Pendant des années, le battage médiatique autour de l'impression 3D a attiré l'attention de la presse grand public. Beaucoup affirmaient que bientôt chaque foyer aurait sa propre imprimante 3D, mais comme ces prédictions étaient peu détaillées, la plupart ne se sont en fin de compte pas concrétisées. Cependant, les possibilités offertes par l'impression 3D étaient indéniables, malgré la jeunesse de la technologie et le nombre relativement restreint d'utilisations viables à l'époque.
Le battage médiatique initial a minimisé les applications réelles de l'impression 3D. Alors que de plus en plus de machines de bureau et d'atelier haute performance arrivent sur le marché, nous constatons qu'un plus grand nombre d'entreprises élargissent leur offre et fournissent de meilleurs produits aux clients.
Que peut-on faire avec une imprimante 3D ? Découvrez 25 cas d'utilisation (souvent inattendus) de l'impression 3D qui illustrent le large nombre d'applications rendues possibles par cette technologie.
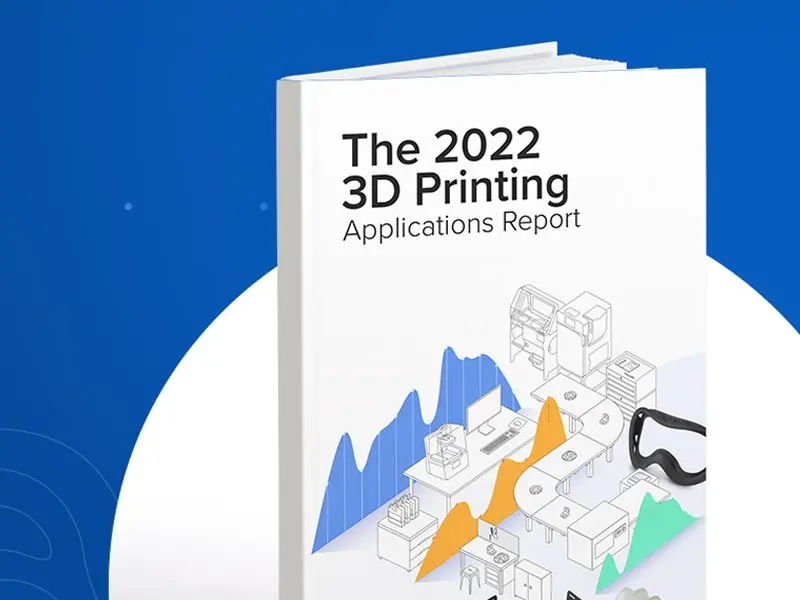
Le rapport 2022 sur les applications de l'impression 3D
Un nouveau rapport sur le secteur qui compare la façon dont les utilisateurs récents et précoces utilisent l'impression 3D pour leur entreprise, et explore les tendances futures de cette technologie.
Concevoir la voiture de demain
L'impression 3D peut apporter des avantages considérables aux chaines d'approvisionnement, et donner accès à une vaste gamme d'applications. Au fur et à mesure que cette technologie devient plus accessible, tant en termes techniques que financiers, les entreprises peuvent intégrer des procédés de fabrication additive en interne pour épauler les processus en place dans les ateliers de production. De nouveaux matériaux d'impression 3D résilients permettent de produire des pièces 3D fonctionnelles de haute précision capables de remplacer les pièces finales. Cela offre des possibilités de personnalisation qui aident les concepteurs à repousser les limites des voitures hautes performances. Le studio de design industriel Vital Auto a mis cette technologie au service de la création de prototypes et de voitures-concepts haute fidélité grâce à toute une série d'outils avancés tels qu'à un large parc d'imprimantes 3D.
« Nous utilisons l’impression 3D depuis le premier jour. Nous voulions l’intégrer dans nos processus de fabrication, non seulement pour réduire les coûts, mais aussi pour donner aux clients plus de diversité dans leurs conceptions et leurs idées », a déclaré l'ingénieur concepteur Anthony Barnicott.
L'industrie automobile a constaté la valeur que la fabrication additive peut apporter à de nombreuses étapes de la création automobile. Elle permet d'aller bien au-delà du prototypage rapide pour :
- Créer des pièces personnalisées, complexes et de haute-performance
- Fabriquer de l'outillage et des aides à la production industrielle
- Produire de pièces de rechange et des pièces détachées à la demande
- Réduire les coûts et les temps de production jusqu'à 90 % par rapport à la sous-traitance
Des écouteurs parfaitement adaptés
Les récentes avancées de la technologie d'impression 3D ont commencé à changer fondamentalement le secteurde l'audio : l'impression numérique d'appareils auditifs sur mesure pour les secteurs de l'audiologie, de la protection contre le bruit et de l'audiologie grand public n'a jamais été aussi abordable. Ces dernières années, les fabricants d'imprimantes 3D ont mis sur le marché des matériaux biocompatibles sans danger pour la peau, ce qui permet de produire en interne des modèles d'oreille et des embouts d'écouteurs.
Cet ajustement personnalisé offre une expérience d'écoute individuelle et unique, basée sur l'ajustement exact de l'écouteur dans l'oreille du client. Cela permet un ajustement sûr qui empêche les écouteurs de tomber, en plus d'un confort et d'une isolation sonore améliorés.
« Nous sommes ravis de pouvoir fabriquer des écouteurs personnalisés pour offrir une expérience sur mesure et améliorer encore l'écoute immersive. Formlabs partage la volonté d'innovation de Sennheiser, et l'amélioration de l'expérience client grâce à ce prototype témoigne de cet état d'esprit. »
Veronique Larcher, directrice de Sennheiser AMBEO Immersive Audio
Les défis qui accompagnent la fabrication personnalisée peuvent être surmontés en associant les imprimantes 3D révolutionnaires de Formlabs, le scan mobile et l'apprentissage automatique. Cela signifie que les clients peuvent désormais facilement avoir accès à des écouteurs sur mesure, avec des délais de production réduits allant de un à quatre jours.
La nouvelle génération d'instruments chirurgicaux imprimés en 3D
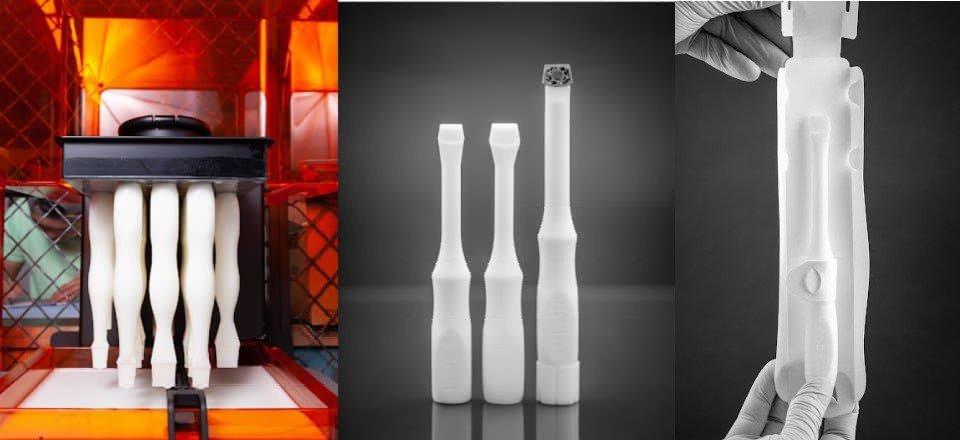
Les outils de restor3D en cours d'impression, ainsi que leur version finale.
Il y a dix ans, peu de gens parlaient de l'impact considérable que l'impression 3D aurait sur le secteur médical, qu'il s'agisse d'aider à créer des dispositifs médicaux avancés ou des guides chirurgicaux spécifiques aux patients. L'entreprise restor3d a su tirer son épingle du jeu : elle exploite les capacités offertes par l'impression 3D pour améliorer radicalement les soins chirurgicaux en imprimant des instruments en polymère spécifiques et adaptés aux implants du rachis cervical.
Avec un parc de plus de 25 imprimantes 3D Formlabs dans sa chaîne de production, restor3D imprime déjà la prochaine génération d'outils chirurgicaux. Pour les chirurgiens qui utilisent ces outils, ce système d'instruments stériles à emballage unique permet d'obtenir les résultats suivants :
- Remplacement des plateaux chirurgicaux volumineux et coûteux.
- Capacité à itérer les conceptions et à introduire rapidement de nouveaux outils ou fonctionnalités en fonction des préférences des chirurgiens.
- Réduction spectaculaire des coûts de la chaîne d'approvisionnement et de la stérilisation pour les hôpitaux.
Accélérer la recherche en ingénierie tissulaire
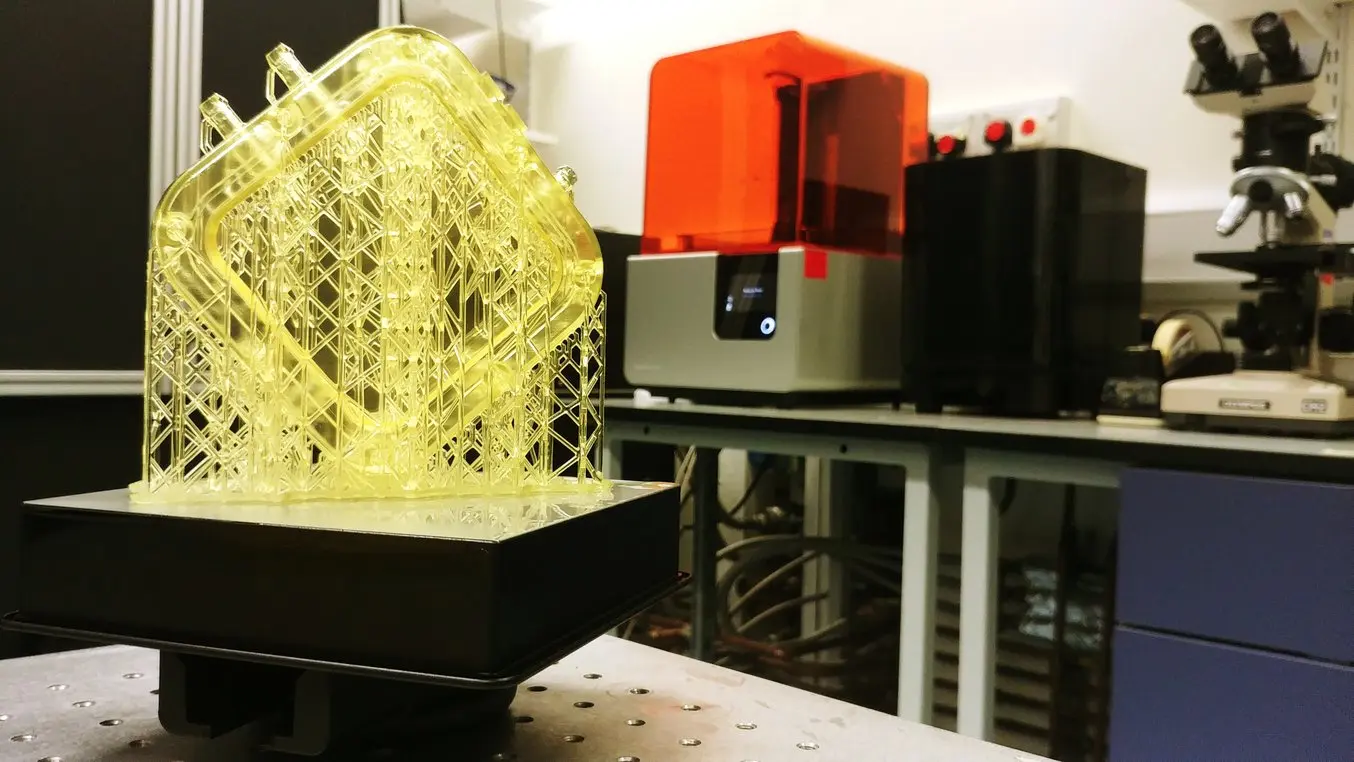
La technique d'impression 3D s'est beaucoup développée ces dernières années, mais bien plus d'usages révolutionnaires sont en cours de développement. Un exemple : les organes imprimés en 3D.
Être capable de fabriquer des organes est l'un des rêves des scientifiques qui travaillent en médecine régénérative depuis des décennies. Bien qu'à ses débuts, l'utilisation du processus de travail en 3D pour produire un tissu organique acceptable pour la transplantation commence à porter ses fruits.
