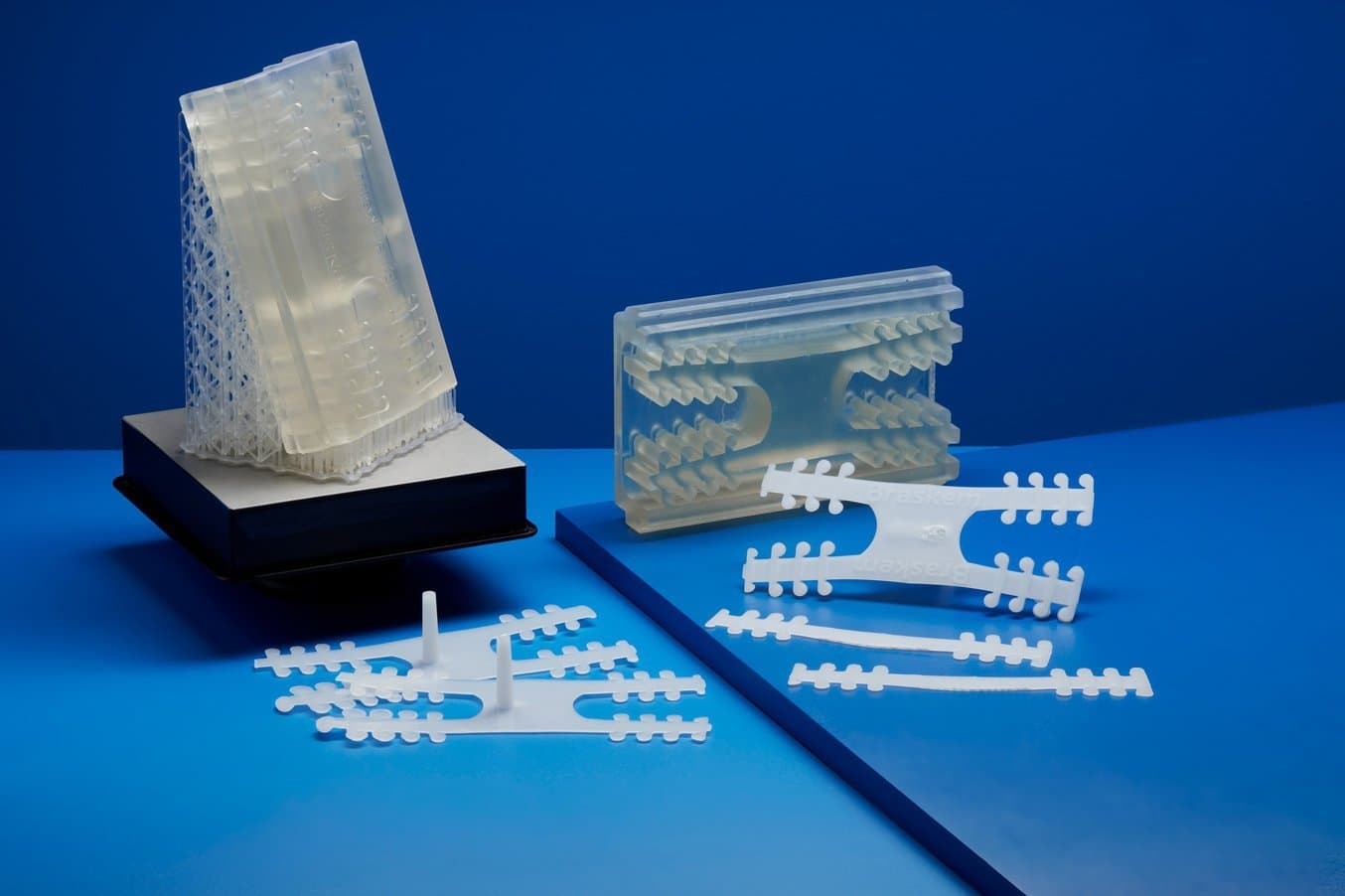
Moldmaking is used across industries by people like product designers, entrepreneurs, and teachers to create short production runs, prototype complex molds, test production in end-use plastics, and generally aid in any situation where it’s necessary to create multiple copies of a part both affordably and easily. It enables production of short-run batches of 150 to 600 parts or testing of mold designs before committing to expensive tooling.
Combining moldmaking with desktop 3D printing allows engineers and designers to expand the realm of materials they’re using and bring the capabilities of their 3D printer beyond rapid rototyping and into the realm of production. Using 3D printed molds, dies, and patterns to supplement the molding process tends to be both faster and less expensive than CNC milling, and easier than working with silicone molds.
