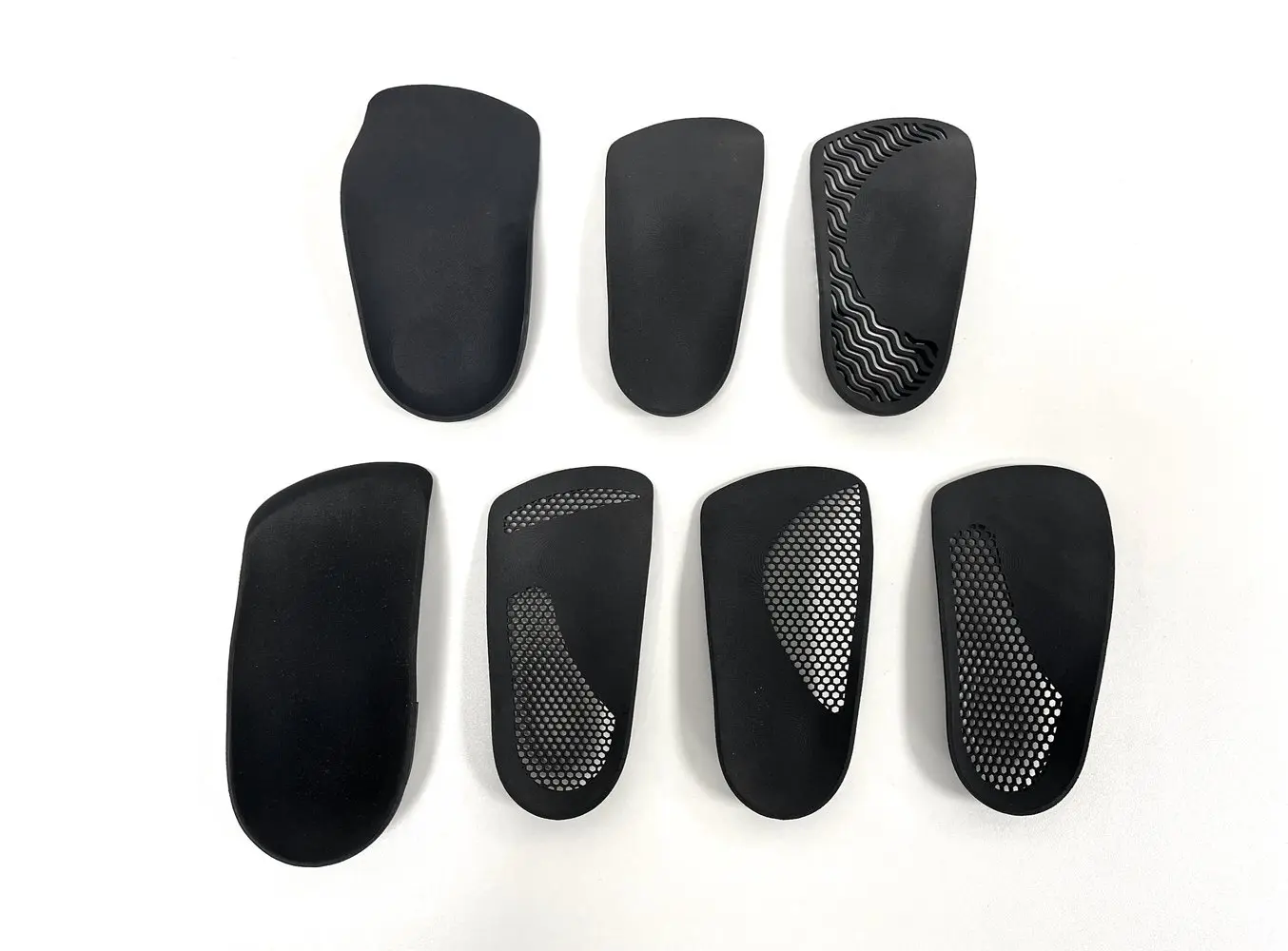
MAG Orthotics Limited in Sheffield, UK, offers bespoke products and repairs to the orthotic and podiatry markets. The company is working to move into the digital future, recently adopting 3D printing to save resources, time, and materials. But transitioning to digital workflows involves not just the manufacturing process, but the choices of the entire network of orthotists and podiatrists MAG works with.
Orthotic manufacturers work within a complex ecosystem that’s still between old manufacturing systems and new ones. Working with distributor Additive-X, software provider Fit360, and their network of podiatrists and orthotists, MAG Orthotics is trying to push the market to digital workflows. As part of this complex network, MAG Orthotics has had to leverage the experience of their partners while also educating providers and specialists on the benefits digital workflows and 3D printed products have to offer.
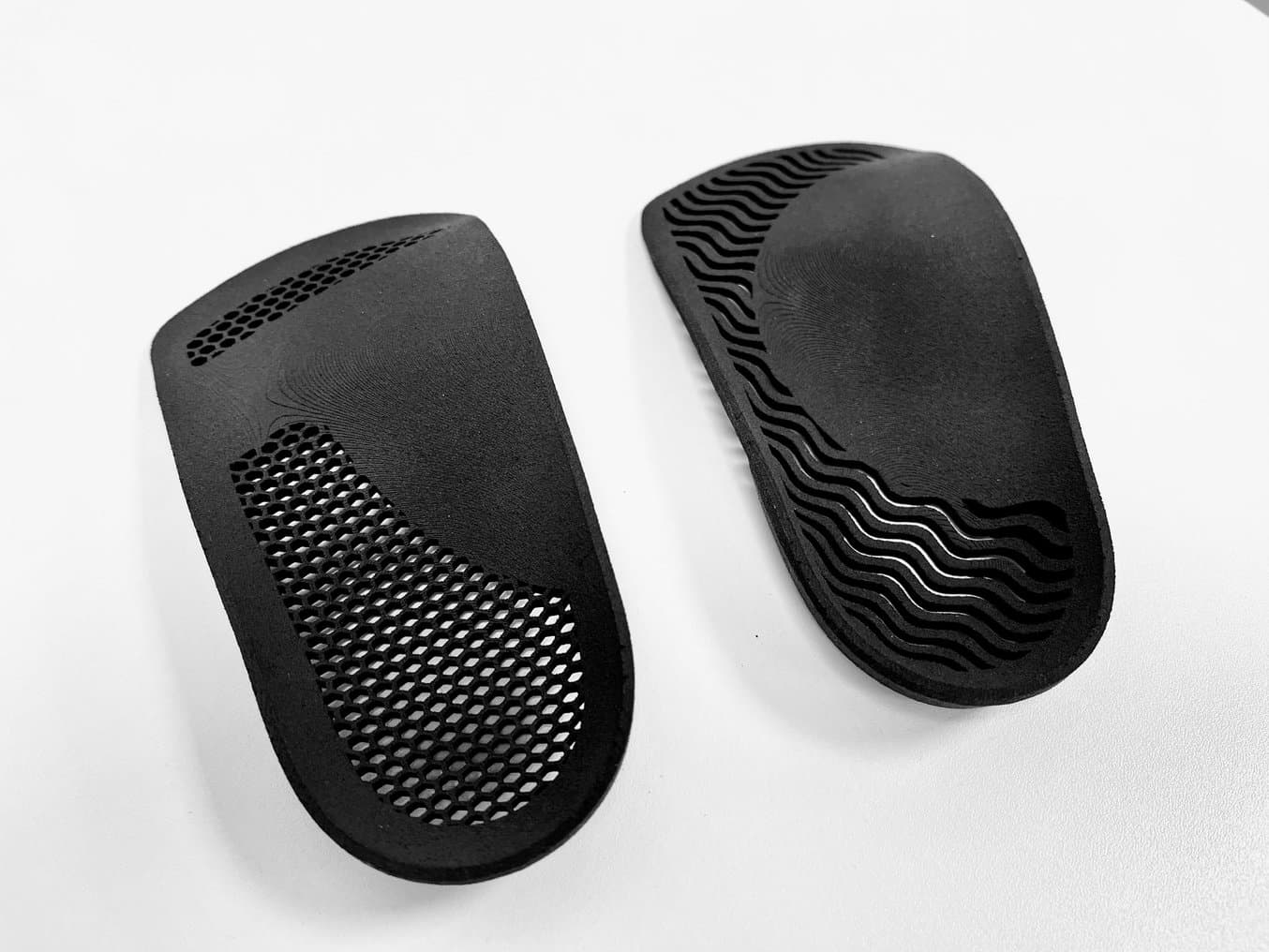
