Nach Angaben des amerikanischen Bureau of Labor Statistics scheitert die Hälfte aller US-Unternehmen in den ersten fünf Jahren. Wie können Unternehmer in Anbetracht dieser Widrigkeiten also die von ihnen angestrebte Langlebigkeit erreichen, Fehlschläge vermeiden und sich gegen Stolpersteine wappnen?
Für Brandon Talkmitt, den Gründer und Inhaber von BTI Gauges, liegt die Antwort auf diese Frage im 3D-Druck mit dem SLS-Drucker (selektives Lasersintern) Fuse 1. Talkmitt hat nicht nur eine Marktnische für sich gewonnen, er hat ein Nebenprojekt in ein erfolgreiches Vollzeitunternehmen verwandelt, das selbst die COVID-19-Pandemie, die Engpässe in der globalen Lieferkette und die steigenden Preise für Rohmaterialien überstanden hat.
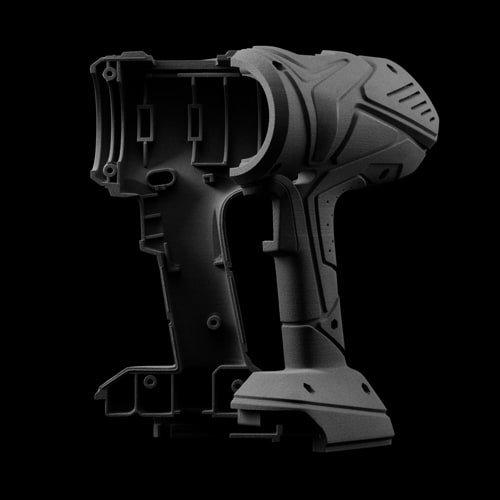
Einführung in den 3D-Druck mit selektivem Lasersintern (SLS)
Suchen Sie nach einem 3D-Drucker, mit dem Sie starke, funktionsfähige Teile herstellen können? Laden Sie unser Whitepaper herunter, erfahren Sie, wie SLS-Druck funktioniert und wieso es ein beliebtes 3D-Druckverfahren für funktionales Prototyping und die Produktion von Teilen für die Endverwendung ist.
Die Marktlücke finden
Wie die meisten erfolgreichen Unternehmen nahm auch BTI Gauges seinen Anfang in einer Marktlücke. Talkmitt suchte nach einer individualisierten Telemetrieanzeige für seinen Sportwagen. In einem herkömmlichen Fahrzeug beschränken sich die Anzeigen im Armaturenbrett auf Werte wie Geschwindigkeit und Umdrehungen. In einem Sportwagen müssen Fahrer aber oft mehr über die Leistung des Fahrzeugs wissen, um bei Geschwindigkeiten über 240 km/h die sichere Kontrolle zu behalten. Bei solch hohen Geschwindigkeiten und der zugehörigen PS-Leistung sind Angaben wie der Druck der Kühlflüssigkeit entscheidend für die Sicherheit. Um all diese Informationen im Blickfeld zu haben, bauen viele Fahrer zusätzliche Messgeräte ein, die Werte anzeigen wie das Luft-Kraftstoff-Verhältnis, die Turboladung, den Druck der Kühlflüssigkeit uvm.
„Sollte mal etwas schieflaufen, läuft es bei der Leistung dieser Autos sehr schnell richtig aus dem Ruder. Und die Reparaturkosten sind unsäglich teuer“, sagt Talkmitt. Um eben dieses Schieflaufen zu verhindern, müssen die Fahrer*innen ein ständiges Auge auf die Anzeigen werfen, falls der Druck zu hoch wird oder der Motor heiß läuft. Jedoch nehmen bei so vielen Werten die Anzeigen im Fahrerbereich bald Überhand.
Talkmitt suchte vergebens nach einer Anzeige, die mehrere Leistungswerte kombiniert, damit seine Windschutzscheibe nicht von Bildschirmen und Ablenkungen übersät war. Und so erschuf er – wie schon so viele Firmengründer vor ihm – selbst das, was er auf dem Markt nicht finden konnte. „Ich suchte etwas, das wohl niemand herstellte. Und so entwarf ich halt selbst eine einzelne runde Anzeige mit einem Touchscreen, auf dem alle Informationen zu finden waren“, erzählt uns Talkmitt. Zunächst entwarf er Prototypen des Anzeigegehäuses auf einem Schmelzschichtungsdrucker (FDM) und testete sie persönlich. Er setzte sie hohen Temperaturen aus wie im Fahrzeuginneren oder im Ofen. Und er passte das Design an, damit es in mehrere Fahrzeuge passte.
