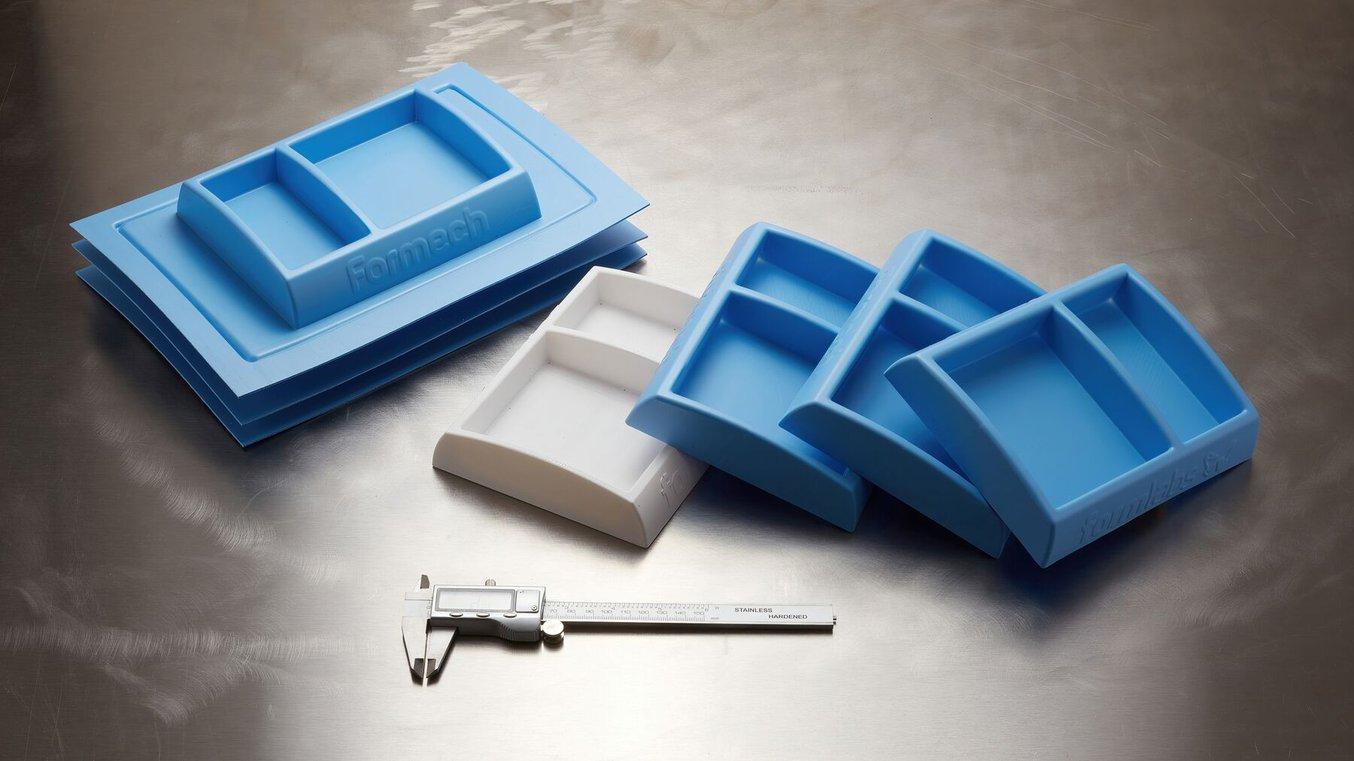
The Formlabs engineering team is pleased to announce that we can now recommend media blasting to further improve mechanical properties of Rigid 10K Resin, one of the most popular and versatile members of our Engineering Resins for Formlabs stereolithography (SLA) 3D printers.
After extensive research and testing, we’ve discovered that media blasting Rigid 10K Resin increased material strength across every metric: tensile, flexural, and impact testing. Test specimens were media blasted with 70-140 mesh glass beads on all surfaces at an air pressure of 90 psi.
Metric | UV Cure* | UV+Thermal Cure* | UV Cure + Media Blast | % Change From Blast |
---|---|---|---|---|
Tensile Modulus (GPa) | 10 | 10 | 11 | 10% |
Ultimate Tensile Strength (MPa) | 65 | 53 | 88 | 35% |
Elongation at Break (%) | 1 | 1 | 1.7 | 70% |
Flexural Modulus (GPa) | 9 | 10 | 9.93 | 10% |
Flexural Modulus (MPa) | 126 | 103 | 158 | 25% |
Notched Impact Strength (J/m) | 16 | 18 | 20 | 25% |
Unnotched Impact Strength | 47 | 41 | 130 | 180% |
Media blasting leads to stronger parts, boosting performance across a wide range of applications which currently deploy the use of Rigid 10K Resin. Users can expect to get more shots out of their thermoforming and injection molding prints, parts that can withstand higher external forces, and objects that are less likely to break.
