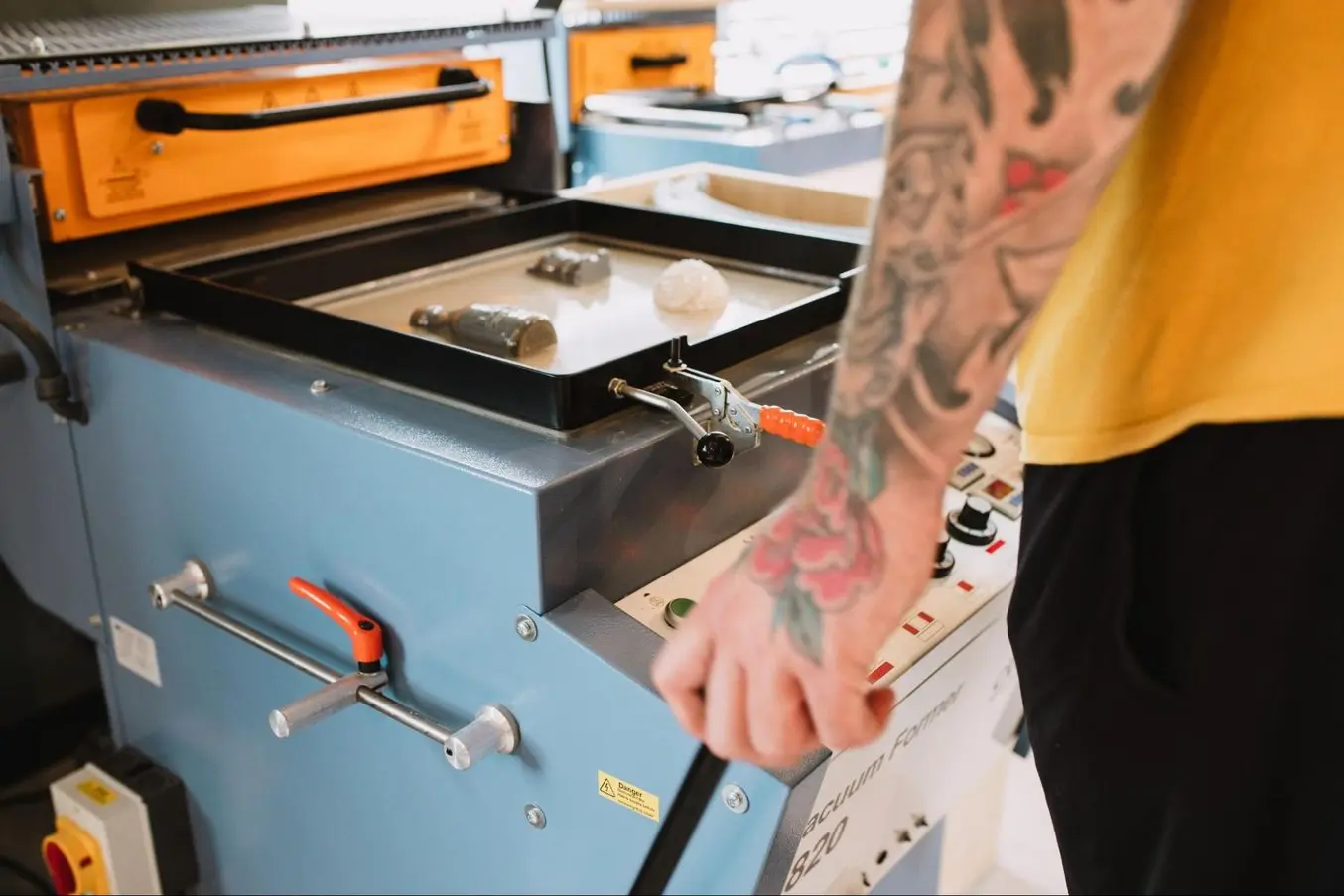
Plastic comes in different sizes, types, colors, and with different material characteristics. The wide variety of plastic makes it a crucial material for manufacturers interested in producing both prototypes and end-use parts for use. Thermoforming is a manufacturing process that empowers manufacturers with a versatile solution for processing plastic sheets.
In this comprehensive guide, learn about the various thermoforming processes, materials, equipment, and how you can create molds for thermoforming, including advanced processes like 3D printing.
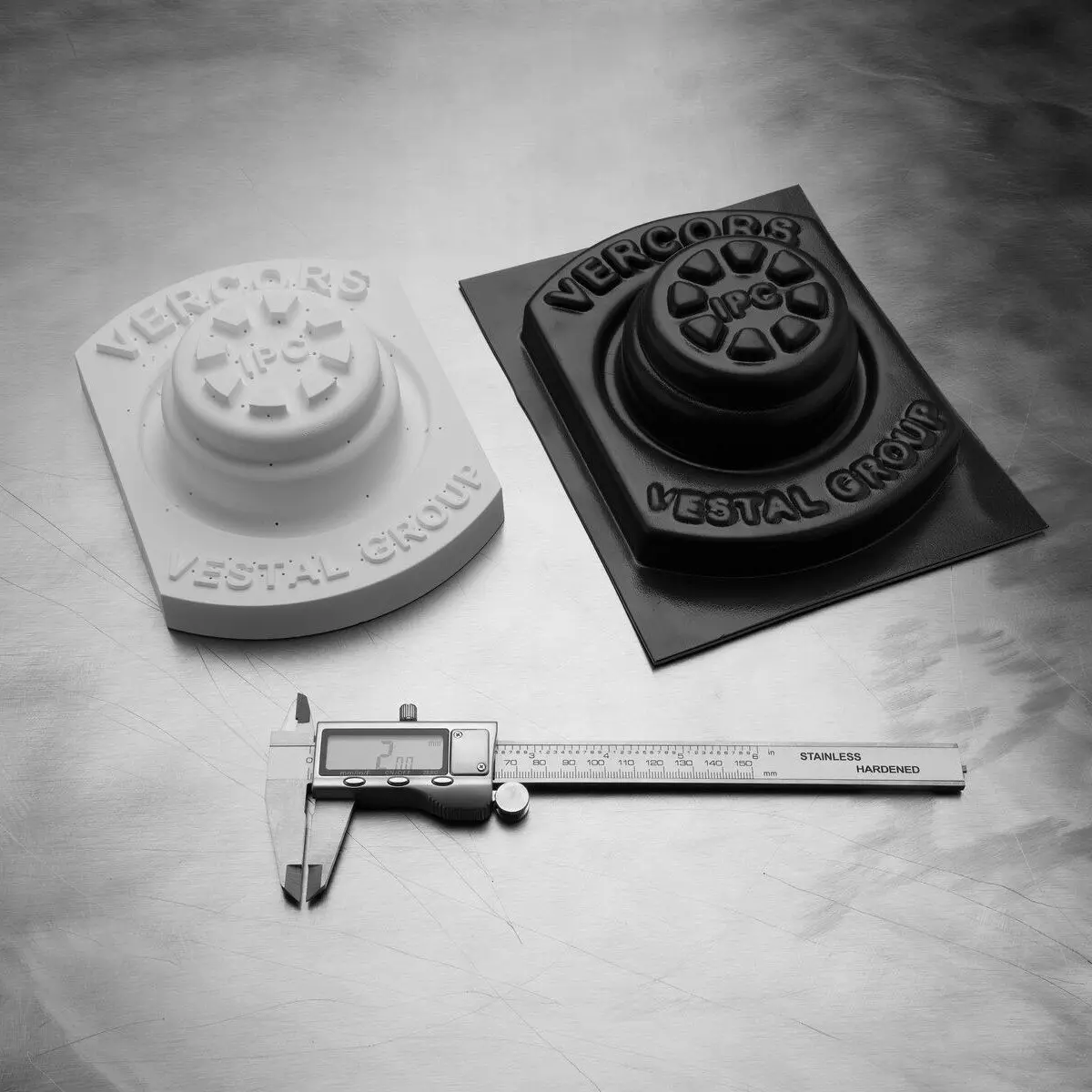
Termoformatura rapida su scala ridotta con stampi realizzati in 3D
Scarica il nostro whitepaper per scoprire come creare stampi complessi in maniera rapida con la stampa 3D e alcuni suggerimenti e linee guida per preparare le parti degli stampi.
