3D-Druck macht den Weg frei: Wie TUM Boring robuste Bauteile für seine Tunnelbohrmaschine 3D-druckte
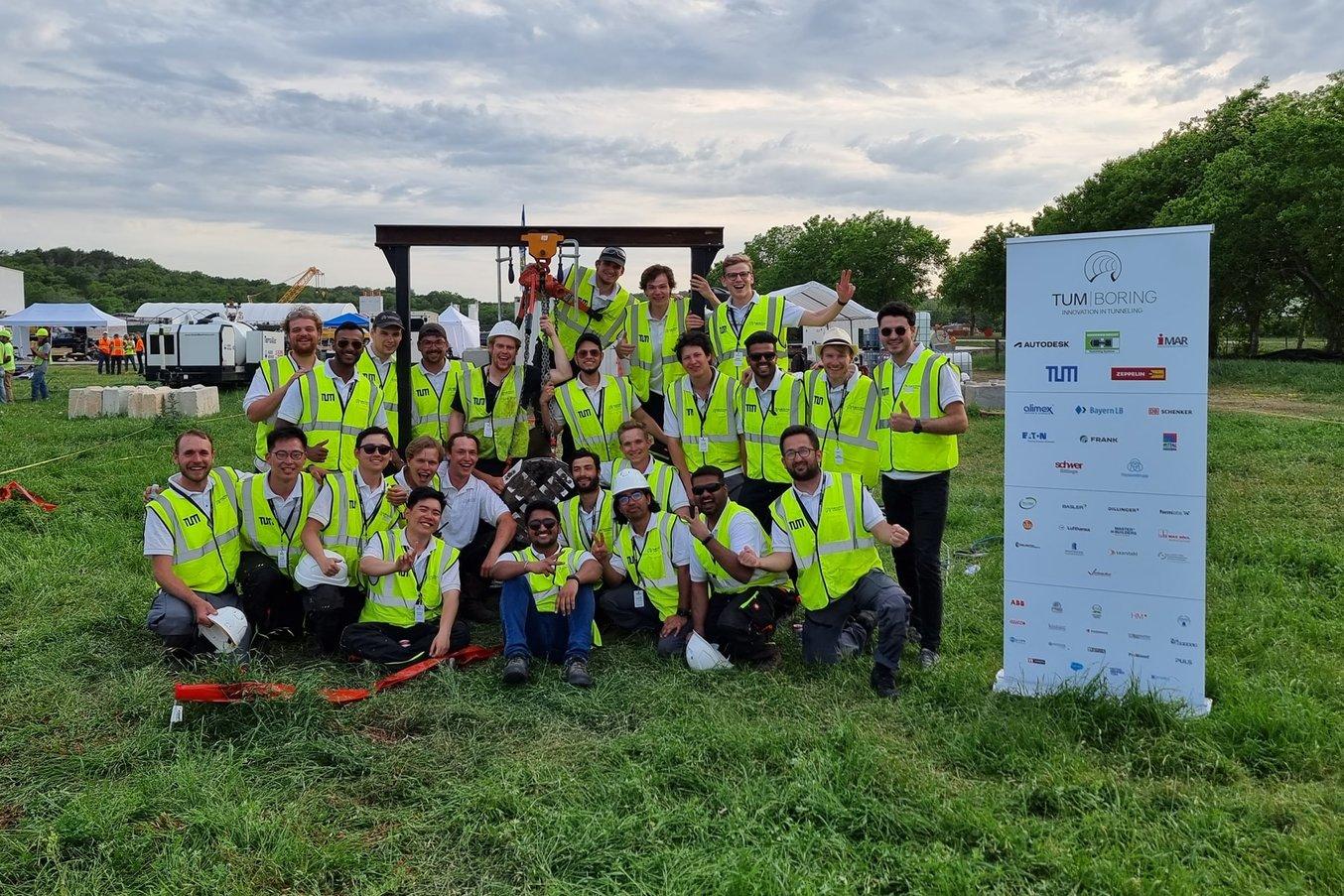
Das Team von TUM Boring in Bastrop, Texas, im April 2023.
TUM Boring ist eine Studierendenorganisation an der Technischen Universität München bestehend aus mehr als 60 Studierenden aus mehr als 16 Ländern. Die Gruppe schloss sich 2020 zusammen, um an dem Wettbewerb Not-a-Boring Competition 2021 teilzunehmen, der von Elon Musks Unternehmen The Boring Company (TBC) ausgerichtet wurde.
Das studentisch geführte Team hat sich der Zukunft der Mobilität verschrieben und sich zum Ziel gesetzt, eine der schnellsten Mikrotunnelbohrmaschinen (TBM) der Welt zu konstruieren, um den Fortschritt im Tunnelbau voranzutreiben. Der Wettbewerb bot den Studierenden den perfekten Schauplatz, um ihr Projekt mit anderen Innovationen rund um den Globus zu messen.
