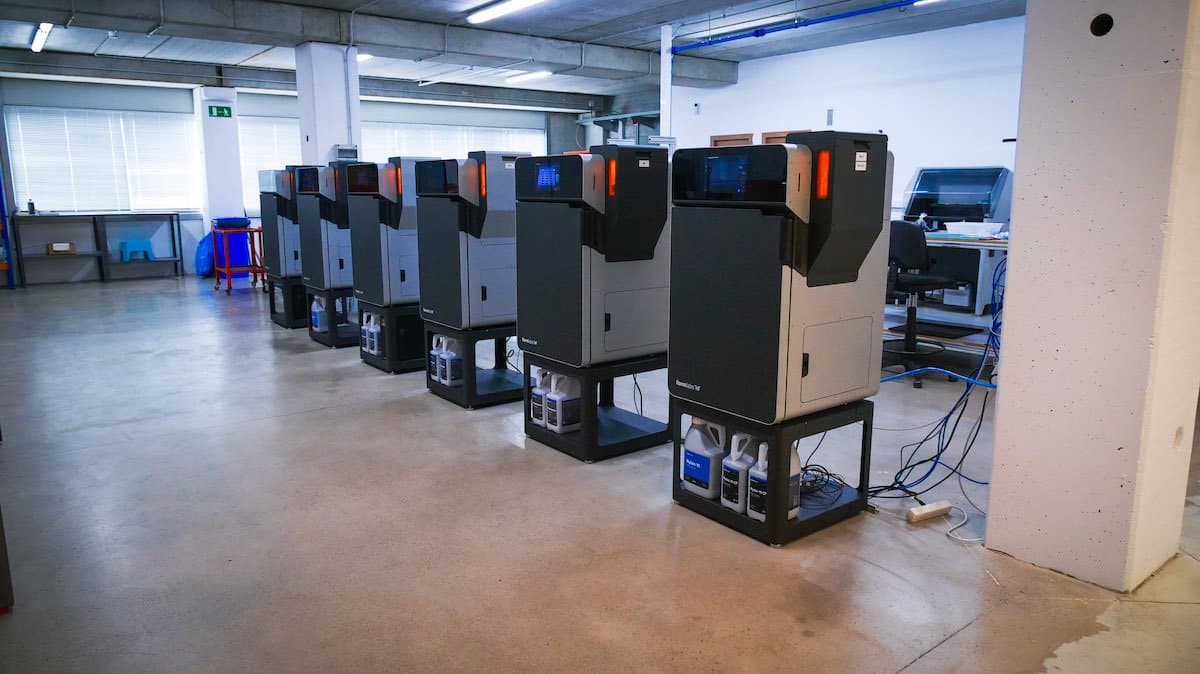
“I think 3D printing is the future,” says Albert Marti, owner of WLD, a contract manufacturer and service bureau outside Barcelona. Marti’s father owned a machine manufacturing company for decades, and though Marti now works with similar customers as his father did, he’s grown his business by investing in additive — rather than subtractive — manufacturing.
WLD currently provides services from design and early prototypes to production runs of thousands of end-use parts. To keep multiple projects running smoothly, maintain high-quality parts, and deliver on tight timelines, WLD relies on both stereolithography (SLA) and selective laser sintering (SLS) technologies. WLD leverages the speed and surface finish of Form 4, the large-format size of Form 3L, and the high-volume capacity and geometric freedom of six Fuse 1+ 30W 3D printers.
By building an agile fleet of Fuse Series printers, WLD has distinguished itself from competitors — they can offer each of Formlabs’ six SLS Powders — while the competition can only offer one traditional nylon material. “The Formlabs 3D printers can do so many things, and it’s a good company to work with,” Marti says. Together with Formlabs partner SICNOVA, Marti has built a business that stands out from his competition. WLD has been able to continuously scale by bringing new technologies in-house and expanding the range of materials their customers can access.
