Introduction à l'impression 3D médicale et aux imprimantes 3D dédiées au secteur de la santé
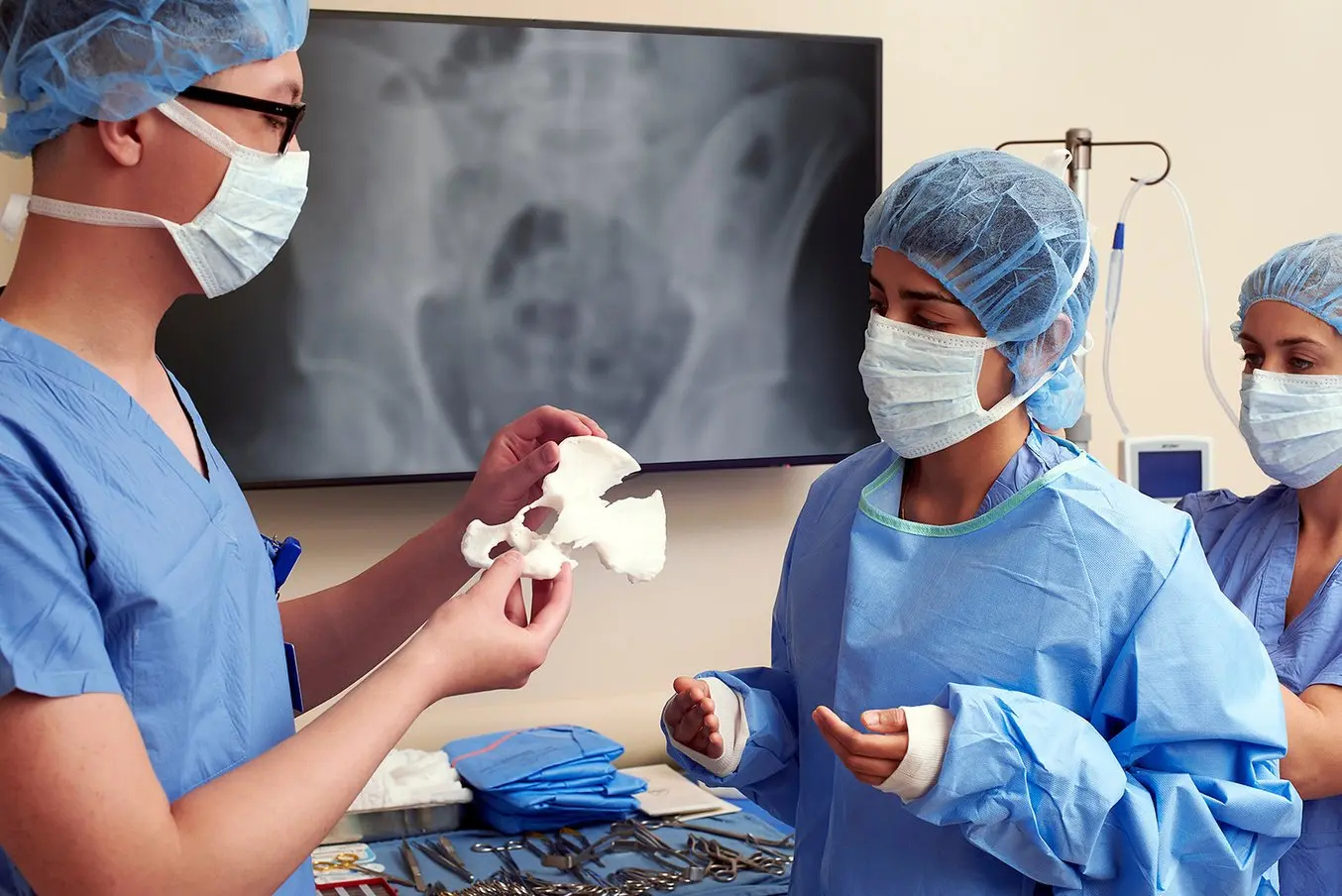
La médecine personnalisée de précision est en plein essor. De nouveaux outils et des technologies avancées permettent un rapprochement entre docteurs et patients. Les traitements et les dispositifs fournis sont personnalisés et donc adaptés au mieux à chaque individu.
Les progrès en technique d’impression 3D médicale ont apporté des solutions à toutes les branches du secteur médical. Pour les patients, de nouveaux outils et de nouvelles méthodes thérapeutiques développés par impression 3D apportent un nouveau degré de confort et de personnalisation aux traitements. Pour les docteurs, cette nouvelle technologie désormais accessible permet une meilleure compréhension des cas complexes et fournit de nouveaux outils qui peuvent finir par rehausser le niveau de la norme de soin.
Des modèles chirurgicaux spécifiques aux patients aux dispositifs médicaux imprimés en 3D, lisez la suite pour découvrir six façons dont l'impression 3D médicale prend son essor, pourquoi de nombreux professionnels de la santé sont enthousiasmés par le potentiel de l'impression 3D dans le domaine médical et comment différents types de technologie d'impression 3D peuvent être utilisés pour des applications spécifiques dans le secteur de la santé.
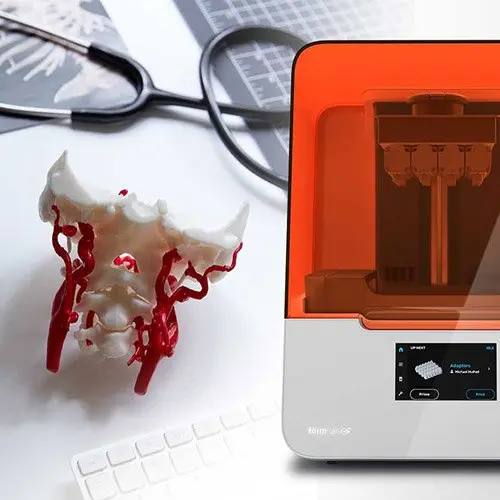
Introduction à l'impression 3D médicale
Rejoignez cette introduction de Formlabs pour apprendre les meilleures pratiques en matière d'impression 3D médicale et découvrir l'écosystème médical de Formlabs, avec plusieurs nouveaux produits de qualité médicale !
L’impression 3D dans le secteur de la santé
1. Modèles chirurgicaux spécifiques aux patients
Les modèles anatomiques imprimés en 3D à partir de données de scan d’un patient deviennent des outils de plus en plus utiles dans la médecine personnalisée et de précision telle qu’on peut l’exercer aujourd’hui. À mesure que les cas se complexifient et que l’efficacité en salle opératoire gagne en importance pour les opérations de routine, les modèles de référence visuels et tactiles peuvent améliorer la compréhension et la communication au sein des équipes de salle opératoire ou avec les patients.
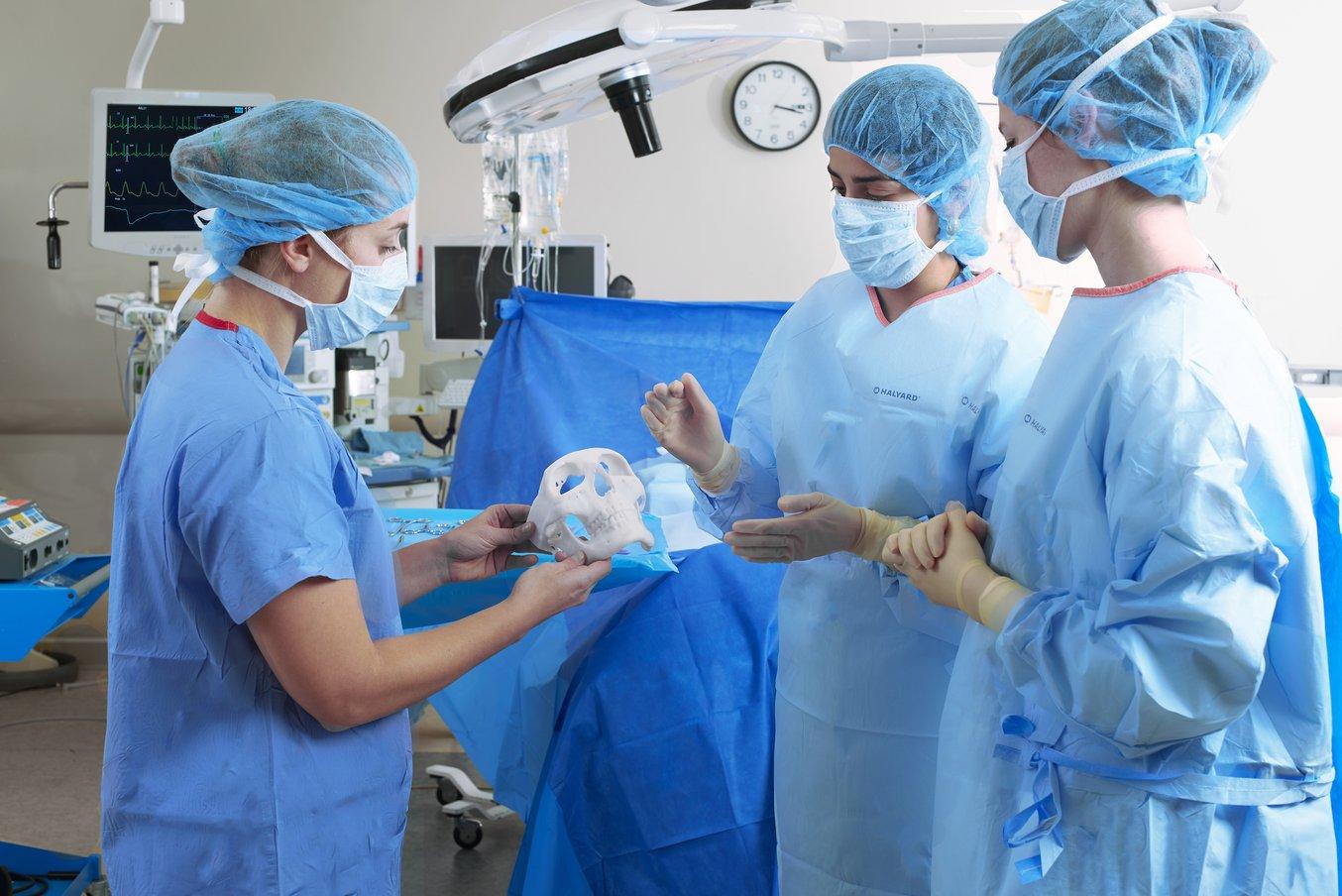
Comment imprimer en 3D des modèles anatomiques pour la planification pré-opératoire et permettre au patient de donner son consentement éclairé
Ce livre blanc propose aux médecins et aux techniciens de la santé une procédure pas à pas concrète pour se lancer dans la réalisation de modèles anatomiques imprimés en 3D à partir des scans des patients. Il passe en revue les meilleures pratiques pour la configuration d'un scan TDM/IRM, la segmentation des ensembles de données et la conversion des fichiers en un format imprimable en 3D.
Les professionnels de la santé, les hôpitaux et les organismes de recherche médicale partout dans le monde utilisent des modèles anatomiques imprimés en 3D comme outils de référence pour la planification préopératoire, la visualisation préopératoire et le dimensionnement ou l’ajustement préliminaire de l’équipement médical pour les opérations de routine comme pour les procédures hautement complexes documentées dans des centaines de publications.
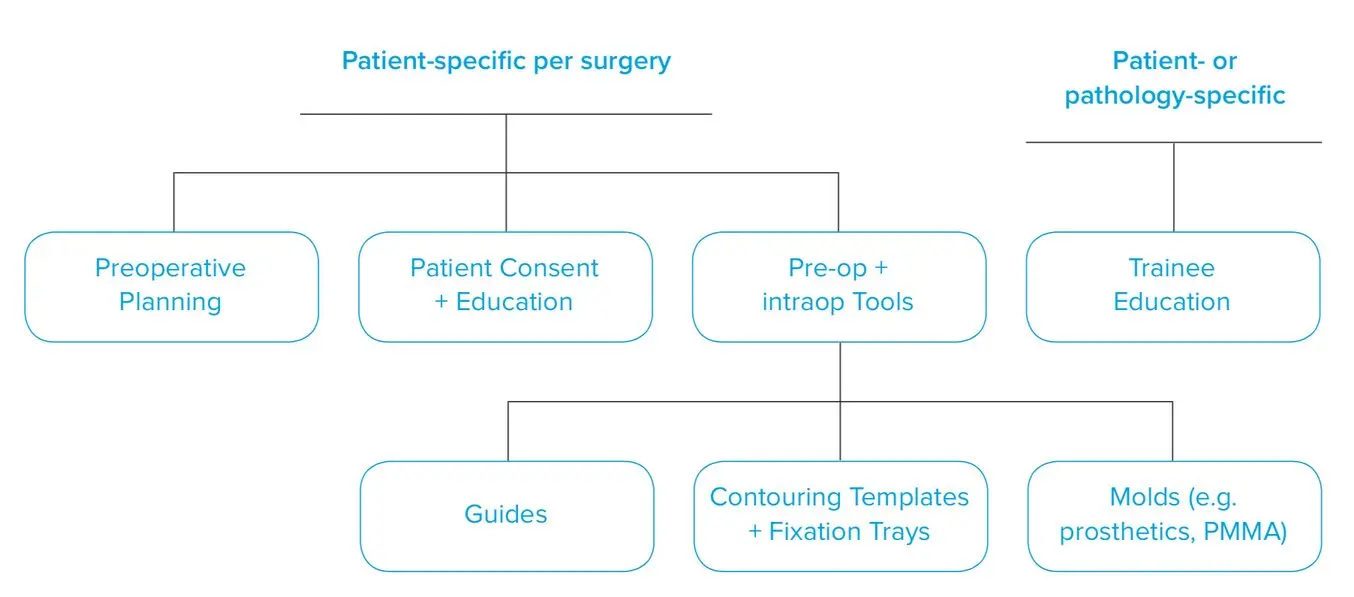
La création de modèles tactiles spécifiques au patient à partir de scans par tomodensitométrie ou IRM est désormais abordable et facile à réaliser grâce à l’impression 3D. La littérature spécialisée validée par comité de lecture montre que ces modèles apportent une visualisation supplémentaire qui aide les praticiens à mieux se préparer pour les chirurgies, ce qui réduit le temps passé en salle opératoire et les coûts associés, tout en améliorant le degré de satisfaction du patient par une baisse de son niveau d’anxiété et le raccourcissement de sa convalescence.
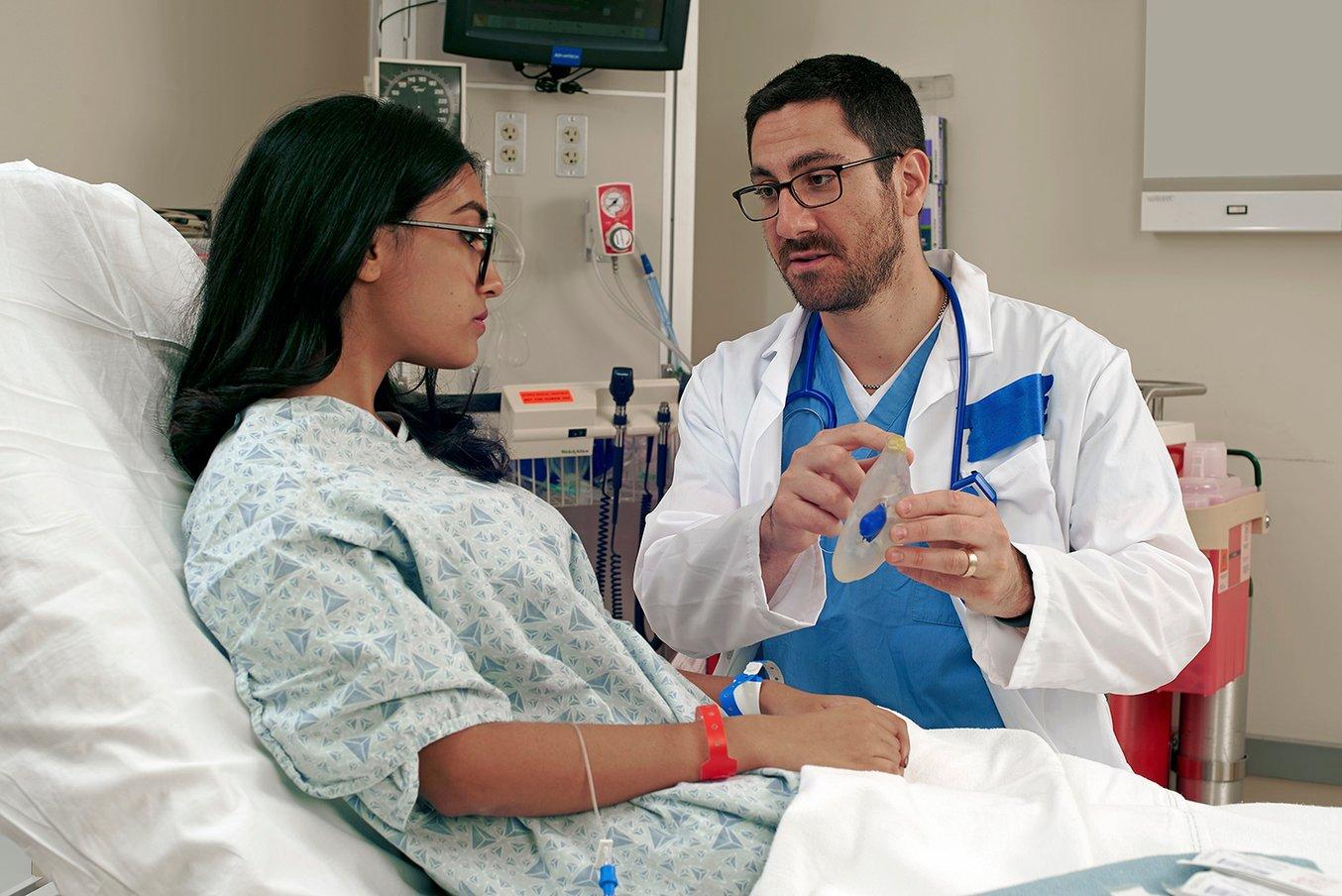
Les praticiens peuvent utiliser des modèles chirurgicaux spécifiques au patient pour lui expliquer l’opération au préalable, ce qui renforce l’adhésion du patient et diminue son anxiété.
