Wie die US Naval Academy 3D-Druck als Teil der Ausbildung der nächsten Generation von Marineoffizieren nutzt
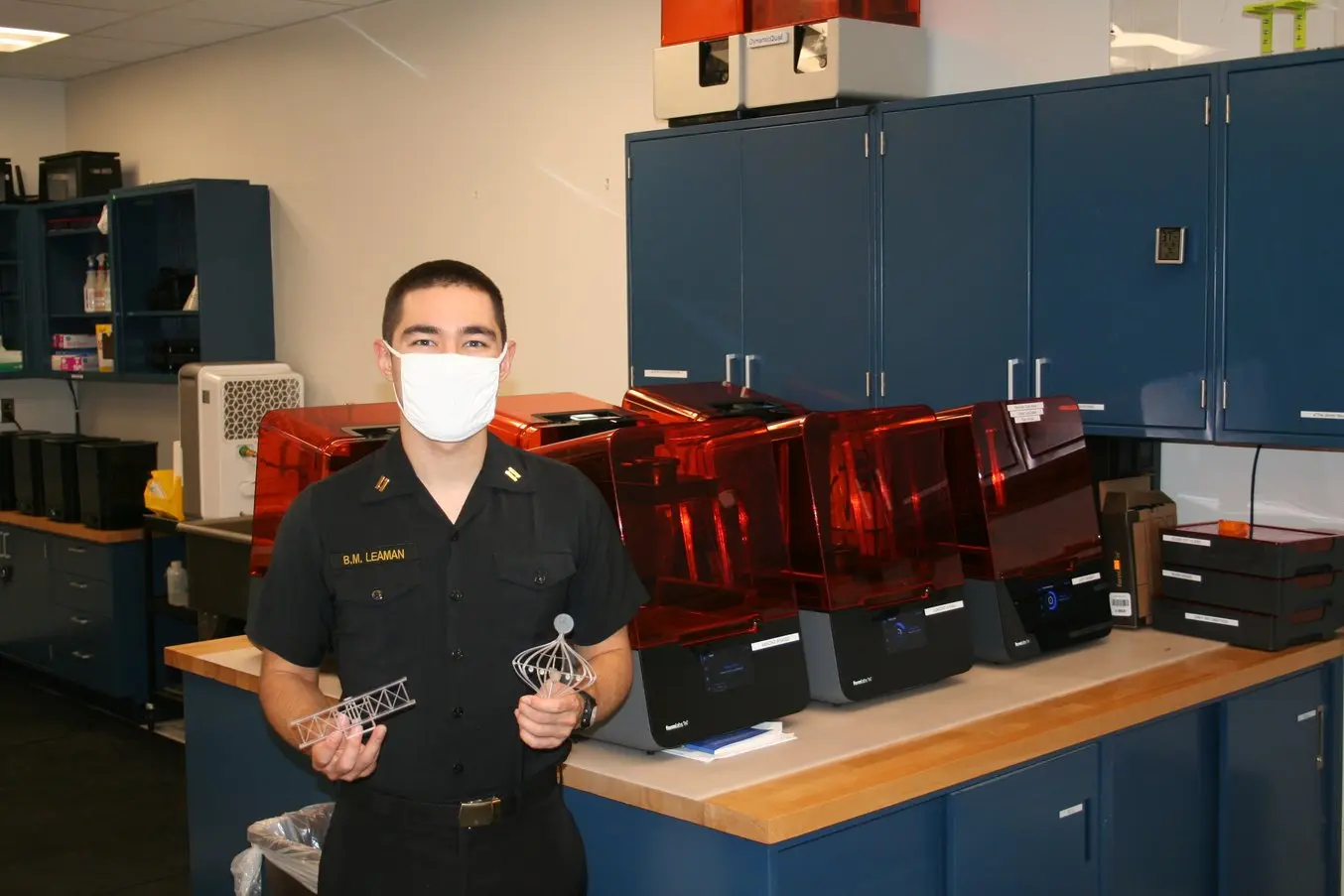
Midshipman First Class Ben Leaman, Student mit Hauptfach Schiffstechnik an der USNA, zeigt seine preisgekrönten Drucke aus dem Formlabs Form 3 bei den AM Olympics 2021.
Die Bundesrichtlinien zur Integration der additiven Fertigung bei den US-amerikanischen Streitkräften werden zunehmend klarer und ausdrücklicher, da die weltweite Krise Hersteller dazu zwingt, Alternativen und reaktionsschnellere Wege der Produktion zu beschreiten. Um das Militärpersonal an diesen Technologien auszubilden, legen die Bildungskräfte der Studiengänge bei den Streitmächten den Fokus zunehmend auf den 3D-Druck. Der Assistenzprofessor an der United States Naval Academy (USNA) Captain Brad Baker ist dabei schon einen Schritt weiter. Er konzentriert sich bereits seit Jahren auf verschiedene additive Fertigungsverfahren.
