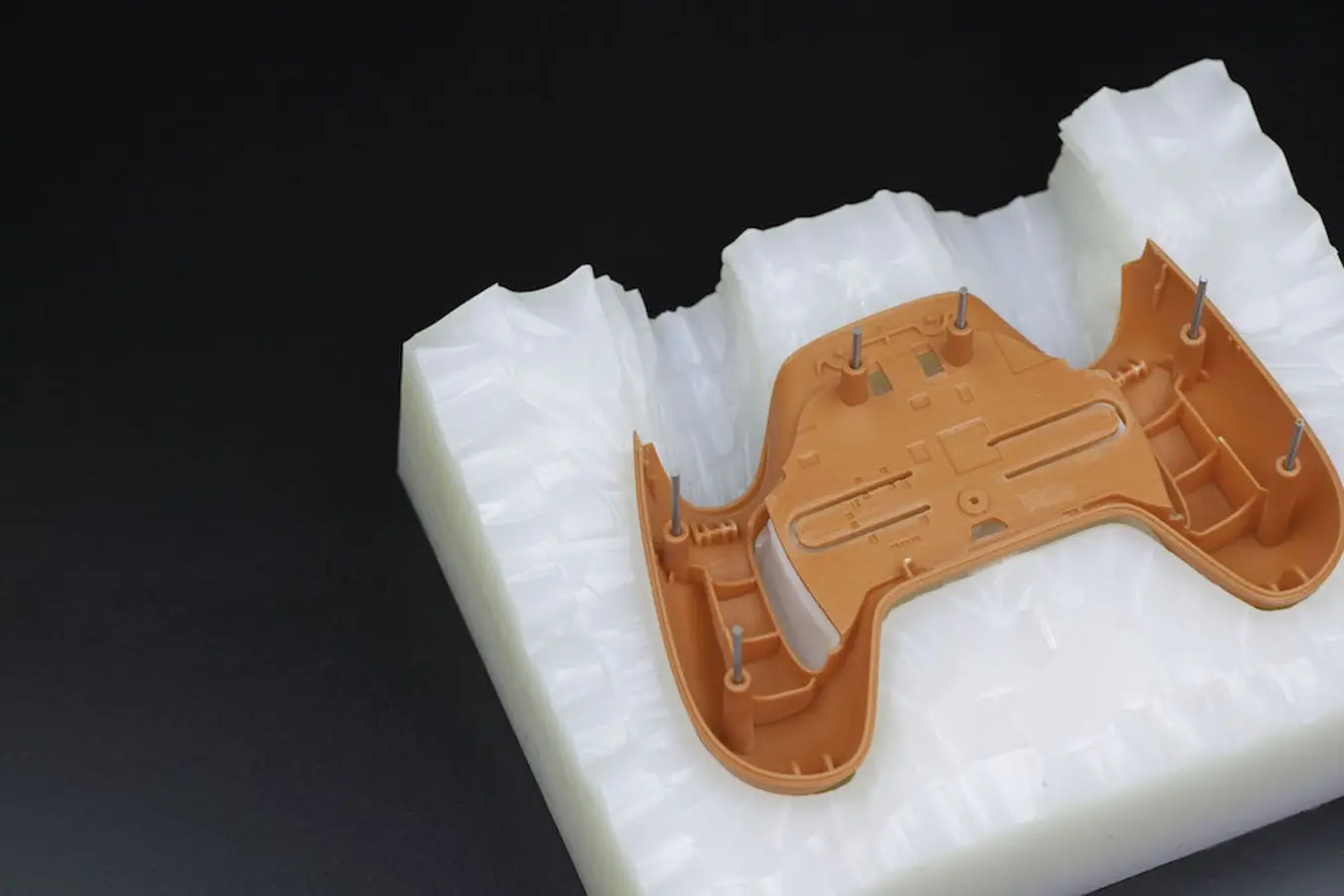
Un prototype produit par moulage d’uréthane. Source : Fictiv
La coulée sous vide est une méthode de fabrication courante pour la production en petits lots de prototypes à tester sur un marché, de produits personnalisés, de dispositifs médicaux sur mesure, etc.
Ce guide explorera les spécificités du processus de coulée sous vide, le comparera à d’autres techniques de production, présentera les meilleurs équipements de moulage d’uréthane et expliquera comment produire des modèles imprimés en 3D pour la coulée sous vide.
Qu’est-ce que la coulée sous vide (ou moulage d’uréthane) ?
La coulée sous vide désigne un processus de fabrication similaire au moulage par injection. De la résine d’uréthane est moulée dans la cavité entre les deux moitiés d’un moule en silicone.
Ce processus reproduit un modèle maître en versant un moule en silicone autour de celui-ci. Au cours d’une procédure hautement spécialisée, le moule est divisé en deux moitiés, le modèle maître est retiré, puis un système de passage et de ventilation est ajouté. Par la suite, le fabricant du modèle moule de la résine à base d’uréthane dans la cavité obtenue, puis la polymérise sous vide pour empêcher l’apparition de bulles d’air.
Le résultat : une reproduction très précise de l’objet original.
Remarque : la coulée sous vide est plus connue sous le nom de moulage d’uréthane ou moulage de polyuréthane aux États-Unis. Cet article utilise ces termes de façon interchangeable.
Les applications de la coulée sous vide
La coulée sous vide est un processus de fabrication idéal pour créer de petits lots d’articles dont la qualité doit s’approcher des normes de production.
Ce processus crée des modèles très détaillés qui sont virtuellement identiques au produit final. Les modèles moulés en uréthane constituent donc une option de choix pour les présentations aux investisseurs, les salons et les photographies commerciales. Un moule en silicone pouvant produire environ 50 moulages, la coulée sous vide permet également aux entreprises de lancer une première série de leur produit à tester rapidement sur le marché.
Si le projet requiert une quantité plus importante, les clients disposent de plusieurs options :
-
Le même modèle maître peut être réutilisé pour créer de multiples moules en silicone.
-
Plusieurs modèles maîtres peuvent être utilisés pour créer un moule composé de plusieurs cavités.
-
À la place du silicone à vulcanisation à température ambiante (RTV), les fabricants de moules peuvent utiliser du caoutchouc ou du silicone à vulcanisation à température élevée (HTV). Les moules ainsi produits sont plus durables et leur durée de vie est allongée jusqu’à 300 à 500 moulages par moule.
Étant donné que le délai de production entre la fabrication du modèle maître et la réception des produits moulés dure environ 10 jours, la coulée sous vide n’est pas seulement utile pour la création rapide de prototypes. Elle sert aussi pour la production de transition, sans exiger un investissement d’entrée conséquent, comme c’est le cas pour des procédés de fabrication de niveau industriel, tels que le moulage par injection, le thermoformage et le moulage par centrifugation.
Comme la coulée sous vide crée des modèles extrêmement détaillés à la finition de surface parfaite et dans une vaste gamme de matériaux aux propriétés mécaniques diverses, elle est applicable à des produits finis conçus en petites quantités, par exemple :
-
Les dispositifs médicaux sur mesure, tels que les prothèses, les orthèses, les appareils auditifs
-
Les pièces automobiles : panneaux du tableau de bord, boutons, jauges, emblèmes, ornements de capot, objectifs des phares, collecteurs d’entrée
-
L’électronique grand public : clôtures, télécommandes, panneaux d’interface utilisateur, intégration de capteur
-
Les composants critiques et les pièces de rechanges pour le secteur industriel et robotique
-
Les biens de consommation : lunettes de soleil en édition limitée, stylos, étuis de téléphone
-
Les instruments de musique
-
Les instruments scientifiques
-
Les compléments d’équipements sportifs
-
L’art, les figurines, les modèles à l’échelle et les accessoires
La coulée sous vide est également une solution couramment utilisée pour copier des objets existants sans avoir à recourir à un flux complexe de rétroconception. Il s’agit fréquemment d’objets rares ou qui ne sont plus disponibles, tels que des sculptures, des fossiles, des reliques historiques, des antiquités, des objets de collection et des maquettes, pour lesquels aucun modèle de CAO ni aucune autre forme de plan n’est disponible.
