Heat-Resistant 3D Printing Materials Guide: Compare Processes, Materials, and Applications
As 3D printing hardware has increased in sophistication and ability, the material properties of the resins, powders, and filaments involved have become even more important in establishing new workflows and enabling new applications. Heat-resistant 3D printing materials are in high demand as applications in industries such as automotive, aerospace, energy and gas, and industrial manufacturing become more widespread.
Most 3D printing materials are some form of plastics, though there are 3D printers that can print metal or ceramic parts. Plastics are not known typically for their heat resistance, but new material developments in fused deposition modeling (FDM), stereolithography (SLA), and selective laser sintering (SLS) 3D printing technology have made heat-resistant resins, heat-resistant filaments, and heat-resistant powders available.
In the following article, we’ll cover the various types of 3D printers, heat-resistant 3D printing materials including heat-resistant filaments, resins, and powders, and the advantages and disadvantages of each.
Comparison: Heat-Resistant 3D Printing Processes
FUSED DEPOSITION MODELING (FDM) | STEREOLITHOGRAPHY (SLA) | SELECTIVE LASER SINTERING (SLS) | |
---|---|---|---|
Resolution | ★★☆☆☆ | ★★★★★ | ★★★★☆ |
Accuracy | ★★★★☆ | ★★★★★ | ★★★★★ |
Surface Finish | ★★☆☆☆ | ★★★★★ | ★★★★☆ |
Throughput | ★★★☆☆ | ★★★★☆ | ★★★★★ |
Complex Designs | ★★★☆☆ | ★★★★☆ | ★★★★★ |
Ease of Use | ★★★★★ | ★★★★★ | ★★★★☆ |
Materials Available | PLA, ABS, Polycarbonate (PC), PEEK, ULTEM | Heat-resistant resins True silicone Technical ceramic | Nylon 12, nylon 11, carbon and glass-filled nylon, TPU, polypropylene |
Highest Heat Deflection Temperature @ 0.45 MPa | 260 ºC (PEEK) | Plastics: 238 °C (High Temp Resin and Rigid 10K Resin) Ceramic: up to 1500 °C | 188 °C (Nylon 11 CF Powder) |
Cost | Budget FDM printers and 3D printer kits start at around $200. Professional desktop FDM printers range from $2,000 to $8,000, and industrial systems are available from $15,000. | Professional SLA 3D printers cost around $2,500 to $10,000, and large-format resin 3D printers are in the $5,000 to $25,000 range. | Benchtop industrial SLS 3D printers start just under $30,000 for the printer and $60,000 for the entire ecosystem, including powder management and cleaning stations. Traditional industrial SLS printers start at around $200,000. |
Advantages | Inexpensive consumer machines and materials | Accuracy Smooth surface finish Wide range of materials Biocompatible materials available | Strong functional parts Design freedom No need for support structures Biocompatible materials available |
Disadvantages | Lower quality Parts are not isotropic Limited design freedom | Sensitive to long exposure to UV light | Rough surface finish Limited material options |
Applications | Basic prototyping | Functional prototyping Short-run, bridge, or custom manufacturing Rapid tooling (molds, patterns) Manufacturing aids (jigs, fixtures) Dental and medical applications | Functional prototyping Short-run, bridge, or custom manufacturing Manufacturing aids (jigs, fixtures) |

How to Choose a 3D Printing Technology
Having trouble finding the best plastic 3D printer for your needs? In this video guide, we compare FDM, SLA, and SLS technologies across popular buying considerations.
Measuring Heat Resistance of 3D Printed Parts
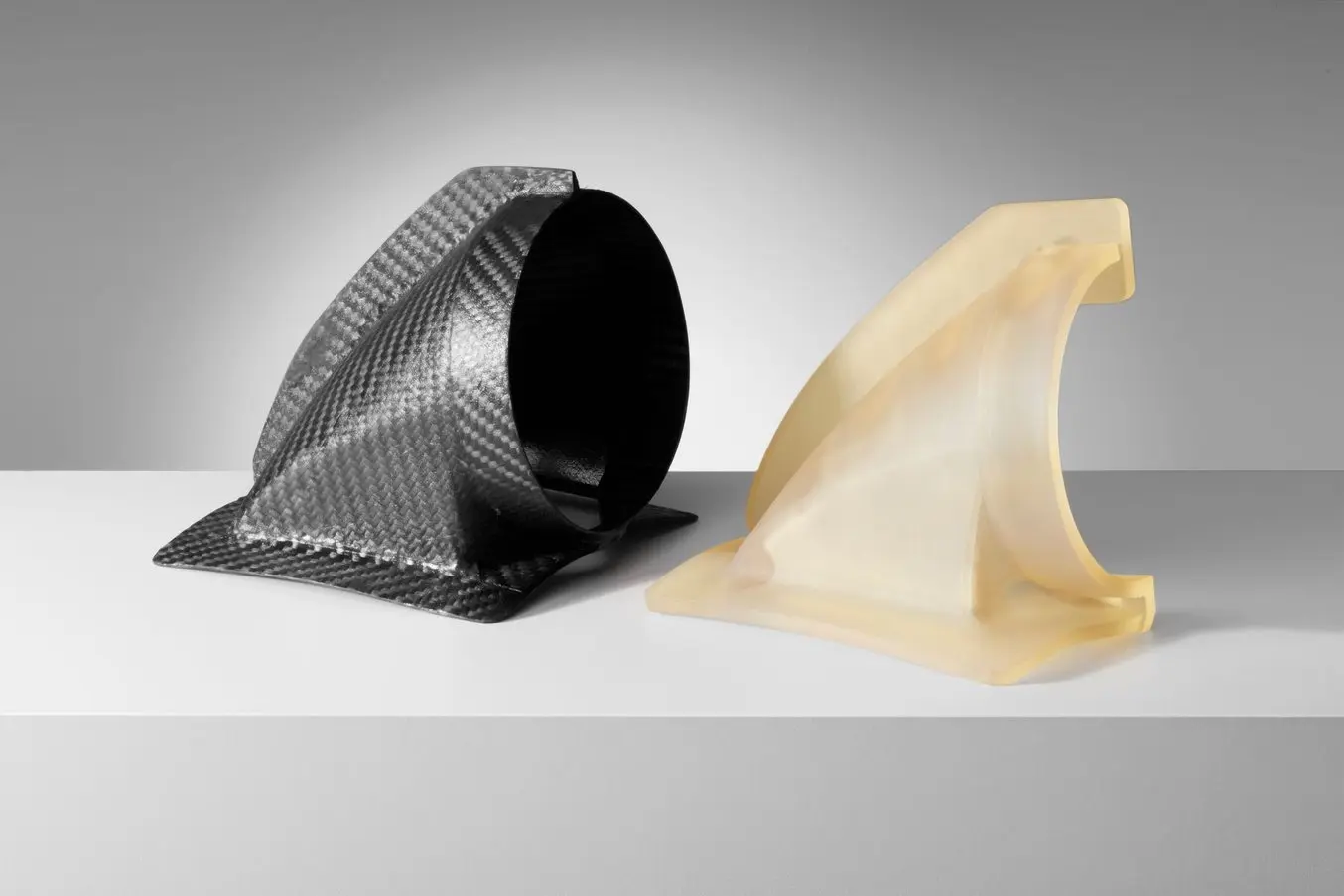
Materials that can maintain their strength even under high temperatures are ideally suited for applications like molding to fabricate end-use products, such as this carbon fiber manifold component (left) made using a High Temp Resin mold printed on the Form 3+ printer (right).
The catch-all term ‘heat resistance’ can refer to several measurable material properties that are specifically applicable in certain situations. The three mechanical properties are:
-
Heat deflection temperature (HDT): measures how well a material resists deformation under strain when at an elevated temperature, or more simply, how stiff a material is when heated.
-
Vicat softening point: measures the temperature at which a flat head needle can penetrate the surface of a material by a depth of 1 mm, or more simply, the point at which the stability of the solid form begins to break down. This measurement is helpful for flexible materials — for which HDT doesn’t make sense.
-
Glass transition temperature (Tg): measures the temperature at which a solid material melts.
These mechanical properties cannot be used interchangeably, as the measurements for a single material will differ considerably when looking at these three standards: a 3D printed resin will deform slightly under strain at one temperature (HDT), be susceptible to scratching or penetration (Vicat softening point) at another, and turn to liquid at a much higher temperature.
The most commonly used term is HDT for evaluating a material’s usefulness in a heated environment or application. Because HDT measures performance under strain, it’s important to note that there are two common strain measurements used when evaluating HDT: HDT at 0.45 MPa (67 psi) and HDT at 1.8 MPa (264 psi).
