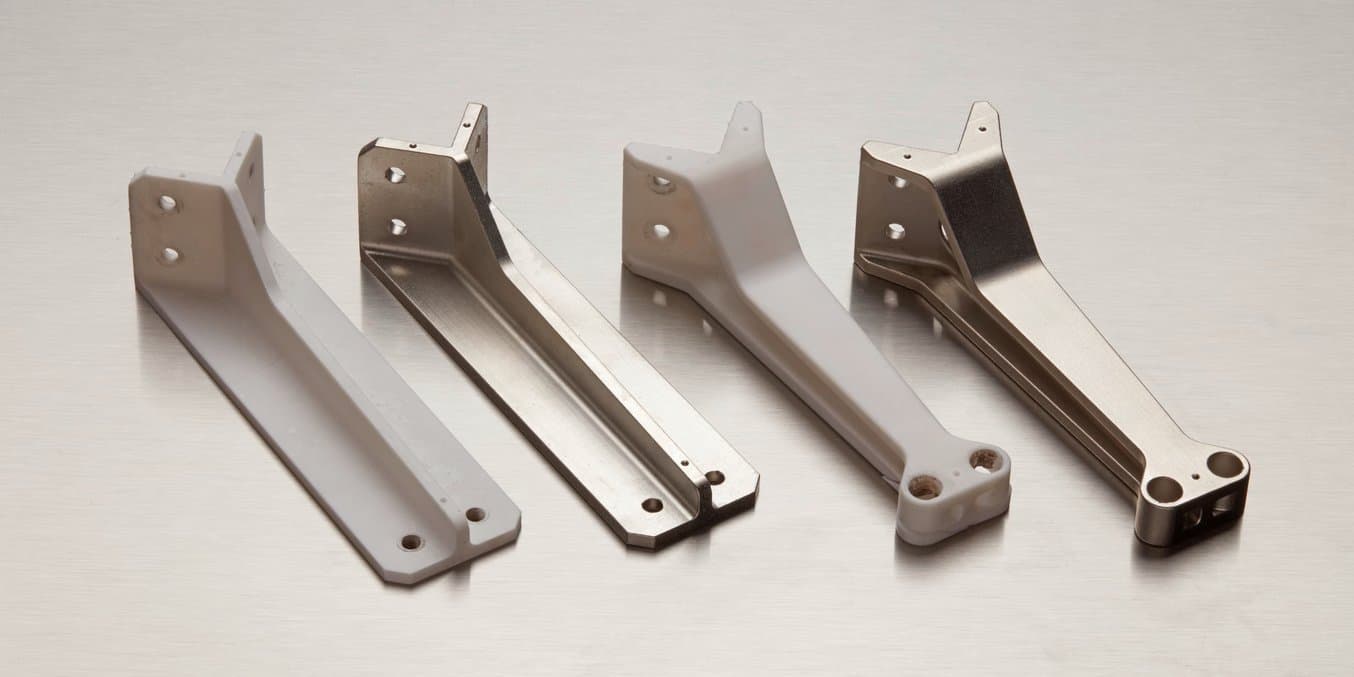
Electroplating lets you combine the strength, electrical conductivity, abrasion and corrosion resistance, and appearance of certain metals with different materials that boast their own benefits, such as affordable and/or lightweight metals or plastics.
In this guide, you’ll learn why many engineers, researchers, and artists use electroplating and metal plating in every stage of manufacturing—from prototyping to mass production.
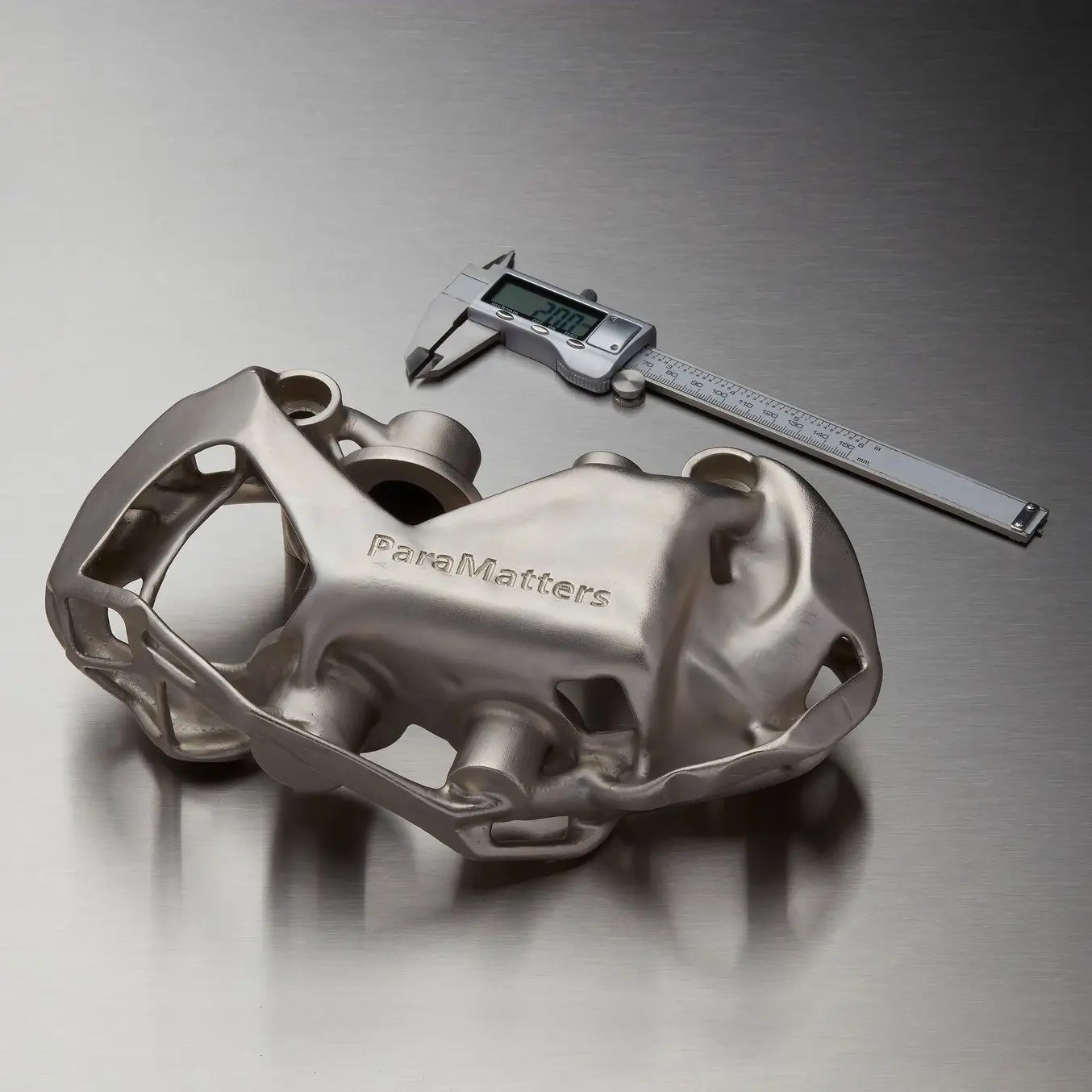
Strength from Metal: Strategies and Use Cases for Electroplating SLA Parts
Read on to learn how engineers are adding metal to resin 3D prints, and why hybrid metal parts can open doors to a surprising range of applications, including (but not limited to) end-use strength and durability.