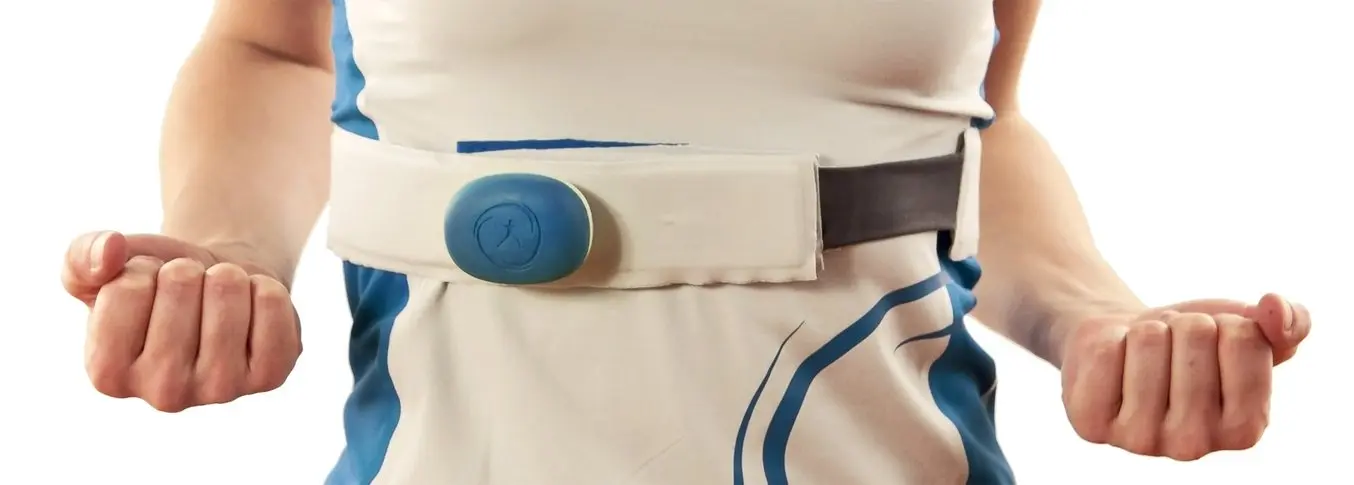
Étui pour un capteur de respiration portable, fabriqué avec un surmoulage de silicone par coulée sous vide. Source : conception de produit IDZone. Moulage : Venture Rapid Technologies.
Le moulage d’uréthane et ses alternatives
Le moulage d’uréthane et le moulage par injection
Les concepteurs de produits et les ingénieurs ont souvent recours à l’impression 3D pour valider les conceptions et passent immédiatement au moulage par injection pour la validation de la production. Cependant, le problème est que le coût d’un moule par injection, fabriqué à partir d’acier de haute qualité à usinage CNC et pouvant être utilisé pour des millions de pièces, peut être compris entre 5000 et 100 000 €, suivant la taille et la complexité de la pièce.
C’est pourquoi des outils de moins bonne qualité sont souvent utilisés à l’étape intermédiaire pour l’outillage dur. Un moule en aluminium peut garantir jusqu’à 1000 à 5000 cycles de moulage à un prix bien moindre. Dans la mesure où les processus d’outillage souple sont plus rapides et permettent une conception simplifiée du moule, ils divisent le délai de production par deux environ par rapport au moulage par injection.
Un moule en acrylique ou un moulage par injection de faible volume avec des moules imprimés en 3D peuvent constituer une alternative, en fonction des quantités et de la qualité requise pour les pièces. Un moule imprimé en 3D créé avec une imprimante SLA de Formlabs coûte habituellement moins de 100 € et permet de créer plus de 100 pièces sans perte significative de qualité.
Toutefois, les développeurs de produits ignorent régulièrement le fait que la coulée sous vide représente souvent une approche plus intelligente de la transition entre les prototypes et la production. Parmi toutes les méthodes de prototypage utilisées à un stade précoce, le processus de moulage de la résine se rapproche le plus du moulage par injection. En outre, ce procédé est très rentable : les moules coûtent entre 200 et 1000 € et le prix typique à l’unité est compris entre 10 et 100 €.
Un moule en silicone pour le moulage d’uréthane est fabriqué d’une façon similaire à un moulage par injection. Il comporte deux moitiés, l’une formant le centre et l’autre la cavité, et le matériau liquéfié est injecté entre les moitiés pour former le produit final. Il existe cependant plusieurs différences :
-
Lors du moulage par injection, un polymère fondu est introduit dans la cavité du moule à l’aide d’une trémie et d’une vis sans fin, alors que la pression et la température sont élevées. La coulée sous vide opère à des températures basses. À la place du plastique fondu, elle utilise des résines liquides qui sont aspirées dans le moule sous vide, ce qui rappelle l’action capillaire dans la tige d’une plante. Ainsi, bien qu’il existe de nombreuses résines différentes capables d’imiter divers polymères, le prototypage dans le matériau final du moulage par injection n’est pas possible.
-
Après la cuisson dans un four, les pièces font encore l’object d’une post-polymérisation pendant une durée allant jusqu’à une semaine et demeurent vulnérables aux radiations UV et aux températures élevées.
-
Le moule étant flexible, les dimensions et la forme de la pièce sont limitées. Néanmoins, des techniques spécifiques peuvent permettre des exceptions. Par exemple, le moulage par phase utilisant des supports en métal peut contrer la gravité pour le moulage de pièces allongées dans un moule composé de trois ou quatre pièces.
-
La coulée sous vide est plus adaptée aux parois de diverses épaisseurs que le moulage par injection, car il n’y a pas de cycle de chauffage et de refroidissement du matériau moulé. La distorsion des pièces est donc moindre.
-
Un moule en silicone permet de produire un nombre important de contre-dépouilles lors de la conception de la pièce. Cependant, lors des tests pour le moulage par injection, il est recommandé de s’en tenir autant que possible au modèle moulé par injection et de construire les angles de dépouille requis pour le produit fini.
-
La coulée sous vide ne produit quasiment aucun déchet, tandis que le moulage par injection gaspille jusqu’à 20 % du polymère utilisé en raison des taux de rebut, des résidus et de la surproduction.
La haute fidélité entre un modèle coulé sous vide et un produit final sorti d’un moule par injection permet aux ingénieurs d’optimiser la conception en vue de la fabrication. Elle leur fournit un aperçu du produit de haute qualité, sans avoir à imposer aux dirigeants les coûts fixes astronomiques qui peuvent accompagner la fabrication sous contrat dans une usine de moulage par injection.
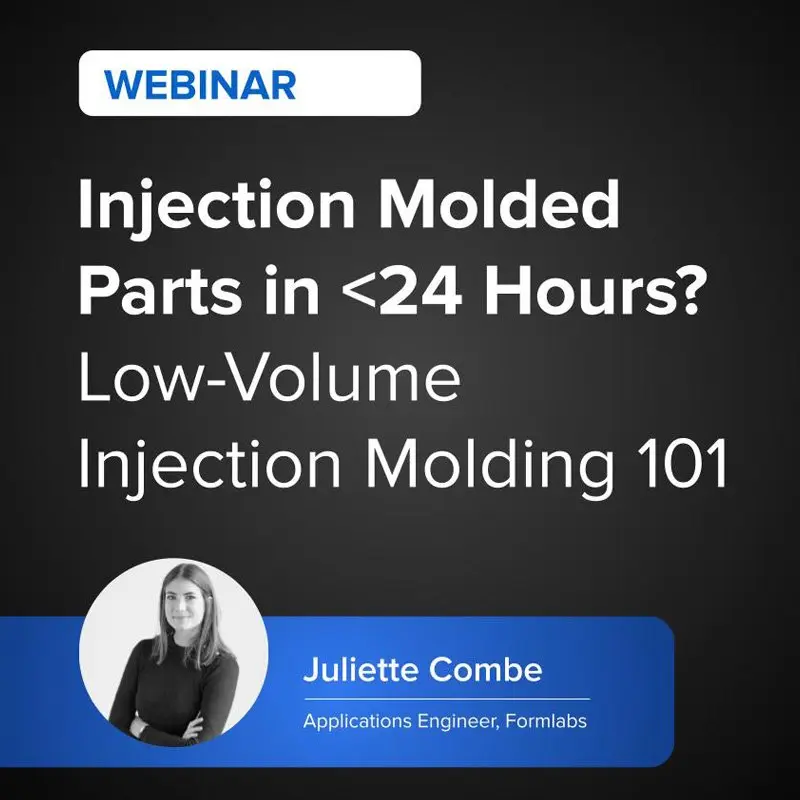
Des pièces moulées par injection en moins de 24 heures ? Le b.a.-ba du moulage par injection en petite série
Dans ce webinaire, nous vous montrerons comment des moules imprimés en 3D par stéréolithographie (SLA) peuvent être utilisés dans le processus de moulage par injection afin de réduire les coûts et les délais de fabrication et de lancer des produits plus qualitatifs sur le marché.
La coulée sous vide et l’impression 3D
It is a common misunderstanding that 3D printing is restricted to one-offs only. On the contrary, it is a viable method for low volume manufacturing of end-use parts. It is also increasingly popular for companies to invest in an in-house print farm. Such an array of 3D printers can handle low-volume batches of hundreds or even thousands of products.
The main factor influencing a choice between 3D printing and vacuum casting is product geometry. Vacuum casting is explicitly intended to simulate injection-molded parts. As a low-investment alternative to full-scale injection molding, it can even combine flexible and rigid materials in an overmold or add metal components directly in the prototype through insert molding. For creating a small series of injection-moldable components, vacuum casting is more cost-effective than 3D printing.