The Future of Insole Production and Zero Waste-to-Landfill with MAG Orthotics: Transforming Practices with Formlabs and FIT360
Discover the power of digitizing the insole production including to design and print. Hear firsthand from MAG Orthotics about their journey to 3D printing and commitment to sustainability.
The Complex Ecosystem
MAG Orthotics works with orthotists and podiatrists at the National Health Service (NHS), separate hospitals, and private clinics around the United Kingdom. Lee Lingard is the CAD and 3D development specialist for MAG Orthotics, running all 3D printing for the company. Podiatrists and orthotists will either send MAG Orthotics a scan via email or a physical foam impression box (FIB) which MAG will then scan. This prescription is then sent to Lingard, who will determine the best way to design and manufacture the device.
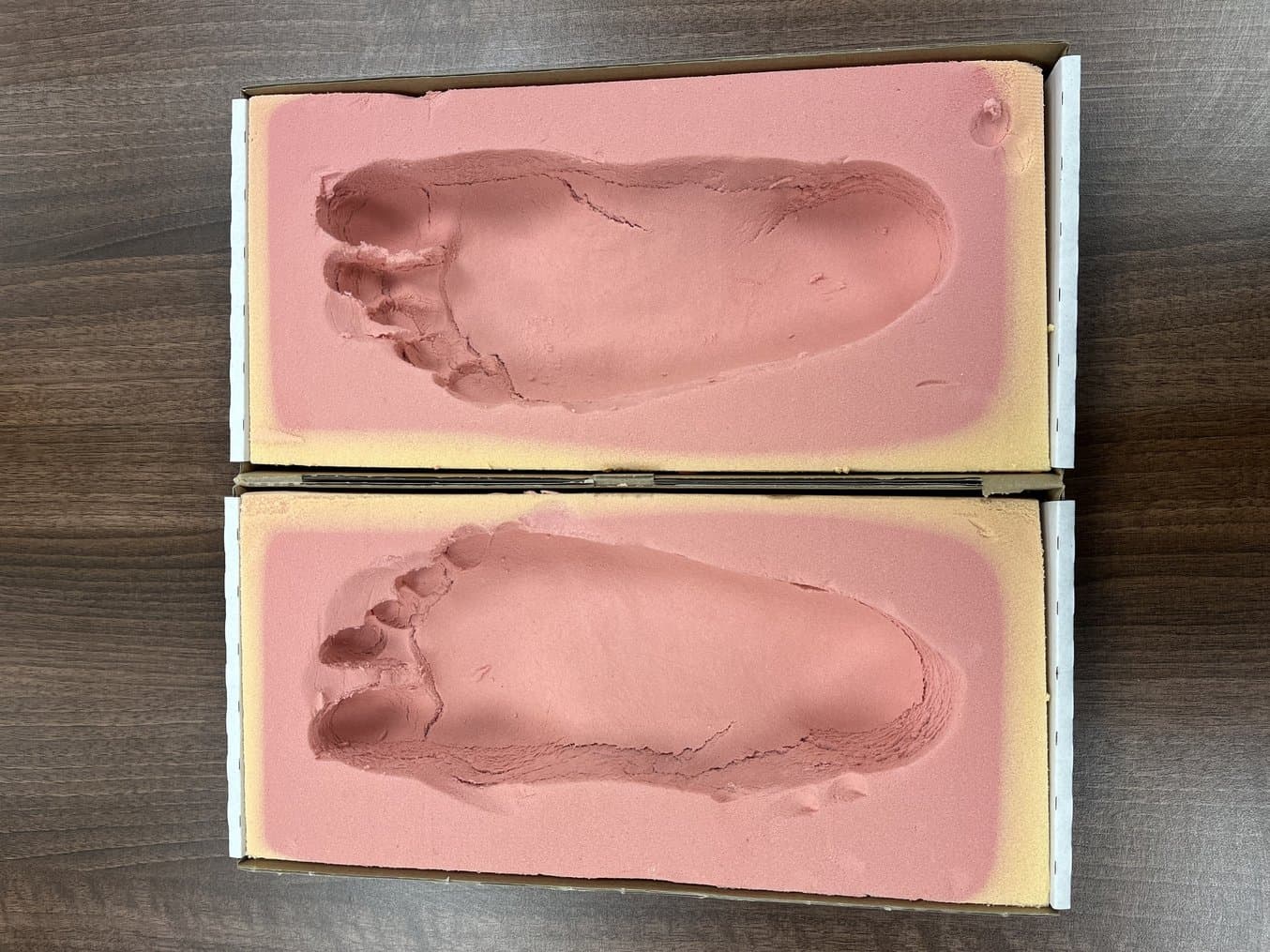
Some orthotists and podiatrists still send a physical foam impression box (FIB) to MAG Orthotics.

FIBs must first be scanned, adding time over a purely digital workflow.