What Is Electroplating?
Electroplating is the process of using electrodeposition to coat an object in a layer of metal(s). Engineers use controlled electrolysis to transfer the desired metal coating from an anode (a part containing the metal that will be used as the plating) to a cathode (the part to be plated).
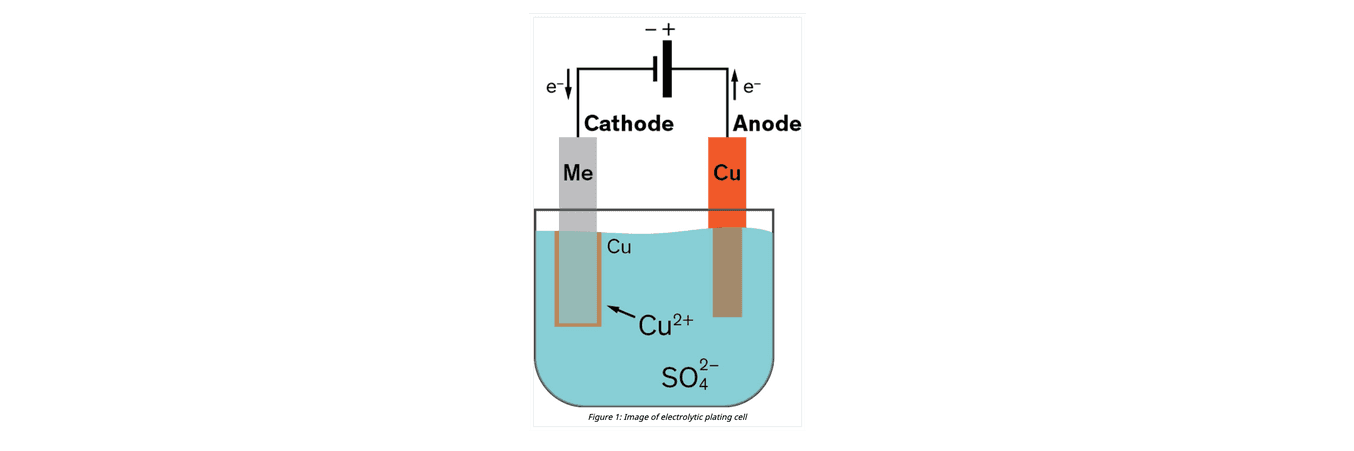
Diagram of copper electroplating using an electrolyte bath of copper sulfate, sulfuric acid, and chloride ions. (image source)
The anode and cathode are placed in an electrolyte chemical bath and exposed to a continuous electrical charge. Electricity causes negatively charged ions (anions) to move to the anode and positively charged ions (cations) to transfer to the cathode, covering or plating the desired part in an even metal coating. Electroplating takes a substrate material (often a lighter and/or lower-cost material) and encapsulates the substrate in a thin shell of metal, such as nickel or copper.
Electroplating is most commonly applied to other metals, because of the basic requirement that the underlying material (the substrate) is conductive. Although less common, autocatalytic pre-coatings have been developed which produce an ultra-thin conductive interface, allowing a variety of metals - most notably copper and nickel alloys - to be plated onto plastic parts.
Electroplating vs. Electroforming
Electroplating and electroforming are both performed using electrodeposition. The difference is that electroforming uses a mold that is removed after a part is formed. Electroforming is used to create solid metal pieces, whereas electroplating is used to cover an existing part (which is made of a different material) in metal.
Electroplating Material Options
You can electroplate a single metal onto an object, or a combination of metals. Many manufacturers choose to layer metals, such as copper and nickel, to maximize strength and conductivity. Materials commonly used in electroplating include:
- Brass
- Cadmium
- Chromium
- Copper
- Gold
- Iron
- Nickel
- Silver
- Titanium
- Zinc
Substrates can be made of almost any material, from stainless steel and other metals to plastics. Artisans have electroplated organic materials, such as flowers, as well as soft fabric ribbons.
It’s important to note that non-conductive substrates such as plastic, wood, or glass must first be made conductive before they can be electroplated. This can be done by coating a non-conductive substrate in a layer of conductive paint or spray.
Electroplating (3D Printed) Plastic Parts
Thanks to scientific advances in materials and plastic manufacturing, lightweight and low cost plastic parts have replaced more expensive metal parts in a wide variety of applications serving various industries, from automobiles to plumbing pipes.
Although plastic boasts an array of advantages over metal, there are many applications where metal still reigns supreme. Try as you might, you’ll never get plastic to have the same opulent finish as copper. And while plastic might be more flexible material than the majority of metals, it’s not nearly as strong. This is where metal plating comes in.
