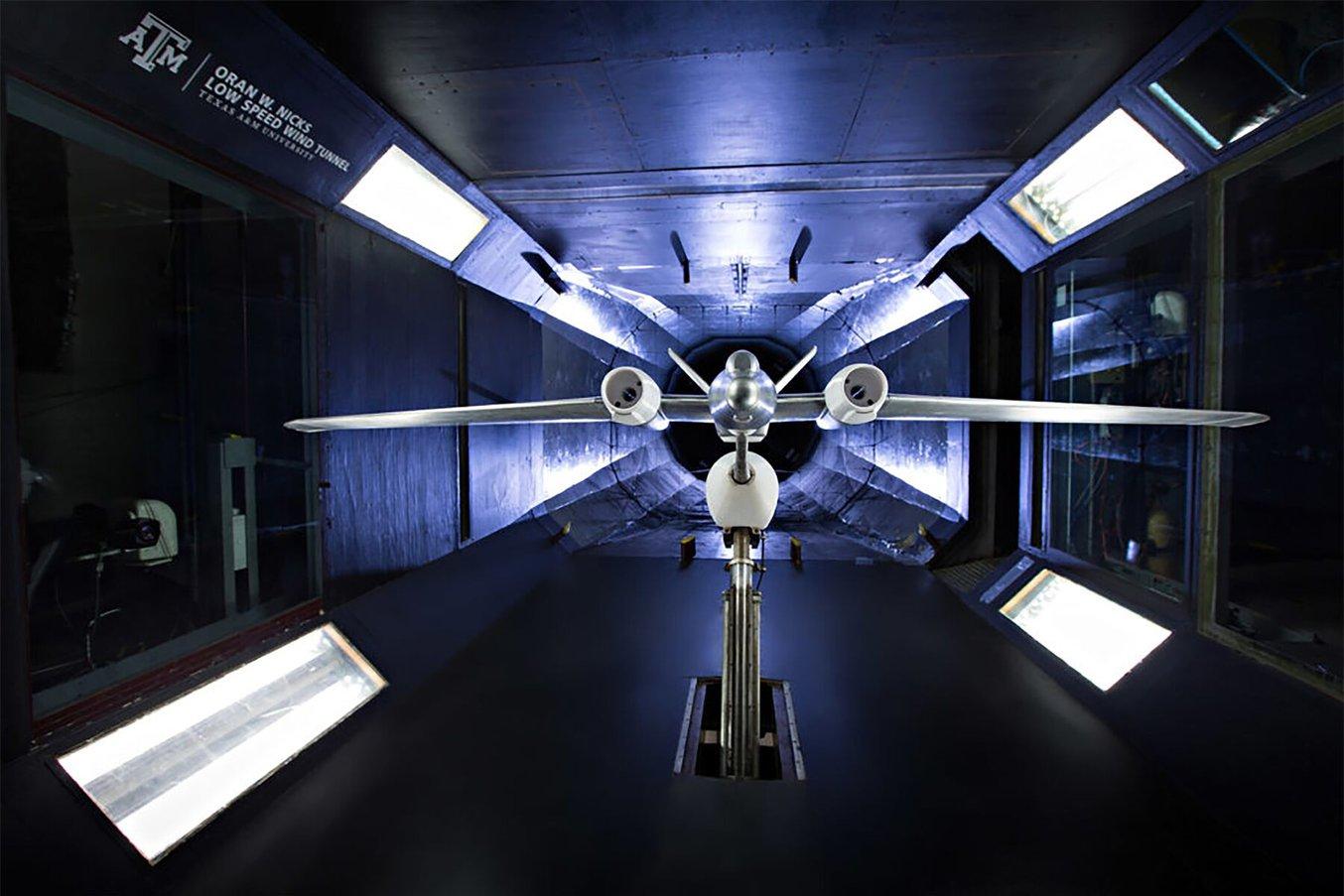
Additive manufacturing, also called 3D printing, has many applications in the aerospace industry, from design to manufacturing and beyond.
The aerospace industry was one of the earliest commercial adopters of 3D printing, or additive manufacturing, when it was invented. Indeed, many OEMs, suppliers, and government agencies have used 3D printing for decades already and the latest generations of commercial airplanes fly with 1000+ 3D printed parts.
However, traditional industrial 3D printers are prohibitively expensive for all but the largest and best-funded organizations. In the past 10 years, we’ve seen a dramatic decrease in the price of even high-performance 3D printers, and innovations in materials science that enable many higher-performance applications. When priced accessibly, 3D printers can now be used by smaller organizations—and in new branches of large organizations, where they previously would have been siloed away in centralized prototyping shops. By bringing additive technology to more end-users, Formlabs 3D printers are enabling more aerospace engineers and researchers to push forward the boundaries of their field.
Read on to find nine key ways 3D printing is powering innovation across the aerospace industry, from design to manufacturing and beyond.
3D Printing for Aerospace Product Development
1. 3D Printed Rapid Prototypes for Functional Rocket Testing
Gravity Industries is developing jet suits that look like they belong in a sci-fi movie. Their jet suits are intended to be used in cases like search & rescue where a helicopter can’t reach, or safely land. Using multiple kinds of 3D printing technology has accelerated their prototype and testing process, including some tests where thermoset photopolymer resin was the best choice available.
Sam Rogers, test pilot and lead designer, used parts made in Clear Resin on the Form 3 to develop the design for a vortex-cooled rocket engine igniter. The transparent material was great for the test environment, so Rogers could observe the combustion patterns on the interior of the test rig.
During the design tests, Rogers designed the chamber to be modular, so they could mix and match different versions of both the chamber and the nozzle. With a “shield of swirling oxygen” keeping the highest heat away from the chamber walls, the resin parts were able to last several seconds each. That was long enough, because each test firing only needed to be long enough to observe the ignition pattern.
If Rogers had gotten his dozens of different designs made in metal, it would have been enormously expensive. Instead, since the tests were short and the parts had very low material costs, he settled on a high-performance design with minimal expenditure and lead time.
