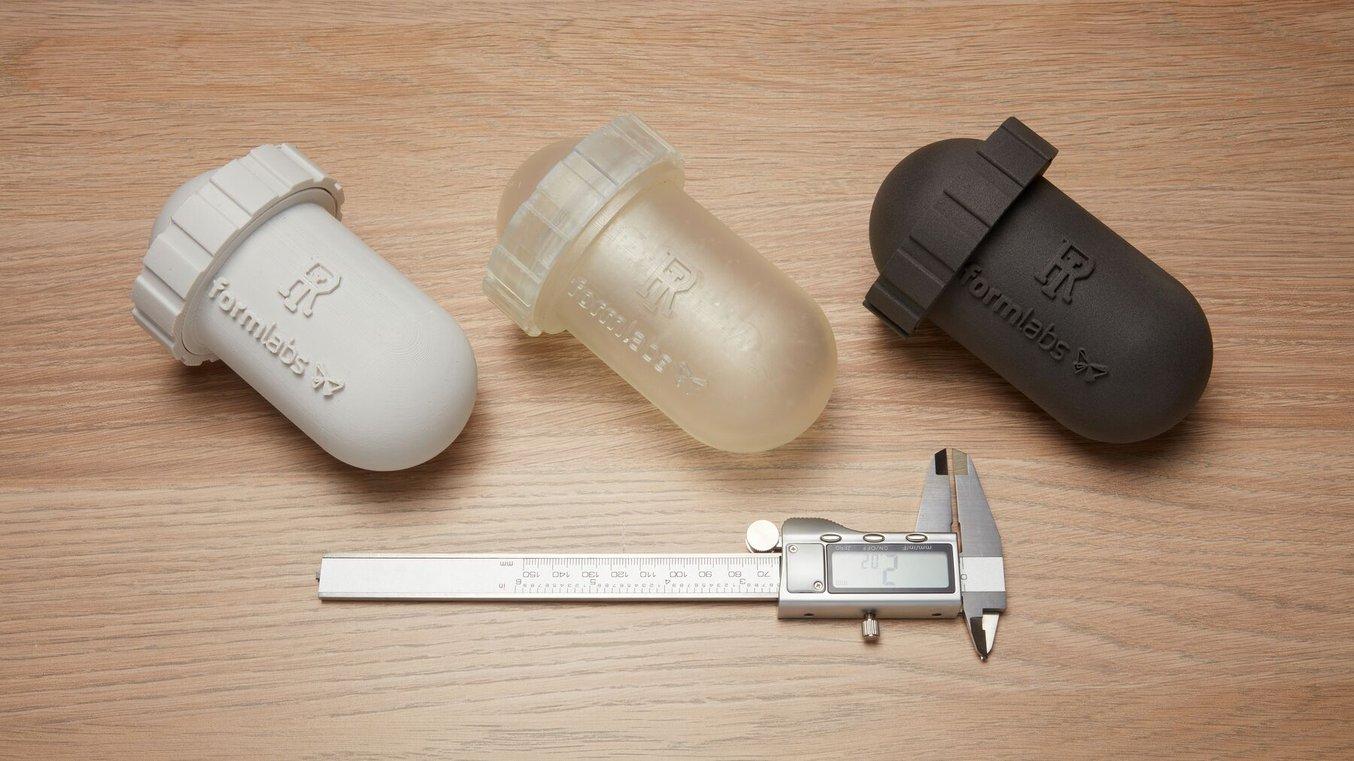
L'esigenza di parti ermetiche e a tenuta di gas prodotte in modo personalizzato o in volumi ridotti è diffusa in diversi settori, come la ricerca marina, la robotica subacquea e l'ingegneria delle tecnologie sostenibili, nonché le industrie del petrolio e del gas e la difesa. Sebbene alcune tecnologie di stampa 3D rappresentino una soluzione ideale a questo scopo, la percezione comune è che le parti realizzate mediante produzione additiva siano porose e non possano essere utilizzate in ambienti pressurizzati.
Grazie alla collaborazione tra Formlabs e l'Undersea Robotics and Imaging Lab (URIL) della University of Rhode Island, assemblaggi a più componenti realizzati tramite modellazione a deposizione fusa (FDM), stereolitografia (SLA) e sinterizzazione laser selettiva (SLS) sono stati testati in una camera a pressione per la simulazione delle condizioni subacquee. Nel whitepaper qui di seguito vengono illustrati i risultati dei test, accompagnati da diagrammi, raccomandazioni sugli O-ring e linee guida di progettazione.
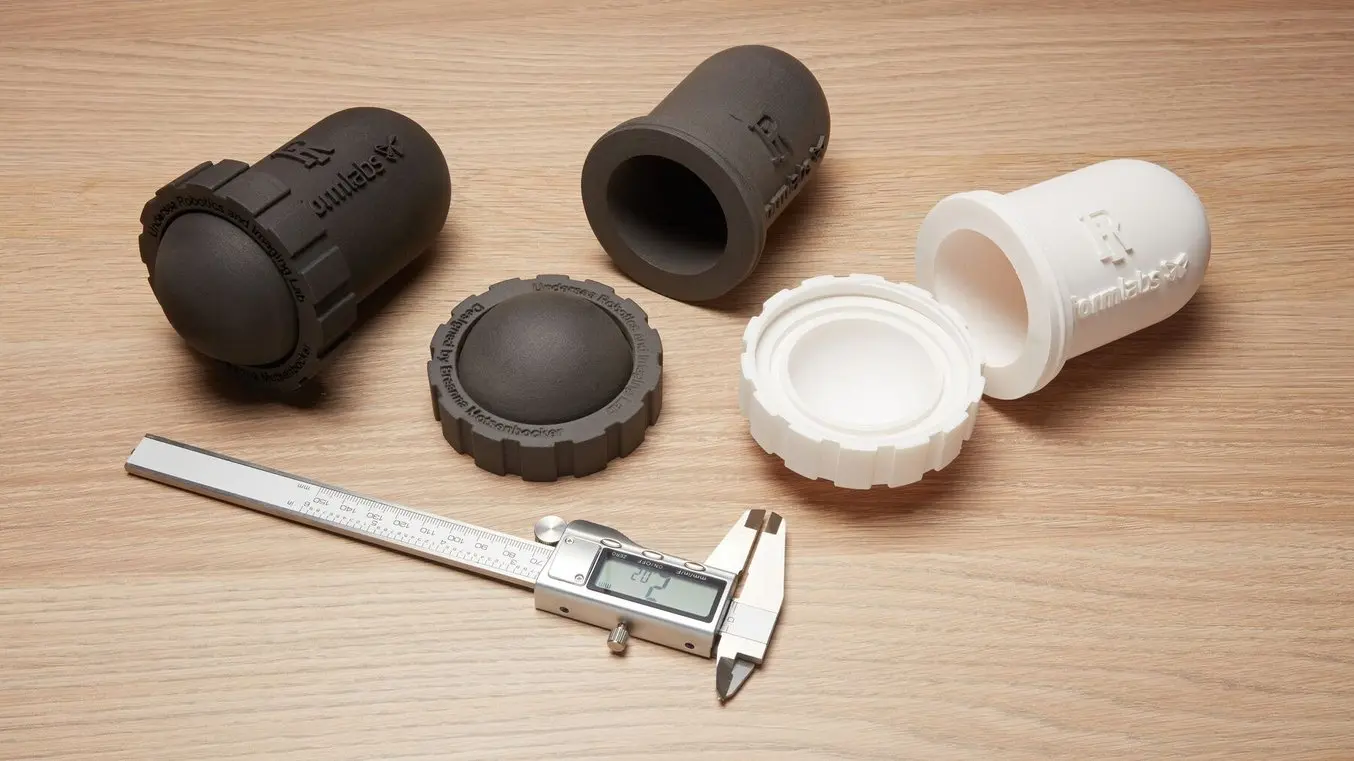
Alloggiamenti ermetici realizzati con la stampa 3D e risultati dei test di pressione
In questo whitepaper illustriamo i risultati dei test e forniamo linee guida chiare su come stampare in 3D alloggiamenti ermetici personalizzati a costi contenuti.