Klasse Optik, tolle Leistung
Es gab sofort Interesse an dem Produkt – Kund*innen mit japanischen Rennwagen im Stil der 90er, Lamborghinis, Dodge Vipers und andere Sportwagen. Autoliebhaber*innen, die sich in die Ästhetik eines Wagens verlieben, sehen es nur ungern, wenn ihr Armaturenbrett mit hässlichen Anzeigen vollgestopft wird. Ein einzelner schnittiger Touchscreen mit Daten erwies sich sowohl als effizient als auch als optisch ansprechend.
Doch dabei stieß Talkmitt auf das nächste Problem. Die Oberflächenqualität der FDM-Drucke konnte mit dem hochklassigen Aussehen und der angestrebten Haptik des Designs nicht mithalten. „Viele störten sich an den Schichtlinien“, berichtet Talkmitt. „Wir mussten die Schichtlinien abschleifen und dann alles mit Spachtelmasse wieder auffüllen. Das war ein mühsamer Prozess.“
Deshalb schaute sich Talkmitt nach anderen 3D-Drucklösungen um, unter anderem teure 3D-Drucker mit Kunststoffpulverbettfusion, aber auch Kunstharzdrucker und eine kostengünstige und kompakte SLS-Option. Doch in Anbetracht eines Preises von einer halben Million Dollar auf der einen Seite und komplizierter Materialbeschaffung auf der anderen wollte sich die richtige Option einfach nicht finden lassen. Zumindest nicht, bis er vom Fuse 1 erfuhr. „Als ich den Probedruck in den Händen hielt, dachte ich: ‚Junge, wenn dein Teil auch so aussehen könnte ...‘ Also führte ich einige Tests durch. Ich untersuchte, mit welcher Hitze es fertig werden würde. Ich habe meinen Fertigstellungsprozess und die Lackierung daran ausprobiert. Und alles war einwandfrei“, so Talkmitt.