Nachdem TUM Boring den Wettbewerb 2021 gewann, erhielt das Team Zugang zu einem SLA-3D-Drucker (Stereolithografie), dem Form 3+, und hatte auch Gelegenheit, mit Druckteilen aus dem Fuse 1+ 30W zu arbeiten, einem 3D-Drucker für selektives Lasersintern (SLS). Die neu erworbene 3D-Drucktechnologie brachte merkliche Verbesserungen in den Arbeitsprozess des Teams. Vom Rapid Prototyping bis hin zum Druck von Endverbrauchsteilen sorgte der Form 3+ für einen deutlichen Wandel im täglichen Betrieb von TUM Boring und verhalf dem Team zu einem erneuten Sieg bei der Neuauflage von Not-a-Boring Competition im April 2023.
Entdecken Sie, wie TUM Boring sich den 3D-Druck zunutze machte, um starke, haltbare Bauteile für seine Tunnelbohrmaschine zu fertigen, und damit die Konkurrenz hinter sich zurückließ und zweimal in Folge den ersten Platz erlangte.
Rekordschnelle Designiteration mit SLA-3D-Druck
Den Form 3+ intern verfügbar zu haben machte es dem Team von TUM Boring möglich, seine Iterationskapazitäten entscheidend zu steigern. Um sich die Verbindungen der verschiedenen Rohre innerhalb der TBM zu verdeutlichen, druckte das Team auf dem Form 3+ Miniatur-Prototypen verschiedener Konzeptideen aus Grey Resin. So konnte es die mechanischen Zusammenhänge visualisieren, ohne direkt an der lebensgroßen Maschine arbeiten zu müssen, was Zeit sparte und den Prozess effizienter machte.
„Wir konnten ein Design skizzieren und schon am Abend einen Prototyp zur Begutachtung vor uns haben. Auf dessen Grundlage entwarfen wir dann Iterationen.“
Tom Luca Reinhardt, Vorstandsmitglied bei TUM Boring und einer der Leiter des Maschinenbauteams
Die Studierenden waren auch in der Lage, an einer 3D-gedruckten Schneidradkomponente mehrere Runden von Funktionstests durchzuführen. Indem sie aus Flexible 80A Resin Miniaturen des Schneidrads mit leicht unterschiedlichen Strukturen druckten, erhielten die Studierenden einen viel plastischeren Eindruck von ihrem Produkt, als es rein mithilfe von CAD-Programmen möglich gewesen wäre. Auch Tom Luca Reinhardt bestätigt: „Wir haben ja ein CAD-Programm, aber was man darin sehen kann, hat seine Grenzen. Es ist immer besser, das physische Produkt in den Händen zu halten und es sich aus verschiedenen Perspektiven ansehen zu können.“
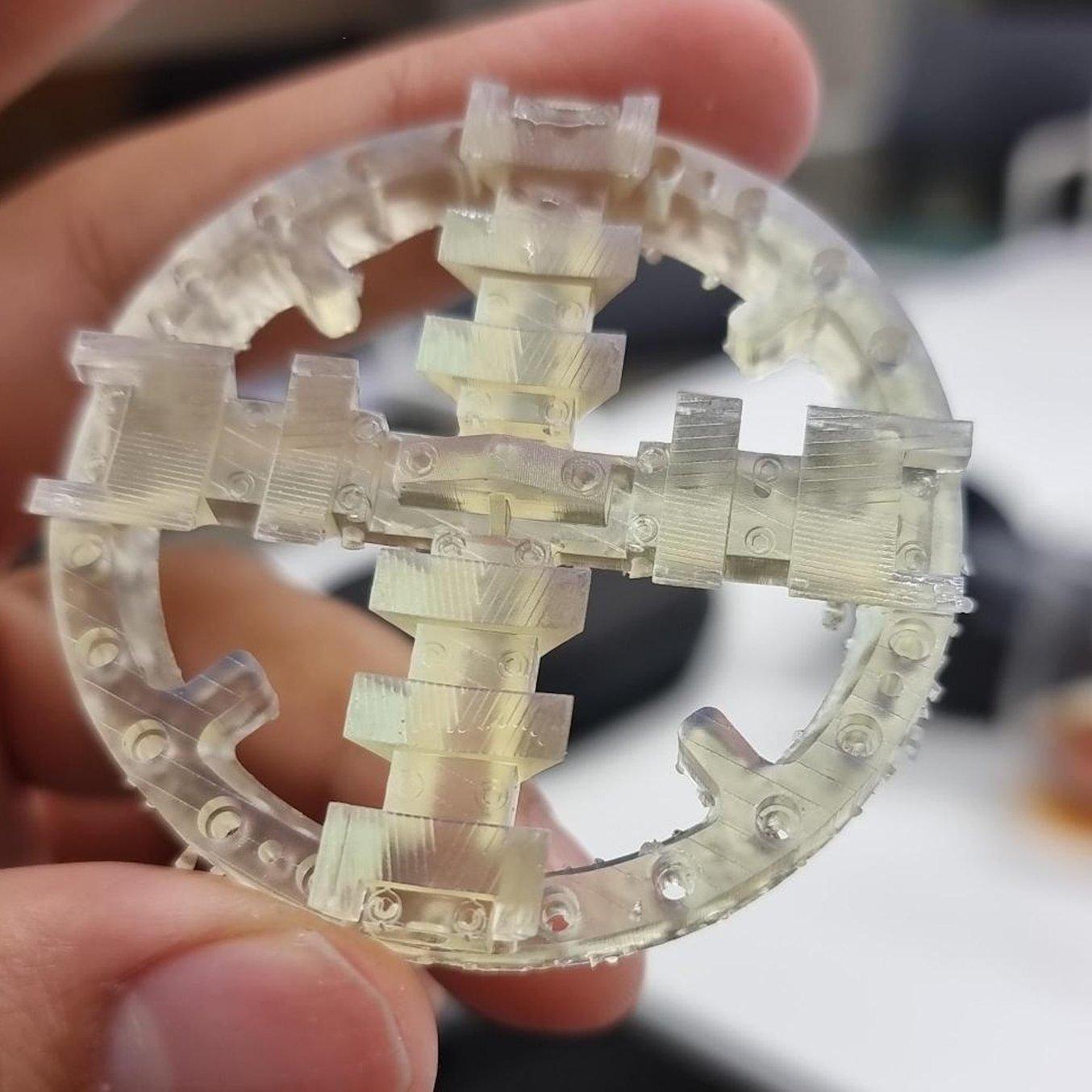
Der SLA-3D-Druck erlaubte es dem Team, verschiedene Konzepte zu visualisieren und schnell und reibungslos zu iterieren.