Design at MAG Orthotics is done with Fit360, CAM software for designing custom orthotics for milling, machining, and 3D printing. Choosing which method of fabrication will be used is primarily dependent on the material requested by the orthotist. At MAG Orthotics, manufacturing devices is done on CNC machines, an FDM printer, and two Formlabs Fuse 1+ 30W selective laser sintering (SLS) 3D printers.
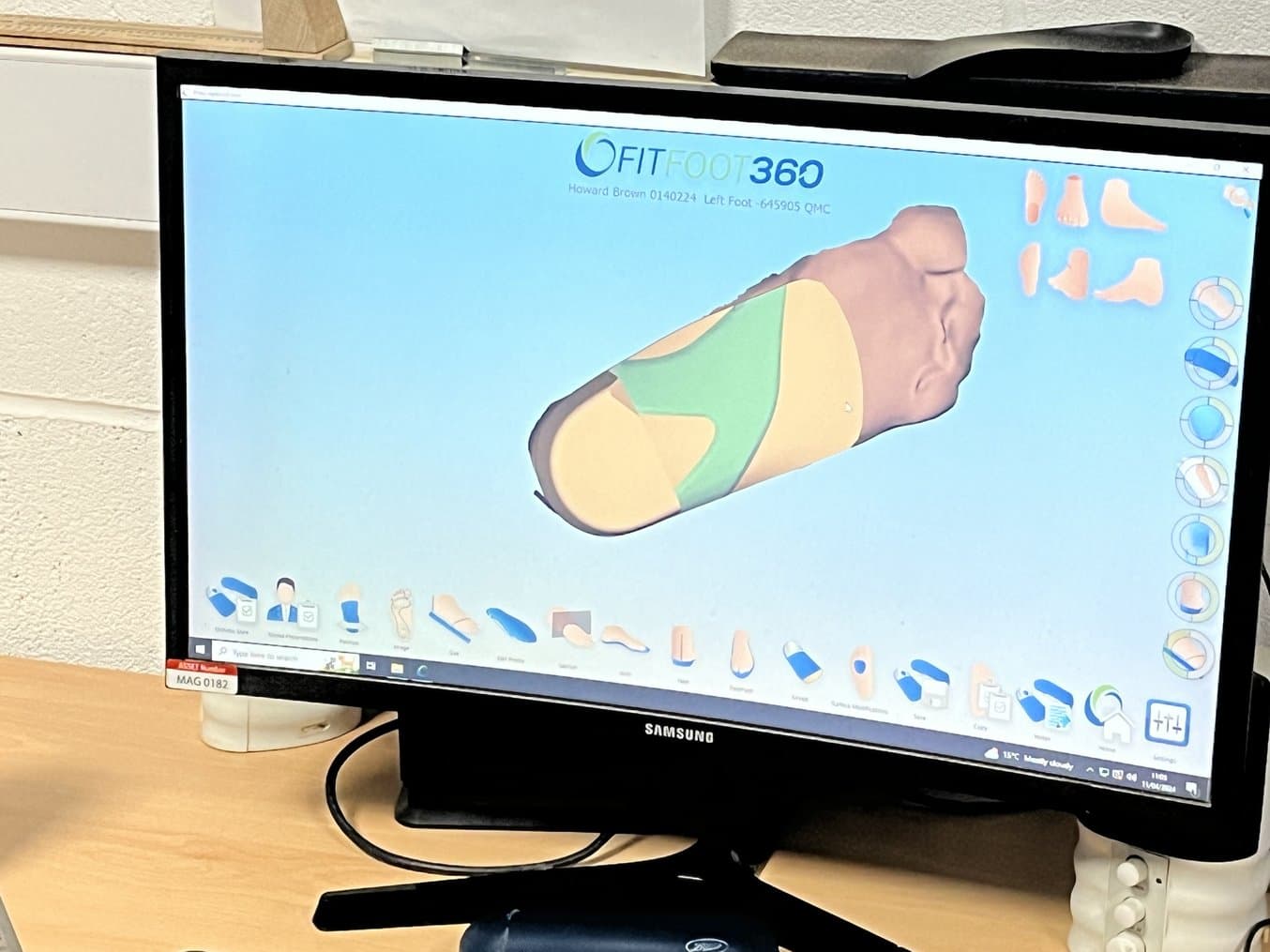
MAG Orthotics uses Fit360 software to design their insoles.
Chris Lawrie, owner and CEO of Fit360, says, “The great thing about our relationship with MAG is that they can choose in the software whether that's going to be milled, whether that's going to be printed as rigid or whether it's actually going to be printed as a soft device through a different method as well.” At a time when the production of orthotics is transitioning between manufacturing technologies and materials, these options enable MAG to deliver the orthotic prescribed while incorporating a consistent design workflow.
Stepping Away From Traditional Methods
Moving from a traditional, milled product to a printed product is difficult, as new technology and its associated workflows must be learned. Lingard says, “If something new comes out, I'm eager to get in and learn it, so to me it was exciting. I love technology.”
But while Lingard is embracing the digital future, the industry as a whole has yet to transition. “I've been doing CAD design for 15 years now,” says Lingard, “but we still get the odd orthotist that will still ask for the traditional way. So you can see our big gap.”
This big gap is a reason MAG still uses some traditional methods of production. As a lab, their role is to interpret prescriptions into shape. Right now, that still involves some legacy mills as they work to shift manufacturing to digital processes that are more environmentally sustainable.
