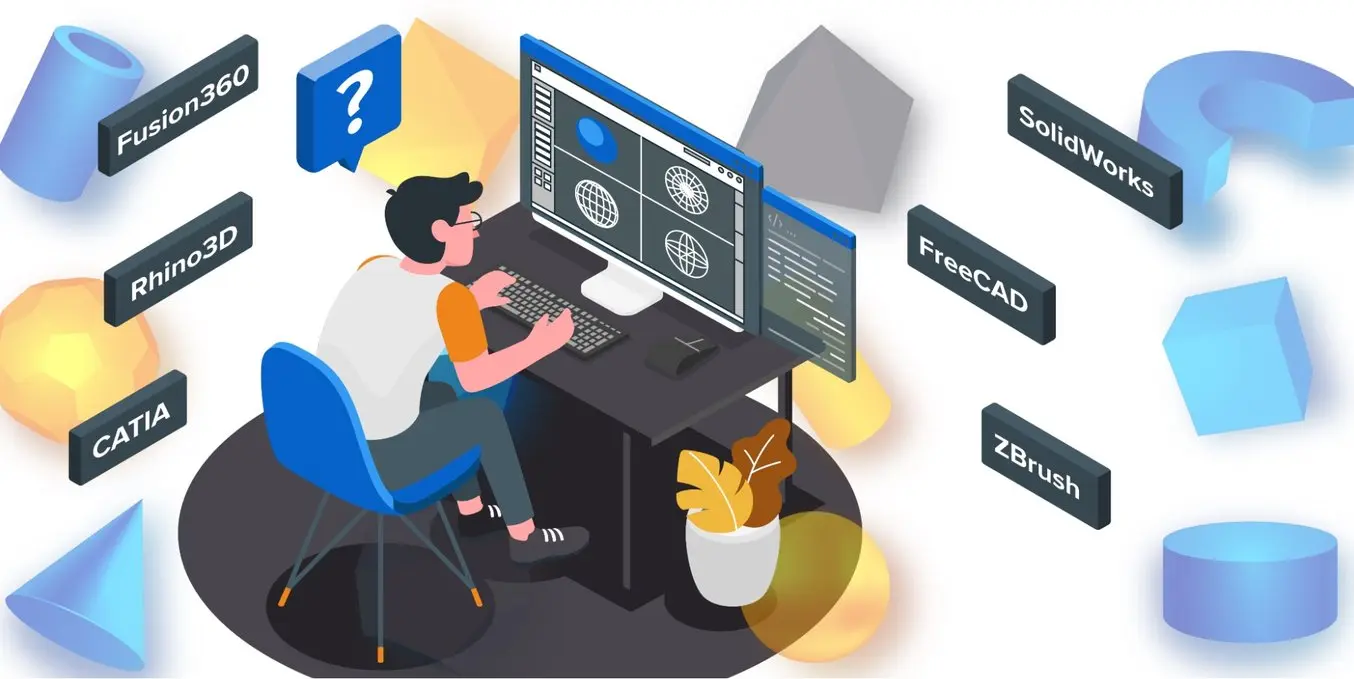
CAD (computer-aided design) is the tool that brings a design to a manufacture-ready state. It is the all-important software environment where designers and engineers translate concept sketches into three-dimensional models which are then visualized, optimized, simulated, and can be directly 3D printed or produced with traditional manufacturing tools.
Over the span of several decades, a core base of CAD programs has branched out to now include dozens of viable alternatives, each with its own pros and cons, modeling approaches, and niche uses. Let’s take a look at the offerings so that you can make the right choice in selecting a virtual work environment that might stay with you for an entire career.
What is CAD Software?
Computer-aided design (CAD) is a method to digitally create 2D drawings and 3D models that has replaced manual drafting across a wide range of industries. CAD software tools empower designers to explore design ideas, modify designs easily, visualize concepts through renderings, simulate how a design performs in the real world, draft documentation, share designs for feedback, and more—facilitating innovation and allowing companies to get to market faster.
CAD software has been around since 1959, when Doug Ross, a researcher at MIT, coined the term ‘computer-aided design’ after developing a program that allowed his team to draw electronic circuit drawings on a computer, thereby realizing its potential for rapid modification and exploration.
By the early 1980s, CAD had become integrated into the workflow of the automotive, aviation, and consumer electronics manufacturers that could afford it. In the 1990s, solid modeling engines were enhanced with boundary representation, a more consistent way to describe virtual objects by their boundaries and interconnections. This was adopted by the now well-known systems SolidWorks (1995), SolidEdge (1996), and Autodesk Inventor (1999).
The 2000s marked an emergence of open-source CAD systems such as FreeCAD. In addition, new features and modules were developed for a variety of CAD programs that allowed designers to not only develop the physical product, but also render, animate, and simulate it, as well as integrate product development into the overarching processes of project management and product lifecycle management (PLM).
The most recent CAD software systems are cloud-based, enabling developers to collaborate on the same model through different workstations and delegate intensive algorithms such as generative design, simulation, and rendering to the cloud. Advanced simulations allow testing of a design according to numerous mechanical aspects and take only hours instead of days. Generative design makes the computer a co-creator using artificial intelligence to suggest optimal shapes to meet specific mechanical problems.
The benefits of CAD integration across the product development process are:
-
Rapid concept development: Envisioned designs can be accurately sketched for early visualization and 3D printed rapid prototypes.
-
Specialization: Spreading CAD throughout the organization develops specific knowledge which results in a common understanding of how to bring specific parts to the manufacturing-ready stage.
-
Visualization: Clients and target customers can be informed and impressed with cutting-edge 3D renderings, animations, and virtual reality experiences of works-in-progress.
-
Optimization: Faults and imperfections can be detected and optimized much faster in a virtual environment. Gaps between design intent and manufacturing reality are bridged using accurately toleranced mechanical drawings.
-
Rapid manufacturing: Products can be brought to production faster using CAM systems and rapid manufacturing technologies.
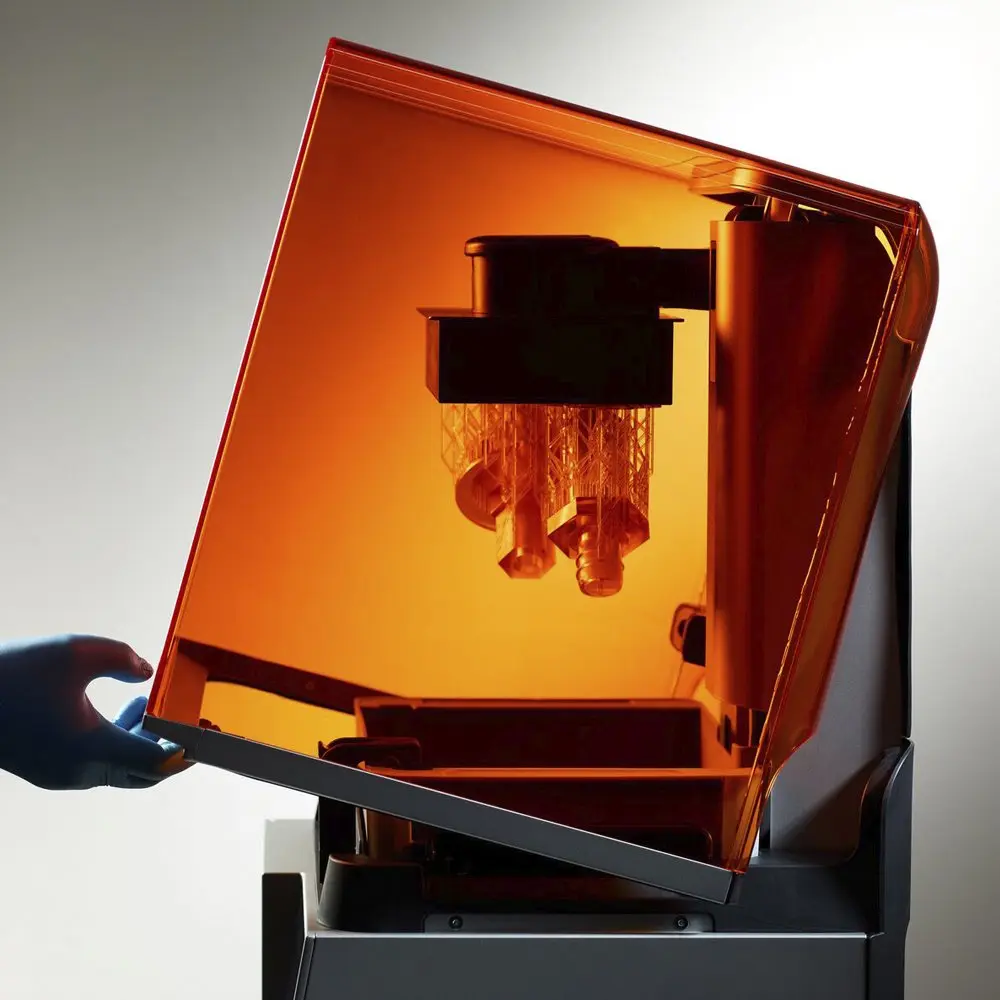
Introduction to 3D Printing With Desktop Stereolithography (SLA)
Looking for a 3D printer to realize your 3D models in high resolution? Download our white paper to learn how SLA printing works and why it's the most popular 3D printing process for creating models with incredible details.
Uses of CAD
Traditionally, CAD software systems lead to the generation of a set of mechanical drawings that inform the factory how to produce a product, along with the manufacturing technology, materials, mold finishes, and tolerances required. Nowadays though, they do much more:
-
Creating photorealistic renderings for internal presentations and marketing collateral
-
BOM (Bill of Materials) integration for managing all parts in an assembly as well as cost estimation.
-
Direct import of standard mechanical parts and/or ornamental elements from linked databases of various suppliers
-
Deriving an injection mold design from a part after setting up some basic parameters
-
Assisting the design and simulation of sheet metal components, welded frames, and composite parts
-
Stress and buckling analysis (FEA), drop test simulation, and generative design (GD)-generated suggestions for optimization
-
Mold flow analysis for injection molding
-
Thermal, vibration, and aerodynamics analysis
-
Motion analysis and interference detection for assemblies
-
Ergonomics analysis with posable 3D manikins
-
Surface flattening for die-cut drawings based on a 3D model
-
Nesting algorithms for optimizing the layout of parts on the 2D bed of a laser cutter or 3D printer
-
Automatic gemstone prong settings for jewelry design
-
Simulation of fabrics and inflatables
-
PLM systems to manage assemblies, part version history, releases, engineering changes, file formats, metadata, cost estimation, vendors and suppliers, collaborations, access control, revision control, manufacturing process planning, and related part files, documents, and presentations
-
Advanced Geometric Dimensioning and Tolerancing (GD&T) in order to convey design intent and optimize the manufacturing process.
-
Direct import of 3D scanning data for reverse engineering
-
Preparing models for 3D printing
-
Texture mapping and painting for use in art, video games, movies, and full-color 3D printing
Types of CAD Software Systems
In more purist professional circles, CAD typically refers to a parametric system that has a history tree and advanced capabilities to work with highly constrained and complex assemblies, as opposed to 3D software that is mostly meant to generate models for visualization or artistic purposes. In this article, we use CAD to refer to any program that can generate workable 3D models for manufacturing processes such as injection molding, thermoforming, or 3D printing. The amount of parametric control, in the end, is itself a parameter of the program which the designer can decide to go for.
The least dimensional control is given by freeform modelers or virtual clay sculptors, where the user draws shapes out of a base mesh object, modifying it freely without any numerical constraints. The most important examples are ZBrush and Mudbox.
In polygonal modeling also known as mesh, wireframe, or box modeling, the user also starts with a base mesh but instead of roughly sculpting out shapes, deforms it by means of operations on the mesh’s elements: its vertices, edges, and faces. In addition, there are modifiers/deformers that work on the entire shape, such as bending, twisting, smoothening, and morphing shapes. This provides the designer some numerical control although parts remain unrelated to all other parts of the model. Wings3D is a free option but box modelers such as 3D Studio Max, Maya, Blender, and Cinema4D also include advanced animation and rendering capabilities.
Solid modeling is the simplest way of doing 3D design towards manufacturable models. From the start, the virtual design is treated as a manufacturable solid object which the user then adds or removes material from using constructive solid geometry (CSG) techniques. Programs such as SolidWorks and SolidEdge allow creating sketches on various parts of the model that can then be extruded or revolved around an axis in order to create new features.