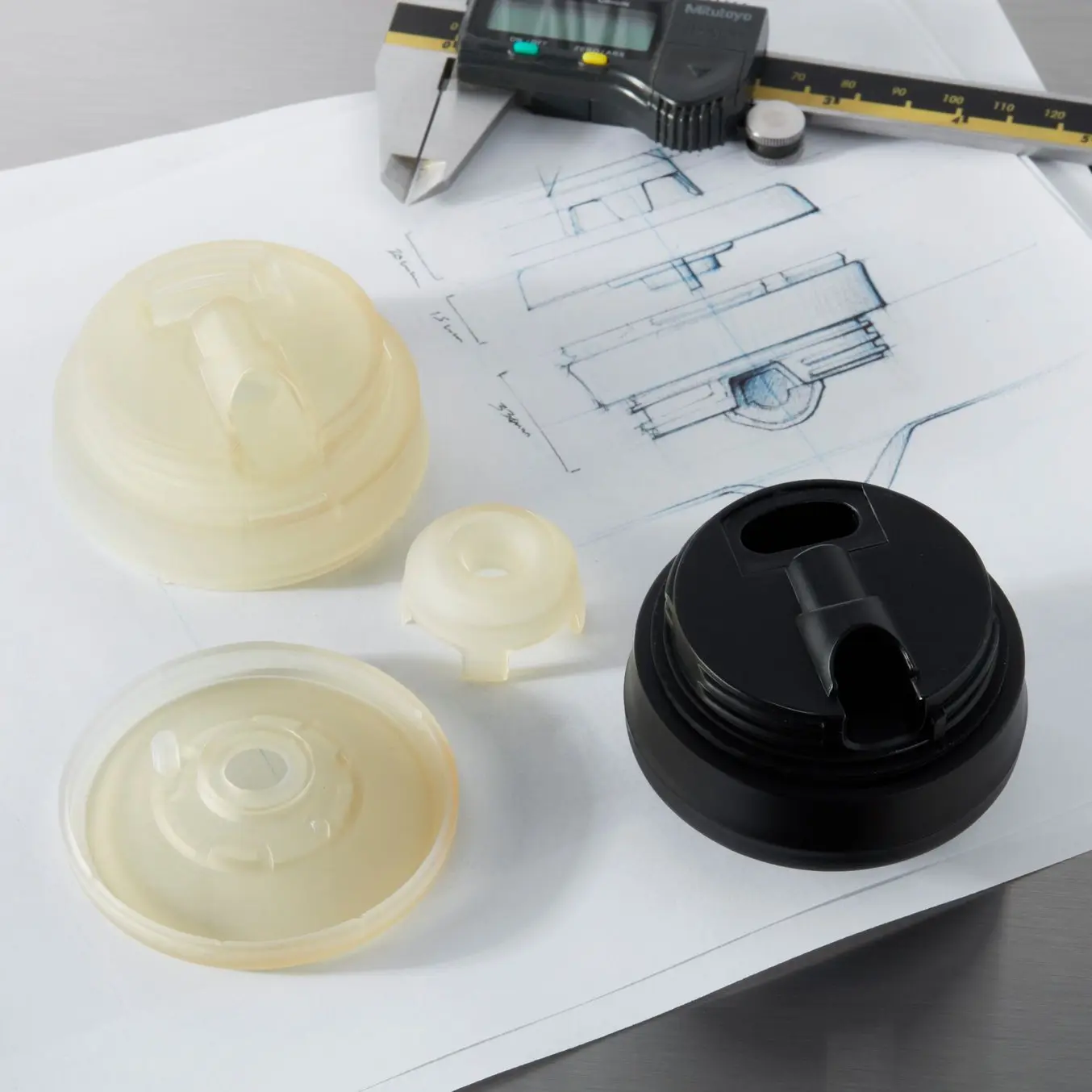
Guide to Rapid Prototyping for Product Development
In this guide, you’ll learn how rapid prototyping fits into the product development process, its applications, and what rapid prototyping tools are available to today’s product development teams.
2. Create Complex Rocket Parts With 3D Printing
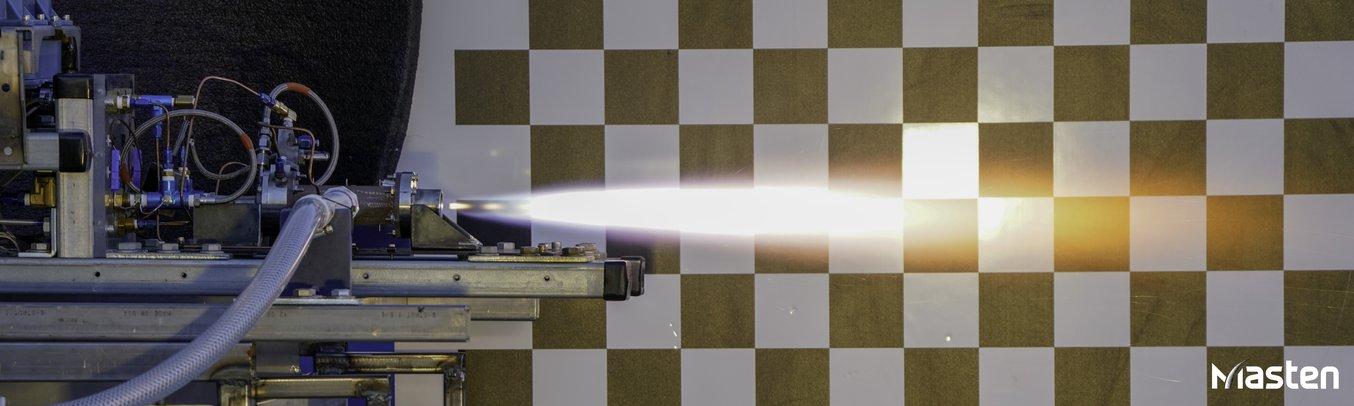
Masten Space Systems produces complex rocket parts using 3D printing.
Masten Space Systems specializes in vertical takeoff and vertical landing rocketry. Masten started 3D printing rocket engines in 2014, starting with small test thrusters and then eventually scaling up to a 25,000-pound thrust broadsword engine in 2016. Their additive experience includes both plastics and metals. According to Kimberly Devore, research and test engineer at Masten, the company has used both traditional machining and 3D printing to produce rocket engines. While Masten still uses some traditional manufacturing in their older engines, they’ve embraced 3D printing for design flexibility and production speed.
“What's nice about that [3D printing] is you can model it exactly the way you want it. And it doesn't require the same level of iterations over it as you would if you were doing traditional machining. Really, you can just design it the way you need it,” Devore said. “A lot of times, with traditional machining you probably need to make things pretty basic. Every single additional feature you add is an additional as just additional money that you're going to have to pay.”
With 3D printing, though, adding complexity to improve performance doesn’t cost extra—and neither does risk-taking. Since it’s relatively quick and inexpensive to make multiples, they are able to try new things. “Being able to rapidly iterate on that kind of stuff is huge.”