Another advantage of vacuum casting is that bigger parts can be created much faster and cheaper than 3D printing. It allows for mold sizes of roughly 50 cm (20 inches) for the longest dimension, and casting weight up to 1.5kg (3.3 lbs).
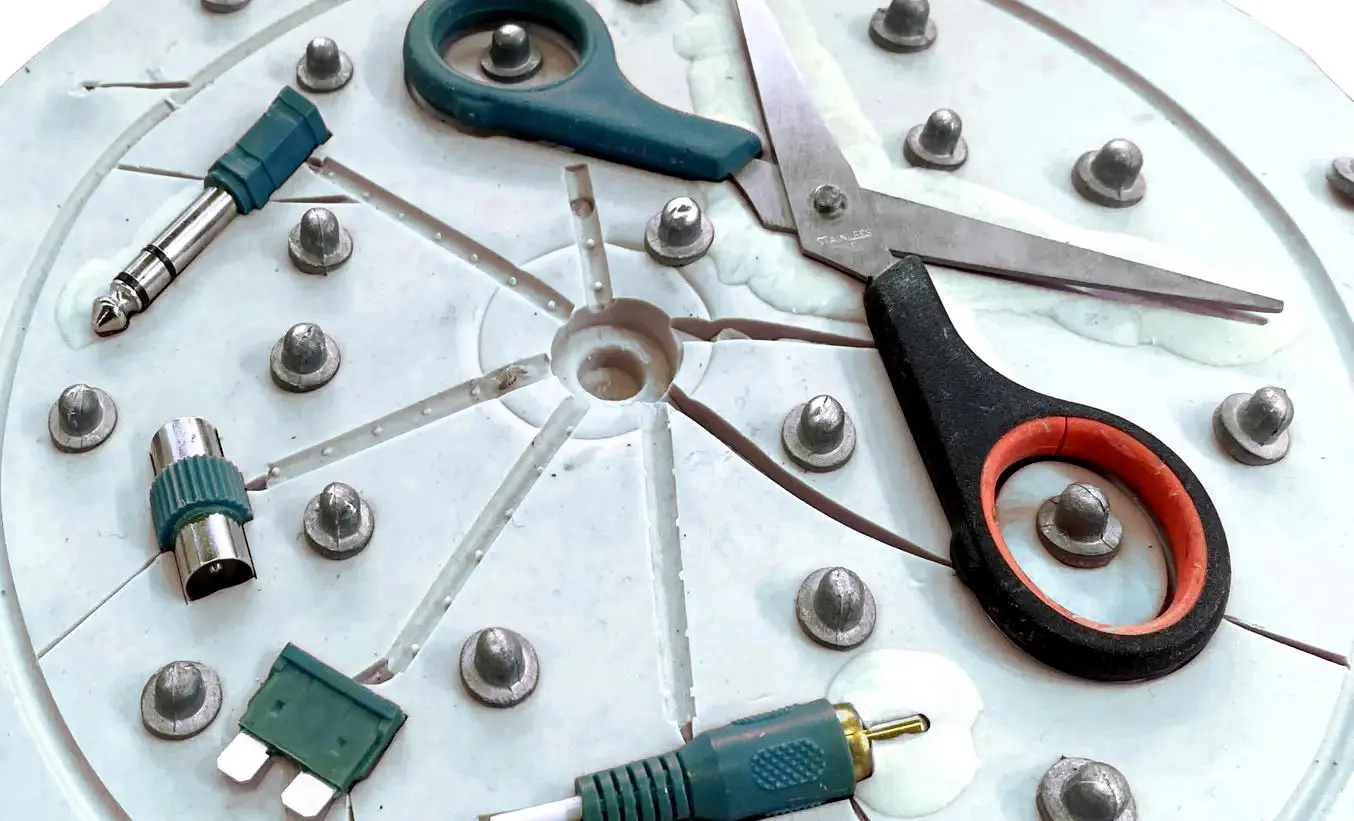
Coulée sous vide dans un moule en silicone avec des inserts en métal.
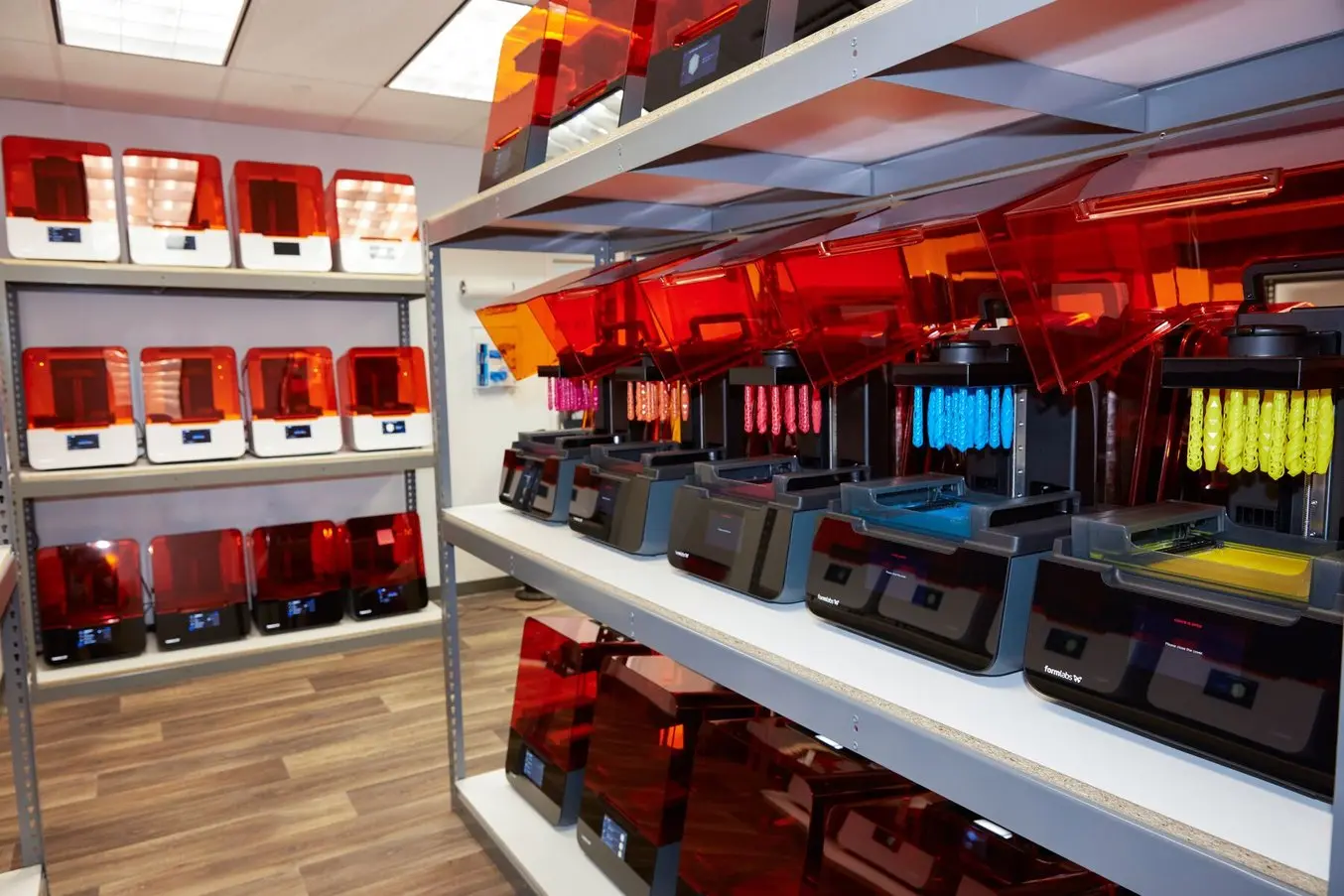
Comment produire de petites séries personnalisée avec des pièces d'utilisation finale imprimées en 3D
Regardez ce webinaire pour découvrir comment fabriquer sur mesure de petites séries de pièces finales rapidement et à moindre coût grâce à l’impression 3D.
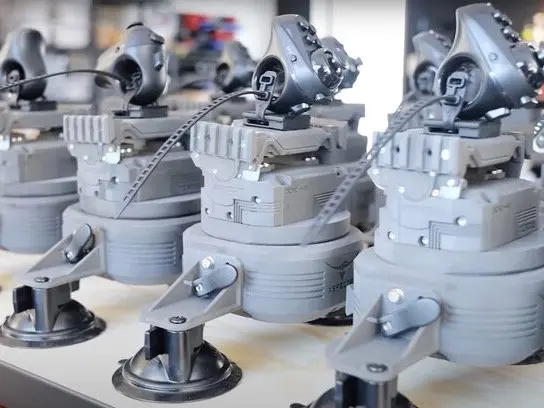
Test de résistance de pièces imprimées en 3D pour les applications finales
Ce livre blanc présente le matériel d’impression 3D de Formlabs et les solutions de matériau pour la production de pièces finales, y compris les études de cas et les résultats des tests de contraintes pour vérifier l’adéquation des matériaux d’impression 3D aux applications finales.
