Guide de l'impression 3D de dispositifs médicaux : du prototypage à la commercialisation
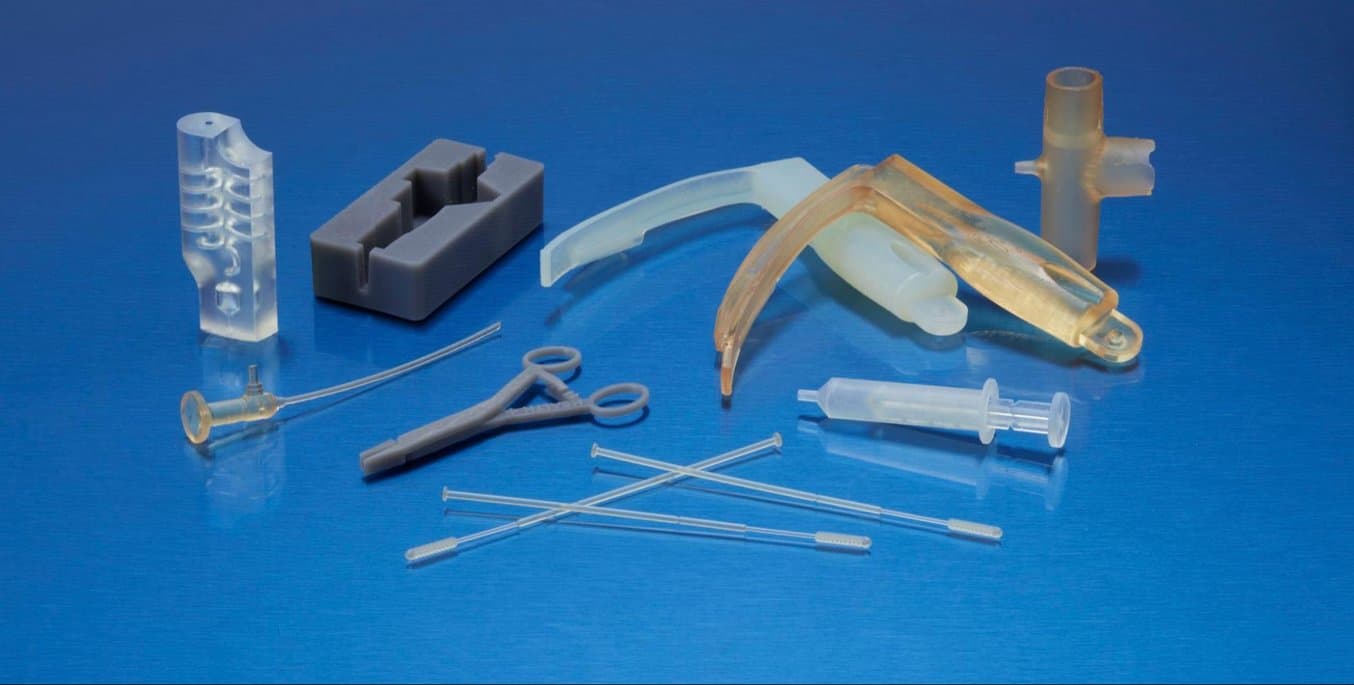
Depuis des décennies, l'impression 3D permet de trouver des solutions innovantes et de développer des dispositifs médicaux, du processus R&D à la production. Les imprimantes 3D sont devenues plus abordables et les investissements dans les appareils et les matériaux ont augmenté, permettant à de plus en plus d'entreprises d'avoir accès à l'impression 3D et de révolutionner le secteur des soins de santé.
En intégrant l'impression 3D en interne, les développeurs et les fabricants de dispositifs médicaux peuvent réduire à la fois les coûts et les délais de commercialisation. Cette technologie permet de développer des produits plus agiles, de créer de nouvelles pièces à usage final et de créer des dispositifs médicaux personnalisés qu'il serait impossible de produire avec des outils traditionnels. Comme nous avons pu le constater depuis le début de l'année 2020, la fabrication additive permet également de passer de la conception à la production de masse de fournitures médicales d'urgence à une vitesse sans précédent.
Dans ce guide complet, nous examinons les différentes applications de l'impression 3D pour la fabrication de dispositifs médicaux, nous comparons les processus d'impression 3D les plus courants dans le secteur médical et nous fournissons un bref aperçu (et des liens vers d'autres ressources) du processus réglementaire pour les dispositifs médicaux imprimés en 3D.
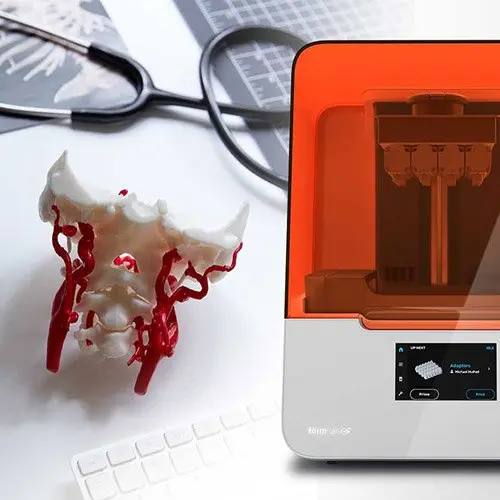
Comment réussir l'impression 3D de dispositifs médicaux
Dans ce rapport, découvrez comment Formlabs Medical aide les entreprises de dispositifs médicaux à adopter la fabrication numérique en interne, et inspirez-vous des exemples de quatre entreprises qui créent actuellement des dispositifs révolutionnaires grâce à l'impression 3D.
Applications de l'impression 3D pour les dispositifs médicaux
La vitesse, la réduction des coûts, la personnalisation et la liberté de conception offertes par l'impression 3D ont conduit à un grand nombre de cas d'utilisation dans le secteur des dispositifs médicaux. Examinons les applications les plus courantes et les exemples concrets qui mettent en évidence la polyvalence de l'impression 3D.
Prototypage rapide de dispositifs médicaux
Le développement de produits innovants va de pair avec l'amélioration des soins aux patients et des résultats obtenus dans le secteur des soins de santé. Le prototypage est un élément clé de ce processus itératif dans lequel des modifications sont apportées au produit, puis mises en œuvre et testées dans un environnement contrôlé.
Le prototypage rapide est l'ensemble des techniques utilisées pour fabriquer rapidement un modèle grandeur nature d'une pièce physique ou d'un assemblage à l'aide de données 3D de conception assistée par ordinateur (CAO). L'impression 3D convient parfaitement au prototypage : elle offre une liberté de création presque illimitée, ne nécessite pas d'outillage et peut produire des pièces dont les propriétés mécaniques sont très proches de celles produites par les méthodes de fabrication traditionnelles.
« Auparavant, nous comptions presque exclusivement sur des fournisseurs externes pour la fabrication de nos prototypes. Aujourd’hui, nous utilisons quatre machines Formlabs et l’impact a été conséquent. Notre taux d’impression 3D a doublé, les coûts ont été réduits de 70 % et le niveau de détail de l’impression permet de communiquer clairement sur la conception de dispositifs avec les chirurgiens orthopédistes. »
Alex Drew, ingénieur Projet mécanique, DJO Surgical
L'impression 3D offre aux fabricants la possibilité de développer des prototypes visuels, tactiles et fonctionnels, même pour les dispositifs médicaux les plus complexes. De nouvelles itérations peuvent être réalisées en quelques heures et validées pour déterminer si d'autres modifications sont nécessaires. L'impression 3D permet également de développer des prototypes de dispositifs médicaux et d'utiliser divers matériaux pour créer des produits solides, flexibles ou résistants à la chaleur.
En testant un prototype fonctionnel à l'aide de processus de validation éprouvés, le fabricant dispose de résultats sur lesquels il peut s'appuyer pour réaliser d'autres itérations. Les prototypes imprimés en 3D peuvent également être utilisés pour présenter un concept à des investisseurs ou à de futurs clients.
La facilité d'utilisation et le faible coût de l'impression 3D en interne ont également révolutionné le développement des produits. Plus de 85 % des 50 plus grands fabricants de dispositifs médicaux ont adopté la technologie Formlabs pour produire des prototypes, des aides à la fabrication ou des dispositifs d'utilisation finale. En raison d'un CAPEX débutant à moins de 5000 $, de nombreuses startups et petites entreprises ont également bénéficié de cette technologie.
Par exemple, la société britannique Coalesce Product Development, spécialisée dans la conception de dispositifs médicaux, développe des dispositifs d'administration de médicaments, notamment des inhalateurs et des injecteurs. Le fabricant avait du mal à développer des prototypes de dispositifs médicaux complexes en utilisant des processus de fabrication traditionnels, car les coûts de démarrage étaient élevés et les outils de production traditionnels difficiles à utiliser.
L'équipe de Coalesce s'est tournée vers l'impression 3D de bureau stéréolithographique (SLA) en interne pour prototyper, tester et fabriquer divers dispositifs de formes et de tailles différentes. Grâce à l'impression 3D, ils ont créé de nouveaux prototypes en moins de 24 heures à un coût 10 à 20 fois inférieur à celui de la sous-traitance. Outre l'impression 3D des prototypes, ils impriment également en 3D des fixations et des gabarits d'essai pour accélérer les tests de leurs inhalateurs.
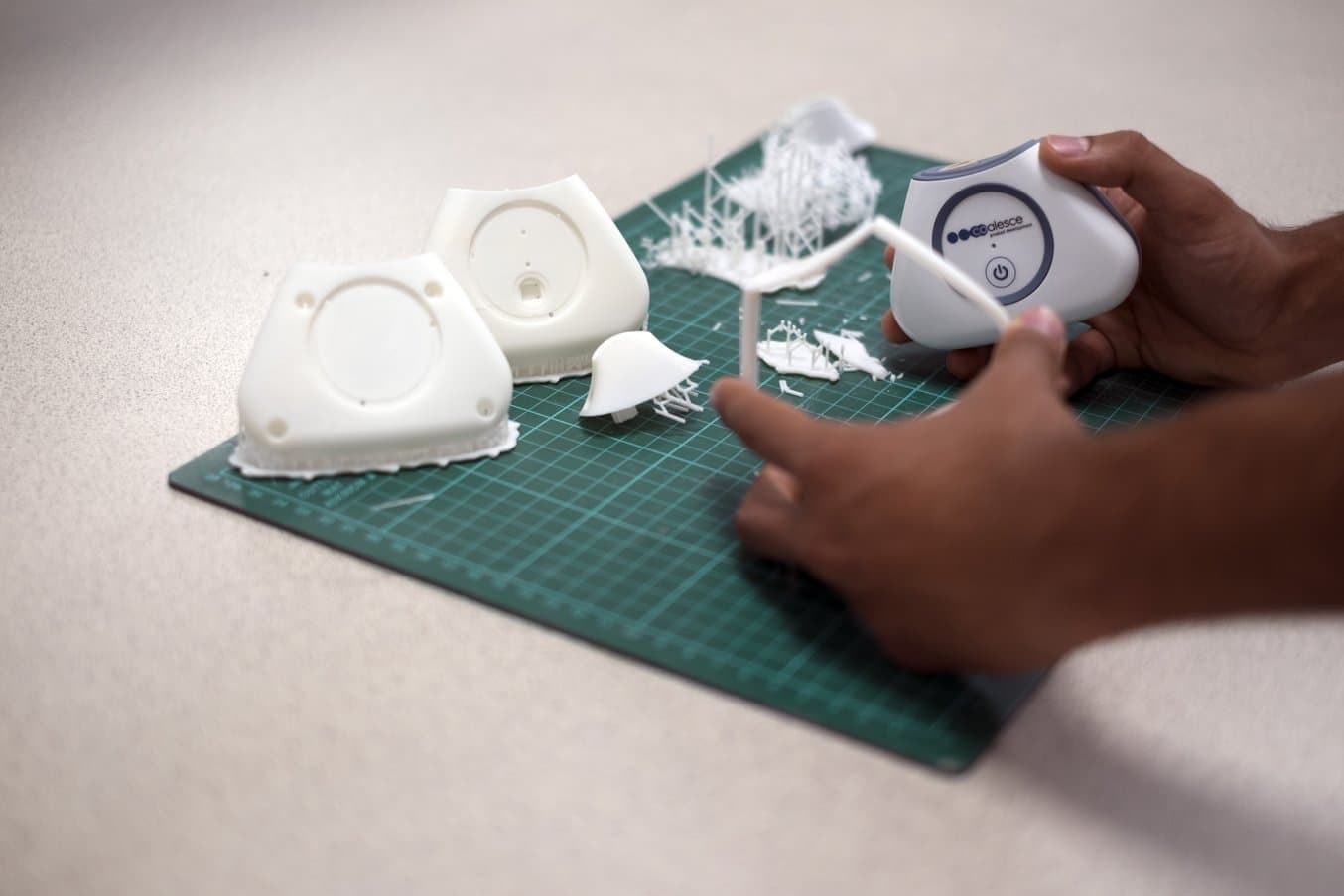
La société de conception de dispositifs médicaux Coalesce utilise l'impression 3D pour réaliser des prototypes de dispositifs d'administration de médicaments, tels que des inhalateurs.