3. Prototyping Aerospace Tooling With 3D Printing
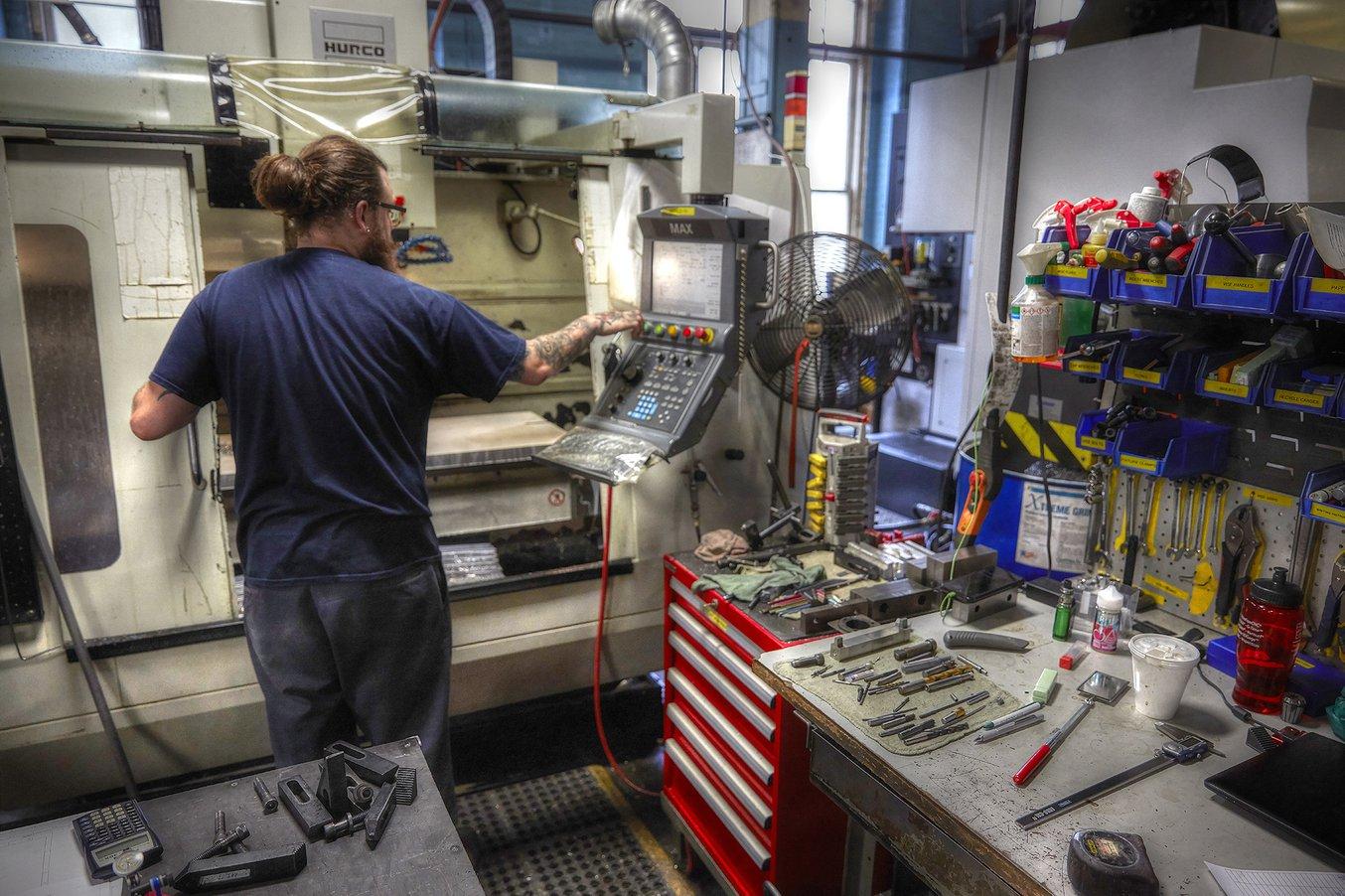
CNC machines take skill and time to program. If a part doesn’t need to be metal, 3D printing can be a practical tool for creating prototypes or production tools much faster and at a lower cost.
A&M Tool and Design produces parts and custom machines for aerospace, optics, and robotics. The shop has modernized over the years to introduce a range of new equipment, including 3D printing, in addition to reliable traditional technology and retrofitted solutions. Ryan Little, an A&M Tool mechanical engineer, researched which 3D printer would best match for their needs, and selected Formlabs 3D printers.
For prototyping, the shop started using 3D prints to test fit and function. 3D printing allows Little and the team to make parts much faster and utilize all hours of the day, setting up prints to run overnight and then using parts the next day. Printing is especially helpful for geometries that are costly and time-consuming to produce on a CNC machine.
“The printer almost feels like an auxiliary tool in addition to CAD,” Little said. “We do a ton of prototyping for different types of tooling. If we didn’t have the Form 2, many prototypes would just stay in CAD until we were ready to machine, and there would be some things that would never get made or designed because it wouldn't be practical.”
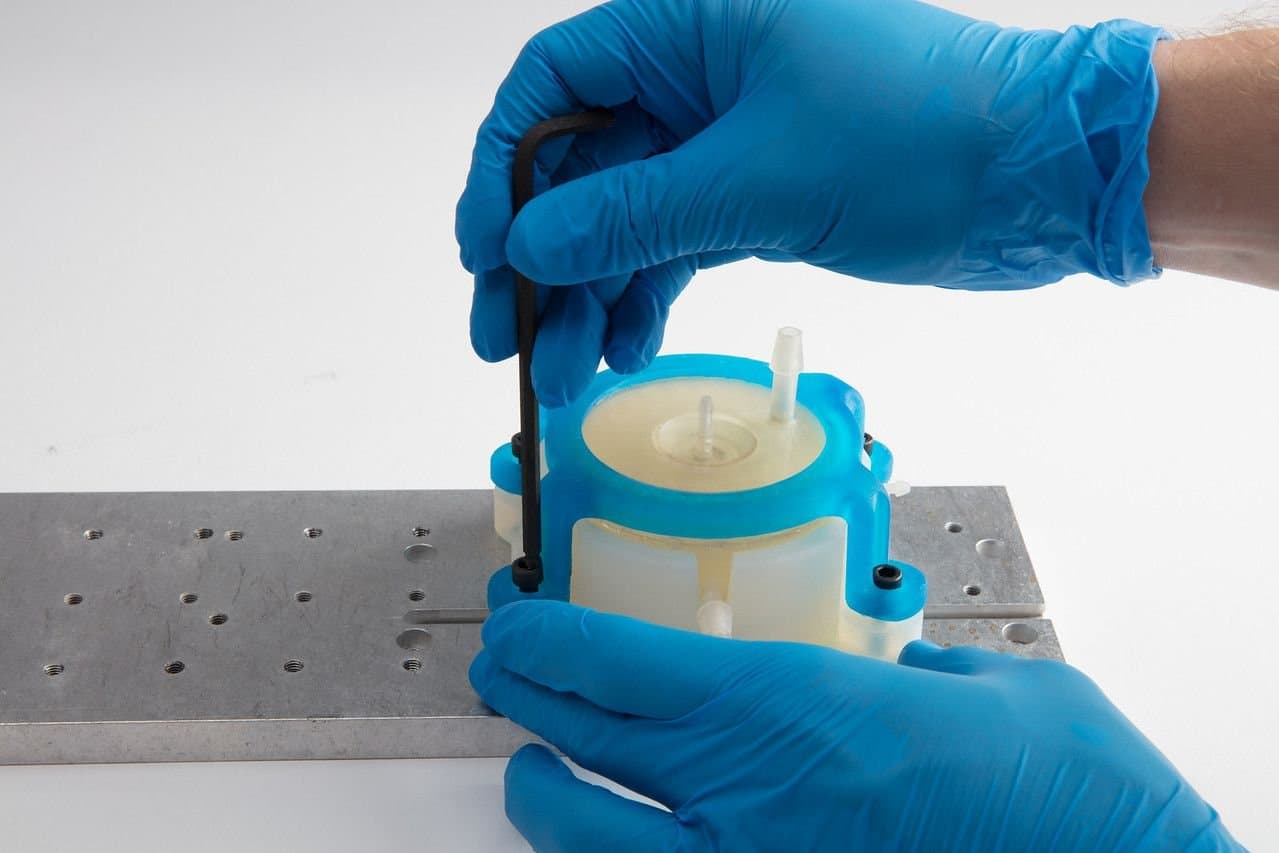
Designing Jigs & Fixtures with 3D Printing
For manufacturers, maximizing production speed while maintaining high part quality is critical for success. Jigs and fixtures are used to make manufacturing and assembly processes simpler, more reliable, and more efficient, reducing cycle times and at the same time improving worker safety.
