Jeden Tag werden Abertausende von Teilen mithilfe additiver Fertigung hergestellt. Im Laufe der Jahre sind Milliardenbeträge und zahllose Entwicklungsstunden in die Hardware geflossen, mit der diese Teile produziert werden. Das hat die Geräte zuverlässiger, genauer, schneller und besser denn je zur Fertigung komplexer, filigraner Geometrien fähig gemacht.
Doch die 3D-Drucker sind nur eine Seite der Medaille. Intelligente CAD-Programme und leistungsstarke 3D-Drucker erlauben es Unternehmen jeder Größenordnung, unfassbar detaillierte, individuelle Teile herzustellen – aber woraus bestehen diese Teile? Wozu eignen Sie sich? Die Materialeigenschaften der Druckteile sind ebenso wichtig wie ihre Form. Lange Zeit stand die Forschung an Materialien für die additive Fertigung jedoch an zweiter Stelle hinter der Hardware- und Software-Entwicklung. Drew Prindle von Digital Trends brachte dies auf den Punkt: „Die additive Fertigung war gefesselt durch eine mangelnde Vielfalt bei den Materialoptionen.“ Man könne zwar alles Mögliche drucken, fügte er hinzu, aber nur, solange es aus einfachem Kunststoff besteht.
Wir bei Formlabs haben eine andere Einstellung zu Materialien. Schon von Beginn an legen wir auf die bahnbrechende Materialwissenschaft, die immer mehr fortschrittliche Anwendungsbereiche eröffnet, genauso viel Wert wie auf unsere benutzerfreundlichen, professionellen Drucker. Tatsächlich ist der Stellenwert der Materialvielfalt mit der Zeit nur noch gestiegen. Mit einer Bibliothek von über 45 Materialien sind wir ebenso Materialhersteller wie Gerätehersteller, und darauf sind wir auch stolz.
Von elastisch und flexibel bis extrem steif, von flammhemmend bis statisch ableitend: Formlabs hat die Grenzen der additiven Fertigung mit seiner umfassenden Bibliothek leistungsstarker Materialien immer weiter ausgedehnt. Jetzt ebnen wir erneut den Weg für bisher unerschlossene kritische Anwendungsbereiche, mit zwei brandneuen, bahnbrechenden Formulierungen: Alumina 4N Resin und Silicone 40A Resin. Wenn Sie unseren Hauptsitz in Boston besuchen, begegnen Ihnen Dutzende Materialwissenschaftler*innen in Laborkitteln, die mit der Entwicklung der nächsten Generation fortschrittlicher 3D-Druckmaterialien beschäftigt sind. An Tagen wie diesem, wenn diese sorgfältig formulierten und unfassbar nützlichen Materialien auch für unsere Kunden erhältlich werden, ist es offensichtlich, dass wir viel mehr sind als nur ein Hardware-Entwickler – wir sind auch voll und ganz ein Materialunternehmen.
Die Bandbreite und die einzigartigen Eigenschaften dieser Materialien waren es, die unseren Kunden (mehr als 100 000 von ihnen!) dazu verholfen haben, Innovation, Effizienz und Leistung voranzutreiben. Wir sind unsäglich stolz auf unser materialwissenschaftliches Programm – deshalb möchten wir Ihnen heute einen Blick hinter die Kulissen gewähren.
Erfahren Sie im Folgenden mehr über:
- Die Geschichte der Materialentwicklung
- Die branchenführende Materialbibliothek
- Unser Team erstklassiger Materialwissenschaftler*innen
- Die vertikal integrierte Materialherstellung
- Pläne für noch mehr Materialflexibilität und Freiheiten für unsere Kunden
Die Demokratisierung des Zugangs zu industrieller Leistung
Schon vom ersten Tag an war die Materialentwicklung ein zentraler Teil unserer Mission. Zuerst konzentrierten wir uns auf Allzweckmaterialien, die schnell druckbar sind und in einer großen Bandbreite von Anwendungen gute Leistungen erbringen. Frühe Materialien wie unsere Allzweck-Kunstharze Clear Resin, Grey Resin, Black Resin und White Resin boten Kunden den perfekten Einblick darin, welche Möglichkeiten ein 3D-Drucker für den Desktop eröffnet. Als Produktentwickler und Hersteller unsere Produkte jedoch für mehr als nur Prototypen zu nutzen begannen, stellte sich unser Materialentwicklungsteam der Herausforderung und kreierte die ersten technischen Kunstharze, beispielsweise Flexible Resin, Tough Resin und Durable Resin. Jedes dieser Materialien wurde von Grund auf neu entwickelt und darauf ausgelegt, die kritischsten und häufigsten Anforderungen von Maschinenbau und Produktentwicklung zu erfüllen. Sie wurden so lange angepasst und ausgiebig getestet, bis gewährleistet war, dass sie sofort und jedes Mal funktionieren würden.