Comparaison : la coulée sous vide et les méthodes de production alternatives
Examinons les avantages et les inconvénients des différentes techniques de fabrication :
Coulée sous vide | Moulage par injection | Impression 3D | Outillage rapide | Usinage | Fabrication à la main | ||
---|---|---|---|---|---|---|---|
Liberté de conception | ★★★☆☆ | ★★☆☆☆ | ★★★★★ | ★★☆☆☆ | ★★★★☆ | ★★★☆☆ | |
Taille de la pièce | ★★★★☆ | ★★★★☆ | ★★★☆☆ | ★★★☆☆ | ★★★★☆ | ★★★★★ | |
Volume de production | ★★★☆☆ | ★★★★★ | ★★★☆☆ | ★★★★☆ | ★★☆☆☆ | ★☆☆☆☆ | |
Gamme de matériaux | ★★★☆☆ | ★★★★☆ | ★★★★☆ | ★★★★☆ | ★★★★★ | ★★★☆☆ | |
Coût de l’investissement | ★★★☆☆ | ★☆☆☆☆ | ★★★☆☆ | ★★☆☆☆ | ★★★★★ | ★★☆☆☆ | |
Coût par pièce | ★★★★☆ | ★★★★★ | ★★★☆☆ | ★★★★☆ | ★★★☆☆ | ★★★☆☆ | |
Délai de production | ★★★★☆ | ★☆☆☆☆ | ★★★★★ | ★★★☆☆ | ★★★★☆ | ★★☆☆☆ |
Le processus de coulée sous vide
La coulée sous vide est une procédure hautement spécialisée qui se compose de quatre étapes.
1. Conception CAO
Un concepteur ou un ingénieur crée une représentation numérique de l’objet à produire dans un environnement de logiciel CAO, comme Fusion 360 ou SolidWorks. À cette étape, il convient de garder à l’esprit les recommandations suivantes pour la conception par moulage d’uréthane :
-
L’épaisseur des parois doit être comprise entre 1,5 et 4 mm. L’épaisseur minimum absolue est de 1 mm.
-
Les nervures peuvent être plus fines, atteignant 60 % de l’épaisseur de la paroi.
-
Utilisez des rayons généreux supérieurs à 3 mm.
-
Évitez les parois à 90 degrés pour améliorer la solidité de la pièce.
-
Intégrez un sillon de 0,5 mm entre deux coques qui s’emboîtent pour améliorer l’aspect du produit.
-
L’épaisseur de paroi du bossage des vis doit être égale au diamètre du trou.
-
La profondeur idéale pour la gravure de lettres est de 0,25 mm.
Lorsqu’il est terminé, le modèle CAO est exporté au format STL pour la production.
2. Réalisation du modèle maître
Le modèle maître est le modèle positif à partir duquel les copies seront créées par moulage. Dans la mesure où un moule pour coulée sous vide en silicone permet d’obtenir des copies exactes du modèle maître, il est essentiel que le modèle imprimé en 3D représente précisément le modèle CAO original, en particulier en ce qui concerne la qualité de surface ultra-lisse. D’autres caractéristiques secondaires d’un bon modèle maître sont la solidité, la résistance chimique et thermique, ainsi que la durabilité pour empêcher la dégradation au fil du temps.
Si les modèles maîtres fraisés par commande numérique par ordinateur étaient auparavant la norme, leur production est coûteuse et chronophage. Ils comportent également des limitations par rapport aux trous, aux canaux, aux rayons internes et aux surfaces organiques. Alternative de pointe, l’impression 3D est actuellement la méthode préférée pour la production de modèles maîtres.
De multiples types d’imprimantes 3D sont disponibles, à la fois pour les clients particuliers et professionnels, mais les impressions 3D SLA et SLS constituent les processus les plus couramment utilisés pour le moulage d’uréthane.
L’impression 3D SLA produit des pièces dont la surface de finition est la plus lisse, ce qui est idéal pour les modèles de coulée sous vide. Bien que les impressions SLA soient déjà lisses lorsque les paramètres d’impression adéquats sont utilisés, elles requièrent toutefois un sablage et un polissage pour le retrait des supports et l’obtention d’une finition impeccable. Certains matériaux avancés, tels que Rigid 10K Resin, offrent également des propriétés mécaniques, une thermorésistance et une durabilité supérieures.
L’impression 3D SLS avec du nylon produit des impressions solides, thermorésistantes et précises. Dans la mesure où cette technique ne requiert pas de supports, elle est également idéale pour des caractéristiques avancées, telles que des parois fines, des détails gravés, des assemblages par encliquetage, des charnières et des pièces qui s’emboîtent ou s’engrangent. La finition de surface des pièces imprimées est un peu trop irrégulière pour imprimer des modèles maîtres pour coulée sous vide. Les pièces imprimées en 3D SLS peuvent donc bénéficier d’un sablage ou d’un polissage par vibration pour atténuer l’irrégularité de surface.
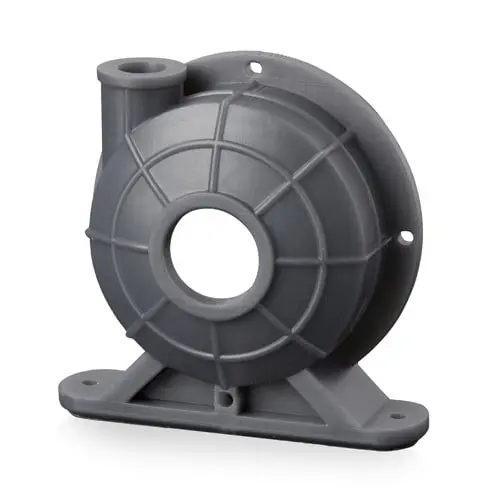
Commander un échantillon gratuit
Examinez et constatez par vous-même la qualité Formlabs. Nous enverrons un échantillon gratuit à votre bureau.
3. Création du moule
À cette étape du procédé, qui demande le plus de travail, le fabricant du modèle crée un boîtier pour le moule à partir d’une plaque de mélamine et de colle chaude. Il fixe ensuite le modèle maître au fond avec de petites gouttes de superglue. Parfois, des poches sont créées à l’aide d’un outil rotatif où des bords intégrés au modèle maître seront placés pour plus de traction.
Pour que la ligne de jonction entre les deux moitiés du moule soit nette, tous les trous entre le modèle maître et le panneau inférieur doivent être remplis. Des blocs de styrène et de l’argile à modeler Plastalina sont les matériaux les plus utilisés pour cette étape. Des tenons et des barres de repérage sont ensuite ajoutés pour un alignement parfait avec l’autre moitié du moule.
Après avoir été vigoureusement mélangé, le silicone à deux composants est versé et dégazé dans une chambre à vide. Avant cela, le fabricant du modèle remplit tous les petits trous du modèle maître avec un mélange de silicone à l’aide d’une brosse d’acide afin d’empêcher les poches d’air, puis verse le silicone pour former la première moitié du moule.
Après plusieurs heures de polymérisation, la moitié du moule est retirée du boîtier du moule et retournée. Le fabricant du moule installe avec expertise des évents, des masselottes et un orifice de remplissage en acrylique pour la seconde moitié du processus. Un agent démoulant est vaporisé sur le dessus du silicone et déposé dans les zones creuses avec une brosse. Ensuite, un nouveau boîtier de moule est conçu pour verser la seconde moitié du moule de la même manière.
Pour préparer le moule pour la coulée sous vide, il faut le sortir du boîtier de moule et déposer une couche régulière d’agent démoulant d’uréthane E236. Les moitiés du moule sont combinées pour former un seul bloc, puis les tenons et les clés de repérage sont insérés pour l’alignement.
4. Coulée sous vide d’uréthane
Lors de cette étape, le modèle maître original est reproduit par moulage dans une chambre à vide. Le moule est d’abord fixé à une planche en bois et des tubes de ventilation, ainsi qu’en entonnoir de versement, y sont ajoutés.
La résine à deux composants est mesurée et mélangée avec un agent colorant pour la pigmentation. Ensuite, le matériau de moulage est dégazé dans une chambre à vide pendant quelques minutes.
Le mélange de polyuréthane est ensuite prêt à être versé. Les tubes de la masselotte indiquent quand la cavité est complètement remplie. Après polymérisation à 70 °C, le moule est ouvert pour révéler une copie du modèle original, qui conserve tous les détails et les textures des surfaces.
La finalisation consiste à rogner les bords lorsque le matériau a bavé, effectuer un cycle de polissage supplémentaire avec du papier de verre de grain 1000 et une polymérisation au four pour améliorer les propriétés matérielles de la pièce.