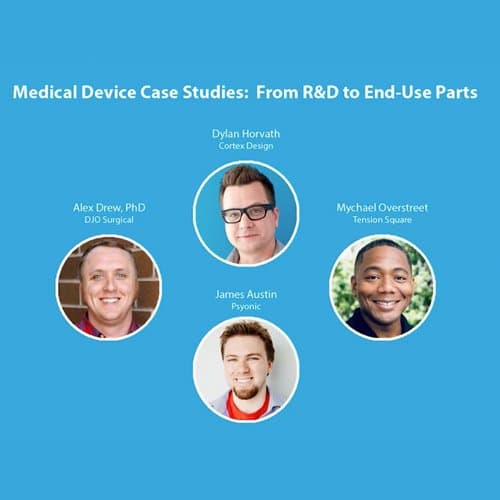
Études de cas sur les dispositifs médicaux : de la R&D à l'utilisation finale des pièces
Dans ce webinaire, Gaurav Manchanda, directeur du développement du marché médical chez Formlabs, accueille des clients Formlabs travaillant dans le secteur médical. Les entreprises représentées incluent des startups tout comme de grandes sociétés réalisant plus d'un milliard de dollars de chiffre d'affaires, notamment Cortex Design, DJO Surgical, Psyonic et TensionSquare.
Fabrication de dispositifs médicaux spécifiques aux patients
La plupart des procédés de fabrication traditionnels, tels que le moulage par injection ou le thermoformage, nécessitent un outillage coûteux, ce qui les rend inadaptés pour produire des pièces sur mesure ou personnalisées. L'impression 3D permet de résoudre ce problème de deux façons.
Outillage rapide pour les processus de fabrication traditionnels
Tout d'abord, l'impression 3D peut être utilisée pour fabriquer des outils rapides personnalisés tels que des moules, des modèles, des pièces à couler et des matrices pour toute une série de procédés de fabrication traditionnels, notamment le moulage par injection, le thermoformage, le moulage en silicone, le surmoulage, le moulage par insertion, le moulage par compression, la fonderie, etc.
Le formage sous vide permet par exemple de créer des plaques occlusales et des appareils de maintien dentaires qui sont conçus et créés sur mesure grâce à des dispositifs de scan intraoral ou de bureau. La fabrication de ces dispositifs consiste à former sous vide une feuille de plastique sur un modèle personnalisé pour chaque étape du traitement. Comme les imprimantes 3D peuvent produire ces modèles directement à partir des fichiers numériques en quelques heures à peine, elles sont devenues l'outil de choix pour produire ces dispositifs, qui sont de plus en plus populaires en orthodontie.
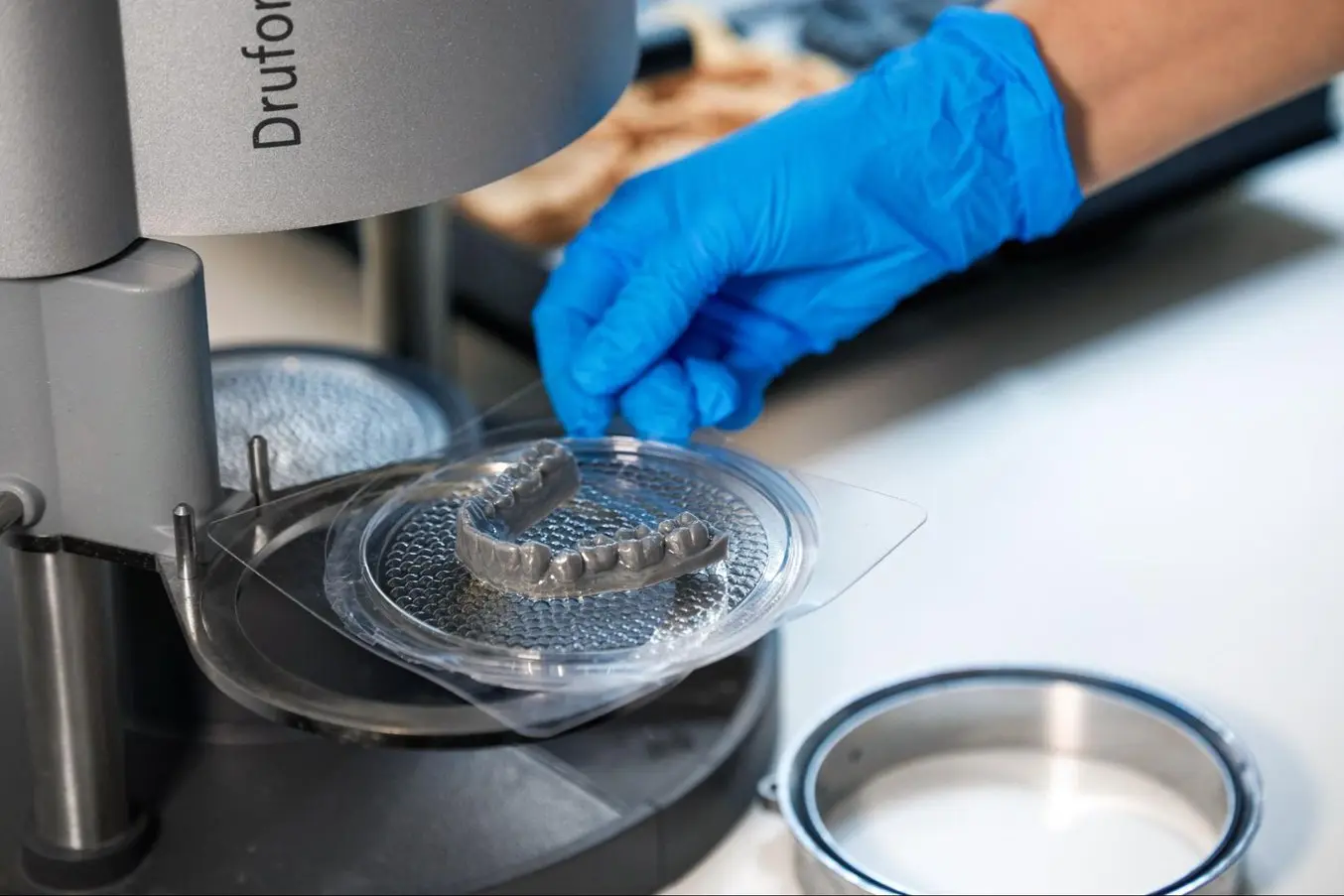
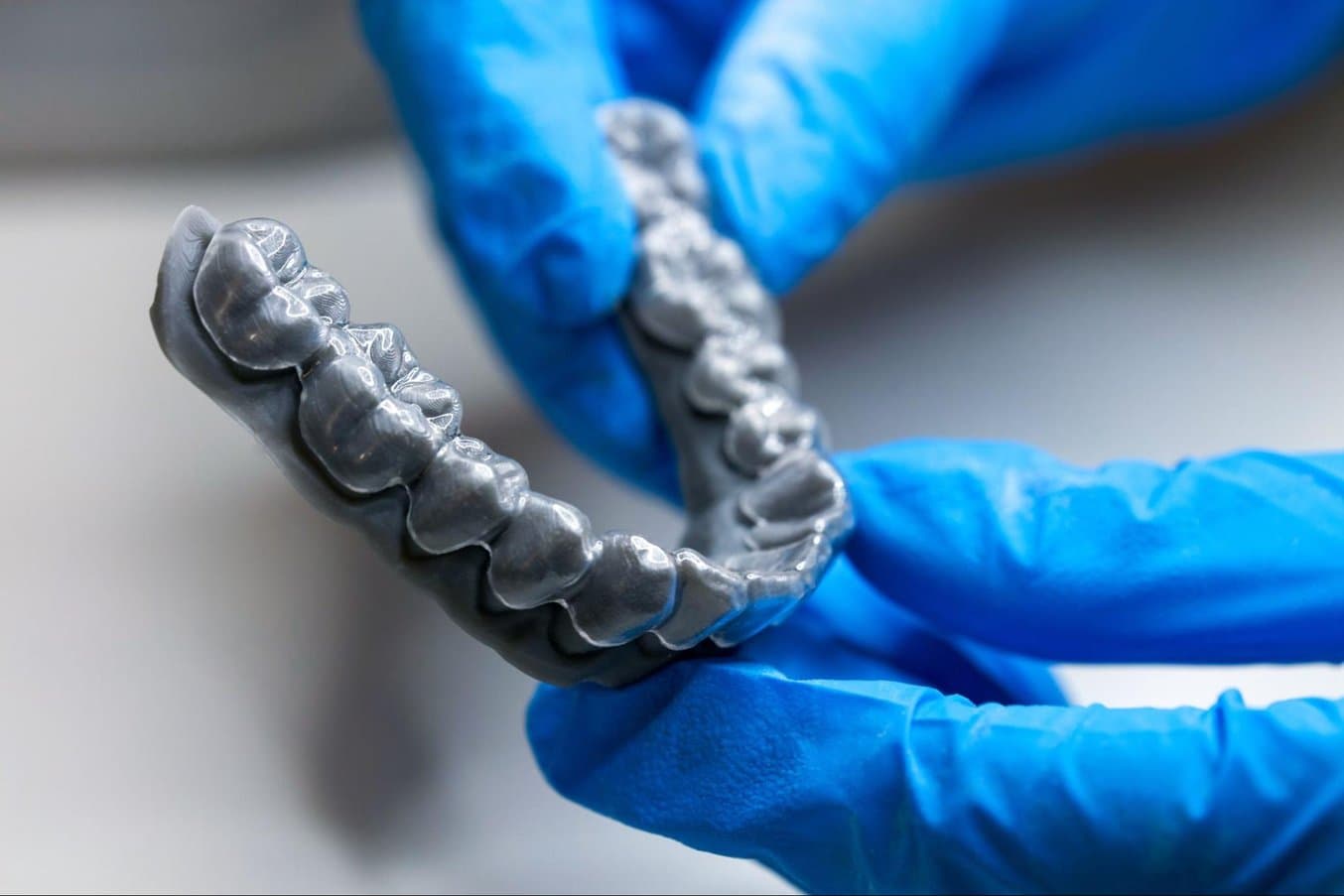
L'impression 3D est la méthode de prédilection pour fabriquer des modèles destinés au formage sous vide de plaques occlusales et d'appareils de maintien transparents.
Un autre exemple nous est présenté par Cosm, une entreprise de dispositifs médicaux qui développe un traitement pour les patients souffrant de troubles du périnée. L'entreprise utilise des moules imprimés en 3D pour le moulage de silicone afin de créer des dispositifs sur mesure adaptés à chaque patient.
L'impression 3D donne à Cosm la flexibilité et la rentabilité dont l'entreprise a besoin pour fabriquer des moules de pessaires personnalisés en 24 heures.
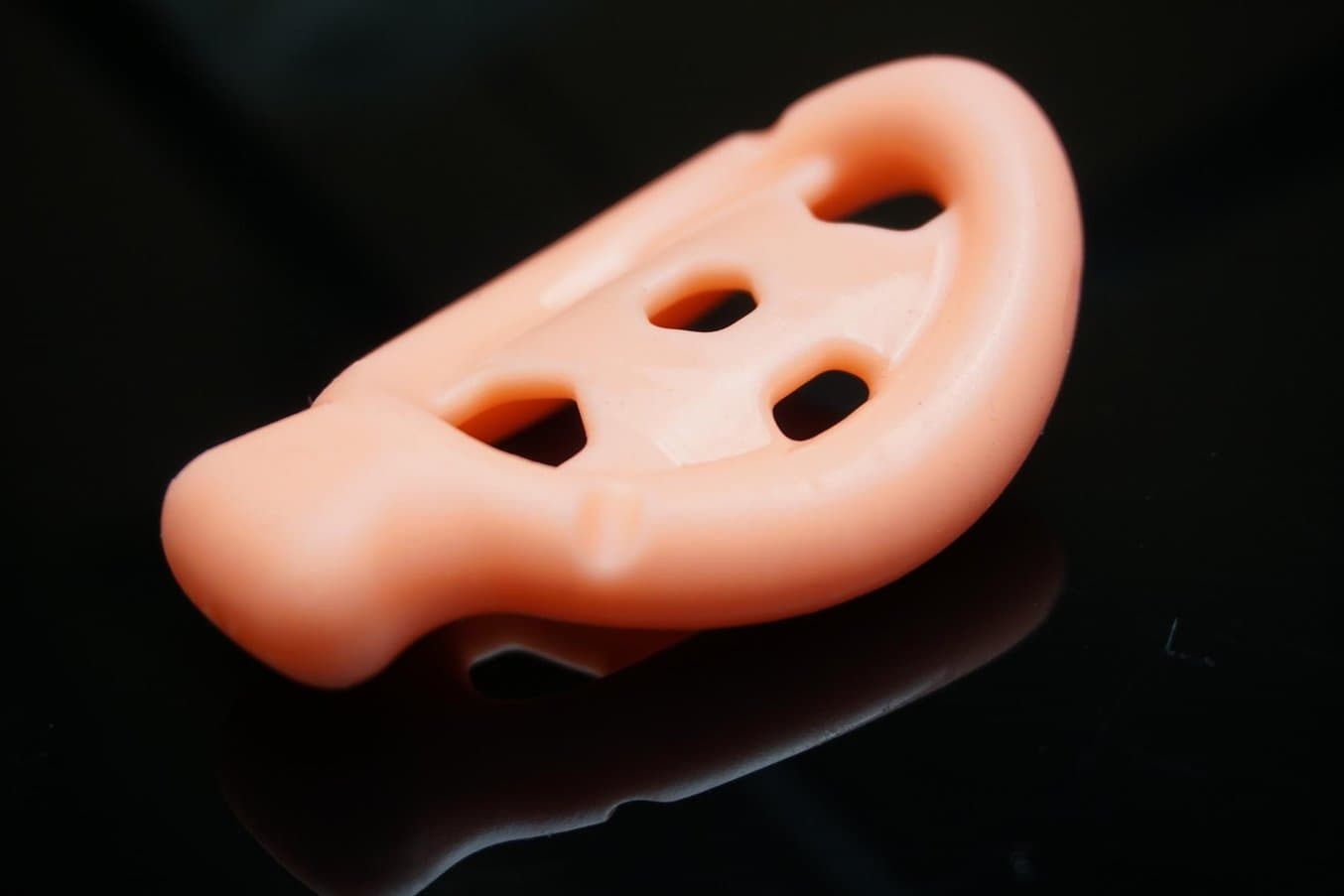
Cosm fabrique des pessaires personnalisés en utilisant le moulage de silicone.