For consistent blasting results, Formlabs' Fuse Blast is an automated media blasting solution that can replace a standard media blasting cabinet, eliminating labor and also offering an ergonomic manual mode for delicate parts.
Rigid 10K Resin Applications
Businesses around the world have already been using Rigid 10K Resin in various applications. Now, with the addition of media blasting, these applications will last longer and perform at a higher level. Let’s examine a few ways Rigid 10K Resin is being used.
In-House 3D Printing For Injection Molding
In-house injection molding has completely changed the way many businesses solve problems. It allows businesses to accelerate product development, reduce costs and lead times, and bring better products to market by incorporating 3D printing and short-run injection molding into the development process. While Formlabs offers multiple materials that can be used for injection molding, such as Grey Pro Resin and High Temp Resin, Rigid 10K Resin is often the preferred solution depending on the design and requirements of your mold.
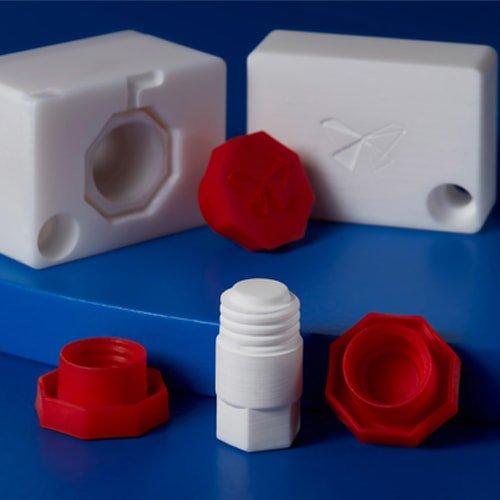
Low-Volume Rapid Injection Molding With 3D Printed Molds
Download our white paper for guidelines for using 3D printed molds in the injection molding process to lower costs and lead time and see real-life case studies with Braskem, Holimaker, and Novus Applications.
Novus Applications, a product development company focused on consumer goods, has incorporated in-house injection molding into their prototyping process, reducing their reliance on costly and time-consuming outsourced injection molds, while still producing high-quality and repeatable parts. By 3D printing injection molds using Formlabs’ Rigid 10K Resin, Novus was able to fabricate high-quality and repeatable prototypes, saving costs and cutting lead time by several days.
Multiplus runs a China-based micro injection molding workshop which offers solutions that cover the entire production cycle, from design to manufacturing of plastic products, both large and small, single or multi-shot (where two or more colors or materials are injection molded simultaneously into a single mold). Today, Multiplus provides services to over 250 clients per year, including some Fortune 500 companies.
“Not many 3D printed materials can withstand the repeated pressure, heating, and cooling during the injection molding process. Our experience is that even with a material claimed to withstand high temperatures, the printed mold might be able to withstand 10-20 injection cycles but would crack shortly after that, or the quality degrades so that the finished part becomes undesirable. The first batch we produced with the Rigid 10K mold produced 100 parts with no issues,” said Mr. Lin Wei, Multiplus’ injection molding department manager.