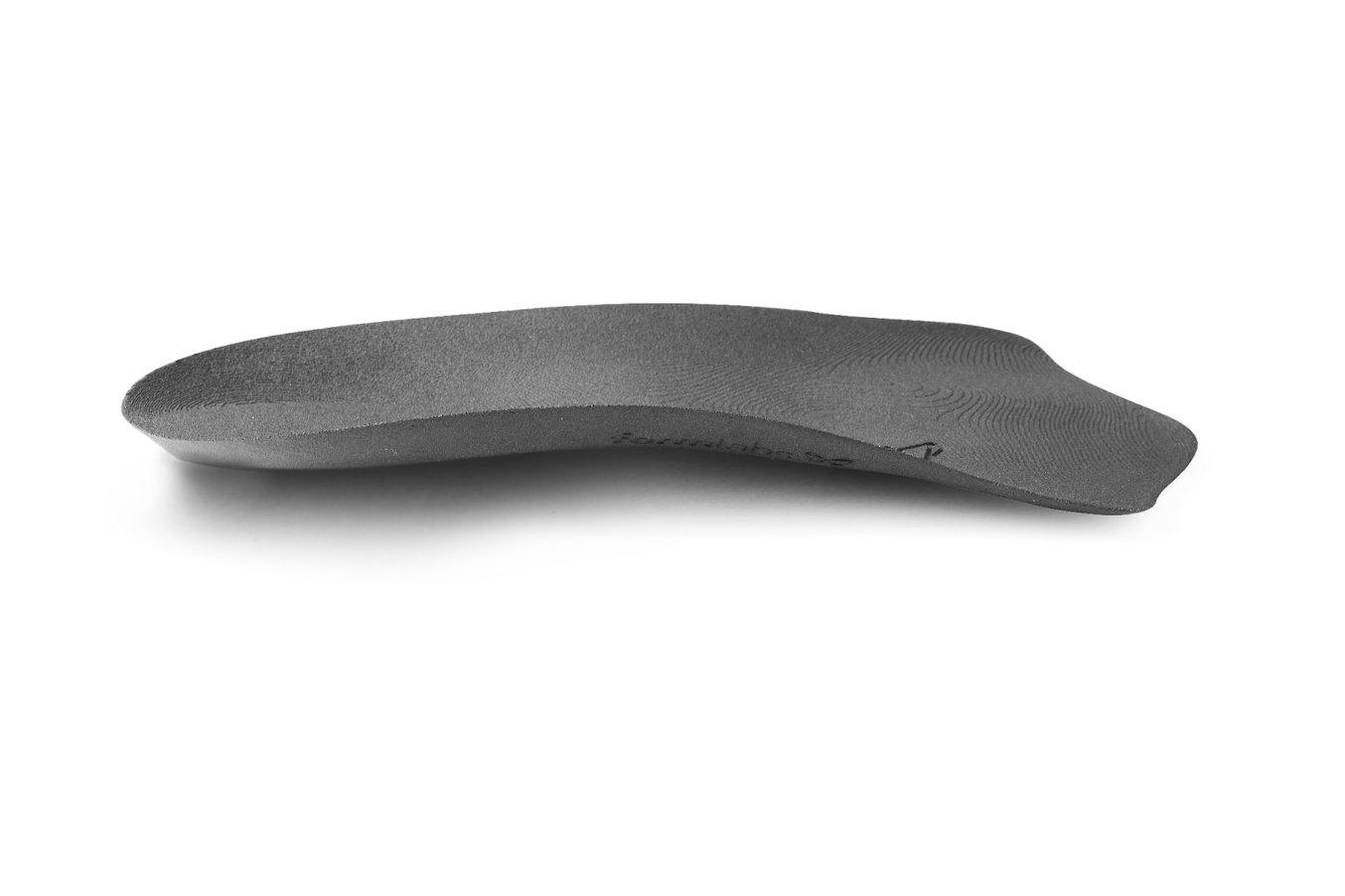
Request Your 3D Printed Insole Shell Sample Part
Discover the power of Nylon 11 Powder and revolutionize your insole game. Experience excellent energy return and durability, independently tested to exceed four million steps.
Embracing SLS 3D Printing
MAG Orthotics Works Manager Mark Joyce sees 3D printing as a big step in moving to more sustainable processes. At first, MAG outsourced their 3D printing, just to see how it went. Outsourcing was costly and added time, as orthotics had to be shipped back to MAG Orthotics. At that point, Joyce says, “We thought, well, we needed to be able to get into the industry itself.”
Joyce worked with Additive-X to find a printer that would best suit their operations. Key factors in their evaluation were cost, longevity, and reliability. Researching other SLS printers, Joyce found that most other solutions were too complex and expensive, and landed on the Fuse 1+ 30W as a printer with the materials, hardware, and price point that fit their requirements.
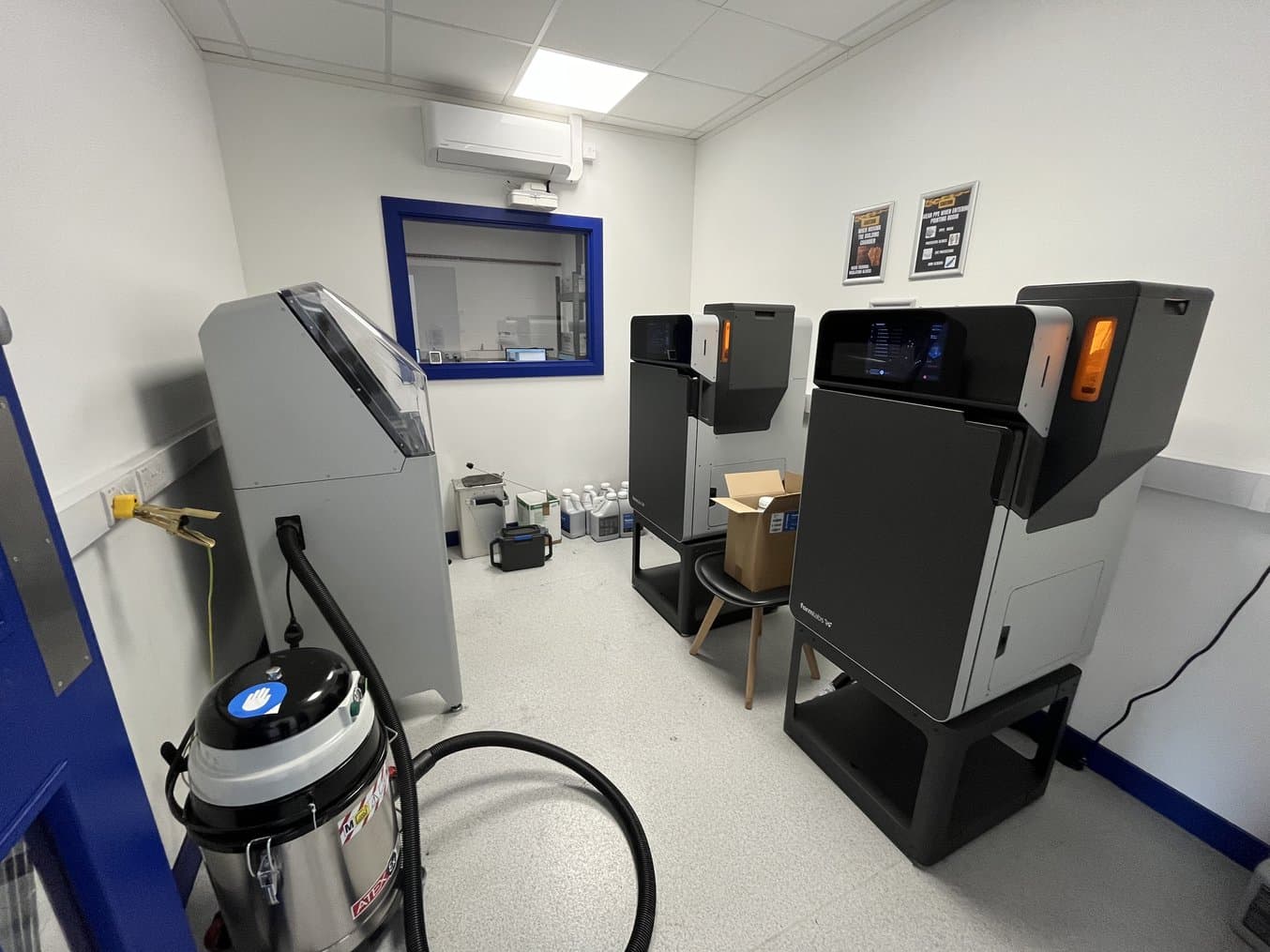
MAG Orthotics prints in-house on two Fuse 1+ 30W 3D printers (right) which adds redundancy to their production.
