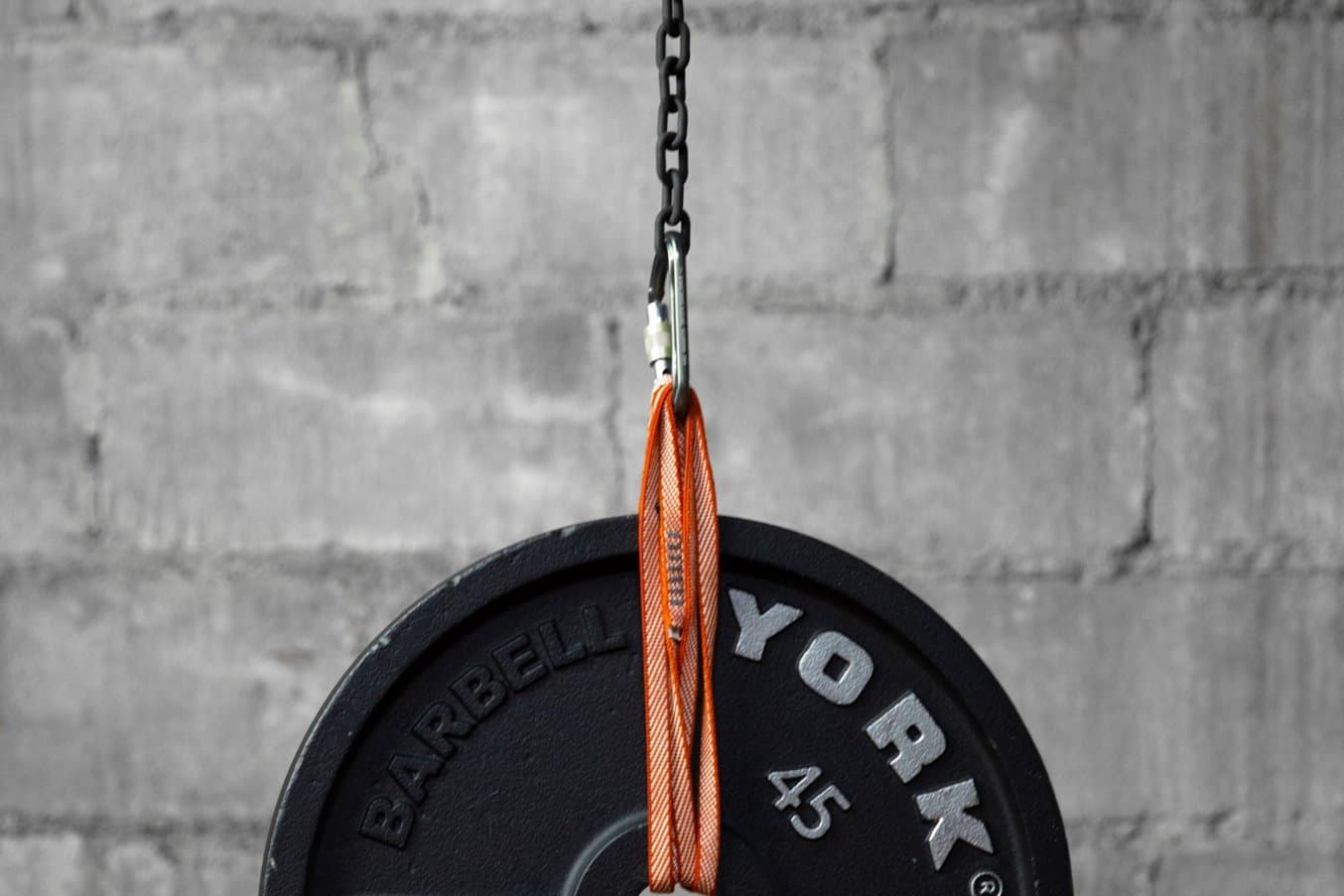
Fahrräder, Rennwagen, Drohnen und Tennisschläger – Produkte mit äußerst verschiedenen Verwendungszwecken, die aber alle den Anspruch haben, ohne zusätzliches Gewicht eine hohe Festigkeit und Stabilität zu erreichen. Genau diese Kombination von Materialeigenschaften ist bei kohlenstofffaserverstärkten Kunststoffen gegeben (auch CFK genannt), welche von Fahrgestellen in Formel-1-Wagen bis zu den Rahmen leichter Verkehrsfahrräder in den verschiedensten Anwendungsbereichen Einsatz finden.
Da zahlreiche 3D-Drucker Materialien auf Polymerbasis nutzen, die häufig Verbundstoffe sind, stellen sich viele zu Recht die Frage: Kann man CFK 3D-drucken?
Tatsächlich gibt es zwei Methoden, mithilfe von 3D-Druck Teile aus kohlenstofffaserverstärktem Kunststoff zu fertigen: entweder durch die Kombination traditioneller Fertigungsmethoden mit 3D-gedruckten Formen oder durch den direkten 3D-Druck kohlenstofffaserverstärkter Verbundwerkstoffe. In diesem Artikel stellen wir konventionelle Fertigungsverfahren und neue Prozesse zur Herstellung 3D-gedruckter Formen für CFK vor, und außerdem gehen wir auch auf den direkten 3D-Druck von Carbonfaserverbundstoffen ein.
Traditionelle Herstellungsverfahren für CFK-Teile in Kombination mit 3D-Druck
Unter kohlenstofffaserverstärktem Kunststoff (auch carbonfaserverstärkter Kunststoff, kurz CFK oder Carbon) versteht man einen Verbundwerkstoff, der üblicherweise durch das Verweben von langen Strängen aus Kohlenstofffaser hergestellt wird, die dann mit einem Polymer weiter verbunden werden. Die Fasern können so verwoben werden, dass ihre Festigkeit entlang eines bestimmten Vektors ausgerichtet ist, oder auch ungeordnet, sodass das Endprodukt in jeder Richtung über erhöhte Festigkeit verfügt. Das so hergestellte Halbzeug wird in der Regel über eines von drei Verfahren zum gewünschten Produkt umgeformt: Handlaminierung, Prepreg-Laminierung oder Resin Transfer Molding (RTM).
Handlaminierung
Beim Handlaminieren werden CFK-Platten zugeschnitten, in eine Form gepresst und anschließend mit einem flüssigen Kunstharz lackiert, welches die Platten in der gewünschten Form bindet, während es aushärtet. Diese Methode hat den geringsten Bedarf an Ausrüstung und ist für Einsteiger auch am leichtesten zu erlernen. Da es fast vollständig von Hand ausgeführt werden kann, ist das Handlaminieren eines der kostengünstigsten Verfahren. Im Gegenzug sind die gefertigten Teile jedoch weniger formtreu gegenüber der Urform als bei anderen Umformungsverfahren.