3D printing offers unique advantages when combined with electroplating. Engineers often choose to 3D print substrates because of additive manufacturing’s design freedom. It is often cheaper to electroplate 3D printed parts than to cast, machine, or use other manufacturing methods, especially when it comes to prototyping.
Stereolithography (SLA) 3D printing is ideal for electroplating because it creates 3D printed parts with very smooth or finely textured surfaces that make the transition between the two materials—plastics and metals—seamless. It also creates watertight parts that won’t get damaged when submerged in the chemical bath required during the electroplating process.
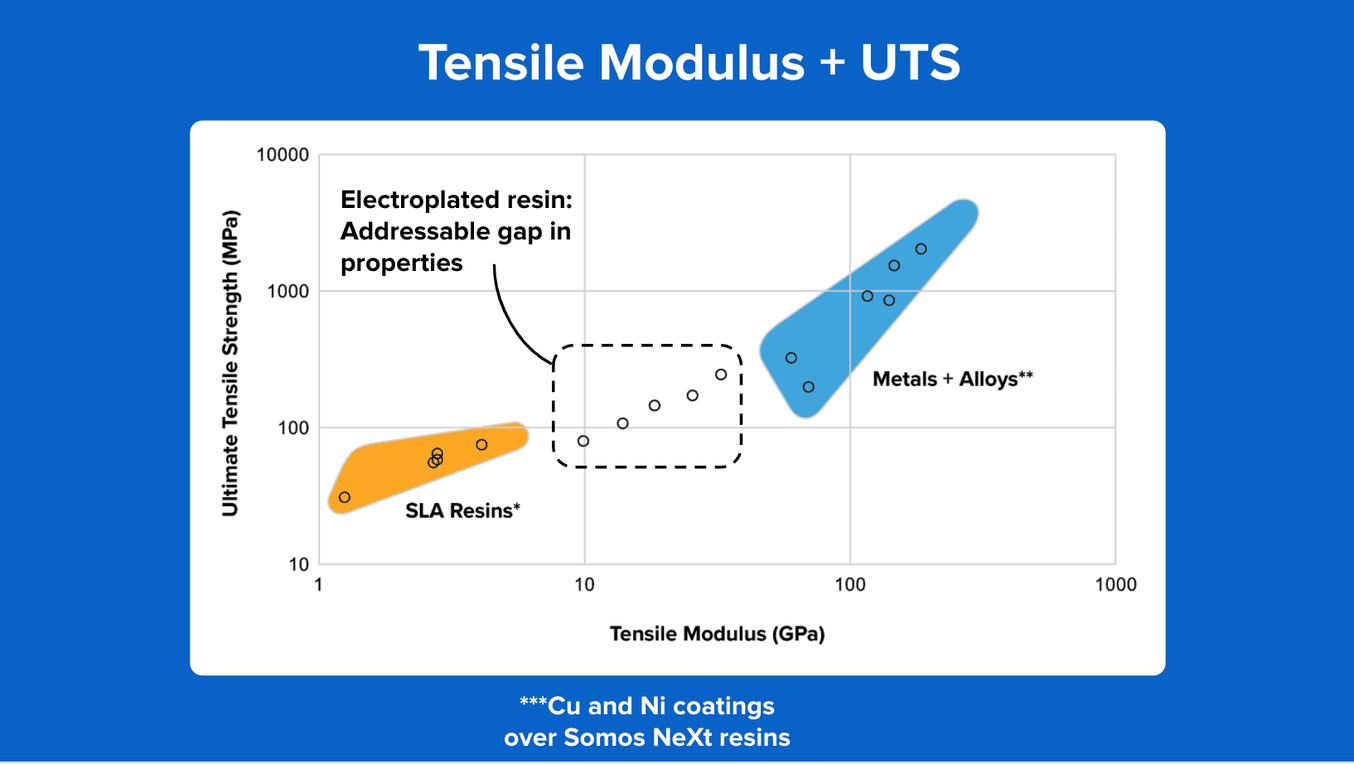
From an engineering standpoint, the combination of 3D printing and electroplating offers unique tensile strength options for finished designs. As you can see in the chart above, the combination of these two manufacturing processes bridges the gap in tensile strength between the two material groups.
Metal plating can have a major impact on the mechanical performance of (3D printed) plastic parts. With a structural metal skin and a lightweight plastic core, parts can be produced with surprisingly high flexural strength characteristics.
In addition to improving mechanical behavior, electroplating can be used to protect plastic parts from environmental degradation. In applications where plastic parts are exposed to chemical attack or ultraviolet light, metal plating provides a permanent barrier that can extend the life of your parts from months to years.
When used as an aesthetic treatment, plating offers an easy way to create prototypes that both look and feel like metal. Depending on the plate thickness, electroplated plastic can be thin and light, or add noticeable weight to a part. Thicker electroplated coatings can even be texturized or polished to achieve a variety of metal finishes, from cast aluminum to mirrored chrome. More complex textures can be achieved by 3D printing a textured resin substrate.
Given the potential combinations of 3D printable materials, a variety of plating metals, and plate thickness ratios, it’s easy to see how electroplating gives engineers a new field of design options to consider.
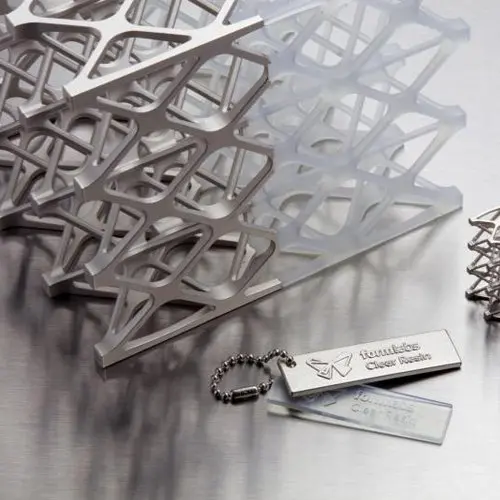
The Closest Thing to Metal 3D Printing With a $3500 Printer
In this webinar, learn how electroplating expands the material palette of SLA 3D printing to achieve high-stiffness, wear resistant end-use parts.