Surface modelers treat a virtual object as a set of surfaces, and only if these are fully connected on all sides the model can be called ‘watertight’ and subsequently converted into a solid body ready for production, for example, 3D printing. The creator starts by creating sketches that are subsequently swept over a rail, revolved around an axis, or lofted towards other sketches. Surfaces can then be blended and trimmed with each other in order to create a complex part design. Surfaces can be tangent, meaning that one flows directly into the other. This is called G1 continuity. However, when the change of tangency also remains consistent across a surface it can be called curvature continuous or G2. Advanced surface modeling capabilities in the G2 range are offered by programs like Alias, Creo, and Rhinoceros. When the change of curvature also has to remain smooth, for example in aerodynamics optimization, this is G3 and the designer enters the realm of Class-A surfacing for which only the most advanced software systems such as CATIA are suitable. When opting for a surface modeler, it is important to be aware of the engine behind it being based on NURBS, Bézier, T-Splines, or the outdated Coons-type definitions.
Parametric modelers give the designer full control over the modeling process, as opposed to direct modelers. Every feature can be created based on a set of dimensions and constraints that decide its size, shape, and location. These elements build on top of each other to create a historical model tree that reflects how the model was constructed. The designer here works more directly on the parameters driving the design rather than the geometry itself. This enriches the workflow in that it makes it possible to program, or script, parts of the design, opening up an enormous scope of new possibilities in textures, patterns, and variations for product customization. Parametric modelers make the most out of CAD, yet always evaluate if they hamper conceptual exploration. The step to parametric is made too early in the creative process all too often. CATIA, Creo, and OnShape all include advanced parametric modeling features. While Rhinoceros is a direct modeler, its plug-in Grasshopper is a prime example of how parametric control can be infused into the process. In OpenSCAD, all of the geometry is coded in a separate window rather than drawn directly into the virtual space. Antimony replaces textual scripting with a more intuitive node-based flow diagram akin to Grasshopper. Even SolidWorks allows some data-driven control using a spreadsheet document as input definition.
In generative design (GD), complex results are computer-generated beyond the scope of vision of a human designer only. The definition of a design can be changed by manually tweaking the input numbers and the model will update accordingly. It can also be partially or fully done by artificial intelligence which can augment the 3D-modeling process with recursion and evolution towards optimal shapes as seen in topology optimization.
Most current-day CAD systems are hybrids in that they contain aspects and tools from multiple types of CAD modeling approaches, according to the demands of a specific industry or product type. SolidWorks and Cobalt are best with solids but offer amazing surfacing capabilities as well. CATIA, Siemens NX, and Creo have both advanced solid and surface modeling capacities as well as options for freeform modeling while being fully parametric. Blender offers both polygonal modeling and sculpting in a single environment. SelfCAD and Fusion360 combine mesh modeling with solid modeling. Even ZBrush is a hybrid system in that next to a lump of virtual clay to work on, it offers excellent polygonal modeling tools as well.
With respect to hardware, a powerful CPU, GPU, and expanded RAM memory are must-haves, especially for parametric CAD software, and non-cloud-based systems. Investing in a controller or mouse dedicated to 3D design is of substantial benefit.
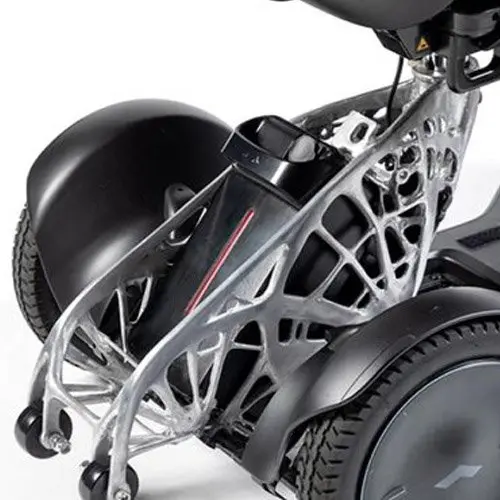
An Introduction to Generative Design for Producing Lightweight Parts With 3D Printing
In this webinar, Formlabs Product Marketing Lead Jennifer Milne will provide a simple overview explaining what generative design is, framed in a way that is applicable to mechanical part design, including a step-by-step tutorial of Fusion 360 where she’ll produce a lightweight bracket.
CAD Software Solutions by Industry
CAD software started out as an elite commodity, available only to the largest companies in aerospace and automotive, but has become widespread among even the smallest companies over the past few decades. Here is an overview of various industries and their virtual studios of choice:
Industry | Software |
---|---|
Automotive | CATIA, Siemens NX, Alias, Creo, Rhinoceros |
Architecture | AutoCAD, Revit, ArchiCAD, Microstation, SketchUp, Rhinoceros+Grasshopper |
Dental | 3Shape, exocad, CEREC, OrthoCAD, PlanCAD, Ceramill Mind, Zirkonzahn, Maestro3D, RealGUIDE |
Engineering & Product Design | SolidWorks, Onshape, Creo, Siemens NX |
Furniture | Cobalt, SolidWorks, Rhinoceros |
Fashion | Marvelous Designer, CLO |
Footwear | Modo, ICad3D+, MindCAD, Geomagic Freeform, Blender, Rhinoceros |
Interior Design | Homestyler, HomeByMe, Virtual Architect, FloorPlanner, RoomStyler |
Jewelry | 3Design, ZBrush + GemCut Pro, Rhinoceros (+ Grasshopper, Matrix, 2Shapes, Weaverbird, Peacock, and Lunchbox plug-ins) |
Manufacturing | Inventor, SolidEdge, SolidWorks |
Makerspace / 3D Printing | ZBrush, Mudbox, Fusion360, MeshMixer, Rhinoceros + Grasshopper |
Medical | SolidWorks, Inventor, Siemens NX, Spaceclaim, Rodin4D Neo, Adept, Within Medical |
Model Making & Entertainment | Maya, 3D Studio Max, Houdini, Modo, Cinema4D, Blender, Daz3D |
Landscaping | Vectorworks Landmark, LandFX, Rhinoceros + Lands Design, SketchUp |
Research & Education | SelfCAD, TinkerCAD, 3DBuilder, SketchUp, BlocksCAD |
Virtual Reality | Maya LT, 3D Studio Max, Creo, SketchUp |

How to Choose a 3D Printing Technology
Having trouble finding the best 3D printing technology for your needs? In this video guide, we compare FDM, SLA, and SLS technologies across popular buying considerations.
How to Choose a CAD Environment
It can be tempting to select a piece of CAD software based on features that have a certain appeal or novelty value. However, it is paramount to evaluate whether those features are indeed game-changers, radical innovations, or only incremental improvements of marginal value.
Being able to meet the required complexity of your product is of vital importance for the virtual workspace you choose. Will your product involve advanced surfacing such as curvature blends, surface flattening for soft goods, or patterning features such as graded transitions? Will it need advanced features for wall thickening, parametric control over all dimensions, or advanced assembly design for 100+ parts?
In adding CAD tools to the development pipeline, do not underestimate file format compatibility. In case of a mismatch, it can take a while to make sure nothing is lost between formats.
Second, examine the complexity required for the entire work process further down the line beyond part design. Will the program be used only for technical conversions of concept drawings done on paper, or also for creative explorations itself? Will mechanical analyses be required towards production? Will the company produce several releases of the same product, or similar products in the same family that share the same parts? Will parts require radical revisions that require control of the entire history tree? Is there an opportunity for cloud storage or network rendering, or will everything rely on local servers and workstations? How often will you need to 3D print prototypes or end-use parts?
It is best to evaluate a trial version of the software for several weeks before making a purchasing decision. This allows you to check how heavy the software gets on the computer’s CPU and GPU, if it is robust enough or still contains bugs, even leading to crashes, as well as how file management will work.
Then, check if the software is a standard part of the local educational curriculum. If the design or engineering team in the company is most likely unfamiliar with the software, consider if the user interface is intuitive enough for them to go through a short learning curve and rapidly be able to step in on projects. Is the GUI customizable for meeting the needs of beginners as well as expert users and providing instant shortcuts to the most used commands?
And lastly, since advanced CAD systems are increasingly expensive, it is in some cases worth considering some free or affordable alternatives. DesignSpark is a free alternative to AutoCAD. Instead of ZBrush, there is the free ZBrushCoreMini and Sculptris. Blender is entirely free and produces results on par with Maya and 3D Studio Max, and if that is too complicated, Wings3D is an easy-to-learn and equally free polygonal modeler. SolidEdge is a simplified derivative of NX, while SolidWorks, although less advanced and comprehensive, works just as well as CATIA in many cases. FreeCAD is free of charge, open-source, and a great start for those wanting to dive into feature-based modeling.
Here is how our selection of 3D CAD software programs scores on the most important criteria:
Sculp | Polygon | Solid | Surface | Parametric | Features | Scalability | UX | Price | |
---|---|---|---|---|---|---|---|---|---|
3DBuilder | ★☆☆☆☆ | ☆☆☆☆☆ | ☆☆☆☆☆ | ☆☆☆☆☆ | ☆☆☆☆☆ | ★☆☆☆☆ | ☆☆☆☆☆ | ★★★☆☆ | ★★★★★ |
Blender | ★★★★☆ | ★★★★★ | ★★☆☆☆ | ☆☆☆☆☆ | ★★☆☆☆ | ★★★★☆ | ★☆☆☆☆ | ★☆☆☆☆ | ★★★★★ |
CATIA | ★★★☆☆ | ★★☆☆☆ | ★★★★★ | ★★★★★ | ★★★★★ | ★★★★★ | ★★★★★ | ★★☆☆☆ | ☆☆☆☆☆ |
Creo | ☆☆☆☆☆ | ★★★☆☆ | ★★★★★ | ★★★★☆ | ★★★★★ | ★★★★☆ | ★★★★★ | ★★★☆☆ | ★☆☆☆☆ |
FreeCAD | ☆☆☆☆☆ | ★☆☆☆☆ | ★★★★☆ | ★★☆☆☆ | ★★☆☆☆ | ★★★☆☆ | ★★★☆☆ | ★☆☆☆☆ | ★★★★★ |
Fusion 360 | ☆☆☆☆☆ | ★☆☆☆☆ | ★★★★☆ | ★★☆☆☆ | ★★★☆☆ | ★★★☆☆ | ★★★☆☆ | ★★★★☆ | ★★★★★ |
MeshMixer | ★★★☆☆ | ★★☆☆☆ | ★☆☆☆☆ | ☆☆☆☆☆ | ☆☆☆☆☆ | ★★☆☆☆ | ☆☆☆☆☆ | ★★★★☆ | ★★★★★ |
NX | ★★★★☆ | ★★☆☆☆ | ★★★★☆ | ★★★★★ | ★★★★☆ | ★★★★☆ | ★★★★★ | ★★★★☆ | ★☆☆☆☆ |
Onshape | ☆☆☆☆☆ | ☆☆☆☆☆ | ★★★★☆ | ★★★☆☆ | ★★★★★ | ★★★☆☆ | ★★★★★ | ★★★☆☆ | ★☆☆☆☆ |
Rhinoceros | ☆☆☆☆☆ | ★☆☆☆☆ | ★★☆☆☆ | ★★★★★ | ★★★☆☆ | ★★★★★ | ★★★☆☆ | ★☆☆☆☆ | ★★★☆☆ |
SelfCAD | ★★★☆☆ | ★★☆☆☆ | ★★★☆☆ | ★☆☆☆☆ | ★☆☆☆☆ | ★★☆☆☆ | ★☆☆☆☆ | ★★★☆☆ | ★★★★☆ |
SketchUp | ☆☆☆☆☆ | ★★★☆☆ | ★★★☆☆ | ★☆☆☆☆ | ★☆☆☆☆ | ★★☆☆☆ | ★☆☆☆☆ | ★★★☆☆ | ★★★★☆ |
SolidWorks | ☆☆☆☆☆ | ☆☆☆☆☆ | ★★★★★ | ★★★☆☆ | ★★★☆☆ | ★★★★☆ | ★★★★★ | ★★★★☆ | ★☆☆☆☆ |
TinkerCAD | ☆☆☆☆☆ | ☆☆☆☆☆ | ★☆☆☆☆ | ☆☆☆☆☆ | ☆☆☆☆☆ | ★☆☆☆☆ | ☆☆☆☆☆ | ★★★★☆ | ★★★★★ |
ZBrush | ★★★★★ | ★★★☆☆ | ★☆☆☆☆ | ☆☆☆☆☆ | ★☆☆☆☆ | ★★★☆☆ | ☆☆☆☆☆ | ★★★☆☆ | ★★☆☆☆ |
The first five scores pertain mostly to feature depth and robustness for each modeling style. Versatility is based on the number of different use cases and fields of application a program has. Scalability means the ability to handle different types of models from concept to manufacturing phase, to manage complex assemblies, and to set up entire product lines with interlinked parts and documents. UX combines the user-friendliness of the GUI and difficulty to learn.