The team now prints on the Fuse every day. Lingard says, “We're still milling the CNCs, but we're trying to phase these in if we can.” But one of the biggest hurdles to embracing digital workflows hasn’t been internal.
“Our biggest battle is the orthotists because they like the old ways, it's hard to get them to move forward onto these new technologies,” says Lingard. To tackle this problem, Lingard has begun offering orthotists a pair of 3D printed insoles and EVA ones to compare for themselves. One orthotist, who is a runner and hiker, found she liked the 3D printed insoles once she’d tried them for a week.
“It's a cost to ourselves because obviously it's time, lead time, materials, et cetera. And we're doing that basically to try and get people to buy into these new technologies,” says Lingard. But by investing now, MAG Orthotics is paving the way for cleaner, faster production down the line.
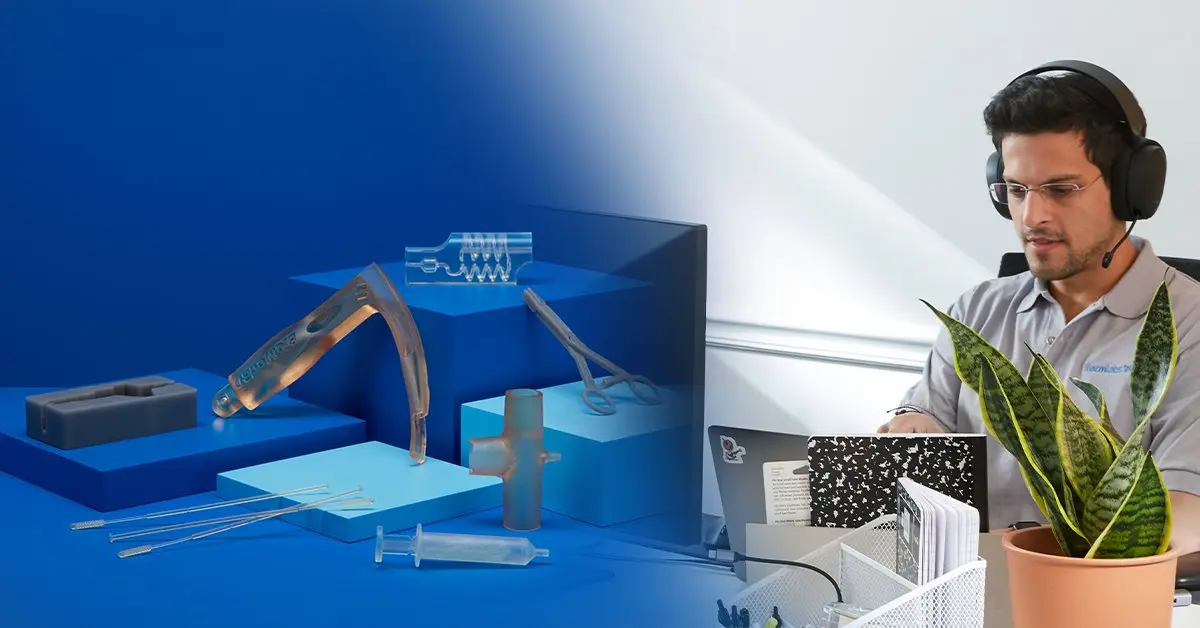
Talk to Our Medical Sales Team
Whether you need to make patient-matched surgical tools or are prototyping for a cardiac medical device, we’re here to help. Formlabs Medical team are dedicated specialists who know exactly how to support you and your company's needs.
Zero Waste
In the UK, “zero to landfill” policies and carbon footprint are taken into account when tendering for a contract. Part of MAG Orthotics’ goal in shifting to digital workflows and 3D printing is minimizing the waste involved in production.
“We used to use a lot of plaster, so it'd be hand-molded with plaster and then molded around the plaster with EVA or polypropylene. We then moved forward and we started using CAD design and using CNC machines to mill them, but there was still a lot of waste. But with powder and TPU there's very, very little waste and that's the way forward environmentally.”
Mark Joyce, General Manager, MAG Orthotics
As an SLS printer, the Fuse 1+ 30W prints powder. Unlike CNC, in which material that is not a part of the finished insole is thrown away, the unfused powder in each build can be recycled into the next build.
