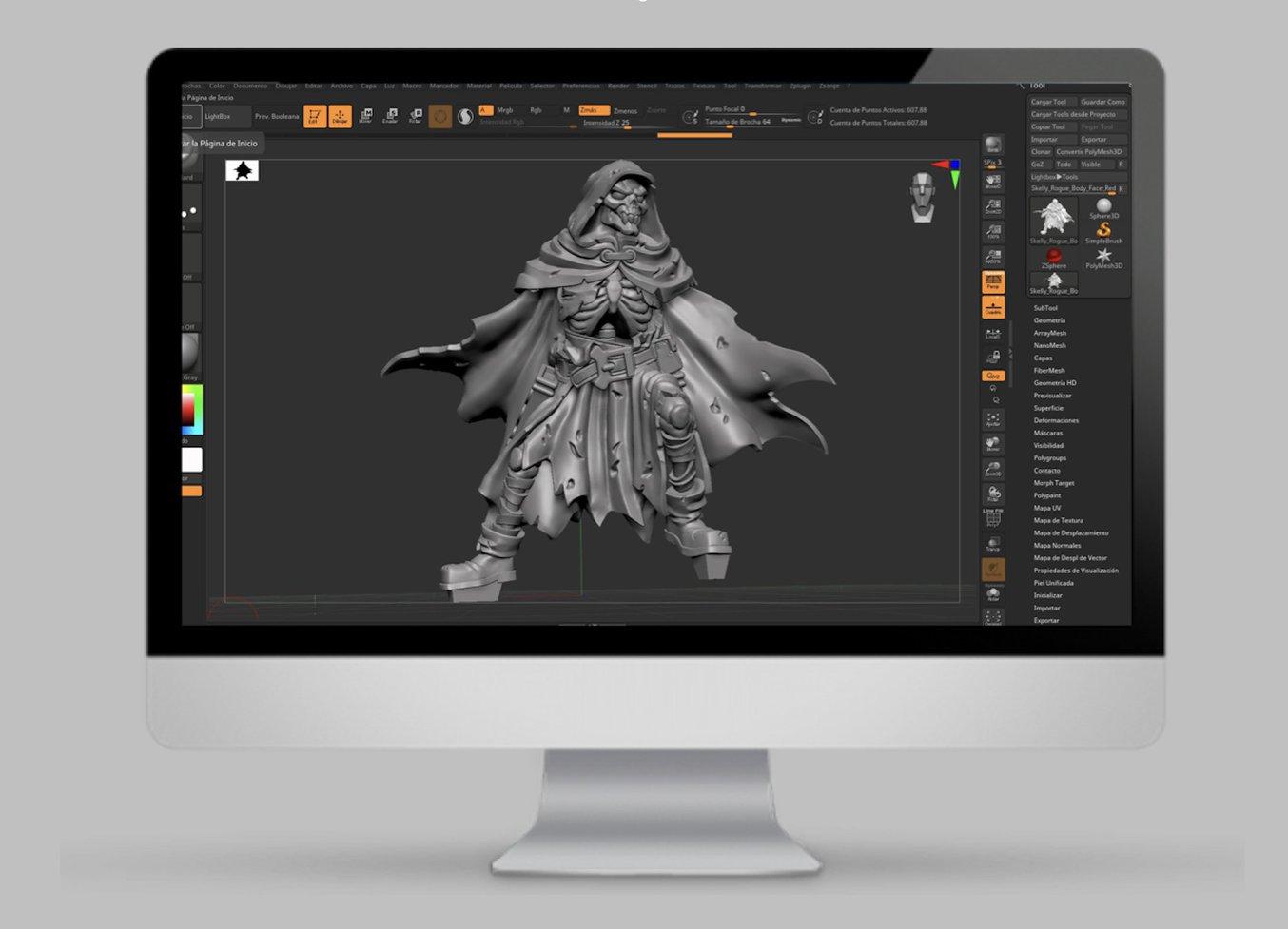
modèle 3D conçu par Broken Anvil Miniatures.
À l'aide du logiciel de CAO , le concepteur modélise les pièces avec autant de détails que possible, car ceux-ci seront reproduits dans la pièce imprimée en 3D, puis transférés au moule SiOCAST, puis aux pièces moulées. Le processus SiOCAST permet également de fabriquer des modèles avec des contre-dépouilles importantes. Actuellement, l'épaisseur maximale des pièces fabriquées à partir du SiOform1 est de 40 mm. Pendant le processus, les carottes pour le moulage par injection sont également ajoutées à partir de la gamme de fichiers standardisée.
2. Impression 3D pour les masters et les canaux
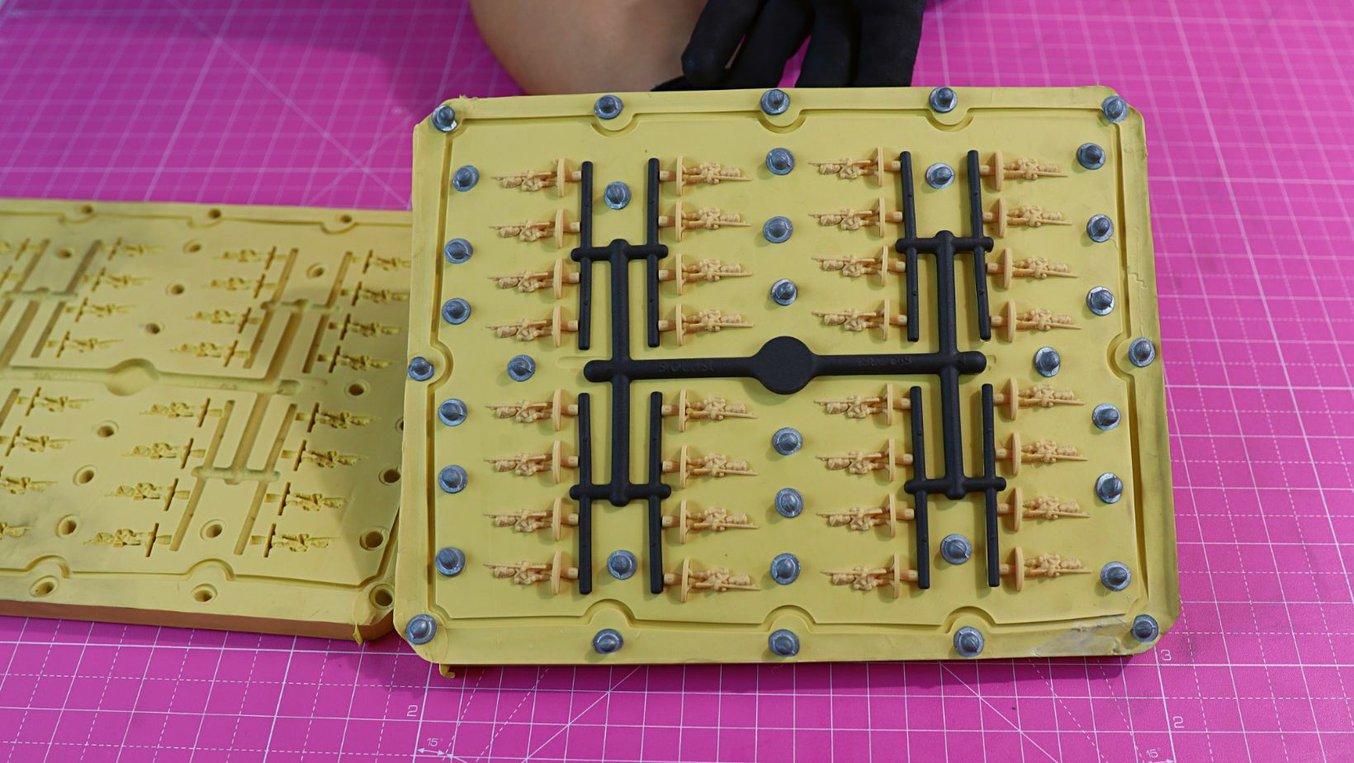
Les masters imprimés en 3D sur la Form 3+ et les canaux imprimés sur la Fuse 1.
Une fois le moule numérique finalisé, SiOCAST utilise le logiciel de préparation d'impression de Formlabs, PreForm et l'imprimante 3D Form 3+ SLA pour imprimer le moule principal à l'aide de Model V2 Resin, qui résiste à des températures élevées et offre de bonnes propriétés mécaniques dans le processus de vulcanisation.
Ils orientent les pièces à environ 45 degrés. Lorsque des surfaces planes sont fixées à la plateforme de fabrication, elles sont biseautées pour éviter que les racloirs ne cassent les pièces.
