„Oft entspringen Ideen daraus, dass man das volle Potenzial einer Technologien kennenlernt, die man täglich verwendet. Hätten wir keinen Zugang zu 3D-Druckern, wäre der NOVA Foot gar nicht erst kreiert worden. Erst durch die Arbeit mit dem Fuse 1+ 30W kam mir der Gedanke, eine wirklich funktionale und für jeden zugängliche Prothese zu erschaffen, die den Alltag von Amputierten revolutionieren würde.“
Marco Garano, Geschäftsführer, C.P.T.
Der NOVA Foot ist ein individualisierter Prothesenfuß mit hoher Energierückgabe, der in sechs Größen erhältlich ist. Der von Marco Garano, Geschäftsführer von C.P.T. (Custom Precision Technology), entwickelte NOVA Foot wurde mit Formlabs-3D-Druckern prototypisiert, getestet und nun produziert. Ohne den Zugang zum 3D-Druck gäbe es diese Prothese nicht, da jede andere Art der Fertigung zu kostspielig und ineffizient gewesen wäre. NOVA Foot wird von Protosystem vertrieben, einem Tochterunternehmen von C.P.T., das mit dem Ziel gegründet wurde, funktionale und zugängliche Orthopädieprodukte bereitzustellen.
„Dank des 3D-Drucks, mit dem wir die Fertigungskosten erheblich senken konnten, ist NOVA Foot für alle Fußamputierten in Italien zugänglich und wird vollständig von der gesetzlichen Krankenkasse übernommen.“
Valentina Garano, Leiterin Vertrieb und Marketing, Protosystem
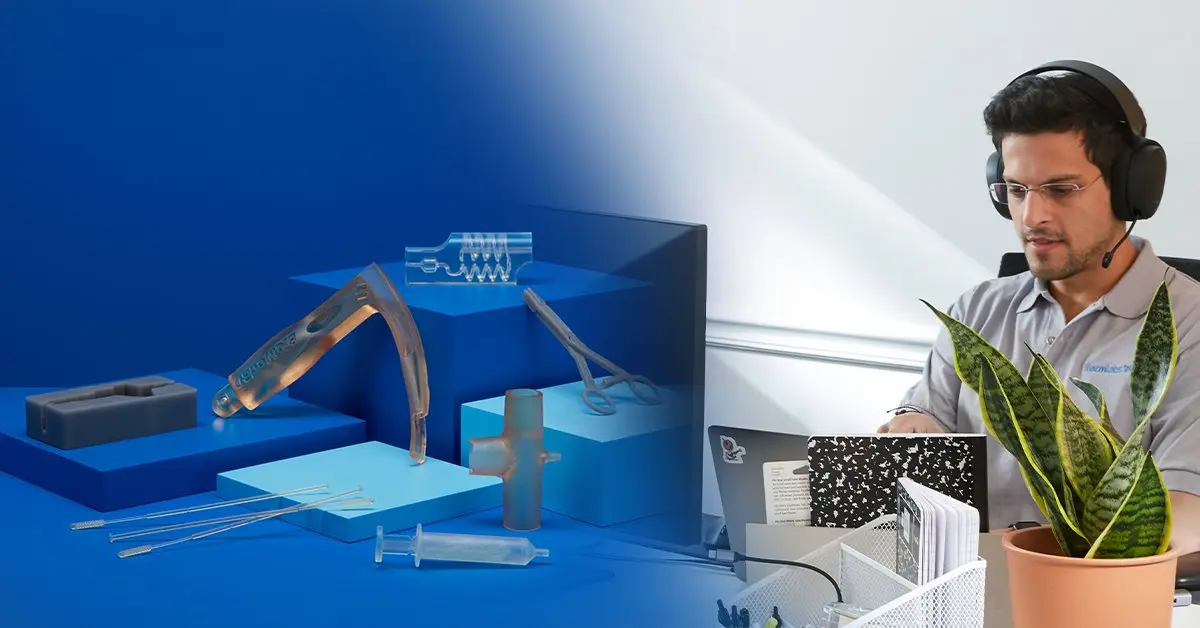
Kontakt zum Vertriebsteam von Formlabs Medical
Ob Sie patientenspezifische chirurgische Instrumente erstellen möchten oder Prototypen kardiologischer Medizinprodukte anfertigen: Wir stehen Ihnen zur Seite. Hinter Formlabs Medical steht ein engagiertes Spezialistenteam, das Sie und Ihr Unternehmen bei Bedarf mit professioneller Hilfe unterstützt.
NOVA Foot: Anpassbar für verbesserten Komfort
Die meisten Fußprothesen verlangen Patient*innen viel Anpassungvermögen ab. Mit dem Nova Foot war das Ziel, die Prothese stattdessen an den Patienten anzupassen und ihm beim täglichen Gebrauch Komfort und Stabilität zu garantieren.