Progettazione e realizzazione di parti ermetiche personalizzate
L'ermeticità si riferisce alla capacità di un oggetto di impedire all'acqua di filtrare all'interno o di fuoriuscire da un alloggiamento ed è molto più legata alla costruzione di quest'ultimo o dell'assemblaggio che alla natura intrinseca del materiale dei componenti. Tuttavia, se si considera la pressione che queste parti subiscono durante la discesa sotto la superficie, le proprietà specifiche dei materiali assumono un ruolo più importante. L'esperimento condotto dall'URIL riguarda il design, il metodo di sigillatura e le proprietà dei materiali.
Applicazioni delle parti ermetiche
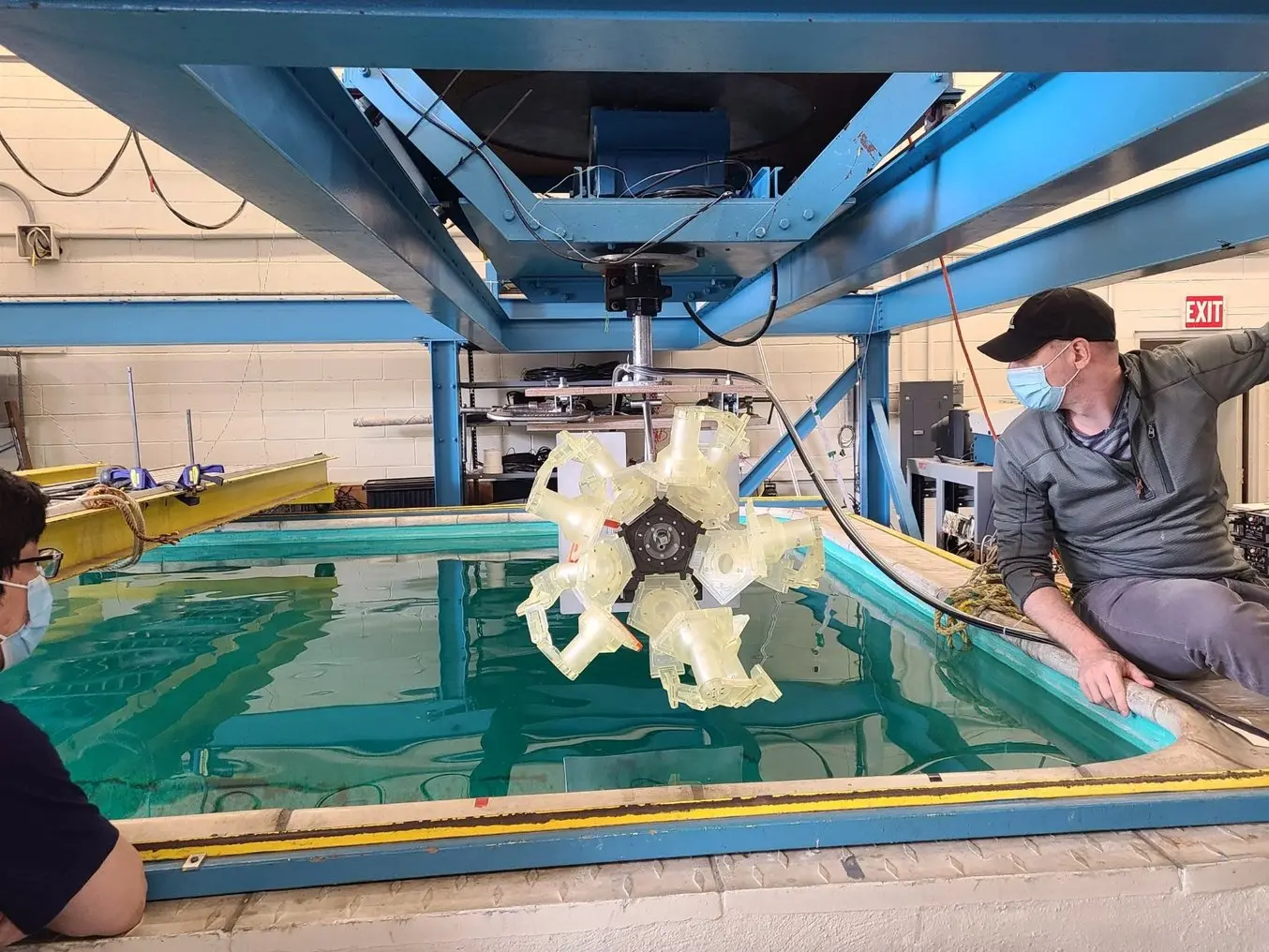
La stampa 3D consente di realizzare forme nuove e complesse per le attrezzature destinate a test e raccolta di campioni, come questo strumento con componenti stampati in Clear Resin.
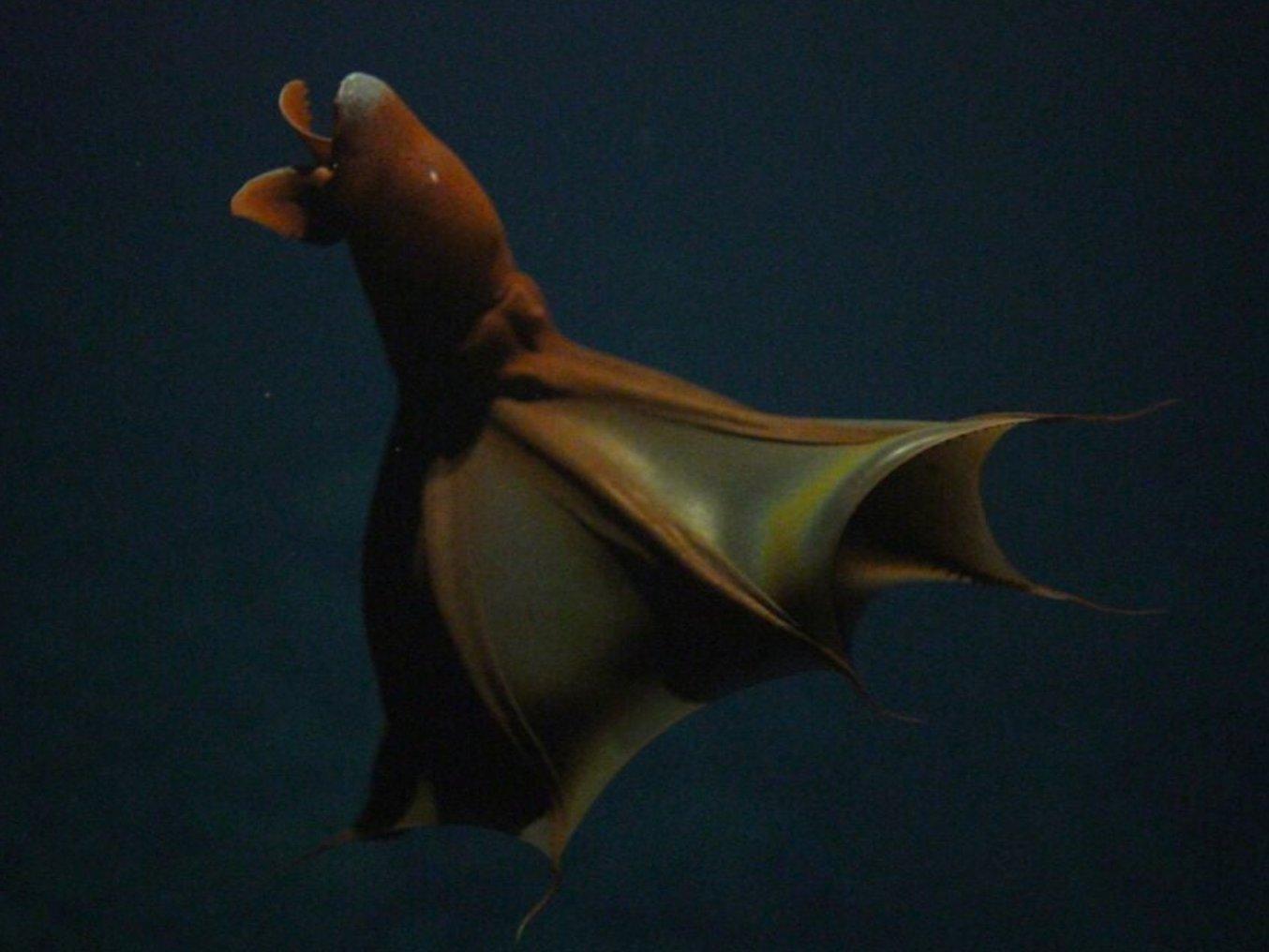
Gli alloggiamenti ermetici permettono di scattare immagini in profondità, come questa foto di un vampyroteuthis, anche senza costosi apparecchi fotografici subacquei.