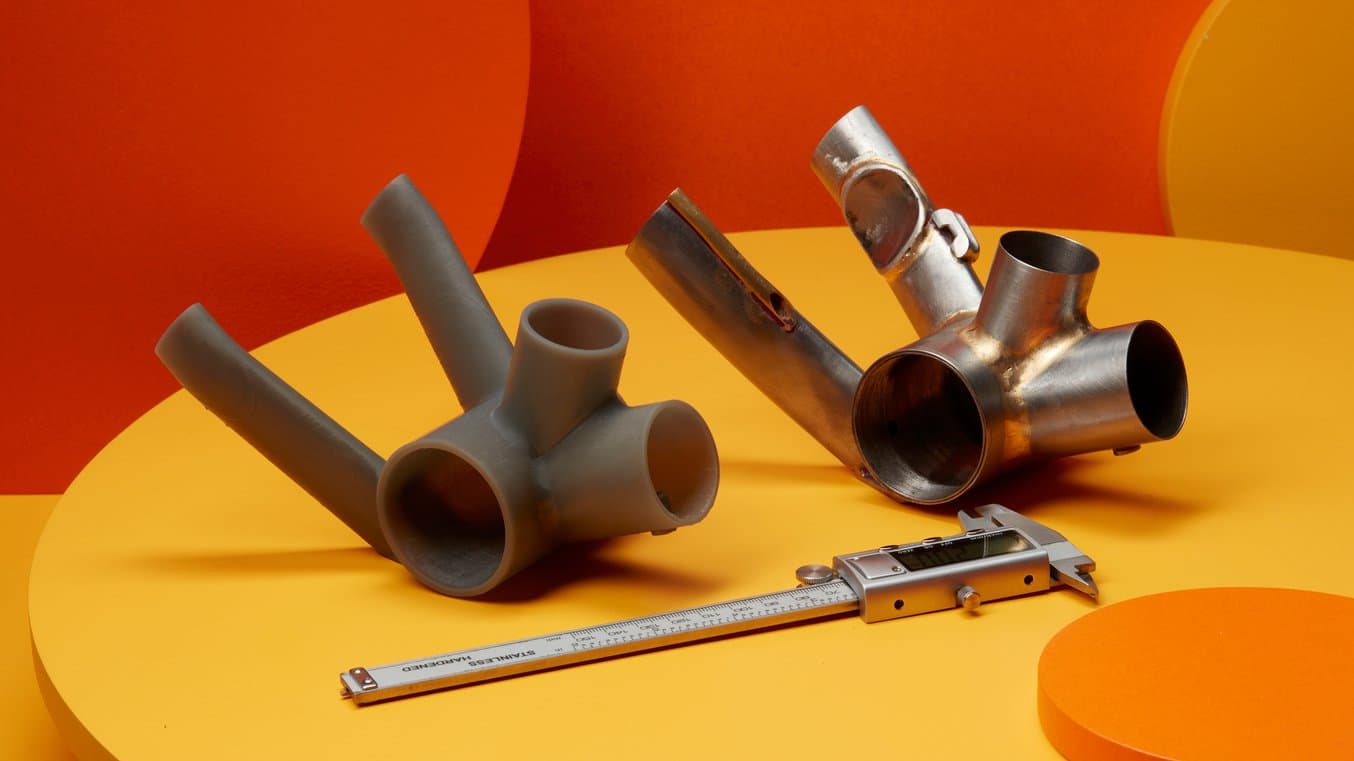
Rapid Prototyping: Die Wahl des richtigen Verfahrens und Materials
Erfahren Sie in diesem Webinar, wie Sie Konzeptnachweise und funktionale Prototypen schneller denn je erstellen und Ihre Designs in kürzester Zeit anhand von Praxistests überarbeiten.
Fertigung von Endverbrauchsteilen mit SLA: Effizient und kostensparend
Abgesehen vom Prototyping nutzte TUM Boring den SLA-3D-Druck auch zur Fertigung von Endverbrauchsteilen wie Abdeckungen für Schraubenlöcher und Sensorenhalterungen.
