Holimaker produce centinaia di prototipi e parti per la pre-produzione con stampi a iniezione realizzati in 3D
La start-up francese Holimaker ha l'obiettivo di rendere accessibile la lavorazione di plastiche realizzando strumenti per il micro-settore adatti a processare questi materiali. Il suo prodotto principale, la Holipress, è una macchina per lo stampaggio a iniezione manuale che consente a ingegneri e designer di prodotto di lavorare la plastica da desktop per produrre piccole quantità di parti per prototipi, produzione pilota o anche serie limitate di parti per uso finale.
Holimaker offre ai suoi clienti studi di fattibilità e si serve degli stampi realizzati in 3D per garantire tempi di consegna rapidi a un prezzo conveniente. Questo permette ai clienti di realizzare prototipi dei loro progetti in modo veloce e a un prezzo accessibile così da convalidare le condizioni di produzione definitive durante la fase pilota dell'immissione sul mercato del nuovo prodotto. Poiché viene usato lo stesso metodo di produzione, compresa la progettazione dello stampo e i materiali, le parti possono essere testate sul campo in modo da assicurarsi che i progetti siano pronti per essere prodotti su larga scala. I progetti degli stampi realizzati in 3D possono essere facilmente adattati per le attrezzature in acciaio necessarie durante la produzione in serie.
Oggi Holimaker utilizza stampi a iniezione realizzati in 3D in una percentuale tra l'80 e il 90% dei suoi progetti. Abbiamo incontrato Aurélien Stoky, il direttore generale, e Vivien Salamone, il direttore marketing, per capire in che modo la start-up coniuga le due tecnologie.
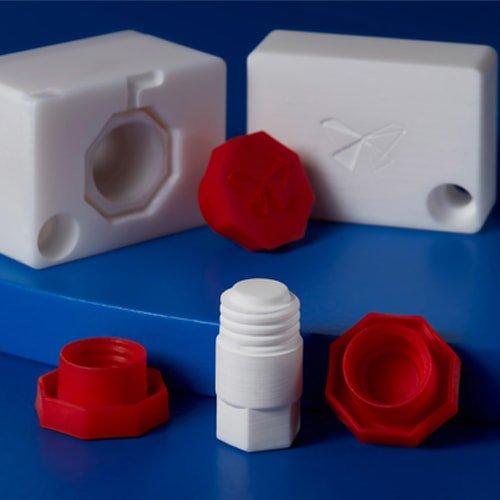
Stampaggio a iniezione rapido su scala ridotta con stampi realizzati in 3D
Scarica il nostro whitepaper per ottenere linee guida su come utilizzare stampi realizzati in 3D per i processi di stampaggio a iniezione, in modo tale da poter ridurre costi e tempi di realizzazione. Inoltre potrai esaminare i casi studio reali di Braskem, Holimaker e Novus Applications.
Perché realizzare in 3D stampi a iniezione?
Tradizionalmente gli stampi a iniezione sono realizzati tramite costosi metodi industriali come la lavorazione meccanica CNC o l'elettroerosione (EDM). Tuttavia, quando è necessario produrre parti in quantità minori, i costi, i tempi, l'attrezzatura specialistica e la manodopera qualificata necessari per fabbricare stampi con normali metalli e metodi di produzione tradizionali diventano problematici, e per molte aziende lo stampaggio a iniezione risulta spesso inaccessibile per le piccole quantità. L’impiego della stampa 3D per fabbricare stampi a iniezione per la prototipazione e la produzione in piccoli volumi, consentendo di produrre parti riproducibili di alta qualità, riduce significativamente gli ostacoli associati all'uso di stampi in metallo.
