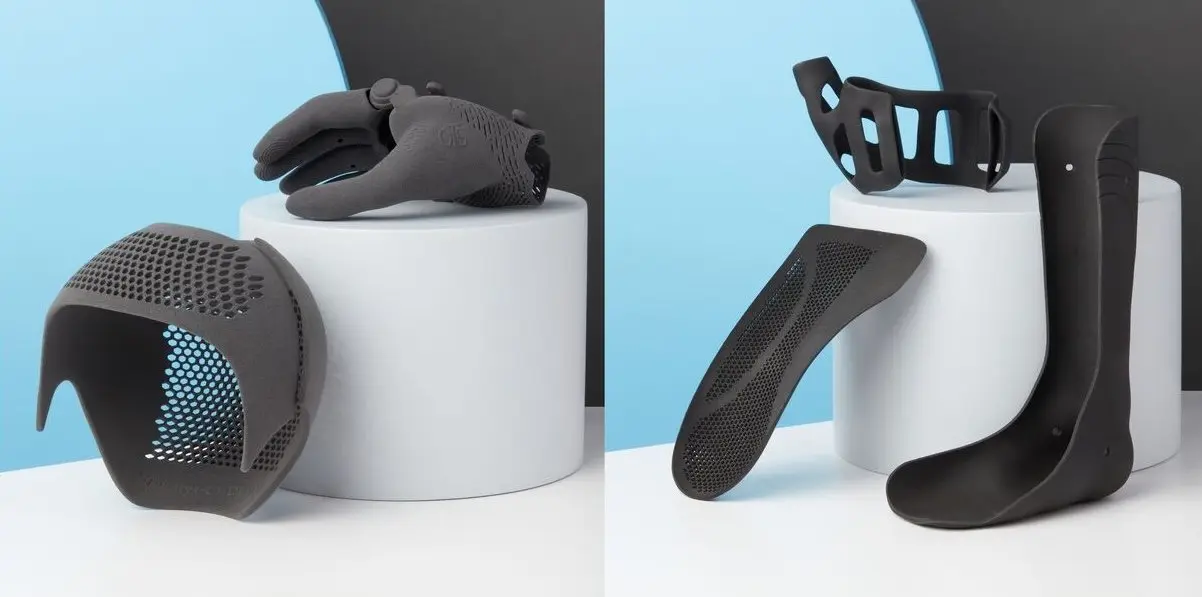
Le ortesi sono dispositivi medici esterni creati per trattare o fornire sostegno a regioni interessate da deformità muscolari o scheletriche. Possono inoltre favorire la mobilità o il recupero articolare, alleviare il dolore e prevenire lo sviluppo di problemi a lungo termine.
Alcuni esempi dei dispositivi ortesici più comuni:
- Tutori per ginocchia, che riducono la pressione e la forza esercitata sull'articolazione durante l'attività fisica
- Ortesi per caviglia e piede, che stabilizzano il piede e migliorano l'andatura
- Ortesi per polso e mano, che forniscono sostegno alle articolazioni e alla mobilità dell'arto
Il mercato odierno delle ortesi ha un valore di circa 6,5 miliardi di euro, con un tasso di crescita annuale previsto pari al 4,2%. Tale crescita è spinta dalla necessità di migliorare la qualità delle cure mediante soluzioni realizzate su misura. I dispositivi tradizionali possono infatti provocare disagio a chi li indossa, oltre a problemi di salute causati dalla scarsa aderenza. Nonostante la personalizzazione offra una soluzione, in quanto consente di realizzare dispositivi su misura, i metodi tradizionali di produzione personalizzata hanno costi aggiuntivi e lunghi tempi di consegna.
Per produrre dispositivi ortesici personalizzati, molti professionisti e professioniste del settore sanitario stanno ora adottando la stampa 3D. Seguendo workflow convalidati, questa tecnologia permette di risparmiare tempo e risorse, consentendo la realizzazione in tempi record di ortesi su misura. Continua a leggere per scoprire di più su come le ortesi personalizzate stampate in 3D migliorino l'esperienza dei pazienti e l'efficienza di produzione.
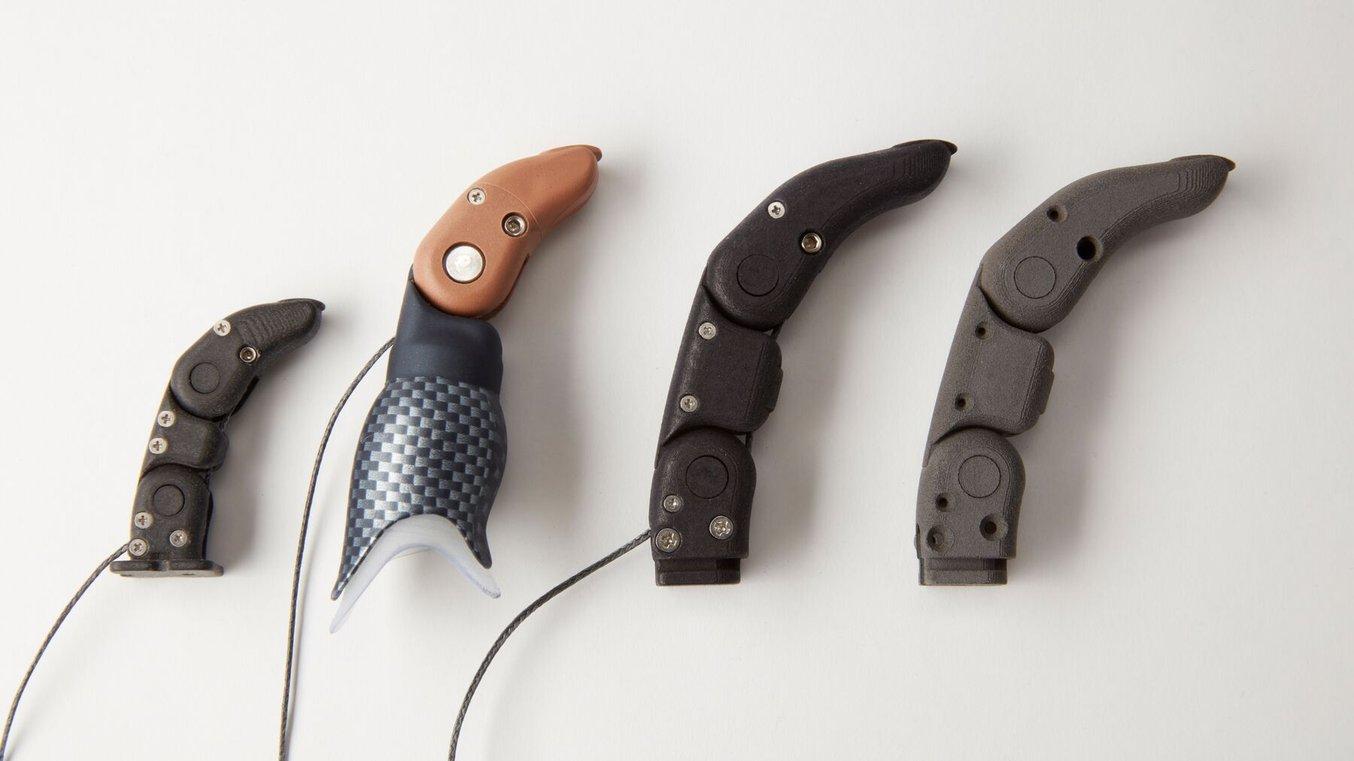
La stampa 3D nel settore dei plantari e delle protesi
Questo whitepaper è un'introduzione all'utilizzo della stampa 3D per la creazione di plantari e protesi di nuova generazione.
Come la stampa 3D ha rivoluzionato il settore delle ortesi
Il processo tradizionale di creazione delle ortesi fa parte di quelle procedure che seguono il principio del "se non è rotto, non ripararlo". I workflow tradizionali consentono di realizzare ortesi su misura per i pazienti, ma comportano molto tempo e manodopera e quindi costi aggiuntivi, il che lascia un significativo margine di miglioramento.
I workflow digitali per la realizzazione di ortesi personalizzate comprendono nuove opzioni di progettazione, test e produzione pensate per ridurre i costi di personalizzazione e velocizzare i cicli di produzione, con conseguenti tempi di consegna ridotti, dispositivi con una migliore aderenza e risultati ottimizzati per i pazienti. La stampa 3D, nota per la sua rapidità di produzione e i processi relativamente convenienti, offre a chi opera nel settore delle ortesi una soluzione efficace per ottenere applicazioni personalizzabili in modo rapido ed economico.
Ortesi tradizionali e stampate in 3D a confronto
Le ortesi vengono prodotte in modi differenti a seconda del loro utilizzo finale. Per la produzione delle ortesi si può ricorrere a processi tradizionali come la realizzazione di calchi in gesso o in schiuma per impronte, la lavorazione meccanica convenzionale, la termoformatura e la fusione della cera.
Indipendentemente dai metodi utilizzati, i workflow di base possono essere riassunti come segue:
- Si crea una mappa della parte interessata tramite un'impronta o un calco, disegni tecnici e misurazioni. L'operazione può richiedere fino a un'ora.
- Dalla mappa topografica si crea un modello di sviluppo. A seconda del processo utilizzato, questa operazione può durare da una a due ore.
- Il modello viene adattato e scolpito per garantire un'aderenza ottimale. Possono servire diverse sedute per apportare al modello le modifiche necessarie. A seconda del piano di trattamento, le sedute possono arrivare a richiedere diverse ore nell'arco di più settimane.
- Infine, l'ortesi viene sottoposta a post-elaborazione e finitura per prepararla all'uso.
Trattandosi di un processo manuale, è potenzialmente soggetto a errori a ogni fase del workflow, tra cui difetti nei calchi, misure non accurate ed errori di progettazione, che possono renderlo ancora più lungo e aumentare la manodopera necessaria, i tempi di produzione e il numero di sedute. Inoltre, questo workflow manuale richiede personale specializzato e si svolge in un ambiente pieno di polvere e fumi chimici. Alla luce di tutti questi fattori, per completare un singolo articolo personalizzato possono essere necessarie dalle tre alle sei settimane.