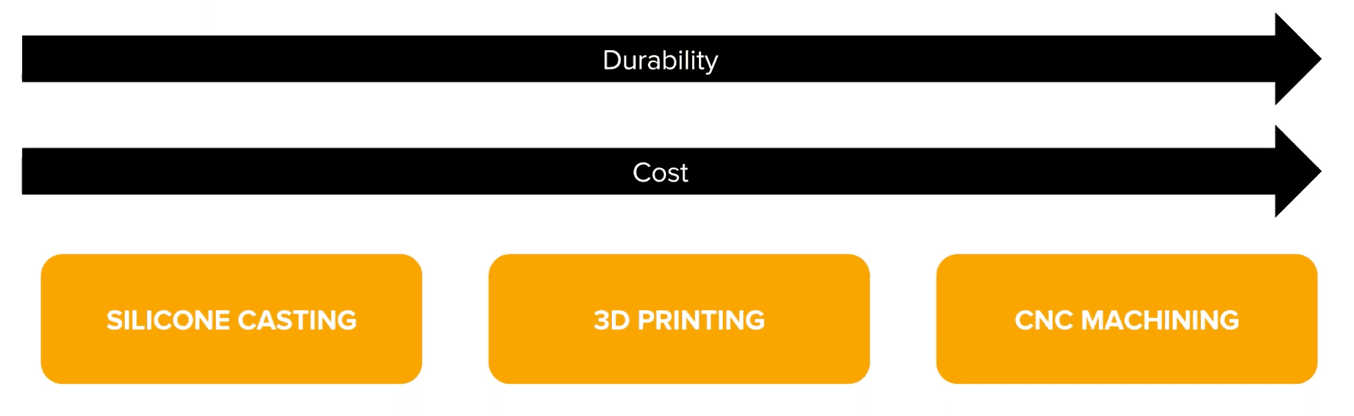
In this post, we’ll walk through three moldmaking techniques easily supplemented by 3D printing: injection molding, casting, and thermoforming. For a more in-depth look at these techniques, as well as design guidelines for moldmaking and 3D printing, watch our recent webinar.
Injection Molding
Injection molding was invented in 1872 by John Wesley Hyatt, and originally operated much like a hypodermic needle. The modern injection molding machine was fully realized in 1956 with the invention of the reciprocating screw.
In the modern injection molding process, a reciprocating screw drives plastic polymer pellets through a hopper into a heated barrel. As the pellets get closer to the heater, they melt and are pushed into the mold cavity, where pressure is applied. After the part forms and cools within the mold, the part is ejected and the mold can be re-used.
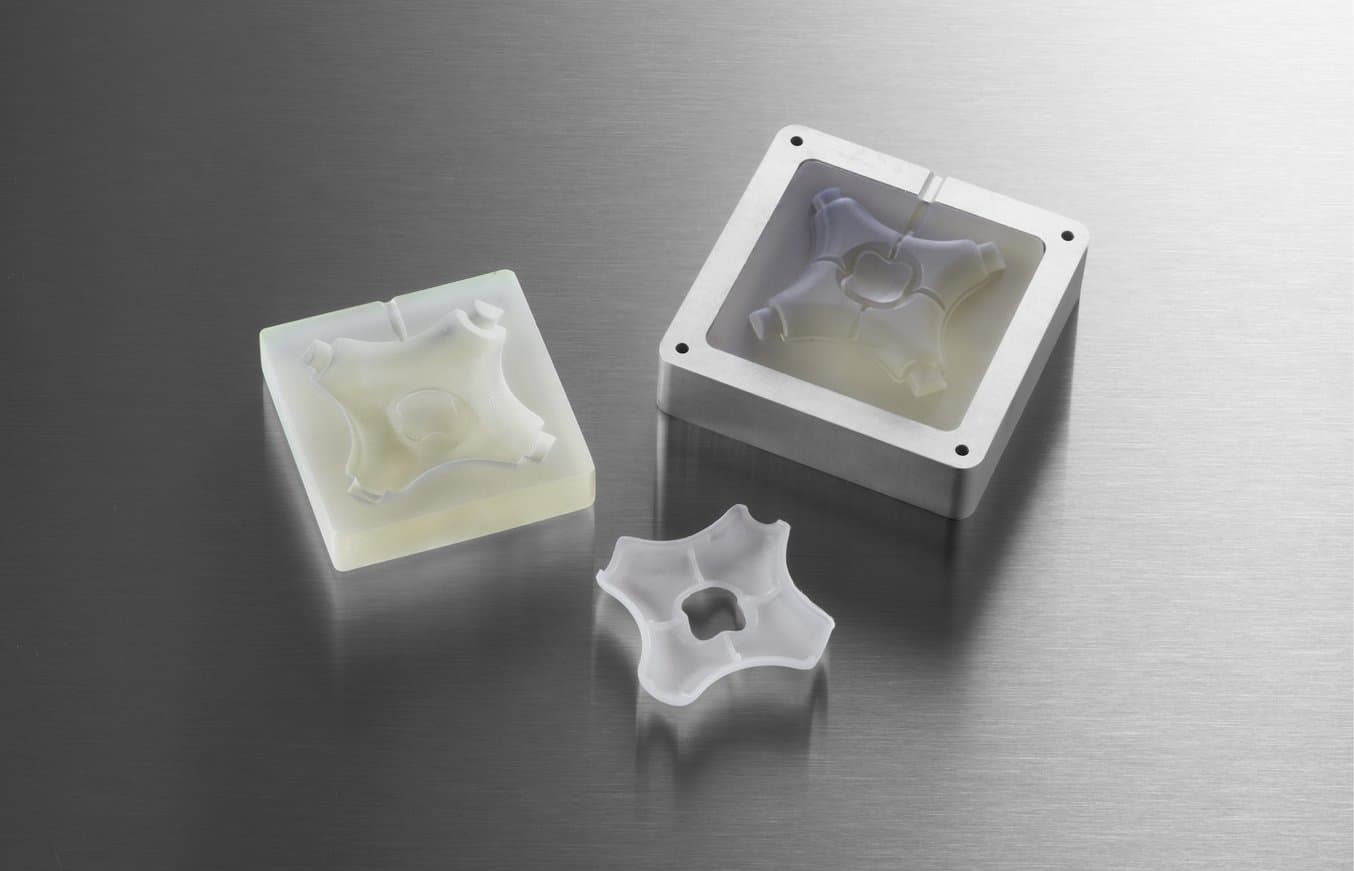
A small plastic part, created using an injection mold 3D printed directly with Formlabs High Temp Resin.
The polymers used by injection molding processes are relatively cheap and can be used to achieve a wide variety of properties, so injection molding is popular for creating packaging and consumer products (fun fact: LEGO bricks, which need to be both strong and precise, are injection molded).