3D Printing for Aerospace Manufacturing
4. Saving Money With 3D Printed Custom Tooling for Aircraft Parts
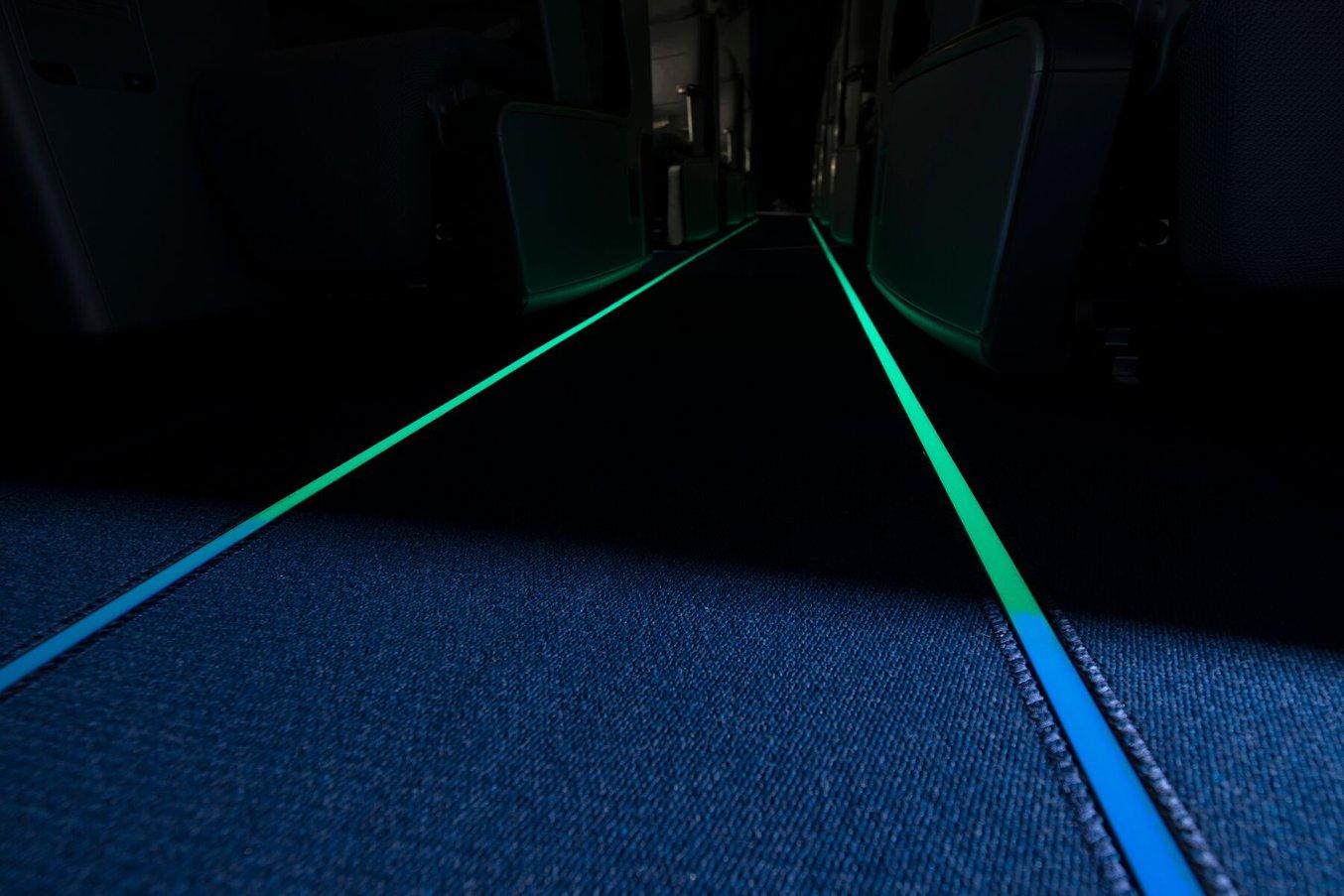
Lufthansa Technik 3D printed the extrusion nozzle to produce these self-luminous escape route markings.
Lufthansa Technik is one of the world’s largest aviation suppliers and maintenance, repair, and overhaul (MRO) providers. Their proprietary Guide U escape route markings are designed for aftermarket installation in aircraft cabins. These innovative floor markings are photoluminescent, which means they are equipped with self-luminous color pigments that are charged by normal cabin light and continue to glow in the dark in the event of an emergency without electricity.
Before production, several tooling materials and fabrication processes were tested. 3D printing custom extrusion nozzles was found to be the most cost-effective and flexible manufacturing method. “Theoretically, we could also injection mold our parts. But we would never have been so flexible in the shape and adjustment of the nozzle. That's where I see the great advantage of 3D printing," explains Ulrich Zarth, Guide U project engineer.
This production tool was printed on the Form 3L in cooperation with Formlabs partner myprintoo. The large area of the build platform in the Form 3L allowed 72 nozzles to be produced in a single print run. Several Formlabs materials were tested and the choice fell on Clear Resin which, in addition to offering the right stability and surface quality, also helps Lufthansa Technik constantly optimize its production process.
“If you want precise geometries, especially in the plastics sector, and you want them quickly, I would always use 3D printing.”
Ulrich Zarth, Project Engineer, Lufthansa Technik AG
Zarth and his team saved a tremendous amount of time and money in their production process by 3D printing this small component in-house. Compared to conventional methods for manufacturing tooling of this type, they were also able to avoid high minimum order quantities and remained significantly more flexible in their process optimization.