Am Außengehäuse der TBM gibt es mehrere Schraubenlöcher, die leicht zugänglich sein müssen, falls der Bohrkopf demontiert werden muss, aber zum Schutz vor Erde und Lehm dennoch abgedeckt werden müssen. Der 3D-Druck von Abdeckungen für diese Löcher ist eine kosteneffiziente Lösung, um maßgefertigte Teile in kleinen Stückzahlen herzustellen, die sich leicht entfernen lassen und die Maschine dennoch vor Ablagerungen bewahren.
Wie Reinhardt erläutert, bedeutete dies für das Team „eine deutliche Effizienzsteigerung“. Nachdem verschiedene technische Materialien getestet wurden, entschied sich das Team für Grey Resin, das keine zusätzlichen Nachbearbeitungsschritte erfordert und eine besonders hohe Oberflächenqualität bietet.

Die 3D-gedruckten Abdeckungen aus Grey Resin bieten einen leichten Zugang zu den Schrauben, was bei Wartungsarbeiten Zeit einspart.
Der für geringe Stückzahlen geeignete Arbeitsprozess, die Materialvielfalt und die erstklassige Oberflächengüte beim SLA-3D-Druck ermöglichen auch die Produktion anderer Teile für die Endverwendung. Die TBM verfügt über zahlreiche Sensoren, die sich während des Betriebs auf keinen Fall aus ihrer Position verschieben dürfen. Daher benötigt jeder Sensor eine maßgefertigte Halterung, die stark genug ist, um Druck und Stößen standzuhalten.
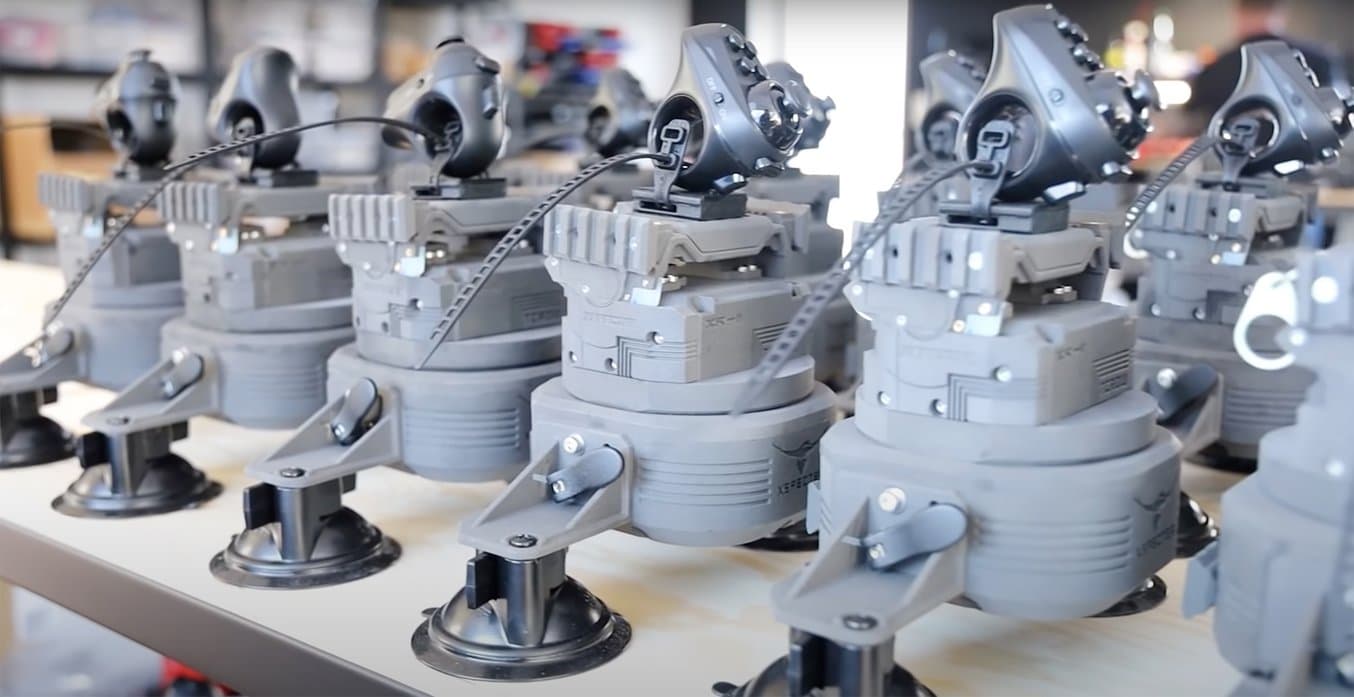
3D-gedruckte Teile für die Endverwendung im Belastungstest
In diesem Whitepaper stellen wir Formlabs' Hardware und Materialien für den 3D-Druck von Endverbrauchsteilen vor.
Nachdem diese Sensorenhalterungen zuvor von einem Fertigungsdienstleister aus Edelstahl produziert wurden, optimierte das Team seinen Prozess, in dem es sie aus Tough 2000 Resin auf dem Form 3+ druckte. Das Outsourcing der Bauteile hatte oft mehrere Tage oder sogar Wochen beansprucht, zu deutlich höheren Kosten als bei interner Fertigung. Mithilfe von 3D-Druck sendet das Team nun einfach das 3D-Modell an den Form 3+ und kann die Halterungen innerhalb von etwa viereinhalb Stunden drucken.