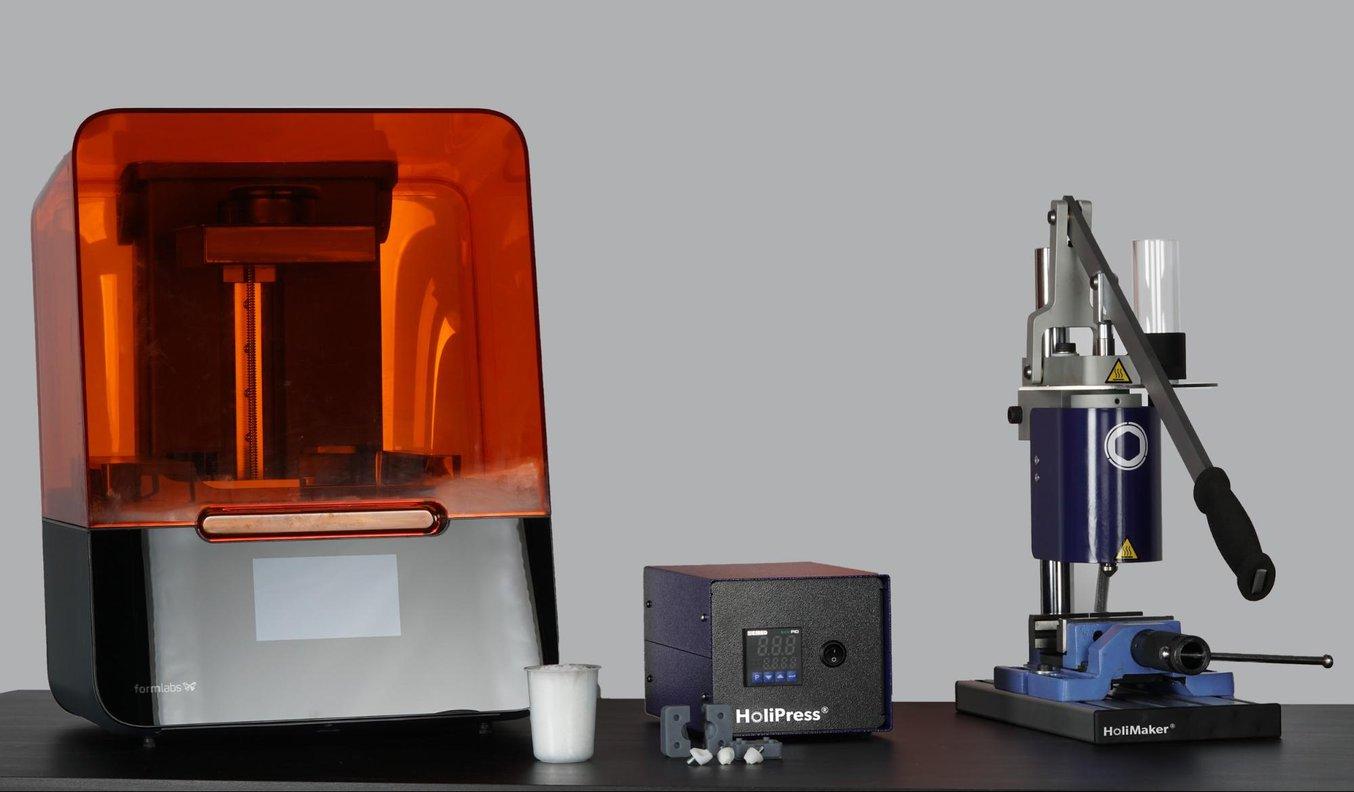
La Holipress accanto alla stampante Form 3.
"Quello che spesso dissuade dall'utilizzare lo stampaggio a iniezione è il problema dello stampo. Per rendere più democratico e accessibile a tutti lo stampaggio a iniezione, dovevamo trovare una tecnologia complementare per produrre lo stampo. La stampa desktop era perfetta per questo scopo. Uniamo la flessibilità della stampa 3D alla produttività e alla qualità delle plastiche realizzate tramite stampaggio a iniezione" affermano Stoky e Salamone.
Il vantaggio principale di questo processo alternativo è che permette di ridurre il tempo che intercorre tra la fase di ideazione e la produzione, realizzando una serie di parti nelle tradizionali termoplastiche. Grazie alla Holipress, l'azienda può realizzare piccoli lotti di prototipi e parti per la pre-produzione. Questo consente loro di testare il materiale definitivo e la linea di produzione che saranno adottati nella produzione in serie, e persino di realizzare volumi limitati di parti per uso finale. Inoltre, grazie alla stampa 3D stereolitografica (SLA) desktop, questo è possibile nel giro di pochi giorni, con un'attrezzatura ridotta al minimo e senza bisogno di operatori specializzati.