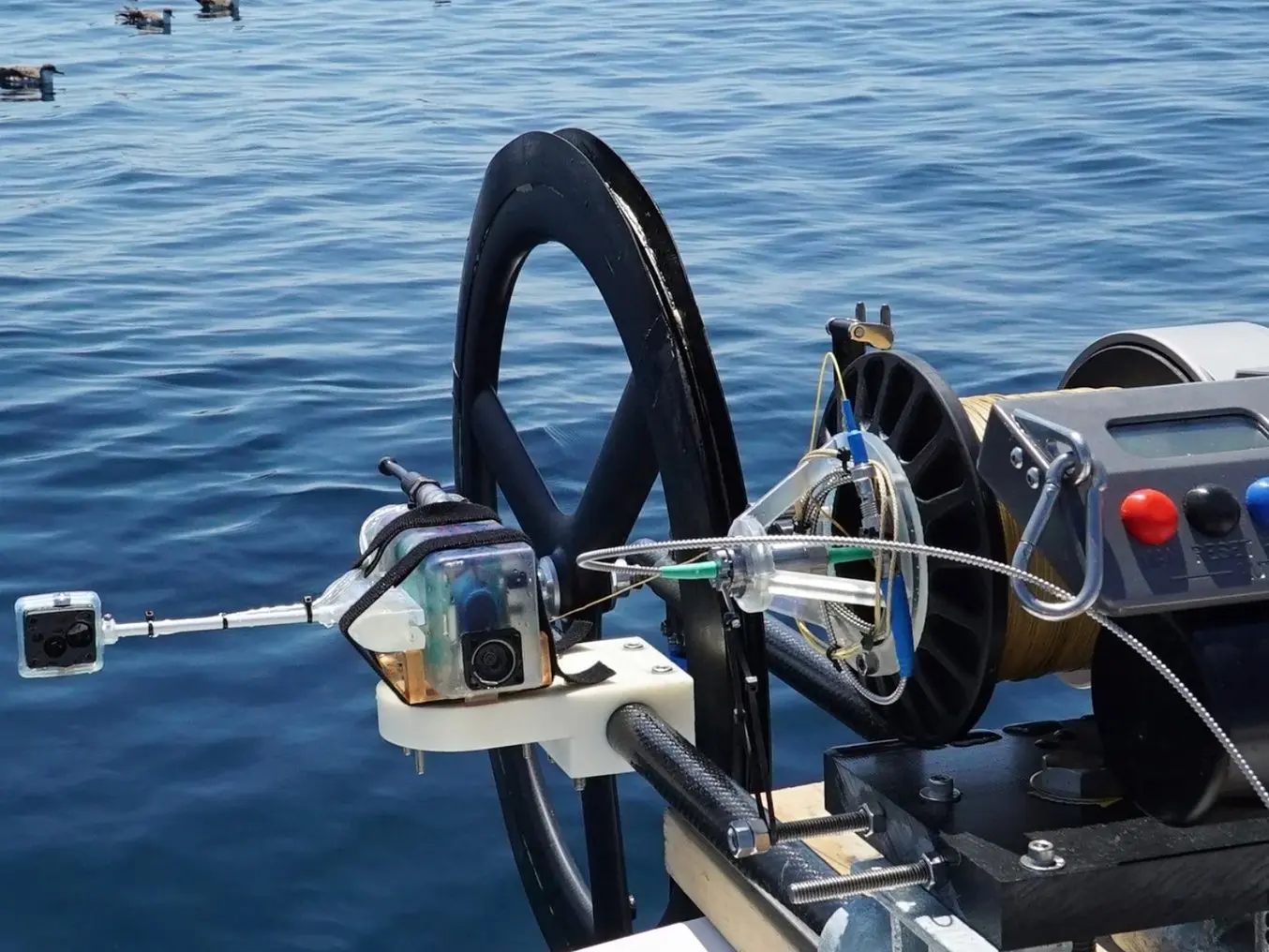
La natura agile della stampa 3D su richiesta consente di realizzare dime e fissaggi personalizzati per la ricerca marina a costi contenuti.
Le parti ermetiche vengono utilizzate in contesti diversi, come nei motori fuoribordo per la nautica da diporto, l'esplorazione robotica in acque profonde, la fotografia subacquea e molto altro. Le parti ermetiche possono trattenere anche altri fluidi, per questo sono estremamente utili nelle applicazioni in cui tubi trasportano liquidi tra vari componenti, come nel settore automobilistico, nella ricerca chimica, nei servizi pubblici, nell'edilizia e in molti altri contesti.
Per le applicazioni di ricerca nei campi dell'ecologia, geologia o climatologia, creare apparecchi personalizzati per lo studio e il campionamento è spesso eccessivamente costoso. Poiché ogni applicazione è unica e gli ambienti in cui le parti vengono impiegate sono in continua evoluzione e difficili da gestire dalla superficie, i componenti subacquei o fluidodinamici spesso devono avere un certo grado di personalizzazione.
Stampa 3D di parti ermetiche presso la NOAA
Per contrastare la scomparsa della barriera corallina, i team scientifici e di ricerca dell'Atlantic Oceanographic and Meteorological Laboratory (AOML) della National Oceanic and Atmospheric Administration (NOAA), insieme alle istituzioni partner, utilizzano metodi innovativi per studiare i coralli in natura, riprodurre determinate condizioni con impostazioni controllate in laboratorio e quindi coltivare nuove specie di coralli in grado di resistere meglio a condizioni estreme.
L'AOML ha iniziato a sfruttare la stampa 3D per facilitare la ricerca sul campo e in laboratorio. L'uso delle stampanti Formlabs ha contribuito a standardizzare e a migliorare l'accuratezza e la comparabilità degli esperimenti, semplificando inoltre lo sviluppo di nuove tecnologie. La gamma di materiali disponibili per le stampanti Formlabs facilita la progettazione, l'esecuzione di iterazioni e l'utilizzo di parti ermetiche stampate in 3D.