What is Thermoforming?
Thermoforming is a plastic manufacturing process that involves heating a plastic sheet and forming it using a mold to specific shapes. The shaped plastic then gets cooled down and trimmed to result in the finished part. The process is executed using a thermoforming machine to heat and stretch the pliable thermoplastic sheet over the mold. Modern thermoforming machines are generally equipped to handle the trimming and cutting process, while for more conventional machines, trimming and cooling may be done externally.
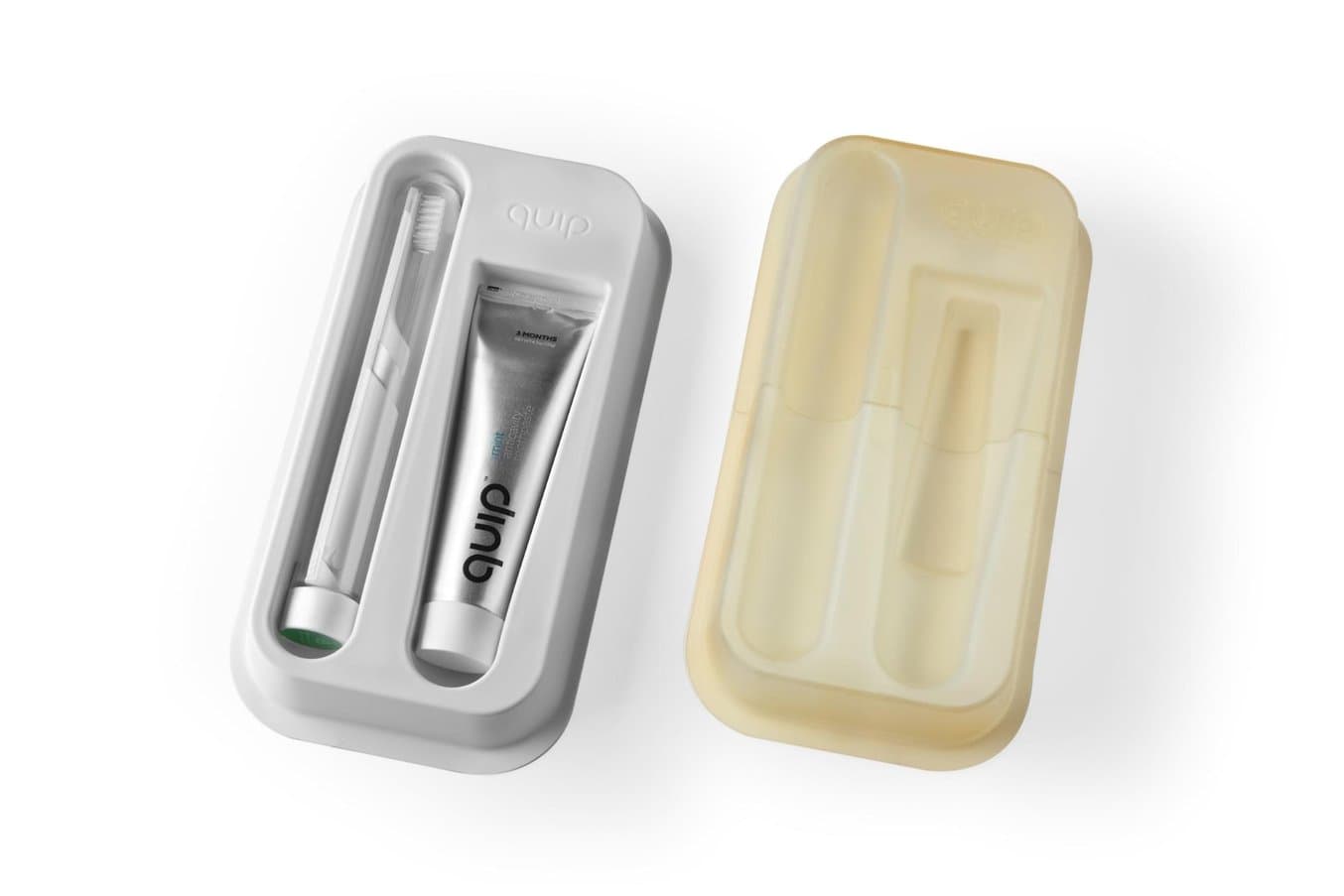
Thermoforming is a common method for producing plastic packaging.
Thermoplastics are the materials used for thermoforming. These materials include ABS, polystyrene, polycarbonate, PETG, etc. The choice of material depends on the manufacturing project and the required characteristics of the produced item.
Thermoforming is used in manufacturing packaging for agricultural products, pharmaceutical products, consumer goods, domestic appliances, and more. It is also used in manufacturing durable end-use parts such as aircraft components, material handling equipment, automobile interiors, and medical equipment.
Compared to other conventional manufacturing processes, thermoforming enables manufacturers to produce small to large volumes of packaging at an affordable cost. The ability to utilize almost all thermoplastic types to rapidly produce high-quality end-use items is another important advantage of thermoforming.
The disadvantages of thermoforming include its restriction to producing thin-walled designs, uneven thickness, and limited versatility for manufacturing parts with complex geometry. Manufacturers interested in leveraging thermoforming can use this guide to gain insight into amplifying its benefits and limiting its disadvantages to improve productivity and reduce costs.
Thermoforming Processes
Thermoforming is an all-inclusive manufacturing process that embraces all the different ways manufacturers may choose to form heated sheets of plastic. A manufacturer which chooses the vacuum forming process or pressure forming process is taking advantage of thermoforming.
Although a variety of processes exist, the most popular thermoforming techniques are the following:
-
Vacuum Forming: This thermoforming process makes use of a vacuum to shape the sheet. First, the plastic sheet is heated to ensure it is flexible. The vacuum forming machine then pulls the air out, forcing the sheet against a mold. The vacuum process is known for its cost-effectiveness and the speed of the manufacturing process.
-
Pressure Forming: The pressure forming process similarly involves the heating of the plastic sheet and utilizing a vacuum to pull air away to force the sheet against a mold. But there’s an extra step. A pressing tool applies pressure once the air is removed to ensure the shaped plastic better maintains its final shape. Pressure forming is used when higher levels of details are required from the thermoforming process.
-
Mechanical Forming: This process involves the use of a direct mechanical force to shape the preheated plastic sheet. A core plug forces the pliable sheet to fill a space between the plug and the mold, and this imprints the surface patterns onto the plastic sheet. Mechanical thermoforming is used when precision and high levels of detail are required.
-
Drape Forming: In drape forming, the heated plastic sheet is draped onto a mandrel designed with specific patterns. The mandrel’s pattern is pressed onto the plastic sheet to form the finished part. The drape forming process is one of the most-affordable thermoforming techniques because limited tooling is required. As the thickness of the material can be maintained, the process doesn’t result in weaknesses in the parts.
-
Matched Mold Forming: This thermoforming process is applied when manufacturing items that require higher levels of accuracy. The matched mold forming process involves the use of a male and female mold to shape the heated plastic sheet. The forming machine applies force to bring the molds together onto the plastic sheet. The sheet then takes the pattern or shape designed into the two molds.