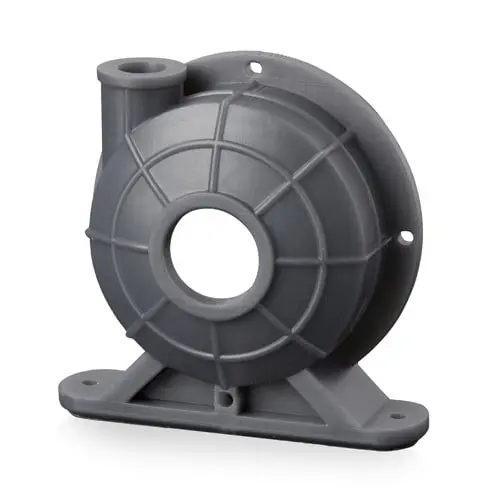
Request a Free 3D Printed Sample Part
See and feel Formlabs quality firsthand. We’ll ship a free 3D printed sample part to your office.
CAD Software Programs Compared
In this section, we are going to compare different CAD programs grouped by user type. This includes the best CAD software for beginners, students, professional designers and engineers, large enterprises, and for 3D printing.
Best CAD Software for Beginners
SelfCAD
Developer: CrossBrowser3D
Released: 2016
Platforms: All, in-browser
Ideal for: Education (middle/high school), 3D Printing
Price: $599 or a free simplified version
SelfCAD is a basic in-browser direct modeling environment for those wanting to get their feet wet in 3D. It offers multiple options for starting objects that the user can then modify, sculpt, or combine with other objects. SelfCAD allows some parametric control through sketching and extruding, revolving, or lofting these sketches. SVG images can be imported for custom extrusions. Details such as roundovers and chamfers can be added to individual edges in a fairly intuitive user interface with tutorial videos ready at hand.
The free version includes a basic set of modeling and sculpting tools, MyMiniFactory database integration, and a rendering engine for semi-professional visualizations. The paid version costs $140/year or $599 for a perpetual license and includes mesh modifiers, 3D sketching, file import/export, basic animation, ImageTo3D, and 3D printing support.
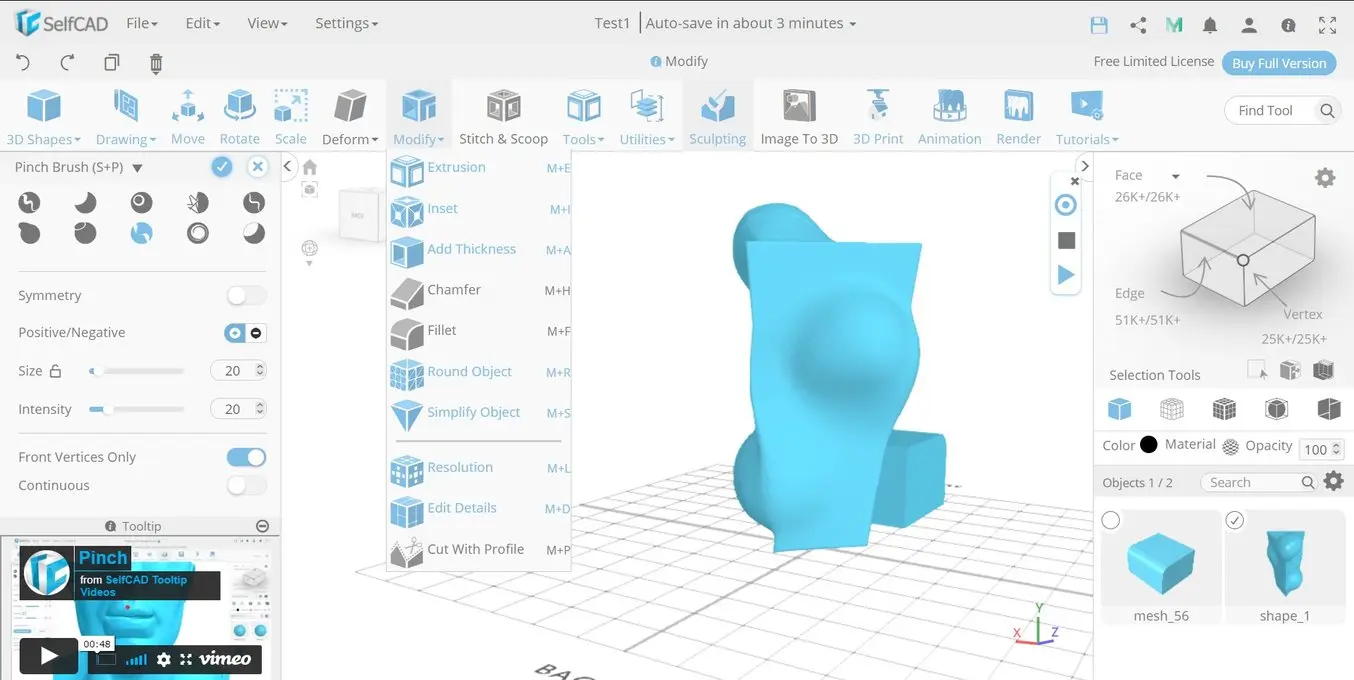
SelfCAD offers starter-level modeling commands in an attractive user interface with tooltips.
TinkerCAD
Developer: Autodesk
Released: 2011
Platforms: All WebGL-enabled browsers
Ideal for: Education (elementary/middle school), 3D Printing
Price: Free
The successor to Autodesk 123D, TinkerCAD is simple enough to teach even the youngest among us about 3D modeling. Start from a library of shapes and build upon them using standard primitives which can then be accurately rotated, moved, and rescaled before landing in their intended position. Granted, this virtual block-building approach results in simplistic shapes, but the upside is an easy-to-learn user interface that stimulates the creativity of young minds towards creating surprisingly refreshing results.
TinkerCAD works in-browser with cloud storage and is entirely free. Shape libraries include standard primitives, hinges and ball joints to make movable parts, as well as 3D printable fossils and pieces from the Smithsonian National Museum of Natural History.
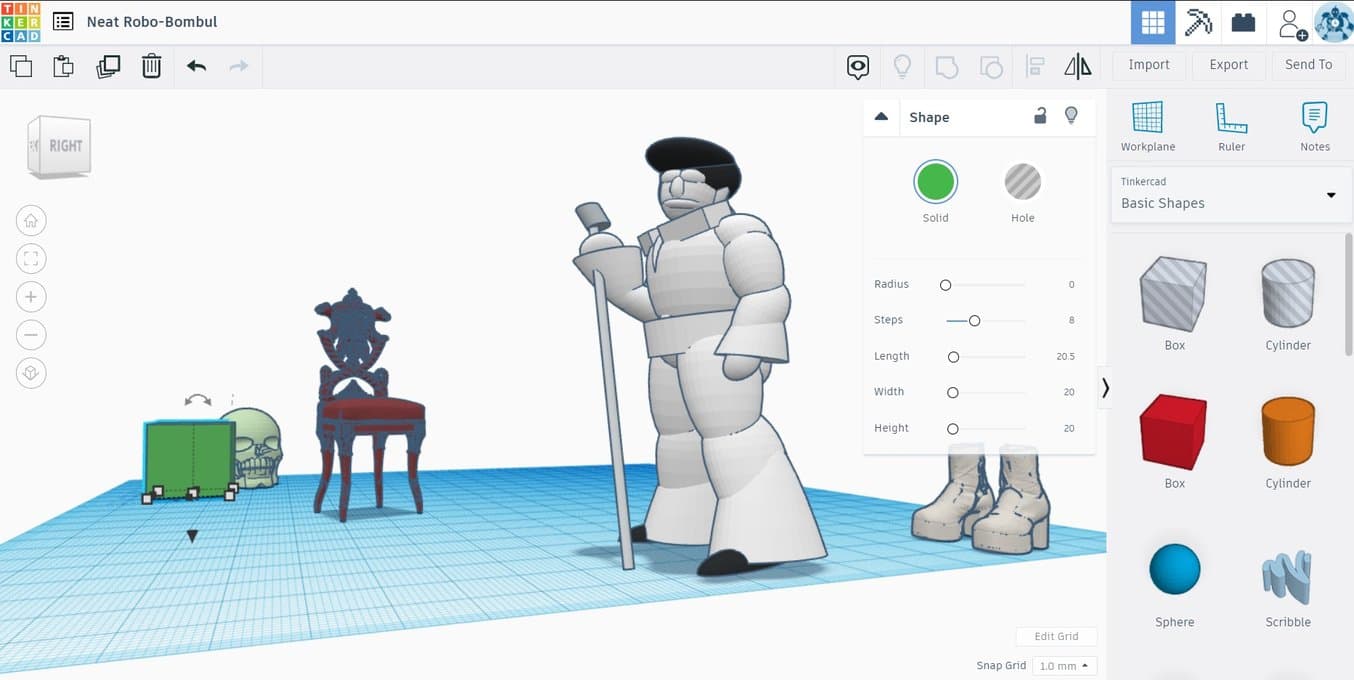
TinkerCAD offers a first taste of 3D modeling with simple building blocks and a fun object library to tap into.
Best CAD Software for Students and Professionals
Rhinoceros
Developer: Robert McNeel & Associates
Released: 1998
Platforms: Windows, macOS with limited features
Ideal for: Part Design, Freeform Surfacing, Footwear, 3D Printing, Data-Driven Design, Jewelry
Price: $995, $195 for students
Rhinoceros is the best introduction kit for anyone intending to dive into the world of professional 3D modeling. Its tutorials are high-level right from the start as is its user interface. This is unavoidable given the unlimited modeling features and toolsets the program offers. As the user’s expertise grows, so will his or her familiarity with hotkeys and textual input methods which drastically speed up the workflow. Another nice feature is that Rhino has layers. This allows the grouping of specific selection sets, visualizing them in different colors, which altogether improves the level of organization.
Rhino3D is a freeform NURBS-based surface modeler especially suited for creating complex artwork or graphics using complex surface blends, two-rail sweeps, and dummy surface transitions. It is also used in the professional areas of product design, jewelry, footwear, and automotive surfacing. What makes the software unique is the active online community and availability of third-party plugins which extend its use towards fields like architecture, 3D printing, and landscaping.
The most notable Rhino plugin is Grasshopper3D. In a separate window, it has its own node-based flowchart interface in which complex models and patterns can be crafted, even simulated, by scripting. These can be transferred to the Rhino viewport in a process called ‘baking’. Grasshopper itself knows dozens of plugins for almost unlimited functionality. There are Matrix and Peacock for jewelry design, Weaverbird for mesh smoothening, HoopSnake and Anemone for iterative feedback loops, Kangaroo for physics-based simulation, Lunchbox for panelization, Millipede for structural analysis and optimization, and Nudibranch for vector field mapping. Grasshopper models are hardly ever watertight and will need substantial rework in Rhino before being 3D printable.
Rhinoceros can be purchased by students for just under two hundred dollars, whereas regular users will pay nearly a thousand. Grasshopper3D and most important plugins are free to download.