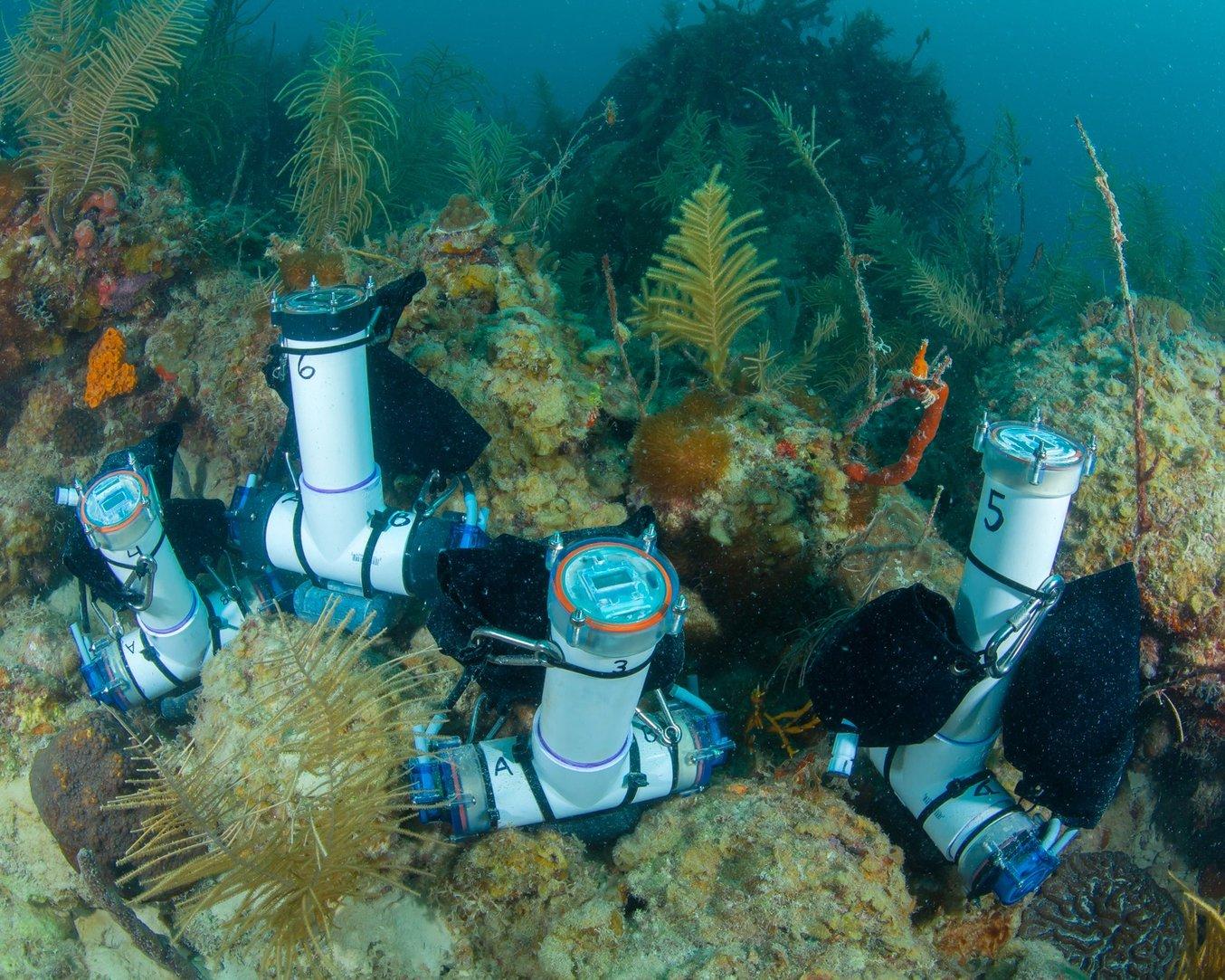
Le ricerche dell'AOML richiedono apparecchi sofisticati e spesso personalizzati per monitorare gli habitat dei coralli selvatici. (Immagini per gentile concessione della NOAA)
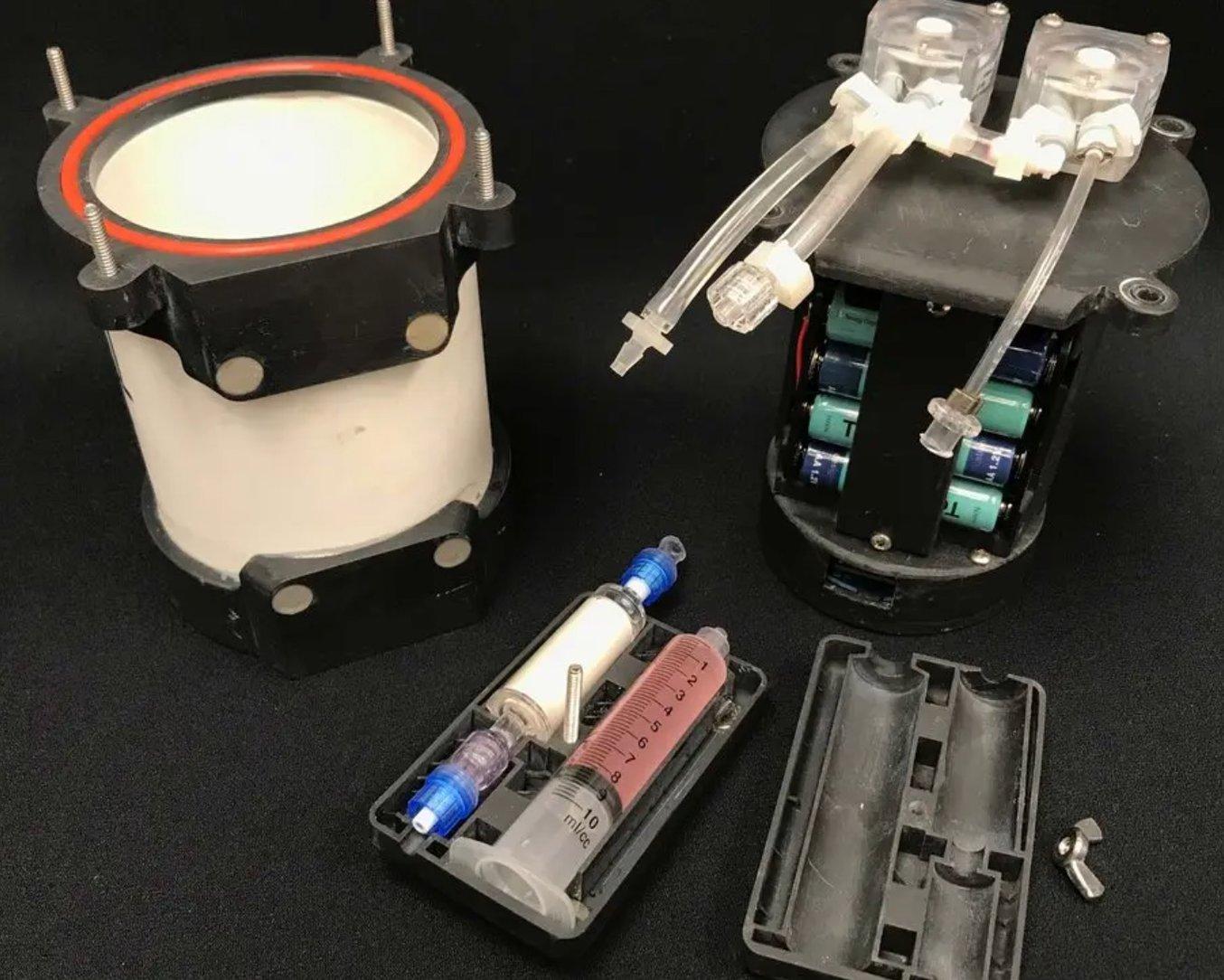
Il laboratorio dell'AOML ha progettato e fabbricato questo campionatore automatico subacqueo per eDNA utilizzando le stampanti SLA di Formlabs per la realizzazione di cappucci protettivi, cartuccia di campionamento e armatura interna.
Utilizzando quattro stampanti a resina Formlabs e la stampante a sinterizzazione laser selettiva (SLS) Fuse 1, Nate Formel e i suoi colleghi dell'AOML stampano alloggiamenti per campionatori per uso intensivo, dime per sensori, nonché apparecchi sperimentali e componenti personalizzati per i loro acquari in-house, ovvero strutture costruite per studiare l'adattamento dei coralli e i metodi per migliorare la resilienza di questi ultimi rispetto all'aumento della temperatura dell'acqua e alle condizioni estreme provocate dal cambiamento climatico.