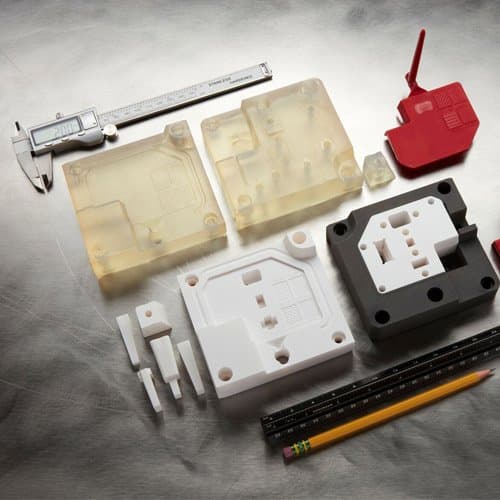
Fabrication de moules par impression 3D : techniques de prototypage et de production
Téléchargez notre livre blanc pour découvrir six procédés de fabrication de moules qui sont possibles avec une imprimante 3D SLA en interne, notamment le moulage par injection, le formage sous vide, le moulage en silicone, etc.
Impression 3D de dispositifs médicaux spécifiques aux patients
L'impression 3D est également de plus en plus utilisée pour fabriquer des dispositifs médicaux à usage final spécifiques aux patients. Comme les processus d'impression 3D ne nécessitent pas d'outillage, ils permettent de créer des pièces personnalisées et des conceptions complexes de manière efficace et rentable.
Une fois de plus, la dentisterie est l'un des domaines de la médecine où l'impression 3D est la plus utilisée. Il est possible d'imprimer en 3D des guides chirurgicaux, des gouttières, des restaurations temporaires et permanentes, ainsi que des prothèses dentaires.
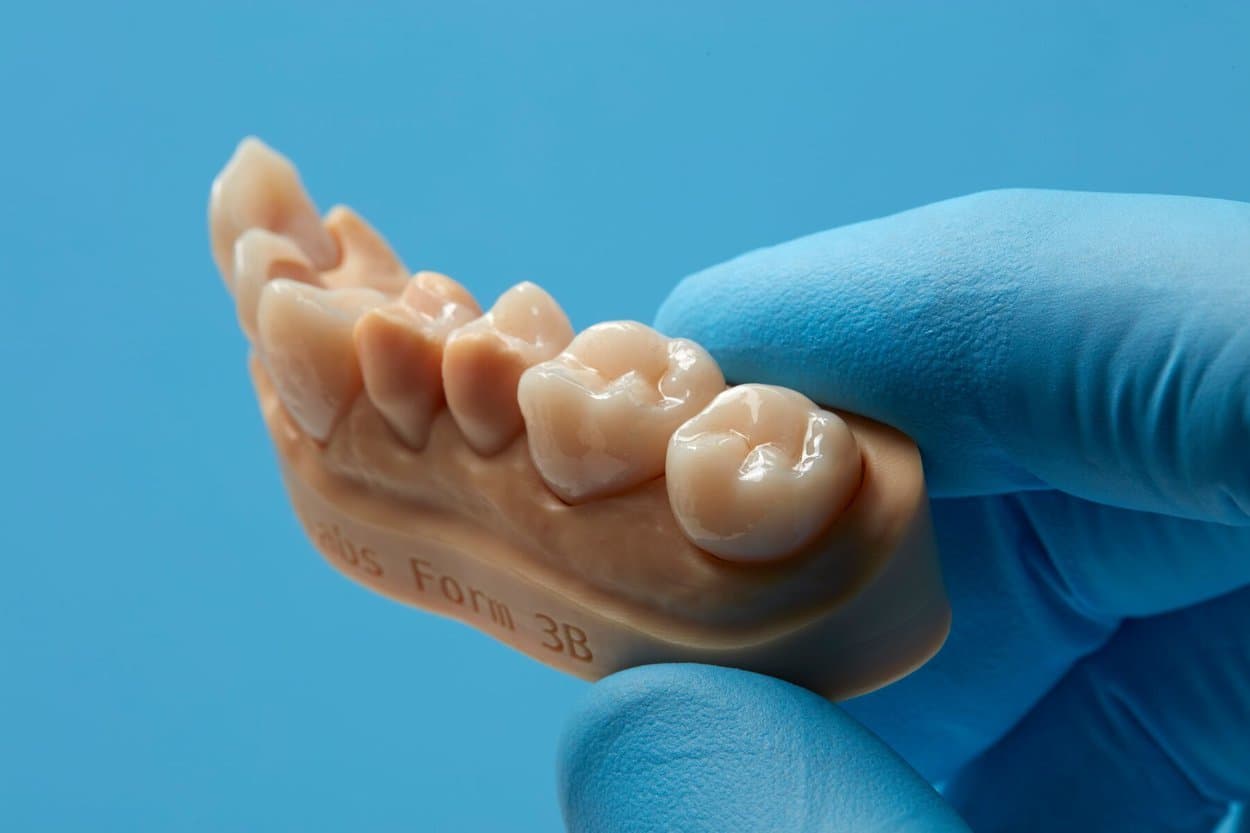
Couronnes permanentes fabriquées à l'aide d'un matériau en résine à charge de céramique.
Parmi les dispositifs médicaux pouvant être imprimés en 3D, citons notamment les dispositifs auditifs sur mesure tels que les prothèses auditives et les équipements de protection contre le bruit, ainsi que les prothèses et orthèses sur mesure solides et durables.
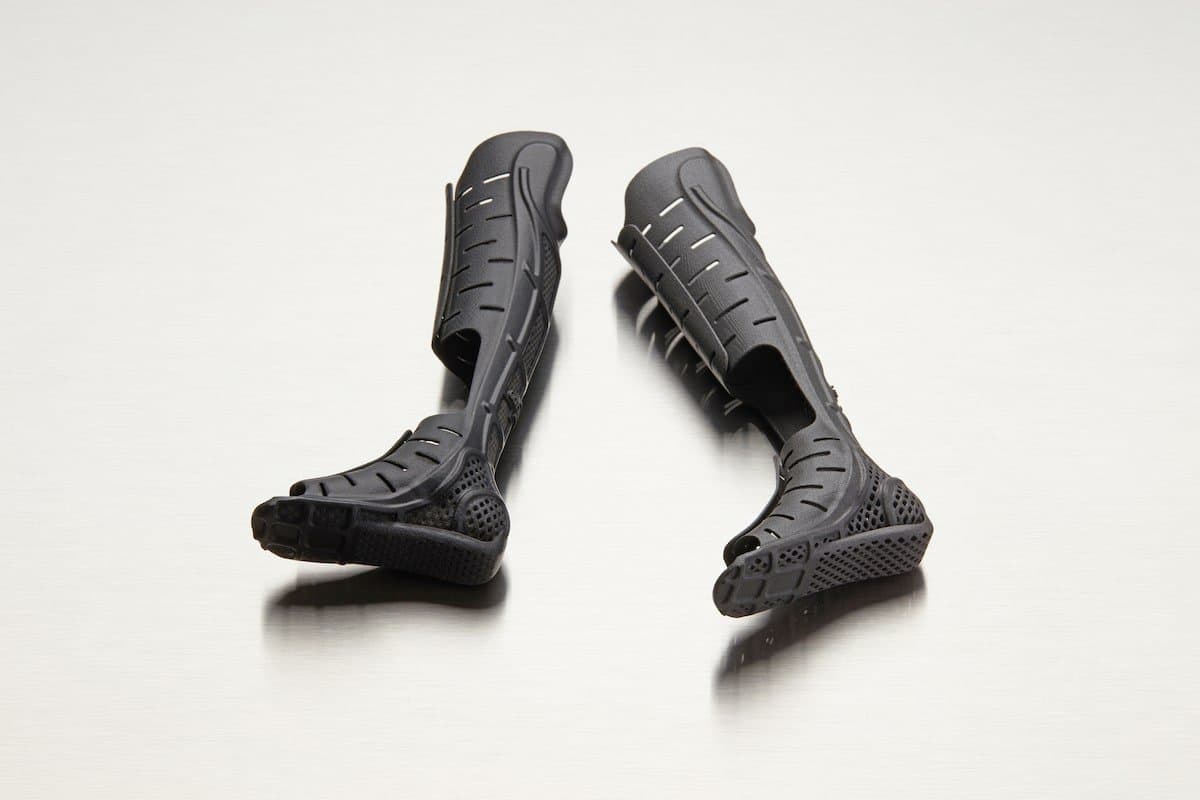
L'impression 3D peut être utilisée pour créer des prothèses et des orthèses durables et biocompatibles sur mesure rapidement et à un prix abordable.
Le fabricant d'instruments chirurgicaux restor3d améliore radicalement la qualité des soins chirurgicaux en imprimant en 3D des instruments nécessaires pour le placement d'implants cervicaux. L'utilisation de l'impression 3D et un processus de développement agile leur permet de créer des outils stériles conçus par des chirurgiens. La méthode de restor3d permet de réduire les coûts de stérilisation, de stockage et de salle d'opération pour les hôpitaux et les centres chirurgicaux. La demande a été élevée : plus de 25 machines Formlabs fabriquent des dispositifs 24 heures sur 24.
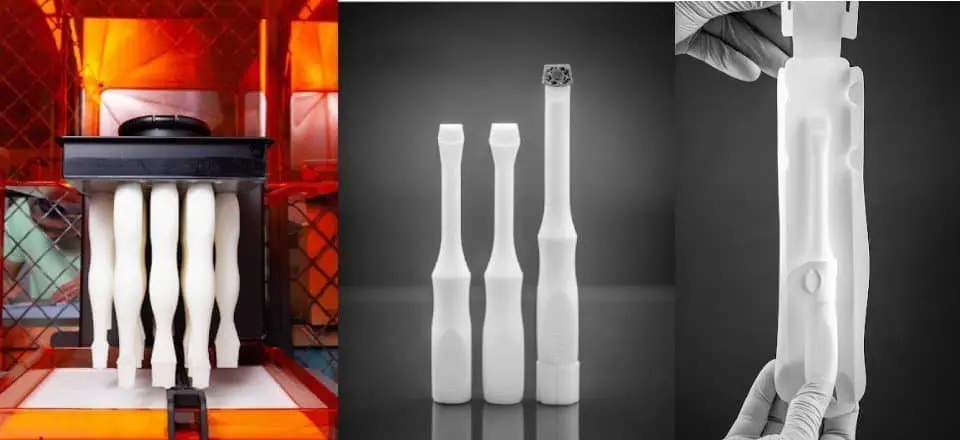
restor3d utilise l'impression 3D pour fabriquer des instruments chirurgicaux spécifiques.