-
Twin Sheet Forming: This process involves the forming of two layers and combining them to form one item. The plastic sheets are heated simultaneously, formed, and joined together to produce an item. The twin sheet forming process is best used to manufacture hollowed items or items with double walls.
-
Billow Forming: The billow forming process is a free-form thermoforming technique that does not rely on molds to shape the heated plastic. Here, the forming machine uses air jets to blast the plastic into a bubble until the final design is formed.
Thermoforming Process | Cost-Effectiveness | Production Volume | Applicazione |
---|---|---|---|
Formatura sottovuoto | Very affordable, quick manufacturing process | Low to large-volume productions | For producing items when precision and accuracy aren’t crucial, such as domestic items and packaging |
Pressure Forming | Affordable manufacturing process | Low to large-volume productions | For producing items when durability and uniformity are requirements |
Mechanical Forming | Affordable manufacturing process | Medium to large-volume production | Used for manufacturing high-quality and precision items |
Drape Forming | Very affordable, quick manufacturing process | Medium to large-volume production | Large components and thick section materials with simple curved shapes |
Matched Mold Forming | Expensive manufacturing process because of the tooling required | Medium to large-volume production | Used to manufacture durable parts and components such as vehicle trimmings and fixtures |
Twin Sheet Forming | Affordable manufacturing process | Medium to large-volume production | Used for manufacturing packaging items such as hollowed and double-walled items |
Billow Forming | More expensive compared to other options | Low-volume production | Used to manufacture skylights, domes, etc. |
Thermoforming Materials
Thermoforming is applied to produce food packages, aircraft components, toys, pallets, and other plastic items. Hence, it is necessary for manufacturers to consider a diverse range of plastic materials prior to a production cycle. The more commonly used materials for thermoforming include:
-
Polypropylene (PP): PP is the most popular plastic material for thermoforming in terms of value and volume. It is commonly used in manufacturing packages, ventilators, toys, and other plastic items. Polypropylene is used because of its innate properties such as excellent resistance to chemicals, fatigue, and heat. Polypropylene is also an affordable material and can be used with the diverse thermoforming processes highlighted here.
-
Polystyrene (PS): This aromatic hydrocarbon polymer provides manufacturers with a clear, hard, and brittle plastic to work with. Polystyrene is widely used as a thermoforming packing material as it offers qualities such as resistance to water and air. Manufacturers use polystyrene to manufacture food packaging, jewel cases, CD cases, and domestic items.
-
Polyethylene Terephthalate (PET): PET provides very good alcohol and essential oil barrier properties, good chemical resistance, and a high degree of impact resistance and tensile strength. It is commonly used for carbonated beverages, water bottles, and many food products.
-
Low-Density Polyethylene (LDPE): LDPE is a thermoplastic that is resistant to chemicals and UV rays. This plastic is also flexible and has high tensile strength. Manufacturers can utilize LDPE to manufacture packaging films, DVDs, cable insulation, containers, and chemical-resistant items.
-
High-Density Polyethylene (HDPE): HDPE is similar to LDPE in terms of its base characteristics and is noted as being resistant to chemicals, UV rays, and water. It is a durable thermoplastic that may be used to manufacture packaging film, blown bottles, containers, pipes, and plastic bags.
-
Polyvinyl Chloride (PVC): PVC is another popular plastic used in manufacturing pipes, window frames, automotive interiors, domestic items, packages, and footwear. PVC can be developed to be either rigid or flexible depending on the manufacturer’s requirements. This thermoplastic is also dense, durable, and resistant to water. It is important to note that PVC isn’t completely chemical resistant and may react to chlorine.
-
Polycarbonate (PC): Polycarbonates are strong, tough materials that can undergo large plastic deformations without cracking or breaking. They’re heat-resistant, flame-retardant, and have good electrical insulator properties. Some grades of PC are also optically transparent and highly transparent to visible light. PCs are used for plastic lenses in eyewear, in medical devices, automotive components, protective gear (lenses, safety helmets), bullet-proof glass, car headlamps, and construction.
-
Cellulose Acetate: Manufacturers in search of eco-friendly thermoplastic materials may consider cellulose acetate. This thermoplastic is made from renewable resources such as processed wood pulp. Cellulose acetate is generally colorless and transparent. It is used for manufacturing domestic items, packaging film, glass frames, and pill coverings.
-
Polymethyl methacrylate (PMMA): The properties of PMMA include high strength, resistance to weather elements, durability, and transparency. Manufacturers take advantage of PMMA to produce lenses, headlamps for vehicles, and transparent packaging. The durability of PMMA ensures that end-use parts serve their purpose for the long term.
-
Acrylonitrile-Butadiene-Styrene (ABS): The characteristics of ABS include rigidity, resistance to abrasion, and resistance to low temperatures. Manufacturers can leverage thermoforming and ABS to produce electronic packaging, food containers, and domestic appliances.
Other materials that manufacturers can use include polytetrafluoroethylene (PTFE), polyamide, HIPS, and more. The choice of material depends on the intended thermoforming technique and the project requirements. The application table can help with making the right choice for potential projects.
Applicazioni | Materiali | Common Thermoforming Techniques |
---|---|---|
Packaging | ABS, PP, PMMA, PVC, PET, LDPE | Pressure forming, vacuum forming, matched mold forming, twin sheet forming, mechanical forming |
Household and consumer goods | ABS, PS, PVC, PP, PC | Pressure forming, vacuum forming, mechanical forming |
Automotive interiors and components | PC, PMMA, HDPE, LDPE | Drape forming, match mold forming, pressure forming |
Healthcare and medical devices | Cellulose Acetate, LDPE, PC | Pressure forming, mechanical forming, vacuum forming |
Construction, HVAC, and plumbing | PVC, HDPE, PC | Mechanical forming, pressure forming, vacuum forming, drape forming |
Heavy Gauge vs. Thin Gauge Thermoforming
The dimensional difference between the plastic sheets used in thermoforming is the differentiating factor between thin and heavy-gauge thermoforming. Thin-gauge thermoforming equipment is fed using thin sheets from plastic rolls. Heavy-gauge (or thick-gauge) thermoforming is fed using thick plastic sheets. The thickness variations play crucial roles when selecting thermoforming equipment.
For example, manufacturers intending to produce plastic cups and food packaging rely on thin-gauge thermoforming to produce thinner items. Conversely, producing pallets and containers requires heavy-gauge thermoforming and supporting equipment. Heavy-gauge thermoforming equipment is designed for low to mid-volume production and thin-gauge thermoforming is designed for high-volume production.
Here’s an overview of the differentiating factors between heavy and thin-gauge thermoforming:
Plastic Thermoforming | Heavy Gauge | Thin Gauge |
---|---|---|
Part Thickness | .060–.375″ 1.5–9.5 mm | < .125” < 3 mm |
Machinery Type | Plastic-sheet fed | Thin-roll fed |
Thermoplastic Materials Used | ABS, HDPE, Polypropylene | PETG, PET, PVC |
Production Volume | Low to medium volume | Medium to high volume |
Use Cases | Electronic enclosures, interior parts, industrial tooling, permanent structural components, pallets, baths, shower trays. luggage. | Rigid or semi-rigid disposable packaging, single-use items (food containers, disposable cups, plates, and trays), and small medical device packaging. |
Thermoforming Equipment
Each thermoforming process requires specialized equipment, for example, different machines are required for vacuum forming, pressure forming, twin sheet forming, or drape forming.
Thermoforming equipment can be broken down further into categories defined by their use cases. These categories are spread across desktop, industrial, and DIY thermoforming equipment. Professional manufacturers and enthusiasts can choose from these options depending on the application.