Conseils d’experts
La procédure décrite ci-dessus s’applique principalement aux prototypes à paroi fine, tels que les étuis pour appareils électroniques, les récipients de stockage et d’autres cas où il est souhaitable d’éviter une ligne de jonction visible sur la surface du produit.
Pour d’autres articles où cet aspect est moins critique, il suffit d’encapsuler le modèle maître dans un bloc de silicone et de couper manuellement pour l’ouvrir. La découpe suit une onde sinusoïdale, ce qui requiert une certaine expérience et de la dextérité.
Voici certaines des meilleures pratiques à appliquer pour améliorer les résultats lors du moulage d’uréthane :
-
Faites attention lorsque vous vaporisez un agent de démoulage directement sur le modèle, car il peut donner à la surface une légère texture qui sera visible lors du moulage.
-
Préchauffez les résines à 40 °C, de préférence un jour avant l’utilisation et retourner périodiquement la bouteille pour éviter la cristallisation.
-
Empêchez que l’humidité n’entre dans les bouteilles de résine : c’est un agent bloquant pour le polyuréthane. Une façon d’y parvenir est de remplir les bouteilles avec du gaz d’argon immédiatement après usage.
-
Lors du mélange de produits chimiques à deux composants, utilisez toujours la méthode de mélange à double cavités. Verser le produit du premier récipient directement est une façon certaine de créer des lignes non mélangées et de détériorer le moulage.
-
Utilisez de l’alcool à friction pour détacher la colle chaude lorsque vous désassemblez le boîtier du moule pour une utilisation postérieure.
-
Installez un orifice de remplissage dans un coin du produit qui fournit la distance moyenne la plus courte avec différentes sections de la pièce. Cela garantit que toutes les zones soient remplies.
-
Pour empêcher la formation de bulles d’aires, versez depuis un seul point autour des zones délicates et détaillées, jamais directement au-dessus de ces zones.
-
Placez le passage en bas et l’évent en haut.
-
Ajoutez des poudres métalliques pour une finition d’une brillance spectaculaire ou pensez à utiliser du polypyrrole ou de la poudre de graphite pour la conductivité électrique.
-
Lorsque vous mélangez de l’uréthane, laissez de l’espace au-dessus de la surface, car le mélange liquide moussera et montera dans la chambre à vide, comme un marshmallow au micro-ondes.
-
Utilisez une machine de coulée sous vide professionnelle pour accélérer le processus et obtenir des résultats plus fiables.
Les machines de coulée sous vide
Due to the complexity of the process, most companies subcontract jobs to third-party urethane casting service providers.
For those planning to do vacuum casting in house, a professional vacuum casting machine provides an integral solution for taking prototyping efforts to the next level and speeding up the process towards production ramp-up. As much as fifty castings can be achieved within two days, each in a different material and color if needed.
A vacuum resin casting machine is a refrigerator-sized contraption that automates the process from mixing to casting to curing. It lets operators control parameters such as chamber pressurization, mixer speed, heated cup, and oven heat. The latest systems are programmable so that operators can create custom sequences to optimize casting cycles for specific materials and product types.
Vacuum casting machines come in different sizes to allow for different mold sizes. Most models can, next to working with resin, also be set up for casting injection-grade nylon, ceramics, wax, and even low-melt metal alloys.
Urethane casting machines are ideal for pre-production runs because they pull a vacuum much quicker and minimize manual labor. The downside is that they cost tens of thousands of dollars. Jewelry vacuum casting machines are much smaller and generally cost a few thousand dollars.
Here are some of the best vacuum casting machines:
-
Renishaw 5/01 PLC: Max. mold size 530 x 450 x 420 mm, price roughly $45k. The larger 5/04 model allows molds up to 750 x 750 x 900 mm and more materials, like glass-fiber reinforced nylon and wax, but it comes at nearly double the price.
-
SLM VCM 04: Max. mold size 750 x 750 x 900 mm, casting volume 2.2L, and includes casting with nylon and wax.
-
MCP 5/01: Max. part size 400 x 400 x 400 mm. MCP offers many larger models, including the MCP 003 with 560 x 600 x 600 mm part size, the 4/04 with 900 x 750 x 600 mm part size, and the 4/05 with 1300 x 750 x 800 mm part size. These machines are fully programmable and allow vario-pressure casting with wax, silicone, and nylon, next to PU resins. They can also be used with 3D printed injection molds.
-
Scott AM 1000: Max. mold size 500 x 450 x 425 mm, 1 kg casting weight. The 4000 model has a max. mold size of 750 x 750 x 900 mm and 5 kg casting weight. Besides resins, these apparatuses can be used for vacuum investment casting with ceramics and metals.
-
Multistation CSV 340: Max. mold size 340 x 340 x 435 mm, casting volume 600 mL. The CSV500 model fits molds up to 500 x 500 x 635 mm and casting volumes up to 1 liter.
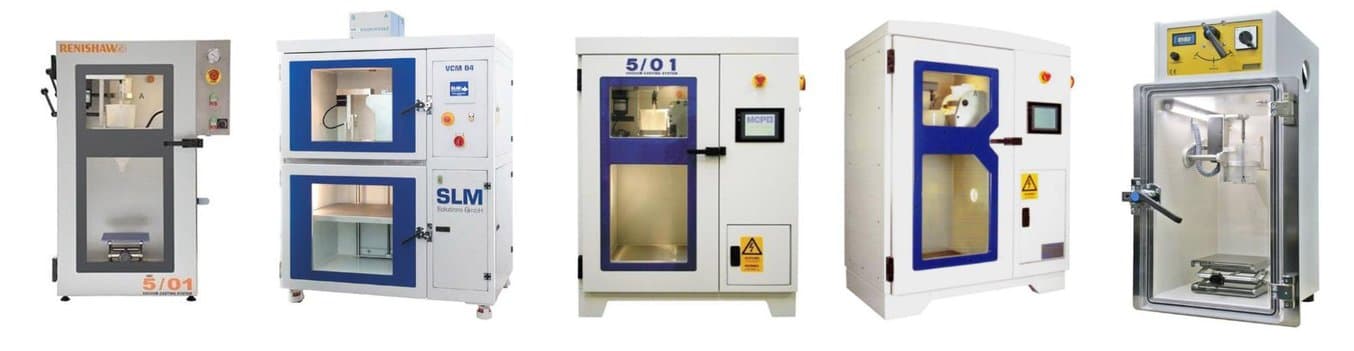
Une série de machines de coulée sous vide par Renishaw, SLM, MCP, Scott AM et Multistation.
Les machines de coulée sous vide et les chambres à pression
Si vous cherchez une alternative à petit budget, il est parfaitement possible de concevoir votre proche machine de coulée sous vide. Dans la mesure où une seule bulle d’air à l’intérieur du moule peut détériorer un moulage entier, le dégazage représente un défi crucial dans le processus de moulage de résine.
Pour retirer toutes les bulles du mélange, deux armes de choix sont à votre disposition lorsque vous construisez une machine de coulée sous vide vous-même : une chambre à vide ou un pot à pression.
Une chambre à vide est une cuve qui peut être utilisée pour retirer l’air du caoutchouc en silicone avant de créer le moule. Dans la mesure où l’approche centrée sur le vide est plus lente que celle utilisant une pression élevée, une chambre à vide ne fonctionne qu’avec des résines à prise lente dont la durée de polymérisation est de vingt minutes ou plus.
Une chambre à vide comporte deux leviers : un pour l’entrée d’air et l’autre pour la pompe à vide. Elle est accompagnée d’une jauge pour voir si le vide a été créé et un couvercle en acrylique transparent pour vérifier la dégazéification. Bien que plus cher, un couvercle en verre tempéré est un investissement rentable, car il ne se fissurera pas au fil du temps, contrairement à un couvercle en plastique.
Les pots à pression coûtent un peu plus cher, car ils requièrent un compresseur d’air. Cependant, ils constituent indubitablement le meilleur moyen de créer des moulages et des mélanges de résine sans bulles. Contrairement aux chambres à vide, ils peuvent être utilisés avec le moule, ils sont adaptés aux résines à prise rapide qui offrent une fenêtre de travail limitée et les moulages obtenus sont parfaitement exempts de bulles d’air.
Une chambre à vide a l’avantage d’être utile pour de nombreuses applications, par exemple retirer l’air du plâtre, du béton ou des infusions de bois, tandis qu’un pot à pression ne sera généralement utilisé que pour dégazer des lots de silicone.