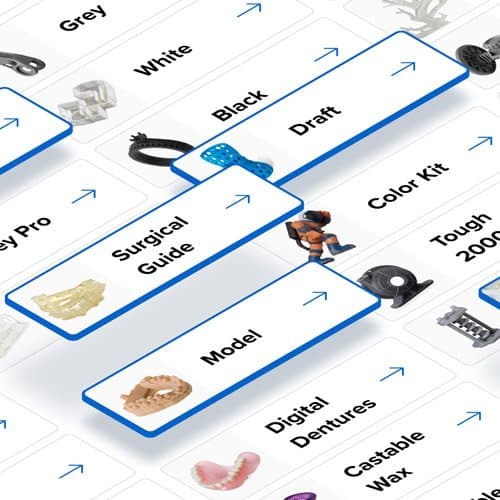
Find the Right Material for Your Application
Need some help figuring out which 3D printing material you should choose? Our interactive materials catalog helps you make the right material decisions based on your application and the properties you care the most about from our growing library of 3D printing materials.
Heat-Resistant Filaments for FDM 3D Printing
Fused deposition modeling (FDM), also known as fused filament fabrication (FFF), is the most widely used form of 3D printing at the consumer level, fueled by the emergence of hobbyist 3D printers. FDM 3D printers build parts by melting and extruding thermoplastic filament, which a printer nozzle deposits layer by layer in the build area.
Most FDM printers can print with filaments that offer heat resistance to around 100 ºC, while some industrial FDM 3D printers can also print parts for high-heat applications with heat-resistant filaments that have an HDT of 280 ºC.
Heat-Resistant FDM 3D Printing: Pros and Cons
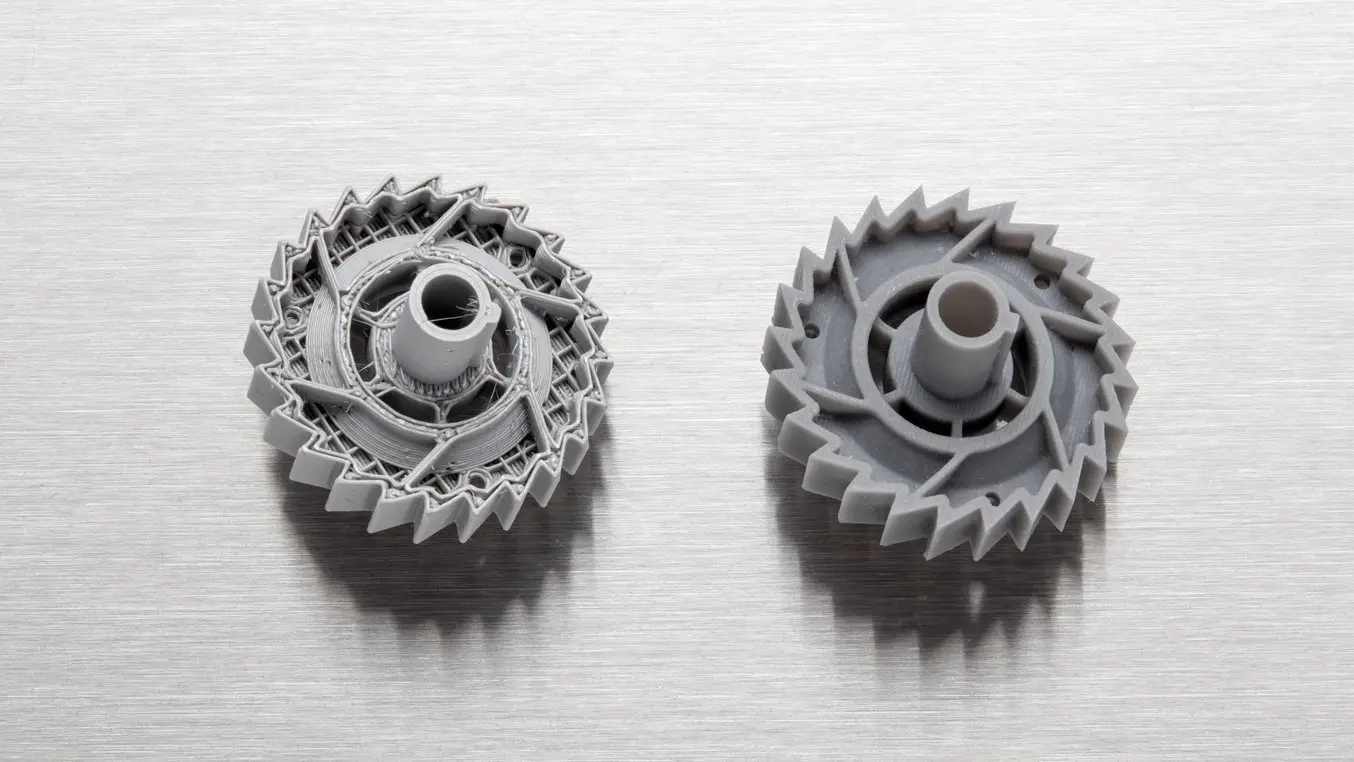
FDM printers struggle with complex designs or parts with intricate features (left), compared to SLA printers (right).
FDM 3D printing is well-suited for basic proof-of-concept models, as well as quick and low-cost prototyping of simple parts, such as parts that might typically be machined. It can be fast for simple designs and because many people think of FDM technology and the ‘hot glue gun’ process when they visualize 3D printing, it can be an easy introduction to 3D printing.
However, FDM has the lowest resolution and accuracy when compared to SLA or SLS and is not the best option for printing complex designs or parts with intricate features. Most professional and industrial FDM 3D printers use soluble supports to mitigate some of these issues and offer a wider range of engineering thermoplastics, but they also come at a steep price.
Printers for Heat-Resistant FDM 3D Printing
There are a wide range of FDM printers available for fabricating heat-resistant 3D printed parts. Many printers have open platforms as well, so that customers can print with multiple types of filaments from different manufacturers.
The main requirement for FDM 3D printing heat-resistant parts is making sure that the printer extruder and print bed can achieve the higher temperature settings necessary to melt and extrude heat-resistant filaments and to stabilize the parts during the printing process. A closed build chamber is recommended to maintain a consistent and high temperature during printing. Filaments that offer the highest heat resistance, like PEEK or ULTEM, are only compatible with specialized industrial FDM printers.
Because these materials are designed to resist deformation at higher temperatures, melting and extruding them also often present difficulties and can create inconsistent prints, nozzle jams, or other issues.
Compare Heat-Resistant 3D Printing Filaments
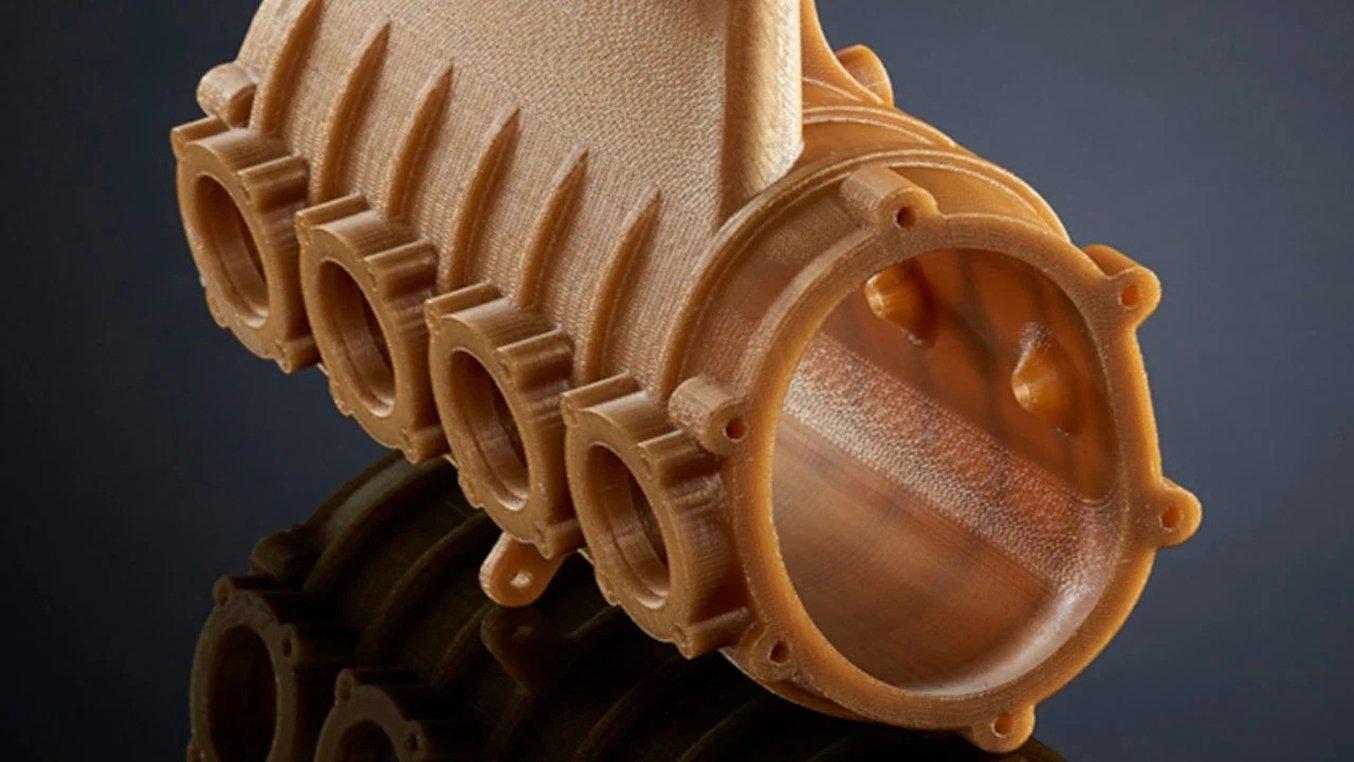
Some advanced FDM filaments like ULTEM have high heat resistance, and can be used for prototyping in higher heat applications, such as automotive components.