Diese Materialien gaben Früheinsteigern die Möglichkeit, zu Funktionstests und sogar zur Produktion von Endverbrauchsteilen überzugehen. Sie eröffneten Unternehmen die Chance, mehr und mehr Schritte ihres Arbeitsprozesses betriebsintern zu lösen, die zuvor ausgelagert wurden, sie verhalfen ihnen zu Innovationen und verdeutlichten auch uns, wie viele neue Möglichkeiten die Erweiterung unserer Materialbibliothek für unsere Kunden erschließt. Unternehmen, die bis dahin an (langsame, kostspielige und unflexible) konventionelle Fertigungsprozesse gebunden waren, erlangten plötzlich die Freiheit, die Kapazitäten des 3D-Drucks auszuschöpfen.
Als wir diesen Wandel beobachteten, legten wir deshalb umso mehr Fokus auf die Materialentwicklung und kurbelten unsere F&E an, um mehr Hochleistungsmaterialien zu kreieren.
Das breiteste Spektrum von Materialien
Zahlreiche Ingenieur-, Produktentwicklungs- und Designteams gehen Ihre Projekte inzwischen aus der Perspektive des 3D-Drucks an. Der 3D-Druck ist heute oft die Standardlösung für die Produktion, und hierbei spielt die Materialvielfalt eine Schlüsselrolle.
Immer mehr Kunden bauen in erster Linie aufgrund der Bandbreite der Materialoptionen auf Formlabs, wie zum Beispiel Labconco, ein Hersteller von Laborausrüstung. „Der Grund, weshalb wir den Form 3L gekauft haben, war, dass wir Zugriff auf die Kunstharz-Bibliothek von Formlabs haben wollten. Ich wusste, dass ich damit mehr Flexibilität erhalte und sie mir neue Möglichkeiten und Chancen eröffnen würde“, erzählt uns Brent Griffith, Produktentwickler bei Labconco.
Die Bibliothek von über 45 Materialien eröffnet zahllose Anwendungsbereiche, einschließlich sekundärer Fertigungstechniken wie 3D-gedrucktes Rapid Tooling für das Spritzgießen, Thermoformen und mehr. Die Möglichkeit, Spritzgussformen statt durch kostspieliges Fräsen von Metall mittels 3D-Druck aus Rigid 10K Resin zu fertigen, kann für viele Hersteller Kosteneinsparungen im Tausenderbereich bedeuten.
Im September 2023 veröffentlichte Formlabs ein Material aus reiner Keramik, Alumina 4N Resin. Damit wurden 3D-gedruckte Keramikkomponenten für die Luft- und Raumfahrt, die Automobilbranche und industrielle Gießprozesse zu einem 10-mal niedrigeren Preis erreichbar als mit führenden Alternativen. Mit einem erschwinglichen Desktop-3D-Drucker können Unternehmen jeder Größenordnung, von Ein-Personen-Beraterfirmen bis zu Großorganisationen wie NASA, auf eine Technologie zugreifen, die lange Zeit außer Reichweite war.
Silikon ist ein Material, das allen Ingenieur*innen und Herstellern nur allzu bekannt ist – es wird überall auf der Welt in Produkten verwendet, die wir tagtäglich benutzen. Im Bereich des 3D-Drucks war es bisher jedoch eine Rarität, denn es war nur auf wenigen unsagbar teuren und komplizierten 3D-Drucksystemen verfügbar. Basierend auf Formlabs' neuer, zum Patent angemeldeter Pure Silicone Technology™ ist Silicone 40A Resin das erste erschwingliche 3D-Druckmaterial aus 100 % Silikon. Kombiniert mit dem niedrigen Einstiegspreis und der Gestaltungsfreiheit der Kunstharz-3D-Drucker der Serie Form 3 für den Desktop macht dieses Material neue Wege für Innovationen und Kleinserienproduktion frei, die bisher für viele Hersteller unerreichbar waren.
In der Gesundheitsbranche, von der Orthopädie bis zur Dentalchirurgie, liegen die Eintrittsbarrieren des 3D-Drucks am höchsten. Jede Stufe im Lebenszyklus eines Produktes ist hier reguliert und muss einen Zulassungsprozess durchlaufen – aus gutem Grund. Angefangen bei unserem ersten Material mit Zulassung für intraorale Bohrschablonen, Dental SG Resin, bis hin zu Langzeitmaterialien wie Dental LT Comfort Resin, haben unsere biokompatiblen Materialien eine Anwendung nach der anderen eröffnet. Diese spezialisierten Materialien machen es Gesundheitsversorgern möglich, sich auf Ihre Arbeit zu fokussieren, ohne sich um die Sicherheit ihrer Produkte und Anwendungen sorgen zu müssen.