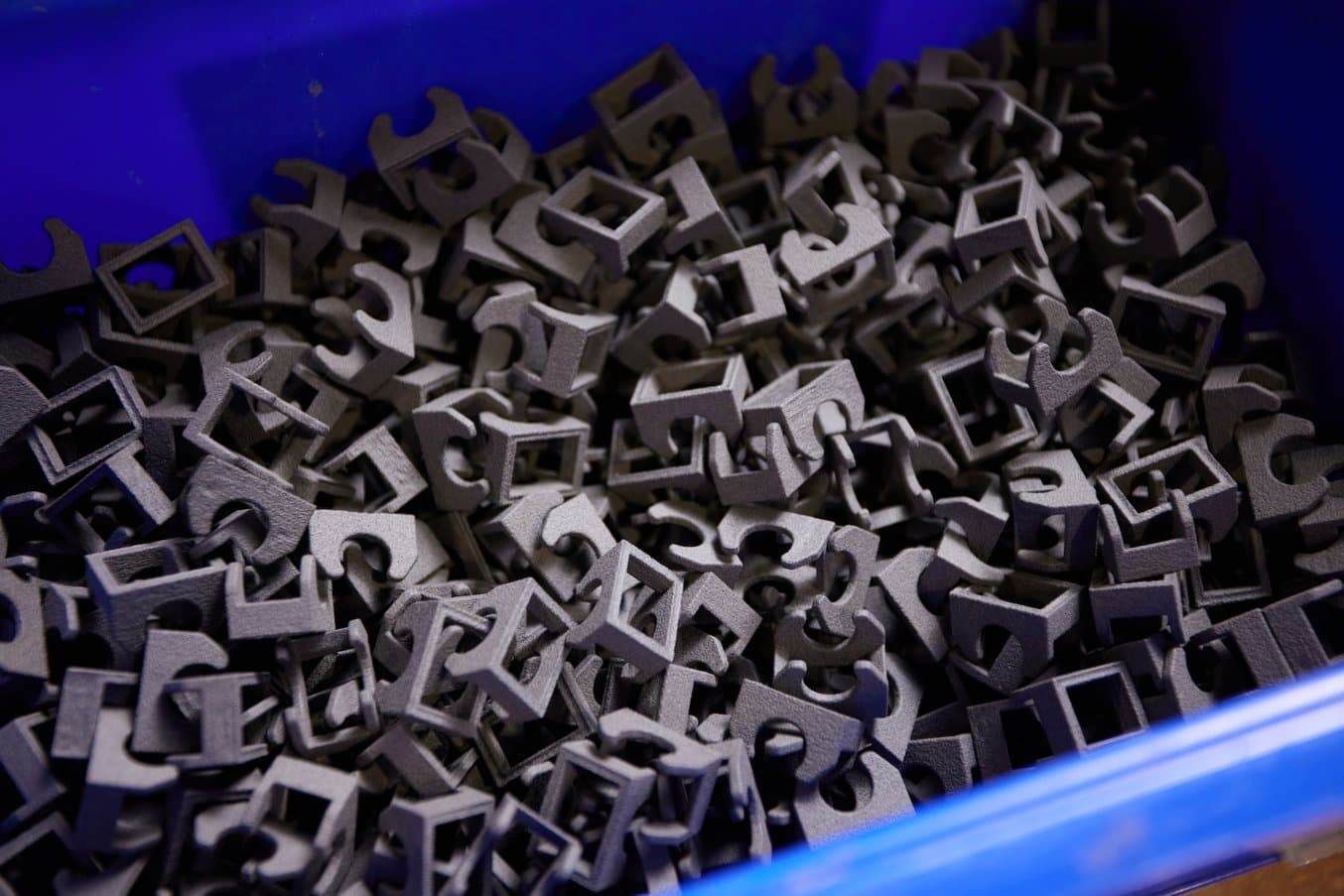
SLS for End-Use Production
3D printing for end-use production is not only possible, it's more affordable, agile, and scalable than ever with the Fuse SLS Ecosystem. Visit our SLS for Production page to compare production methods, learn about bulk powder pricing, and see production in action for 15 different manufacturers currently using the Fuse Series.