To choose the right thermoforming equipment, the following product specifications should be considered:
-
Forming area: The forming area refers to the build space where the plastic pattern or design is formed. The forming area is equipped with the designed mold(s), core plug, or the mechanism that applies patterns to the preheated plastic sheet.
-
Depth of draw: The depth of draw or draw ratio is crucial to understanding the thermoforming process. The draw ratio lets the manufacturer know the gauge of plastic required for individual thermoforming projects. Knowledge of the “depth of draw” the equipment utilizes enables the manufacturer to determine the thickness of the plastic part and the surface area the plastic sheet should cover during the thermoforming process.
-
Machine dimensions: The dimensions of the thermoforming equipment determine the size of components or plastic parts the chosen equipment can produce. Desktop thermoforming equipment is compact, and therefore offers limited forming dimensions, while industrial solutions are much larger.
-
Clamping force: Some thermoforming machinery, such as the pressure forming, twin sheet, and matched mold forming equipment, clamps down on the plastic sheet to form the finished part. The clamping force is an important consideration because it helps determine the type of material that may be used.
-
Tool-change capabilities: Evaluating the tool-change capabilities of a thermoforming machine can help manufacturers determine how quickly tool changes can be executed. Faster tool change increases the efficiency and cost-effectiveness of the equipment in production.
Types of Thermoforming Equipment
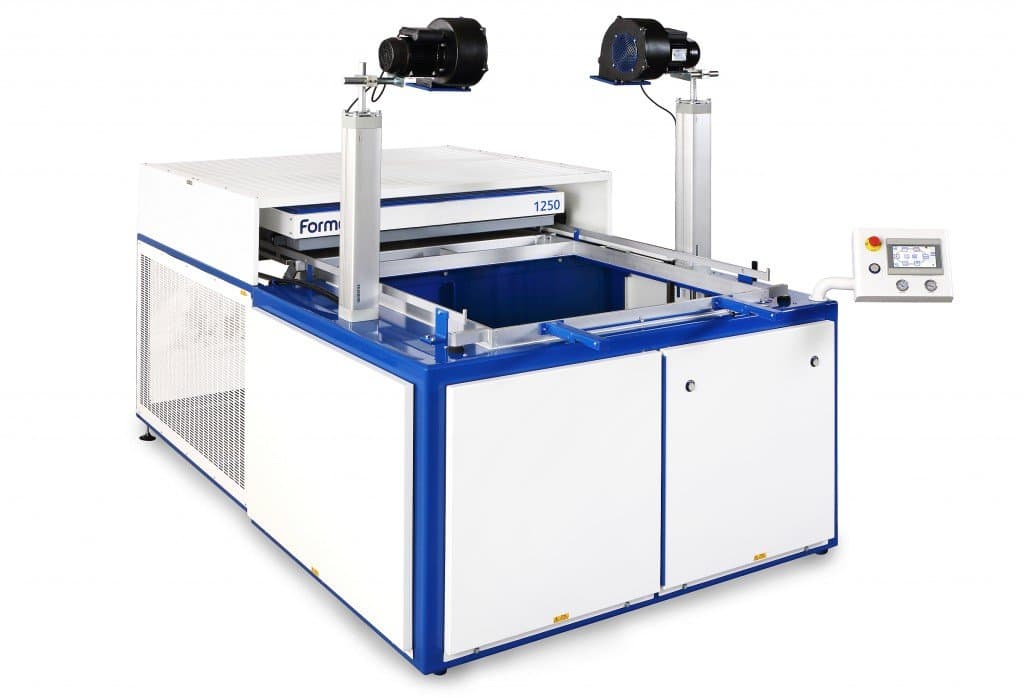
Large-format industrial vacuum forming machine by Formech.
Once the characteristics are known, a manufacturer may choose a thermoforming machine that falls into one of these categories:
-
Industrial thermoforming equipment: These are large-scale machines built for mid-to large-volume production. Industrial vacuum forming machines are compatible with a wider range of materials and sheet thicknesses, offer a deeper draw, and have stronger vacuum forces or pressure to form complex and intricate details and achieve a part quality similar to injection molding. Examples of industrial thermoforming equipment include the GN, Ridat, Formech, and Belovac vacuum forming machines. The cost of industrial thermoforming equipment starts at around $10,000 and goes well beyond that.
-
Desktop thermoforming equipment: Desktop thermoformers come with reduced dimensions, material choice, and exert lower forces. Manufacturers, product developers, and hobbyists utilize desktop thermoforming equipment for prototyping, custom parts, and low-volume production. Desktop thermoforming equipment starts below $1,000, with a wide range of options offered below $10,000. Examples include Formech, Mayku, and Smartform.
-
DIY thermoforming equipment: Enthusiasts who intend to experiment with thermoforming can choose to manufacture their own DIY equipment for low-volume production. DIY equipment is generally more affordable compared to standard thermoforming equipment, but it is more labor-intensive and requires expertise.
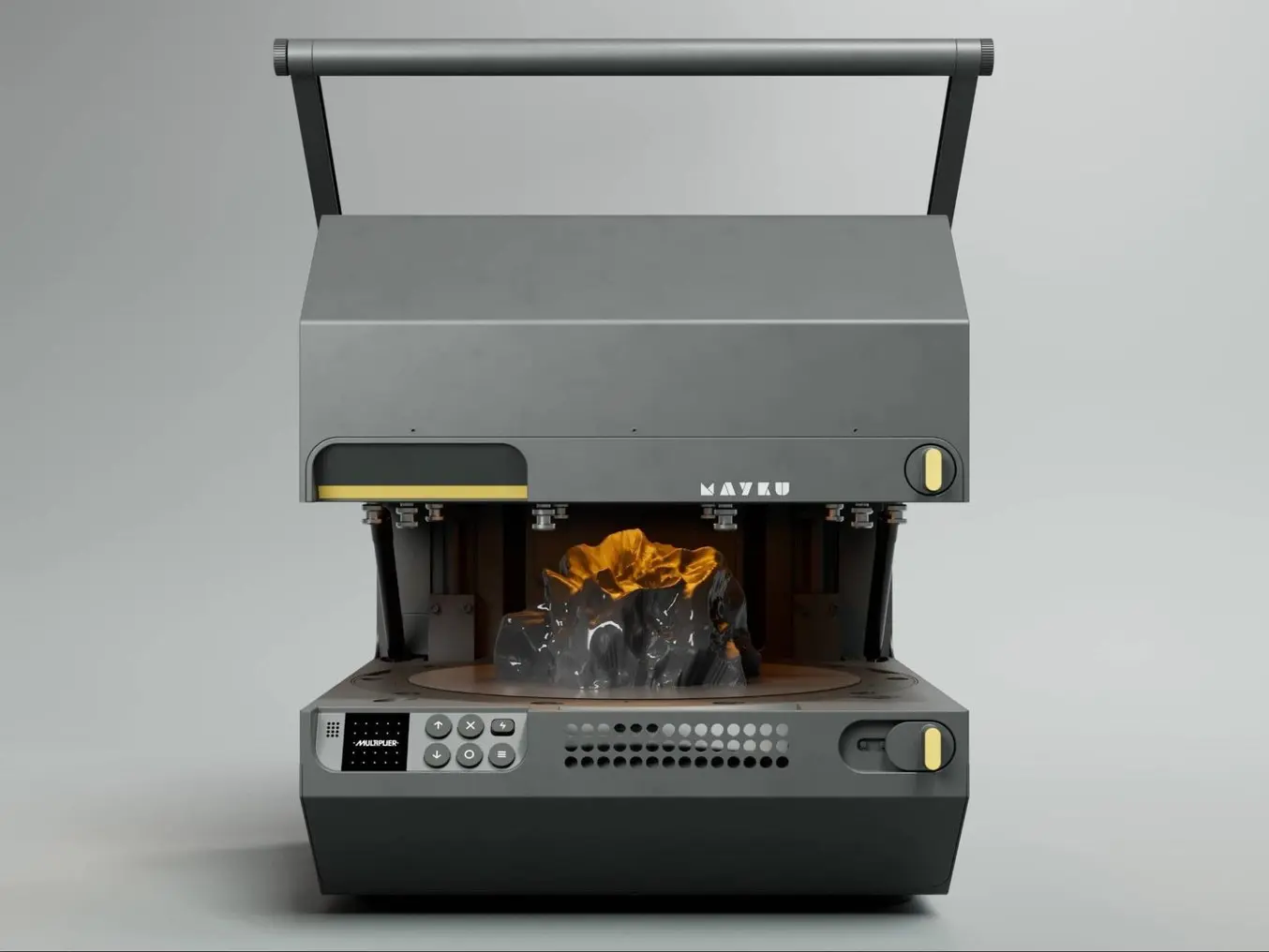
A desktop pressure former produced by Mayku.
