In den vergangenen zehneinhalb Jahren hat Formlabs so einige Meisterleistungen vollbracht – angefangen von der Kickstarter-Kampagne im Jahr 2011 bis hin zur Erreichung eines Unternehmenswertes von 2 Mrd. USD im Juli 2021. Unsere Mission, den Zugang zur digitalen Fertigung zu erweitern, damit alle Anwender ihre individuellen Ideen umsetzen können, hat bei Tausenden von Menschen Anklang gefunden – und alle ihrer Ideen werden Wirklichkeit. Formlabs' Kunden drucken Endverbrauchsteile für die Automobilindustrie, Requisiten für Hollywood-Blockbuster und lebensrettende Medizinprodukte, alles dank unserer 3D-Drucker nach den Technologien Stereolithografie (SLA) und selektives Lasersintern (SLS).
Neue Produktionsmöglichkeiten
Um in nur zehn Jahren die Marke von 100 000 000 zu erreichen, haben unsere Anwender zahllose verschiedene Teile gedruckt, aber nicht nur das: Sie haben auch die Produktion einzelner Teile in Serie ausgeweitet, und das mehrmals. Wir haben hart dafür gearbeitet, die Produktionskapazitäten unserer Drucker zu erhöhen. Dafür haben wir die Reproduzierbarkeit und Einheitlichkeit der Technologie gesteigert, um sicherzustellen, dass unsere Drucker ununterbrochen laufen und Unternehmen als unermüdliches Arbeitstier dienen.
Einer unserer Kunden setzte in Sachen Produktionskapazität neue Maßstäbe, mit der Herstellung genau jenes Produktes, das jedem Land, jeder Gemeinde und jedem Menschen nach den vergangenen zwei Jahren nur allzu bekannt ist: des Abstrichtupfers für COVID-19-Tests. Der Singapurer Gesundheitsverband National Additive Manufacturing Innovation Cluster (NAMIC) schloss sich mit dem Formlabs-Partner Eye-to-Eye Communications zusammen und druckte auf Druckern des Typs Form 3 mehr als 30 000 Nasenrachenabstrichtupfer pro Tag aus Surgical Guide Resin. Maxim Lobovsky, Gründungsmitglied und CEO von Formlabs, sprach für die gesamte 3D-Druck-Community, als er erklärte, Formlabs' Arbeit sei „ein Zeugnis für die Agilität und die dezentralen Herstellungskapazitäten, die 3D-Druck bieten kann.“
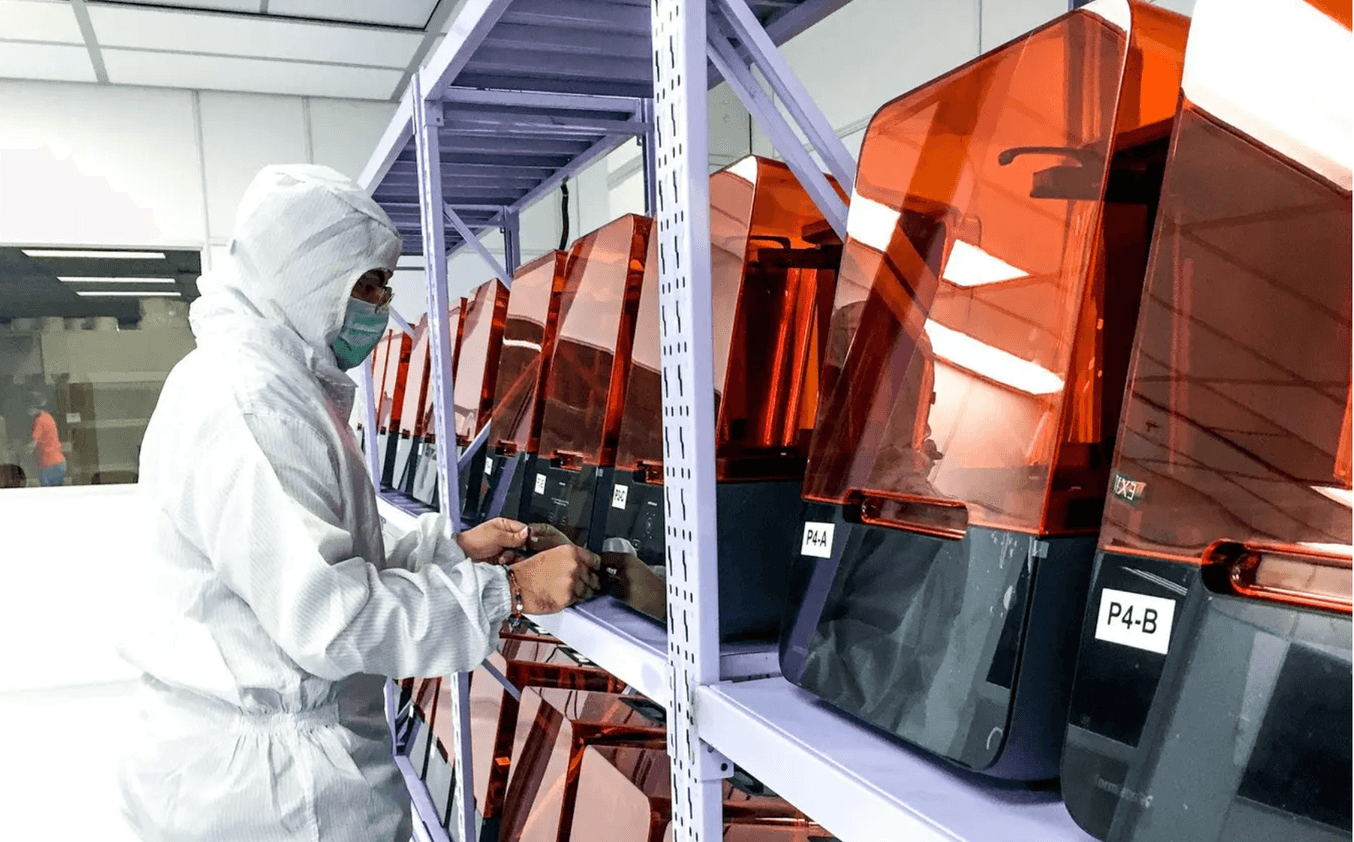
Ein weiterer Kunde aus der Produktion, Ashley Furniture, nutzt alle Drucker von Formlabs, den Form 2, Form 3, Form 3L und jetzt auch den Fuse 1, um einen effizienten Fertigungsprozess zu gewährleisten. Indem das Unternehmen Halterungen und Vorrichtungen 3D-druckte, konnte Ashley Furniture seine Produktionskapazitäten steigern, ohne Ressourcen für kostspielige Werkzeugbestückung aufwenden zu müssen, die für jede Produktreihe oder jedes Modell ausgetauscht werden muss. Allein mit den Form-2-Druckern produzierte das Unternehmen 700 Teile, um seine Produktion schließlich durch die Ergänzung eines Form 3, Form 3L und Fuse 1 an zwei weiteren Fertigungsstandorten auszudehnen.