Investitionen in Forschung und Entwicklung
Um derartige Meilensteine zu erreichen, spart Formlabs nicht an Investitionen in die Materialentwicklung – da wir unsere Materialien in unserer Produktentwicklung und Produktion selbst einsetzen und eng mit unseren Kunden zusammenarbeiten, sind wir uns dessen im Klaren, dass Materialien den Schlüssel zum dauerhaften Erfolg bedeuten.
Ein Team von über 60 Chemieingenieuren und Entwicklern
Wer Materialien entwickeln will, die eine Branche revolutionieren, braucht die besten, klügsten Köpfe. Formlabs hat ein Team von über 40 Materialwissenschaftler*innen und Ingenieur*innen aufgebaut, das für die Erforschung, Entwicklung und Prüfung der Materialien zuständig ist, mit denen unsere 3D-Drucker für Desktop und Benchtop zu leistungsstarken Treibern der Innovation werden. Die geografische Nähe unseres Hauptsitzes zu Giganten der Forschung, Bildung und Fertigung wie MIT, Harvard und verschiedenen biowissenschaftlichen Instituten trägt zur Schaffung eines Umfelds bei, in dem führende innovative Geister zum Lernen, Kollaborieren und einander Herausfordern zusammenkommen.
Zusätzlich zu den 40 Chemieingenieur*innen, die an den Formulierungen neuer Materialien arbeiten, verfügt Formlabs über ein Team von 20 Fachleuten für die Optimierung der Druckeinstellungen, welche für ein reibungsloses Zusammenspiel von Druckern und Materialien sorgen. Vielen Herstellern gelingt die Entwicklung von Materialien, die im Labor unter perfekten Bedingungen die gewünschte Leistung erbringen. Doch Formlabs setzt alles daran, sicherzustellen, dass unsere Materialien auch im Praxiseinsatz und selbst unter extremen Bedingungen gleiche Leistungen erzielen.
Materialspezifische Einstellungen: Der Schlüssel zu einheitlichen Drucken
Werden 3D-Drucker und Materialien separat entwickelt, gibt es keinerlei Garantie, dass ein Material auf verschiedenen Druckermodellen unterschiedlicher Hersteller konsistente Ergebnisse liefert. Das hat zur Folge, dass Kunden oft selbst nach Lösungen für Probleme suchen und Online-Foren durchforsten müssen, um die besten Druckeinstellungen zu finden.
Es ist ein Alleinstellungsmerkmal von Formlabs in dieser Branche, dass ein eigens zuständiges Team die passenden Druckeinstellungen für jedes Druckermodell entwickelt und validiert, um die höchstmögliche Druckerfolgsrate zu gewährleisten und unseren Kunden die Mühe des Ausprobierens zu ersparen. Das ist der Schlüssel dazu, all unseren Kunden einheitliche Druckergebnisse zu bieten, egal ob sie eins oder 100 Teile pro Tag drucken.
„Es war uns von Anfang an wichtig, dass Formlabs einen zuverlässigen und leicht zugänglichen Druckprozess bietet. Für erfolgreiche Drucke zu sorgen, das beanspruchte gründliche Maschinenbauprozesse, innovative Materialentwicklungen und die Bereitstellung eines umfassenden Arbeitsprozesses für unsere Anwender.“
Max Lobovsky, Mitgründer und Geschäftsführer von Formlabs
Formlabs hat nicht nur in die Vergrößerung seines Teams investiert, sondern auch in die Weiterentwicklung der bestehenden Ingenieur- und Materialwissenschaftlerteams. Das Unternehmen steckt viel Mühe in die Kultivierung eines Innovationsgeistes, der alle Teammitglieder dazu anregt, die besten Leistungen abzuliefern. Und diese Mühe war nicht umsonst: Zu unserer großen Freude wurden wir 2023 als einer der besten Arbeitsplätze für Innovatoren weltweit ausgezeichnet. Indem wir ein hochmodernes Nasslabor unterhalten, das im Grundriss unseres Hauptsitzes eine entscheidende Position einnimmt, behalten wir die Materialentwicklung stets direkt vor Augen.