Durch den MakerSpaceUSNA kommen alle Studierenden der United States Naval Academy ungeachtet ihres Studiengangs in Kontakt mit den additiven Fertigungstechnologien. Beim Ingenieurstudiengang reicht das Ganze noch etwas weiter. Dort werden die Studierenden auf die Arbeit als Schiffstechniker*innen und Führungskräfte in der fortgeschrittenen Fertigung und im Verteidigungswesen vorbereitet. Diese Ausbildungsstufe wird durch eine Flotte an 3D-Druckern ermöglicht. Dazu zählen neben den Geräten anderer Hersteller auch der Form 3, Form 3B, Form 3L und Fuse 1 von Formlabs.
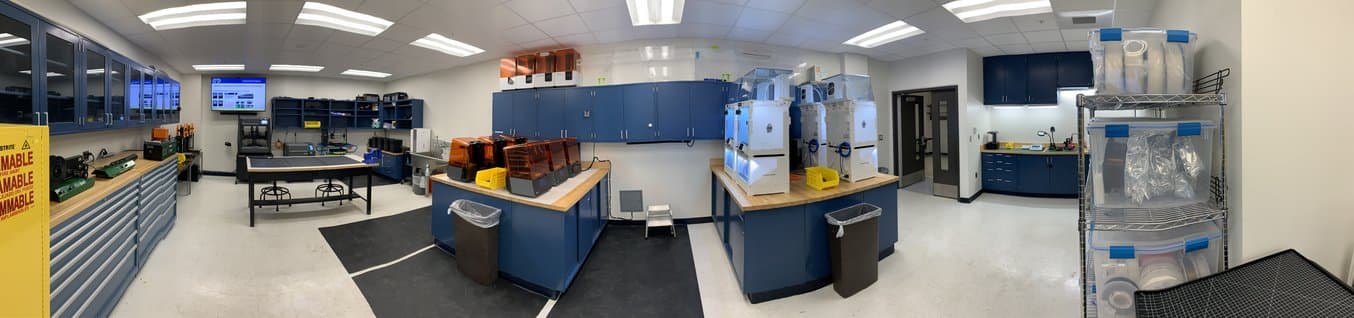
Captain Baker ist der Labordirektor für Materialwissenschaften und dessen Ausrüstung in der Maschinentechnikabteilung und der Maschinenbau- und Waffenschule der US Naval Academy (USNA). Dort überwacht er alles von der Mikroskopie über die Materialentwicklung bis zur heutigen additiven Fertigung. Wir haben mit ihm über seinen Ansatz zum Unterricht fortgeschrittener Fertigungskenntnisse gesprochen, über bundesweite und abteilungsspezifische Vorgaben bei diesen Technologien und über einige der Projekte, an denen die Studierenden im Makerspace arbeiten.
Aller Anfang ist schwer
Captain Baker rief den MakerSpaceUSNA vor fünf Jahren ins Leben, nachdem er als technischer Berater an einem Maschinenbauprojekt der Studierenden beteiligt war. Während seiner Beratertätigkeiten bei einem Designprojekt für ein vom U-Boot aus eingesetztes unbemanntes Luftfahrzeug erkannte Captain Baker, dass der iterative Prozess der Studierenden und somit ihre Lernkurve unter dem mangelndem Zugang zu Fertigungsgeräten litt. Obwohl eine Werkstatt für die Projekte der Studierenden zur Verfügung stand, war es Individuen oder Teams nicht möglich, mehr als drei oder vier Iterationen pro Jahr durchzuführen.