The two most common materials for FDM printing are PLA and ABS. Of the two, ABS offers higher heat resistance. There are also other more heat-resistant filaments available, however, these are often harder to print with or require specialized industrial 3D printers.
PLA
PLA is the most common plastic material for filament 3D printers — it’s low cost, has a very simple workflow, and comes in many colors, making it appealing to the hobbyist and K-12 education market. Standard PLA has a relatively low heat resistance, with an HDT of around 50 ºC at 0.45MPa. Therefore, for those looking to preserve the ease of use while being able to quickly and easily print heat-resistant PLA parts, many manufacturers offer a PLA material with additives that improve its heat resistance. Additionally, some workflows recommend an annealing step — meaning finished parts are reheated to further crystallize their structures and prevent creep or slow deformation when under strain.
ABS
ABS is the most common FDM 3D printing filament for engineering and other professional applications. It produces parts that are strong and impact-resistant. With an HDT of 90 ºC at 0.45MPa, it has better heat resistance than other common filament types like PLA or PETG. ABS parts are ideal for rapid prototyping applications and in education; the low cost and accessible workflow make it a popular choice for quick prints.
Polycarbonate (PC)
Polycarbonate materials, though known for their high tensile strength and temperature resistance, are typically difficult to 3D print because they expand when exposed to heat, and 3D printed parts can crack or malfunction. FDM 3D printer manufacturers often get around this by creating polycarbonate composites with additives that increase their adhesive ability. Some heat-resistant polycarbonate composite filaments can achieve HDTs of up to 110 ºC to 140 ºC at 0.45MPa, but require high temperatures for the print bed and extrusion nozzle, which can limit the types of printers available.
PEEK
PEEK or PEEK composite filaments offer the highest heat resistance for FDM 3D printing. These filaments, when combined with a material such as carbon fiber, as is the case with PEEK-CF, a carbon fiber PEEK composite, can reach up to 260 ºC before deforming under strain, making them ideal for quick prototyping of electrical connectors, outdoor products, or jigs and fixtures around molding applications and processes. The material is highly chemical resistant, friction resistant, and can be machined once in a solid form post-printing. PEEK’s heat resistant properties make it difficult to melt and extrude smoothly, and many users report that reliability and consistency with PEEK are harder to achieve. PEEK filaments are only compatible with a a few indsutrial FDM printers. To ensure good results, printers must have an extruder that can reach 400 °C, a chamber that can be heated to 120 °C, and a build plate that can heat to 230 °C. PEEK is also subsitantially more expensive than other filaments.
ULTEM (PEI)
ULTEM is another name for polyetherimide (PEI), a high-performance thermoplastic frequently used in FDM 3D printing because of its heat resistance and strength. With an HDT of around 150 °C at 0.45MPa and a high tensile strength, it is a worthy, and less expensive, replacement for PEEK in a variety of applications. ULTEM is more easily printed than PEEK, but still requires a high heat extruder — around 360 °C — to achieve good results, therefore only a limited range of FDM printers are suited for printing ULTEM filament.
Material | Heat Resistance | Ideal For: |
---|---|---|
PLA | 50 °C | Stiff and strong prototypes, jigs and fixtures, gauges |
ABS | 90 °C | Impact-resistant, consumer electronics prototyping |
Polycarbonate (PC) | 140 °C | Durable, lightweight, and shatter-resistant parts for enclosures |
ULTEM | 150 ºC | Chemical and temperature resistant jigs, fixtures, enclosures, and prototypes |
PEEK | 260 ºC | Prototyping or functionally testing electrical connectors to minimize thermal expansion, provide chemical resistance, and to promote effective sealing |
Note: Heat resistance refers to heat deflection temperature @ 0.45 MPa for all materials.
Heat Resistant Resins for SLA 3D Printing
Resin 3D printing, such as stereolithography (SLA) 3D printers, uses a laser or other light source to cure a liquid vat of plastic one layer at a time, and offers many options for heat-resistant 3D printing materials.
Resin 3D printer manufacturers mostly manufacture their own materials — so they aren’t as easy to identify and group as FDM 3D printing heat-resistant filaments. Many general-purpose 3D printing resins are not highly heat-resistant, but advanced materials can achieve the highest heat-resistance of all plastics 3D printing processes.
Heat-Resistant Resin 3D Printing: Pros and Cons
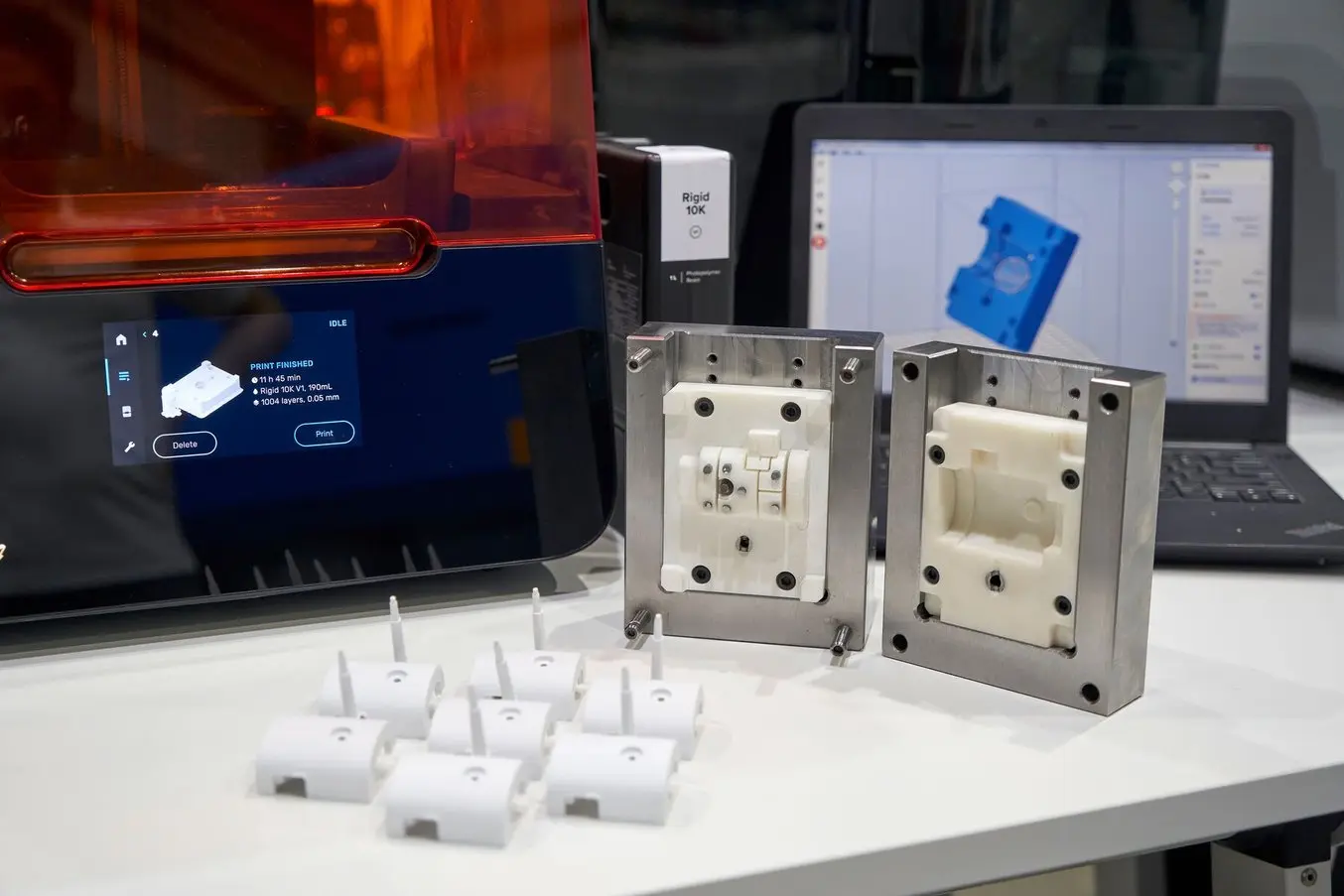
Resin 3D printing can be used for high heat and high pressure applications. Rigid 10K Resin molds provide a cost-effective alternative to machining aluminum molds for low-volume injection molding.