Starting With SLA, Scaling to Multi-Material SLS
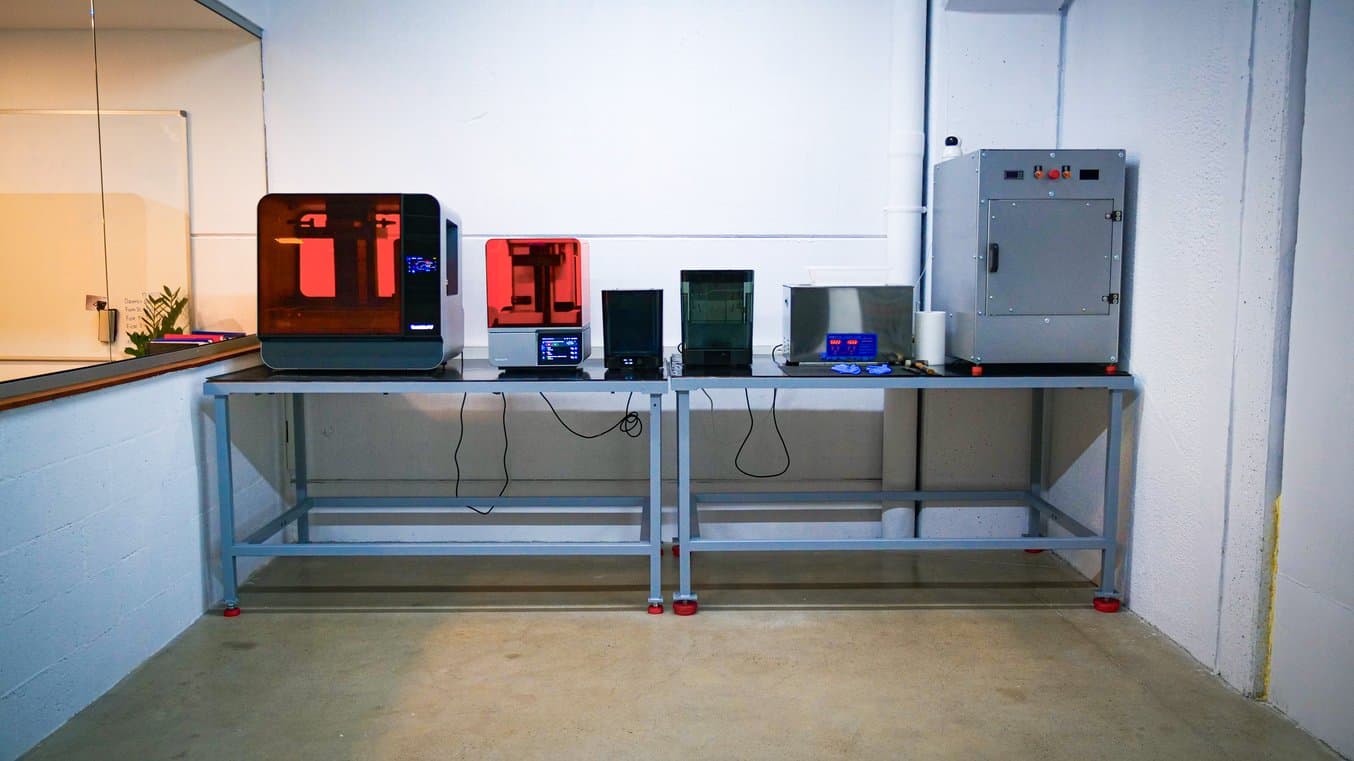
Marti started with the Form 3L, then added Form 4 along with the fleet of Fuse Series SLS printers.
In 2021, Marti was working as a private contractor for industrial manufacturers, helping them with CAD work and equipment programming. When he purchased a Form 3L, he started using SLA 3D printed parts in small projects for clients, and the business grew from there. “I had a really good relationship with my customers after showing them the Form 3L prototypes, and quickly realized I needed a solution for final-stage parts – I realized there was tremendous opportunity for growth in this part of the market,” says Marti.
His belief in market demand was backed up by the current competitive landscape — service bureaus in Spain were all using HP MJF printers and producing steady volumes of nylon parts for their customers. Marti knew that to keep his business agile, responsive, and competitive against entrenched competition, he needed to offer something more.
WLD purchased their first Fuse 1+ 30W printer and Fuse Sift for Nylon 12 Powder, and immediately began fulfilling orders.
“Our first prints on the Fuse went very well and lived up to expectations. I had a lot of support from SICNOVA right from the start, and that made producing the first round of orders easy. Though it took a while to consolidate a bigger customer base, I noticed that after printing SLS parts for them, customers always came back for more — which I took to be a good sign.”
