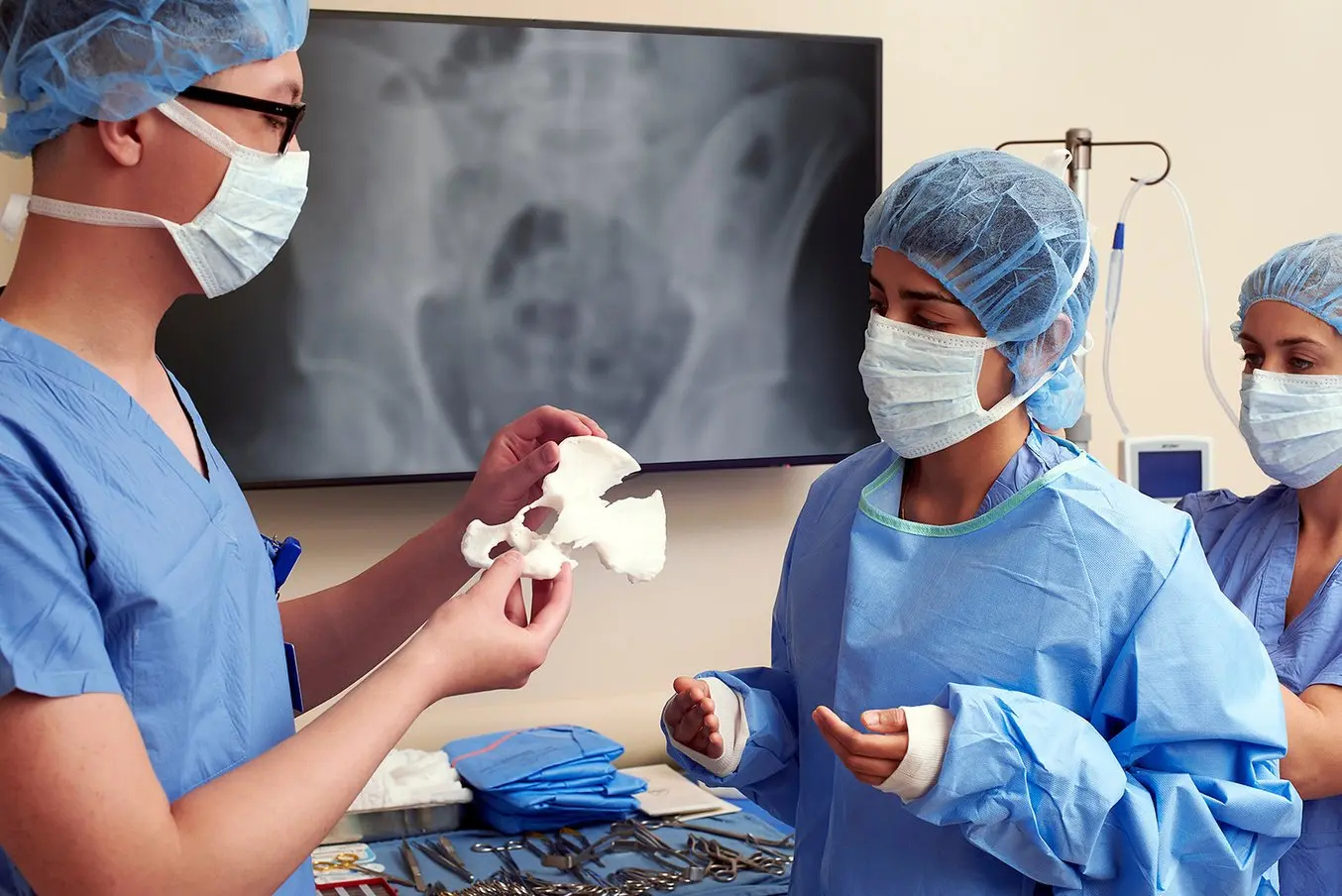
La medicina personalizzata e di precisione è in costante crescita. Nuovi strumenti e tecnologie avanzate avvicinano medici e pazienti, fornendo trattamenti e apparecchiature personalizzati in grado di fornire il miglior servizio possibile a ciascun individuo.
I progressi nel campo della tecnologia di stampa 3D per la medicina hanno dato un contributo fondamentale al settore sanitario in diversi ambiti. Ai pazienti, i nuovi strumenti e i nuovi metodi terapeutici sviluppati grazie alla stampa 3D possono offrire un maggior comfort e una maggior personalizzazione della cura. Questa tecnologia adesso accessibile permette ai medici una migliore comprensione dei casi complessi e fornisce nuovi strumenti in grado di garantire standard di cura più elevati.
In questo articolo vengono illustrate sei applicazioni della stampa 3D in medicina, dai dispositivi medici stampati in 3D fino ai modelli chirurgici specifici per i pazienti. Capirai perché professionisti e professioniste del settore sanitario sono entusiasti del potenziale di questa tecnologia e vedrai come varie tecniche di stampa 3D possono essere usate per applicazioni specifiche in ambito medico.
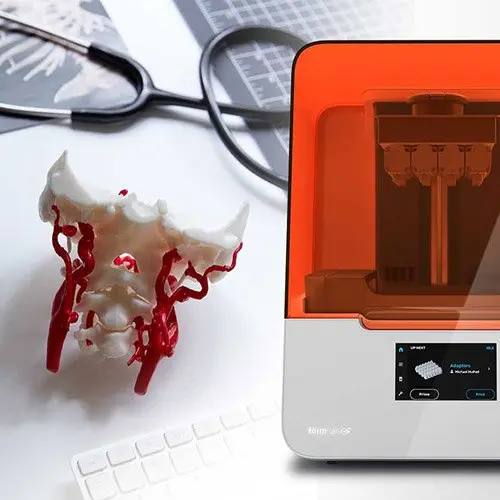
Introduzione alla stampa 3D in medicina
Unisciti a Formlabs per scoprire le buone pratiche per la stampa 3D in medicina, il nuovo ecosistema Formlabs Medical e numerosi nuovi prodotti per uso sanitario.
Stampa 3D nel settore sanitario
1. Modelli chirurgici su misura per i pazienti
I modelli anatomici stampati in 3D realizzati a partire dai dati del paziente stanno diventando strumenti sempre più utili nella pratica della medicina di precisione personalizzata. Via via che i casi diventano più complessi e che l'efficienza operatoria assume un ruolo sempre più importante nei casi di routine, l'uso di modelli di riferimento visivi e tattili può migliorare la comprensione e la comunicazione all'interno delle équipe mediche e con i pazienti.
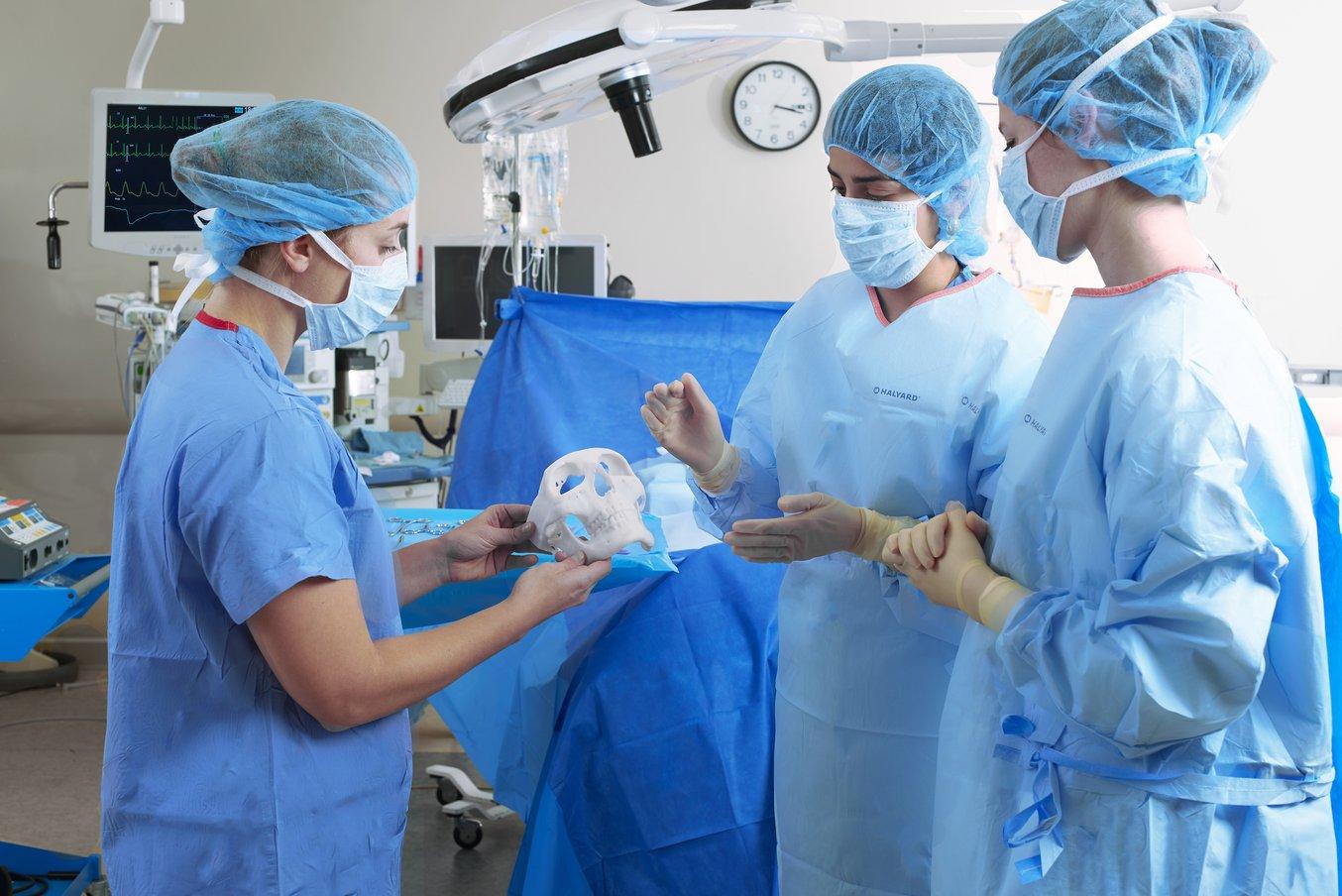
Come stampare modelli anatomici in 3D per la pianificazione preoperatoria e migliorare le possibilità di ottenere il consenso dei pazienti
Questo whitepaper presenta una procedura di guida rivolta ai team medici e tecnici per iniziare a stampare in 3D modelli anatomici a partire dalle scansioni dei pazienti. Inoltre, illustra le buone pratiche per configurare risonanze magnetiche o TAC, segmentare i dati e convertire i file in un formato stampabile in 3D.
Professioniste e professionisti sanitari, ospedali e istituti di ricerca di tutto il mondo si servono di modelli anatomici stampati in 3D come strumenti di riferimento in vari contesti: la pianificazione preoperatoria, la visualizzazione intraoperatoria e il dimensionamento o l'adattamento preventivo delle attrezzature mediche in interventi tanto di routine quanto complessi, come documentato da centinaia di pubblicazioni.
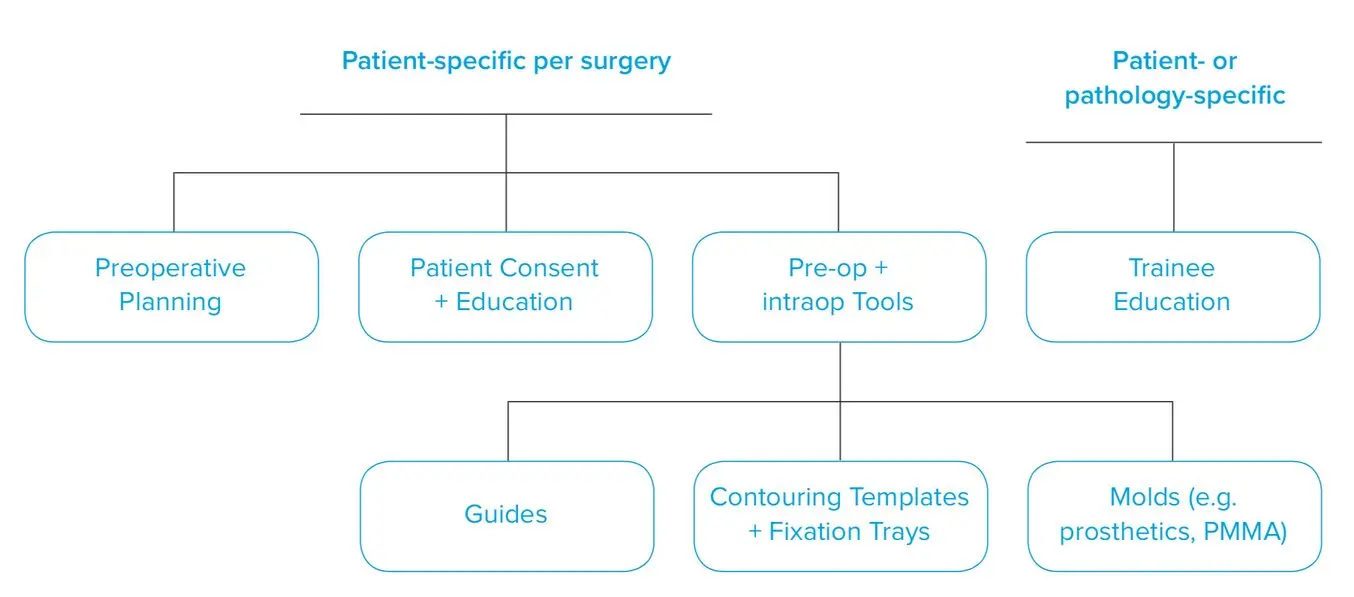
Realizzare modelli di riferimento tattili su misura per i pazienti a partire dai dati di TAC e risonanze magnetiche è facile e conveniente con la stampa 3D. La letteratura sottoposta a revisione paritaria dimostra che questi modelli forniscono una visualizzazione più approfondita, che permette ai team medici di prepararsi meglio agli interventi, riducendo drasticamente tempo e costi in sala operatoria e offrendo vantaggi per i pazienti in termini di soddisfazione, nonché di riduzione dell'ansia e dei tempi di recupero.
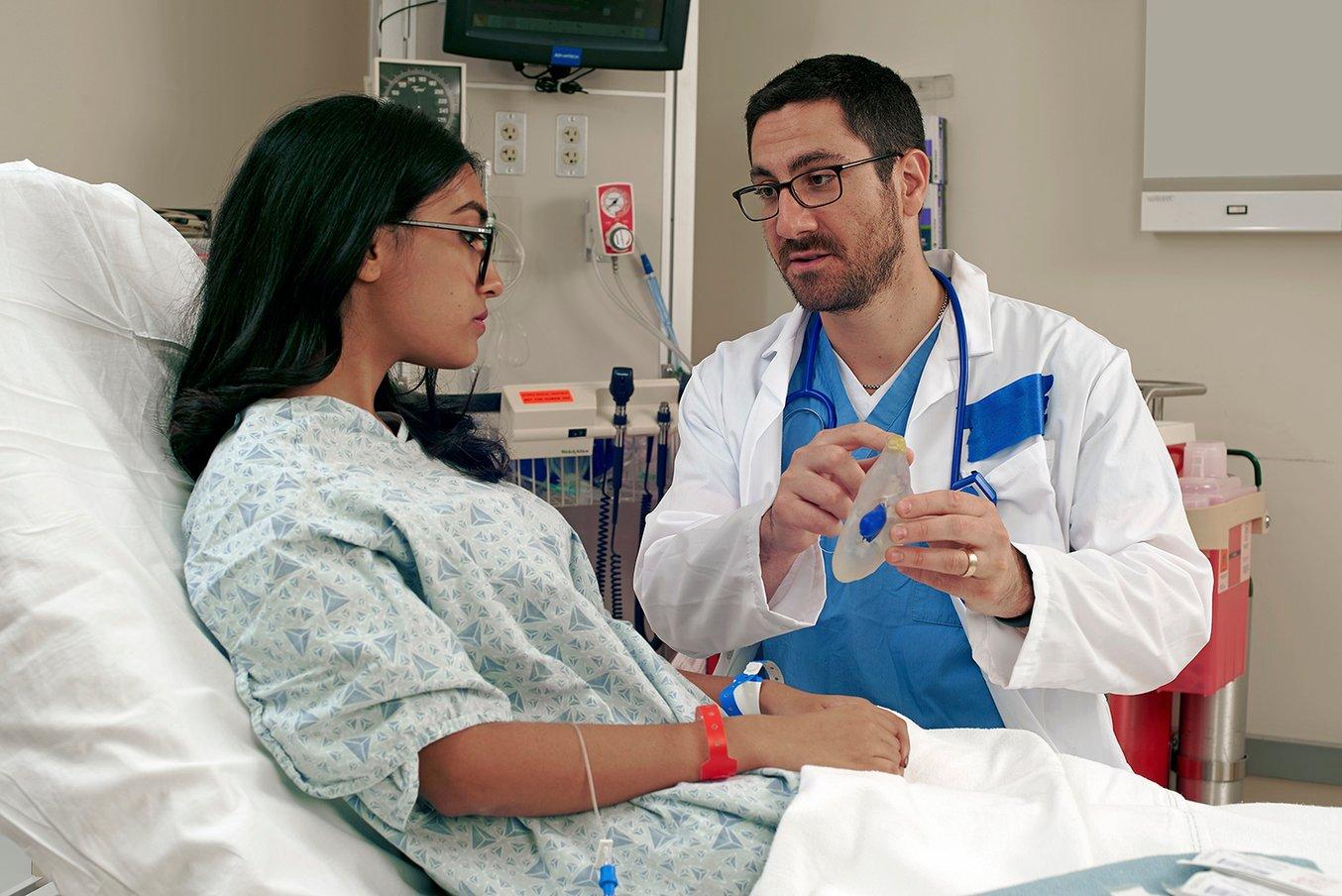
I medici possono usare modelli chirurgici su misura per spiegare la procedura ai pazienti prima dell'intervento, aumentando il loro consenso e riducendone l'ansia.