« Nous disposons de quatre imprimantes Formlabs qui fonctionnent en permanence. Nos clients aussi : ils se procurent le système SiOCAST et ont besoin d'une ou deux imprimantes Formlabs pour couvrir leurs besoins en modèles originaux. Certains clients possèdent jusqu'à quatre machines Formlabs, car ils ont une forte demande d'impression », explique Ferran.
Avec l'imprimante 3D SLA Form 3+, il est possible de réaliser des masters de haute qualité et peu coûteux en quelques heures seulement. Pour obtenir un maximum de détails, l'entreprise imprime les figurines à une hauteur de couche de 25 microns.
Nous avons déjà essayé différentes techniques et machines d'impression 3D : le DLP, le SLA et le SLS. Certains clients optent pour la technologie DLP pour obtenir des détails plus fins, mais les résines ne sont pas toujours aussi durables. Nous utilisons les imprimantes SLA de Formlabs en grande partie pour des applications qui nécessitent un haut niveau de détail et de robustesse pour la vulcanisation. Maintenant, nous étendons cela aux composants techniques, et la hauteur de couche de 25 microns de la Form 3+ suffit amplement pour ce type de modèles.
Ferran Navarro, PDG et cofondateur de Siocast
Après l'impression des pièces, celles-ci sont traitées avec le système automatisé de nettoyage et de post-polymérisation de Formlabs, la Form Wash et la Form Cure.
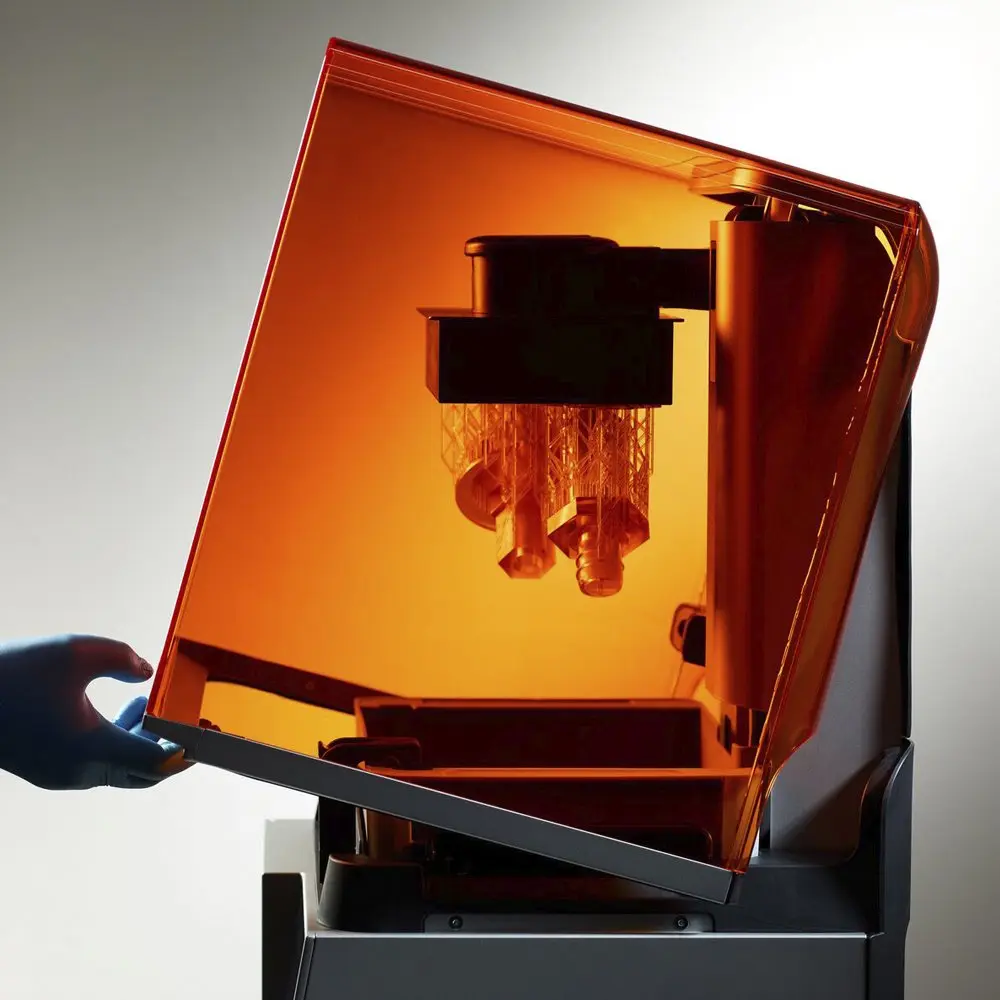
Introduction à l’impression 3D avec la stéréolithographie de bureau (SLA)
Vous cherchez une imprimante 3D pour créer des modèles 3D haute résolution ? Téléchargez notre livre blanc pour découvrir comment fonctionne l’impression SLA et pourquoi elle est tant utilisée pour créer des modèles aux détails incroyables.
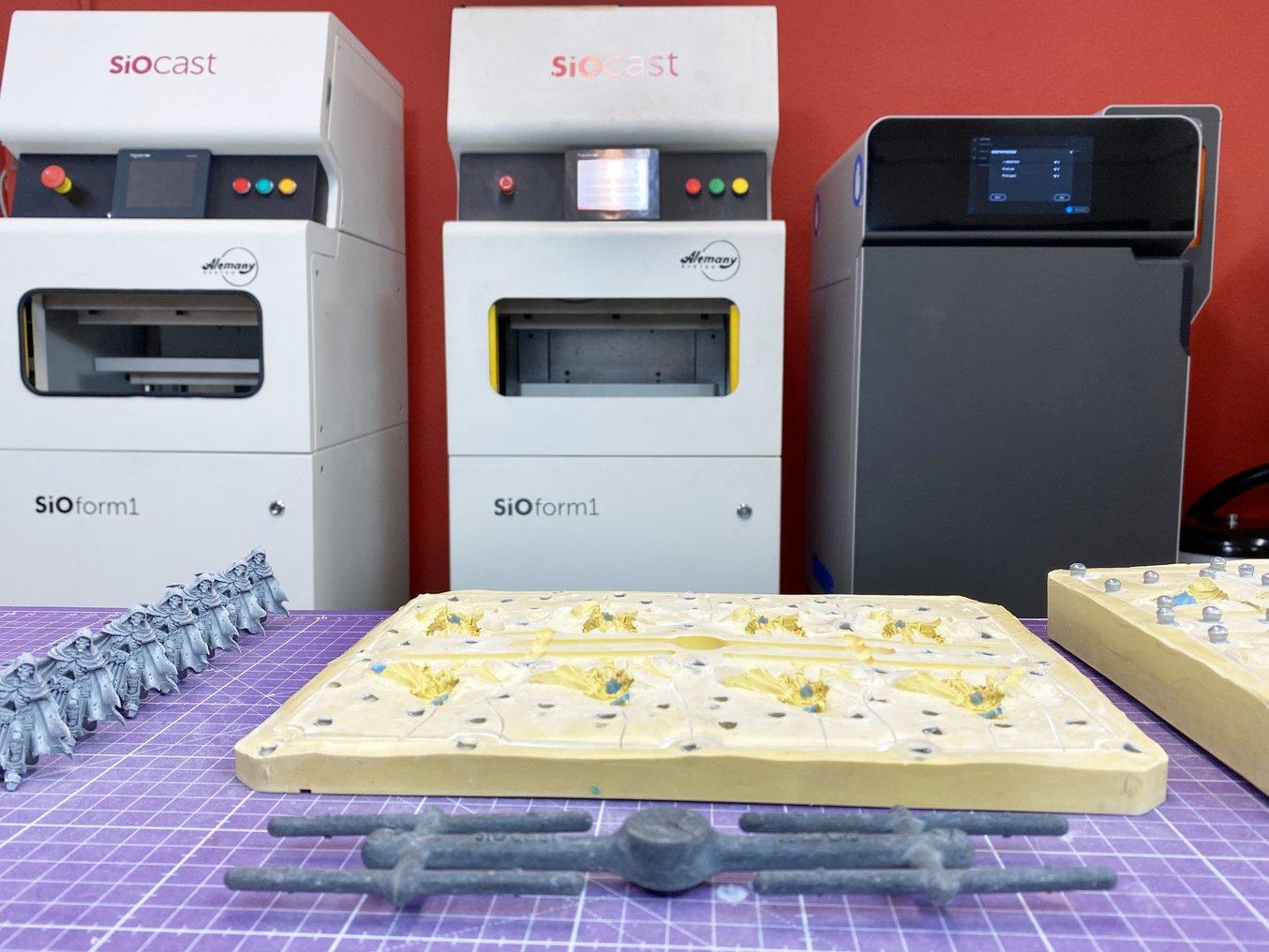
Canaux imprimés en 3D sur la Fuse 1.