Vantaggi della stampa 3D di ortesi
L'elevato grado di personalizzazione delle ortesi stampate in 3D offre non solo una maggiore precisione biomeccanica, ma anche più comfort a chi le indossa. I design vengono adattati direttamente alle esigenze specifiche di ogni caso, consentendo un trattamento e un'aderenza ottimali.
"Le ortesi dovrebbero essere realizzate su misura e trattare solo i sintomi, non essere soluzioni standardizzate e limitanti."
Matej Vlašič, aNImaKe
L'efficienza e la convenienza delle ortesi stampate in 3D rendono le soluzioni realizzate su misura accessibili a un maggior numero di persone, ma anche vantaggiose per chi le produce. Dopo l'introduzione di nuovi workflow, l'adozione della stampa 3D di ortesi ha dimostrato di aumentare la produttività e ridurre i costi.
Risparmio di tempo: i workflow digitali permettono di risparmiare tempo sia al personale ortopedico che ai pazienti. I workflow semplici ed efficienti consentono infatti di dedicare meno tempo alla creazione dei modelli e alla post-elaborazione e più tempo ad attività di maggior valore. Per i pazienti, ciò si traduce in un minor numero di sedute per la verifica dell'aderenza e in meno tempo per l'acquisizione di impronte e misure.
Risparmio economico: digitalizza e semplifica il workflow con la stampa 3D per ridurre i costi di produzione, manodopera, materiali, conservazione e spedizione. I workflow tradizionali richiedono più materiali per l'acquisizione delle impronte e la creazione degli stampi, senza contare le esigenze di conservazione che ne conseguono. Con la stampa 3D, questo non è più un problema. Inoltre, la post-elaborazione delle ortesi stampate in 3D richiede meno manodopera e garantisce una maggiore efficienza.
Workflow semplificato: i workflow digitali richiedono meno manodopera e meno passaggi, il che porta all'eliminazione di intere sequenze di processi manuali, inclusa una riduzione del numero di sedute per le verifiche dell'aderenza. Inoltre, la stampa in lotti consente di stampare più ortesi alla volta, a seconda delle dimensioni e delle applicazioni da stampare.
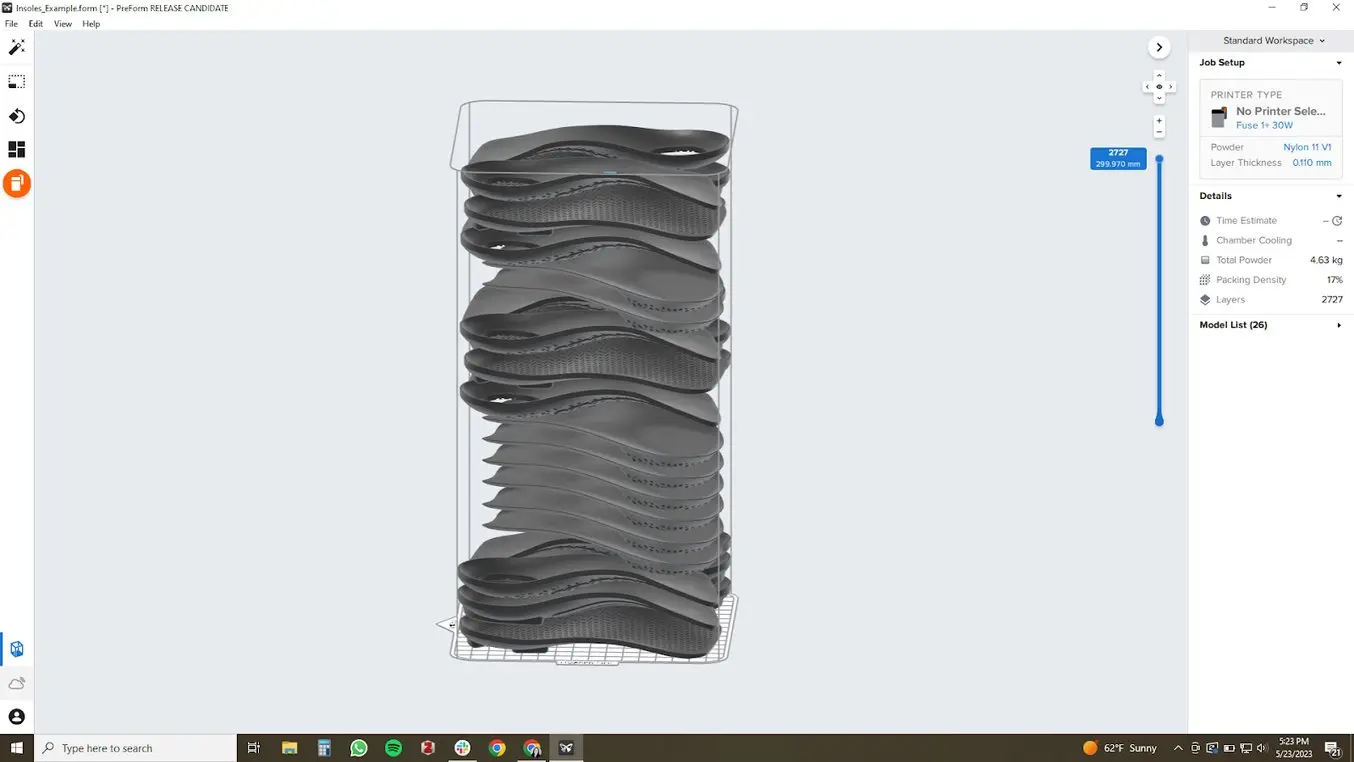
La stampa 3D SLS permette di stampare molte parti in un'unica sessione, con conseguente miglioramento dell'efficienza e riduzione dei costi.
Logistica migliorata: la digitalizzazione semplifica la gestione della logistica. Le scansioni 3D possono essere effettuate ovunque e inviate in remoto per la modellazione digitale e la progettazione. Una volta progettati, i file digitali possono essere inviati direttamente alla stampante, sia in loco che fuori sede.
Sostenibilità: nel workflow digitale, la realizzazione del prodotto finale richiede una quantità inferiore di materie prime, in quanto non è più necessario creare un modello o una replica fisica. La stampa 3D a sinterizzazione laser selettiva (SLS), che viene adottata per la produzione di diversi tipi di ortesi, consente di riutilizzare la polvere nella stampa successiva per ridurre o persino eliminare gli sprechi. A differenza dei metodi di produzione tradizionali, in cui i modelli e la plastica devono essere smaltiti, la stampa 3D riduce al minimo gli sprechi e l'utilizzo di sostanze chimiche aggressive.
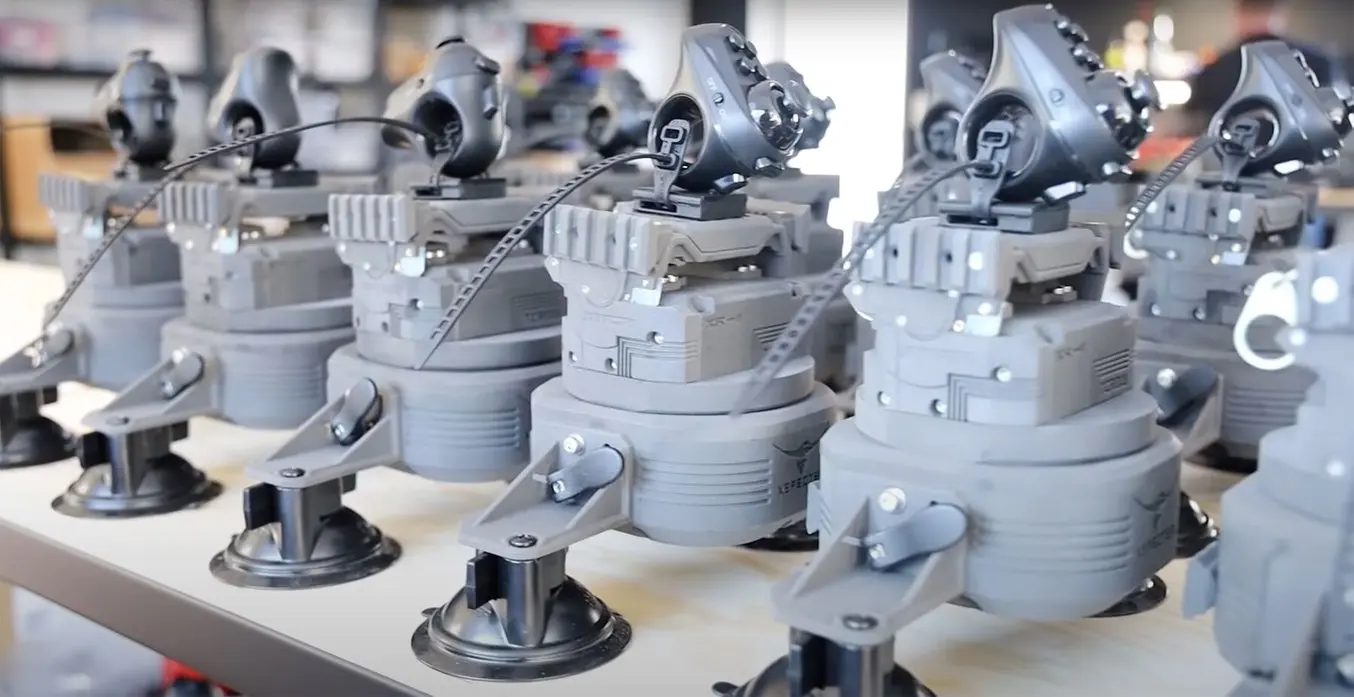
Produzione SLS per utilizzo finale
La stampa 3D per utilizzo finale non è solamente possibile, ma ora, grazie all'ecosistema SLS Fuse, è anche più economica, agile e scalabile che mai. Visita la nostra pagina dedicata alla produzione SLS per confrontare i metodi, scoprire di più sui prezzi all'ingrosso della polvere e vedere come 15 aziende già utilizzano la serie Fuse.