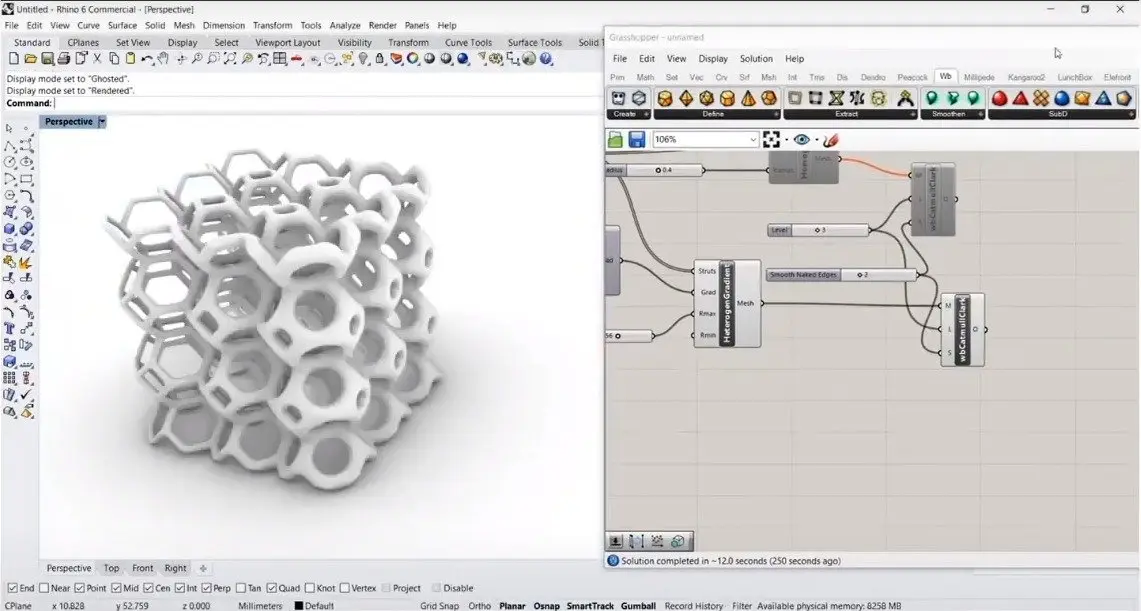
Grasshopper3D for Rhino is at the cutting edge of complex geometry generation.
Fusion 360
Developer: Autodesk
Released: 2013
Platforms: Windows (x64), macOS
Ideal for: Product/Part Design, Makerspaces, 3D Printing
Price: $495/year, free for students and startups
Fusion 360 is Autodesk’s cloud-based CAD solution that is entirely free for students and startups. Models can be parametrically defined and the program includes a simplified version of a history tree that can be disabled for direct modeling approaches. The modern user interface incorporates seven workspaces. In the Design workbench, parts are created using basic operators for solid and surface geometry. There are inspection and assembly design tools as with other software, even if the toolkit is somewhat reduced to the essentials. It is also possible to import standard components from the inventory of various suppliers such as McMaster-Carr, 3M, ABB, Bosch, Essentra, Fabory, Farnell, Lego, NXP, Mitsubishi, Panasonic, Philips, Siemens, and hundreds of others.
Parts can be tested on mechanical stress, vibrations, thermal properties, buckling loads, and impact events in the Simulation workbench. This also includes Shape Optimization where designers can employ the power of artificial intelligence for optimal shape finding given specific load cases. The output is a complex part that can be converted into a B-rep and further developed with polygonal modeling tools.
The Generative Design workbench is part of a paid subscription and akin to Shape Optimization. It allows for the incorporation not just of mechanical load cases, but of several different input parameters and the creation of several output variants targeted to specific materials and manufacturing techniques. Three additional workbenches are present for basic animations, renderings, and production drawings. The key advantage of being a cloud-based CAD platform is that resource-intensive operations happen on the network, independent of the local workstation’s processing power.
As you can read in our tutorial, Fusion 360 is very well suited for creating 3D printable parts and offers direct integration with Formlabs 3D printers.
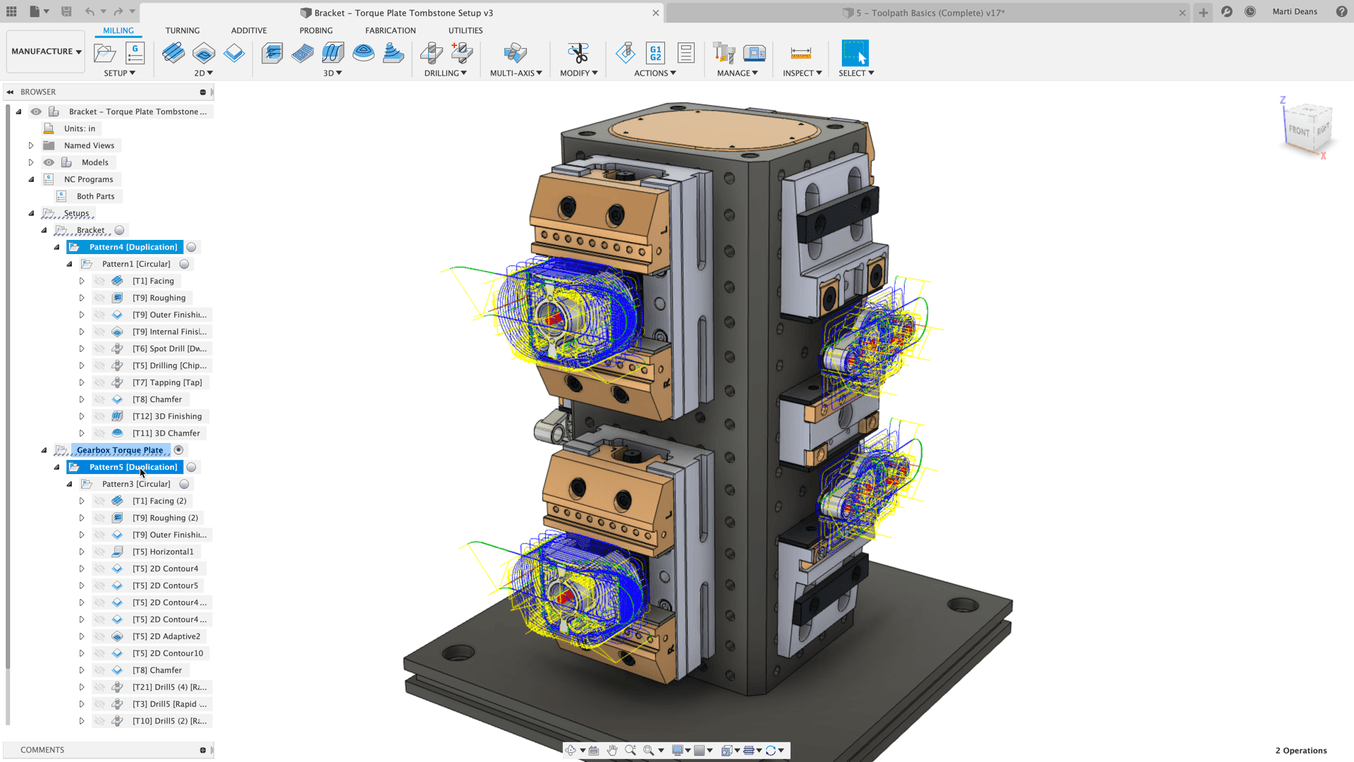
Fusion 360 has an intuitive user interface and all the basics needed for the beginning 3D designer.
SolidWorks
Developer: Dassault Systèmes
Released: 1995
Platforms: Windows
Ideal for: Product Design & Engineering, University-level Education, Furniture, Medical
Price: $3,995+$1,295/year, $99/year for students
SolidWorks is the most widely used professional 3D CAD software worldwide. It is also notorious for being the antithesis of direct modeling. Nothing can be dragged, sculpted, or directly manipulated in any other way. With constraint-based modeling, all features are saved in a history tree along with their parameters. Right from the first sketch, the designer needs to input numbers to lock the sketch into its intended position, as well as its relationships to other elements of the design. The same goes for assemblies. Parts are tightly interconnected to other parts, and subassemblies to other assemblies. Where part constraints define product geometry and manufacturing intent, mating constraints determine how parts can move in an assembly.
The main advantage of this style of modeling is that in case of updates and revisions, the model will dynamically update as the design requirements change. Once this is mastered, it will become increasingly intuitive. This powerful way of modeling requires careful planning and a rigorously procedural working method as opposed to more exploratory approaches. One of the software’s downsides is that errors will happen in the feature tree when parts are not properly constrained or surfaces consist of multiple complex input curves. This can happen even on reloading the same part, causing the history tree to light up with red warnings as if it was a Christmas tree. In worst-case scenarios, error handling can take days for hefty assemblies.
SolidWorks offers both powerful solid modeling as well as surfacing tools, such as lofts, single-rail sweeps, boundary surfaces, fills, curvature fillets, shelling, and surface flattening. Besides part design modules, SolidWorks offers advanced assembly design, sheet metal design, mechanical simulation, mold flow analysis, 3D scan data import, and photorealistic rendering. Despite criticisms of not being able to modify mesh files for 3D printing, it does a good job in exporting STL files from solid or surface models, even if these need some post-optimization. For more information on its capabilities, read our SolidWorks tutorial for 3D printing.
Whereas the professional version of SolidWorks requires an upfront investment of several thousands of dollars and a yearly fee of well over one thousand dollars, for students the entire software package costs only a hundred dollars a year and is often available for free through educational institutions.
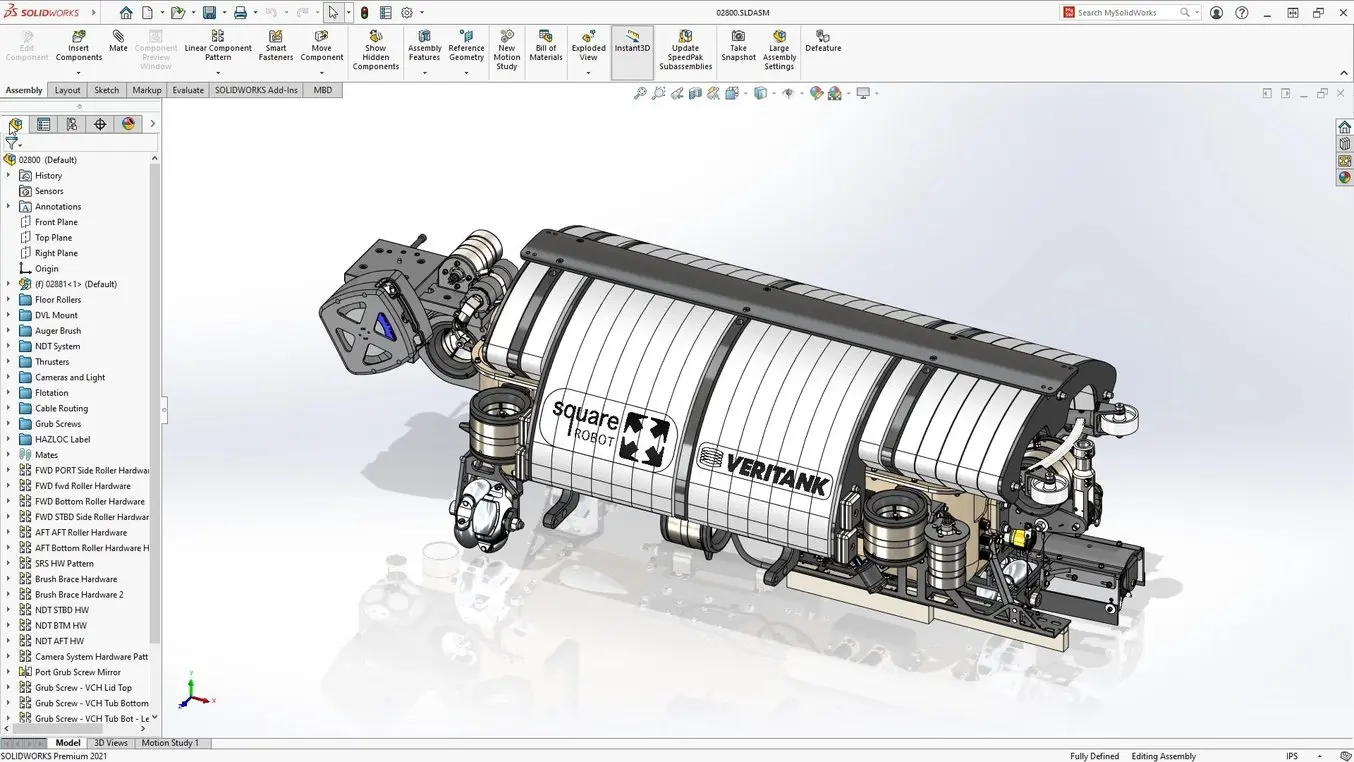
SolidWorks offers enough tools for complex modeling while rigidly defining parts and assemblies towards the engineering and manufacturing stage.