The Benefits of Electroplating
Electroplating offers many benefits, including increased strength, lifespan, and conductivity of parts. Engineers, manufacturers, and artists capitalize on these benefits in a variety of ways.
Engineers often use electroplating to increase the strength and durability of various designs. You can increase the tensile strength of various parts by coating them in metals such as copper and nickel. Place a metallic skin on parts and you can improve their resistance to environmental factors like chemical exposure and UV light for outdoor or corrosive applications.
Artists often use electroplating to preserve natural elements prone to decay, such as leaves, and turn them into more durable works of art. In the medical community, electroplating is used to make medical implants that are corrosion-resistant and can be properly sterilized.
Electroplating is an effective way to add cosmetic metal finishes to customer products, sculptures, figurines, and art pieces. Many manufacturers also choose to electroplate a substrate to create more lightweight parts that are easier and cheaper to move and ship.
Electroplating also offers the benefit of conductivity. Because metals are inherently conductive, electroplating is a great way to increase the conductivity of a part. Antennas, electrical components, and other parts can be electroplated to increase performance.
The Limitations of Electroplating
Though electroplating boasts plenty of benefits, its limitations lie in the complexity and hazardous nature of the process itself. Workers performing electroplating can suffer from hexavalent chromium exposure if they don’t take proper precautions. It is essential for workers to have a properly ventilated workspace. The U.S. Department of Labor Occupational Safety and Health Administration has published numerous documents outlining the risks involved in electroplating.
Although it is possible to electroplate resin parts yourself, amateur users may run into difficulty. The main reason is quality and capability. Laminate adhesion strength using DIY electroplating methods is usually lower than what is achieved by a professional plating service. Structural plating, which requires long plate times, multiple baths, and compatibility between metals, is quite difficult to execute reliably. Successful applications of in-house plating are typically simple and small, such as jewelry prototyping, and thin (single layer) RF copper coatings.
Because of the expertise required and the dangers involved, many engineers and designers choose to hire a third-party electroplating manufacturer specializing in this process. Luckily, several companies, such as RePliForm and Sharretts Plating, specialize in custom electroplating projects. Download our white paper for a list of electroplating services by region and job size.
The video above shows how to electroplate with easy-to-acquire tools, such as a cell phone charger and spare copper pipe. We recommend you wear a mask, gloves, and eye protection while electroplating and only work in a well-ventilated space.
The Many Applications of Electroplating
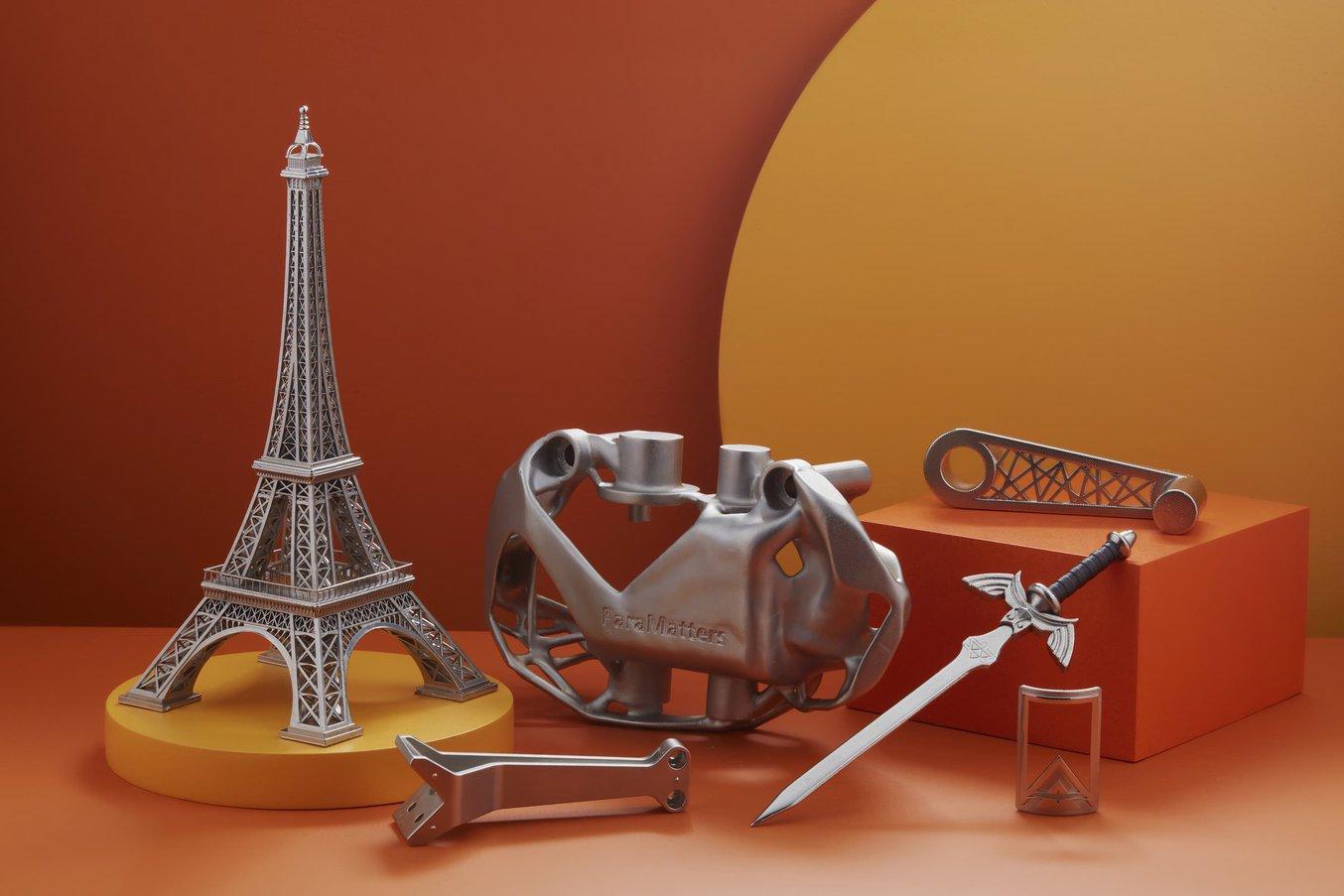
Numerous industries use electroplating to make everything from engagement rings to electrical antennas. Here are some common examples:
Aerospace
Many airplane components are electroplated to add a “sacrificial coating,” which increases the lifespan of parts by slowing down corrosion. Because aircraft components are subject to extreme temperature changes and environmental factors, an additional metal layer is added to a metal substrate so that the functionality of a part isn’t compromised by normal wear and tear.