Applicazioni delle ortesi stampate in 3D
Le ortesi vengono utilizzate per trattare numerosi problemi. Le differenze di dimensioni e forma dell'anatomia, oltre ai requisiti del dispositivo, fanno sì che le ortesi standard possano risultare scomode a causa della scarsa aderenza, il che può influire sull'indossabilità e sull'efficacia, arrivando anche a causare disturbi secondari. Le ortesi standard, poiché prodotte in serie con dimensioni preimpostate, sono tradizionalmente meno costose delle soluzioni personalizzate. Tuttavia, ciò va a scapito del comfort e, in molti casi, dell'efficacia. È per questo che le ortesi personalizzate vengono utilizzate in un'ampia gamma di applicazioni importanti, tra cui quelle presentate di seguito.
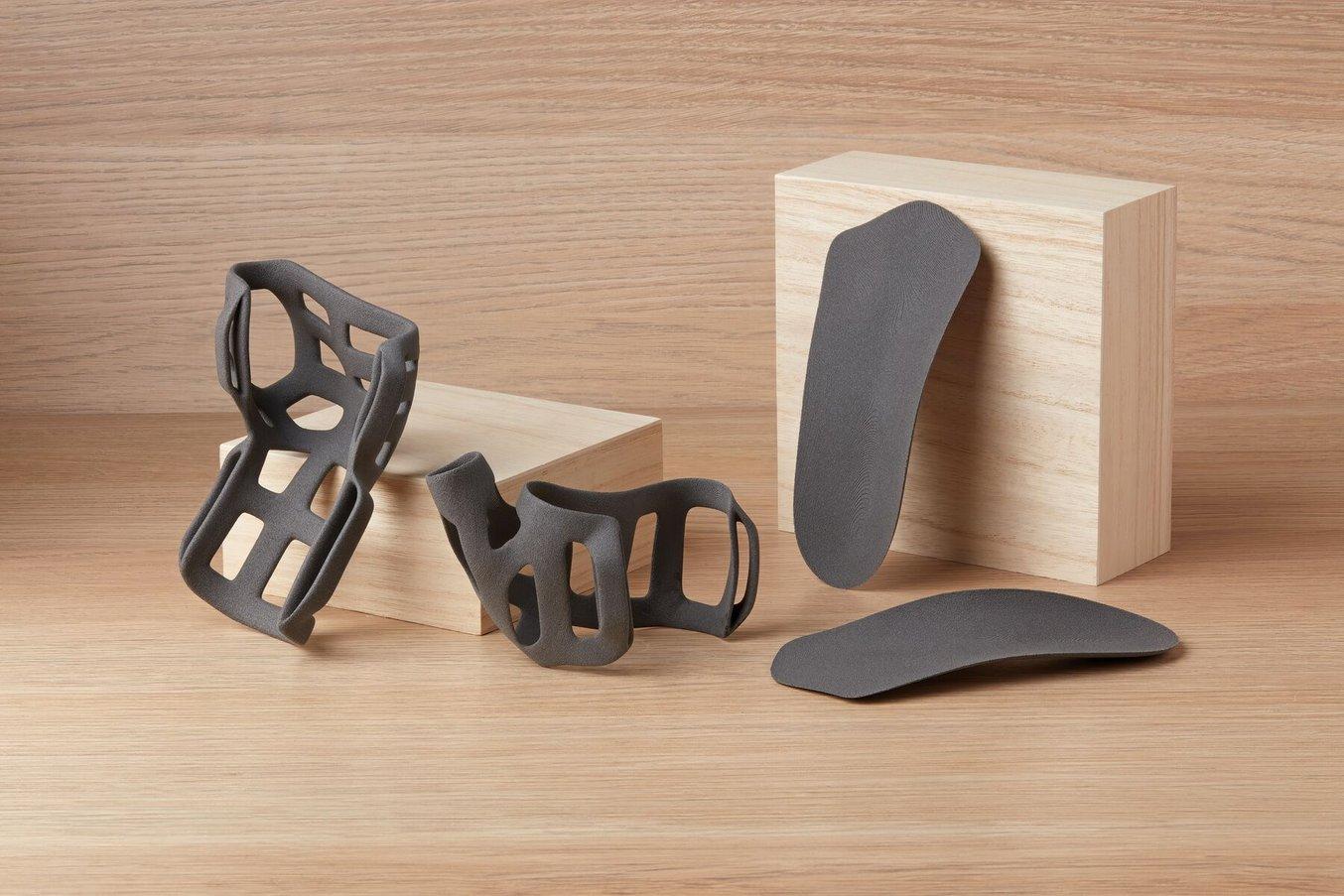
Esempi di ortesi per polso, ortesi per mano e solette plantari realizzate con la stampante SLS Fuse 1+ 30W.
Solette: le solette plantari, anche chiamate ortesi per il piede, vengono inserite nella scarpa per fornire sostegno, ma servono anche a correggere eventuali disturbi del piede e a ridurre il dolore. Posso essere prescritte in caso di dolore o fastidio causato da alluce valgo, artrite, piede cavo o fascite plantare.
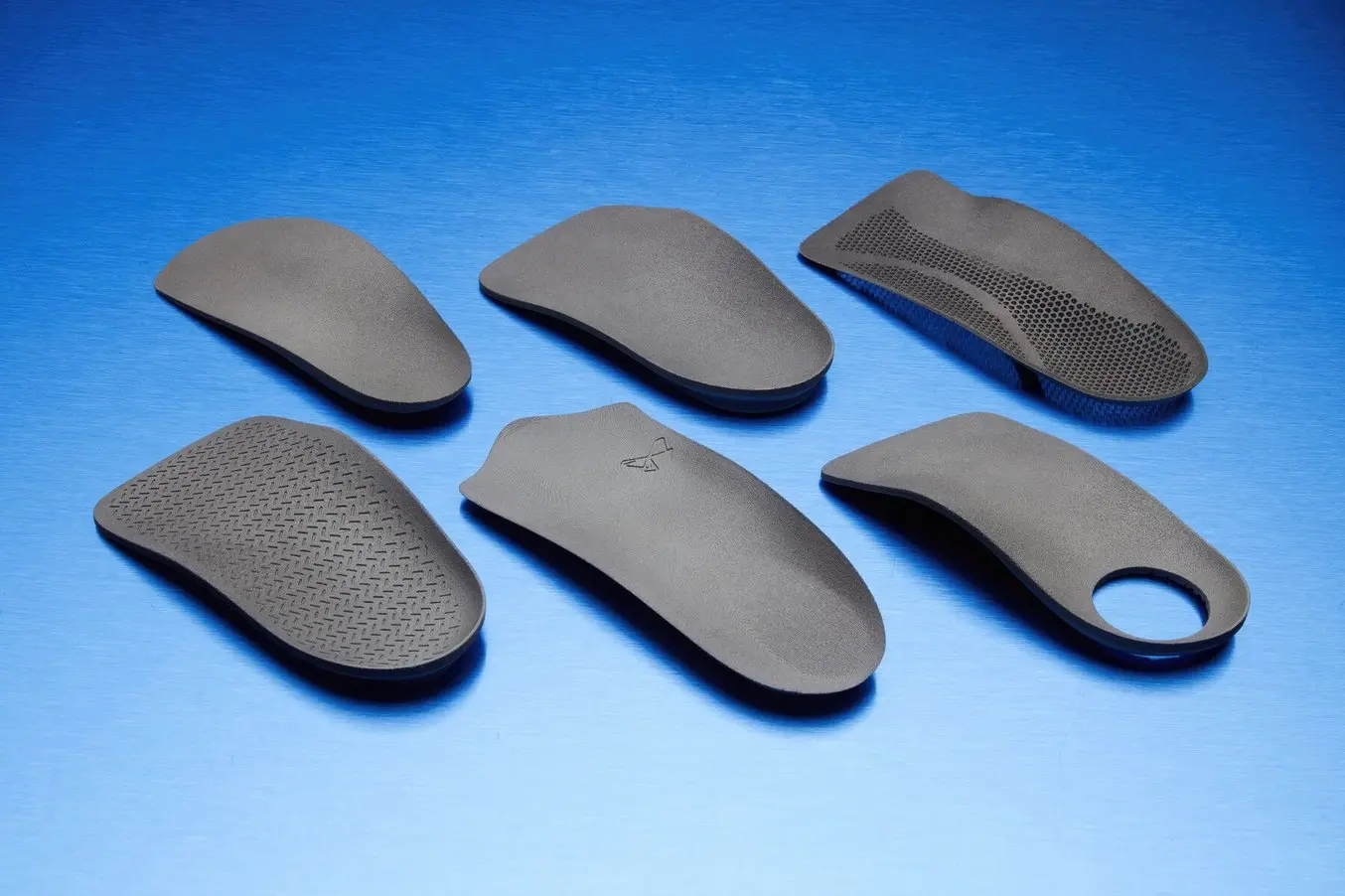
Rivoluziona il tuo modo di produrre solette grazie alla Fuse 1+ 30W di Formlabs
Migliora la produzione di solette risparmiando tempo e denaro. In questo webinar illustriamo le ragioni per cui la Fuse 1+ 30W di Formlabs è la soluzione perfetta per iniziare la transizione verso la produzione digitale o per incrementare la produzione in modo economico ed efficiente.
Ortesi per polso e mano: le ortesi per il polso e la mano immobilizzano le articolazioni per il trattamento di alcuni disturbi, tra cui fratture, artrite, lesioni ai legamenti, innesti cutanei, deformità, tendinite e distorsioni. Ne esistono di diverse tipologie: solo per il pollice, per alcune dita o per tutta la mano, ma anche per l'intero avambraccio, a seconda del piano di trattamento.