OnShape
Developer: PTC
Released: 2012
Platforms: iOS, Android, Linux, macOS, Windows
Ideal for: Product and part design
Price: $1,500/year, free for students and teachers
Being cloud-based and originated by the co-founder of SolidWorks, Onshape aspires to become one of the game-changers in the world of 21st century CAD. It does not have the advanced surface modeling features of SolidWorks, Rhino, or Creo yet, but new features are being added with continuous updates. What Onshape does offer is a synchronous collaboration from multiple workstations including smartphones and browsers on Macs, task automation with FeatureScript, sheet metal tools, content libraries, a mold design wizard, analytics, version control, and the possibility to save selection sets.
Other than that, it is comparable to SolidWorks in being a constraint-based parametric modeler. Changing a feature consequently changes all related features downstream, even up to the production drawings. It excels in the way it organizes (potentially table-driven) inter-part relationships, which enables optimized multi-part design and sets a higher bar for how parametric design should be experienced.
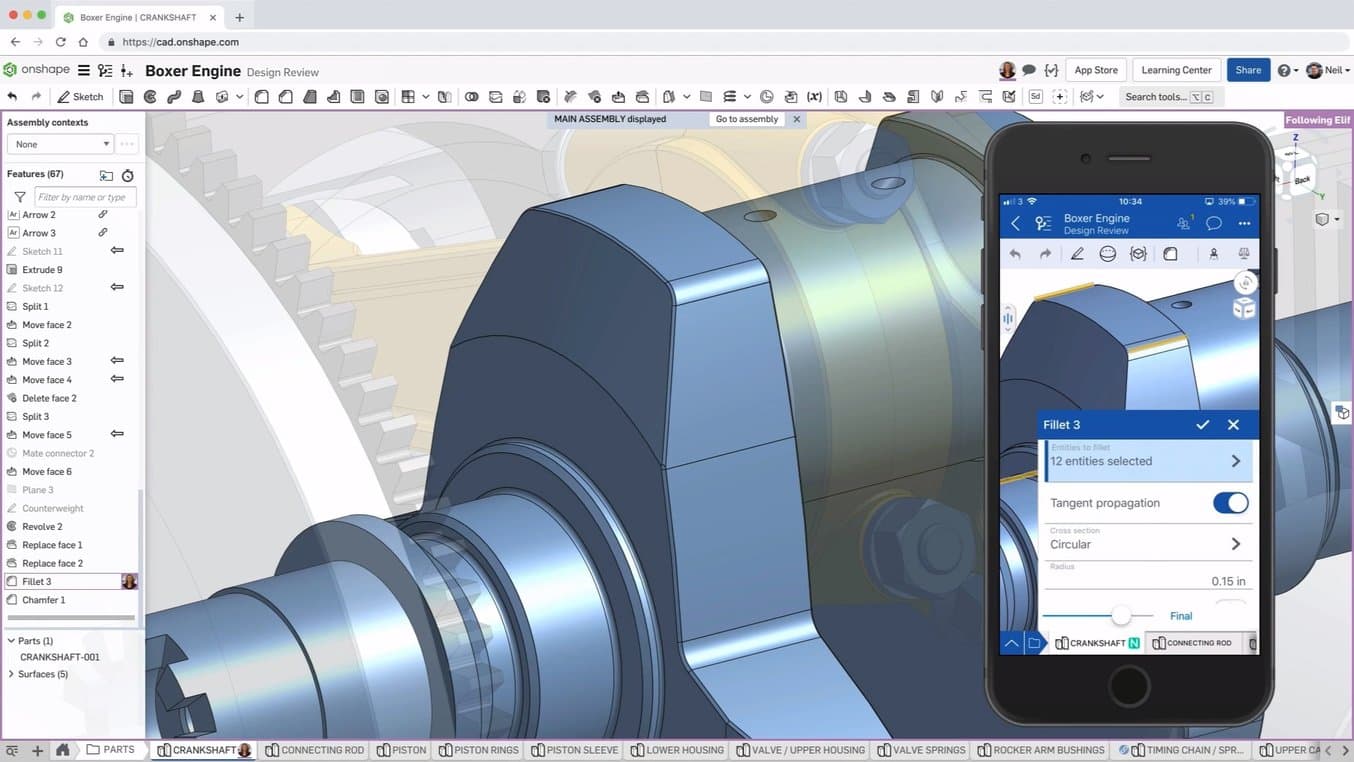
OnShape works simultaneously on multiple devices and is flawless in its parametric design capabilities.
ZBrush
Developer: Pixologic
Released: 1999
Platforms: Windows, macOS
Ideal for: Art, Game Design, 3D Printing, Jewelry
Price: free, US$895 or US$360/year
To make the intricate geometries 3D printing is renowned for, designers either turn to generative solutions like Grasshopper3D or sculpting environments. In the latter category, ZBrush remains the reigning champion. Its comprehensive set of tools ensures an enjoyable and efficient crafting process. If the designer wants to create a limb, there is a dedicated brush to pull one out of a body. Alternatively, he or she can add a ready-made one from the inbuilt libraries. Mesh topologies can be perfected towards just the right level of detail (LOD) for each specific area. Creasing and pinching tools can be attuned to gain just the right effect which is crucial in complex sculpts such as photorealistic portraits. Custom brushes can be created for rapid three-dimensional texturizing. Randomized scattering of objects and textures can be done with nanomesh.
ZBrush to some extent works with solids in that geometric primitives can be parametrically set up, for example, for different bracelet sizings. These are converted into sculptable meshes using the PolyMesh3D tool. With ZModeler, an essential subset of mesh editing tools, edges can be individually highlighted for making roundovers, bevels, selective creasing, or smoothening. The user can start with a wireframe skeleton and add clay to it, just like a real sculpt. Zspheres are another way of creating a base body instead of having to sculpt the proportions manually. Multiple bodies can be generated and sculpted in the same space, enabling the creation of environments rather than individual objects. Rulers and numerical input fields ensure accuracy where needed. Gem Cut Studio makes it possible to import gemstones and prong settings. Lastly, there is a direct bridge to Keyshot for instant photorealistic rendering. These flagship features set ZBrush apart from other sculpting engines and makes it suitable for a variety of industries. For an impression of ZBrush’s sculpting possibilities for hyperrealism, check out our story with Modern Life Workshop.
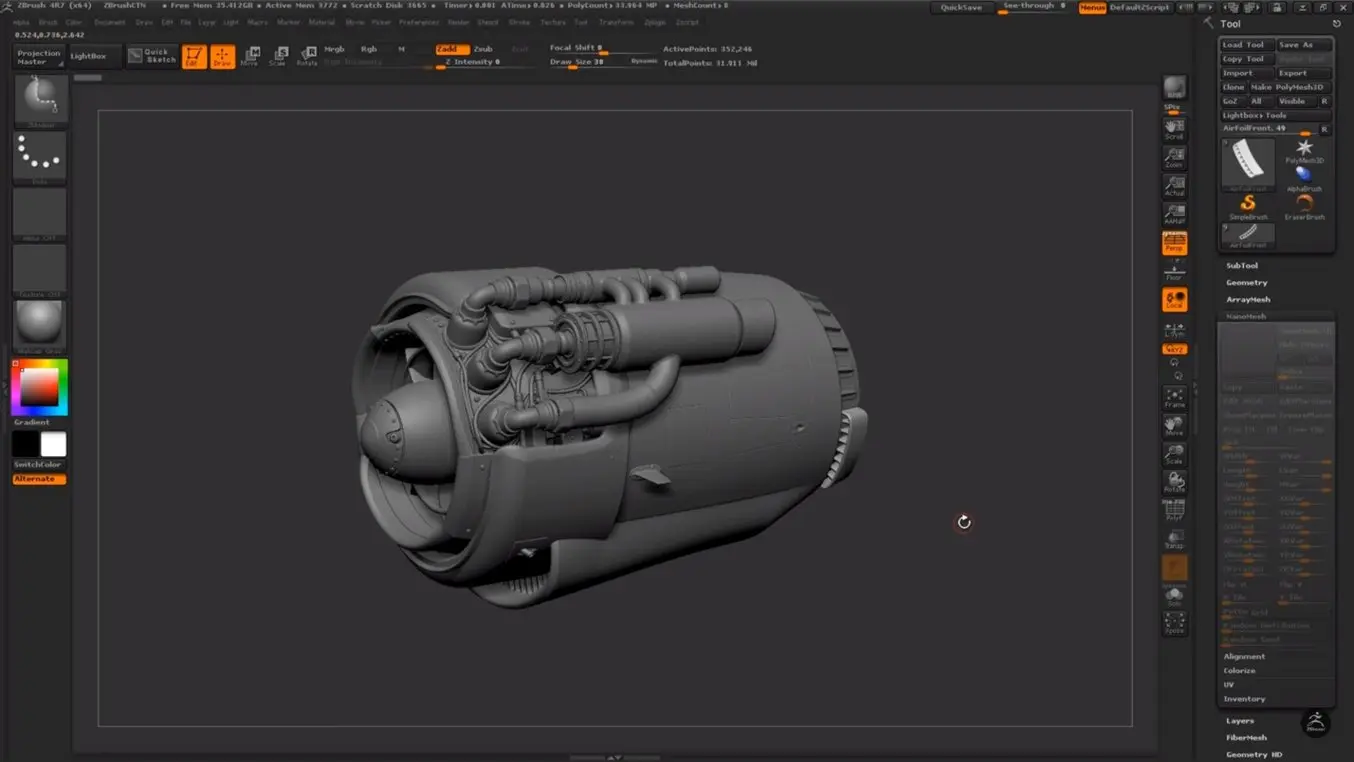
ZBrush, a winning interface between mesh modeling and freeform sculpting.
Best CAD Software for Large Enterprises
CATIA
Developer: Dassault Systèmes
Released: 1982
Platforms: Windows, Unix
Ideal for: Automotive, Aerospace, Product Design, Engineering, Assembly Design
Price: approx. $12,000 + $2,000/year
CATIA is an acronym for Computer-Aided Three-Dimensional Interactive Application and at the same time the most advanced modeling system on the planet. CATIA is not just CAD but a fully-fledged digital infrastructure towards manufacturing of the most complex products such as cars at Ford, Honda, Tesla, and Renault, and aircraft at Airbus and Boeing.
It includes the same high-level control offered by history-based modeling as known from other parametric modelers, together with advanced integration for CAM and CAE. In addition, it has top-notch surfacing features in its Generative Shape Design and FreeStyle modules, while the Shape Sculptor allows freeform sculpting in virtual clay. Furthermore, there are modules for sheet metal design, composite parts, tooling, assembly design, drafting, rendering, part repair, weldments, tolerancing, reverse engineering from scan data, aerodynamics design, structural analysis, ergonomics evaluation, virtual reality with 3DExperience to explore styling variants, CNC machining, generative design, lattice designer for additive manufacturing, and file preparation for 3D printing. A drawback of CATIA is that it, being driven by a decades-old backbone, can result in longer waiting times for large assemblies.