With affordable desktop 3D printers, temperature resistant 3D printing materials, and injection molding machines, it is possible to create 3D printed injection molds in-house to produce functional prototypes and small, functional parts in production plastics. For low-volume production (approximately 10-100 parts), 3D printed injection molds save time and money compared to expensive metal molds. They also enable a more agile manufacturing approach, allowing engineers and designers to prototype injection molds and test mold configurations or to easily modify molds and continue to iterate on their designs with low lead times and cost.
Molds can be directly 3D printed in a variety of materials, such as Formlabs Rigid 10K Resin or High Temp Resin. The testing for our white paper on injection molding was done using the Galomb Model-B100 Injection Molder, which runs at around $3,500.
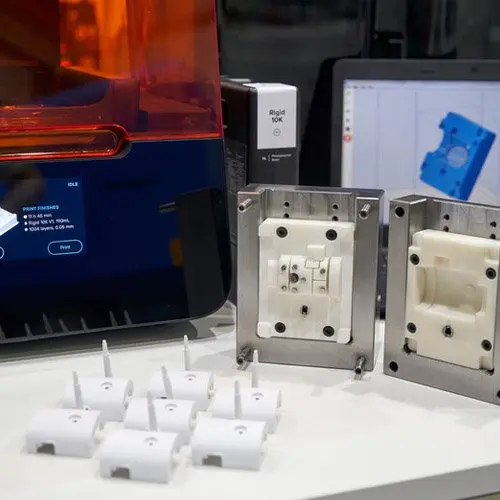
Low-Volume Rapid Injection Molding With 3D Printed Molds
Download our white paper for guidelines for using 3D printed molds in the injection molding process to lower costs and lead time and see real-life case studies with Braskem, Holimaker, and Novus Applications.
Casting
Metal casting is a popular technique in many industries, jewelry, dentistry, and engineering in particular. It can be used for small and large parts in a wide variety of metals. Originating over 5,000 years ago, casting enables creators to work with a wide variety of materials and is one of the easiest ways to make metal parts.