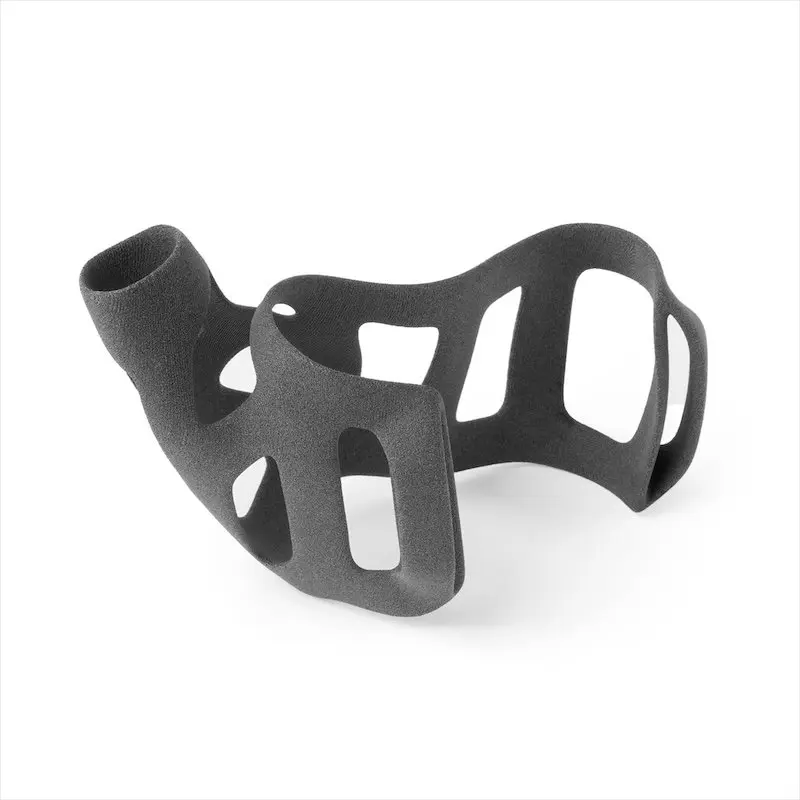
Ortesi per immobilizzare il pollice.
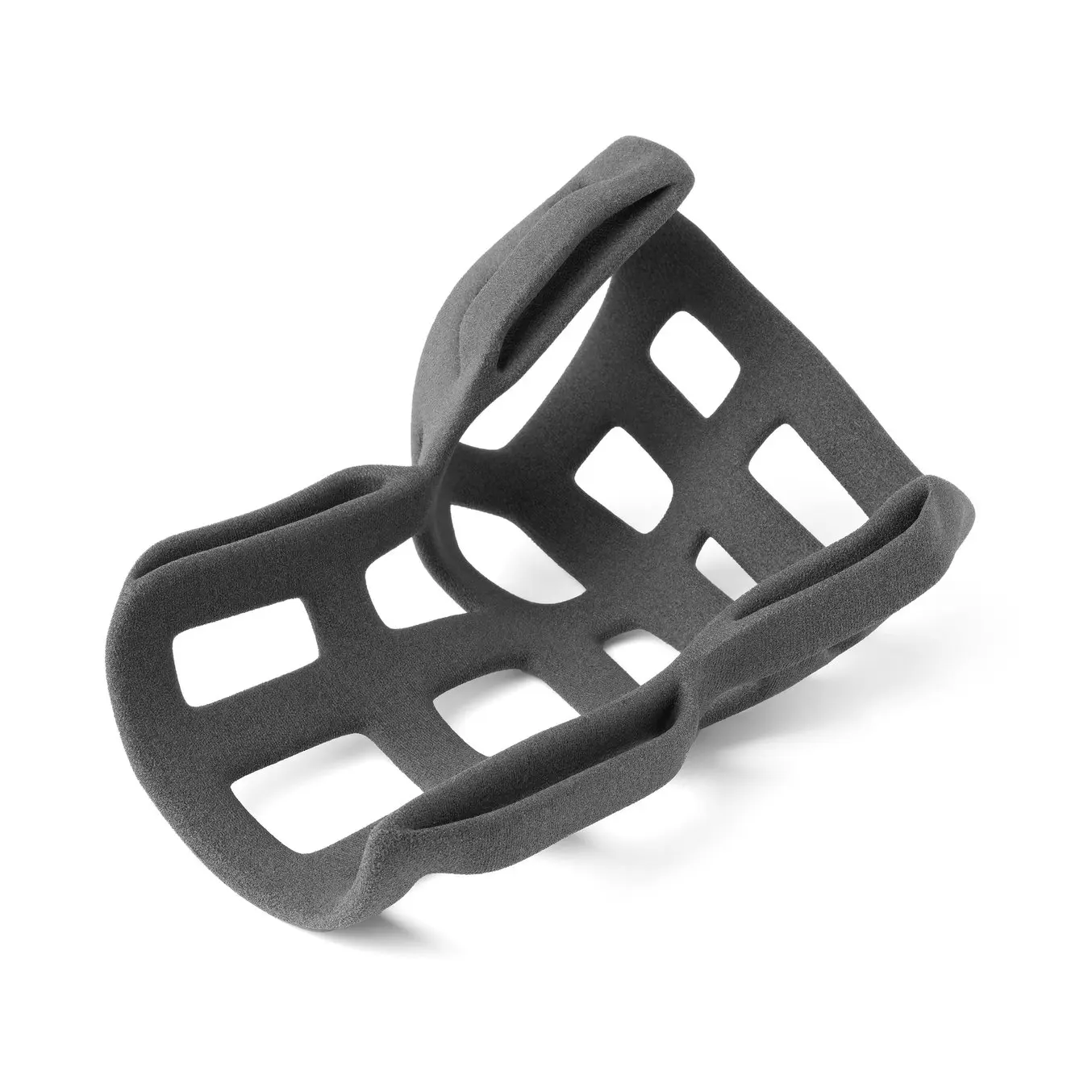
Ortesi per il polso realizzata con la stampante SLS Fuse 1+ 30W.
Ortesi per caviglia e piede: possono essere prescritte per correggere l'allineamento o fornire sostegno al fine di migliorare la mobilità nei casi di limitato controllo motorio degli arti inferiori. Queste condizioni possono derivare da una serie di disturbi neurologici e muscolo-scheletrici, tra cui ictus, paralisi cerebrale e sclerosi multipla, e interessano persone di tutte le età.
Caschetti di rimodellamento cranico: queste ortesi sono dispositivi simili a caschi destinati ai neonati di età inferiore ai 18 mesi che presentano plagiocefalia o deformazioni craniche, causate il più delle volte dall'eccessivo tempo trascorso in posizione distesa sulla schiena, e servono a proteggere la testa o correggerne la forma. La Nylon 11 Powder può essere utilizzata per stampare in 3D il componente esterno rigido sulla macchina a sinterizzazione laser selettiva (SLS) Fuse 1+ 30W. Per lo strato ammortizzato interno può invece essere utilizzata la TPU 90A Powder.
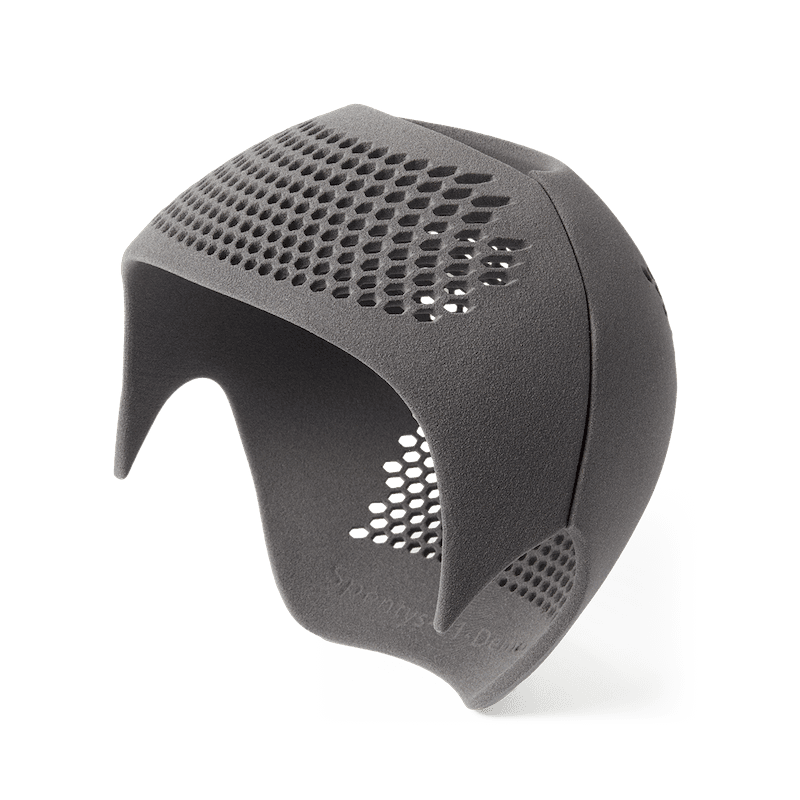
Caschetto di rimodellamento cranico stampato con la TPU 90A Powder.
Maschere protettive per il naso: le maschere protettive per il naso o il viso vengono spesso prescritte a seguito di fratture del naso o di altre parti del viso. Per realizzare questi dispositivi, il processo più indicato è la stampa 3D SLS con la Nylon 11 Powder. Nel caso di maschere trasparenti, spesso richieste per motivi estetici, si consiglia invece la stampa 3D stereolitografica (SLA) con la BioMed Durable Resin, un materiale trasparente e resistente agli urti per le stampanti 3D SLA Form 3+/3L.