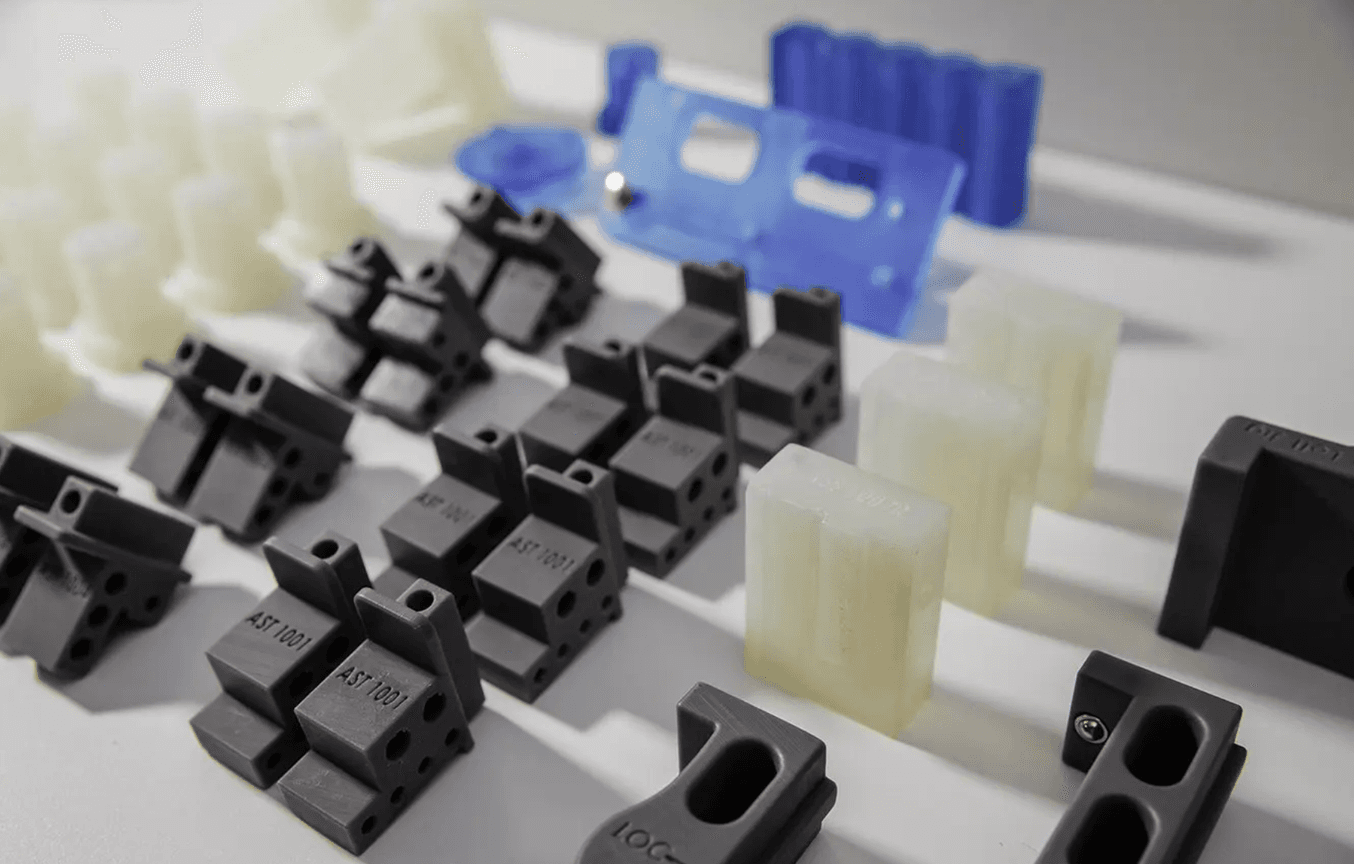
Maßanfertigung und Individualisierung
Obwohl die Massenproduktion sicherlich immer den größten Anteil an der Gesamtzahl der durchgeführten Drucke haben wird, gewinnt der Bereich der Maßanfertigung immer mehr an Einfluss in allen Branchen, die additive Fertigung – und besonders die Drucker von Formlabs – nutzen. Und beim Thema Maßanfertigung führt kein Weg an der Dentalindustrie vorbei. Formlabs setzt alles daran, für Zahnärzte, Leiter von Dentallaboren, Zahntechniker, Kieferorthopäden, Chirurgen und Prothetiker ein Partner zu sein, auf den sie sich verlassen können. Die meisten Menschen wird das überraschen, doch die Herstellung kieferorthopädischer Modelle – auf denen Retainer und Aligner geformt werden – ist der zählenmäßig größte Anwendungsbereich von 3D-Druck überhaupt!
Die Integration innovativer Technologien für Scan und Design mit den Druckern und Materialien von Formlabs erhöht das Versorgungsniveau und macht den Weg frei für eine Individualisierung der Produkte je nach Patient, Klinik und Praxis. Bereits hunderttausende dentale Anwendungen wurden von Formlabs-Kunden gedruckt, wie etwa Modelle aus Grey Resin für thermogeformte kieferorthopädische Anwendungen, Zahnersatz aus Permanent Crown Resin oder sogar Prothesen aus Denture Base Resin und Denture Teeth Resin. Dentallabore und Zahnarztpraxen gehörten zu den Früheinsteigern der 3D-Drucktechnologie und tragen noch heute erheblich dazu bei, die Branche in Richtung immer schnellerer und präziserer Drucker und Materialien voranzutreiben. Durch unser Model Resin nach neuer Formel verhelfen wir Laboren und Praxen zu noch mehr Effizienz. Mit seiner hohen Genauigkeit und Einheitlichkeit ist es speziell für Anwender in der Zahnmedizin konzipiert.