„Mit 3D-Druck laden wir einfach die STL-Datei hoch und haben innerhalb weniger Stunden die fertige Halterung in der Hand, mit der wir den Sensor montieren können.“
Tom Luca Reinhardt, Vorstandsmitglied bei TUM Boring und einer der Leiter des Maschinenbauteams
Unter den vom Team getesteten Kunstharzen war Tough 2000 Resin aufgrund seiner Robustheit und Zuverlässigkeit eindeutig die beste Wahl für diese spezifische Anwendung. Und tatsächlich stellte das Team von TUM Boring nach einigen Tests fest, dass das Bauteil „einiges an Belastung aushielt“ und unter Stößen nicht brach.
SLS-3D-gedruckte Schneidwerkzeuge im Belastungstest unter hohem Druck
Zusätzlich zu SLA-Druckteilen testete TUM Boring auch verschiedene Schneidradstrukturen mit Schneidwerkzeug aus dem SLS-3D-Drucker. Dank des Fuse 1+ 30W war das Team in der Lage, mehrere unterschiedliche Iterationen zu drucken, bevor es sich für die optimale Geometrie für den Wettbewerb entschied. Das gewählte Design beinhaltete Schneidwerkzeuge mit schärferen Kanten, die glatt ins Gelände einschneiden, sowie flachkantige Werkzeuge, die beim Bohrvorgang mehr Widerstandsfähigkeit bieten. Die endgültige Geometrie wurde an einen Fertigungsdienstleister gesendet und aus Edelstahl gefertigt.