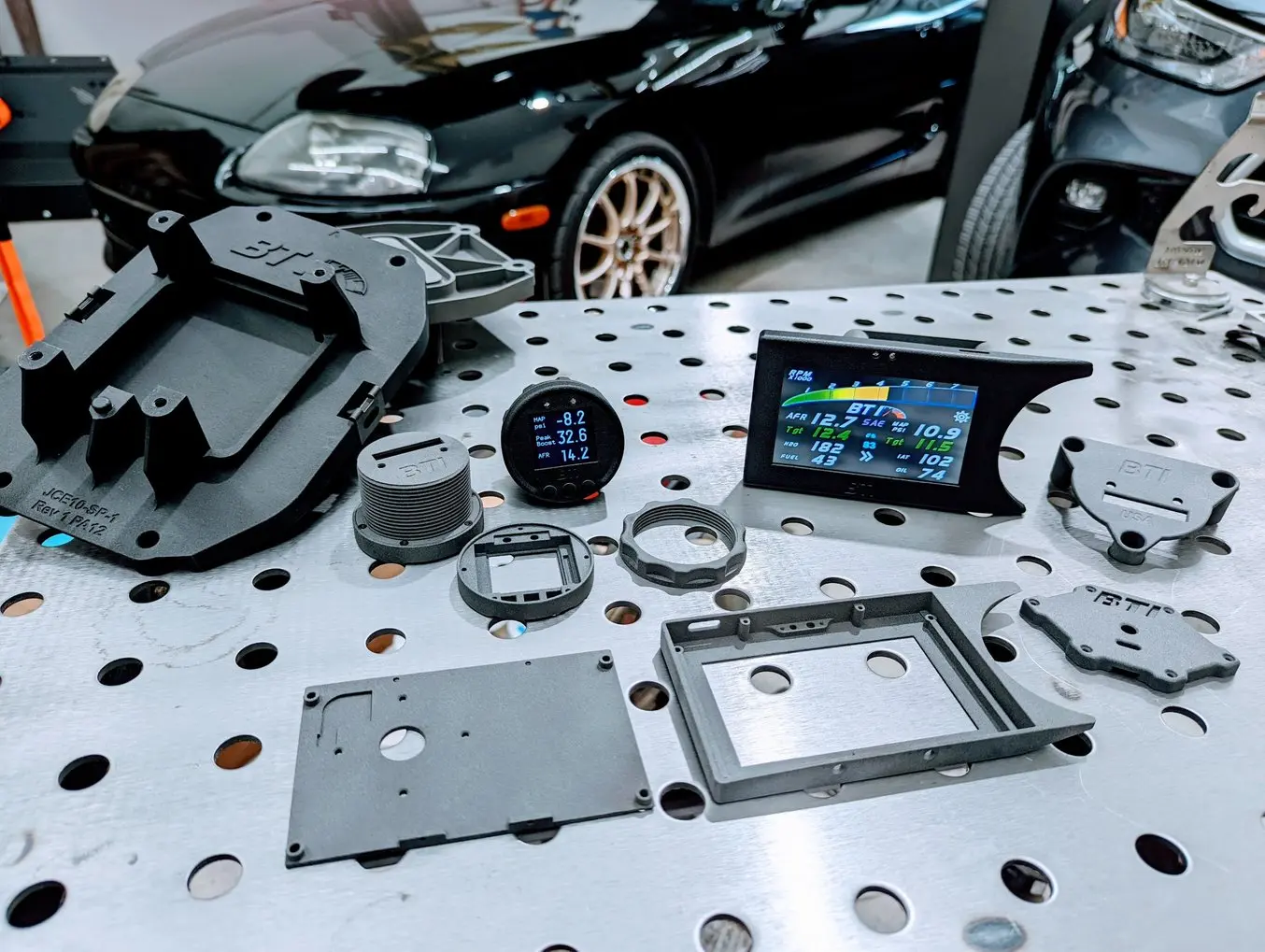
Haargenaue Präzision
Für Talkmitt kam es auf mehr an als nur auf das Aussehen, um mit der Produktion auf dem Fuse 1 durchzustarten. Die Teile mussten gleichmäßige Genauigkeit aufweisen, selbst in großen Mengen. Und nun hatte er endlich einen Drucker, der diese engen Toleranzen durchgängig erreichte. In seinen Dateien konnte Talkmitt die nötige Präzision ausloten, immer in dem Wissen, dass der Fuse 1 die von ihm entworfenen detailreichen Merkmale auch präzise drucken würde.
„Ich habe ein Loch von 40 × 40 mm entworfen. Und auf dem Fuse 1 kann ich jetzt einen Stift von 40 × 40 drucken und weiß, dass er genau passt. Wir fügen auch Gewinde ein und andere Merkmale, die genau stimmen müssen. Wenn es um Autos geht, verziehen sich Teile oft. Aber seit wir zum Fuse 1 übergegangen sind, habe ich nicht ein einziges verzogenes Teil gesehen.“
Brandon Talkmitt
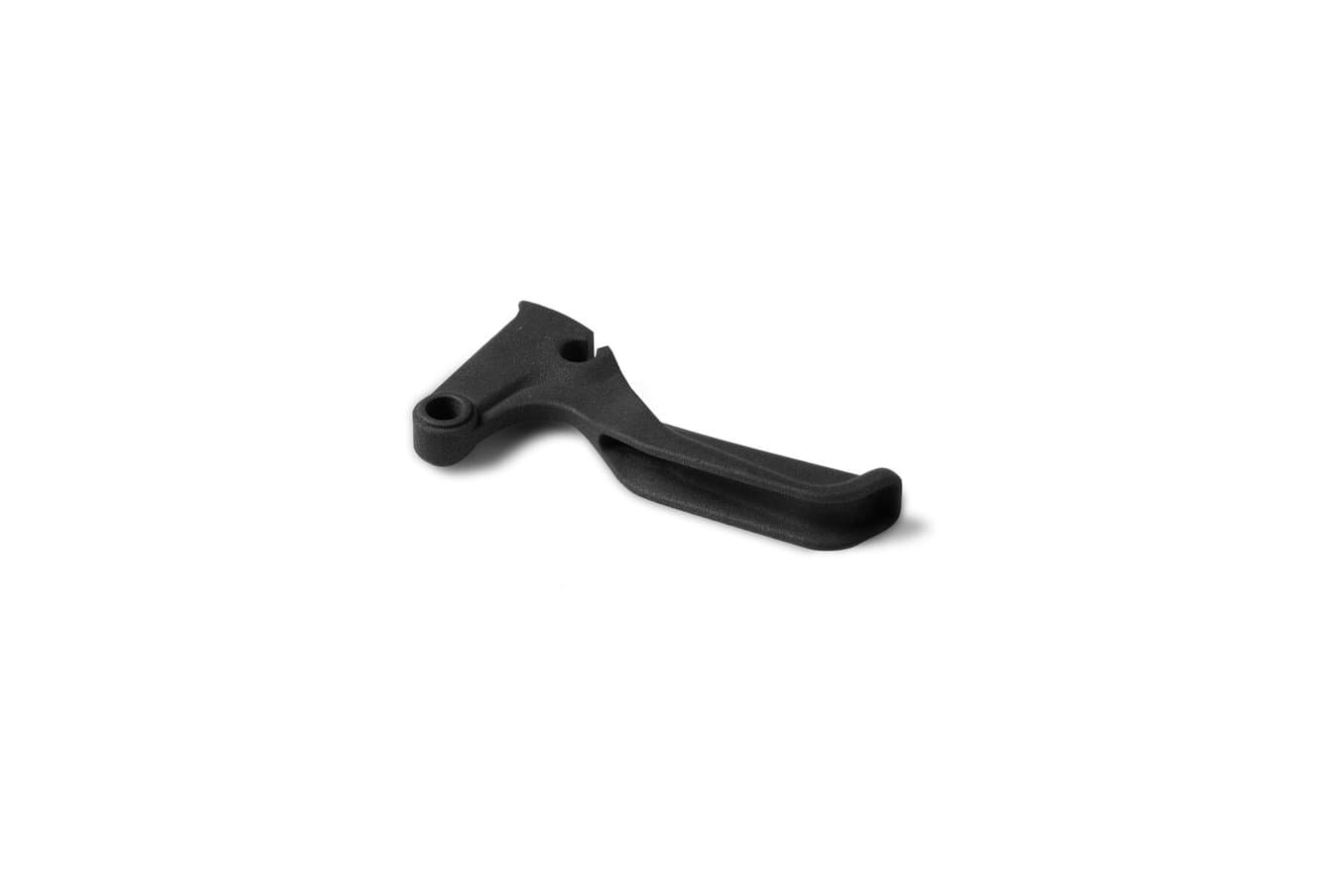
Fordern Sie einen kostenlosen Probedruck an
Erfahren Sie Formlabs Qualität aus erster Hand: Wir senden Ihnen einen kostenlosen SLS-Probedruck aus dem Fuse1+30W an Ihren Arbeitsplatz.
„Antifragile“ Fertigung
Teile dieser Art könnten auf vielfältige Weise hergestellt werden. Worin liegt also der Vorteil eines betriebsinternen SLS-Druckers? BTI Gauges erreicht damit etwas, dass Autor Nassim Nicholas Taleb als „Antifragilität“ bezeichnet. „Antifragile“ Sachen halten Druck