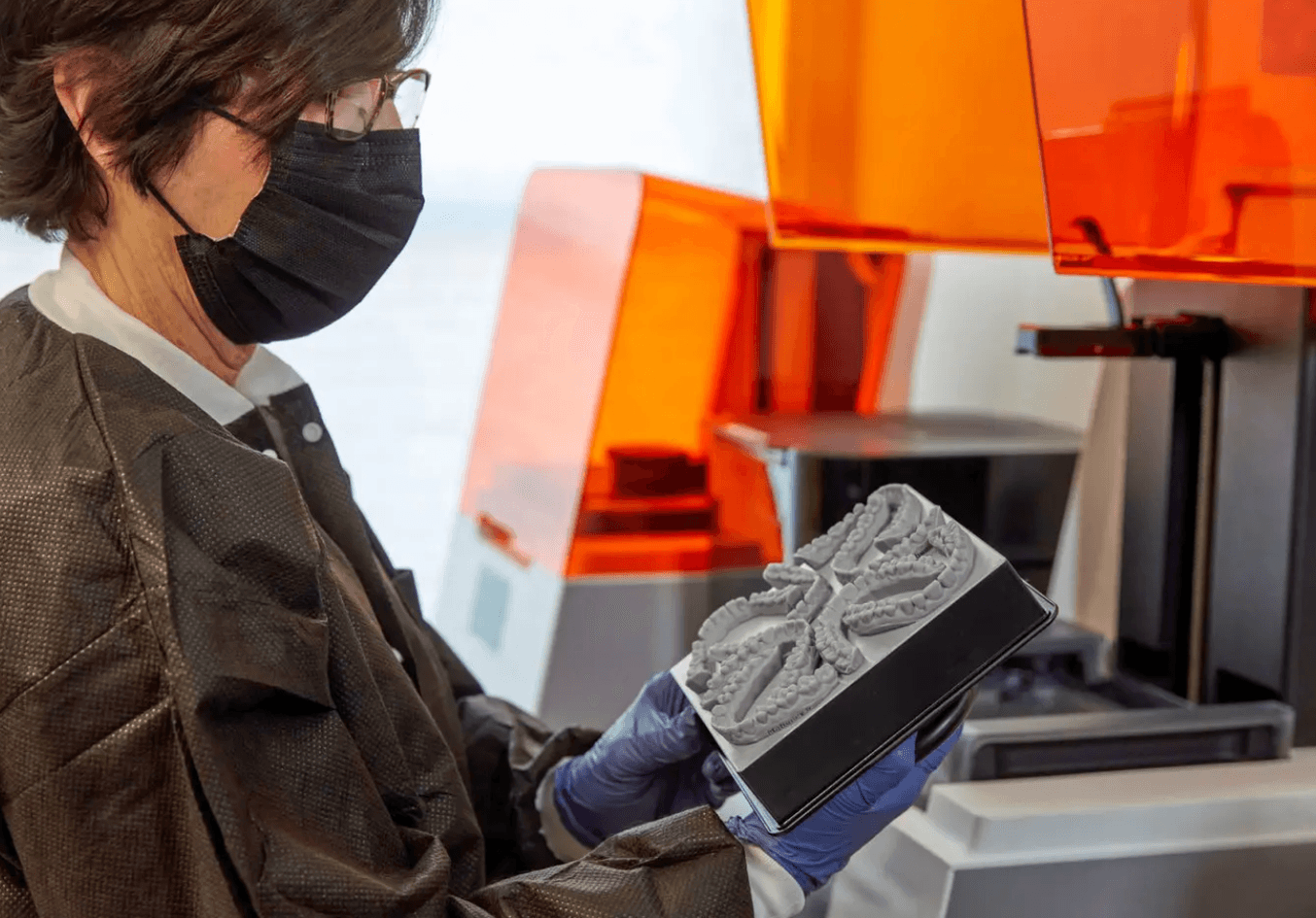
Hinsichtlich der Anzahl gedruckter Teile bringen medizinische Maßanfertigungen keine hohen Ergebnisse ein – schließlich sollte jede Operation so wenig Knochen wie möglich betreffen. In Bezug auf die Operationsdauer, Genesungszeit und das Operationsergebnis lässt sich jedoch eine echte, messbare Verbesserung feststellen, wenn unsere Kunden am Behandlungsort Modelle auf ihren Formlabs-Druckern Form 3+ und Form 3L herstellen.