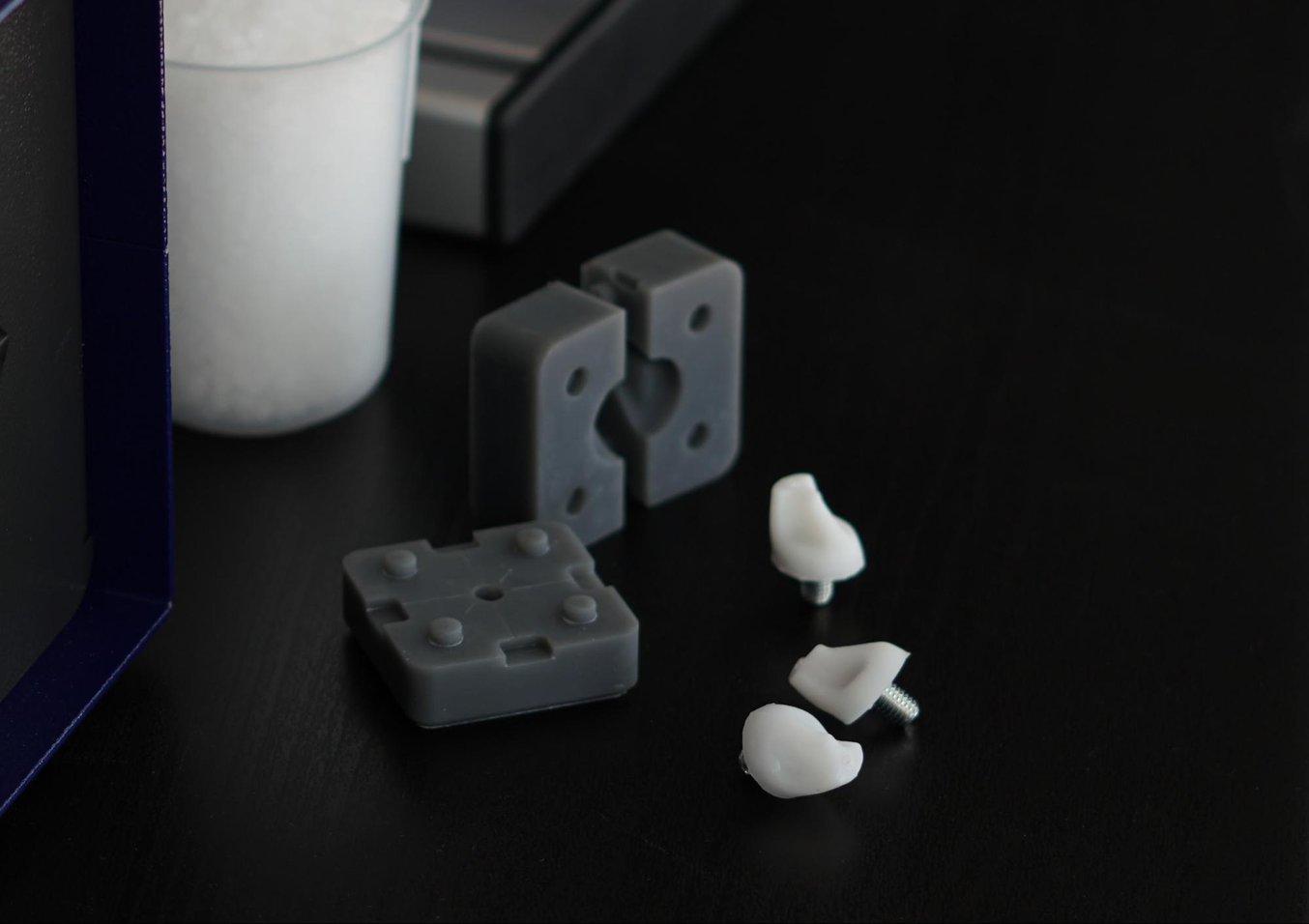
I prototipi pre-produzione di questi tacchetti per scarpe da calcio sono stati stampati a iniezione con stampi realizzati in 3D in tre diverse termoplastiche: il poliossimetilene (180 °C), il poliammide 6.6 (270 °C) e il polipropilene (210 °C).
Con la stampa in 3D, il team di Holimaker può ridurre drasticamente il tempo di produzione degli stampi ed eseguire iterazioni di nuovi design per ottimizzare la geometria in una sola giornata.
"Spesso progettiamo lo stampo la mattina, lo stampiamo durante la giornata e siamo in grado di testare l'iniezione nel pomeriggio per modificare il design e avviare una seconda stampa durante la notte. Con i metodi tradizionali sarebbe necessario realizzare nuovamente lo stampo tramite lavorazione meccanica, e questo richiederebbe settimane" afferma Stoky.
Holimaker ha cercato modi alternativi per la realizzazione dello stampo. Per ordini di oltre un migliaio di parti, usava uno stampo in alluminio prodotto tramite lavorazione meccanica, ma per quantità minori, si affidava agli stampi realizzati in 3D. In alcuni casi utilizza entrambi i metodi: per volumi consistenti con geometrie complesse, realizza la parte esterna dello stampo meccanicamente e stampa in 3D l'inserto, che nel tempo viene sostituito.
La stampa 3D in-house ha inoltre permesso all'azienda di andare oltre le limitazioni imposte dalle tecniche di lavorazione meccanica. In molti progetti Holimaker è riuscita a realizzare design di stampi complessi che sarebbero stati difficili da produrre con le tecniche tradizionali, e in questo modo ha permesso ai suoi clienti di innovare ancora di più.
"In termini di geometria, alcuni dei nostri progetti non sarebbero stati realizzabili senza la stampa 3D" spiega Stoky.