Imparare dai modelli preoperatori può anche influire sul corso del trattamento. È il caso dell'esperienza del dott. Michael Eames. Dopo aver riprodotto le ossa dell'avambraccio di un giovane paziente, il dott. Eames si è reso conto che la lesione era diversa da come pensava inizialmente.
Il medico ha quindi optato per una nuova procedura per i tessuti molli, molto meno invasiva, che ha ridotto la durata della riabilitazione e l'entità delle cicatrici. Servendosi della riproduzione dell'osso stampata in 3D, il dott. Eames ha illustrato la procedura chirurgica al paziente e ai genitori, ottenendone il consenso.
Il risultato? L'intervento è durato meno di 30 minuti, invece delle tre ore previste inizialmente. La durata inferiore dell'intervento ha portato a un risparmio stimato di 5500 $ per l'ospedale e ha fatto sì che il paziente potesse trascorrere meno tempo nel reparto di riabilitazione.
"Tutti i chirurghi ortopedici a tempo pieno e quasi la metà dei chirurghi part-time del San Francisco Veteran's Affairs Medical Center hanno utilizzato i modelli stampati in 3D per la cura dei pazienti. Abbiamo notato che la stampa 3D migliora le prestazioni nei momenti cruciali."
Dottor Alexis Dang, chirurgo ortopedico presso l'Università della California San Francisco (UCSF) e del San Francisco Veteran's Affairs Medical Center
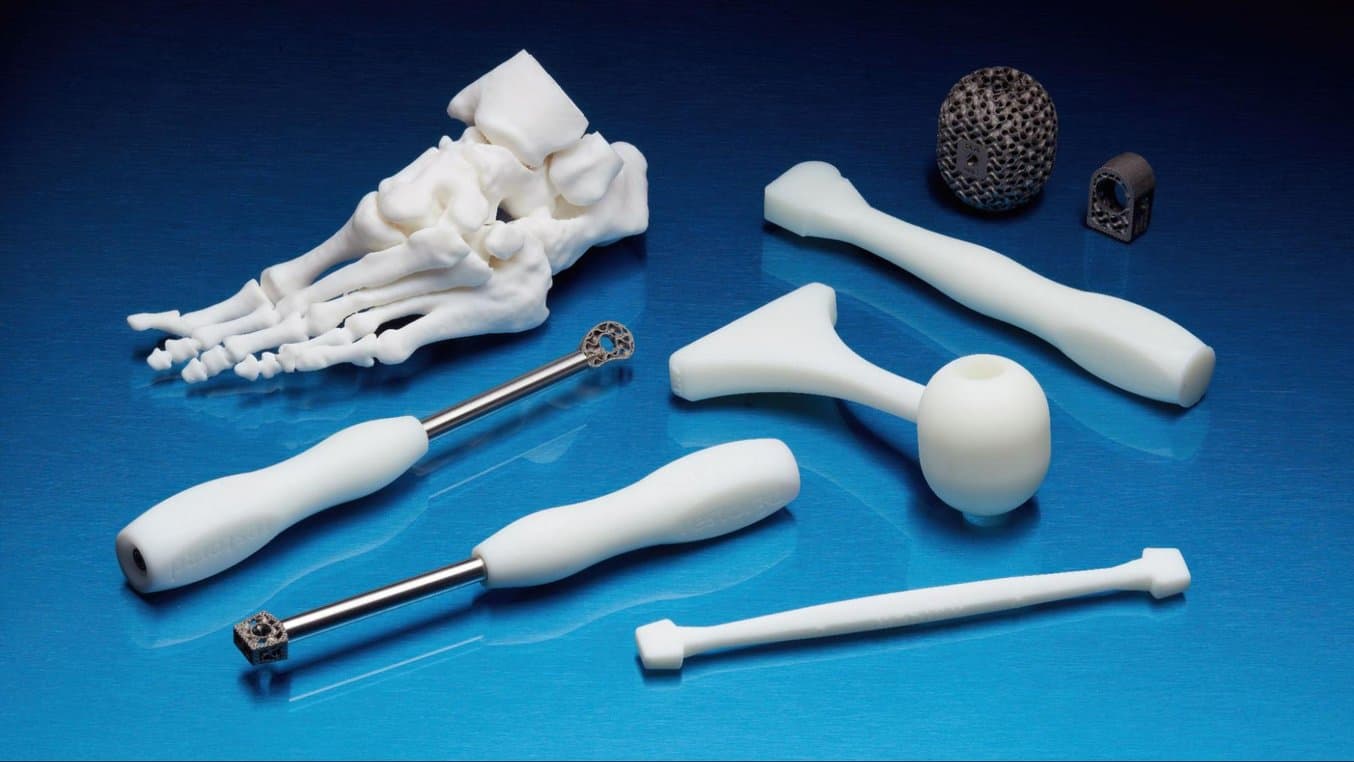
Chirurgia personalizzata grazie alla stampa 3D: domande e risposte con Insight Surgery (precedentemente 3D LifePrints)
Segui questa sessione di domande e risposte con 3D LifePrints sulla stampa 3D nel settore medico e scopri il metodo di lavoro innovativo e versatile che usano per la creazione di dispositivi medici su misura per i pazienti.
Il dott. Frederik Verstreken dell'ospedale AZ Monica nell'area di Anversa, in Belgio, è specializzato in chirurgia della mano, del polso e dell'avambraccio. Verstreken afferma che la combinazione di visualizzazione, pianificazione digitale e modelli anatomici stampati in 3D consente ai medici di risparmiare circa il 30-40% del tempo in sala operatoria. Nei casi complessi di osteotomia, a volte non era possibile ripristinare l'anatomia dei pazienti. Ma grazie i modelli chirurgici stampati in 3D, i medici possono prepararsi molto meglio all'intervento, ridurre l'esposizione dei pazienti alle radiazioni e ottenere comunque una precisione sostanzialmente migliore, che permette a chi subisce l'intervento di provare meno dolore e tornare a muoversi normalmente.
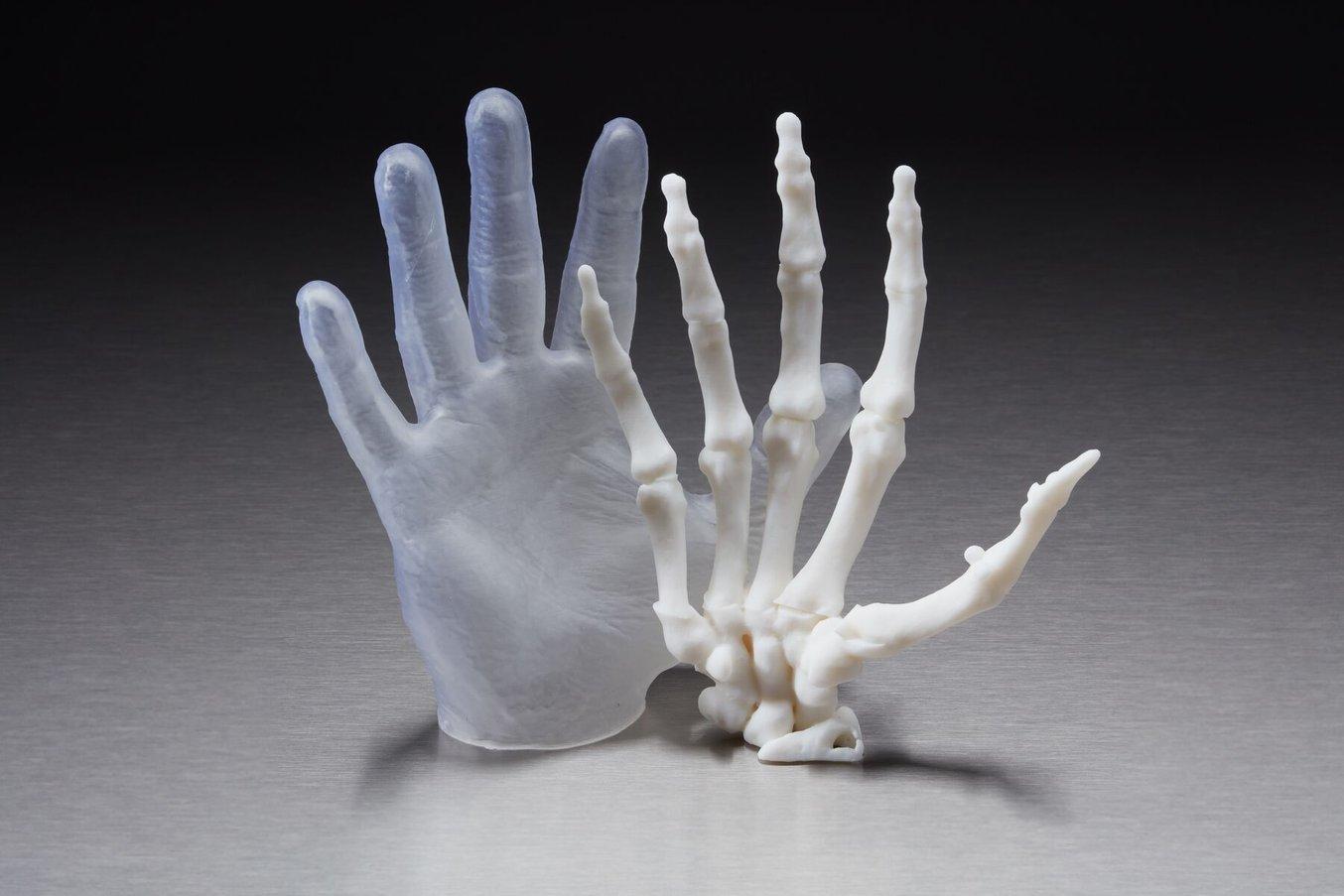
Modello anatomico di una mano, con tanto di "pelle" realizzata con un materiale di stampa 3D elastico.
Il dott. Todd Goldstein, docente presso il Feinstein Institute for Medical Research, non ha dubbi sull'importanza che la stampa 3D ha assunto nel suo dipartimento. Stima che se Northwell Health usasse i modelli stampati in 3D nel 10-15% dei casi, potrebbe risparmiare 1 750 000 $ all'anno.
Le dime aiutano i team chirurghi a comprendere meglio l'anatomia e la patologia proprie di ogni paziente, facilitando l'analisi dei rischi, la scelta dell'approccio migliore e la familiarizzazione con il caso prima dell'intervento. La scelta di materiali con specifiche proprietà, come l'elasticità, consente ai chirurghi di fare pratica con i modelli, riducendo la durata degli interventi e migliorando i risultati.
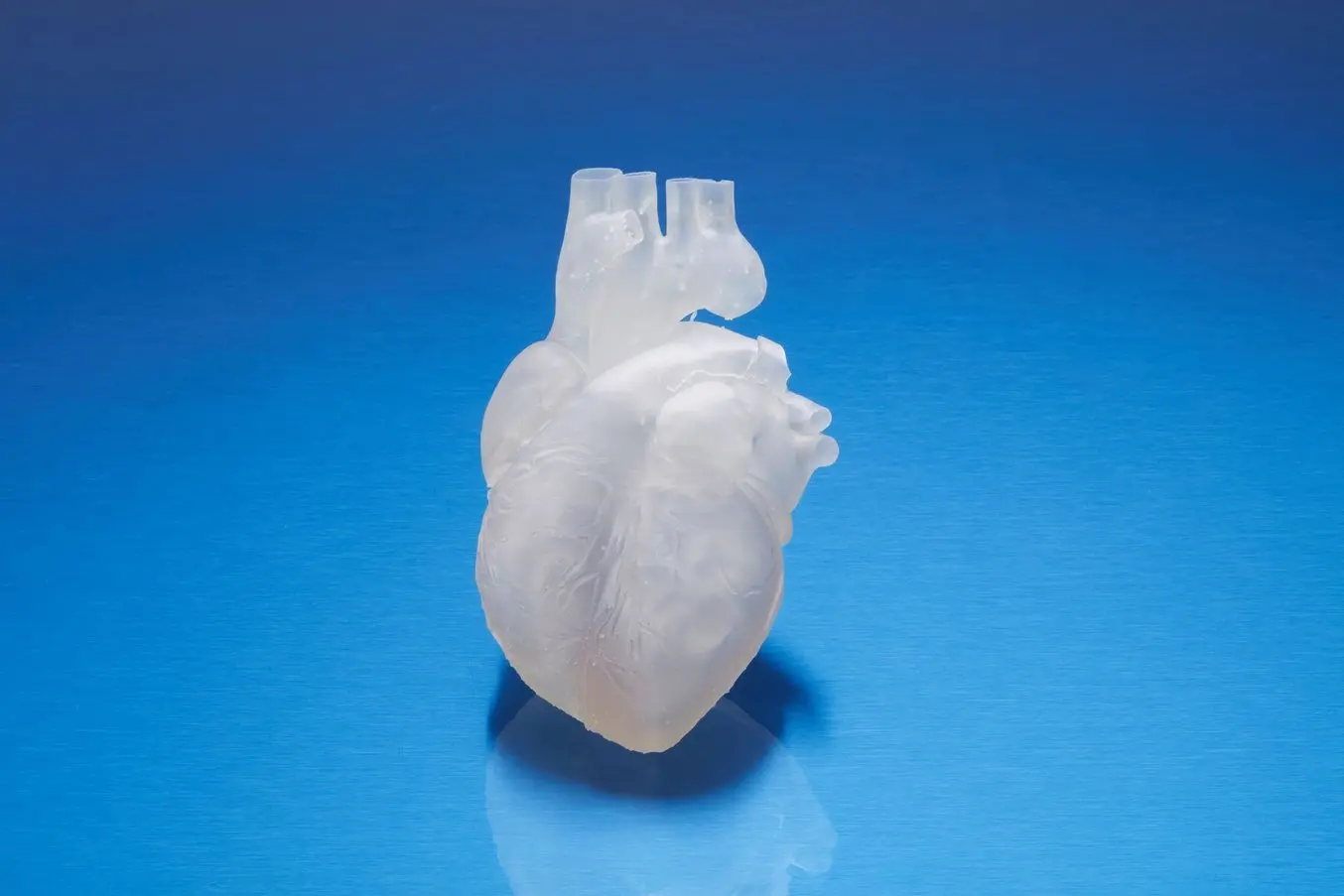
Elastomeri biocompatibili di Formlabs per modelli anatomici vascolari
Scopri come professioniste e professionisti del settore medico riescono a integrare materiali elastomerici e biocompatibili in workflow di stampa 3D innovativi utilizzando le nuove BioMed Flex 80A Resin e BioMed Elastic 50A Resin di Formlabs.
2. Strumenti chirurgici su misura per i pazienti
Nuovi materiali biocompatibili per la stampa 3D in medicina hanno permesso anche di sviluppare nuove tecniche e strumenti chirurgici, allo scopo di migliorare ulteriormente l'esperienza clinica in sala operatoria. I sistemi di strumentazione tradizionali vengono migliorati con fatica, comportano costi iniziali notevoli e presentano spesso complicazioni nello svolgimento del workflow chirurgico. Le stampanti 3D e i materiali biocompatibili rendono più semplice e conveniente la creazione di impianti, guide di taglio e strumenti chirurgici specifici per gli interventi e spesso anche per i singoli pazienti.