Albert Marti, Owner, WLD
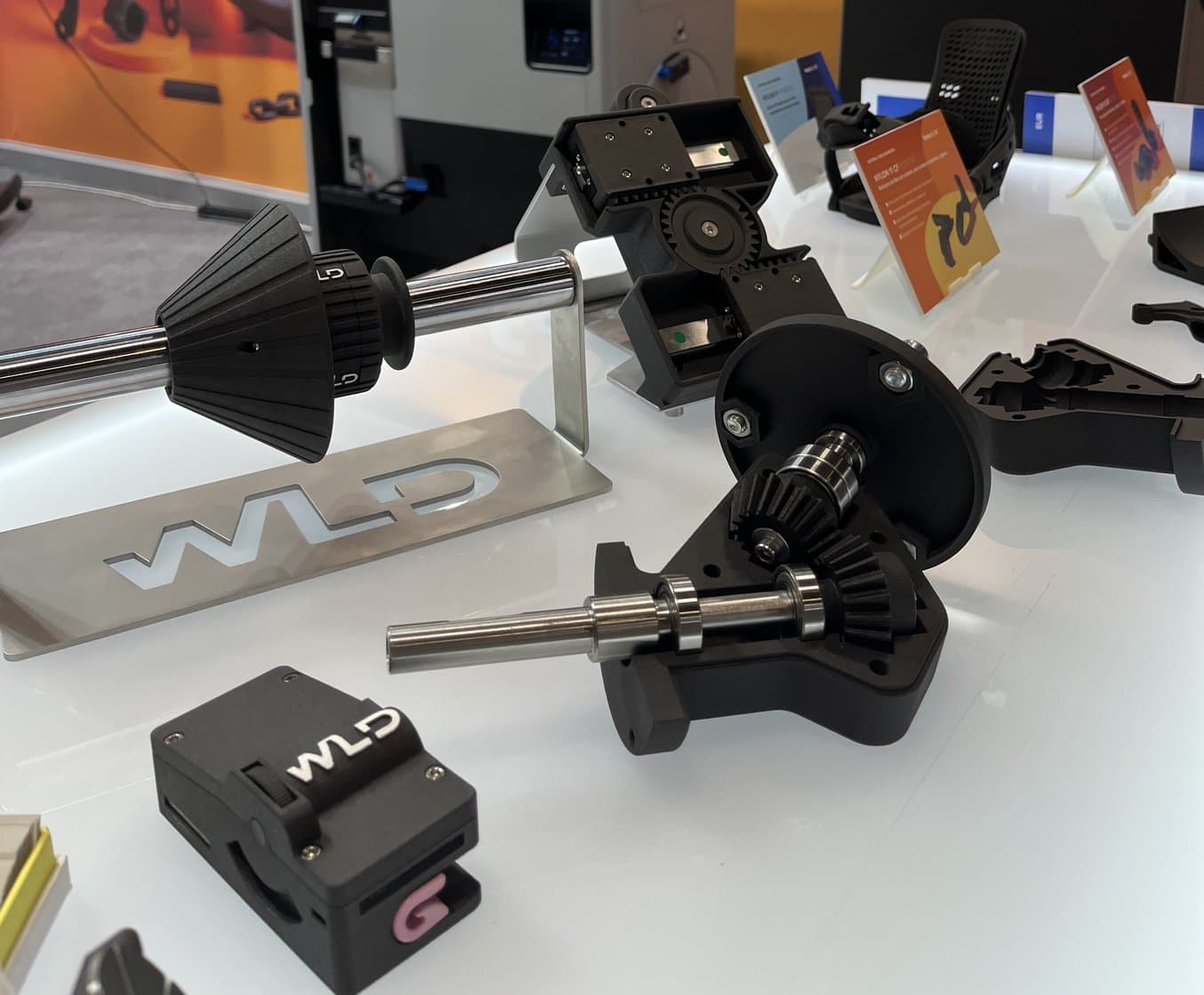
Once Marti started providing SLS parts to his customers, their orders increased and he was able to build up a consistent volume of SLS part requests.
Because WLD had built relationships with businesses in the insoles industry and machinery manufacturing industry, the market for end-use SLS parts was already there. Marti was finally able to fulfill requests for functional machinery replacement parts and customized insoles with SLS 3D printing.
With such immediate success, Marti could start scaling. He purchased a second Fuse 1+ 30W printer to match the volume of Nylon 12 Powder orders, and then added four more, so that he could offer each Formlabs SLS Powder. “This is the biggest advantage with Fuse, I can differentiate from the competition who are only offering PA12 powders,” says Marti.