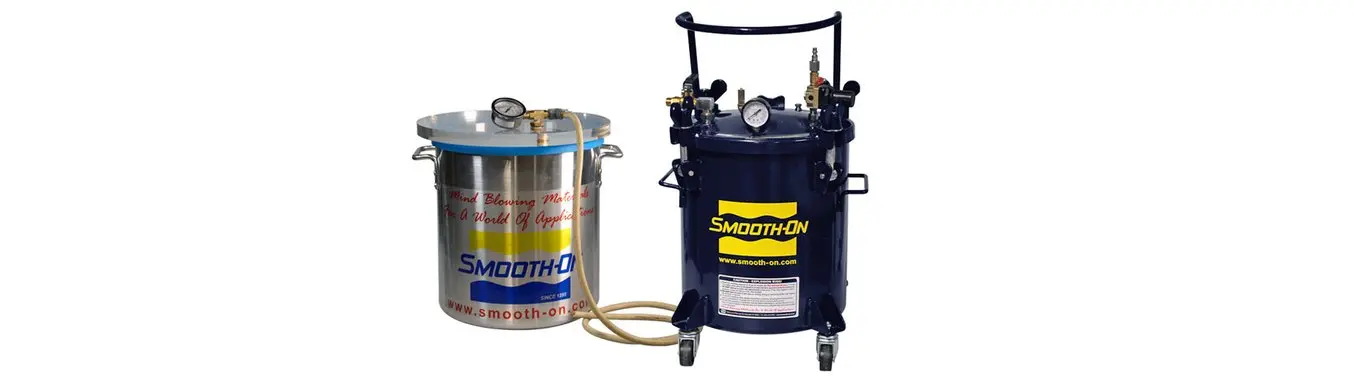
Chambre à vide (gauche) et pot à pression (droite).
Les matériaux de coulée sous vide
Les matériaux de moule en silicone
Les silicones de moulage peuvent être divisés entre les silicones polycondensation et polyaddition. Les silicones polycondensation, aussi appelés tin-cure, subissent un rétrécissement compris en 1 et 4 %. Bien que les fabricants de modèles fassent de leur mieux pour compenser le taux de contraction, il est recommandé de choisir du silicone polyaddition de meilleure qualité ou des caoutchoucs à vulcanisation à température élevée (HTV) pour les applications à haute tolérance.
Une dureté Shore A de 40 à 50 permet de créer un moule durable pouvant être réutilisé des dizaines de fois, tout en facilitant le démoulage, même pour les pièces qui pourraient rester coincées dans un moule rigide en raison de problèmes de retour d’air. L’utilisation d’un silicone translucide est recommandée, car ce matériau permet de voir les poches d’air, les bulles, les contaminants et tout ce qui se trouve à l’intérieur du moule.
SmoothOn, Elastosil, V-Sure et Silicones and More (S.A.M.) sont d’excellentes marques de silicone à deux composants. Commander directement auprès d’usines de produits chimiques à l’étranger peut également réduire le prix, tout en fournissant un produit de qualité professionnelle conforme aux spécifications exactes de l’acheteur, en particulier pour les commandes importantes.
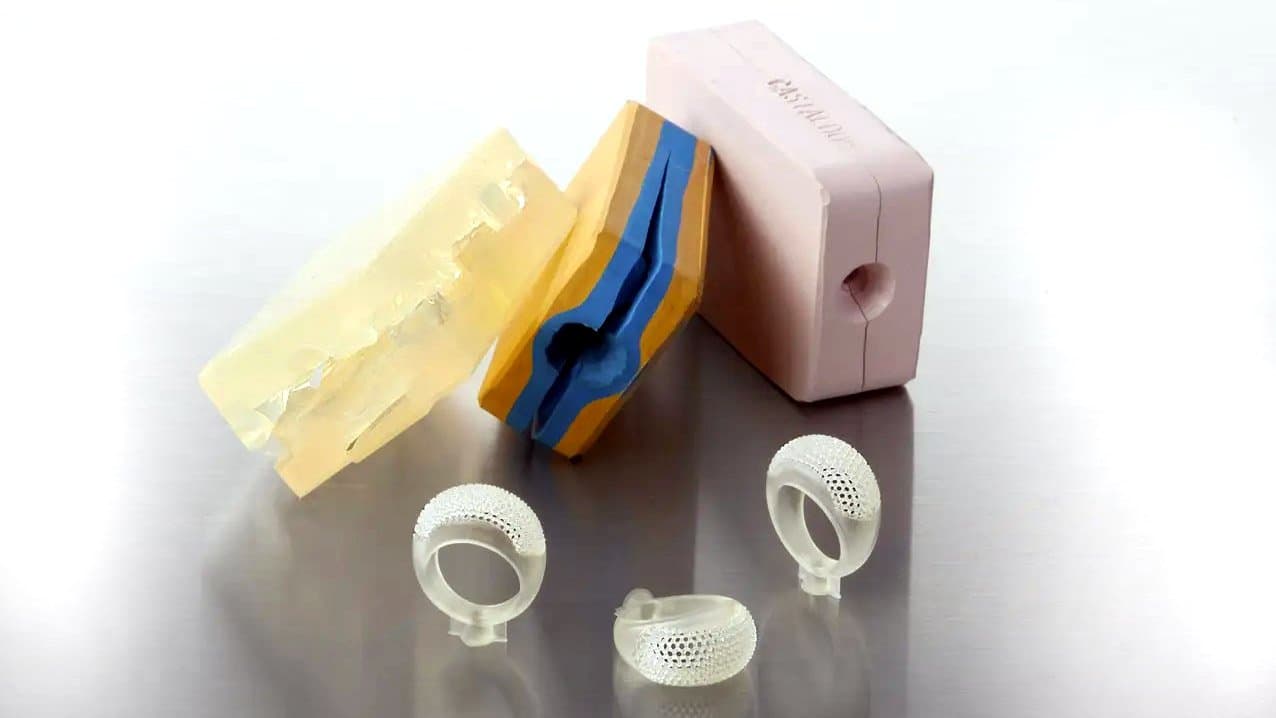
Les moules de joaillerie RTV et HTV sont utilisés pour la production dans le secteur de la joaillerie et peuvent capturer des détails subtils en filigrane.
Les résines en uréthane pour le moulage
Il existe de nombreux matériaux pour la coulée sous vide, dotés de propriétés différentes en termes de flexibilité, d’élasticité, de rigidité et de solidité :
-
Résine standard de type ABS
-
Matériau à charge de verre semblable à du nylon pour une rigidité supérieure
-
Elastomère de type TPE pour des applications comme les objets de technologie portable, les revêtements de poignées, les boutons, les joints et les sceaux
-
De type PC (polycarbonate)
-
Uréthane de moulage translucide ou transparent (semblable à de l’acrylique)
-
Matériaux thermorésistants comme du polyoxyméthylène ou du polyuréthane
On trouve également plusieurs matériaux de moulage d’uréthane exotiques, tels que le verre brisé, la cire, l’époxy, la céramique, les composites, ainsi que des options de qualité alimentaire, conductrices, à basse densité et ignifuges. Smooth-On et SRC Specialty Resin sont des marques connues de résine à prise rapide pour le moulage d’uréthane.
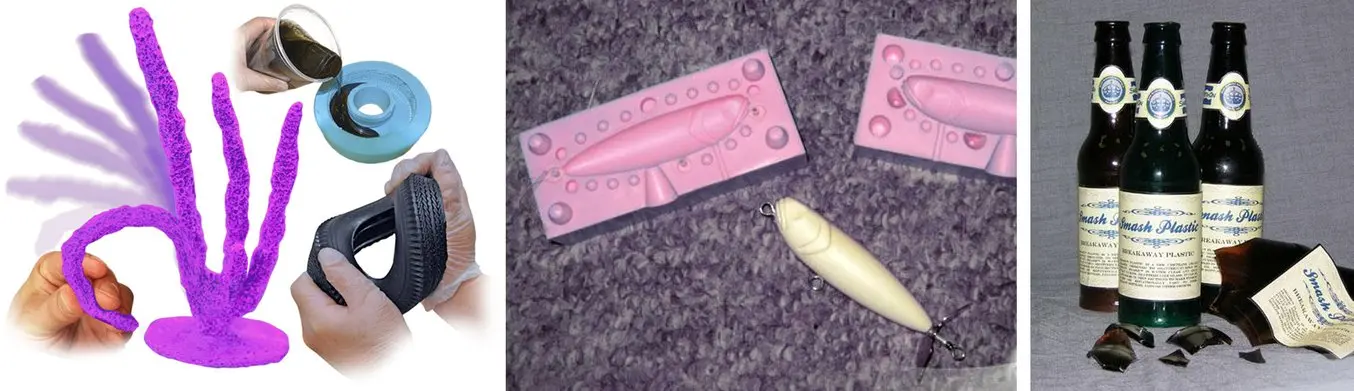
Un assortiment de résines d’uréthane, à l’apparence de caoutchouc, de flotteur ou de verre.
Études de cas : le moulage d’uréthane avec des modèles imprimés en 3D
Calibur Fencing
La coulée sous vide est idéale pour la pré-production de lots permettant de tester et d’affiner le produit final avant d’investir dans de l’outillage de production en série pour le moulage par injection. Calibur Fencing, un objet de technologie portable sans fil qui compte les points en escrime, est un exemple de réussite.