"Ora possiamo contare su componenti stampati in 3D estremamente personalizzati, dotati dei punti di connessione e delle fessure di cui abbiamo bisogno per raccogliere i campioni d'acqua. Il design del campionatore originario aveva un costo di 1000 $, mentre adesso realizziamo ciascun pezzo a un costo di 220 $. Ciò significa che ora posso creare cinque campionatori, mentre prima ne potevo realizzare solo uno", afferma Formel.
Metodi di fabbricazione attuali per parti ermetiche
Gli attuali metodi di fabbricazione di questi componenti ermetici prevedono solitamente l'impiego di materiali molto comuni, come il metallo, la plastica stampata a iniezione o la gomma. I componenti prodotti in massa sono accessibili, ma configurarli in modo da soddisfare le esigenze specifiche di ogni singola applicazione può essere difficile e richiedere connettori, fissaggi o alloggiamenti personalizzati. Per gli assemblaggi a più componenti, i componenti vengono sigillati con una combinazione di filettature a vite, elementi di interblocco o di accoppiamento, O-ring o guarnizioni.
La scelta degli O-ring può essere estremamente difficile e la configurazione dei giusti parametri per ciascun alloggiamento può richiedere molto tempo. Il manuale sugli O-ring di Parker contiene migliaia di raccomandazioni basate su compressione, diametro, spessore, materiale, pressurizzazione e altre caratteristiche. Il processo di scelta di un O-ring personalizzato è così difficile che spesso si ricorre a componenti standardizzati e prodotti in massa, il che limita la capacità di innovazione e le nuove applicazioni.
Come scegliere la tecnologia migliore per la stampa 3D di parti ermetiche
Le applicazioni subacquee sono state tradizionalmente limitate a imprese con alta disponibilità di fondi, in grado di costruire costosi macchinari e attrezzature personalizzate. La stampa 3D può essere il punto di svolta, poiché consente di fabbricare parti personalizzate per la ricerca e lo sviluppo a una frazione del costo dei metodi tradizionali. Per implementare con successo una soluzione subacquea stampata in 3D, è necessario valutare attentamente il tipo di tecnologia e il materiale usati.
Sia la tecnologia SLA che quella SLS sono ampiamente utilizzate nell'ambito dell'ingegneria e della ricerca, ma offrono prestazioni ottimali anche in situazioni diverse. La tecnologia SLS è straordinaria per la produzione in volumi ridotti di parti per utilizzo finale. Inoltre, dispone di un catalogo di materiali ben noti, tra cui nylon e poliuretano termoplastico, e permette di creare parti resistenti e di qualità industriale. Le stampanti SLA sono ideali nei casi in cui è richiesta una finitura superficiale liscia e proprietà dei materiali molto specifiche. In questo test, sia la finitura superficiale liscia delle parti stampate tramite SLA che la loro densità hanno contribuito a fornire prestazioni ottimali in un ambiente pressurizzato. Le stampanti a modellazione a deposizione fusa (FDM) sono spesso utilizzate per la prototipazione rapida, ma non permettono di creare parti ermetiche e quindi non sono utilizzate in applicazioni di questo tipo.
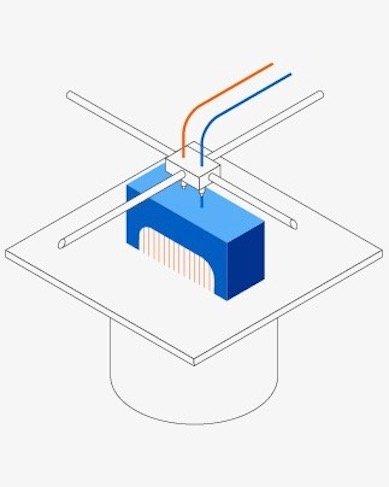
Tecnologia di stampa 3D a modellazione a deposizione fusa (FDM).
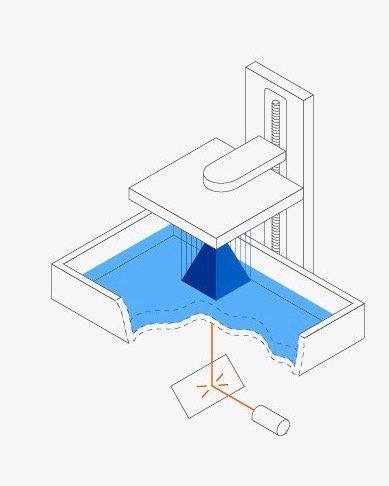
Tecnologia di stampa 3D a stereolitografia (SLA).
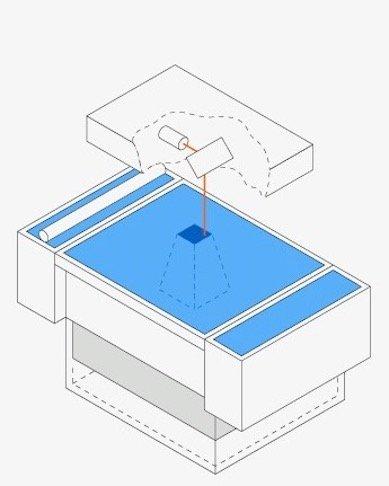
Tecnologia di stampa 3D a sinterizzazione laser selettiva (SLS).
Modellazione a deposizione fusa (FDM)
La tecnologia di stampa 3D più conosciuta, la modellazione a deposizione fusa (FDM), non permette di creare parti ermetiche. Da questa incapacità deriva l'errata credenza che in generale le parti stampate in 3D non possano essere utilizzate in applicazioni ermetiche. La tecnologia FDM si basa sull'estrusione della plastica fusa attraverso un ugello, che deposita il materiale strato per strato, ma senza che tra questi ultimi si crei un legame chimico.
Le parti stampate con modellazione a deposizione fusa sono anisotropiche, cioè hanno proprietà meccaniche diverse in base alla direzione in cui si verificano le sollecitazioni meccaniche, e sono inoltre meno dense rispetto a oggetti simili prodotti con metodi alternativi. Poiché gli strati non sono chimicamente legati tra loro, i liquidi possono infiltrarsi nella superficie della parte attraverso i microscopici spazi tra gli strati. Gli alloggiamenti stampati con le stampanti FDM non sono quindi ermetici, a meno che le parti non vengano sottoposte a importanti fasi di post-elaborazione e sigillate tramite passaggi aggiuntivi, come la levigazione a vapore o il rivestimento. Queste parti sono destinate a implodere sotto pressione e a rompersi lungo le linee degli strati.
Se occorre creare parti ermetiche con le stampanti 3D FDM, è possibile sfruttare alcune tecniche per cercare di migliorarne l'ermeticità, tra cui progettare la parte senza spazi vuoti, fessure o altre aperture, nonché ricorrere alla "sovraestrusione" e all'utilizzo di strati più spessi. Oltre a ciò, rimangono necessarie alcune fasi di post-elaborazione aggiuntive, quali levigazione, smussatura e rivestimento. Scegliere un filamento di polietilene tereftalato glicole o polipropilene è un altro buon modo per cercare di ottimizzare l'ermeticità, anche se questi metodi non sono adatti all'utilizzo delle parti in ambienti pressurizzati.