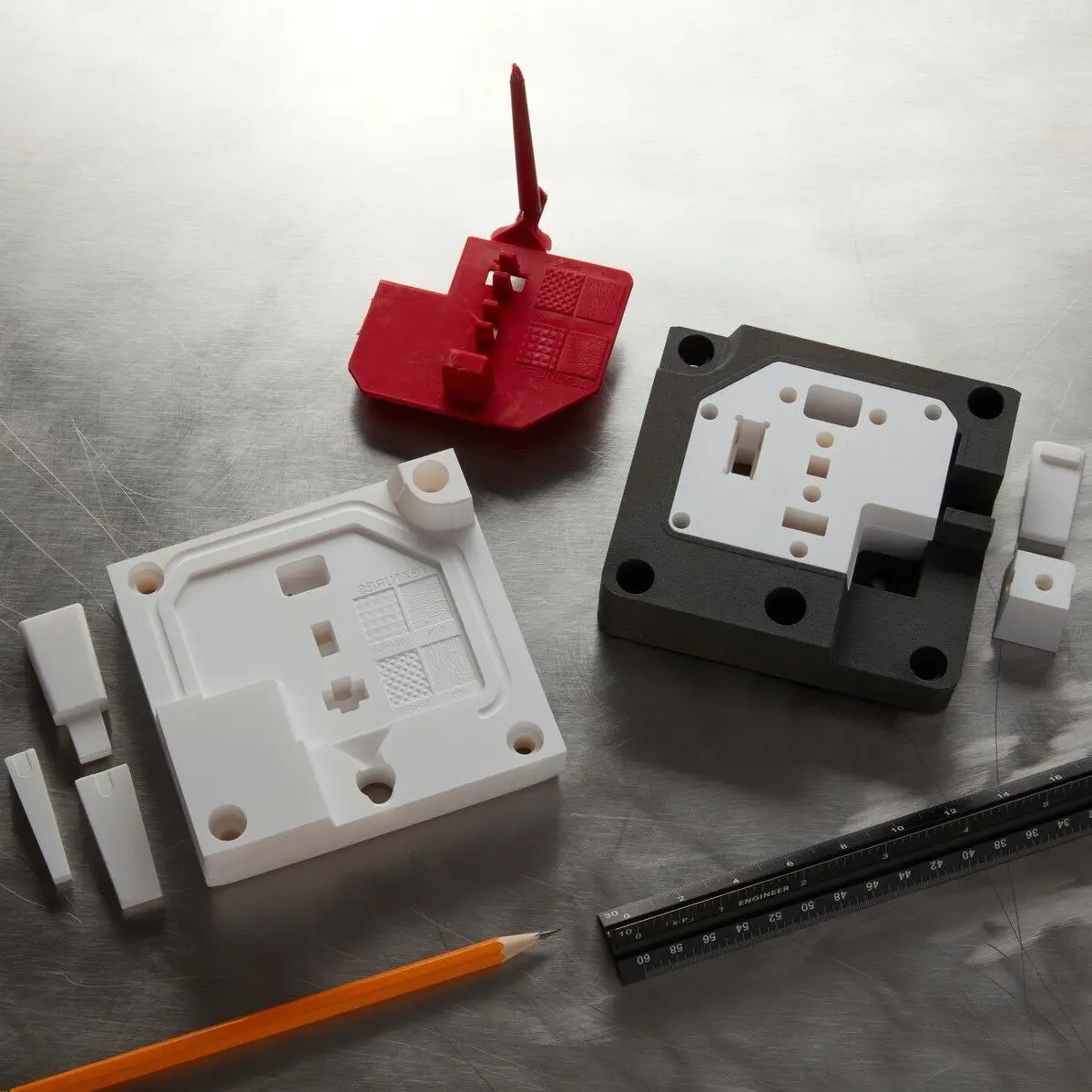
Guide to Rapid Tooling
In this white paper, learn how to combine rapid tooling with traditional manufacturing processes like injection molding, thermoforming, or casting.
5. Saving Time in Aerospace Manufacturing With 3D Printed Masking Jigs
The Integrated Manufacturing Group at AMRC works with industrial partners to bring together advanced technologies and develop integrated systems. The research group worked on a project for Airbus, Europe’s largest aerospace manufacturer, that involved high-tolerance drilling and machining of carbon fiber, aluminum, and titanium components. “After drilling one hole and moving onto the next hole, we needed to cover up the first one, so that any scrap that was generated didn't cross-contaminate the second hole,” said George Sleath, a project engineer at AMRC.
The team first tried to use an aluminum piece with a small rubber O-ring, but that wasn't solving the problem sufficiently. And there were two added wrinkles: the caps were needed in many sizes, and they had only ten days to source 500 caps in total in order to meet their deadline.
With such a short turnaround for custom products, virtually all other manufacturing options besides 3D printing would be unfeasible. Unsure at the time about AMRC’s in-house capabilities, Sleath requested quotes from three external printing bureaus, but the price quotes were expensive.
“I then spoke to Mark Cocking in our Design and Prototyping Group and asked if we could get anything manufactured in-house. I actually didn't hear back from him for 24 hours, but when I did he said, ‘Yeah, we've got half of them printed already.’ 250 of these drilling caps were manufactured in 24 hours, it was an astonishing turnaround,” Sleath said.
In the end, Cocking managed to get all of the components manufactured within two days, and the caps performed exactly as intended in the field. “The feedback that I got from the operators who were installing them was fantastic. The vast majority of the parts performed exactly as intended and none of them broke during operation,” Sleath said.