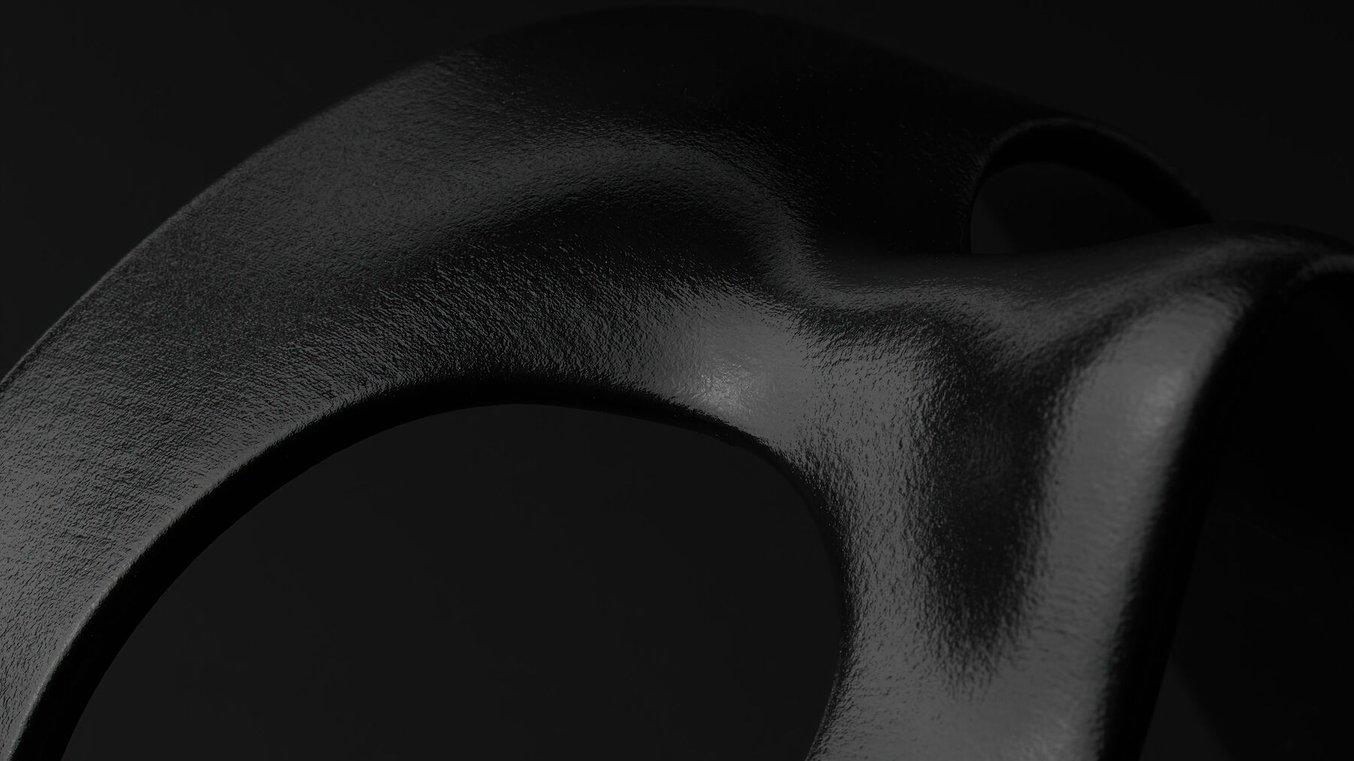
Primo piano di una maschera protettiva per il naso stampata con la Nylon 11 Powder e sottoposta a post-elaborazione tramite levigazione a vapore.
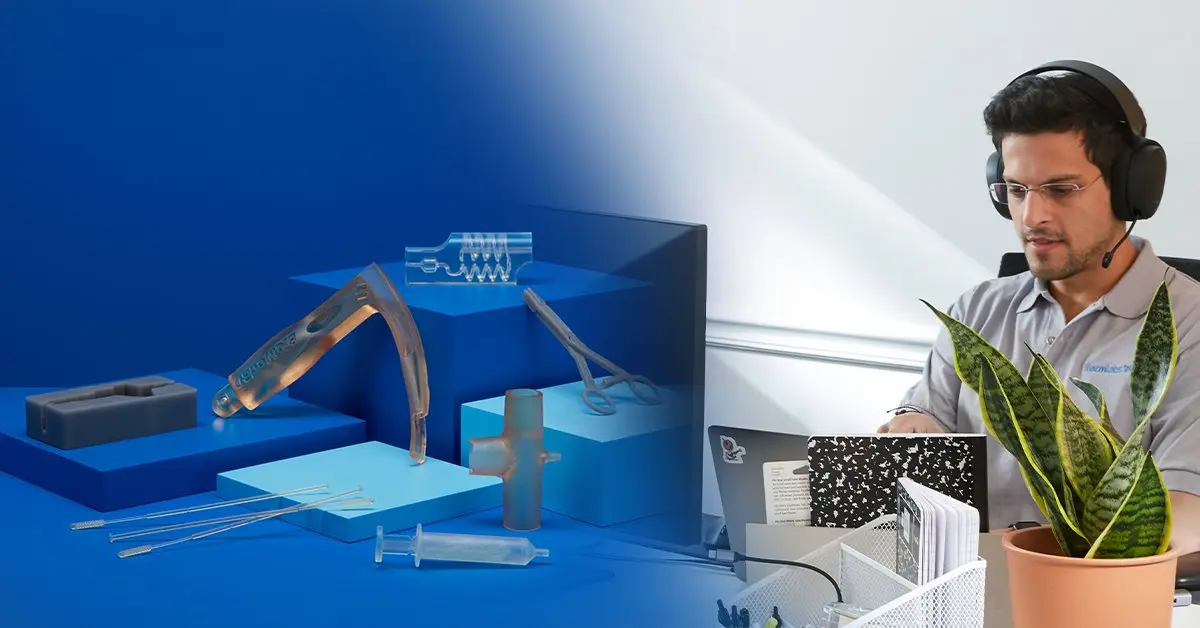
Contatta il nostro team vendite per il settore sanitario
Siamo qui per aiutarti a raggiungere i tuoi obiettivi, che si tratti di stampare strumenti chirurgici su misura per i pazienti o di creare il prototipo di un dispositivo medico cardiaco. Il team Formlabs Medical è composto da specialisti che sanno esattamente come assisterti per soddisfare le necessità della tua azienda.
Workflow digitali per la creazione di ortesi personalizzate con la stampa 3D
Per la realizzazione di ortesi personalizzate con la stampa 3D occorrono uno scanner 3D, un software CAD e una stampante 3D con un materiale compatibile. Esistono diverse opzioni a seconda di tipo di ortesi, volume di produzione, usi previsti, workflow, spazio disponibile e investimento iniziale. Tuttavia, l'adozione della stampa 3D per creare ortesi personalizzate è ora più accessibile che mai.
1. Scansione
Il primo passo per creare ortesi stampate in 3D è l'acquisizione di un'immagine o scansione della parte anatomica interessata. Questi dati anatomici vengono poi trasformati in un modello 3D digitale, che può essere utilizzato per progettare l'ortesi.
Rispetto ai processi tradizionali di creazione di impronte e modelli, la scansione 3D offre elevata accuratezza, maggiore velocità di acquisizione, manodopera ridotta e flessibilità nella scelta dei punti di acquisizione. Esistono diverse aziende produttrici di scanner digitali che offrono soluzioni per la stampa 3D di ortesi. Questi dispositivi sono disponibili in un'ampia gamma di prezzi e tecnologie, tra cui LiDAR, TAC in carico, infrarossi e laser. Scopri di più sulle opzioni disponibili per le solette plantari in questa guida.
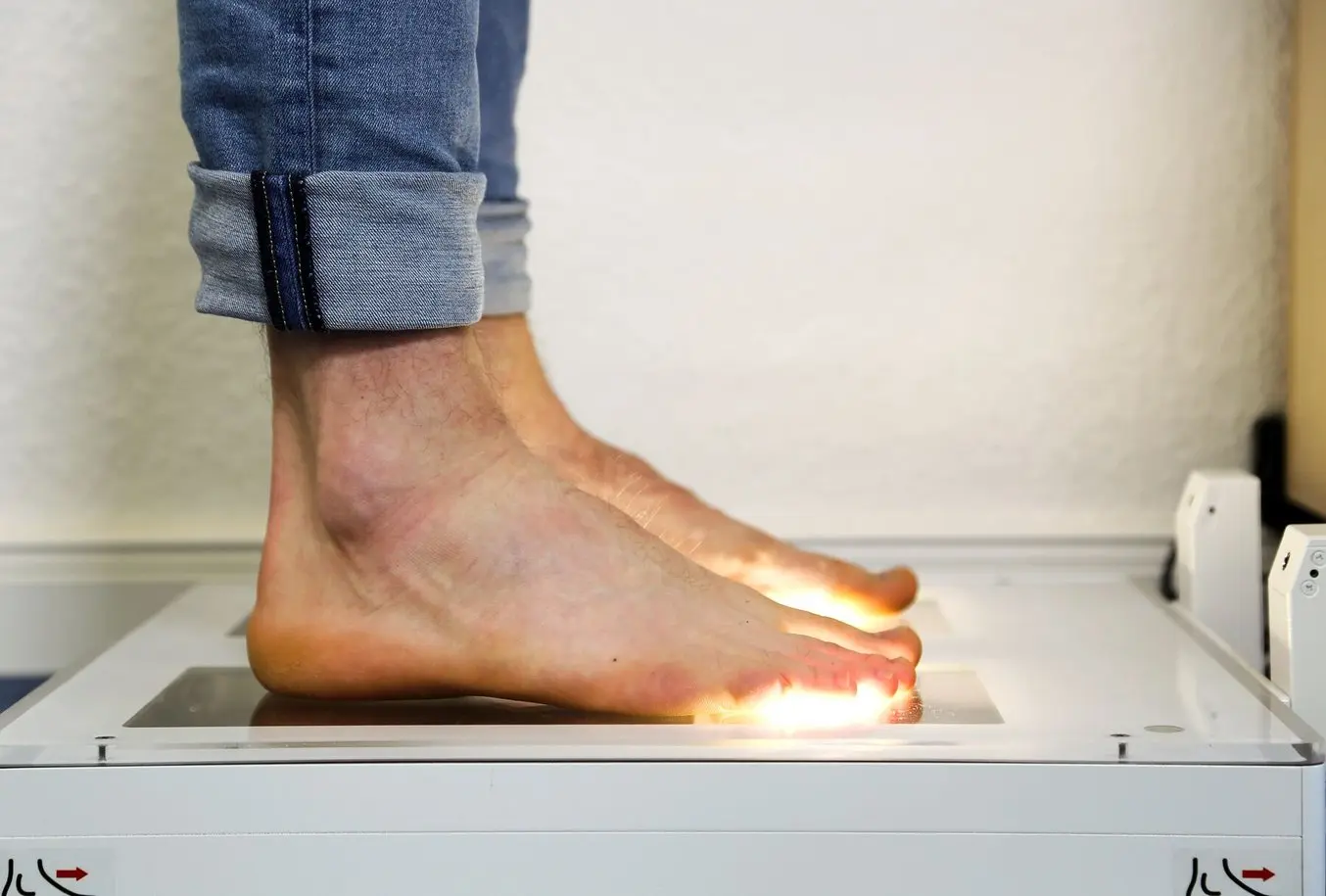
La scansione 3D è in grado di acquisire un'impronta più accurata e completa del piede rispetto ai metodi tradizionali.