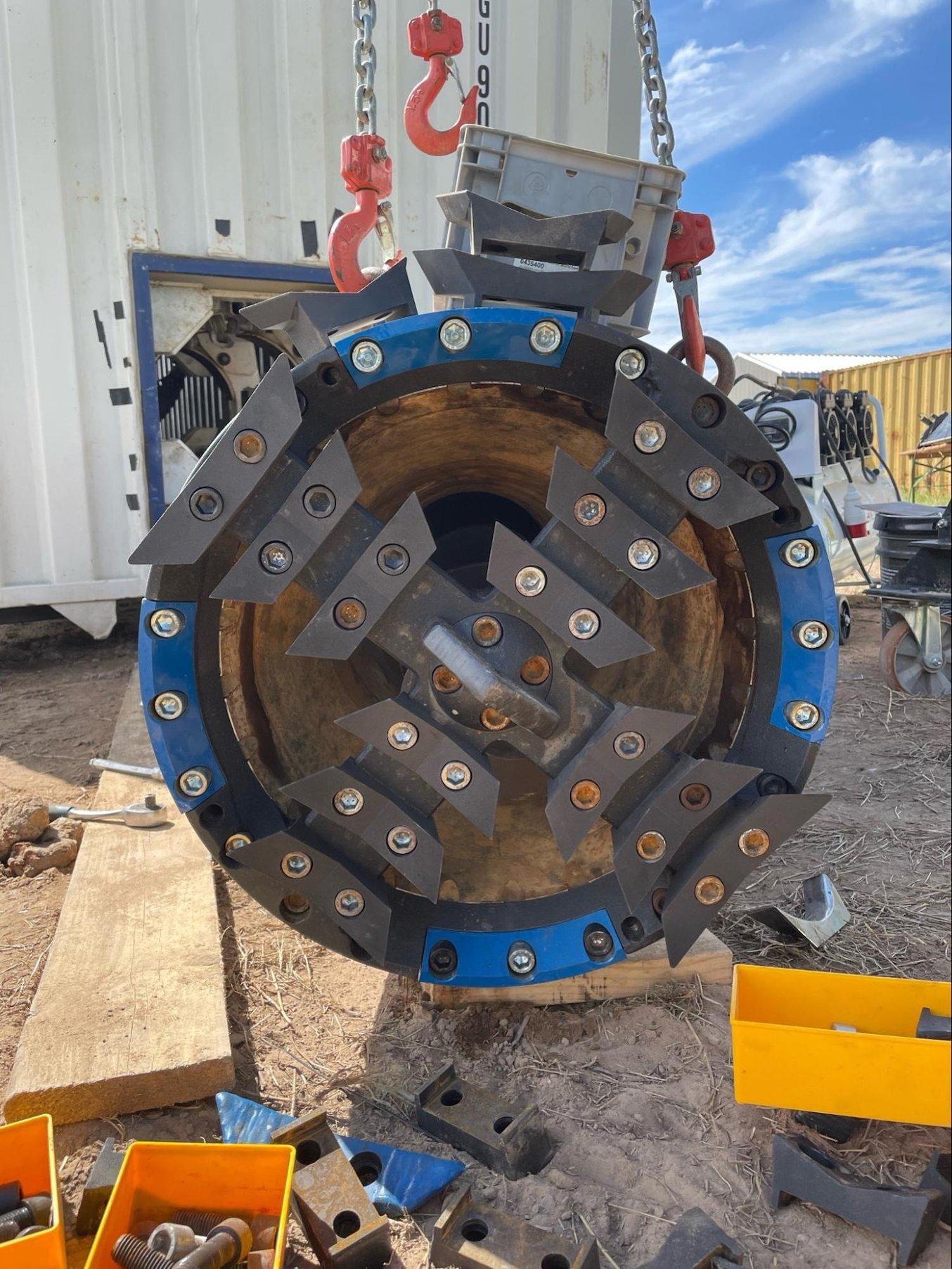
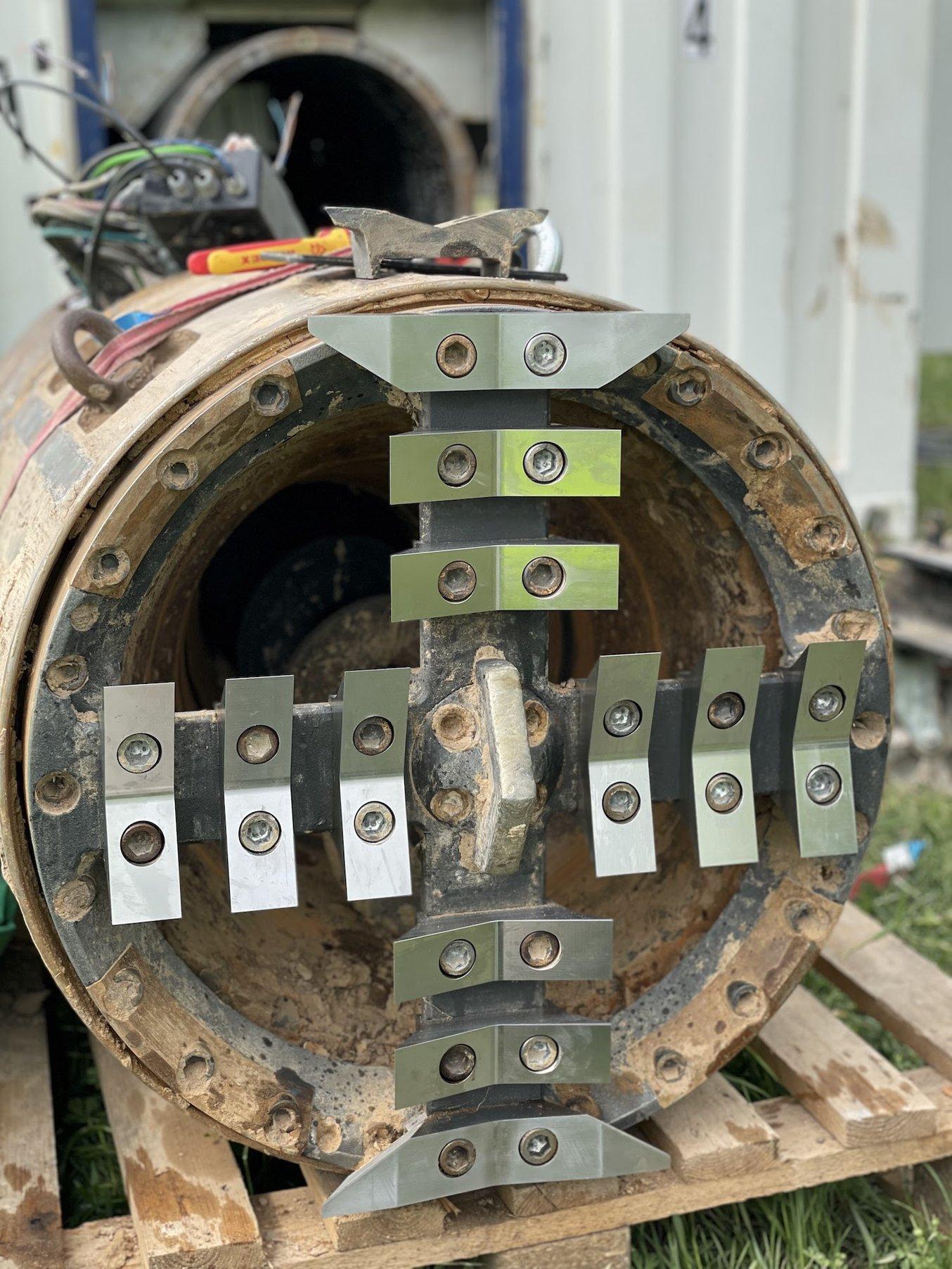
Nylon 11 CF Powder (links) erwies sich als deutlich stärker als vom Team zunächst erwartet und erlaubte es ihnen, mehrere Versionen des Schneidwerkzeugs an der Maschine zu testen, bevor die Bauteile aus Edelstahl (rechts) geliefert wurden.
Unter den von Formlabs angebotenen SLS-Pulvern befand das Team Nylon 11 CF Powder als das beste Material für diese Anwendung, bei der es vor allem auf Haltbarkeit, Steifigkeit und Schlagfestigkeit ankommt. Während der Funktionstests werden die Bauteile hohem Druck und starker Schlagbelastung ausgesetzt. „Wir haben mit diesen Teilen so viel Kraft auf den Boden angewandt, dass wir unseren 15-Tonnen-Behälter bewegen konnten, und haben dabei keinerlei Brüche festgestellt“, berichtet Reinhardt. Tatsächlich war das Team positiv überrascht, wie gut derart leichte Bauteile dem Belastungstest standhielten, und das ganz ohne Anzeichen von Rissen oder Brüchen.