Stereolitografia (SLA)
Al contrario, le parti stampate in 3D tramite stereolitografia (SLA) sono ermetiche, perché ogni strato è legato chimicamente a quello successivo. Questa tecnologia sfrutta un laser che polimerizza la resina liquida uno strato per volta, creando un legame incrociato tra le catene di polimeri all'interno di ciascuno strato, nonché con gli strati immediatamente precedenti e successivi. Questo procedimento permette di creare una finitura superficiale liscia, praticamente senza linee degli strati, e una superficie non porosa attraverso la quale l'acqua non può penetrare. Queste parti hanno tolleranze estremamente buone, per cui gli assemblaggi a più componenti, come gli alloggiamenti utilizzati per i test di questo articolo, possono essere filettati gli uni negli altri senza quasi alcuno spazio d'aria tra di loro. Se abbinati a una sigillatura o a una guarnizione, gli alloggiamenti diventano completamente ermetici e possono sopportare pressioni estremamente elevate.
Sinterizzazione laser selettiva (SLS)
Per la creazione delle parti, la tecnologia di sinterizzazione laser selettiva (SLS) si basa sulla sinterizzazione di una sezione trasversale del pezzo sopra un letto di polvere, che viene poi ricoperto con altra polvere procedendo in tal modo fino al completamento della parte. Le parti risultanti sono in una certa misura isotropiche, ma possono presentare differenze in termini di proprietà meccaniche a seconda della direzione di applicazione della forza. Le parti SLS sono ermetiche se progettate con le tolleranze e le tecniche di sigillatura adeguate.
Consigli di progettazione per la stampa 3D di parti ermetiche
Come già detto, l'ermeticità di un alloggiamento dipende sia dall'ermeticità dei componenti stessi, sia dal design della parte, ovvero da come questi componenti sono assemblati tra loro. Le tecnologie di stampa 3D SLA e SLS sono in grado di creare componenti con tolleranze così ridotte che gli alloggiamenti con elementi di interblocco o filettature possono essere completamente ermetici senza effettuare ulteriori passaggi. Tuttavia, in ambienti estremamente pressurizzati come quelli testati in questo esperimento, fasi supplementari come l'aggiunta di O-ring possono aumentare l'efficacia degli alloggiamenti.
Design dell'alloggiamento
L'URIL punta a democratizzare la ricerca in acque profonde. Stampanti 3D a prezzi accessibili come la Form 3+ e la Form 3L di grande formato hanno reso possibile la progettazione e fabbricazione di strumenti altamente sofisticati per l'esplorazione subacquea e la condivisione di questi design con l'intera comunità scientifica.
L'URIL ha pubblicato diversi articoli sulla sua ricerca in acque profonde, tra cui una guida al design innovativo di DEEPi, sistema di imaging e controllo in acque profonde, una ricerca sull'uso della stabilizzazione passiva per supportare la stampa SLA a bordo di un'imbarcazione in movimento e un'indagine sull'uso della biomimesi nella progettazione di alloggiamenti basata sulle forme dei nautiloidi.
Il ricercatore principale Brennan Philips e la dottoranda Breanna Motsenbocker hanno eseguito per anni iterazioni delle loro telecamere subacquee e alloggiamenti robotici, pubblicando diversi articoli per illustrare i risultati del loro lavoro. Il laboratorio ha pubblicato il proprio design opensource nel tentativo di rendere il processo di fabbricazione accessibile alle comunità prive dei fondi necessari per portare avanti la raccolta di dati o la ricerca subacquea.
L'URIL ha reso accessibili in forma opensource e disponibili per la riproduzione pubblica entrambi i design, uno utilizzato nei test con pareti sottili e l'altro, non testato, con pareti più spesse. Per avere accesso a questi design, scarica il whitepaper completo.
Design biomimetici
Philips e Motsenbocker, in collaborazione con altri team di ricerca, hanno anche studiato come i design biomimetici possono migliorare la funzionalità dei loro alloggiamenti ermetici. In un articolo pubblicato nell'ottobre del 2023, i team di ricerca hanno osservato come il guscio del Nautilus pompilius (un membro della famiglia dei molluschi) impedisca all'acqua di penetrare all'interno, anche a profondità estreme. I risultati potrebbero far luce su come le complesse morfologie del loro guscio possano indicare geometrie resistenti alla pressione, paragonabili a quelle "ideali" attualmente utilizzate nella robotica marina per acque profonde, ovvero sfere e cilindri semplici, che hanno un rapporto superficie/volume ridotto al minimo e un processo di produzione più facile. Per scoprire i risultati completi della loro ricerca, leggi l'articolo pubblicato sulla rivista.
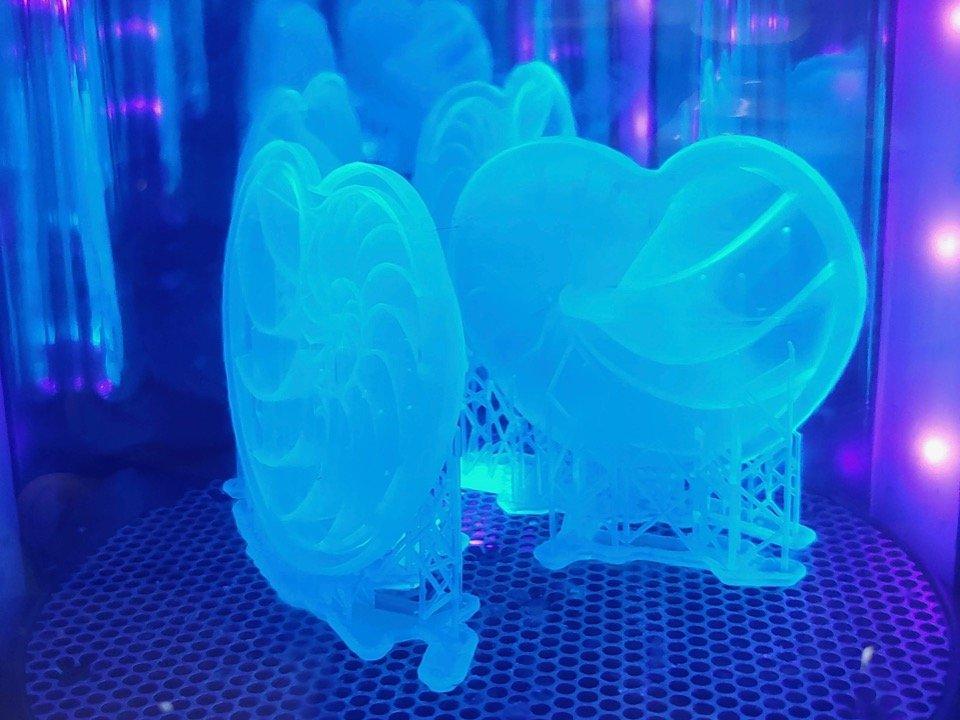
Questi componenti stampati in 3D sono stati progettati ispirandosi al Nautilus pompilius, un membro della famiglia dei molluschi che può sopportare pressioni estremamente elevate sott'acqua senza subire danni al guscio.
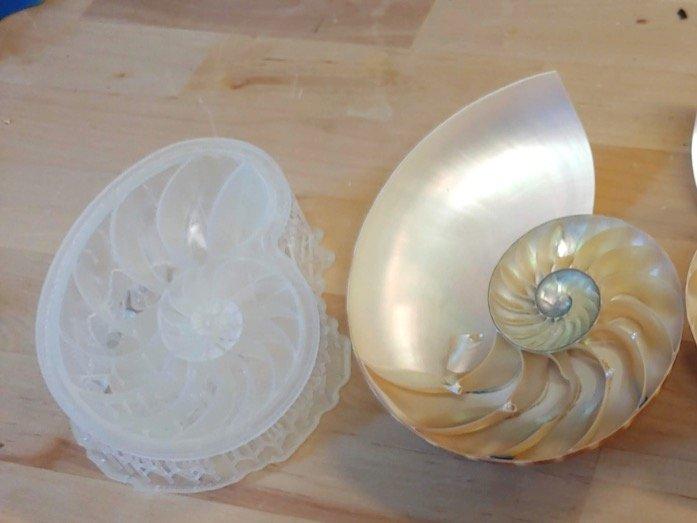
La scansione dei molluschi (a destra) e l'utilizzo del design digitale per ricreare la loro geometria per la stampa 3D (a sinistra, in Clear Resin) possono aiutare i team di ricerca a capire come questi animali si sono evoluti per sopravvivere in ambienti inospitali.