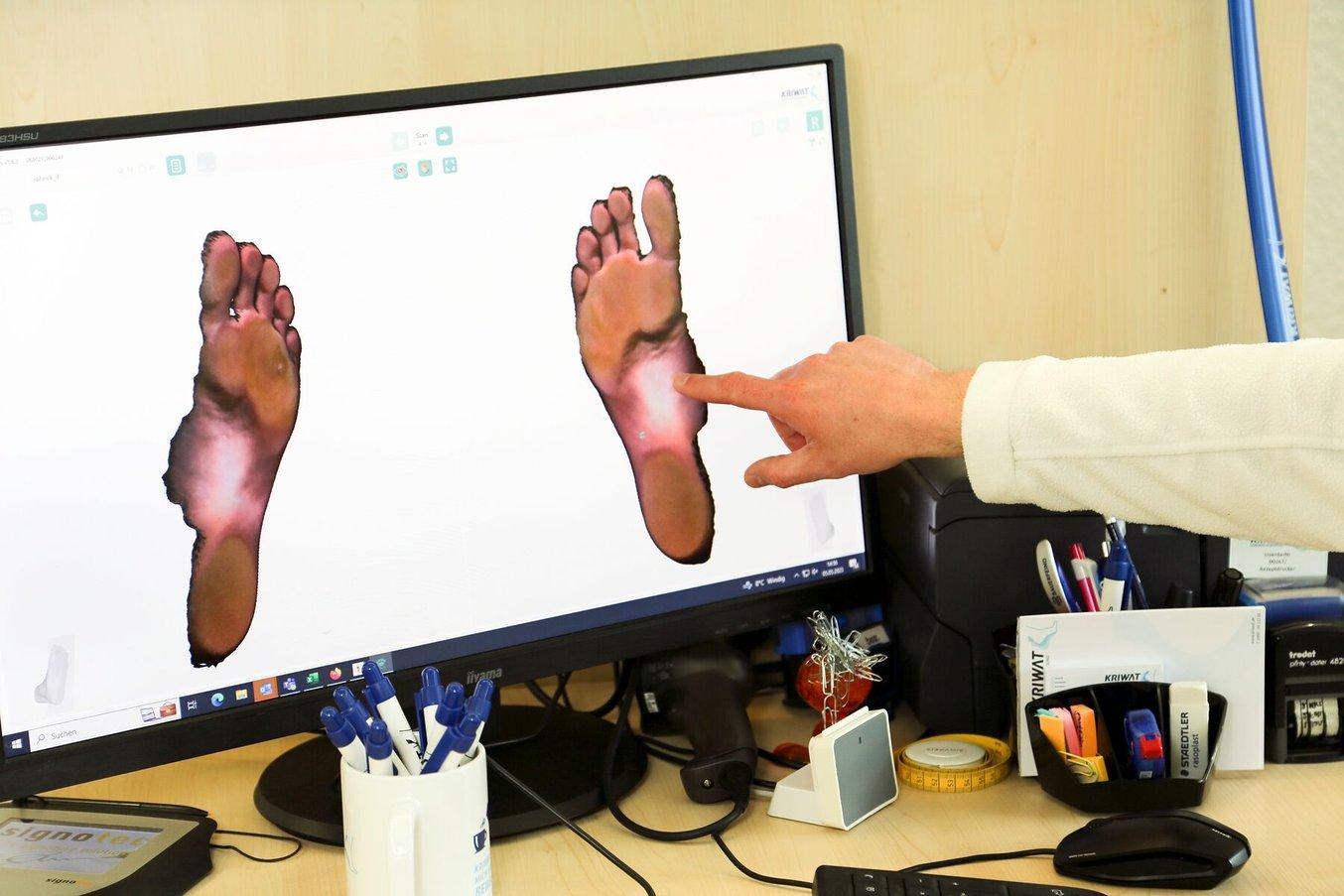
La scansione semplifica l'invio dei dati in formato digitale per la progettazione e la stampa.
2. Modellazione digitale
Una volta che la scansione ha acquisito i dati richiesti, è necessario sviluppare un modello accurato utilizzando un software CAD o CAM. Per la progettazione sono disponibili vari modelli di software da diversi fornitori e la scelta dipende dall'applicazione specifica. Alcuni di questi programmi offrono prestazioni elevate in termini di accuratezza, facilità di utilizzo e personalizzazione, che consentono di progettare un'ortesi in pochi minuti. Per scoprire di più sui vari programmi CAD disponibili per la progettazione specifica di solette plantari, leggi la nostra guida.
Nella maggior parte dei casi, occorre modificare i dati acquisiti attraverso riparazioni della mesh per sviluppare modelli stampabili in 3D per la fase successiva del processo di personalizzazione. Una volta completata la progettazione, i dati vengono salvati come file STL, OBJ o 3MF e importati in un software di preparazione della stampa, come PreForm.
Per ottimizzare il workflow, è possibile stampare più ortesi in un'unica sessione, a seconda delle dimensioni e dell'orientamento dei dispositivi.
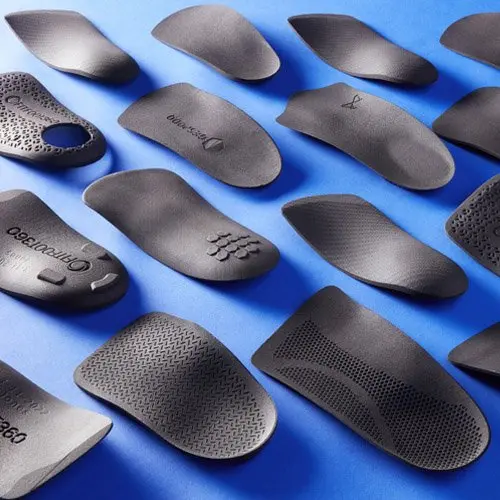
Stampa 3D di solette parziali rigide
Scopri come produrre solette parziali resistenti, duttili e in grado di superare 4 milioni di cicli di piegatura con l'ecosistema SLS compatto e conveniente di Formlabs. Questa guida completa ti aiuterà a partire in quarta con la produzione di solette parziali con la Fuse 1+ 30W.
3. Stampa 3D delle ortesi
I fornitori di servizi ortopedici e sanitari possono sfruttare le diverse tecnologie di stampa 3D disponibili per produrre dispositivi pronti per l'uso. Nella scelta della tecnologia di stampa, l'applicazione della parte per utilizzo finale, le sue dimensioni, il volume di produzione e le complessità progettuali sono alcuni importanti criteri da tenere in considerazione.
Per la stampa 3D di ortesi personalizzate, la tecnologia SLS è una soluzione conveniente e di alta qualità. Le stampanti SLS sono in grado di stampare più dispositivi in un unico ciclo di stampa e offrono un'ampia gamma di materiali biocompatibili, tra cui opzioni flessibili e rigide. Con la stampa SLS è possibile produrre ortesi resistenti e geometrie complesse con un'elevata precisione. A differenza di altri tipi di stampa 3D, la SLS non richiede strutture di supporto e ha un workflow completo semplificato, dall'impostazione della stampa alla parte finita.
La stampa 3D a fusione multi-getto (MJF) è un'alternativa simile alla SLS. Tuttavia, pur garantendo parti di alta qualità, ha costi di investimento iniziali molto più elevati, il che significa che è accessibile solo ai laboratori e alle aziende di ortesi che producono su larga scala.
Per alcune applicazioni, tra cui gli interni dei caschetti di rimodellamento cranico o le maschere protettive per il naso trasparenti, viene spesso scelta la stampa 3D SLA. Infine, la modellazione a deposizione fusa (FDM) è una tecnologia di stampa 3D a basso costo che può essere utilizzata per la prototipazione, ma non offre la resistenza che le ortesi per utilizzo finale richiedono.
Parla con i nostri esperti di stampa 3D per scoprire qual è la tecnologia più adatta per raggiungere i tuoi obiettivi.
Scelta dei materiali per la stampa 3D di ortesi
Nella scelta dei materiali per la stampa 3D SLS di ortesi, si devono considerare proprietà specifiche in base all'applicazione e alle esigenze della persona, tra cui resistenza, flessibilità, elasticità e rigidità. Nel catalogo Formlabs, due materiali in particolare, la TPU 90A Powder e la Nylon 11 Powder, sono ideali per la produzione di ortesi.