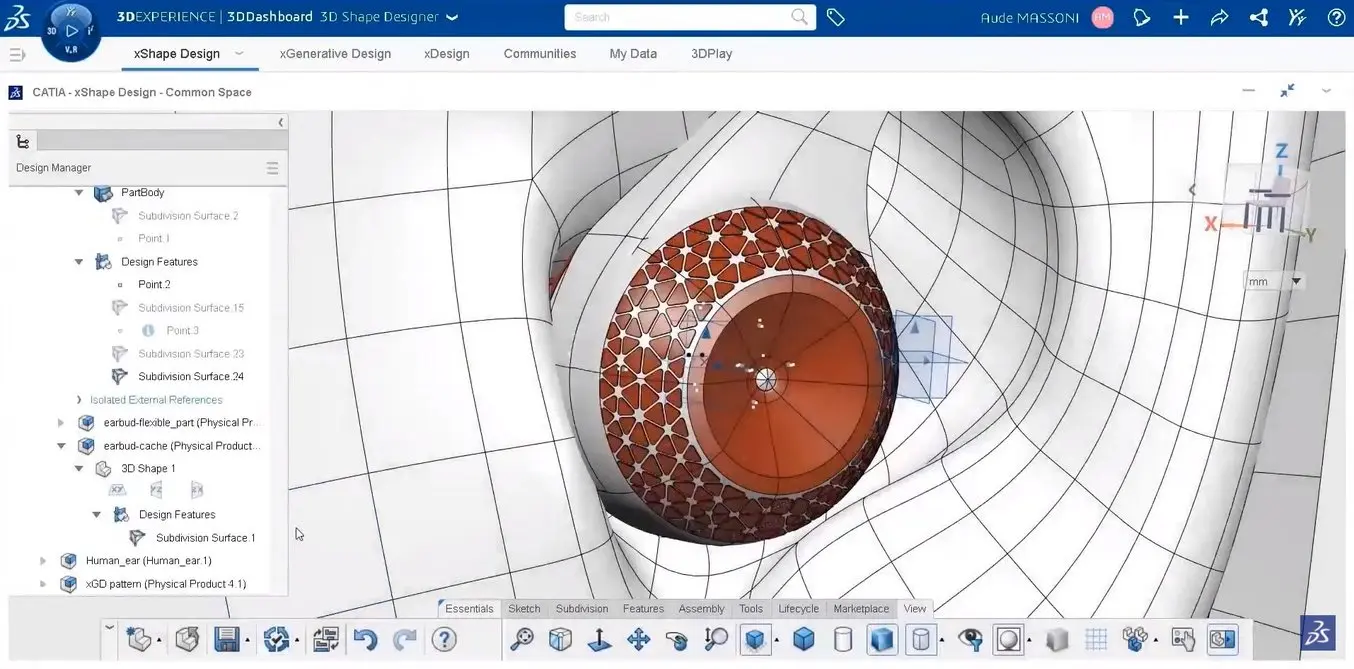
The latest release of CATIA organizes modules in separate tabs with a more user-friendly interface. It even includes Grasshopper-like generative design possibilities.
Creo
Developer: PTC
Released: 1982
Platforms: Windows, Unix
Ideal for: Product Design & Engineering, Automotive, Virtual Reality
Price: $2,310
Formerly known as Pro/Engineer, Creo is a fully parametric modeling package. It is suitable for working for assemblies of over 1,000 parts and as such is used by corporations like Aston Martin, John Deere, Volkswagen, Toyota, and Amazon. It combines solid, surfacing, and polygonal modeling approaches plus an advanced generative design module for shape optimization. Surfacing tools such as blends and sweeps are somewhat more reliable than in some other competing software packages.
Engineers will benefit from investing in Creo’s Advanced Plus package which includes advanced surfacing, a 3D printing slicer, GD&T, mold design, and simulation. When combining Creo with PTC’s PLM solution Windchill, it offers the user high-level management of assemblies, part lists and vendors, access and revision control, and much more.
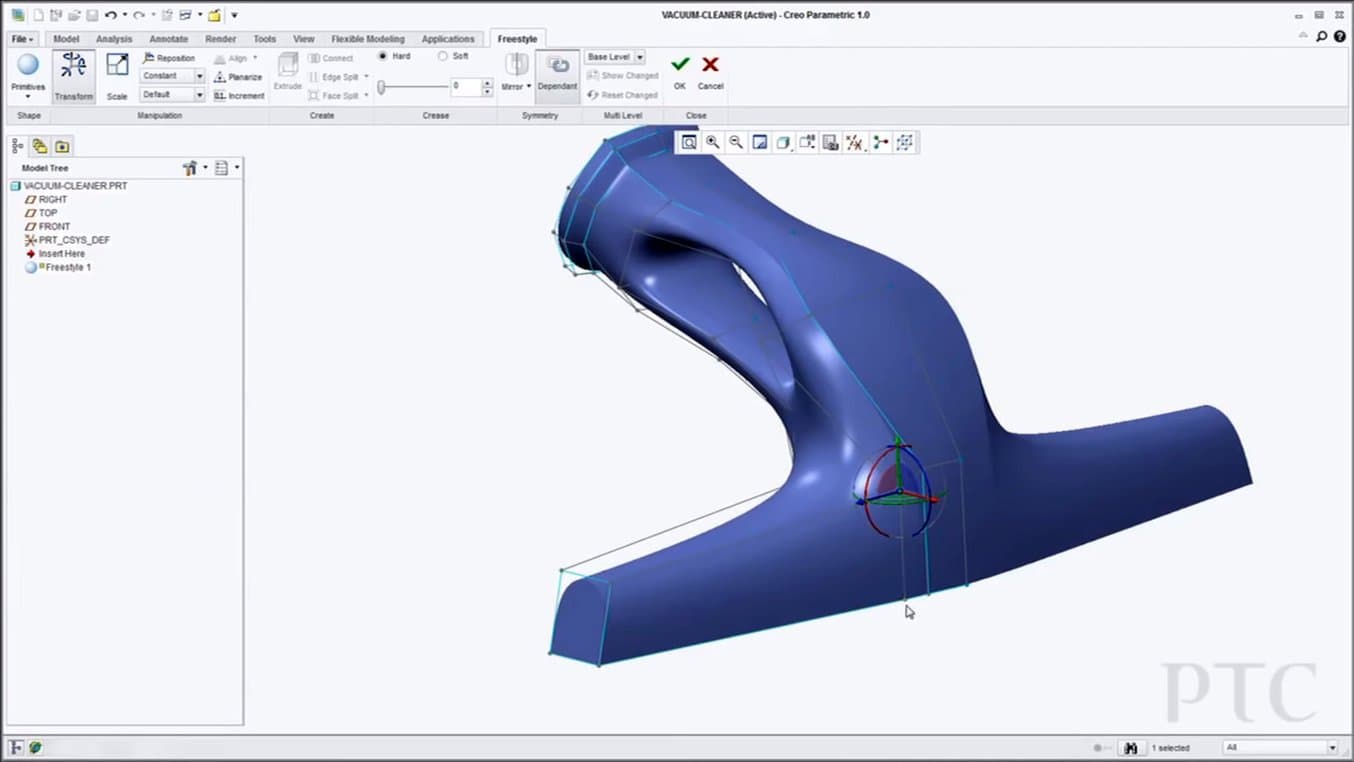
Creo reminds of SolidWorks yet is slightly more powerful in terms of surfacing capabilities such as the FreeStyle module.
NX
Developer: Siemens
Released: 1973
Platforms: Windows (x64)
Ideal for: Product Design & Engineering, Medical, Automotive, PLM
Price: $5,900 + $1,600/year
Until Siemens took over in 2007, NX was known as Unigraphics. Like its fellow contenders in the race for the best CAD package, NX offers advanced part design, assembling, and drafting functionalities as well as high-level solutions towards PLM, CAM, and CAE. This is why large companies like Apple, Tata, Mazda, Nissan, Daimler Mercedes, and SpaceX have adopted it, some even abandoning powerful systems such as CATIA for the migration to NX. Needless to say, it is a state-of-the-art system.
What sets it apart is its hybrid modeling approach with freeform mesh, solid, and Class-A surfacing methods part of the toolkit that approach the quality of CATIA. Without letting go completely of constraint-based modeling, NX’s so-called Synchronous Technology allows users to push and pull on certain features of the model for intelligent direct editing. Siemens NX is especially user-friendly and even has an adaptive UI that predicts commands that will be used most frequently in future projects. A disadvantage is that the old Unigraphics codebase still lingers on behind the scenes, causing some aspects of the program to run more slowly than expected.
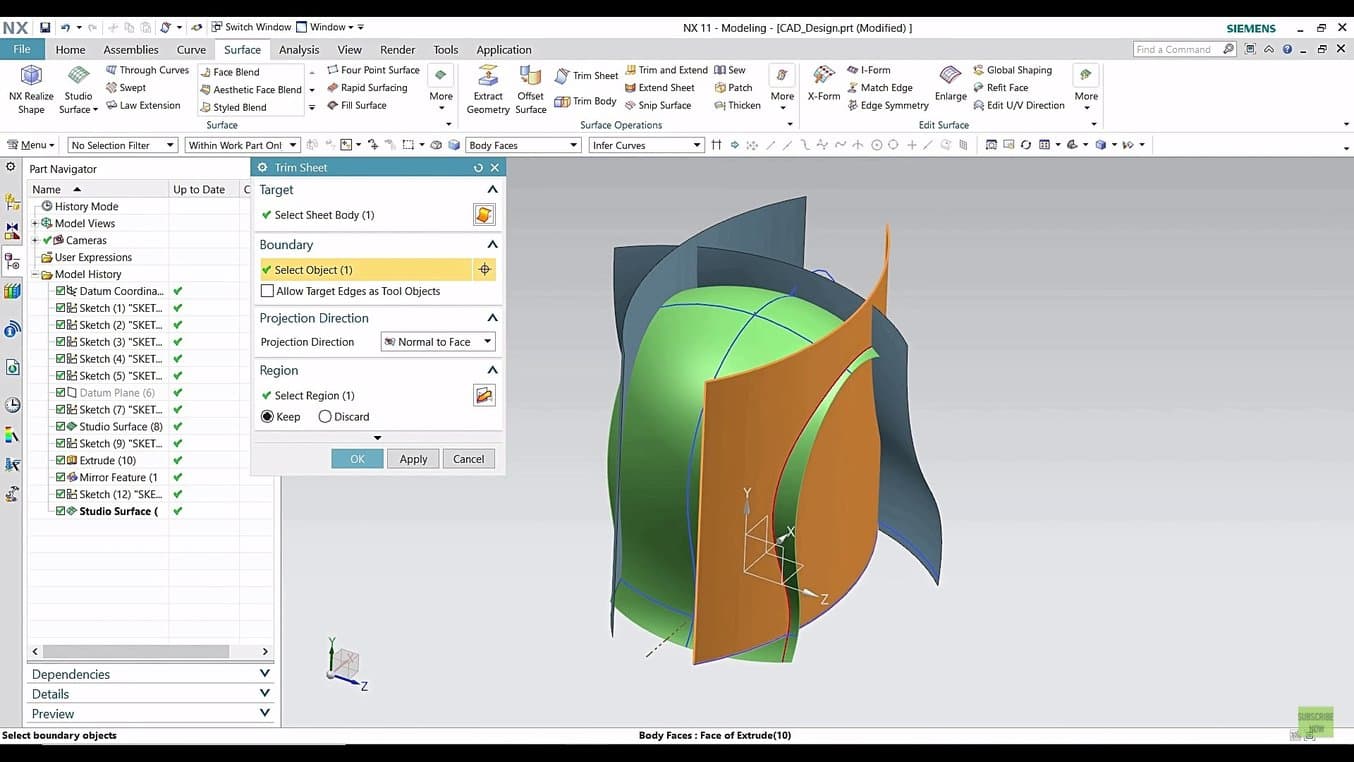
Siemens NX offers a highly complete set of surfacing features.
Best Free CAD Software
FreeCAD
Developer: Jürgen Riegel, Werner Mayer, Yorik van Havre
Released: 2002
Platforms: Linux, Unix, macOS, Windows
Ideal for: Concept and part design, 3D Printing
Price: free
For those looking for a free CAD solution beyond the levels of TinkerCAD, but at the same time without the professional prowess of Fusion360, there is FreeCAD. FreeCAD is parametric to some extent as designers build up parts from sketches with dimensional constraints. The engine works mainly with solids but offers some surface-based operations as well. These are by far not as diverse and advanced as with other players in the industry, but do the job to three-dimensionally visualize a concept. And there is the rare option for a two-rail sweep. Instead of a feature tree, there is an undo/redo stack the program keeps track of. In addition, sketches remain linked to surfaces so the model will update to some extent with post hoc changes.
FreeCAD is not perfect. Constraining sketches can become a bit messy, especially when adding mirror operations and multiple tangent curves. Trimming surfaces can get glitchy as well. Fortunately, though, there are workarounds for many of these cases. The icon-based user interface feels a bit outdated. Hotkeys are available for the most important commands, and overall, the tool takes a bit of a learning curve to master.
The most important additional features are a Mesh Design workbench with mesh repair and STL file export features for 3D printing, a ray trace rendering workbench, one for structural finite element analysis (FEA), and computational fluid dynamics (CFD). This is called OpenFoam and can be used for fluid flow and aerodynamics analysis. FreeCAD is open-source and parts of it, such as added animation features, can be scripted in Python or through a C++ API.