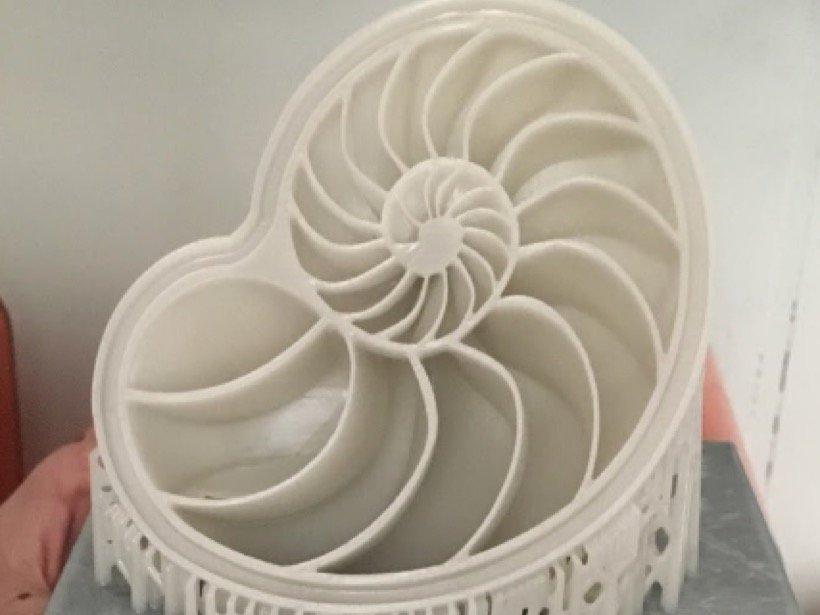
Questa parte più grande, stampata in White Resin, potrebbe essere utilizzata per racchiudere piccole telecamere per la ricerca in acque profonde.
Come scegliere un O-ring per un alloggiamento ermetico stampato in 3D
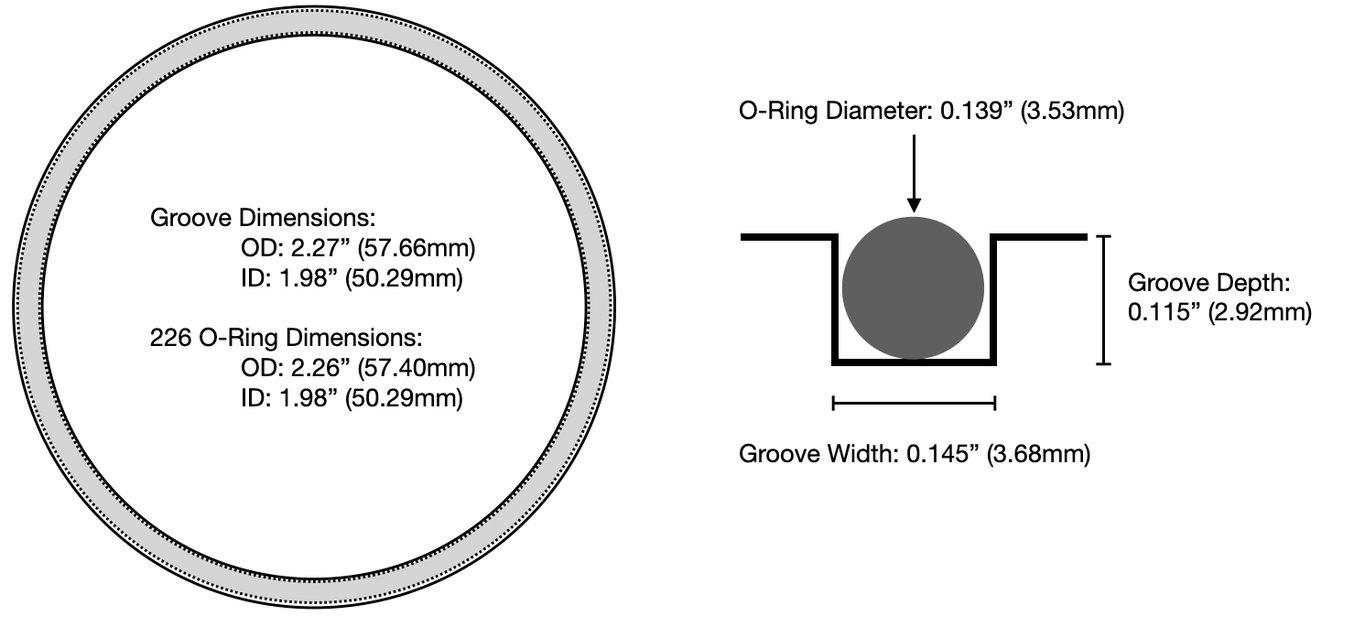
L'URIL ha sperimentato con successo sia guarnizioni O-ring di tenuta frontale sia guarnizioni a foro, preferendo tuttavia il primo tipo di soluzione.
Una volta scelti i diametri interno ed esterno dell'alloggiamento, è possibile selezionare un O-ring di tenuta frontale in base al diametro interno. L'O-ring deve aderire correttamente alla superficie tra il cappuccio protettivo e il corpo. Gli O-ring con numero di riferimento che inizia con "2", o quelli con una larghezza frazionaria di ⅛" (0,139"), creano la tenuta più affidabile per le parti stampate tramite SLA. Per conoscere le raccomandazioni e i risultati specifici dell'URIL, scarica il whitepaper completo.
Stampa 3D di parti ermetiche: test e risultati
Per creare gli alloggiamenti sono state utilizzate le tecnologie di stampa 3D FDM, SLA e SLS. La Nylon 12 GF Powder è stata stampata sulla macchina 3D SLS Fuse 1+ 30W, mentre gli altri materiali (ovvero la Grey Resin, Clear Resin, BioMed Amber Resin e Rigid 10K Resin) sono stati stampati sulla macchina 3D SLA Form 3+. Le parti stampate tramite modellazione a deposizione fusa su una stampante Craftbot con filamento di acido polilattico hanno dimostrato di assorbire l'acqua immediatamente dopo l'immersione e sono state quindi eliminate dai test.