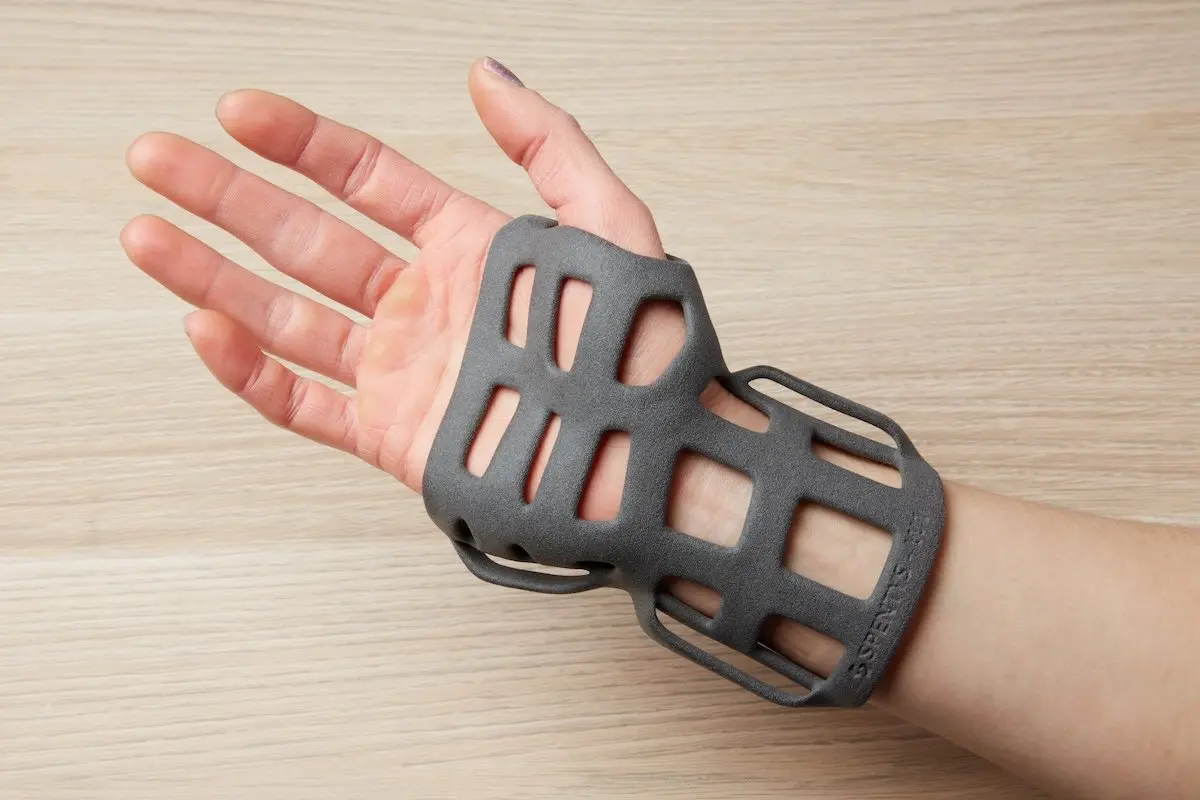
Ortesi per il polso realizzata con la stampante SLS Fuse 1+ 30W.
La TPU 90A Powder è un elastomero flessibile che combina l'elevato allungamento a rottura e la straordinaria resistenza alla lacerazione dei materiali in gomma con la libertà di design e la robustezza della stampa 3D SLS. Il poliuretano termoplastico (TPU) è una termoplastica elastomerica molto diffusa. Nel settore delle ortesi, questo materiale sicuro per la pelle viene spesso utilizzato per produrre:
- Prototipi di dispositivi medici e dispositivi medici e componenti per utilizzo finale
- Solette plantari e invasature protesiche
- Dispositivi indossabili
- Caschetti di rimodellamento cranico
La Nylon 11 Powder è il materiale ideale per stampare ortesi rigide, comprese solette parziali, con elevata duttilità e stabilità a lungo termine. Inoltre, le parti stampate con questa polvere sono stabili dal punto di vista ambientale, assorbono pochissima umidità e sono resistenti a luce, calore e sostanze chimiche. La Nylon 11 Powder ha infine la certificazione di biocompatibilità per il contatto con la pelle, che la rende ideale per la stampa di ortesi e maschere protettive per il naso. Questo materiale resistente e sicuro per la pelle viene spesso utilizzato per produrre i seguenti dispositivi medici e ortesici:
- Solette correttive e per calzature sportive
- Ortesi per caviglia e piede
- Maschere protettive per il naso
- Bite dentali
- Prototipi di dispositivi medici e dispositivi medici e componenti per utilizzo finale
Per dimostrare la resilienza della Nylon 11 Powder, è stato eseguito un confronto tra solette Formlabs stampate con questo materiale e solette in polipropilene prodotte con metodi tradizionali. Le solette Formlabs hanno dimostrato una straordinaria resistenza a un uso intenso e il mantenimento di una rigidità costante. In un test di flessione dinamica a 3 punti, le solette Formlabs stampate con la Nylon 11 Powder hanno resistito all'equivalente di 10 959 passi al giorno per 365 giorni, un numero di gran lunga superiore ai passi mediamente percorsi da una persona adulta. Per vedere i risultati completi dell'analisi delle prestazioni meccaniche, scarica il whitepaper.
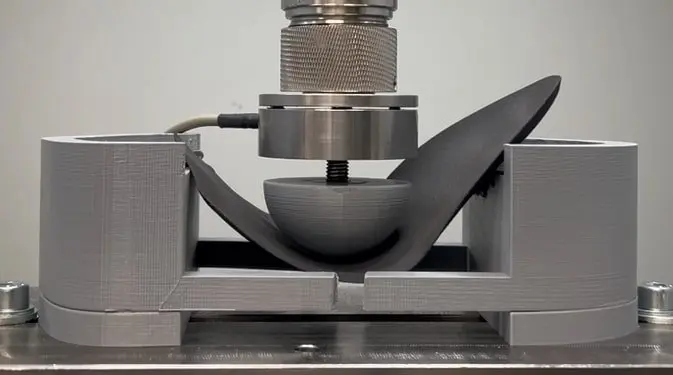
Prestazioni meccaniche di solette prodotte con stampa 3D e in modo tradizionale
In questo studio vengono analizzate le proprietà dei materiali e i metodi di produzione di solette personalizzate: la Fuse 1+ 30W e la Nylon 11 Powder di Formlabs, la 3D HR PA 11 di HP e il polipropilene prodotto in modo tradizionale.
4. Finitura e post-elaborazione
Le ortesi stampate in 3D devono essere sottoposte a post-elaborazione e spesso vengono assemblate a componenti standard come coperture e imbottiture. I workflow di post-elaborazione variano a seconda del tipo di stampa e della finitura superficiale desiderata. A seconda dei requisiti dell'ortesi finale, si possono anche aggiungere cinghie, imbottiture e tessuti.
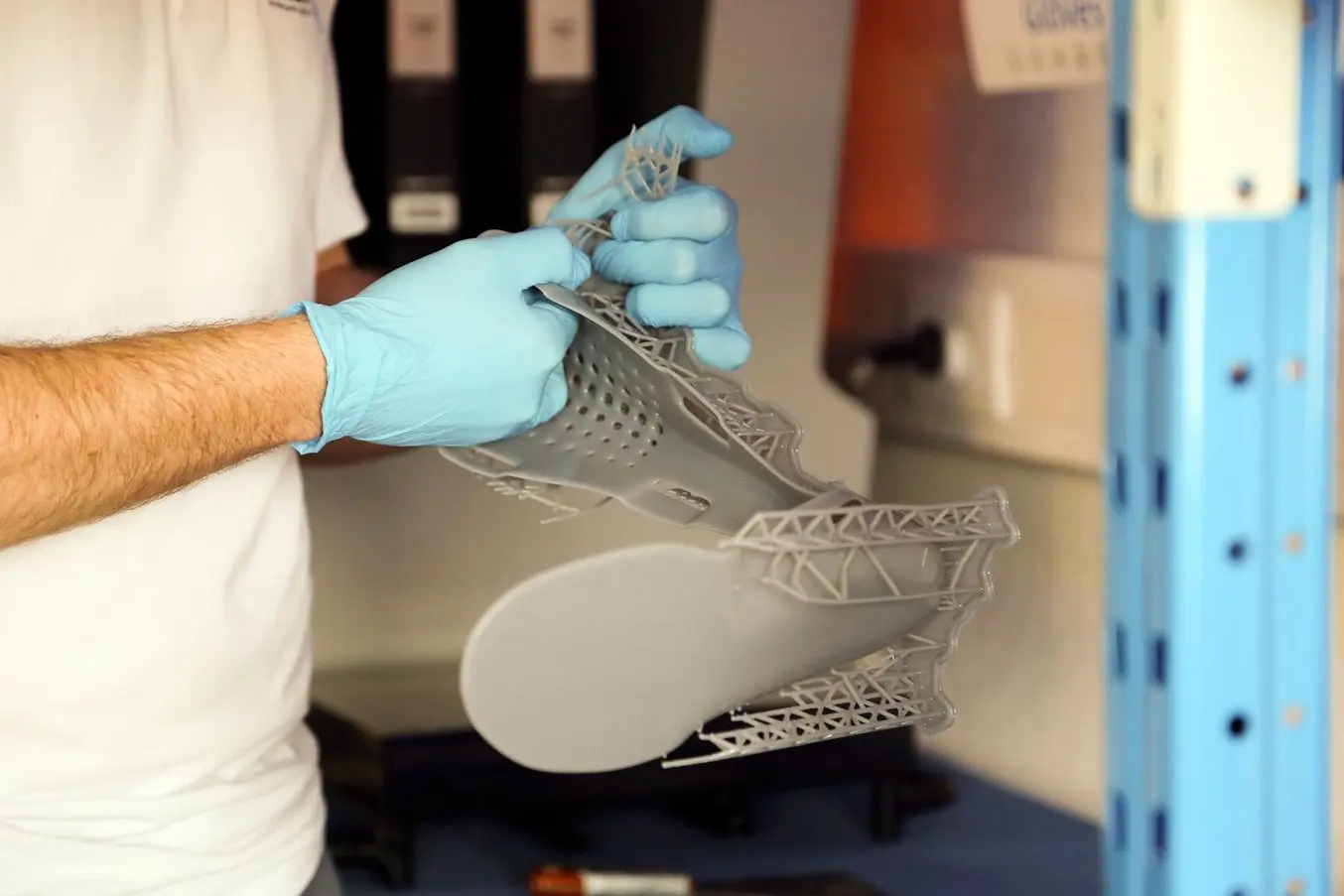
Rimozione dei supporti da un'ortesi realizzata su una stampante 3D SLA Form 3BL.
Le ortesi stampate tramite SLA vengono lavate in alcool isopropilico prima della rimozione dei supporti stampati. Le parti vengono quindi polimerizzate per un periodo di tempo prestabilito a seconda della resina impiegata per la stampa. Scopri le indicazioni complete per la post-elaborazione per le stampanti SLA Form 3+/3BL.
Per la stampa 3D SLS e con la Fuse 1+ 30W, la Fuse Sift offre un sistema integrato per la gestione della polvere, in grado di raccogliere e setacciare la polvere. Una volta trattate le parti nella Fuse Sift, la finitura superficiale risulta leggermente ruvida, caratteristica che la rende ideale per l'applicazione di agenti adesivi e soluzioni di rivestimento per creare il prodotto finale.