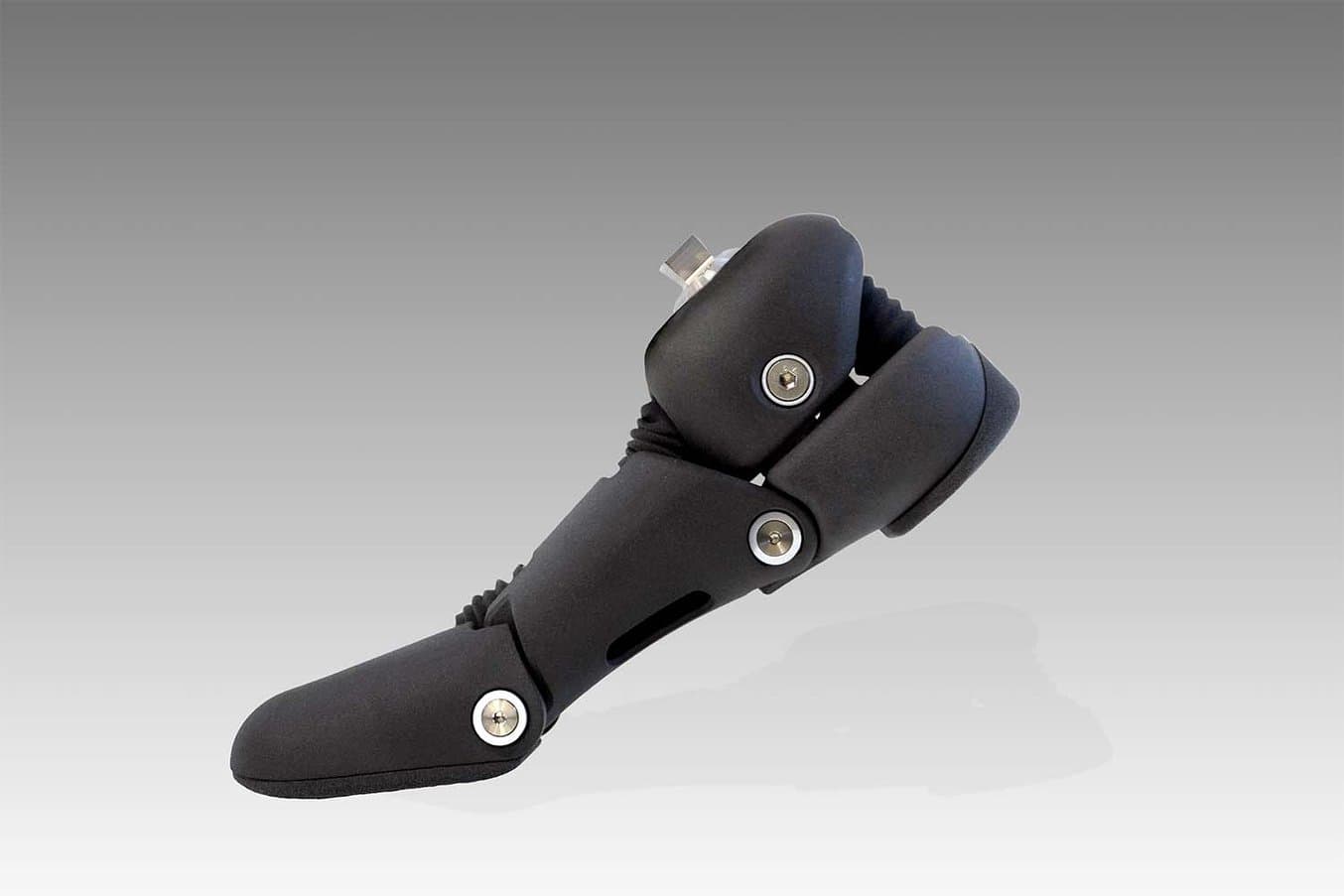
Der NOVA Foot wird mit 3D-Druck auf Formlabs' Fuse 1+ 30W produziert, wobei zusätzliche Bauteile auf dem Form 3B+ gedruckt werden.
Der NOVA Foot besteht aus mehreren Abschnitten für den Vorfuß, den Mittelfuß, die Ferse und den Knöchel. Jedes Segment kann an die individuellen Patientenbedürfnisse angepasst werden Diese hochgradig individualisierbaren Teile werden mit selektivem Lasersintern (SLS) auf dem 3D-Drucker Fuse 1+ 30W hergestellt. Zusätzliche Sohlen im Zehen- und Fersenbereich, die ebenfalls auf dem Fuse 1+ 30W gedruckt werden, sind absolut wasserfest und bieten Halt und Stabilität in nasser Umgebung, wie etwa in der Dusche.
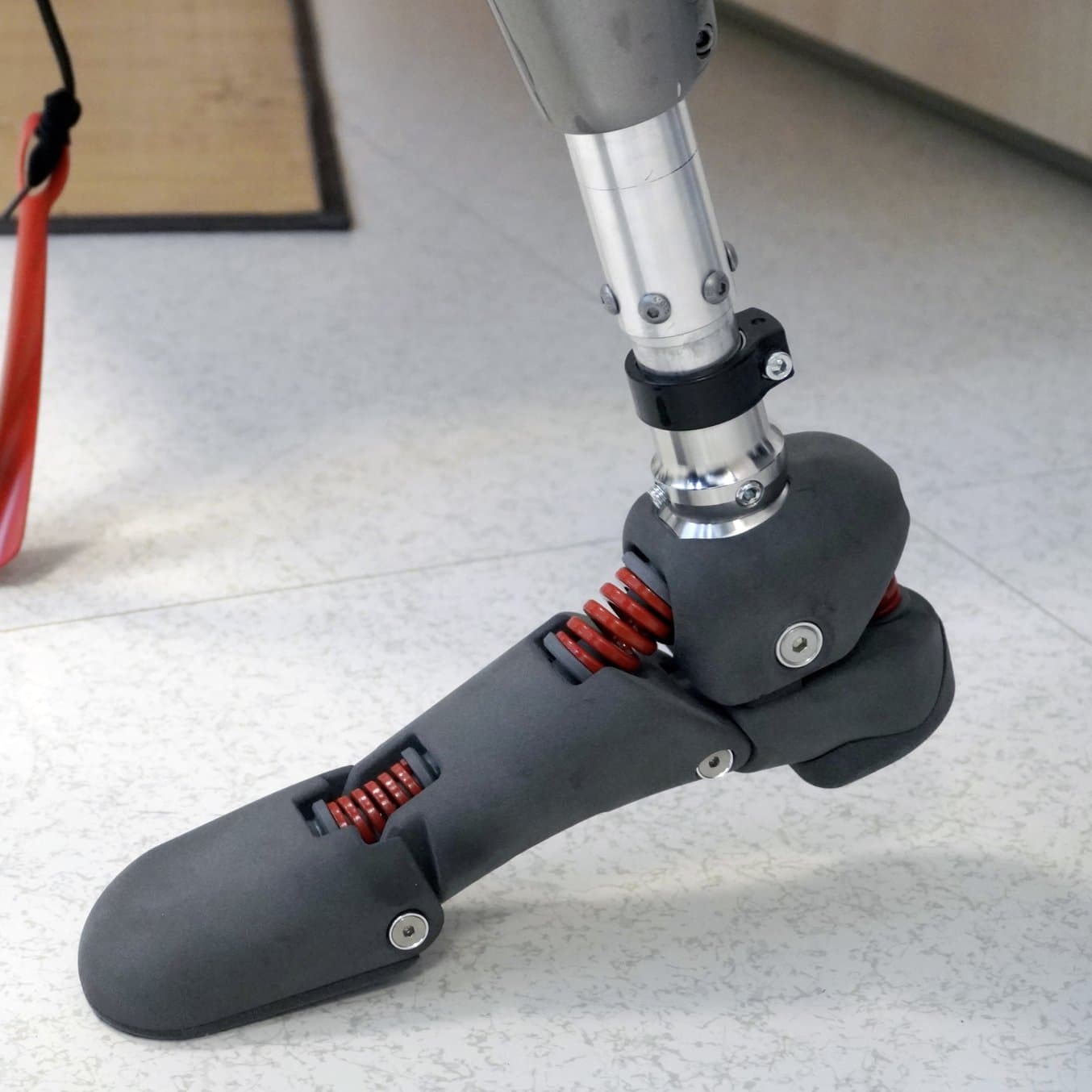
Die Federn im NOVA Foot, hier in Rot, können gegen weichere oder steifere Federn ausgetauscht werden, um die Reaktion des NOVA Foot anzupassen.