SiOCAST utilise l'impression 3D non seulement pour la fabrication de masters, mais aussi pour les canaux d'injection nécessaires au processus de coulée. Pour cette application, ils utilisent une imprimante 3D à frittage sélectif par laser (SLS) de Formlabs , la Fuse 1. Les canaux SLS sont durables, et plusieurs d'entre eux peuvent être placés dans la chambre de fabrication sans aucun support, ce qui permet à SiOCAST de fournir ces canaux à ses utilisateurs dans le monde entier.
La Fuse 1 accélère les conceptions que nous créons, ce qui permet d'effectuer un grand nombre d'itérations pour les canaux. Dans le cadre d'un projet interne de R&D, nous avons progressé davantage au cours des deux dernières semaines qu'au cours des deux dernières années.
Ferran Navarro, PDG et cofondateur de Siocast
Le processus d'impression 3D SLS est similaire au processus SLA : le fichier d'impression est préparé avec PreForm, puis imprimé en Nylon 12 Powder sur l'imprimante 3D Fuse 1. Ensuite, les étapes de post-traitement sont effectuées avec le logiciel Fuse Sift. SiOCAST utilise également la solution de post-traitement Abrast de Coniex pour nettoyer les surfaces. Elle est spécialement conçue pour les pièces fabriquées de manière additive.
3. Fabrication de moules en silicone avec vulcanisation
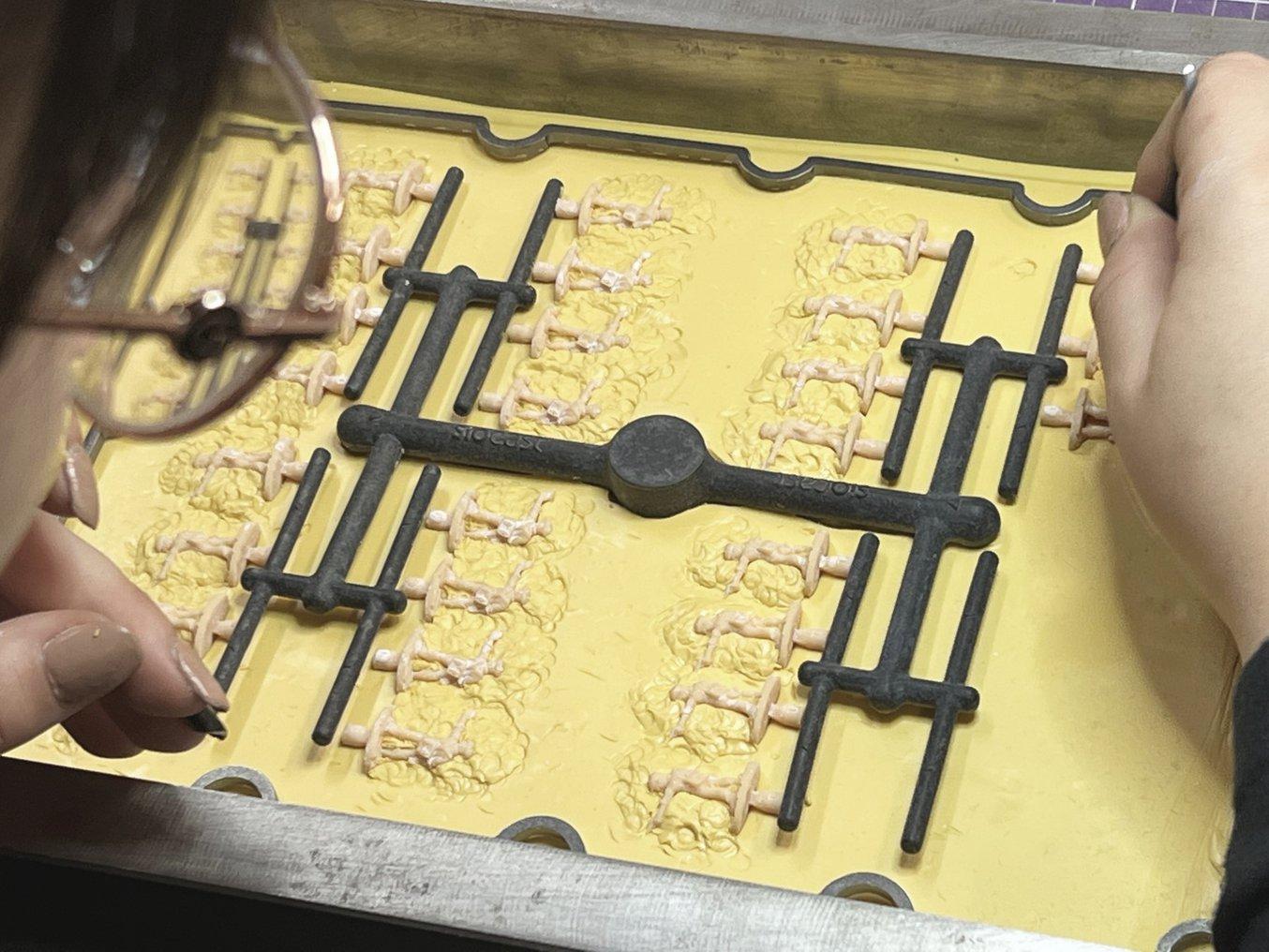
Préparation du moule pour la vulcanisation.
Une fois que les masters et les canaux ont été imprimés en 3D, l'étape suivante consiste à créer les moules à l'aide du caoutchouc silicone SiOmold . Il s'agit du matériau silicone dur HTV de SiOCAST (vulcanisé à haute température) d'une dureté Shore de 65A ou 80A, composé d'un élastomère spécialement fabriqué par le groupe CONIEX et présentant une résistance thermique et mécanique incroyable. Le laminé de silicone est versé dans un cadre métallique rigide et précis, fabriqué par usinage CNC. Les modèles originaux imprimés en 3D sont ensuite placés uniformément sur le silicone et encastrés avec précaution en versant davantage de silicone autour d'eux afin d'obtenir la ligne de séparation souhaitée. Les canaux imprimés en 3D SLS sont également insérés et pressés dans la plaque résultante.
Les guides de centrage sont ajoutés pour maintenir les deux parties du moule ensemble. Le talc est ensuite étalé sur le dessus comme agent de démoulage qui empêchera les deux côtés du silicone de coller l'un à l'autre. La couche supérieure de silicone est ajoutée et le cadre de la boîte métallique est fermé. Selon la complexité du moule, ce processus peut prendre de dix minutes à deux ou trois heures.
La boîte métallique est ensuite placée dans la presse à vulcaniser SiOpress, dans laquelle le silicone et les masters imprimés en 3D sont pressurisés à 10 bars pour libérer l'air, et chauffés à 120 degrés Celsius.
Pendant les 40 à 60 minutes que dure le processus de vulcanisation , le silicone devient liquide et, à ce moment-là, il reproduit chaque détail des modèles imprimés en 3D avant de coller les chaînes d'élastomère et de devenir un moule vulcanisé.Après refroidissement, le moule est ouvert et les pièces imprimées en 3D sont retirées des cavités, ce qui donne le moule final qui sera utilisé dans la machine SiOCAST. Les masters imprimés en 3D peuvent ensuite être réutilisés pour d'autres cycles de vulcanisation.
Nous utilisons un agent de démoulage spécial pour que les masters imprimés en 3D ne collent pas au silicone après la vulcanisation et qu'ils puissent être réutilisés pour fabriquer le moule suivant. En général, un master imprimé en 3D par Formlabs est capable de réaliser trois ou quatre vulcanisations au total, voire plus.