Stampi per termoformatura
Most common thermoforming techniques make use of patterned molds to form the plastic sheet into the finished part, including vacuum forming, pressure forming, matched mold forming, mechanical forming, and twin sheet forming.
The molds required for the thermoforming process can be developed using diverse manufacturing processes, including hand sculpting wood, CNC machining plastic, structural foam, fiberglass, engineered composites, or metals, 3D printing polymers, or casting plaster or metal.
Mold design and the right process for producing the mold is dependent on part design and the following factors:
-
Production volume: Wood, plaster, composites, and 3D printed plastic molds are generally the most cost-effective for custom parts, prototypes, and low-volume production, while 3D printed, machined, or cast polymer and composite molds are also ideal for medium runs. For high-volume production, metal molds are the most common due to their improved thermal conductivity and strength, which results in better control of the mold surface temperature, greater part-to-part uniformity, reduced cycle times, and better durability.
-
Part design: Handcrafting molds from wood might be ideal for simple molds, but parts with complex geometries and requiring precision and accuracy are better suited for casting and digital tools like machining or 3D printing.
-
Thermoforming temperature: Depending on the material thermoformed, the mold might require higher thermal resistance. Including cooling channels in the mold can improve cooling rates, uniformity, and reduce cycle times.
-
Thermoforming forces: The tool should be strong enough to withstand the forming forces involved in the process such as vacuum forces, pressures, or mechanical actions. The intensity of those forces will depend on the material type, sheet gauge, and requirements on part quality such as surface finish and level of details.
-
Mold design features: The mold should include critical features such as multiple ventilation holes to circulate the air from the forming process and draft angles to help demold the part.
-
Mold surface finish: The requirements on part quality such as the surface finish, level of details, dimensional accuracy, and stability are to take into consideration when manufacturing the tool.
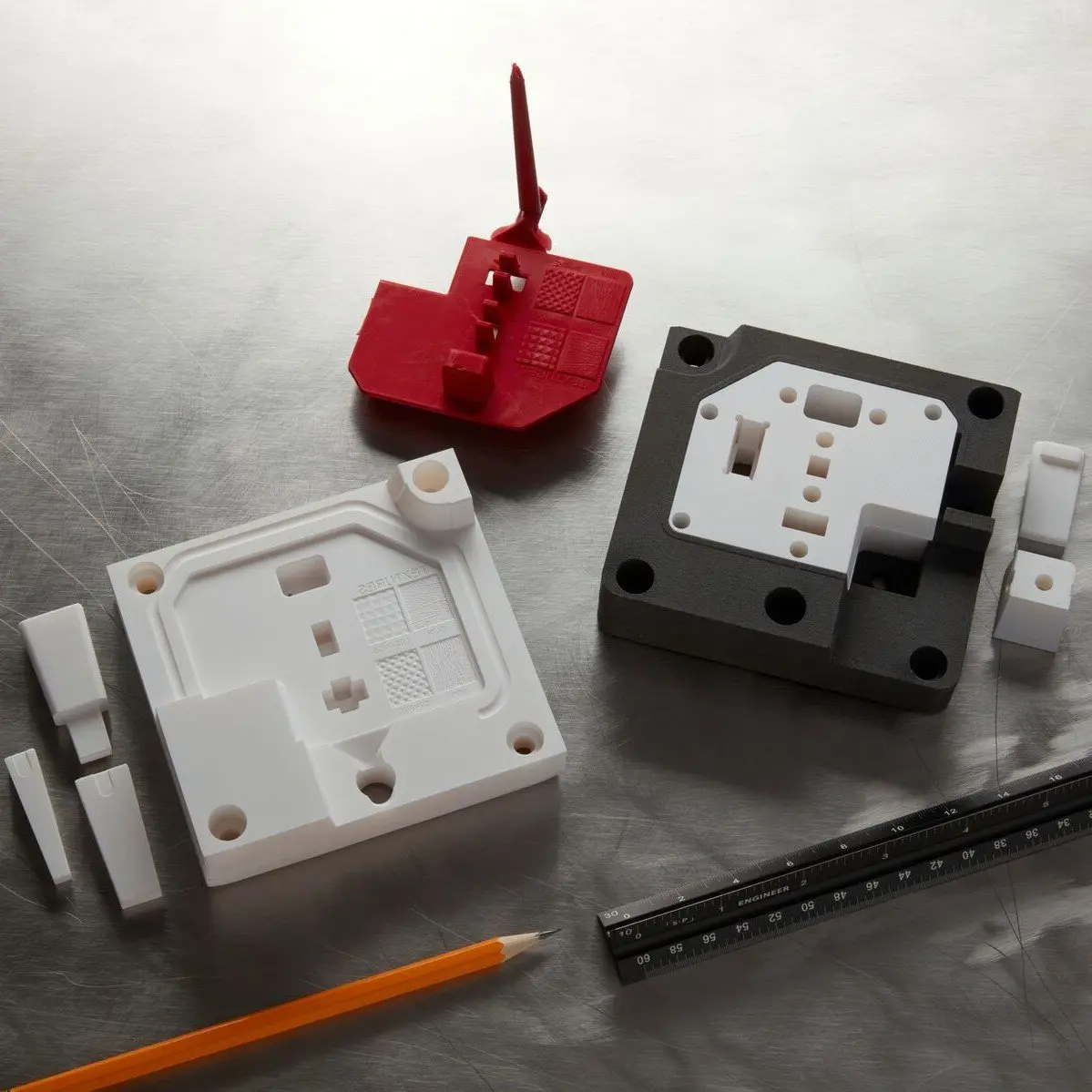
Guida alla creazione rapida di attrezzature
In questo whitepaper scoprirai di più su come combinare la creazione rapida di attrezzature con processi di fabbricazione tradizionali come lo stampaggio a iniezione, la termoformatura o la colata.
Manufacturing Thermoforming Molds With 3D Printing
Traditional methods for mold production are often costly, labor-intensive, and have long lead times, which can limit the efficiency of thermoforming processes.
Many businesses are turning to stereolithography (SLA) 3D printing to create molds for thermoforming processes—also known as rapid tooling, because it offers a fast turnaround time at a low price point, especially for shorter runs, custom parts, and prototype designs. 3D printing also offers unmatched design freedom to create complex and intricate molds. Use the Form 3+ desktop SLA printer to produce smaller molds, and the Form 3L large format 3D printer for mold sizes up to 33.5 × 20 × 30 cm (13.2 × 7.9 × 11.8 in).
The advantages of using 3D printing to develop thermoforming molds include:
-
Speed: 3D printers can create small to mid-sized molds for thermoforming in most cases in less than 24 hours.