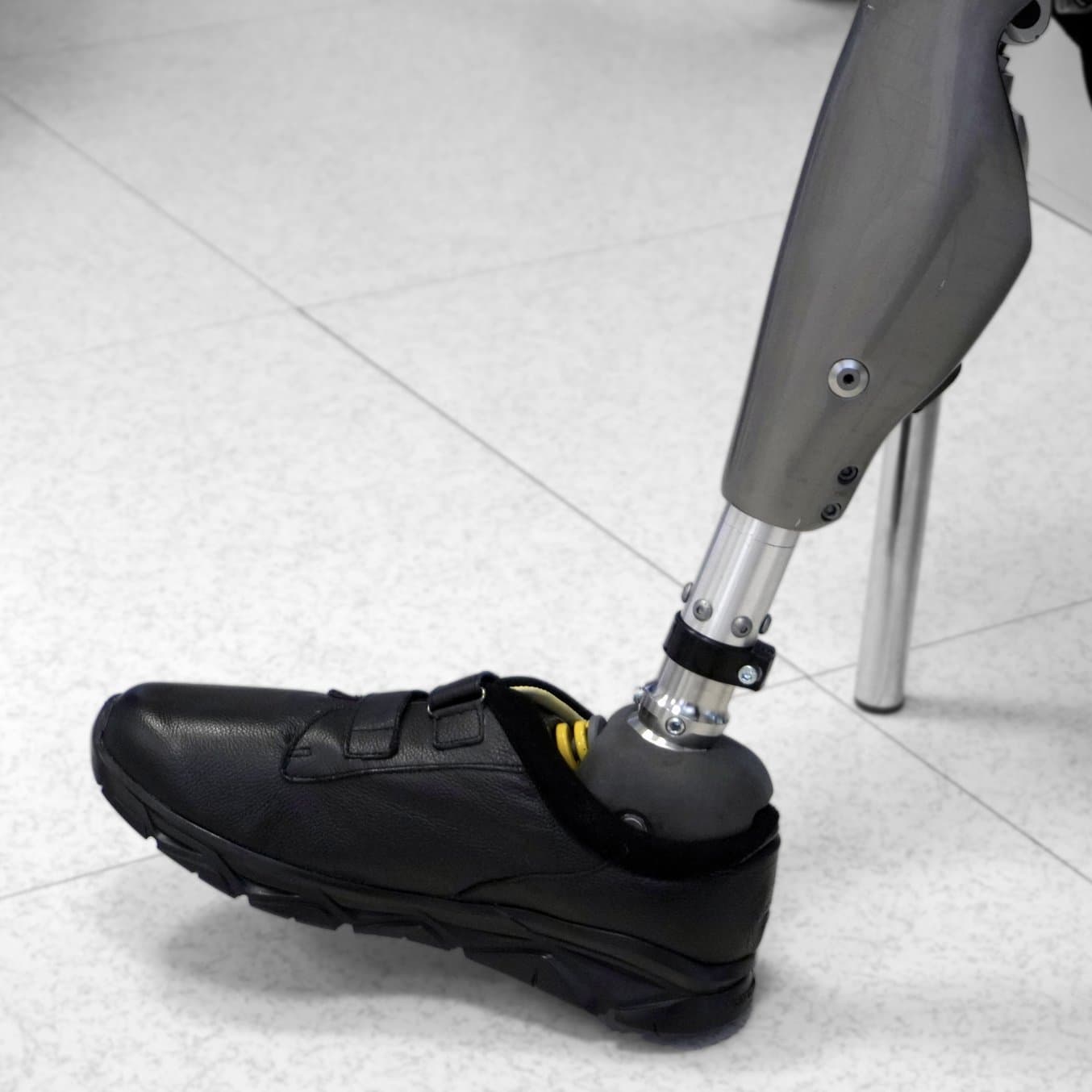
Der NOVA Foot kann im Schuh oder auch unbedeckt verwendet werden.
Drei Federn sorgen dafür, dass die 3D-gedruckten Komponenten des Fußes beweglich sind. Die Beugung des Fußes kann mit weicheren oder härteren Federn angepasst werden. Da die drei Federn jederzeit ausgetauscht werden können, ist der NOVA Foot ideal für weniger aktive Patienten, die eine Prothese mit reibungslosen Bewegungsabläufen und Komfort vorziehen, aber auch für aktivere Patienten, die eine reaktionsfähige Prothese benötigen, die bei kurzen sportlichen Aktivitäten Energie zurückgibt. Der Austausch der drei Federn unterstützt auch den rehabilitativen Verlauf unmittelbar nach einer Beinamputation.
Wünscht sich ein Patient zum Beispiel mehr Komfort während der Fersenauftrittphase und mehr Druck während der Zehenabdruckphase, kann eine weichere Feder in der Ferse und zwei steifere im Vorfuß eingebaut werden, um die Reaktion des NOVA Foot individuell anzupassen.