und Schlägen nicht nur Stand, sie werden dadurch stärker, besser, effizienter. Während der Lieferkettenprobleme der letzten zwei Jahre sah sich BTI Gauges mehreren Engpässen bei den Touchscreens gegenüber sowie bei anderen Komponenten der neun Produktserien. Bei einem „fragilen“ Hersteller wäre die Produktion vielleicht zum Erliegen gekommen, die Auftragserfüllung, der Umsatz. Talkmitt war gezwungen, auf andere Displays umzuschwenken, was wiederum einen Prozessorwechsel nach sich zog und damit eine andere Leiterplatine, die dem Produkt eine andere Form verlieh.
Doch dank des betriebsinternen Fuse 1 konnte er unverzüglich auf das neue Design umschwenken, ohne Tausende Dollar für neue Werkzeugbestückung auszugeben oder sich mit einem Lagerbestand nun ausgedienter Komponenten rumzuschlagen. „Das ganze Kunststoffzeug hätte bei mir nur herumgelegen. Aber mithilfe des Fuse 1 konnte ich alles ganz leicht im Prozess umstellen. Es hat mich gerade einmal 30 Minuten gekostet, die Dateien anzupassen. Anderenfalls würde ich jetzt definitiv feststecken“, gibt Talkmitt an.
Talkmitt war nicht von einem externen Zulieferer abhängig und hielt seine Abläufe so geschlossen wie möglich. Aufgrund der Engpässe legt er eine Art digitales Inventar der Ersatzteile an, um sich gegen zukünftige Engpässe zu wappnen. Der wirtschaftliche Druck von außen hat sein Geschäftsmodell nur gestärkt. So ist er heute vor zukünftigen Störungen geschützt. Das entspricht der Textbuchdefinition von „Antifragilität“.