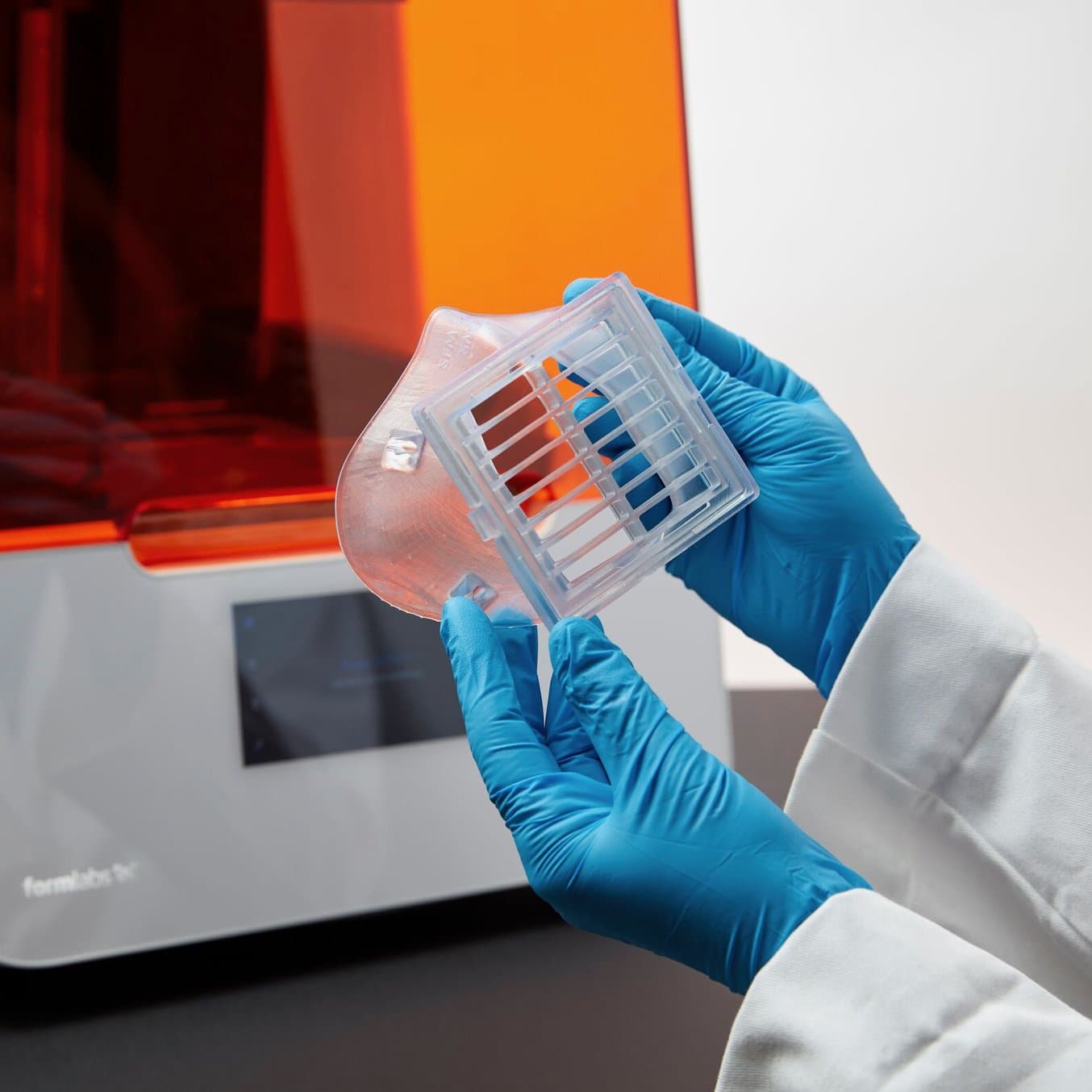
Comment réussir l'impression 3D de dispositifs médicaux
Dans ce rapport, découvrez comment Formlabs Medical aide les entreprises de dispositifs médicaux à adopter la fabrication numérique en interne, et inspirez-vous des exemples de quatre entreprises qui créent actuellement des dispositifs révolutionnaires grâce à l'impression 3D.
Produire des dispositifs médicaux d'utilisation finale
Au-delà des outils chirurgicaux, l'impression 3D est également de plus en plus populaire pour produire des dispositifs médicaux ou des composants de dispositifs médicaux, en particulier pour les conceptions complexes qu'il serait difficile voire impossible de fabriquer avec des procédés traditionnels.
Tension Square a commercialisé un dispositif qui permet de maintenir en place une aiguille de décompression sécurisée. En effet, le vrillage, le pliage ou le délogement de l'aiguille conduisent souvent à des accidents mortels sur le terrain. Après des années de R&D, l'entreprise fabrique désormais le dispositif final avec une imprimante 3D à frittage sélectif par laser (SLS) Fuse 1, ce qui lui permet de réduire sa dépendance à l'égard des fournisseurs externes et de produire plus de 100 dispositifs par imprimante en 24 heures. La société, fondée par un vétéran travaillant comme secouriste, a pour but de produire des millions de pièces par an en utilisant l'impression 3D dans ses installations de fabrication basées aux États-Unis.
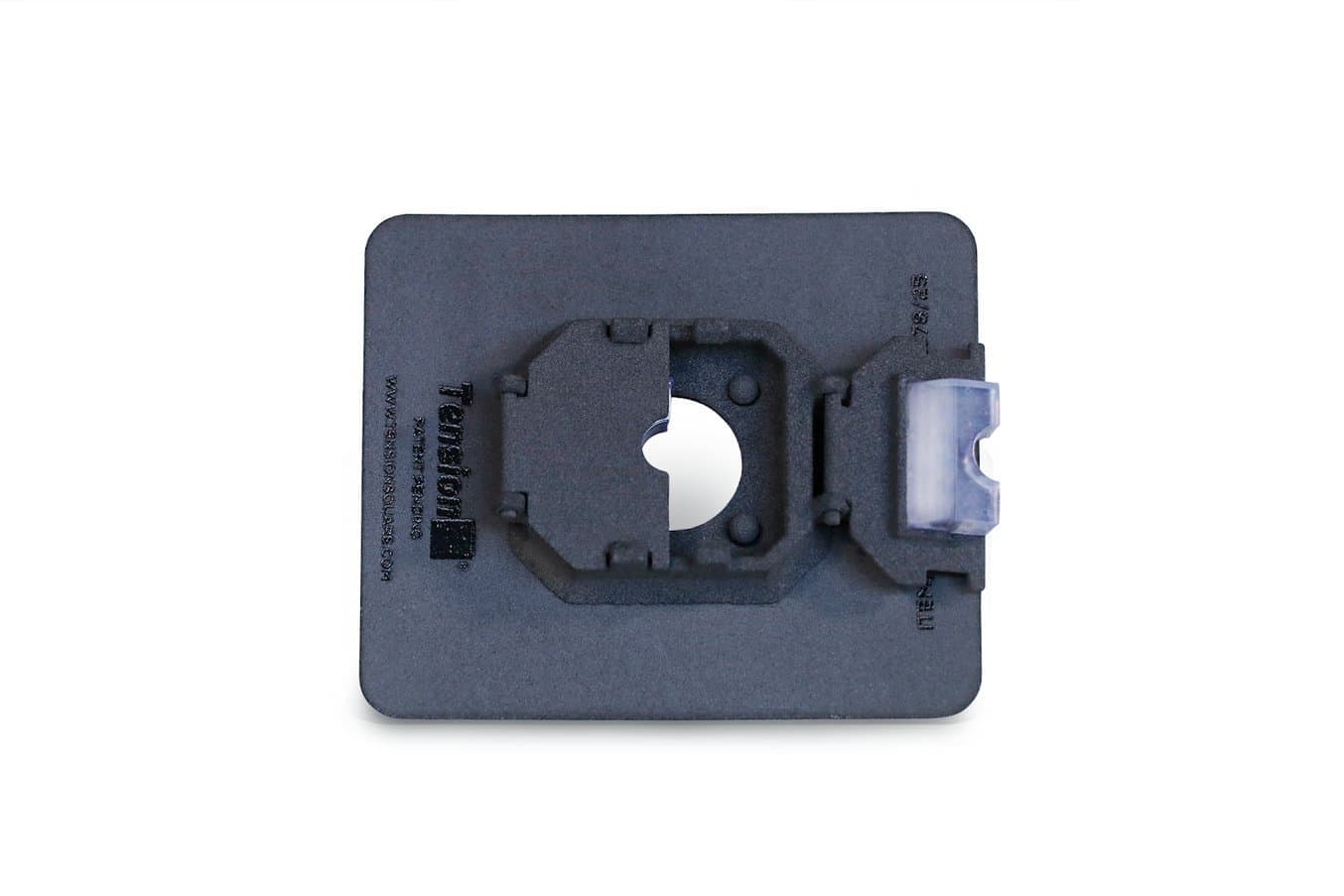
Grâce à l'impression 3D SLS, Tension Square fabrique un dispositif permettant de maintenir en place un cathéter de décompression PTX.
VO2 Master met au point un analyseur métabolique portable, plus facile à utiliser et moins cher que d'autres produits sur le marché. Après avoir utilisé l'impression 3D de manière intensive dans le processus de prototypage, la société a également décidé d'imprimer en 3D les coques extérieures de l'appareil afin de pouvoir le commercialiser plus rapidement. Les coques sont imprimées sur des imprimantes 3D SLA avec Tough 1500 Resin, un matériau résistant qui simule la solidité et la rigidité du polypropylène. Les pièces imprimées sont peintes en blanc avant d'être fixées au masque afin d'améliorer la finition de la surface, la coloration du relief et la durabilité.
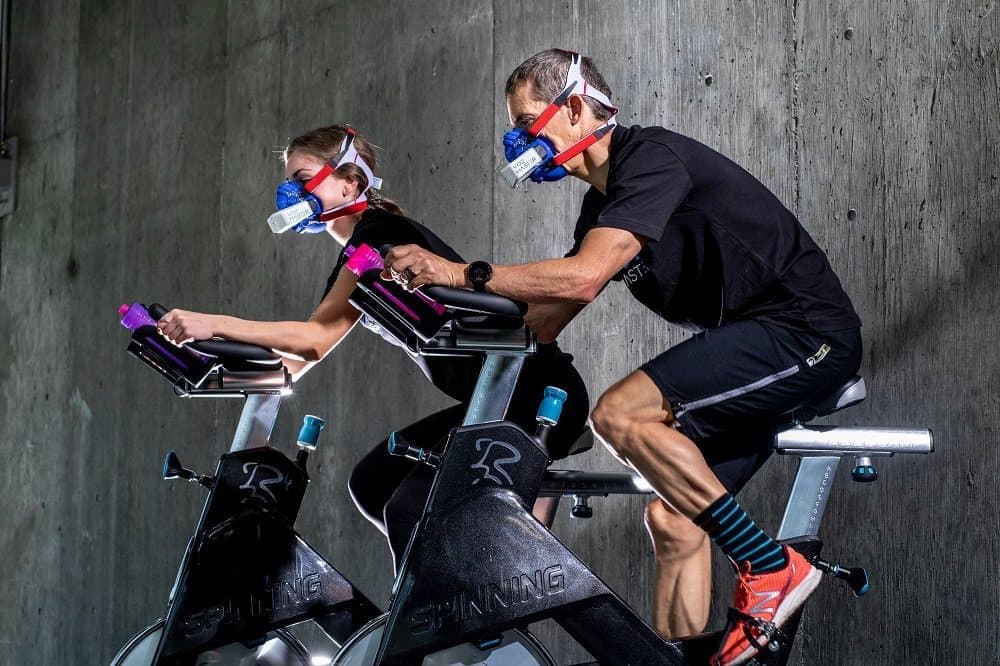
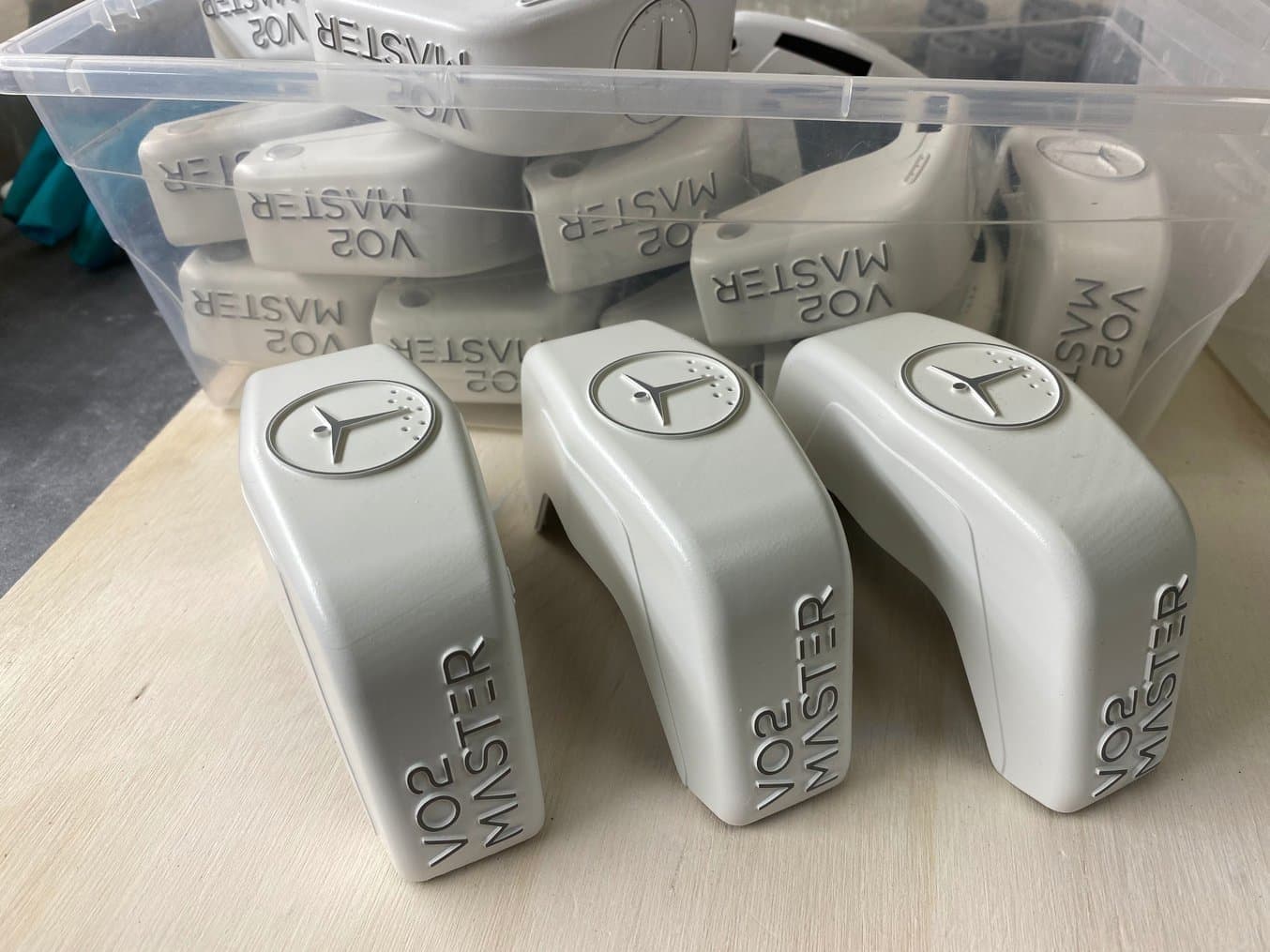
VO2 Master imprime en 3D la coque extérieure de son analyseur métabolique portable, ce qui lui permet de commercialiser le produit plus rapidement.