Warum mit 3D-Druck fertigen?
„Mit 3D-Druck sind wir in der Lage, die Teile in sehr kurzer Zeit intern zu produzieren. Dadurch können wir sehr schnell von der Idee zum Prototyp und vom Prototyp zur Fertigung übergehen. Zudem können wir mit 3D-Druck auch komplexe Geometrien herstellen, die mit herkömmlichen Fertigungstechnologien nicht möglich wären.“
Marco Garano, Geschäftsführer, C.P.T.
Die Herstellung des NOVA Foot wäre mit einer anderen Fertigungsmethode nicht möglich. Der hohe Grad an Individualisierung so vieler Elemente wäre bei anderen Produktionsverfahren, z. B. Spritzguss oder Zerspanung, unerschwinglich. Darüber hinaus erklärt Marco Garano: „Da wir die Teile mit dem Fuse 1+ 30W herstellen, sind wir in der Lage, sehr komplexe, im Inneren hohle Geometrien umzusetzen, mit Verstärkungen an bestimmten Stellen, die mit der Finite-Elemente-Methode ermittelt wurden. Dadurch sind die Teile leicht, aber gleichzeitig robust und funktionsfähig. Ein weiteres Beispiel ist die Einlage mit Fersenstütze aus TPU, die einen inneren Hohlraum hat, um die Dichte an diesem speziellen Punkt zu verringern.“
„Wir haben uns zur Herstellung der Bestandteile des NOVA Foot für den 3D-Druck entschieden, weil wir die volle Kontrolle über den Fertigungsprozess behalten wollten. Und wenn wir die Teile anpassen müssen, um sie auf die Bedürfnisse des Patienten zuzuschneiden, müssen wir dafür nicht die Kosten für die Anpassung der Formwerkzeuge aufbringen.“
Valentina Garano, Leiterin Vertrieb und Marketing, Protosystem
Die Kosten für Spritzgussformen zur Fertigung aller Bestandteile des NOVA Foot können auf 50 000 bis 60 000 € pro Fußgröße geschätzt werden, bei einer Mindestanzahl von sechs Größen. Allein die Formwerkzeuge für die sechs Größen würden sich auf Kosten von mindestens 300 000 € belaufen, was für das Unternehmen unerschwinglich ist.
Der betriebsinterne 3D-Druck bietet außerdem eine widerstandsfähige Lieferkette, ein geringeres Risiko und kurze Durchlaufzeiten sowohl für die Prototypenentwicklung als auch für die Fertigung. Außerdem wird durch die Neuzuführung gebrauchten Pulvers beim SLS-Druck der Abfall minimiert. Derzeit dauert der Druck eines einzigen NOVA Foot im Fuse 1+ 30W etwa fünf Stunden, und es können bis zu vier Prothesen in einem einzigen Druckvorgang hergestellt werden.
„Aus unserer Sicht liegen die Vorteile des Formlabs-Ecosystems (SLS und SLA) in der Möglichkeit, die Kosten sofort abzuschätzen, in der Einfachheit des Workflows vom Einfüllen des Materials bis zur Nachbearbeitung und in der sehr präzisen Druckzeitanalyse in PreForm.“
Marco Garano, Geschäftsführer, C.P.T.
Protosystem verwendet sowohl einen SLS-3D-Drucker vom Typ Fuse 1+ 30W als auch den SLA-3D-Drucker (Stereolithografie) Form 3B+ für das Prototyping und die Produktion, während bei der Druckvorbereitung Formlabs' Software PreForm zum Einsatz kommt. PreForm ermöglicht es Marco Garano, in Echtzeit genaue Schätzungen der Druckzeit und des Materialverbrauchs einzusehen, was ihm die Kontrolle seiner Fertigungsprozesse erleichtert.
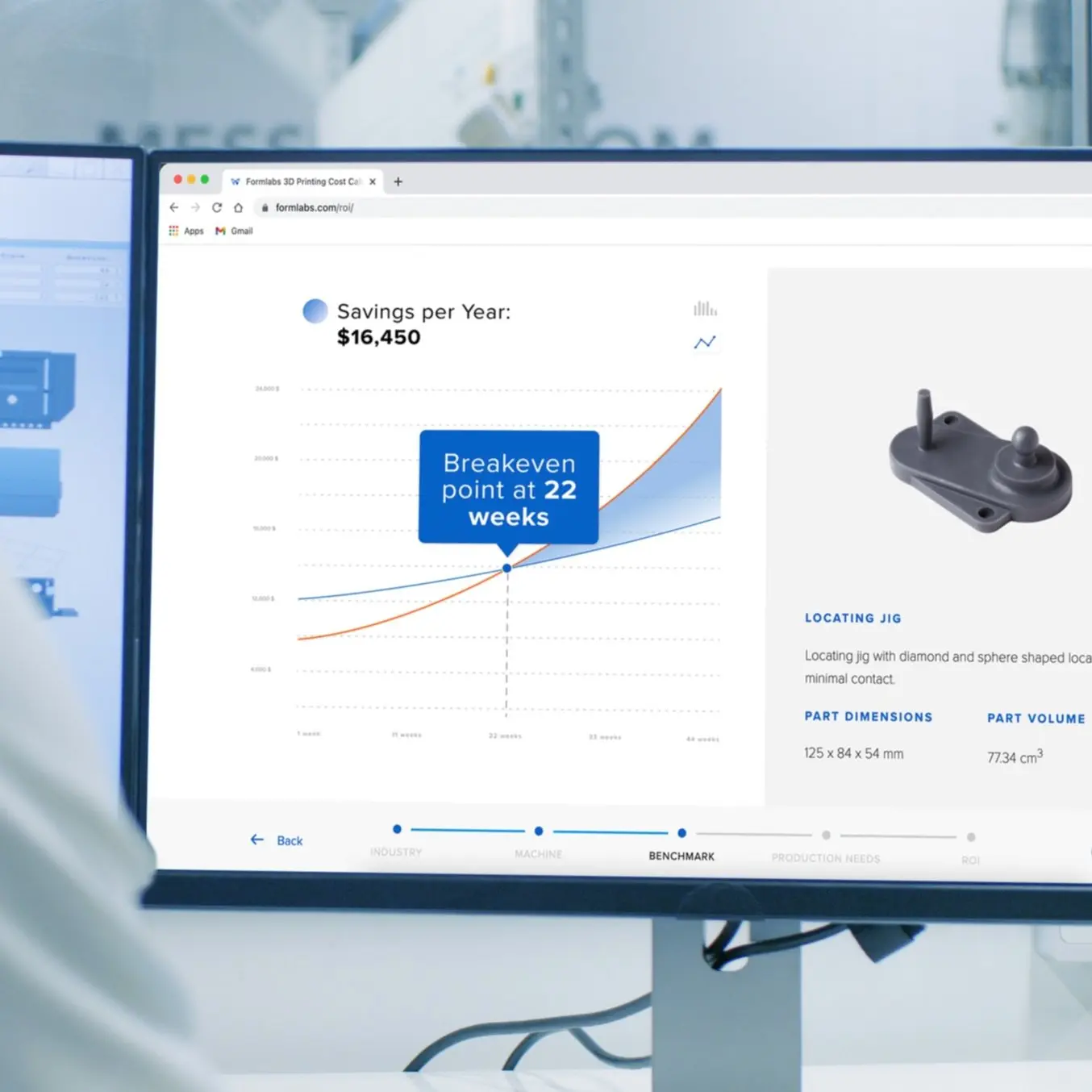
Berechnen Sie Ihre Zeit- und Kostenersparnis
Nutzen Sie unser interaktives ROI-Tool zur Berechnung Ihrer Zeit- und Kostenersparnis beim 3D-Druck mit einem Formlabs-Drucker.