Le Dr Sam Pashneh-Tala de l'Université de Sheffield est l'un des pionniers du secteur. Ses recherches utilisent l’impression 3D par stéréolithographie (SLA) de bureau de haute précision pour permettre la production de vaisseaux sanguins par ingénierie tissulaire avec une variété de géométries. Cela permettra de concevoir des greffons vasculaires spécifiques au patient et d'améliorer les options chirurgicales et fournira une plateforme de test unique pour de nouveaux dispositifs vasculaires destinés aux personnes souffrant de maladies cardiovasculaires, ce qui est actuellement la première cause de décès dans le monde.
« Ce qui me différencie, c'est que je suis capable de créer des vaisseaux sanguins avec des géométries au plus proche de celles trouvées dans le corps. Cela offre la possibilité d'améliorer les options chirurgicales et même de concevoir des vaisseaux sanguins adaptés au patient. Sans accès à une impression 3D abordable et de haute précision, la création de ces formes ne serait pas possible. », nous dit le Dr Pashneh-Tal.
Reconstituer des villes
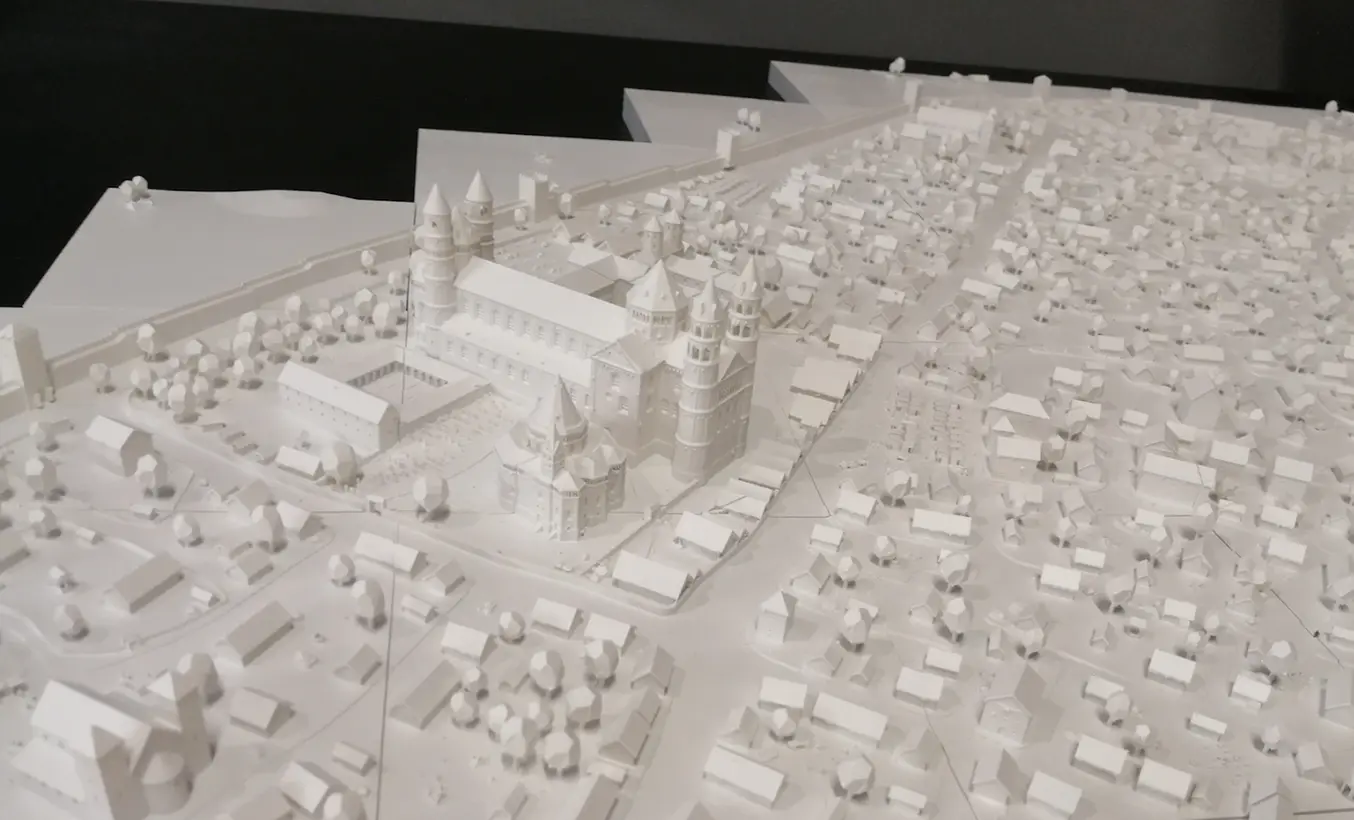
La reconstitution de trois villes à deux époques différentes a demandé plus de 650 segments mesurant 12 x 12cm, imprimés à l'aide de White Resin de Formlabs.
Ce secteur étant déjà fondé sur la conception géométrique, le prototypage et la modélisation, il est prêt à tirer d'énormes avantages des avancées dans la technique d'impression 3D.
En plus du gain de temps pendant la production du modèle, les modèles imprimés en 3D permettent aux architectes d'anticiper les effets de certaines caractéristiques de conception avec plus de certitude. Un architecte peut par exemple mesurer avec plus de précision le flux de lumière à travers la structure en observant un modèle fabriqué avec plus de choix de matériaux.
Mais l'utilisation de l'impression 3D ne se limite pas à un modèle unique : certaines entreprises recréent des villes entières. Institut d'architecture de la Hochschule Mainz - Université des sciences appliquées. Le résultat en est une exposition extraordinaire qui présente six modèles à grande échelle de villes dans les années 800 et 1250. Les modèles sont composés de plus de 650 pièces, toutes créées à l'aide de la technologie d'impression 3D SLA.
Pièces finales pour des chaussures haute performance
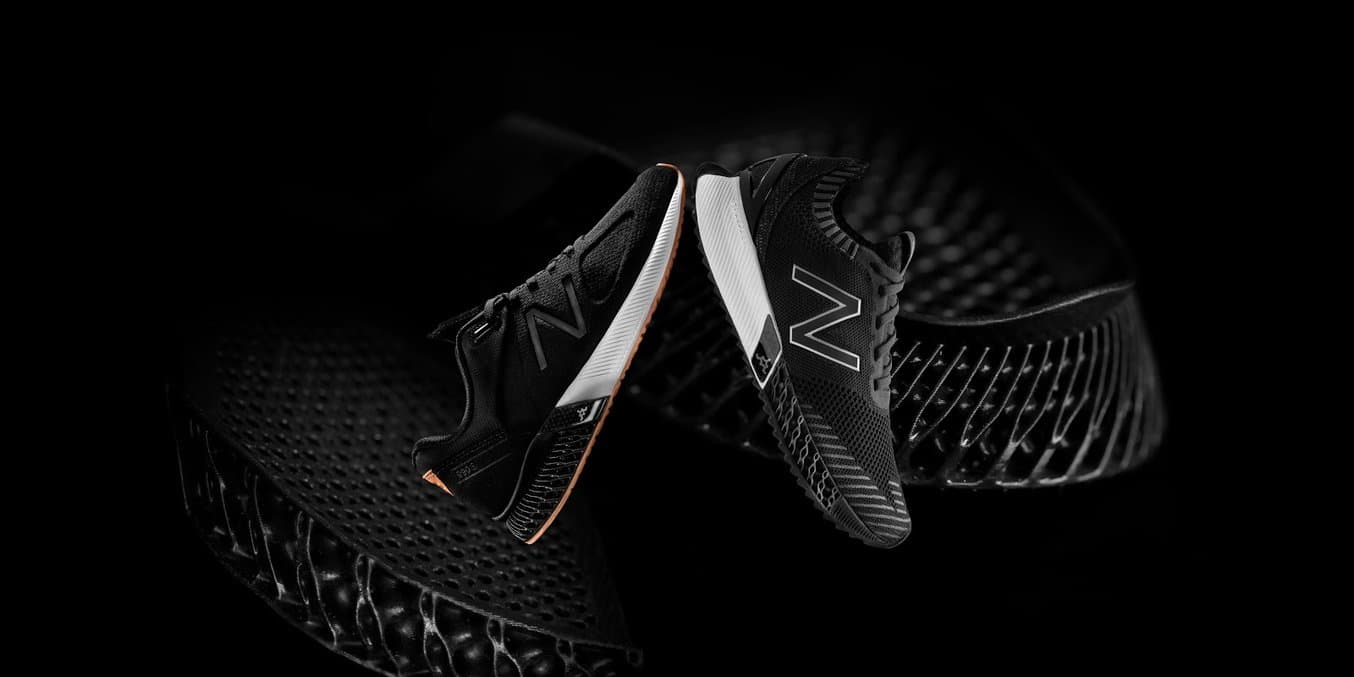
Le 990S TripleCell et le FuelCell Echo Triple.
Le secteur des chaussures de sport a depuis longtemps eu recours à la technologie pour optimiser les performances de leurs produits, et les options de personnalisation se multiplient comme jamais avec le processus numérique.
De grandes marques telles que New Balance, Adidas et Nike ont reconnu la puissance de la fabrication additive et cherchent à produire en masse des semelles intermédiaires sur mesure fabriquées en matériaux d'impression 3D. Ici comme dans les autres secteurs, le processus numérique viendra en renfort des méthodes de fabrication traditionnelles. La fabrication des composants essentiels et hautement personnalisés de chaque produit sera confié à l'impression 3D et le reste aux méthodes traditionnelles.
Compte tenu des propriétés uniques requises pour leurs chaussures, New Balance a travaillé avec Formlabs pour créer un matériau d'impression personnalisé capable de résister à l'usure quotidienne d'une chaussure de sport. Les matériaux de la chaussure sont confrontés à une multitude d'environnements et doivent faire face à divers niveaux de pression, et ce des milliers de fois tous les jours. Conçue pour créer des structures en treillis élastiques et solides, Rebound Resin présente un retour élastique bien plus élevé, une résistance au déchirement et une capacité d'allongement bien supérieures à tout autre matériau Formlabs. Rebound Resin est suffisamment résistante pour être utilisée dans des joints, des garnitures et des intérieurs automobiles. Elle est également suffisamment souple et légère pour convenir dans la semelle d'une chaussure.
« Un des éléments qui nous motive le plus, c'est d'offrir au coureur une expérience différente. »
Katherine Petrecca, Directrice Générale de Chaussures au Innovation Design Studio, New Balance
Une nouvelle façon de raconter des histoires
L'impression 3D a déjà été intégrée à la production des films d'Hollywood et est largement utilisée pour réaliser des effets spéciaux et des costumes.
Alors que la réalisation des créatures de film les plus fantastiques nécessitait auparavant un travail artisanal méticuleux, la pression toujours plus forte des délais de plus en plus courts à laquelle est soumis maintenant le secteur cinématographique exigeait une méthode plus rapide de création des effets spéciaux. Les studios d'effets spéciaux comme Aaron Sims Creative utilise maintenant une approche hybride, où le processus numérique vient améliorer les effets spéciaux pratiques, afin de créer de nouvelles opportunités de collaboration et de réduire les délais de réalisation de nouvelles idées.
« Le Démogorgon a été l'une des premières impressions que nous avons effectuées avec les imprimantes 3D Formlabs, et nous avons été sidérés. Avant, nous sous-traitions toujours l'impression. Le fait de pouvoir le faire en interne, et de voir là sous nos yeux un modèle dont nous avions participé à la conception dès le tout début, a été réellement merveilleux. Cela nous a ramenés aux jours où nous modelions de l'argile », nous dit Aaron Sims.
Un nouveau type de danse et de musique
Le potentiel artistique de l'impression 3D ne se limite pas à l'art physique. Elle a aussi la capacité d'apporter des dimensions totalement nouvelles à la danse ou à la musique. Compte tenu de la liberté de conception offerte par l'impression 3D, même les instruments les plus complexes ou uniques peuvent être modifiés ou créés de toutes pièces, pour une fraction du prix des instruments fabriqués traditionnellement.
Tout le monde peut par exemple reconnaître la forme d'un violon, qui est restée pratiquement inchangée à travers les siècles. La musique de violon est si connue que l'instrument a atteint un statut presque légendaire dans notre culture. Brian Chan, ingénieur chez Formlabs, s'est mis au défi de créer un violon acoustique entièrement fonctionnel avec une imprimante 3D.