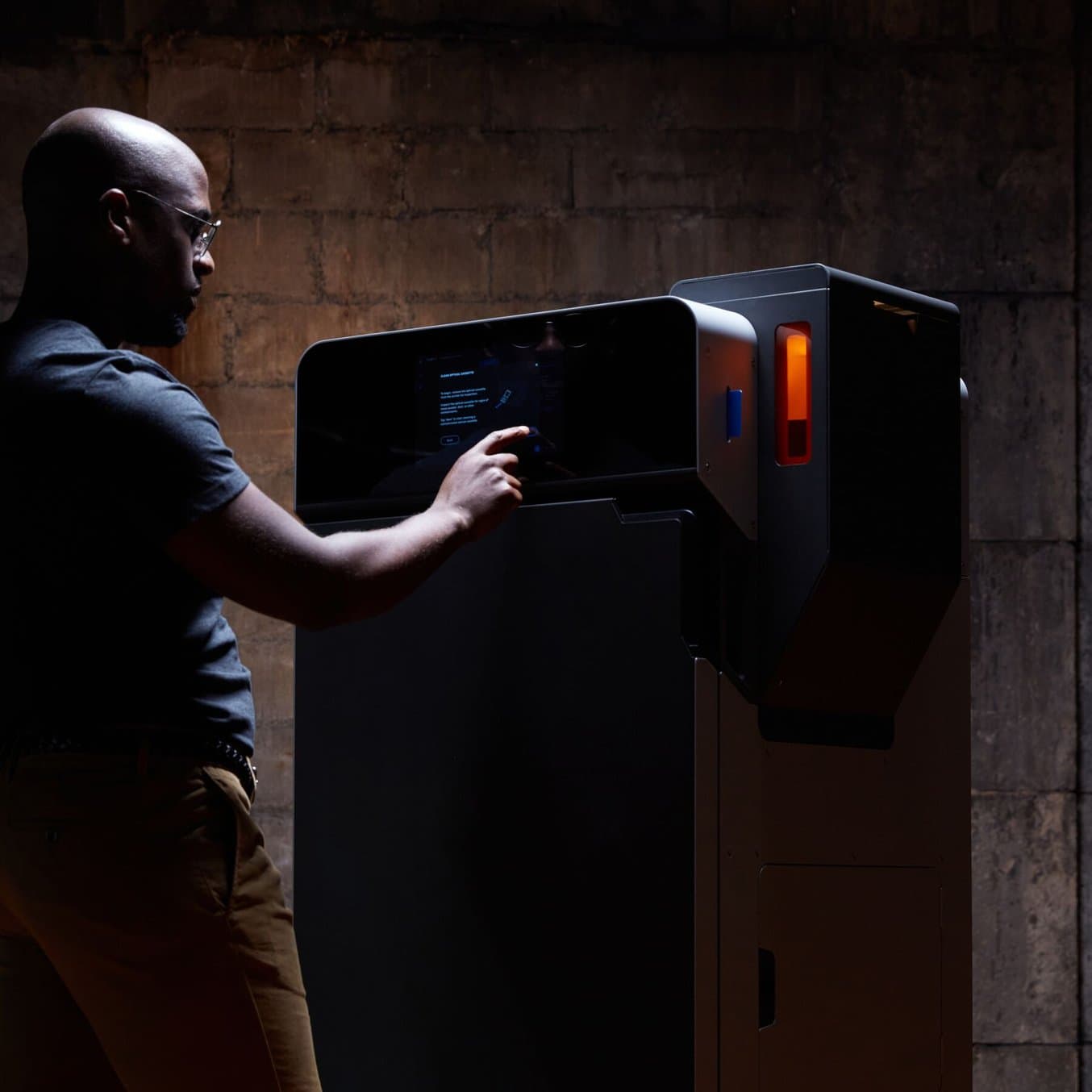
Outsourcing oder betriebsintern: Wann sollte man SLS-3D-Druck in den eigenen Betrieb holen?
In diesem Whitepaper untersuchen wir den Mehrwert betriebsinterner SLS-3D-Drucker im Vergleich zum Outsourcing von SLS-Teilen an einen Fertigungsdienstleister.
Hochleistungsproduktion
Um auch in Zukunft kosteneffizient und tragbar zu produzieren, verlässt sich Talkmitt auf die Effizienz der gesamten Fuse-Serie. Mithilfe von PreForms fortschrittlichem Packalgorithmus positioniert er kleine Teile in größeren Teilen, was seine Packdichte erhöht, damit sie so nah wie möglich mit der 30-prozentigen Neuzuführungsrate von Nylon 12 Powder übereinstimmt. „Wir haben eine Anzeige von 4,3 mm, die aus einem Vorder- und einem Hinterteil besteht. Da bleibt dann jedoch dieser große Hohlraum in der Mitte. Also nehme ich ein Teil von 3,5 mm und positioniere das darin. Wir füllen das Fertigungsvolumen ganz strategisch und erreichen damit regelmäßig eine Packdichte von 25 %“, führt Talkmitt aus.