Il processo passo dopo passo
Progettazione
Di solito il team esegue iterazioni su tre o quattro modelli per progetto, al fine di ottimizzare il design, seguendo le raccomandazioni generali per lo stampaggio e per il design per la fabbricazione quali l’inclusione di angoli di sformo. Si concentra soprattutto su piccole parti e aggiunge sfiati di 0,1 mm e canali di 0,5 mm.
Inoltre, rispetta alcune regole della stampa 3D, come quella di includere smussature per agevolare la rimozione della parte dalla piattaforma di stampa, utilizzare perni di centraggio per allineare le due metà dello stampo e aggiungere ugelli per facilitare l'apertura con un cacciavite. In genere vengono usati stampi di uno spessore di 10 mm e si evitano le sezioni trasversali sottili. Le parti con uno spessore di 1-2 mm non riescono a resistere alle alte temperature.
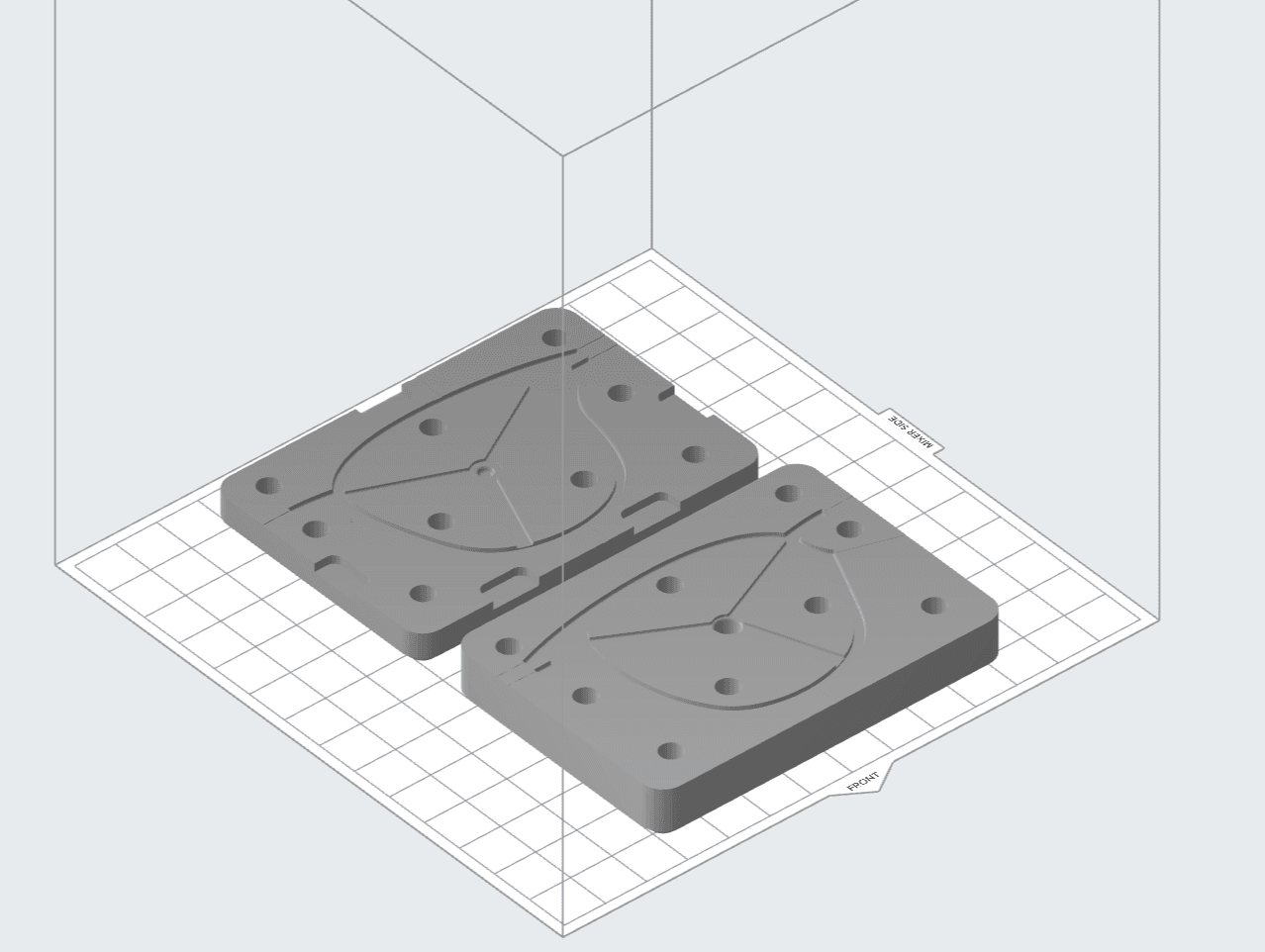
Vari design di stampi a iniezione sul software di preparazione della stampa PreForm di Formlabs.