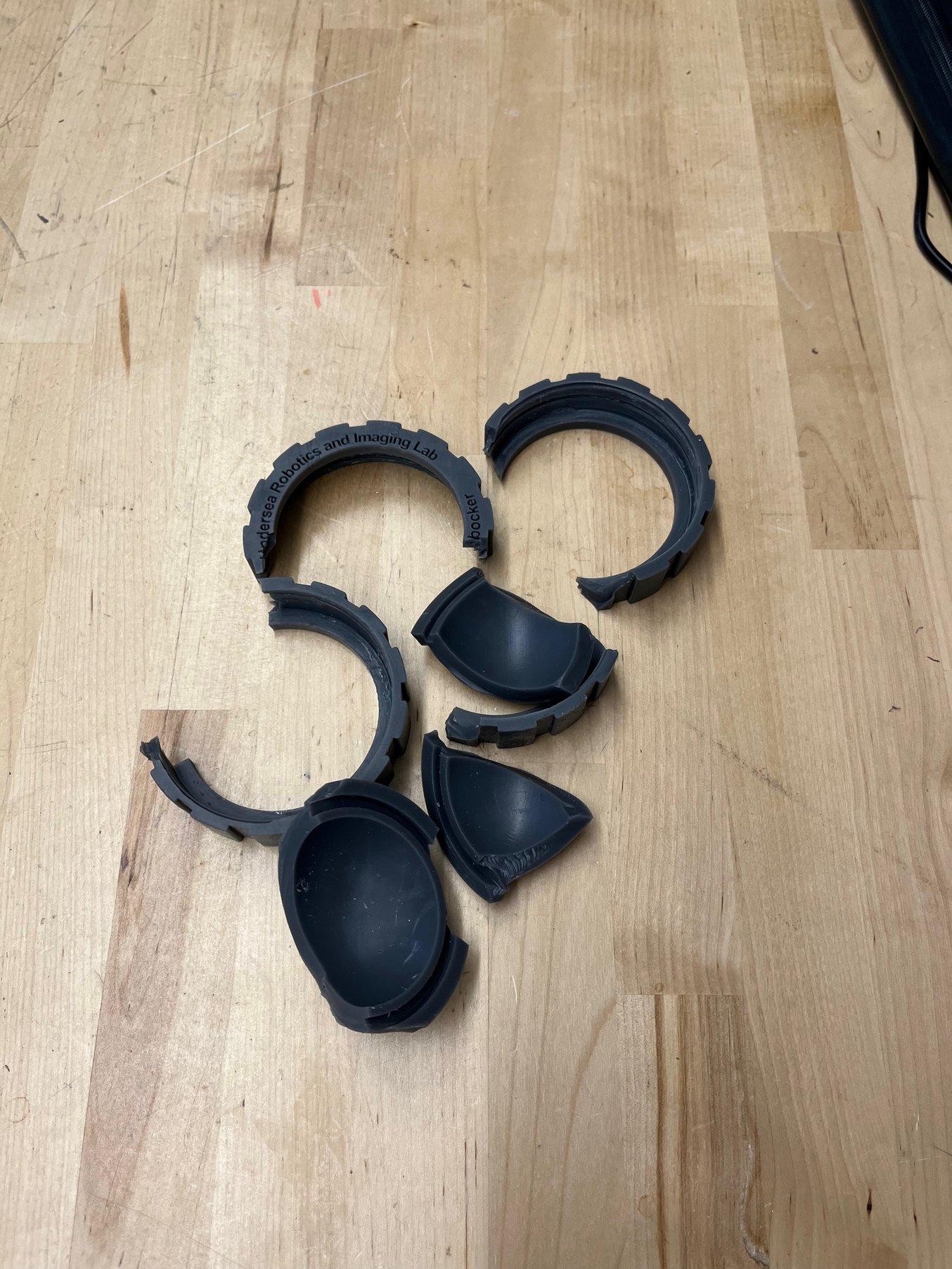
La parte creata in Nylon 12 GF Powder è implosa alla pressione più bassa, ovvero una media di 1304 psi.
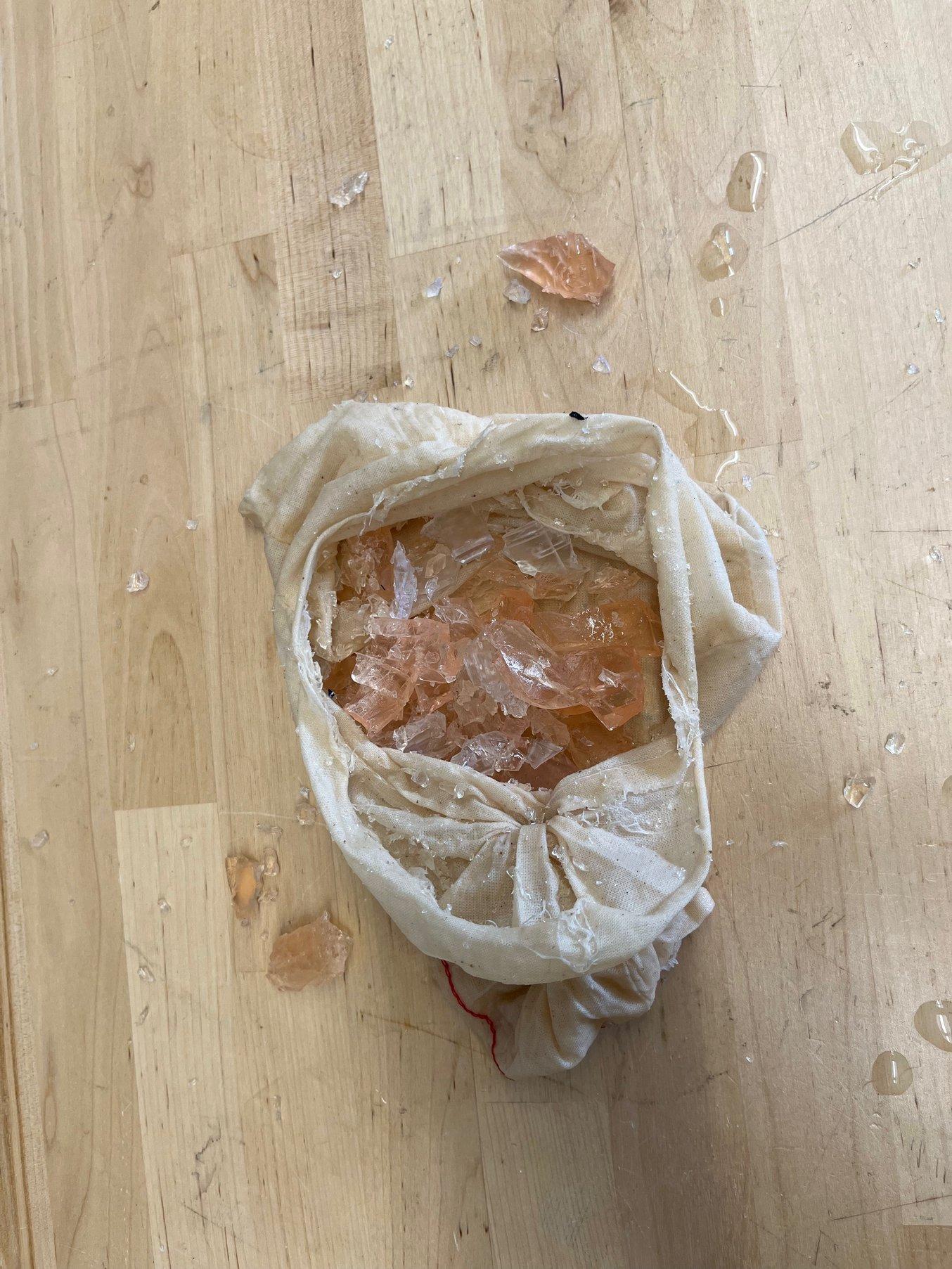
La BioMed Amber Resin ha resistito a una pressione molto più elevata, implodendo a una media di 2907 psi.
I risultati hanno dimostrato che la stampa 3D SLA e SLS, se unite all'utilizzo di guarnizioni O-ring, sono metodi efficaci per creare alloggiamenti ermetici. Tra le due, la stampa 3D SLA ha fornito i risultati migliori: alcune parti realizzate con questa tecnologia hanno resistito a una pressione estrema, equivalente a profondità di 4000 m sotto il livello del mare. Le parti stampate in FDM sono risultate inadatte a questa applicazione, poiché assorbono acqua immediatamente dopo l'immersione e non riescono a sopportare alcun tipo di pressione.
I materiali SLA più rigidi hanno fornito le migliori prestazioni sotto pressione. Inoltre, metodi di post-elaborazione come la sabbiatura possono ottimizzare ulteriormente le prestazioni delle parti riducendo la porosità di superficie. Per scoprire i risultati completi e il comportamento di ciascun materiale, scarica il nostro whitepaper.
Per saperne di più sulla robotica subacquea e su come sfruttare le stampanti e i materiali 3D per realizzare alloggiamenti completamente ermetici e resistenti alla pressione, parla con il nostro team, che ti metterà in contatto con le persone esperte della rete Formlabs attualmente impegnate in queste applicazioni.