Ferran Navarro, PDG et cofondateur de Siocast
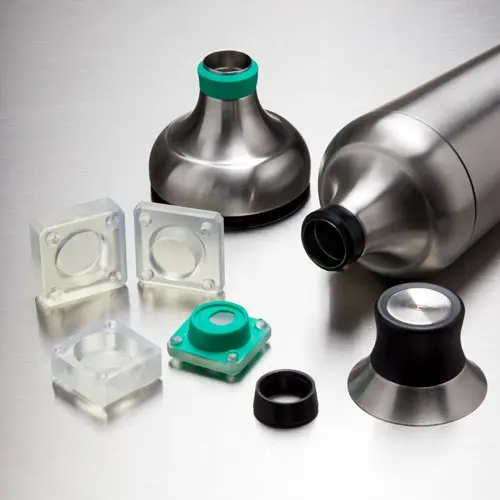
Moulage en silicone pour la conception de produits
Téléchargez ce rapport pour découvrir les études de cas des entreprises OXO, Tinta Crayons et Dame Products, qui illustrent trois mises en œuvre différentes du moulage en silicone pour la conception et la fabrication de produits, dont le surmoulage et le moulage d’insert.
4. Production de figurines avec le SiOform1
Dans le SiOform1, les deux moitiés du moule en silicone vulcanisé sont assemblées et placées dans l'appareil, la matière à injecter est sélectionnée et il suffit d'appuyer sur un bouton pour que la machine soit déjà en marche : elle évacue l'air du moule et injecte la résine thermoplastique liquide à une température de 240°C.
Une fois le moule refroidi, il peut être retiré de la machine. Toute cette partie du processus ne prend qu'environ 30 secondes (jusqu'à 1 minute s'il s'agit d'un moule plus épais), et un nouveau moule peut être inséré immédiatement pour le lot suivant.
Après quelques secondes de refroidissement à l'extérieur de la machine, le premier lot de figurines peut être démoulé et décollé. La combinaison de la résine thermoplastique de SiOCAST et du caoutchouc de silicone développé en interne permet aux figurines de se démouler facilement.
Chaque coulée produit en moyenne 4 à 64 figurines, en fonction de la taille des pièces et du volume, qui est limité à 100 g par coulée, et l'ensemble du processus est environ 10 à 20 fois plus rapide que la coulée de résine traditionnelle.
Vous pouvez faire tourner les moules pendant que vous les laissez refroidir avant de les réutiliser dans la machine. Normalement, on travaille avec trois à neuf moules différents en rotation. Vous pouvez réaliser 25 à 40 moulages par heure. Et s'il y a un système d'automatisation, nous pouvons aller jusqu'à 60 – 80 injections par heure, produisant de 100 à 1000 pièces par heure, toutes avec le même niveau de détail que le modèle original imprimé en 3D.
Ferran Navarro, PDG et cofondateur de Siocast
Chaque moule en silicone mesure 210 x 270 millimètres et peut avoir une épaisseur maximale de 50 millimètres, ce qui permet d'obtenir des pièces finales d'une épaisseur maximale de 40 millimètres. Les moules peuvent supporter environ 300 à 500 pièces, ce qui en fait une option viable pour la production à court terme et la production en série.
Les clients de SiOCAST peuvent soit acheter les moules en silicone finaux directement auprès d'eux avec le service readyCAST, soit fabriquer leurs propres moules en interne, ce qui est la solution standard préférée. L'entreprise propose un programme de formation complet pour permettre aux débutants d'acquérir les compétences nécessaires à chaque étape du processus.
Un système qui change la donne dans le secteur
L'impression 3D directe de figurines est toujours une excellente option pour les amateurs et les pièces uniques ou les petites séries, mais pour la fabrication professionnelle de figurines, SiOCAST a établi une nouvelle norme.
Les consommateurs finaux affirment qu'ils obtiennent des pièces plus durables, beaucoup plus détaillées et plus faciles à peindre, ce qu'ils ne peuvent pas obtenir avec la coulée de résine, les figurines en métal ou les pièces moulées par injection.
Des entreprises telles que Monster Fight Club (The Witcher, Cyberpunk RED), Warlord Games (Blood Red Skies, Bolt Action), Reaper Miniatures (Bones USA), Titan Forge Miniatures, Corvus Belli (Infinity the Universe), Yedharo Models et Creature Caster sont quelques-uns des acteurs qui ont adopté le système de SiOCAST.
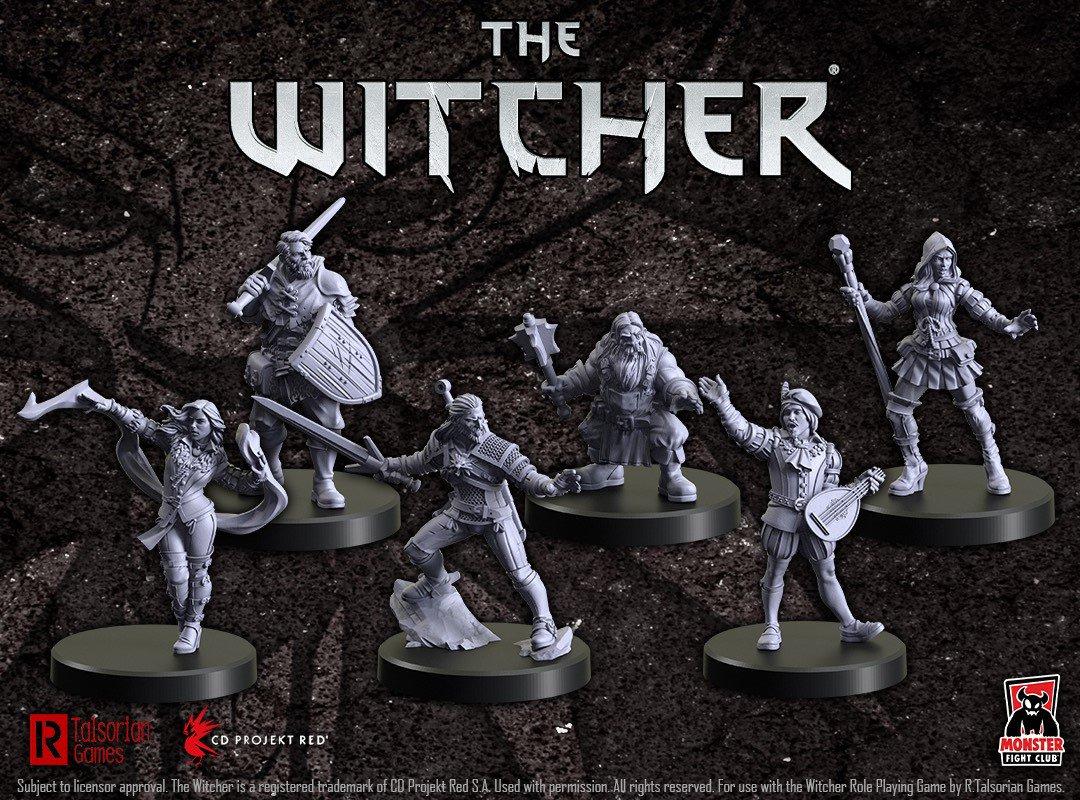
Les figurines de Monster Fight Club pour The Witcher.
Le système SiOCAST a été très bien accueilli sur le marché des figurines, mais aussi dans l'industrie de l'animé et du manga.