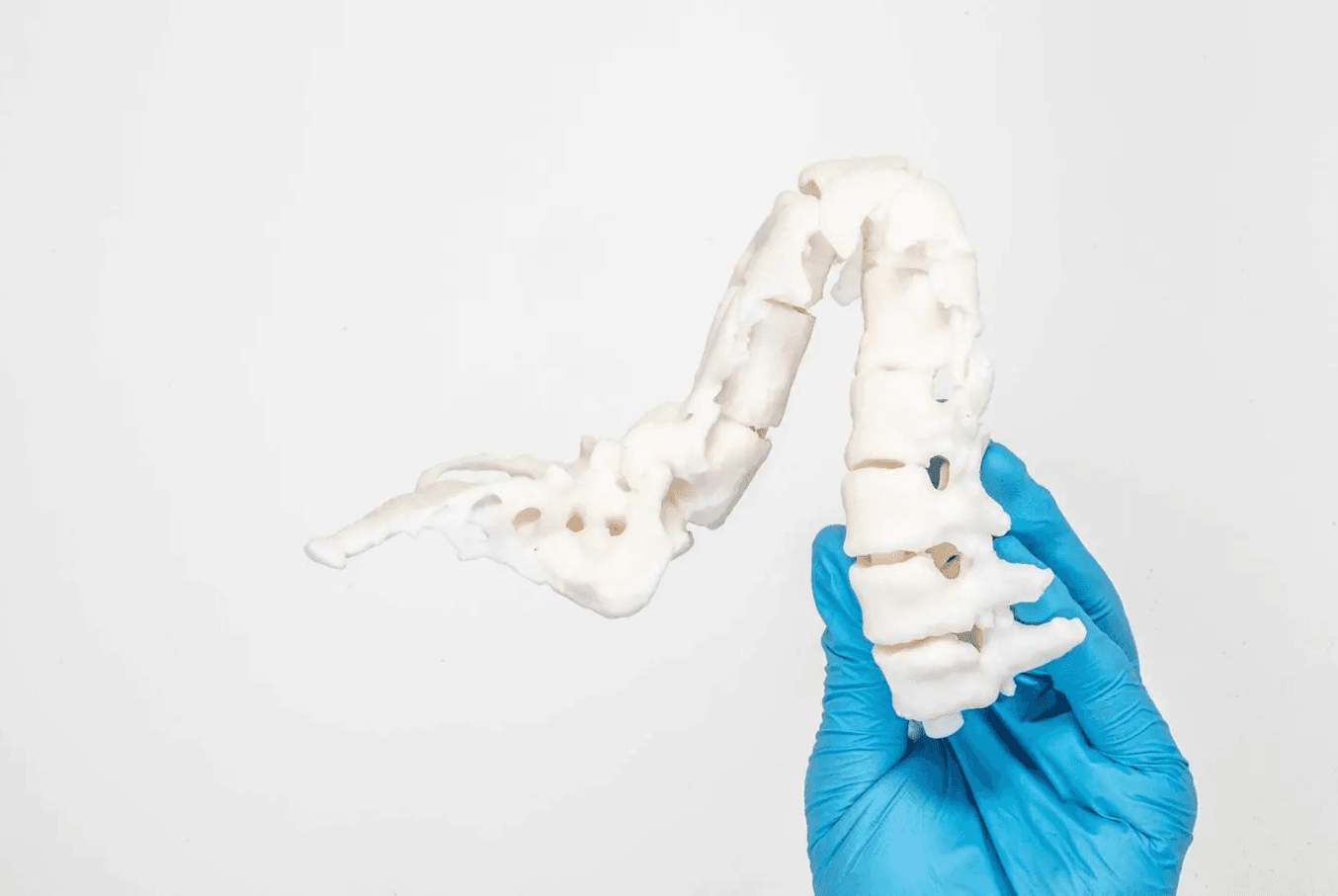
In einigen Fällen findet die Individualisierung von Produkten auch im großen Maßstab statt. Unser Partner Gillette stellte in seinem innovativen Projekt Razor Maker™ individualisierte Rasierergriffe für seine Kunden her, mittels hunderter auf dem Form 2 gedruckter Modelle aus einer Vielzahl unserer Kunstharze. Die Individualisierung von Verbraucherprodukten ist eine relativ neue Domäne, doch dank ihres einmaligen Markenbewusstseins schafften es unsere Partner in Boston, auf die Möglichkeiten des 3D-Drucks für diesen Bereich aufmerksam zu machen.
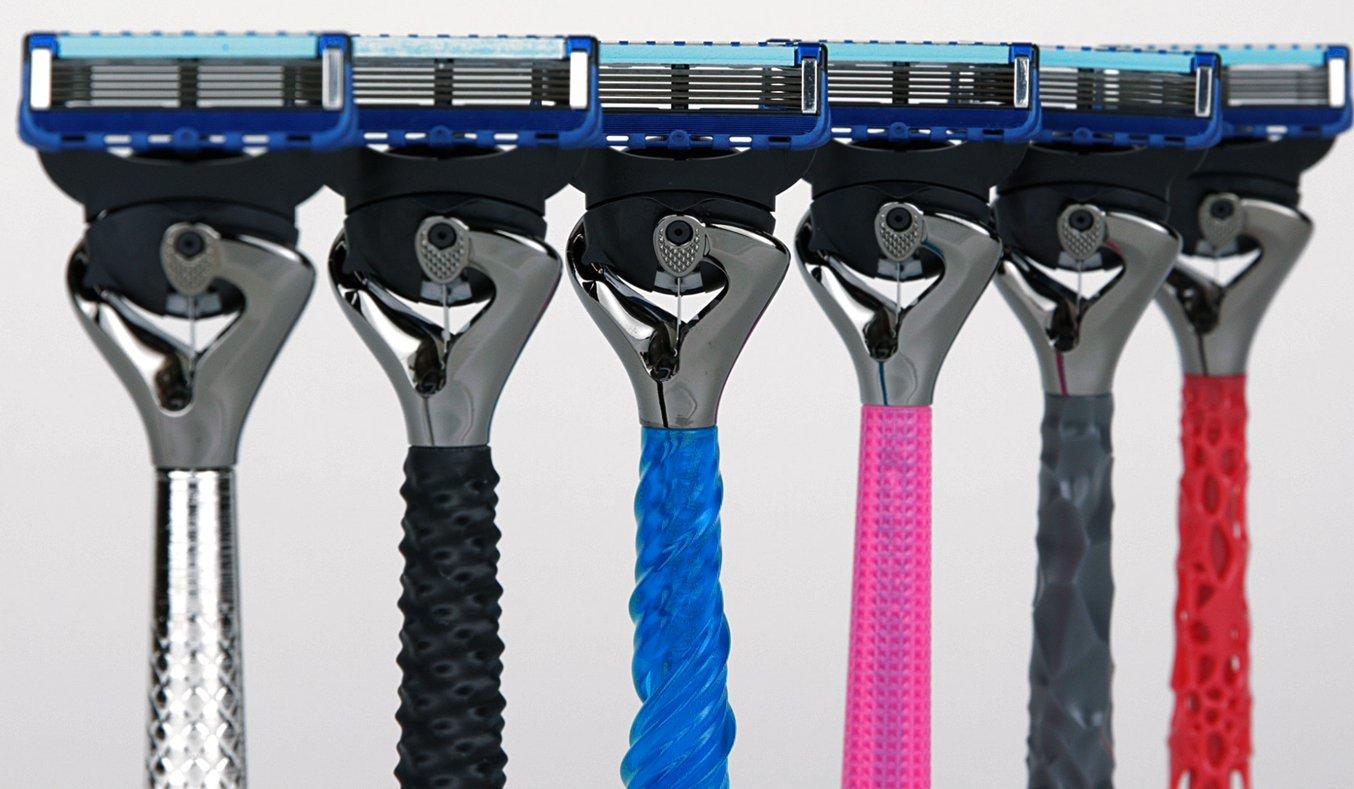
Auf Formlabs-Druckern gedruckte Rasierergriffe für die Plattform Gillette's Razor Maker™
Formlabs' Evolution in der Unterhaltungsbranche
Dass die leistungsstarken SLA-Drucker von Formlabs in der digitalen Bildhauerei genau in ihrem Element sein würden, das war uns von Anfang an klar. Doch wir hätten uns nie träumen lassen, an was für einer beeindruckenden Bandbreite von Projekten unsere Drucker teilhaben würden.