Les concepteurs ont commencé à tester les fonctionnalités de l’appareil sur de simples prototypes, puis sont passés à l’impression FDM pour obtenir des maquettes grossières afin d’identifier la forme appropriée. Enfin, une imprimante SLA Form 3 de Formlabs s’est révélée indispensable pour créer des prototypes de haute qualité représentant le produit fini.
L’équipe a ensuite utilisé les pièces imprimées en 3D SLA comme modèles et les a expédiées à un fournisseur de service de coulée sous vide pour produire et tester en version bêta des unités pour le client et obtenir rapidement un produit final, tout en assurant le contrôle qualité.
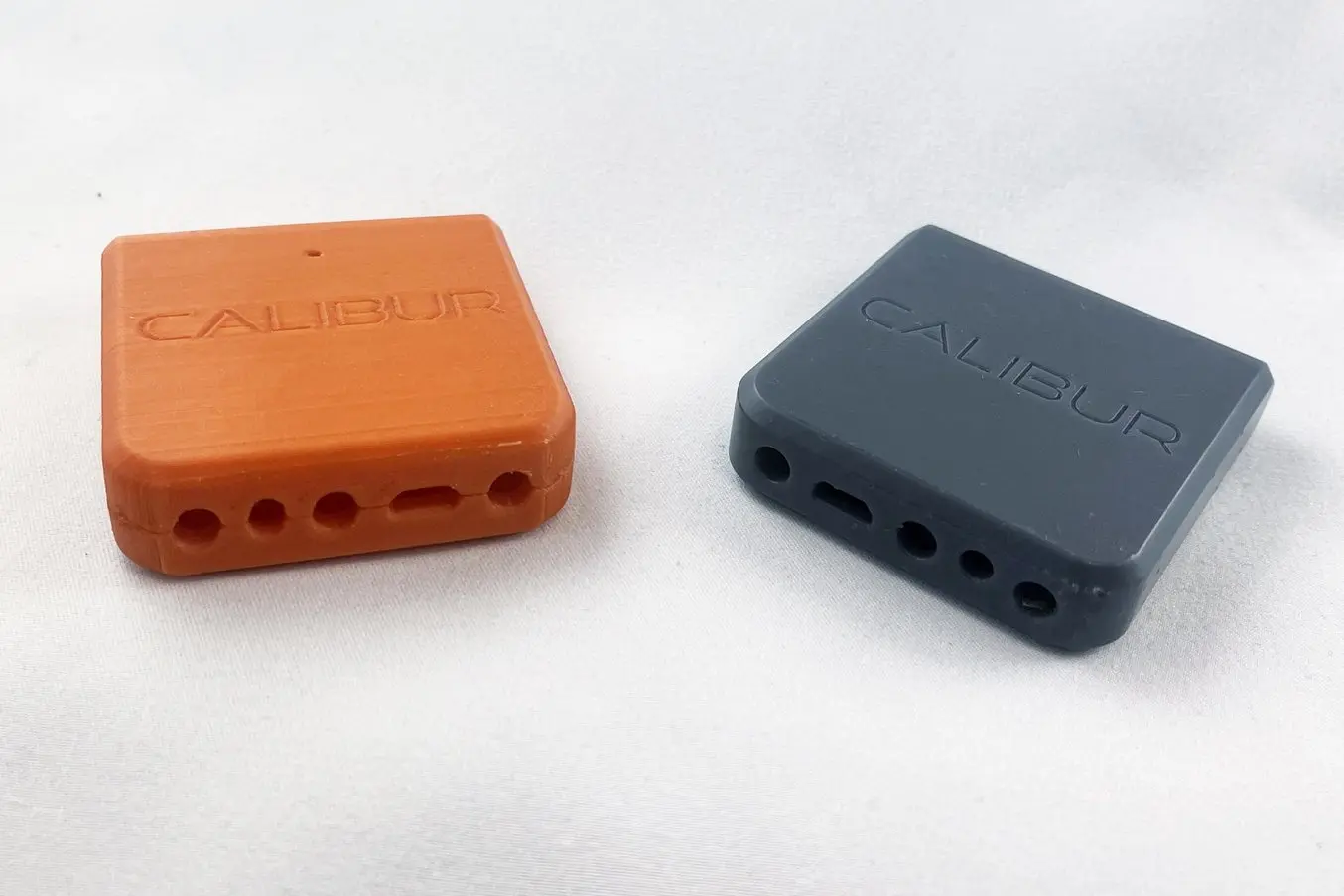
L’équipe de Calibur a utilisé l’impression 3D FDM pour les premières maquettes, puis est passée à l’impression 3D SLA pour obtenir des prototypes réalistes et fonctionnels.
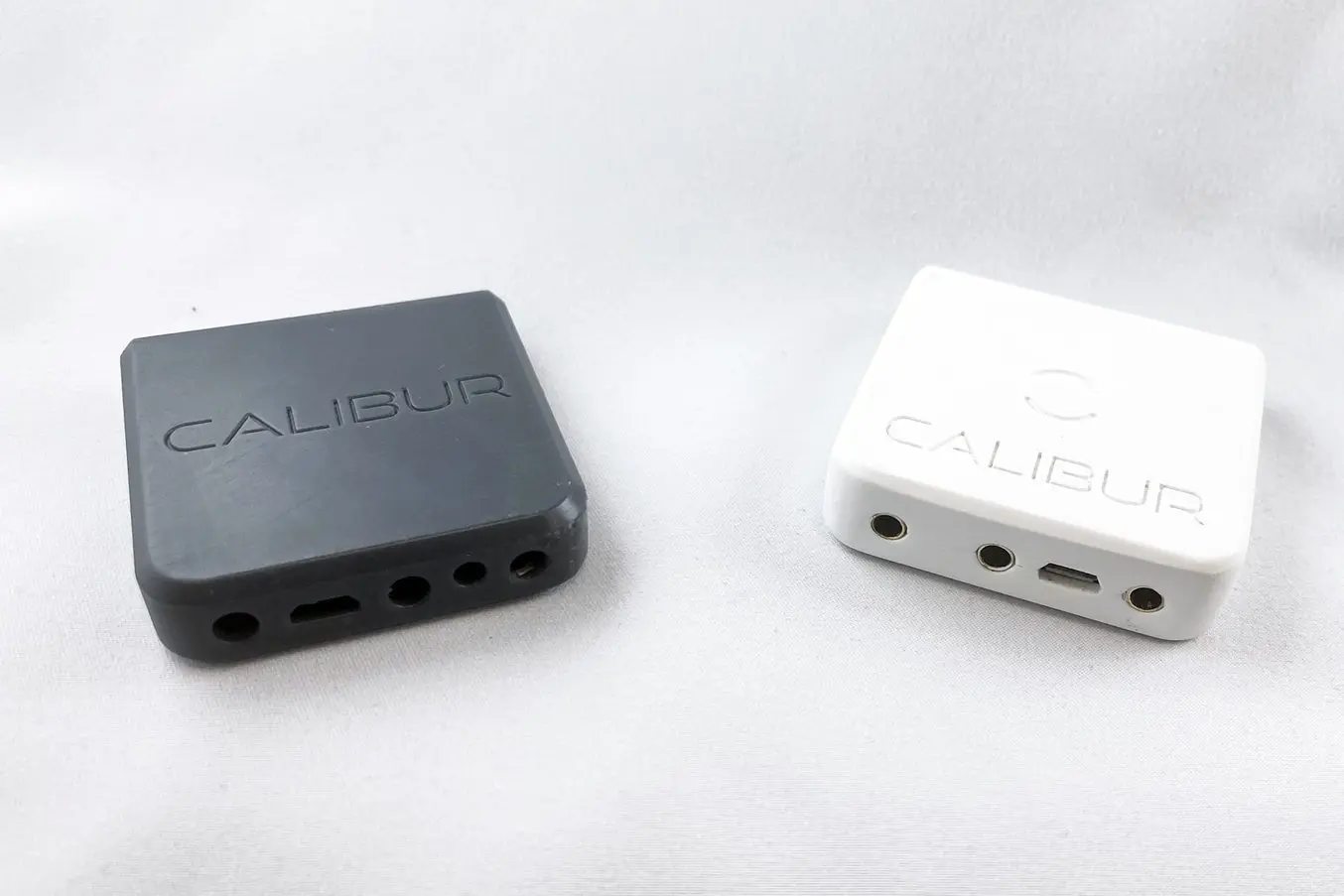
L’équipe a ensuite utilisé les pièces imprimées en 3D SLA comme modèles pour couler sous vide la première série limitée d’unités finales de test.
Louisville Slugger
L’équipe au centre d’innovation de Louisville Slugger s’est aperçue que de petits détails pouvaient faire une grande différence. L’entreprise produit des battes de baseball depuis 1884 et connaît tous les facteurs qui permettent de frapper plus rapidement et avec plus de puissance.