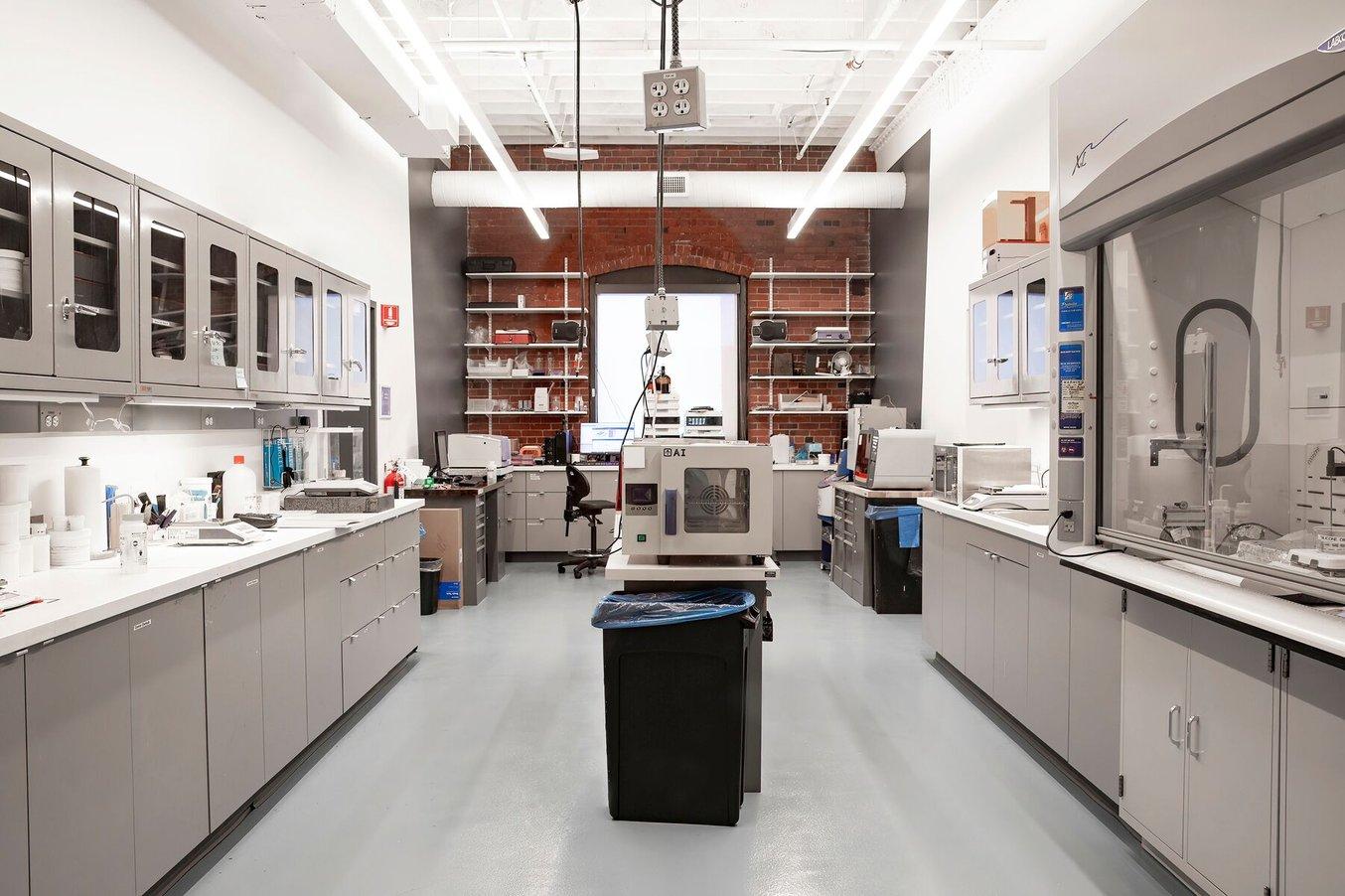
Die Kontrolle einer wachsenden Lieferkette für Materialien
Auch wenn Innovationen ihren Anfang im Labor nehmen, müssen sie durch jede Phase des Fertigungsprozesses geführt werden, damit garantiert ist, dass die in unseren Laboren validierten mechanischen Eigenschaften auch von unseren Kunden in ihren Produktionsprozessen erzielt werden können. Unser Fokus auf Qualität und Zuverlässigkeit beschränkt sich nicht allein auf unsere Drucker – wir gehen bis zum letzten Tropfen unserer Materialien mit derselben Sorgfalt vor. Das bedeutet, dass wir uns bei der Herstellung unserer Materialien auf unsere eigenen Qualitätsstandards und Betriebsabläufe verlassen.
Genau aus diesem Grund haben wir uns für die vertikale Integration entschieden und eines der besten Materialherstellungsunternehmen der Welt gekauft, um sicherzustellen, dass unsere Materialien unseren außerordentlich strengen Ansprüchen entsprechen.