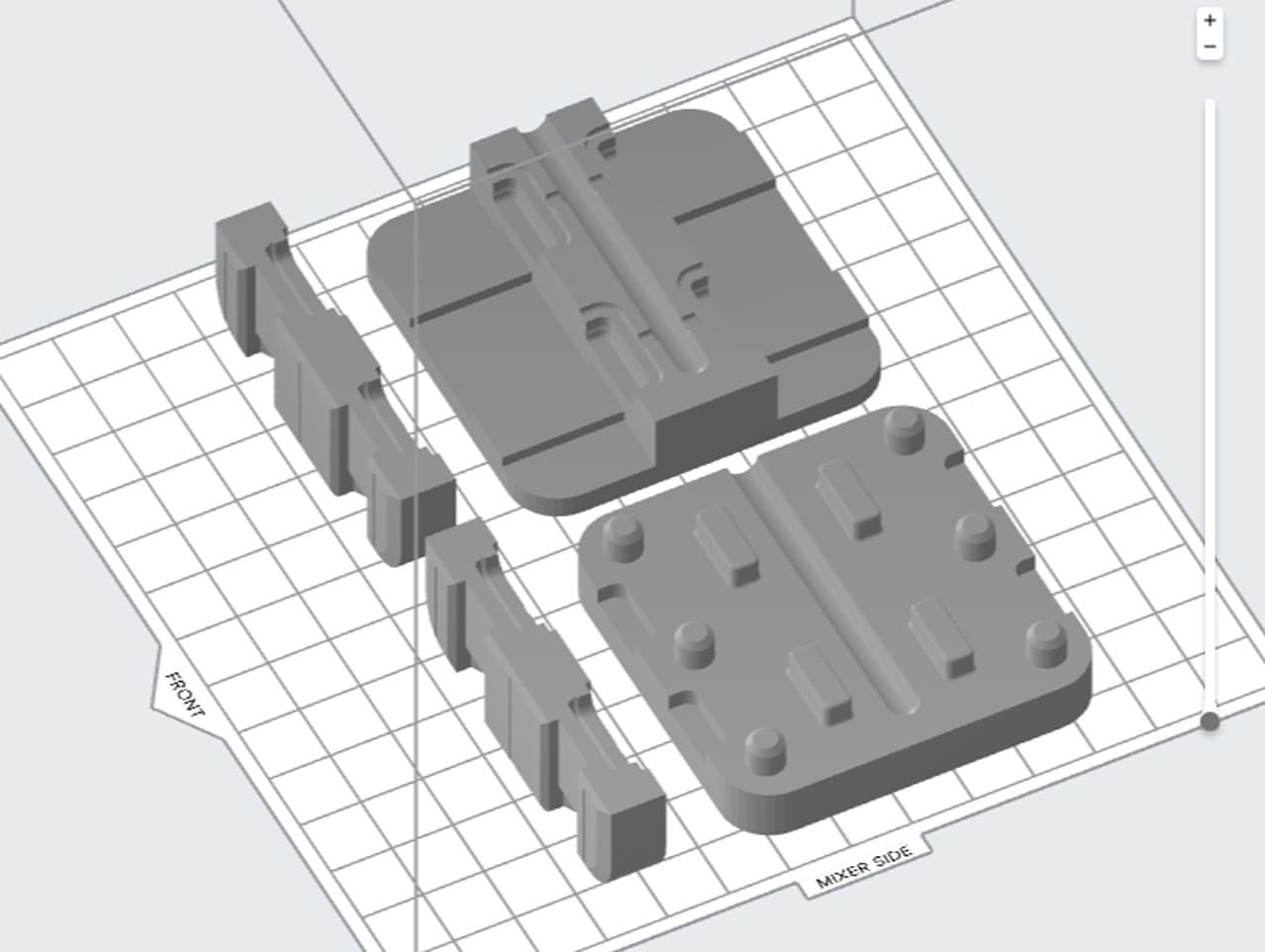
Passare da uno stampo realizzato in 3D per la produzione in piccoli volumi a uno stampo in metallo per la produzione in serie ottenuto tramite lavorazione meccanica è molto semplice. Potrebbero essere necessarie semplici modifiche agli angoli di sformo, alle aperture, alle dimensioni degli sfiati.