-
Cost-effectiveness: 3D printing enables manufacturers to reduce the cost of mold production, dramatically increasing the cost-effectiveness of thermoforming for shorter runs and custom parts.
-
Complex mold designs: 3D printing eliminates the challenges of developing molds with complex geometries using traditional manufacturing processes. For example, 3D printing allows for including design features difficult to machine and the forming process can be improved by adding more air vents for a better draw or pressure. Manufacturers can also leverage the professional 3D printer to develop complex molds for thermoforming processes such as twin sheets and matched mold forming.
-
Rapid mold prototyping: 3D printing empowers manufacturers to iterate and test different mold designs rapidly and at a low cost. The 3D printed molds can then be used directly in manufacturing for custom parts and low volumes, for example for bridge manufacturing until the final mold is delivered.
-
Increased material options: 3D printing offers a wide range of materials, which means that manufacturers can experiment with molds with varying levels of cost, quality, heat resistance, and durability.
-
Surface finish: SLA and resin-based 3D printing technologies enable a smooth surface finish and a high level of detail.
-
Ease of use: Desktop and benchtop (SLA) resin 3D printers can be integrated into any thermoforming workflow seamlessly as they are easy to implement, operate, and maintain, saving CNC time and skilled operators for other high-value tasks in the meantime.
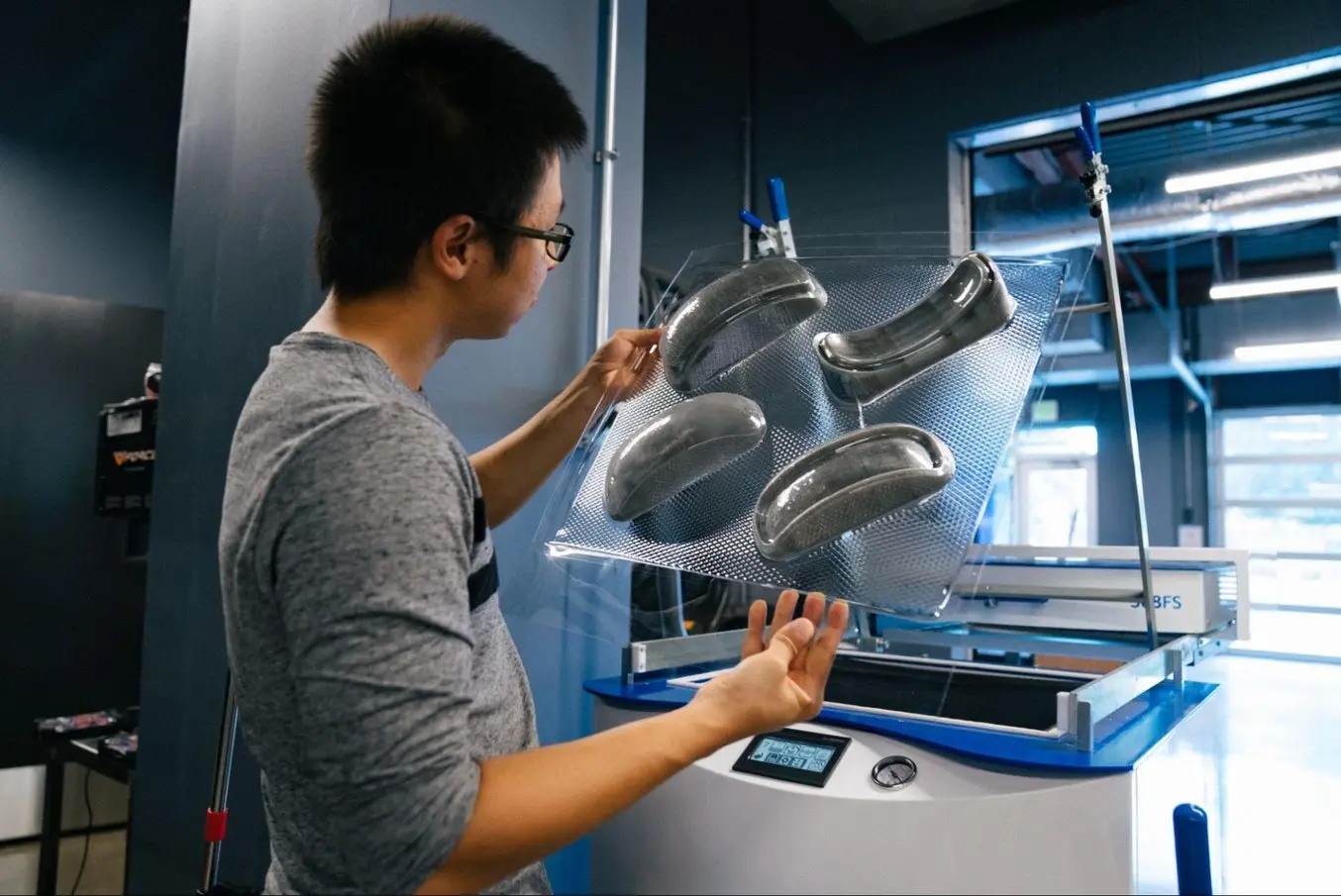
Product development firm Glassboard uses 3D printed molds to thermoform polycarbonate prototypes such as helmet shells or packaging.
To produce thermoplastic prototypes, product development firm Glassboard leverages the printing speed of Draft Resin to quickly produce molds and thermoform polycarbonate prototypes such as helmet shells or packaging. They can achieve complicated mold shapes that would be difficult to manufacture traditionally, including small features and holes for an even better vacuum distribution across the surface.
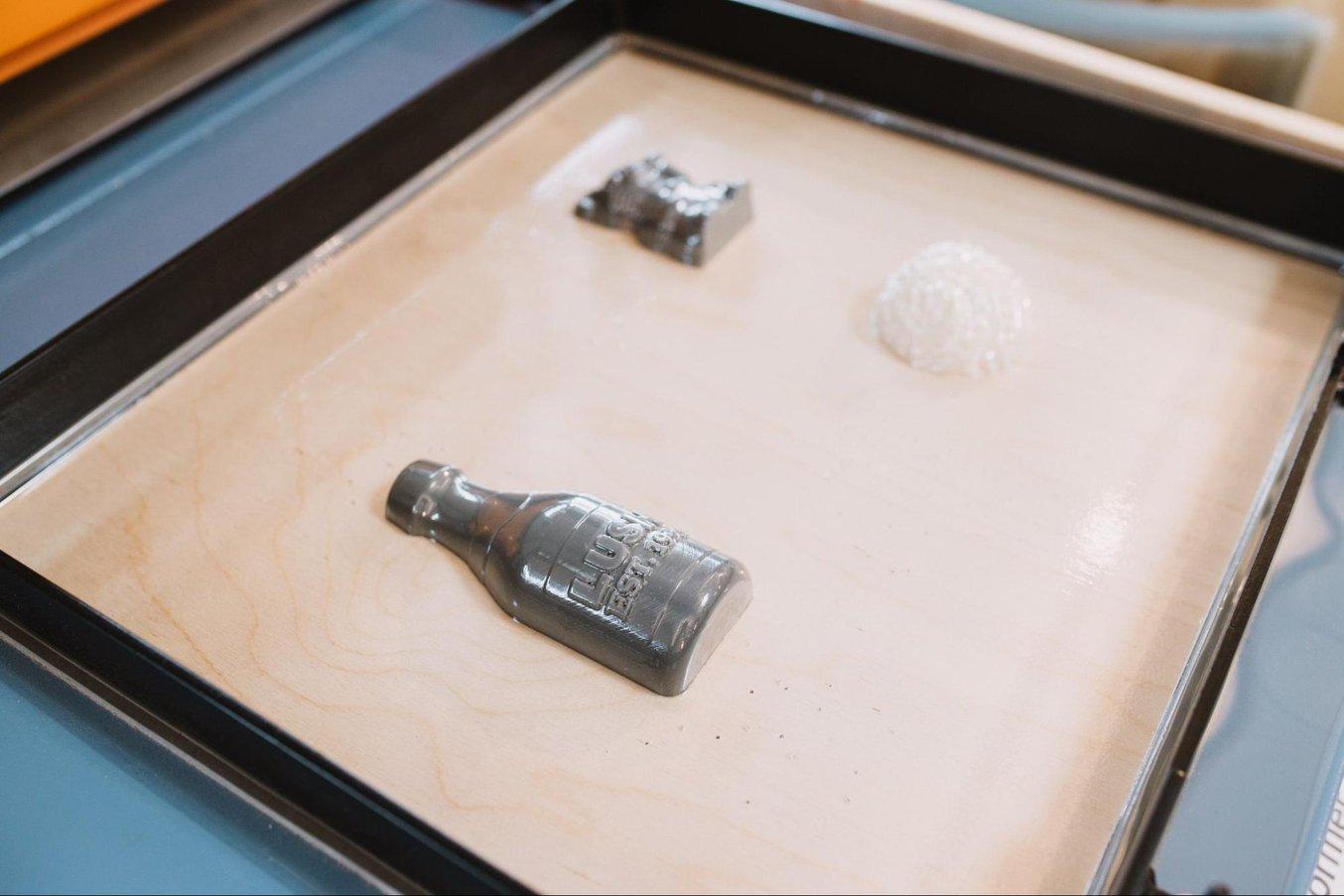
Cosmetics manufacturer Lush uses 3D printed molds to create vacuum forming molds for detailed and textured designs within 24 hours.