„Ein Vorteil von Formlabs ist die Bandbreite an Materialien, die zum Erstellen und Testen verschiedener Teile zur Verfügung steht.“
Valentina Garano, Leiterin Vertrieb und Marketing, Protosystem
Der Zugang zu Formlabs' umfassender Palette von über 40 Hochleistungsmaterialien war ein entscheidender Vorteil, um die anspruchsvollen Anforderungen dieses Projekts erfüllen zu können. Der NOVA Foot erforderte einige ganz bestimmte Materialeigenschaften: Er musste haltbar, leicht, wasserfest, ästhetisch ansprechend und erschwinglich sein und wiederholtem Einsatz unter Belastung standhalten. Marco Garano arbeitete hierfür mit SLS-Materialien; zunächst nutzte er Nylon 11 Powder für die Prototypenentwicklung und ging dann zu Nylon 12 Powder für die Fertigung über.
Nylon 12 Powder wird für den Großteil des Fußes verwendet, da es leicht, aber gleichzeitig resistent gegen Kompression und Stöße ist und eine hohe Umweltstabilität aufweist. Marco Garano erklärt: „Wir haben uns für Nylon 12 Powder entschieden, weil die Drucktoleranzen bei diesem Material besser sind, die Teile, die sich berühren, nicht manuell angepasst werden müssen und die Kosten für die endgültigen Teile etwas niedriger sind als bei Nylon 11 Powder.“
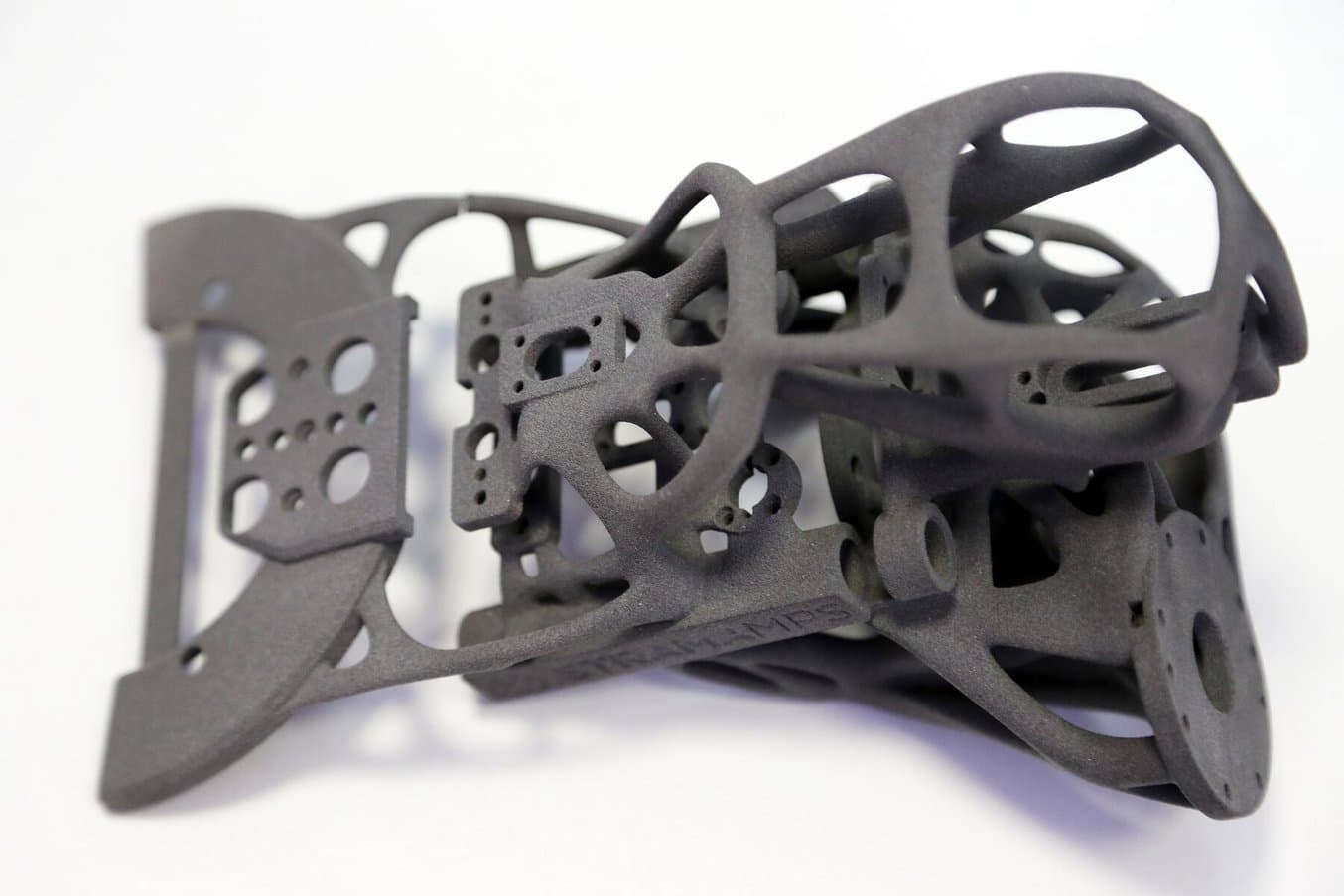
Design-Leitfaden für die Fuse-Serie
Dieser Leitfaden behandelt die wichtigen Abmessungen und Designüberlegungen, die bei der Konstruktion von Teilen für den SLS-3D-Druck auf der Fuse-Serie zu beachten sind. Sie lernen, wie Sie sich diese Praktiken zunutze machen, um leistungsstarke Teile zu produzieren.