La Fuse Blast è una soluzione di pulizia e lucidatura completamente automatizzata che consente la pulizia manuale o automatica delle stampe. Scegliendo quest'ultima opzione, bastano solo dieci minuti per ottenere parti pulite al tatto. La funzione è completamente automatizzata e include programmi predefiniti che rendono la produzione ancora più semplice. È inoltre presente una funzione di lucidatura che conferisce alle parti una finitura superficiale liscia.
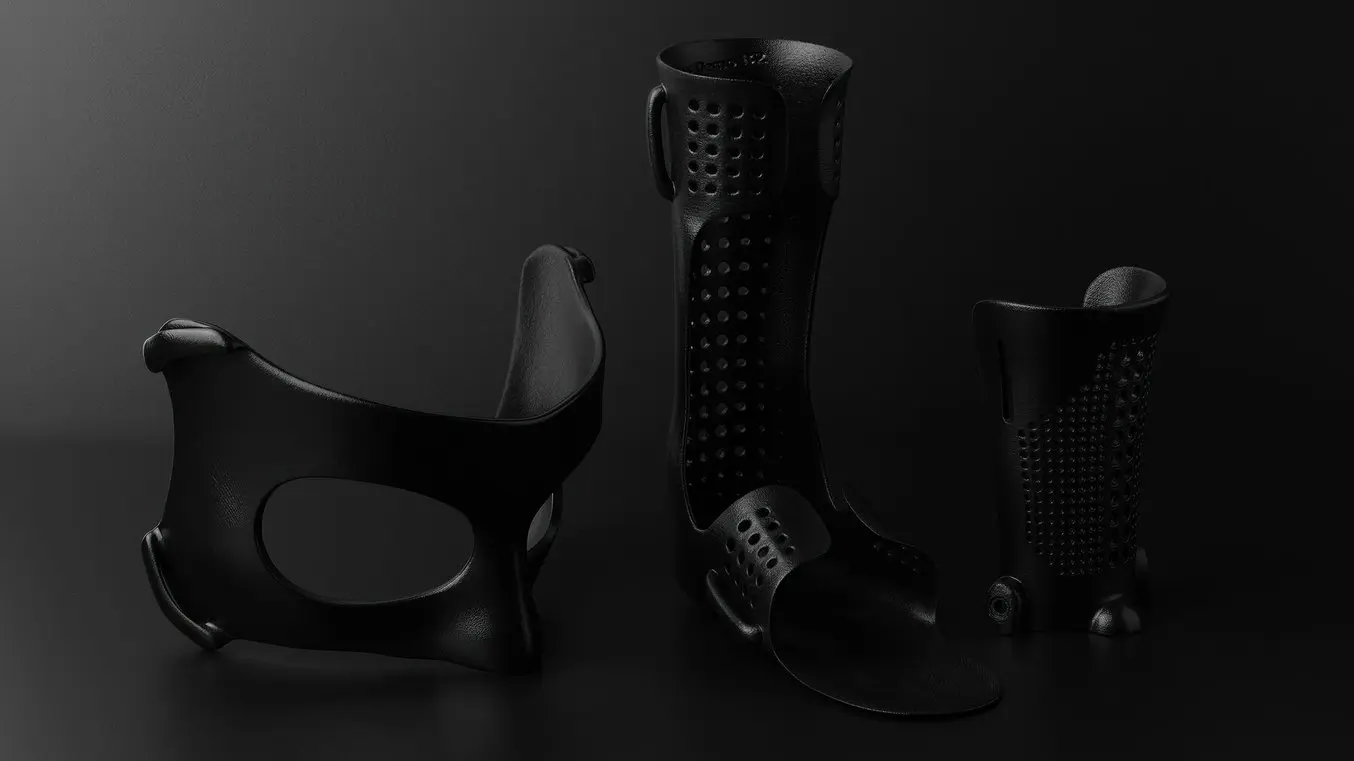
Ortesi stampate in Nylon 11 Powder e sottoposte a finitura tramite levigazione a vapore.
Per le ortesi che richiedono una finitura superficiale liscia, la levigazione a vapore è un comune processo di post-elaborazione che consente di migliorare la porosità e ridurre la rugosità delle parti realizzate tramite stampa 3D SLS. Questo trattamento permette inoltre di ridurre notevolmente la frizione superficiale che può avvertire chi indossa dispositivi ortesici. Si tratta di un processo chimico in cui la superficie di una parte stampata in 3D tramite SLS viene esposta a un solvente vaporizzato. Le parti SLS sottoposte a levigazione a vapore presentano una resistenza e una finitura superficiale paragonabili a quelle delle parti stampate a iniezione, ma anche una riduzione della proliferazione batterica e dell'assorbimento di umidità.
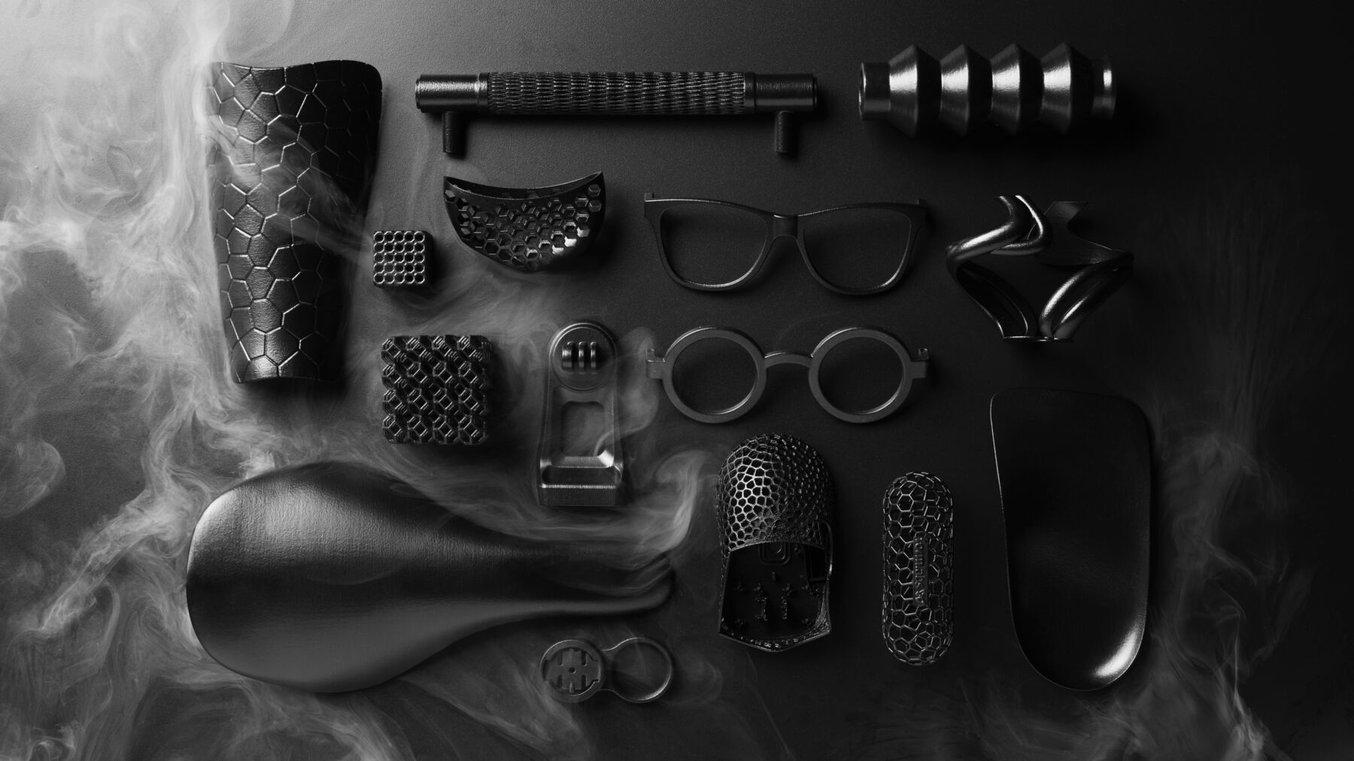
La levigazione a vapore per migliorare la finitura superficiale delle parti SLS: uno studio di Formlabs e AMT
In questo whitepaper esamineremo le considerazioni e i vantaggi legati alla levigazione a vapore e riporteremo i risultati dei test condotti sulle polveri SLS di Formlabs con il sistema di levigazione a vapore di AMT.
Entra nel mondo della stampa 3D di ortesi
La stampa 3D ha rivoluzionato la progettazione delle ortesi e consente di produrre dispositivi specifici per i pazienti con workflow semplificati che fanno risparmiare tempo e denaro. Ne conseguono diversi vantaggi per i pazienti: minor numero di visite, tempi di consegna rapidi e massima personalizzazione per un maggiore comfort, il tutto a un costo inferiore rispetto ai metodi tradizionali di produzione di ortesi personalizzate. Per i team ortopedici e le aziende produttrici, i workflow di stampa 3D permettono di risparmiare tempo e risorse e di creare al contempo un ambiente di lavoro più confortevole.
La stampa 3D SLS si è dimostrata un metodo affidabile ed efficiente per produrre ortesi, mentre la stampante SLS Fuse 1+ 30W di Formlabs combina prestazioni di livello industriale con un workflow accessibile e conveniente. Poiché la Fuse 1+ 30W è una stampante SLS compatta, può essere facilmente installata in ogni spazio di produzione. Inoltre, il catalogo di materiali della Fuse 1+ 30W include la Nylon 11 Powder, un materiale resistente e flessibile che riproduce fedelmente le proprietà dei materiali delle attuali ortesi per utilizzo finale, e la TPU 90A Powder, un materiale elastico e sicuro per il contatto con la pelle.
Vuoi approfondire un argomento in particolare? Per una panoramica completa dei workflow digitali e della stampa 3D nel settore delle ortesi e delle protesi, scarica il nostro whitepaper, oppure parla con gli esperti Formlabs per trovare la soluzione più adatta per te.