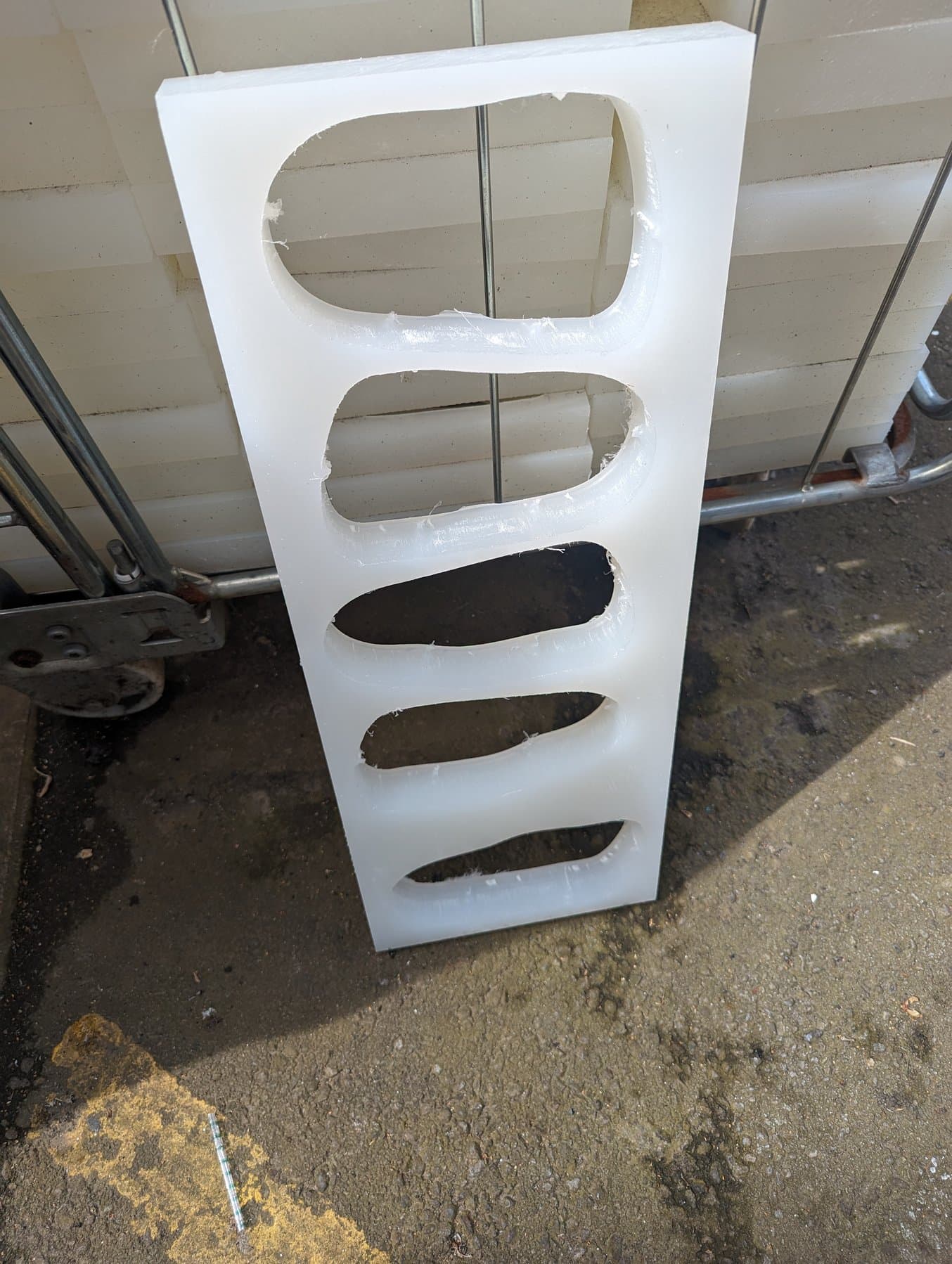
Polypropylene material waste from CNC manufacturing adds up quickly.
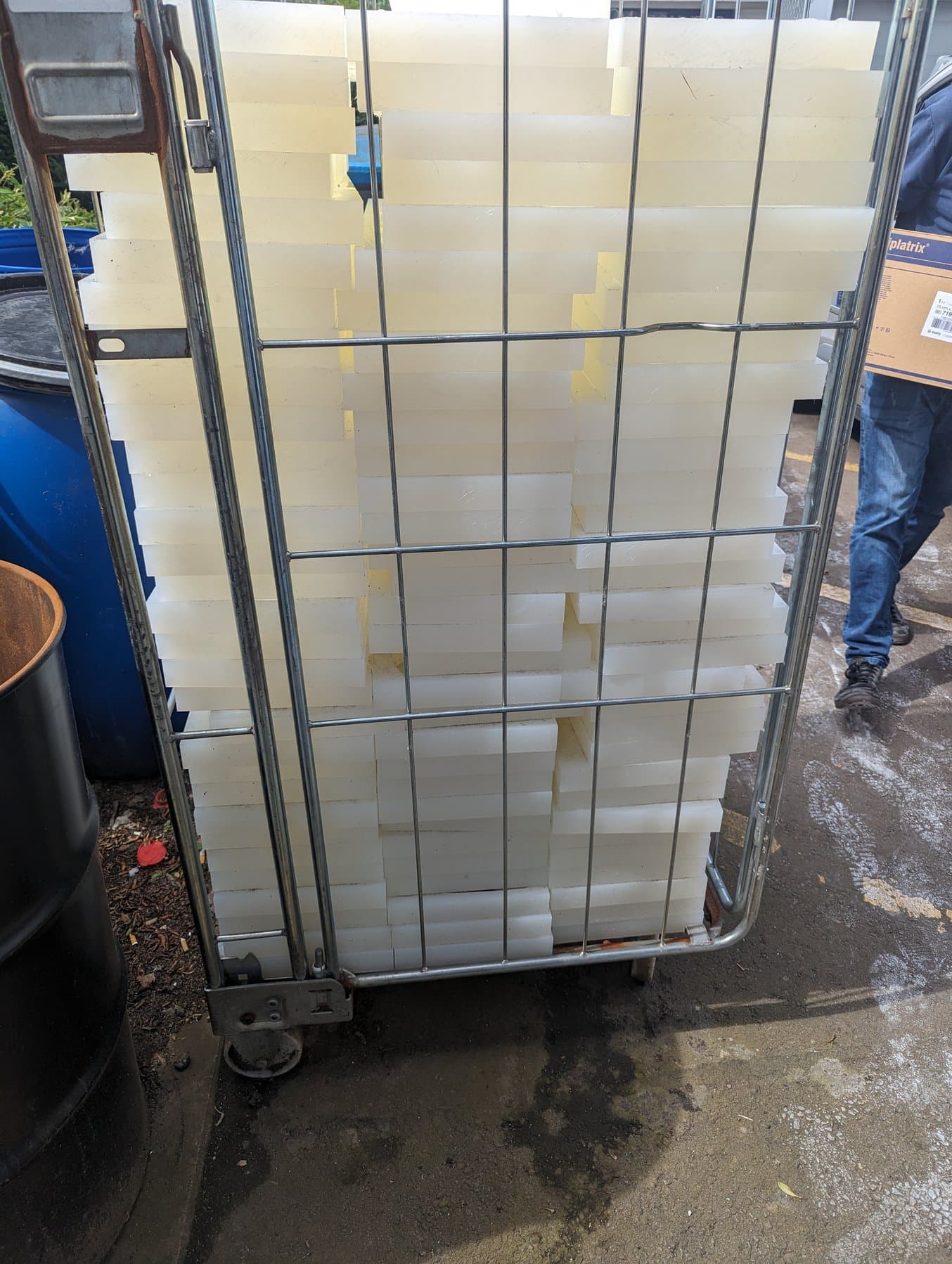
Reducing this accumulated waste is a primary reason MAG Orthotics has adopted 3D printing.
MAG prints insoles in Nylon 11 Powder, which is a strong and highly ductile material approved for skin contact. Nylon 11 Powder prints absorb very little moisture and are resistant to light, heat, and chemicals, making it an ideal material for insole production. Printing Nylon 11 Powder with inert atmosphere, in this case nitrogen, means there is less oxidation of the powder, leading to higher refresh rates and even less waste.