Le personnel du centre d’innovation de Slugger a maintenu une approche analytique de la conception axée sur le sport et a créé un supplément pour la prise en main à l’aide des solutions d’impression 3D de Formlabs. La géométrie échelonnée aide les batteurs à avoir une prise en main parfaite pour frapper le plus fermement possible.
Comme dans d’autres cas, l’équipe de conception de Slugger a conclu qu’avoir des capacités d’impression 3D et de coulée sous vide en interne accélérait les itérations de conception, tout en permettant de tirer des conclusions plus rapidement. Les modèles de prototypes détaillés, imprimés sur une imprimante SLA Form 3 avec une épaisseur de couche de 50 μm, ont servi pour créer un moule. La puissance du moulage d’uréthane a permis de créer des modèles durables et testables dont la qualité se rapproche d’un produit final moulé par injection de silicone.
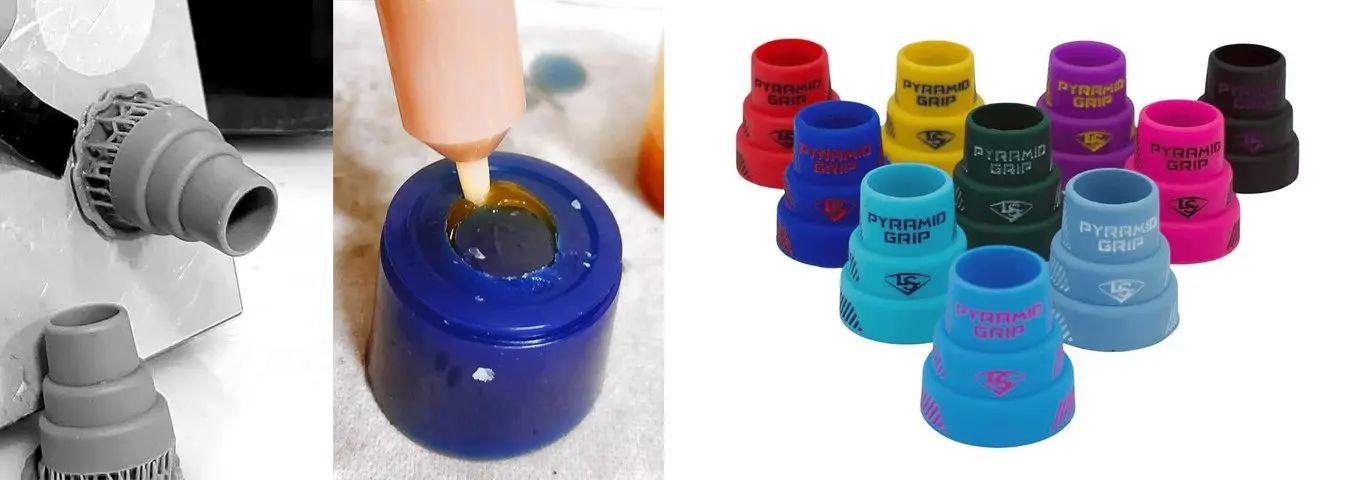
Épreuve imprimée en 3D, moulage en interne et produit fini.
SiOCAST
SiOCAST a bénéficié d’une trajectoire unique concernant l’intégration de l’impression 3D avec le moulage de résine. Le gain de popularité des jeux MMORPG en ligne et des jeux de plateaux RPG s’est accompagné d’une demande en croissance rapide pour des figurines miniatures personnalisées. Au lieu de choisir la voie coûteuse du moulage par centrifugation ou des séries limitées qui peuvent être fabriquées avec des moules en silicone de coulée sous vide, l’entreprise a développé un système breveté d’injection de résine qui fonctionne avec une machine développée exclusivement et des moules en caoutchouc HTV.
Le matériau propriétaire, SiOres, fonctionne même avec des résines thermoplastiques liquéfiées jusqu’à 240 °C. Une machine SiOCAST est jusqu’à vingt fois plus rapide que le moulage de résine traditionnel et peut produire jusqu’à 1000 pièces par heure grâce à l’automatisation et à la rotation entre divers moules à plusieurs cavités.
Tous les modèles maîtres sont imprimés en 3D avec une imprimante SLA de Formlabs et post-traités avec les systèmes de polymérisation et de nettoyage automatisés de Formlabs, Form Wash et Form Cure. Grâce aux canaux réutilisables produits avec l’impression 3D SLS, le processus est encore accéléré pour créer jusqu’à 64 miniatures par moulage.
Là où le moulage par injection produit des erreurs occasionnelles, car il doit faire face à des conditions plus critiques et à des matériaux visqueux, ces modèles de coulée sous vide produisent à chaque fois des répliques impeccables de la sculpture originales, prêtes à satisfaire l’âme numérique de beaucoup de joueurs.
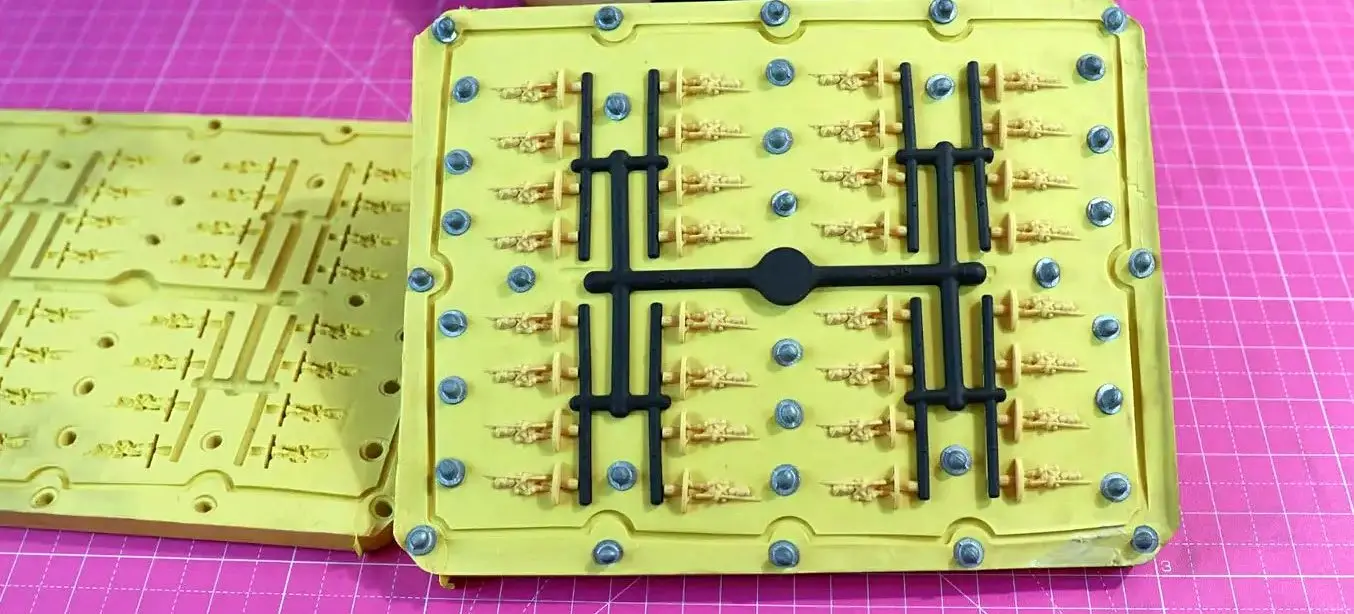
SiOCAST utilise un silicone HTV propriétaire, des modèles maîtres SLA et des canaux en nylon SLS réutilisables pour dupliquer des miniatures en séries comprenant jusqu’à 10 000 unités.
Commencez avec la coulée sous vide et l’impression 3D
La coulée sous vide est un processus idéal pour le moulage de produits, qui ne requiert pas d’entrée de jeu les investissements importants accompagnant les méthodes de production de niveau industriel. Elle peut être utilisée pour créer des prototypes, des modèles similaires, des séries en pré-production, ainsi que des produits finaux pour à peu près toutes les applications. Le modèle moulé est une réplique exacte du modèle maître, à condition que la géométrie du produit permette le démoulage et réponde aux instructions de conception spécifiques à la coulée sous vide.
La coulée sous vide bénéficie également des nouveaux développements dans le secteur de l’impression 3D : la possibilité d’imprimer en 3D des modèles maîtres très détaillés avec une finition parfaitement lisse fait de cette méthode le complément idéal pour le processus de coulée sous vide.
Toutefois, contrairement à l’impression 3D, la coulée sous vide n’est pas facile à mettre en place en interne et exige de suivre des procédures strictes. Grâce à sa grande précision, à son flux de travail simple et à ses délais de production courts, l’impression 3D offre aussi une alternative viable à la coulée sous vide pour le prototypage et également, de plus en plus, pour la production de petites séries.