6. 3D Printed End-Use Aerospace Parts With Electroplating
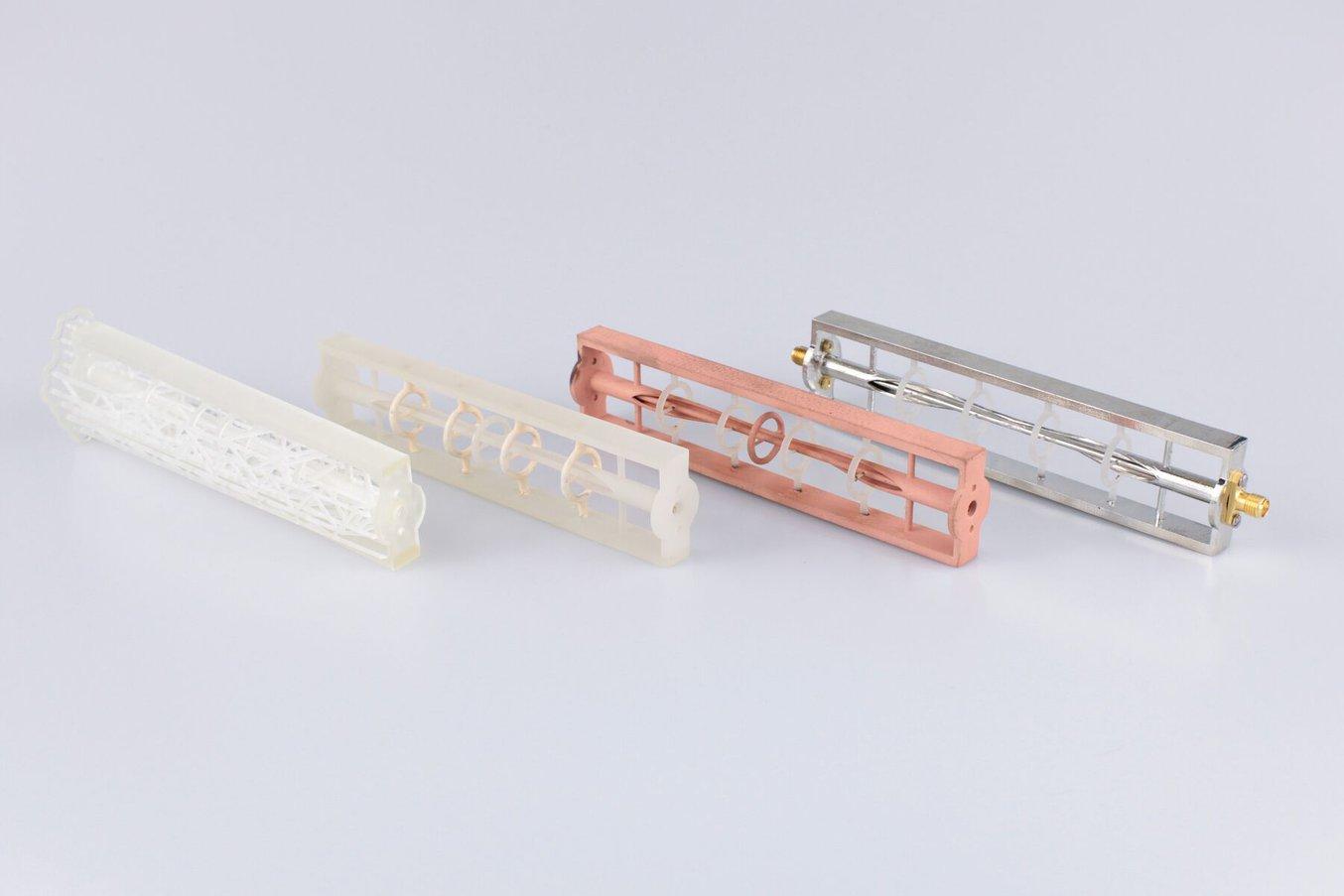
3D printing end-use parts allows Elliptika to create novel antenna designs faster and save money in the process.
Elliptika specializes in the design and development of radio frequency (RF) and microwave products and solutions. The company designs custom filters and antennas that are used for research and development in automotive, defense, medicine, and education. Radio frequency designers Gwendal Cochet and Alexandre Manchec need to achieve complex geometries, keep costs low, and deliver designs rapidly. To achieve these demanding parameters, they have learned to look beyond traditional manufacturing techniques.
Elliptika’s team has worked with different additive manufacturing processes and found stereolithography (SLA) 3D printing to be the best match for electroplating due to the smooth surfaces of the printed parts. "After 3D printing the part, we need to remove the support, clean its surface, and cure it. Then the printed part is put through a chemical process to plate a thin layer (about 3µm) of copper. Finally, the part can receive a surface finishing, for instance, a thicker layer of tin.”
Elliptika achieved a positive ROI on their Formlabs 3D printer with just two jobs. Getting a part made by an external supplier costs about 3000 EUR; the material and labor costs to 3D print and electroplate an antenna in-house costs only 20 EUR.
Their pace of work accelerated, too. With traditional manufacturing techniques, fabricating one antenna could take as long as three months. “With in-house 3D printing, we have working parts in two days. One day for printing, one day for plating, and it's working. So it's much, much shorter,” said Mr. Cochet.
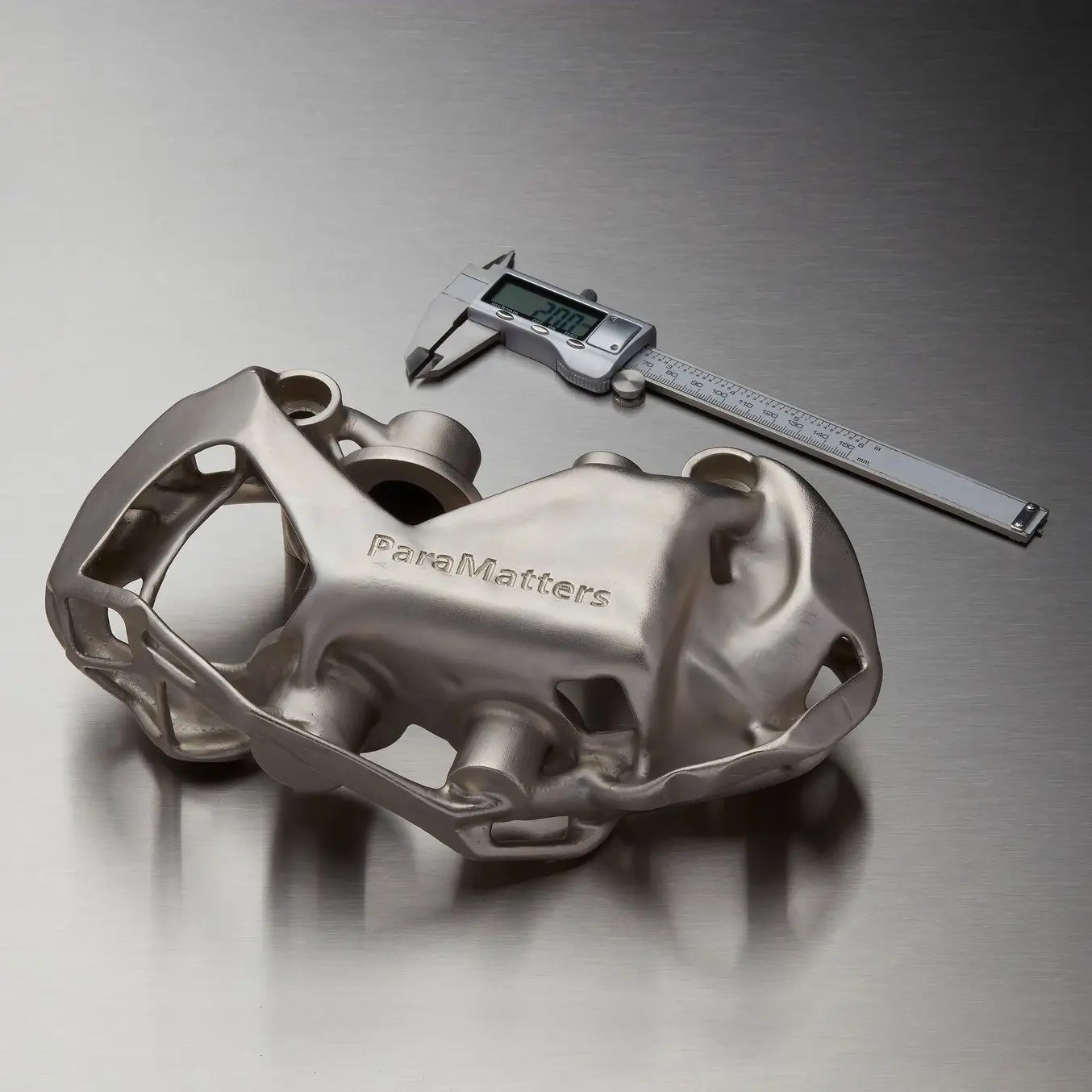
Strength from Metal: Strategies and Use Cases for Electroplating SLA Parts
Read on to learn how engineers are adding metal to resin 3D prints, and why hybrid metal parts can open doors to a surprising range of applications, including (but not limited to) end-use strength and durability.