Additionally, by not having to collect physical impressions from providers, they’re using less fuel and putting less wear and tear on a vehicle, for a process that is better environmentally from start to finish.
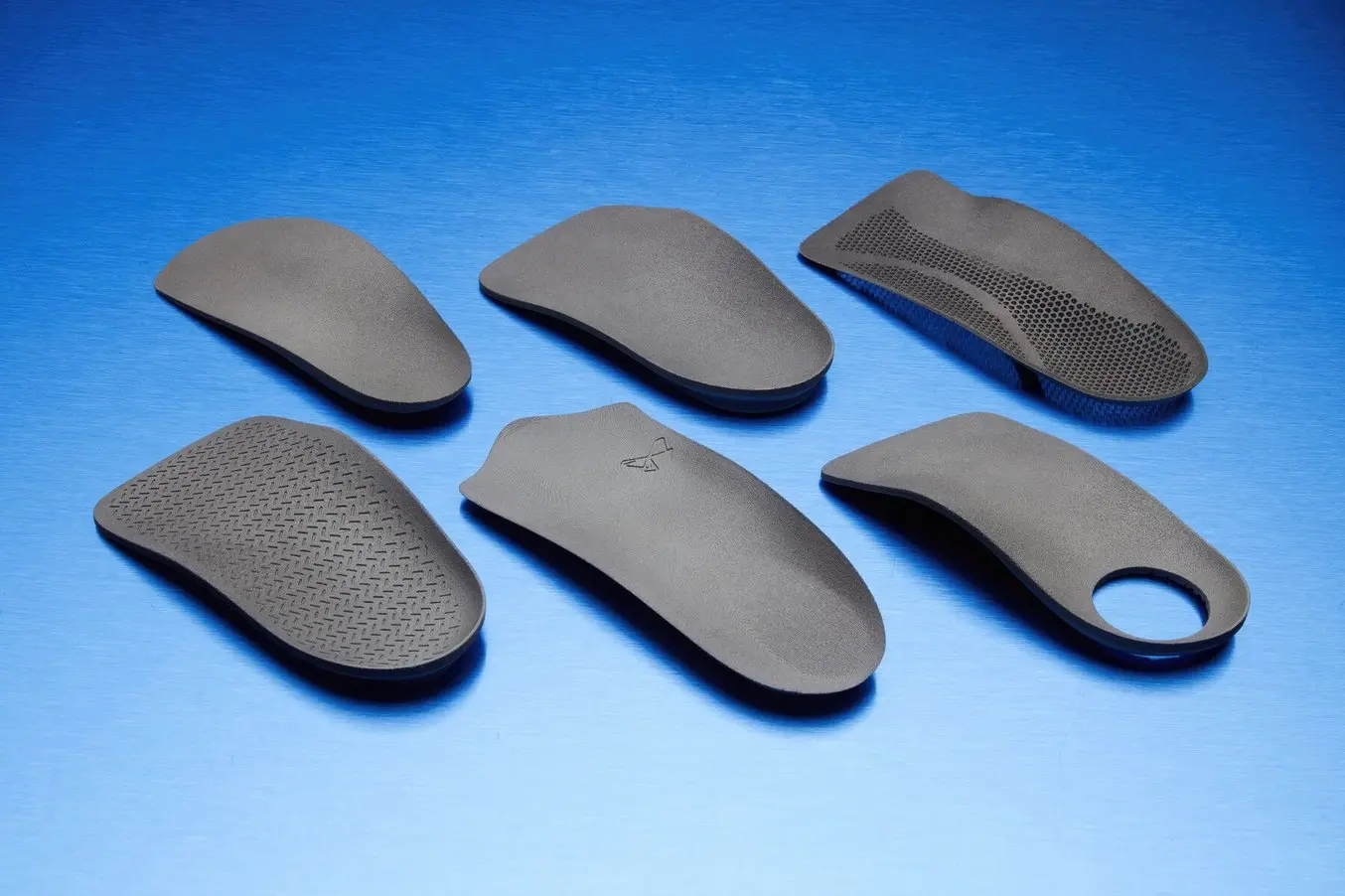
Revolutionize Your Insole Production With Formlabs Fuse 1+ 30W
Step up your insole production while saving time and money. In this webinar, we discuss why Formlabs Fuse 1+ 30W is the perfect solution to begin transitioning to digital manufacturing or scaling your production affordably and efficiently.
Time Savings
Digital workflows have tremendous potential to decrease production timelines. Traditional impressions require driving to clinics to pick up impressions. MAG is working on “Convincing businesses and clinics to invest in a handheld scanner where they can scan the foot,” says Joyce. If a scan and prescription “came just via a quick link via email that's straight in, that's three days you're saving straight away,” says Joyce.
“On an EVA from a CNC, you've got all your flash, the wastage you have to cut off, and you have to put the templates on, cut round all that, then smooth it all in, shape it all, so it takes a lot longer. This is why we like 3D printed insoles, because they're a lot quicker and a lot less work on the bench.”
Lee Lingard, CAD and 3D Development Specialist, MAG Orthotics
With digital workflows, a podiatrist can submit a digital scan and order on Monday morning. An hour later, the order will be processed and, within an hour, it’s possible for Lingard to design the orthotic insoles. Then, the insoles are printed Monday afternoon, with printing happening overnight. By the next day, the insoles could be cleaned and finished, for turnaround in a little more than a day.
In comparison, using FIB boxes takes about 72 hours longer, as it adds collection time and administrative processing time to the order. While the actual print time may be longer than simply the time a worker spends using a CNC machine, a CNC requires hands-on use and significant post-processing. Once a 3D printer is prepared, the actual print time is completely hands-off, freeing up workers for higher-value tasks or enabling printing overnight. Insoles from an SLS printer need cleaning, but require little else in terms of post-processing, meaning the overall digital workflow takes less time and labor. Overall, Joyce says they minimize turnaround time for orders by producing insoles with 3D printing — in addition to decreasing their carbon footprint.