Making a Six Powder Workflow Easy and Cost-Effective
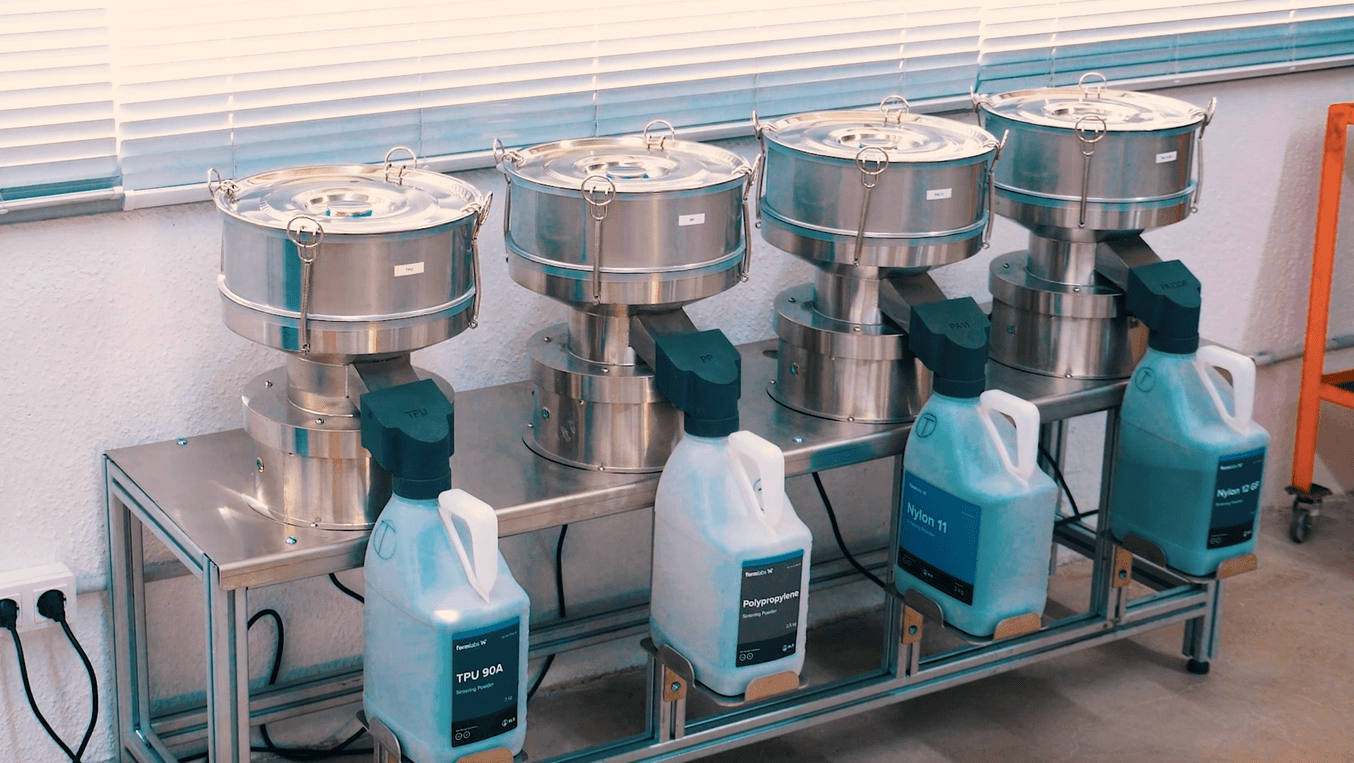
WLD recycles their Nylon 12 Powder using the Fuse Sift, but uses these powder mixing solutions to recycle their other powders after removing unsintered powder from parts with the Fuse Depowdering Kit.
To effectively manage a fleet of six SLS printers and two SLA printers, Marti relies on print preparation and queue management through PreForm and Dashboard, as well as the Fuse Sift and Fuse Blast SLS post-processing machines. Access to the complete ecosystem, from software to post-processing, was one of the attractive features of the Formlabs workflow for Marti. “Another big advantage is that the Fuse is easy to use. The interface and the PreForm software are easy — they update the program consistently to improve the performance of the printers,” says Marti.
Marti has assigned two Fuse Series printers to Nylon 12 Powder to accommodate the larger number of orders he gets for that material. The four remaining SLS printers are assigned to Nylon 12 GF Powder (popular for automotive applications), TPU 90A Powder, and Polypropylene Powder, and one printer switching between Nylon 11 Powder and Nylon 11 CF Powder.
The printers are constantly running, and along with Marti, two technicians remove build chambers each morning, run builds through the Fuse Sift for Nylon 12 Powder or Fuse Depowdering Kit for the other materials, insert new chambers to start the next day’s print, and run every type of powder through the Fuse Blast. The Fuse Depowdering Kit has allowed Marti to add new materials (and thus new income streams) for only about $30,000. To add another material with a large-format industrial printer like an HP would cost more than $200,000.
To ensure production isn’t held up by any issues, Marti works with Formlabs’ and Sicnova’s services team. “The services, too, are fast. If there’s something wrong, the response time is very fast — it’s very reassuring. I know I’ll get the help very quickly, which makes me feel confident,” says Marti.