3D Printing in Aerospace Research and Education
7. Testing 3D Printed Parts in Space
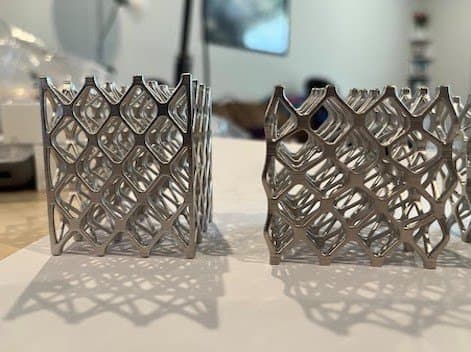
Pre-test electroplated Rigid 10K Resin lattice compression sample (left) and post-test samples (right) that were loaded from the top
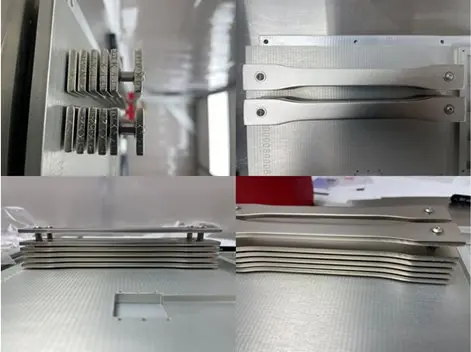
Electroplated Rigid 10K Resin 3D printed parts sent to the ISS.
NASA researchers are looking into how electroplated SLA parts perform in space. Engineers at NASA’s Goddard Space Flight Center designed brackets that were 3D printed on Formlabs printers, electroplated, and sent to space aboard a summer 2022 SpaceX commercial resupply services (CRS-25) mission to the International Space Station (ISS).
Using Alpha Space’s International Space Station test platform Materials International Space Station Experiment (MISSE-16), the samples will be exposed to the external environment of the space station and will later be returned to earth for further testing. The results could inform how NASA and possibly other aerospace manufacturers may incorporate electroplating and additive manufacturing into potential future product plans.
8. 3D Printed Wind Tunnel Test Parts
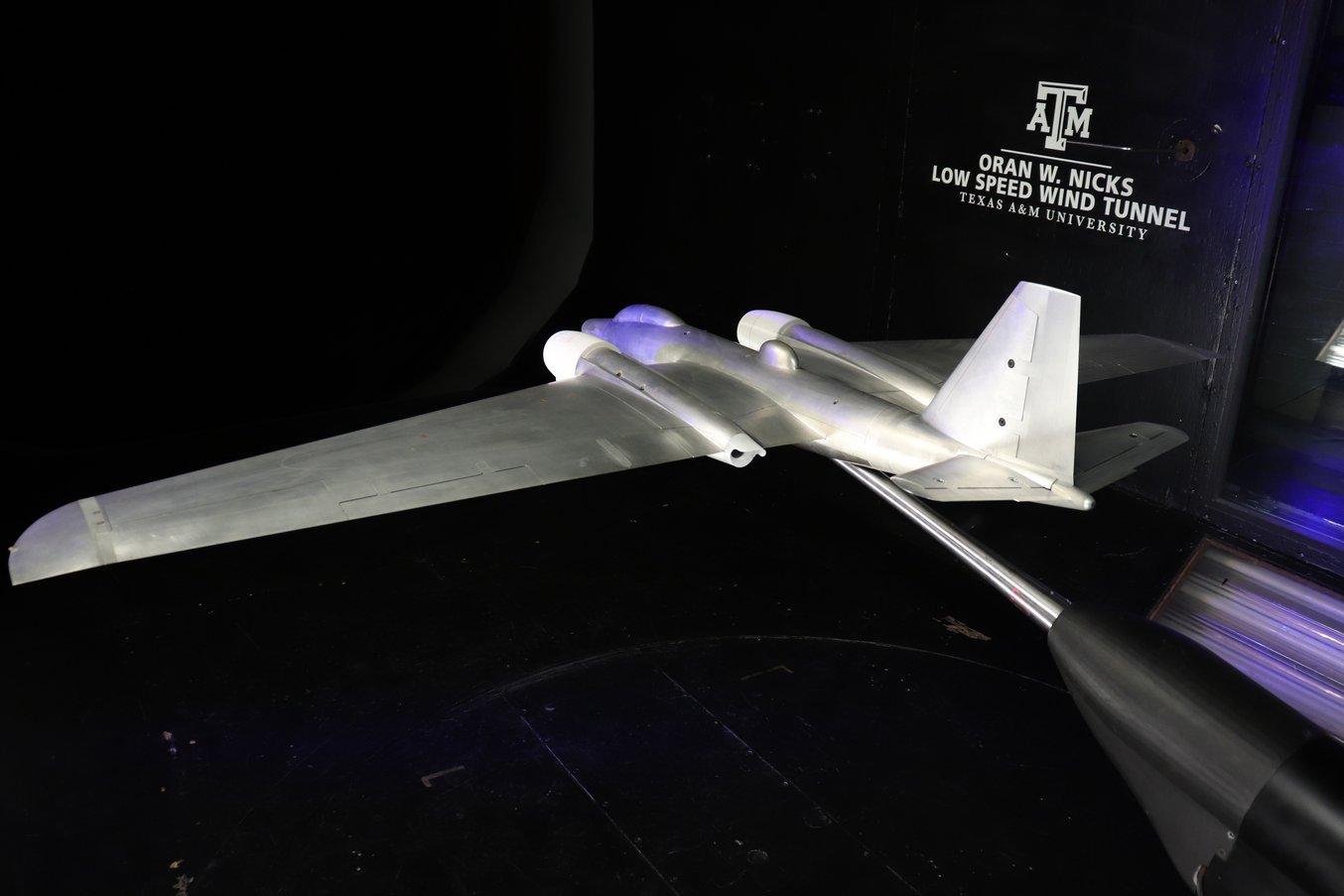
High-performance 3D printed components can be mounted on airplane scale models in a wind tunnel.
Faculty and students around the world are using Formlabs 3D printers in wind tunnel tests to inform their research.
The Texas A&M Oran W. Nicks Low Speed Wind Tunnel conducts wind tunnel testing for a wide range of projects. Lisa Brown, manager and engineer at the Texas A&M Wind Tunnel, helps researchers develop their test plans, design the models, and create the code that helps them collect relevant data. Her team uses 3D printing to create scale models to test a variety of objects.