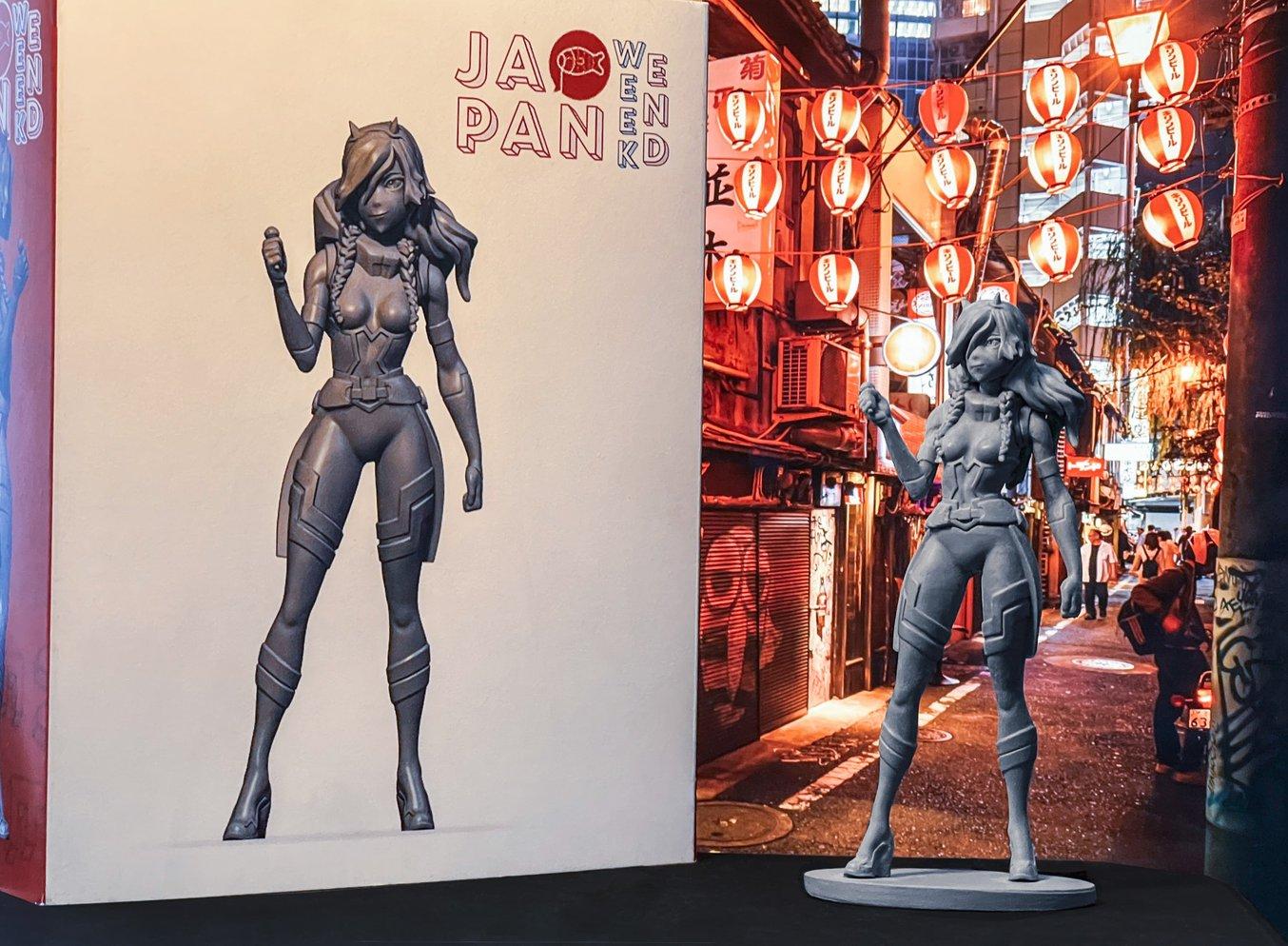
La figurine de Japan Weekend réalisée avec SiOCAST.
L'entreprise se développe également sur le marché des maquettes paysagères et a déjà travaillé avec certains des principaux fabricants de maquettes paysagères.
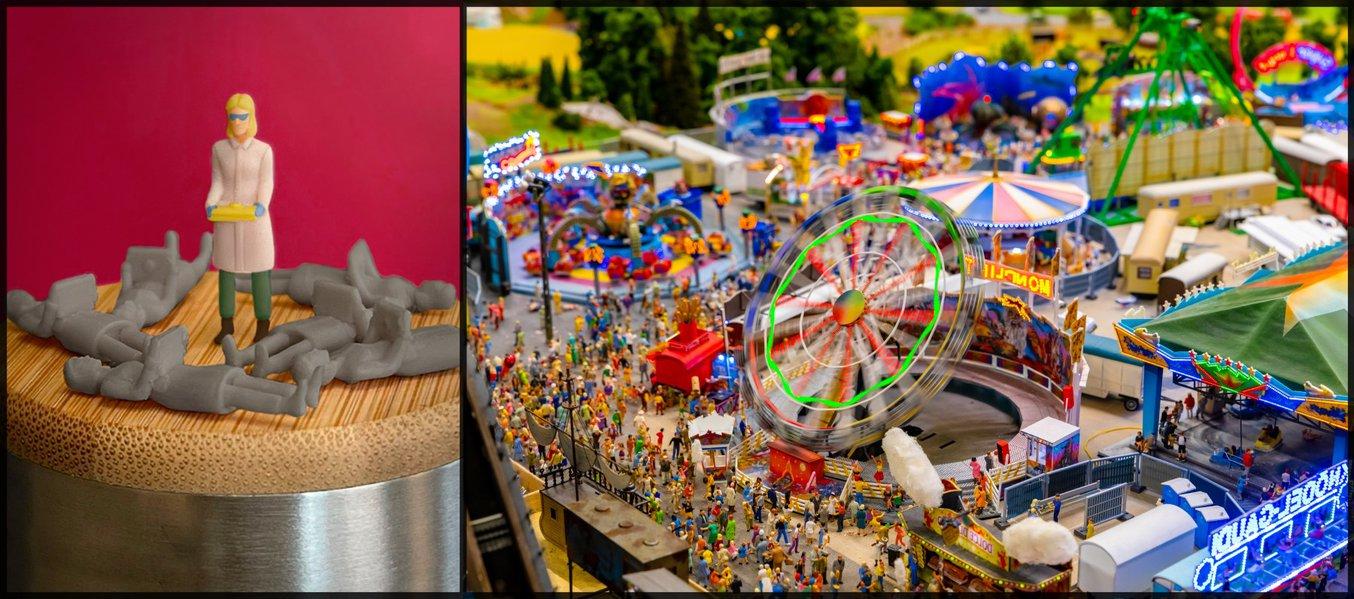
Modèle réduit de paysage de Miniatur Wunderland.
Certains fabricants de jeux de rôle, comme Galladoria Games, étendent les avantages du système SiOCAST au marché du terrain et de la scénographie. Les exemples d'entreprises qui adoptent le système SiOCAST en dehors du marché des figurines sont de plus en plus nombreux.
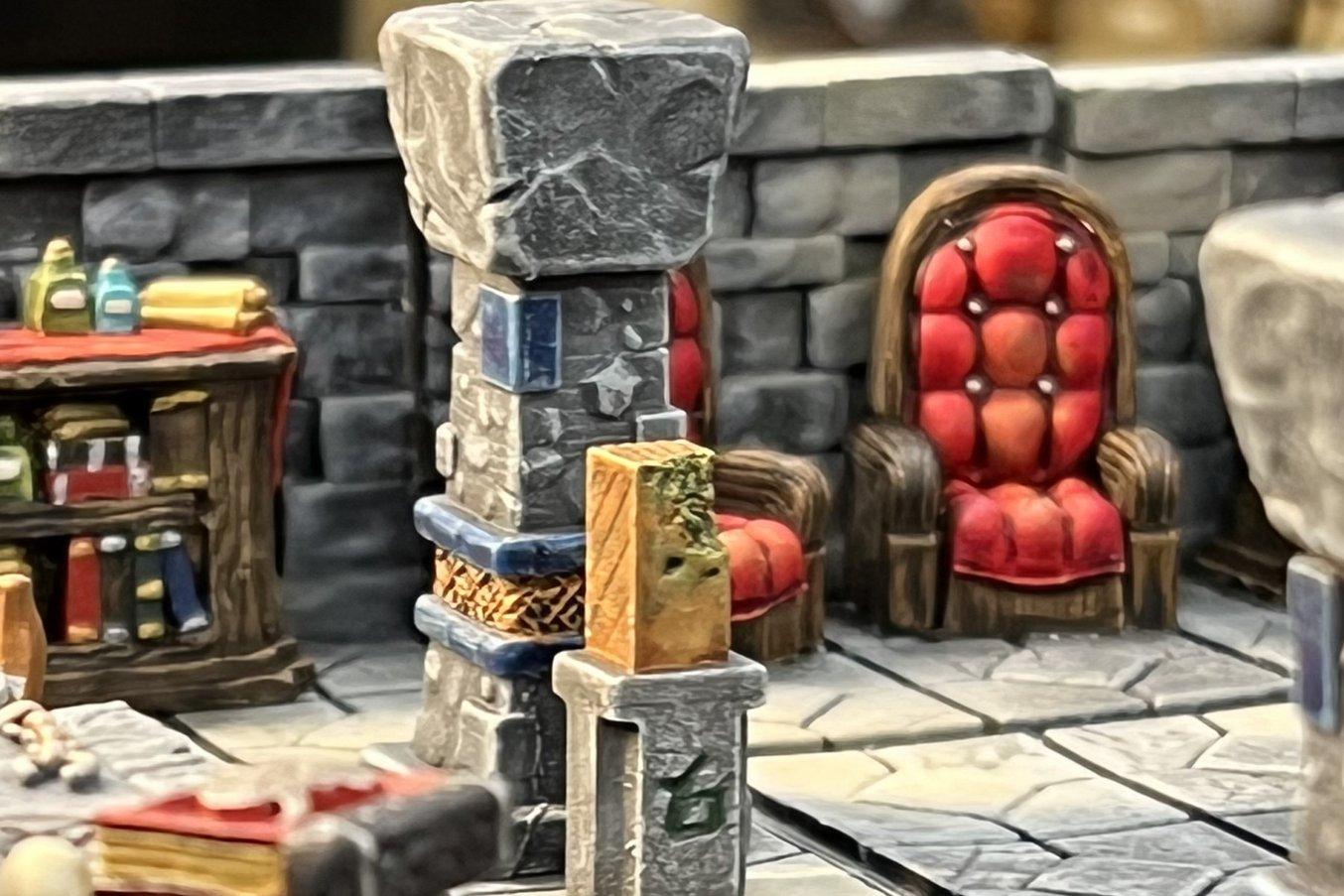
Le terrain D&D de Galladoria.