„Beim Design der Teile und der Skalierung für einen kleinen Raum leisteten die Studierenden großartige Arbeit, aber die Fertigung der Teile führte grundsätzlich zu einer sehr langen Verzögerung, da sie darauf keinen Einfluss hatten. Im Zuge eines Jahres erreichten die Studierenden nur drei oder vier Iteration. Das ist eine äußerst langsame Prototypenentwicklung. Dabei verpassen die Studierenden die Gelegenheit, tatsächlich etwas herzustellen. Diese Lücke wollte ich unbedingt schließen. Ich wollte eine Lösung finden, damit die Teile schneller fertig werden, und die Studierenden in den Fertigungsprozess miteinbeziehen.“
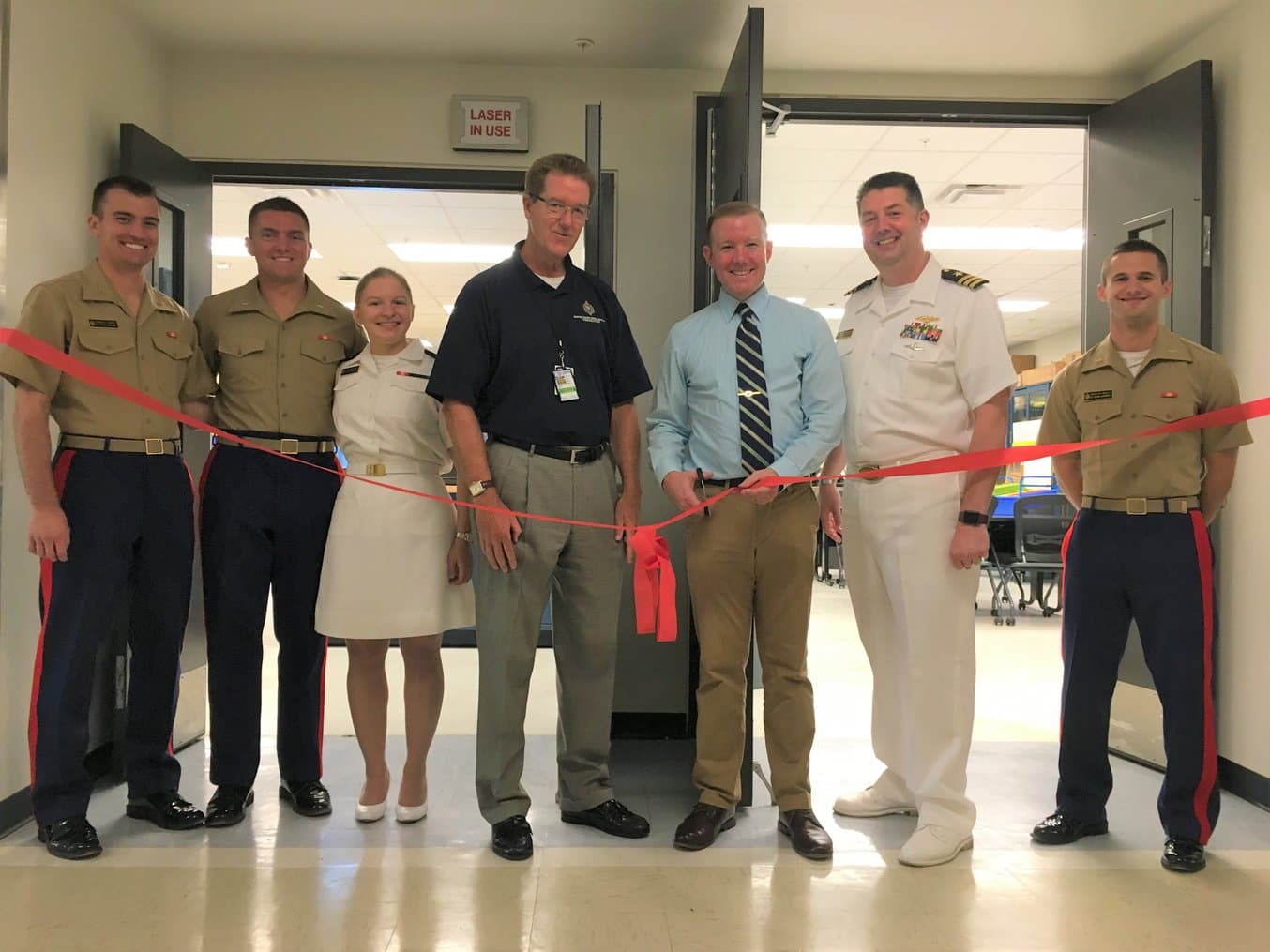
Captain Brad Baker und sein Kollegenkreis am Eröffnungstag des MakerSpaceUSNA
Captain Baker war zwar nicht der erste Dozent an der Hochschule, der Studierenden 3D-Drucker für ihre Projekte anbot, er brachte jedoch sämtliche Ressourcen für Design und Fertigung an einen zentralen Standort, indem er den MakerSpaceUSNA gründete. Als gerade einmal ein paar Schmelzschichtungsdrucker (FDM, Fused Deposition Modeling) vorhanden waren, begann er bereits, die Geräte in den Lehrplan des Maschinenbaustudiums zu integrieren und sie den Studierenden für ihre Abschlussprojekte bereitzustellen.
„Es war auf Anhieb ein Erfolg – die Studierenden waren sofort involviert, interessiert und die Nachfrage war groß. Wir haben mit zwei Druckern angefangen und dann schnell die CAD-Kapazitäten erhöht und den 3D-Druck ausgebaut. Und wir waren der erste Standort am Campus, bei dem leistungsstarke Computer, leistungsfähiges CAD und erstklassige 3D-Drucker zusammenkamen. Das alles stand den Studierenden direkt zur Verfügung.“
Handfeste Lernerfolge
Bei vielen Programmen schreckt die Laborverwaltung aufgrund der hohen Anschaffungskosten davor zurück, Studierenden vollen Zugriff zu den Geräten zu gewähren. Captain Baker hingegen hat keine Bedenken bezüglich Fehlschlägen und Unordnung. Ganz im Gegenteil, er spricht sich dafür aus.