Many steel bolts and fasteners designed for the aerospace industry are electroplated in chromium (or, more recently, zinc-nickel, due to changing restrictions).
Art and Home Decor
Type the word “electroplated” into Etsy, and you’ll be presented with a vast array of electroplated home decor and one-of-a-kind keepsakes. Artisans often turn biodegradable items, including flowers, branches, and even bugs, into durable and long-lasting pieces of art with this process. You can employ electroplating to show off and preserve fine details in items that would otherwise quickly decompose.
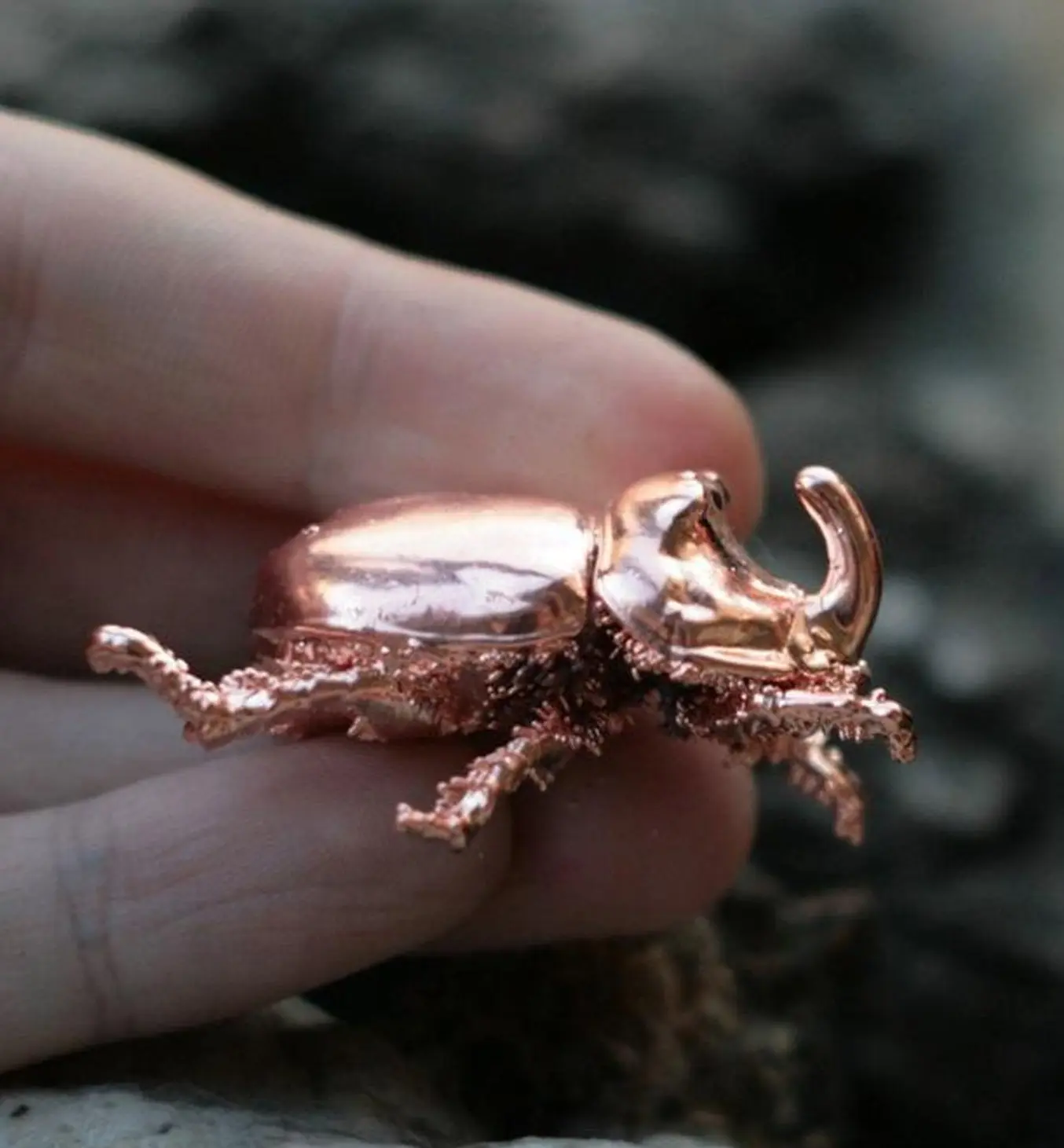
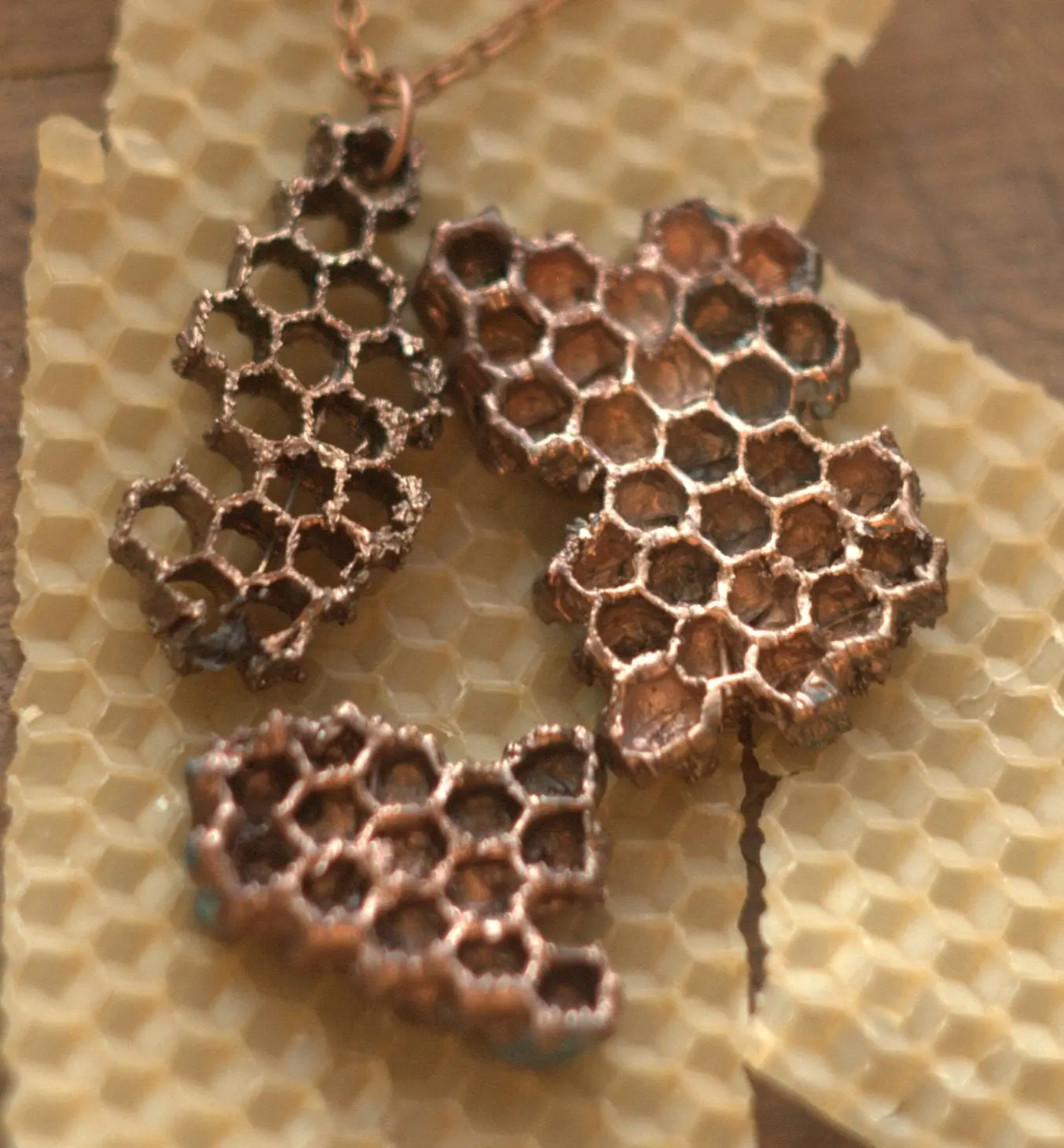
Electroplating is often used to create art, such as this copper-plated beetle and honeycomb. (image source)
Digital designers sometimes use electroplating to produce sculptures. Designers can 3D print a substrate using a desktop 3D printer and then