Resin 3D printers are ideal for creating high-quality parts with smooth surface finishes, tight tolerances, and a wide range of material properties.
Because resin printers cure liquid plastics with a light source, the layers are chemically bonded to each other in all directions, meaning the parts have isotropic mechanical properties, and aren’t prone to shearing along a particular axis like FDM parts are. This means resin 3D printed parts printed with heat-resistant resins can be relied upon for seals and gaskets, electrical connectors that need to mate with other components, or even automotive, aerospace, and energy utility applications where high temperatures are the standard environment.
The SLA process also lends itself to smooth surface finishes, few or nearly invisible layer lines, and a high degree of accuracy and precision. Heat-resistant resins are ideal for functional prototypes, manufacturing aids, and end-use parts in maintenance and repair operations (MRO) applications where the end-use environment might be hot.
Printers for Heat-Resistant Resin 3D Printing
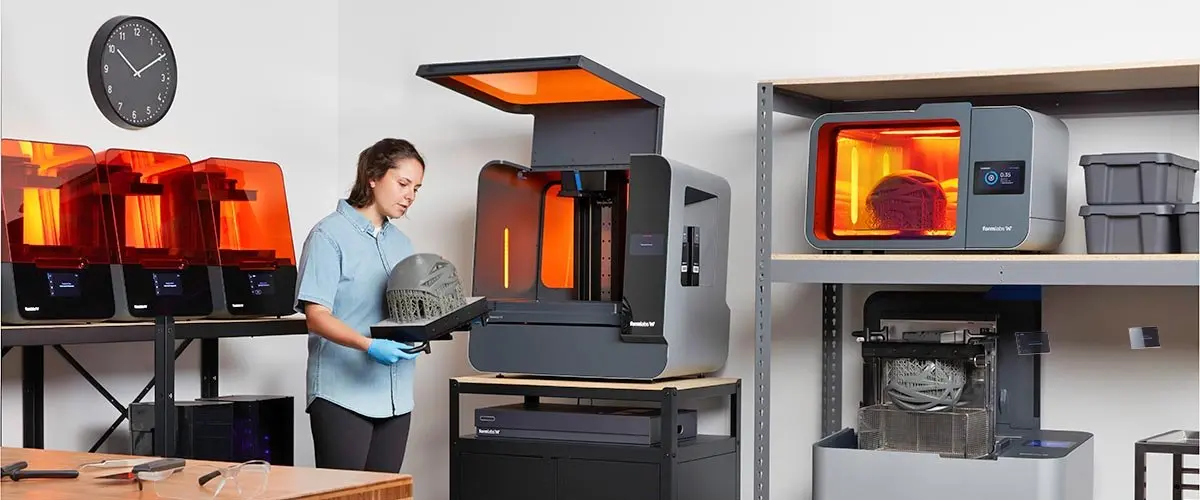
Complete solutions like the Form 3+ and Form 3L ecosystems make it possible to design, print, and post-process heat-resistant parts in hours. Customers can bring industrial quality 3D printing in-house, reducing costs and streamlining their workflows.
Material availability for resin 3D printing is highly dependent on the type of printer. Unlike with FDM 3D printing, where common types of plastic are available for different types of printers, SLA manufacturers often formulate and create their own, proprietary materials.
Formlabs offers over 40 high-performance resins for its line of desktop and large-format resin 3D printers with a diverse range of material properties. Certain resins are specifically designed for heat-resistance, such as High Temp Resin, while others are designed for other material properties, such as tensile strength, but achieve a high HDT as well.
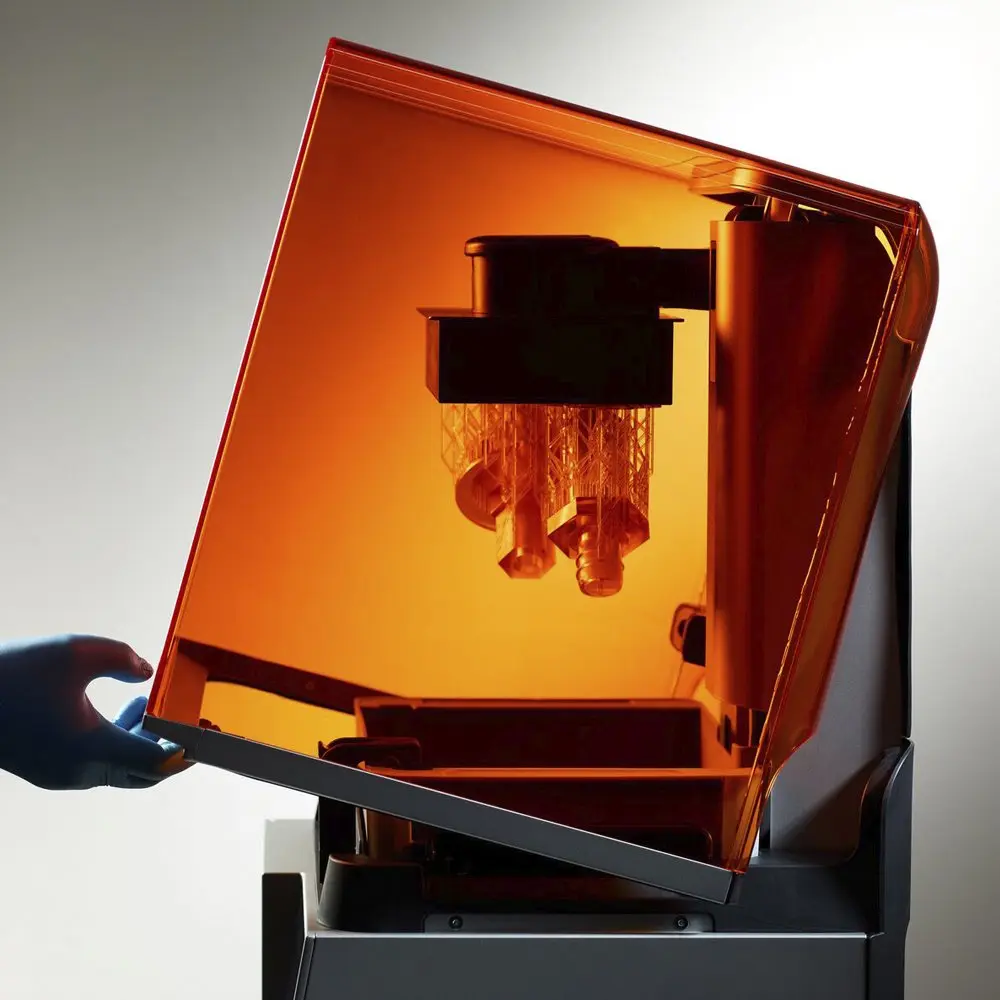
Introduction to 3D Printing With Desktop Stereolithography (SLA)
Looking for a 3D printer to produce high resolution models fast? Download our white paper to learn how SLA printing works and why it's the most popular 3D printing process for creating parts with incredible detail, high dimensional accuracy, and superior surface finish.
Compare Heat-Resistant 3D Printing Resins
SLA 3D printing delivers smooth, end-use quality parts that can perform in a variety of different environments. Formlabs has developed several high-temperature resistant resins specifically for customers working in extreme environments, in addition to creating several exceptionally strong resins that are also heat-resistant.