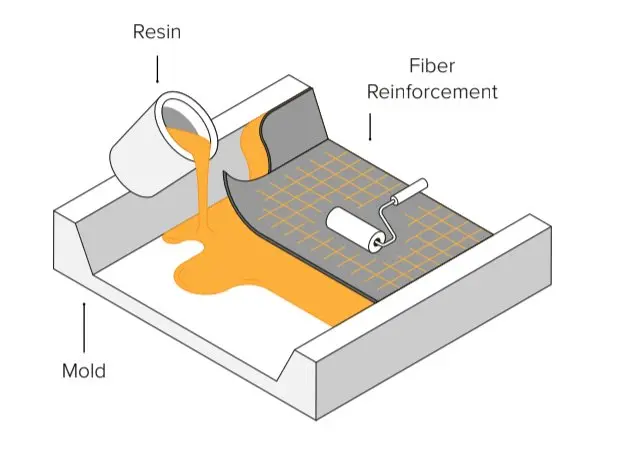
Prepreg-Laminierung
Bei diesem Verfahren ist den Kohlenstofffasern bereits Kunstharz beigemischt. Das Material wird dann in eine Form gefüllt, in der es mittels Druck und Hitze seine endgültige Geometrie erhält. Diese Methode ist die teuerste, da sie spezielle Ausrüstung zur Lagerung und Handhabung der mit Kunstharz angereicherten Platten erfordert, sowie eine Formmaschine mit Hitze- und Druckeinwirkung. Aus denselben Gründen ist die Prepreg-Laminierung jedoch auch die Methode mit der höchsten Wiederholbarkeit und den einheitlichsten Ergebnissen, weshalb sie sich für die Serienproduktion von Carbonfaserteilen am besten eignet.
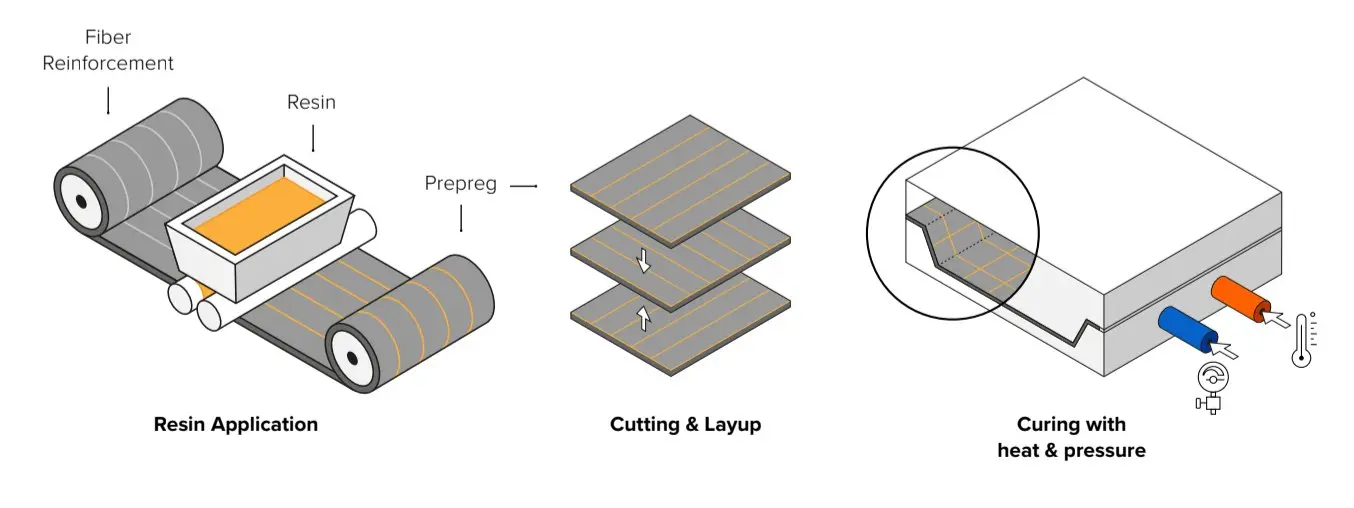
Resin Transfer Molding (RTM)
Beim RTM-Verfahren werden die trockenen Fasern in eine zweiteilige Form eingelegt. Die Form wird fest verschlossen und anschließend wird Kunstharz unter hohem Druck in den Hohlraum gespritzt. Der Prozess ist für gewöhnlich automatisiert und wird zur Produktion großer Mengen eingesetzt.
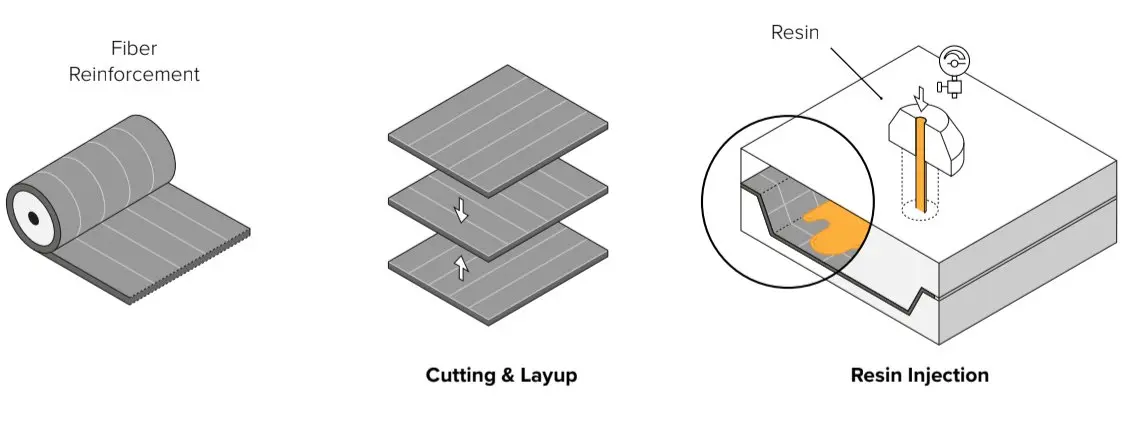
Fertigung von CFK-Teilen mit 3D-gedruckten Formen
In jedem der drei genannten Prozesse kann 3D-Druck genutzt werden, um Kosten zu senken und Durchlaufzeiten zu verkürzen. Alle drei konventionellen Fertigungsmethoden erfordern eine oder mehrere Formen oder Formwerkzeuge, welche bisher über zeitintensive subtraktive Verfahren wie die Zerspanung von Holz, Schaumstoff, Metall, Kunststoff oder Wachs hergestellt wurden. Der 3D-Druck bietet eine alternative Lösung zum Formenbau. 3D-gedruckte Formen sind sowohl individuell anpassbar als auch effizienter und kostengünstiger in der Kleinserienproduktion oder kundenspezifischen Fertigung.
In Anwendungsbereichen wie der Automobilbranche oder Luft- und Raumfahrt, die funktionsfähige Prototypen erfordern, kann der iterative Prozess Hunderte verschiedener Formen beanspruchen. Die Fertigung dieser Iterationen mit konventionellen Verfahren ist oft teuer und zeitaufwendig, weshalb der 3D-Druck für die Produktion kleiner Chargen eine effiziente Lösung darstellt. Formen aus dem 3D-Drucker sind für die Großserienproduktion zwar weniger gut geeignet als Metallformen, können dafür aber kostengünstig betriebsintern hergestellt werden und beschleunigen so die Produktentwicklung und -validierung sowie die Produktion von Kleinserien.