Stampa 3D
Il team di Holimaker realizza gli stampi direttamente sulla piattaforma di stampa con uno spessore dello strato di 50 micron. Questo orientamento consente di risparmiare tempo e resina grazie all'eliminazione delle strutture di supporto. Se si verificano errori dimensionali, accade generalmente sulla parte esterna del blocco che viene sottoposto a post-elaborazione con levigazione a mano per essere inserito all'interno di cornici in metallo standard che forniscono ulteriore supporto.
In generale Formlabs consiglia la Rigid 10K Resin e la High Temp Resin per lo stampaggio a iniezione, ma la Grey Pro Resin può essere una valida alternativa nel caso in cui le forme complesse determinino un insuccesso nello stampaggio. Se il tempo di raffreddamento non è una priorità, la Grey Pro Resin è una buona opzione per allungare la vita utile dello stampo.
Holimaker predilige la Grey Pro Resin per la maggior parte dei suoi studi. Questo materiale è meno resistente alle alte temperature rispetto alla High Temp Resin e alla Rigid 10K Resin, ma è meno fragile e consente un maggior numero di cicli per geometrie complesse. La Grey Pro Resin può anche essere forata e maneggiata più volte, e può essere utilizzata nei processi di iniezione standard.
Stampaggio a iniezione
Il team si serve della macchina per lo stampaggio a iniezione Holipress per tutti gli studi dell'azienda. Si tratta di una piccola pressa manuale, semplice da utilizzare, e disponibile a un decimo del costo di una pressa industriale.
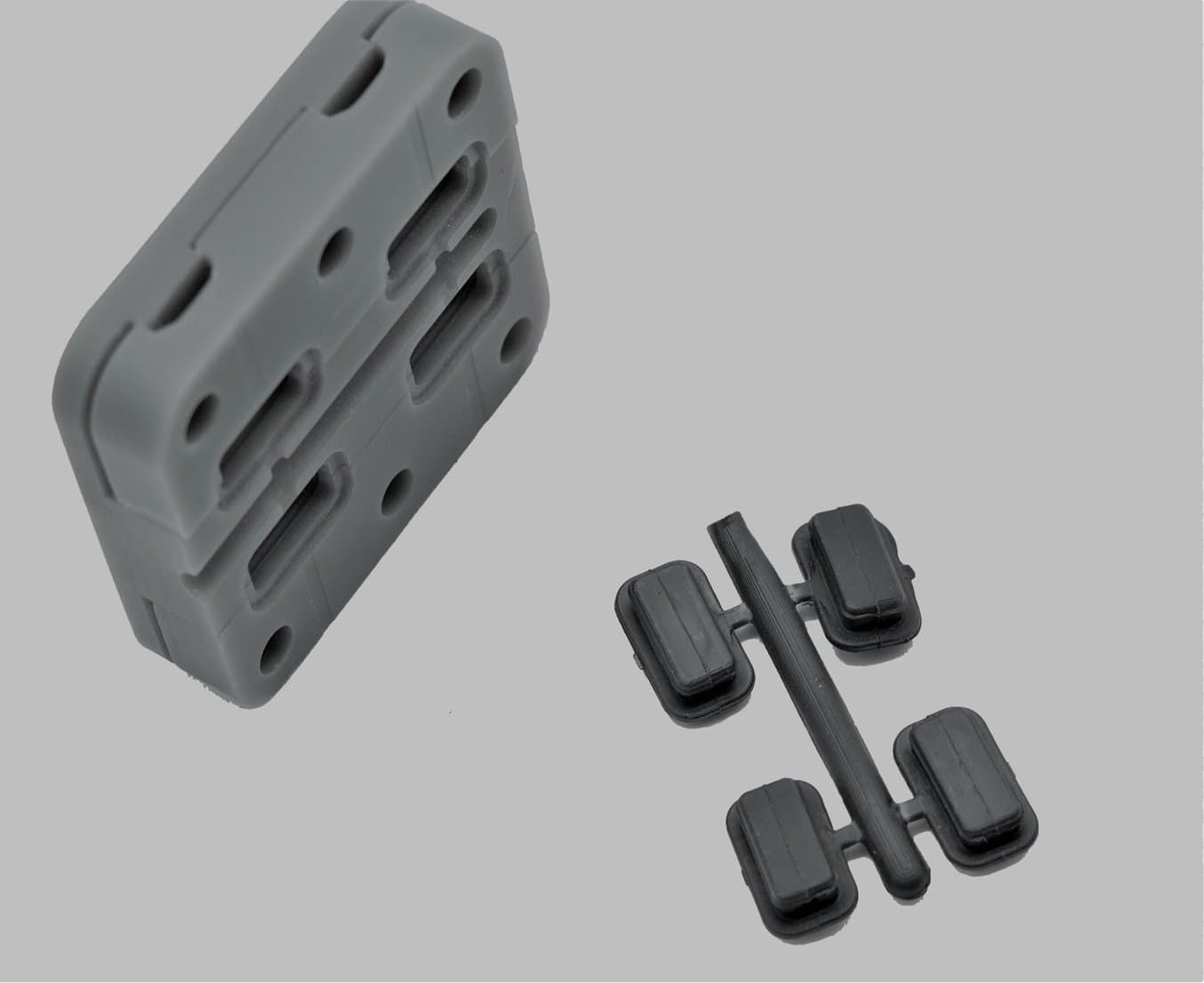
Questi fermagli per schermi facciali sono stati stampati a iniezione con polipropilene (sicuro per gli alimenti, 220 °C).