Le dime chirurgiche personalizzate stampate in 3D aiutano i chirurghi a comprendere meglio l'anatomia e la patologia proprie di ogni paziente, facilitando l'analisi dei rischi, la scelta dell'approccio migliore e la familiarizzazione con il caso prima dell'intervento. Guide di taglio ben progettate permettono di ridurre le tempistiche associate a ogni caso e di diminuire il tempo di utilizzo dei sistemi di navigazione intraoperatori. Ne consegue una minore esposizione dei pazienti alle radiazioni, nonché una durata ridotta degli interventi.
"Le dime ci indicano dove praticare i fori e i tagli, in modo che la placca venga applicata nella posizione corretta. Questi strumenti ci permettono una precisione di gran lunga migliore. Inoltre, risparmiamo almeno il 50% del tempo rispetto alle procedure a mano libera."
Frederik Verstreken, chirurgo della mano e del polso presso l'ospedale AZ Monica
I tempi di produzione brevi della stampa 3D permettono di eseguire le iterazioni dei design in modo rapido. I feedback dei chirurghi possono essere implementati velocemente prima di ristampare lo strumento o la dima chirurgica.
restor3d ha l'obiettivo di fornire i giusti strumenti a chirurghi e operatori sanitari che riparano e ricostruiscono il corpo umano, incentivando l'innovazione nella chirurgia di precisione. L'azienda sfrutta le capacità della stampa 3D per apportare un miglioramento radicale nelle cure chirurgiche tramite la stampa di impianti in metallo e strumentazioni polimeriche specifiche per gli interventi e spesso anche per i singoli pazienti.
restor3d si è affermata come azienda leader nell'uso della stampa 3D per promuovere l'innovazione nelle sale operatorie. Il suo kit di pianificazione preoperatorio leader del settore, gli impianti innovativi ad alta precisione e le soluzioni complete fornite dal kit di strumentazione hanno aiutato gli ospedali a ridurre i costi e a migliorare l'esperienza dei pazienti.
"Riceviamo continuamente feedback dai chirurghi. La stampa 3D ci consente di eseguire rapidamente iterazioni dei design in base ai loro riscontri, fornendo nuove soluzioni in tempi brevi."
Nathan Evans, vicedirettore senior del dipartimento di sviluppo del prodotto, restor3d
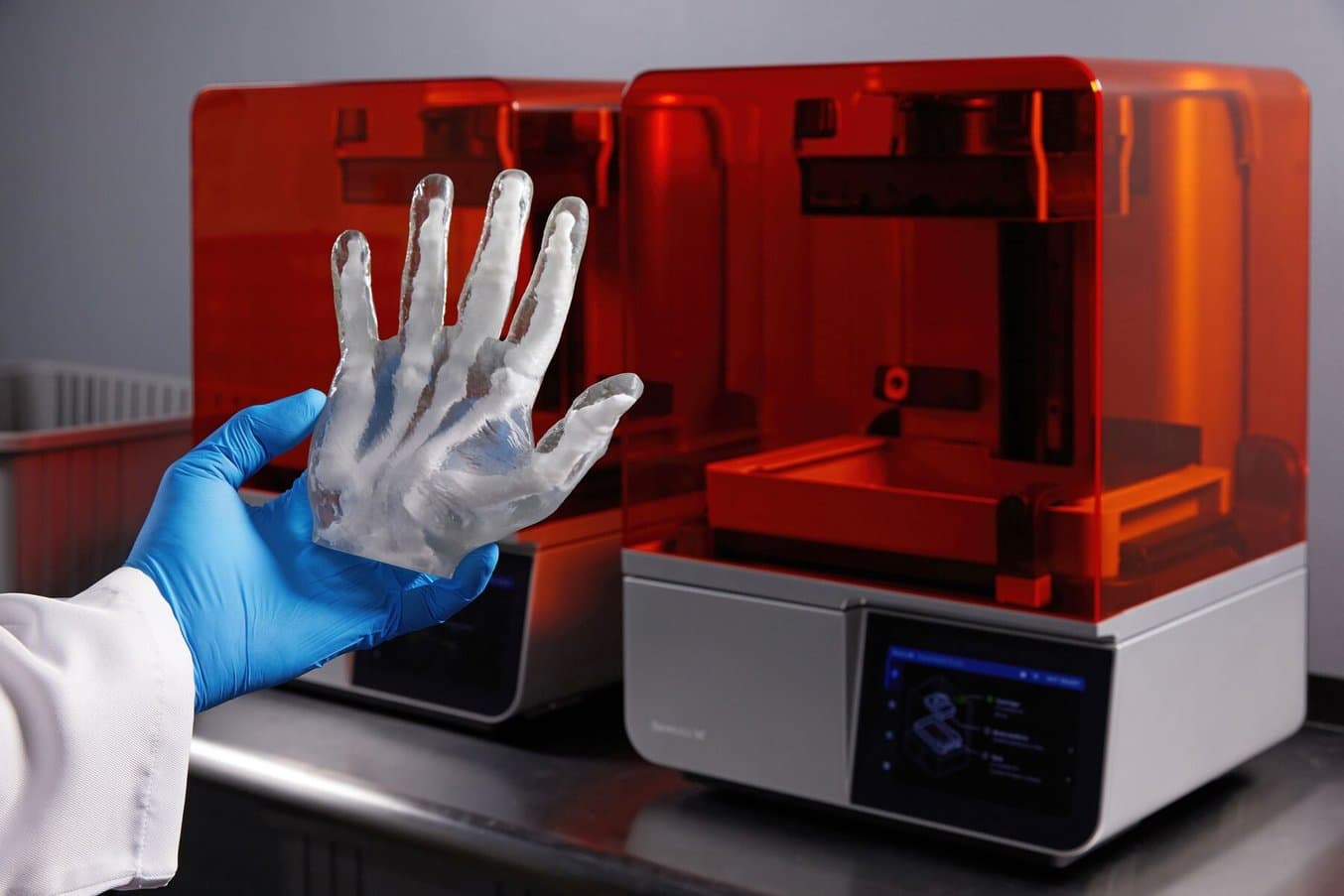
Resine biocompatibili Formlabs: guida completa alla scelta dei materiali più adatti
Attualmente Formlabs offre oltre 40 materiali unici per la stampa 3D stereolitografica (SLA). In questo whitepaper vengono confrontati i materiali biocompatibili presenti nel nostro catalogo per guidare l'utente nella scelta di quello più idoneo per le proprie applicazioni mediche.
3. Nuovi dispositivi medici
La stampa 3D di fatto è diventata sinonimo di prototipazione rapida. La facilità di utilizzo e i costi ridotti della stampa 3D in-house hanno anche rivoluzionato lo sviluppo dei prodotti: molte aziende che realizzano strumenti per il settore medico hanno adottato questa tecnologia per creare nuovi dispositivi e strumenti chirurgici.
Oltre il 90% delle 50 migliori aziende produttrici di dispositivi medici usa la stampa 3D per creare prototipi accurati dei dispositivi, così come dime e fissaggi per semplificare i test, nonché per stampare direttamente dispositivi in 3D.
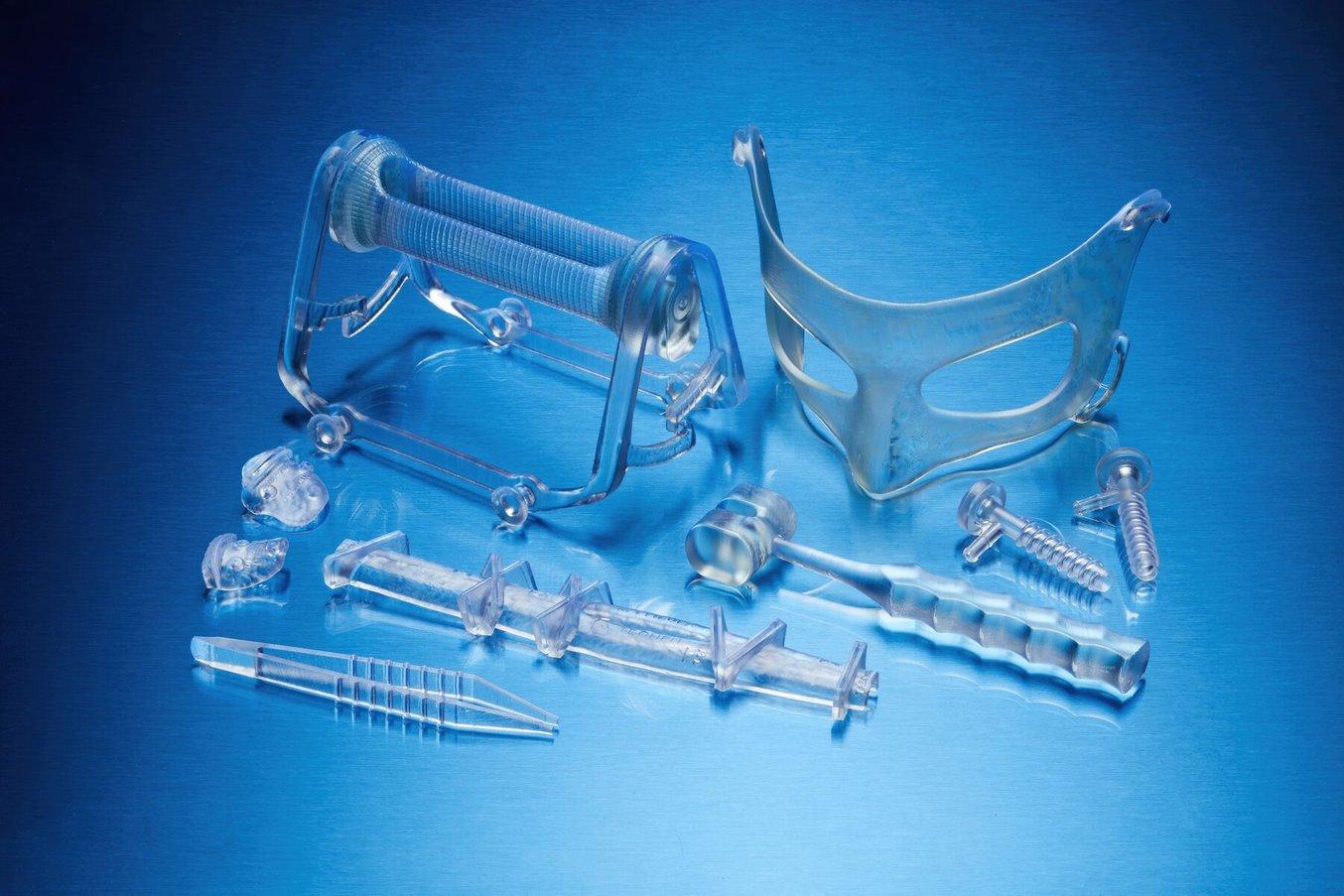
Sviluppare una nuova azienda di dispositivi medici con la produzione additiva di Formlabs
Ascolta l'esperienza di tre startup che hanno sviluppato una nuova attività e lanciato il loro primo dispositivo medico. Scopri perché hanno scelto di integrare le soluzioni Formlabs nei loro processi e come hanno usato la produzione additiva.
"Prima di adottare [la stampante 3D di Formlabs], in DJO Surgical facevamo affidamento quasi esclusivamente su fornitori esterni per la stampa dei prototipi. Oggi usiamo quattro apparecchi Formlabs e l'impatto è stato enorme. Il ritmo della stampa 3D è duplicato, i costi sono stati ridotti del 70% e il livello di dettaglio della stampa consente una comunicazione chiara del design con i chirurghi ortopedici."
Alex Drew, ingegnere di progettazione meccanica presso DJO Surgical
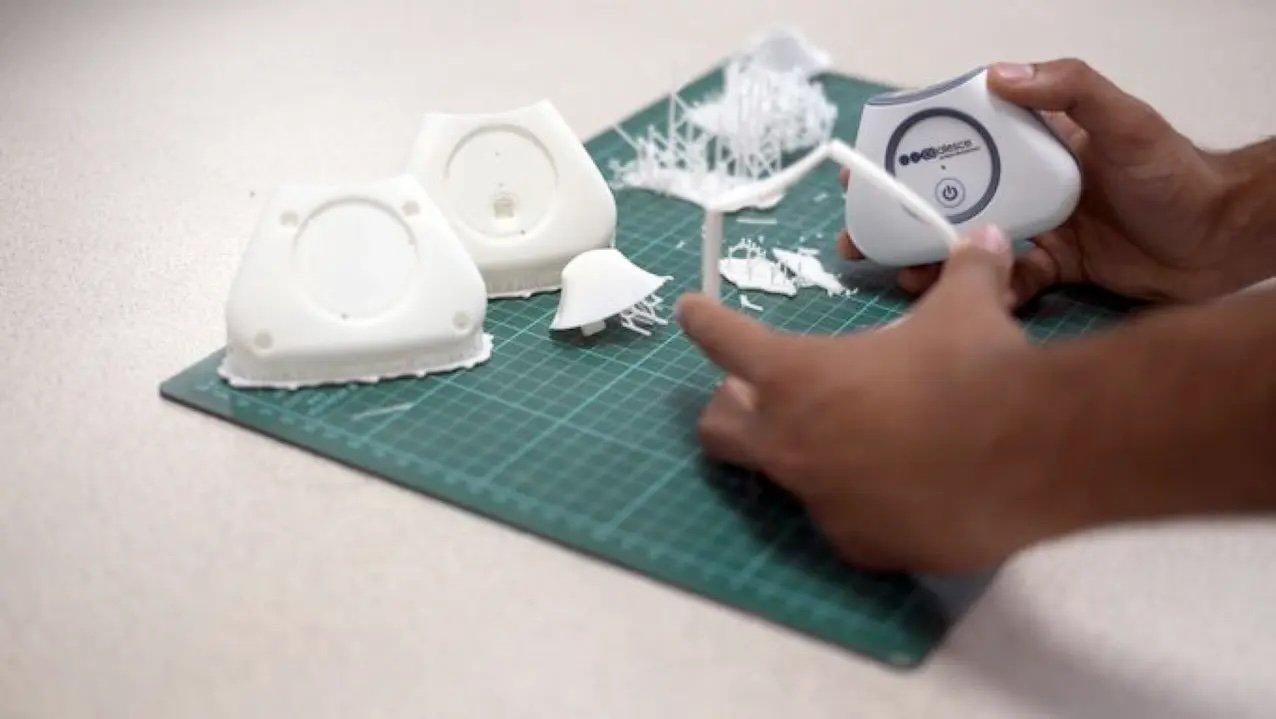
Aziende produttrici di dispositivi medici come Coalesce usano la stampa 3D per creare prototipi di dispositivi accurati.
La stampa 3D può velocizzare la progettazione, permettendo di completare l'iterazione di modelli complessi nel giro di pochi giorni anziché di settimane. Quando Coalesce è stata incaricata di creare un inalatore in grado di valutare digitalmente il profilo del flusso inspiratorio in individui asmatici, l'affidamento della stampa a fornitori esterni avrebbe comportato lunghi tempi di realizzazione per ogni prototipo. I file dei progetti avrebbero dovuto essere perfezionati con cura attraverso varie iterazioni successive prima di essere inviati all'esterno per la realizzazione.
La stampa 3D SLA desktop, invece, ha permesso a Coalesce di mantenere l'intero processo di prototipazione in-house. I prototipi erano adatti all'utilizzo in studi clinici ed erano identici al prodotto finito, al punto che, quando venivano mostrati ai clienti, questi li scambiavano per il dispositivo vero e proprio.
In generale, la produzione in-house ha comportato una riduzione dell'80-90% dei tempi di realizzazione dei prototipi. E, cosa più importante, è stato possibile stampare le parti in sole otto ore e rifinirle e verniciarle nel giro di pochi giorni, mentre le stesse operazioni affidate a fornitori esterni avrebbero richiesto una settimana o due.