TPU 90A Powder wird für ein Fersen- und ein Vorfußpolster sowie für Federabdeckungen verwendet, die Duktilität erfordern. Das Fersenpolster verfügt über eine interne Gitterstruktur, die beim täglichen Gebrauch des Fußes für Komfort sorgt. Gitterstrukturen lassen sich mit anderen Fertigungsmethoden als dem 3D-Druck nicht herstellen.
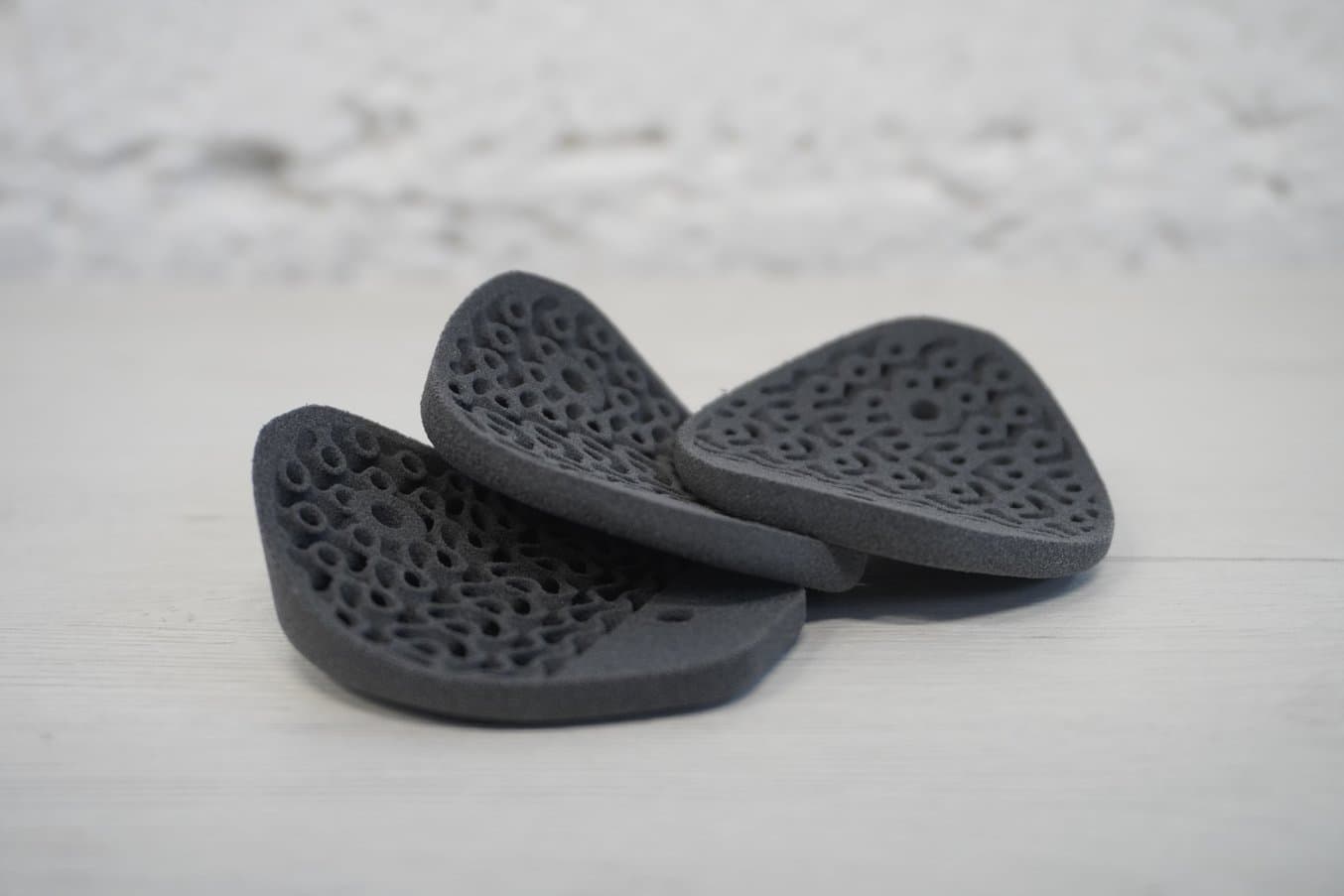
Die Gitterstruktur der Fersenkissen dämpft den Aufprall. Diese internen Strukturen lassen sich mit keiner anderen Fertigungsmethode erstellen als mit 3D-Druck.
Die Polsterung dämpft nicht nur den Aufprall, sondern gibt auch Halt beim Gehen. Marco Garano sagt: „Durch die zwei Einlagen konnten wir einen Überzug wie bei herkömmlichen Prothesen aus Kohlenstofffaser vermeiden und so das endgültige Gewicht der Prothese deutlich reduzieren.“
Bei herkömmlichen Carbon-Prothesen werden Überzüge verwendet, um Haftung zu gewährleisten, den Fuß vor Nässe zu schützen und den Schuh zu füllen. Das Design des NOVA Foot füllt den Schuh aus, ohne dass ein Überzug nötig ist. Außerdem müssen die Materialien, aus denen der NOVA Foot hergestellt wird, nicht vor Wasser geschützt werden, und die Polsterung aus TPU 90A Powder bietet ausreichend Traktion.