Apprendre des modèles préopératoires peut aussi influencer le choix du traitement. C’est précisément ce qui est arrivé au Dr Michael Eames. Après avoir reproduit les os de l’avant-bras d’un jeune patient, le Dr Eames a réalisé que la blessure n’était pas celle qu’il s’imaginait au début.
Le Dr Eames a donc changé d’avis et opté pour une opération sur tissus mous bien moins invasive qui a raccourci le temps de revalidation et a laissé bien moins de cicatrices. Le Dr Eames s’est aidé de la réplique de l’os imprimé pour décrire l’opération au petit patient et à ses parents et ainsi gagner leur adhésion.
Résultat ? Un temps de chirurgie inférieur à 30 minutes, contrairement aux trois heures d’opération initialement prévues. Cette différence du temps de chirurgie a généré une économie estimée à 5500 € pour l’hôpital et a diminué le temps de convalescence passé par le patient en soins post-opératoires.
« Chacun de nos chirurgiens orthopédiques à temps plein et presque tous nos chirurgiens à temps partiel ont utilisé des modèles imprimés en 3D pour le traitement des patients du San Francisco VA. Nous avons tous constaté que l’impression 3D améliore la qualité des opérations le jour de l’intervention. »
Dr Alexis Dang, chirurgienne orthopédique à l’hôpital universitaire de San Francisco, Californie (UCSF, University of California San Francisco) et au centre médical pour vétérans de San Francisco (San Francisco VA, San Francisco Veteran's Affair Medical Center)
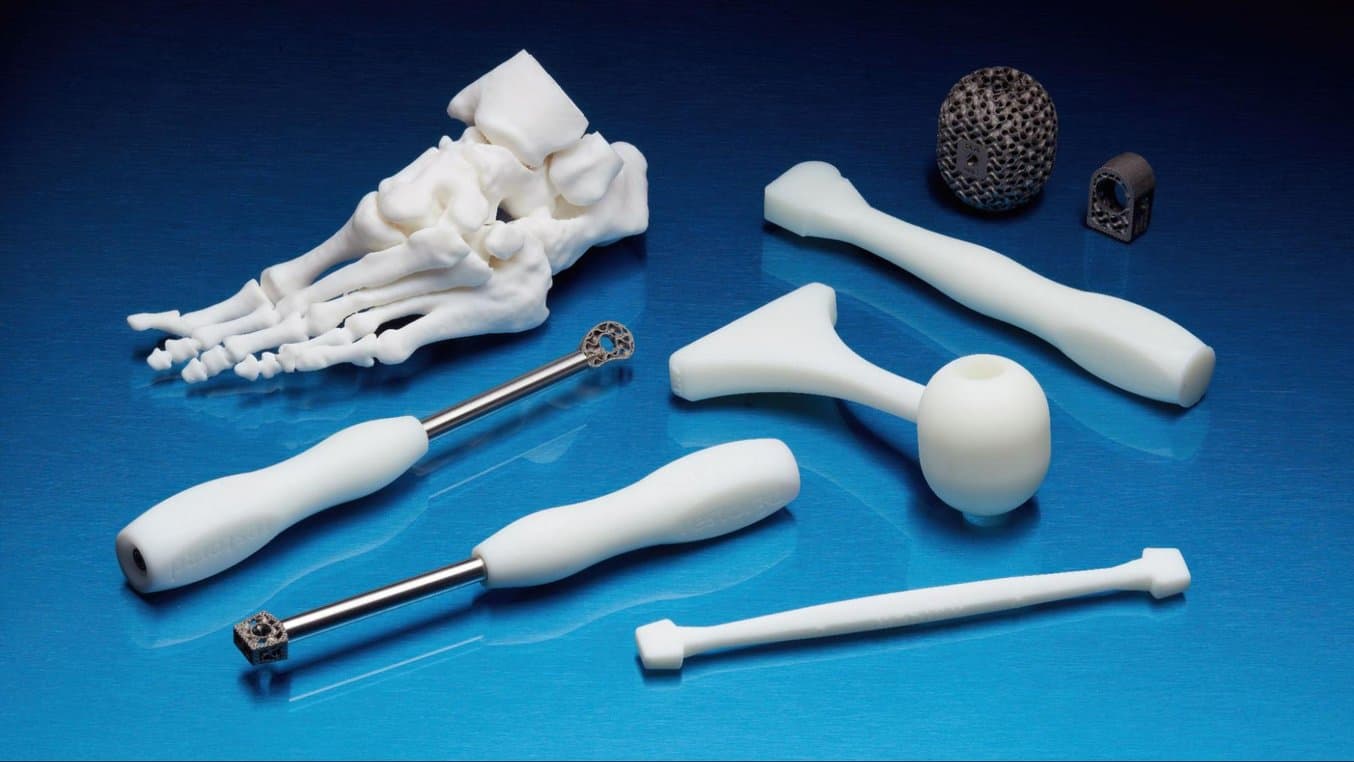
La chirurgie personnalisée grâce à l'impression 3D : Questions et réponses avec Insight Surgery (anciennement 3D LifePrints)
Participez à cette séance de questions-réponses sur l'impression 3D médicale avec 3D LifePrints pour découvrir leur travail innovant et polyvalent de création de dispositifs médicaux spécifiques aux patients.
Le Dr Frederik Verstreken de l'AZ Monica dans la région d'Anvers en Belgique est spécialisé dans la chirurgie de la main, du poignet et de l'avant-bras. Il a déclaré que la combinaison de la visualisation, de la planification numérique et des modèles anatomiques imprimés en 3D permet aux cliniciens de gagner environ 30 à 40 % de temps dans la salle d'opération. Pour les cas d'ostéotomie complexes, il n'a parfois pas été possible de restaurer l'anatomie. Mais avec les modèles chirurgicaux imprimés en 3D, les médecins sont beaucoup mieux préparés à l'opération que sans ces outils numériques, utilisent moins de radiations et atteignent une précision nettement supérieure, ce qui permet aux patients de retrouver des mouvements normaux et de se débarrasser de la douleur.
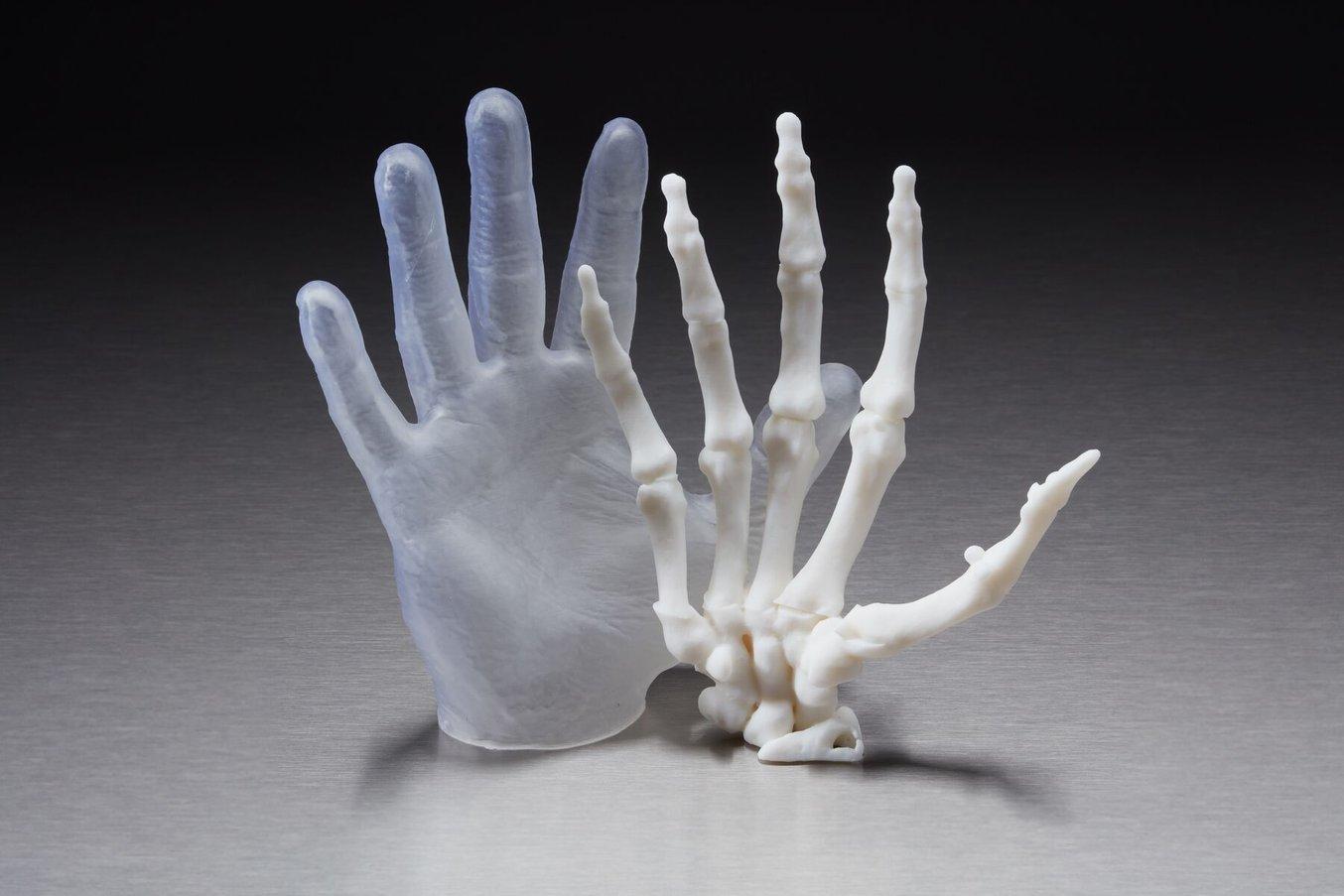
Modèle anatomique d’une main, dont la « peau » est réalisée dans un matériau d’impression 3D élastique.
Pour le docteur Todd Goldstein, instructeur à l’institut de recherche médicale Feinstein, le rôle central qu’a fini par avoir l’impression 3D dans son département ne fait pas l’ombre d’un doute. Il estime que si Northwell utilisait des modèles 3D dans 10 à 15 % de ses cas, cela pourrait lui faire économiser 1 750 000 $ par an.
Les guides chirurgicaux peuvent aider les chirurgiens à comprendre l'anatomie et la pathologie propres à chaque patient, à analyser les risques, à planifier une approche et à se familiariser avec le cas avant d'entrer dans la salle d'opération. La sélection de matériaux pour des propriétés spécifiques, telles que l'élasticité, peut permettre aux chirurgiens de pratiquer des procédures sur des modèles, ce qui permet de réduire le temps d' opération et d'obtenir de meilleurs résultats.
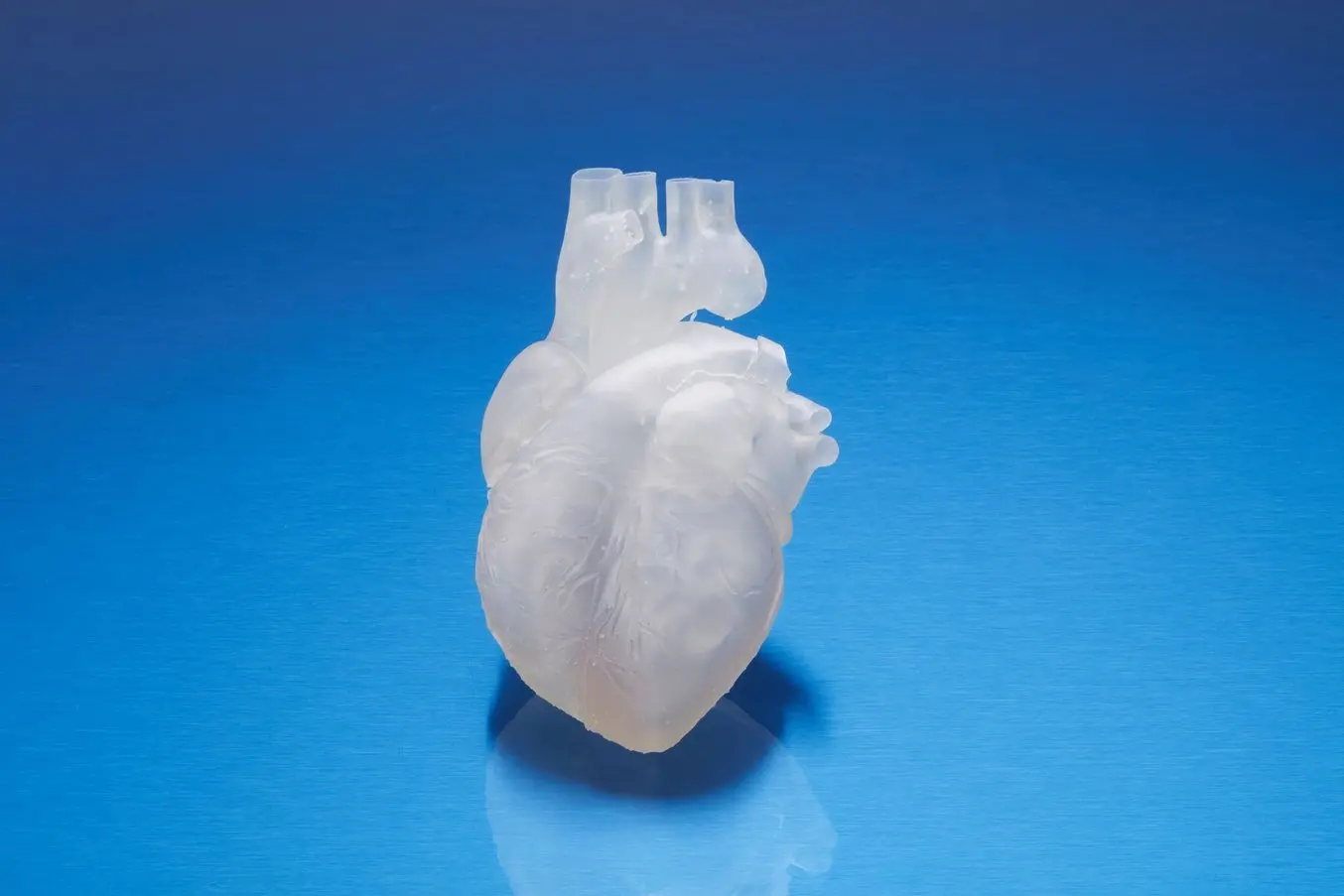
Utiliser les élastomères biocompatibles de Formlabs pour créer des modèles anatomiques vasculaires
Découvrez comment les professionnels de la santé peuvent incorporer des matériaux élastomères et biocompatibles dans des flux de travail d'impression 3D innovants en utilisant les nouvelles BioMed Flex 80A Resin et BioMed Elastic 50A Resin de Formlabs.