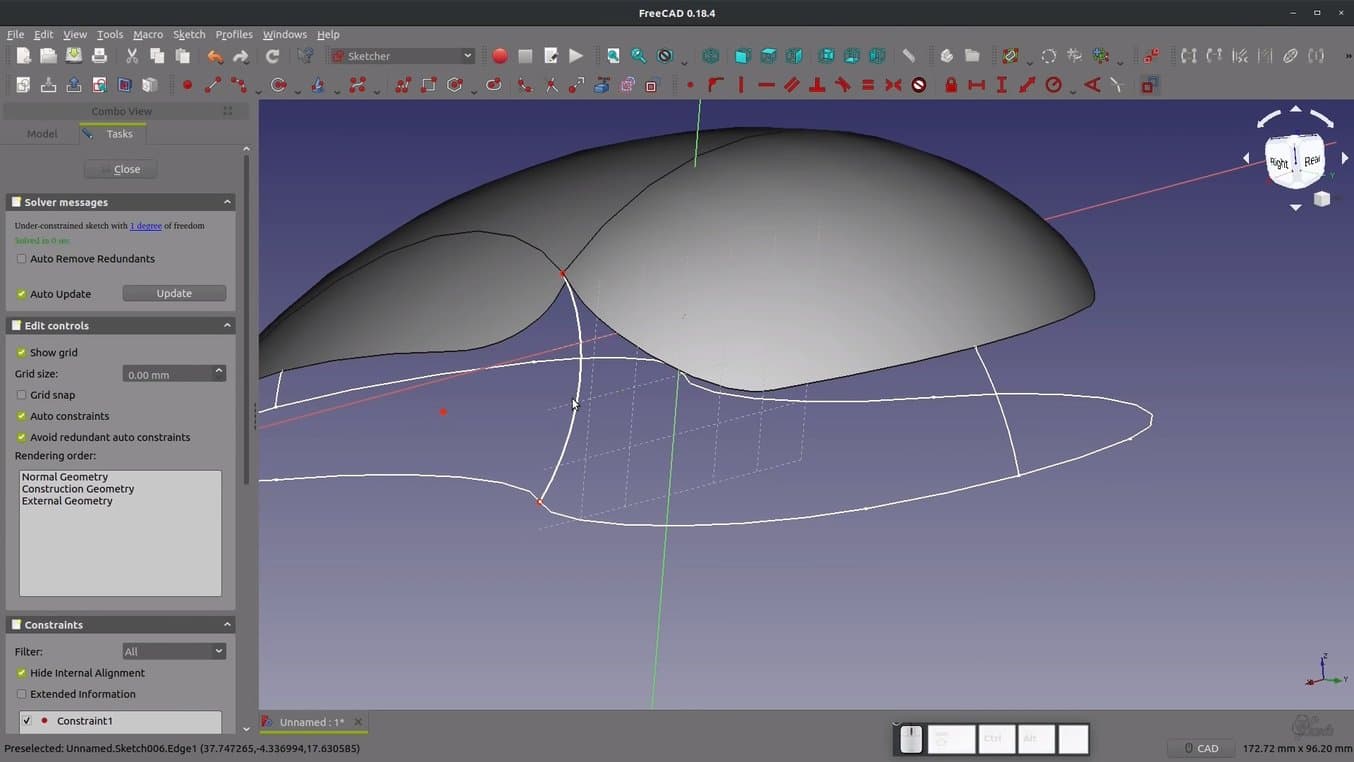
FreeCAD offers a starting inventory of constraint-based solid modeling as well as surfacing features.
Blender
Developer: NeoGeo
Released: 1994
Platforms: Linux, macOS, Windows, Android, BSD
Ideal for: Visual FX, Character Design, Art, Animation, 3D Printing, Virtual Reality
Price: free
Blender has grown up to be a popular open-source alternative to all-encompassing animation studios such as Maya and 3D Studio Max. Its combination of advanced mesh modeling and sculpting renders it attractive for visual effects artists as well as 3D printing enthusiasts.
CG artists will enjoy the intuitive rendering engine, motion tracking capabilities, inverse kinematics for character rigging, and advanced simulation effects such as particle clouds, smoke, fluids, explosions, cloth, skin, and collisions. For beginners in 3D printing or those coming from a more engineering-minded CAD environment, the transition to Blender will entail a steep learning curve. It is probably better to stick to one modeling approach or the other. Nonetheless, once its toolsets have been mastered, the sky's the limit. Meshes can be carefully controlled to create the smallest and most complex of details. They can be deformed by bending, twisting, tapering, stretching, and much more. Blender is based on polygonal modeling yet it allows for some numerical input, for example in the new Geometry Nodes workspace which works much like Grasshopper. Also, mesh modifiers are saved in the modifier stack and can be changed at any point during the modeling process. A nice feature for 3D printing is converting a mesh to a wireframe. This can result in lattice-like structures with intricate patterning that are only realizable using a 3D printer.
Compared to the commercial giants in the marketplace that cost nearly US$2,000/year, Blender is a bit harder to learn, slightly more error-prone regarding features such as mesh booleans, a tad more limited in sculpting features, and overall better tailored to small projects. Nevertheless, it is a great start for those interested in mesh modeling for 3D printing.
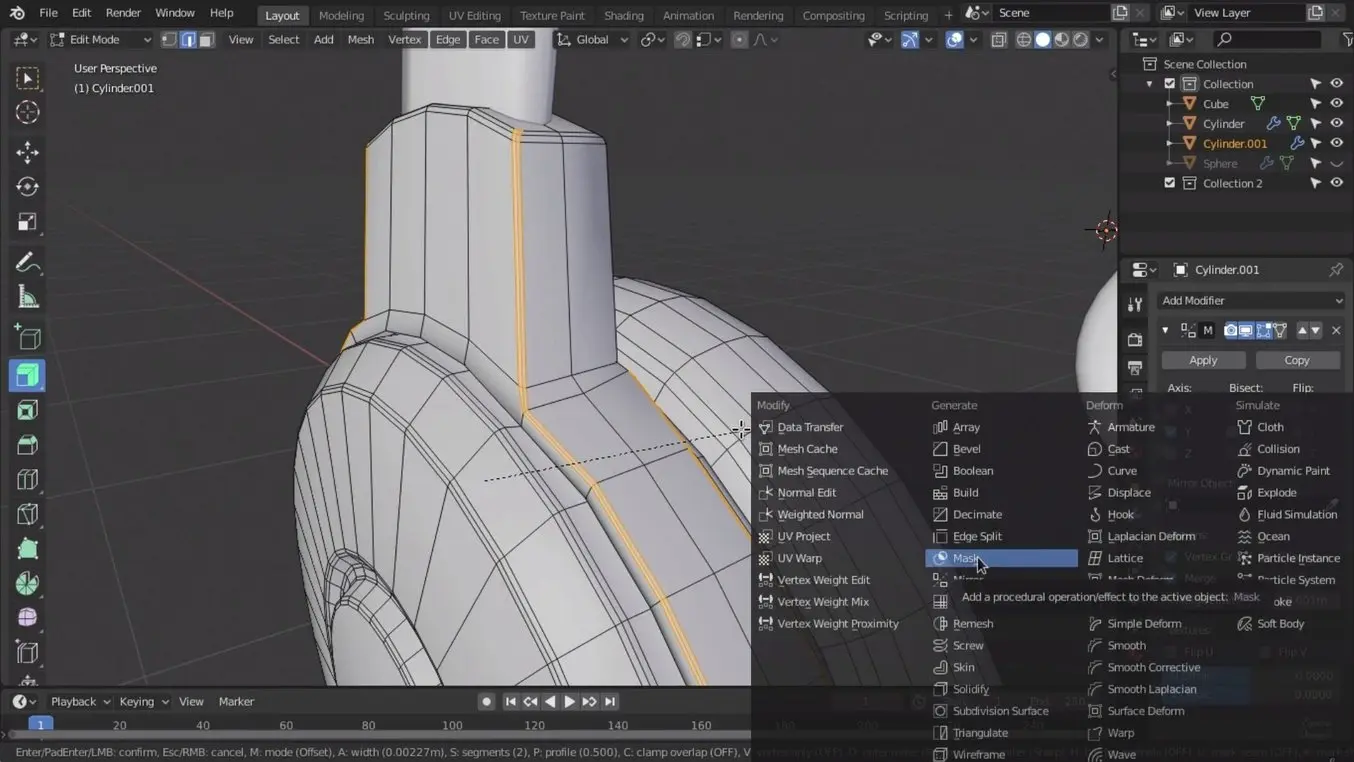
Blender is the mesh modeler of choice for independent designers and startups.
SketchUp
Developer: Trimble Inc.
Released: 2000
Platforms: Windows, macOS
Ideal for: Concept layouts, Architecture, Landscaping Design
Price: Free, Pro $299/year, Studio $699/year, $55/year for students and teachers
SketchUp is one of the simplest entry points for those taking a first dive into the world of 3D modeling. In its ability to quickly set up layout drawings it is popular among architects for rough explorations and demonstrations at the front end of the development process. Paired with a rendering plug-in such as V-Ray, Thea, Maxwell, or the free Lumion LiveSync, as well as the inbuilt fly-through feature, it can be a powerful visualization tool.
Besides setting up a model from scratch it is possible to draw one of the thousands of models out of the 3D Warehouse. And where the possibilities for 3D modeling seem a bit restricted at first, there is the Extension Warehouse for hundreds of additional features. With the right plug-ins, users are empowered to draw complex curves, perform edge chamfers and fillets, do advanced vertex editing and mesh modifications, add project documentation, export STL files for 3D printing, STEP files for other CAD environments, or Keyshot files for external rendering, use Boolean operators, surface flattening, or add parametric modeling to the workflow. It has a bit of a learning curve and even though some modeling features will remain cumbersome or even non-existent, SketchUp is a worthwhile candidate for both the amateur and professional modeler.
SketchUp has a free in-browser app but to take full advantage of additional modules the Pro version is required. SketchUp Shop costs less than half of that and does not have plug-in support but adds the Augmented Reality viewer.
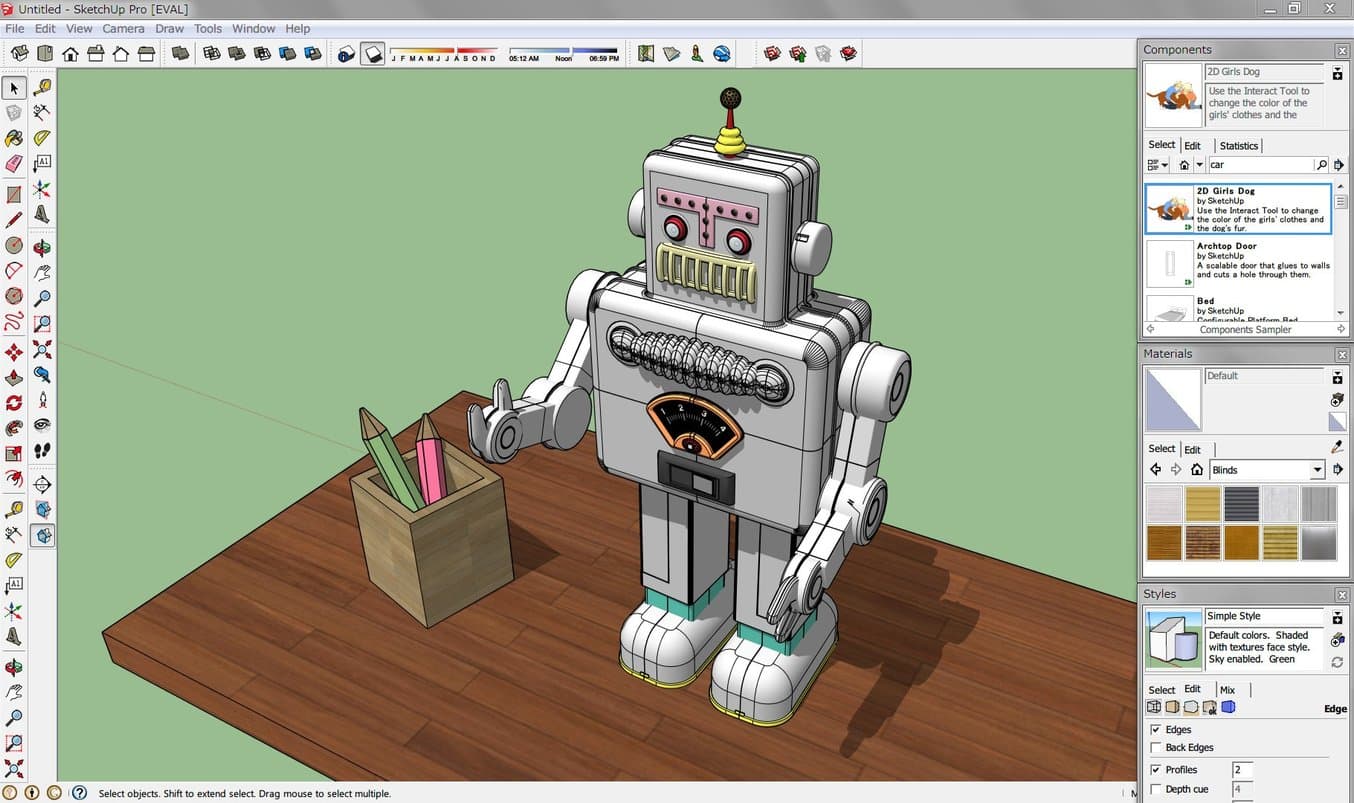
Using add-ons, it is possible to create advanced mesh geometry in SketchUp.