Restauration d'art : redonner vie aux pièces anciennes
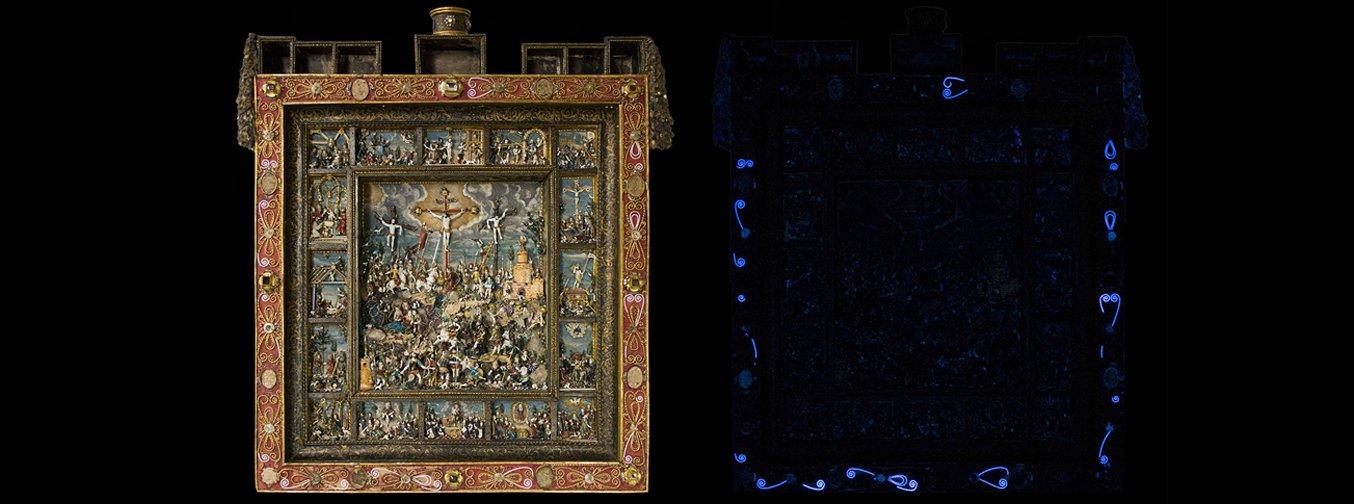
La numérisation 3D, la CAO et l'impression 3D ont été utilisées pour restaurer des œuvres de quelques-uns des artistes les plus fameux de l'histoire comme Michel-Ange et Léonard de Vinci et leur redonner leur gloire passée.
Les projets de restauration d'œuvres d'art peuvent tirer parti de l'impression 3D et de la numérisation 3D, deux technologies puissantes qui permettent aux constructeurs de prendre des objets physiques, de les transformer en formes tridimensionnelles, d'y apporter des modifications ou des restaurations, puis de réimprimer les pièces.
Mattia Mercante utilise la reproduction 3D pour remplacer des parties de sculptures et d’œuvres d’art manquantes à l’institut de renommée mondiale Opificio, situé à Florence. Il permet ainsi aux visiteurs de les admirer telles que le souhaitaient les artistes.
Dans le cas d'un reliquaire du XVIIe siècle, Mercante a scanné d’autres détails complexes de l’œuvre à l’aide d’un scanner 3D à lumière structurée HP, puis il a reproduit les pièces manquantes avec une imprimante 3D Formlabs. Les pièces ont été peintes pour ressembler le plus possible aux décorations originales. Mieux encore : la restauration n’a nécessité aucune modélisation CAO. Elle a été réalisée rapidement et pour un coût moindre que si elle avait été restaurée à la main.
Avions, crânes et valises : résoudre le crime parfait
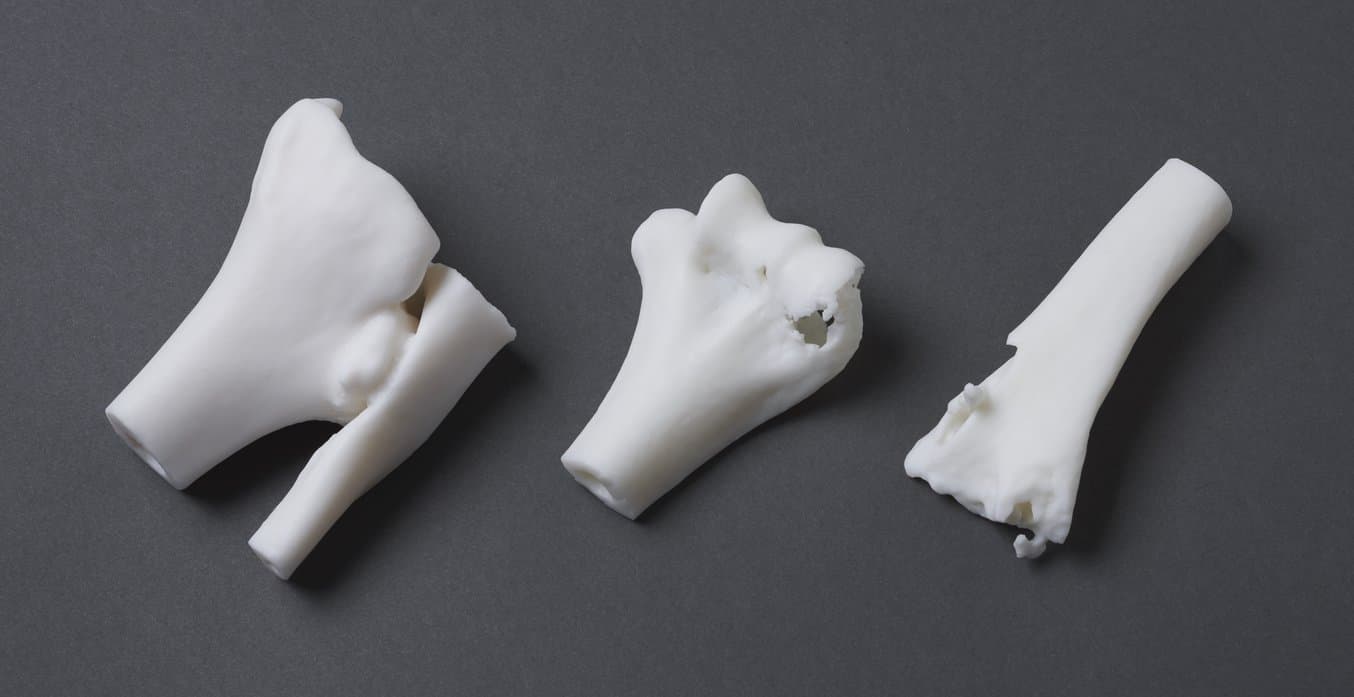
L'impression 3D présente autant d'utilité en reconstruction qu'en production. Le travail d'un portraitiste judiciaire est souvent rendu difficile par le manque d'indices. Les techniques numériques peuvent s'avérer extrêmement utiles dans les enquêtes judiciaires et venir en aide aux portraitistes pour reconstituer des modèles précis de personnes ou de victimes.
Dans ce cas, la procédure numérique consiste à transformer des scans obtenues par tomographie calculée par ordinateur en pièces 3D afin d'aider à l'identification. Par exemple, lorsque les enquêteurs ne trouvent comme indice qu'un morceau de crâne, une imprimante peut modéliser et recréer l'échantillon complet.
Des reconstitutions de l'aspect de victimes de crime ont déjà joué un rôle essentiel dans le domaine de la justice, prouvant une fois de plus l'utilité de l'impression 3D, au-delà des considérations relatives à la conception ou à l'efficacité en production.
Tout comme l'impression 3D peut être utilisée pour la planification préopératoire, les tomodensitogrammes des victimes de crimes peuvent aider les détectives à se rapprocher des os. Les tomodensitogrammes et les radiographies des dépouilles peuvent être utilisées pour produire des répliques imprimées en 3D de diverses parties du corps. Ensuite, le pathologiste peut déterminer les circonstances complètes d'un crime, du nombre de participants jusqu'à la nature de l'arme utilisée.
Construire de meilleures prothèses
L'effet de l'impression 3D ne se limite pas à l'amélioration des processus de travail ou au prototypage rapide. Elle peut complètement changer des vies. 30 millions de personnes ont besoin de membres artificiels et d'appareils orthopédiques, et l'impression 3D donne l'espoir de fournir de nouvelles solutions contournant les obstacles de coût et de spécifications rencontrés jusqu'alors.
L'impression 3D peut constituer une alternative moins coûteuse qui, comme de nombreuses avancées similaires en médecine, peut contribuer à une thérapie mieux adaptée aux besoins du patient. Le moindre prix et la capacité de personnalisation des techniques d'impression 3D peut profondément améliorer la qualité de vie de ceux qui souffrent de blessures ou d'invalidité, comme en témoigne l'histoire de ce père et de son fils.
Nous avons pu voir ce type d'innovation avec le fils de Matej et Mateja, Nik, qui souffrait de paralysie cérébrale. Matej s'est lancé avec un objectif simple : permettre à Nik de marcher. Des mois de recherche et de développement ont suivi, jusqu'à ce qu'une orthèse sur mesure puisse être imprimée en 3D. Elle soutient et corrige la posture de Nik, ce qui l'a finalement aidé à faire ses premiers pas tout seul. Regardez la vidéo complète ci-dessus et lisez leur histoire.
En plus de prothèses qui permettent de restituer des fonctions corporelles, il est possible d'imprimer en 3D des dispositifs qui sont, à certains égards, encore meilleurs que les membres qu'ils remplacent. Grâce à l'impression 3D, il ne s'agit plus d'une vision futuriste de membres bioniques du genre de Robot-Cop, mais de prothèses de pointe bien réelles. Certaines entreprises comme Psyonic fournissent déjà des prothèses avancées.
Nouvelles formes de logement et de construction
Certains pensent sans doute que l'impression 3D sert à produire de petits objets que l'on peut tenir en main. Des entreprises ont cherché à exploiter des flux de travail additifs pour produire des composants fonctionnels beaucoup plus grands. Ces dernières années, diverses initiatives ont été lancées pour créer des maisons et d'autres structures plus grandes produites entièrement par impression 3D, ouvrant de nouvelles perspectives dans le domaine de la construction et du logement durables.
La technique d'impression 3D donne toute liberté aux architectes au niveau de la forme, même avec des matériaux de construction moins malléables comme le béton. De façon plus générale, elle permet de construire des maisons durables et efficaces en énergie, qui respectent également les normes de confort modernes. Ce mode de construction pourrait être entièrement exempt de déchets, moins coûteux et plus écologique que les méthodes traditionnelles.