Formen für die Produktion von Carbonteilen können mit einer Vielzahl von Techniken hergestellt werden. Aufgrund der glatten Oberflächenbeschaffenheit und der umfassenden Materialbibliothek ist der SLA-3D-Druck (Stereolithografie) jedoch eine beliebte Wahl für den betriebsinternen Formenbau. SLA-Teile weisen nahezu keine Schichtlinien oder Porosität auf, sodass die CFK-Platten fest in die Form gepresst werden können, ohne dass texturierte Oberflächen zu befürchten sind.
Panoz, ein Hersteller von Renn- und Sportwagen, benötigte einen maßgefertigten Luftauslass für das Cockpit eines Rennwagens, der die Luft hinausbefördert und so die Innentemperatur senkt. In Zusammenarbeit mit DeltaWing Manufacturing setzte das Team einen SLA-3D-Drucker von Formlabs ein, um ein Modell aus High Temp Resin zu drucken, und goss dann aus hitzebeständigem Epoxidharz manuell eine Form aus dem 3D-gedruckten Modell. Durch die Nutzung von 3D-Druck konnte DeltaWing es umgehen, eine kostspielige Metallform für das maßgefertigte Carbonteil durch Outsourcing zu beziehen, und verringerte somit seine Gesamtkosten und auch die Durchlaufzeit.
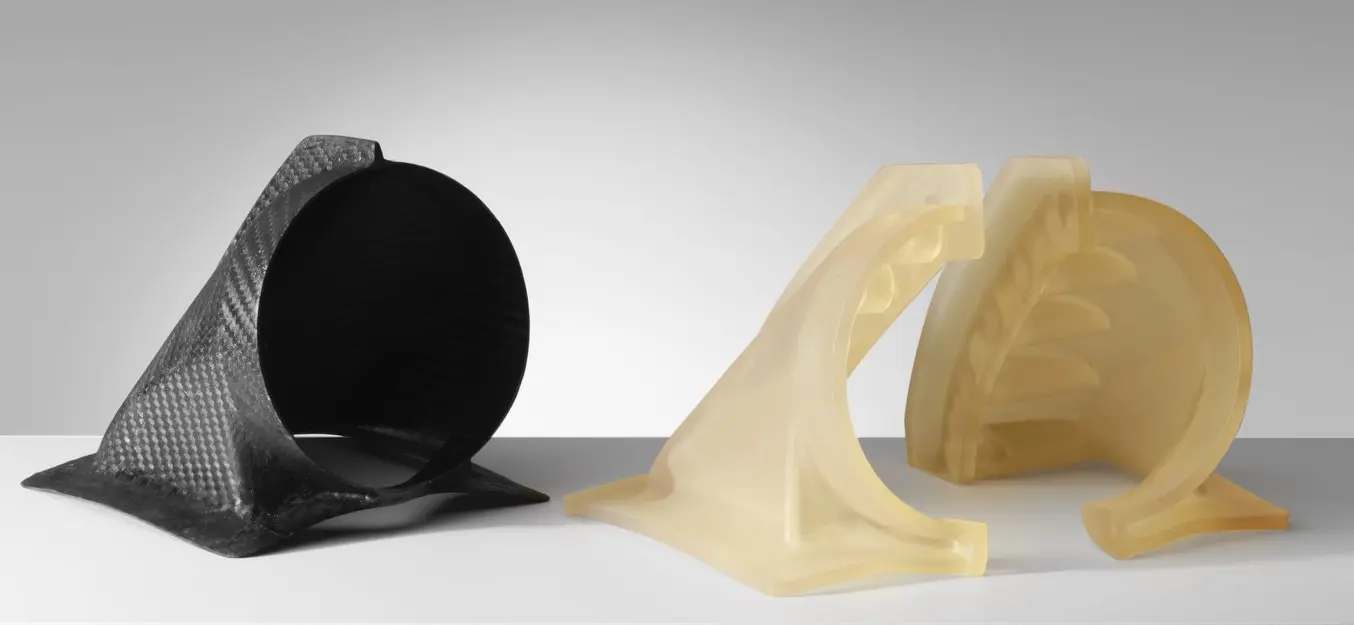
Ein Kotflügellufteinlass aus Carbon neben der zweiteiligen Form aus High Temp Resin, hergestellt von DeltaWing Manufacturing.
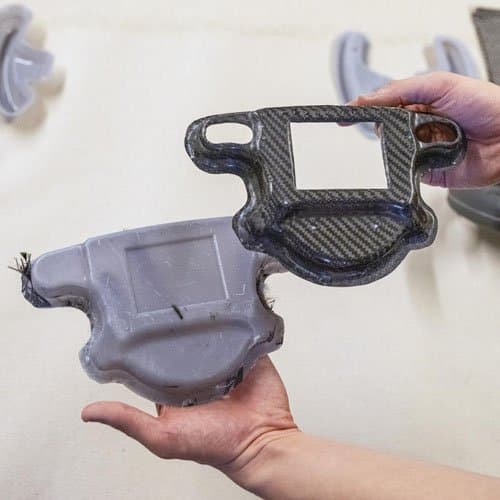
Fertigung von Kohlenstofffaserteilen mit 3D-gedruckten Formen
In diesem Whitepaper zur Herstellung von Kohlenstofffaserteilen erhalten Sie Designleitfäden für Verbundwerkstoffformen sowie schrittweise Anleitungen für die Prepreg- und Handlaminierung.
Direkter 3D-Druck mit kohlenstofffaserverstärktem Kunststoff
Sie suchen den besten 3D-Drucker für CFK? Die Nachfrage nach Arbeitsabläufen, die die Festigkeit, Haltbarkeit und Robustheit traditioneller Carbonfaserteile mit der Agilität, der geometrischen Freiheit und der Reproduzierbarkeit des 3D-Drucks vereinen, ist sehr hoch. Daher überrascht es kaum, dass viele 3D-Druckunternehmen auch 3D-Druck von carbonfaserverstärktem Kunststoff anbieten, wobei die beiden bisher verfügbaren Prozesse entweder zerkleinerte oder durchgängige Fasern einsetzen.
3D-Druck mit Kurzfasern
Bei dieser Art von Werkstoff handelt es sich um Kunststoff-Verbundmaterialien für den 3D-Druck, in die kleine Stücke von Kohlenstofffasern eingebettet sind. Diese Kurzfasern verleihen dem Verbundstoff zusätzliche Festigkeit. Es kann sich dabei um Carbonfaser-Filament für die Schmelzschichtung (FDM) handeln oder auch um Nylonpulver für das selektive Lasersintern (SLS).
Die Hauptvorteile von 3D-Druckmaterialien, die mit Carbon-Kurzfasern verstärkt sind, liegen im Vergleich zu anderen 3D-Druckmaterialien auf Polymerbasis in ihrer Festigkeit, Leichtgewichtigkeit, Hitzebeständigkeit und der geringen Neigung zum Kriechen. Verglichen mit konventionellen Fertigungstechniken für CFK-Teile bietet der 3D-Druck mit Kurzfasern eine höhere geometrische Flexibilität beim Design, besonders beim SLS-3D-Druck. Dadurch kann der erhebliche Arbeitsaufwand traditioneller Formgebungsverfahren potenziell überflüssig gemacht werden und es werden neue innovative Möglichkeiten geboten, das Material in die eigenen Arbeitsprozesse einzubinden.