Hardware Required to 3D Print With Six Different SLS Powders
Fuse Series | Large-Format Industrial SLS/MJF | |
---|---|---|
Printer install | 6x Fuse 1+ 30W SLS 3D printers | 6 x Large-Format industrial SLS or MJF machines |
Post-Processing needs | 1x Fuse Sift, 1 x Fuse Blast, 5 Fuse Depowdering Kits | 6 x each type of post-processing machine |
Cost | $200,000 | $1.2-2.4 million |
High-Volume Production Printing With SLS
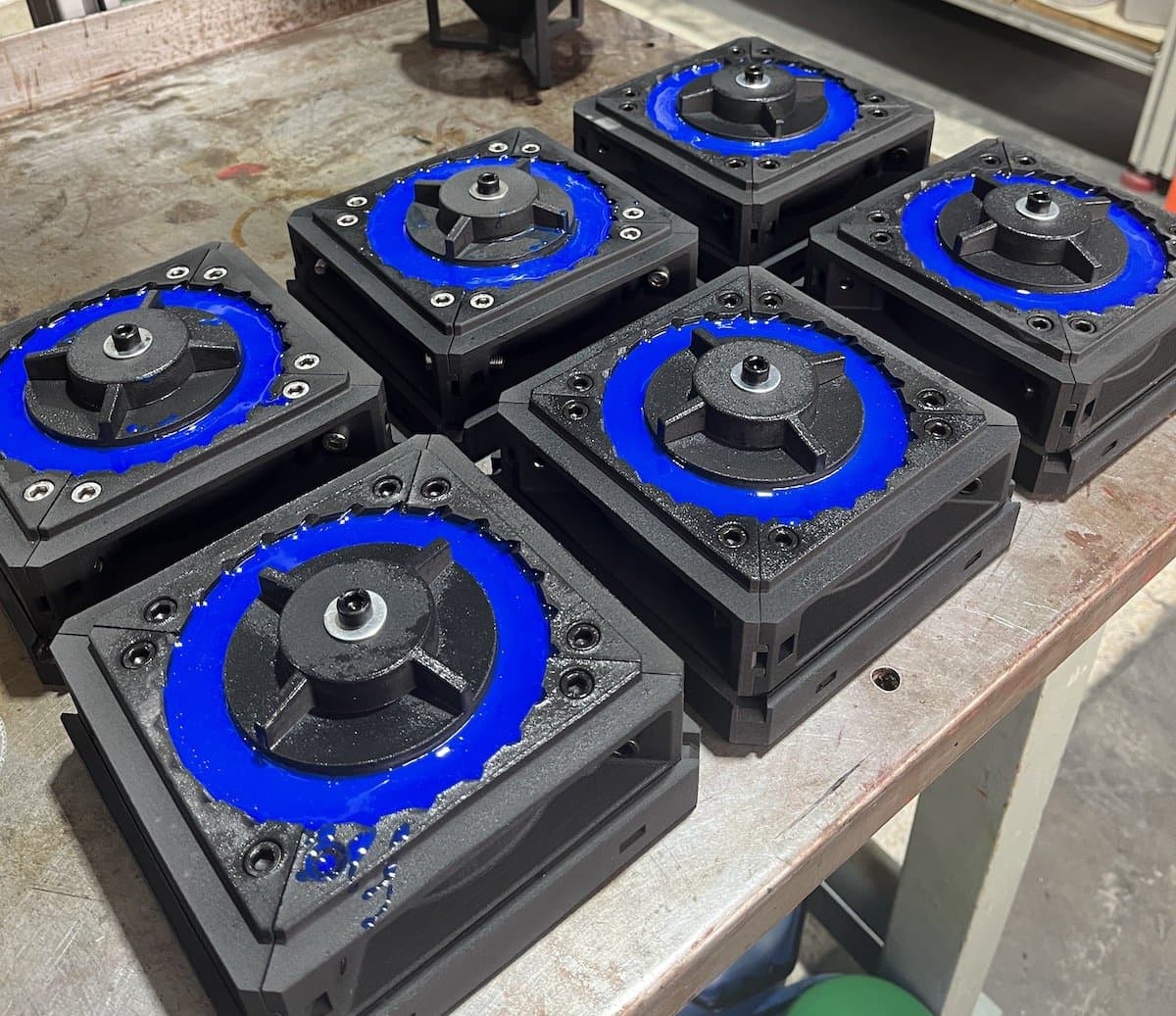
Even large parts like these polyurethane molds for robotic wheels are easy for the Fuse Series. The Fuse 1+ 30W can handle the size and accuracy requirements necessary for this type of rapid tooling.