„Ich möchte, dass die Studierenden Fehldrucke erleben. Bei so etwas stellt sich die größte Lernerfahrung ein. Das kommt vielleicht nicht so gut an und hat auch einen gewissen Preis, aber so lernt es sich am besten. Bis zu 100 Leute nutzen unsere Einrichtung pro Semester. Das ist eine ganze Menge. Also muss ich mich darauf verlassen, dass sie es selbst lernen. Falls Probleme mit der Haftung oder den Stützstrukturen auftreten, dann lernen sie daraus, dass sie mehr Stützen oder bessere Haftung brauchen oder dass sie die Größe oder Ausrichtung des Objekts ändern müssen. So sieht die Herausforderung aus. Und mit Worten allein lässt sich das nur schwer beibringen.“
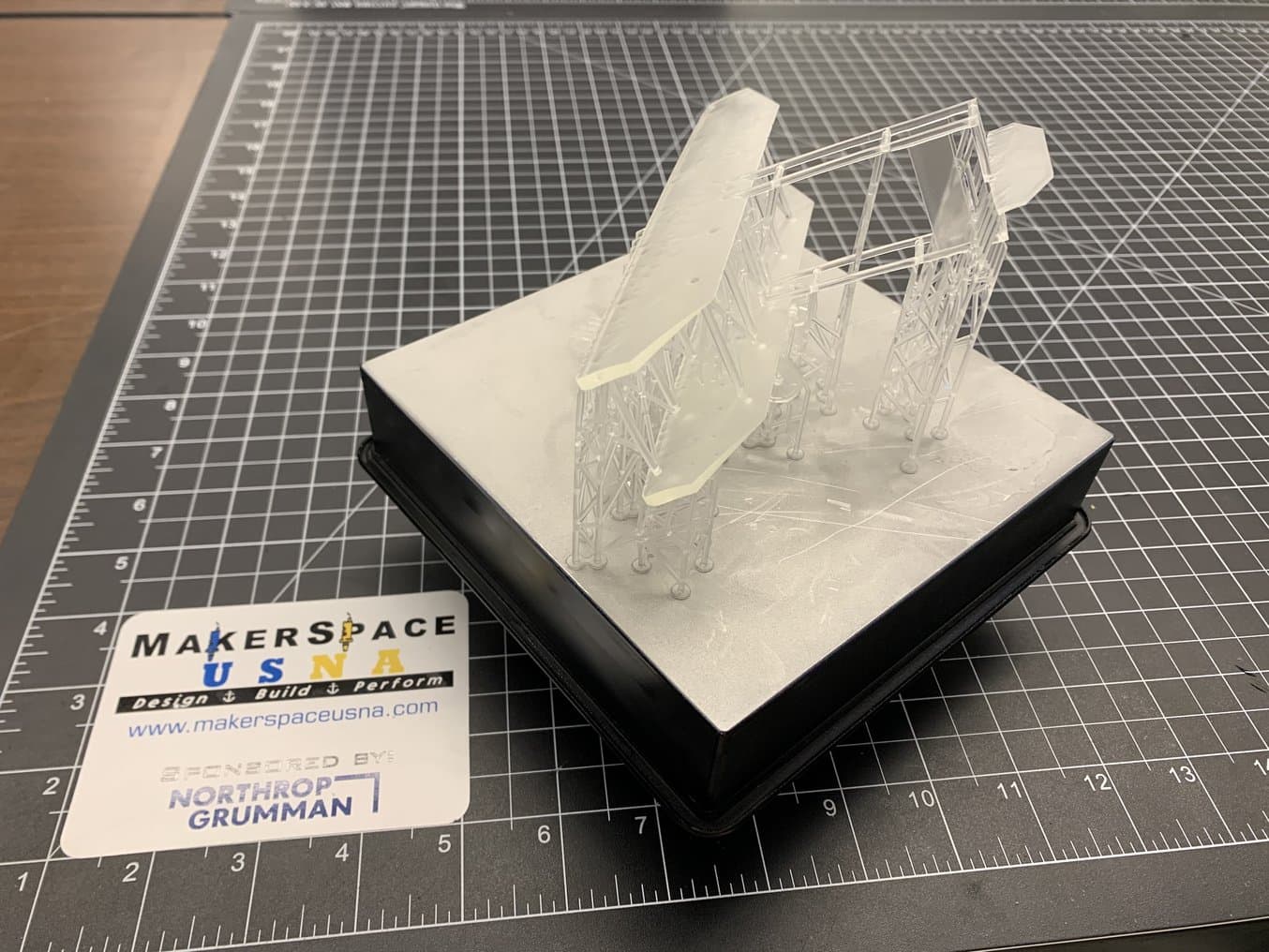
Ein 3D-gedrucktes Modell des Flugzeugs der Gebrüder Wright, gedruckt aus Clear Resin mit dem Form 3
Um den Zeit- und Materialverlust zu verringern, hat Captain Baker jüngst ein Stufenmodell implementiert. Zu Beginn ihres Ingenieurstudiums lernen Studierende zunächst, CAD-Software zu benutzen und FDM-Drucker zu bedienen, gehen dann zur Stereolithografie (SLA) über und gelangen schließlich zum selektiven Lasersintern (SLS). Mittlerweile lernen sie sogar 3D-Scanverfahren, sodass sie mithilfe aller erlernten Hilfsmittel komplette Projekte im Reverse Engineering durchführen.