electroplate the design in copper, silver, gold, or any metal of choice to achieve their desired finish. Combining 3D printing with electroplating in this manner produces pieces that are easier (and cheaper) to manufacture, while still having the same look and finish as a sculpture that is solid cast metal.
Automotive
Electroplating is very common in the automotive industry. Many major automotive companies use electroplating to create chrome bumpers and other metal parts.
Electroplating can also be used to create custom parts for concept vehicles as well. For example, VW teamed up with Autodesk to create hubcaps for their “Type 20” concept vehicle. The prototype hubcaps were 3D-printed and then electroplated.
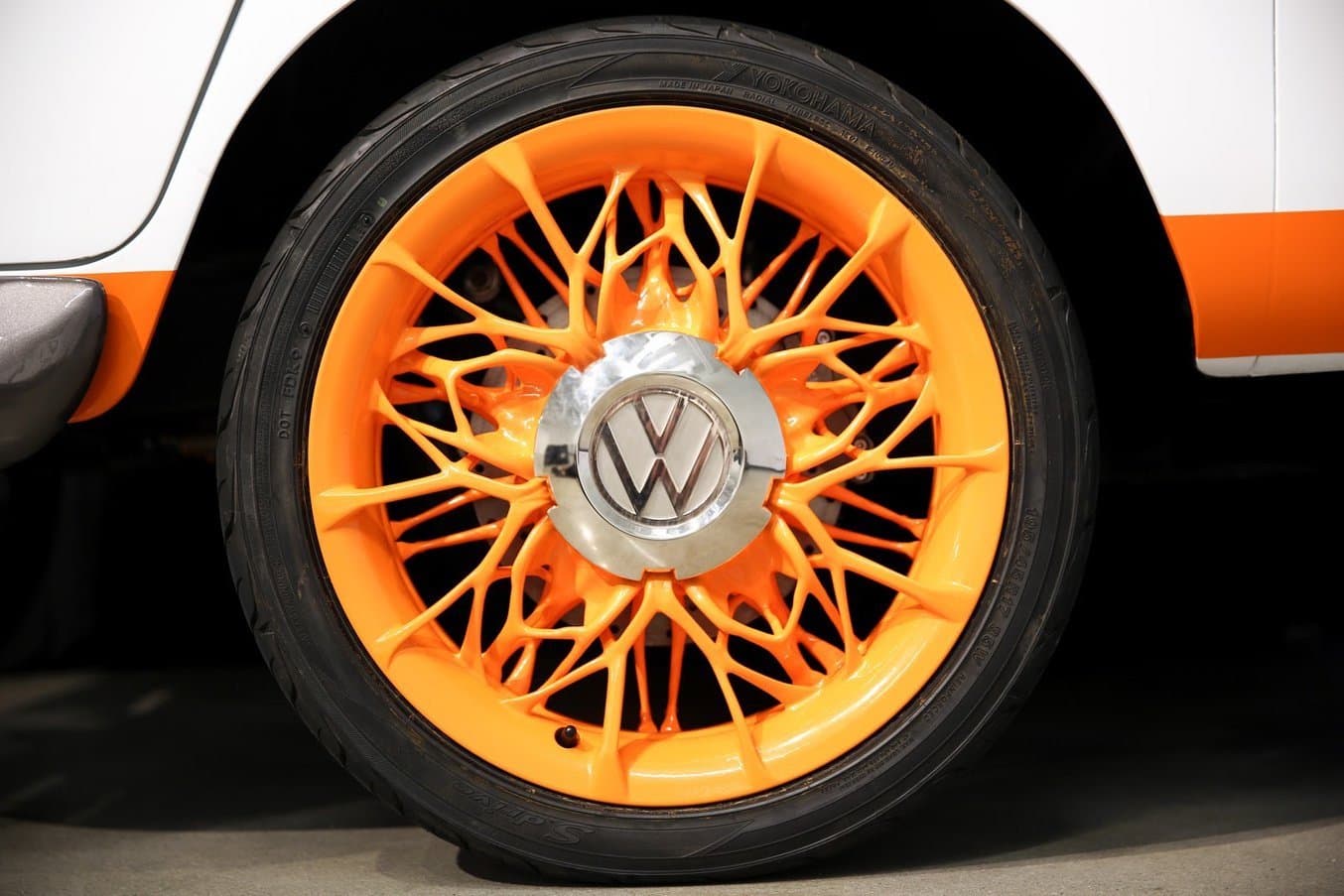
Restoration companies and vehicle customization businesses also use electroplating to apply nickel, chrome, and other finishes to various car and motorcycle parts.