Gli stampi vengono posizionati in una cornice di alluminio prefabbricata che resiste meglio alla pressione e assicura che l'ugello di iniezione non sia a contatto diretto con lo stampo realizzato.
Con gli stampi realizzati con le stampanti Formlabs, Holimaker inietta un'ampia gamma di termoplastiche con diversi livelli di durezza, da Shore 40A a 90A, con un tempo di ciclo che varia tra i tre e i cinque minuti. Il numero di cicli per ciascuno stampo varia da circa 10 parti nel caso di poliammide iniettato a 270 °C, fino a raggiungere centinaia di parti quando il materiale - polipropilene, elastomero termoplastico o poliossimetilene - è iniettato a temperature più basse. Holimaker sta sviluppando un sistema di raffreddamento integrato per contribuire a ridurre il tempo di raffreddamento prima della rimozione dallo stampo.
I risultati
Il team ha scelto la stampa 3D SLA di Formlabs per la sua qualità delle parti e per la facilità di utilizzo.
"La qualità delle parti ottenute tramite stampaggio a iniezione è ottima grazie all'alta qualità degli stampi. E quando avvio una stampa la sera, sono quasi sicuro che il giorno dopo troverò pronto un fantastico stampo" afferma Stoky.
Stoky e Salamone avevano usato un'altra tecnologia di stampa desktop in precedenza, ma avevano riscontrato un'eccessiva deformazione sulle stampe.
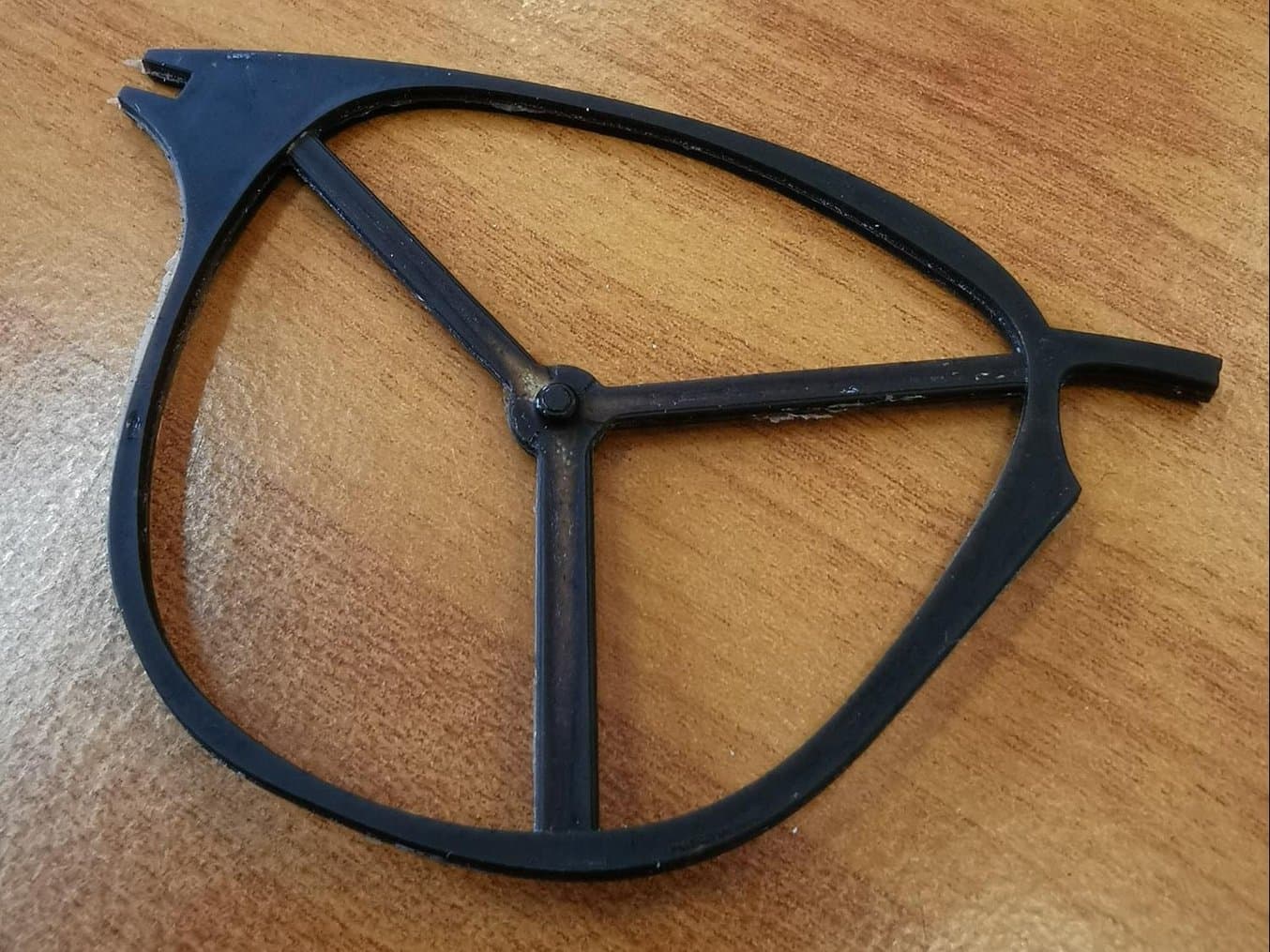
Una montatura per occhiali prodotta con stampi realizzati in 3D.