Im Durchschnitt wiegt eine Erwachsenen-Prothese aus carbonfaserverstärktem Kunststoff zwischen 400 und 600 Gramm, hinzu kommen etwa 200 Gramm für den ästhetischen Überzug. Demgegenüber wiegt der NOVA Foot 550 Gramm und benötigt keinen ästhetischen Überzug, wodurch er leichter ist als eine Prothese aus Kohlenstofffaser.
Zusätzlich zu den mit SLS-3D-Druck hergestellten Teilen kommen auch SLA-Teile zum Einsatz, um die Federn an ihrem Platz zu halten. Diese Federhalterungen benötigen eine sehr glatte Oberfläche, um gleitfähig zu sein, sowie hohe Maßgenauigkeit, um bei minimalem Spiel in die Teile aus Nylon 12 Powder zu passen. Die Federhalterungen werden mit Tough 2000 Resin gedruckt, einem ABS-ähnlichen Material für starke und robuste Teile, die auch langfristigem Gebrauch standhalten.
„Die Verbindung zwischen den Federhalterungen aus Tough 2000 Resin und den Fußteilen aus Nylon 12 Powder stellt die hohe Präzision der Formlabs-Drucker gut zur Schau.“
Valentina Garano, Leiterin Vertrieb und Marketing, Protosystem
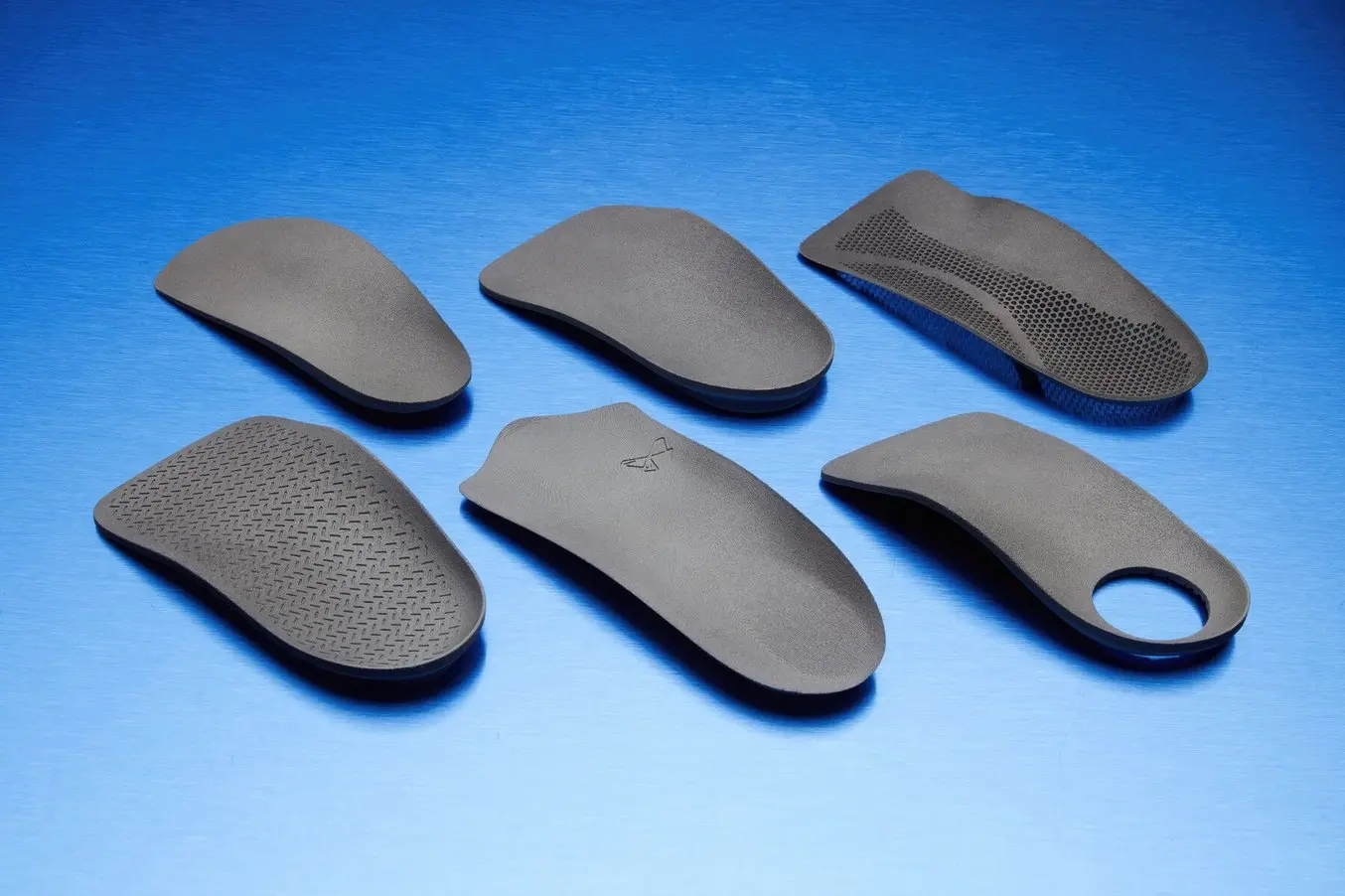
Patientenspezifische Orthesen mit 3D-Druck
Maßgefertigte Orthesen lassen sich jetzt einfach und kostengünstig betriebsintern herstellen: mit einem simplen und sauberen digitalen Prozess, der Kosten und Arbeitsaufwand verringert, die Durchlaufzeit verkürzt und den Vorgang für Kund*innen unkomplizierter macht.