Jewelry
Electroplating is perhaps most commonly associated with the jewelry industry and precious metals. Jewelry designers and manufacturers rely on this process to enhance the color, durability, and aesthetic appeal of rings, bracelets, pendants, and a wide range of other items.
When you see jewelry that is described as being “gold plated” or “silver plated,” there’s a high chance the piece you’re looking at was electroplated. Combinations of various metals are used to achieve uniquely hued finishes. For example, gold is often combined with copper and silver to create rose gold.
Medical and Dental
Electroplating is used to add resilient exteriors to all sorts of medical and dental elements. Gold plating is often employed to create tooth inlays and aid in various dental procedures. Implanted parts such as replacement joints, screws, and plates are frequently electroplated to make parts more corrosion-resistant and compatible with pre-insertion sterilization. Medical and surgical tools, including forceps and radiological parts, are also commonly electroplated.
Power
Numerous electrical and solar components are electroplated to increase conductivity. Solar cell contacts and various types of antennas are routinely manufactured using electroplating. Wires can be electroplated in silver, nickel, and many other types of metal. Gold plating is often used (in conjunction with other metals) to increase durability. Gold is also frequently used to increase the lifespan of parts because it is conductive, very ductile, and doesn’t interact with oxygen.
Prototyping
Producing custom or low-volume metal parts for prototyping can be very costly and time-consuming with traditional manufacturing processes. As a result, engineers often combine electroplating with 3D printing for a low-cost and time-saving solution.
For example, Andreas Osterwalder of the Swiss Federal Institute of Technology in Lausanne (EPFL) has been able to speed up the prototyping process and reduce costs of advanced experimental setups by 3D printing new designs himself on his Formlabs resin 3D printer and working with Galvotec to have those parts electroplated.
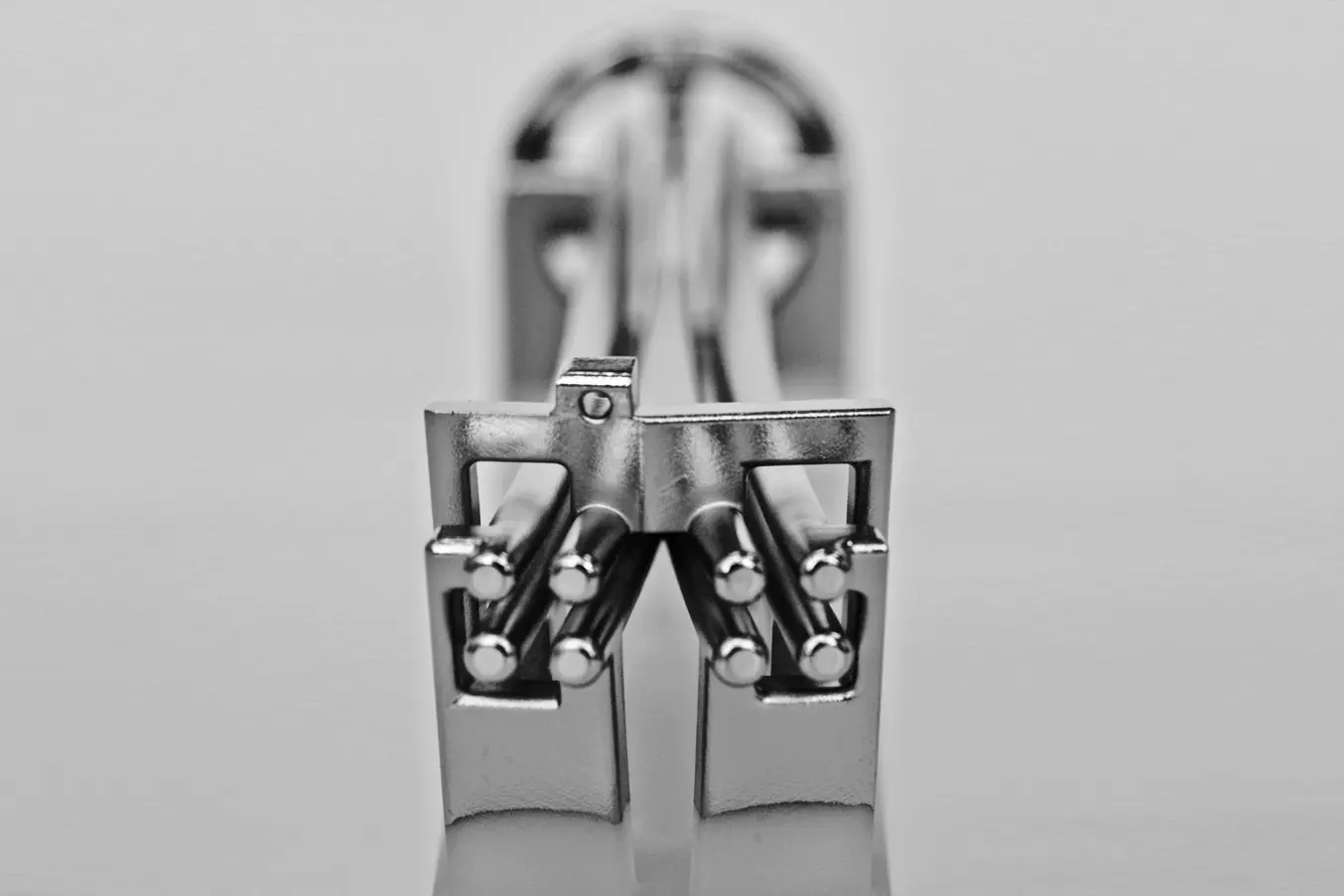
Andreas Osterwalder used 3D printing and electroplating to manufacture this beam splitter.