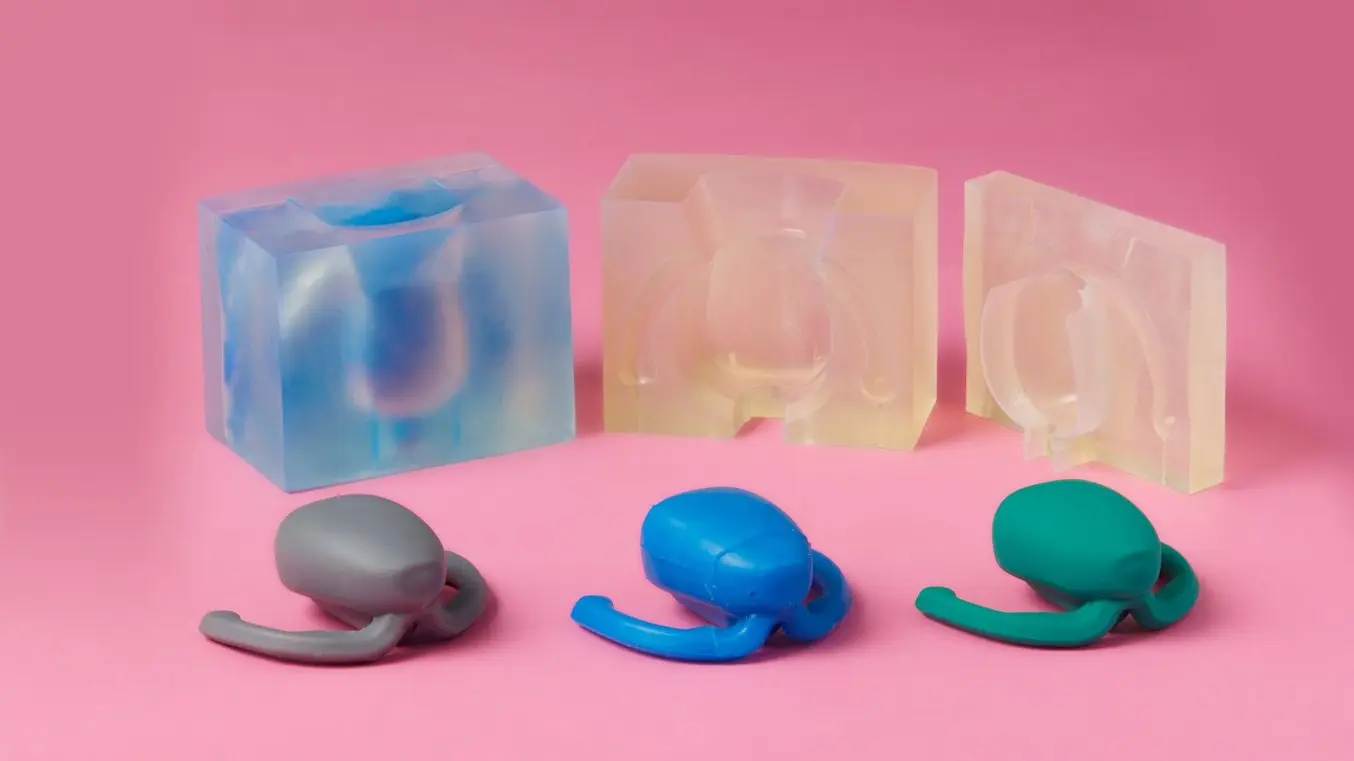
Creazione di dispositivi medici in silicone
Questa guida consente di scegliere il miglior metodo per la produzione di parti in silicone a seconda dell'uso previsto e fornisce istruzioni dettagliate per la stampa 3D con la Silicone 40A Resin, nonché per lo stampaggio in silicone mediante attrezzature realizzate in 3D tramite SLA, tra cui stampi a iniezione in due parti, sovrastampi e stampi a compressione.
Shavini Fernando ha utilizzato la stampa 3D per sviluppare OxiWear, un accessorio indossabile al di sopra dell'orecchio in grado di monitorare le funzioni vitali e segnalare eventuali emergenze. Il suo team ha sfruttato la stampa 3D SLA sia per la realizzazione di prototipi del dispositivo che per la creazione di dime statiche dissipative.
Fernando racconta: "Per un'azienda come la nostra, che sta ancora muovendo i primi passi, la stampa 3D in-house è stata una grande novità: ci ha permesso di ridurre notevolmente i costi durante il processo di sviluppo e di testare più design di prototipi contemporaneamente. Prima della stampa 3D, ogni esternalizzazione di un prototipo ci costava circa 200 €, mentre con la Form 3B stampiamo un dispositivo con pochi centesimi.”
4. Protesi personalizzate accessibili e avanzate
Circa 50 milioni di persone in tutto il pianeta hanno subito un'amputazione in seguito a un trauma fisico. L'ingresso nel mondo delle protesi può risultare doloroso per chi si sta riprendendo da un'emergenza medica. La maggior parte delle persone desidera poter tornare a guidare un'auto, allenarsi in palestra, occuparsi della casa e così via. Ma molte delle protesi tradizionali sono rudimentali, costose e fragili. Al giorno d'oggi, solo il 10% delle persone che necessitano di un braccio protesico avanzato può permettersi questa spesa.
Le protesi semplici sono disponibili solo in una gamma ridotta di dimensioni, quindi i pazienti devono accontentarsi di quella che si adatta meglio. Al contrario, i dispositivi bionici su misura, progettati per riprodurre i movimenti e le prese degli arti e in cui il controllo delle funzioni dipende dai muscoli rimasti alla persona, sono talmente costosi che possono permetterseli solo i pazienti che dispongono di una buona assicurazione sanitaria nei Paesi più sviluppati. Questo problema riguarda in particolare le protesi per bambini e bambine: man mano che crescono, inevitabilmente le loro protesi diventano troppo piccole e richiedono costose sostituzioni. Il principale ostacolo è la mancanza di processi produttivi in grado di creare parti su misura a un prezzo accessibile. Ma sempre più spesso i protesisti possono servirsi dell'ormai nota libertà di design offerta dalla stampa 3D per superare queste barriere finanziarie.
PSYONIC, azienda nota per aver creato la Ability Hand, sta cercando di rivoluzionare il mercato. Progettata e prodotta in-house con metodi di produzione ibrida, la Ability Hand si propone di far tornare i pazienti alla loro vita di sempre. PSYONIC utilizza la stampa 3D per realizzare prototipi rapidi, aumentare l'accessibilità economica e creare parti per utilizzo finale durature con materiali resistenti che sopportano gli urti.
Iniziative come e-NABLE consentono a intere comunità in tutto il mondo di formarsi nella realizzazione delle protesi stampate in 3D. Condividendo gratuitamente online le informazioni e i modelli opensource, stanno favorendo la nascita di un movimento indipendente di produzione protesica che permette ai pazienti di ottenere una protesi su misura a un prezzo di appena 50 €.
Altri inventori, come Lyman Connor, si spingono ancora oltre. Con appena quattro stampanti 3D desktop a disposizione, Lyman ha potuto ultimare e adattare le prime protesi da lui prodotte. Il suo obiettivo finale? Creare una mano bionica personalizzabile vendibile a una frazione del prezzo di una protesi avanzata, che di norma si aggira attorno alle decine di migliaia di euro.
Anche i ricercatori del MIT hanno identificato nella stampa 3D uno strumento perfetto per la realizzazione di protesi con alloggiamenti più confortevoli.
Non occorre dire che il basso costo di realizzazione di queste protesi, oltre alla libertà offerta dal design personalizzato, si è rivelato un fattore decisivo. Le protesi realizzate con la stampa 3D possono essere consegnate in sole due settimane, e il costo per i test e la manutenzione è molto inferiore rispetto a quello delle controparti tradizionali.
Poiché i costi continuano a diminuire e le proprietà dei materiali a migliorare, la stampa 3D avrà senza dubbio un ruolo sempre più importante in questo ambito sanitario.
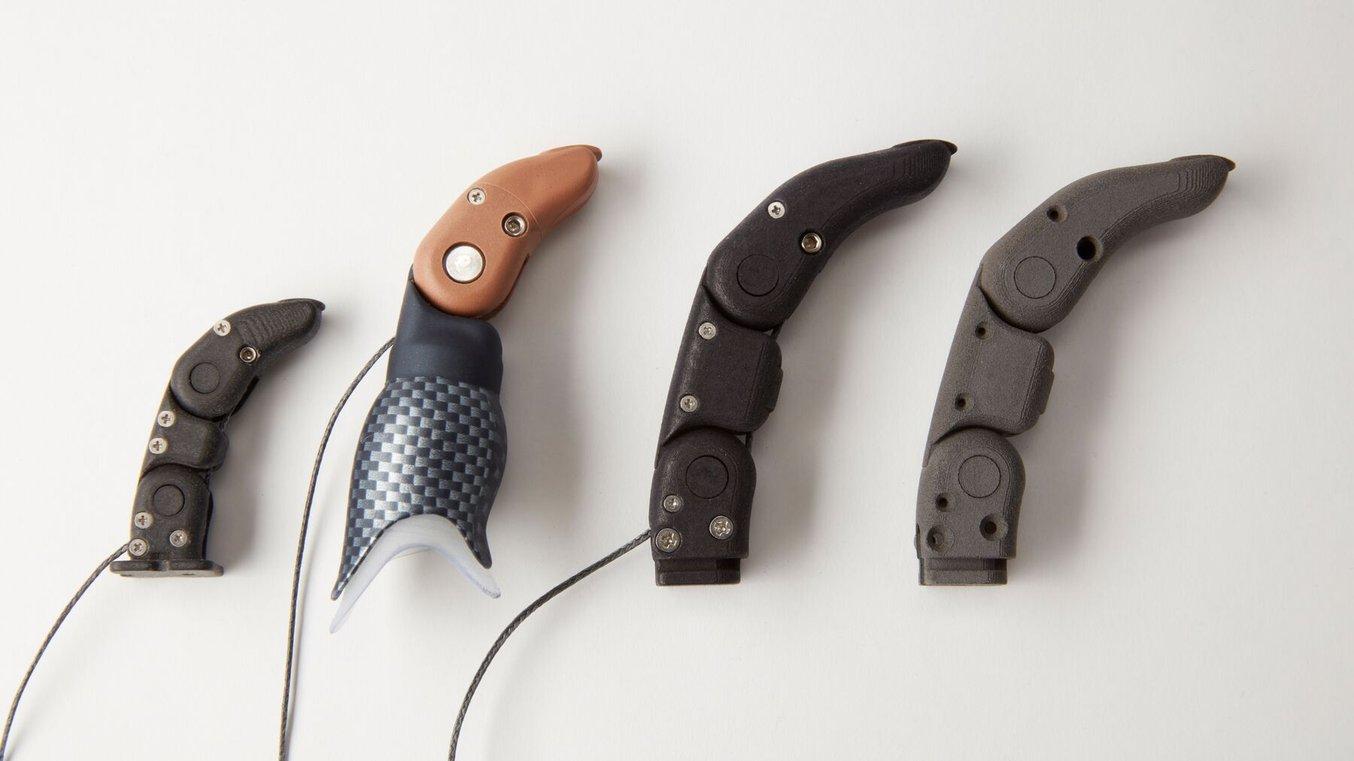
La stampa 3D nel settore dei plantari e delle protesi
Questo whitepaper è un'introduzione all'utilizzo della stampa 3D per la creazione di plantari e protesi di nuova generazione.
5. Plantari personalizzati
Molte delle barriere finanziarie del settore protesico riguardano inoltre la produzione di plantari. Come molti altri dispositivi medici creati su misura, anche i plantari personalizzati spesso hanno un costo proibitivo e la loro realizzazione richiede settimane o mesi. Ma con la stampa 3D le cose sono cambiate.
Molti professionisti e professioniste del settore sanitario stanno adottando questa tecnologia per produrre soluzioni ortopediche personalizzate. Seguendo workflow testati, la stampa 3D permette di risparmiare tempo e risorse, consentendo la realizzazione in tempi record di plantari su misura.
I workflow digitali per la realizzazione di plantari personalizzati comprendono nuove opzioni di test, produzione e progettazione pensate per ridurre i costi di personalizzazione e velocizzare i cicli di produzione, con conseguenti tempi di consegna ridotti, dispositivi con una migliore aderenza e risultati ottimizzati per i pazienti. I plantari stampati in 3D sono una soluzione efficace che consente una personalizzazione rapida e conveniente.
Kriwat GmbH, azienda medica specializzata in ortopedia con sede a Kiel, in Germania, ha dovuto far fronte alla carenza di personale specializzato. In aggiunta, i workflow tradizionali riempivano il loro laboratorio di polvere e vapori chimici. Per risolvere questi problemi, Lais Kriwat, tecnico esperto in calzature ortopediche, ha sviluppato un workflow digitale per la produzione di solette utilizzando due stampanti SLS Fuse 1+ 30W e la Nylon 11 Powder.
Il workflow digitale ha permesso di ridurre i costi associati alla manodopera e ai materiali. Kriwat ha stimato che i costi di produzione sono diminuiti di circa il 15-17% grazie alla stampa 3D. Questa tecnologia ha inoltre permesso di velocizzare la produzione e di conseguenza di occuparsi di un maggior numero di pazienti. "Ora abbiamo la possibilità di creare un plantare con un'aderenza perfetta nel giro di 24 ore", afferma Lais Kriwat.
Le possibilità offerte dalla libertà di design della stampa 3D SLS includono la ridistribuzione del carico durante la camminata, nonché la creazione di singoli prodotti esclusivi, di supporti impossibili da produrre con metodi tradizionali e di prodotti più sottili che forniscono comunque un sostegno ottimale per il piede in sport come la corsa e il calcio.
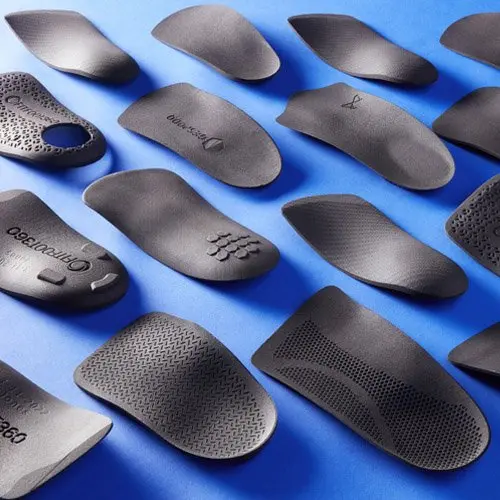
Stampa 3D di solette parziali rigide con la Fuse 1+ 30W e la Nylon 11 Powder
In questo studio vengono analizzate le proprietà dei materiali e i metodi di produzione di solette personalizzate: la Fuse 1+ 30W e la Nylon 11 Powder di Formlabs, la 3D HR PA 11 di HP e il polipropilene prodotto in modo tradizionale.
Matej e suo figlio Nik sono un esempio dell'efficacia dei plantari personalizzati stampati in 3D. Nato prematuro nel 2011, a seguito di un parto difficile Nik è stato colpito da una paralisi cerebrale, una condizione che interessa quasi venti milioni di persone al mondo. Matej ha trovato stimolante la salda determinazione di suo figlio a superare i limiti della propria condizione, ma doveva scegliere tra ortesi standard prefabbricate, che sarebbero state inadeguate e scomode per suo figlio, o una costosa soluzione personalizzata, che avrebbe richiesto settimane o mesi di realizzazione, per poi diventare rapidamente obsoleta con la crescita del bambino.
Perciò ha deciso di prendere in mano la situazione e cercare soluzioni alternative per risolvere il problema. Grazie alla libertà offerta dalle tecnologie digitali, fra cui la scansione e la stampa 3D, i fisioterapisti di Matej e Nik hanno potuto sperimentare liberamente e sviluppare un flusso di lavoro assolutamente innovativo per realizzare ortesi per caviglia e piede.
Le ortesi su misura stampate in 3D hanno fornito a Nik esattamente il sostegno, il comfort e la correzione di cui aveva bisogno, aiutandolo a muovere i primi passi da solo. Questi dispositivi ortesici personalizzati hanno lo stesso grado di adattamento di quelli più costosi, ma a una frazione del prezzo e senza bisogno di ulteriori regolazioni.
Grazie alla stampa 3D è possibile produrre plantari specifici per i pazienti con workflow semplificati che consentono di risparmiare tempo e denaro. Ne conseguono diversi vantaggi per i pazienti: minor numero di visite, tempi di consegna rapidi e massima personalizzazione per un maggiore comfort. Rispetto ai metodi di produzione tradizionali, i workflow di stampa 3D permettono di risparmiare tempo e materiali, diminuendo al contempo le spese e creando un ambiente di lavoro più confortevole.
6. Biostampa, ingegneria tissutale, organi stampati in 3D e molto altro
La biostampa 3D consiste nell'uso di processi di produzione additiva per depositare materiali chiamati bioinchiostri e creare strutture simili ai tessuti che possono essere utilizzate in campo medico. L'ingegneria tissutale ricorre alle diverse tecnologie in via di sviluppo, fra cui la biostampa, per creare in laboratorio tessuti e organi sostitutivi da usare nella cura di lesioni e malattie.
Nel campo della ricerca, la biostampa viene usata per creare tessuti e organi in laboratorio, grazie ai quali si possono compiere progressi nella medicina rigenerativa e nei test di sicurezza. Inoltre, la realizzazione di organi tramite biostampa può aumentare notevolmente le probabilità di successo dei trapianti. Usando cellule prelevate dagli stessi pazienti, la biostampa elimina la possibilità di rigetto da parte del sistema immunitario, che oggi è un problema serio delle procedure tradizionali di trapianto di organi.
Presso l'Università di Osaka, i team di ricerca hanno usato un supporto di stampa e un inchiostro a base di cellule per creare forme specifiche, tra cui un naso. Una volta stampate, le cellule rimangono attive fino a due settimane, il che rappresenta un passo notevole nella creazione di organi sviluppati in laboratorio.