Marti has a range of customer orders — some businesses need quick, one-off prototypes. Others have standing orders for 1000 parts each month. One project, a wheel for a robotic system that cleans solar panels designed by Marti with an SLS spoke system and a polyurethane covering, requires 500 units a month of production in Nylon 12 Powder.
To handle this much volume, Marti purchases between 100 and 150 kilograms a month of SLS Powders. The bulk powder discounting tiers available for production customers as well as ecosystem tools like the Fuse Blast help him drive down cost per part. “The Fuse Ecosystem is reasonably priced for small and medium manufacturers, and gives you very good results,” says Marti.
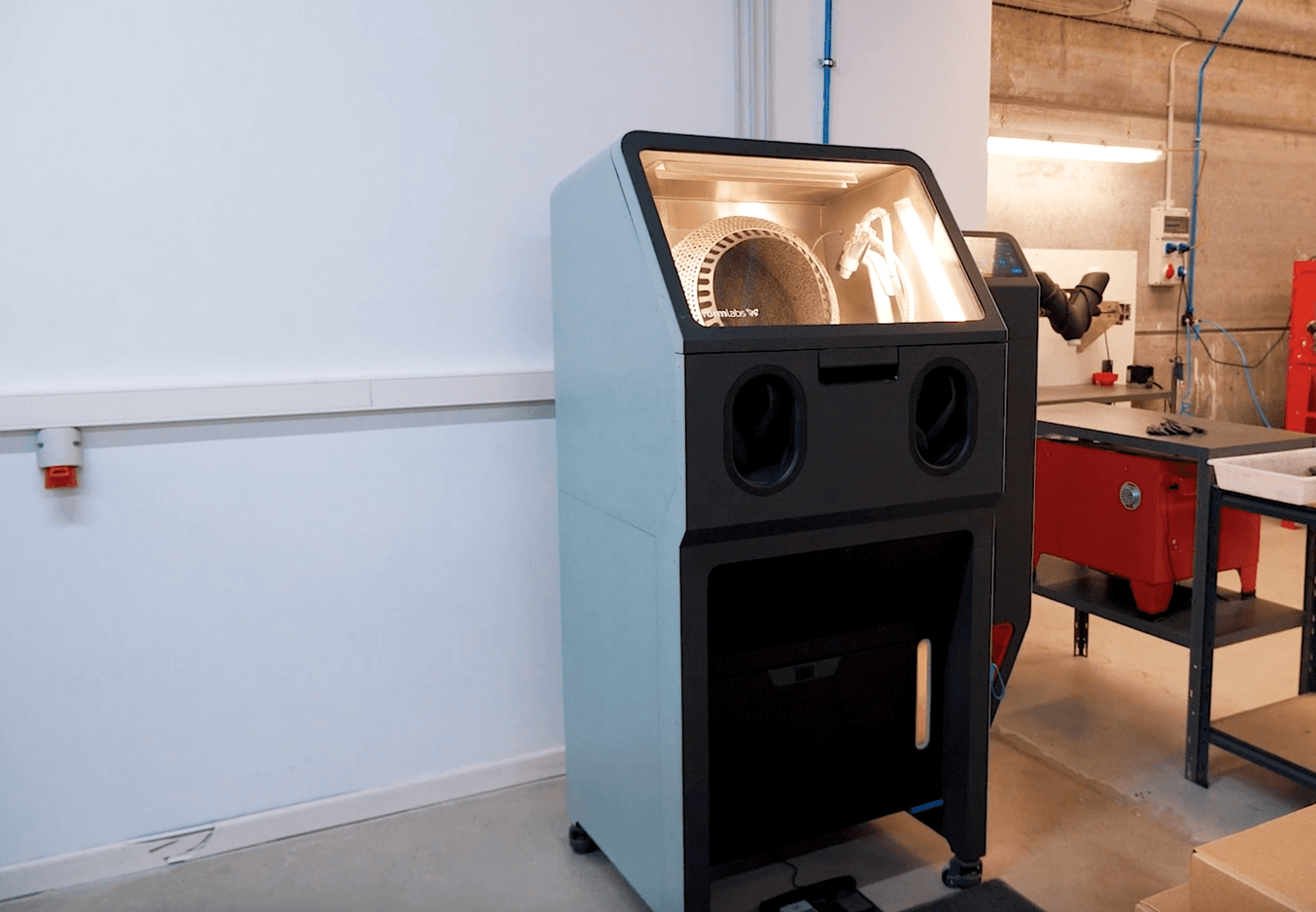
The Fuse Blast has allowed Marti to keep his labor costs low while expanding his business and taking on more orders.