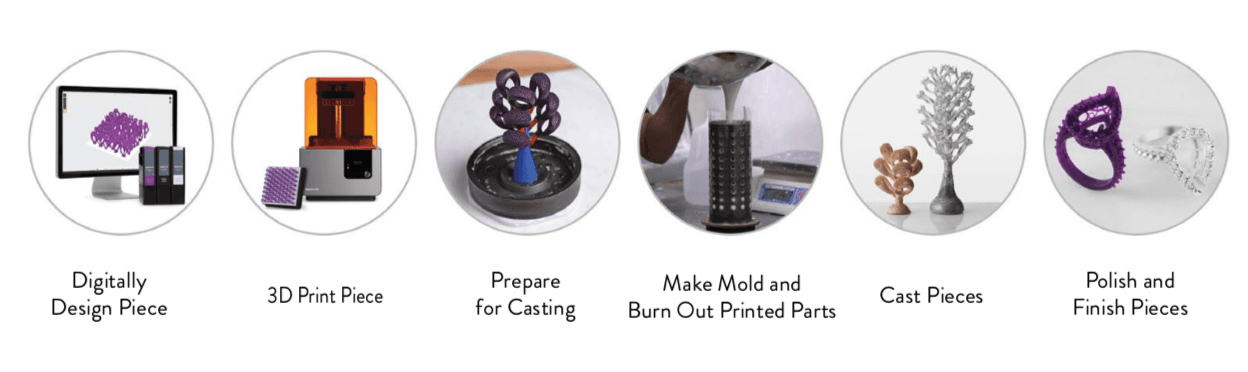
In casting, a hollow mold is created from a master, which could be hand-sculpted or 3D printed (as seen in a video tutorial from BJB Enterprises on how to make silicone molds with a Formlabs SLA 3D printer). The master is immersed in a casting material like sand, clay, concrete, epoxy, plaster, or silicone. The casting material hardens, plastic or metal is poured into the mold, and the master is either removed or burnt out to create the final part.

You can print a detailed master for casting using a material like Formlabs Castable Resin, which burns out to create a reusable mold.
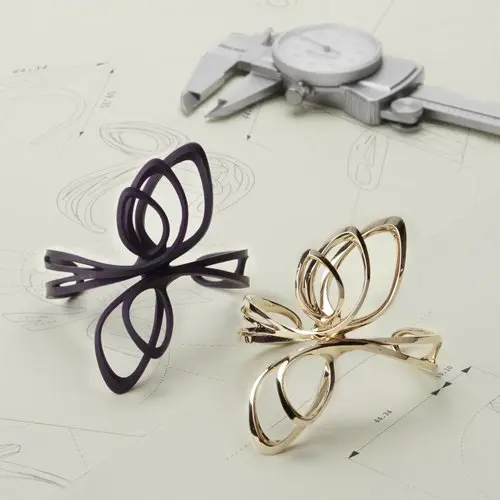
Introduction to Casting for 3D Printed Jewelry Patterns
In this white paper, learn how to cast fine jewelry pieces from 3D printed patterns and how direct investment casting, or lost wax casting, works as a moldmaking technique.
Download the White PaperVulcanized rubber molds can be used to produce wax models in quantity for investment casting of metal parts such as jewelry, small industrial components, and gaming miniatures.
3D printers can produce master models that are used to form room temperature vulcanization (RTV) molds and even durable high temperature vulcanized rubber molds.
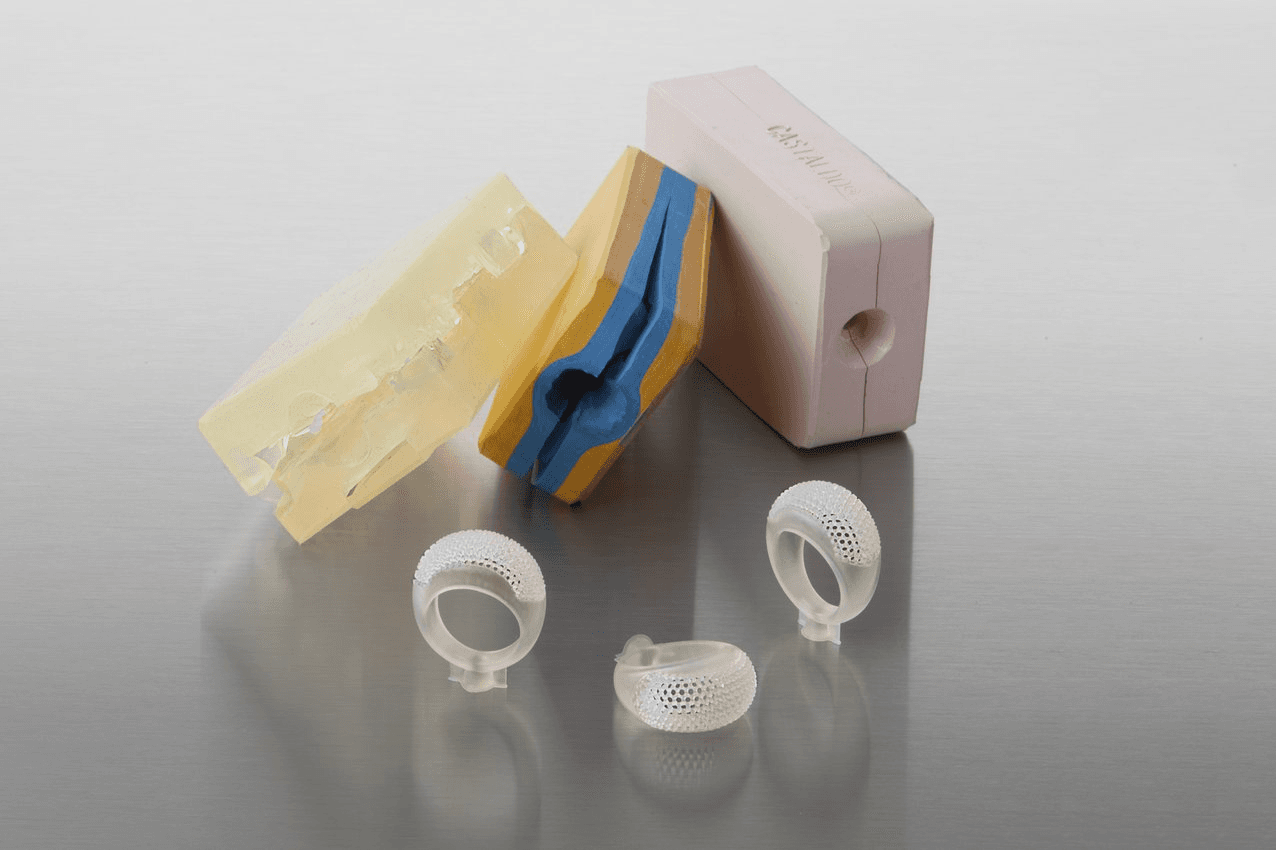
Directly 3D printed jewelry patterns can be used for room temperature vulcanization (RTV) and vulcanization of high temp natural rubber.