Attualmente, per rigenerare la pelle e guarire le lesioni è necessario ricorrere a dolorosi trapianti di pelle, ma la possibilità di stampare quest'ultima rappresenterebbe una valida alternativa per raggiungere questi obiettivi. Nel 2023, il team di ricerca del Wake Forest Institute for Regenerative Medicine ha utilizzato la biostampa per realizzare una pelle a tutto spessore che si è rivelata capace di rigenerare del tutto la pelle in seguito al trapianto in un contesto preclinico.
Il dott. Atala, principale autore della pubblicazione, ha affermato che questi risultati dimostrano che la realizzazione di una pelle umana a tutto spessore è possibile e favorisce una guarigione più rapida e risultati estetici più naturali.
Gli scienziati del Terasaki Institute for Biomedical Innovation hanno sviluppato un bioinchiostro per la stampa capace di favorire la formazione del tessuto muscoloscheletrico. L'obiettivo di questa tecnologia è aiutare le persone che hanno subito una perdita o una lesione muscolare.
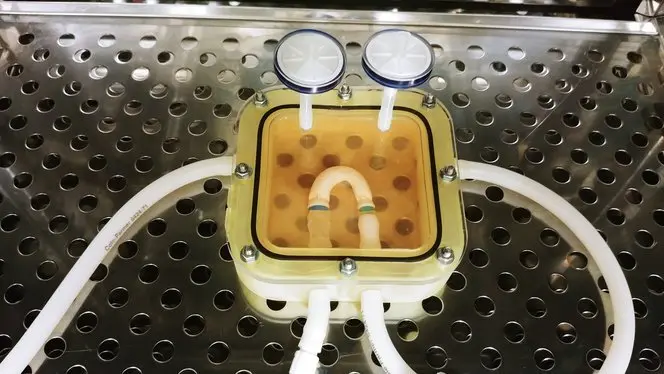
Camera di un bioreattore stampata in 3D in cui si sta sviluppando un'aorta in miniatura realizzata mediante ingegneria tissutale. Il tessuto riprodotto viene coltivato nel bioreattore per acquisire le proprietà meccaniche e biologiche del tessuto organico.
La stampa 3D si è rivelata in grado di rispondere alla sfida di produrre vasi sanguigni sintetici, risolvendo le difficoltà legate all'esatta riproduzione delle forme, delle dimensioni e delle geometrie. La capacità di adattare perfettamente le soluzioni stampate alle esigenze specifiche dei pazienti si è dimostrata cruciale.
Come ha dichiarato il dott. Pashneh-Tala: "[La creazione di vasi sanguigni attraverso la stampa 3D] può potenzialmente offrire migliori opzioni chirurgiche, e perfino produrre vasi sanguigni su misura per i pazienti. Senza poter sfruttare la precisione e l'affidabilità offerte dalla stampa 3D, creare queste forme non sarebbe possibile."
La biostampa sta evolvendo in fretta, grazie al lavoro dei team di ricerca che continuano a spingersi oltre i limiti del possibile. Tramite la riproduzione di ossa, sangue, pelle e muscoli, gli sviluppi della biostampa stanno spianando la strada a futuri miglioramenti nella cura dei pazienti.
Stampa 3D in ambito medico
Nell'ambito della stampa 3D per il settore medico, non tutti i metodi sono uguali: è importante scegliere la tecnologia più adatta a ogni specifico caso d'uso.
Tra le tecnologie di stampa 3D più note in ambito medico vi sono la stereolitografia (SLA), la sinterizzazione laser selettiva (SLS) e la modellazione a deposizione fusa (FDM), che si usano per le parti in plastica, nonché la sinterizzazione laser diretta dei metalli (DMLS) e la fusione laser selettiva (SLM) per i metalli.
Stereolitografia (SLA)
Le stampanti SLA utilizzano un laser per polimerizzare la resina liquida, trasformandola in plastica indurita: questo processo viene chiamato fotopolimerizzazione. La stereolitografia è uno dei processi più apprezzati dai professionisti del settore medico grazie alla precisione, alla versatilità e all'alta risoluzione dei materiali.
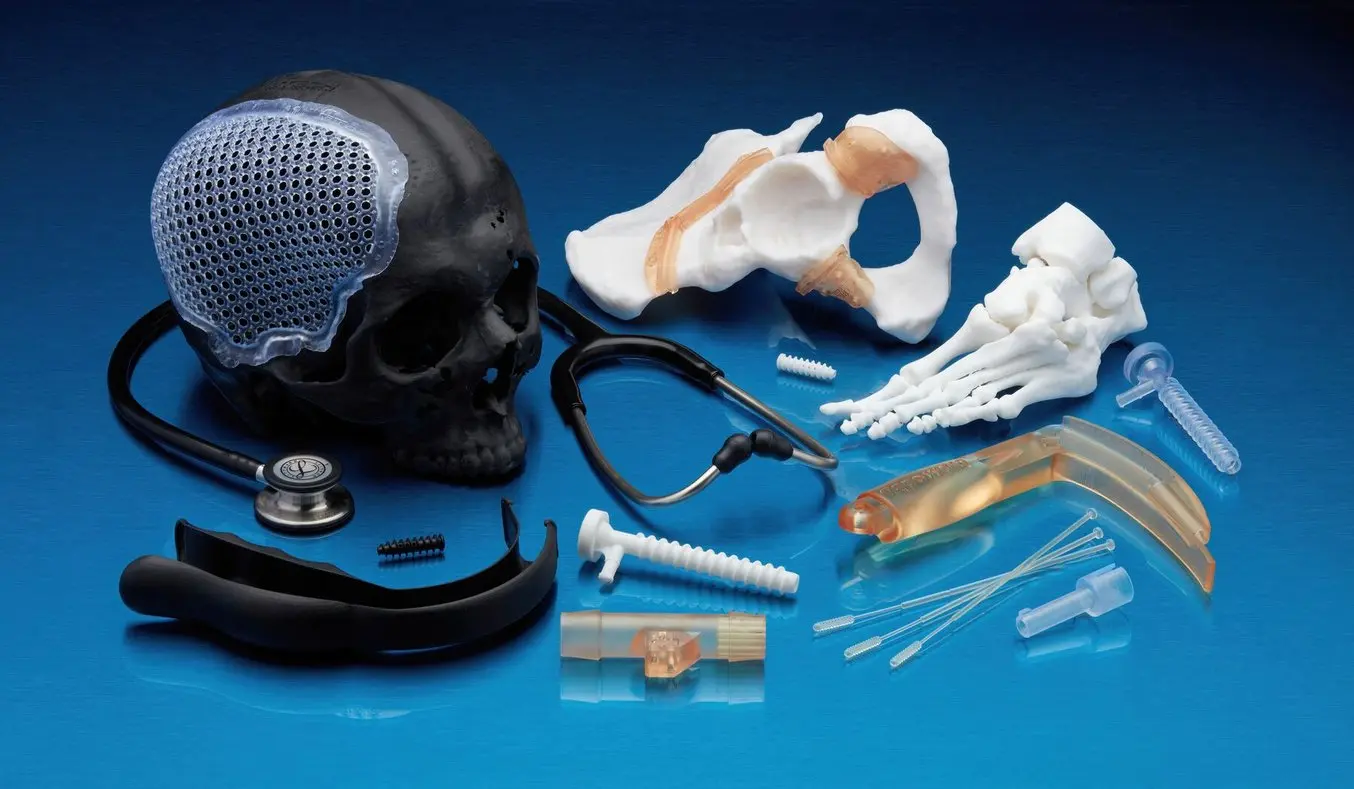
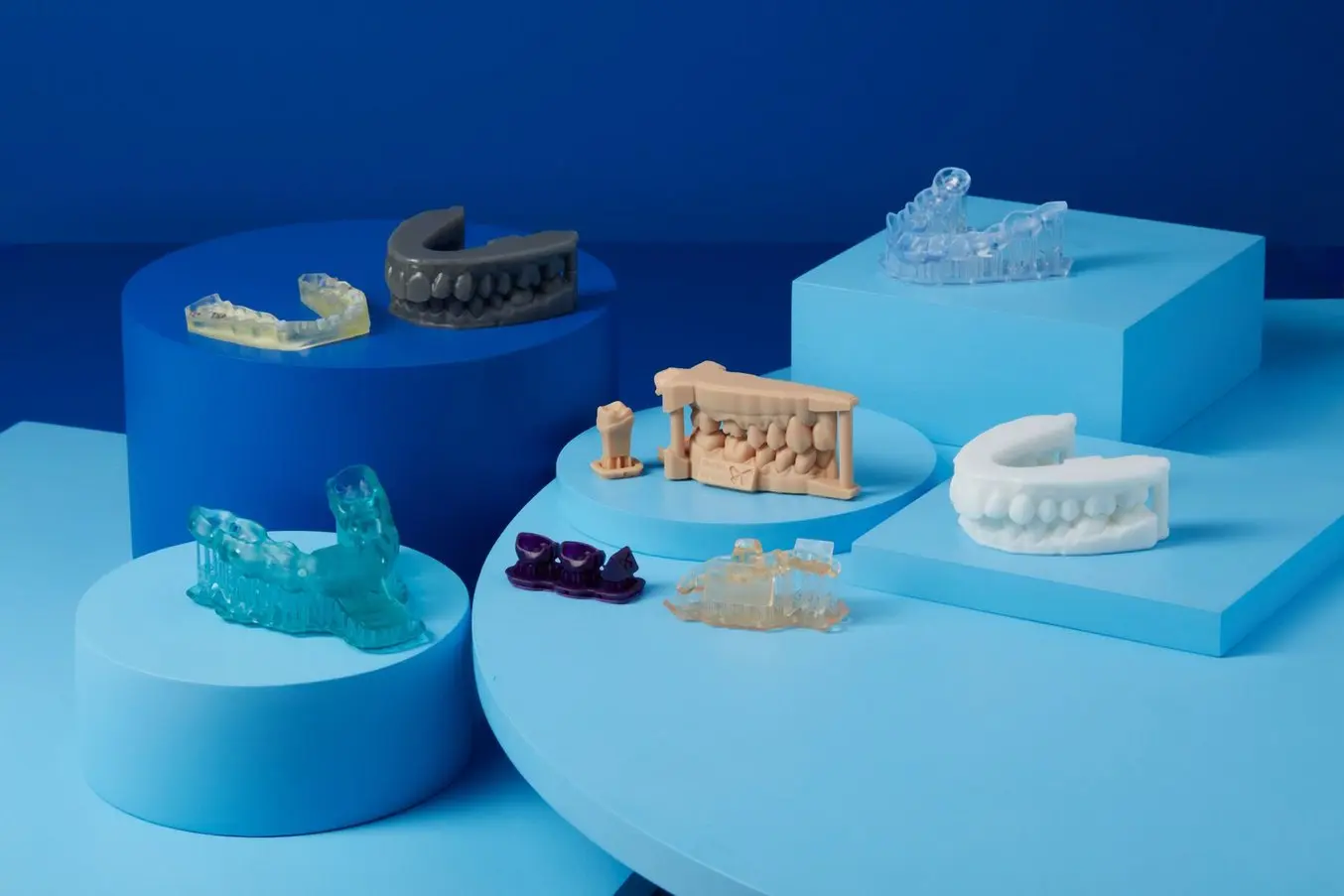
La stampa 3D SLA offre un'ampia gamma di materiali tra cui scegliere, inclusi materiali biocompatibili per una grande varietà di applicazioni mediche e odontoiatriche.
Vantaggi della stereolitografia
Le parti stampate in stereolitografia presentano una migliore risoluzione e accuratezza, dettagli più precisi e finiture superficiali più lisce rispetto a tutte le altre tecnologie di stampa 3D. Il vantaggio principale della SLA rimane comunque la sua versatilità. La formulazione delle resine per stereolitografia offre un'ampia gamma di proprietà ottiche, meccaniche e termiche in grado di imitare quelle delle termoplastiche industriali, standard e ingegneristiche.
La stereolitografia è un'ottima scelta per modelli anatomici e prototipi di dispositivi medici estremamente dettagliati che richiedono tolleranze ridotte e superfici lisce, nonché per stampi, attrezzature, modelli e parti per utilizzo finale funzionali. La stereolitografia offre inoltre la più ampia gamma di materiali biocompatibili per applicazioni mediche e odontoiatriche, come strumenti chirurgici e apparecchi medici destinati al contatto con la pelle o le membrane mucose.
Svantaggi della stereolitografia
L'ampia versatilità della stereolitografia si accompagna a una fascia di prezzo leggermente più alta rispetto alla modellazione a deposizione fusa, ma rimane comunque più economica di tutti gli altri processi di stampa 3D. Dopo la stampa, le parti in resina ottenute tramite stereolitografia richiedono inoltre una post-elaborazione, che comprende il lavaggio e la polimerizzazione post-stampa delle parti.

Richiedi un campione gratuito
Guarda e tocca con mano la precisione della stereolitografia Formlabs. Saremo lieti di inviare presso la tua azienda un campione gratuito.
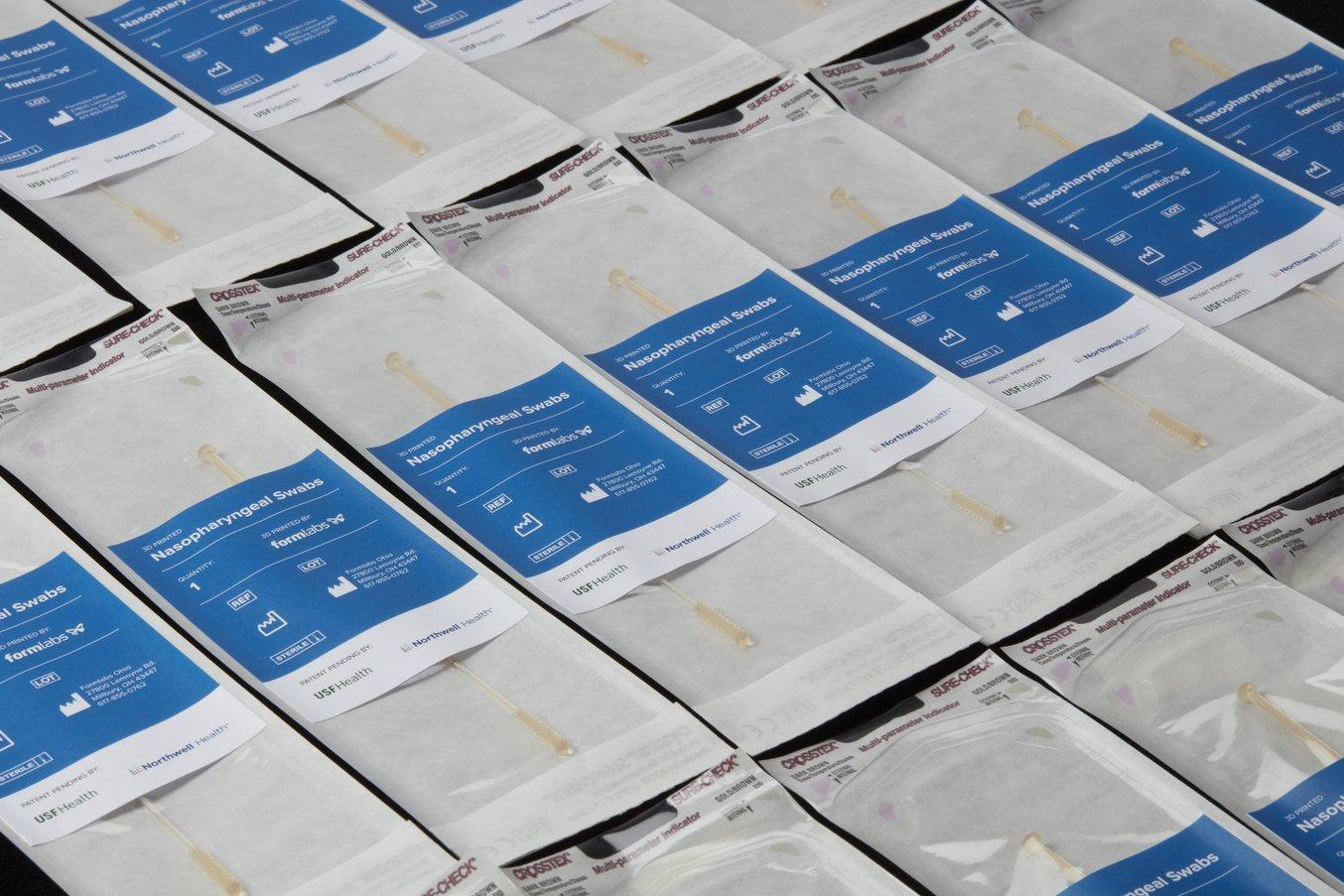
Guida di Formlabs per la gestione del controllo di qualità nella stereolitografia per innovatori del settore sanitario
Questa guida è destinata a professionisti del settore sanitario e illustra le misure da adottare per garantire, monitorare e migliorare la qualità delle parti stampate in 3D tramite stereolitografia.