Formlabs' SLS-3D-Drucker Fuse 1+ 30W ermöglicht diese Art des CFK-3D-Drucks mit dem Material Nylon 11 CF Powder – dem stärksten Material in der SLS-Materialbibliothek von Formlabs. Der Fuse 1+ 30W ist die kostengünstigste Lösung für hochleistungsfähigen SLS-3D-Druck mit Carbon-Kurzfasern. Zwar bieten auch herkömmliche industrielle SLS-Geräte einige CFK-Materialien, doch die hohen Einstiegskosten machen den Mehrwert des 3D-Drucks von Carbon nahezu hinfällig, wenn man das Verfahren RTM oder Prepreg-Laminierung gegenüberstellt.
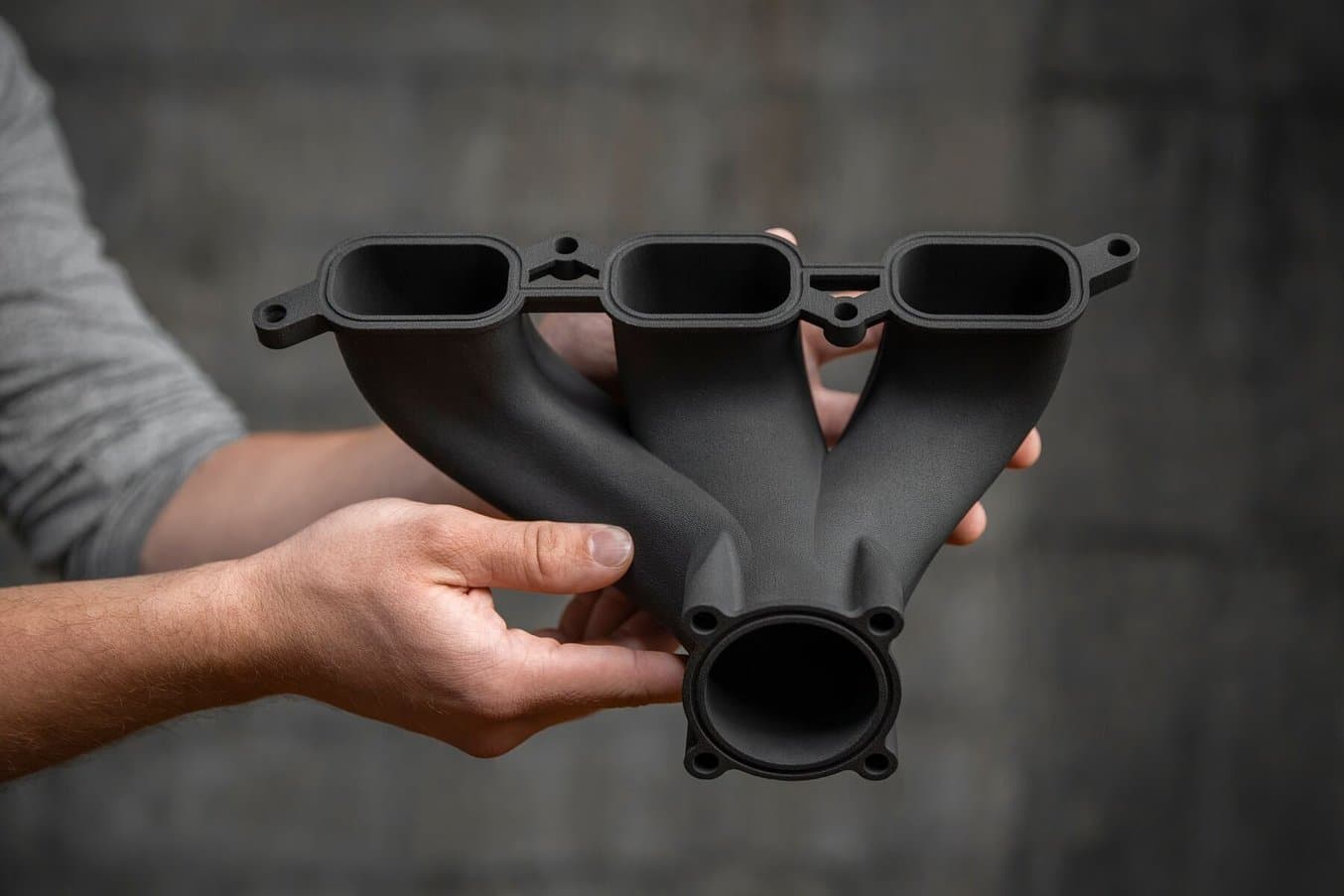
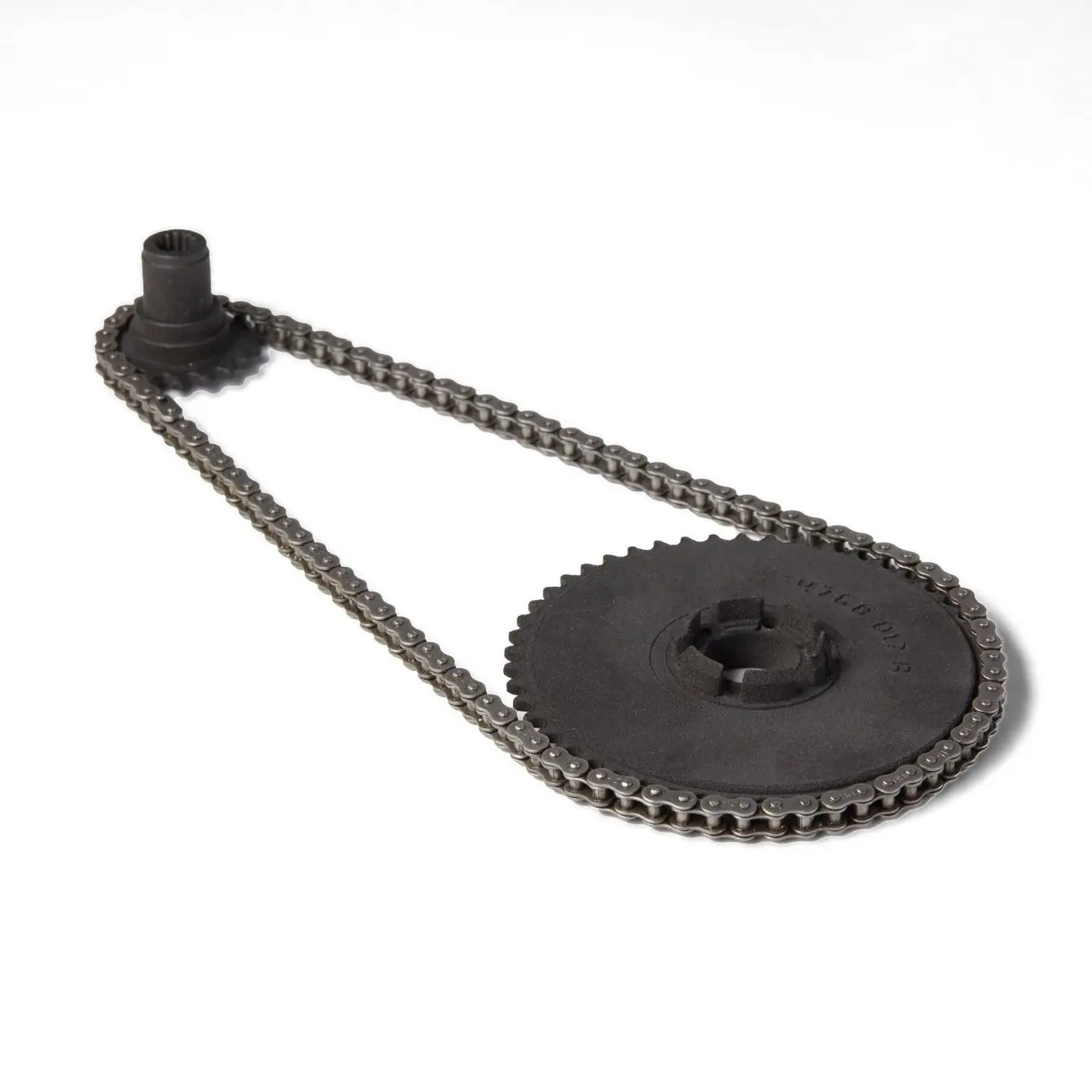
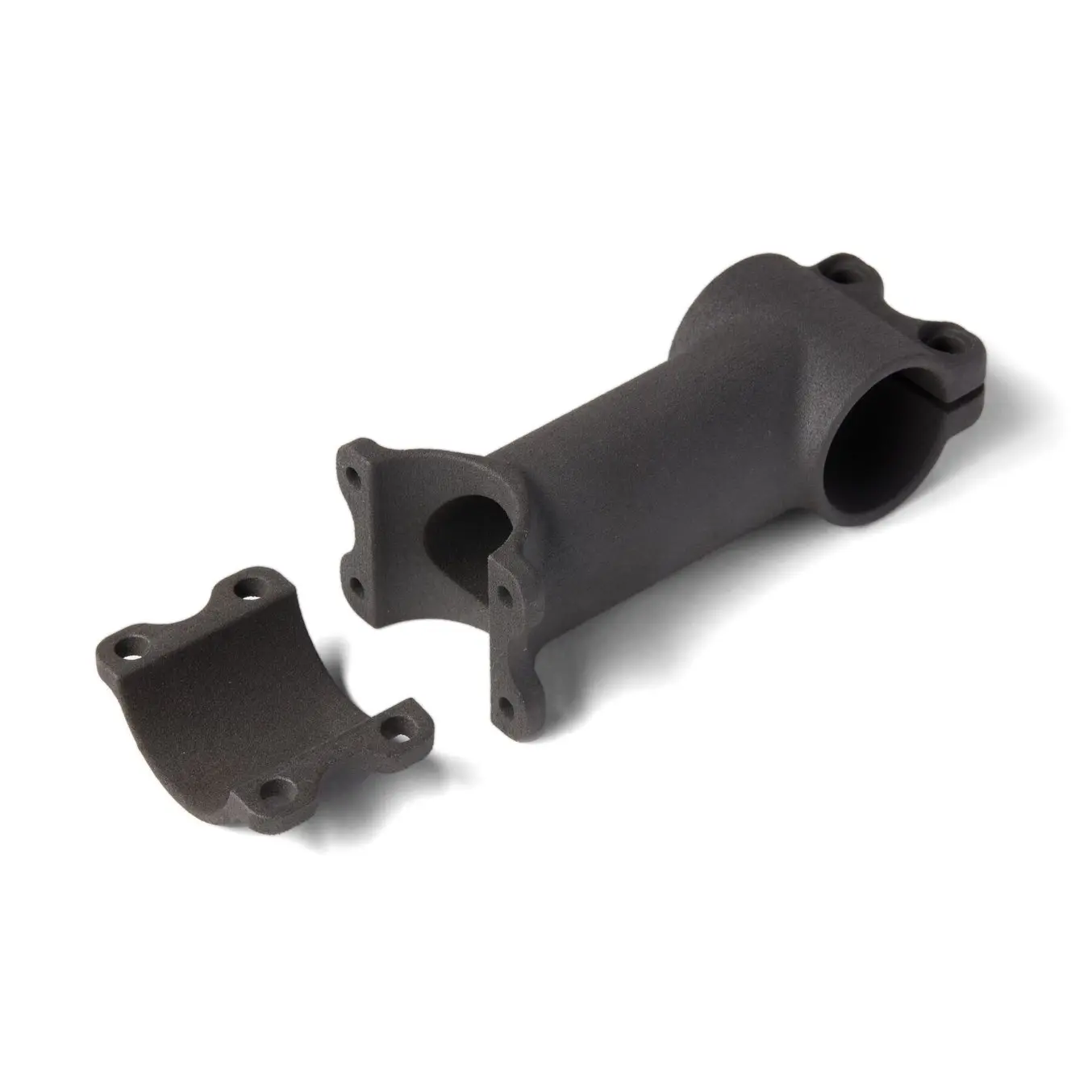
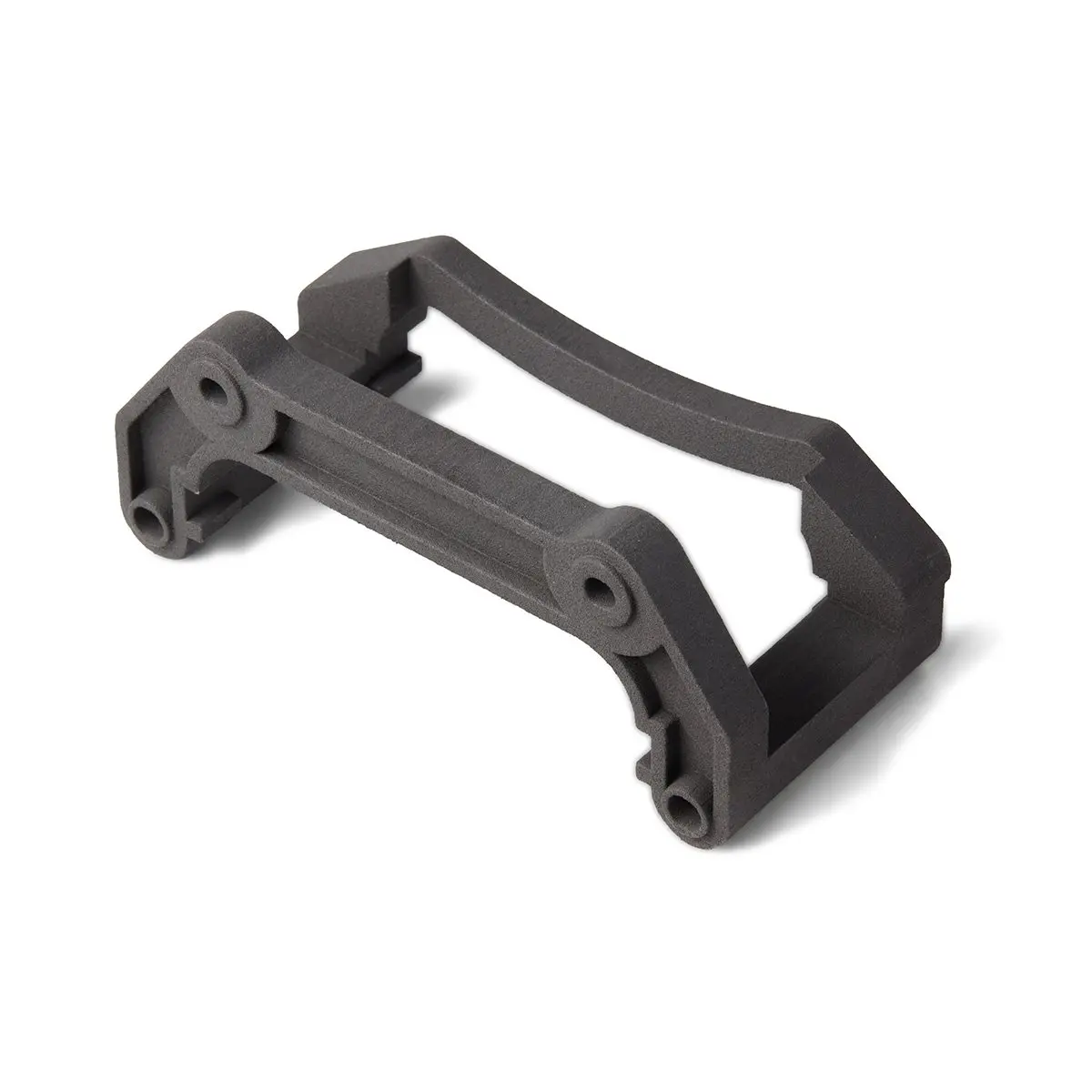
Nylon 11 CF Powder von Formlabs ist stark, leicht und hitzebeständig und damit ideal geeignet für Anwendungen in der Automobilindustrie, Luft- und Raumfahrt und der Fertigung.