Formlabs Ohio
Formlabs übernahm zu diesem Zweck seinen langzeitigen Partner Spectra und brachte so die Materialentwicklung unter sein Dach, was einen effizienteren Prozess von der Validierung bis zum Vertrieb ermöglichte. Die nun als Teil von Formlabs Ohio fungierende Einrichtung ist nicht nur für die Herstellung unserer Materialien zuständig, sondern druckt auch Tausende von Probeteilen pro Woche und dient damit als einer unserer besten Anwendungsfälle für den 3D-Druck mittlerer bis großer Stückzahlen, und das aus jedem unserer über 45 Materialien.
„Die meisten 3D-Druck-Unternehmen sind nicht vertikal integriert und haben keinen Zugriff auf ihre eigene Kunstharzproduktion. Wir glauben jedoch, dass das Material ein entscheidender Faktor bei der Erschließung neuer Anwendungen und Arbeitsabläufe ist und dazu beiträgt, Industriezweige zu revolutionieren.“
Max Lobovsky, Mitgründer und Geschäftsführer von Formlabs
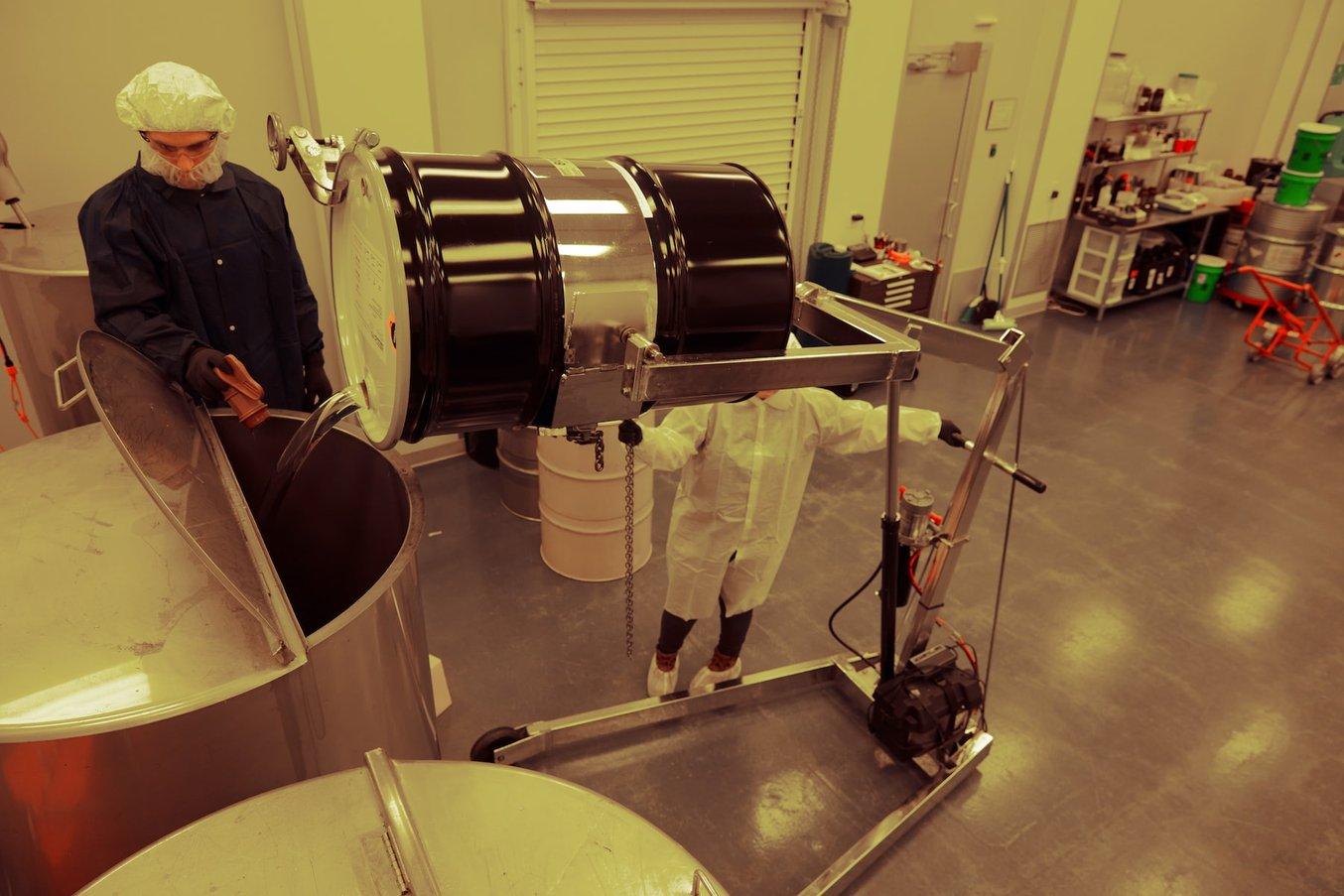
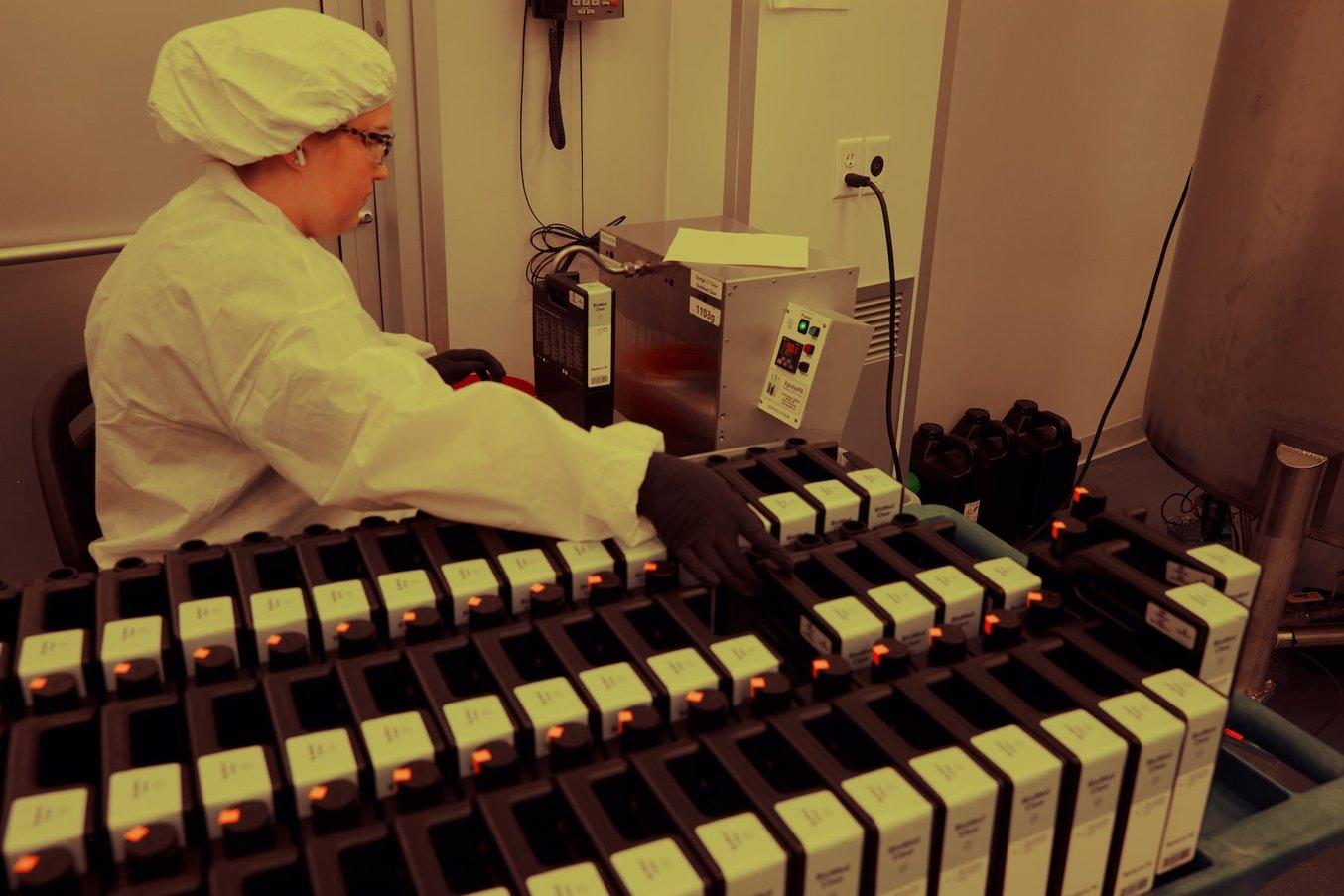
Einige dieser Materialien haben bestimmte Anforderungen, die einen Effekt auf Arbeitsprozesse in der Endverwendung ausüben. Unsere biokompatiblen Materialien haben im vergangenen Jahrzehnt zahlreichen medizinischen Fachleuten dazu verholfen, ihr Behandlungsniveau durch die Digitalisierung ihrer Prozesse zu verbessern. Kunstharze (auch Resins genannt), die für die intraorale Anwendung, den Kontakt mit Schleimhäuten, die Anwendung auf der Haut, mittel- bis langzeitige Implantationen und die intraorale Endanwendung (z. B. zahnmedizinische Bohrschablonen) zugelassen sind, tragen alle zur Verbesserung der Behandlungsergebnisse bei, indem sie die Kosten für Gesundheitsversorger und Behandelte gleichermaßen reduzieren und traditionelle Arbeitsprozesse effizienter machen, die zuvor oft tagelange manuelle Arbeiten erforderten.