Adding the Fuse Blast has enabled WLD to keep their labor costs low even while scaling up print volume to meet increased demand. As Marti began to take on more orders, he realized that each day one technician was completely dedicated to part cleaning and powder removal manually in the Fuse Sift or Fuse Depowdering Kits. When the Fuse Blast was released, he jumped on the chance to automate that part of the workflow. The Fuse Blast made an immediate difference in WLD’s capacity to handle more orders and take on bigger projects.
“The Fuse Blast — it’s helped so much. The Fuse Blast is like having another person doing 8 hours of manual blasting, and it’s cheaper than paying for someone to do this. In three months, we got our investment back.”
Albert Marti, Owner, WLD
Getting Started With The Fuse Series
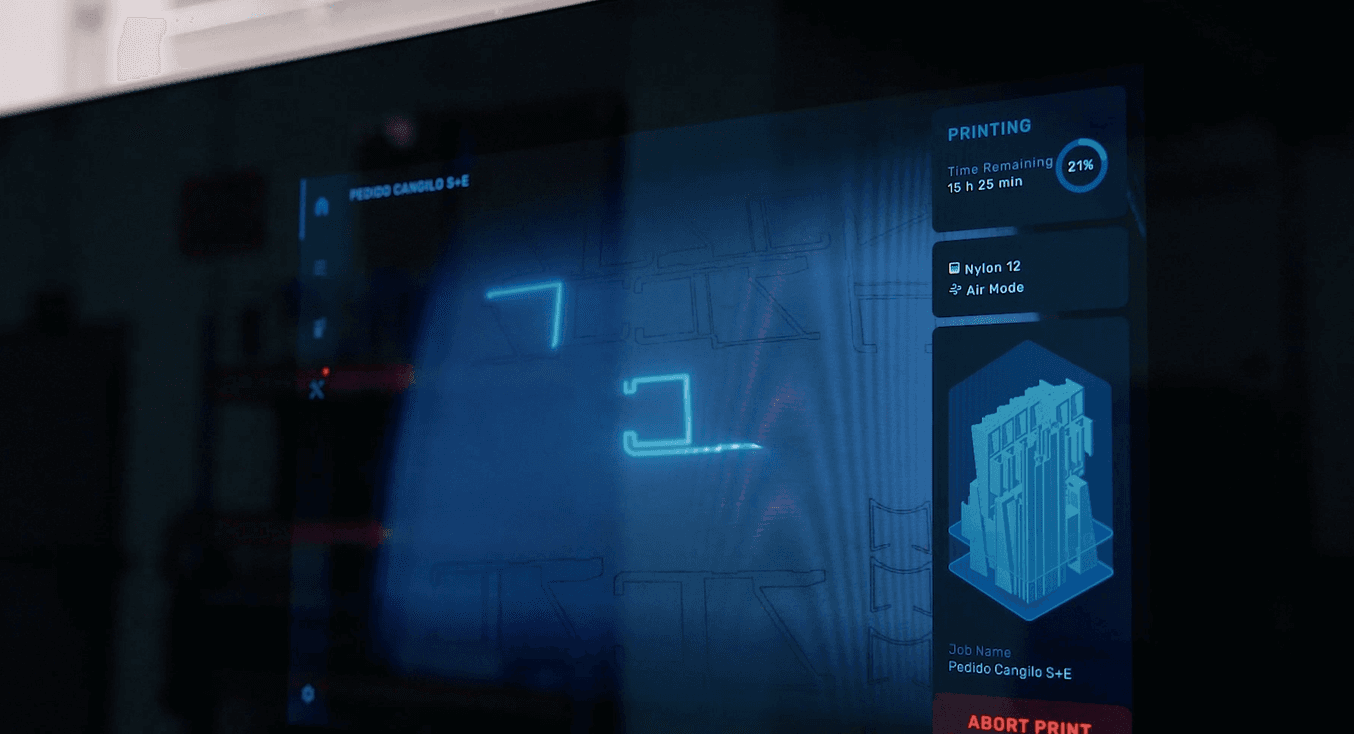
The Fuse Series excels at print jobs where there are multiple unique shapes — PreForm’s packing algorithm can match or outperform even expensive software options for nesting and build volume packing.
As Marti demonstrates with the range of projects, industries, and materials he works with, the Fuse Ecosystem is the most agile 3D printing system available. From one-off prototypes to serial production of thousands of end-use parts each month, SLS 3D printing with the Fuse Series drives down costs and delivers high-quality products.
To learn more about end-use part production and pricing tiers, visit our site. To see the quality of SLS 3D printing for yourself, request a sample.