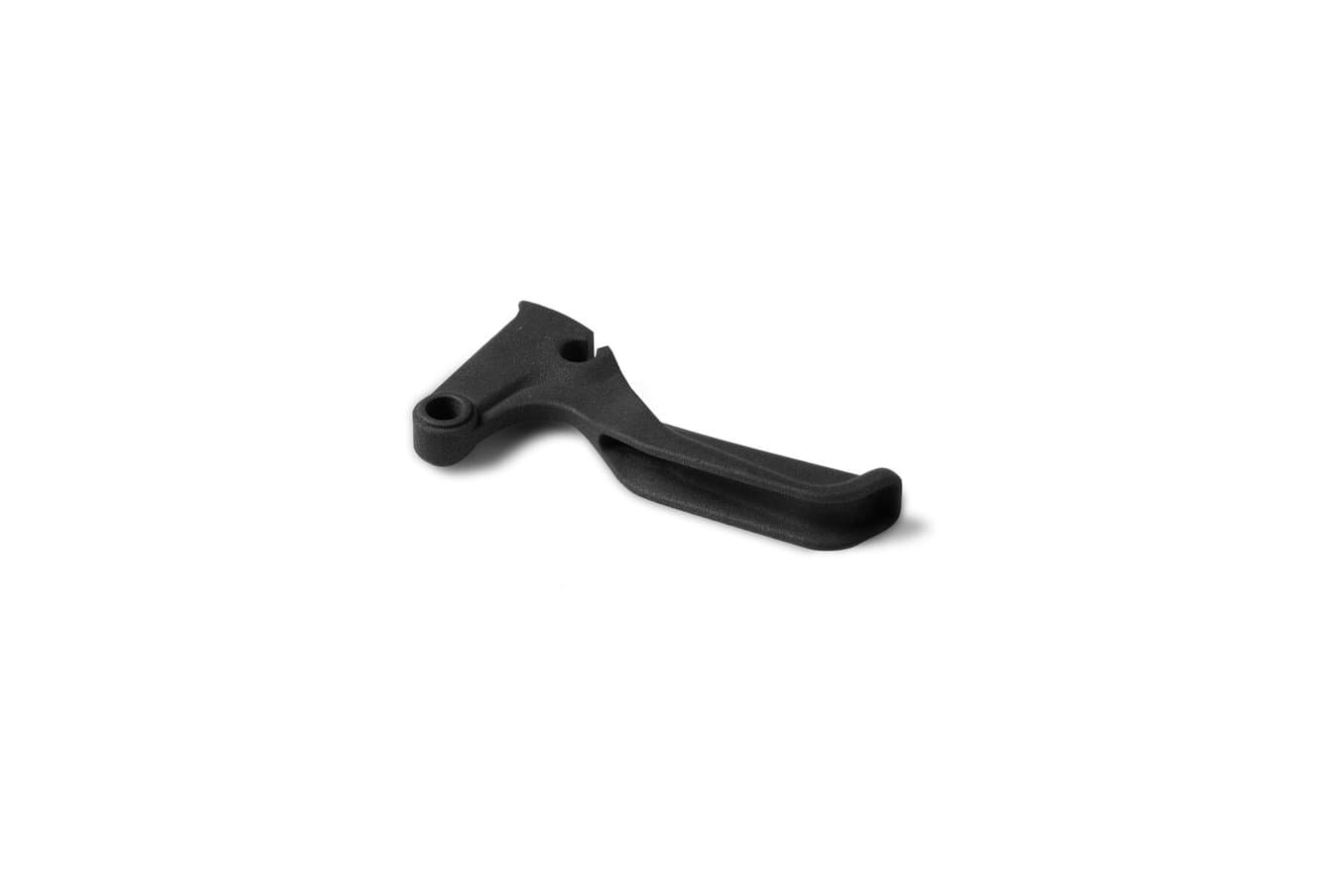
Kostenlosen Probedruck anfordern
Sehen und fühlen Sie selbst die Qualität von Formlabs. Wir senden Ihnen einen kostenlosen Probedruck an Ihren Arbeitsplatz.
Viele FDM-3D-Drucker können auch carbonfaserverstärktes Filament verarbeiten. Allerdings ist der Druck mit solchen Materialien komplizierter als mit standardmäßigen ABS- oder PLA-Filamenten, da sie häufig Blockierungen verursachen und aufgrund des Verschleißeffekts des abrasiven Filaments auf die Kupferdüsen den Wartungsaufwand steigern. Es sind auch FDM-3D-Drucker speziell für Filamente mit Carbon-Kurzfasern erhältlich, allerdings zu einem deutlich höheren Preis.
Der größte Nachteil des 3D-Drucks mit zerkleinerten Kohlenstofffasern liegt sowohl beim SLS- als auch beim FDM-Verfahren darin, dass diese Methoden zwar 3D-Druckteile mit höherer Festigkeit ergeben, nicht aber echte Alternativen zu herkömmlichen CFK-Teilen mit verwobenen, durchgängigen Fasern. Des Weiteren tritt die größte Festigkeitssteigerung in der Dimension auf, in welcher das Teil beim Druck ausgelegt wird – bei SLS-Teilen also auf der X-Achse und bei FDM-Teilen auf der XY-Ebene. Traditionelle Verfahren zur Fertigung von Carbonteilen ermöglichen eine hohe Festigkeit in mehreren Dimensionen, nämlich durch genaue Planung und Platzierung der verschiedenen CFK-Platten vor dem Formprozess.