Si vous ne comptez pas emménager dans une maison imprimée en 3D dans un avenir proche, vous pouvez dès aujourd'hui découvrir des projets de construction imprimés en 3D. Le pont MX3D à Amsterdam est actuellement ouvert à la circulation piétonne. Selon dezzen.com, « la structure contient 4500 kilogrammes d'acier inoxydable, qui ont été imprimés en 3D par des robots dans une usine sur une période de six mois avant d'être mis en place par une grue au-dessus du canal cette année. »
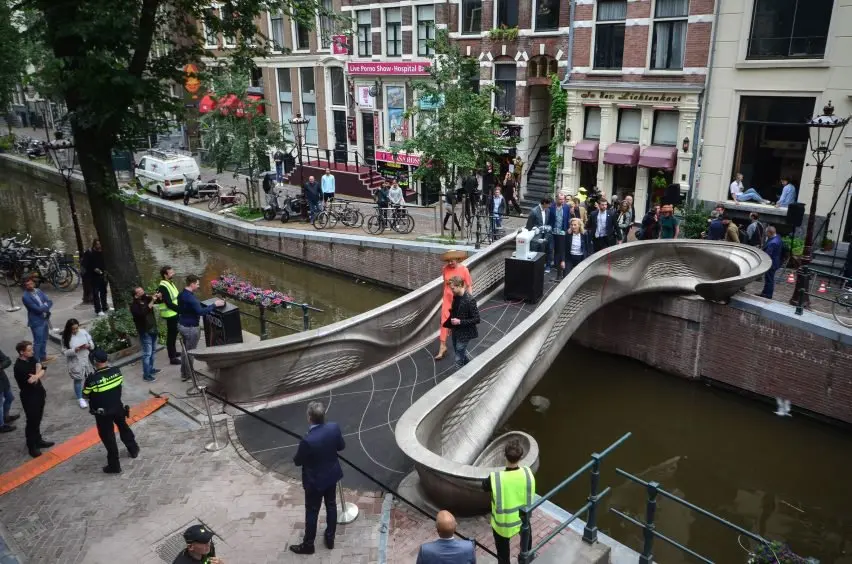
Source: www.dezeen.com
La course à l'espace
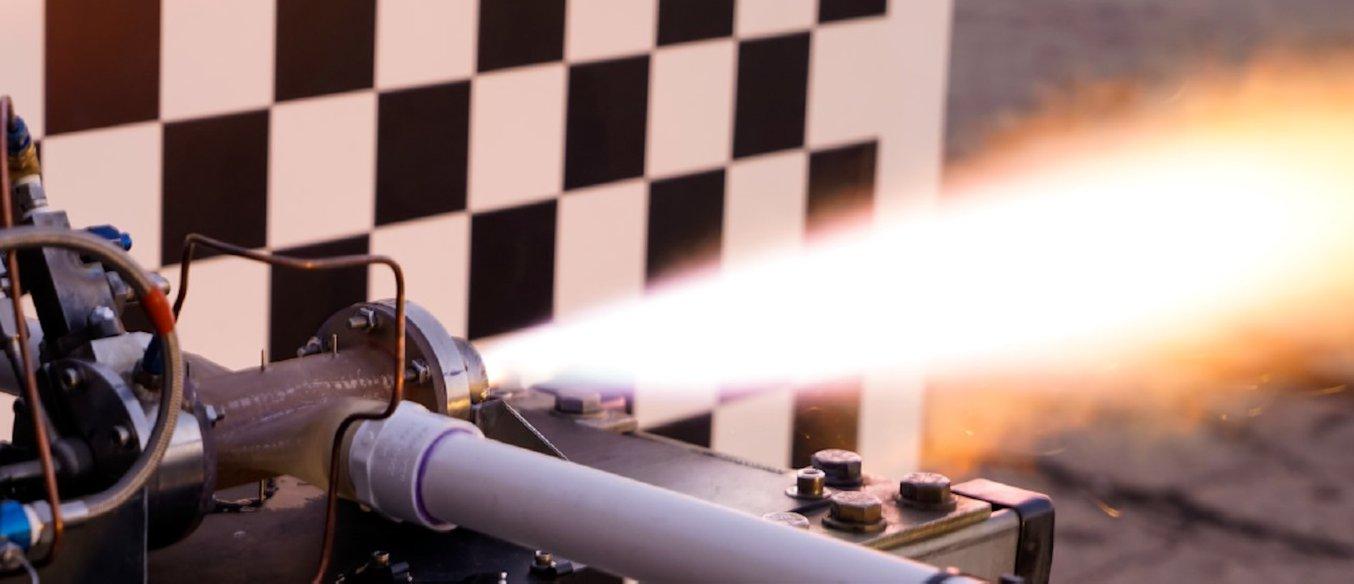
Avec une barrière à l'entrée parmi les plus hautes de tous les secteurs industriels du monde, le voyage dans l'espace est un domaine d'innovation idéal pour l'impression 3D. Réduire les frais de prototypage pour des outils et des machines coûteux spécifiques à l'aérospaciale permettra aux petites entreprises d'innover dans ce secteur.
La start-up Relativity appartenant au secteur de l'aérospatiale a fait des essais de fabrication additive de moteurs de fusée en aluminium. Si cette application est un succès, elle va nettement réduire les coûts et les difficultés pratiques du voyage dans l'espace, ouvrant la voie à une nouvelle activité économique au potentiel de croissance énorme.
Masten Space Systems est un autre acteur de l'impression 3D dans l'industrie aérospatiale : fondée en 2004, l'entreprise est spécialisée dans les fusées à décollage et atterrissage verticaux. L'entreprise lancera une mission vers la lune en 2022 dans le cadre du projet CLPS (Commercial Lunar Payload Services) de la NASA. Grâce aux imprimantes 3D de Formlabs, Masten a produit des moteurs de fusée en plastique pour les tests de R&D.
L'entreprise a déjà de l'expérience dans l'impression 3D de plastiques et de métaux. Elle a même participé au développement de nouveaux métaux personnalisés pour le projet Tipping Point de la NASA. « Nous aimons vraiment les moteurs de fusée imprimés en 3D parce qu'ils permettent de faire beaucoup de choses que vous ne pouvez pas faire dans un processus de fabrication traditionnel. Dans le but de réduire les coûts et d'accroître notre efficacité, nous avons commencé à étudier la manière dont nous pourrions utiliser les imprimantes stéréolithographiques, notamment après le lancement de Ceramic Resin et de High Temp Resin. Leurs propriétés techniques leur permettent d'être utilisées dans une fusée », a déclaré Matthew Kuhns, ingénieur en chef chez Masten.
High Temp Resin et Rigid 10K Resin de Formlabs sont des exemples de matériaux présentant des propriétés techniques optimales pour les applications aérospatiales. High Temp Resin est conçue pour le prototypage fonctionnel dans des applications à haute température, tandis que Rigid 10K Resin est le matériau le plus rigide de notre gamme d'ingénierie, ce qui la rend adaptée aux prototypes de qualité industrielle.
Rendre la conception générative possible
La conception générative est la prochaine frontière à franchir en conception CAO par les ingénieurs de pratiquement tous les secteurs de production industrielle. Elle exploite la puissance de l’intelligence artificielle (IA) pour développer de nouvelles itérations de modèles haute performance, ce qui aide à résoudre des problèmes complexes, à réduire le poids des composants et les coûts de fabrication, à adapter la personnalisation et à optimiser les performances.
L'impression 3D est parfaite pour créer des objets complexes et organiques. Grâce à un large éventail de propriétés matérielles adaptées à des applications commerciales spécifiques, attendez-vous à voir des conceptions jamais vues auparavant. Les ingénieurs peuvent exploiter la conception générative pour trouver et tester des itérations de modèles complexes rapidement, efficacement et à l’échelle, ce qui permet de réduire radicalement les durées de recherche et développement de nouveaux produits. Ensuite, grâce à leur imprimante 3D en interne, ils peuvent donner vie à leur conception complexe pour la tenir en mains et l'examiner.
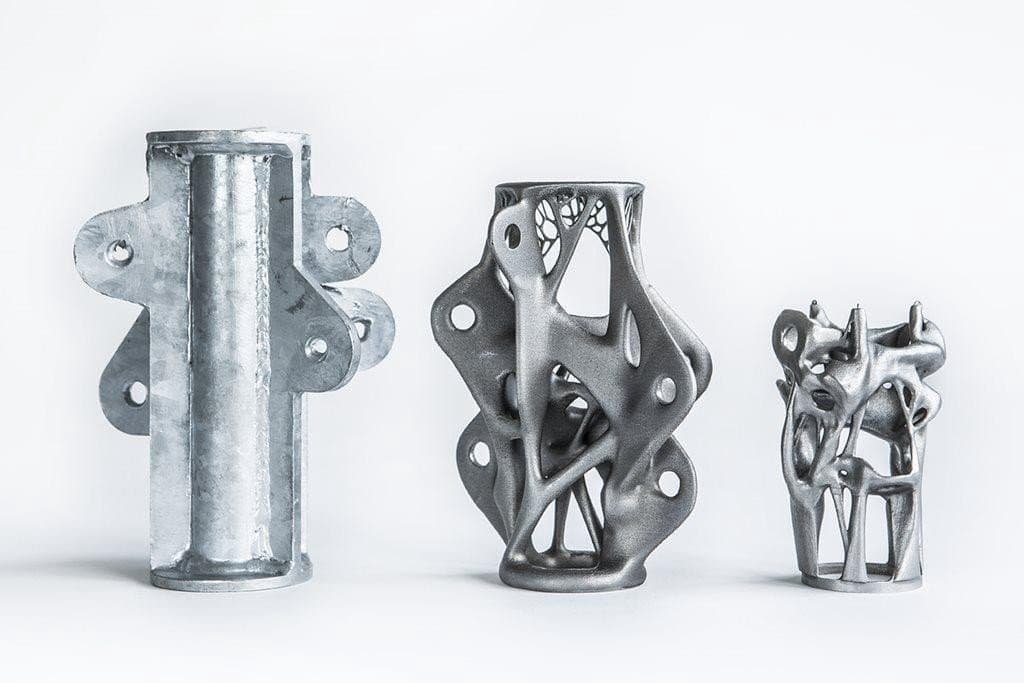
Les supports et les entretoises où les forces appliquées sont bien définies sont celles couramment traitées par conception générative.
Vous souhaitez en savoir plus sur la conception générative ? Regardez notre webinaire gratuit au cours duquel vous apprendrez : pourquoi vous voyez tant de supports lorsque vous recherchez le terme « conception générative » sur Google, comment résoudre un problème de conception dans Autodesk Fusion 360, comment une entreprise a pu alléger de 40 % un support de fauteuil roulant en utilisant pour la première fois un processus de conception générative, et bien plus encore.
Former la main-d'œuvre de demain
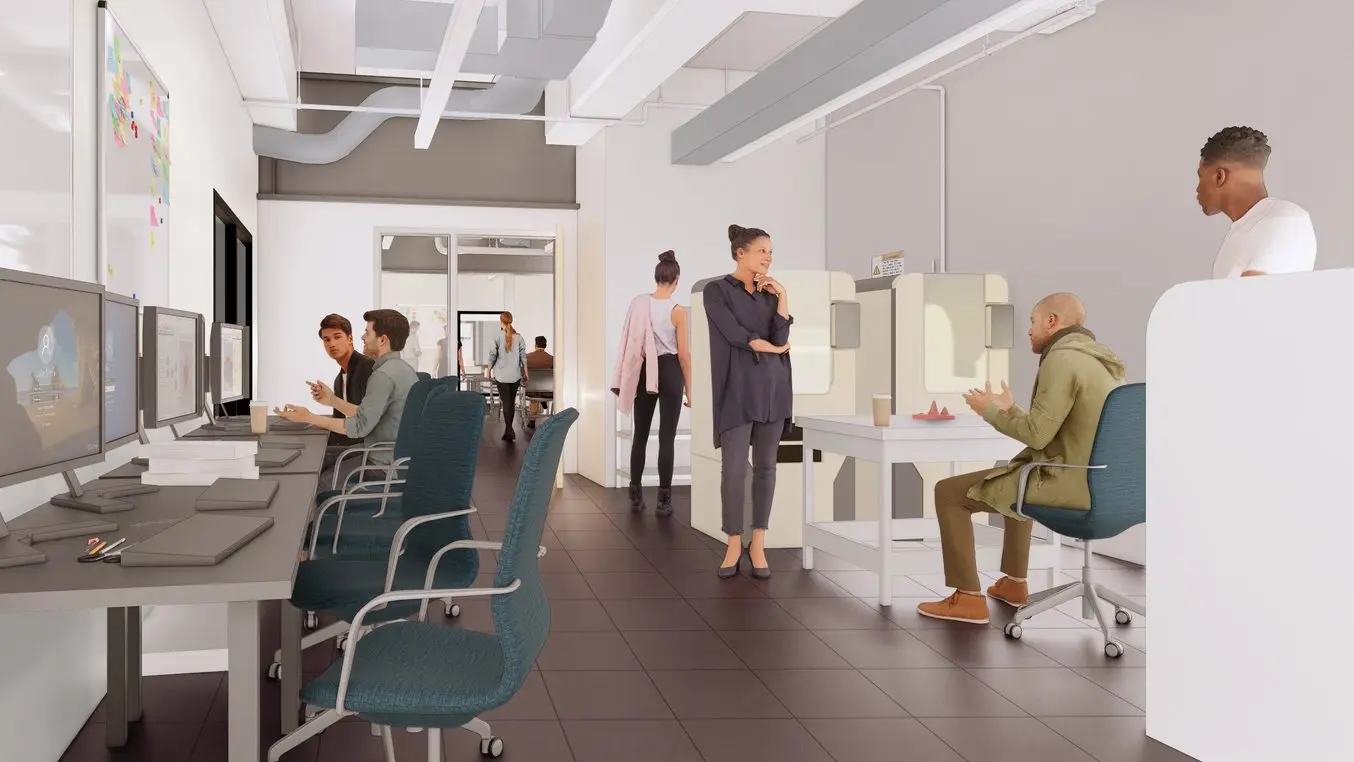
Origin Labs, au sein de l'Innovation Hub, disposera d'un espace dédié à l'impression 3D pour les étudiants et la communauté au sens large.