„Einen Makerspace aufzubauen und am Laufen zu halten, mit nur drei Leuten, war bei 30 3D-Druckern und 100 Nutzern schon eine Herausforderung. Aber wie mich meine Navy-Ausbildung gelehrt hat, ist die beste Vorgehensweise die Ausbildung und Befähigung der Nutzer im Umgang mit der Einrichtung. Wir haben eine Hierarchie für den 3D-Druck. Die Studierenden können sich bis zur Pulverbettfusionierung mit dem Fuse 1 und zu unseren Metalldruckern hocharbeiten, indem sie zunächst Fehlschläge erlernen.
Captain Brad Baker
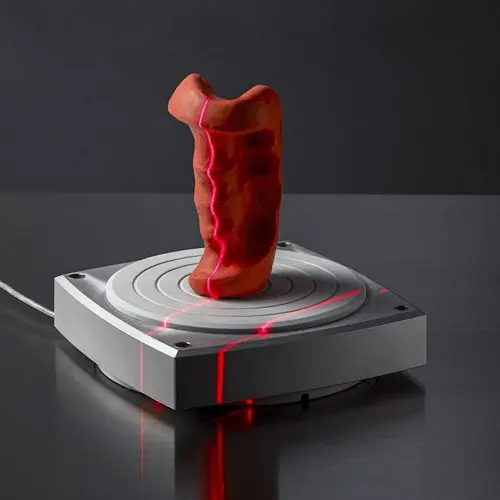
3D-Scannen für Reverse Engineering, Restaurationen und Metrologie
3D-Scan- und -Druckverfahren lassen sich zum Nachbau, zur Restauration, für Reverse Engineering, für verschiedene Messverfahren und viele weitere Anwendungen einsetzen. Laden Sie unser Whitepaper herunter, um diese Anwendungen kennenzulernen, und erfahren Sie, womit Sie beginnen sollten.
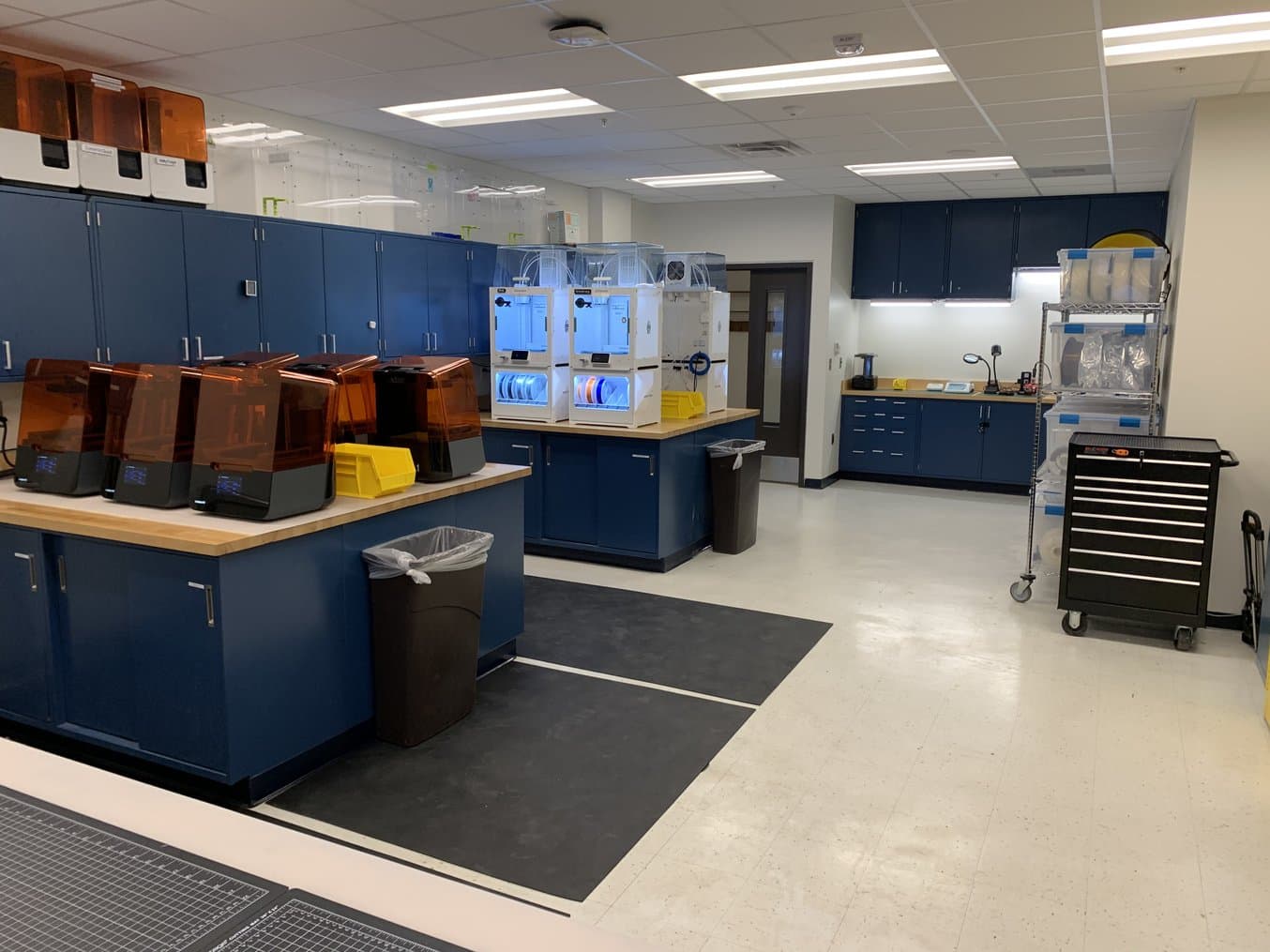
Der Bereich für Fortgeschrittene im MakerSpaceUSNA mit den Druckern Form 2 und Form 3 sowie einigen FDM-Druckern
Die Ausbildung und Befähigung der Nutzer*innen setzt auch den Geräten zu, die gleichbleibende Ergebnisse liefern sollen. Captain Bakers maßgeschneiderter Lehransatz führt die Studierenden von den fehleranfälligeren FDM-Systemen über die schrittweise robusteren SLA-Drucker mit niedrigen Fehlerraten zu den am leichtesten zu bedienenden aber am komplexesten aufgebauten SLS-Systemen.