When choosing a resin printer for a heat-resistant 3D printing workflow, it’s important to delineate which mechanical properties are important in addition to HDT. For instance, if your parts will have an end-use operating environment of 200 ºC, that’s the first mechanical property to evaluate. If they only have an end-use operating environment of 150 ºC, you will have more options to choose from, and can then evaluate the printer based on other materials available, surface finish, ease of use, and price.
Clear Resin
Resin 3D printing offers the unique possibility to create truly transparent 3D printed parts. A standard material designed for strength and durability, Clear Resin has good enough heat-resistance that it can be used for higher heat applications such as hot air or gas ducting. With an HDT of 73 °C at 0.45 MPa, this general purpose material is excellent for functional prototyping. Clear Resin can be used for lower temperature molding applications, such as polyurethane molding, as mold temperatures tend to only reach about 60 °C.
Tough 2000 Resin
For prototyping strong, stiff, and sturdy parts that should not bend easily, Tough 2000 Resin is an excellent choice. It can be used for jigs and fixtures requiring minimal deflection, due to its close simulation of the strength and stiffness of ABS.
High Temp Resin
For high-temperature applications requiring the smooth surface finish and optimized material properties of SLA resins, High Temp Resin is a great fit. It is a purpose-built resin designed for high-heat resistance. With an HDT of 238 °C at 0.45 MPa, the highest among Formlabs resins, High Temp Resin is ideal for applications like functional prototyping of high-heat consumer electronics, hot air, gas, and fluid flow, and molds and inserts.
Flame Retardant Resin
Specially-designed to be self-extinguishing and halogen-free, Flame Retardant Resin is an SLA material with a UL 94 V-0 certification and favorable flame, smoke, and toxicity (FST) ratings. It is ideal for printing flame retardant, heat resistant, stiff, and creep-resistant parts that will perform well long-term in indoor and industrial environments with high temperatures or ignition sources. It has an HDT of 111 ºC at 0.45 MPa.
Rigid 10K Resin
Rigid 10K Resin is highly glass-filled material that is strong, stiff, and resistant to deformation under a variety of forces, pressures, and torques. It offers a very high heat resistance with an HDT of 238 °C at 0.45 MPa. It is ideal for short-run injection mold masters and inserts, aerodynamic test models, and fluid-exposed jigs, fixtures, and connectors.
Silicone 40A Resin
Combining the high performance of silicone and the design freedom of 3D printing to create highly functional silicone parts with excellent chemical and heat resistance (up to 125 °C), Silicone 40A Resin is the first accessible 100% silicone 3D printing resin. It can achieve fine features as small as 0.3 mm, and complex geometries that are not possible with traditional methods.
Alumina 4N Resin
The only accessible, high-performance technical ceramic, Alumina 4N Resin enables new 3D printing applications for extreme environments. Though printing with it does require extra equipment for a true ceramic burnout, once fully completed, Alumina 4N Resin parts have a maximum working temperature of 1500 °C. Using this material opens up new applications in industrial casting, molding, and even in specialty applications such as nuclear waste and liquid metals handling.
Material | Heat Resistance | Ideal For: |
---|---|---|
Clear Resin | 73 °C | Strong, precise concept models and prototypes Fluidics and mold making, optics, lighting, and any parts requiring translucency or showcasing internal features |
Tough 2000 Resin | 63 °C | Jigs and fixtures requiring minimal deflection Strong and stiff prototypes Manufacturing aids Housings and enclosures |
High Temp Resin | 238 °C | Hot air, gas, and fluid flow prototypes Heat resistant mounts, housings, and fixtures Molds and inserts |
Flame Retardant Resin | 111 °C | Flame retardant, heat-resistant, stiff, and creep-resistant parts Interior parts in airplanes, automobiles, and railways Protective and internal consumer or medical electronics components Custom jigs, fixtures, and replacement parts for industrial environments with high temperatures or ignition sources |
Rigid 10K Resin | 238 °C | Precise industrial parts that need to withstand significant load without bending Short-run injection mold masters and inserts Aerodynamic test models Heat resistant and fluid exposed components, jigs, and fixtures |
Silicone 40A Resin | 125 °C | Soft, pliable, and durable parts Seals, gaskets, grommets, connectors, and dampeners for automotive, robotics, and manufacturing Wearables, handles, and grippers for consumer products Flexible fixtures, masking tools, and soft molds for casting urethane or resin |
Alumina 4N Resin | 1500 °C | High voltage components: enclosures, connector housings and covers, terminal blocks Thermal protection: spark plug insulators, electrical mounting, insulating housings or tubes Foundry tools for metal casting: cores, crucibles, gating, sprues, mixing tools, thermocouple sheaths, metal filters |
Note: Heat resistance properties differ as no metric is applicable to all materials. The table shows thermal stability for Silicone 40A Resin, maximum working temperature for Alumina 4N Resin, and heat deflection temperature @ 0.45 MPa for all other materials.
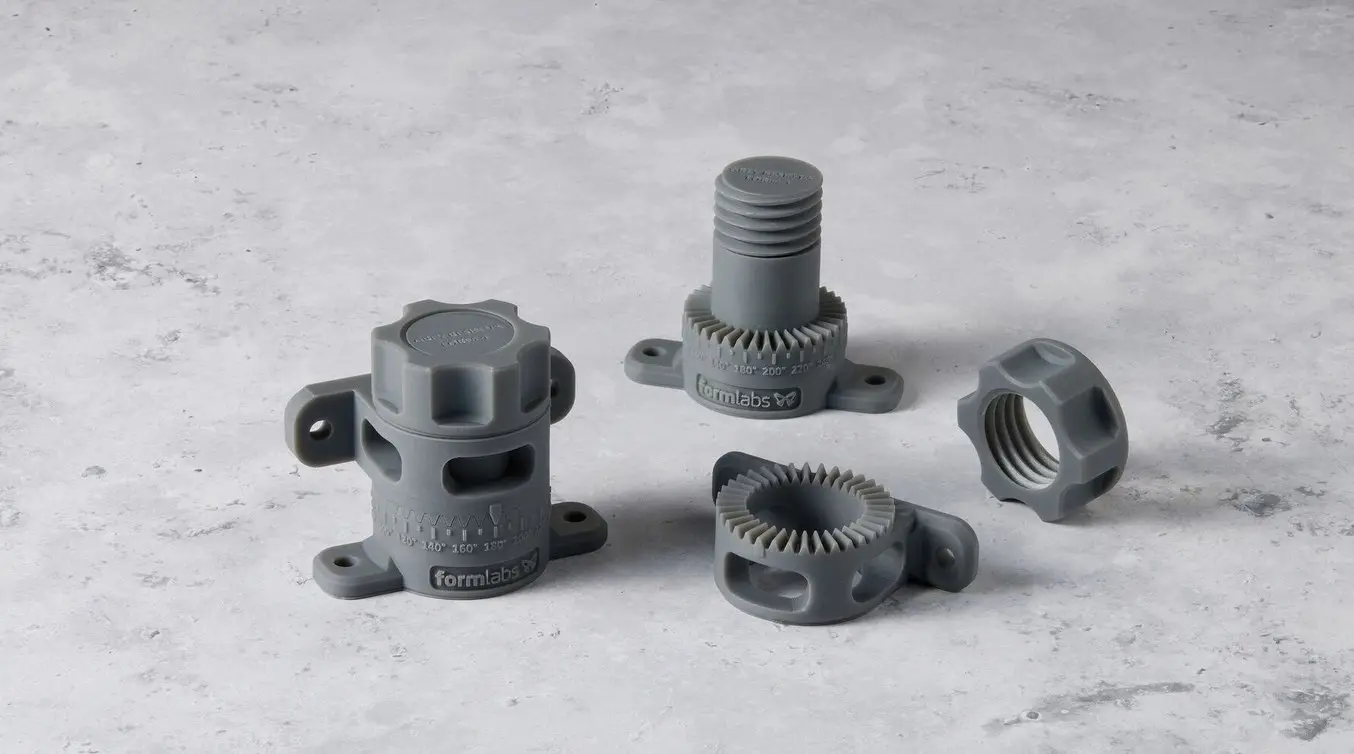
Request a Free Sample Part
See and feel Formlabs quality firsthand. We’ll ship a free SLA sample part to your office.
Heat-Resistant Powders for SLS 3D Printing
Selective laser sintering (SLS) refers to the powder bed fusion 3D printing process where a laser fuses powder particles layer by layer. The unused material supports the parts during printing so you can create complex, interconnecting designs with no need for support structures.