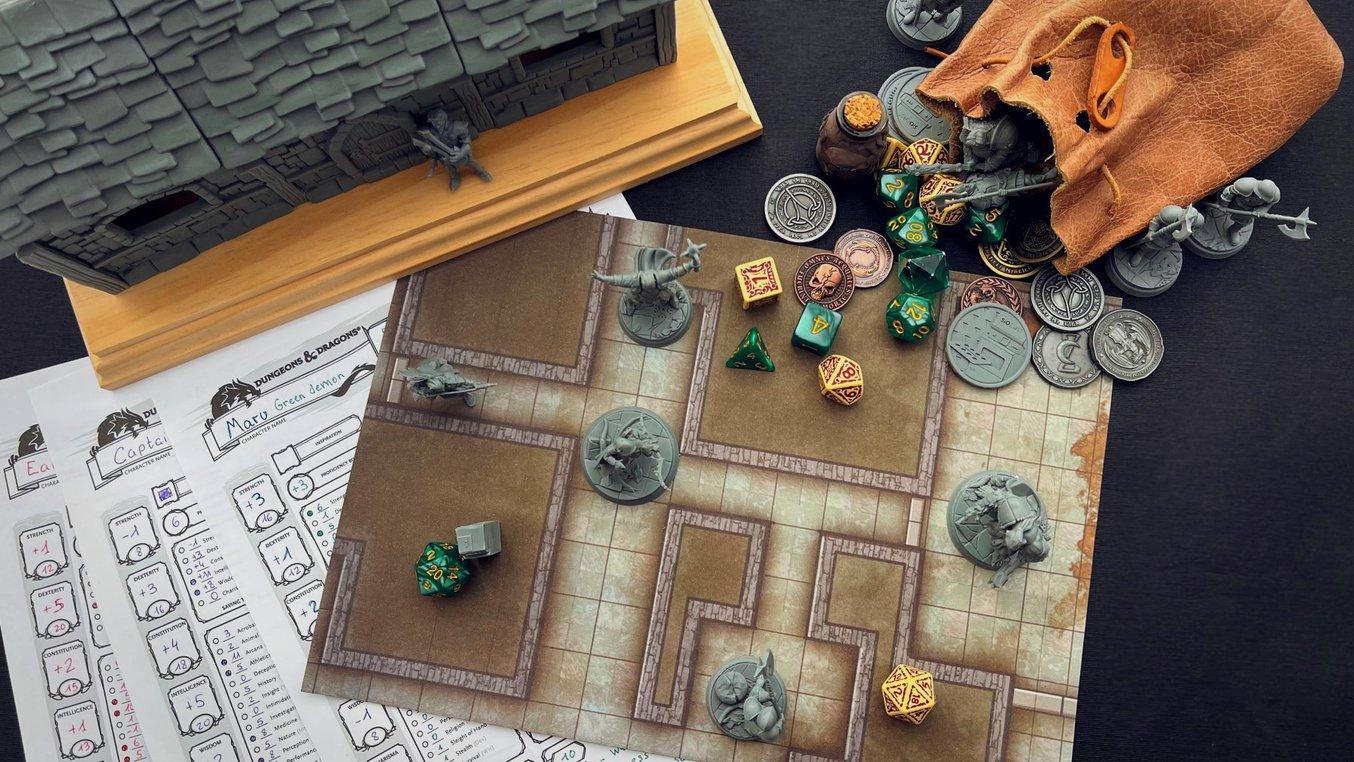
Pièces pour Donjons et Dragons réalisées avec SiOCAST.
Fabriqué localement
Le nouveau système de production fait réellement bouger les choses dans l'industrie. Ferran souligne que seules quelques entreprises de fabrication de figurines dans le monde peuvent produire du plastique à 100 % en interne en utilisant des méthodes traditionnelles. La plupart des entreprises s'approvisionnent en Chine, ce qui s'accompagne généralement de coûts logistiques élevés, ainsi que de longs délais d'exécution et de quantités minimales de commande élevées. Mais aujourd'hui, grâce à SiOCAST, les entreprises de toute taille peuvent produire en interne.
Par exemple, la collection Bones USA de Reaper Miniature représente non seulement un passage des figurines en métal aux figurines en thermoplastique avec SiOCAST, mais aussi une relocalisation de la production de la Chine vers les États-Unis.
Fabrication écologique, sans déchets
SiOCAST souligne également que ses matériaux plastiques SiOres, développés en interne, sont non toxiques et certifiés sans danger pour les jouets selon la norme EN-71, et que son système de production est respectueux de l'environnement. La résine utilisée pour le moulage des figurines est réutilisable, de sorte que les pièces moulées ou les canaux de coulée ratés peuvent être broyés et mélangés à un nouveau matériau. Ce système n'engendre donc aucun gaspillage.
En produisant localement et avec un système adaptable à la demande, il n'est pas nécessaire de stocker ou de gaspiller des produits invendus. Ceci, aligné avec les machines compactes nécessaires à la production des figurines, permet un faible encombrement.
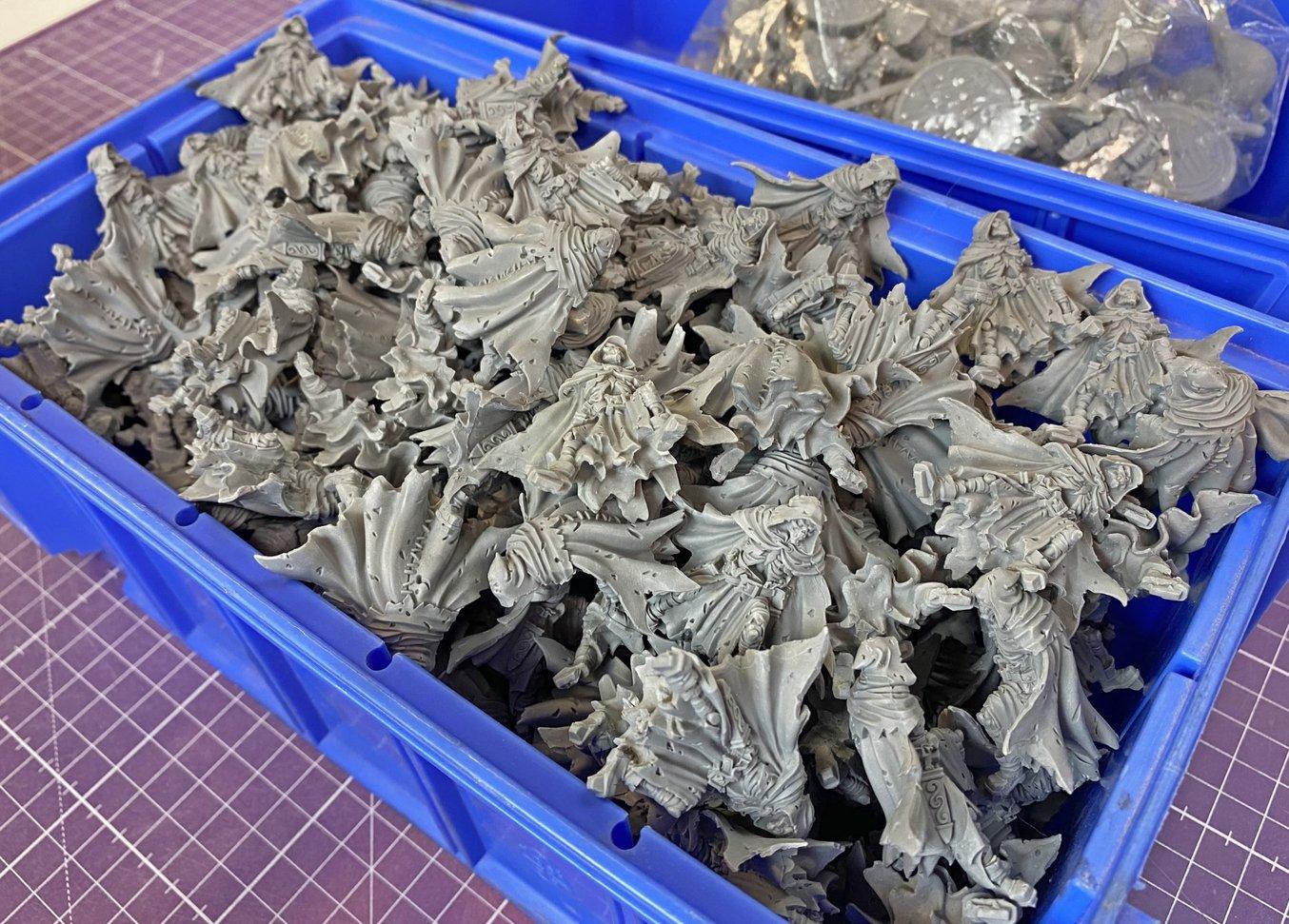
Miniatures de haute qualité produites localement par Broken Anvil Miniature.