Previously, Cosmetics manufacturer Lush hand crafted the master molds for their hugely popular products. But recently, they turned to 3D printing to create vacuum forming molds for detailed and textured designs, which allows them to take ideas from concept to reality in under 24 hours, and test more than a thousand design ideas each year.
3D printed molds for thermoforming are also ideal for manufacturing custom or customized end-use parts cost-effectively. For example, vacuum forming and pressure forming over 3D printed models are the go-to methods for producing clear aligners in orthodontics.

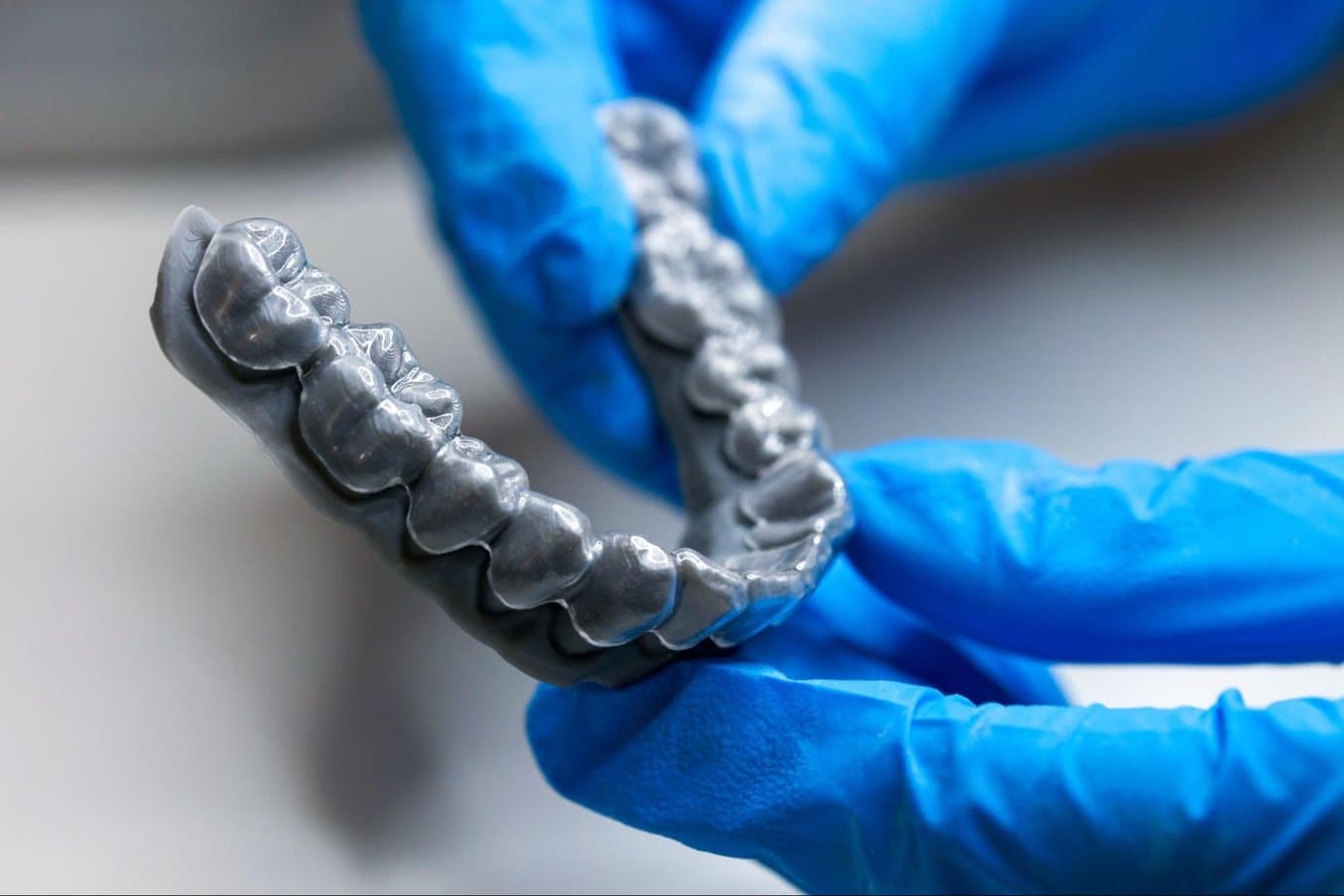
Vacuum forming and pressure forming over 3D printed models are the go-to methods for producing clear aligners in orthodontics.