2. Instruments spécifiques aux patients
De nouveaux matériaux d’impression 3D médicaux biocompatibles ont aussi permis le développement de nouveaux outils et techniques chirurgicaux dans le but précis d’améliorer encore le confort clinique pendant la chirurgie. Les systèmes d’instrumentation traditionnels sont lents à évoluer et ont des coûts initiaux importants. Ils présentent souvent des complications dans le flux de travail chirurgical. Les imprimantes 3D et les matériaux biocompatibles facilitent et rendent plus rentables la fabrication d’implants, d’instruments chirurgicaux et de guides de coupe spécifiques à la procédure ou au patient.
Les guides chirurgicaux personnalisés imprimés en 3D peuvent aider les chirurgiens à comprendre l'anatomie et la pathologie propres à chaque patient, à analyser les risques, à planifier une approche et à se familiariser avec le cas avant d'entrer dans la salle d'opération. Des guides de coupe bien conçus réduisent le temps nécessaire à la réalisation d'un cas et la durée d'utilisation par les chirurgiens d'un système de navigation peropératoire. Cela signifie moins de radiations pour le patient et encore moins de temps dans la salle d'opération.
« Les guides nous indiquent où nous devons faire les trous et où nous devons faire les coupes, de sorte que lorsque nous prenons une plaque, nous pouvons tout de suite la mettre dans la bonne position. Nous sommes beaucoup plus précis avec que sans guides. Nous gagnons au moins 50 % de temps par rapport à un travail à main levée. Et c'est beaucoup plus précis ».
Frederik Verstreken, chirurgien de la main et du poignet, hôpital AZ Monica
Le délai d'exécution rapide de l'impression 3D permet une itération rapide de la conception. Les chirurgiens peuvent donner leur avis ; celui-ci peut alors être mis en application rapidement avec un outil ou un guide réimprimé.
restor3d a pour mission d'aider les chirurgiens et les prestataires de soins de santé qui réparent et reconstruisent le corps humain à innover dans le domaine de la chirurgie de précision. Restor3d exploite les capacités de l'impression 3D pour améliorer radicalement les soins chirurgicaux en imprimant des implants métalliques et des instruments en polymère spécifiques à une procédure, et souvent à un patient donné.
restor3D s'est imposé comme un leader dans l'utilisation de l'impression 3D pour booster l'innovation dans la salle d'opération. Leur kit de planification préopératoire de pointe, leurs implants très précis et innovants ainsi que la solution de bout en bout fournie par leur kit d'instruments ont aidé les hôpitaux à réduire leurs coûts et à améliorer l'expérience des patients.
« Les chirurgiens nous font constamment part de leurs commentaires. L'impression 3D nous permet de modifier rapidement la conception afin de prendre en compte les commentaires des chirurgiens et de fournir rapidement une nouvelle solution. »
Nathan Evans, premier vice-président du développement des produits, restor3D
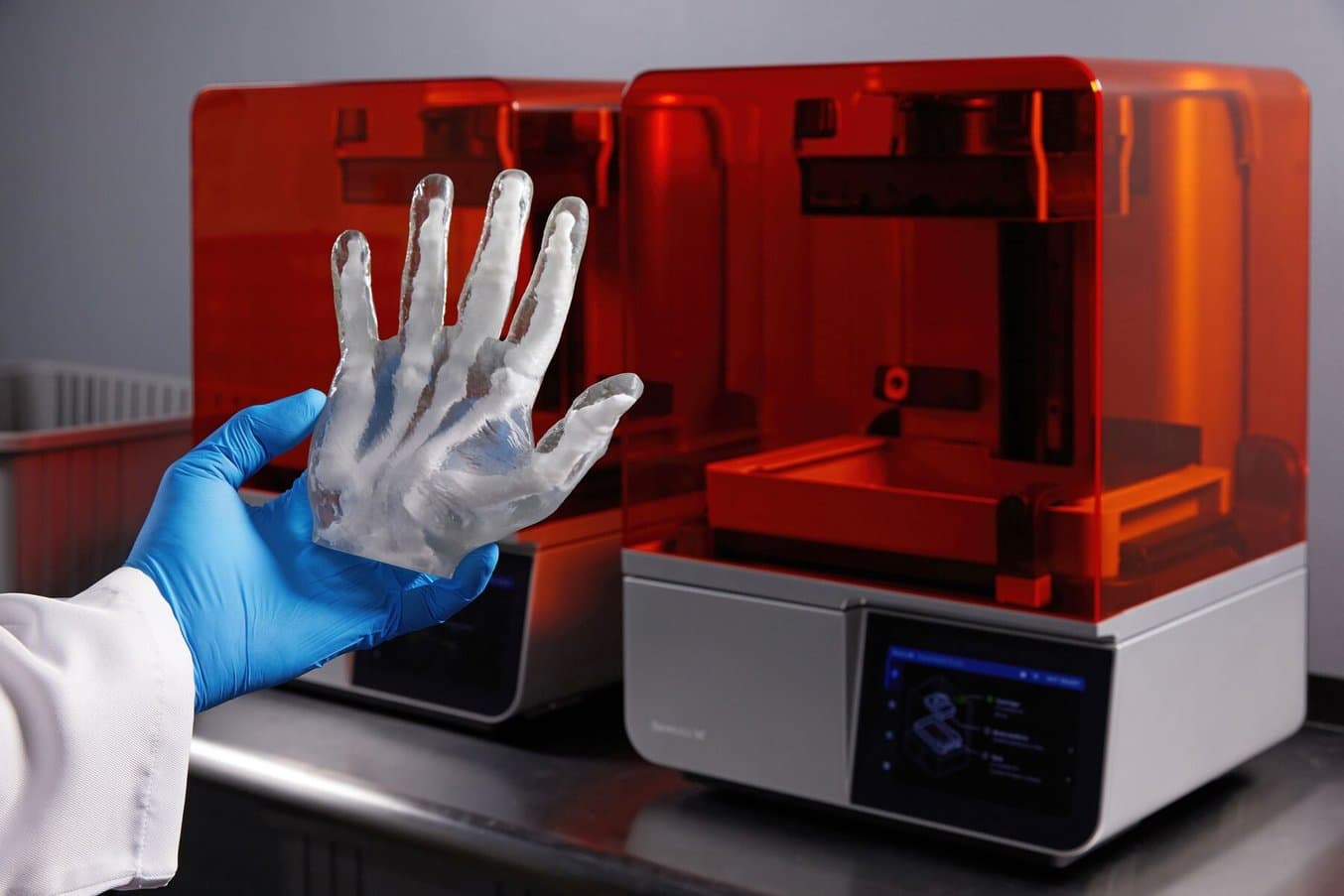
Résines biocompatibles Formlabs : un guide complet pour choisir le bon matériau
Formlabs propose actuellement plus de 40 matériaux uniques pour l'impression 3D stéréolithographique (SLA). Ce document aide les utilisateurs à comparer nos offres biocompatibles et à déterminer l'ajustement le mieux adapté à leurs applications médicales.
3. Nouveaux dispositifs médicaux
L’impression 3D est pour ainsi dire devenue synonyme de prototypage rapide. La facilité d’utilisation et le faible coût de l’impression 3D en interne ont aussi révolutionné le développement de produit à tel point que de nombreux fabricants d’ustensiles médicaux ont adopté cette technologie pour produire de tout nouveaux dispositifs médicaux et instruments chirurgicaux.
Plus de 90 % des 50 plus grands fabricants de dispositifs médicaux utilisent l’impression 3D pour créer des prototypes de dispositifs médicaux précis tels que des gabarits et des fixations pour simplifier le test et imprimer directement en 3D des dispositifs médicaux.
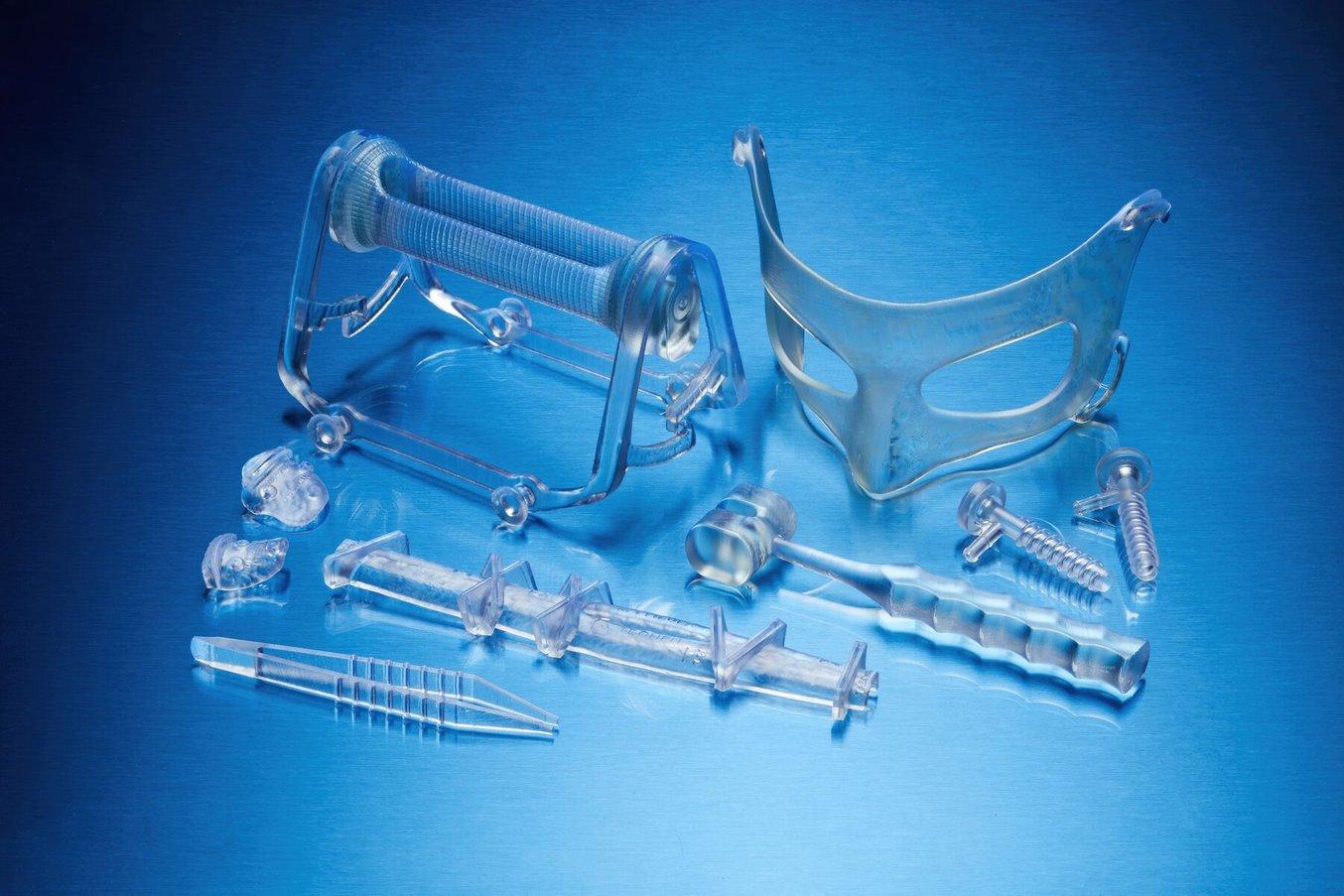
Créer une société de dispositifs médicaux avec les imprimantes Formlabs
Trois jeunes entreprises vous présenteront leur expérience de la création d’une nouvelle entreprise et le lancement simultané de leur premier dispositif médical. Elles nous expliqueront pourquoi elles ont choisi Formlabs pour participer à ce processus et comment la fabrication additive a été utilisée.
« Avant que DJO Surgical s’équipe d’une [imprimante 3D Formlabs], nous dépendions presque exclusivement de sous-traitants d’impression pour les prototypes. Aujourd’hui, nous utilisons quatre machines Formlabs, et l’impact a été conséquent. Notre taux d’impression 3D a doublé, les coûts ont été réduits de 70 % et le niveau de détail de l’impression permet de communiquer clairement sur la conception de dispositifs avec les chirurgiens orthopédistes. »
Alex Drew, ingénieur de projet mécanique chez DJO Surgical
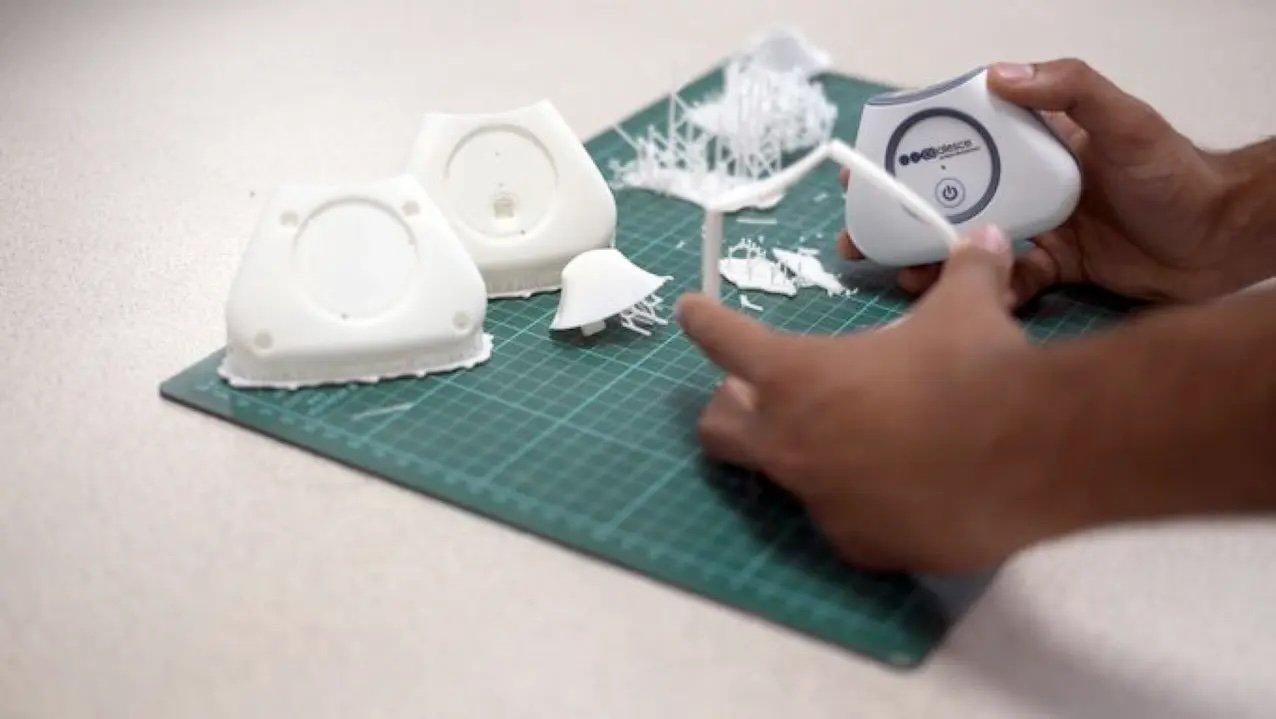
Les entreprises de dispositifs médicaux telles que Coalesce utilisent l’impression 3D pour créer des prototypes de dispositifs médicaux précis.
L’impression 3D peut accélérer le processus de conception en produisant des itérations de modèles complexes en quelques jours au lieu de semaines entières. Quand Coalesce a été chargée de créer un inhalateur capable d’évaluer numériquement le profil de débit inspiratoire des patients asthmatiques, sous-traiter à des prestataires de services aurait entraîné des délais de production importants pour chaque prototype. Les fichiers de conception auraient dû être minutieusement optimisés au fur et à mesure des multiples itérations avant d’être envoyés au prestataire pour la fabrication.
Au lieu de cela, l’impression 3D SLA de bureau à permis à Coalesce de maintenir tout son processus de prototypage en interne. Les prototypes convenaient à un usage pour des études cliniques et ressemblaient exactement au produit fini. En fait, quand Coalesce a présenté son dispositif à son client, celui-ci a pris le prototype pour le produit fini !
En tout, le travail réalisé en interne a réduit de 80 à 90 % le délai de production des prototypes. De plus, les pièces ne prenaient que huit heures à imprimer et pouvaient être finies et peintes en quelques jours alors que le même processus aurait pris une semaine ou deux avec un sous-traitant.