La plupart des établissements d'enseignement supérieur s'attachent à préparer leurs étudiants à la main-d'œuvre de demain. L'université d'État de Pennsylvanie se concentre également sur la main-d'œuvre actuelle et a récemment investi des millions de dollars dans la construction du centre d'innovation Eric J. Barron, qui sert le public ainsi que la communauté universitaire.
La chaîne de montagnes des Appalaches, dans l'ouest et le centre de la Pennsylvanie, a toujours été le centre de l'industrie charbonnière du pays et a bénéficié, grâce à elle, d'une économie solide et prospère dans la première moitié du XXe siècle. Lorsque les économies mondiales et nationales se sont détournées du charbon, la région des Appalaches a souffert, avec un taux de chômage plus élevé et l'un des taux de revenu des ménages les plus bas du pays, comme l'indique la Commission régionale des Appalaches.
Au cours des deux dernières décennies, les dirigeants au niveau local et étatique ont cherché à changer cette situation en investissant dans la production industrielle, l'éducation et la technologie. La Commission régionale des Appalaches offre des subventions d'un million de dollars pour « soutenir les possibilités et les établissements d'enseignement, notamment en reliant le développement des compétences et la formation de la main-d'œuvre aux intérêts et aux possibilités des entreprises locales et régionales ».
Alors que la fabrication additive se développe rapidement dans de nombreuses entreprises (comme le montre bien cet article de blog !), les responsables du recrutement recherchent des employés formés au travail dans des espaces numériques et maîtrisant la CAO. Les universités cherchent à répondre à cette demande du marché en créant des centres d'innovation importants et bien financés.
Améliorer les plans de cours traditionnels
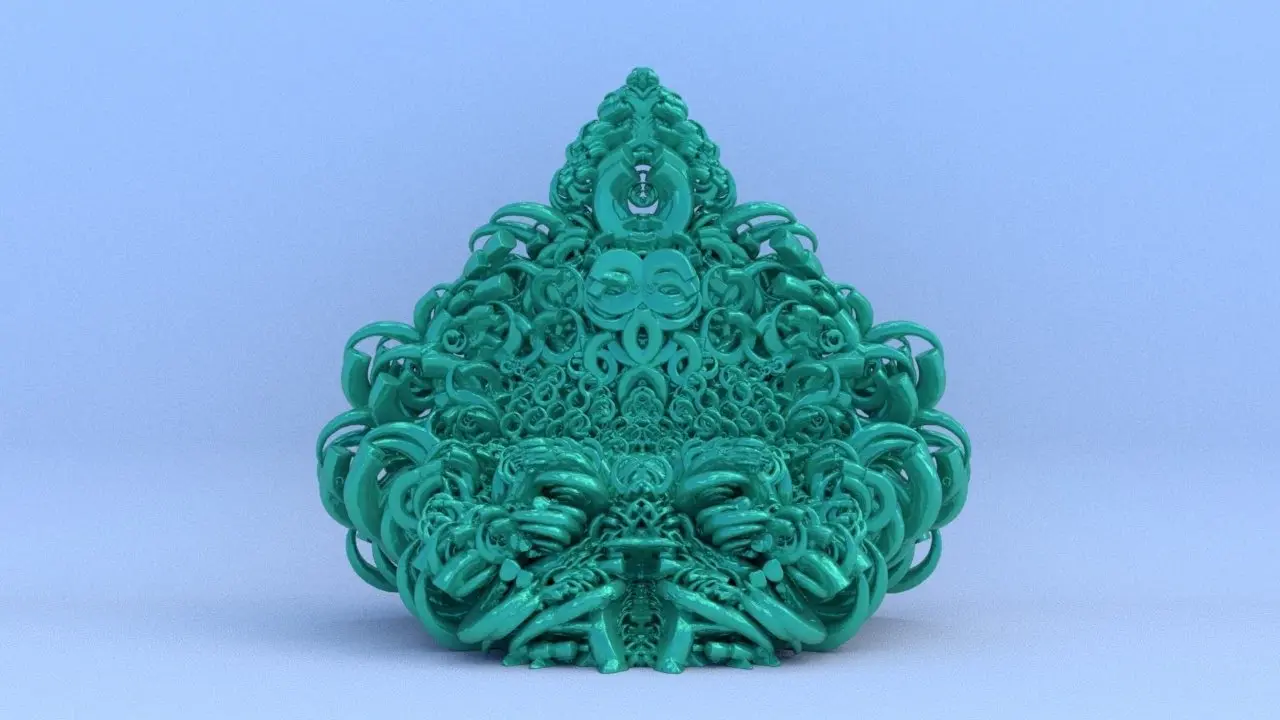
Outre la formation de la main-d'œuvre de demain à la CAO et à l'impression 3D, les universités commencent à réaliser quels avantages les imprimantes 3D peuvent apporter dans un large éventail de disciplines éducatives.
À UMass Lowell, ceci signifie moderniser ses programmes de sculpture et de conception 3D pour les adapter au XXIe siècle. C'est dans cet optique que Yuko Oda a rejoint l'université en 2017, où elle a commencé par commander une multitude d'imprimantes 3D, dont un appareil SLA de Formlabs.
Yuko partage ses passions pour l'art et pour la technologie dans ses cours. Elle enseigne actuellement la sculpture, la conception 3D, l'animation et les médias interactifs. La plupart des étudiants savent qu’ils doivent maîtriser l’animation 3D et la modélisation 3D pour leurs futures carrières dans divers domaines, notamment la conception de sculptures pour le cinéma. Pour les artistes, la modélisation 3D est devenue une compétence essentielle.
« Les élèves sculptent un modèle 3D, l'importent dans Zbrush, puis l'impriment en différentes résines, y compris Clear Resin. La capacité des machines Formlabs à montrer les détails modifiés dans Zbrush est inégalée par rapport aux autres imprimantes du laboratoire. »
Yuko Oda
L'un des développements les plus prometteurs du domaine de la structure est l'intégration de l'impression 3D et de la réalité virtuelle. Cela est particulièrement important pour les étudiants intimidés par la conception 3D. La réalité virtuelle fait rapidement tomber les obstacles à la conception 3D, et permet aux artistes et aux étudiants de créer avec leurs mains dans des programmes tels que Oculus Medium. Yuko a appris à des élèves de 4e à créer des objets en 3D en 30 minutes en réalité virtuelle, puis à les imprimer sur une imprimante 3D. Même pour les sculpteurs expérimentés, la réalité virtuelle réduit le temps qu'il faut pour passer de l'idée à l'objet physique, et elle peut ouvrir de nouveaux domaines d'art expérimental.
Sauver un oiseau en voie de disparition
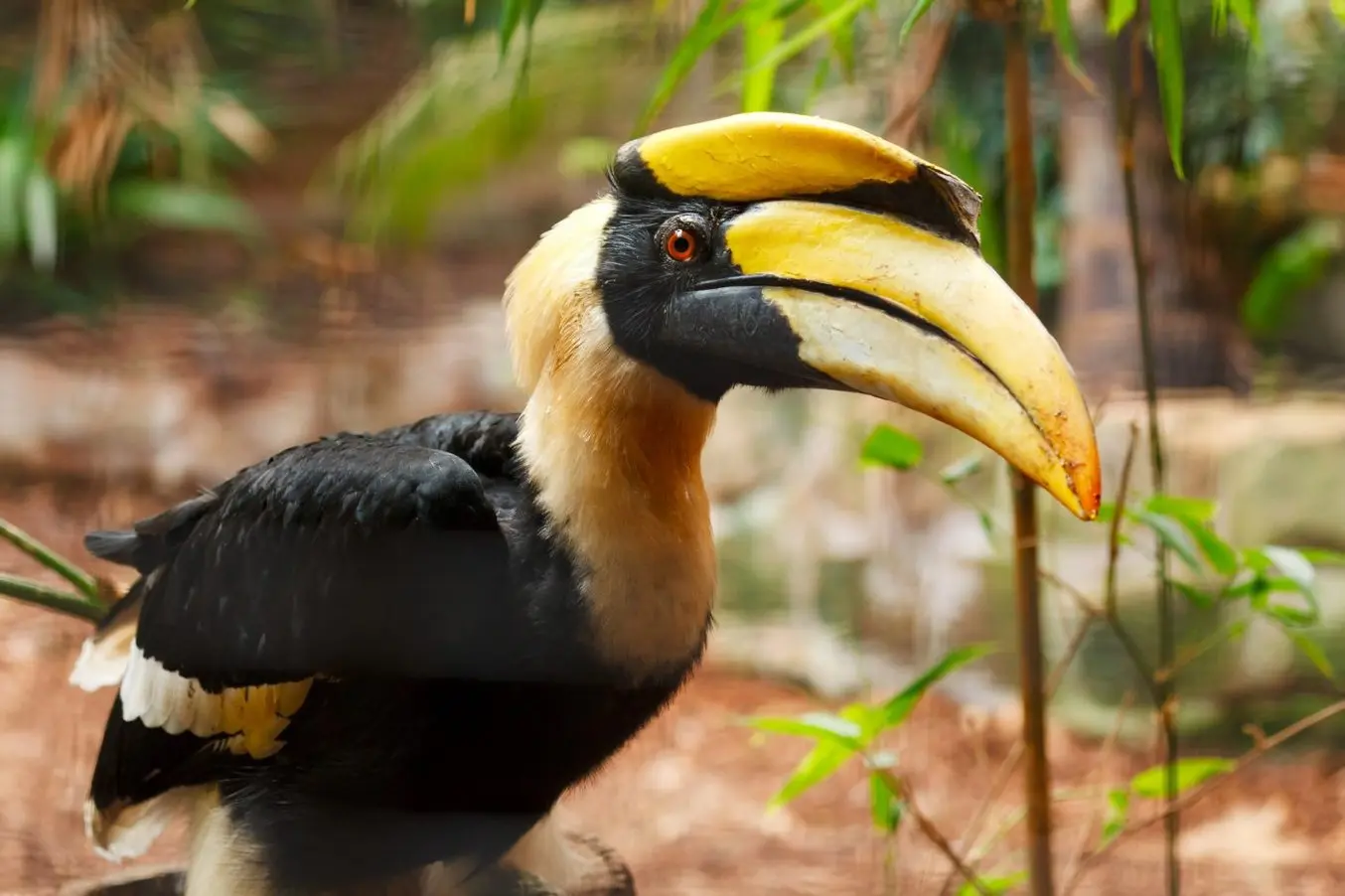
Des soigneurs du ZooTampa effectuant un contrôle de routine sur un grand calao de 25 ans ont découvert une lésion à la base du casque de l'oiseau, l'excroissance jaune en forme de casque située au-dessus de la tête. Des examens plus poussés ont permis de déterminer que l'oiseau, nommé Crescent, souffrait d'un cancer potentiellement mortel.
La tumeur située près du crâne de l'oiseau n'a pas pu être retirée, car cette partie contient des sinus. L'équipe a cherché à savoir s'il était possible de retirer le casque et de le remplacer par une réplique imprimée en 3D, conçue spécifiquement pour cet oiseau. Des prothèses et des dispositifs spécifiques aux patients ont déjà été utilisés pour des humains, mais jamais pour un grand calao. Serait-ce possible, et si oui, quels matériaux seraient sans danger pour l'oiseau ?
ZooTampa indique que le « bec de remplacement » a été imprimé en 3D avec BioMed White Resin. Ce matériau blanc et opaque est destiné aux applications biocompatibles qui nécessitent un contact prolongé avec la peau ou un contact à court terme avec les muqueuses. Occupant une place particulière au sein de la gamme de matériaux d'impression 3D SLA Formlabs, ce matériau de qualité médicale convient pour un contact à court terme avec les tissus, les os et la dentine.