In engineering and manufacturing, metal casting is a cost-effective and highly capable manufacturing process for producing parts with fine features or complex geometries. Manufacturers and engineers use casting for critical components in aerospace, automotive, and healthcare applications.
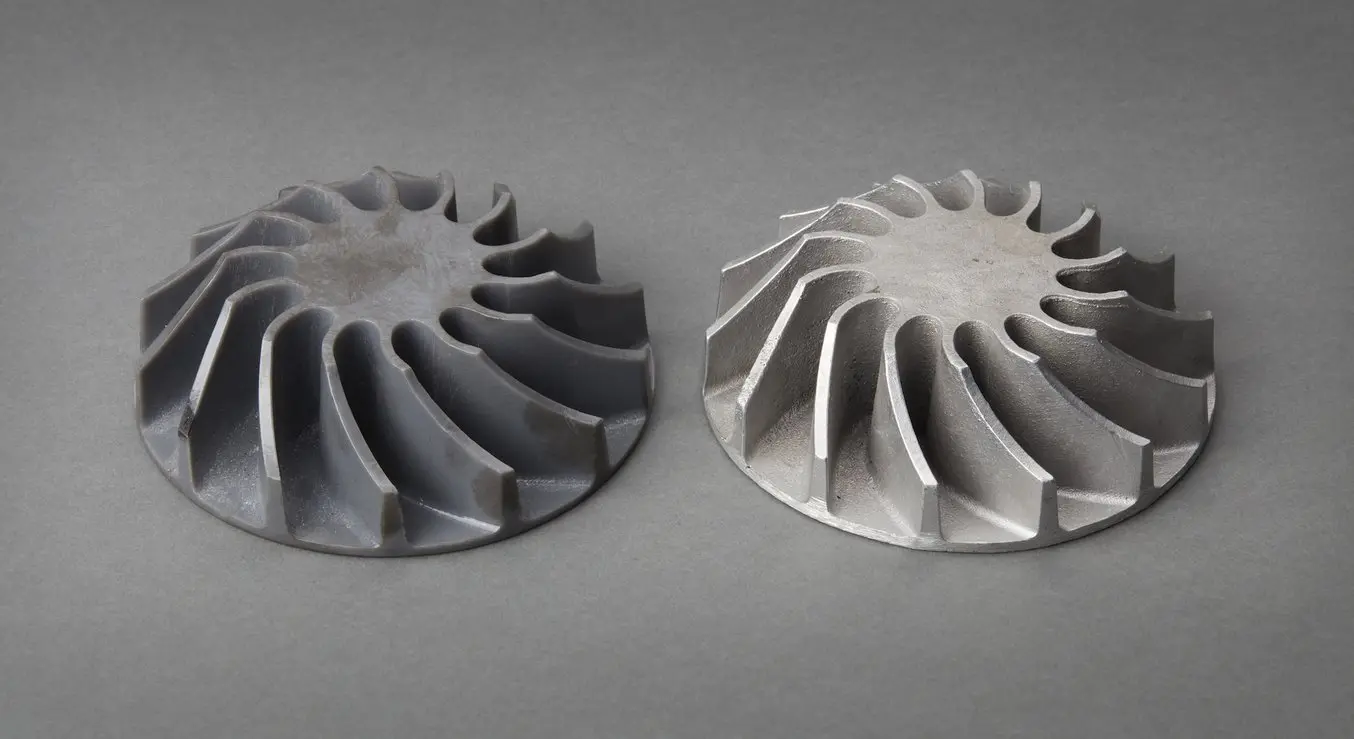
Stereolithography (SLA) 3D printers are well-suited for casting workflows to produce metal parts at a lower cost, with greater design freedom, and in less time than traditional methods and without the expense of direct metal 3D printers.