Angefangen von einem unserer ersten Anwenderberichte aus dem Jahr 2013 mit Robert Vignone, einem digitalen Designer bei Dreamworks, bis hin zu unserer Partnerschaft mit Russell Bobbitt, dem leitenden Requisiteur bei Marvel, hat Formlabs es in Hollywood ganz groß rausgebracht. Wir arbeiten mit großartigen Produktionsfirmen wie Aaron Sims Creative zusammen, die maßgefertigte Requisiten, Prothesen und Kulissen herstellen und sogar die Drucker selbst zum Teil der Handlung machen. Weltweit beliebte Serien wie Raised By Wolves, Stranger Things und Grey's Anatomy verwenden mit Formlabs-Druckern produzierte Kostümkomponenten und Requisiten oder sogar die Drucker selbst!
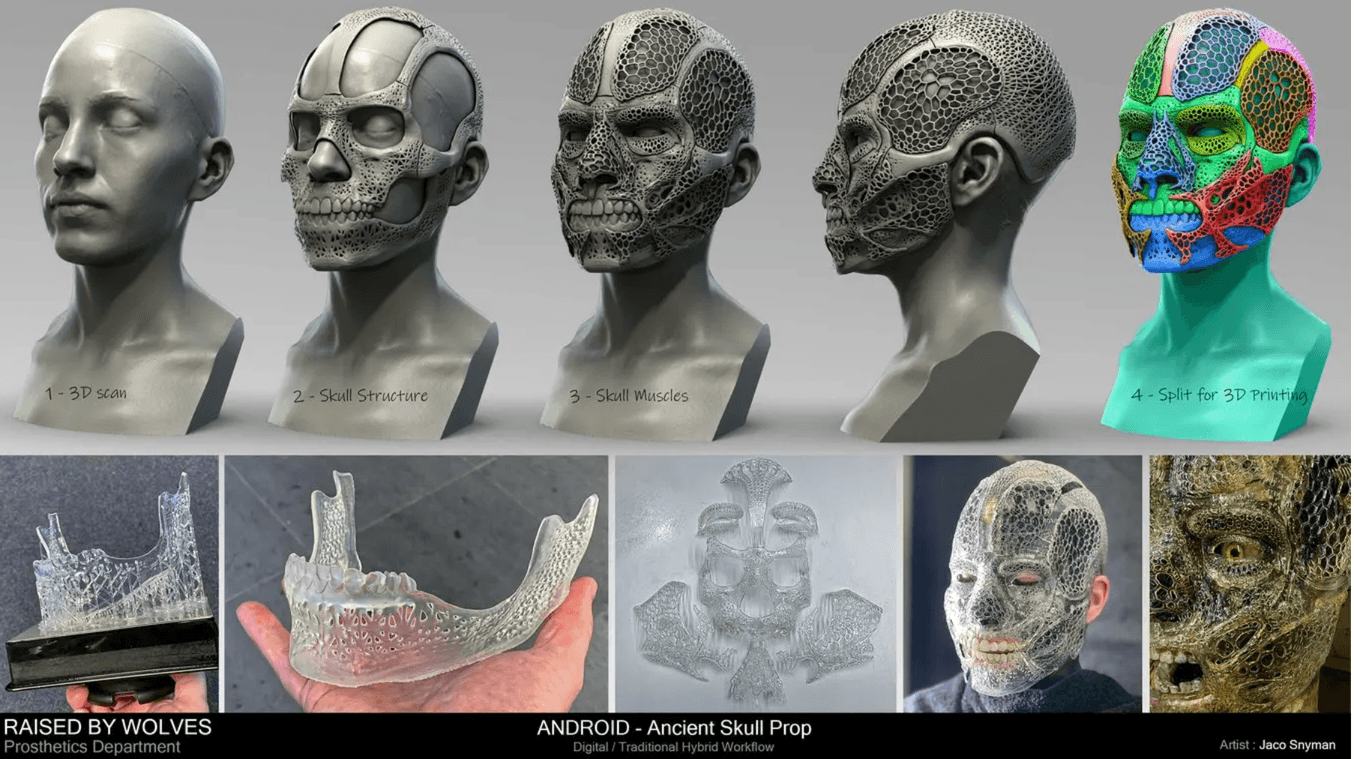
Das Streben nach Perfektion
Sowohl global betrachtet als auch auf die Kundschaft von Formlabs beschränkt ist die am weitesten verbreitete Anwendung des 3D-Drucks das Rapid Prototyping. Schon zu unseren Anfängen vor über 10 Jahren haben Produktentwickler und Ingenieure erkannt, welchen Nutzen 3D-Drucker in leicht handhabbarer Größe und industrieller Qualität bieten. Auch wenn am Ende des Entwicklungsprozesses vielleicht nur ein einziges Produkt steht, erfordert das Streben nach Perfektion dutzende oder sogar hunderte von Iterationen, die alle ihren Teil dazu beigetragen haben, den Meilenstein von 100 Millionen Teilen zu erreichen.