Résoudre les perturbations de la chaîne d'approvisionnement
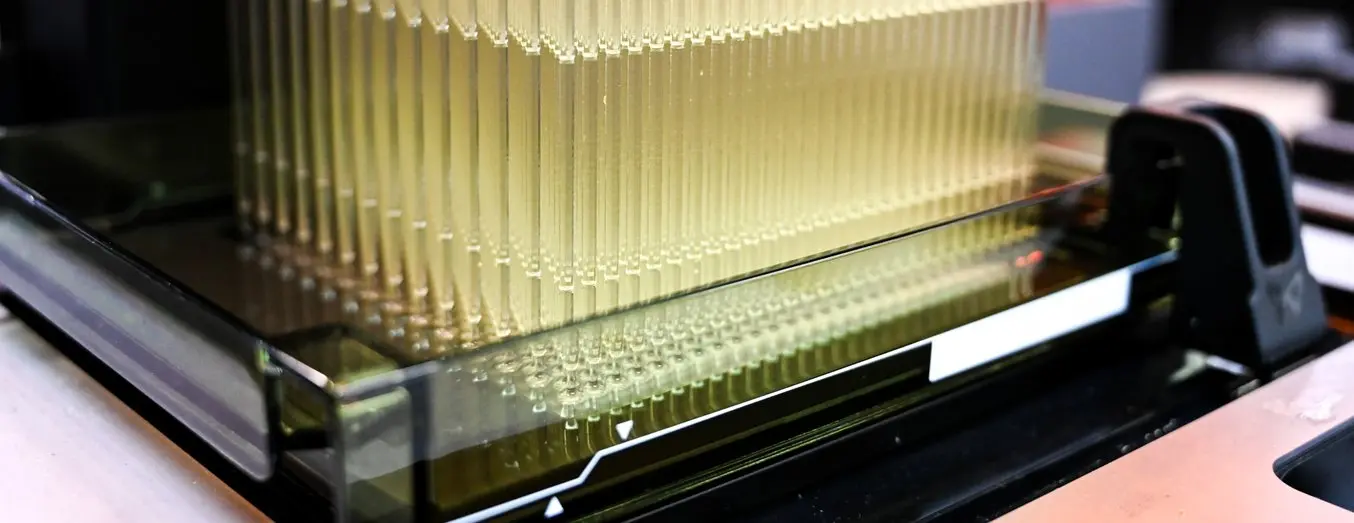
Pendant la pandémie de COVID-19 et les crises de la chaîne d'approvisionnement qui ont suivi en 2021/2022, de nombreuses entreprises se sont tournées vers l'impression 3D pour continuer à produire. Le recours accru à l'impression 3D en interne pour créer des pièces d'utilisation finale, telles que des pièces de rechange pour les machines, a fait de la fabrication additive un outil essentiel pour résoudre les problèmes de la chaîne d'approvisionnement.
Formlabs a commandé le rapport 2022 sur les applications d'impression 3D pour mieux comprendre ce qui, le cas échéant, a changé récemment parmi les utilisateurs d'impression 3D. Le rapport démontre le changement d'attitude à l'égard de l'impression 3D, qui est passée d'un outil de R&D et de prototypage à une technologie de fabrication précieuse permettant de répondre aux préférences changeantes des consommateurs et de résoudre les problèmes de la chaîne d'approvisionnement. Qu'il s'agisse d'alléger les contraintes de la chaîne d'approvisionnement, de créer des produits en série limitée ou de personnaliser des appareils, les entreprises ont été forcées de repenser la manière dont elles produisent des biens pour répondre à la demande des clients.
Impression 3D Imprimantes 3D
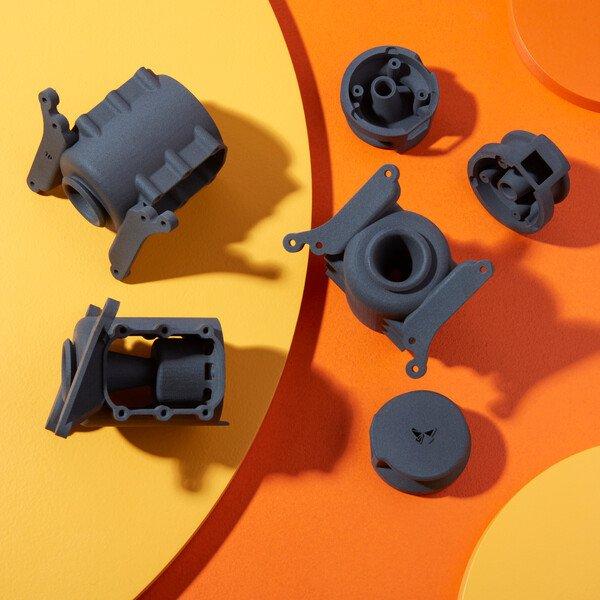
Pièces finales imprimées sur la Fuse 1.
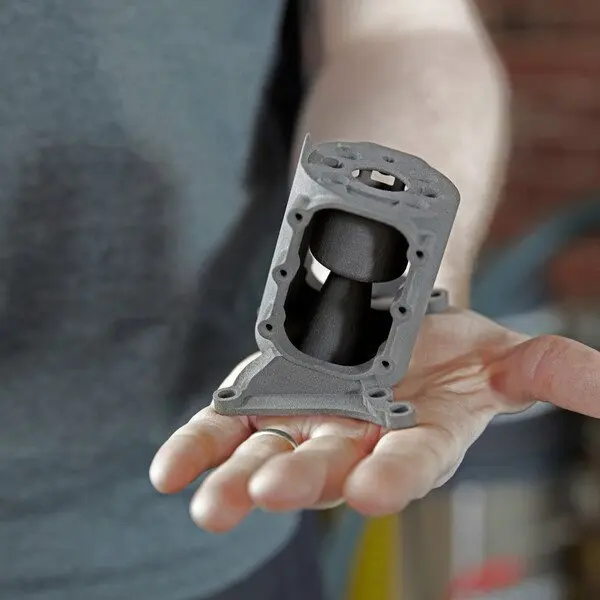
Un purgeur de capteur IR imprimé sur la Fuse 1 avec Nylon 12 Powder.
La construction d'imprimantes 3D est toujours un défi d'ingénierie. Obtenir une performance de niveau industriel avec une imprimante 3D minimaliste a nécessité plus de 8 années de travail d’ingénierie et de conception. C'est notamment le cas de la très attendue imprimante 3D à frittage sélectif par laser (SLS) de Formlabs, la Fuse 1.
L’un des outils utilisés pour réaliser des prototypes a été la Fuse 1 elle-même. Mais le recours à l’impression 3D ne s’est pas arrêté au prototypage. Aujourd’hui, toutes les Fuse 1 livrées aux clients contiennent plusieurs pièces de production imprimées directement sur la Fuse 1 avec Nylon 12 Powder.
L’utilisation de l’imprimante SLS Fuse 1 pour le prototypage et la création de pièces finales offrait trois avantages principaux selon Seth Berg, le responsable du programme d’ingénierie supervisant la Fuse 1 :
- La liberté de créer des pièces complexes sans structures de support internes.
- L’allègement de la chaîne logistique en prototypant et en créant des pièces finales en interne.
- L’élimination de la sous-traitance afin d’obtenir une solution économique pour la production en série limitée avec un matériau en Nylon 12 Powder éprouvé et polyvalent.
Pour voir comment l'équipe a procédé et les pièces finales imprimées en 3D, regardez la vidéo ci-dessous.
Fournitures d'urgence COVID-19 : écouvillons nasaux
En mai 2020, Forbes a publié un article intitulé « Comment l'impression 3D d'écouvillons de test aidera l'Amérique à faire face à la pénurie ». Ils ont remarqué que de grands noms du secteur de l'impression 3D se sont unis pour s'attaquer de front à la pénurie d'écouvillons COVID-19, avec notamment Formlabs, HP, Origin, Carbon, Desktop Metal et d'autres qui collaborent pour augmenter la production d'écouvillons.
L'impact de la pandémie de COVID-19 a nécessité une réponse globale et concertée. En collaborant avec l'USF et Northwell, Formlabs a mis au point une solution qui a été déployée dans le monde entier. Grâce à sa conception accessible, à sa fabrication bon marché et à ses processus validés, l'écouvillon a permis de réaliser plus de 40 millions de tests COVID dans 25 pays. Au cours de l'année dernière, les imprimantes 3D de Formlabs ont continué à être utilisées par les gouvernements et les prestataires de soins de santé pour améliorer les tests et les soins aux patients. Cette solution globale n'est qu'un exemple de la manière dont l'agilité de l'impression 3D peut servir le bien public.
C'est ce qui s'est passé à Singapour, où Eye-2-Eye Communications a augmenté la production d'écouvillons à plus de 30 000 par jour pour assurer la sécurité de la ville.
« Cela n'a pas seulement été une excellente occasion de montrer les avantages qu'apporte l'impression 3D pour une conception et un développement rapides, mais cela a également prouvé l'efficacité de Formlabs à pouvoir produire en masse des produits dans des délais très courts. De plus, comme nous constatons des pics de cas dans le monde entier, il est rassurant de savoir que nous pouvons augmenter notre production relativement facilement pour répondre à la demande si nécessaire », a déclaré Miles Podmore, directeur général de Eye-2-Eye Communications.
Fabrication agile : Pièces après-vente / Pièces sur mesure
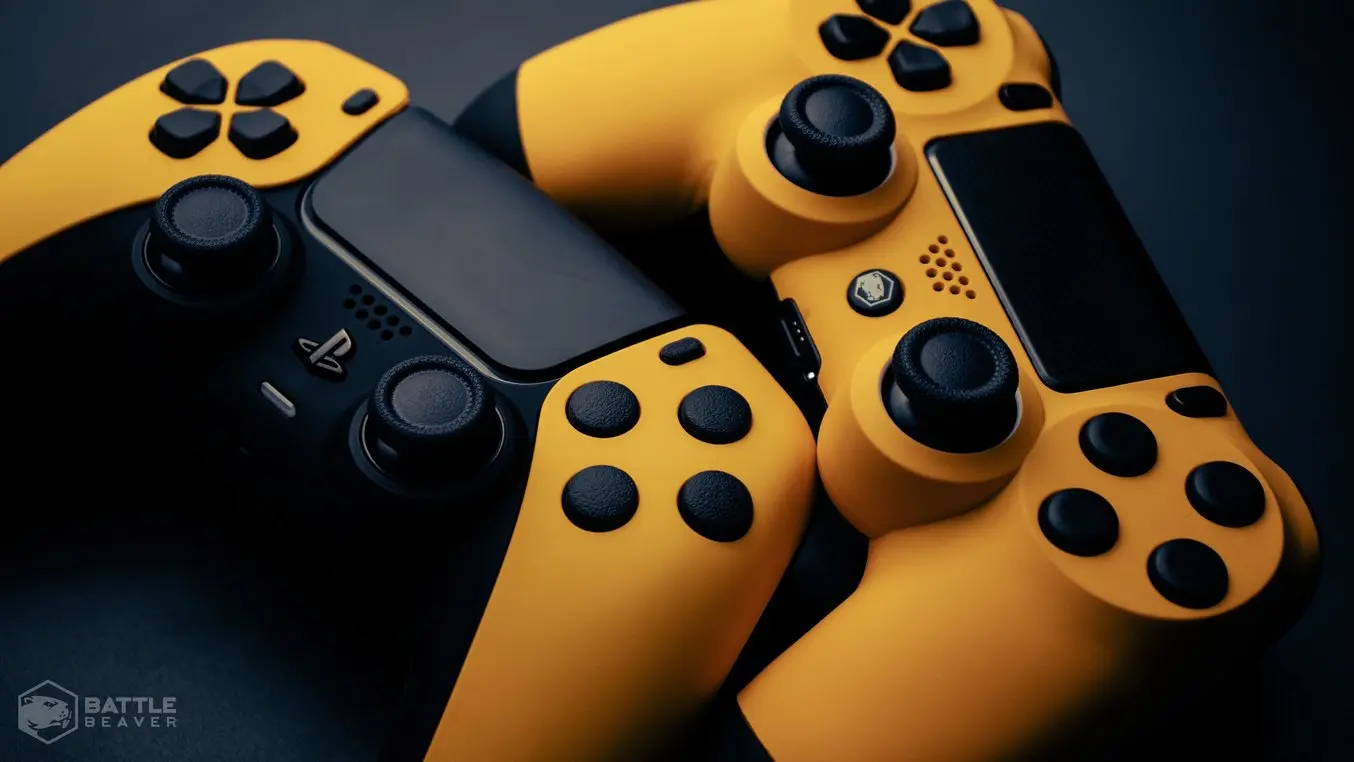
Une manette avec des boutons imprimés sur la Fuse 1 (à gauche), et une autre avec des boutons moulés par injection (à droite).