Nach einigen Tests beobachtete das Team an den kohlenstofffaserverstärkten, 3D-gedruckten Schneidwerkzeugen einen geringfügigen Verschleiß, jedoch in viel geringerem Ausmaß als erwartet. Zudem stellte es nach dem Wettbewerb fest, dass die Prototypen aus carbonfaserverstärktem Kunststoff und die Edelstahlteile für die Endverwendung ungefähr die gleichen Anzeichen von Verschleiß oder Beschädigung aufwiesen, was die Festigkeit und Haltbarkeit von Nylon 11 CF Powder demonstriert. „Das war eine Überraschung für viele unserer Mitglieder, vor allem für jene, die zuvor nicht an 3D-Druck geglaubt hatten oder nicht so viel Vertrauen in das Verfahren hatten. Die konnten wir also vom Gegenteil überzeugen“, so Reinhardt.
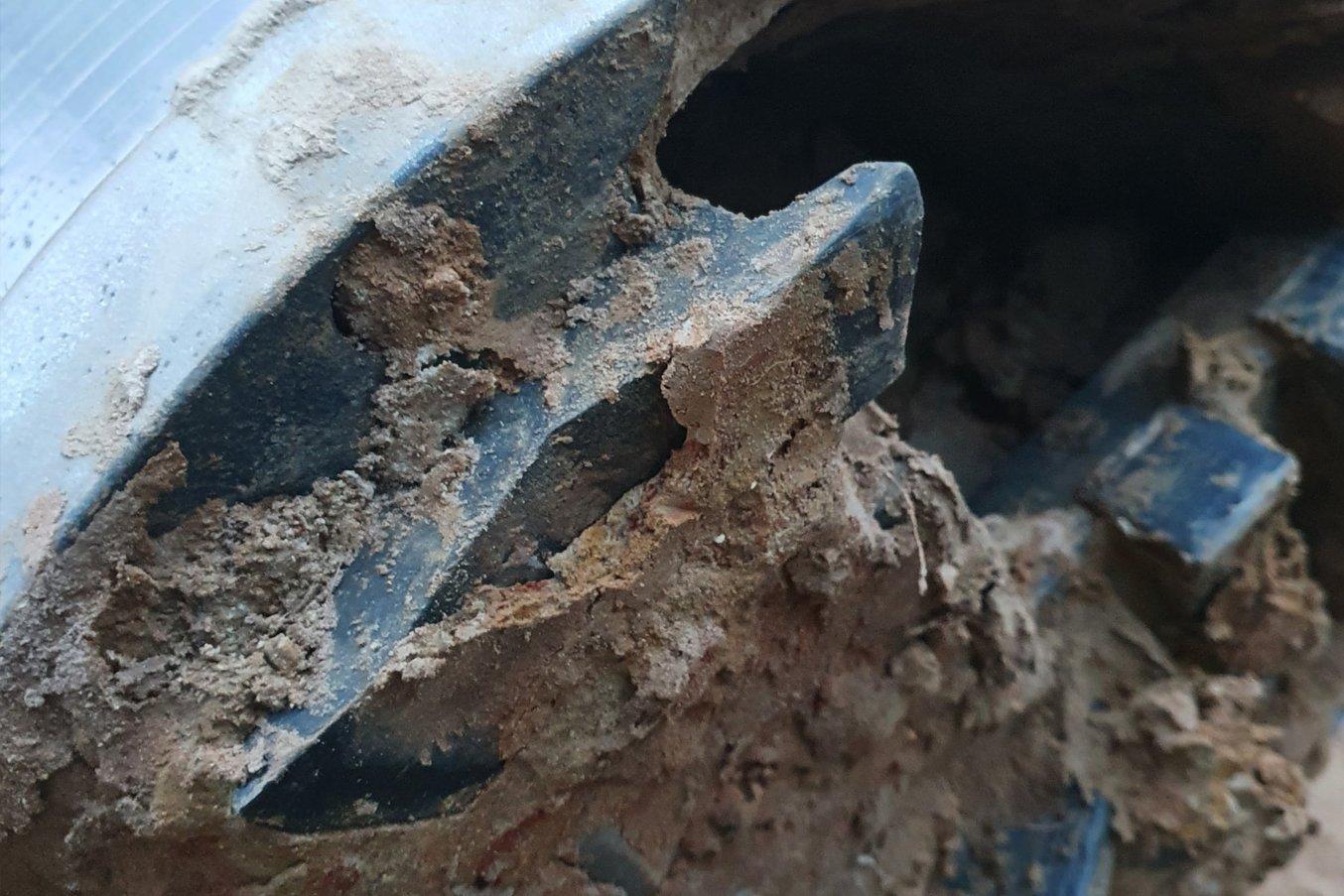
Die kohlenstofffaserverstärkten, 3D-gedruckten Prototypen (hier abgebildet) und die Edelstahlteile für die Endverwendung wiesen in etwa die gleichen Anzeichen von Verschleiß oder Beschädigung auf.
In der Tunnelbaubranche kann der abgetragene Lehm erhebliche Schwierigkeiten bereiten, wenn er am Schneidrad der Bohrmaschine festklebt. Der Lehm härtet aus und blockiert damit das Schneidrad, was den Tunnelbau beträchtlich verzögert. Außerdem kann es zu Korrosion an den Schneidwerkzeugen kommen, welche die Qualität und Präzision der Maschine beeinträchtigt. In einer derart anspruchsvollen Umgebung stellten die Korrosionsbeständigkeit und die Antihafteigenschaften von Nylon 11 CF Powder also einen unerwarteten und entscheidenden Vorteil dar.