Much like with FDM 3D printing, SLS 3D printing manufacturers offer powders that are familiar and well-understood in the engineering world, such as nylon, polypropylene, and TPU. All SLS materials are heat-resistant, offering some of the best material properties of all plastic 3D printing solutions.
Heat-Resistant Powder 3D Printing: Pros and Cons
SLS 3D printers excel at producing end-use quality parts that have the strength and durability of injection molded goods. The self-supporting nature of the powder bed makes it possible to print parts without supports, enabling quicker post-processing and the possibility of shapes that would be difficult to print with SLA or FDM technology.
SLS ecosystems can often recycle powder, leading to higher efficiency and lower cost per part. SLS printers frequently have larger build volumes than other technologies and the self-supporting nature of the technology allows for printing larger batches of parts, which make it possible to accomplish low- to mid-volume production volumes. The high heat that is used to sinter SLS materials means that finished parts can achieve high temperature resistance.
SLS printers can often be more expensive than FDM or SLA technologies, though accessible options like the Formlabs Fuse Series enable in-house production of heat resistant SLS parts at an affordable price. Printed parts also have a slightly rough surface finish, however, this can be easily improved using post-processing solutions.
Printers for Heat-Resistant SLS 3D Printing
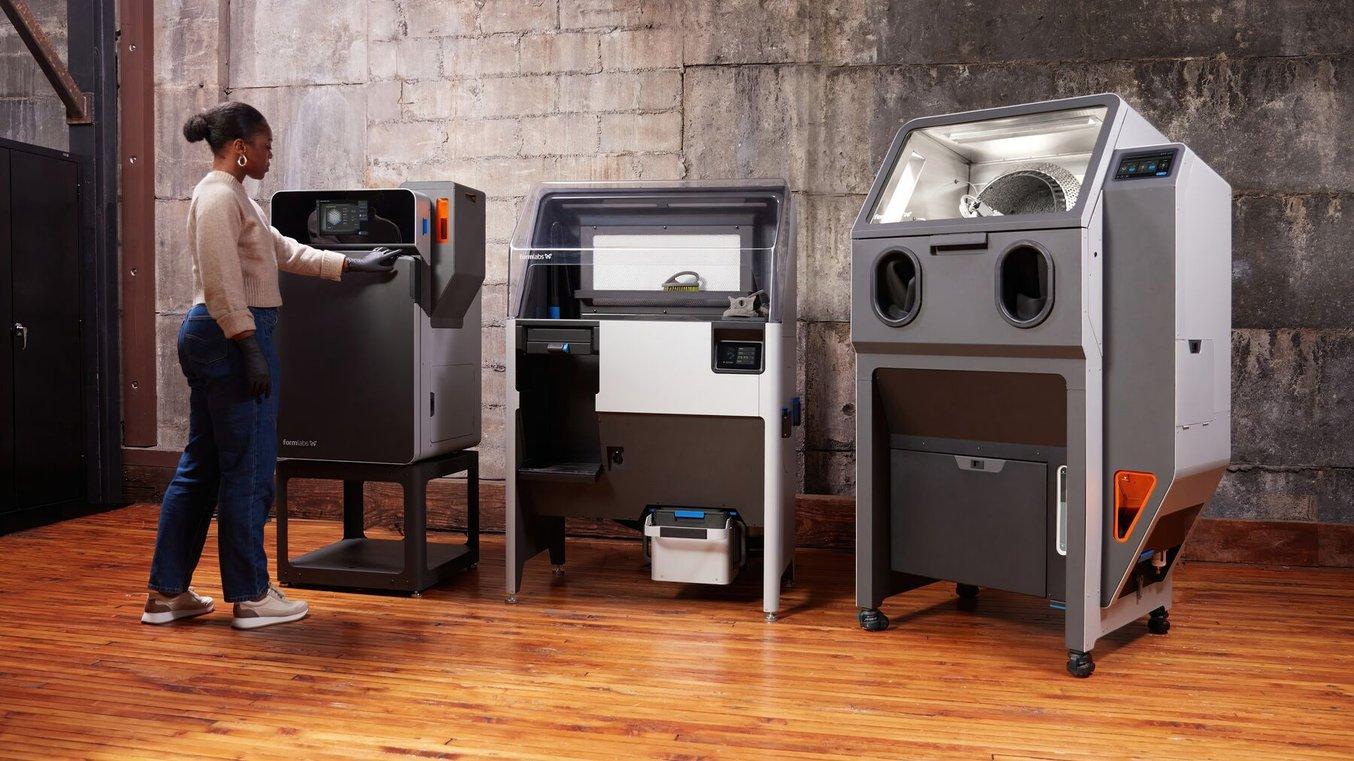
The Fuse Series SLS 3D printer is an affordable, accessible method of producing heat-resistant SLS parts in industry-standard materials like nylon 12 and TPU.
SLS 3D printing powders are naturally heat-resistant, so the options for choosing an SLS printer aren't too limited if the application requires a higher HDT. The go-to material for SLS 3D printing is nylon, while most SLS printer manufacturers offer a range of familiar thermoplastic powders. Because the materials are often common across manufacturers, other features, such as build volume, price, workflow, and infrastructure requirements are typically the differentiating factors when choosing between brands of SLS 3D printer.
The Formlabs Fuse Series introduced an accessible, affordable, benchtop-sized solution for both high-quality prototyping and end-use production. With a range of industry-standard powders available, such as nylon 12, nylon 11, nylon composites, TPU, and polypropylene, it offer many options for producing heat-resistant parts.
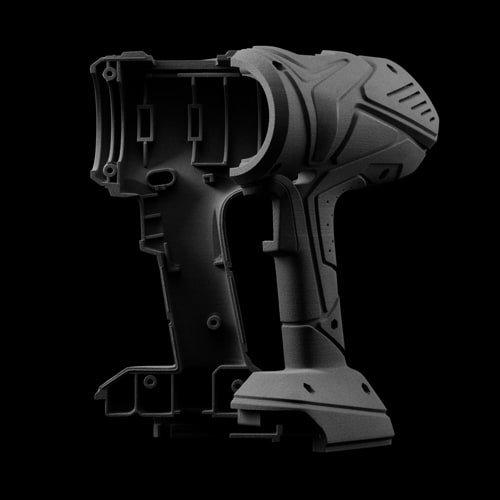
Introduction to Selective Laser Sintering (SLS) 3D Printing
Looking for a 3D printer to create strong, functional parts? Download our white paper to learn how SLS printing works and why it's a popular 3D printing process for functional prototyping and end-use production.
Compare Heat-Resistant SLS Powders
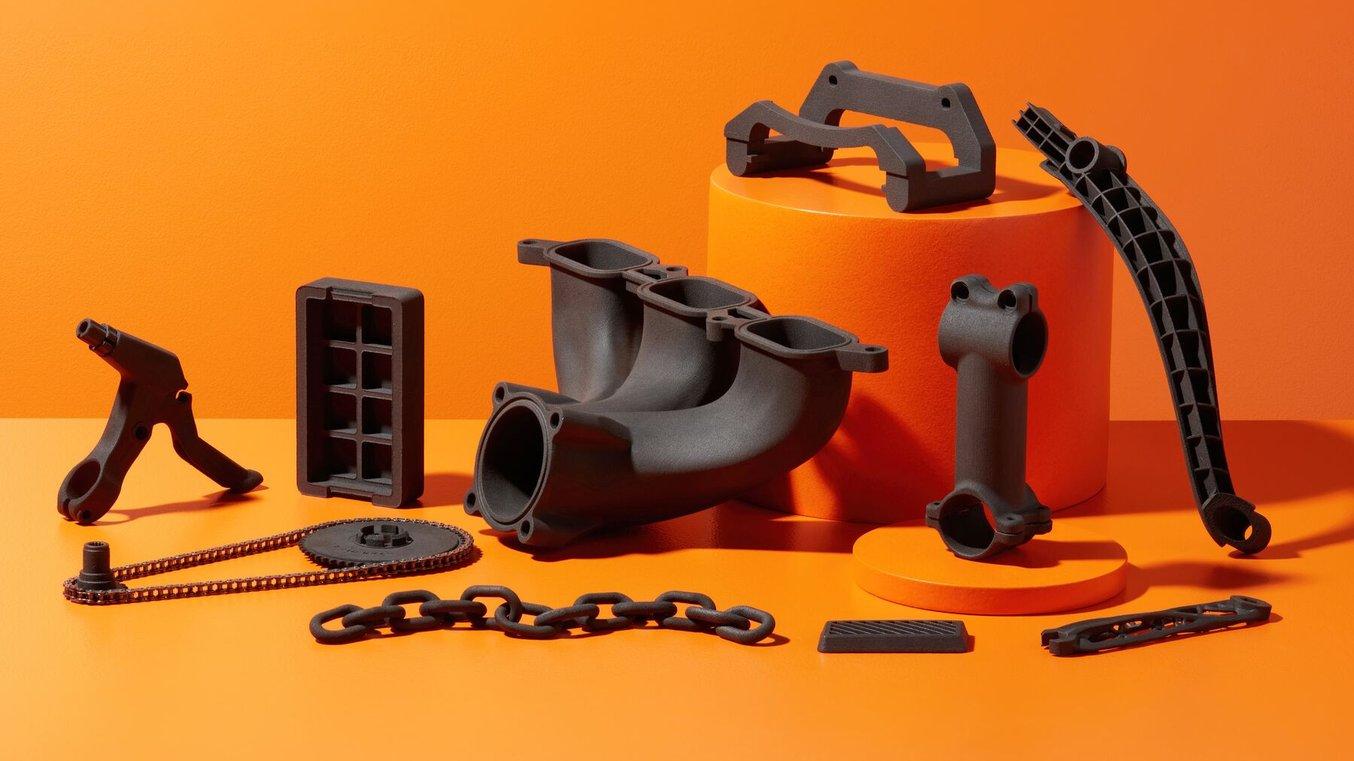
With an HDT of 188 °C at 0.45 MPa, Nylon 11 CF Powder parts are ideal for replacement and spare alternatives to metal parts, high-impact equipment, tooling, jigs, fixtures, and functional composite prototypes.