“Le parti Formlabs offrono precisione dimensionale e finitura superficiale straordinarie. Se si verifica un errore dimensionale, di solito è quasi irrilevante, ed è uniforme su tutti e tre gli assi, così possiamo prevederlo e sottoporlo a post-elaborazione. Con le altre stampanti desktop non riuscivamo a controllare la deformazione" spiega Stoky.
Il team apprezza anche il workflow semplice da memorizzare e da mettere in pratica, senza dimenticare la Form Wash e la Form Cure, strumenti di post-elaborazione automatizzati.
Holimaker ha condiviso con noi alcuni casi di suoi clienti per fornirci una migliore comprensione della parte, delle condizioni di stampaggio e dei risultati degli studi di fattibilità.
Azienda | Smart Power | FERME 3D | Produttore di occhiali | |
---|---|---|---|---|
Prodotto | Tacchetti per scarpe da calcio | Attacco per schermo facciale | Montatura per occhiali | |
Esigenza | Prototipi per la pre-produzione in diverse termoplastiche da testare sul campo prima di scegliere il materiale definitivo per la produzione in serie. | Testare una soluzione per produrre una serie di decine di migliaia di parti in breve tempo. | Testare la compatibilità dei materiali per l'occhialeria con gli stampi per produrre una serie di 200 montature. | |
Materiali iniettati | Poliossimetilene (180 °C), poliammide 6.6 (270 °C), polipropilene (210 °C) | Polipropilene (sicuro per gli alimenti, 220 °C) | Acrilonitrile stirene acrilato (240 °C), poliammide (240 °C) | |
Numero di parti per uno stampo | 60 | 100 | 70 | |
Tempo di ciclo | 2 minuti | 2 minuti | 2 minuti | |
Tempo di realizzazione del progetto | 1 settimana | 1 settimana | 2 settimane |
Risparmiare tempo e denaro con stampi a iniezione realizzati in 3D
L'utilizzo di stampi realizzati in 3D in-house ha prodotto un notevole risparmio di tempo e denaro rispetto all'esternalizzazione di stampi metallici prodotti tramite lavorazione meccanica.
Stampo in metallo realizzato da terzi tramite lavorazione meccanica | Stampo realizzato in 3D in-house | |||
---|---|---|---|---|
Attrezzatura | Holipress, termoplastiche | Holipress, termoplastiche, stampante Form 3, Grey Pro Resin | ||
Tempo di produzione dello stampo | 3-5 settimane | 1 settimana | ||
Costi di produzione dello stampo | 4-5 volte superiore alla stampa in-house | 1 X |
La produzione rapida delle attrezzature con lo stampaggio a iniezione desktop e gli stampi a iniezione realizzati in 3D permettono a Holimaker di produrre velocemente piccoli lotti di parti in termoplastiche su richiesta.
"Possiamo ridurre il tempo che intercorre tra l'idea dell'oggetto e la parte realizzata tramite stampaggio a iniezione. Ci guadagniamo in termini di flessibilità e risparmiamo tempo e denaro" afferma Stoky.
Scarica il nostro whitepaper gratuito o guarda il webinar per conoscere il workflow del processo nel dettaglio e ottenere linee guida per la progettazione e altre buone pratiche su come utilizzare stampi realizzati in 3D per i processi di stampaggio a iniezione e vedere i casi studio reali di Braskem e Nouvus Applications.