3D-Druck mit Endlosfasern
Auf einigen spezialisierten FDM-3D-Druckern ist der 3D-Druck mit durchgängigen Kohlenstofffasern verfügbar, die als Endlosfasern bezeichnet werden. Die so produzierten Teile kommen traditionell gefertigten CFK-Teilen hinsichtlich ihrer Festigkeit nahe, allerdings genau wie beim Kurzfaser-FDM-Druck nur auf der XY-Ebene. Beim Druckverfahren mit Endlosfasern werden durchgängige Stränge Kohlenstofffaser mit dem Thermoplast vermischt. Dabei können die Stränge strategisch eingesetzt werden, um bestimmte Ebenen oder Achsen zu verstärken. Bei dieser Methode kommt entweder eine duale Extrusionsdüse zum Einsatz, um eine Kombination aus Carbonfasersträngen und Polymermaterial abzugeben, oder aber eine 2-in-1-Lösung, bei der eine Düse den Carbonfaserstrang abgibt, während die andere das Filament erhitzt und extrudiert.
Der 3D-Druck mit Carbon-Endlosfasern liefert eine mit traditionell gefertigten Carbonteilen vergleichbare Alternative, wenn auch bei eingeschränkter Gestaltungsfreiheit. Obwohl diese Teile eine unglaubliche Festigkeit aufweisen, tritt diese nur in der XY-Ebene auf, sodass die Druckteile so ausgerichtet werden müssen, dass diese mit der Richtung der Krafteinwirkung übereinstimmt. Für Designs, die das zulassen, ist diese Methode eine gute Option, um Aluminiumteile zu ersetzen und robuste Fertigungshilfen oder Endverbrauchsteile herzustellen.
Vergleich: Konventionelle Fertigung von Carbonteilen und 3D-Druckprozesse mit Carbonfaser
Handlaminierung | Prepreg-Laminierung | Resin Transfer Molding | FDM-3D-Druck mit Kurzfasern | SLS-3D-Druck mit Kurzfasern | FDM-3D-Druck mit Endlosfasern | |
---|---|---|---|---|---|---|
Hersteller und Modell | Verschiedene | Verschiedene | Verschiedene | Markforged Onyx, Markforged X3 | Formlabs Fuse 1+ 30W | Markforged Mark Two, Desktop Metal Fiber, Markforged X7 |
Genauigkeit | ★★★☆☆ | ★★★★★ | ★★★★★ | ★★★☆☆ | ★★★★★ | ★★★☆☆ |
Oberflächengüte | ★★★☆☆ | ★★★★★ | ★★★★★ | ★★★☆☆ | ★★★★☆ | ★★★☆☆ |
Gestaltungsfreiheit | ★★★☆☆ | ★★★☆☆ | ★★★☆☆ | ★★★★☆ | ★★★★★ | ★★★★☆ |
Leichtigkeit | ★★★★★ | ★★★★★ | ★★★★★ | ★★★★☆ | ★★★★☆ | ★★★★☆ |
Festigkeit | ★★★★★ | ★★★★★ | ★★★★★ | ★★★☆☆ | ★★★☆☆ | ★★★★★ |
Dimensionen der Festigkeit | XYZ | XYZ | XYZ | XY | X(Y) | XY |
Durchsatz | ★☆☆☆☆ | ★★★☆☆ | ★★★★★ | ★★★☆☆ | ★★★★☆ | ★★★☆☆ |
Ausrüstungskosten (spezifisch) | Unterschiedlich, ab < 100 € | Unterschiedlich, ab < 3000 € | Unterschiedlich, normalerweise > 100 000 € | Desktop-Lösungen sind ab 5000 € erhältlich, industrielle Lösungen ab ca. 40 000 € | Komplette industrielle Lösungen ab 36 093 € | Desktop-Lösungen sind ab 20 000 € erhältlich, industrielle Lösungen ab ca. 70 000 € |
Kosten pro Teil | $$$$ | $$$ | $$ | $$$ | $$ | $$$$ |
Ideale Anwendungsbereiche | Maßgefertigte Hochleistungsprodukte, Einsteiger-Arbeitsprozess | Kleine bis mittlere Produktionsvolumen | Großserienproduktion | Schnelle Iterationen, starke 3D-Druckteile | Schnelle Iterationen, komplexe Geometrien, Kleinserienfertigung starker 3D-Druckteile | Schnelle Iterationen, 3D-Druckteile mit der Festigkeit herkömmlicher CFK-Teile (in der XY-Ebene) |
Vorteile | Hohe Festigkeit Niedrige Ausrüstungskosten | Hohe Festigkeit | Hohe Festigkeit Präzision und Reproduzierbarkeit Möglichkeiten zur Automatisierung | Erschwinglichkeit
Kein Werkzeugbedarf | Präzision und Reproduzierbarkeit Gestaltungsfreiheit Kein Werkzeugbedarf | Hohe Festigkeit Kein Werkzeugbedarf |
Nachteile | Arbeitsintensiv Hohe Qualität schwer zu halten | Arbeitsintensiv | Hohe Werkzeug- und Ausrüstungskosten | Anisotrope Festigkeit Geringere Festigkeit Schwierig zu drucken | Anisotrope Festigkeit Geringere Festigkeit | Anisotropic strength |
Wie fest sind 3D-gedruckte CFK-Teile?
Die mechanischen Eigenschaften von 3D-gedrucktem kohlenstofffaserverstärktem Kunststoff übertreffen fast jeden anderen 3D-gedruckten Kunststoff hinsichtlich ihrer Festigkeit und Temperaturbeständigkeit. Sehen wir uns an, welche Leistung Carbon-Kurzfasern verglichen mit Endlosfasern und sonstigen gängigen Materialien liefern.
Fertigungsverfahren | SLS - Kurzfasern | FDM - Kurzfasern | FDM - Endlosfasern | FDM - Endlosfasern | Spritzguss | Guss oder Zerspanung |
---|---|---|---|---|---|---|
Material | Formlabs Nylon 11 CF Powder | Kohlenstofffaserverstärktes Nylonfilament | Nylon-6-Filament + Kohlenstofffaser | PEEK-Filament + Kohlenstofffaser | ABS | Aluminum |
Zugmodul (GPa) | 1.6 - 5.3 | 2.4 | 60 - 100 | 145 | 2.3 | 70 |
Maximale Zugfestigkeit (MPa) | 38 - 69 | 40 | 800 - 1000 | 2400 | 39 | 310 |
Biegemodul (GPa) | 4.2 | 3.0 | 51 - 71 | 124 | 2.4 | 70 |
Biegebruchfestigkeit (MPa) | 110 | 71 | 540 - 800 | 1300 | 74 | 310 |
Bruchdehnung | 5 - 15% | 25% | 1.5% | N/A | 6 - 15% | N/A |
Schlagzähigkeit nach IZOD (J/m) | 74 | 330 | 960 | N/A | 200 | N/A |
Wärmeformbeständigkeitstemperatur bei 0,45 MPa (°C) | 188 | 145 | 105 | N/A | 70 - 107 | N/A |
Anwendungen für 3D-gedruckte CFK-Teile
Ihre hohe Festigkeit und Leichtigkeit sowie die Beständigkeit gegenüber Stößen, Hitze und Chemikalien machen 3D-Druckteile aus kohlenstofffaserverstärktem Kunststoff zur idealen Lösung für eine Vielzahl von Anwendungen, für die 3D-Druck bisher überhaupt nicht infrage kam. 3D-Druckteile aus Carbon halten selbst der Hitze stand, die in Motorkomponenten für die Automobilindustrie oder Luft- und Raumfahrt entsteht, dienen als Ersatz für zerspante Aluminiumteile und Fertigungshilfen und ermöglichen die Produktion langlebiger, stoßfester Ausrüstung.