Fabriquer des fournitures médicales d'urgence
La pandémie de COVID-19 a mis une pression sans précédent sur les centres de soins et les fournisseurs médicaux, ce qui a poussé la plupart des gouvernements à rechercher des solutions dans des endroits insoupçonnés. Pour faire face à l'énorme besoin en fournitures, les constructeurs automobiles se sont mis à fabriquer des masques respiratoires, tandis que les maisons de couture ont commencé à produire des équipements de protection pour résoudre les problèmes liées à la pandémie.
Avec l'augmentation des cas de COVID-19, la nécessité de procéder à des tests à grande échelle s'est accrue, ce qui a entraîné une pénurie mondiale d'écouvillons nasopharyngés (NP) nécessaires au prélèvement d'échantillons pour les tests COVID-19. Après avoir constaté que les écouvillons nasaux de tests COVID-19 étaient très demandés et leur approvisionnement extrêmement limité, des équipes de l'USF Health, de Northwell Health et de Formlabs ont collaboré pour créer un produit alternatif imprimé en 3D. Pendant une semaine, les équipes ont collaboré pour mettre au point un prototype d'écouvillon nasal et pour le tester dans les laboratoires USF Health et Northwell Health. En deux jours, USF Health et Northwell Health ont développé des prototypes en utilisant des imprimantes 3D Formlabs et des résines biocompatibles et stérilisables en autoclave. Douze jours seulement après l'idée initiale, la conception finale a été autorisée pour une utilisation clinique et le fichier 3D a été mis à la disposition d'autres systèmes de santé dans le monde entier. En plus du fichier, les collaborateurs ont mis au point un flux de travail détaillé avec des directives à l'intention des utilisateurs qualifiés du secteur des soins de santé pour imprimer les écouvillons et garantir la santé et la sécurité des patients.
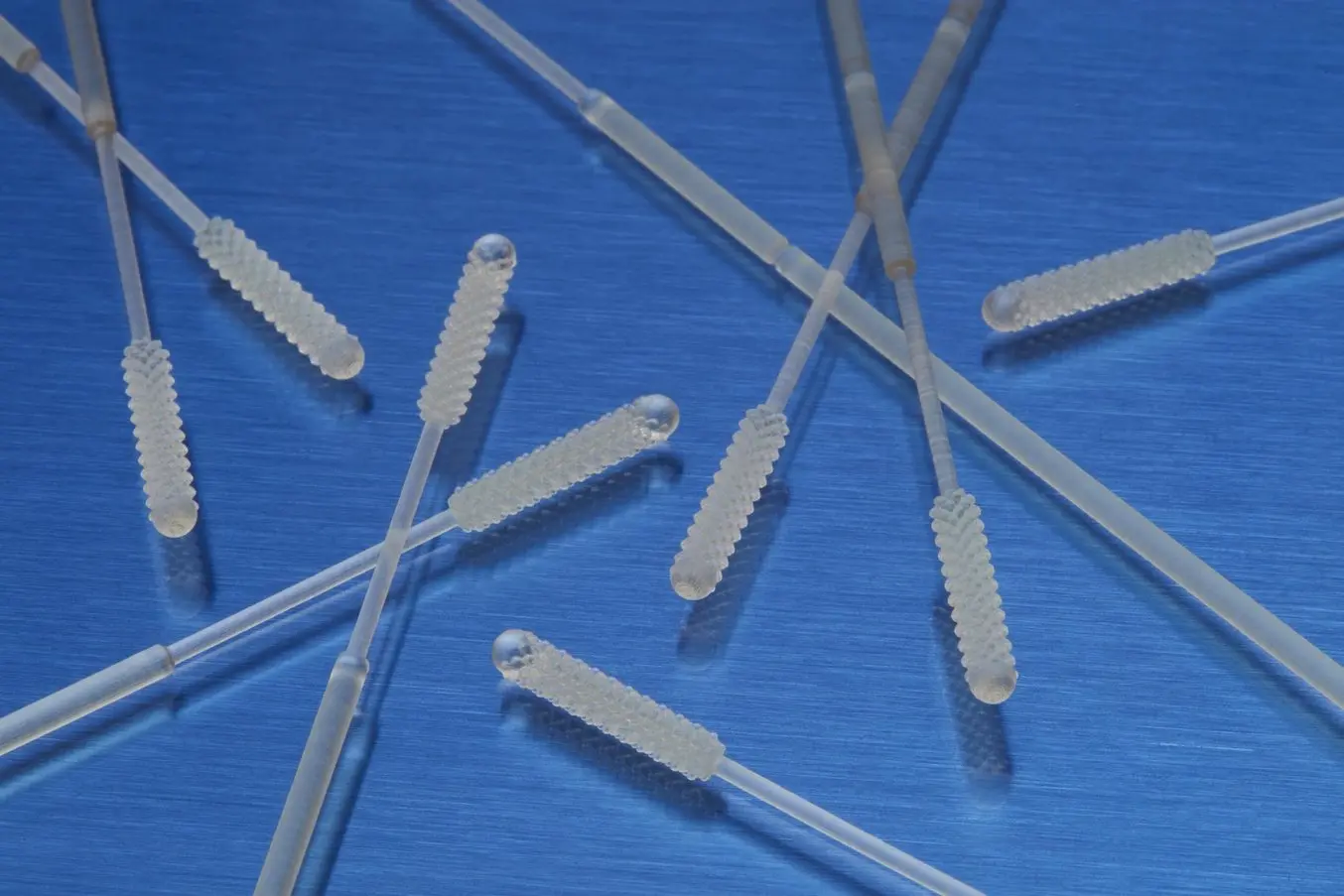
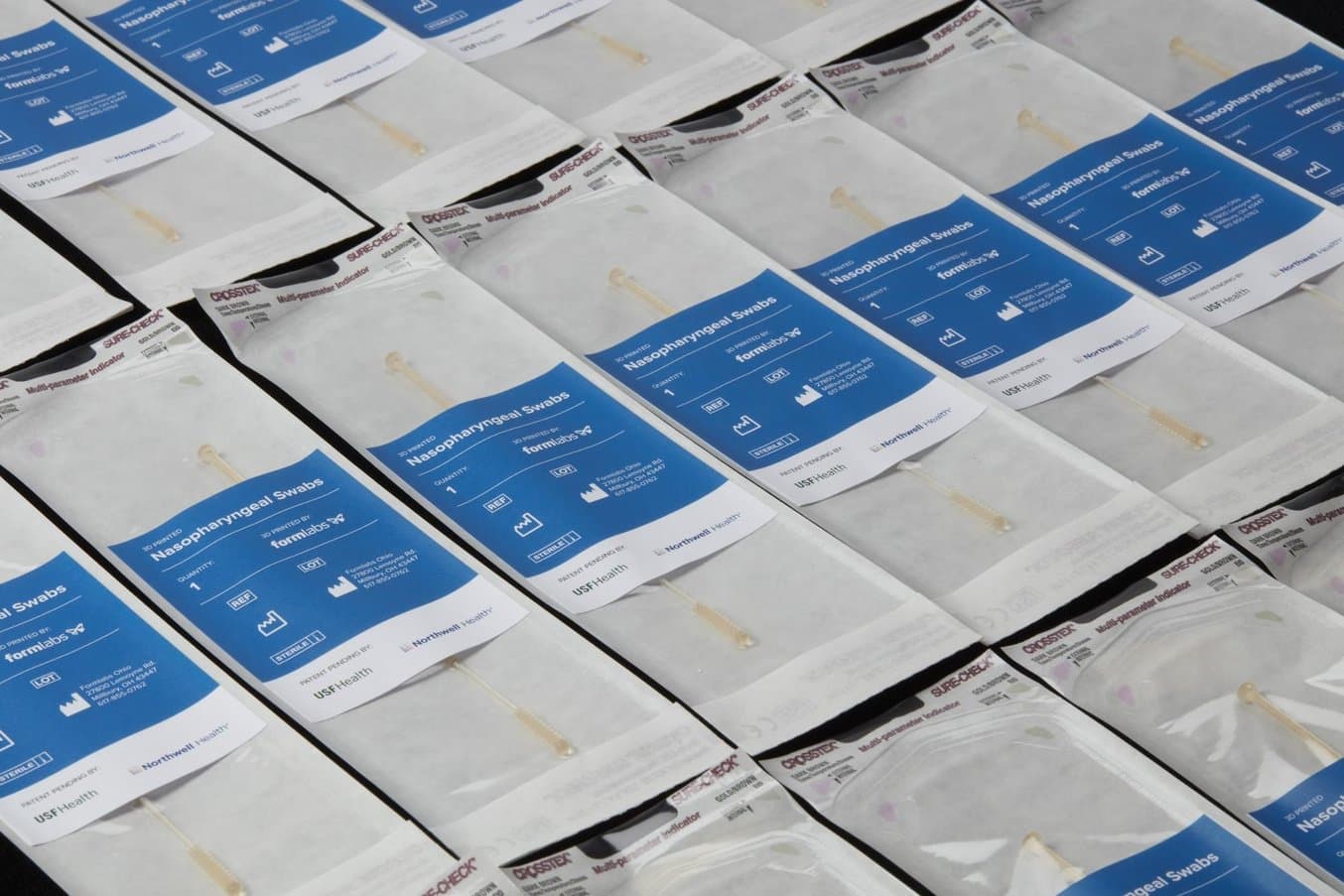
Les écouvillons imprimés en 3D ont permis de réaliser plus de 70 millions de tests COVID dans 25 pays aux premiers stades de la pandémie de COVID-19.
Les hôpitaux, les laboratoires dentaires et les centres médicaux universitaires qui utilisaient leurs imprimantes 3D pour fabriquer des dispositifs chirurgicaux spécifiques aux patients ont pu réutiliser leur équipement et résoudre leurs problèmes de chaîne d'approvisionnement en produisant des écouvillons imprimés en 3D en interne. Grâce à sa conception accessible, à sa fabrication bon marché et à ses processus validés, l'écouvillon a permis de réaliser plus de 70 millions de tests COVID dans 25 pays.
Pour mettre plus de respirateurs à disposition des patients, des machines à pression positive à deux niveaux (BiPAP) normalement utilisées pour soulager l'apnée du sommeil ont été modifiées. Un adaptateur BiPAP a été utilisé pour transformer ces machines en respirateurs mécaniques invasifs fonctionnels.
Pour garantir la création rapide d'un nombre suffisant d'adaptateurs BiPAP, Northwell Health, le plus grand prestataire de soins de santé de New York, a conçu des adaptateurs BiPAP imprimables en 3D. La FDA a accordé à Formlabs une autorisation d'utilisation d'urgence pour imprimer en 3D ces adaptateurs afin d'aider les centres de soins en pénurie de respirateurs traditionnels.
Les processus d'impression 3D pour les dispositifs médicaux
Différentes méthodes existent pour imprimer des dispositifs médicaux en 3D. Il est important de choisir une technologie d'impression adaptée à votre cas d'utilisation.
Les technologies d'impression 3D les plus populaires pour les dispositifs médicaux sont la stéréolithographie (SLA), le frittage sélectif par laser (SLS), le dépôt de fil fondu (FDM), le frittage direct par laser du métal (DMLS) et la fusion sélective par laser (SLM) pour les métaux.
Stéréolithographie (SLA)
Les imprimantes 3D SLA utilisent un laser pour transformer de la résine liquide en plastique durci par un processus dit de photopolymérisation. Ce procédé est le plus apprécié des professionnels médicaux en raison de sa haute résolution, de sa précision et de la polyvalence de ses matériaux.
-
Avantages de la SLA
Les pièces imprimées par stéréolithographie ont l’exactitude et la résolution les plus élevées, les détails les plus précis et la finition de surface la plus lisse de tous les procédés d’impression 3D plastique. Cependant, le principal avantage de la SLA réside dans sa polyvalence. Les résines SLA sont formulées pour présenter une vaste gamme de propriétés optiques, mécaniques et thermiques, qui correspondent aux thermoplastiques standards utilisés en ingénierie et dans l’industrie.