„Die Fehlerquote bei unseren SLA-Druckern ist außergewöhnlich niedrig. Da sage ich immer: ‚Wartet, bis ihr es mit SLS zu tun bekommt.‘ Bei SLS [also beim Fuse 1] ist sie fast 0. So gut wie keine Fehldrucke. Die Materialeigenschaften sind gut und die Genauigkeit ist sehr gut.“
Captain Brad Baker
Neue Anwendungen dank Material Settings Editor
Neben der Vermittlung des Wissens um die Wahl der richtigen 3D-Drucktechnologie für die Projekte der Studierenden der Maschinenbautechnik dienen der Form 3, Form 3L und Fuse 1 auch zur Forschung.
Captain Baker ist im Herzen ein Materialwissenschaftler und experimentiert seit Jahren mit dem – wie er es nennt – „Doping“ der Kunstharze. Er erschafft neue Polymere mit Zusätzen wie Keramikpartikeln. Mit Formlabs' Softwarefunktion „Material Settings Editor“, also einem Editor für Materialeinstellungen, konnte der MakerSpaceUSNA bessere Kontrolle über die Einstellungen des Form 3 gewinnen, um mit Keramikharzen und anderen eigenentwickelten Mischungen zu experimentieren.
„Der Material Settings Editor hat uns ein besseres Verständnis des Druckers vermittelt, wie man die verschiedenen Knöpfe und Hebel des Geräts richtig einstellt. Anfangs hatten wir ihn nur für ganz spezifische Anwendungen, weil wir Keramik verwenden wollten. Hochmütig wie wir waren, wollten wir ein thermoelektrisches Material erschaffen – eines, das unter Hitzefluss Strom produziert. Wir konnten keines für die additive Fertigung finden. Deshalb arbeiteten wir an verschiedenen Optionen, unser eigenes Material herzustellen.“
Erweiterung um den Fuse 1
Solche Forschungsprojekte sind oft Teil der Abschlussprojekte im Ingenieurstudium, was ja auch vor fünf Jahren den Anstoß gab zur Zentralisierung in Form des MakerSpaceUSNA. Doch obgleich die ursprüngliche Idee eine Richtung anstrebt, kann es am Ende in eine ganze andere laufen. So war es auch bei der Idee, sich einen Fuse 1 anzuschaffen. Captain Baker wollte die Materialexperimente und die Projektentwicklung um SLS bereichern. Dafür musste er einen Drucker zu einem erschwinglichen Preis und mit kompakter Stellfläche finden, der zuverlässig Präzisionsteile produziert.