Best CAD Software for 3D Printing
MeshMixer
Developer: Autodesk
Released: 2009
Platforms: Windows, macOS
Ideal for: 3D Printing
Price: free
MeshMixer is the digital Swiss army knife for creating and preparing meshes for 3D printing. In its simplicity, it is to meshes what TinkerCAD is to solids. From a shape library, existing geometry can be imported and combined with the mesh. It is possible to extend the library with your own creations as well. When 3D scanning data is imported, it is possible to extract a partial surface and join it with new geometry for precisely fitting parts or wearables.
Mesh operations are limited to thickening, hollowing, bridging, plane cuts, smoothening, boolean operations, and extruding. Images can be projected for embossing or debossing. Equally interesting are the sculpting tools. Not as extensive as those of ZBrush or Mudbox, yet they are sufficient for developing simple 3D printable items. The mesh repair and support generation tools are among the best in its class, making MeshMixer one of the essential free tools to own for anyone with a 3D printer.
For more information, check out our MeshMixer tutorial with 15 tips to edit STL files for 3D printing.
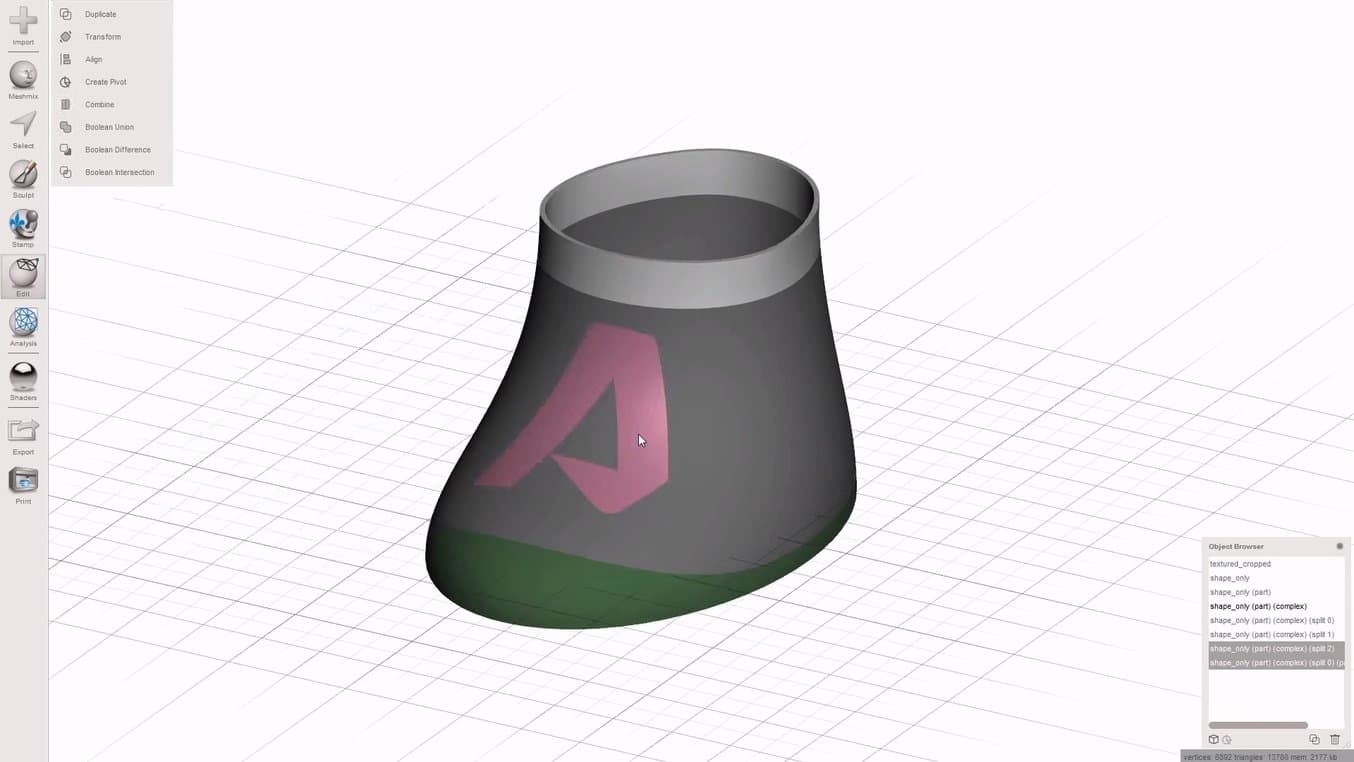
Besides being a mesh fixer, MeshMixer contains a surprising amount of creative CAD possibilities.
3DBuilder
Developer: Microsoft
Released: 2013
Platforms: Windows 10 with Creators Update + mobile
Ideal for: Education (elementary/middle school), 3D Printing
Price: Free
For those who are just getting started with 3D printing and have a 3D model downloaded and ready to print, there is no need to invest in any extraneous CAD software since Windows has a built-in solution. What seems like merely a viewer at first sight also offers some possibilities for texture painting, simple edits including boolean operations, and even three-dimensional engravings and embossings using text and images are part of its repertoire.
3D Builder is a compact application freely obtained from the Microsoft Store. It is compatible with the MS Scan app for importing 3D scan data. It uses the 3MF file format but exports STL and OBJ files as well.
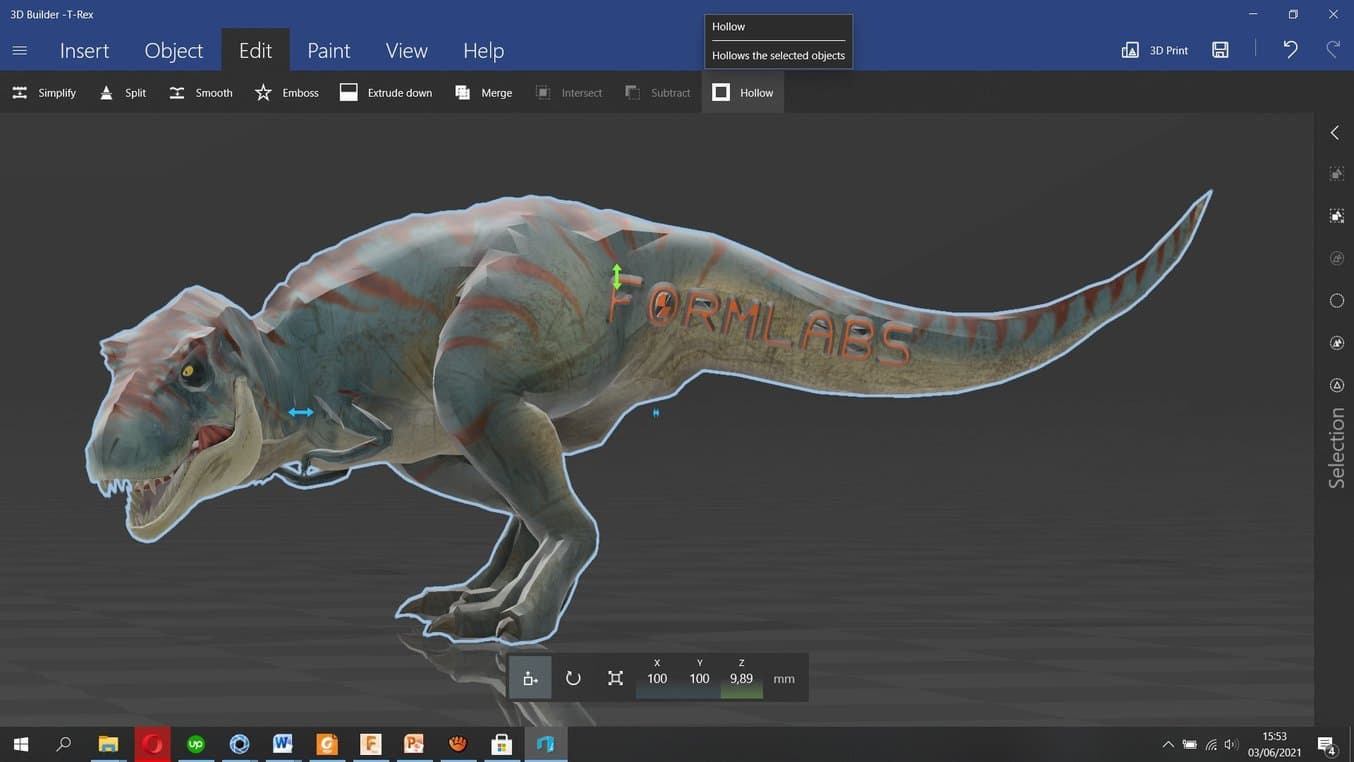
3DBuilder from Windows offers some simple features for editing 3D models and preparing files for 3D printing.
Learning CAD
When starting the software training, it is important to first learn about modeling strategies and proper workflows, such as following conventions in name-giving, grouping parts in a feature tree, creating backups, and consistently referring to global variables and coordinate systems. These will determine the quality of all future work—without a strong foundation, you may have issues solving more complex problems later on.
Modeling-wise, in parametric surface modelers it is usually preferred to create free-floating surfaces that extend freely into space on both ends and trim the different surfaces together into a solid in a later stage, as opposed to ‘patch modeling’ where every surface is created individually and immediately connected to its surroundings. The ‘master modeling’ approach takes planning even further and lays out all known dimensions in sketches before even starting to create resultant solid and surface geometry. This works well only in cases where little creative exploration is needed and the modeler is looking to step to engineering validation as soon as possible. Overly committal approaches can result in structural failures when drastic changes are required. Details such as roundovers and blends are best done together at a later stage, as are computationally heavy operations such as patternings, boolean functions, and text or image embossings. Working from rough to detailed is the standard procedure also in mesh and virtual clay modeling, with plenty of backup saves in-between.
There are a plethora of learning resources available online. Once you have the CAD tool of your choice, just explore tutorials on the website of the developer and on Youtube.
Get Started With CAD and 3D Printing
In this guide, we have evaluated the lion’s share of CAD offerings currently on the market, comparing them on the most important features such as prime uses, level of experience needed, user-friendliness, price, as well as functional versatility and technical depth regarding surface, solid, polygonal, and freeform modeling.
For bigger projects, a parametric modeler will be the best choice. The complexity of the pipeline and product construction will dictate which CAD configuration can best be used. The best systems enable a hybrid between modeling approaches, a wide array of modeling features and file formats, PLM and database integration, data-driven generative design, and a variety of user-friendly workspaces to bring the project all the way from conceptual to design, engineering, manufacturing, scale-up, and sales stages.
Deciding on a software environment is the most important CAD-related decision to be made. It is a wise choice to go for an industry-standard like SolidWorks or NX. Cloud-based systems such as Fusion 360 or OnShape are newer and a bit riskier, but they’re increasingly becoming more feature-rich and reliable. Rhinoceros is a great choice for those looking to rapidly create complex forms without needing the power of dimensional constraining. For artists, a sculpting environment enhanced with polygonal modeling such as ZBrush, Maya, or Blender will be the best choice. For quick projects, the easiest CAD software programs to learn are FreeCAD, TinkerCAD, Fusion 360, and SketchUp.
Are you 3D modeling already and looking to realize your designs? Learn how 3D printing works and how you can create models with incredible details.