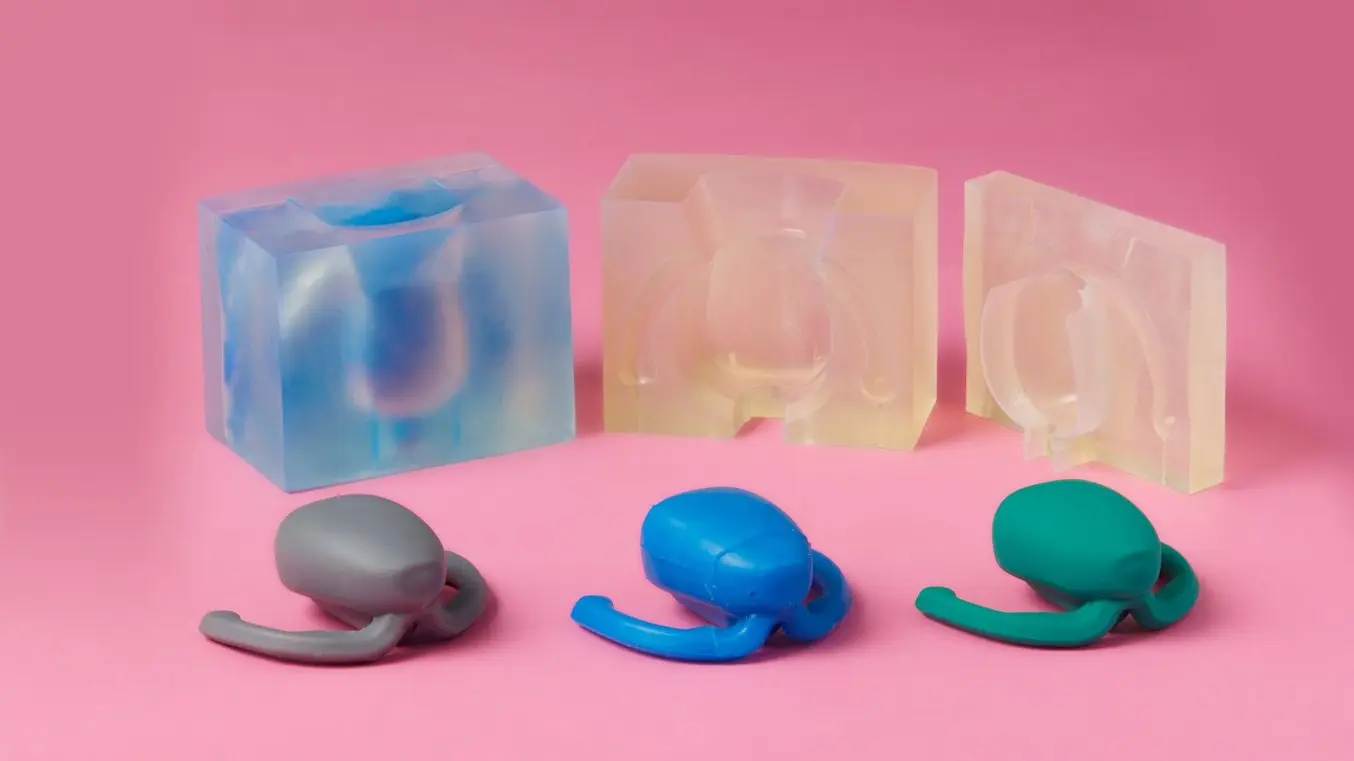
Création de dispositifs médicaux en silicone
Ce guide a pour but d'aider l'utilisateur à choisir la méthode de production de pièces en silicone la mieux adaptée à l'usage qu'il souhaite en faire. Il fournit des instructions pas à pas pour imprimer avec Silicone 40A Resin et le moulage de silicone à l'aide d'outils SLA imprimés en 3D (y compris des moules d'injection en deux parties, des surmoules et des moules de compression).
Shavini Fernando a tiré parti de l'impression 3D pour mettre au point OxiWear, un accessoire de surveillance des signes vitaux et d'alerte d'urgence à porter sur l'oreille. Son équipe a utilisé l'impression 3D SLA pour prototyper le dispositif et créer des gabarits antistatiques.
M. Fernando affirme que « l'impression 3D en interne change la donne pour les startups comme la nôtre, car elle nous permet de réduire considérablement les coûts tout au long du cycle de développement et de tester plusieurs designs de prototypes en même temps. Avant l'impression 3D, chaque fois que nous devions sous-traiter un prototype, cela nous coûtait environ 200 $. Chaque dispositif peut être imprimé sur la Form 3B pour quelques centimes ».
4. Prothèses sur mesure abordables et perfectionnées
Dans le monde, plus de 50 millions de personnes doivent se faire amputer d'un membre en raison de causes traumatiques. Pour les patients se remettant d'une amputation, accepter de porter une prothèse n'est pas toujours facile. La plupart d'entre eux veulent retrouver une vie normale : conduire une voiture, s'entraîner à la salle de sport, faire le ménage dans la maison. Mais la plupart des prothèses traditionnelles sont rudimentaires, coûteuses et fragiles. Aujourd'hui, environ 10 % des patients nécessitant un bras prothétique avancé peuvent se l'offrir.
Les prothèses simples ne sont disponibles qu’en quelques tailles. Les patients doivent donc se contenter de ce qui s’adapte le mieux à leur morphologie. À l’inverse, les dispositifs bioniques développés sur mesure et conçus pour reproduire les mouvements et les interactions des vrais membres en utilisant les muscles du membre résiduel d’une personne pour contrôler la prothèse sont si chers qu’ils ne sont accessibles qu’aux patients les mieux couverts par le système de santé dans les pays les plus développés. Ceci est particulièrement vrai dans le cas des prothèses pour enfants. Au fil de leur croissance, les enfants finissent toujours par devenir trop grands pour leur prothèse ou par endommager celle-ci, ce qui nécessite une réparation ou un remplacement coûteux. La difficulté vient du fait qu’il existe peu de processus de fabrication permettant de produire des pièces sur mesure de manière abordable. Mais de plus en plus, les prothésistes peuvent tirer parti de la liberté de conception bien connue qu’offre l’impression 3D. Grâce à celle-ci, l’obstacle financier empêchant le traitement peut disparaître.
PSYONIC, créateur de l'Ability Hand, est une entreprise qui tente de révolutionner le marché. Conçue et fabriquée en interne à l'aide de méthodes de fabrication hybrides, l'Ability Hand permet aux patients de retrouver leur vie et leur mobilité. PSYONIC utilise l'impression 3D pour créer rapidement des prototypes, réduire les coûts et créer des pièces solides à partir de matériaux durables et résistants aux chocs.
Des initiatives telles que e-NABLE permettent à des communautés entières de par le monde à se former autour des prothèses imprimées en 3D. Ses participants ont donné naissance à un mouvement indépendant de production de prothèses en partageant gratuitement des informations et des modèles libres de droits afin que les patients puissent obtenir une prothèse sur mesure correspondant à leurs besoins pour à peine une cinquantaine de dollars.
D’autres inventeurs tels que Lyman Connor vont encore plus loin. Avec un petit parc d’à peine quatre imprimantes 3D de bureau, Lyman a pu réaliser et poser ses premières prothèses de production. Son objectif final ? Créer une main bionique complète et personnalisable pouvant être vendue pour une fraction du prix affiché actuellement pour des prothèses aussi élaborées, qui se chiffre en dizaines de milliers de dollars.
Ailleurs, des chercheurs du MIT ont aussi déclaré l’impression 3D comme étant le moyen optimal de produire des fixations de prothèse plus confortables.
Il va sans dire que le faible coût de production de ces prothèses, de même que la liberté inhérente à la conception sur mesure ont eu l’effet d’une révélation. Les prothèses réalisées par impression 3D peuvent être produites en deux petites semaines, puis elles peuvent être essayées et entretenues pour un coût bien inférieur à leurs équivalents traditionnels.
À mesure que les coûts continuent de baisser et que les propriétés des matériaux s’améliorent, l’impression 3D va certainement devenir de plus en plus présente dans ce secteur de la santé.
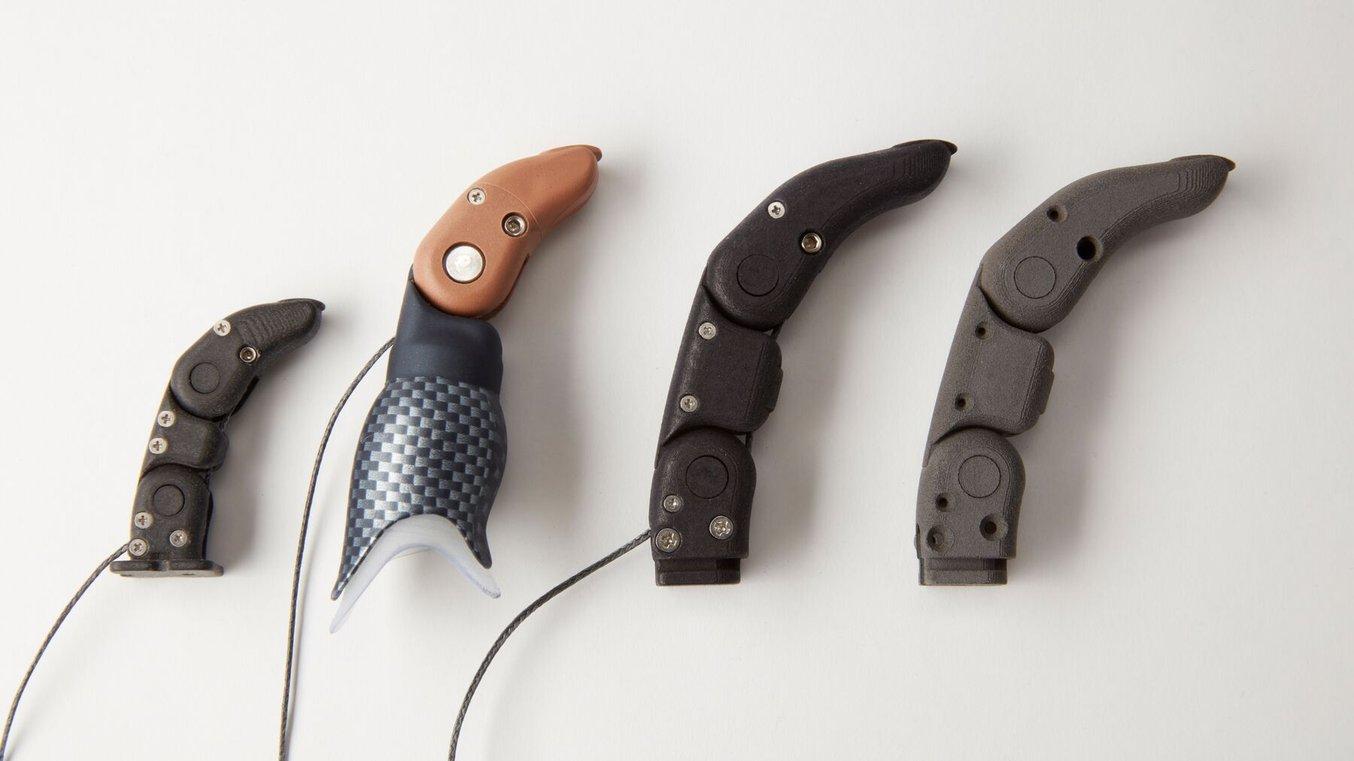
L'impression 3D dans l'industrie des orthèses et des prothèses
Ce livre blanc est une introduction à l'utilisation de la technologie d'impression 3D pour créer des orthèses et des prothèses de nouvelle génération.
5. Orthèses sur mesure
Les mêmes obstacles financiers bloquant l’accès au traitement dans le cas des prothèses sont nombreux à être également inhérents à des secteurs tels que celui des orthèses. Comme bien d’autres dispositifs médicaux spécifiques au patient, les orthèses sur mesure sont souvent financièrement inaccessibles à cause de leur coût élevé. De plus, leur fabrication prend des mois, voire des semaines. Grâce à l’impression 3D, ce ne doit plus être le cas.
De nombreux professionnels de la santé adoptent désormais l'impression 3D pour produire des solutions orthopédiques personnalisées. En suivant des flux de travail éprouvés, l'impression 3D peut faire gagner du temps et des ressources, ce qui permet de produire des orthèses spécifiques au patient en un temps record.
Les flux de travail numériques pour les orthèses personnalisées englobent de nouvelles options de conception, de test et de fabrication afin de réduire les coûts de personnalisation et d'accélérer les cycles de production pour des délais plus courts, des dispositifs mieux adaptés et de meilleurs résultats pour les patients. Les orthèses imprimées en 3D offrent une solution puissante qui permet une personnalisation rapide et peu coûteuse.
Kriwat GmbH, un fournisseur de services médicaux spécialisé en orthopédie et dont le siège se trouve à Kiel en Allemagne, était confronté à une pénurie de main d’œuvre qualifiée. De plus, les flux de travail traditionnels créaient un environnement rempli de poussière et de vapeurs chimiques. Pour résoudre ces problèmes, Lais Kriwat, maître technicien en chaussures orthopédiques, a mis au point un flux de travail numérique pour la production de semelles intérieures à l'aide de deux imprimantes 3D SLS Fuse 1+ 30W, d'un système d'impression 3D Fuse 1+ 30W et de Nylon 11 Powder.
Le flux de travail numérique a permis de réduire les coûts de matériel et de main-d'œuvre. M. Kriwat estime que les coûts de production ont baissé d'environ 15 à 17 % grâce à l'impression 3D. Il a également pu accélérer la production, ce qui a permis aux spécialistes de prendre en charge davantage de patients. « Nous avons désormais la possibilité de créer une orthèse parfaitement adaptée à un patient en l'espace de 24 heures », affirme Lais Kriwat.
Les possibilités offertes par la liberté de conception de l'impression 3D SLS comprennent la redistribution de la pression pendant la marche, des produits individuels haut de gamme, certains supports impossibles à produire avec des méthodes traditionnelles, et des produits de qualité qui offrent au pied un soutien optimal pour des sports tels que la course et le football.
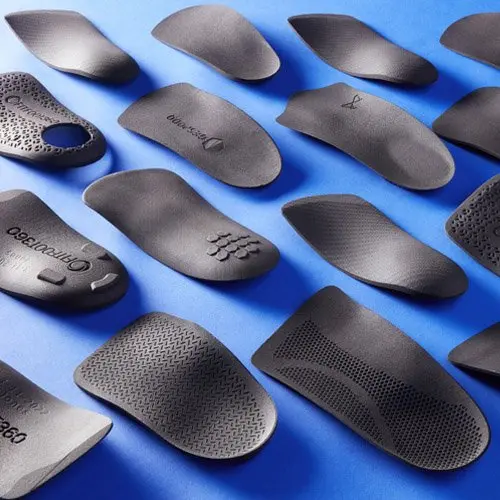
Impression 3D de semelles rigides avec la Fuse 1+ 30W et Nylon 11 Powder
Cette étude compare les propriétés mécaniques et les méthodes de fabrication utilisés pour produire des semelles orthopédiques personnalisées : la Fuse 1+ 30W de Formlabs et Nylon 11 Powder, HP 3D High Reusability PA 11, et un polypropylène fabriqué de façon traditionnelle.
Matej et son fils Nik illustrent le potentiel qu'offrent les orthèses personnalisées imprimées en 3D. Nik est né prématurément en 2011 et des complications lors de l’accouchement lui ont occasionné une paralysie cérébrale, un trouble qui touche presque vingt millions de personnes dans le monde. Matej, encouragé par la volonté inébranlable de son fils à dépasser les limites que lui imposait sa maladie, a dû faire face à un choix : une orthèse standard toute faite qui aurait été inadaptée et inconfortable pour son fils, ou un dispositif sur mesure hors de prix qui n’aurait pu être livré que des semaines ou des mois plus tard, et qui serait vite devenu obsolète en raison de la croissance de l’enfant.
Il a donc décidé de prendre le problème à bras le corps et s’est mis en quête de nouvelles solutions pour atteindre son but. Grâce à la liberté offerte par les technologies numériques telles que le scan 3D et l’impression 3D, Matej et les kinésithérapeutes de Nik ont pu expérimenter à volonté et développer un processus de travail entièrement nouveau pour les orthèses cheville-pied.
L’orthèse imprimée en 3D sur mesure qui en a résulté a donné à Nik le soutien, le confort et la correction à l’endroit précis où ils étaient nécessaires, ce qui a aidé Nik à enfin faire ses premiers pas tout seul. Ce dispositif orthétique sur mesure reproduisait le degré d’ajustement élevé des orthèses de la meilleure qualité pour une fraction du prix et sans nécessiter d’ajustements supplémentaires.
L'impression 3D permet de produire des orthèses spécifiques aux patients avec des flux de travail optimisés qui permettent d'économiser du temps et des ressources. Pour les patients, cela signifie moins de rendez-vous, des délais d'exécution rapides et une personnalisation précise pour un confort accru. Par rapport aux méthodes de fabrication traditionnelles, les flux de travail d'impression 3D permettent de gagner du temps et d'économiser des ressources matérielles, tout en réduisant les dépenses et en offrant un environnement de travail plus confortable.