Ferran explique que même dans un espace d'à peine dix mètres carrés, il est possible de « faire fonctionner sa propre installation de production à haut rendement. » Cela n'est pas possible avec les presses manuelles à injection, qui sont de très bonnes machines, mais qui sont limitées en termes de taille ou de capacité ».
« Avec le moulage par injection de carottes, il y a beaucoup de déchets. Environ 20 % du plastique est mis à la poubelle. Les figurines sont généralement fabriquées à l'étranger et doivent voyager jusqu'aux États-Unis. De plus, le fabricant doit produire 20 000 unités, dont il vendra peut-être la moitié et se débarrassera du reste. Le moulage par injection n'est donc judicieux que pour les grandes quantités : il est rentable, mais il n'est pas très écologique et a une empreinte carbone élevée. Les systèmes de coulée de résine produisent environ 20 fois plus de résidus de silicone que le système de SiOCAST, et environ 30 à 40 % de la résine toxique est gaspillée dans des canaux d'injection qui ne sont jamais utilisés », ajoute Ferran.
Des pièces détaillées de haute qualité à un prix raisonnable
Lorsqu'on demande aux joueurs ce qu'ils attendent d'une figurine, le niveau de détail est toujours la première réponse.
Cependant, atteindre un tel niveau de détail à un coût abordable est un véritable défi. Comme l'explique Ferran, « Ce qui importe à tous, quelle que soit l'application, c'est de combiner les avantages de la fabrication d'outils à bas prix et du niveau de détail élevé qui peut être reproduit avec le silicone, avec la productivité des technologies industrielles comme le moulage par injection ».
Un autre exemple de réussite est celui de l'entreprise Warlord Games qui, grâce au procédé SiOCAST, a pu produire plus de 400 000 unités d'un avion pour Blood Red Skies en quatre couleurs différentes. Traditionnellement, ce type de production en grande série n'est possible qu'avec le moulage par injection, et le niveau de détail n'est pas le même.
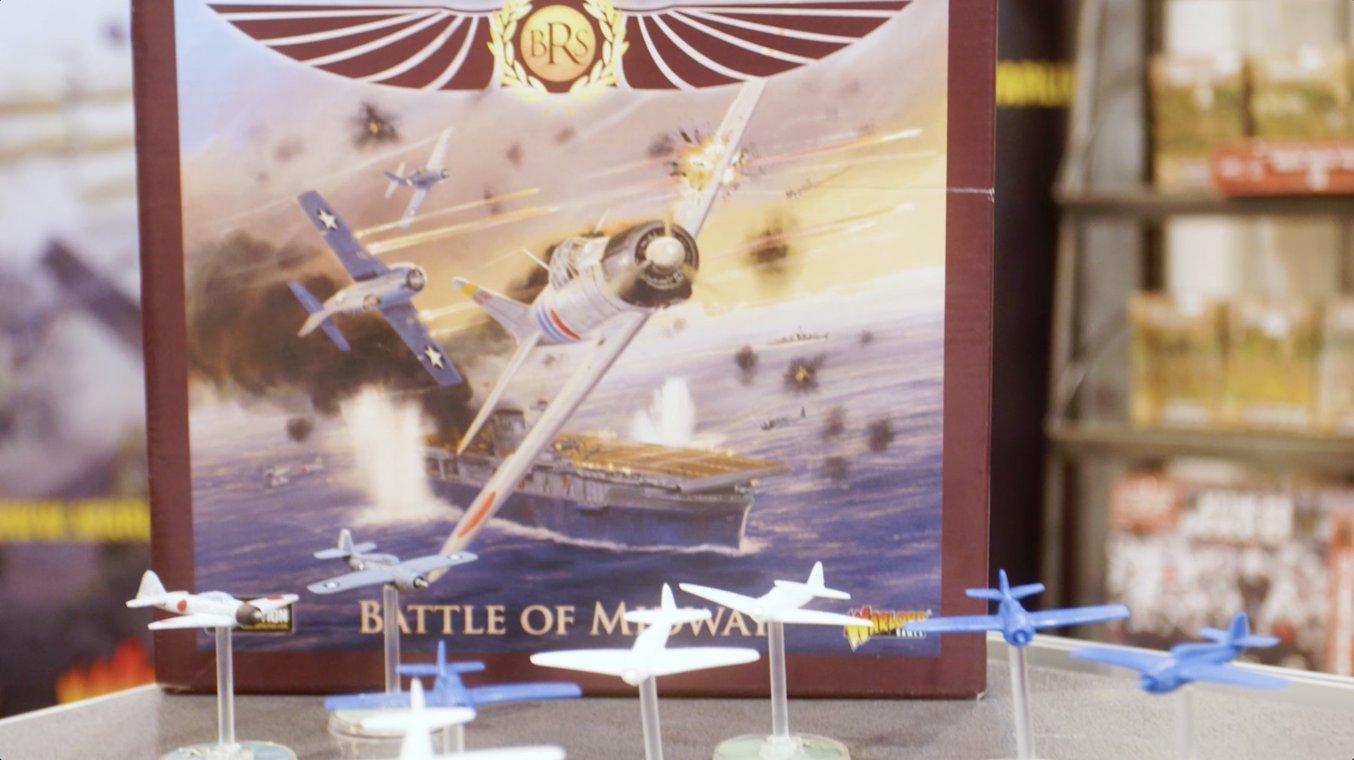
Plus de 400 000 unités de l'avion de Red Blood Skies ont été produites avec SiOCAST.
Avec le moulage par injection, le seuil de rentabilité se situe autour de dix à quinze mille unités d'un même produit, le moule pouvant coûter de cinq à dix mille euros. Bien sûr, les plastiques moulés par injection sont vraiment bon marché, mais il faut ensuite ajouter le délai de livraison, la disponibilité et le niveau de détail. Même si vous regardez les fabricants de figurines de la plus haute qualité sur le marché qui utilisent le moulage par injection, ils n'obtiennent pas les mêmes détails qu'avec le silicone. La différence est assez importante.
Ferran Navarro, PDG et cofondateur de Siocast
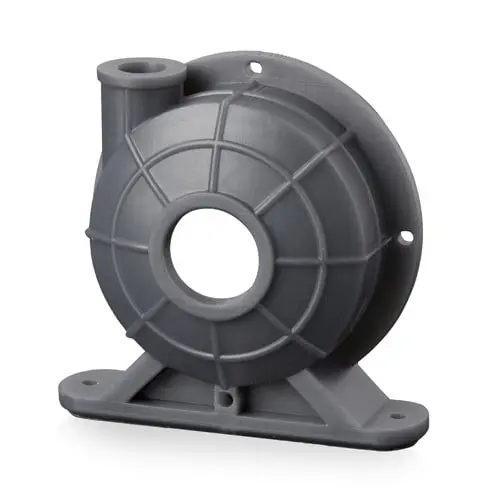
Commander un échantillon gratuit imprimé en 3D
Regardez et touchez par vous-même un master imprimé en 3D en haute résolution. Nous enverrons un échantillon gratuit à votre bureau.