Juweliermeister Tariq Riaz lässt sich bei der Erschaffung seiner Kunstwerke von der Architektur inspirieren. Aufbauend auf seinen ingenieurwissenschaftlichen Hintergrund kreiert er Ringe als funktionale, bewegliche Konstruktionen aus bis zu 60 kleinen Einzelteilen. Dafür erstellt er eine Reihe von Prototypen, denn jedes der 60 Einzelteile kann bis zu 20 verschiedene Designs erfordern. Diese Teile sind zwar klein, doch sie müssen perfekt ineinanderpassen, um sich mit den Bewegungen des Ringträgers problemlos auszuweiten oder zusammenzuziehen.
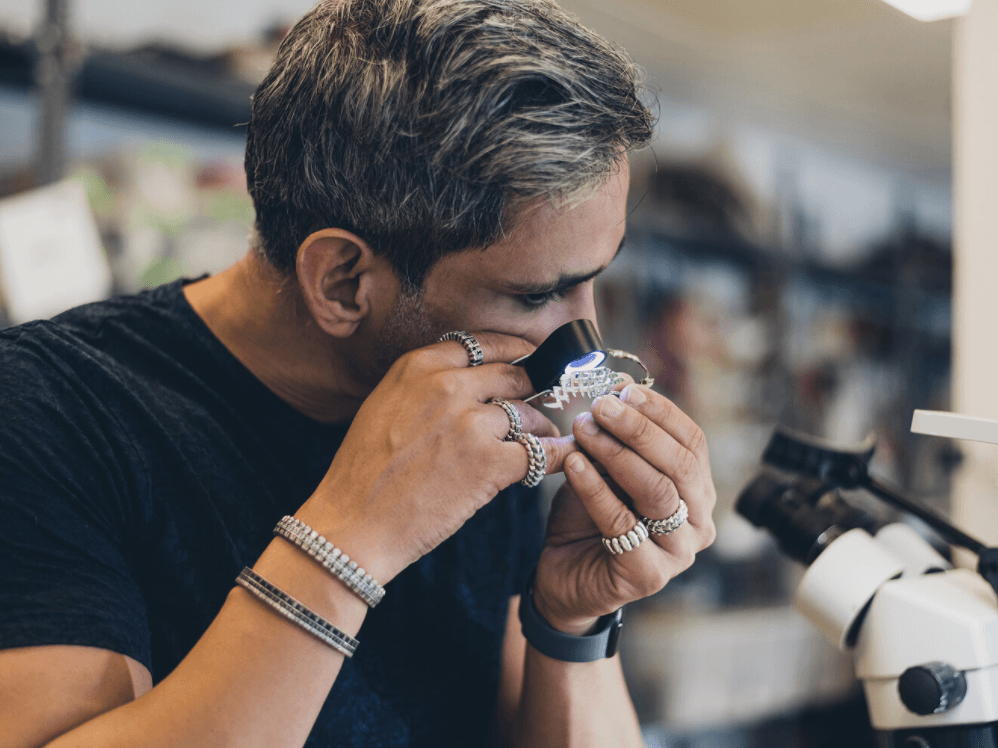
Die Automobilindustrie hat schon immer eine Vorreiterrolle eingenommen, seitdem Henry Ford 1908 die moderne Fließbandproduktion entwickelte. Ihr stetiges Streben nach neuen Rekorden öffnet die Tore für neue Technologien.
Der Aftermarket-Hersteller Dorman Products stellt auf einem Form 3 und einem großformatigen Form 3L Prototypen von Auto-Ersatzteilen her. Die Produktpalette des Unternehmens umfasst bereits 180 000 Posten, und jeder davon durchläuft den Prozess der Prototypenentwicklung! Dabei verwendet Dorman nahezu alle bei Formlabs verfügbaren Kunstharze und baut auf die einheitliche Qualität des Form 3 und Form 3L, um bis zu 5000 neue Produkte pro Jahr auf den Markt zu bringen.
Eine neue Generation von Innovatoren
Obwohl der Fokus meistens auf Kunden liegt, die unsere Drucker in ihrer Arbeit als Ingenieure, Techniker, Zahnärzte oder Designer einsetzen, wurde ein großer Teil der Arbeit, die uns zu diesem Meilenstein von 100 Millionen Teilen geführt hat, von Menschen geleistet, deren berufliche Laufbahn gerade erst beginnt. An Schulen, Berufs- und Fachhochschulen sowie Universitäten stellen Lernende Teile her, die konventionelle Vorstellungen von Design und Fertigung sprengen, und ihre Fähigkeiten im 3D-Design und 3D-Druck sind gefragter denn je.
Um weiter mit 3D-Druck zu arbeiten, sind große Industriekunden auf neue, talentierte Arbeitskräfte angewiesen, und diese lassen sich am besten auf ihre Rolle vorbereiten, indem 3D-Druck bereits in die Ausbildung integriert wird. An großen Universitäten wie der Pennsylvania State University legen sowohl Lehrkräfte als auch die Universitätsverwaltung das Augenmerk auf 3D-Druck als ein Werkzeug, das die Studierenden nicht nur auf die Berufswelt vorbereitet, sondern Arbeitskräfte auch durch die Kollaboration in einer Gemeinschaft weiterbildet. Im Eric J. Barron Innovation Hub können Studierende und die Mitglieder der Community mit den Druckern Form 3, Form 3L und Fuse 1 von Prototypen bis zu Kleinserien alles Erdenkliche produzieren.