6. Bioimpression, génie tissulaire, organes imprimés en 3D et plus encore
La bioimpression 3D désigne l’utilisation de procédés de fabrication additive par dépôt de matériau appelé bioencre pour créer des structures similaires aux tissus à usage médical. Le génie tissulaire, lui, fait référence aux diverses technologies évolutives, dont la bioimpression, permettant de cultiver du tissu et des organes de remplacement en laboratoire afin de traiter les blessures et les maladies.
Les chercheurs utilisent la bio-impression pour développer des tissus et des organes cultivés en laboratoire. La réalisation de ces objectifs permettrait de faire progresser la médecine régénérative et les tests de sécurité. En outre, la possibilité de bio-imprimer des organes pourrait augmenter considérablement les chances de réussite des greffes. Étant donné que la bio-impression utilise des cellules prélevées sur le patient nécessitant le traitement, elle élimine le risque de rejet par le système immunitaire, qui est un problème majeur dans les procédures conventionnelles de transplantation d'organes aujourd'hui.
À l'université d'Osaka, des chercheurs ont utilisé de l'encre à base de cellules et un support d'impression pour créer des formes spécifiques, notamment un nez. Une fois imprimées, les cellules restent viables jusqu'à deux semaines, ce qui constitue une étape importante dans le développement d'organes cultivés en laboratoire.
Actuellement, la régénération de la peau et la cicatrisation des plaies sont traitées par des greffes de peau douloureuses. La possibilité d'imprimer la peau offre une alternative qui favoriserait la régénération de la peau et la cicatrisation des plaies. En 2023, des chercheurs du Wake Forest Institute for Regenerative Medicine ont réussi à bio-imprimer une peau de pleine épaisseur qui a présenté une cicatrisation complète lorsqu'elle a été transplantée dans des environnements précliniques.
Le Dr Atala, auteur principal du document, rapporte : « Les résultats montrent qu'il est possible de fabriquer de la peau humaine pleine épaisseur par bioingénierie et que cela favorise une guérison plus rapide et des résultats d'apparence plus naturelle. »
Des scientifiques de l'Institut Terasaki pour l'innovation biomédicale ont mis au point une encre biologique pour l'impression qui peut améliorer la formation de tissus musculaires squelettiques. À terme, on espère que cette technologie pourra être utilisée pour aider les personnes souffrant d'une perte musculaire ou d'une blessure.
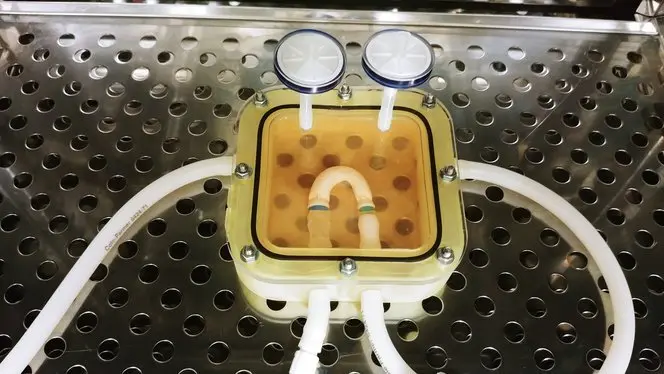
Une chambre de bioréacteur imprimée en 3D dans laquelle une aorte miniature en tissu de synthèse est en train de grandir. Le tissu est cultivé dans le bioréacteur pour obtenir les caractéristiques mécaniques et biologiques du tissu organique.
L’impression 3D s’est montrée capable de surmonter les défis posés par la production de vaisseaux sanguins synthétiques en apportant une solution pour reproduire précisément la forme, la taille et la géométrie des vaisseaux désirés. Pouvoir fournir une solution imprimée qui répond précisément aux besoins spécifiques du patient a changé la donne.
Comme le dit le Dr Pashneh-Tala : « [Créer des vaisseaux sanguins par impression 3D] offre la possibilité d’améliorer les options chirurgicales et même de concevoir des vaisseaux sanguins adaptés au patient. Sans accès à une impression 3D abordable et de haute précision, la création de ces formes ne serait pas possible. »
La bio-impression évolue rapidement à mesure que les chercheurs repoussent les limites du possible. Des os et du sang à la peau et aux muscles, les progrès de la bio-impression ouvrent la voie à de futures améliorations dans les soins aux patients.
Impression 3D médicale
Différentes méthodes existent pour imprimer des dispositifs médicaux en 3D. Il est important de choisir une technologie d'impression adaptée à votre cas d'utilisation.
Les technologies d'impression 3D médicale les plus populaires pour les dispositifs médicaux sont la stéréolithographie (SLA), le frittage sélectif par laser (SLS), le dépôt de fil fondu (FDM), et la fusion sélective par laser (SLM) pour les métaux.
Stéréolithographie (SLA)
Les imprimantes 3D SLA utilisent un laser pour transformer de la résine liquide en plastique durci par un processus dit de photopolymérisation. Ce procédé est le plus apprécié des professionnels médicaux en raison de sa haute résolution, de sa précision et de la polyvalence de ses matériaux.
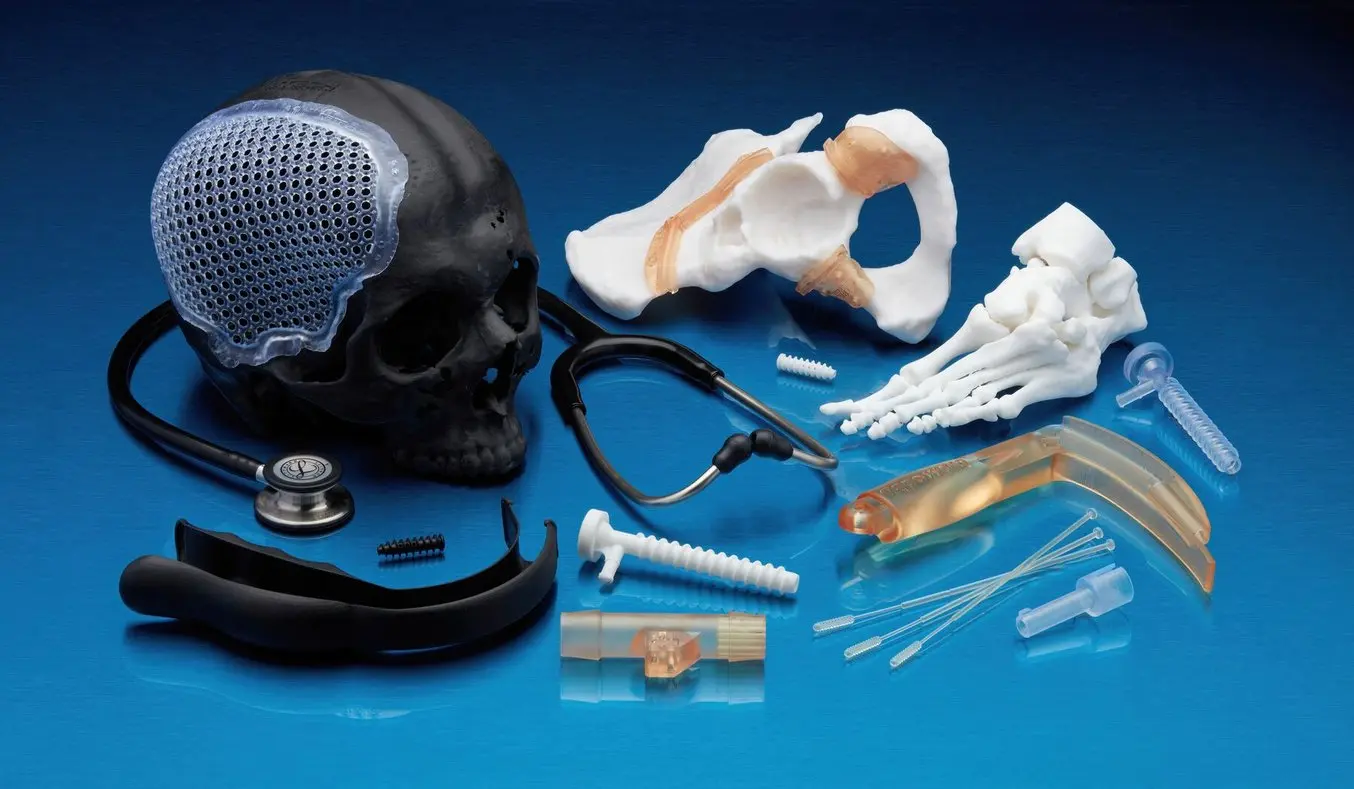
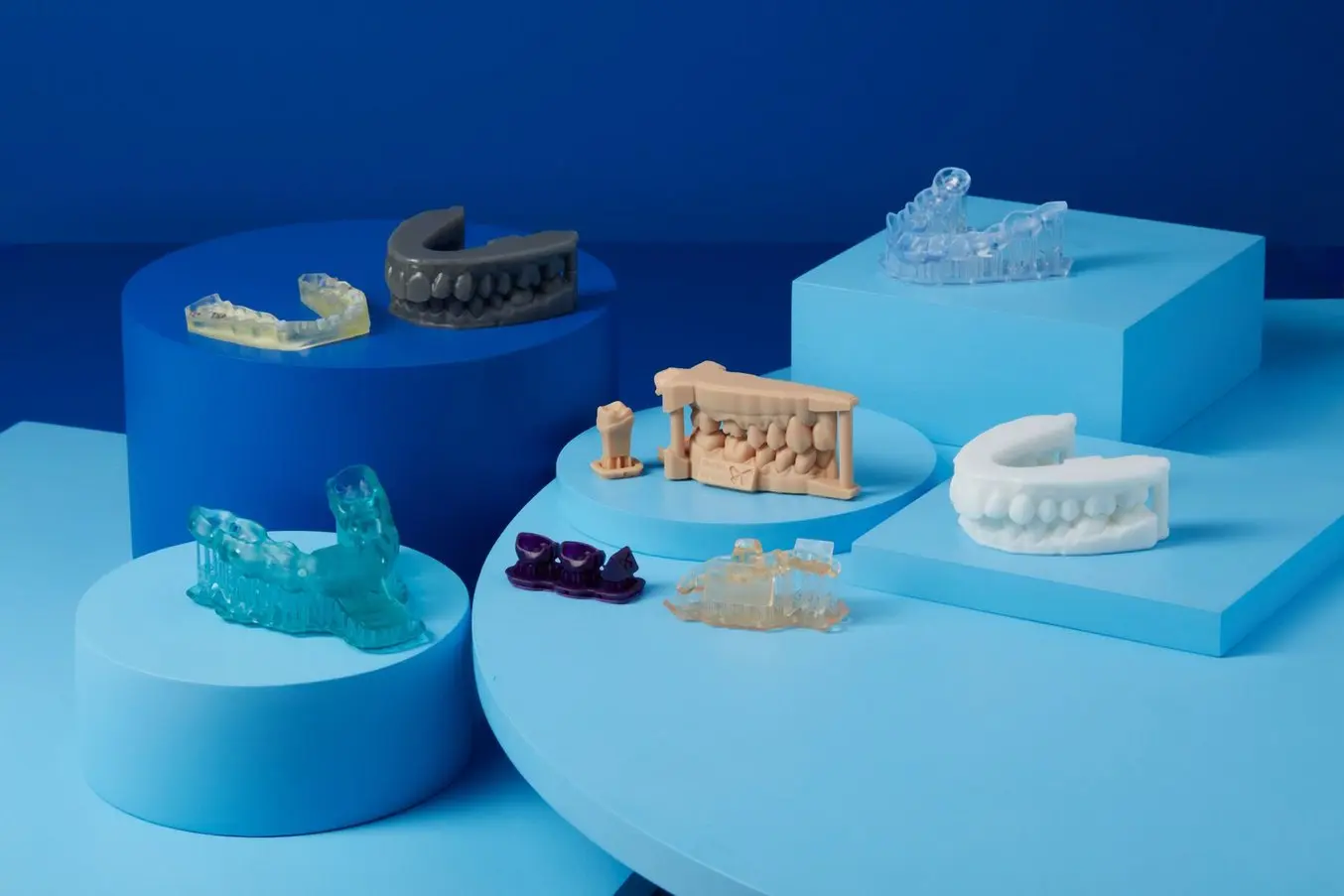
L'impression 3D SLA offre un large choix de matériaux d'impression 3D, y compris des matériaux biocompatibles, pour toute une série d'applications médicales et dentaires.
Avantages du SLA
Les pièces imprimées par stéréolithographie ont l’exactitude et la résolution les plus élevées, les détails les plus précis et la finition de surface la plus lisse de tous les procédés d’impression 3D plastique. Cependant, le principal avantage duSLA réside dans sa polyvalence. Les résines SLA présentent une vaste gamme de propriétés optiques, mécaniques et thermiques qui correspondent à celles des thermoplastiques standards, techniques et industriels.
Le SLA est parfait pour imprimer des modèles anatomiques, des prototypes de dispositifs médicaux avec un haut niveau de détail, des tolérances serrées et une surface lisse, ainsi que des moules, de l’outillage, et des pièces finales fonctionnelles. Le SLA offre également le plus grand choix de matériaux biocompatibles pour les applications dentaires et médicales, telles que les instruments chirurgicaux et les appareils médicaux nécessitant un contact avec la peau ou les muqueuses.
Inconvénients du SLA
Du fait de la polyvalence de ses matériaux, le SLA revient un peu plus cher que le procédé FDM, mais reste tout de même plus abordable que tous les autres procédés d’impression 3D. Les pièces en résine SLA requièrent également un post-traitement après impression. Elles doivent être lavées et post-polymérisées.

Commander un échantillon gratuit
Examinez et constatez par vous-même la qualité Formlabs. Nous enverrons un échantillon gratuit à votre bureau.
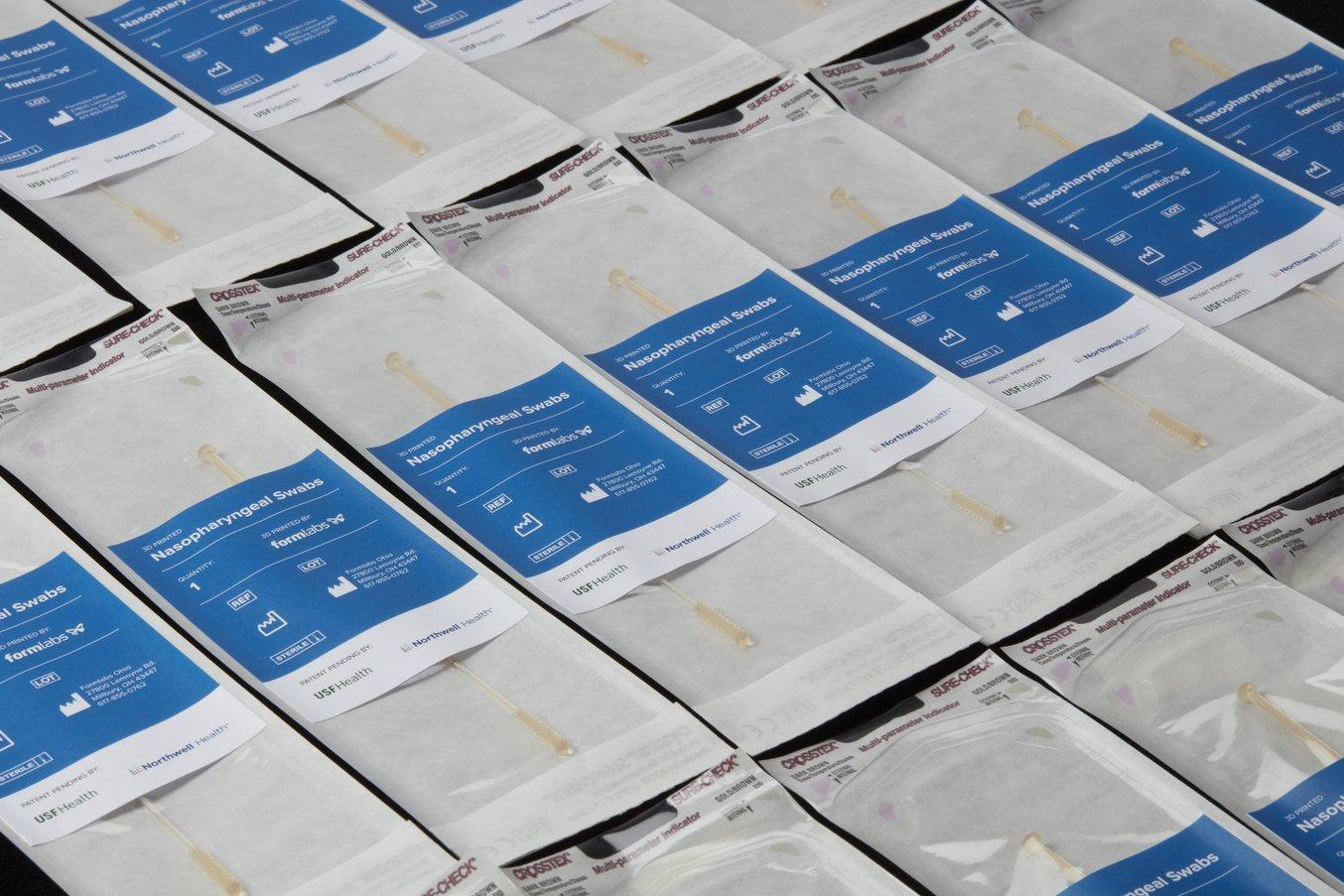
Guide de Formlabs sur la gestion du contrôle de la qualité pour les innovateurs du secteur de la santé
Ce guide décrit les étapes que les professionnels de la santé peuvent suivre pour maintenir, contrôler et améliorer la qualité des pièces SLA imprimées en 3D.