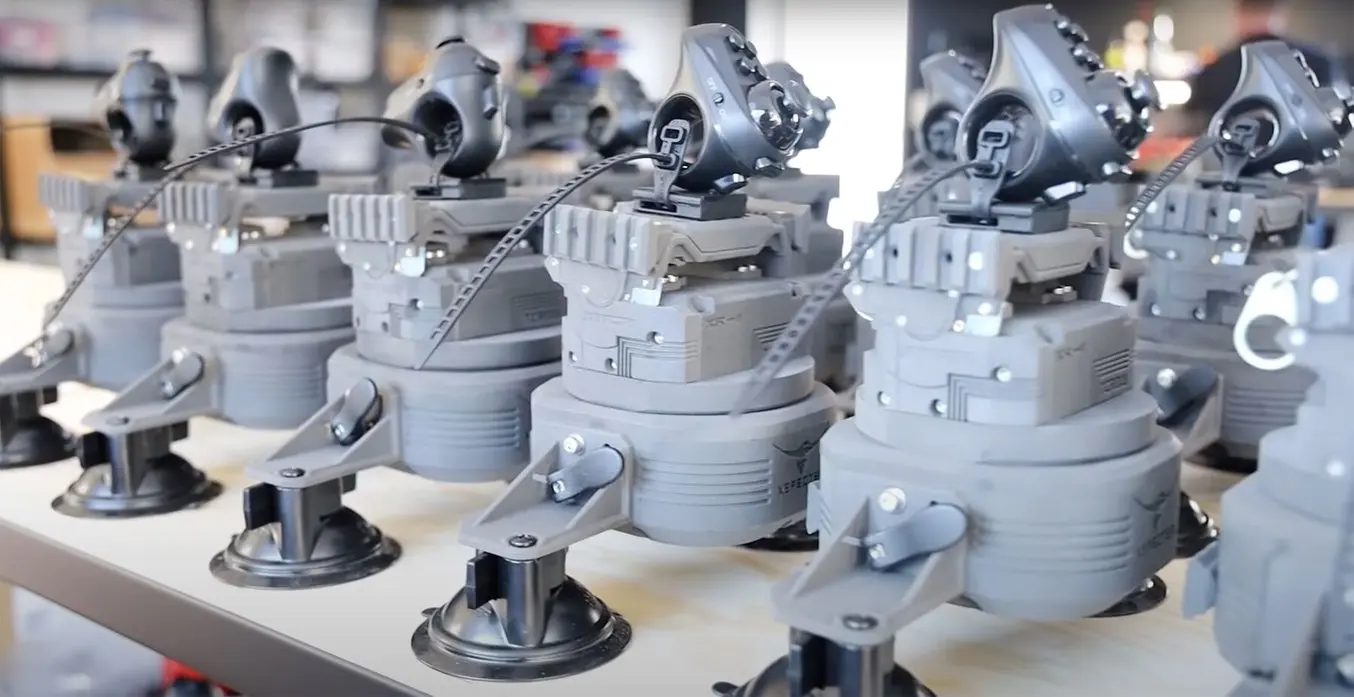
SLS for End-Use Production
3D printing for end-use production is not only possible, it's more affordable, agile, and scalable than ever with the Fuse SLS Ecosystem. Visit our SLS for Production page to compare production methods, learn about bulk powder pricing, and see production in action for 15 different manufacturers currently using the Fuse Series.
Striding Into the Future
As MAG Orthotics continues to work with orthotists to shift to digital workflows, they are scaling their SLS production. Two Fuse 1+ 30W 3D printers add redundancy for printing, ensuring there can always be at least one printer running. MAG Orthotics is also looking into the option of providing vapor smoothing, a common post-processing step performed on SLS 3D printed parts to improve porosity and reduce roughness, for a slicker, shinier texture.
Working with Fit360, Additive-X, Formlabs, and their network of orthotists and podiatrists, the team at MAG Orthotics is working to shift toward digital workflows — and their zero waste goals. Adding 3D printing technologies, like the Fuse 1+ 30W, are helping them get there.
Learn more about 3D printing orthotic insoles or talk to a 3D printing expert to find the solution that’s right for your business.
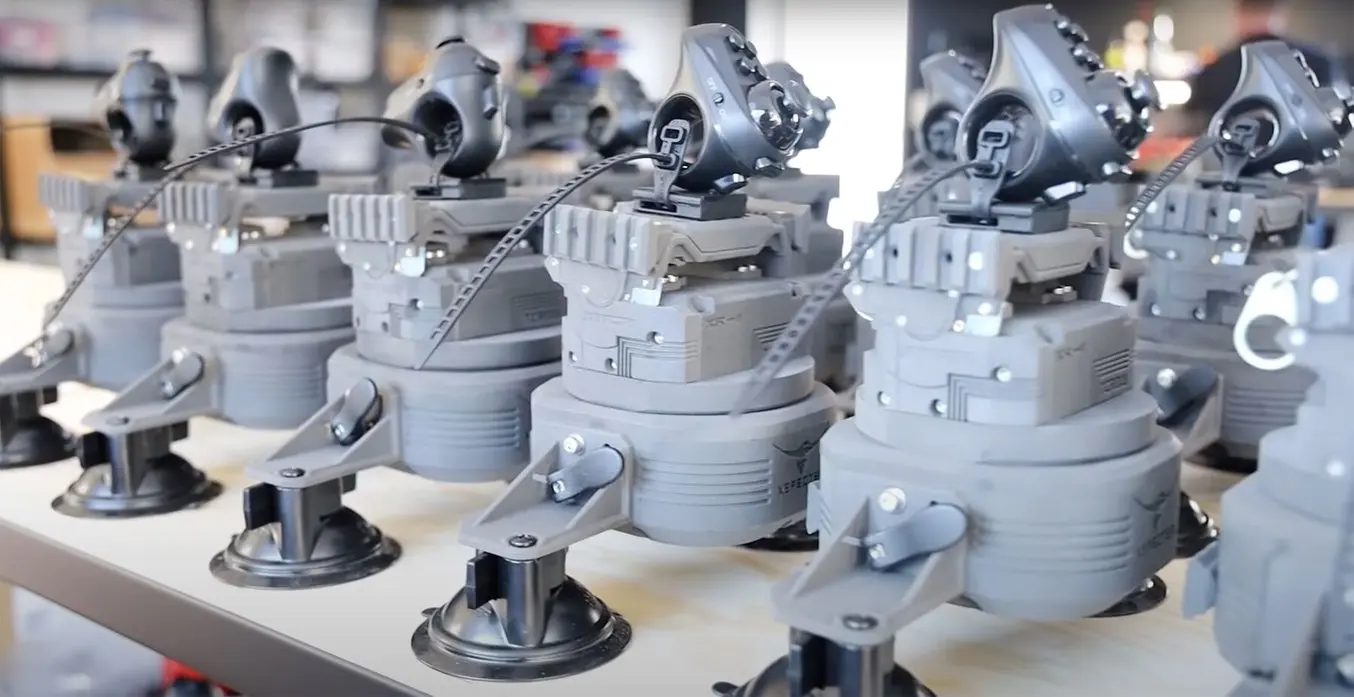
SLS for End-Use Production
3D printing for end-use production is not only possible, it's more affordable, agile, and scalable than ever with the Fuse SLS Ecosystem. Visit our SLS for Production page to compare production methods, learn about bulk powder pricing, and see production in action for 15 different manufacturers currently using the Fuse Series.