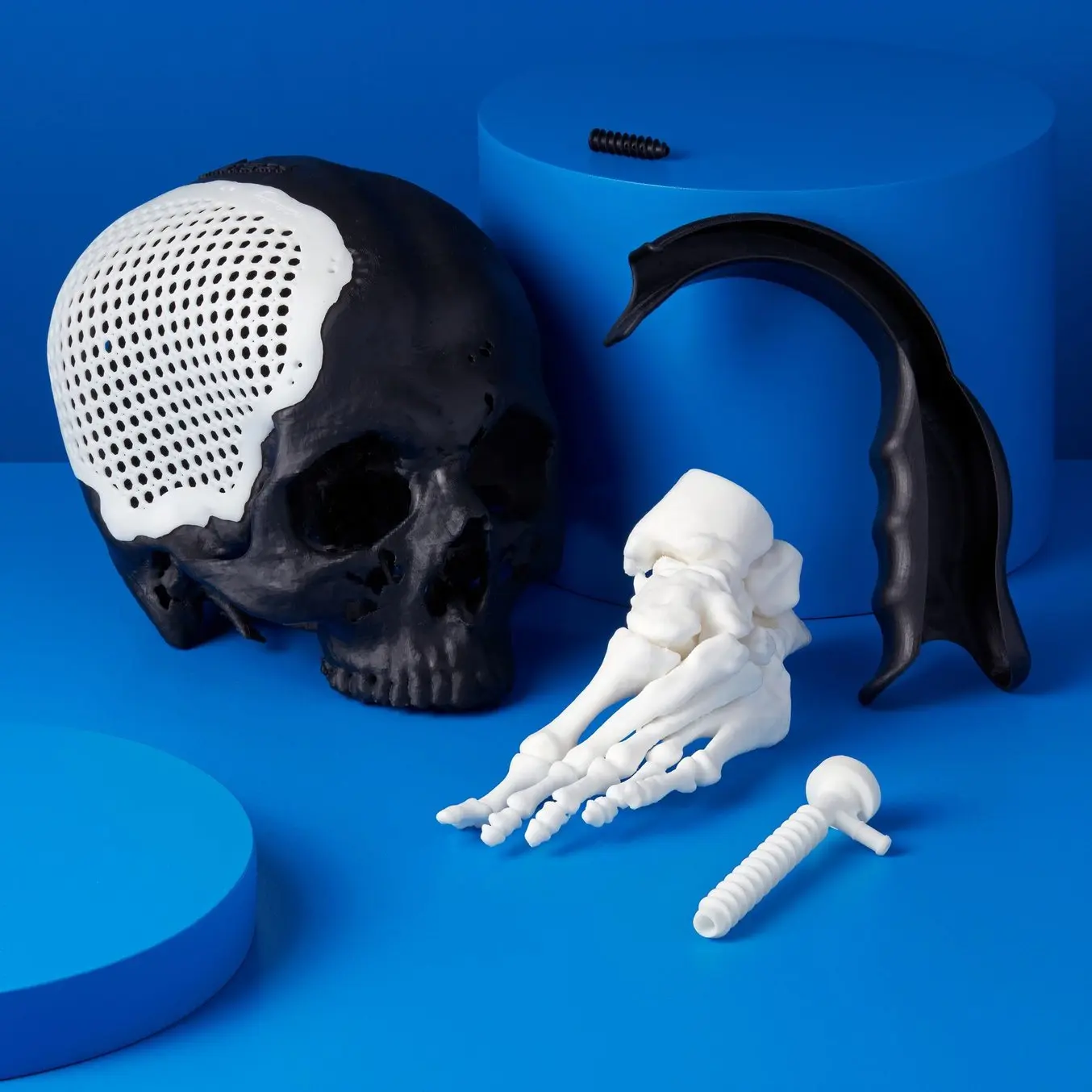
Dispositivi medici stampati in 3D per la chirurgia di precisione: prospettive cliniche, commerciali e normative
Unisciti a Formlabs e Nelson Labs per approfondire il tema della biocompatibilità, con esperti del settore che ti introdurranno ai nostri nuovi materiali e alle buone pratiche per produrre dispositivi medici.
Sinterizzazione laser selettiva (SLS)
Le stampanti 3D SLS utilizzano un laser ad alta potenza per fondere piccole particelle di polvere di polimeri. La polvere non fusa sostiene la parte durante il processo di stampa ed elimina la necessità di strutture di supporto dedicate, una caratteristica che rende la sinterizzazione laser selettiva particolarmente efficace per la realizzazione di parti meccaniche complesse.
Grazie alla sua capacità di produrre parti con ottime proprietà meccaniche, la sinterizzazione laser selettiva è la tecnica di produzione additiva polimerica più comune per le applicazioni industriali. A seconda del materiale scelto, le parti SLS possono anche essere biocompatibili e sterilizzabili, il che le rende ideali per la produzione di dispositivi medici, prototipi, dime chirurgiche, dispositivi indossabili e plantari.
Vantaggi della sinterizzazione laser selettiva
La sinterizzazione laser selettiva (SLS) non richiede strutture di supporto specifiche ed è ideale per figure geometriche complesse, inclusi dettagli interni, sottosquadri, pareti sottili e dettagli in negativo. Le parti prodotte con la stampa SLS hanno caratteristiche meccaniche eccellenti, con una resistenza simile a quella delle parti create con stampaggio a iniezione.
La combinazione di costo ridotto per parte, alta produttività, materiali testati e biocompatibilità rende la sinterizzazione laser selettiva una scelta molto comune adottata dalle aziende di dispositivi medici per la prototipazione funzionale.
Svantaggi della sinterizzazione laser selettiva
Le stampanti SLS, rispetto a quelle FDM e SLA, richiedono un investimento iniziale più alto. Nonostante siano disponibili molti materiali per la sinterizzazione laser selettiva, la gamma tra cui scegliere è comunque più limitata rispetto alla stereolitografia. Le parti escono dalla stampante con una finitura superficiale leggermente ruvida e per renderle lisce è necessario sottoporle a post-elaborazione, ad esempio tramite sabbiatura.

La stampa 3D SLS è ideale per ottenere prototipi funzionali robusti, nonché parti per utilizzo finale come protesi e plantari.
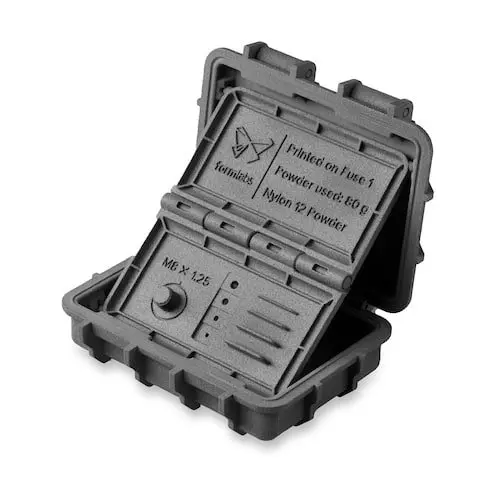
Richiedi un campione gratuito
Guarda e tocca con mano la qualità della stampa SLS di Formlabs. Saremo lieti di inviare presso la tua azienda un campione gratuito.
Modellazione a deposizione fusa (FDM)
La stampa 3D FDM, nota anche come fabbricazione a fusione di filamento (FFF), è un metodo di stampa che permette di creare parti fondendo ed estrudendo un filamento termoplastico, che viene poi depositato sull’area di stampa dall’ugello della stampante, strato per strato.
È la forma di stampa 3D più diffusa tra i consumatori, soprattutto grazie a un numero crescente di hobbisti e hobbiste. Ma le stampanti FDM industriali sono diffuse anche tra i professionisti.
Vantaggi della modellazione a deposizione fusa
La modellazione a deposizione fusa può essere utilizzata con un’ampia gamma di termoplastiche standard, come ad esempio l’acrilonitrile-butadiene-stirene (ABS), l’acido polilattico (PLA) e le loro varie miscele. Questo comporta un costo contenuto per l’investimento iniziale e i materiali. La modellazione a deposizione fusa è più adatta ai modelli Proof-of-Concept semplici e alla prototipazione a basso costo di parti semplici. Alcuni materiali FDM sono anche biocompatibili.
Svantaggi della modellazione a deposizione fusa
La modellazione a deposizione fusa offre una risoluzione e una precisione inferiori rispetto ad altre tecniche di stampa 3D per le plastiche come la stereolitografia o la sinterizzazione laser selettiva. Questo vuol dire che non è l'opzione più adatta per la stampa di design complessi o parti con dettagli elaborati, come i modelli anatomici. Per ottenere una finitura di qualità superiore sono necessari lenti processi di lucidatura meccanica e chimica, che richiedono molta manodopera. Alcune stampanti 3D FDM industriali utilizzano supporti solubili per ridurre al minimo queste problematiche e offrire una vasta gamma di termoplastiche ingegneristiche, ma hanno un costo decisamente elevato. Inoltre, quando si realizzano parti di grandi dimensioni, la stampa FDM tende a essere più lenta della stereolitografia o della sinterizzazione laser selettiva.
Sinterizzazione laser diretta dei metalli (DMLS) e fusione laser selettiva (SLM)
Le stampanti 3D a sinterizzazione laser diretta dei metalli (DMLS) e a fusione laser selettiva (SLM) hanno un funzionamento simile alle stampanti SLS, ma anziché servirsi dei polimeri, usano un laser per fondere insieme particelle di polvere di metallo strato dopo strato.
Le stampanti 3D DMLS e SLM sono in grado di creare prodotti in metallo robusti, precisi e complessi, il che rende questa tecnica ideale per svariate applicazioni mediche.
Vantaggi della sinterizzazione laser diretta dei metalli e della fusione laser selettiva
Il più grande vantaggio di questi processi è costituito naturalmente dai materiali, perché le stampanti 3D DMLS ed SLM sono in grado di produrre dispositivi medici per utilizzo finale ad alte prestazioni e componenti metallici. Questi processi possono riprodurre geometrie complesse e i prodotti finali sono robusti, resistenti e biocompatibili. Possono inoltre essere usati per produrre impianti generici (per ginocchia, anche, colonna vertebrale, ecc.) e impianti personalizzati per il trattamento di tumori o di traumi, nonché per protesi dentali e per prodotti tecnologici medici e ortopedici.
Svantaggi della sinterizzazione laser diretta dei metalli e della fusione laser selettiva
Anche se i prezzi delle stampanti 3D per il metallo hanno iniziato ad abbassarsi, con costi che vanno da 200 000 $ a oltre un milione di dollari, risultano ancora proibitivi per la maggior parte delle aziende. I processi di stampa 3D in metallo hanno inoltre un workflow complesso e impegnativo.
In alternativa, la stampa 3D SLA è adatta a workflow di fusione dei metalli per la creazione di parti in metallo a costi ridotti, con una maggiore libertà di design e tempi di realizzazione inferiori rispetto ai metodi tradizionali.
Stampanti 3D per il settore medico a confronto
Stereolitografia (SLA) | Sinterizzazione laser selettiva (SLS) | Modellazione a deposizione fusa (FDM) | Stampa 3D in metallo (DMLS, SLM) | |
---|---|---|---|---|
Volume di stampa | Fino a 300 x 335 x 200 mm (stampanti 3D desktop e da banco) | Fino a 165 x 165 x 300 mm (stampanti 3D da banco industriali) | Fino a 300 x 300 x 600 mm (stampanti 3D desktop e da banco) | Fino a 400 x 400 x 400 mm (DMLS/SLM industriali di grande formato) |
Fascia di prezzo | Le stampanti desktop professionali partono da 2399 €, le stampanti da banco di grande formato sono disponibili a partire da 8999 €, mentre le macchine industriali per volumi elevati sono acquistabili a partire da 80 000 €. | I sistemi da banco industriali partono da 23 899 €, mentre le stampanti industriali tradizionali sono disponibili a partire da 100 000 €. | I prezzi delle stampanti 3D economiche e dei relativi pacchetti partono da poche centinaia di euro. Le stampanti desktop di fascia media di maggiore qualità partono da 2000 €, mentre i sistemi industriali sono disponibili a partire da 15 000 €. | A partire da 200 000 €. |
Materiali | Varietà di resine (plastiche termoindurenti). Standard, ingegneristiche (simil-ABS, simil-polipropilene, flessibili, resistenti al calore), colabili, dentali e mediche (biocompatibili). Puro silicone e ceramica. | Termoplastiche ingegneristiche (compresi materiali biocompatibili). Nylon 11, nylon 12, compositi di nylon rinforzati con vetro o carbonio, PP, TPU (elastomero). | Termoplastiche standard, ad esempio ABS, PLA e loro miscele. | Acciaio inossidabile, acciaio per strumenti, titanio, cobalto cromato e alluminio. |
Applicazioni ideali | Modelli anatomici (biocompatibili), strumenti chirurgici (biocompatibili), dispositivi medici (biocompatibili), apparecchi dentali (biocompatibili), supporti di produzione, parti per utilizzo finale, attrezzature e prototipi creati in modo rapido. | Modelli anatomici (biocompatibili), strumenti chirurgici (biocompatibili), dispositivi medici (biocompatibili), plantari e protesi, supporti di produzione, parti per utilizzo finale, attrezzature e prototipi creati in modo rapido. | Modelli Proof-of-Concept semplici. Prototipi di parti semplici a basso costo. | Parti robuste e resistenti con geometrie complesse, impianti, protesi dentali, componenti medici e ortopedici in metallo. |
Materiali per la stampa 3D nel settore medico
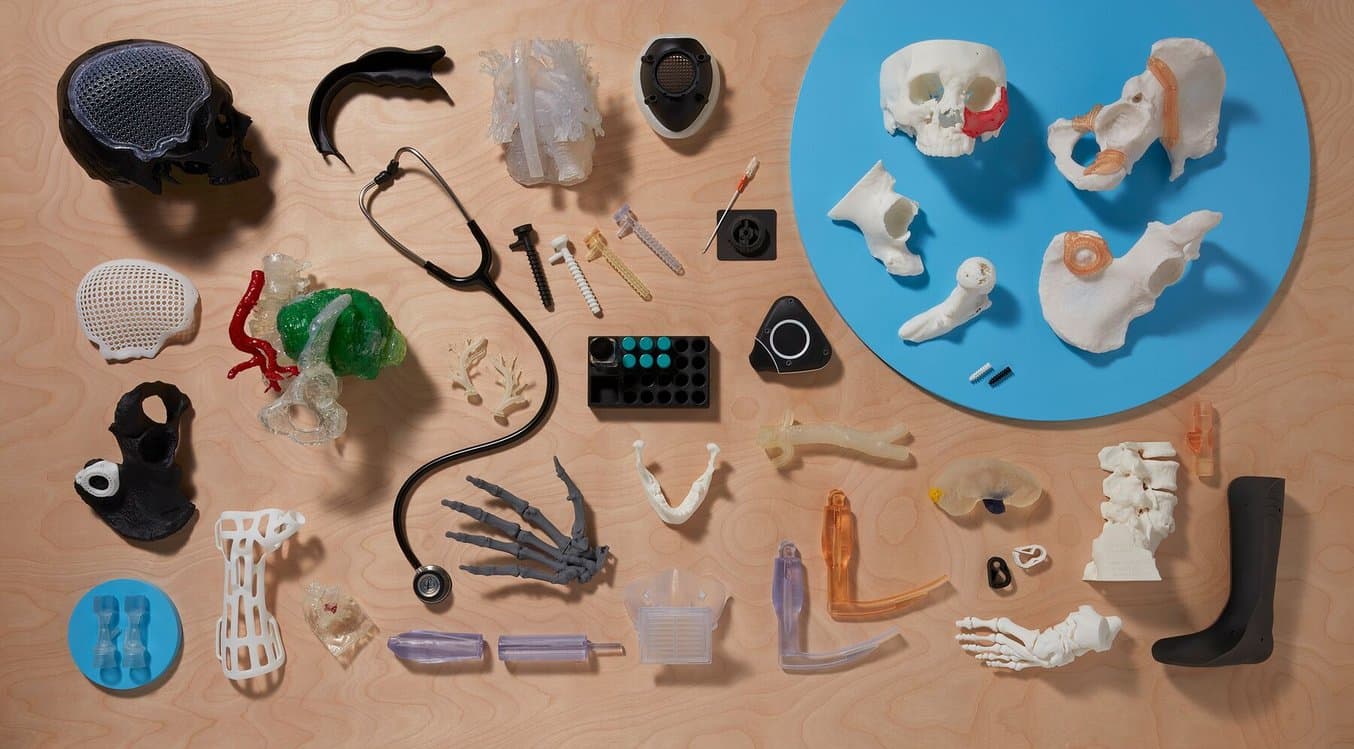
Il catalogo dei materiali Formlabs include resine per la stampa SLA e polveri per la stampa SLS ottimizzate per una varietà di applicazioni mediche.