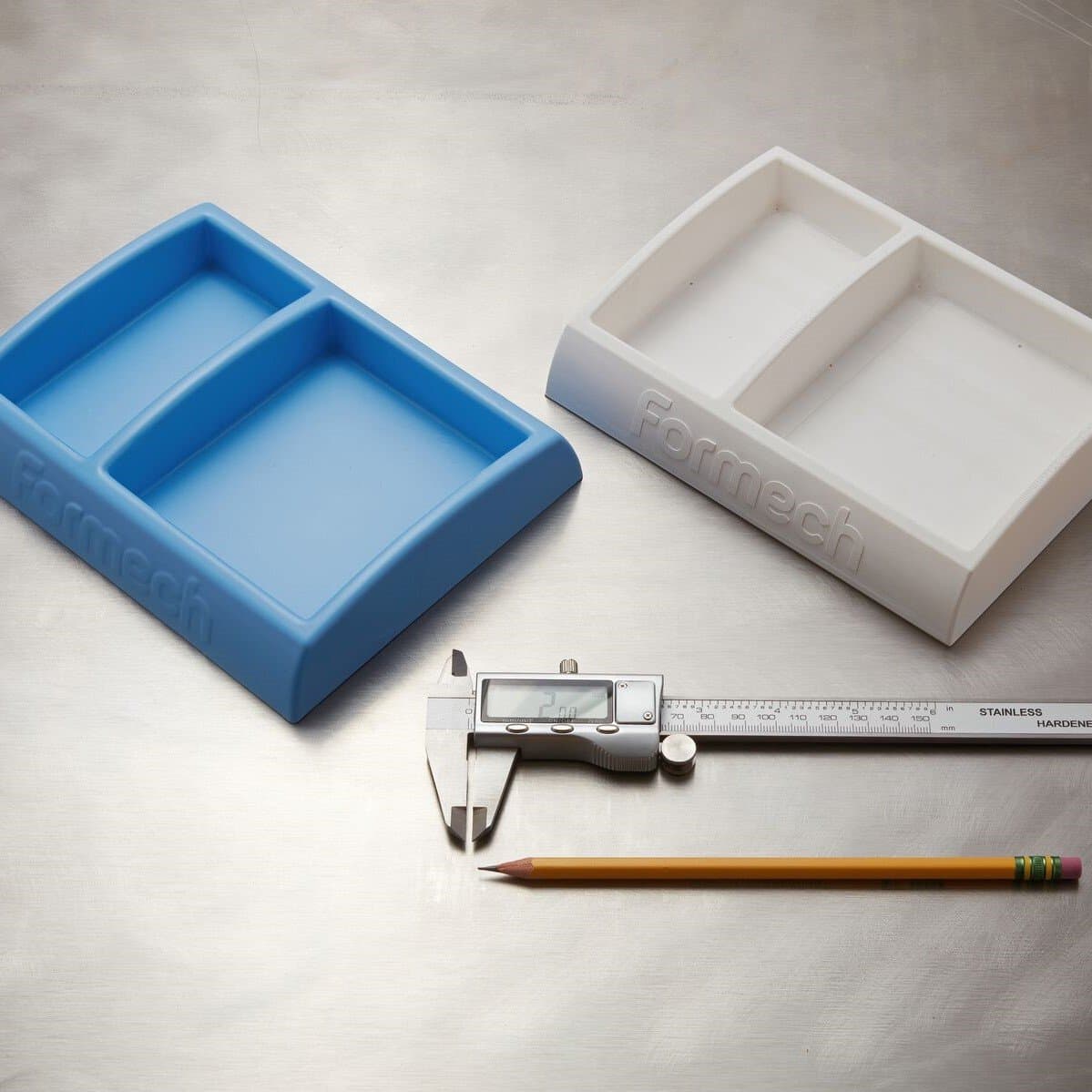
Termoformatura rapida con stampi realizzati in 3D: una guida pratica
Accelera lo sviluppo del prodotto, riduci costi e tempi di realizzazione, e crea facilmente prodotti personalizzati o in volumi ridotti combinando la produzione rapida di attrezzature tramite stampa 3D con la termoformatura.
How to Create Thermoforming Molds With 3D Printing
Integrating 3D printing to speed up the thermoforming process changes the traditional manufacturing workflow highlighted above. The workflow with 3D printing includes the following steps:
-
Design the mold using a CAD application.
-
Choose the right resin from our expansive materials library and 3D print the part on a Formlabs SLA 3D printer.
-
Insert the 3D printed mold in your thermoforming equipment and carry out the production process.
-
Remove the part and carry out any of the standard post-processing steps that may be required to get the produced item ready for use.
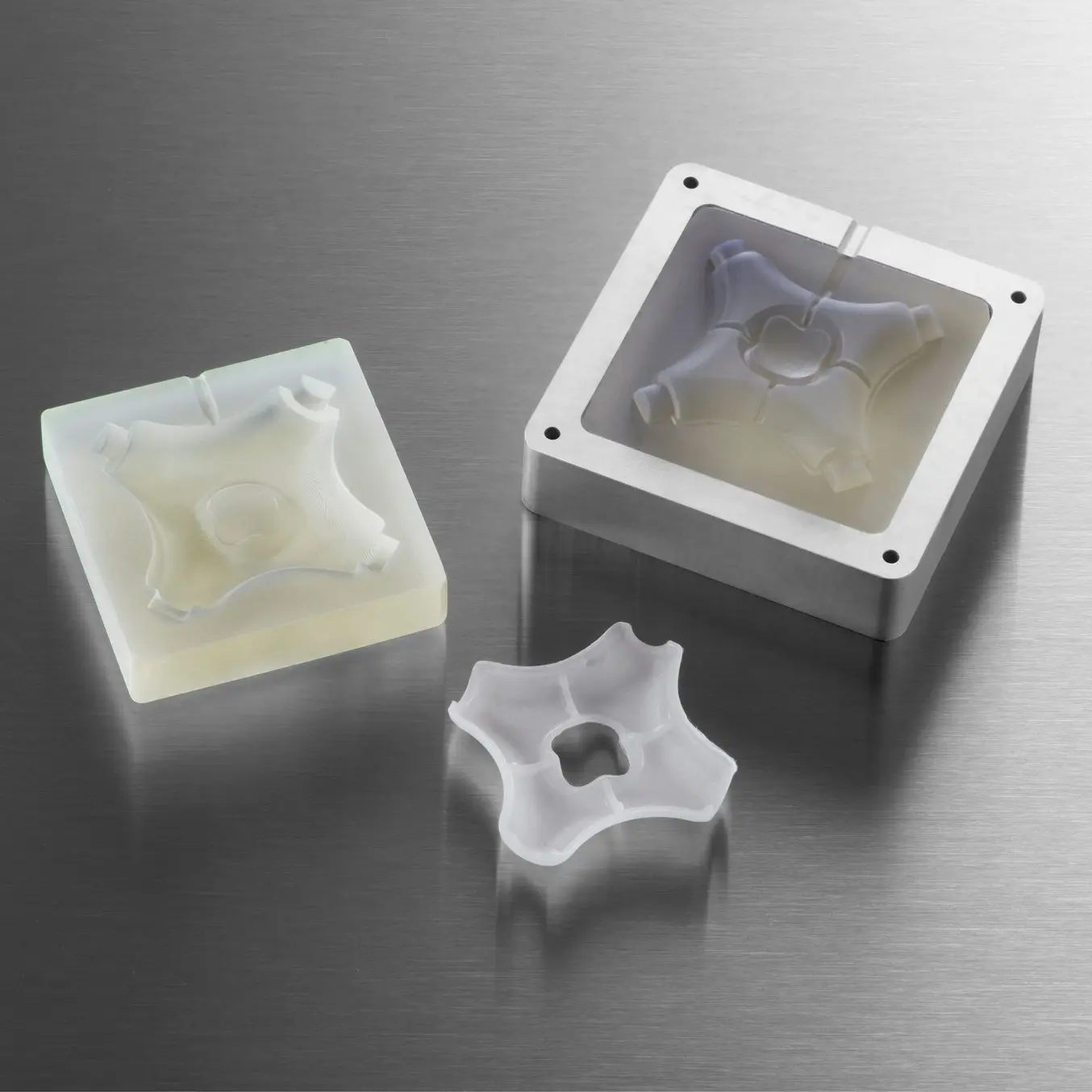
Realizzazione di stampi con la stampa 3D: tecniche di prototipazione e produzione
Scarica il nostro whitepaper per scoprire sei processi di stampaggio che si possono seguire con una stampante 3D SLA in-house, tra cui lo stampaggio a iniezione, la formatura sottovuoto, lo stampaggio in silicone e tanti altri.
Get Started With 3D Printing Thermoforming Molds
Combining 3D printed molds with thermoforming allows you to enhance the production process by improving its flexibility, agility, scalability, and cost-efficiency. Validate your design and material choice prior to transitioning to mass production and produce custom or limited series of end-use parts with thermoforming and 3D printed molds.
Download our white paper to learn more about the design guidelines, detailed workflows, forming process conditions, and real-life case studies with 3D printed thermoforming molds.