Brown recalls a project where the team researched a flapping helicopter blade and incorporated 3D printing in the test. “If we go fast enough and the blades are flapping fast enough, you actually get shockwaves off the leading edge of those blades. And that's not what you want for helicopters. So we were actually able to see those shock waves happen in our low speed tunnel, which was really exciting,” Brown said. “We had a small printed insert to that leading edge with some sensors inside of it. So the whole model was an aluminum wing with this little insert that we could replace.”
To find out which material Brown chose and why, read our case study.
On the other side of the Atlantic Ocean, the Karlsruhe Institute of Technology (KIT)’s wind tunnel tests 3D printed parts, too. Doctoral student Lars von Deyn studies methods of predicting turbulent flows. His work has the potential to inform material and design choices to reduce friction in mobility.
To create his test parts, von Deyn looked to 3D printing. "I would like to examine structures that are very difficult to produce using machining processes," he says. He chose the Form 3L because the large build area meant he could cover the wind tunnel test area with fewer individual parts, and therefore fewer interruptions in the pattern.
Find the results of his experiments in our case study.
9. Training the Next Generation of Engineers With 3D Printing
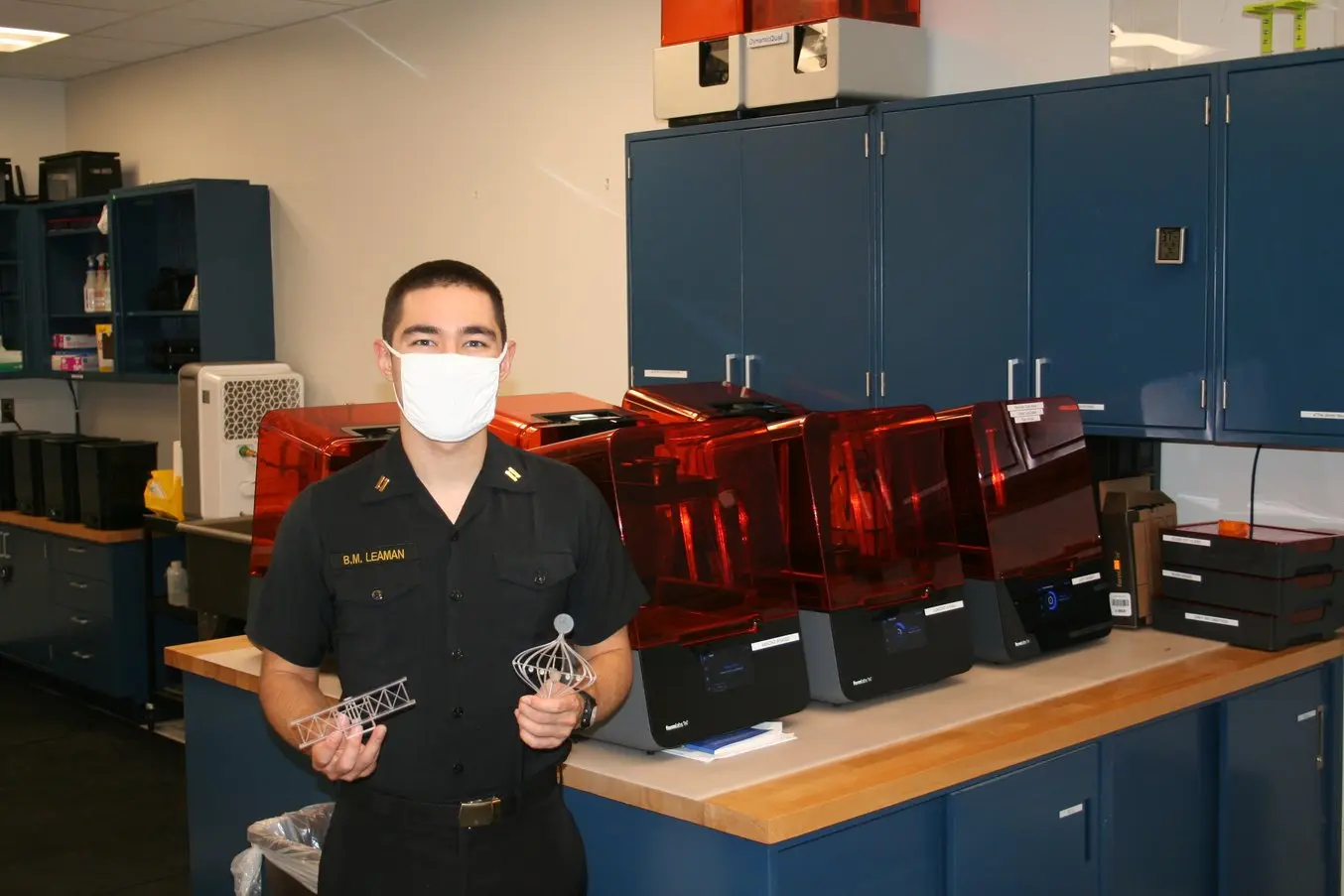
Midshipman 1/C Ben Leaman, a Naval Architecture major at USNA, showing his award winning prints using Formlabs Form 3 printers during an AM Olympics challenge in 2021.
The United States Naval Academy prepares young men and women to become professional officers in the U.S. Navy and Marine Corps. Captain Brad Baker, an Associate Professor at USNA, realized that his engineering students’ iterative process, and thus pace of learning, was impeded by a lack of access to manufacturing capabilities. Even with a machine shop dedicated to the students’ capstone projects, each individual or team wasn’t able to do more than three or four iterations over the course of a year.
Captain Baker wasn’t the first professor on campus to offer 3D printers to the students for their coursework, but he brought the design and manufacturing capabilities all under one centralized location when he started MakerSpaceUSNA. With just a couple of fused deposition modeling (FDM) printers to start, he began integrating the machines into the mechanical engineering curriculum and making the machines available to students completing their capstone projects.
When students enter the engineering curriculum, they first learn how to use CAD software, then how to operate FDM printers, then move to stereolithography (SLA), and finally work their way up to selective laser sintering (SLS) 3D printers. Now they even learn 3D scanning and can complete full reverse engineering projects using all the tools they have learned.
Having high-quality, reliable printers that use FDM, SLA, and SLS technologies allows MakerSpaceUSNA to provide every single USNA student experience with a wide variety of additive manufacturing technologies. Captain Baker’s philosophy of hands-on education and a learning-through-failure approach takes that exposure a step further for the engineering students, and prepares them for careers serving in the United States Navy and beyond.
What’s Next for 3D Printing in Aerospace?
With more powerful and accessible additive technologies than ever, the industry is poised for contributions to come from a wider range of contributors. It’s hard to say whether the biggest breakthroughs in the next 5-10 years will come from OEMs, suppliers, public agencies, startups, or academia, but with more people than ever getting hands-on with 3D printing, those innovations will come faster than ever before.
As the understanding of 3D printing continues to spread through the aerospace industry, and as the technology and available material base grow ever more versatile, additive technology will continue to reshape the way we build and maintain aircraft and spacecraft.