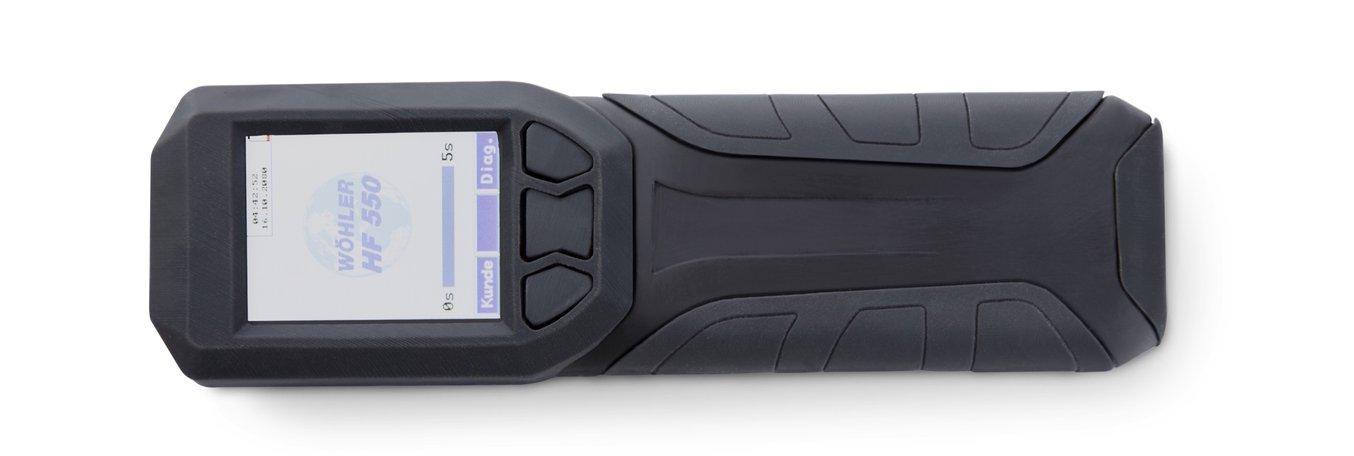
Sebastian Leifels was posed with a challenge: to create a looks-like, works-like prototype to get a new product ready for casting and final manufacturing. As a product designer at Wohler, a Germany-based manufacturer of metrology and inspection technology, Sebastian needed to design a prototype that had the final product’s aesthetics and function. He explains, “It is extremely important to prevent mistakes at this stage of the design process. Changes to the casting device as well as the end product are expensive. The costs range from a three digit up to a five digit euro figure.”
This risk was on Sebastian’s mind as he prototyped the Wohler HF 550 Wood Moisture Meter, a device that measures the level of moisture in firewood and wood products like pellets and wood chips. Here are a few lessons that the Sebastian and the Wohler team learned during their rapid prototyping process.
Prototyping in house leads to a better final design.

Sebastian had to make changes to prototypes quickly and easily to stay on deadline, so he decided to use desktop 3D printing. He opted for a Formlabs 3D printer, which uses stereolithography (SLA) technology to create precise models in hours. He recalls, “The production of a prototype dropped from several days to a few hours. As we used the printer to design parts for the device housing, we saved several weeks in the entire development process.”
Keeping production in house enabled the Wohler team to have greater control and speed in the design process. Sebastian recalls, “If it was needed during the current development state, we ran the printer day and night for several weeks.” With a large number of prototypes, the team could test out more ideas along the way, resulting in a better final product.
In choosing tools, price doesn’t determine quality.

Early in the design process, Sebastian had a desktop 3D printer that used Fused Deposition Modeling (FDM) technology that cost more than four times the Formlabs machine. Yet the FDM printer could not produce accurate details. “The printer allowed greater precision,” Sebastian explains. “Our previous machine had a minimum layer size of 0.178 mm. The Formlabs 3D printer had a minimum layer size of 0.025 mm.” He continues, “Even if you choose the same layer size, the Formlabs printer will always have smoother results.”
Combining multiple materials improves user testing.

To prototype the wood moisture meter, Sebastian had to incorporate several different materials. The team’s initial FDM 3D printer could not print flexible materials, so they originally went through a complex process. First, they designed a trial casting model and printed it on the FDM printer. Then they painstakingly post-processed the casting model to smooth the surfaces. Finally, they grouted the model with rubber compound. Sebastian recalls, “This was a time-consuming process, and we still couldn’t reach fine details. Now, we simplified our process by directly printing detailed parts.”
Sebastian used Black Resin for the case and Flexible Resin for the keypad. The keys had to compress when the user pushed them, so the button walls had to be very thin yet durable. He says that Flexible Resin allowed the team to “conduct a wide range of tests with the prototypes without any damages or functional constraints of the part.”
With in-house 3D printing, we have the advantage of testing the parts for each device before mass production. The risk of reworking the device later is low.
Sebastian and his team now use their Formlabs 3D printer for all prototypes at Wohler: “With in-house 3D printing, we have the advantage of testing the parts for each device before mass production. The risk of reworking the device later is low.” Using a single machine that produces multiple materials opens up new prototyping possibilities for the Wohler team. Although in-house 3D printing saves them time and money, the biggest advantage is the ability to create better final products.