In-House 3D Printing Thermoforming
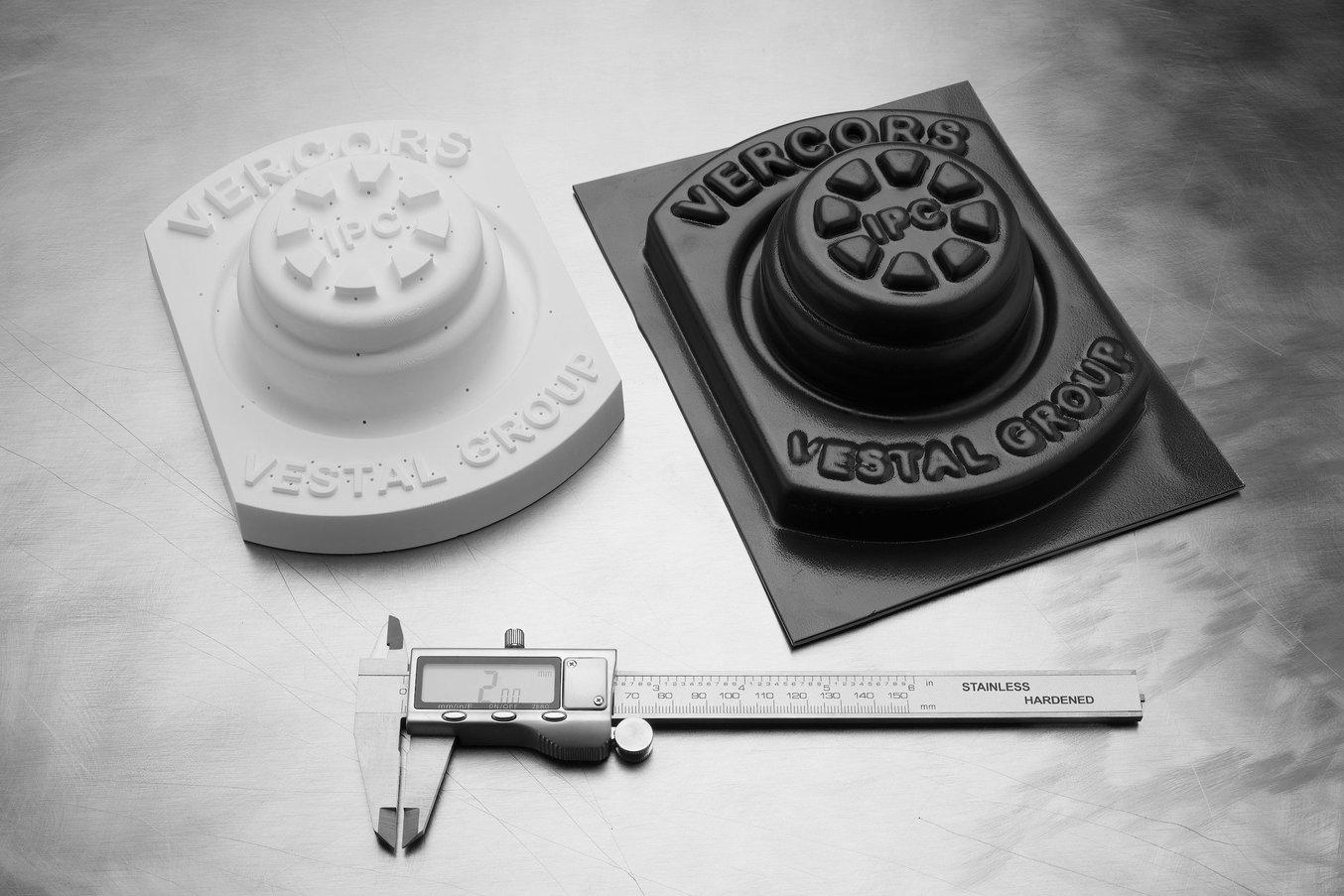
Rigid 10K Resin is the perfect choice for in-house thermoforming, due to its ability to create industrial quality parts which can withstand significant load without bending. Its smooth finish and high resistance to heat means users will get dozens of presses—sometimes up to 50 cycles—out of a single print.
Traditionally, thermoforming tools—also referred to as molds, forms, or bucks—are fabricated by CNC machined metal for large production, or wood or composite board (foam or fiberglass) for smaller batches. Desktop 3D printing is a powerful solution to fabricate tools rapidly and at a low cost. It requires minimal equipment, saving CNC time and freeing up skilled operators for other high-value tasks. With in-house 3D printing, manufacturers and product designers can introduce rapid tooling into the product development process to validate design and material choices prior to transitioning to mass production. They can iterate quickly, accelerate product development and bring better products to market.
A study by the industrial technical center IPC demonstrated that molds 3D printed with Formlabs Rigid 10K Resin are able to thermoform thick PS sheets, for up to 20 to 50 cycles. Incorporating cooling channels in the mold design increases the mold longevity while maintaining a reasonable cycle time for low to medium production. Lead times are three to seven times shorter than with traditional tooling, and costs are cut at least in half.