The most common material for selective laser sintering is nylon, a highly capable engineering thermoplastic that is resistant to UV, light, heat, moisture, solvents, temperature, and water. It is ideal for complex assemblies and durable parts with high environmental stability. It is available in multiple variants and in composite forms, each tailored to different applications. Other popular SLS materials include the ductile polypropylene (PP) and the flexible TPU, both offering good heat-resistant properties.
Nylon 12 Powder
Balancing strength and detail, Nylon 12 Powder is a highly capable material for both functional prototyping and end-use production of complex assemblies and durable parts with high environmental stability. It offers an HDT of 171 °C at 0.45 MPa, making it one of the best general purpose materials for high-temperature applications.
Nylon 12 GF Powder
Nylon 12 GF Powder is a glass-filled material with enhanced stiffness and heat resistance under strain to endure demanding manufacturing conditions. Ideal for applications where structural rigidity and thermal stability are critical, such as high-performance functional prototypes or robust end-use parts that need to maintain dimensional accuracy.
Nylon 11 Powder
Nylon 11 Powder is a ductile and robust material with an HDT of 182 °C at 0.45 MPa. It is suitable for 3D printing heat-resistant parts that need to bend or take impact, for functional prototyping and small batch production.
Nylon 11 CF Powder
Nylon 11 CF Powder is a carbon fiber reinforced powder that is ideal for stiff, strong, lightweight parts that can endure high heat for long-term use. It has an HDT of 188 °C at 0.45 MPa, making it Formlabs' most temperature resistant SLS powder. It is ideal for high-heat applications that require strength and stiffness, such as replacement and spare alternatives to metal parts.
Polypropylene Powder
Polypropylene Powder is a genuine polypropylene (PP) that offers high ductility, allowing for repeated bending and flexing while ensuring durability, without the need for inert atmospheric control. With an HDT of 113 °C at 0.45 MPa, it has a bit lower heat resistance than nylon, but can still produce works-like prototypes and durable end-use parts that are chemically resistant, weldable, and watertight.
TPU 90A Powder
SLS 3D printers can also create flexible TPU parts with unmatched design freedom and ease. Combining the temperature resistance, high tear strength, and elongation at break of rubber materials with the versatility of SLS 3D printing, TPU 90A Powder is ideal for producing flexible, skin-safe prototypes and end-use parts that withstand the demands of everyday use.
Material | Heat Resistance | Ideal For: | |
---|---|---|---|
Nylon 12 Powder | 171 °C | High performance prototyping Small batch manufacturing Permanent jigs, fixtures, and tooling | |
Nylon 12 GF Powder | 170 °C | Robust jigs, fixtures and replacement parts Small batch enclosures and equipment Parts undergoing sustained loading High-temperature applications | |
Nylon 11 Powder | 182 °C | Impact-resistant prototypes, jigs, and fixtures Snaps, clips, and hinges Thin-walled ducts and enclosures Orthotics and prosthetics | |
Nylon 11 CF Powder | 188 °C | Replacement and spare alternatives to metal parts High-impact equipment Tooling, jigs, fixtures Functional composite prototypes | |
Polypropylene Powder | 113 °C | Packaging prototypes, watertight housings, cases Automotive interior components Orthotics and prosthetics Strong and chemically resistant fixtures, tools, and jigs | |
TPU 90A Powder | 94.3 °C | Wearables, orthotics, prosthetics, gaskets, seals, belts, plugs, tubes, padding, dampers |
Note: Heat resistance properties differ as no metric is applicable to all materials. The table shows Vicat softening point for TPU 90A Powder and heat deflection temperature @ 0.45 MPa for all other materials.
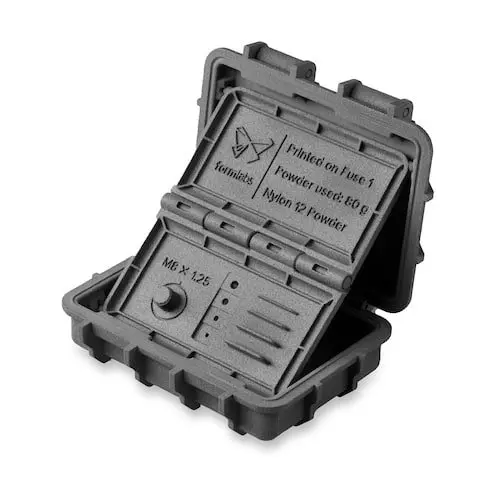
Request a Free Sample Part
See and feel Formlabs SLS quality firsthand. We’ll ship a free SLS sample part to your office.
Metal 3D Printing
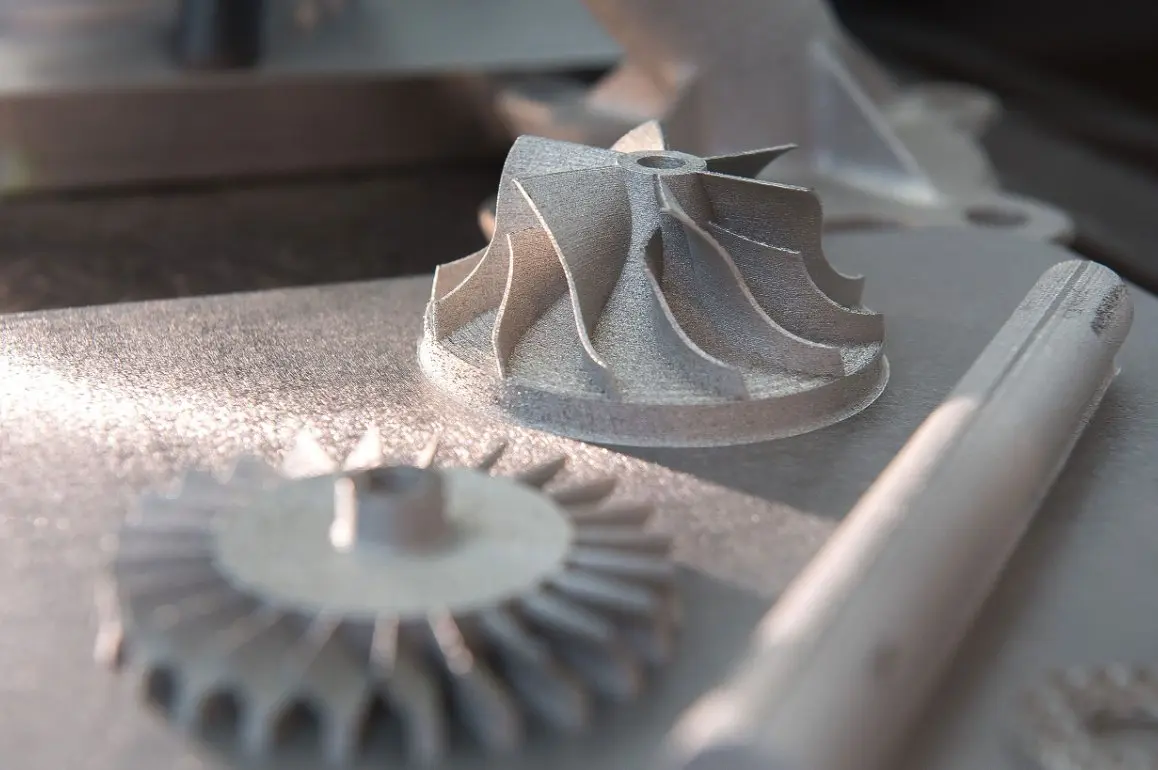
Metal 3D printing has gained popularity as printers have become more accessible, but they're still out of reach for most businesses.