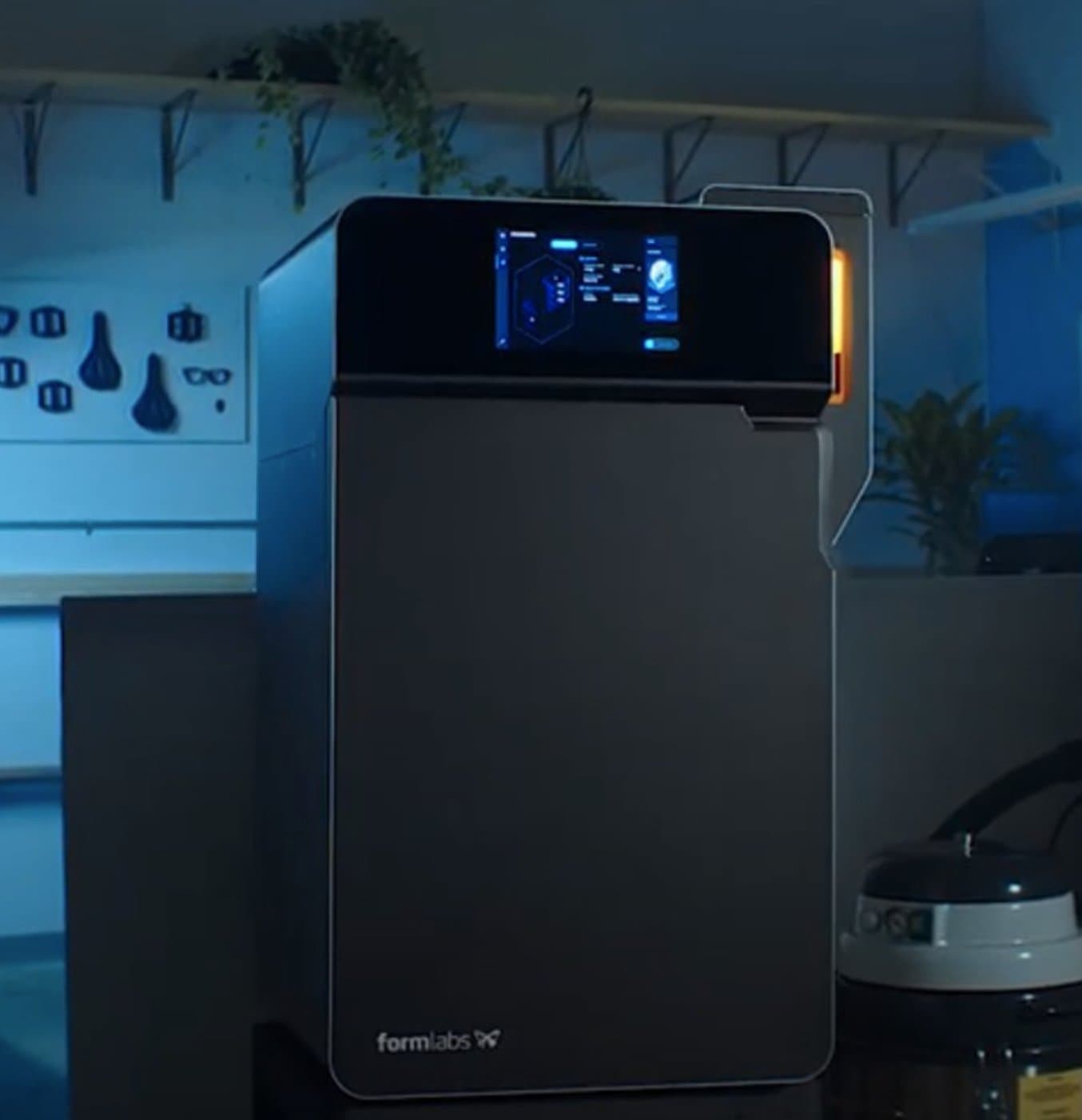
Outsourcing oder betriebsintern: Wann sollte man SLS-3D-Druck in den eigenen Betrieb holen?
In diesem Whitepaper untersuchen wir den Mehrwert betriebsinterner SLS-3D-Drucker im Vergleich zum Outsourcing von SLS-Teilen an einen Fertigungsdienstleister.
Neue Maßstäbe der Effizienz im Tunnelbau
„[Diese Erfahrung] hat uns das Selbstvertrauen gegeben, zukünftig andere Wege auszuprobieren und uns auch mehr auf 3D-Druck zu stützen.“
Tom Luca Reinhardt, Vorstandsmitglied bei TUM Boring und einer der Leiter des Maschinenbauteams
Nach dem wiederholten Sieg des Teams von TUM Boring ist noch nicht klar, ob es an der nächsten Austragung des Bohrwettbewerbs von The Boring Company abermals teilnehmen wird. Eines ist jedoch sicher: Das Team wird danach streben, seine Nutzung des 3D-Drucks weiterzuentwickeln und diesen ihn seine zukünftigen Projekte zu integrieren.