La SLA est parfaite pour imprimer des prototypes de dispositifs médicaux avec un haut niveau de détail, des tolérances serrées et une surface lisse, ainsi que des moules, de l’outillage, des modèles médicaux et des pièces finales fonctionnelles. La SLA offre également le plus grand choix de matériaux biocompatibles pour les applications dentaires et médicales. En utilisant Draft Resin, les imprimantes SLA Formlabs sont aussi les plus rapides pour imprimer des prototypes de grande taille. Elles peuvent imprimer jusqu’à 10 fois plus vite que le FDM.
-
Inconvénients de la SLA
Du fait de la polyvalence de ses matériaux, la SLA revient un peu plus cher que le procédé FDM, mais reste tout de même plus abordable que tous les autres procédés d’impression 3D. Les pièces en résine SLA requièrent également un post-traitement après impression. Elles doivent être lavées et post-polymérisées.
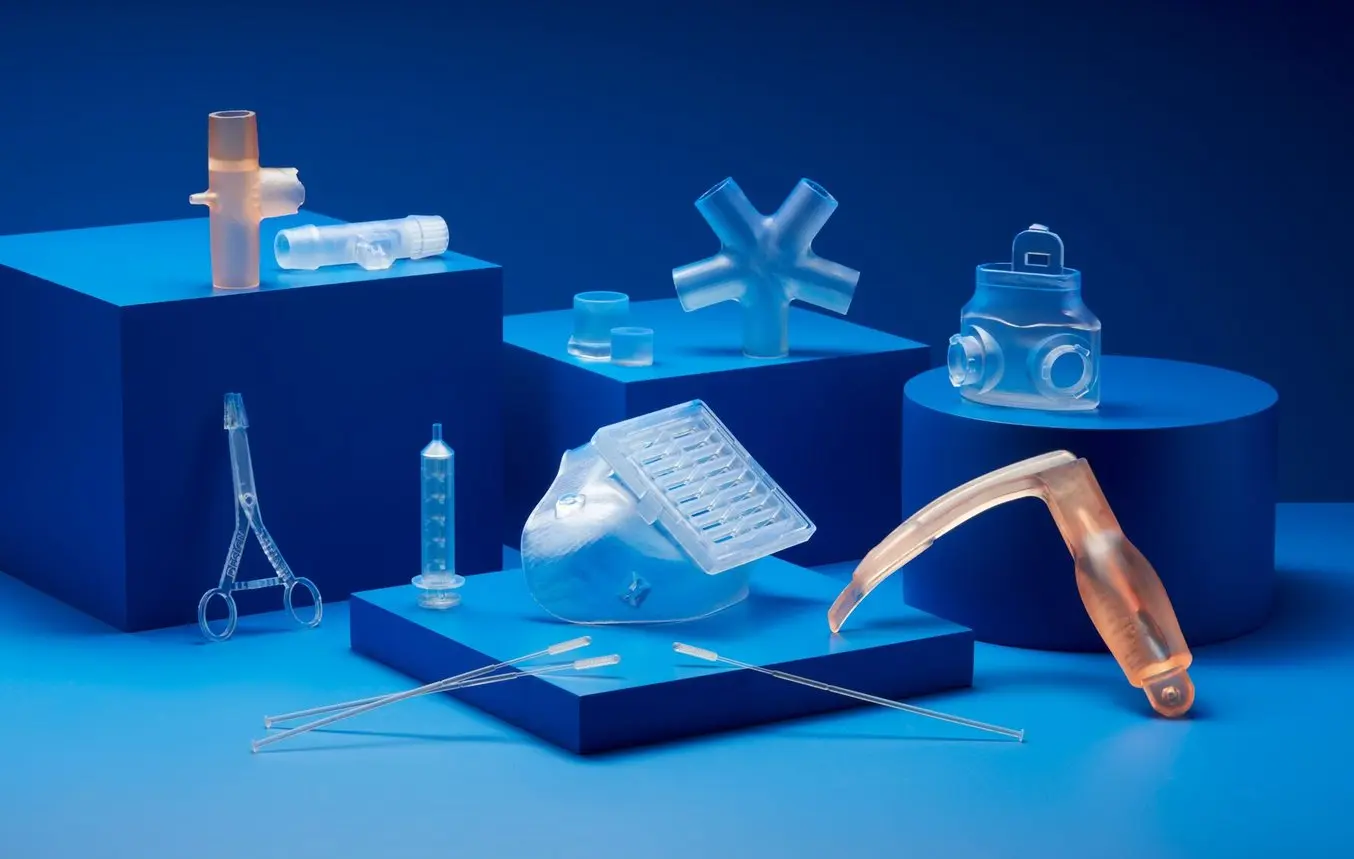
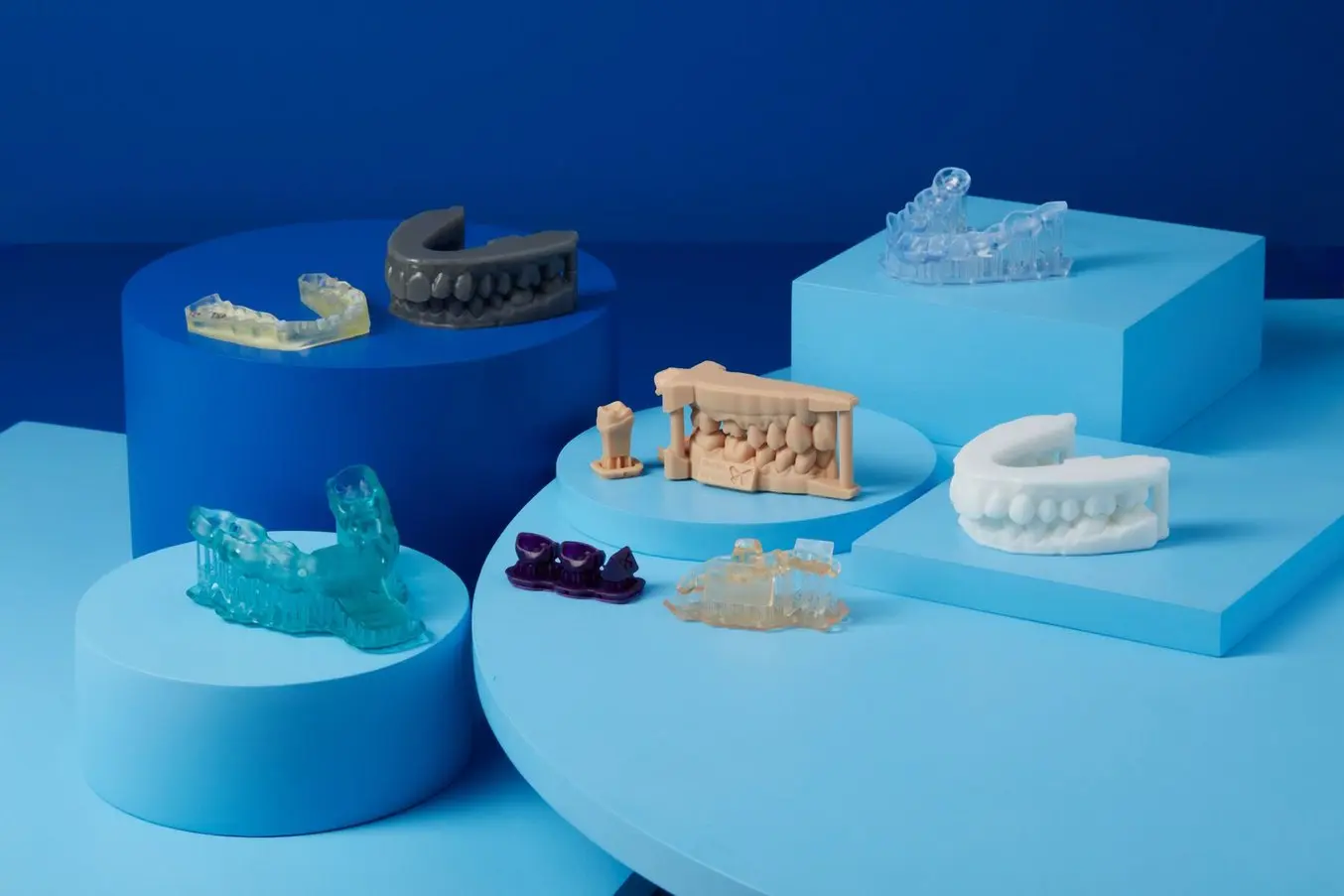
L'impression 3D SLA offre un large choix de matériaux d'impression 3D, y compris des matériaux biocompatibles, pour toute une série d'applications médicales et dentaires.
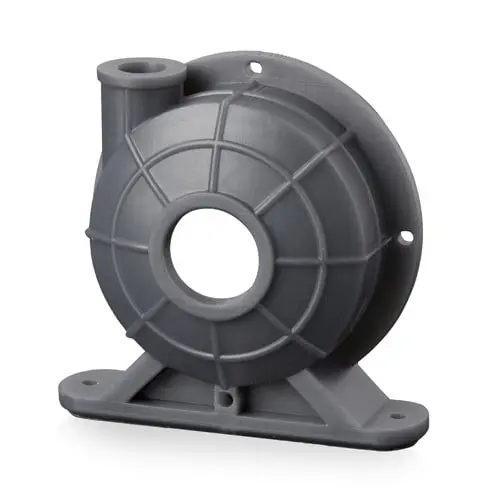
Commandez un échantillon gratuit
Examinez et constatez par vous-même la qualité Formlabs. Nous enverrons un échantillon gratuit à votre bureau.
Frittage sélectif par laser (SLS)
Les imprimantes 3D SLS utilisent un laser de forte puissance pour fondre de petites particules de poudre de polymère. La poudre non fondue supporte la pièce pendant l’opération, ce qui évite d’avoir à lui ajouter des structures de support et rend ce procédé particulièrement efficace pour imprimer des pièces mécaniques complexes.
Le SLS est le procédé de fabrication additive le plus utilisé dans le secteur industriel, du fait des excellentes propriétés mécaniques des pièces produites. En fonction du matériau, les pièces en nylon SLS peuvent également être biocompatibles et stérilisables.
-
Avantages du SLS
Du fait que le SLS ne requiert pas de structures de support, il est idéal pour des pièces à géométrie complexe, présentant des formes internes ou en creux, des contre-dépouilles ou des parois fines. Les pièces fabriquées par SLS présentent d’excellentes caractéristiques mécaniques, leur résistance s’apparentant à celle de pièces moulées par injection.
Le matériau le plus utilisé en SLS est le nylon, thermoplastique courant en ingénierie, dont les propriétés mécaniques sont excellentes. Le nylon est léger, solide et flexible, et il est résistant aux chocs, aux produits chimiques, à la chaleur, aux rayons UV, à l'eau et à la saleté. Les pièces en nylon imprimées en 3D peuvent également être biocompatibles et non sensibilisantes, ce qui signifie qu'elles peuvent rester en contact avec la peau et être utilisées en toute sécurité.
Le faible coût par pièce, la productivité élevée, les matériaux éprouvés et la biocompatibilité font du SLS le procédé le plus apprécié par les ingénieurs médicaux pour réaliser des prototypes fonctionnels, et une alternative rentable au moulage par injection pour réaliser des lots de taille restreinte ou de complément.
-
Inconvénients du SLS
Les imprimantes 3D SLS ont un prix d'entrée plus élevé que les technologies FDM ou SLA. De plus, bien que le nylon soit un matériau polyvalent, le choix des matériaux pour le SLS est plus limité que pour le FDM ou la SLA. En sortant de l’imprimante, les pièces présentent une surface légèrement rugueuse qui nécessite un sablage pour la lisser.

L'impression 3D SLS est idéale pour fabriquer des prototypes solides et fonctionnels et des pièces d'utilisation finale, telles que des prothèses et des orthèses.
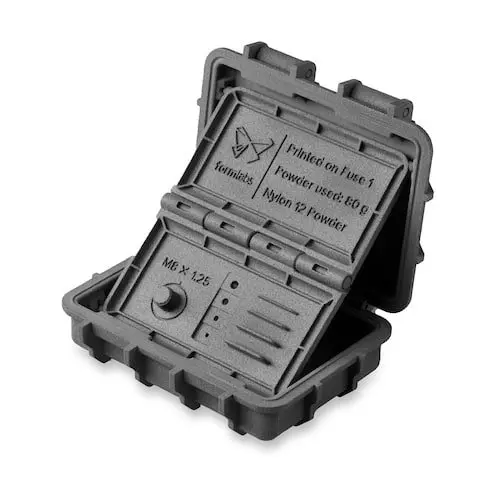
Commandez un échantillon gratuit
Examinez et constatez par vous-même la qualité Formlabs. Nous enverrons un échantillon gratuit à votre bureau.
Dépôt de fil fondu (FDM)
Les pièces fabriquées en FDM, ou encore FFF (fabrication par filament fondu) sont obtenues en extrudant un filament thermoplastique fondu, qu’une buse dépose couche par couche sur la zone de fabrication.
Le procédé FDM est le procédé le plus utilisé au niveau des consommateurs, du fait de l’émergence d’imprimantes 3D pour amateurs. Mais les imprimantes FDM industrielles sont aussi appréciées des professionnels.