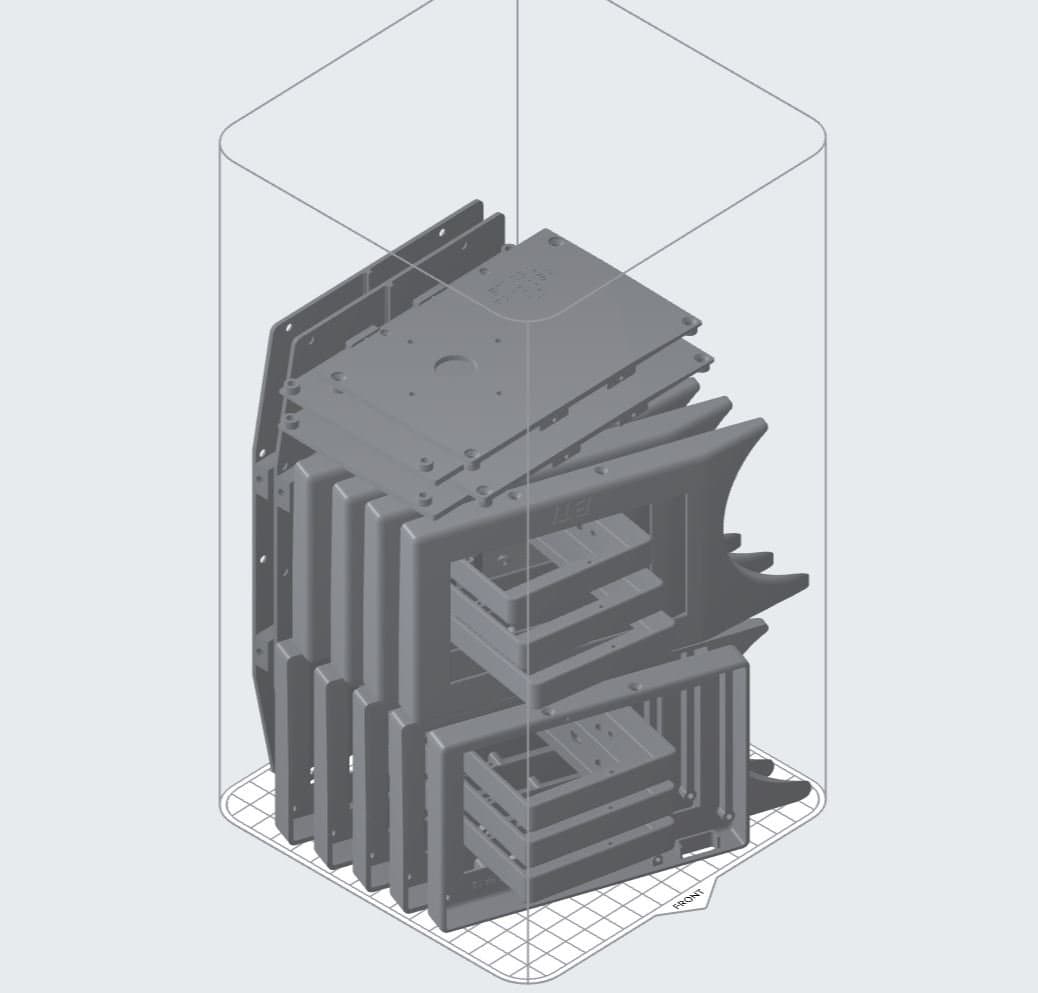
Visualisierung einer vollgepackten Konstruktionskammer in PreForm mit Teilen innerhalb größerer Teile (links) und ein Druckteil aus dem Fuse 1 in der Nachbearbeitungsphase (rechts)
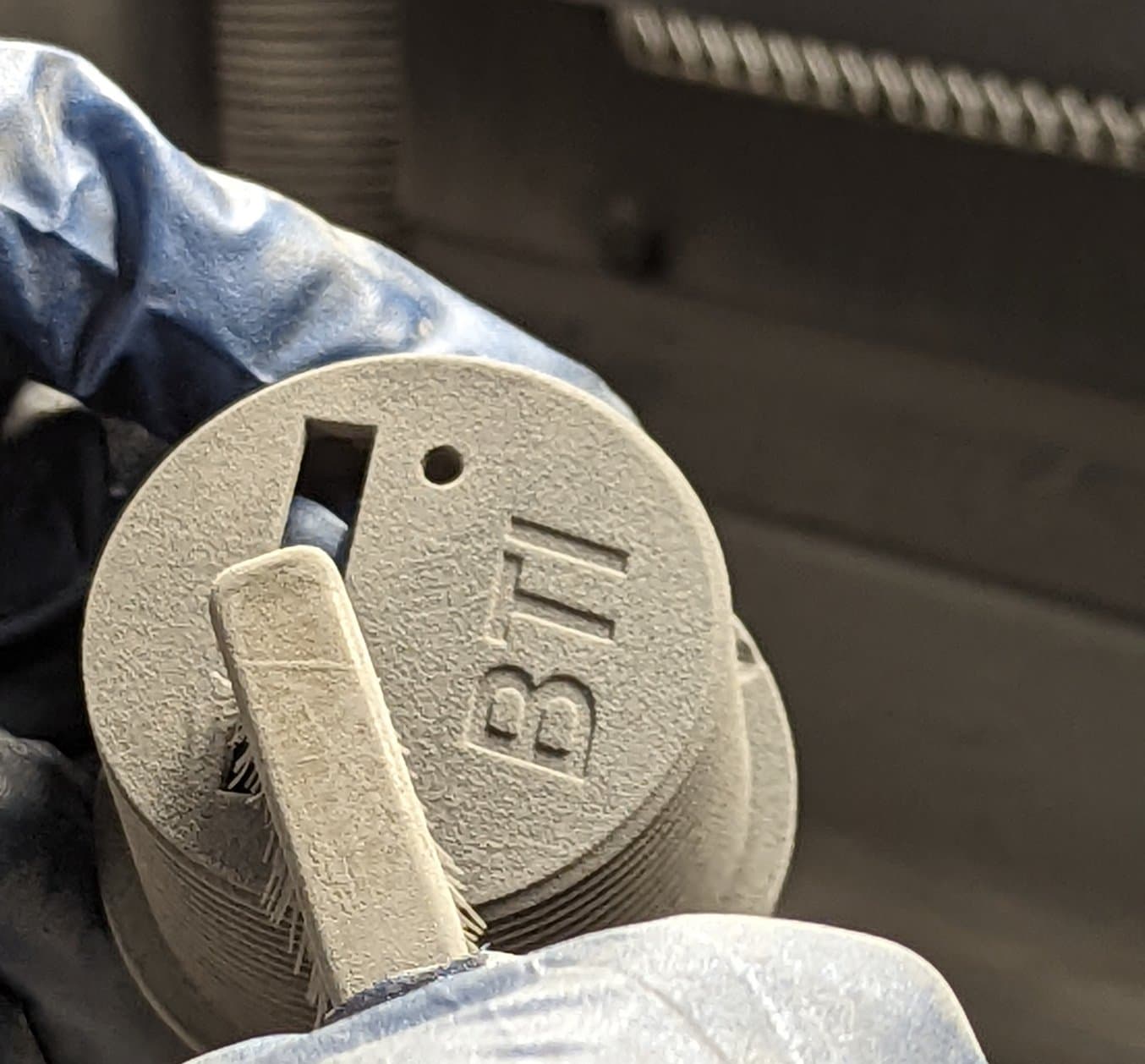
Durch diese effiziente Packdichte erreicht Talkmitt beinahe einen abfallfreien Druckprozess, bei dem jedes bisschen Pulver in fortwährenden Druckzyklen aufgebraucht wird. Für kleine Hersteller bedeutet diese Effizienz niedrigere Kosten pro Teil und schnellere Kapitalrendite.
Der hohe Durchsatz des Fuse 1 ermöglichte Talkmitt den Übergang von drei durchgängig arbeitenden FDM-Druckern zu einer einzelnen vollgepackten Konstruktionskammer pro Woche auf dem Fuse 1. Und durch die optimierten Arbeitsabläufe des Fuse Sift verbringt Talkmitt weniger Zeit mit der Nachbearbeitung und mehr Zeit mit dem Entwerfen neuer Teile und der Markenpräsenz. „Im hinteren Bereich unserer Werkstatt stehen der Fuse 1, der Fuse Sift und der Sandstrahler. Die Lackierung, der Zusammenbau und die Verpackung bilden dann von dort aus eine Schlange durch die Werkstatt. Die Größe und Stellfläche des Fuse 1 sind ideal für unseren Arbeitsprozess“, kommentiert Talkmitt.