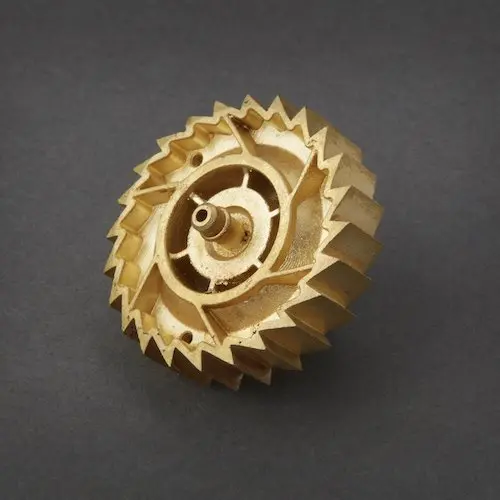
Fabricating Metal Parts With 3D Printing
In this white paper, learn how engineers can leverage the speed and flexibility of 3D printing without the expense of direct metal printers by using metal casting workflows, including detailed walkthroughs of sand casting and investment casting processes with Formlabs 3D printers and resins.
Download the White PaperThermoforming and Vacuum Forming
The two processes of thermoforming and vacuum forming are similar to injection molding in that they use heat and pressure to create final plastic parts. These methods first originated in the 1940s to produce aircraft canopies without blemishes and army relief maps.
Today, they are commonly used to produce anything consumer packaging to automotive components for components where dimensional accuracy may not be as critical and non-uniform thickness is acceptable.
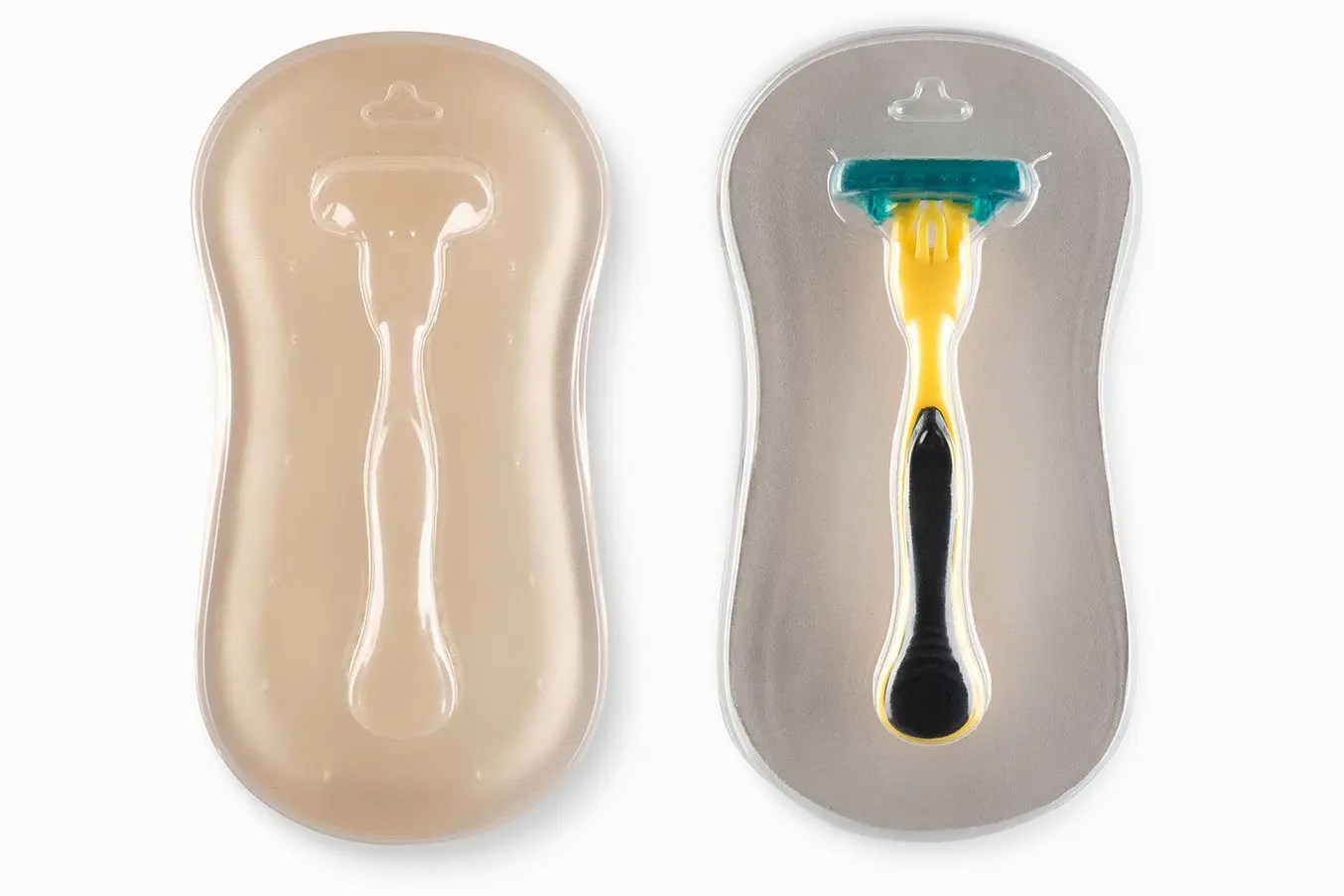
In thermoforming, a heated sheet of plastic is pressed between two mold halves to create a part. In vacuum forming, only one half of the mold is used, with suction used to pull the plastic down over the mold. The machinery used for these methods is very cheap, and it’s even possible to build them yourself.