Extension à de nouvelles applications
Le système SiOCAST a également reçu un bon accueil dans d'autres secteurs et domaines d'application, comme la fabrication de chaussures, de caches de touches, de pièces de connexion médicales, de composants pour le surmoulage et d'autres pièces souples et robustes. Par exemple, l'un de ses clients a fabriqué des roues et des interrupteurs pour un simulateur de vol, en utilisant des masters imprimés sur la Fuse 1 et la Form 3+. Les avantages de SiOCAST permettent à cette entreprise de produire des pièces d'utilisation finale avec une qualité de surface élevée, tout en fabriquant localement avec des délais d'exécution courts et à des coûts réduits. Aucune autre technologie ne répond actuellement à ces exigences.
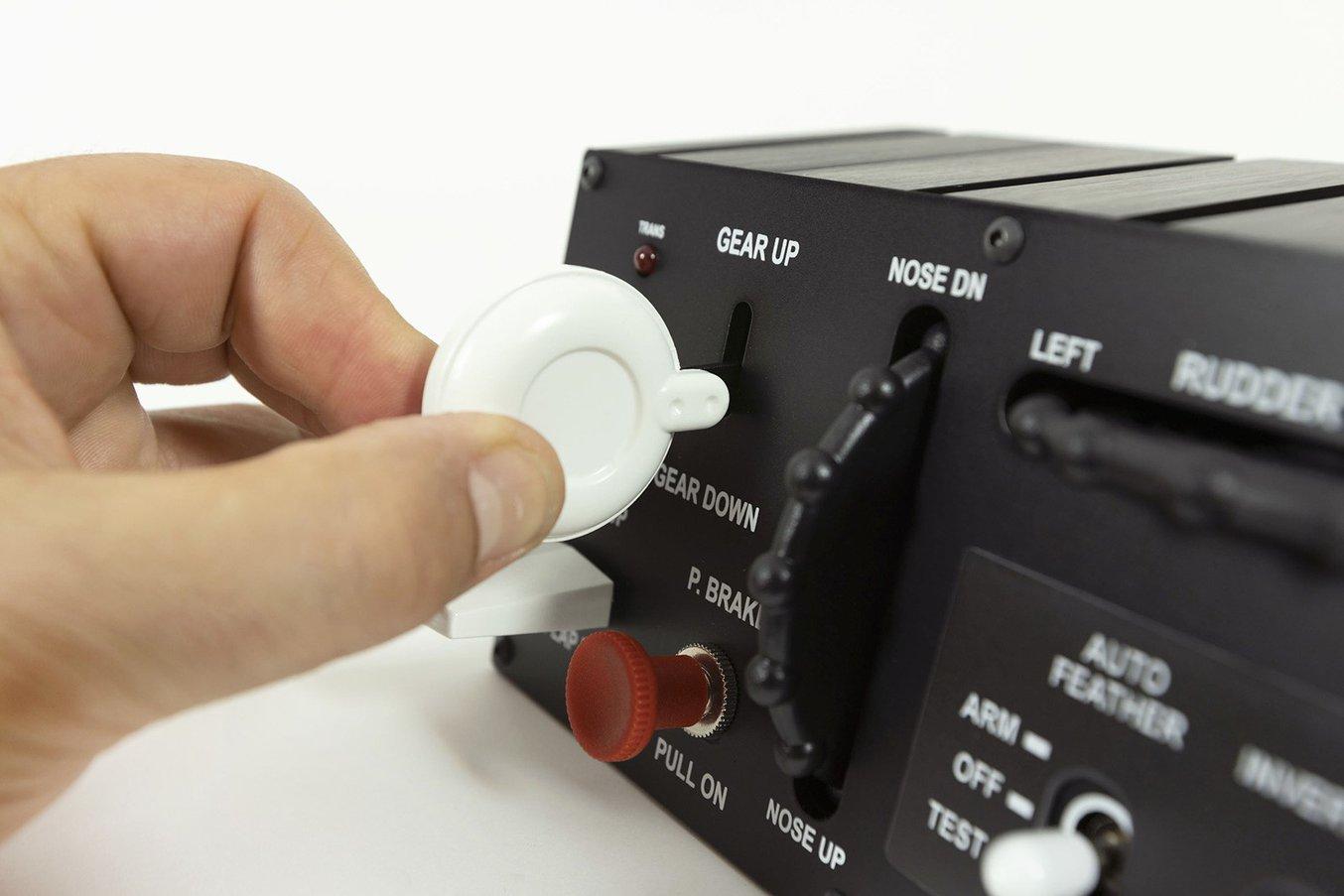
Pièce de simulateur de vol d'Aplica Design réalisée avec SiOCAST.
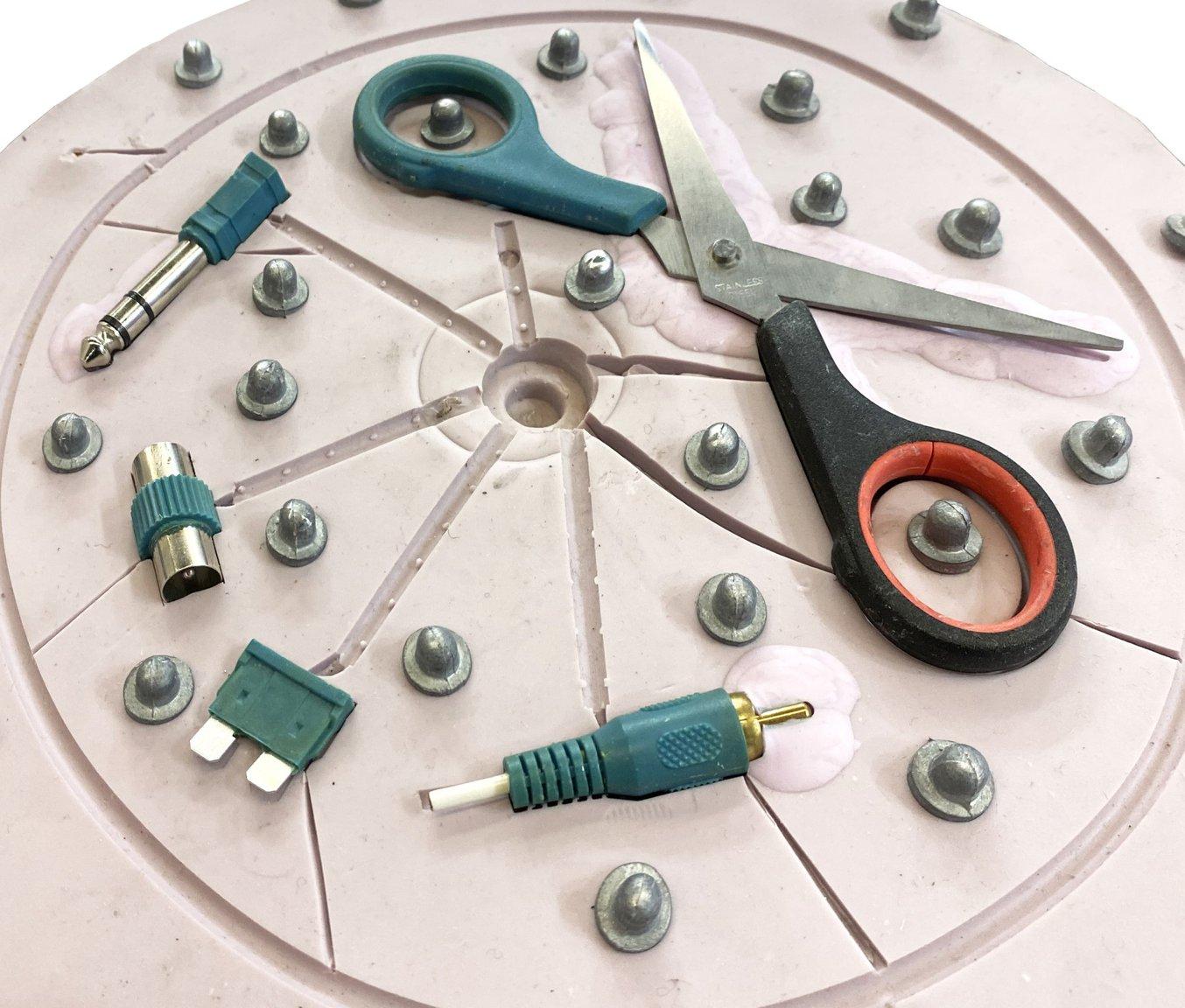
Surmoulage avec des moules SiOCAST.
« Si les figurines ont été notre premier domaine d'activité, c'est parce que nous nous y connaissions déjà, mais il existe encore des milliers d'autres applications possibles », explique Ferran.