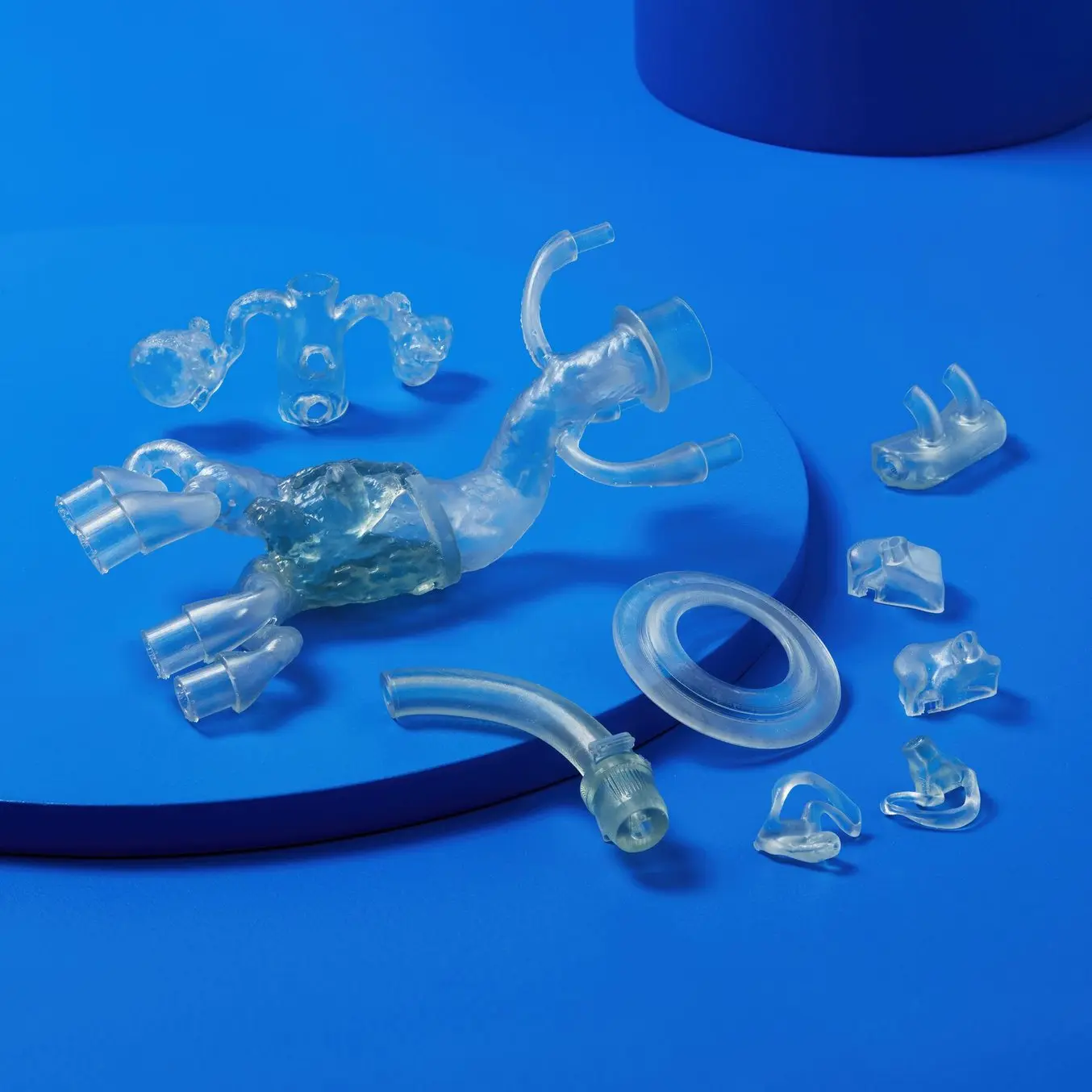
Scegliere i giusti materiali per stampare in 3D dispositivi medici
In questo webinar, Shiden Yohannes, ingegnere medico di Formlabs, illustra i vari materiali disponibili per la stampa 3D e le loro proprietà uniche, aiutandoti a scegliere consapevolmente sulla base delle tue necessità.
Resine per la sinterizzazione laser selettiva
La stereolitografia è adatta a una vasta gamma di applicazioni, ad esempio nel settore ingegneristico, produttivo e sanitario. Le resine per la stereolitografia sono state sviluppate con specifiche proprietà dei materiali, incluse opzioni elastiche, resistenti e biocompatibili.
Le resine BioMed di Formlabs sono materiali per uso medico adatti a una vasta gamma di applicazioni per le quali prestazioni e biocompatibilità sono fondamentali. I materiali della famiglia di resine BioMed vengono sviluppati e prodotti in una struttura con certificazione ISO 13485 e sono compatibili con i comuni metodi di disinfezione e sterilizzazione.
La scelta della giusta resina varia in base all'applicazione, ai requisiti meccanici del materiale e al caso d'uso. Le resine BioMed di Formlabs includono sia opzioni rigide che elastiche, tra cui alcune adatte anche al contatto con le membrane mucose o il contatto a lungo termine con altre parti del corpo.
Inoltre, è stato sviluppato un catalogo di materiali appositamente progettati per soddisfare le esigenze dei professionisti dell'odontoiatria. Tra le varie resine troviamo la Premium Teeth Resin, pensata per la stampa diretta di denti per protesi dentali, e la Dental LT Comfort Resin per bite occlusali. Il catalogo completo dei materiali e tutte le informazioni utili sulle oltre 17 applicazioni delle resine dentali di Formlabs sono disponibili su Formlabs Dental.
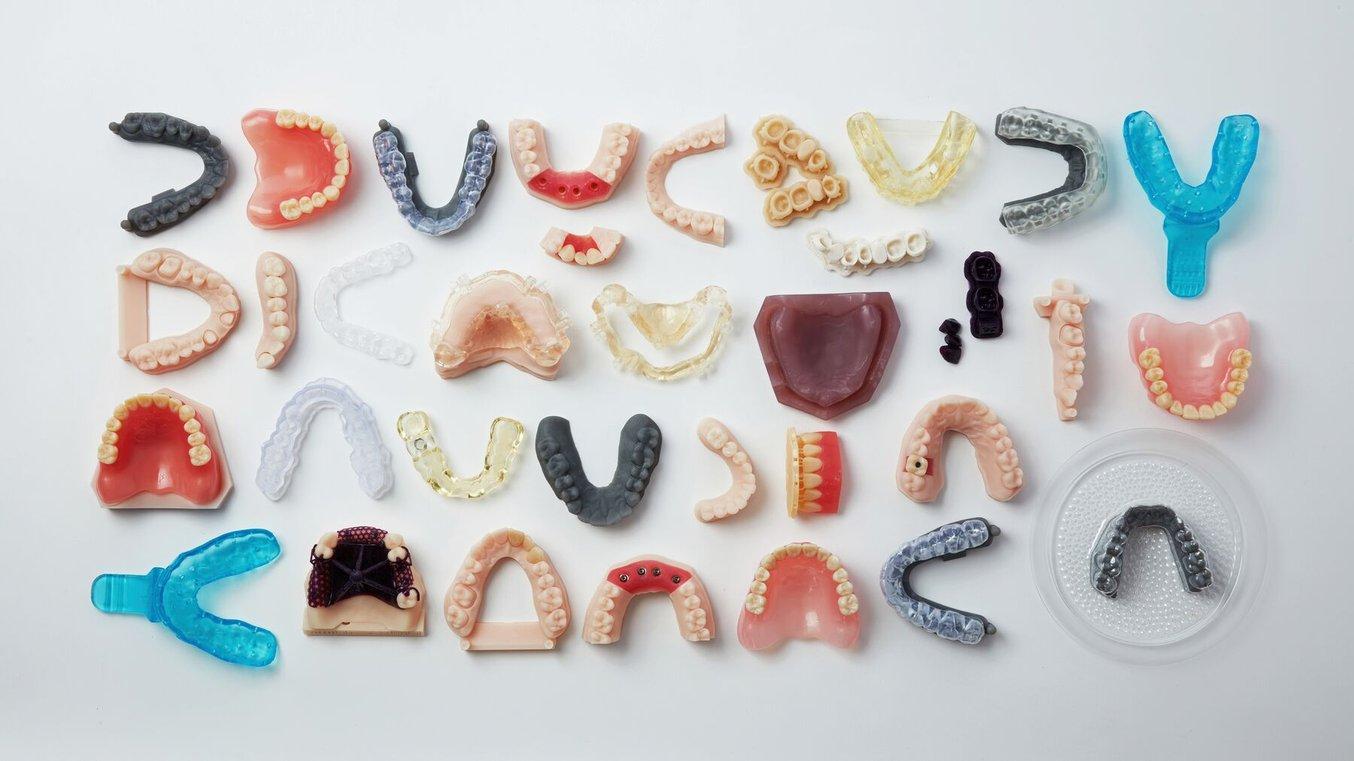
Le resine Formlabs formulate appositamente per il settore dell'odontoiatria possono essere usate in oltre 17 applicazioni.
L'uso di resine mediche di vario tipo aiuta professioniste e professionisti sanitari in molti ambiti, dalla creazione di dispositivi medici alla pianificazione delle procedure chirurgiche, fino allo sviluppo di impianti personalizzati e la ricerca. Le resine BioMed forniscono svariate opzioni di materiali per il settore sanitario, ampliando le possibilità della stampa 3D. La tabella seguente mette a confronto le proprietà e le applicazioni delle resine BioMed di Formlabs.
Materiale | Descrizione | Applicazioni |
---|---|---|
BioMed White Resin | Rigida e dal colore bianco opaco. Approvata per il contatto a lungo termine (oltre 30 giorni) con la pelle o il contatto a breve termine (meno di 24 ore) con ossa, tessuti, dentina e membrane mucose. | Dispositivi medici per utilizzo finale e componenti di dispositivi; stampi e modelli di dimensionamento delle protesi specifici per i pazienti; guide di taglio e di foratura; strumenti e modelli chirurgici; stampi, dime e fissaggi biocompatibili; modelli anatomici utilizzabili in sala operatoria. |
BioMed Black Resin | Rigida e dal colore nero opaco. Approvata per il contatto a lungo termine (oltre 30 giorni) con la pelle o il contatto a breve termine (meno di 24 ore) con le membrane mucose. | Dispositivi medici e componenti di dispositivi; stampi, dime e fissaggi biocompatibili; parti per utilizzo finale destinate al contatto con il corpo; beni di consumo. |
BioMed Amber Resin | Rigida e semitrasparente. Approvata per il contatto a lungo termine (oltre 30 giorni) con la pelle o il contatto a breve termine (meno di 24 ore) con ossa, tessuti, dentina e membrane mucose. | Dispositivi medici per utilizzo finale; modelli di dimensionamento delle protesi; guide di taglio e di foratura. |
BioMed Clear Resin | Rigida e trasparente. Approvata per il contatto a lungo termine con pelle (oltre 30 giorni) e vie respiratorie e membrane mucose (oltre 30 ore) o il contatto a breve termine (meno di 24 ore) con ossa, tessuti e dentina. | Dispositivi per utilizzo finale, anche per le vie respiratorie; prototipi, stampi, dime e fissaggi biocompatibili; modelli per la visualizzazione e il dimensionamento delle protesi; dispositivi per colture cellulari e bioprocessi. |
BioMed Durable Resin | Resistente a urti, rottura e abrasione. Trasparente. Approvata per il contatto a lungo termine con pelle (oltre 30 giorni) e membrane mucose (oltre 30 ore) o il contatto a breve termine (meno di 24 ore) con ossa, tessuti e dentina. | Strumenti monouso e strumenti specifici per i pazienti; dispositivi per utilizzo finale e componenti che richiedono biocompatibilità e resistenza agli urti. |
BioMed Elastic 50A Resin | Morbida e simile al silicone. Traslucida. Approvata per il contatto a lungo termine (oltre 30 giorni) con la pelle o il contatto a breve termine (meno di 24 ore) con le membrane mucose. | Dispositivi medici confortevoli destinati al contatto a lungo termine con la pelle; modelli di tessuti morbidi biocompatibili da usare come riferimento in sala operatoria. |
BioMed Flex 80A Resin | Dura e simile alla gomma. Traslucida. Approvata per il contatto a lungo termine (oltre 30 giorni) con la pelle o il contatto a breve termine (meno di 24 ore) con le membrane mucose. | Componenti e dispositivi medici flessibili biocompatibili; dispositivi medici destinati al contatto a breve termine con le membrane mucose; modelli dei tessuti rigidi destinati all'uso in sala operatoria. |
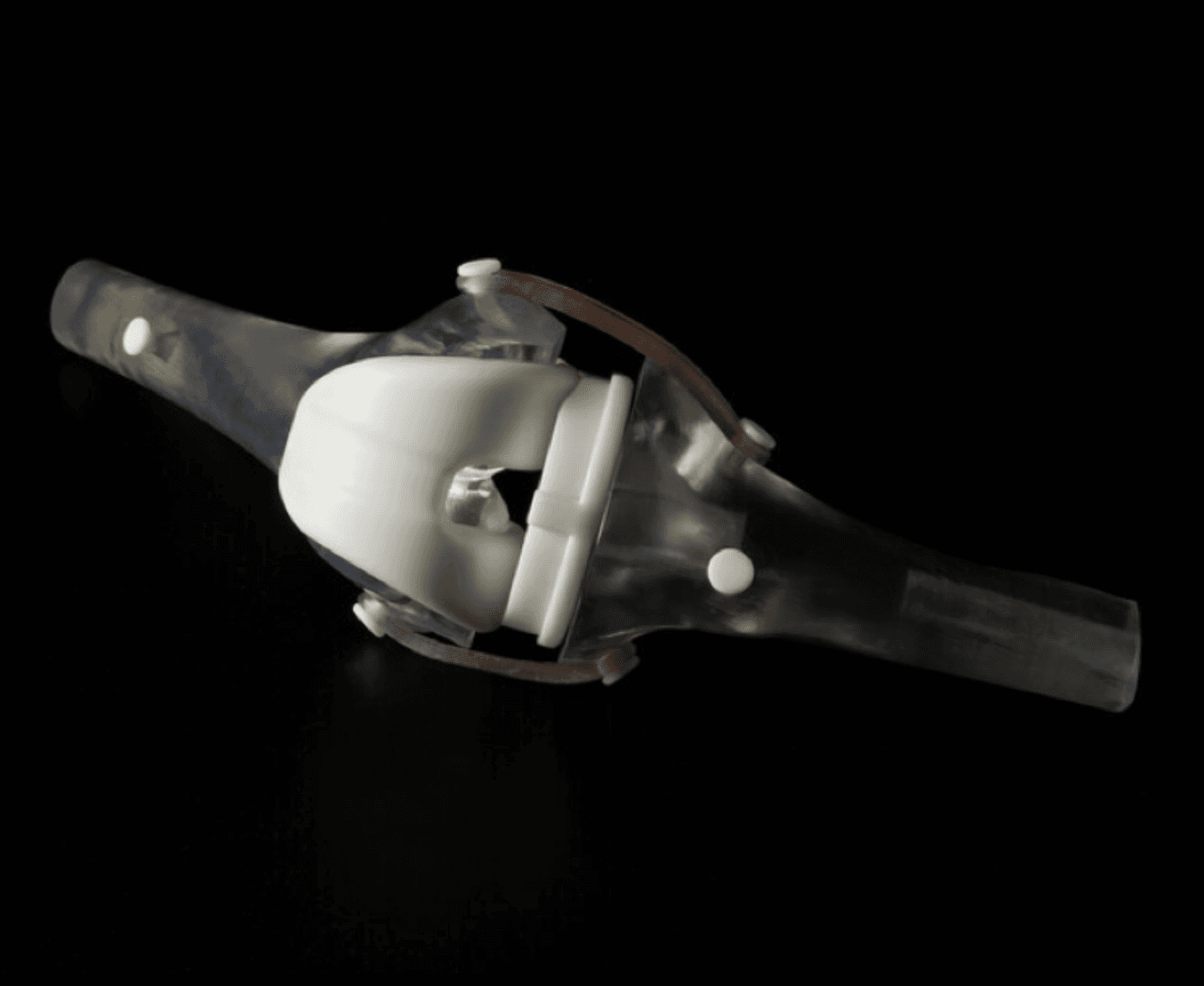
Creazione di modelli di simulazione ossea per taglio e foratura
I modelli di simulazione ossea stampati in 3D stanno rivoluzionando la formazione in ambito medico, la pianificazione chirurgica, nonché la ricerca e lo sviluppo di dispositivi medici. Questo manuale operativo illustra i diversi materiali disponibili per stampare i modelli tramite stereolitografia (SLA) e l'intero processo di fabbricazione in-house per modelli anatomici simili alle ossa destinati al taglio e alla foratura.