-
Avantages du FDM
Le procédé FDM fonctionne avec toute une gamme de thermoplastiques standard, comme l’ABS, le PLA et leurs variantes. Le prix d’entrée et le coût des matériaux en deviennent plus bas. Le FDM convient aux modèles simples de démonstration de faisabilité et au prototypage peu coûteux des pièces les plus simples. Certains matériaux FDM sont également biocompatibles.
-
Inconvénients du FDM
De toutes les technologies d’impression 3D pour les plastiques, comme la SLA et le SLS, le FDM est celle qui présente la résolution et l’exactitude les plus faibles. Il ne convient donc pas à la fabrication de modèles compliqués ou de pièces avec des parties complexes. La qualité de la finition peut être améliorée par des procédés de polissage chimique ou mécanique longs et gourmands en main-d’œuvre. Des imprimantes 3D FDM peuvent utiliser des supports solubles pour atténuer certains de ces problèmes. Elles travaillent avec une gamme plus large de thermoplastiques techniques, mais leur coût est nettement plus élevé. Lors de la création de grandes pièces, l'impression FDM a également tendance à être plus lente que l'impression SLA ou SLS.
Frittage direct par laser du métal (DMLS) et fusion sélective par laser (SLM)
Les imprimantes 3D à frittage direct par laser du métal (DMLS) et à fusion sélective par laser (SLM) fonctionnent de manière similaire aux imprimantes SLS, mais fondent couche par couche avec un laser des particules de poudre de métal, et non des polymères.
Les imprimantes 3D DMLS et SLM peuvent créer des produits métalliques solides, précis et complexes, ce qui rend ce procédé idéal pour diverses applications médicales.
-
Avantages de la DMLS et de la SLM
Le principal avantage de ces procédés réside évidemment dans les matériaux, car les imprimantes 3D DMLS et SLM sont capables de produire des dispositifs et des composants médicaux à usage final très performants à partir de métal. Ces procédés permettent de reproduire des géométries complexes et de fabriquer des produits finis solides, durables et biocompatibles. Ils peuvent être utilisés pour fabriquer des implants génériques (hanches, genoux, implants de la colonne vertébrale, etc.), des implants personnalisés pour le traitement du cancer ou des traumatismes, des prothèses dentaires, ainsi que des produits technologiques médicaux et orthopédiques.
-
Inconvénients de la DMLS et de la SLM
Bien que le prix des imprimantes 3D métal ait également commencé à baisser, avec des coûts allant de 200 000 € à 1 million € voire plus, la plupart des entreprises ne peuvent toujours pas se permettre d’investir dans ces systèmes. Les processus d'impression 3D métal sont également plus complexes.
Au contraire, l’impression 3D SLA convient très bien aux processus de moulage pour produire des pièces métalliques à moindre coût, avec une plus grande liberté de conception et des délais plus courts que les méthodes traditionnelles.
Comparer les procédés d'impression 3D pour les dispositifs médicaux
Le tableau ci-dessous met en évidence les technologies d'impression 3D les mieux adaptées pour produire différents types de dispositifs médicaux.
Stéréolithographie (SLA) | Frittage sélectif par laser (SLS) | Dépôt de fil fondu (FDM) | Impression 3D en métal (DMLS, SLM) | |
---|---|---|---|---|
Volume d’impression | Jusqu’à 300 x 335 x 200 mm (imprimantes 3D de bureau et d’atelier) | Jusqu’à 165 x 165 x 300 mm (imprimantes 3D d’atelier industrielles) | Jusqu’à 300 x 300 x 600 mm (imprimantes 3D de bureau et d’atelier) | Jusqu’à 400 x 400 x 400 mm (DMLS/SLM grand format) |
Gamme de prix | À partir de 3500 € | À partir de 16 500 € | À partir de 2500 € | À partir de 200 000 € |
Matériaux | Variantes de résines (plastiques thermodurcissables). Résines standard, techniques (similaires à l’ABS, au polypropylène ou au silicone, souples, résistantes à la chaleur, rigides), moulables, dentaires et médicales (biocompatibles). | Thermoplastiques techniques, comme le nylon et ses composites (le nylon est biocompatible et convient à la stérilisation). | Thermoplastiques standard, tels que l’ABS, le PLA et leurs variantes. | Acier inoxydable, acier à outils, titane, cobalt-chrome et aluminium. |
Applications idéales | Prototypes très détaillés nécessitant des tolérances serrées et des surfaces lisses (moules, outillage, modèles, modèles médicaux, pièces fonctionnelles, appareils dentaires et médicaux à usage final). | Formes complexes, prototypes fonctionnels, fabrication en petite série ou de complément, orthèses et prothèses. | Modèles de démonstration de faisabilité simples, prototypage peu coûteux de pièces simples. | Pièces solides et durables à géométrie complexe, implants, prothèses dentaires, composants médicaux et orthopédiques en métal. |
La biocompatibilité des matériaux d'impression 3D
En fonction de l'application, des pièces biocompatibles peuvent être requises pour les dispositifs médicaux. Les informations sur la biocompatibilité sont nécessaires pour introduire une demande d'autorisation 510(k) et d'autorisation de mise sur le marché (PMA) aux États-Unis. C'est également le cas pour d'autres demandes réglementaires dans le monde entier. Cela permet de vérifier si le dispositif sera compatible avec le système biologique auquel il est destiné. Des informations manquantes ou inadéquates peuvent retarder la commercialisation du dispositif.
Les exigences en matière d'essais de biocompatibilité doivent être déterminées en fonction de l'utilisation prévue du dispositif (type, zone et durée d'exposition). Déterminer les exigences en matière d'essais dès le début du processus de développement vous donne suffisamment de temps pour effectuer les essais avant de les soumettre aux organismes de réglementation. Il convient de prendre en compte le type de contact prévu entre l'appareil et le corps humain.
Il existe trois types de contact :
-
Contact direct : entre en contact physique avec le patient.
-
Contact indirect : entre en contact physique avec un fluide, un gaz ou une autre matière qui a un contact direct avec le patient.
-
Aucun contact : n'a pas de contact direct ou indirect avec le patient et ne doit donc pas se conformer aux exigences de biocompatibilité.
Certains fabricants d'imprimantes 3D et de matériaux d'impression 3D tels que Formlabs effectuent des tests de biocompatibilité basés sur les normes ISO 10993, ISO 18562 et ISO 7405 et publient les informations sur les matériaux concernés.
Comme les tests sont effectués sur des échantillons imprimés standard, les fabricants sont responsables du respect des instructions d'impression et de post-traitement, ainsi que de la validation de la biocompatibilité pour leurs pièces respectives.
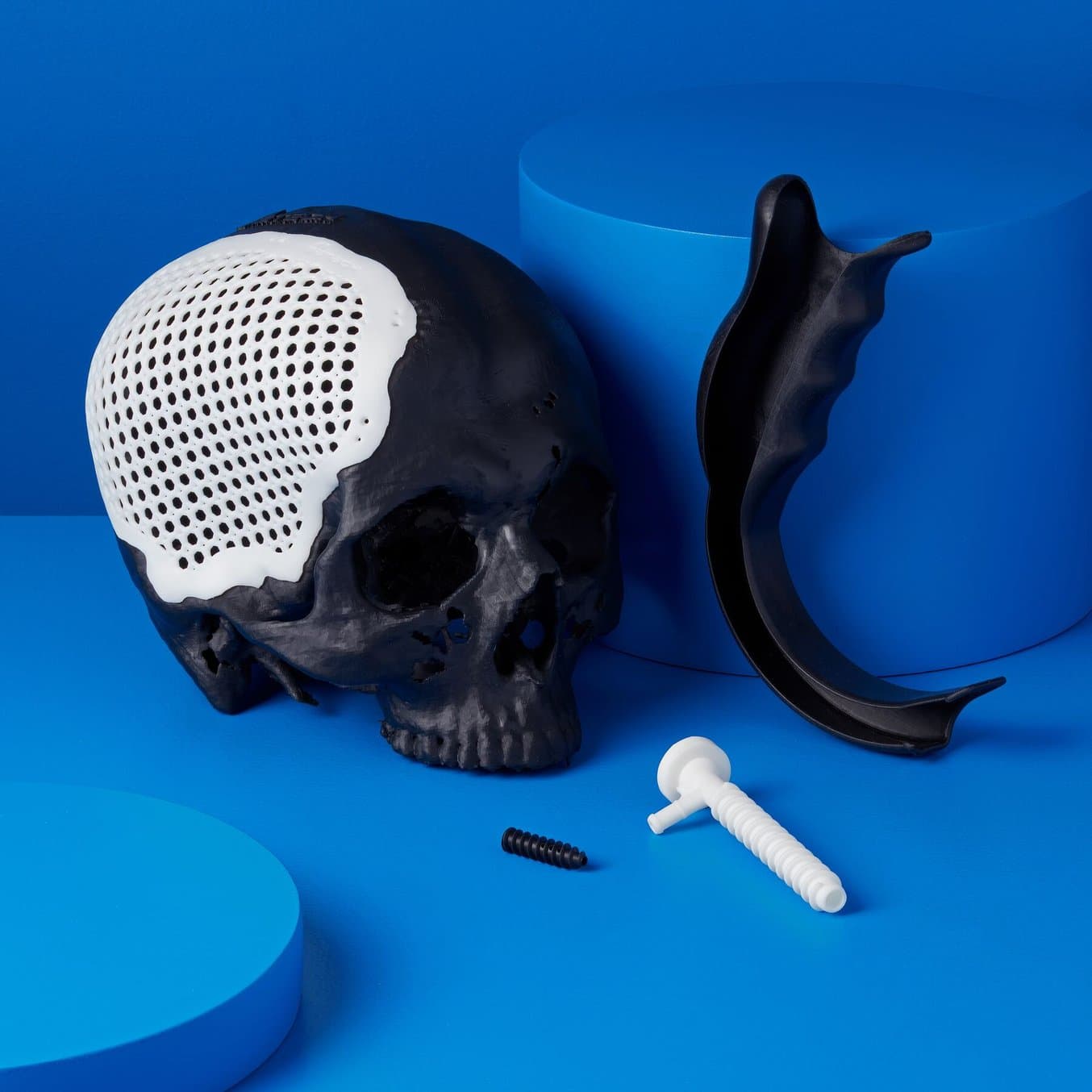
Dispositifs médicaux imprimés en 3D pour la chirurgie de précision : perspectives cliniques, commerciales et réglementaires
Rejoignez Formlabs et Nelson Labs pour un focus approfondi sur la biocompatibilité, incluant une présentation de nos nouveaux matériaux et des meilleures pratiques pour les fabricants de produits médicaux par des experts du secteur.
La réglementation concernant les dispositifs médicaux imprimés en 3D
Les dispositifs médicaux imprimés en 3D doivent répondre aux directives réglementaires en vigueur dans leurs pays respectifs.
Une partie de ce processus consiste à établir un système de gestion de la qualité (SGQ) qui comprend l'ensemble des règles, procédures, formulaires et instructions de travail, ainsi que leur séquence, leurs interactions et les ressources nécessaires pour mener à bien les activités d'une entreprise de dispositifs médicaux.
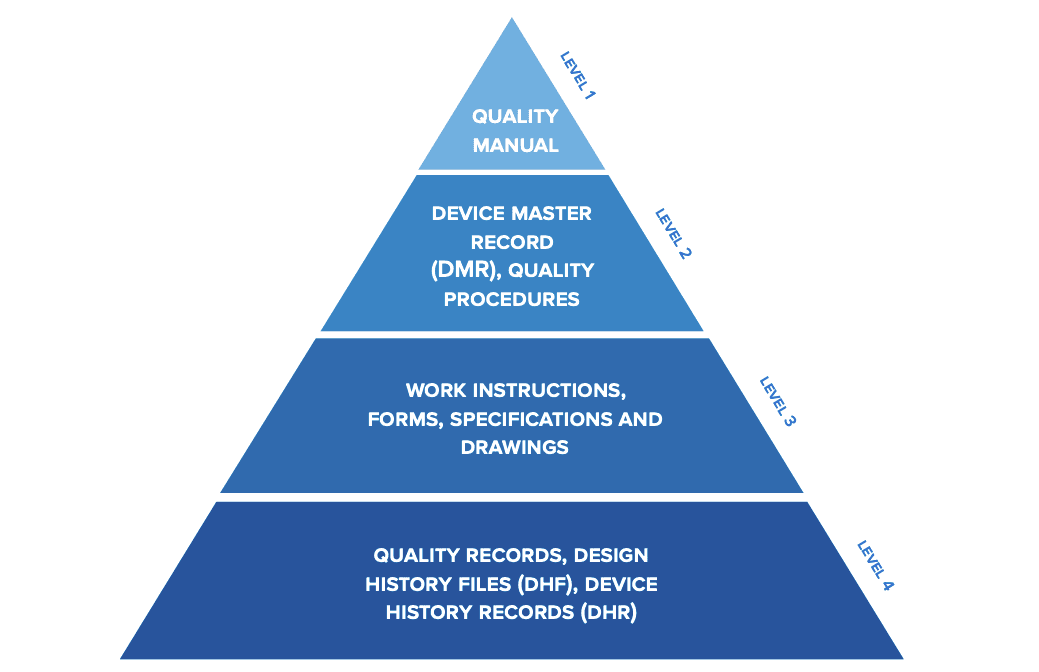
Exemple de hiérarchie SMQ.