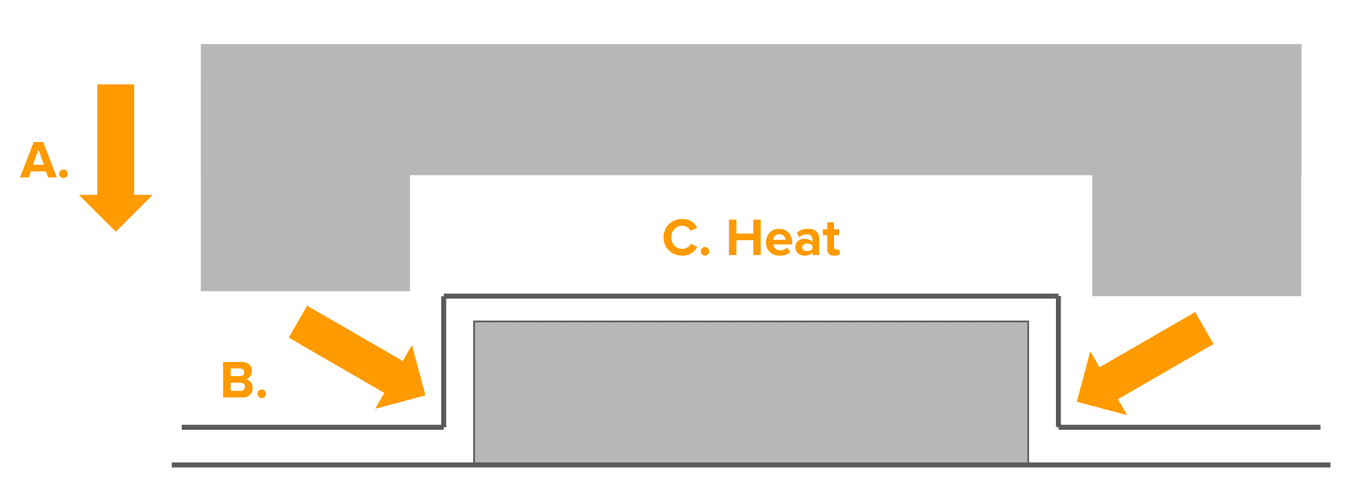
3D printing thermoform dies with SLA 3D printing is a fast and effective method to create high quality vacuum-formed parts for small batch production. Printed thermoform dies can be used to make packaging prototypes, clear orthodontic retainers, and food-safe molds for chocolate confections.