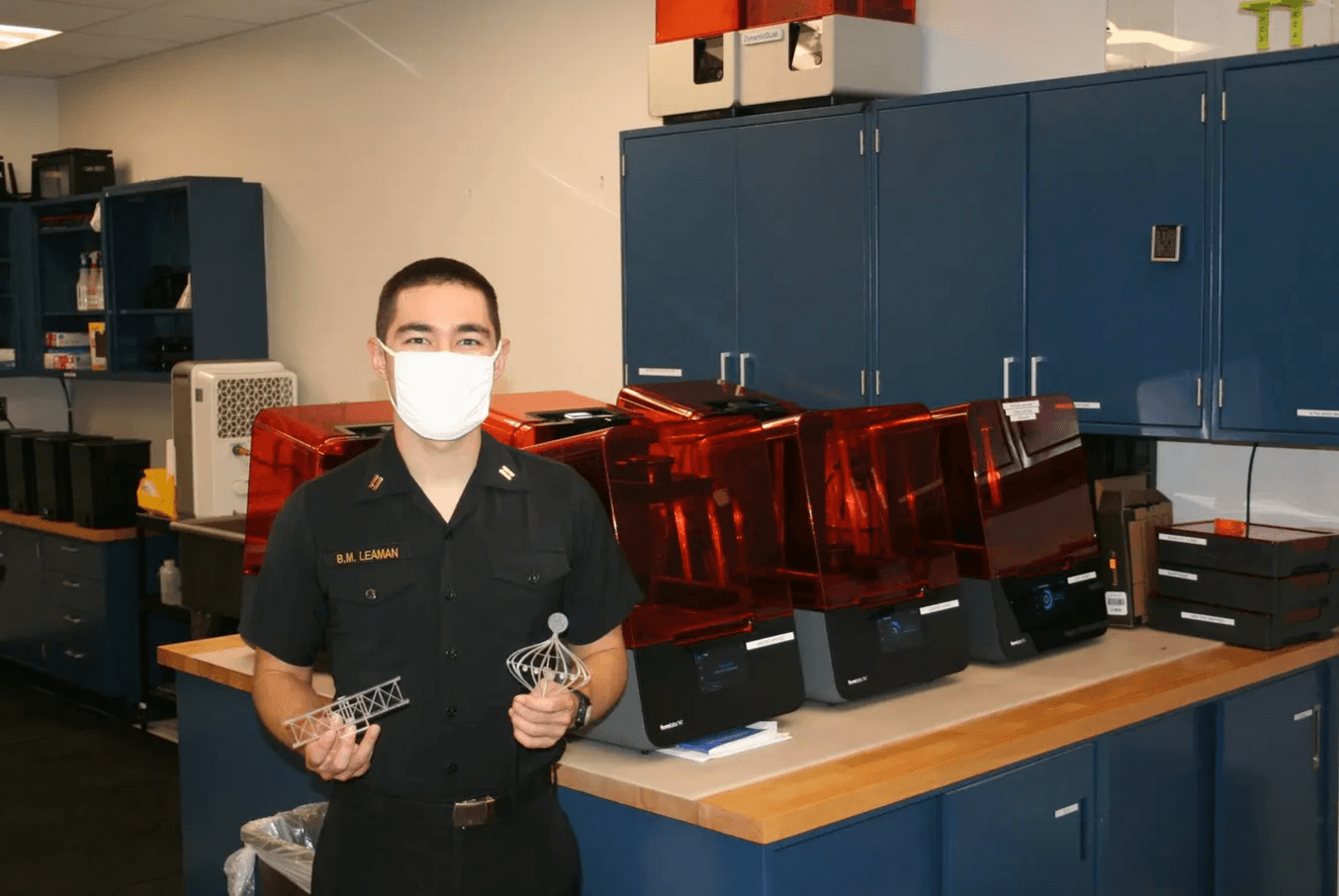
Im MakerSpaceUSNA der US Naval Academy sind die Drucker des Typs Form 3 tagtäglich im Einsatz.
Zur Feier der Formlabs-Community
Mit Freuden geben wir bekannt, dass zur Feier unserer Anwender*innen vom 26. bis zum 27. Oktober erneut ein Formlabs User Summit stattfinden wird, in vollkommen virtueller Form. Letztes Jahr haben wir auf Veranstaltungen in sieben Sprachen tausende Anwender*innen aus 150 Ländern getroffen. Dieses Jahr rechnen wir mit einer noch weitreichenderen globalen Repräsentation. Gemeinsam blicken wir auf ein Jahrzehnt voller Innovationen zurück, teilen Erkenntnisse und feiern Meilensteine. Die Teilnahme ist vollkommen kostenlos. Wir freuen uns auf Sie!
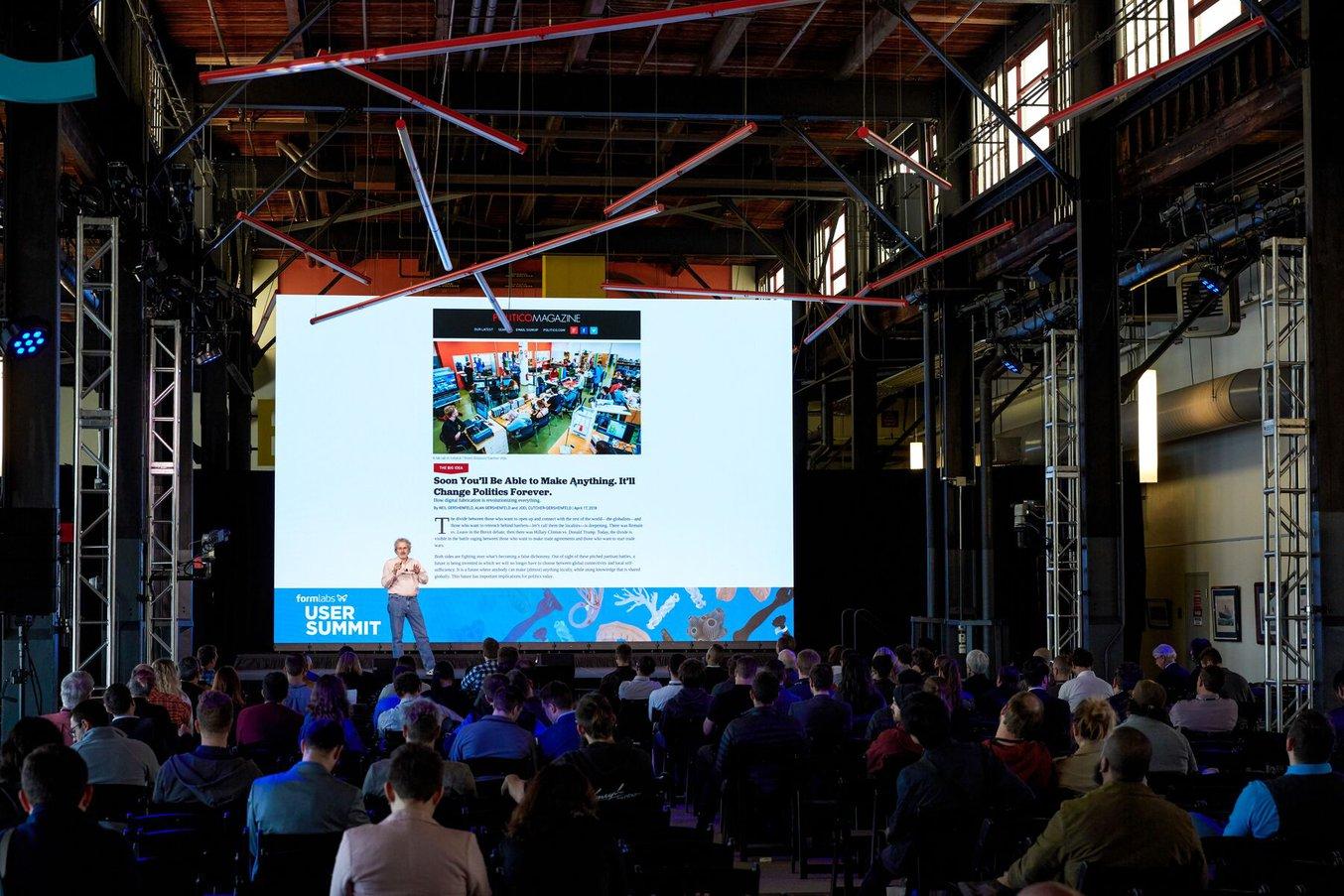
Auf dem Formlabs User Summit 2019 kamen Anwender*innen aus aller Welt zusammen, um sich auszutauschen, zu lernen und zusammenzuarbeiten. Wir freuen uns darauf, unsere fantastische Community auf dem FUS 2022 wiederzutreffen!