Le problème pour produire des pièces d'après-vente personnalisées, c'est qu'elles sont généralement produites en petite série et doivent s'adapter aux modifications apportées aux produits d'origine. Mais avec l'essor de l'impression 3D en interne, la fabrication personnalisée a fait son apparition dans de multiples secteurs.
Battle Beaver Customs se donne pour mission d'offrir une expérience de jeu unique grâce à des manettes de jeu personnalisées. Leurs modifications rendent les manettes plus réactives et plus compétitives, ce qui permet aux joueurs d'augmenter leur potentiel et d'atteindre des performances maximales dans toute une série de jeux. Le prototypage rapide avec l'imprimante 3D SLS Fuse 1 permet à Battle Beaver Customs de modifier rapidement la conception de ses supports et de ses boutons. Dans le secteur des produits de consommation personnalisés, des délais de production rapides peuvent faire toute la différence pour les entreprises qui cherchent à devancer leurs concurrents. Selon Michael Crunelle, responsable de la recherche et de la conception chez Battle Beaver Customs, « la Fuse 1 nous a permis d'apporter rapidement des modifications, du concept initial à la pièce finale. Nos concurrents n'arrivent pas à nous suivre. »
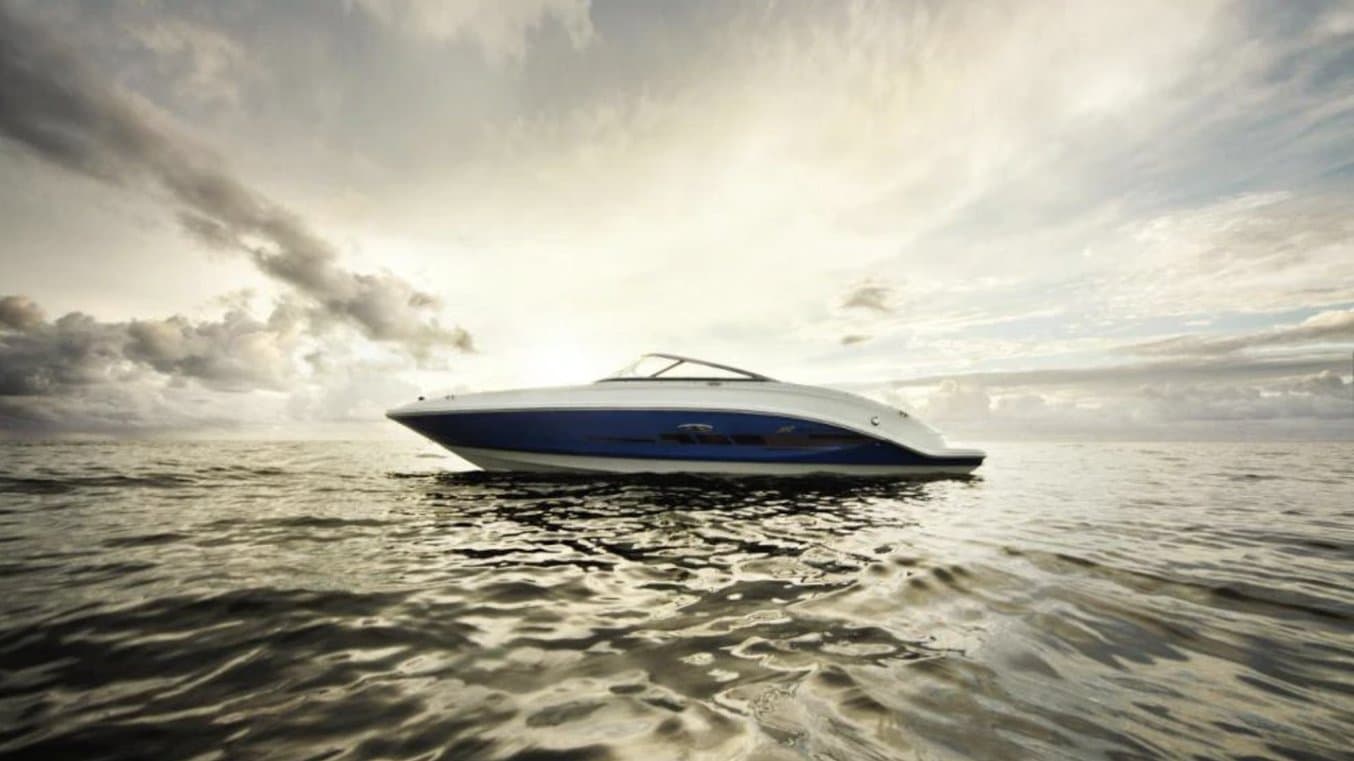
JetBoatPilot, fabricant de pièces et d'accessoires nautiques, s'est forgé une réputation dans le secteur en créant des produits d'après-vente qui améliorent les performances et le maniement à basse vitesse des bateaux à réaction.
JetBoatPilot utilise les imprimantes 3D SLA Form 3 et à frittage sélectif par laser (SLS) Fuse 1 pour prototyper et fabriquer ses pièces d'après-vente. Un produit nouvellement conçu et très performant, le Lateral Thruster 2.0, a été conçu et fabriqué avec la Fuse 1. Grâce à la Fuse 1 et à Nylon 12 Powder, JetBoatPilot a pu réduire de six fois ses coûts par rapport aux méthodes de fabrication utilisées précédemment. « J'aurais probablement fait en sorte que le prix de vente au détail de cette version (en aluminium) se situe quelque part dans la fourchette des 400 €, peut-être même des 600 €, si j'avais vraiment insisté. Mais je n'en aurais certainement pas vendu autant à 600 €. Mais maintenant je le vends à 187 €, pour le plus grand plaisir des clients. Cela représente près de vingt fois le coût des matières premières », dit Will Owens, fondateur de JetBoardPilot.
Créer les meilleures bombes de bain
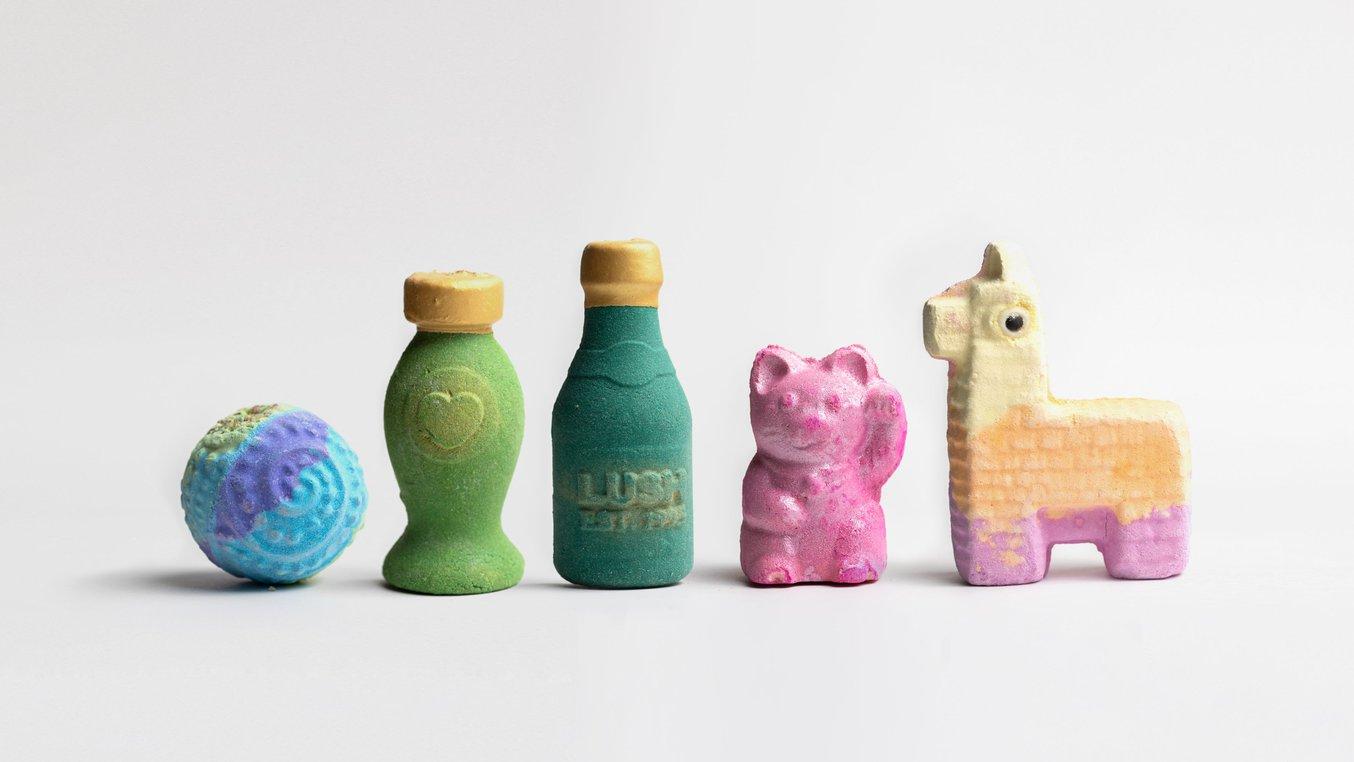
Mondialement connue pour ses produits de beauté faits main, créatifs et attrayants tels que les barres de massage, les crèmes pour le corps, les bombes de bain et bien d’autres, Lush Cosmetics est une chaîne avec 928 boutiques réparties dans 48 pays qui attribue son succès au fait de pouvoir répondre rapidement aux tendances et aux demandes des clients.
Pour donner vie à de nouveaux produits cosmétiques révolutionnaires et très détaillés, Lush a dû se tourner vers l'impression 3D pour bien plus que le prototypage de nouvelles formes. La compagnie a investi dans un centre de fabrication additive de nouvelle génération pour la création de moules, d'outils et de pièces d'utilisation finale.
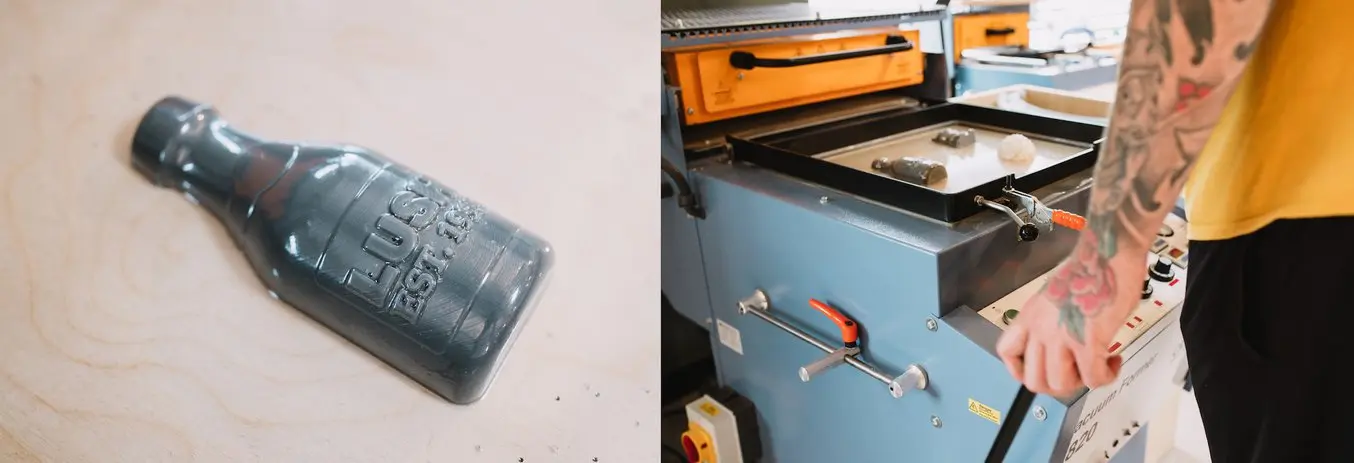
L’équipe de Lush Cosmetics forme sous vide grâce à des moules imprimés en 3D en interne.
« Nous utilisons nos imprimantes 3D Formlabs pour la création de moules, la fabrication d’outillage sur mesure et la production de pièces finales. Nous sommes une entreprise réactive, et avoir cette capacité de production en interne signifie que nous n’avons pas à partager nos modèles avec des sous-traitants, puisque nous réalisons toutes les étapes du processus de développement de produits. », a déclaré Damien Carter, responsable du laboratoire d'innovation de Lush Cosmetics.