„Wir haben den Fuse 1 aus ungewöhnlichen Gründen erworben, doch war es aus zahlreichen Zusatzgründen ein voller Erfolg. Der Drucker ist im Vergleich erstaunlich schnell. Er war ein großer Erfolg. Die Auflösung ist gut, die Maßgenauigkeit ist außergewöhnlich. Seine Maßgenauigkeit übertrifft alle anderen Drucker in unserem Bestand. Die Studierenden fragen mich oft, warum wir nicht mit dem Fuse 1 angefangen haben. Darauf erwidere ich dann: ‚man muss sich das Privileg des Fuse 1 erst verdienen.‘“
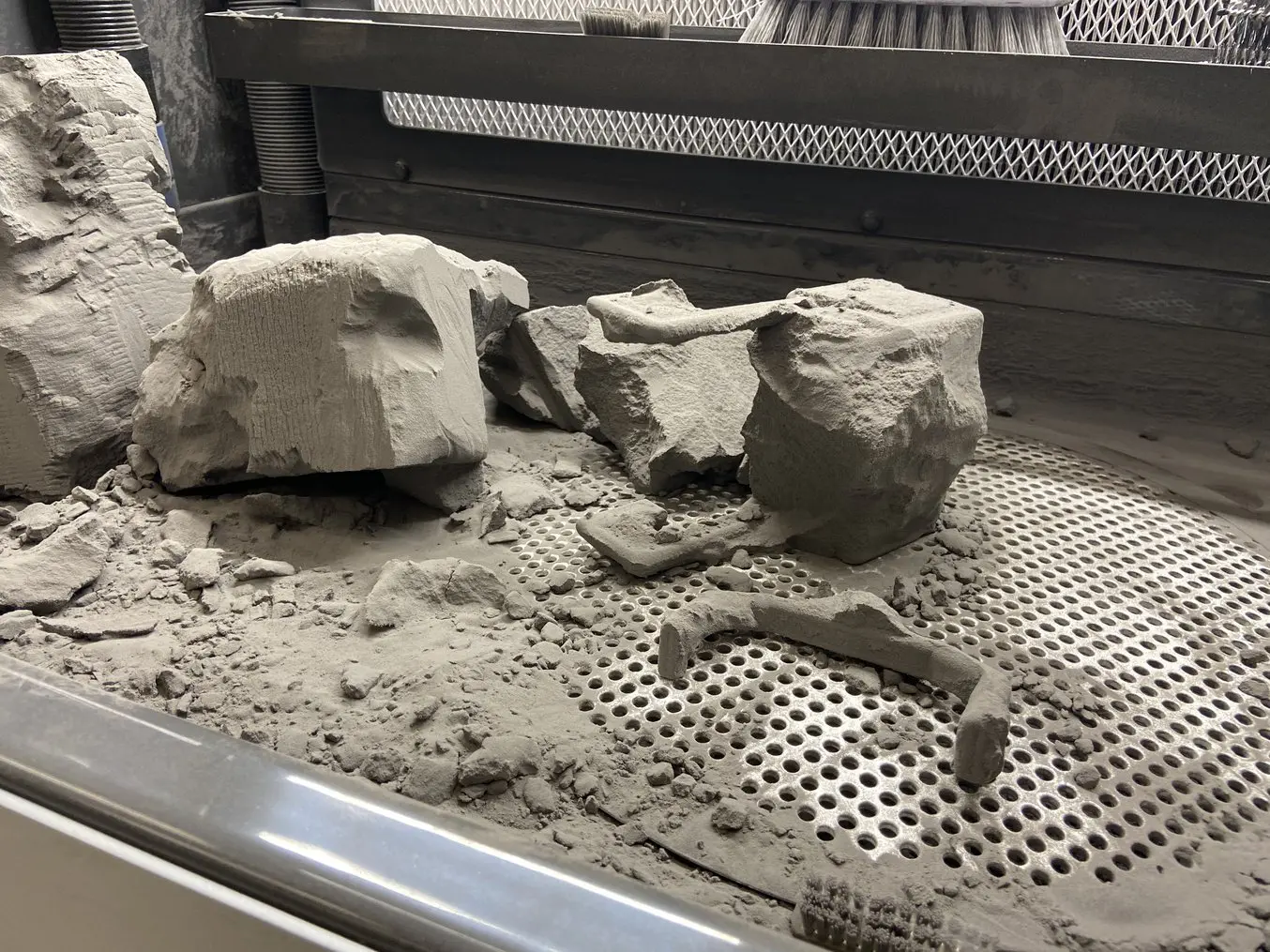
Teile aus Nylon 12 Powder bei der Nachbearbeitung im Fuse Sift
Obschon es anfänglich um neue Materialentwicklung ging, erwies sich die Arbeit mit Formlabs' Nylon 12 Powder für Captain Baker als unproblematisch und effizient. Er sagt: „Die Materialeigenschaften von Nylon 12 Powder sind äußerst ansprechend. Es ist leicht und dennoch stark. Wir haben Teile für unbemannte Luftfahrtzeuge gedruckt sowie einige Endverwendungsteile. Die Festigkeit ist gut mit genügend Duktilität. Es ist solide und was vielleicht am besten ist, es benötigt keine Stützstrukturen. Deshalb kann man damit auch schwierige Modelle sehr gut drucken.“
Vielfalt an Technologien, Materialien und Anwendungen
Eine Anwendung, die Captain Baker beim Aufbau seines Labors nicht auf dem Schirm hatte, war die Zahntechnik. In enger Zusammenarbeit mit dem Marine-Zahnprothetiker Captain Peter Barndt entwickelte er einen Arbeitsablauf aus Scan, digitalem Design und 3D-Druck für die zahnmedizinischen Bedürfnisse der Naval Academy. Mithilfe des Form 3 und Form 3B sowie Grey Resin, Draft Resin, Surgical Guide Resin und BioMed Clear Resin arbeiten Captain Baker und sein Kollege Captain Barndt am Druck von Mundschutzen, Knirscherschienen und selbst Bohrschablonen. Bei all den Studentenprojekten und den Nebenanwendungen wie der Zahntechnik laufen Captain Bakers Geräte ununterbrochen.