NOVA Foot im Test
Die ersten Tests werden mit der Finite-Elemente-Analyse (FEA) in SolidWorks fertiggestellt. Sobald das Design getestet ist, wird es gedruckt und physischen Tests unterzogen. Mithilfe von Maschinen wird die mechanische Bewegung verschiedener Tätigkeiten simuliert und der Fuß einem Belastungstest ausgesetzt. Das fertige Produkt muss in der Lage sein, wiederholten, gewichttragenden Bewegungen standzuhalten. Da bei der Prototypenentwicklung dasselbe Verfahren eingesetzt wird wie bei der Fertigung, lässt sich anhand der Tests genau nachvollziehen, wie der NOVA Foot funktionieren wird.
Die Federn im NOVA Foot müssen jedes Jahr von Nutzerseite ausgetauscht werden, um die volle Funktionalität zu erhalten. Da die Teile aus Nylon 12 Powder jedoch nur Stauchung ausgesetzt sind, sollten sie über drei Jahre halten.
Nach internen Tests arbeitet Protosystem mit orthopädischen Fachleuten und Orthopädiezentren zusammen, um das Produkt in der Praxis zu testen. Vor der Freigabe wurde der NOVA Foot von freiwilligen Patient*innen in einem Sportzentrum für Amputierte sowie auch im Alltag getestet. Wie Protosystem berichtet, waren die Tester*innen von der flüssigen Bewegung des Nova Foot beim hinauf- und hinablaufen auf einer Rampe begeistert. Sie berichteten auch, dass die Energierückgabe des NOVA Foot beim Gehen sehr hoch ist und sie bei jedem Schritt unterstützt.
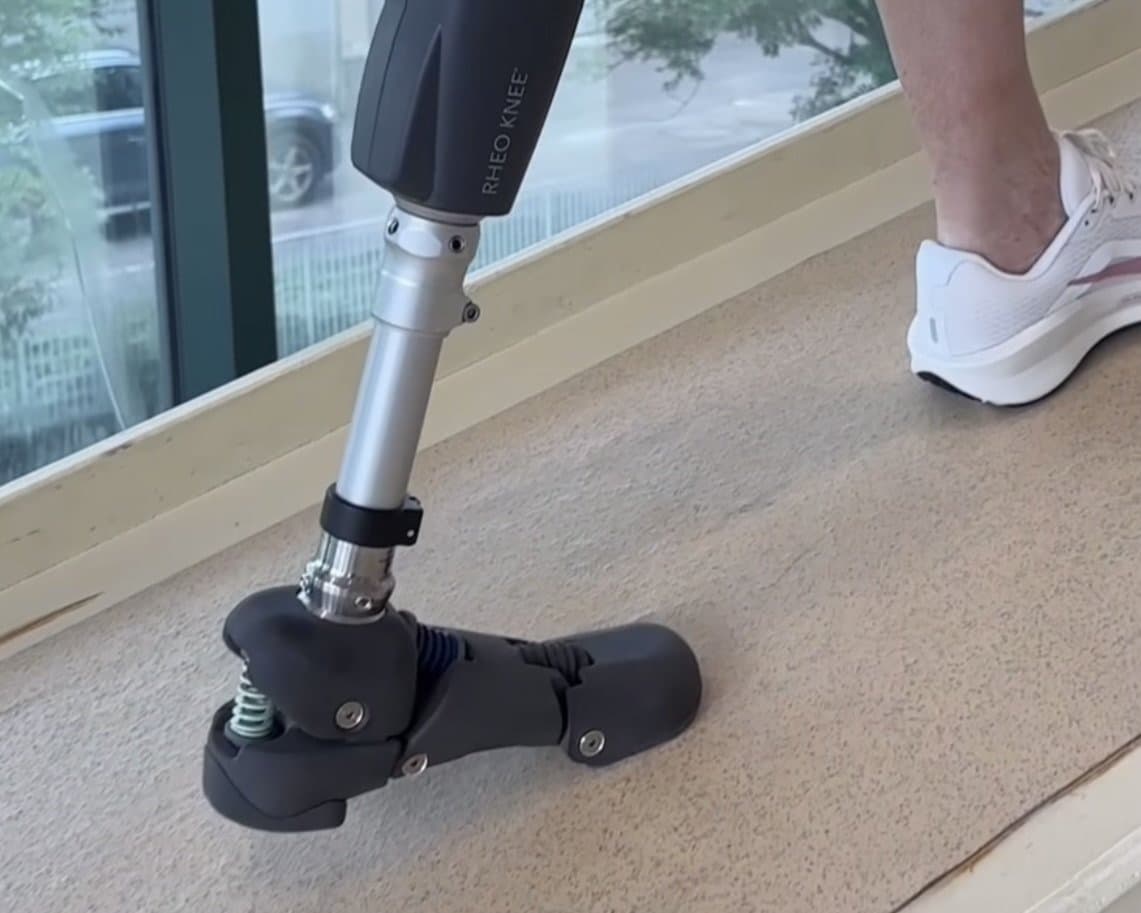
NOVA Foot wurde sowohl beim Sport als auch im Alltag getestet, wobei die Tester*innen anmerkten, wie flüssig sie damit Rampen hinaufgehen konnten.
Dank des 3D-Drucks können Änderungen und Anpassungen anhand eingehender Patientenrückmeldungen dynamisch vorgenommen werden, ohne dass die Fertigung unterbrochen werden muss. Ein Amputationspatient benötigte zum Beispiel zusätzlichen Halt in der Fersenauftrittphase sowie mehr Stoßdämpfung. Marco Garano konnte das Modell in wenigen Stunden individualisieren, indem er den oberen Teil des Fußes und die Befestigung anpasste, um den Halt zu verbessern und mehr Stoßdämpfung zu bieten. Nachdem die Änderungen vorgenommen wurden, dauert der Druck des Fußes nur fünf Stunden, sodass derartige Anpassungen bereits innerhalb eines Tages möglich sind.
Nach einem Jahr der Forschung und verschiedenen Iterationen von Prototypen wurde NOVA Foot im März 2025 auf den Markt gebracht und stieß bei den Patient*innen, die die Prothese bisher ausprobiert haben, dank ihrer einzigartigen Eigenschaften auf viel Begeisterung.