Unsere biokompatiblen Materialien werden von Anfang bis Ende in einer vollkommen regulierten Umgebung produziert, damit unsere Kunden (und ihre Patient*innen) auf die Sicherheit ihrer Prozesse und die Übereinstimmung mit behördlichen Vorschriften vertrauen können. Um diese Produkte durchgehend und sicher in hohen Stückzahlen herstellen zu können, hat Formlabs Zeit und Mühe darin investiert, seine Einrichtung nach ISO 13485 für die Entwicklung medizinischer Materialien zertifizieren zu lassen und einen nach ISO Klasse 8 zertifizierten Reinraum für Experimente aufzubauen.
Der Aufwand, die regulatorische Seite unserer Materialproduktion auszubauen, machte sich während der COVID-19-Pandemie bezahlt. Dank eines bereits zugelassenen und zertifizierten Arbeitsprozesses war Formlabs in Kooperation mit der University of South Florida und Northwell Health in der Lage, seine Fertigung schnell auf die Massenproduktion von Millionen von Nasen-Rachen-Abstrichtupfern umzustellen, um auf den landesweiten Mangel an Testtupfern zu reagieren.
Direkt von der Quelle: Kooperation mit Fachleuten für Spezialformulierungen
Bei der Entwicklung neuer Materialien und dem Iterieren bestehender Materialien arbeitet unser Team eng mit unseren Kunden zusammen, um neue Tätigkeitsbereiche ausfindig zu machen. Diese Art der Kollaboration wird mit der weitläufigeren Implementierung des 3D-Drucks nur weiter an Bedeutung gewinnen. Für viele ist es nicht der Gerätepreis, der eine Einstiegsbarriere darstellt – sondern der Bedarf nach einem spezialisierten Material.
Unternehmen, denen es lediglich auf die Gestaltungsfreiheit oder die internen Fertigungskapazitäten des 3D-Drucks ankommt, haben diesen bereits integriert; bei den noch unschlüssigen Unternehmen handelt es sich um jene, die bisher nicht verfügbare Hochleistungsmaterialien benötigen. Während die gesamte Branche danach strebt, ihren Marktanteil zu erhöhen und Kunden dazuzugewinnen, kann sich Formlabs auf mehr als ein Jahrzehnt der Erfahrung mit bewährten Prozessen stützen, um Anwendungsfälle zu identifizieren und in enger Zusammenarbeit mit Fachleuten die perfekten Formulierungen zu entwickeln.
Brandneue Materialien wie Silicone 40A Resin und Alumina 4N Resin sowie bereits früher veröffentlichte Materialien wie die Polyurethan-Kunstharze demonstrieren Formlabs' Erfolgsgeschichte bei der Entwicklung spezialisierter Formulierungen für anspruchsvolle Industriezweige und Hochleistungsanwendungen. Unser Materialteam stellt ausgiebige Forschungen an, um die für unsere Kundschaft entscheidendsten mechanischen und ästhetischen Eigenschaften zu bestimmen.
Erhöhte Flexibilität und Freiheit
Formlabs widmet der Entwicklung seiner firmeneigenen Kunstharze viel Überlegung (und Forschungsarbeit), damit diese so zuverlässig und effektiv wie möglich sind. Wir wissen jedoch auch, dass einige unserer Kunden sich möglichst viel Freiheit zum Testen neuer Anwendungen, Erproben neuer Produktionstechniken und mehr wünschen. Deshalb haben wir neue Möglichkeiten geschaffen, das Ecosystem von Formlabs so vielseitig wie möglich zu gestalten.