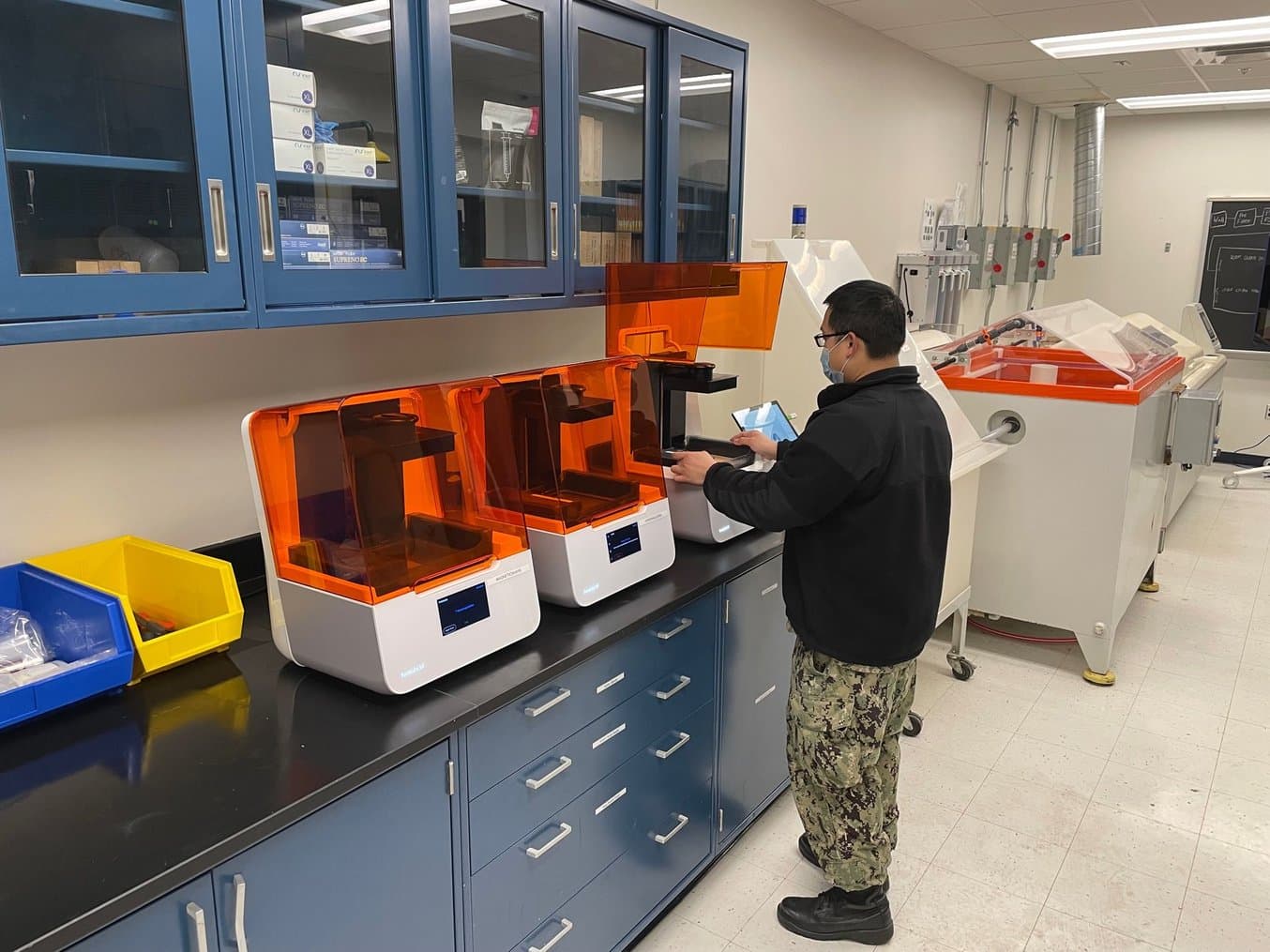
Ein Zahntechniker der USNA setzt einen Harztank in einen Form 3B ein.
Dank der hochwertigen, zuverlässigen Drucker mit FDM-, SLA- und SLS-Technologie gelingt im MakerSpaceUSNA etwas, das fast unmöglich erscheint: Man macht alle Studierenden der USNA mit drei verschiedenen additiven Fertigungsverfahren vertraut. Captain Baker geht durch seinen Ansatz einer praxisnahen Ausbildung und durch seine Philosophie, aus Misserfolgen zu lernen, noch einen Schritt weiter und bereitet seine Studierenden so auf eine Karriere im Dienst der US Navy und darüber hinaus vor.
„Es ist offensichtlich, dass die Navy Ambitionen bezüglich der additiven Fertigung hat. Informationen stehen der Öffentlichkeit zur Verfügung und es ist durchaus klar, dass das Marine Corps und die restlichen Institutionen des Verteidigungsministeriums sich in diese Richtung bewegen. Das Verteidigungsministerium will diese Technologie für sich nutzen, kann die Geräte aber nicht einfach mit auf die Einsätze zaubern. Erst muss eine Personalbasis aufgebaut werden, die das Ganze unterstützt. Und das fängt beim MakerSpaceUSNA an.“