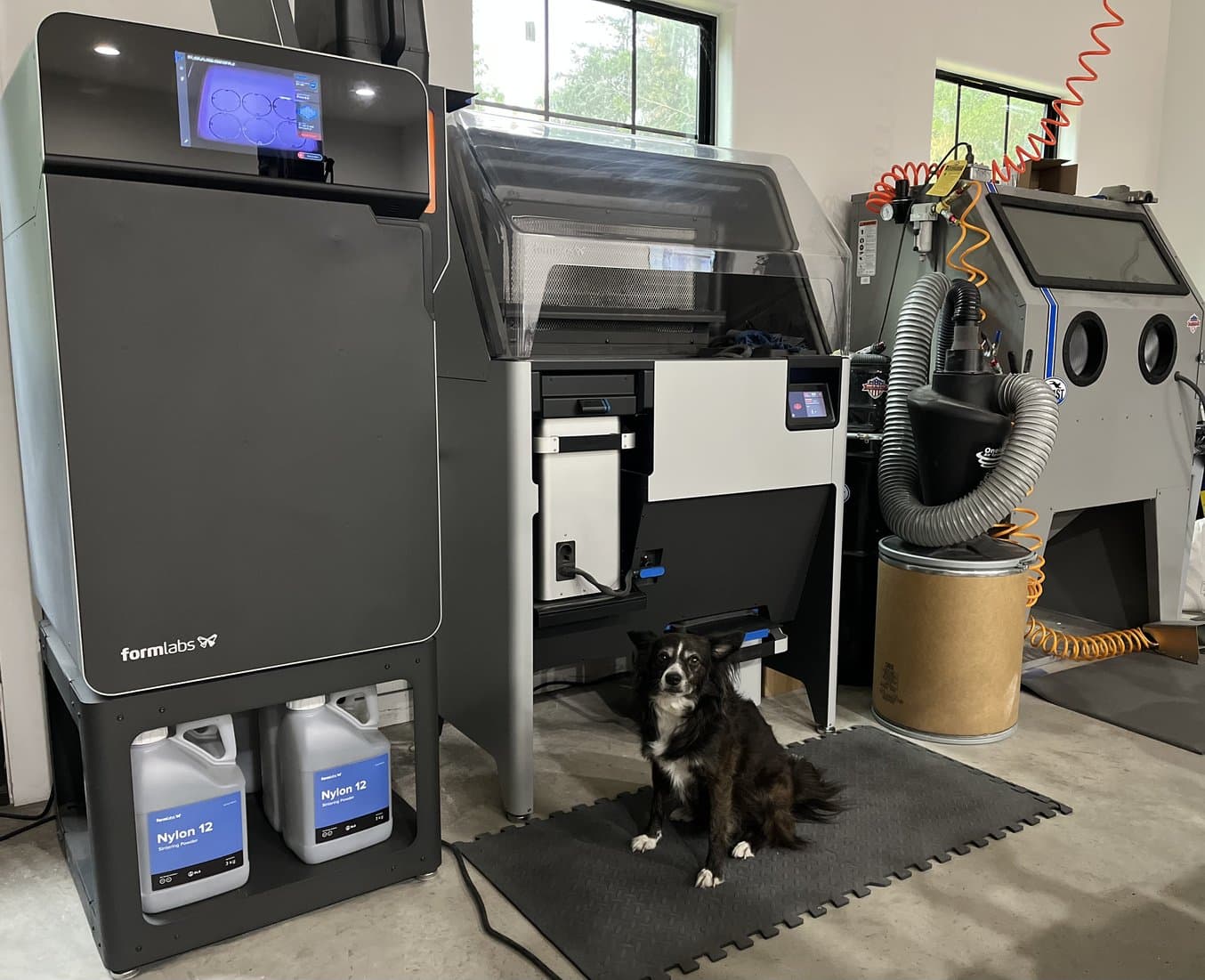
Der Fuse 1 und der Fuse Sift bieten eine platzsparende Stellfläche und einen optimierten Arbeitsablauf. Sie lassen sich leicht in einem bestehenden Arbeitsbereich unterbringen.
Vorwärts Marsch
Als junges Unternehmen ist es schwierig, sich auf einem Markt zu etablieren, auf dem Autos üblicherweise für Hunderttausende Dollar verkauft werden. Fügt man stockenden Welthandel, internationale Lieferkettenengpässe und Wirtschaftsturbolenzen hinzu, dann ist es nahezu unmöglich.
Nur dank betriebsinterner Fertigung mit einem hochqualitativen SLS-Drucker wie dem Fuse 1 kontrollierte und sicherte das Unternehmen seine Produktionsleistung, was es über alle hinweg katapultierte, die auf traditionelle Fertigung und externe Zulieferer angewiesen waren. „Ich kann es nur empfehlen. Der Fuse 1 hat für uns komplett neue Maßstäbe gesetzt“, zieht Talkmitt Bilanz.