Heat-Resistant End Use Parts
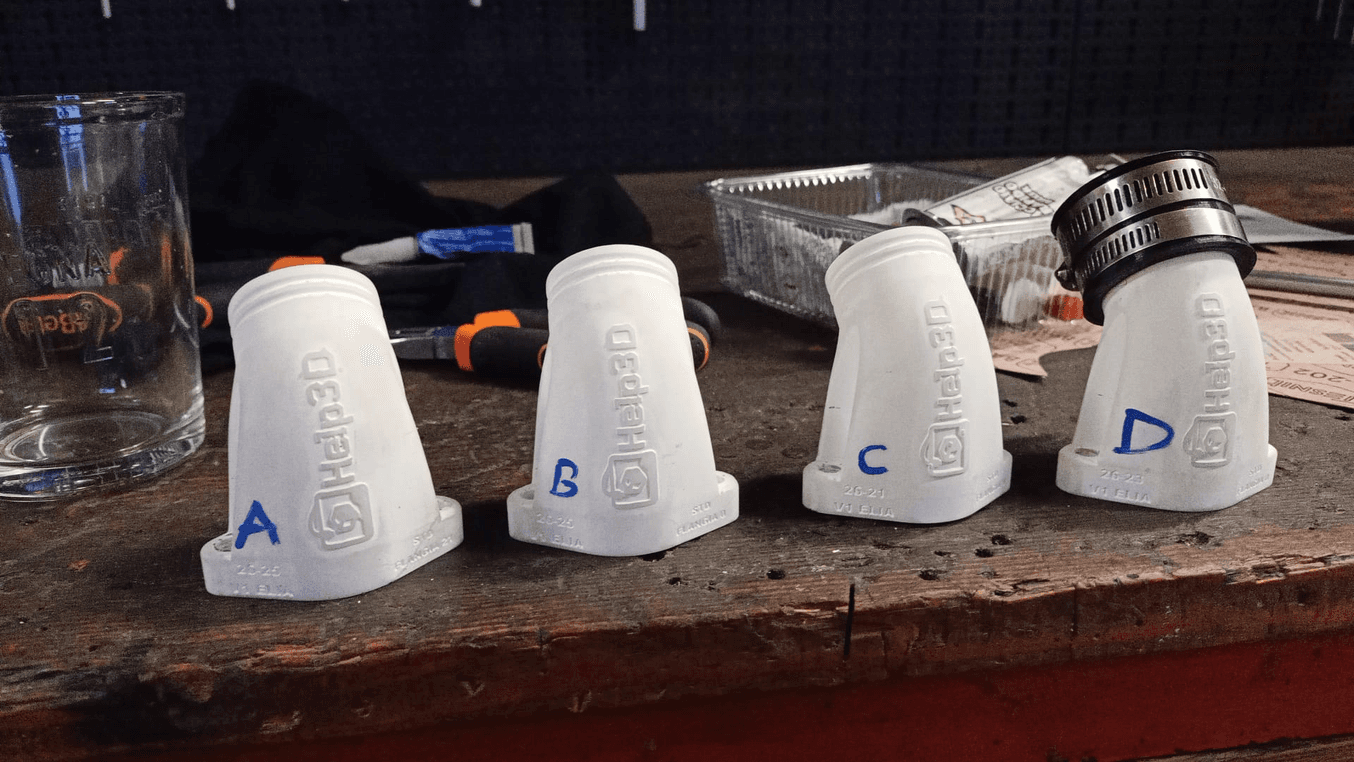
Different versions of the intake manifolds printed with the Form 3.
In-house 3D printing is empowering small businesses to design their products, replacement parts, modifications and more. When Andrea Pirazzini, the founder of Help3D, first saw Rigid 10K Resin, he wanted to see if he could create his own intake manifold for a pit bike that he was to ride at the 12 Pollici Italian Cup championship.
The new manifold design was printed with a Formlabs SLA 3D printer using the Rigid 10K Resin at a 100 microns layer height, creating a smooth surface without visible layer lines. For the finish, Pirazzini used classic water-based sandpaper to smooth the surface. Unlike an FDM manifold, which has to be treated externally and internally to be watertight, SLA printing creates solid and waterproof parts.
Texas A&M Wind Tunnel
Lisa Brown, manager and engineer at the Texas A&M Wind Tunnel, helps customers develop their test plans, design the models, and create the code that helps them collect relevant data. Brown and her team sought out Formlabs’ Rigid 10K Resin for replacing pieces on a NASA aircraft model test.
“We could directly compare the FDM to the Formlabs prints. That was a first big eye opener for us, is that the big difference in surface quality between the two. So we started there and then we started printing some parts that would replace the metal pieces that we had made. And so that was an interesting comparison as well, to see how close a printed version could approximate the metal tail surface that we had made here,” Brown said.
Get Stronger, Better Engineering Parts with Rigid 10K Resin.
With today’s news, Rigid 10K Resin is ready to be used for high-performance heat-resistant end use parts, thermoforming, injection molding, and more.
With an affordable and easy-to-use 3D printing platform like Formlabs, these high-quality results are within reach for businesses of any size, from Help3D to Multiplus. Buy Rigid 10K Resin today, or request a free sample part below.