Die nächsten hundert Millionen
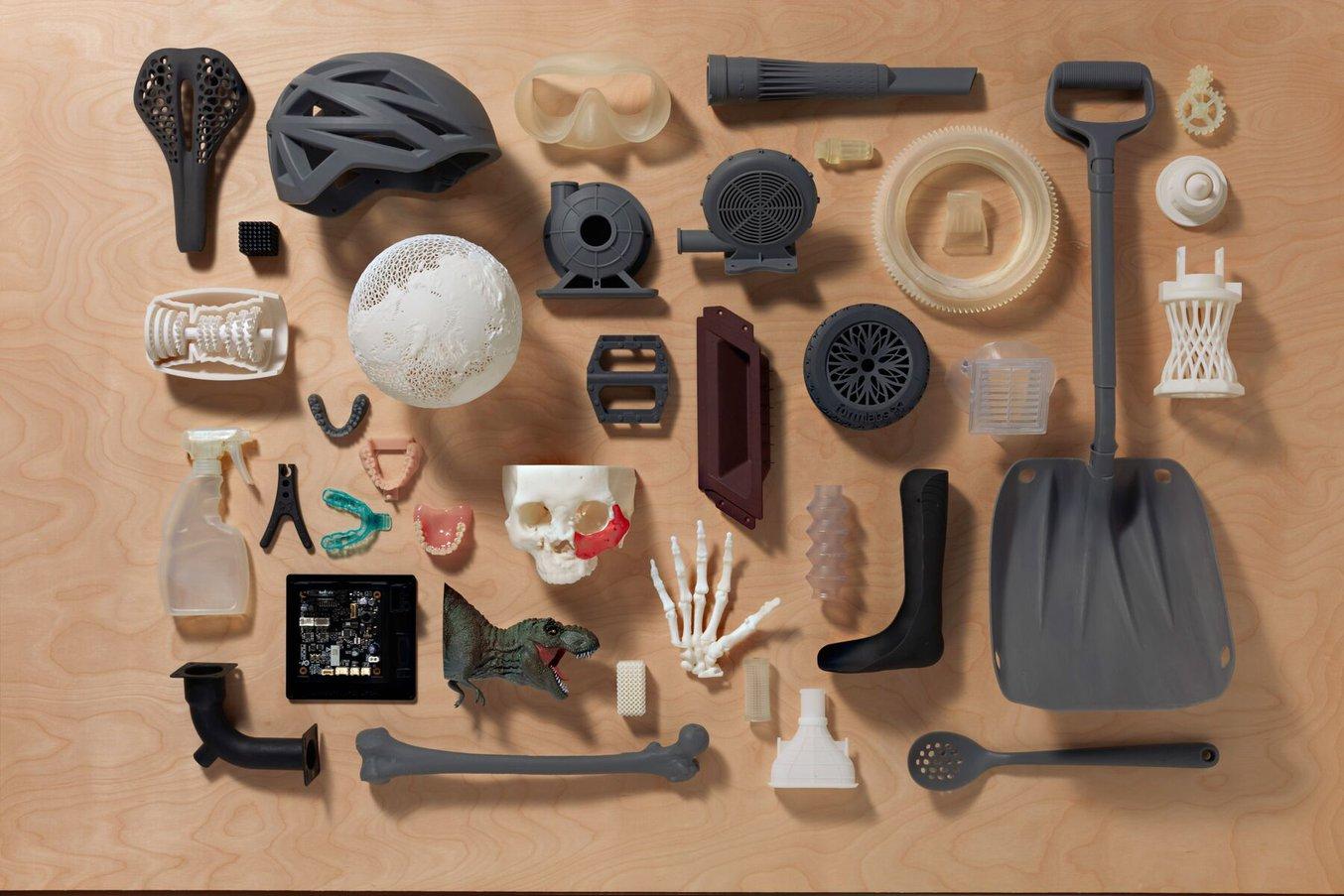
Die 3D-Druckindustrie hat den Blick stets auf die Zukunft gerichtet, setzt immer wieder neue Maßstäbe für Geschwindigkeit, Größe und Stärke und erschließt dadurch laufend neue Möglichkeiten. Für diesen Moment blickt Formlabs jedoch stolz zurück auf alles, was unsere Community bisher erreicht hat.
Diese 100 Millionen Teile sind eine gemeinsame Leistung, ein Streben danach, auszuprobieren, zu iterieren, zu erneuern, zu vergrößern, zu verkleinern und zu überholen. Wir können es kaum erwarten, die nächsten hundert Millionen Teile mit Ihnen zu drucken, und sind gespannt, was Sie als nächstes erschaffen.