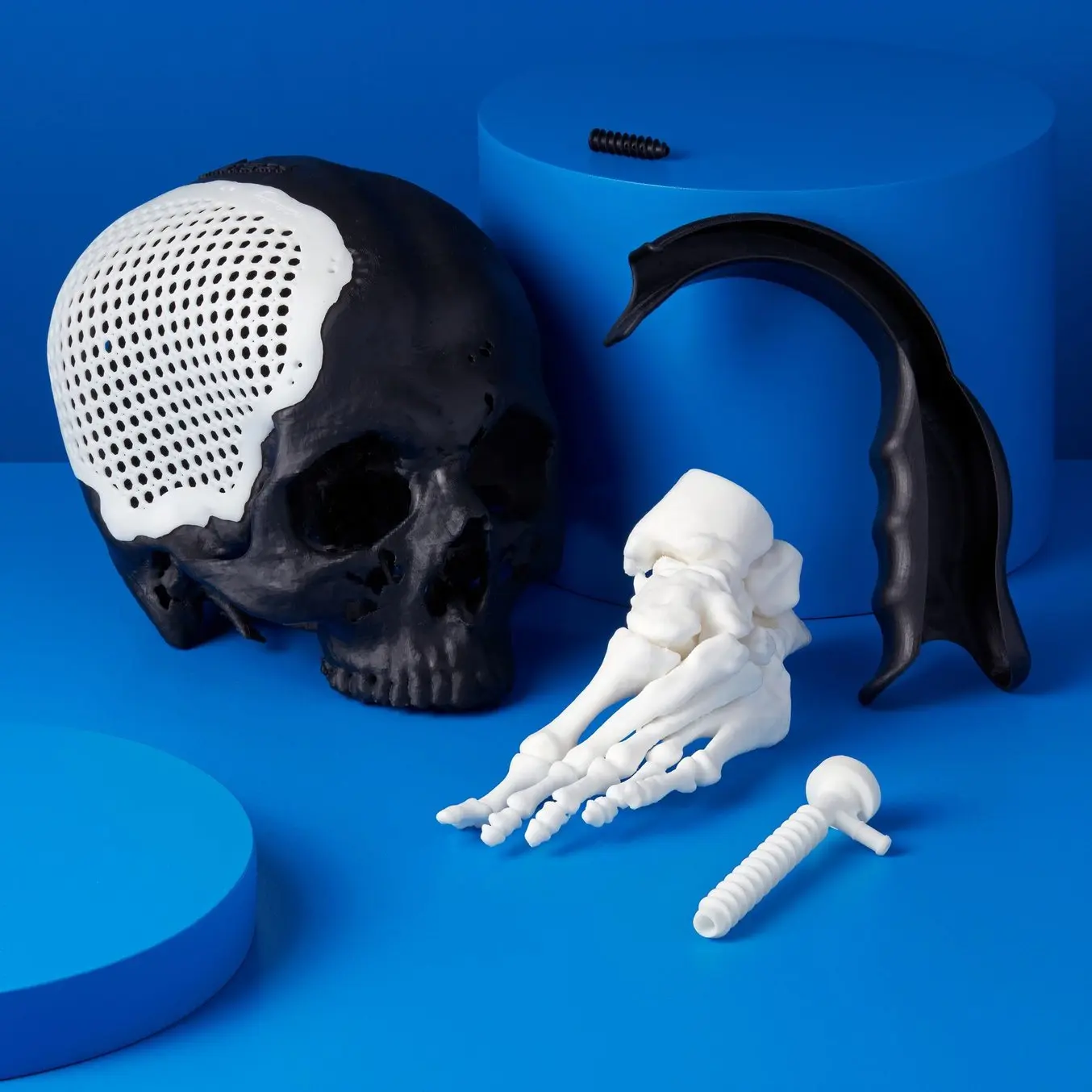
Dispositifs médicaux imprimés en 3D pour la chirurgie de précision : perspectives cliniques, commerciales et réglementaires
Rejoignez Formlabs et Nelson Labs pour un focus approfondi sur la biocompatibilité, incluant une présentation de nos nouveaux matériaux et des meilleures pratiques pour les fabricants de produits médicaux par des experts du secteur.
Frittage sélectif par laser (SLS)
Les imprimantes 3D SLS utilisent un laser de forte puissance pour fondre de petites particules de poudre de polymère. La poudre non fondue supporte la pièce pendant l’opération, ce qui évite d’avoir à lui ajouter des structures de support et rend ce procédé particulièrement efficace pour imprimer des pièces mécaniques complexes.
Le SLS est le procédé de fabrication additive le plus utilisé dans le secteur industriel, du fait des excellentes propriétés mécaniques des pièces produites. En fonction du matériau, les pièces SLS peuvent également être biocompatibles et stérilisables, ce qui les rend idéales pour les dispositifs médicaux, les prototypes, les guides chirurgicaux, les objets de technologie portable et les orthèses.
Avantages du SLS
Du fait que le SLS ne requiert pas de structures de support, il est idéal pour des pièces à géométrie complexe, présentant des formes internes ou en creux, des contre-dépouilles ou des parois fines. Les pièces fabriquées par SLS présentent d’excellentes caractéristiques mécaniques, leur résistance s’apparentant à celle de pièces moulées par injection.
Le faible coût par pièce, la productivité élevée, les matériaux éprouvés et la biocompatibilité font du SLS le procédé le plus apprécié par les ingénieurs médicaux pour réaliser des prototypes fonctionnels.
Inconvénients du SLS
Les imprimantes 3D SLS ont un prix d'entrée plus élevé que les technologies FDM ou SLA. Bien qu'une gamme de matériaux soit disponible, la sélection des matériaux pour le SLS est plus limitée que pour le SLA. Les pièces sortent de l'imprimante avec une surface légèrement rugueuse et nécessitent un post-traitement tel que le sablage pour obtenir une finition lisse.

L'impression 3D SLS est idéale pour fabriquer des prototypes solides et fonctionnels et des pièces d'utilisation finale, telles que des prothèses et des orthèses.
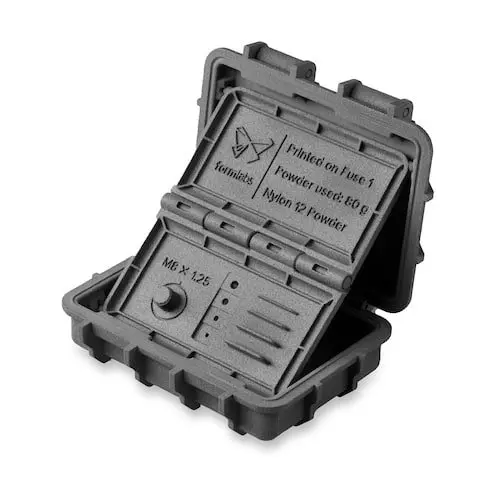
Commander un échantillon gratuit
Examinez et ressentez par vous-même la qualité des imprimantes SLS Formlabs. Nous enverrons un échantillon gratuit à votre bureau.
Dépôt de fil fondu (FDM)
L'impression 3D FDM, aussi appelée FFF (fabrication par filament fondu), fabrique des pièces en faisant fondre et en extrudant un filament thermoplastique qu’une buse dépose couche par couche sur la zone de fabrication.
La technologie FDM est la plus utilisée au niveau des consommateurs, du fait de l’émergence d’imprimantes 3D pour amateurs. Mais les imprimantes FDM industrielles sont aussi appréciées des professionnels.
Avantages du FDM
Le procédé FDM fonctionne avec toute une gamme de thermoplastiques standard, comme l’ABS, le PLA et leurs variantes. Le prix d’entrée et le coût des matériaux en deviennent plus bas. Le FDM convient aux modèles simples de démonstration de faisabilité et au prototypage peu coûteux des pièces les plus simples. Certains matériaux FDM sont également biocompatibles.
Inconvénients du FDM
De toutes les technologies d’impression 3D pour les plastiques, comme le SLA et le SLS, le FDM est celle qui présente la résolution et l’exactitude les plus faibles. Il ne convient donc pas à la fabrication de modèles compliqués ou de pièces avec des parties complexes, comme par exemple les modèles anatomiques. La qualité de la finition peut être améliorée par des procédés de polissage chimique ou mécanique longs et gourmands en main-d’œuvre. Des imprimantes 3D FDM peuvent utiliser des supports solubles pour atténuer certains de ces problèmes. Elles travaillent avec une gamme plus large de thermoplastiques techniques, mais leur coût est nettement plus élevé. Lors de la création de grandes pièces, l'impression FDM a également tendance à être plus lente que l'impression SLA ou SLS.
Frittage direct par laser du métal (DMLS) et fusion sélective par laser (SLM)
Les imprimantes 3D à frittage direct par laser du métal (DMLS) et à fusion sélective par laser (SLM) fonctionnent de manière similaire aux imprimantes SLS, mais fondent couche par couche avec un laser des particules de poudre de métal, et non des polymères.
Les imprimantes 3D DMLS et SLM peuvent créer des produits métalliques solides, précis et complexes, ce qui rend ce procédé idéal pour diverses applications médicales.
Avantages de la DMLS et de la SLM
Le principal avantage de ces procédés réside évidemment dans les matériaux, car les imprimantes 3D DMLS et SLM sont capables de produire des dispositifs et des composants médicaux à usage final très performants à partir de métal. Ces procédés permettent de reproduire des géométries complexes et de fabriquer des produits finis solides, durables et biocompatibles. Ils peuvent être utilisés pour fabriquer des implants génériques (hanches, genoux, implants de la colonne vertébrale, etc.), des implants personnalisés pour le traitement du cancer ou des traumatismes, des prothèses dentaires, ainsi que des produits technologiques médicaux et orthopédiques.
Inconvénients de la DMLS et de la SLM
Bien que le prix des imprimantes 3D métal ait également commencé à baisser, avec des coûts allant de 200 000 € à 1 million € voire plus, la plupart des entreprises ne peuvent toujours pas se permettre d’investir dans ces systèmes. Les processus d'impression 3D métal sont également plus complexes.
Au contraire, l’impression 3D SLA convient très bien aux processus de moulage de métal pour produire des pièces métalliques à moindre coût, avec une plus grande liberté de conception et des délais plus courts que les méthodes traditionnelles.
Comparer les imprimantes 3D médicales
Stéréolithographie (SLA) | Frittage sélectif par laser (SLS) | Dépôt de fil fondu (FDM) | Impression 3D en métal (DMLS, SLM) | |
---|---|---|---|---|
Volume d’impression | Jusqu’à 300 x 335 x 200 mm (imprimantes 3D de bureau et d’atelier) | Jusqu’à 165 x 165 x 300 mm (imprimantes 3D d’atelier industrielles) | Jusqu’à 300 x 300 x 600 mm (imprimantes 3D de bureau et d’atelier) | Jusqu’à 400 x 400 x 400 mm (DMLS/SLM grand format) |
Gamme de prix | Les imprimantes de bureau professionnelles commencent à 2399 €, les imprimantes d’atelier grand format à 8999 € et les machines industrielles à grande échelle sont disponibles à partir de 80 000 €. | Les systèmes industriels d'atelier commencent à 23 899 €, et les imprimantes industrielles traditionnelles sont disponibles à partir de 100 000 €. | Les imprimantes et les kits d'impression 3D entrée de gamme commencent à quelques centaines d'euros. Les imprimantes de bureau milieu de gamme de meilleure qualité commencent autour de 2000 €, et les systèmes industriels sont disponibles à partir de 15 000 €. | À partir de 200 000 € |
Matériaux | Variantes de résines (plastiques thermodurcissables). Résines standard, techniques (similaires à l’ABS ou au polypropylène, souples, résistantes à la chaleur), coulables, dentaires et médicales (biocompatibles). Silicone et céramique purs. | Thermoplastiques techniques (y compris les matériaux biocompatibles ). Nylon 11, nylon 12, composites en nylon à charge de verre ou de carbone, polypropylène, TPU (élastomère). | Thermoplastiques standard, tels que l’ABS, le PLA et leurs variantes. | Acier inoxydable, acier à outils, titane, cobalt-chrome et aluminium. |
Applications idéales | Modèles anatomiques (biocompatibles), instruments chirurgicaux(biocompatibles), dispositifs médicaux(biocompatibles), appareils dentaires(biocompatibles), prototypage rapide, outillage rapide, aides à la fabrication et pièces à usage final. | Modèles anatomiques (biocompatibles), instruments chirurgicaux(biocompatibles), dispositifs médicaux (biocompatibles), orthèses et prothèses, prototypage rapide, outillage rapide, aides à la fabrication et pièces à usage final. | Modèles simples de preuve de concept Prototypage à faible coût de pièces simples. | Pièces solides et durables à géométrie complexe, implants, prothèses dentaires, composants médicaux et orthopédiques en métal. |
Matériaux pour les applications médicales d'impression 3D
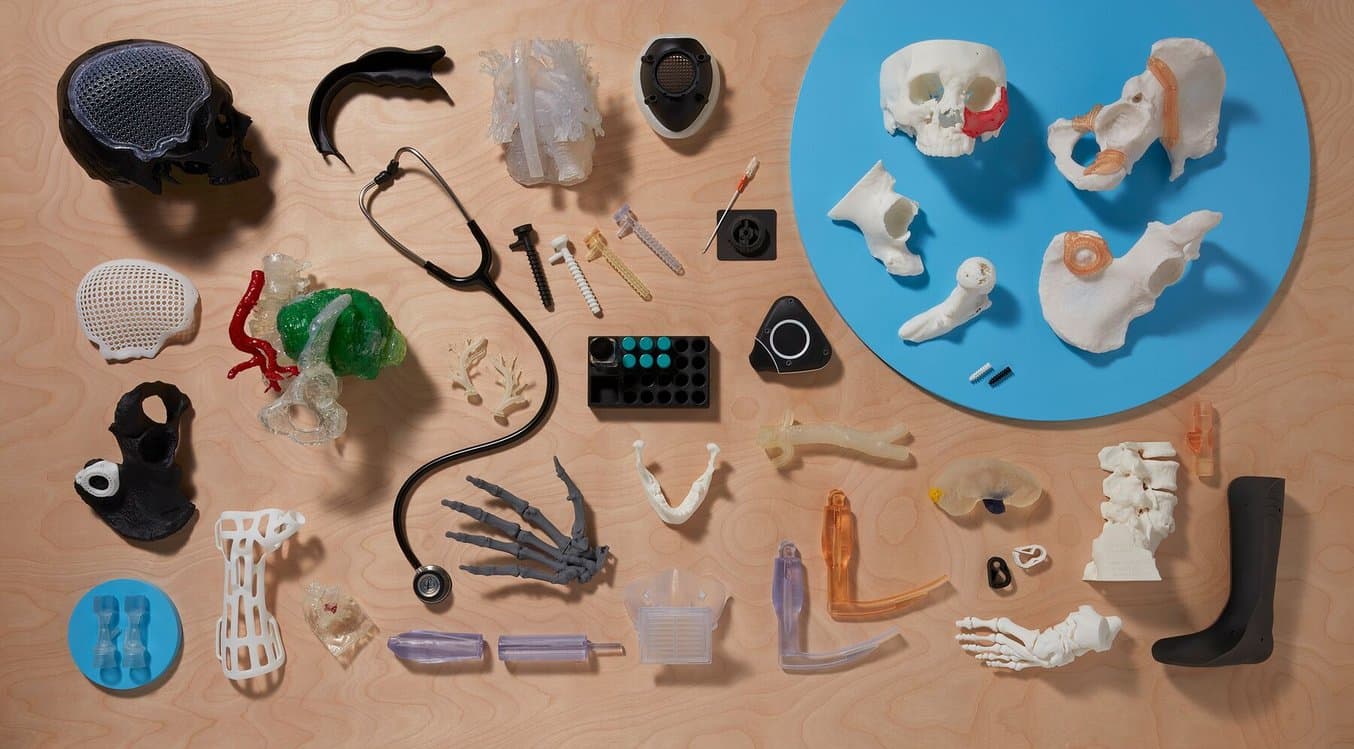
La gamme de matériaux Formlabs comprend des résines pour l'impression SLA et des poudres pour l'impression SLS optimisées pour une variété d'applications médicales.