Polveri per la sinterizzazione laser selettiva
Le polveri SLS possono essere biocompatibili, sterilizzabili e sicure per il contatto con la pelle e consentono la realizzazione di design con dettagli precisi e pareti sottili. Queste proprietà le rendono ideali per applicazioni nel settore sanitario tra cui dispositivi medici, prototipi, protesi, strumenti chirurgici e plantari.
Il materiale più utilizzato per la sinterizzazione laser selettiva è il nylon, una termoplastica ingegneristica molto diffusa, con proprietà meccaniche eccellenti. Il nylon è leggero, robusto, flessibile e resistente a urti, sostanze chimiche, calore, raggi UV, acqua e sporco. Le parti stampate in 3D in nylon possono anche essere biocompatibili e non sensibilizzanti, quindi sono pronte da indossare e garantiscono un uso sicuro in molti contesti.
La Nylon 12 Powder offre equilibrio tra resistenza e precisione, con un carico di rottura pari a 50 MPa. Adatta alla realizzazione di assemblaggi complessi e parti resistenti con elevata stabilità ambientale, la Nylon 12 Powder è ideale per la creazione di prototipi ad alte prestazioni, la produzione con volumi ridotti e la realizzazione di dime, fissaggi e attrezzature permanenti. Le parti risultanti sono biocompatibili e sterilizzabili, il che rende la Nylon 12 Powder perfetta per le applicazioni mediche, come le dime chirurgiche.
La Nylon 11 Powder è un materiale ideale per la creazione di plantari, tra cui solette parziali, dotati di tenacia, elevata duttilità e stabilità a lungo termine. Leggi questa analisi delle prestazioni per scoprire di più sulla resistenza di questo materiale.
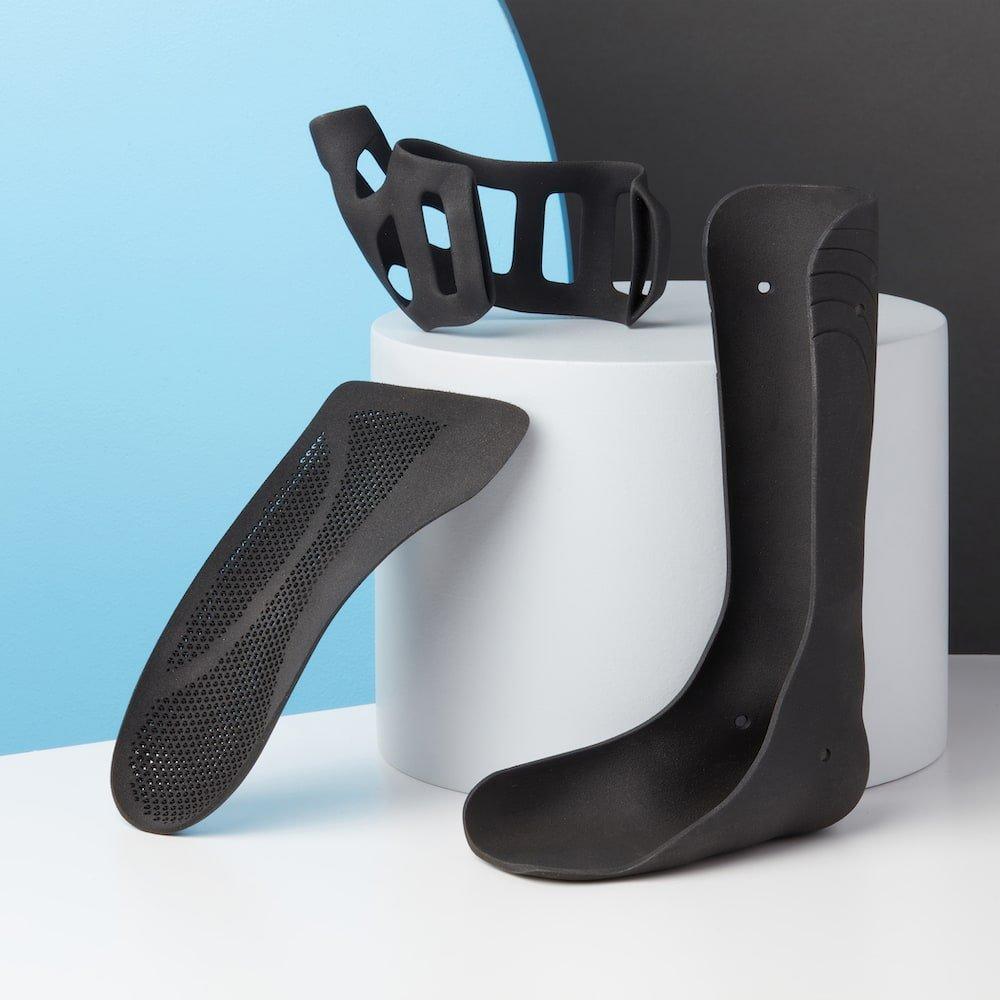
Plantari stampati con la Nylon 11 Powder.
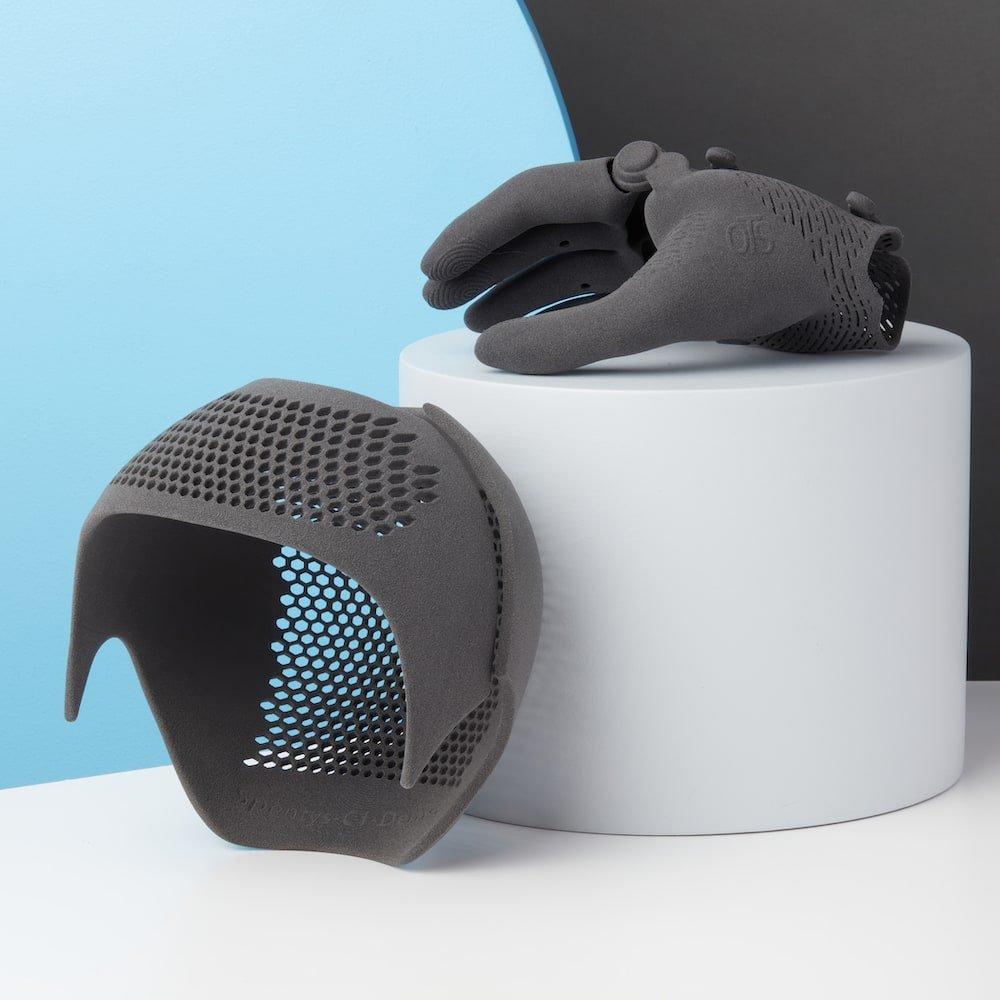
Caschetto di rimodellamento cranico e prototipo di protesi di mano stampati con la TPU 90A Powder.
La Polypropylene Powder è una polvere in vero polipropilene che può essere utilizzata per produrre prototipi funzionali e parti per utilizzo finale resistenti. La sua elevata duttilità consente di piegare e flettere le parti ripetutamente mantenendone sempre la resistenza. Le parti stampate in Polypropylene Powder sono impermeabili, saldabili e resistenti alle sostanze chimiche, il che le rende ideali per la produzione di plantari, protesi, dime, fissaggi e attrezzature.
La TPU 90A Powder è un elastomero flessibile che combina l'elevato allungamento a rottura e la straordinaria resistenza alla lacerazione dei materiali in gomma con la libertà di design e la robustezza della stampa 3D SLS. Il poliuretano termoplastico (TPU) è una termoplastica elastomerica molto diffusa. Questo materiale sicuro per il contatto con la pelle è spesso usato per la realizzazione di prototipi di dispositivi medici, dispositivi medici per utilizzo finale e componenti, nonché per la creazione di solette plantari, rivestimenti protesici, tutori, caschetti di rimodellamento cranico e solette correttive o per calzature sportive.
La tabella seguente illustra alcune delle applicazioni e proprietà dei materiali delle polveri SLS di Formlabs.
Materiale | Descrizione | Applicazioni |
---|---|---|
Nylon 12 Powder | Biocompatibile, sterilizzabile e dotata di elevato carico di rottura e resistenza. | Dispositivi medici per utilizzo finale e componenti di dispositivi; stampi e modelli di dimensionamento delle protesi specifici per i pazienti; guide di taglio e di foratura; strumenti e modelli chirurgici; stampi, dime e fissaggi biocompatibili; modelli anatomici utilizzabili in sala operatoria. |
Nylon 11 Powder | Altamente duttile e robusta. Più flessibile, meno fragile e più adatta alla stampa di pareti sottili rispetto alla Nylon 12 Powder. Sterilizzabile e biocompatibile. | Plantari e protesi, prototipi resistenti agli urti, dispositivi medici, parti per utilizzo finale. |
Polypropylene Powder | Duttile, robusta, impermeabile, saldabile e resistente alle sostanze chimiche. | Plantari e protesi; alloggiamenti e involucri impermeabili; attrezzature, dime e fissaggi robusti e resistenti alle sostanze chimiche. |
TPU 90A Powder | Elastomero tenace, sicuro per il contatto con la pelle, resistente alla deformazione, dotato di allungamento a rottura e resistenza alla lacerazione elevati. | Suole, tutori, plantari e protesi; dispositivi indossabili ed elementi morbidi al tatto; imbottiture, ammortizzatori e impugnature. |
Le proprietà del materiale possono variare in base al design della parte e ai processi di produzione. È responsabilità dell'azienda produttrice validare l'idoneità delle parti stampate per l'uso previsto.
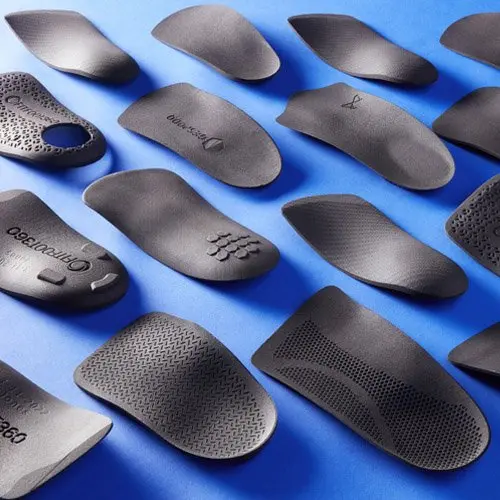
Stampa 3D di solette parziali rigide
Scopri come produrre solette parziali resistenti, duttili e in grado di superare 4 milioni di cicli di piegatura con l'ecosistema SLS compatto e conveniente di Formlabs. Questa guida completa ti aiuterà a partire in quarta con la produzione di solette parziali con la Fuse 1+ 30W.
Entra nel mondo della stampa 3D in ambito medico
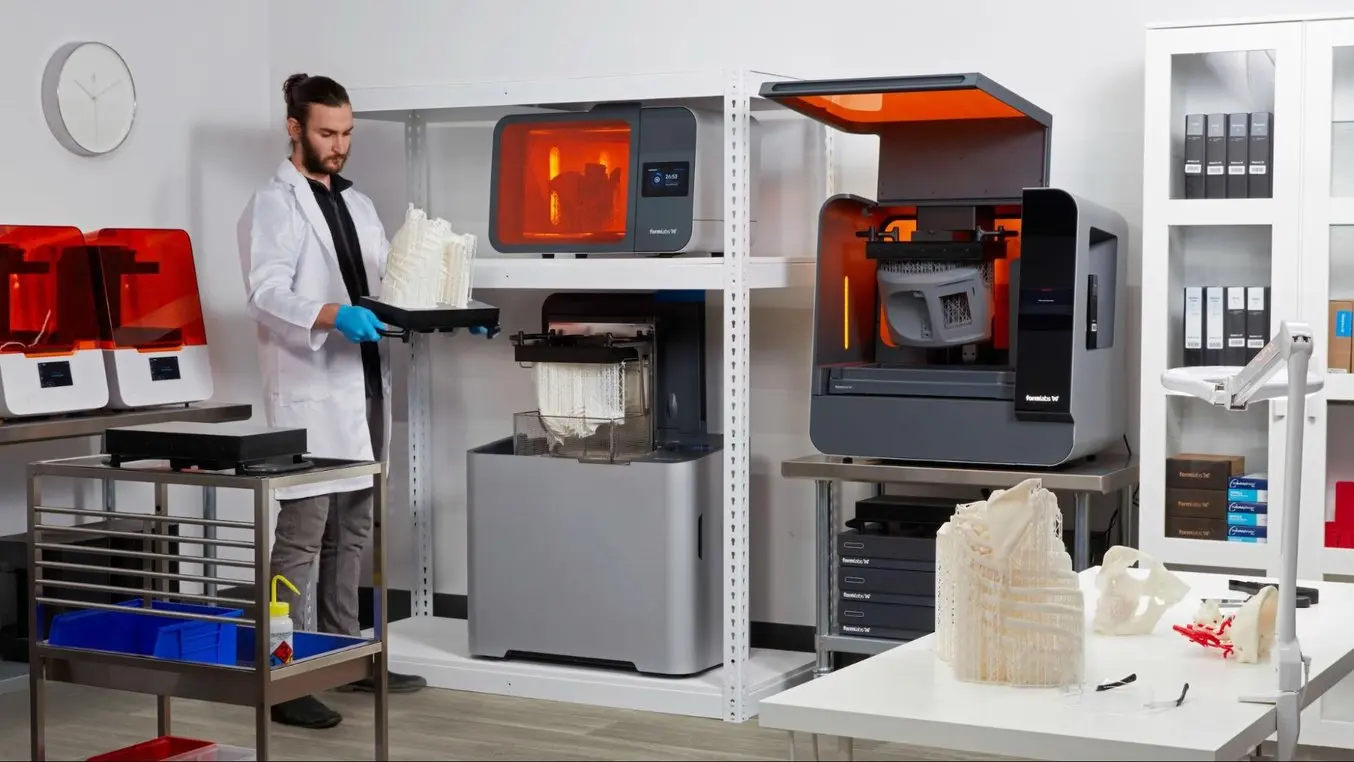
I processi di stampa 3D precisi ed economici per il settore sanitario stanno democratizzando l'accesso alla tecnologia, consentendo ai medici di offrire trattamenti innovativi in tutto il mondo, nonché a professioniste e professionisti sanitari di sviluppare nuove soluzioni cliniche e realizzare rapidamente dispositivi su misura. I continui progressi nel campo delle tecnologie e dei materiali per la stampa 3D in medicina spianano la strada a cure personalizzate e applicazioni mediche di grande impatto.
Ogni struttura sanitaria dovrebbe avere accesso agli strumenti più recenti per migliorare le cure e fornire la migliore esperienza possibile ai pazienti. Inizia ora a stampare o amplia la tua produzione in-house con Formlabs, un partner affidabile e all'avanguardia nella stampa 3D per il settore medico.
Parla con i nostri esperti in ambito sanitario per saperne di più su come la stampa 3D in-house può fornire un trattamento migliore e integrarsi nel tuo attuale workflow di design e di produzione di dispositivi medici.