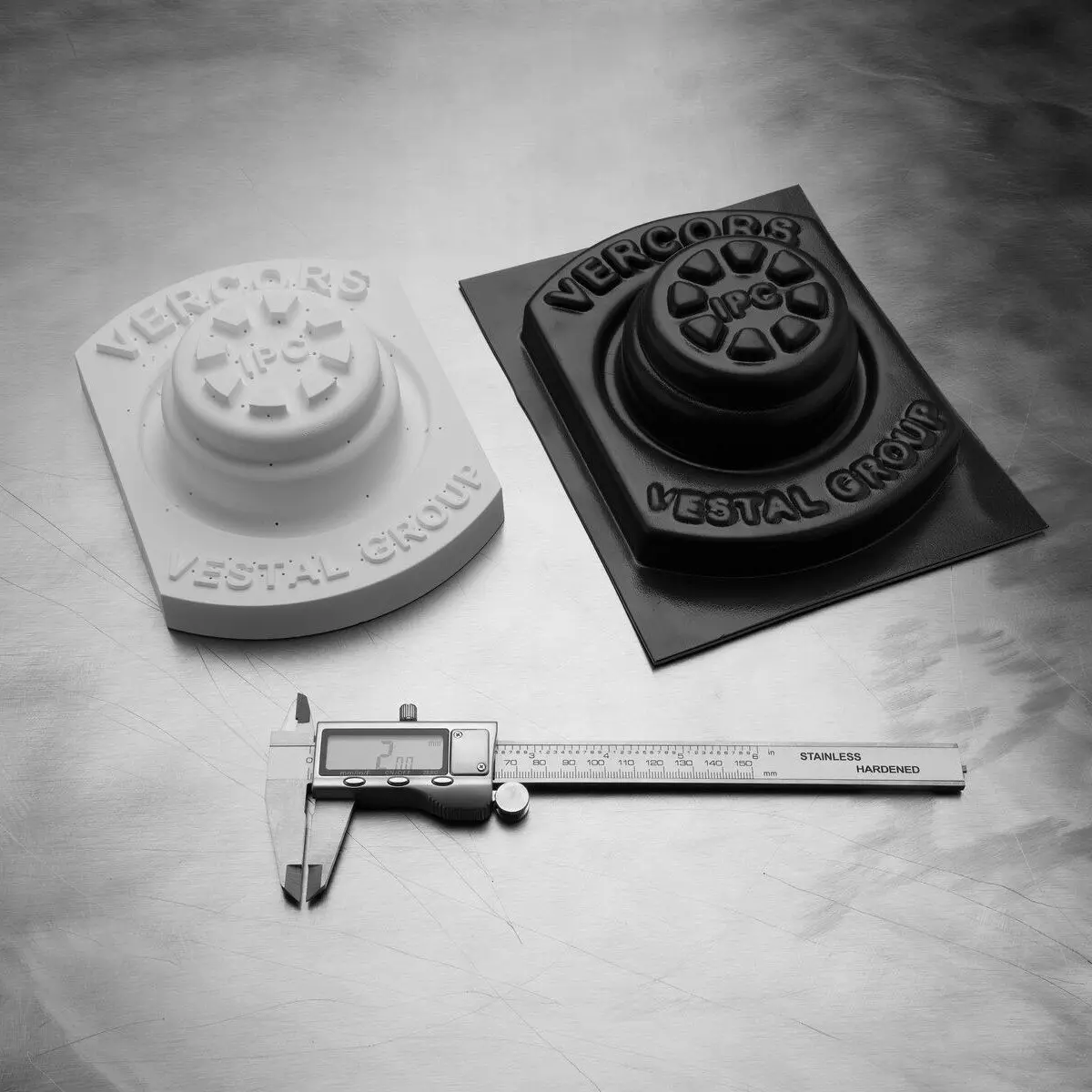
Low-Volume Rapid Thermoforming With 3D Printed Molds
Download our white paper to see how to create complex molds with 3D printing fast and learn about tips and guidelines that you’ll want to follow when preparing your mold parts.
How to Make Molds With 3D Printing
When you’re modeling parts for moldmaking, you need to consider factors like pressure, outgassing, and differential cooling and heating.
Watch our webinar to explore various moldmaking techniques and learn how to make 3D printed injection molds, thermoforming molds, and molds for casting.
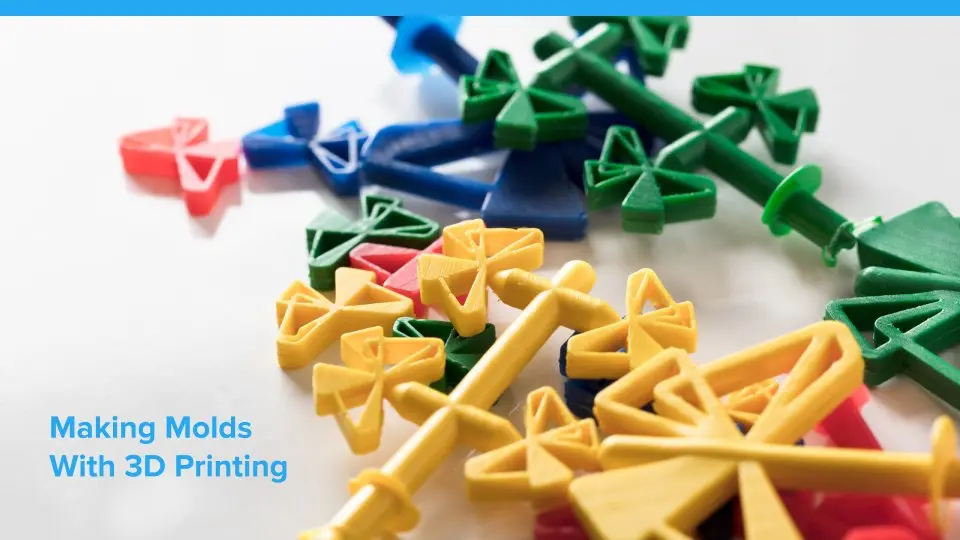