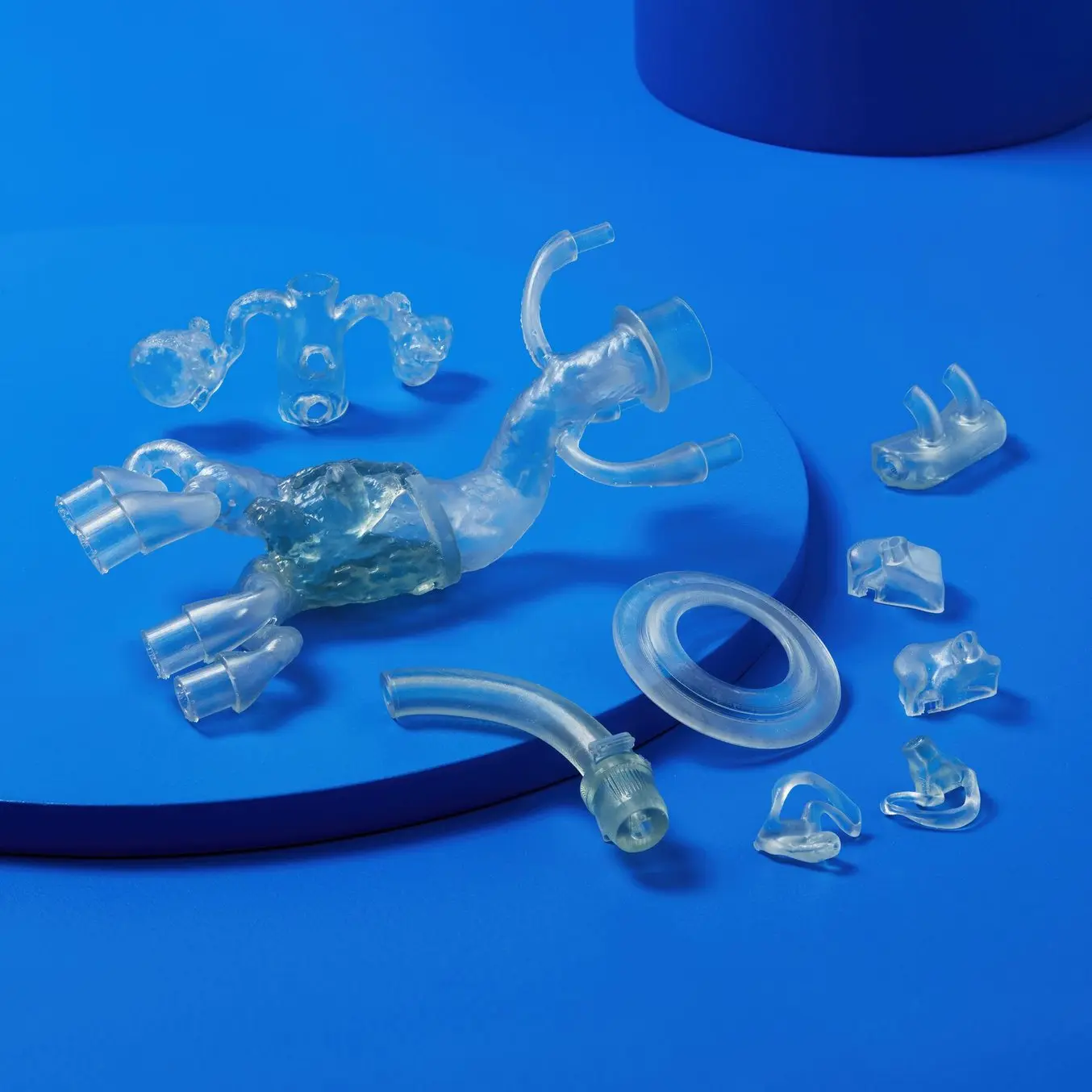
Maîtriser les matériaux pour imprimer en 3D des dispositifs médicaux
Dans ce webinaire, Shiden Yohannes, ingénieur médical chez Formlabs, explore les différents matériaux disponibles pour l'impression 3D et leurs propriétés uniques, vous aidant à faire le bon choix pour vos besoins spécifiques.
Résines pour le SLA
Le SLA prend en charge un large éventail d'applications, notamment dans les domaines de l'ingénierie, de la fabrication et des soins de santé. Les résines SLA ont été développées avec des propriétés matérielles spécifiques, y compris des options élastiques, durables et biocompatibles.
Pour les professionnels de la santé, les résines BioMed de Formlabs sont des matériaux de qualité médicale pour des applications exigeant performance et biocompatibilité. Les matériaux de notre famille de résines BioMed sont développés et fabriqués dans une installation certifiée ISO 13485 et sont compatibles avec les méthodes courantes de désinfection et de stérilisation.
Le choix de la résine appropriée dépend de l'application, des exigences mécaniques du matériau et du cas d'utilisation. Les résines BioMed de Formlabs comprennent des options rigides et élastiques, dont certaines pour le contact à long terme ou avec les muqueuses.
En outre, une gamme de matériaux a été développée spécifiquement pour répondre aux besoins des professionnels dentaires. Les résines comprennent Premium Teeth Resin pour l'impression directe de dents de prothèses, et Dental LT Comfort Resin pour les gouttières occlusales. Un catalogue complet des matériaux et des informations sur plus de 17 applications pour les résines dentaires de Formlabs sont disponibles sur Formlabs Dental.
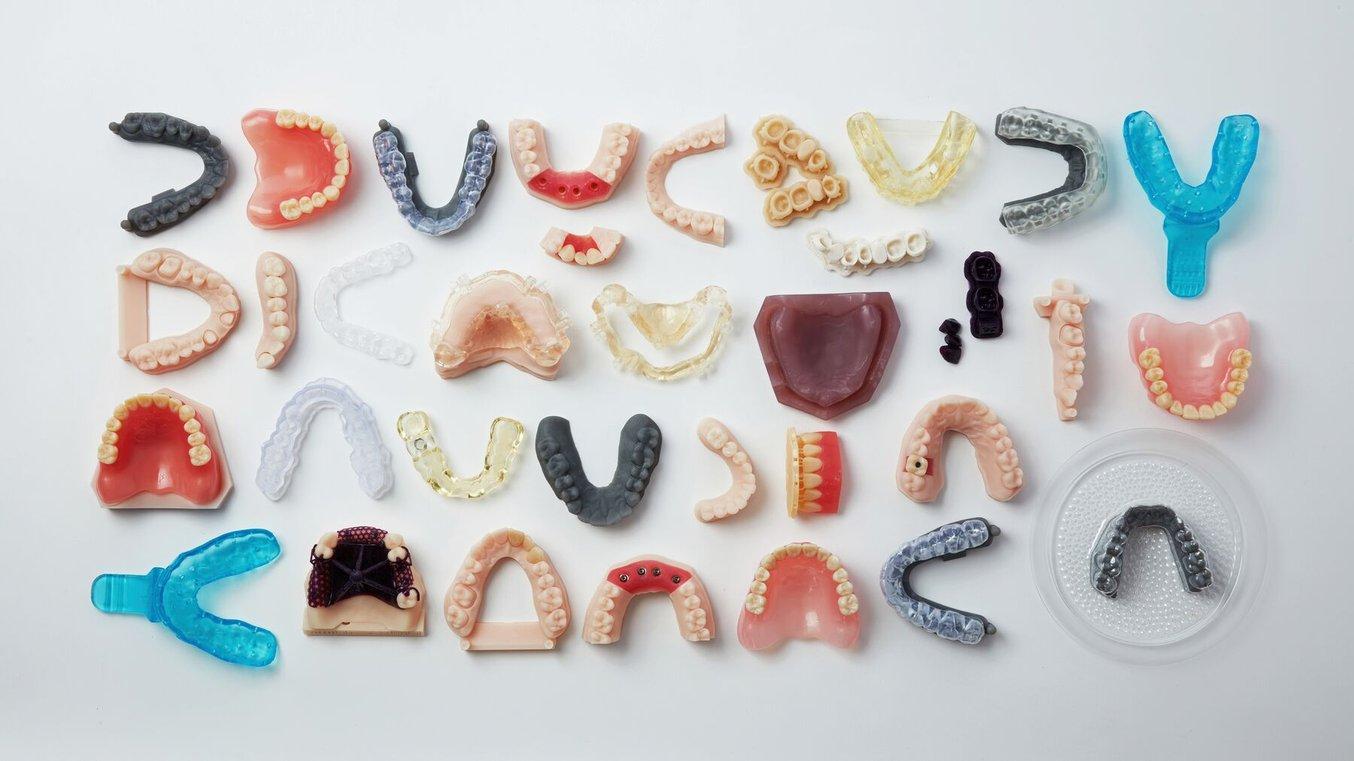
Les résines Formlabs spécialement formulées pour le marché dentaire peuvent être utilisées pour imprimer plus de 17 applications dentaires.
Diversifier les types de résines médicales peut aider les professionnels de la santé dans toute une série de tâches importantes : la création de dispositifs médicaux, la planification des procédures chirurgicales, le développement de nouveaux implants sur mesure et la recherche. Les résines BioMed offrent aux professionnels de la santé une variété d'options de matériaux, élargissant ainsi les capacités d'impression 3D. Le tableau ci-dessous compare les propriétés et les applications de la résine BioMed de Formlabs.
Matériau | Description | Applications |
---|---|---|
BioMed White Resin | Rigide et blanc opaque. Approuvé pour un contact à long terme avec la peau (>30 jours) ou à court terme avec les os, les tissus, la dentine et les muqueuses (<24 heures). | Dispositifs médicaux à usage final et composants de dispositifs; modèles et moules de dimensionnement d'implants spécifiques au patient ; guides de coupe et de forage; outils et gabarits chirurgicaux; moules, gabarits et montages biocompatibles; modèles anatomiques pouvant être utilisés en salle d'opération. |
BioMed Black Resin | Rigide et noir mat. Approuvé pour le contact à long terme avec la peau (>30 jours) et à court terme avec les muqueuses (<24 heures). | Dispositifs médicaux et composants de dispositifs; moules, gabarits et fixations biocompatibles; pièces d'utilisation finale nécessitant un contact avec le patient ; biens de consommation. |
BioMed Amber Resin | Rigide et semi-transparent. Approuvé pour un contact à long terme avec la peau (>30 jours) ou à court terme avec les os, les tissus, la dentine et les muqueuses (<24 heures). | Dispositifs médicaux à usage final; modèles de dimensionnement d'implants; guides de coupe et de forage. |
BioMed Clear Resin | Rigide et transparent. Approuvé pour un contact à long terme avec la peau (>30 jours), les voies respiratoires et les muqueuses (>30 heures) ou à court terme avec les os, les tissus et la dentine (<24 heures). | Dispositifs d'utilisation finale, y compris les dispositifs de respiration ; prototypes, moules, gabarits et fixations biocompatibles; modèles pour la visualisation et le dimensionnement des implants; dispositifs pour la culture cellulaire et les bioprocédés. |
BioMed Durable Resin | Résistant aux chocs, aux éclats et à l'abrasion. Transparent. Approuvé pour un contact à long terme avec la peau (>30 jours) et les muqueuses (>30 heures) ou à court terme avec les tissus, les os et la dentine (<24 heures). | Instruments spécifiques aux patients ; instruments à usage unique; dispositifs et composants à usage final nécessitant une biocompatibilité et une résistance aux chocs. |
BioMed Elastic 50A Resin | Doux et semblable à du silicone. Translucide. Approuvé pour un contact à long terme avec la peau (>30 jours) ou à court terme avec les muqueuses (<24 heures). | Dispositifs médicaux confortables nécessitant un contact prolongé avec la peau; modèles de tissus mous biocompatibles que les chirurgiens peuvent utiliser comme modèle dans la salle d'opération. |
BioMed Flex 80A Resin | Semblable à du caoutchouc dur. Translucide. Approuvé pour le contact à long terme avec la peau (>30 jours) et à court terme avec les muqueuses (<24 heures). | Dispositifs et composants médicaux biocompatibles flexibles; dispositifs médicaux nécessitant un contact de courte durée avec les muqueuses; modèles de tissus fermes pour faciliter les interventions chirurgicales. |
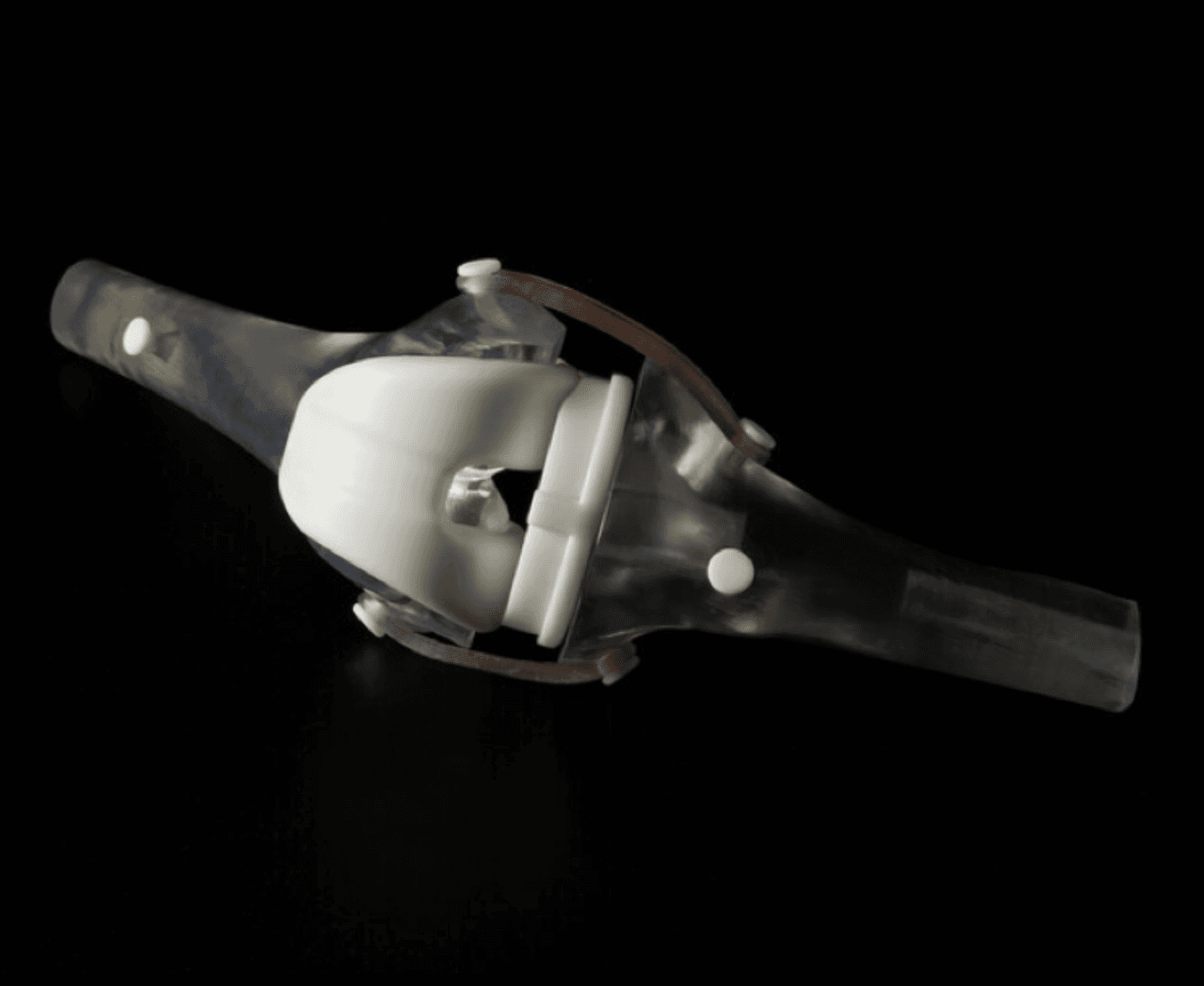
Créer des modèles de simulation osseuse pour le perçage et la coupe
Les modèles de simulation osseuse imprimés en 3D révolutionnent la formation médicale, la planification chirurgicale, la recherche et le développement de dispositifs médicaux. Ce guide d'application présente les options de matériaux de simulation osseuse pour l'impression 3D stéréolithographique (SLA) et l'ensemble du procédé de fabrication interne de modèles anatomiques semblables à des os destinés à l'entaille et au perçage.