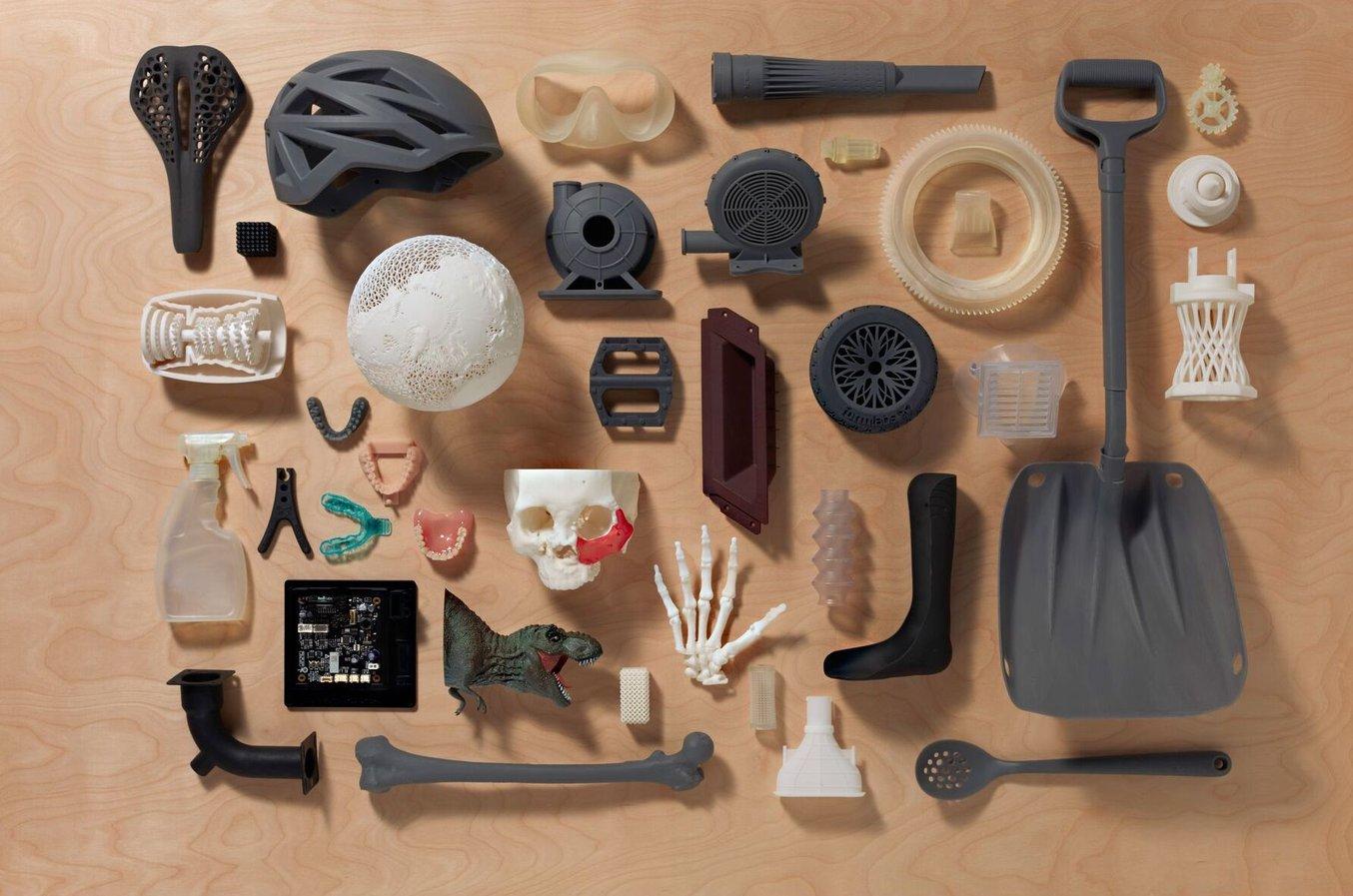
Dies haben wir durch die Einführung des Open Material Mode vor Kurzem verwirklicht – eine neue Möglichkeit für Formlabs-Kunden, ihre Materialoptionen zu erweitern. Damit ist es nun möglich, für eine benutzerdefinierte Druckleistung die Druckeinstellungen individuell anzupassen. Außerdem können Formlabs-Kunden auf eine Auswahl leistungsstarker Materialien von erstklassigen Drittanbietern zurückgreifen. Der Open Material Mode bietet fortgeschrittenen Anwender*innen die Freiheit, auf den zuverlässigen 3D-Druckern von Formlabs mit jedem beliebigen Photopolymer-Kunstharz von Drittanbietern zu drucken, das bei 405 nm aushärtet. Die neuen Materialien, die durch den Open Material Mode verfügbar werden, können die speziellen Anforderungen bestimmter Branchen erfüllen oder individuelle Eigenschaften bieten.
Wir sind unglaublich stolz auf die Materialien, die wir entwickelt haben, freuen uns aber auch, der Formlabs-Community mehr Freiheiten gewähren zu können, ihre Projekte selbst in die Hand zu nehmen.
Der Blick in die Zukunft
Indem Formlabs der Entwicklung neuer Kunstharze für die Stereolithografie (SLA) und Pulver für das selektive Lasersintern (SLS) viele Anstrengungen und Investitionen gewidmet hat, ist das Unternehmen zum weltweit marktführenden Hersteller professioneller 3D-Drucker dieser Technologien geworden. Im Hinblick auf die Zukunft unserer Branche sind wir überzeugt, dass die kontinuierliche Ausweitung des Materialangebots ein treibender Faktor der nächsten industriellen Revolution sein wird.