Metal 3D printing is still less accessible, but it is starting to become a possibility for manufacturers, engineers, and product designers. Metal 3D printing offers multiple materials with a temperature resistance above 1000 ºC.
Heat-Resistant Metal 3D Printing: Pros and Cons
Metal 3D printing is valued for its ability to combine the strength, durability, and heat resistance of metal parts with the design freedom of 3D printing. Metal 3D printed parts are sought after for use in the aerospace and automotive industries, where lightweighting parts through generative design can deliver high performance without added weight; something that wouldn’t be possible through traditional machining methods of metal fabrication.
The high power inputs required to manipulate, melt, and/or extrude metal or metal-composite materials mean that these metal printers are often extremely expensive — one model deemed ‘entry-level’ costs upwards of $80,000. Industry leaders in the metal 3D printing space offer machines commonly priced at half a million dollars or more, and require extensive infrastructure to support their processes, like separate rooms and dedicated operators.
Printers for Heat-Resistant Metal 3D Printing
There are fewer metal 3D printer manufacturers than for plastic 3D printing, but the number is growing as the demand increases for workflows that can deliver both the strength and industry-familiar materials of metal parts and the design possibilities of 3D printing.
These manufacturers are grouped into roughly two technologies: extrusion and powder bed fusion. Metal FDM printers work similarly to traditional FDM printers, but use extrude metal rods held together by polymer binders. The finished “green” parts are then sintered in a furnace to remove the binder. Selective laser melting (SLM) and direct metal laser sintering (DMLS) metal 3D printers work similarly to SLS printers, but instead of fusing polymer powders, they fuse metal powder particles together layer by layer using a laser.
Popular Heat-Resistant 3D Printing Metals
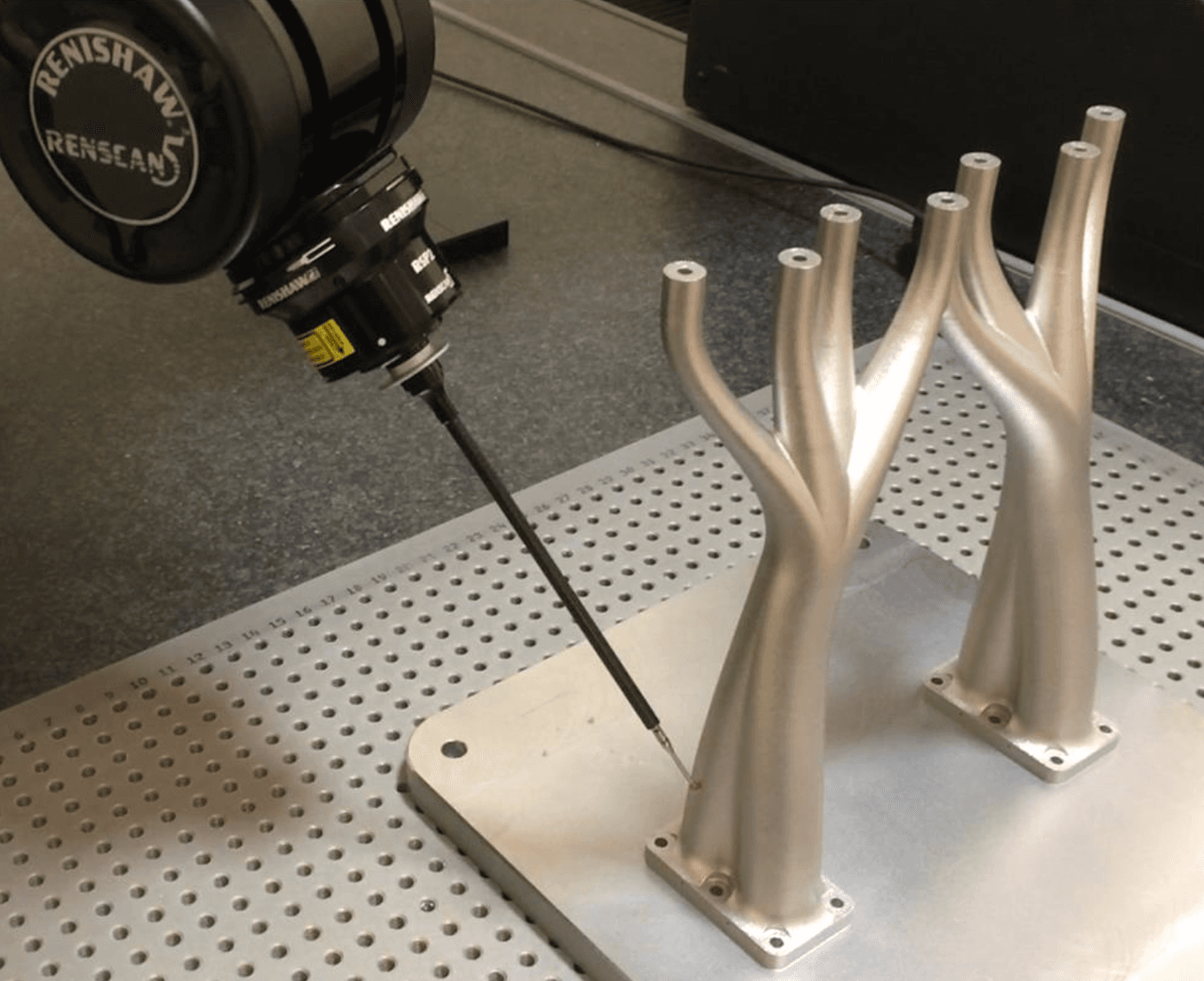
Metal 3D printing materials are familiar to manufacturers, and many 3D printing users are excited about the idea of combining industry-standard metals with the design freedom of 3D printing.
One of the strengths of metal 3D printing is that each material is familiar to customers — whether they start as rods that are melted and bound together, or powder that is sintered into form, metal materials like steel or aluminum are easy recognizable and understood by potential 3D printing users. The most popular materials are the same metals that are found already in aerospace, automotive, industrial, agricultural, and utilities industries.
Titanium
Titanium is a highly temperature-resistant metal and one of the most commonly used alloys in 3D printing. It is resistant to corrosion and has light weight in relation to its strength.
Stainless Steel
Stainless steel is a well-known material that is used in many easily visible architecture, design, automotive, and aerospace applications. 3D printing stainless steel can be useful for one-off replacement parts for applications like manufacturing, where traditional fabrication methods might take weeks, or for remote locations such as naval ships printing parts while at sea. The melt point of stainless steel changes based on the exact formulation of the material, which is a composite, but ranges between 1370 °C to 1530 °C.
Aluminum
Aluminum is a popular material for lightweight parts with low density. With a melt point of 660 °C, it is on the lower end of heat-resistant for metal 3D printing materials.
Material | Heat Resistance | Ideal For: |
---|---|---|
Titanium | 1,668 °C | Corrosion-resistant fixtures, jigs, and end-use enclosures |
Stainless Steel | 1370°C to 1530 °C | On-demand manufacturing of aerospace, naval, and manufacturing parts |
Aluminum | 660 °C | Lightweight parts, turbine blades, drone components |
Note: Heat resistance refers to melting point for all materials.
Heat-Resistance in 3D Printing
As industries like aerospace engineering and automotive manufacturing increase adoption of 3D printing technology, heat-resistant materials are increasingly in high demand. The geometric flexibility, design freedom, and rapid iterative cycles of 3D printed parts mean that companies can reduce costs while pushing the boundaries of part performance.
Plastic and metal 3D printing process offer a wide range of heat-resistant 3D printing materials — some are familiar, like nylon and metal powders like aluminum or titanium, and some are unique to the 3D printing world. Each technology and material has unique benefits, and some are suited better for certain applications.
To learn more about which 3D printing technology and material is right for your application, contact our experts. To explore Formlabs’ range of heat-resistant materials, visit our materials catalog.