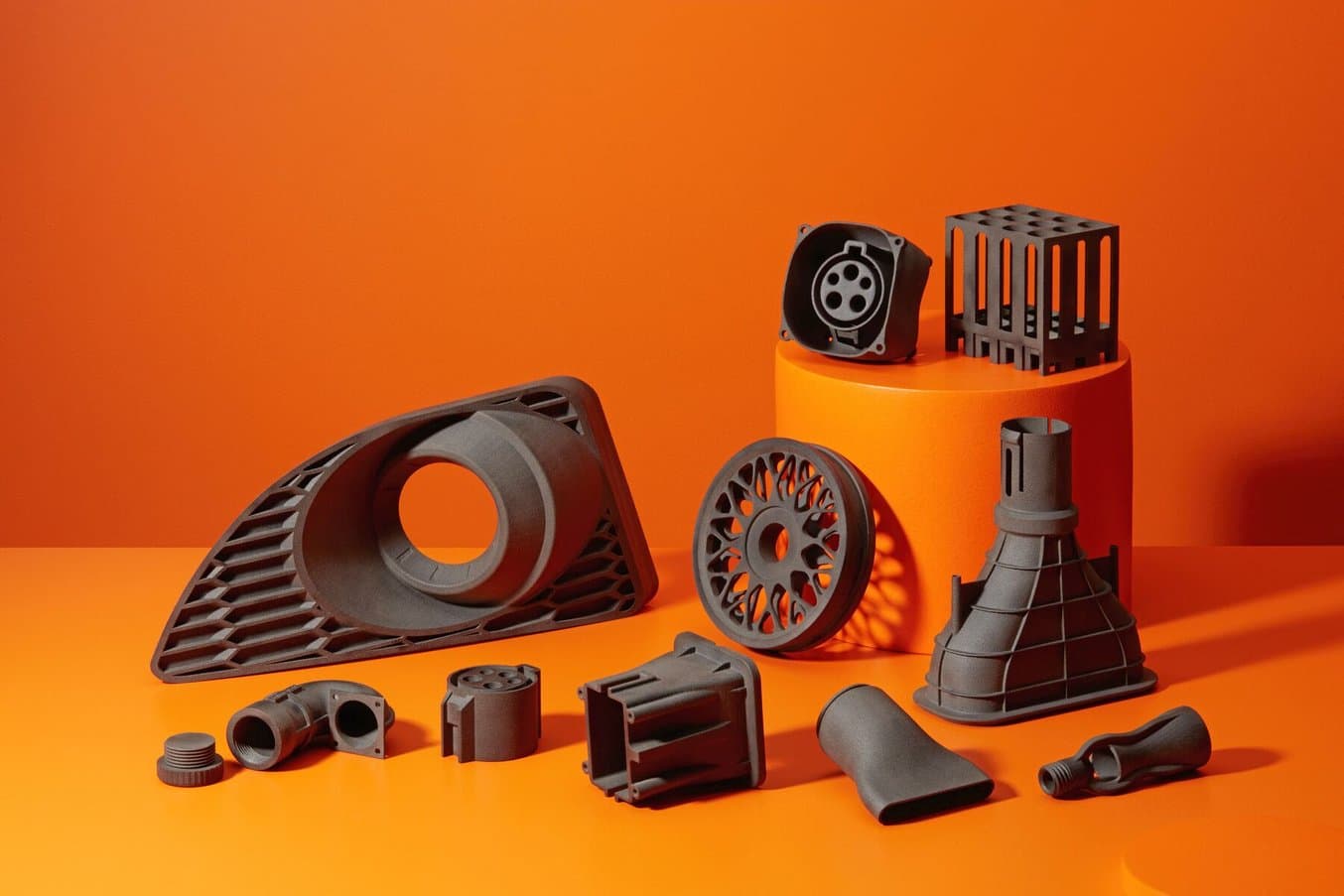
Kohlenstofffaserverstärkte 3D-Druckteile eignen sich ideal für das Rapid Prototyping, die Herstellung verschleißbeständiger und haltbarer Fertigungshilfen wie Halterungen und Vorrichtungen sowie für die Kleinserienfertigung fester Endverbrauchsteile mit komplexen Geometrien.
3D-Drucktechnologien haben in den Bereichen Design und Fertigung neue Möglichkeiten eröffnet, und der 3D-Druck kohlenstofffaserverstärkter Kunststoffe bringt sie noch einen Schritt weiter: Er ermöglicht der Automobilindustrie, der Luft- und Raumfahrt, der Rüstungsindustrie und der Fertigung die Produktion hochfester, temperaturbeständiger Teile mit hoher geometrischer Flexibilität, und das in kürzester Zeit und höchst effizient. Indem traditionelle Zerspanungs- und Gussverfahren umgangen werden, können kundenspezifische oder maßgefertigte Teile, Ersatzteile und funktionsfähige Prototypen viel leichter hergestellt werden. Da die zusätzliche Festigkeit bei kohlenstofffaserverstärkten 3D-Druckteilen nur auf einer Ebene der Geometrie auftritt, stellen sie zwar keinen vollkommenen Ersatz für herkömmliche Fertigungstechniken dar, sind aber dennoch fester als die meisten anderen Kunststoffe und damit von überaus großem Wert für zahlreiche Anwendungsbereiche.
Welches das passende Verfahren zur Herstellung von CFK-Teilen über Umformung oder direkten 3D-Druck ist, hängt im hohen Maße von der jeweiligen Anwendung ab und wird von Faktoren wie Teildesign, Produktionsvolumen und mehr beeinflusst. Der SLS-3D-Druck mit Carbon-Kurzfasern bietet einen guten Kompromiss für Hersteller, die Teile mit hoher Festigkeit benötigen, jedoch nicht zwingend in dem Maße, das mit konventionell geformten Carbonteilen erreicht wird.
Der Fuse 1+ 30W von Formlabs mit Nylon 11 CF Powder erlaubt es auch Unternehmen mit eingeschränktem Budget und engem Zeitplan, schnell zu iterieren und Endverbrauchsteile mit hoher Festigkeit und fortgeschrittenen mechanischen Eigenschaften zu produzieren, die über herkömmliche Kunststoffe hinausgehen. Zudem können Hersteller die Teile Funktionstests unterziehen und Designänderungen anschließend ganz einfach in der CAD-Datei vornehmen, womit die Leistung der Produkte gesteigert wird und diese schneller auf den Markt gebracht werden.
Fordern Sie einen kostenlosen Probedruck an, um sich selbst ein Bild von der Qualität und Festigkeit eines SLS-3D-gedruckten Teils mit einem Gehalt zerkleinerter Kohlenstofffasern zu machen, oder sprechen Sie mit einem Mitglied unseres Expertenteams, um die richtige Lösung für Ihre Anwendung zu finden.