Poudres SLS
Les poudres SLS peuvent être biocompatibles, sans danger pour la peau et stérilisables, et les conceptions peuvent avoir des détails fins et des parois minces. Ces propriétés les rendent idéales pour les applications dans le domaine de la santé, notamment les dispositifs médicaux, les prototypes, les prothèses, les instruments chirurgicaux et les orthèses.
Le matériau le plus utilisé en SLS est le nylon, thermoplastique courant en ingénierie, dont les propriétés mécaniques sont excellentes. Le nylon est léger, solide et flexible, et il est résistant aux chocs, aux produits chimiques, à la chaleur, aux rayons UV, à l'eau et à la saleté. Les pièces en nylon imprimées en 3D peuvent également être biocompatibles et non sensibilisantes, ce qui signifie qu'elles peuvent rester en contact avec la peau et être utilisées en toute sécurité.
Nylon 12 Powder offre une résistance à la rupture de 50 MPa, ce qui lui confère une grande souplesse d'utilisation. Capable de réaliser des assemblages complexes et des pièces durables avec une grande stabilité environnementale, Nylon 12 Powder est idéale pour le prototypage de haute performance, la fabrication de petites séries et les gabarits, fixations et outils permanents. Les pièces sont biocompatibles et stérilisables, ce qui rend Nylon 12 Powder idéale pour les applications médicales, telles que les guides chirurgicaux.
Nylon 11 Powder est un matériau idéal pour les orthèses résistantes présentant une ductilité élevée et une stabilité à long terme, y compris les semelles intérieures. Pour en savoir plus sur la durabilité de ce matériau, consultez l'analyse des performances.
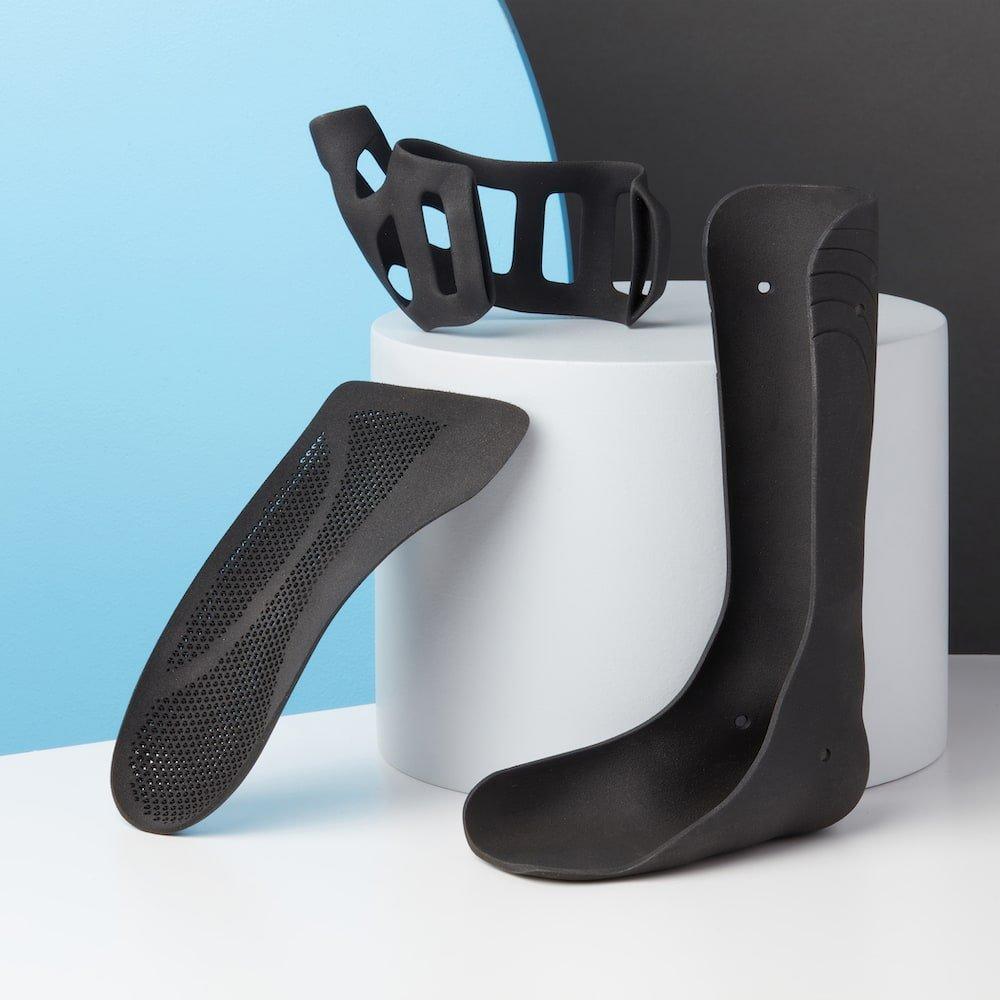
Orthèses imprimées avec Nylon 11 Powder.
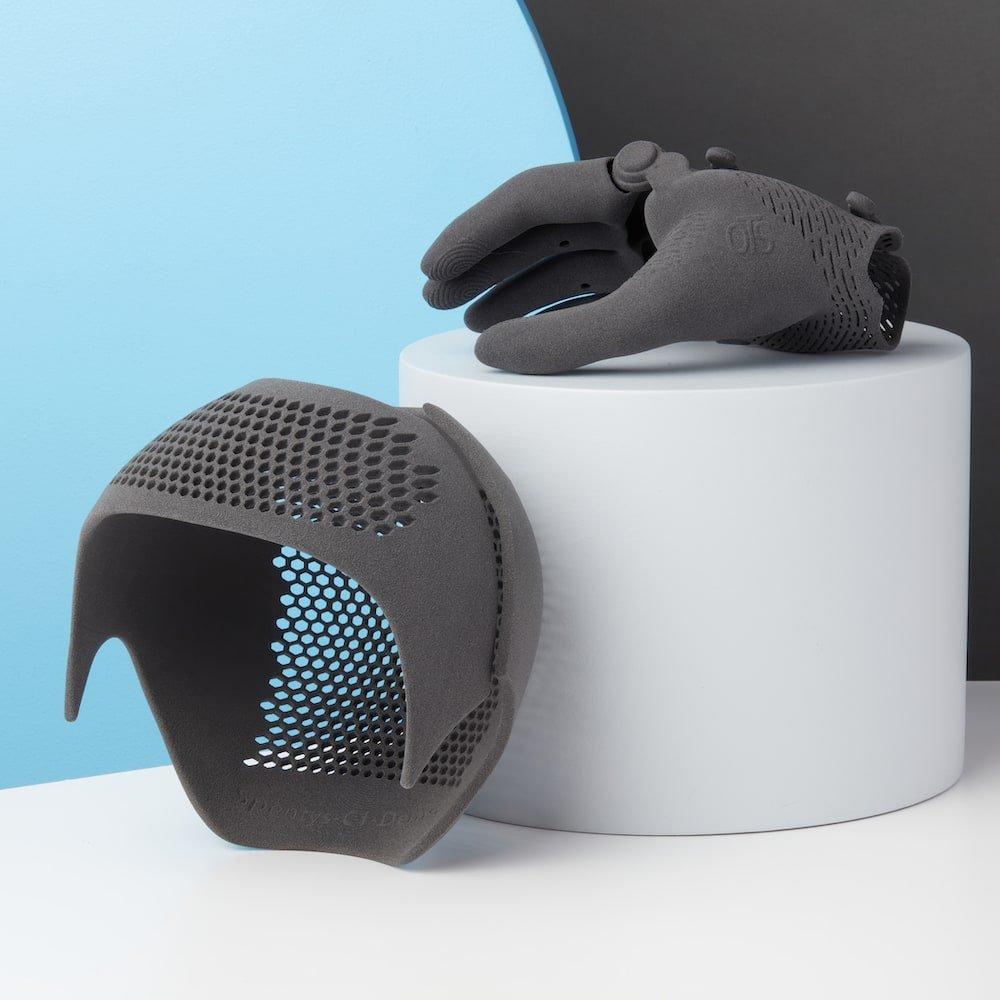
Un casque de remodelage crânien et un prototype de prothèse imprimé avec TPU 90A Powder.
Polypropylene Powder peut être utilisée pour produire des prototypes dignes d'une œuvre et des pièces durables destinées à l'utilisation finale. Grâce à sa grande ductilité, elle peut être plié à plusieurs reprises et garder une excellente durabilité. Les pièces imprimées avec Polypropylene Powder sont chimiquement résistantes, soudables et étanches, ce qui les rend idéales pour les orthèses, les prothèses, les fixations, les outils et les gabarits.
TPU 90A Powderest un élastomère flexible qui combine une résistance à la déchirure et un allongement à la rupture élevés avec la liberté de conception et la durabilité de l'impression 3D SLS. Le TPU, ou polyuréthane thermoplastique, est un thermoplastique élastomère couramment utilisé. En orthétique, ce matériau sûr pour la peau est souvent utilisé pour les prototypes de dispositifs médicaux et les dispositifs et composants médicaux finaux, les coussinets orthétiques et les doublures de prothèses, les attelles, les casques de remodelage crânien et les semelles athlétiques et correctives.
Le tableau ci-dessous présente quelques-unes des propriétés et des applications des poudres SLS de Formlabs.
Matériau | Description | Applications |
---|---|---|
Nylon 12 Powder | Haute résistance à la traction et durabilité, biocompatible, stérilisable. | Dispositifs médicaux à usage final et composants de dispositifs; modèles et moules de dimensionnement d'implants spécifiques au patient ; guides de coupe et de forage; outils et gabarits chirurgicaux; moules, gabarits et montages biocompatibles; modèles anatomiques pouvant être utilisés en salle d'opération. |
Nylon 11 Powder | Très ductile et robuste. Plus souple, moins cassant et mieux adapté à l'impression de parois fines que Nylon 12 Powder. Biocompatible, stérilisable. | Orthèses et prothèses, prototypes résistants aux chocs, dispositifs médicaux, pièces d'utilisation finale. |
Polypropylene Powder | Ductile et durable, résistant aux produits chimiques, étanche, soudable | Orthèses et prothèses, boîtiers et étuis étanches, montages, outils et gabarits solides et chimiquement résistants. |
TPU 90A Powder | Élastomère durable, sûr pour la peau, résistant à la déformation, avec un allongement élevé à la rupture et une excellente résistance au déchirement. | Semelles, attelles, orthèses et prothèses. Objets de technologie portable et éléments doux au toucher. Rembourrage, coussins et pinces. |
Les propriétés du matériau peuvent varier en fonction du modèle de la pièce et des pratiques de fabrication. La validation de l’adéquation des pièces imprimées pour leur usage prévu est la responsabilité du fabricant.
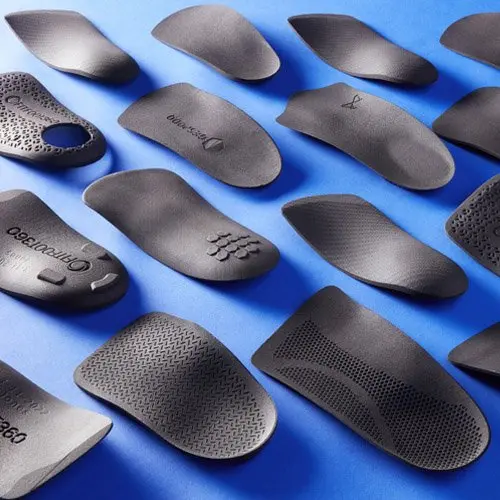
Impression 3D de semelles rigides
Découvrez comment produire des semelles intérieures solides et ductiles dépassant les 4 millions de cycles de pliage grâce à l'écosystème SLS compact et abordable de Formlabs. Ce guide complet vous aidera à vous lancer dans la production d'enveloppes de semelles sur la Fuse 1+ 30W.
Débuter en impression 3D médicale
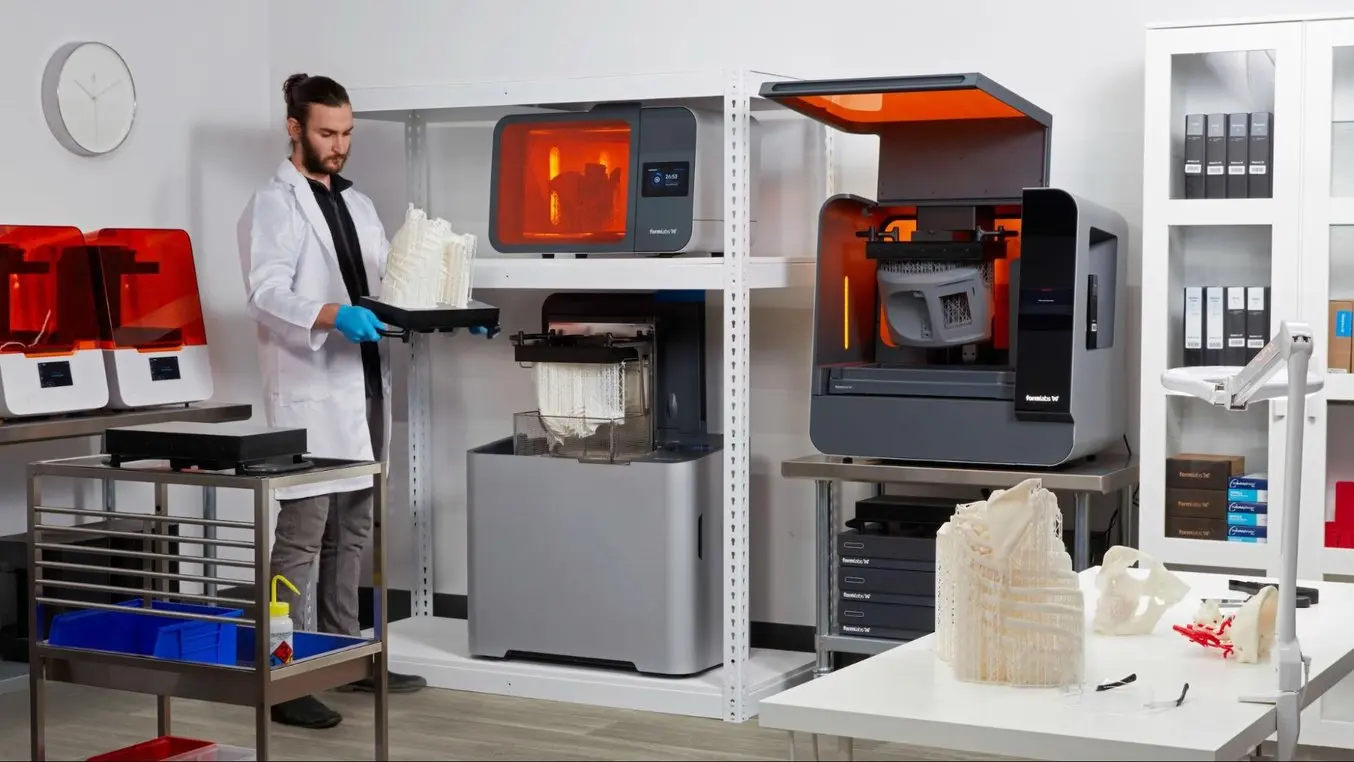
Des processus d’impression 3D médicale précis et abordables sont en train de démocratiser l’accès à cette technologie, donnant aux professionnels de la santé les armes pour développer de nouvelles solutions cliniques, fabriquer rapidement des dispositifs sur mesure, et permettant aux praticiens d’administrer de nouveaux traitements partout dans le monde. À mesure que les technologies et les matériaux d’impression 3D médicale continueront de s’améliorer, ils prépareront le terrain pour le soin personnalisé et des applications médicales révolutionnaires.
Chaque établissement médical doit avoir accès aux outils les plus modernes pour améliorer les soins proposés et offrir la meilleure expérience possible aux patients. Lancez-vous dès maintenant ou internalisez votre production avec Formlabs, un partenaire qui a fait ses preuves en technologie de pointe d'impression 3D médicale.
Contactez nos experts médicaux pour en savoir plus sur la façon dont l'impression 3D en interne peut vous aider à fournir de meilleurs traitements et s'intégrer à votre flux de travail pour concevoir et fabriquer des dispositifs médicaux.