Les dossiers qualité sont des documents qui montrent que le SMQ est exécuté et suivi. Ils décrivent également dans quelle mesure votre entreprise répond aux réglementations relatives aux dispositifs médicaux. La FDA définit ces règles dans le document 21 CFR, partie 820. Si vous envisagez de commercialiser vos produits aux États-Unis, ces réglementations sont obligatoires.
En dehors des États-Unis, l'Europe exige la mise en place d'un système de qualité pour répondre aux réglementations sur les dispositifs médicaux (et/ou les réglementations IVD). De nombreuses entreprises de dispositifs médicaux mettent en œuvre un système de qualité certifié ISO 13485:2016 pour répondre aux besoins de l'UE.
Pour en savoir plus sur les exigences réglementaires spécifiques, téléchargez notre livre blanc complet, co-rédigé par le partenaire de Formlabs Greenlight Guru, qui comprend toute une série de ressources destinées à aider les utilisateurs à chaque étape du processus.
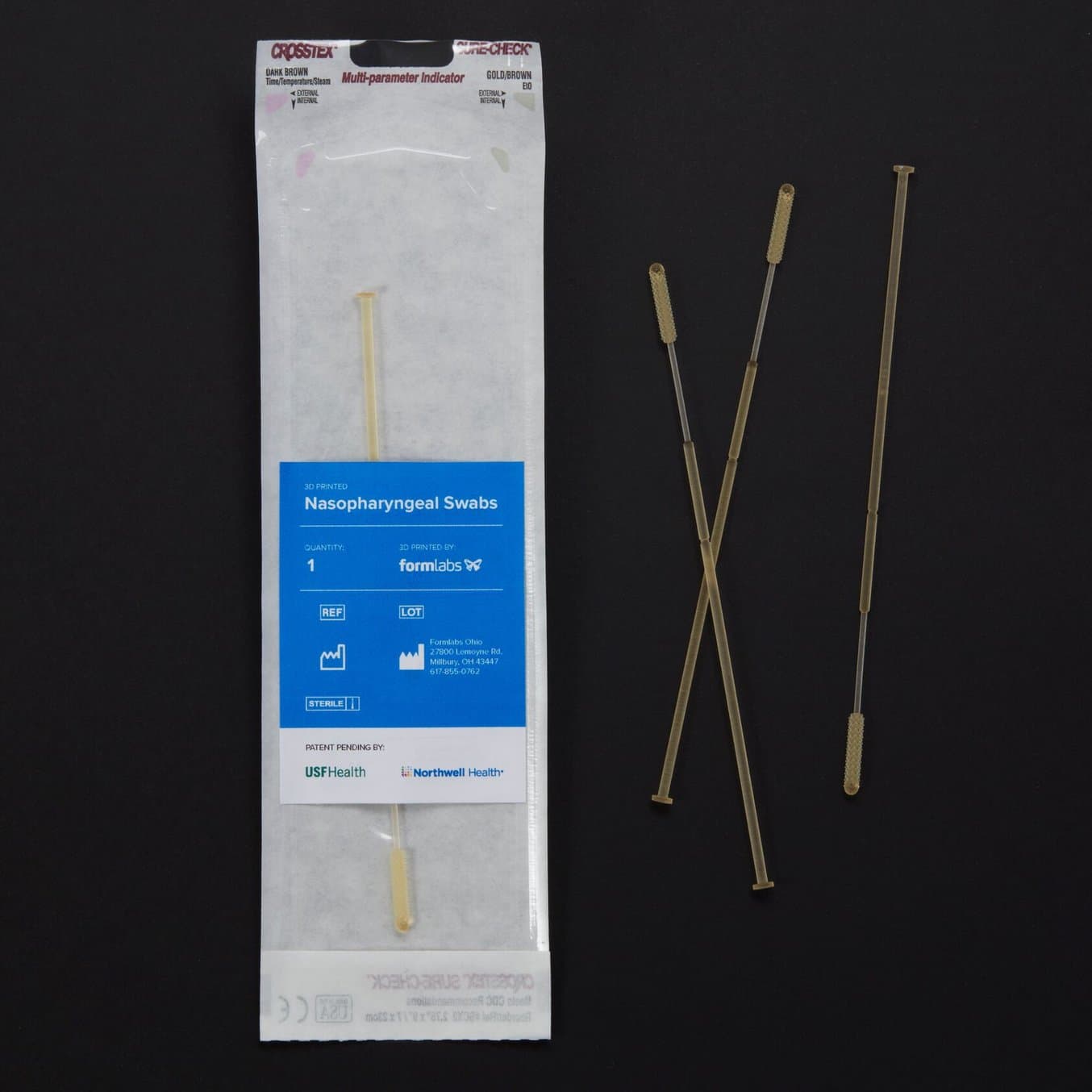
Le guide ultime de l'assurance qualité et des affaires réglementaires dans l'impression 3D médicale
Ce livre blanc vise à guider les utilisateurs de l'industrie des dispositifs médicaux à travers chaque étape du processus de développement de produits, de l'évaluation des méthodes de fabrication et des technologies d'impression 3D aux exigences réglementaires spécifiques pour la commercialisation et le marketing des dispositifs médicaux à usage final imprimés en 3D.
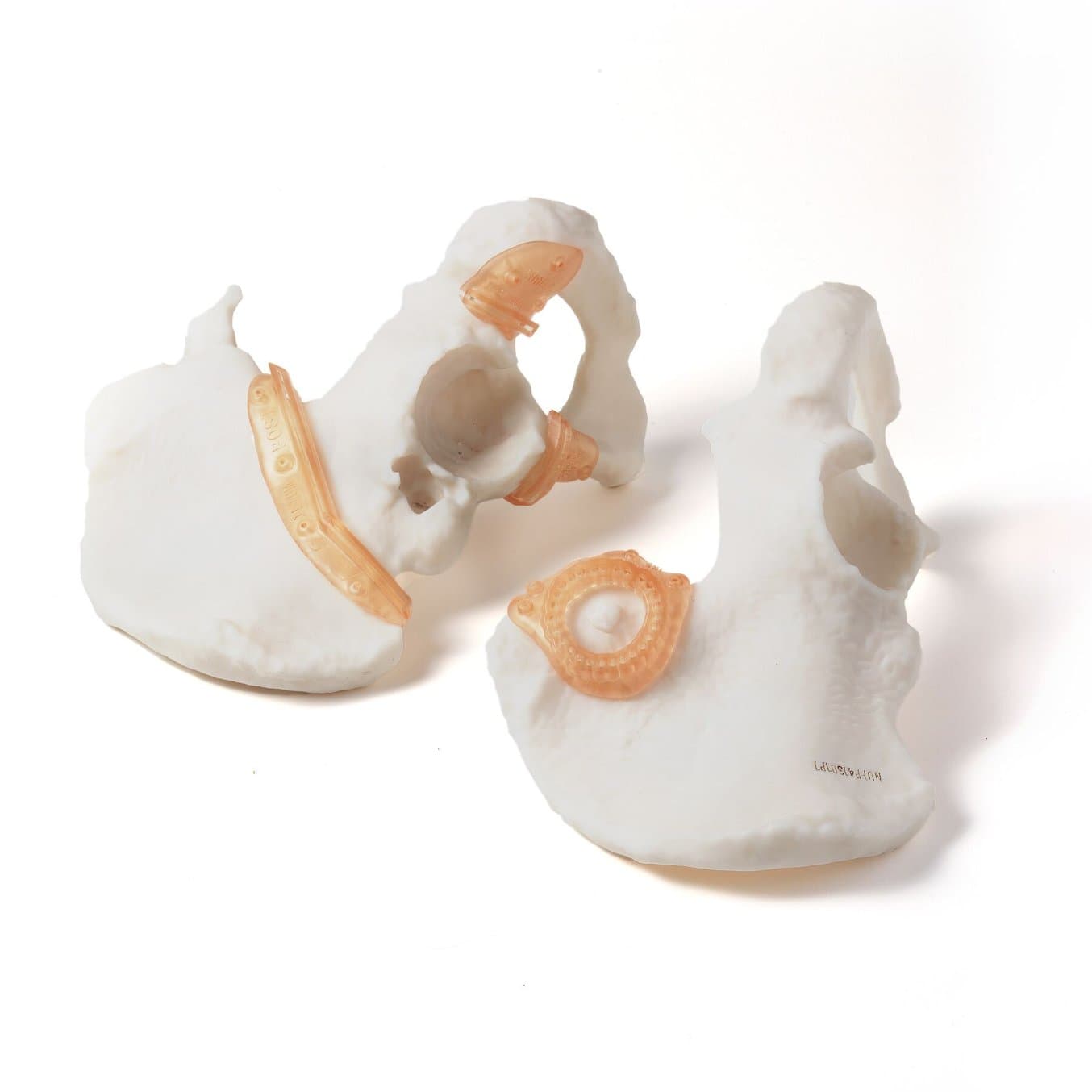
Biocompatibilité, matériaux et stratégies pour la fabrication additive médicale
Dans ce webinaire, des représentants de la FDA et du secteur médical discutent des derniers développements et répondent à des questions intéressantes:
Lancez-vous dans l'impression 3D de dispositifs médicaux
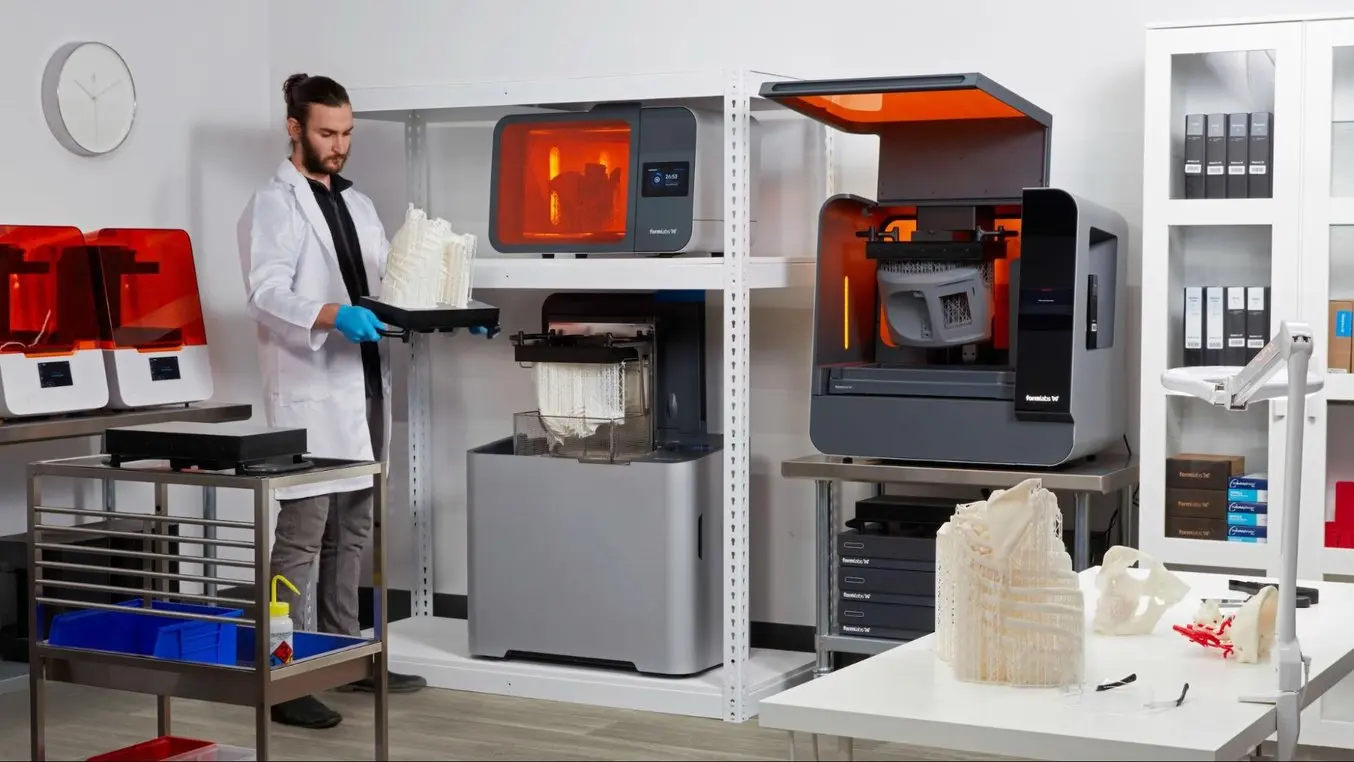
L'impression 3D en interne permet aux entreprises de dispositifs médicaux de raccourcir les cycles d'itération rapides, ce qui accélère le cycle de développement du produit et donne plus de temps pour trouver des solutions créatives.
Chaque établissement médical doit avoir accès aux outils les plus modernes pour améliorer les soins proposés et offrir la meilleure expérience possible aux patients. Lancez-vous dès maintenant ou agrandissez votre capacité de production en interne avec Formlabs, un partenaire dont les produits d'impression 3D médicale de pointe ont fait leurs preuves.
Contactez nos experts médicaux pour en savoir plus sur la façon dont l'impression 3D en interne peut s'intégrer à votre flux de travail pour concevoir et fabriquer des dispositifs médicaux.