Novus Applications Fabricates Injection Molded Prototypes With Rigid 10K Resin Molds
Injection molding is a common and versatile manufacturing process used to produce a high volume of parts. Used in manufacturing processes for home appliances, electronics, automotive, and more, many manufacturers turn to injection molding to achieve precise, repeatable parts. Mold fabrication can be expensive and time consuming. With high upfront equipment costs, machining molds can be cumbersome, but this cost is often absorbed over the hundreds of thousands of final parts that are produced. For smaller part quantities though, the cost, time, specialized equipment, and skilled labor required to fabricate the mold out of common tooling metals and with common manufacturing methods introduces barriers to the process, often making injection molding at this scale unobtainable for many companies. However, there are alternatives to machining molds out of metal.
Novus Applications, a product development company focused on consumer goods, takes injection molding to the next level by incorporating 3D printing into the workflow to speed up the process, enabling an agile manufacturing approach. By leveraging 3D printing to fabricate injection molds for prototype parts, Novus significantly reduced these barriers compared to metal molds, while still producing high-quality and repeatable parts. By 3D printing injection molds using Formlabs’ Rigid 10K Resin, Novus was able to fabricate high-quality and repeatable prototypes, saving costs and cutting lead time by several days.
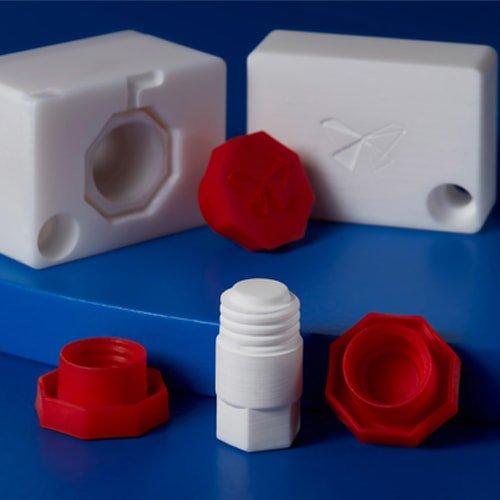
Low-Volume Rapid Injection Molding With 3D Printed Molds
Download our white paper for guidelines for using 3D printed molds in the injection molding process to lower costs and lead time and see real-life case studies with Braskem, Holimaker, and Novus Applications.
Novus Sees High Demand for Injection Molding
Novus has a far reach, working with some of the largest brands in the personal care, homecare, and oral care sectors. They complete designs for the manufacturer, conduct moldability studies, prototype and iterate quickly, 3D print parts and components, and produce small scale prototypes so that their customers can test their products. Novus focuses on injection molded plastics and the use of those plastic parts in consumer assemblies.
From medical companies to major brands like Colgate and Liquiglide, injection molded parts are in high demand. Novus honed their craft with years of experience.
“Injection molding is inherently demanding from a precision standpoint and an experience standpoint. So to be a good injection molder, you have to have a lot of experience in it. To walk in and mold well without much experience, there's a lot of trial by error and frustration and a lot of unknowns unless you understand what you're looking at,” said Mark Bartlett, president and founder of Novus.
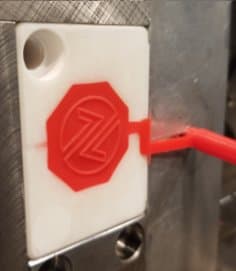
The mold cavity after the injection of P5M6K-048 Red (left) and PP1013H1 White (right) materials.
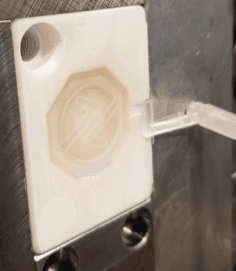
How to Leverage 3D Printing in the Injection Molding Workflow
By 3D printing, Novus can eschew high-end software and machining processes, saving time on labor. As a result, the process is more automated. Formlabs’ complete, easy-to-use ecosystem makes it simple to get started with 3D printing injection molds.
“The production of those parts is in an unattended fashion. I don't need a highly experienced individual, although I do need a person with experience and 3D printing. So the learning curve is faster. The production is far more unattended,” Bartlett said.
Novus produces a lot of caps and closures. The company needed to produce a lot of small series of prototypes, requiring a fast method of production. Bartlett said that rapidly prototyping a cap in a 3D printed mold set helped streamline their workflow.
How Rigid 10K Resin Enabled Novus to Design Faster
Selecting the right 3D printing material for the mold is critical for success. Rigid 10K Resin’s combination of strength, stiffness, and thermal resistance makes it ideal for short-run injection molds. Novus needed to quickly produce a lot of small series of prototypes.
Accuracy is key in injection molding, making part quality critical. Novus needed a material capable of bearing the high heat and pressure of this process while rendering small features. In particular, the threaded core was a delicate part. The advanced strength ensures the mold made from Rigid 10K Resin could withstand the clamping and injection pressures without breaking, while the high stiffness enabled the mold to maintain its shape under these pressures and produce accurate parts. Thanks to this set of properties, they were able to inject hundreds of parts of polypropylene and polyethylene with just one mold without breakage.
Not only did Rigid 10K Resin exhibit good dimensional stability, but it was also faster and easier to print compared to milling aluminum and steel. “How does it handle the pressures and temperatures in the materials we were running? It performed excellent...it was performing at a level that we hadn't seen historically capable in the traditional [Rigid 4000] material,” Bartlett said.
Novus went though one iteration to reach the final design and was able to save on time. “I can print complex forms accurately, way faster than I'm going to machine them,” he said. Though Bartlett did not anticipate achieving completely perfect parts, Novus didn’t have to adjust molding surfaces, they only groomed the outside of the stacks. “Once we got at the mold, we ran it. And then we inspected the molded plastic parts and we were surprisingly accurate for not having done any iterations. We did one print, one run, and it worked great,” Bartlett said.
In the end, Novus was able to leverage 3D printed injection molds to quickly and affordably prototype designs for their clients with end-use materials and manufacturing methods. They were able to print the mold, test the design and material, and modify the part within the same day to iterate quickly and help their customers bring better products to market.
Download our free white paper or watch the webinar for a detailed process workflow, design guidelines, and other best practices for using 3D printed molds in the injection molding process and see additional real-life case studies with Braskem, Holimaker, and Multiplus.