RF and Microwave Products
Antennas need to have electrical conductivity to propagate radio waves. While plastic 3D printed parts don’t conduct electricity, they offer almost infinite design freedom and materials with good mechanical and thermal properties. These benefits can be combined with electroplating to achieve the desired conductivity, resulting in a great solution for custom antennas for research and development in the automotive, defense, medicine, and education.
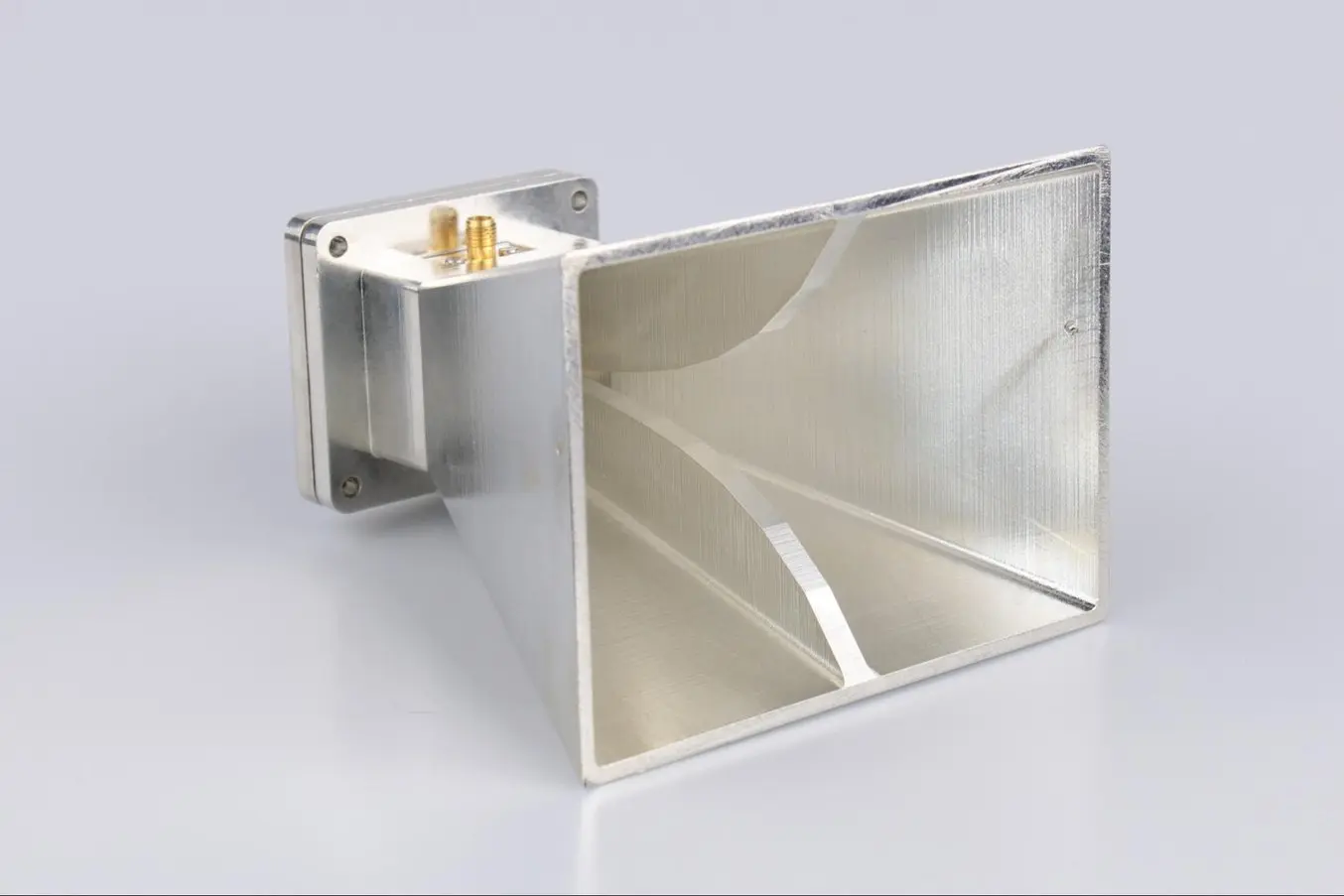
Electroplating plastic parts creates conductive parts that enable high performance RF applications.
Best Practices for Electroplating 3D Printed Parts
Electroplated composites are a means to a wide variety of ends. Because of its versatility, electroplating opens up countless possibilities across different industries. Want to learn more about electroplating 3D printed parts?
Download our white paper to learn how engineers are adding metal to resin 3D prints, and why hybrid metal parts can open doors to a surprising range of applications, including (but not limited to) enduse strength and durability. By the end of the white paper, you will learn new ways to apply electroplating, as well as design considerations and practical tips on using metal electroplating to amplify the performance of your SLA parts.