La personnalisation de masse, accessible pour la première fois
L'impression 3D ouvre la porte à de nouvelles possibilités et opportunités commerciales, comme la personnalisation en masse. Ce qui était auparavant trop complexe, trop cher ou peu pratique à produire avec des méthodes traditionnelles est désormais disponible sans coût supplémentaire avec les technologies numériques, ce qui donne un contrôle total aux concepteurs et aux fabricants et permet de réaliser des produits entièrement personnalisables.
Un bon exemple en est Razor Maker™ de Gillette, qui donne aux clients la possibilité de personnaliser le manche de leur rasoir en choisissant divers motifs, couleurs ou en ajoutant un texte personnalisé.
« Pour Gillette, piloter Razor Maker™ représente une étape cruciale dans l’évolution de la personnalisation, dans laquelle une nouvelle technologie et de nouveaux modèles d’activité doivent s’associer pour fournir des produits aussi différents entre eux que peuvent l’être nos clients », déclare Donato Diez, responsable de la marque locale pour Gillette et Razor Maker™.
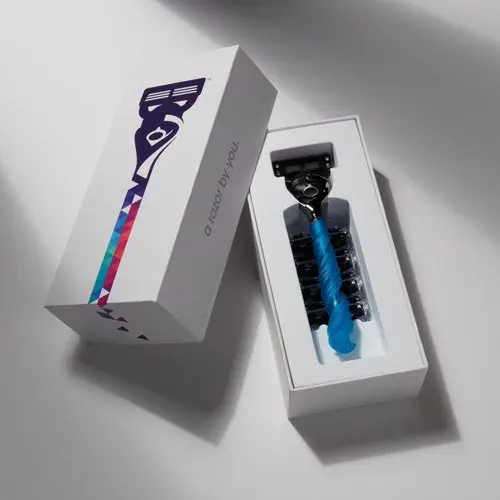
Guide de la personnalisation de masse
Ce guide donnera aux fabricants un aperçu des différentes approches de la personnalisation, des techniques les plus pertinentes et bien plus.
Imprimer des dents
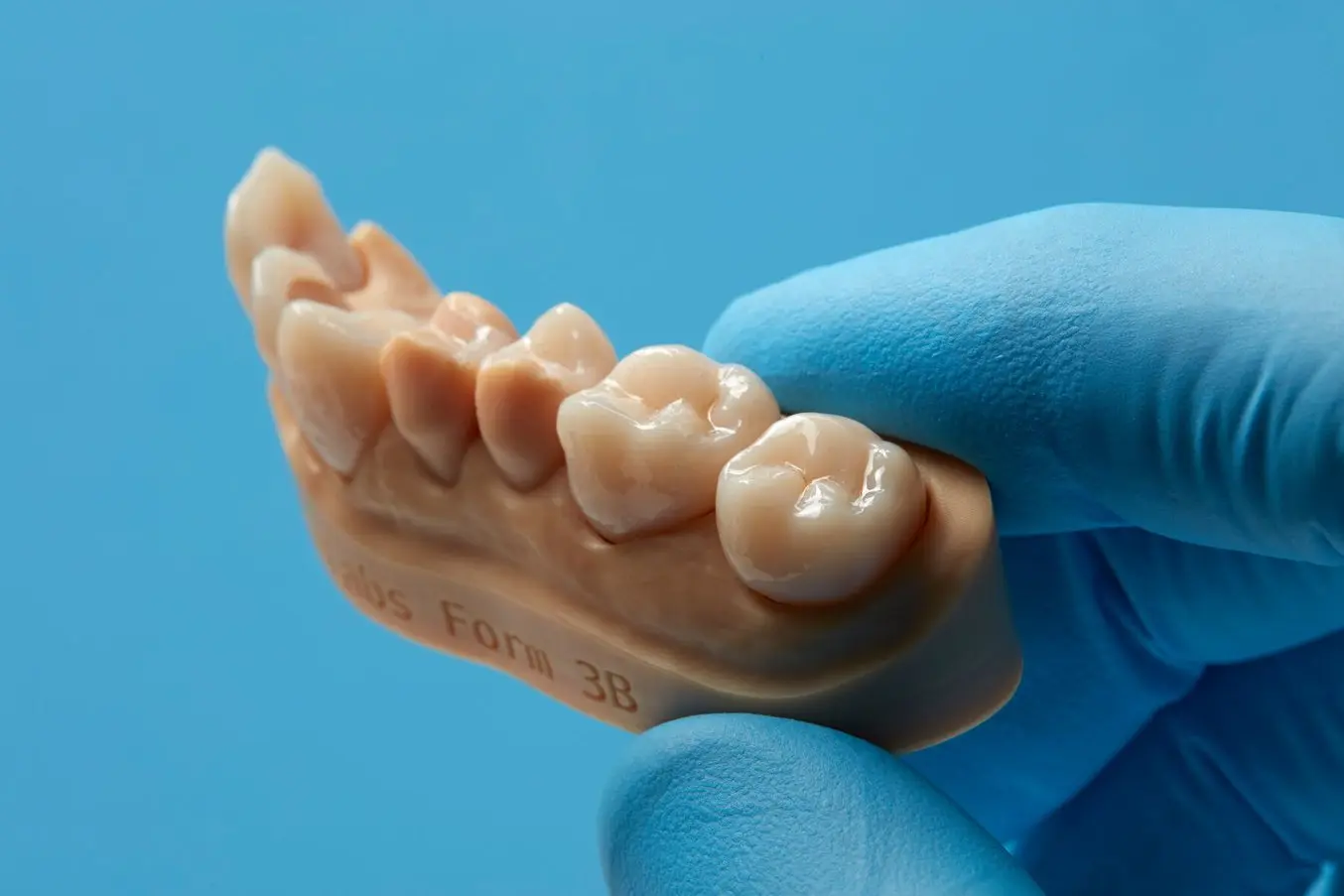
La dentisterie est également l'un des principaux moteurs d'investissement dans l'impression 3D. Les imprimantes 3D de bureau sont de plus en plus présentes dans les laboratoires et les cabinets dentaires. En fait, les plaques occlusales transparentes, thermoformées sur des moules imprimés en 3D, sont probablement l'exemple d'utilisation de l'impression 3D le plus réussi jusqu'à maintenant.
Au cours des dix dernières années, l'impression 3D a tellement progressé dans le domaine dentaire qu'aujourd'hui, aucun nouveau laboratoire dentaire n'ouvre sans utiliser une forme de dentisterie numérique. Avec des matériaux si bons qu'ils peuvent imprimer en 3D des couronnes permanentes, des prothèses complètes, et plus encore.
Les techniques d'impression 3D prospèrent là où des solutions sur mesure doivent être adaptées à l'anatomie de chacun. C'est pourquoi le secteur dentaire connait une transformation numérique rapide, les processus numériques apportant aux cabinets et laboratoires dentaires des améliorations de l'efficacité, une qualité élevée et constante et des réductions de coûts.
Lunettes de luxe imprimées en 3D
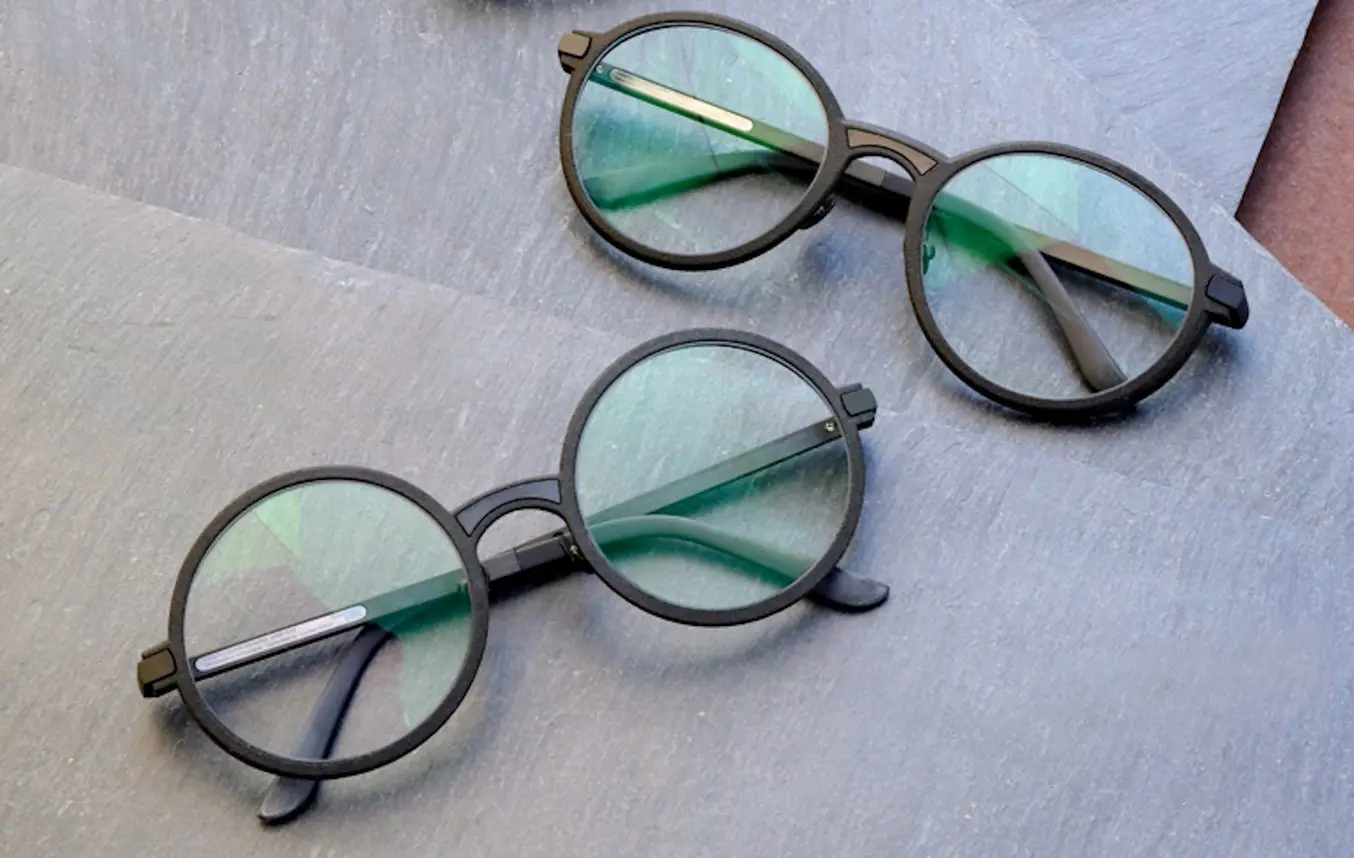
La prochaine fois que vous sortirez pour une soirée en ville, gardez en tête notre prochain cas d'utilisation inattendu de l'impression 3D : l'impression 3D de montures de lunettes personnalisées.
Marcus Marienfeld AG se distingue de la concurrence en utilisant des techniques de production différentes et uniques pour créer ses montures. Récemment, ils ont commencé à intégrer l'impression 3D par frittage laser sélectif (SLS) dans la chaîne de production de montures dans leur atelier suisse pour l'impression de pièces d'utilisation finale et l'outillage rapide pour le formage du titane.
« On devient très inventif et imaginatif quand on a une imprimante 3D en interne. Je peux tenter des choses que je n'aurais jamais crues possibles sans effort », a déclaré Marcus Marienfeld.
Des possibilités infinies
Visualiser des changements apportés par l'impression 3D dans la manière dont les objets sont fabriqués ne demandent plus les mêmes prouesses d'imagination que dans le passé. Les processus de travail se sont développés ces dernières années, ont pris pied dans plusieurs secteurs, et nous commençons à constater leur potentiel révolutionnaire.
Le public interagit de plus en plus avec les produits finis fabriqués par impression 3D des secteurs de la dentisterie aux biens de consommation en passant par la santé, l'architecture et la production industrielle. Étant donné que l'impression 3D permet de réaliser des pièces personnalisées à moindre coût, qu'elle réduit les délais et les coûts, et qu'elle permet aux consommateurs de se rapprocher des produits qu'ils souhaitent, son expansion ne peut que continuer.